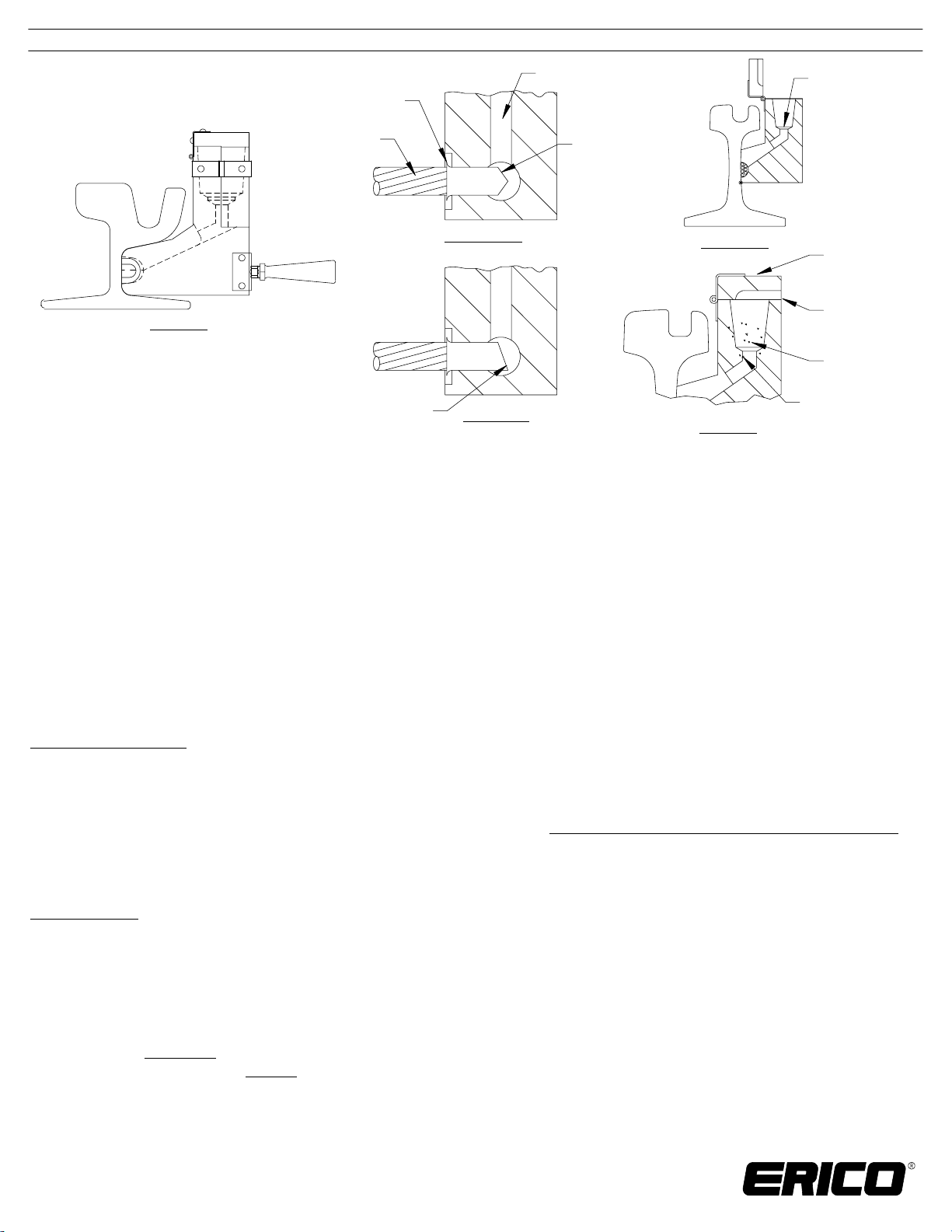
INSTRUCTION SHEET
Rail Girder
Flare of
Terminal Against
Tap Hole
Steel Disk
Side of Mold
Connection
Bond
Figure 2a
(Left
Hand Shown)
Figure 1
Single Cut
Bond
Prior to making a connection, read and follow the full instruction sheet IPRPW, the full instruction sheet shipped with ERICO CADWELD
(IPX) and special instruction below.
Insert web bond into mold and push until flare of sleeve is against mold. This positions bond in weld cavity and terminal under center
1.
of tap hole correctly (See Fig. 2a and 2b).
Fig. 2b - For single cut bond, angle of bond faces. upward. Left hand bond requires left hand mold; right hand bond requires right
hand mold.
Insert one steel disk, dished (concave) side up, in crucible to cover tap hole. See Fig. 3.
2.
Dump contents of one welding material container into crucible being careful not to upset disk. See Fig. 4.
3.
Tap welding material container to loosen starting material. Place a portion of the starting material on the top edge of mold at cover
4.
opening. Distribute the remaining starting material evenly over welding material and close cover. See Fig. 4.
Standing on field side of rail, ignite starting material on mold edge with flint igniter. Withdraw igniter quickly to prevent fouling.
5.
After approximately 10-15 seconds, open cover, release crucible hinge and break up the slag using mold cleaner tool, B136D.
6.
Unlock clamp and remove welder.
Dump the slag from the crucible and remove the slag from the tap hole using the end of the mold cleaner. Dump slag in the ballast,
7.
not on the ties.Check the mold for breakage or residual slag before proceeding with next bond.
Note:
Fig. 2a - For double cut bonds, bond is interchangeable for left or right hand molds.
Figure 2b
Double Cut
Bond
Figure 3
Crucible
Cover
Starting
Material
Welding
Material
Steel Disk
Figure 4
®®
Connection Preparation:
Dry the molds before the first connection of the day. Check bond terminals and disks for rust or corrosion. Clean and/or replace
•
accordingly.Check mold conditions (cracks, wear, chipped corners, etc.) Replace accordingly.
Welders should be clamped firmly to the rail but not so tight the clamps are difficult to close thus avoiding breaking or damaging the
•
molds.
Make sure the proper ERICO CADWELD welding material is being used.
•
prefix part number; i.e., SB25)
Place the disk in the mold, dished side up. Dump (don't pour) the welding material into mold. Always use mold cover and wear
•
. (Yellow Cap)
Use only F80 material for connection to rail (SB or PB
safety equipment as specified. Stand upwind and on field side of rail when igniting the ERICO CADWELD welding material.
Rail Preparation:
Remove grease and oil from the rail before grinding. Remove moisture from the rail.
•
Only use grinding/cleaning wheels approved by ERICO for ERICO CADWELD applications. Avoid using wheels designed for cutting
•
as they can damage the rail.
WARNING:
1. ERICO products shall be installed and used only as indicated in ERICO product instruction sheets and training materials. Instruction sheets are available at
www.erico.com
2. ERICO products must never be used for a purpose other than the purpose for which they were designed or in a manner that exceeds specified load ratings.
3. All instructions must be
4. Improper installation, misuse, misapplication or other failure to completely follow ERICO's instructions and warnings may cause product malfunction, property
damage, serious bodily injury and death.
SAFETY INSTRUCTIONS:
All governing codes and regulations and those required by the job site must be observed.
Always use appropriate safety equipment such as eye protection, hard hat, and gloves as appropriate to the application.
CADDY, CADWELD, CRITEC, ERICO, ERIFLEX, ERITECH, and LENTON are registered trademarks of ERICO International Corporation.
TECHNICAL SUPPORT:
www.erico.com
and from your ERICO customer service representative.
completely
followed to ensure proper and safe installation and performance.
IP7947_B
1 OF 1
© 2005, 2014
ERICO International Corporation