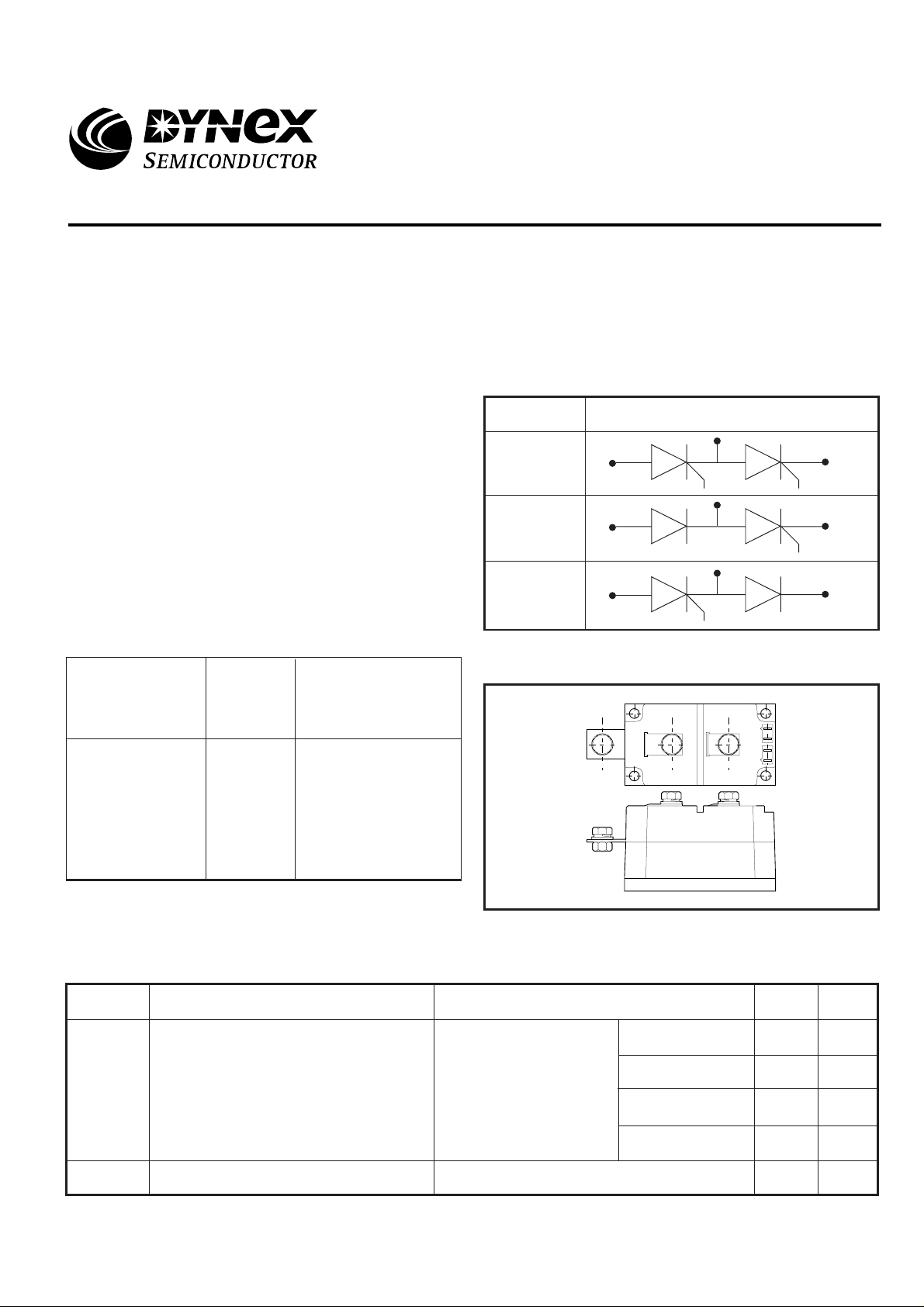
MP03 XXX 130 Series
MP03 XXX 130 Series
Phase Control Dual SCR, SCR/Diode Modules
Replaces December 1998 version, DS4480-3.0 DS4480-4.0 January 2000
FEATURES
■ Dual Device Module
■ Electrically Isolated Package
■ Pressure Contact Construction
■ International Standard Footprint
■ Alumina (non-toxic) Isolation Medium
APPLICATIONS
■ Motor Control
■ Controlled Rectifier Bridges
■ Heater Control
■ AC Phase Control
VOLTAGE RATINGS
Type
Number
MP03/130-20
MP03/130-18
MP03/130-16
Repetitive
Peak
Voltages
V
DRM VRRM
2000
1800
1600
Conditions
Tvj = 125oC
I
= I
DRM
RRM
V
& V
DSM
V
& V
DRM
respectively
= 30mA
=
RSM
+ 100V
RRM
Code
HBT
HBP
HBN
KEY PARAMETERS
V
DRM
I
TSM
I
(per arm) 134A
T(AV)
V
isol
CIRCUIT OPTIONS
Circuit
PACKAGE OUTLINE
2000V
4000A
2500V
Lower voltage grades available. For full description of
part number see "Ordering Instructions" on page 3.
CURRENT RATINGS - PER ARM
Symbol
I
T(AV)
I
T(RMS)
Mean on-state current
RMS value
Parameter
Module type code: MP03.
See Package Details for futher information.
Conditions
Halfwave, resistive load
T
= 75oC
case
T
case
T
case
T
heatsink
T
heatsink
= 75oC
= 85oC
= 75oC
= 85oC
Max.
134
112
114
95
210
Units
A
A
A
A
A
1/10
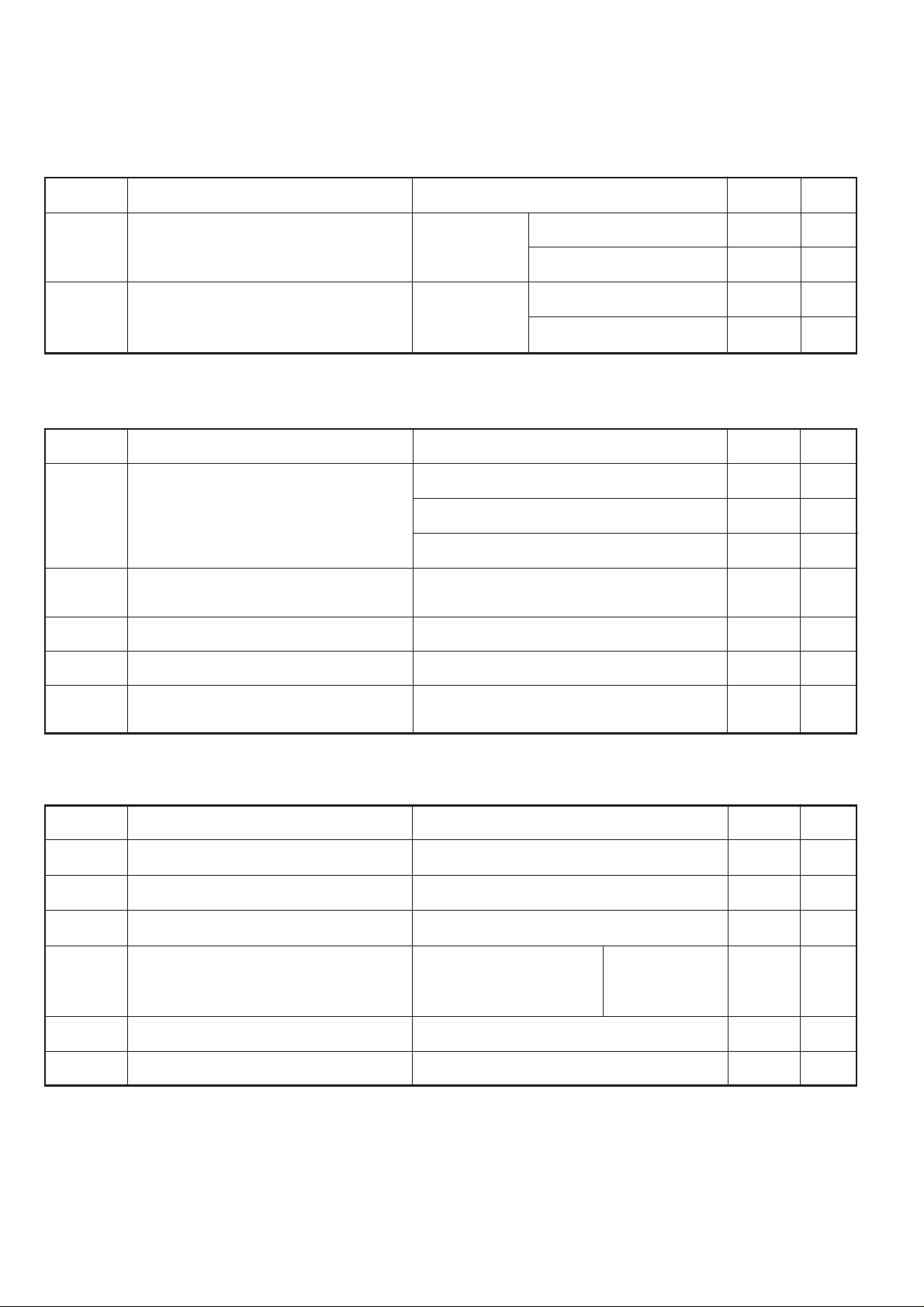
MP03 XXX 130 Series
SURGE RATINGS - PER ARM
Symbol
I
TSM
I2t
Surge (non-repetitive) on-state current
I2t for fusing
Parameter
THERMAL & MECHANICAL RATINGS
Symbol
R
th(j-c)
R
th(c-hs)
vj
T
sto
Thermal resistance - junction to case
per Thyristor or Diode
Thermal resistance - case to heatsink
per Thyristor or Diode
Virtual junction temperatureT
Storage temperature range
Parameter
Conditions Max.
10ms half sine;
Tj = 125oC
10ms half sine;
Tj = 125oC
VR = 0
VR = 50% V
VR = 0
VR = 50% V
Conditions
dc
halfwave
3 phase
Mounting torque = 5Nm
with mounting compound
RRM
RRM
4000 A
3200
80000
51200
Max.
0.21
0.22
0.23
0.05
125
-40 to 125
Units
A
A2s
A2s
Units
o
C/W
o
C/W
o
C/W
o
C/W
o
C
o
C
isol
Isolation voltageV
Commoned terminals to base plate
AC RMS, 1min, 50Hz
2.5
DYNAMIC CHARACTERISTICS
Symbol
TM
I
RRM/IDRM
dV/dt
dI/dt
V
T(TO)
r
T
* Higher dV/dt values available, contact factory for particular requirements.
Note 1: The data given in this datasheet with regard to forward voltage drop is for calculation of the power dissipation in the
semiconductor elements only. Forward voltage drops measured at the power terminals of the module will be in excess of these
figures due to the impedance of the busbar from the terminal to the semiconductor.
On-state voltageV
Peak reverse and off-state current
Linear rate of rise of off-state voltage
Rate of rise of on-state current
Threshold voltage
On-state slope resistance
Parameter
At 450A, T
At V
RRM/VDRM
To 60% V
From 67% V
= 25oC - See Note 1
case
, Tj = 125oC
= 125oC
DRM Tj
to 400A Repetitive 50Hz
DRM
Gate source 20V, 20Ω
Rise time 0.5µs, Tj =125oC
At Tvj = 125oC - See Note 1
At Tvj = 125oC - See Note 1
Max.Conditions
1.90
30
200*
100
1.25
1.33
Units
V/µs
A/µs
kV
V
mA
V
mΩ
2/10
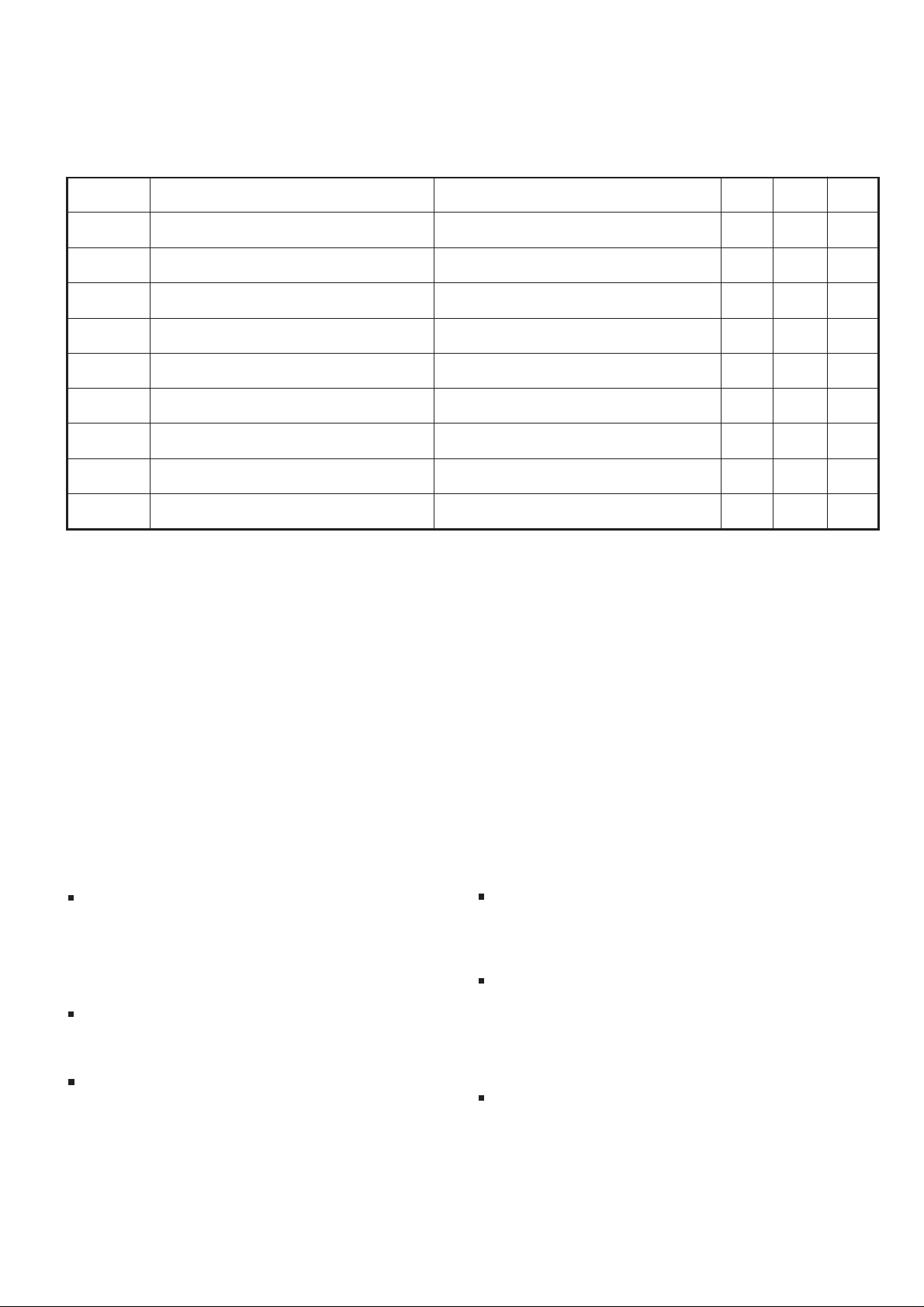
GATE TRIGGER CHARACTERISTICS AND RATINGS
MP03 XXX 130 Series
Symbol
V
GT
I
GT
V
GD
V
FGM
V
FGN
V
RGM
I
FGM
P
GM
P
G(AV)
Gate trigger voltage
Gate trigger current
Gate non-trigger voltage
Peak forward gate voltage
Peak forward gate voltage
Peak reverse gate voltage V5.0Peak forward gate current
Peak gate power
Mean gate power
Parameter
V
= 5V, T
DRM
V
= 5V, T
DRM
V
= 5V, T
DRM
Anode positive with respect to cathode
Anode negative with respect to cathode
Anode positive with respect to cathode
ORDERING INSTRUCTIONS
Part number is made up as follows:
MP03 HBT 130 - 18
MP = Pressure contact module
03 = Outline type
HBT = Circuit configuration code (see "circuit options" - front page)
130 = Nominal average current rating at T
18 = V
RRM
/100
= 75oC
case
Conditions
= 25oC
case
= 25oC
case
= 25oC
case
Examples:
MP03 HBP130-16
MP03 HBN130-20
MP03 HBT130-16
Typ.
-
-
-
-
-
-
-
Max.
3.0
200
0.2
30
0.25
4
16
3
Units
V
mA
V
V
V
AW
W
Note: Diode ratings and characteristics are comparable with SCR in types HBP or HBN.
Types HBP or HBN can also be supplied with diode polarity reversed, to special order.
MOUNTING RECOMMENDATIONS
Adequate heatsinking is required to maintain the base
temperature at 75oC if full rated current is to be achieved.
Power dissipation may be calculated by use of V
information in accordance with standard formulae. We can
provide assistance with calculations or choice of heatsink if
required.
The heatsink surface must be smooth and flat; a surface finish
of N6 (32µin) and a flatness within 0.05mm (0.002") are
recommended.
Immediately prior to mounting, the heatsink surface should be
lightly scrubbed with fine emery, Scotch Brite or a mild
chemical etchant and then cleaned with a solvent to remove
oxide build up and foreign material. Care should be taken to
ensure no foreign particles remain.
T(TO)
and r
T
An even coating of thermal compound (eg. Unial) should be
applied to both the heatsink and module mounting surfaces. This
should ideally be 0.05mm (0.002") per surface to ensure optimum
thermal performance.
After application of thermal compound, place the module squarely
over the mounting holes, (or 'T' slots) in the heatsink. Using a
torque wrench, slowly tighten the recommended fixing bolts at
each end, rotating each in turn no more than 1/4 of a revolution at
a time. Continue until the required torque of 5Nm (44lb.ins) is
reached at both ends.
It is not acceptable to fully tighten one fixing bolt before starting to
tighten the others. Such action may DAMAGE the module.
3/10