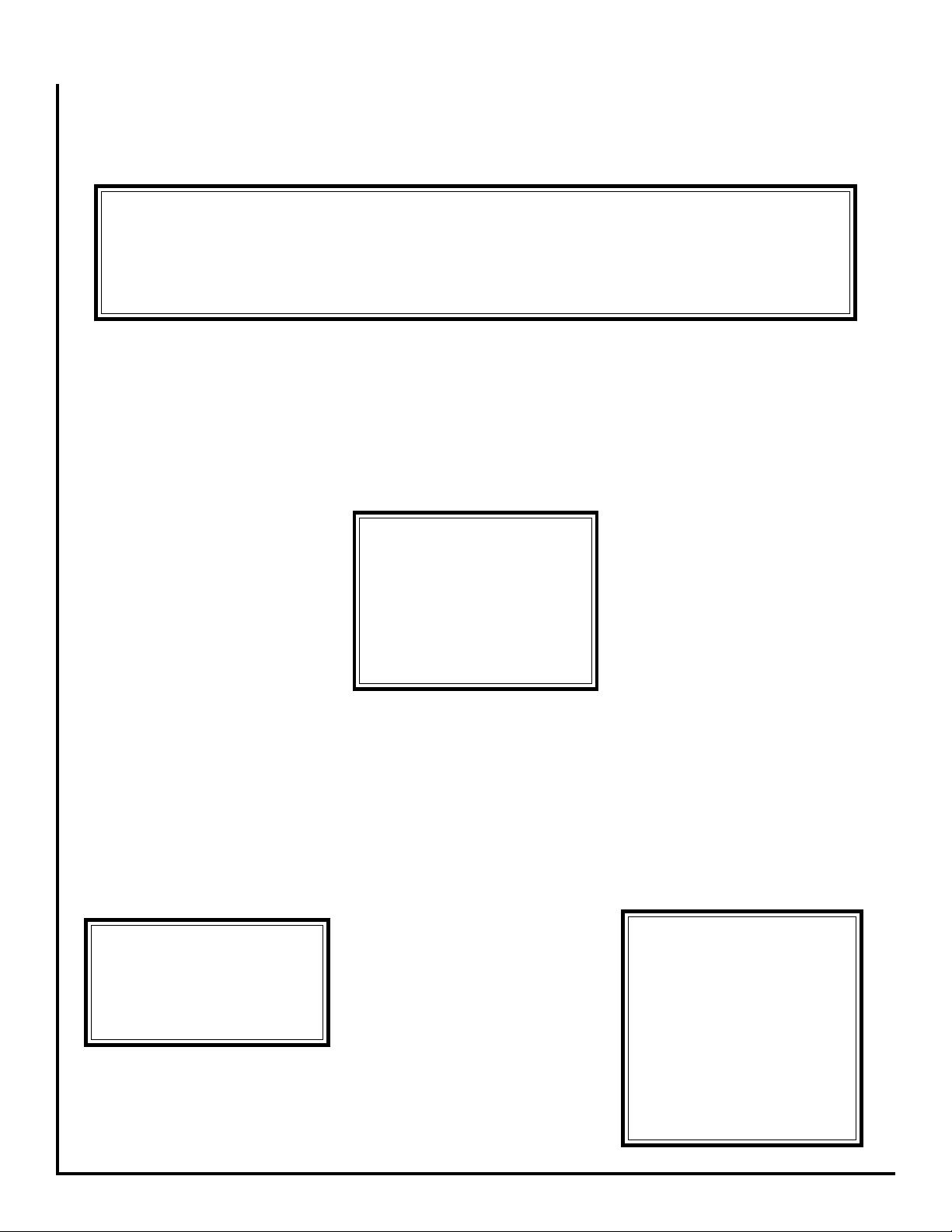
CLQ FAN COIL UNIT
****** W ARNING ******
Unit must not be operated
during building construction
due to excessive airborne dust
and debris. The unit must not
be operated under any
circumstances without an air
filter in place.
****** W ARNING ******
Any devices such as fan
switches or thermostats that
have been furnished by the
factory for field installation
must be wired in strict accordance with the wiring diagram
that is supplied with the unit.
Failure to do so could result
in damage to components
and will void all warranties.
****** W ARNING ******
Extreme caution must be
taken that no internal damage
will result if screws or holes are
drilled into the cabinet.
INSTALLATION, OPERATION & MAINTENANCE INSTRUCTIONS
**WARNING TO INSTALLER, SERVICE PERSONNEL AND OWNER**
Altering the product or replacing parts with non authorized factory parts voids all warranty or implied warranty
and may result in adverse operational performance and/or a possible hazardous safety condition to service
personnel and occupants. Company employees and/or contractors are not authorized to waive this warning.
Current Maintenance Program is available at www.firstco.com under "Product Information".
GENERAL
The manufacturer assumes no responsibility for equipment installed in
violation of any code requirement.
These instructions give information
relative to the installation of these fan
coil units only. For other related
equipment refer to the proper instructions.
Material in this shipment has been
inspected at the factory and released
to the transportation agency in good
condition. When received, a visual
inspection of all cartons should be
made immediately. Any evidence of
rough handling or apparent damage
should be noted on the delivery receipt and the material inspected in
the presence of the carrier’s representative. If damage is found, a claim
should be filed against the carrier
immediately.
Note: State of MA.-248 CMR code of the
state of MA. requires a pump timer (60
seconds on every 6 hours). See diagram.
FAN COIL UNIT
The installer must adhere strictly
to all local and national code requirements pertaining to the installation of
this equipment.
ance to combustible materials. This
includes the unit cabinet, discharge
plenum and connecting ducts. Sufficient clearance must be provided at
the front of the unit to allow access to
the air filter, electrical controls and
removal of the motor / blower assembly for servicing. This clearance distance should be approximately the
same depth as the fan coil unit.
NOTE: It is important at this point to
consider noise and vibration. If this
installation in a noise sensitive area
then placement of resilient isolators or
other means of sound deadening may
be necessary.
These fan coils are designed for
quiet operation, however, all air conditioning equipment will transfer some
amount of noise to the conditioned
space. This should be taken into consideration when planning the location
of the equipment as well.
ducting of the same size as the fan
coil connections. However, unique
arrangements or long duct runs must
be confirmed by a local professional.
The manufacturer will not be responsible for misapplied equipment. See
fig. 3.
ELECTRICAL
All wiring must comply with local
and national code requirements.
Units are provided with wiring diagrams and nameplate data to provide
information required for necessary
field wiring.
Knockouts are provided on both
sides of cabinet for connection to the
power supply.
These units may be provided with a
Class 2 transformer for 24-volt control
circuits. Should any add-on equipment also have a Class 2 transformer
furnished, care must be taken to prevent interconnecting outputs of the
two transformers by using a thermostat with isolating contacts.
INSTALLATION
PRECAUTIONS
Installation of this fan coil should
only be performed by a licensed contractor to ensure proper installation
and the safety of the installer. The
following are some precautions to be
These units are designed to be
installed in a vertical, upflow position
either hung on a wall or set on a
platform within an equipment closet.
All fan coil units are U.L. listed for
installation with zero inches clear-
AIR DISTRIBUTION
DUCTS
All duct work must be installed in
accordance with National Fire Protection Association Codes 90A and 90B.
Ducts should be adequately insulated
to prevent condensation during the
cooling cycle and to minimize heat
loss during the heating cycle. All
return air must be filtered to prevent
dirt buildup on the coil surface. In
many cases it is acceptable to use
L2398 10/09

followed for typical installations.
****** WARNING ******
When connecting piping to
fan coil units, do not bend or
reposition the coil header tubing for alignment purposes.
This could cause a tubing fracture resulting in a water leak
when water pressure is applied to the system.
****** W ARNING ******
R-410a can become combustible if mixed with air at elevated temperatures and/or
pressures. Property damage,
personal injury or death could
result if this warning is ignored.
• Always use proper tools and equipment.
• No wiring or other work should be
attempted without first ensuring that
the fan coil is completely disconnected from the power source and
locked out. Always verify that a good
ground connection exists prior to energizing any power sources.
• Always review the nameplate on
each unit for proper voltage and control configurations. This information
is determined from the components
and wiring of the unit and may vary
from unit to unit.
• When soldering or brazing to the
unit, it is recommended to have a fire
extinguisher readily available. When
soldering close to the cabinet wall or
near heat labile components, heat
shields or wet rags are required to
prevent damage.
• When the fan coil unit is in operation components are rotating at high
speeds.
• Units must be installed level to
ensure proper drainage and operation.
• Check unit prior to operation to
ensure that the condensate water will
drain toward the drain connection. An
overflow drain or an auxiliary drain
pan under the fan coil may be required
as a back up to a clogged primary
drain.
• Be sure that the drain pan is free
from foreign material prior to start up.
• Check filter media installation to
ensure that it is installed correctly.
Use the directional arrows or other
information on the filter to determine
the proper flow direction.
• Ensure that the air distribution system does not exceed the external
static rating of the unit.
COOLING COIL PIPING
The CLQ fan coil unit is supplied
with a direct expansion refrigerant
coil. The suction and liquid refrigerant
lines must be sized in accordance
with the outdoor unit manufacturer’s
recommendations.
Condensate drain lines must be
installed with adequate slope away
from the unit to assure positive drainage. Since the drain pan is located on
the suction side of the blower, a
negative pressure exists at the drain
pan and a minimum trap of 1-1/2
inches must be provided in the drain
line to assure proper drainage.
NOTE: If a Condensate Overflow
Shut-off Switch, that is designed to
be installed in the drain line, is used
in place of a secondary drain line, then
the cut-off switch should be located
in the primary drain line between the
fan coil unit and the P-trap.
HOT WATER COIL
PIPING PRECAUTIONS
• Flush all field piping prior to connection to remove all debris.
• Use wet cotton rags to cool valve
bodies when soldering.
• Open all valves (midway for hand
valves, manually open on motorized
valves) prior to soldering.
• When soldering to bronze or brass,
heat the piping while in the socket/
cup and begin introducing the solder
when the flux boils rapidly.
Avoid direct flame into the solder joint.
• Heat can only be applied to the cup
of the valve body for a minimal time
before damage occurs (even with the
use of wet rags.
• Avoid rapid quenching of solder
joints as this will produce joints of
inferior quality.
• Connect all piping per accepted
industry standards and observe all
regulations governing installation of
piping systems. When all connections are complete the system must
be pressure tested. Repair any solder joint leaks and gently tighten any
leaking valve packing nuts and piping
accessories as required. Hydronic
systems are not designed to hold
pressurized air and should only be
tested with water.
****** WARNING ******
An expansion tank may be
required if a back-flow
preventer is installed in the
system.
HOT WATER COIL PIPING
Figure 1 illustrates a typical piping
schematic for an Aqua Therm System.
The hot water coil connections are
1/2 inch nominal (5/8” OD) copper.
The hot water supply to the fan coil is
on the left when facing the fan coil
from the front.
All piping between the water heater
and fan coil unit should be copper and
should not exceed 200 feet of total
piping using 3/4” nominal pipe. It is
recommended that 3/4” nominal (7/8”
OD) piping be used on CLQ units to
prevent excessive head pressure
losses, so a 7/8” to 5/8” bell reducer
will then be needed. (Consult the
factory for other piping applications.)
It is also recommended that all
piping be adequately insulated to pre-
vent freezing when piping is run in an
unconditioned space.
Solder Connections - All copper
joints in the water lines must be made
with low temperature - non lead
solder.
"T" Connections (at the water
heater) Water lines to and from the fan coil
unit must be taken from the horizontal
connection of the "T" fittings in the
vertical hot and cold water supply
lines at the water heater. This ensures that any air in the system will be
purged each time water is used in the
dwelling. (See figure 1)
Isolation Valves - Two valves are
recommended to be installed within
the circulating loop to permit servicing
of the system if required and to assist
in purging the system.