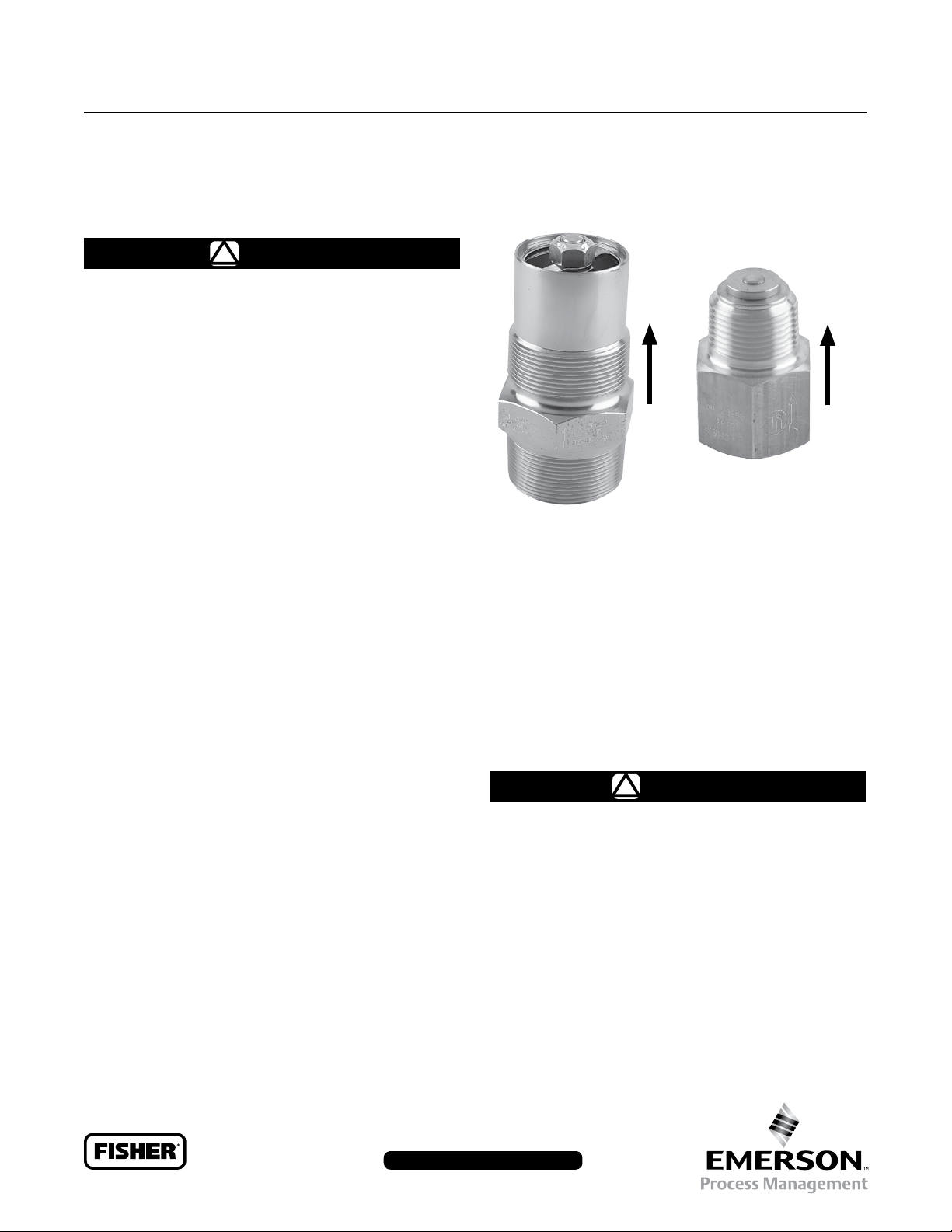
Instruction Manual
MCK-1095
September 2015
G100 Series Back Check Valves
WARNING
!
Failure to follow these instructions or to
properly install and maintain this equipment
could result in an explosion and/or re causing
property damage and personal injury or death.
Fisher® equipment must be installed, operated,
and maintained in accordance with federal,
state, and local codes and manufacturer’s
instructions. The installation in most states
must also comply with NFPA No. 58 or ANSI
K61.1 standards.
G100 Series
P1038
Only personnel trained in the proper
procedures, codes, standards, and regulations
of the LPG industry should install and service
this equipment.
Introduction
Scope of the Manual
This instruction manual covers installation and maintenance
for Fisher G100 Series Back Check Valves used on LPG
and anhydrous ammonia.
Description
Back check valves are normally closed valves that allow
ow in only one direction. When ow, in the direction
of the arrow starts, the valve poppet opens. When
ow stops or reverses, the valve poppet closes. Back
check valves are installed in liquid lling connections on
stationary storage tanks and bobtail delivery trucks, as
well as liquid transfer lines. The valves are frequently
used in conjunction with globe and angle valves or large
single-check ller valves.
Two styles of seat construction are available: soft
seat or metal-to-metal. The soft-seated construction is
intended for the lling connection on bobtail delivery
P1039
G105 SERIES
Figure 1. G100 Series Back Check Valves
(Arrow indicates direction of ow)
trucks. Because the valves give tight shutoff, piping on
the bobtail can be blown down easily for maintenance or
repair without experiencing leakage.
G100 SERIES
Installation
CAUTION
If the valve is to be used in service other than
LPG or anhydrous ammonia, contact the
factory to determine if the valve materials are
suitable for the particular service.
Flow through the back check valve must
be in the same direction as the flow arrow
stamped on the valve.
www.sherregulators.com
D450017T012

G100 Series
Specifications
This section lists the specications for the G100 Series valve. Factory specications are stamped on the nameplate fastened on
the valve at the factory.
SEAT CONSTRUCTION
Metal-to-Metal
Soft Seat
OUTLET CONNECTION,
IN.
3/4 FNPT 3/4 MNPT 21 GPM / 79.5 l/min G100 - - - -
1-1/4 FNPT 1-1/4 MNPT 55 GPM / 208 l/min G101 - - - -
2 FNPT 2 MNPT 150 GPM / 568 l/min G102 G112
2 FNPT 2 FNPT 150 GPM / 568 l/min G109 - - - -
3 FNPT 3 MNPT 250 GPM / 946 l/min - - - - G104
2 MNPT and 1-1/4 FNPT 2 MNPT 137.5 GPM / 520 l/min - - - - G105
2 MNPT 3 FNPT 254 GPM / 961 l/min - - - - G106
3 MNPT and 2 FNPT 3 MNPT 254 GPM / 961 l/min - - - - G107
INLET CONNECTION,
IN.
Maximum Operating Pressure: 250 psig / 17.2 bar
1. Brass valves are not suitabe for NH
applications.
3
2. Manually operate the back check valve’s poppet
before installation to assure parts were not damaged in
shipment or blocked with dirt or foreign material.
3. Install valve so that arrow points in the direction of flow
through the valve.
4. Use pipe dope on the main threads of the valve or
the pipeline. Polytetrafluoroethylene (PTFE) tape or
PTFE pipe dope compound is recommended for the
male threads of the larger valves such as the 2 and
3 in. sizes.
5. Test the valve for proper operation after installation and
before placing the system into full service. To make the
test, pressure the system through the back check valve
and then quickly bleed pressure from the valve inlet
piping. Check for pressure build-up in the inlet piping.
On soft seated valves, there should be no build-up
in the inlet side. On metal-to-metal seated valves, a
slow pressure build-up is permissible. A rapid pressure
build-up on either valve style indicates that the valve
has malfunctioned.
PROPANE FLOW CAPACITY AT
10 psig / 0.69 bar
DIFFERENTIAL PRESSURE
!
WARNING
TYPE NUMBER
Brass Steel
Trained personnel should test the back check
valve in a safe location.
To ensure that the valve is still functional,
back check closure should be checked
annually if there is no other regularly
scheduled test program.
Maintenance
Annually TEST back check valve for closure. Back check valves
are non-repairable. Replace non-functioning valves.
LPG Equipment
Emerson Process Management
Regulator Technologies, Inc.
USA - Headquarters
McKinney, Texas 75070 USA
Tel: +1 800 558 5853
Outside U.S. +1 972 548 3574
For further information visit www.fisherregulators.com
The Emerson logo is a trademark and service mark of Emerson Electric Co. All other marks are the property of their prospective owners. Fisher is a mark owned by Fisher Controls International LLC,
a business of Emerson Process Management.
The contents of this publication are presented for informational purposes only, and while every effort has been made to ensure their accuracy, they are not to be construed as warranties or
guarantees, express or implied, regarding the products or services described herein or their use or applicability. We reserve the right to modify or improve the designs or specications of such
products at any time without notice.
Emerson Process Management Regulator Technologies, Inc. does not assume responsibility for the selection, use or maintenance of any product. Responsibility for proper selection, use and
maintenance of any Emerson Process Management Regulator Technologies, Inc. product remains solely with the purchaser.
©Emerson Process Management Regulator Technologies, Inc., 2001, 2015; All Rights Reserved