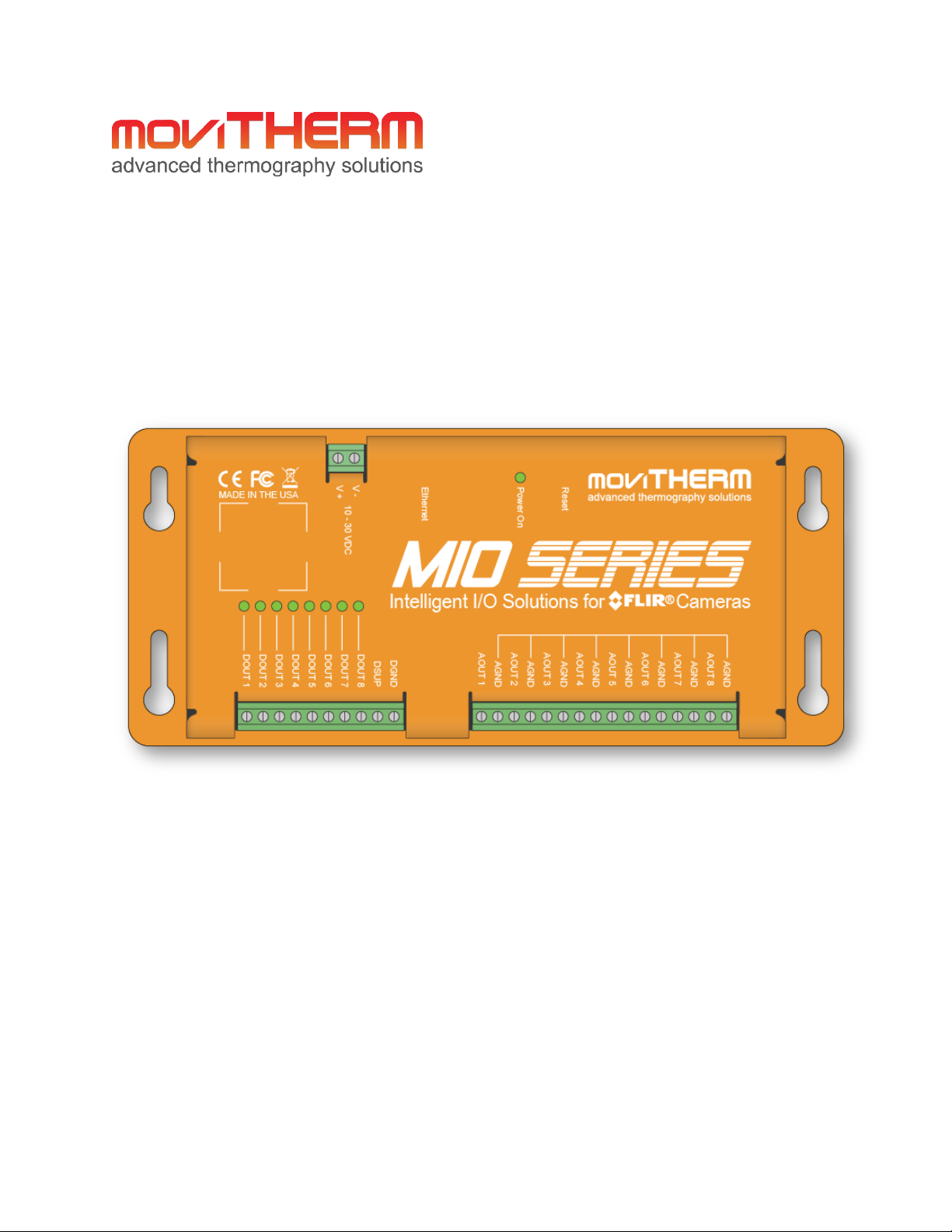
MoviTHERM MIO Series of Intelligent I/O Modules
Intelligent I/O Module for FLIR® A310 & A310(f) Cameras
User Manual
September 2016
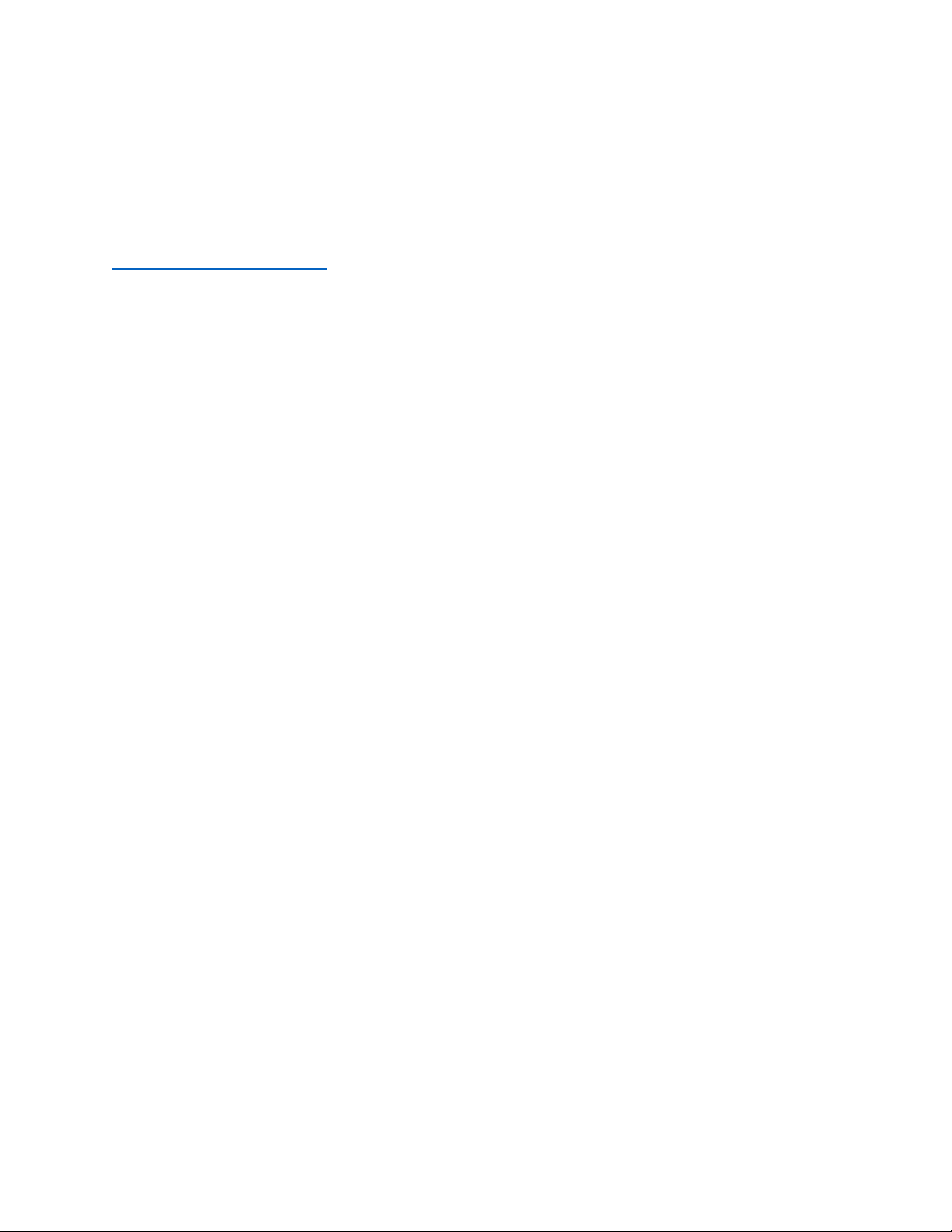
Revision 1.4
Support
Thank you for selecting MoviTHERM Products.
For product updates and web support, visit:
http://www.movitherm.com
General Disclaimer
MoviTHERM temperature monitoring solutions (hardware and software) are intended for
supplemental thermal monitoring. The device described in this document is only intended to
alert human operators of an emergency situation. The MoviTHERM device is not intended as a
substitute for prudent fire prevention practices and conventional fire prevention equipment,
nor is it a substitute for life and property insurance. The MoviTHERM device must be installed
and serviced by qualified professionals who, along with this documentation package, will
provide information about the capabilities and limitations of the device. While generally very
reliable, the device may not work under all conditions such as (but not limited to) interruptions
to power, component failure, and/or other unanticipated operational conditions that were not
present during installation, testing and validation. When correctly installed and maintained, the
MoviTHERM device explained in this document should reliably provide years of trouble-free
service. All MoviTHERM systems and devices must be used in combination with redundant fire
detection and response systems.
Compliance
The MIO I/O module is CE/FCC compliant. Refer to the MoviTHERM MIO Compliance
documentation supplied with the device.
Trademarks
FLIR, the FLIR logo, and all FLIR product names referenced in this document are trademarks
and/or registered trademarks of FLIR Systems, Inc. and/or its subsidiaries.
Information is subject to change without notice. ©2015 MoviTHERM - All rights reserved.

Table of Contents
1 Foreword .............................................................................................................................. 1
2 Device Overview .................................................................................................................. 2
3 Unpacking ............................................................................................................................ 2
4 Connecting the MIO I/O Module ......................................................................................... 3
5 Specifications ....................................................................................................................... 5
6 System Installation and Set-up ............................................................................................ 5
6.1 Configuration Procedure .................................................................................................. 6
6.1.1 IP Configuration ........................................................................................................ 7
6.2 Preparing MIO for Configuration ..................................................................................... 8
6.3 Assigning Actions to Camera Regions: The MIO Controller Utility .................................. 8
6.3.2 The Camera Settings Tab ........................................................................................ 14
6.3.3 The Debug Tab ........................................................................................................ 21
6.4 Recovery Mode .............................................................................................................. 22
6.4.1 Password Reset ....................................................................................................... 23
7 Operations ......................................................................................................................... 24
7.1 I/O Connections .............................................................................................................. 24
7.1.1 Digital Output Pin Definitions ................................................................................. 25
7.1.2 Analog Output Pin Definitions ................................................................................ 25
8 Troubleshooting Common Issues ...................................................................................... 28
9 Appendix A: Default Settings ............................................................................................. 30
10 Appendix B: Technical Specifications ................................................................................. 30
10.1 Absolute Maximum Ratings ........................................................................................... 30
10.2 Operating Specifications ................................................................................................ 30
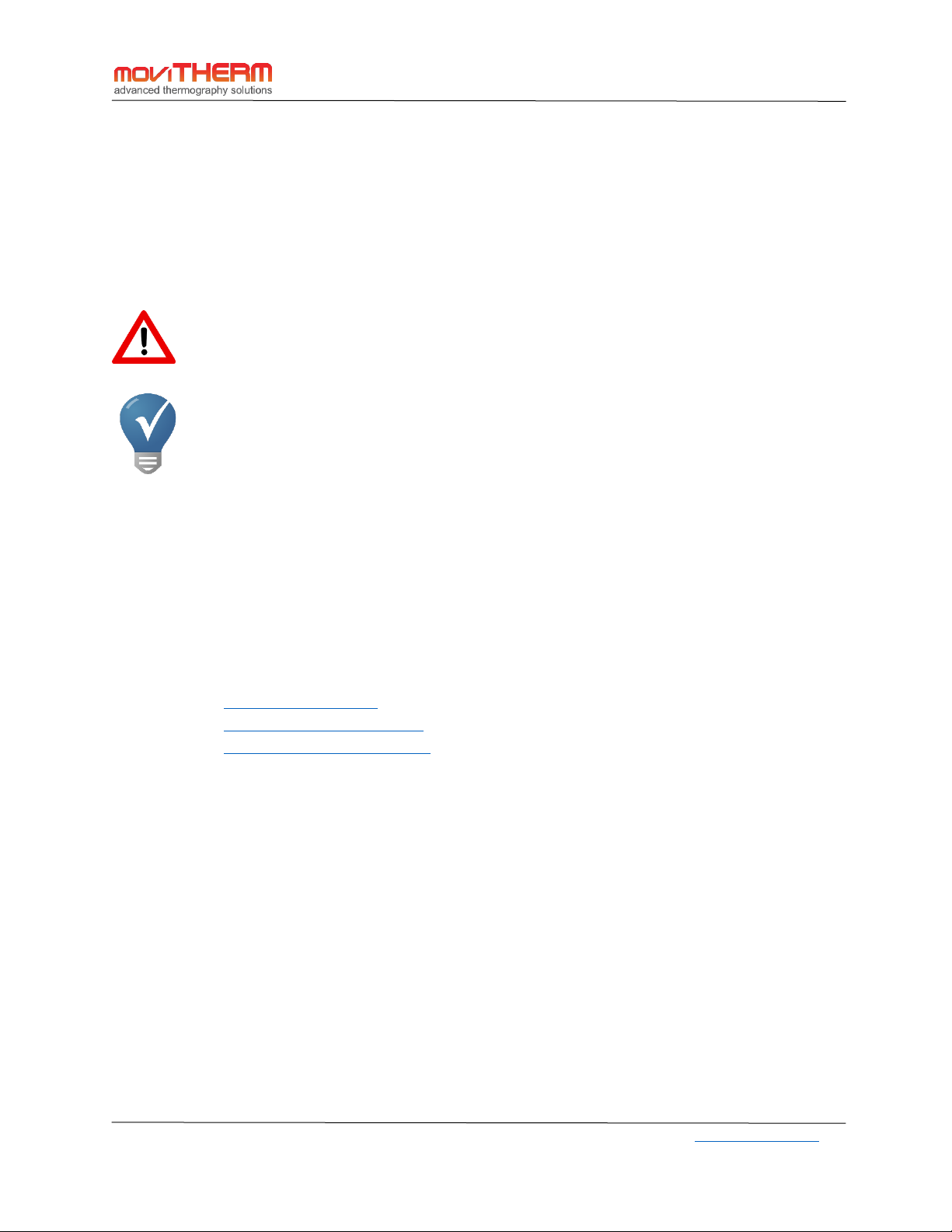
MoviTHERM MIO-A310-7 Manual
MoviTHERM – Advanced Thermography Solutions| 15540 Rockfield Blvd., Suite C110, Irvine, CA, USA| www.movitherm.com
1
1 Foreword
Congratulations on your purchase of the MoviTHERM MIO Series of Intelligent I/O Module. We
appreciate your business and want to make sure that your installation is successful. This manual
provides important information for installation, setup, configuration and care of your new product.
PLEASE MAKE SURE TO READ THE ENTIRE MANUAL CAREFULLY BEFORE OPERATING THIS DEVICE.
Whenever you see the symbol to the left, please pay special attention. This is a warning
symbol. Carefully consider all warnings in this document in order to prevent any mistakes.
The blue light bulb and checkmark symbol indicates a useful tip or information.
We invite any suggestions that you might have for improving our products or this user manual. Please
feel free to contact us at any time with your questions, suggestions or concerns:
MoviTHERM – Advanced Thermography Solutions
15540 Rockfield Blvd., Suite C110
Irvine, CA, USA
Phone: +1 949.699.6600
Fax: +1 949.699.6601
Email: info@movitherm.com
Website: http://www.movitherm.com
Twitter: www.twitter.com/movitherm
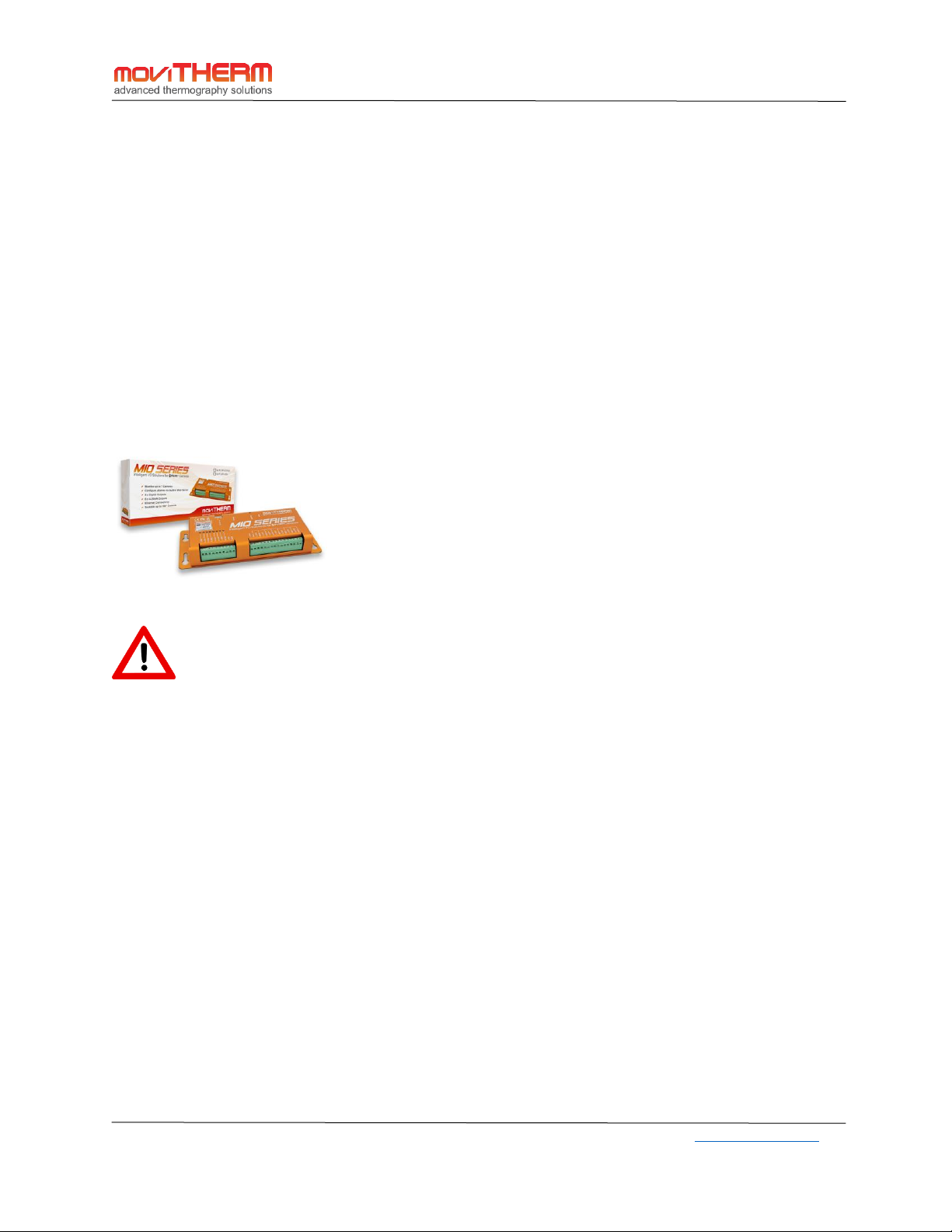
MoviTHERM MIO-A310-7 Manual
MoviTHERM – Advanced Thermography Solutions| 15540 Rockfield Blvd., Suite C110, Irvine, CA, USA| www.movitherm.com
2
2 Device Overview
This User’s Guide describes how to install, configure, and use the MoviTHERM MIO Intelligent I/O
device. For detailed device specifications, refer to the specifications section at the end of this document.
The MoviTHERM MIO Intelligent I/O device provides TCP/IP connectivity for up to 7 cameras over
100Base-T Ethernet connections. Each unit provides up to 8 channels of isolated, loop-powered analog
(4-20mA) outputs, and up to 8 solid state (24VDC) relay outputs.
3 Unpacking
The MoviTHERM MIO Intelligent I/O device or module ships in a custom printed cardboard box, as
shown in the photo below.
After removing the device from the packaging, inspect for damage that may have occurred
during shipping. Damaged devices should not be put into service. Contact your distributor
and/or MoviTHERM immediately if the device appears damaged in any way. If the damages
occurred during shipping, please file a claim with your shipping company.
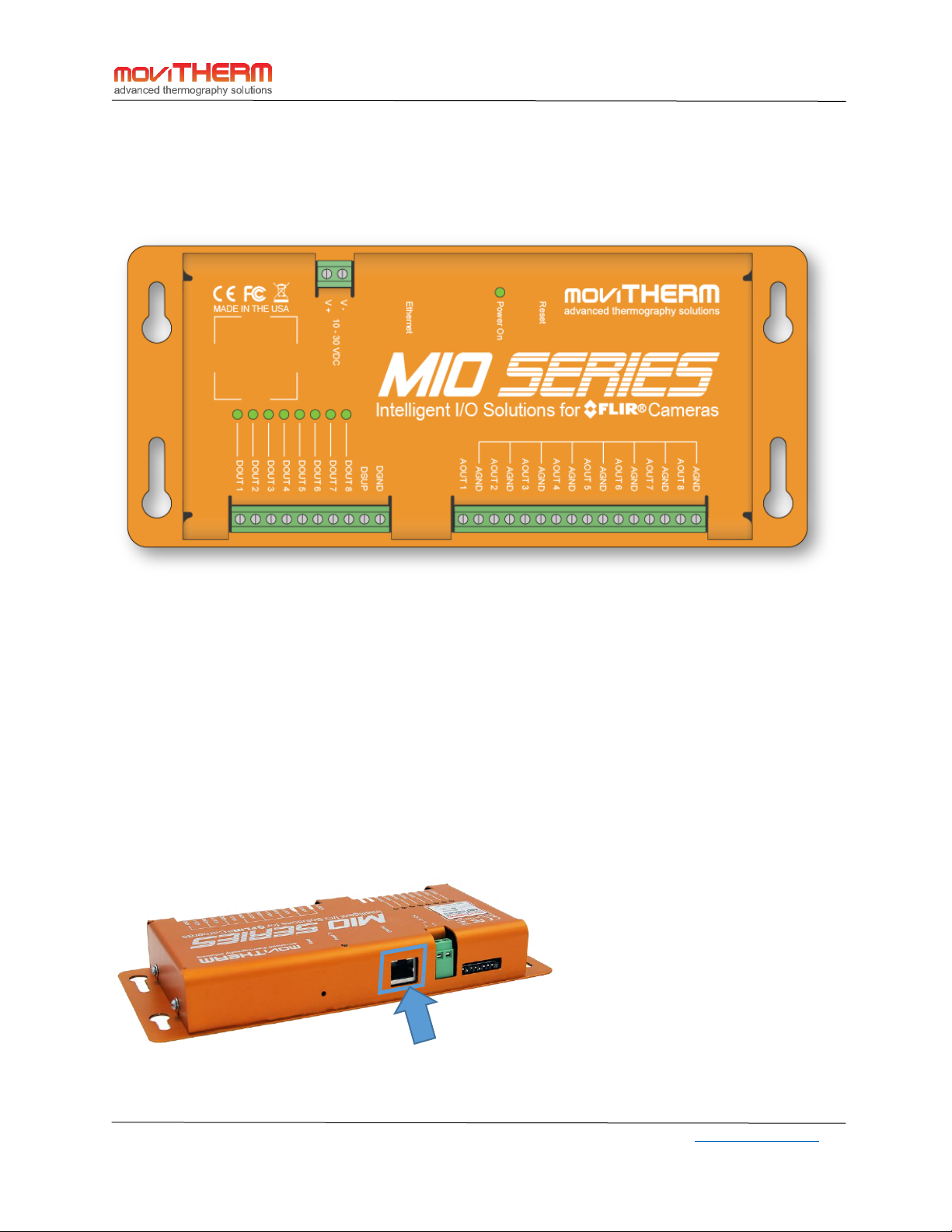
MoviTHERM MIO-A310-7 Manual
MoviTHERM – Advanced Thermography Solutions| 15540 Rockfield Blvd., Suite C110, Irvine, CA, USA| www.movitherm.com
3
4 Connecting the MIO I/O Module
Inspect the device to locate the various ports and connectors. (See Figure 1.)
Figure 1: MIO Device Connections
The device is powered using a 24VDC power supply. Under full load conditions, the unit draws about
0.3A (7W). This does not count the current needed to supply the digital outputs. The digital outputs can
source 0.5A each, but shall not exceed 1.5A total for all outputs. A power supply does not come included
with the MIO module. However, it is available as an accessory. The provided power source or supply
shall be regulated and stabilized to assure reliable performance.
The power terminals shown in Figure 1 must be connected to an industrial 24VDC power supply. The
unit will also work with a 12VDC supply. Its input voltage needs to be between 10VDC and 30VDC.
Please connect the positive lead to the screw terminal marked “V+” and the negative or ground lead to
the terminal marked “V- “. Please make sure not to reverse the polarity. The unit has a reverse polarity
protection built in. However, the unit will not turn on.
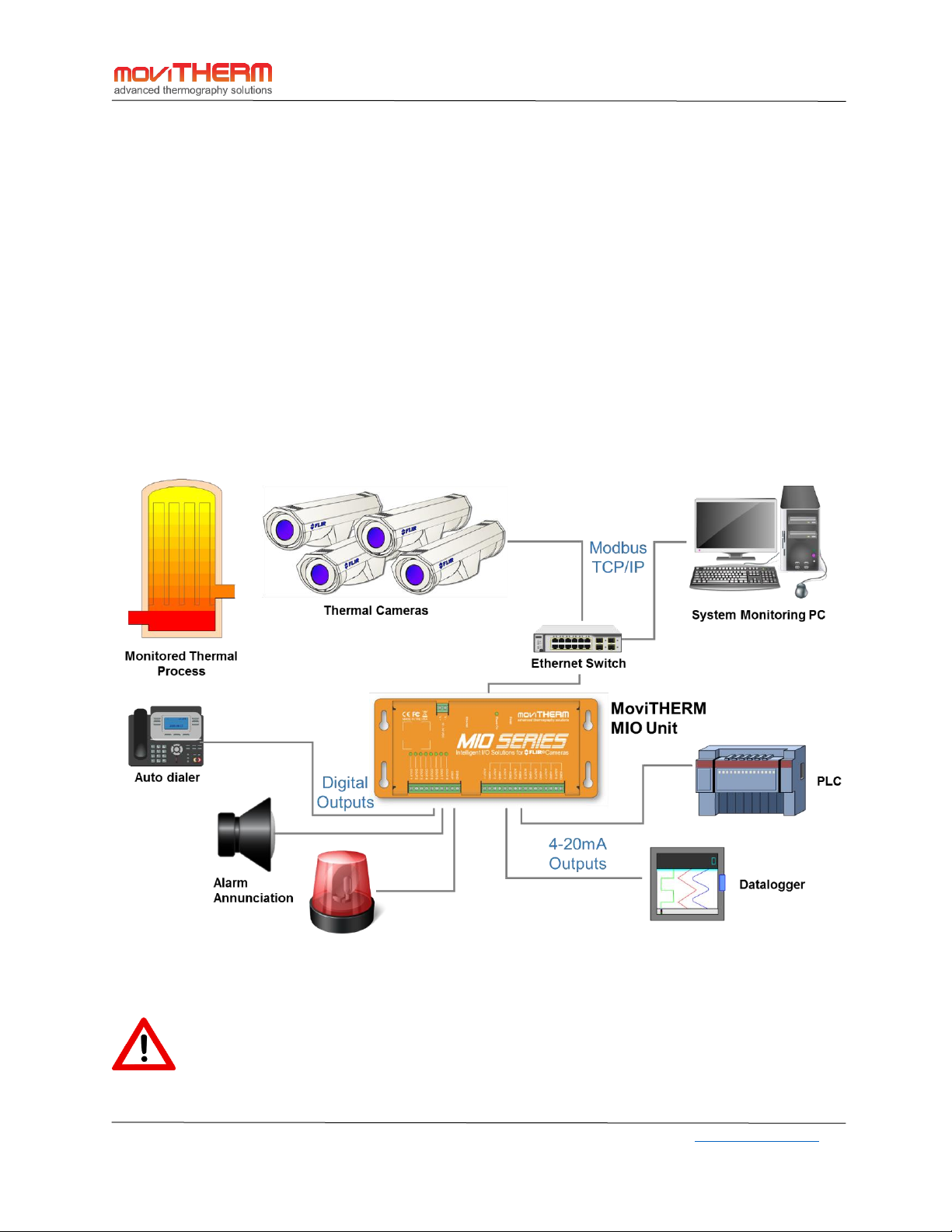
MoviTHERM MIO-A310-7 Manual
MoviTHERM – Advanced Thermography Solutions| 15540 Rockfield Blvd., Suite C110, Irvine, CA, USA| www.movitherm.com
4
Connect the Ethernet RJ-45 port to the camera network or an Ethernet switch. The camera network
typically includes 1 to 7 FLIR cameras connected to a single Ethernet Switch. You may also connect a PC
or laptop to the Ethernet switch for configuration of the cameras and the MIO module.
Connect the 4-20mA analog outputs to any device with 4-20mA signal inputs, such as industrial PLCs, 420mA data loggers, 4-20mA signal monitoring/alarm devices, etc. Keep in mind that from the
perspective of the MoviTHERM MIO I/O module, these are outputs. The 4 to 20mA outputs are active, or
loop powered. This indicates that they will provide a loop voltage to the connected device. No additional
power source is necessary or should be added. Make sure to observe the connected polarity of the 4 to
20mA device.
Connect the digital outputs to discrete signal inputs on alarms, warning lamps, auto-dialers, PLCs, etc.
For more details on how to connect devices, please go to Section 7.1 – I/O Connections.
Figure 2 illustrates a typical installation scenario.
Figure 2: A typical MoviTHERM MIO Monitoring Installation
Do not operate the device in a manner that is not specified in this document. Misuse of the
device may result in a malfunction or safety hazard. It will also void the warranty.
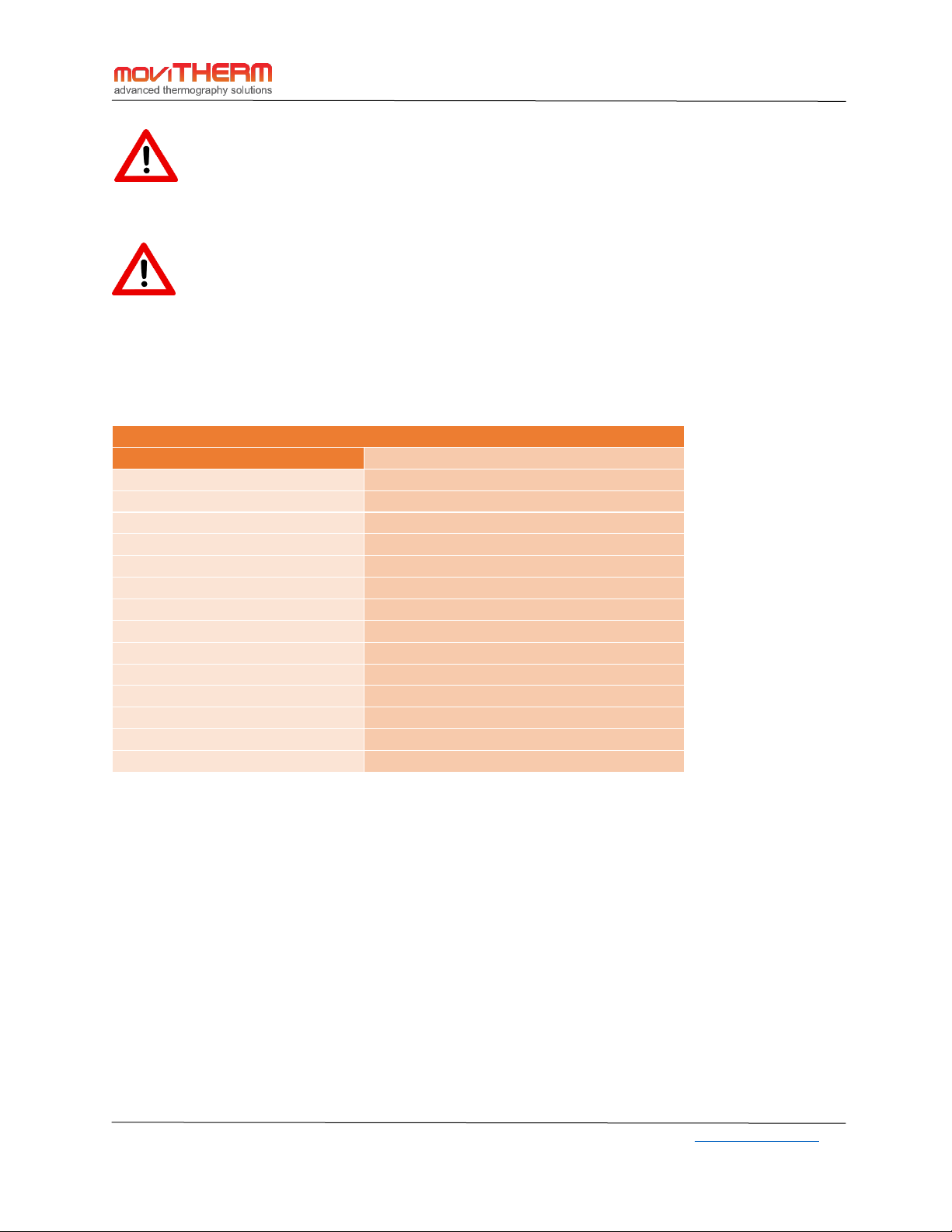
MoviTHERM MIO-A310-7 Manual
MoviTHERM – Advanced Thermography Solutions| 15540 Rockfield Blvd., Suite C110, Irvine, CA, USA| www.movitherm.com
5
Never operate this device in an explosive environment where flammable gases, dust, fumes
or other volatile materials may be present. If you must operate this device in a hazardous or
explosive environment, it must be installed in a suitably rated enclosure with the necessary
provisions.
To ensure proper performance consistent with the specifications of this device, please
carefully read this user manual and observe all cautions, operating conditions and limits.
5 Specifications
Maximum Cameras Supported
4-20mA Transmitter Channels
8 CH, Group Isolated, Self-Powered
0.5A per Channel, 1.5A all Channels
Maximum Power Consumption
8.8 x 3.9 x 1.2 in (223 x 99 x 31 mm)
0°C to 50°C (32°F to 122°F)
0% to 95% RH, non-condensing
6 System Installation and Set-up
The MoviTHERM MIO-A310-7 Intelligent I/O modules are packaged in an anodized aluminum enclosure.
This enclosure is intended to protect the internal electronics only from larger objects and general
handling. The MIO I/O module is intended to be mounted inside an existing electrical cabinet or other
protective enclosure.
The MIO I/O Module is rated NEMA1 / IP20
Enclosures constructed for indoor use to provide a degree of protection to personnel against incidental
contact with the enclosed equipment and to provide a degree of protection against falling dirt.
Protected against solid foreign objects of 12mm in diameter and greater. No protection against water.
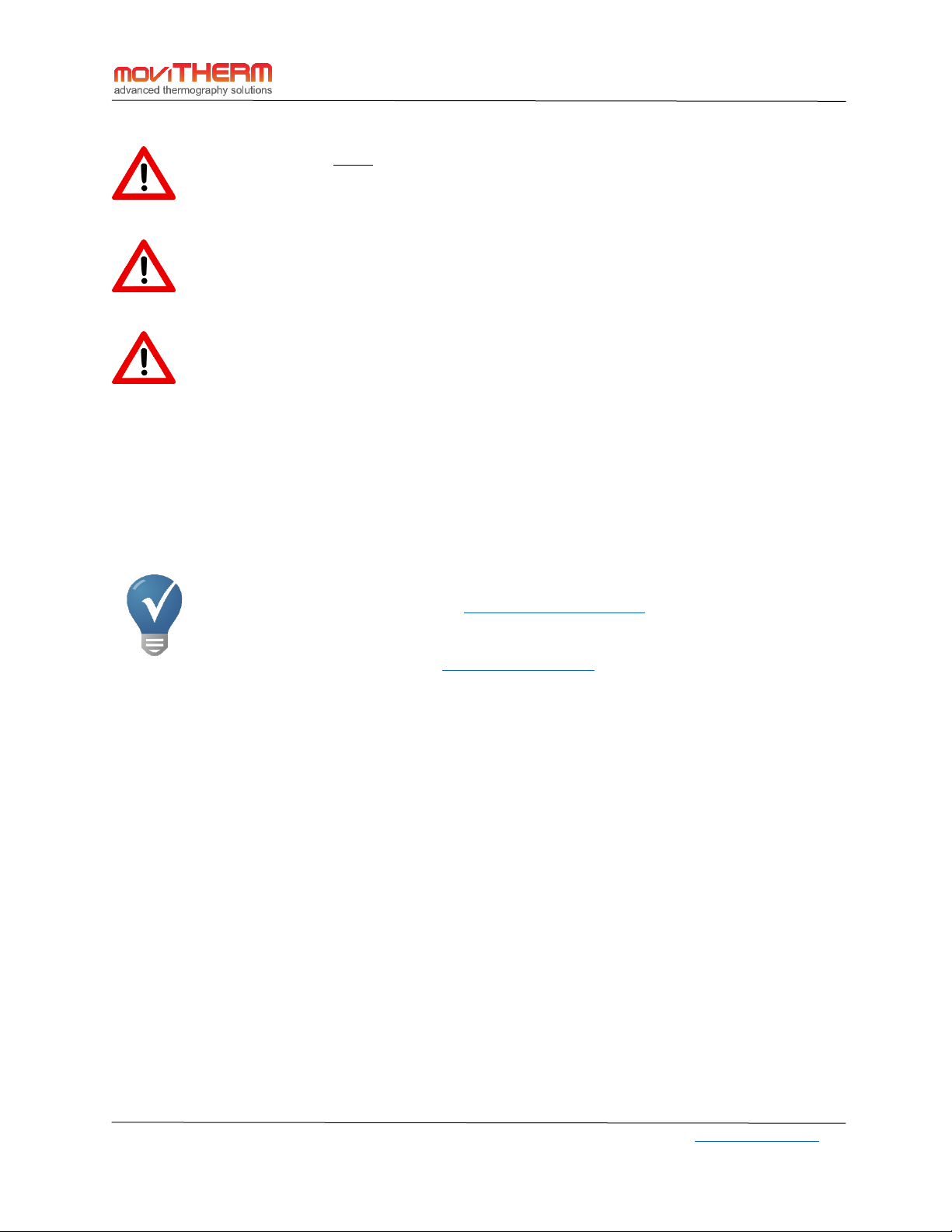
MoviTHERM MIO-A310-7 Manual
MoviTHERM – Advanced Thermography Solutions| 15540 Rockfield Blvd., Suite C110, Irvine, CA, USA| www.movitherm.com
6
The MIO I/O module is not protected against ingress of dust, conductive particles, moisture
or liquid splashing.
For installations in dirty, dusty, hot, wet or otherwise harsh or hazardous areas, provisions
have to be made to adequately protect the MIO I/O module.
Please do not stick any tools or metal objects inside the MIO module. This may create an
electrical shortcut and permanently damage the unit. This will also void the warranty.
For indoor industrial or outdoor environments, we recommend placing the MIO I/O module at least
inside an electrical enclosure rated NEMA4 or NEMA4x. No cooling is required, as long as the inside
temperature of the protective enclosure will not exceed the max allowable operating temperature of
the MIO module.
To ensure proper operation and continuing reliability, all set-up and configuration tasks should be
completed by qualified engineers or service technicians. The information in this manual provides some
direction, but should not be considered a substitute for extensive experience.
If you are unsure how to proceed, contact your distributor or MoviTHERM technical
support for further directions under support@movitherm.com. Please include the serial
number of your MoviTHERM MIO.
Or visit the MoviTHERM Website www.movitherm.com and use the contact methods
provided there.
6.1 Configuration Procedure
After the electrical connections have been made and verified, it is time to configure the cameras and the
MoviTHERM MIO device. The FLIR A310 cameras are configured using FLIR software and utilities (FLIR IP
Config, and FLIR IR Monitor). The MIO device is configured using the browser-based MoviTHERM MIO
Configuration Utility, as discussed later in the manual.
Configuring the system is a four-step process:
1) Set the cameras to a fixed IP addresses using the FLIR IP Config application.
2) Configure the Regions of Interest or “ROIs” in each camera using the FLIR IR Monitor Software
Package
3) Define the thresholds and action criteria for each ROI using the browser-based MoviTHERM
MIO Configuration Utility.
4) Configure the MIO board response using the MoviTHERM MIO Configuration Utility.
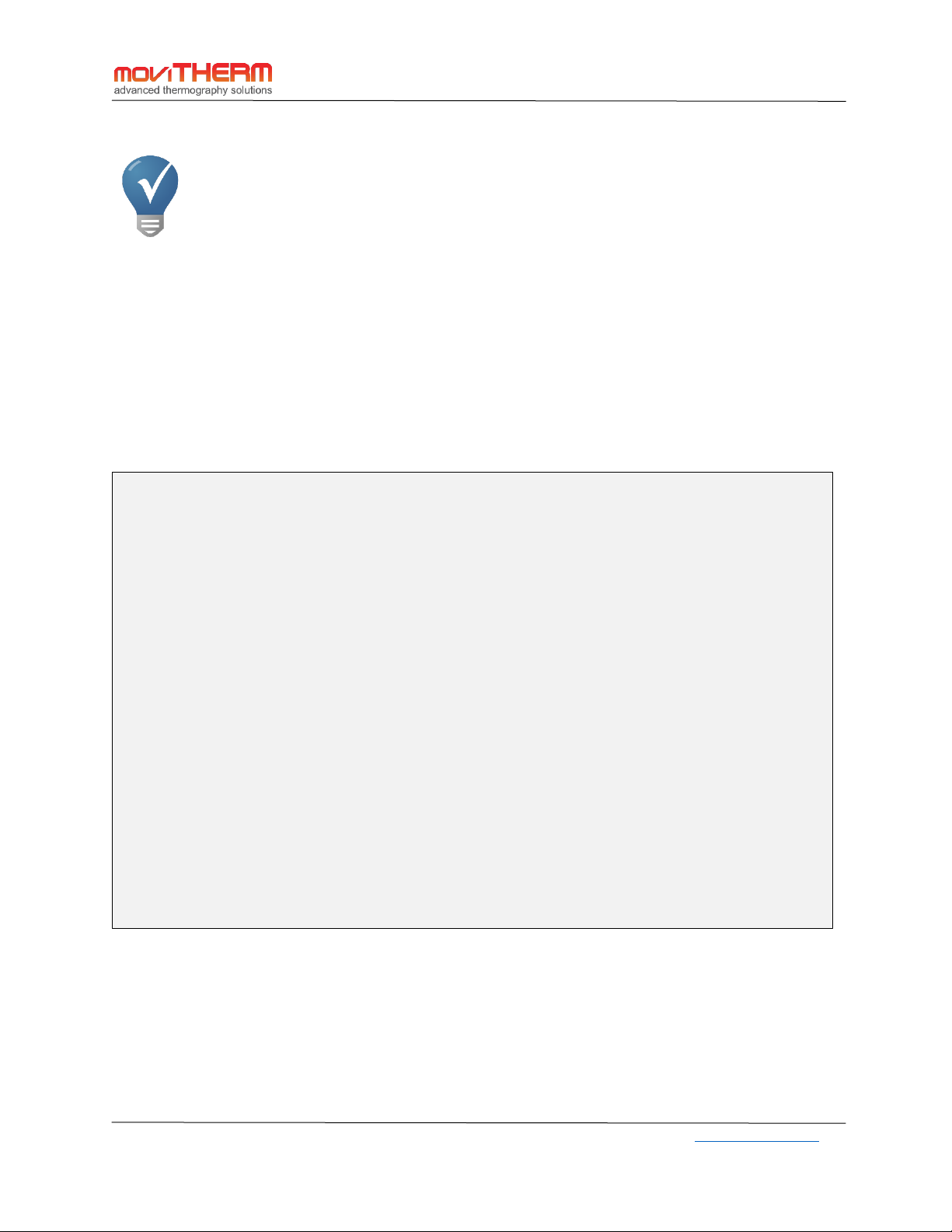
MoviTHERM MIO-A310-7 Manual
MoviTHERM – Advanced Thermography Solutions| 15540 Rockfield Blvd., Suite C110, Irvine, CA, USA| www.movitherm.com
7
Steps 3 & 4 cannot be completed until Steps 1 and 2 are complete. Step 1 requires the
FLIR IP Config software utility bundled with the camera. Step 2 requires the FLIR IR
Monitor software application also bundled with the camera. Steps 3 & 4 use a standard
web browser interface to access the MoviTHERM MIO Configuration Utility. Consult the
appropriate FLIR camera user manual for details on how to setup the camera.
6.1.1 IP Configuration
It is important to understand that although the MIO device and the cameras share a single Ethernet
connection, the cameras and the MIO device must all have separate and unique TCP/IP addresses. The
cameras must be configured to use static IP addresses. The FLIR IP Config utility software is used to set
the camera IP addresses. The MoviTHERM MIO Configuration Utility will be used to set up the IP
address on the MIO device (as discussed in the next chapter).
After the camera IP addresses have been assigned, you will be ready to define the Regions of Interest
that will be used by the MIO device. Refer to the FLIR IR Monitor User Manual for detailed information
about defining the camera regions of interest for FLIR-A310 camera models. You must complete the
Region of Interest configuration before moving on to configure the MoviTHERM MIO device.
IP SUBNET CONFIGURATION - IMPORTANT NOTE:
The cameras and the MIO device must all be assigned unique IP addresses. However, in order
to share the same Ethernet cable connection, all of the IP addresses must reside within the
same subnet. This is most easily accomplished by ensuring that the 1st, 2nd, and 3rd IP address
fields are common for all devices, while the 4th field is unique for each device.
For example, the default IP address for the MIO device is defined as follows:
MIO IP address: 192.168.1.2
Subnet mask: 255.255.255.0
If this default is left unchanged, suitable camera IP addresses might be:
Camera IP address 1: 192.168.1.3
Camera IP address 2: 192.168.1.4
Camera IP address 3: 192.168.1.89 (etc.)
If the MIO device IP is modified (as outlined later in this document), the camera IP address may
need to be updated accordingly.

MoviTHERM MIO-A310-7 Manual
MoviTHERM – Advanced Thermography Solutions| 15540 Rockfield Blvd., Suite C110, Irvine, CA, USA| www.movitherm.com
8
6.2 Preparing MIO for Configuration
You always need to have the regions of interest configured in the A310s before you configure the MIO.
The MIO must be able to locate the pre-configured regions of interest in each camera in order to
perform the selected actions. You can configure one or many ROIs in each camera. You are only limited
by the number of available outputs on the MIO I/O. If more outputs are needed, or you need to monitor
more than seven cameras in your application, simply add another MIO I/O module to your network.
Supported Web Browsers - The following web browsers are supported by the MIO. If
you are using an older version than the supported version and are experiencing issues,
update to the latest version or use another supported browser.
Microsoft Edge – 38.0
Google Chrome – 53.0
Firefox – 48.0
6.3 Assigning Actions to Camera Regions: The MIO Controller Utility
Once Regions have been defined in the cameras, you are ready to assign actions based on temperatures
detected. Start by launching a web browser (Google Chrome, Microsoft Edge, Firefox) from your
Windows Desktop or Start Menu. When the browser window opens, type the MIO Controller Board IP
address into the Address (URL) field at the top of the browser window, as shown in Figure 4.
Figure 4: MIO Access Log-in Dialog
If the correct IP address is entered, the Password Login dialog will appear in the browser window as
shown here.

MoviTHERM MIO-A310-7 Manual
MoviTHERM – Advanced Thermography Solutions| 15540 Rockfield Blvd., Suite C110, Irvine, CA, USA| www.movitherm.com
9
Enter the Administrator log-in password in the field provided, and click the Log In button to continue.
When the correct password has been entered, the Device Settings Tab will open in the browser window,
as shown in Figure 5 (on the next page).
6.3.1.1 The Device Settings Tab
The Device Settings tab (shown in Figure 5 on the next page) is the default start-up page. When you
access the MIO Board Configuration from your browser, this is the tab that will appear after entering the
correct log-in password. The text fields with a white background are editable fields. The text fields with a
grey background display current system parameters, but are not user-editable.
The Device Settings tab is used to:
1) set the Network Configuration (IP Address and Subnet),
2) enter an optional user-defined Device Name
3) execute a firmware update
NOTES:
For simplicity, the default log-in password is set to “password”. After system installation, you may want
to change the password to reduce the potential for unauthorized system access. (Additional information
about changing the password can be found in the section that discusses Recovery Mode.)
The MoviTHERM MIO Device IP Address has been pre-configured to 192.168.1.2. This is the factory
default IP setting. However, the board’s IP address is configurable, so if the IP address has been
changed, you may need to provide a different IP address than the one shown here. If you know the
correct IP address, enter it into the Address (URL) field. If you are uncertain, try the default IP address:
192.168.1.2 first. If you are unable to connect using this address, you may need to perform a Network
Reset. (For more information, refer to the IP Address Reset section later in this chapter for more
details.)

MoviTHERM MIO-A310-7 Manual
MoviTHERM – Advanced Thermography Solutions| 15540 Rockfield Blvd., Suite C110, Irvine, CA, USA| www.movitherm.com
10
Figure 5: The MIO Controller Utility opens to the Device Settings tab after the correct password has been entered.
6.3.1.2 Network Configuration
To change the Network Configuration, simply type the new Device IP address and Subnet mask in the
fields provided. Similarly, to change the Device name, simply type a user-specified name into the Device
name field provided. Click “Save Settings and Reboot” to save the changes.
Note: If you change the IP address and then click “Save Settings and Reboot”, the board will run through
a short reset cycle before opening a link to the new IP address. When the browser page updates, the
Device IP address and Subnet mask fields will reflect the changes. (See Figure 6.)

MoviTHERM MIO-A310-7 Manual
MoviTHERM – Advanced Thermography Solutions| 15540 Rockfield Blvd., Suite C110, Irvine, CA, USA| www.movitherm.com
11
Figure 6: IP Address changed - view after Save and Reboot
6.3.1.3 IP Address Reset
If you changed the IP Address, but have forgotten the new setting, an IP Address Reset operation will
temporarily reset the IP address to the factory default. In order to reset the IP address, you will need to
access the DIP switches on the MIO device. (The DIP switches can be accessed through the cut-out port
located to the right of the MIO Ethernet port as shown here.)

MoviTHERM MIO-A310-7 Manual
MoviTHERM – Advanced Thermography Solutions| 15540 Rockfield Blvd., Suite C110, Irvine, CA, USA| www.movitherm.com
12
When you have located the DIP switches, follow these steps to reset the IP address to the factory
default setting: 192.168.1.2 (Subnet Mask: 255.255.255.0)
While the unit is powered on:
Step 1: Turn on the IP Reset DIP switch
(see Figure 7)
Step 2: Reset the device by either:
a) Power module off, wait 10 seconds, power on
Or
b) Press the reset button, using a paper clip. The reset button is located behind a small hole on the
backside of the enclosure. See left blue arrow above.
Step 3: After the device reboots, log in to the device using the default IP address: 192.168.1.2
Step 4: Turn off the IP Reset DIP switch
(see Figure 8)
For setting the IP Address back to a user-defined value, return to the previous Network
Configuration section of this document. Keep in mind that every time you are changing
the IP address of the device, the connection in your browser (or to all other devices)
may be lost. Make sure to change the IP address in the browser to the newly configured
IP address to re-establish the connection.
Figure 7: Set the IP reset DIP Switch to ON
Figure 8: Clear the IP reset DIP Switch (OFF)

MoviTHERM MIO-A310-7 Manual
MoviTHERM – Advanced Thermography Solutions| 15540 Rockfield Blvd., Suite C110, Irvine, CA, USA| www.movitherm.com
13
6.3.1.4 Firmware Update
The Firmware Update option at the top of the Device Settings tab is an advanced feature that allows you
to quickly and easily upgrade the Firmware (embedded software) running on the board. The Firmware
Update process involves the following steps:
1) Download the Firmware file to
your PC
2) Click the “Choose File” button
under “Firmware Update” on the
“Device Settings” tab (Fig. 9)
3) Navigate to the Firmware file
(from Step 1) using the file
browser, and select it. The
filename will appear next to the
“Choose File” button.
4) Click the “Update” button under
“Firmware Update” on the
“Device Settings” tab (Fig. 9)
5) The firmware update will be
loaded into the MIO Device. The
device will reboot and reconnect.
When the Firmware update cycle is complete, you will be returned the Device Settings Tab.
Figure 9: Buttons for initiating the Firmware Update

MoviTHERM MIO-A310-7 Manual
MoviTHERM – Advanced Thermography Solutions| 15540 Rockfield Blvd., Suite C110, Irvine, CA, USA| www.movitherm.com
14
6.3.2 The Camera Settings Tab
The Camera Settings Tab is used to link the camera IP addresses to the MIO Controller board. This step
permits the cameras to communicate with the board, enabling its functionality. When you click on the
Camera Settings tab, the tab depicted in Figure 10 loads into the browser window.
Figure 10: The Camera Settings Tab - awaiting configuration
Enter a name or alias for each camera in the field provided, along with the
corresponding IP address for the camera, as illustrated in Figure 11, and press the “Save
Configuration” button. As the MIO Board connects to the cameras, the green
“Connected” text will replace the red “Not Connected” text to the right of the camera
specification, as shown in Figure 11.
The “Alias” allows the user to provide a more meaningful name or reference to any particular camera,
rather than having to memorize a cryptic IP address number. The alias name has no other use than that
and will not affect any functionality.

MoviTHERM MIO-A310-7 Manual
MoviTHERM – Advanced Thermography Solutions| 15540 Rockfield Blvd., Suite C110, Irvine, CA, USA| www.movitherm.com
15
Figure 11: Sample Camera Configuration
6.3.2.1 Saving and Loading Configurations
The MIO device maintains one complete configuration in non-volatile memory. You can use the “Save
Configuration” button to store the current configuration as displayed on the Camera Settings tab into
the device memory. On power reset, the most recently saved configuration is used by the device. You
can also use the “Get Current Settings” button to load the most recently saved configuration from the
device memory into the Camera Settings tab for inspection or further editing.
6.3.2.2 The Script Commands Tab
After the camera settings have been set up, the next task is to set up the script commands that create
the intended system responses. The Script Commands tab is used to configure the commands
configuration. (See Figure 12.)

MoviTHERM MIO-A310-7 Manual
MoviTHERM – Advanced Thermography Solutions| 15540 Rockfield Blvd., Suite C110, Irvine, CA, USA| www.movitherm.com
16
Figure 12: The Script Commands tab - prior to configuration.
The configuration procedure is straight-forward:
1) Select the Camera from the pull-down menu in the left-most column
2) Select a Command from the second pull-down menu (as shown in Figure 13)
3) Assign the selected Command to a Region of Interest (ROI) by selecting the Region Interest using
the pull-down menu. (The Regions of Interest must be predefined in the camera using FLIR IR
Monitor as discussed previously.)
4) In the case of an Analog Output command, assign the Analog Output Mode, “Linear” or
“Threshold” (information about these modes is provided below).
5) If “Threshold” mode is used, set the Temperature Threshold(s) needed to initiate the specified
action in the Low Temperature box. If “Linear” mode is used, enter the value which should
correspond to 4 mA in the Low Temperature box and the value which should correspond to 20
mA in the High Temperature box.

MoviTHERM MIO-A310-7 Manual
MoviTHERM – Advanced Thermography Solutions| 15540 Rockfield Blvd., Suite C110, Irvine, CA, USA| www.movitherm.com
17
Repeat these steps for each Analog and/or Digital channel as needed, then save the configuration by
clicking the “Save Configuration” button.
Figure 13: Command pull-down menu options
You can assign multiple outputs (digital and analog) to the same camera, if needed. For
example, if you have four regions of interest configured within one and the same
camera, you can also assign four separate digital outputs to these regions. Each with
their own alarm threshold. In addition, you can also assign analog 4 to 20mA to the
same regions as well for external monitoring or control. It is entirely up to you, how you
utilize the resources in the MIO I/O module. If you run out of outputs, you can add
another MIO I/O module to the network and expand your system that way.
6.3.2.3 Command Options
The Command Options can be summarized in the following categories:
1) System Status
2) Delta Temperature
3) Internal Camera Temperature
4) Spot Temperature
5) Box Temperature (Max, Min, or Average)
6) Alarm trigger

MoviTHERM MIO-A310-7 Manual
MoviTHERM – Advanced Thermography Solutions| 15540 Rockfield Blvd., Suite C110, Irvine, CA, USA| www.movitherm.com
18
System Status
System Status is a special configuration option that can be used to monitor camera connectivity. When
the System Status Command is assigned to an output channel, the selected channel can be used to
monitor Ethernet connectivity. If all of the cameras entered in the “Camera Settings” tab have active
Ethernet connections to the MIO (0.0.0.0 IP address are not considered), the output will be logical
"HIGH" (20mA output). If one or more camera connectivity issues are detected, the selected output
channel will reflect a logical "LOW" (4.0 mA) state.
Delta Temperature
The Delta Temperature command enables you to initiate an action based on the difference between two
parameters. For example, an action could be based on the difference between the minimum and
maximum temperature readings within a single region. Alternatively, two regions could be compared, or
the camera’s internal temperature register could even be compared with a region in the image. The
difference between any two eligible camera parameters can be used as the basis for the delta
comparison. (Refer to the FLIR Camera user manual for how to setup delta temperature functions in the
camera)
Internal Camera Temperature
The Internal Camera Temperature option selects the camera’s internal temperature as the data source.
This option can be used to monitor the temperature environment of the camera, and alert the user to
unusual operating conditions.
Spot Temperature
Select the Spot Temperature option to use a predefined spot temperature as the data source. (Refer to
the FLIR Camera manual for more details about configuring a Spot Temperature measurement.)
Box Temperature (Max, Min, or Average)
Select the Box Temperature option to use a predefined Box temperature (max, min or average) as the
data source. . (Refer to the FLIR Camera manual for more details about configuring a Box Temperature
measurement.)
Alarm Trigger
Each camera can be configured to generate Alarm Trigger events in response to a variety of inputs.
Measurement results from within the image, the instantaneous state of a digital input, or even a
camera’s internal temperature could potentially be configured to generate an alarm. Selecting the Alarm
Trigger option assigns the state of the alarm flag as the data source for MIO device operations. (Refer to
the FLIR Camera manual for more details about configuring alarms in the camera.)

MoviTHERM MIO-A310-7 Manual
MoviTHERM – Advanced Thermography Solutions| 15540 Rockfield Blvd., Suite C110, Irvine, CA, USA| www.movitherm.com
19
6.3.2.4 Region of Interest Selection
The Region of Interest field is located to the right of the Command field. The available Region of
Interest options will depend on the Command option selected. For example, if you select the System
Status, Internal Camera Temperature, Delta Temperature, or Alarm option in the Command pull-down,
the Region of Interest specification is not relevant. The Region of Interest field will be disabled and
unavailable for editing. However, if you select a Spot or Box source in the Command field, it becomes
necessary to specify which of the pre-defined Spots or Boxes applies. In this case, the Region of Interest
field will be enabled and populated with all the available regions (Spots and Boxes). After specifying the
appropriate region, you can move on to specify the Output Mode (in the case of Analog Output
channels), and the temperature threshold(s).
6.3.2.5 Analog Output Mode
The Analog Output Mode selection determines the behavior of the specific analog output channel. Two
options are available: Linear Output or Threshold Output. When Linear Output is selected, the specified
output channel will produce a scaled 4-20mA signal based on the selected Command and Region of
Interest. The scaling is based on the values entered in the Low and High Temperature fields (4mA for
values ≤ Low Temperature, 20mA for values ≥ High Temperature). When Threshold Output is selected,
the output channel will produce a discrete low (4mA) or high (20mA) signal, based on the temperature
threshold value(s) set in the Low Temperature field.
You can scale the 4 to 20mA output to either the selected temperature range of the
camera, or a custom scale. For example, if the selected temperature range of the
camera is 0°C to 350°C, then enter ‘0’ in the field “Low Temperature” and ‘350’ in the
field named “High Temperature. In this example, a 4mA output signal equals to 0°C and
20mA equals to 350°C. Setting the low temperature or high temperature outside the
selected camera temperature range is not recommended. However, you may select a
different range within the calibrated temperature range of the camera. This is useful, if
you know that your process temperature may never go below or above a certain value.
For example, your process temperature may be between 70°C and 150°C, while the
temperature range of the camera is 0°C to 350°C. Setting the scaling of the 4 to 20mA
output of the MIO module to your min. and max. range of your expected process
temperature allows you to stretch the range across the entire 4 to 20mA range.
However, this will not increase the accuracy of your system.
It is also possible to use the analog 4 to 20mA outputs as threshold or alarm outputs. In
other words, if you select the “Threshold” option, rather than the “Linear Output”
option. This function allows any analog output to behave like a digital output in a sense.
In this case a 4mA current indicates a logic low signal and a 20mA current signals a logic
high or alarm. This is useful, if you run out of digital outputs and want to extend the I/O
of the module. Some 4 to 20mA controllers also “understand” this sort of signaling as
alarm condition.

MoviTHERM MIO-A310-7 Manual
MoviTHERM – Advanced Thermography Solutions| 15540 Rockfield Blvd., Suite C110, Irvine, CA, USA| www.movitherm.com
20
An example of a completed configuration is shown in Figure 14.
Figure 14: Sample Configuration
To summarize, each output channel is configured via the Script Commands tab (as shown in Figure 14).
The usual procedure is to start by selecting a camera using the pull-down camera selector menu. After
selecting a camera, a Command should be specified. If the selected Command specifies a Spot or Box
temperature, you will also need to select a Region of Interest. For Analog Outputs, an Analog Output
Mode must be selected – either a Linear 4-20 mA analog signal that changes proportionally based on the
selected Region of Interest, or a discrete 4 or 20mA Threshold Output, based on a comparison of the
Region of Interest with the temperature threshold settings. (Note that the Digital Channels behave
similarly to the Analog Threshold Output mode.)
6.3.2.6 Saving and Loading Configurations
Just like the Camera Configuration (discussed previously), the MIO device maintains one complete set of
Script Commands in non-volatile memory. You can use the “Save Configuration” button to store the
current configuration as displayed on the Script Commands tab into the device memory. On power
reset, the most recently saved configuration is used by the device. You can also use the “Get Current
Settings” button to load the most recently saved configuration from the device memory into the Script
Commands tab for inspection or further editing.

MoviTHERM MIO-A310-7 Manual
MoviTHERM – Advanced Thermography Solutions| 15540 Rockfield Blvd., Suite C110, Irvine, CA, USA| www.movitherm.com
21
6.3.3 The Debug Tab
After the configuration has been defined, the Debug Tab (in Figure 15) provides a convenient,
interactive window into the real-time operation of the MIO Board. Using the Debug tab, you can observe
the current status of all output channels and DIP switches at a glance. You can use this tab to validate
output channel operations.
Figure 15: The Debug Tab shows the current output state of each MIO Board output channels and the DIP switch states
6.3.3.1 MIO Board DIP Switches
The DIP Switches control advanced board functions. The position of each switch is shown below in
Figure 16.
Figure 16: MIO Board DIP Switches
6.3.3.2 DIP Switch Functions
Switch 1 – Filter: Enabling the Filter switch activates a running average filter (10 samples) on the
temperature INPUTS. This function may provide better performance for monitoring applications
involving a constantly variable temperature source such as a flickering flame. The filter is globally
applied to all seven cameras and all configured regions of interest.

MoviTHERM MIO-A310-7 Manual
MoviTHERM – Advanced Thermography Solutions| 15540 Rockfield Blvd., Suite C110, Irvine, CA, USA| www.movitherm.com
22
Switch 2 – IP Reset: The IP Reset switch is used to reset the IP address to the factory default setting. (For
more information, refer to IP Address Reset under the Device Settings Tab discussions earlier in this
document.)
Switch 3 – 4mA Test: When enabled, all analog channels will output a “logical low” 4mA signal.
Switch 4 – 20mA Test: When enabled, all analog channels will output a “logical high” 20mA signal.
NOTE: When both Switch 3 (4mA Test) and Switch 4 (20mA Test) are enabled, a 12mA half-scale signal
will be output on all analog channels
Switches 5-8: [Reserved for Future Expansion]
All MIO Series I/O modules have a built-in loop calibrator and simulator. The 4 to 20mA
signal has 16-bit resolution and is very accurate. By using dip switch 3,4 and 3&4 together
you can simulate 4mA, 12mA or 20mA in your setup. The current that the board outputs is
being indicated on the debug page. Therefore, you do not need a separate instrument
such as a loop calibrator or multi-meter to verify your system. This feature lets you troubleshoot issue
and quickly very how your scaling is setup on the MIO I/O module as well as on the receiving device.
6.4 Recovery Mode
The Recovery Mode (depicted in Figure 17) is an advanced mode that can be used to reset the MIO
device to its original factory settings. Similar in appearance to the Device Settings Tab discussed
previously, the Recovery page includes two key differences:
1) a button to clear camera and script settings
2) a field to enter a new system password.
To enter into Recovery Mode, you must first set all the DIP switches to the ON position and reset the
board. The reset function is activated by pressing the Reset button (on the reverse side of the board), or
by power-cycling the unit.
Only use the recover mode as a last resort. You may lose all system settings. The recovery
mode is typically only necessary, if a firmware update has failed or you can’t access the unit
via the web-browser anymore.
Before attempting a system recovery, please make sure to try an IP Address reset first to
see, if you can access the MIO I/O module. Sometimes Windows Firewall settings, Virus
Scanners, web browser privacy or security settings may prevent you from accessing the unit
instead.

MoviTHERM MIO-A310-7 Manual
MoviTHERM – Advanced Thermography Solutions| 15540 Rockfield Blvd., Suite C110, Irvine, CA, USA| www.movitherm.com
23
Figure 17: Set all DIP switches ON and power-cycle to open the Recovery panel
6.4.1 Password Reset
To reset the access password, make sure the unit is already in “Recovery Bootloader Mode”
1. Type a new password into the current password field
2. Switch all DIP switches to the OFF position
3. Click the “Save Settings and Reboot” button
4. When the system restarts, use the new password to log into the Device Settings tab
5. Switch the DIP switches switched to OFF under 2.) back to the desired position

MoviTHERM MIO-A310-7 Manual
MoviTHERM – Advanced Thermography Solutions| 15540 Rockfield Blvd., Suite C110, Irvine, CA, USA| www.movitherm.com
24
7 Operations
The MIO-A310-7 provide eight (8) 4 to 20mA analog outputs and eight (8) digital outputs. In order to
benefit from this connectivity, the MIO signals must be connected to other devices such as PLCs, dataloggers, warning lamps, alarm equipment, etc. This chapter is devoted to connecting the MIO unit to
external devices.
7.1 I/O Connections
All I/O connections are made via the screw terminal I/O Connectors as denoted in Figure 18.
Figure 18: I/O Mapping and Connectivity
The I/O ports are organized into two groups: Digital Outputs and Analog Outputs. When looking at the
side of the MIO enclosure with the I/O port cutouts, the Digital Outputs appear to the left of the Analog
outputs.
MIO 8 Channel
1 2 3 4 5 6 7 8 9 10
Digital Outputs
Digital Output 1Digital Output
2
Digital Output 3Digital Output 4Digital Output 5Digital Output
6
Digital Output 7Digital Output 8Digital Supply
Digital GND
Digital supply voltage range: 9-34 VDC
Maximum current all channels: 1.5 A
Maximum current per channel: 500 mA
On-state resistance: 0.4Ω Max
Inductive load clamping
9-34 DC
Load
9 10 11 12 13 14 15 16
Analog Output 5Analog GND
Analog Output 6Analog GND
Analog Output
7
Analog GND
Analog Output 8Analog GND
Isolation Voltage
Digital GND to Supply GND: 3750V
Analog GND to Supply GND: 1000V
Analog GND pins internally connected
Current sourcing output: 4-20 mA
Loop voltage: 24V ±1%
Resolution: 16 bit
V-V+
Positive Vin
Negative Vin
EthernetPower
Supply voltage range: 10-30 VDC
Maximum Power: 1 Watt
10-30 DC
1 2 3 4 5 6 7 8
Analog Output 1Analog GND
Analog Output 2Analog GND
Analog Output 3Analog GND
Analog Output
4
Analog GND
Analog Outputs
A

MoviTHERM MIO-A310-7 Manual
MoviTHERM – Advanced Thermography Solutions| 15540 Rockfield Blvd., Suite C110, Irvine, CA, USA| www.movitherm.com
25
7.1.1 Digital Output Pin Definitions
From left to right, the DOUT pins are defined as:
Pin 1: DOUT 1
Pin 2: DOUT 2
Pin 3: DOUT 3
Pin 4: DOUT 4
Pin 5: DOUT 5
Pin 6: DOUT 6
Pin 7: DOUT 7
Pin 8: DOUT 8
Pin 9: DSUP (DOUT Supply)
Pin 10: DGND (DOUT Ground)
Refer to Figure 19 for DOUT channel circuit and connection diagram.
7.1.2 Analog Output Pin Definitions
From left to right, the AOUT pins are defined as:
Pin 1: AOUT 1
Pin 2: AGND
Pin 3: AOUT 2
Pin 4: AGND
Pin 5: AOUT 3
Pin 6: AGND
Pin 7: AOUT 4
Pin 8: AGND
Pin 9: AOUT 5
Pin 10: AGND
Pin 11: AOUT 6
Pin 12: AGND
Pin 13: AOUT 7
Pin 14: AGND
Pin 15: AOUT 8
Pin 16: AGND
Refer to Figure 19 for AOUT channel circuit and connection diagram.
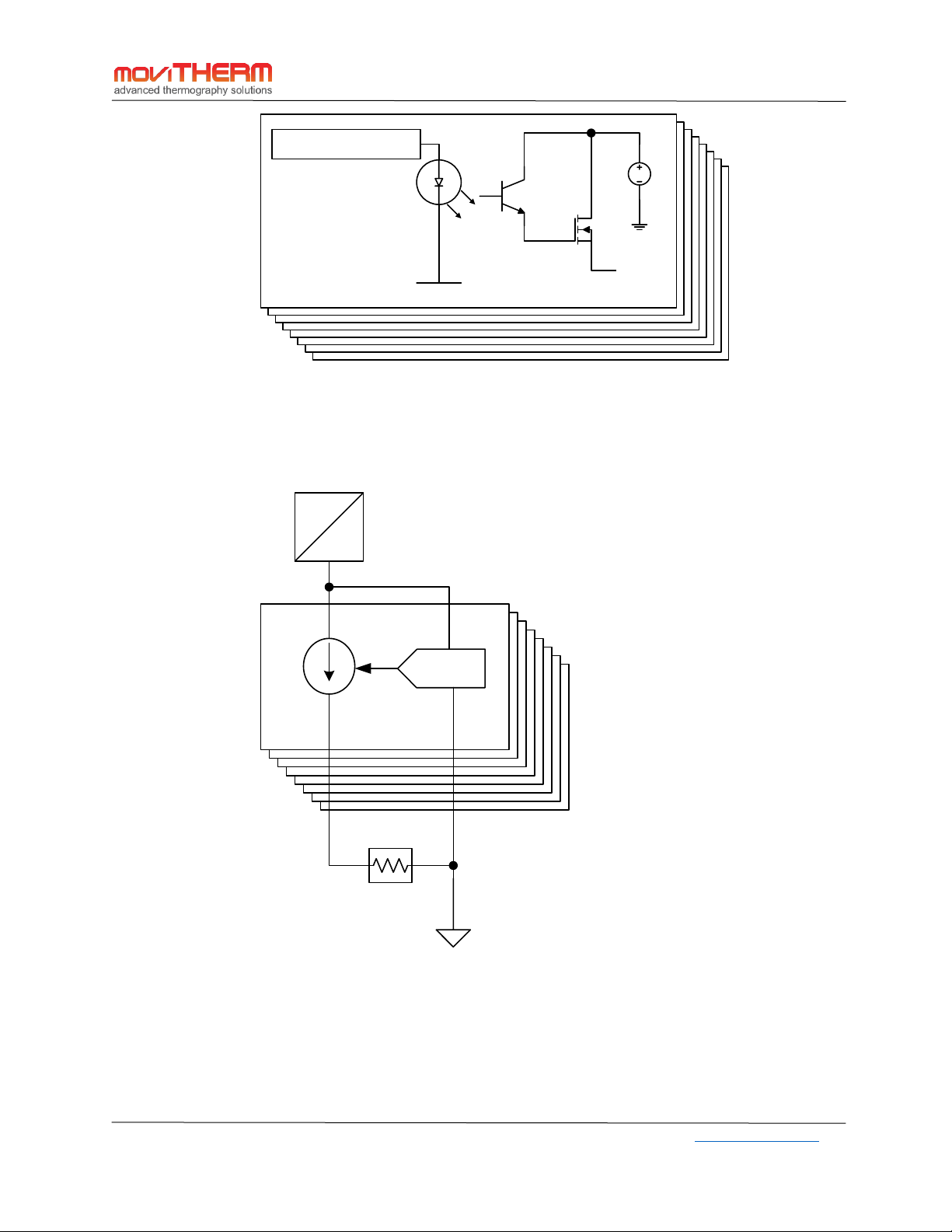
MoviTHERM MIO-A310-7 Manual
MoviTHERM – Advanced Thermography Solutions| 15540 Rockfield Blvd., Suite C110, Irvine, CA, USA| www.movitherm.com
26
Figure 19: DOUT and AOUT Channel Circuit Diagrams
The DOUT signals (DOUT 1 to DOUT 8) when active (turned on) will source the voltage connected to the
DSUP terminal with reference to DGND. Therefore, an external power supply needs to be connected to
the terminal DSUP (‘+’) and DGND (‘-‘). The supplied voltage can be between 9 and 34VDC. Most
common voltages used are either +12VDC or +24VDC.
Analog
Channels
Digital
Channels
Digital Output
VCCIO
OUT
0V
x8
DAC
Load
x8
DC
DC

MoviTHERM MIO-A310-7 Manual
MoviTHERM – Advanced Thermography Solutions| 15540 Rockfield Blvd., Suite C110, Irvine, CA, USA| www.movitherm.com
27
Each output can source up to 0.5A individually. However, the total sum of all current sourced
through any of the digital outputs cannot and shall not exceed 1.5A. If higher currents are
required, please add a relay or other suitable power switch to protect the output.
If all outputs are turned on, then the following needs to be observed:
1.5A/8 = 0.188A max. per digital output. In other words, if you would like to connect a
relay to each output, please make sure that each relay coil draws <= 0.188A.
Example: You are using a 12VDC/2A external power supply for the digital outputs. The
power supply is connected to DSUP (‘+’) and DGND (‘-‘). You have eight electromechanical relays with 12VDC coils. The coil resistance is 120Ω.
To calculate the required current per each relay, we can use the Ohm’s Law.
Coil Current = Coil Voltage/Coil Resistance
= 12V/120Ω
= 0.1A or 100mA
The above relay would be suitable, since it only draws 0.1A.
0.1A x 8 Channels = 0.8A total.
The digital outputs are protected against thermal overload, over current and transients from inductive
loads. It is good engineering practice to select relays with a coil current less than 0.15A or 150mA.
The positive (+) terminal of the external (load) device is connected to the DOUT channel on the MIO
device, as illustrated in Figure 18. The load’s negative (-) terminal must be connected to the Digital
Ground (Pin 10), which will share a connection to the negative (-) terminal of the 9-34VDC digital power
supply.
The AOUT signal pairs are “self-powered” 4-20mA output signals. Loop power is provided by an on-
board isolated 24VDC power supply. The recommended wiring configuration is depicted in Figures 18
and 19. The positive (+) terminal of the power source should be connected to the lower-numbered pin
of the pair (i.e. Pin 1 for AOUT 1 or Pin 3 for AOUT 2). The negative (-) load terminal should be connected
to the AGRND, which is connected to the negative (-) terminal of the power source.
AOUT(n) channels are group isolated outputs, which is to say that they are isolated from the main 24V
power and all other digital output signals, but not from each other. All AGNDs are connected to each
other internally.
NOTE: If using the digital output to signal a digital input device, a pull-down resistor must be used. A
common value is 10K. This may also be the case for driving SSR (Solid State Relays).

MoviTHERM MIO-A310-7 Manual
MoviTHERM – Advanced Thermography Solutions| 15540 Rockfield Blvd., Suite C110, Irvine, CA, USA| www.movitherm.com
28
8 Troubleshooting Common Issues
Unable to connect to
the Thermal Camera
over Ethernet
1) No Camera Power
2) No Ethernet Connection
3) Incorrect IP Settings
4) Camera Hardware Failure
1) Check Power Supply and Cables
2) Check Ethernet cables, switches, etc.
3) Set IP address with FLIR IP Config
4) Check Camera operations
Camera connection lost
during normal operation
after working
previously.
1) Camera Power cable broken
2) Ethernet cable broken
3) Camera Software Fault
4) Camera Hardware Failure
5) Camera thermal issue
(overheating)
1) Check Power Supply and Cables
2) Check Ethernet Cable
3) Power-cycle the Camera
4) Check Camera operations
5) Power down and allow to cool.
A) Camera connection
appears to be OK, but
no image appears.
B) Camera image is
blank and/or the
camera temperature
range is much higher
than expected.
1) Camera temperature range is
not properly set*.
2) Camera Software Fault
3) Camera Hardware Failure
*NOTE: This may happen if the
camera Ethernet connection is
unplugged while the camera is
running.
1) Set correct Camera Configuration in
FLIR IR Monitor or web browser
2) Power-cycle the Camera
3) Check Camera operations
Camera images appear
as expected, but no
output signal is
generated.
1) IR Monitor Recipe
Configuration Error
2) Output line connection fault
3) I/O Module Error or hardware
failure
1) Verify Output Channel parameters
are set correctly on the MIO Utility’s
Script Commands tab
2) Check Output signal wiring
3) Verify Output signal using a volt
meter or 4-20mA loop tested
Analog output current is
unaffected by camera
input.
1) Analog channel is reading from
incorrect camera (in multicamera configurations)
2) Camera connection issue (See
above)
3) MIO Device test current dip
switches are enabled
1) Verify proper camera selection on
the MIO Utility’s Script Commands
tab
2) Verify camera connection on the MIO
Utility’s Camera Settings tab
3) Move dip switches 3 and 4 on the
MIO device to the OFF position

MoviTHERM MIO-A310-7 Manual
MoviTHERM – Advanced Thermography Solutions| 15540 Rockfield Blvd., Suite C110, Irvine, CA, USA| www.movitherm.com
29
Unable to log in to the
MIO Device
Configuration Utility
1) No Ethernet Connection to MIO
Device
2) Incorrect IP Address
3) Incorrect Password
1) Check Ethernet cables, switches, etc.
2) Reset IP address to Default (Recovery
Mode)
3) Reset Access Password
(Recovery Mode)
Unable to access
Camera Configuration
items in the Script
Commands tab
1) No Ethernet Connection to the
camera
2) IR Monitor Camera
Configuration not complete
3) IR Monitor Camera
Configuration error
1) Check Ethernet cables, switches, etc.
2) Verify Regions are set correctly in the
FLIR IR Monitor application
3) Verify Regions are set correctly in the
FLIR IR Monitor application
Device is unresponsive
after firmware update
Updated firmware is invalid
MIO Device was interrupted during
update
Firmware binary file is corrupted
Reboot the device in Recovery mode, and
try updating the firmware again
If the device is still unresponsive, try
updating to a previous working version of
the firmware
Contact MoviTHERM support.
Digital Output voltage
when off is too high
The attached load’s resistance is
too high
Install a pull down resistor in parallel with
the load

MoviTHERM MIO-A310-7 Manual
MoviTHERM – Advanced Thermography Solutions| 15540 Rockfield Blvd., Suite C110, Irvine, CA, USA| www.movitherm.com
30
9 Appendix A: Default Settings
Default Device Name: “MIO-A310-7”
Default Password: password
Default Device IP Address: 192.168.1.2
Default Subnet Mask: 255.255.255.0
10 Appendix B: Technical Specifications
10.1 Absolute Maximum Ratings
Vin – Input Power Voltage Range
Vd_in – Digital Voltage In
Digital inductive load switch-off
energy dissipation
10.2 Operating Specifications
Output Current Error
vs Temperature (-30°C to 85°C)
Analog Current Output Resolution
Digital Output On-State Resistance