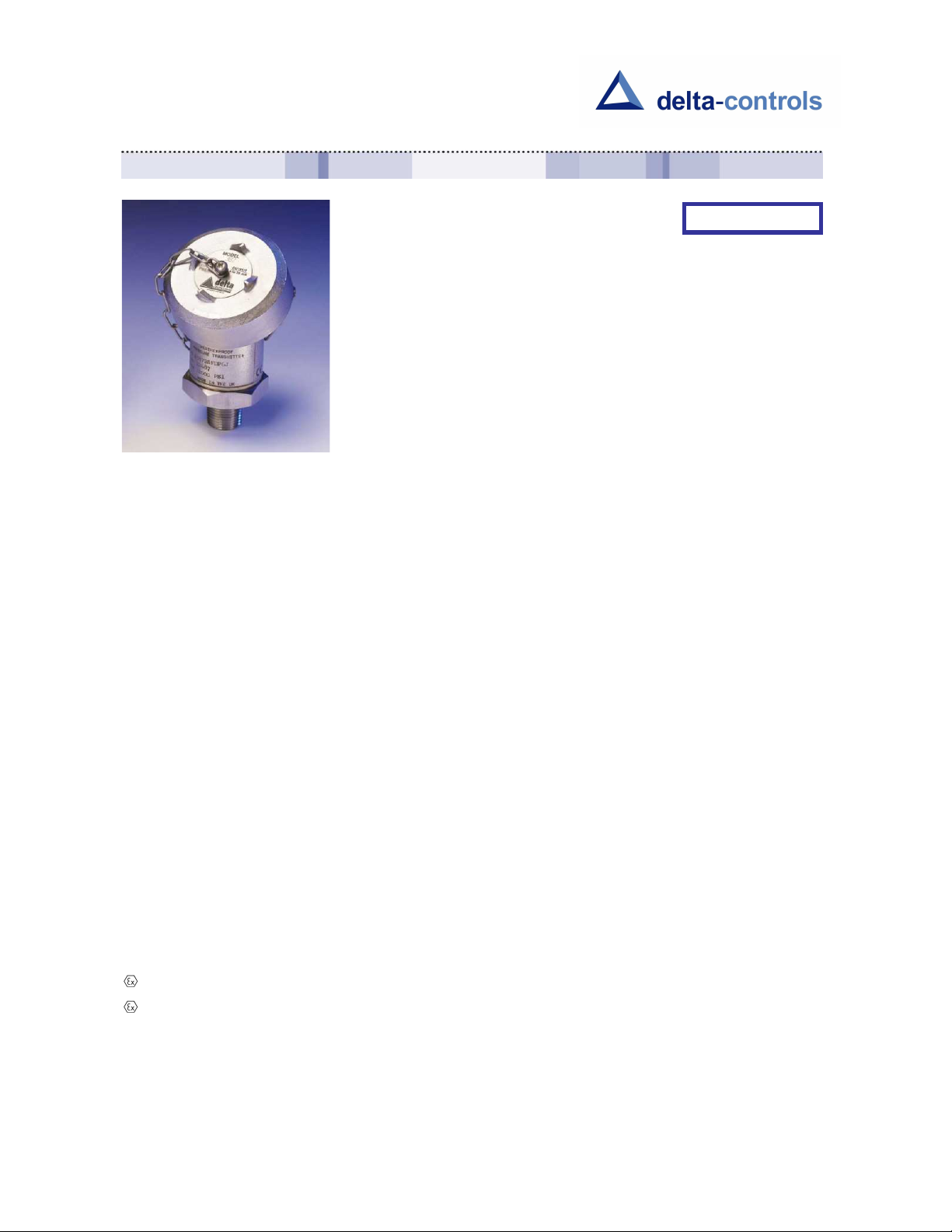
Installation, Operating and
Maintenance Instructions for
Series 387 Analogue Transmitter
DESCRIPTION
Series 387 Transmitters/transducers employ strain gauge pressure
sensing and a precision amplifier providing a 4 to 20 mA current output
capable of being used in control and indicating loops without further
amplification.
Each instrument is coded to provide a complete description of the
facilities offered.
IMPORTANT INFORMATION
Delta Controls cannot guarantee performance, standards compliance,
or accept liability for any eventuality arising if the instrument is installed
or operated in any way contrary to the guidance contained herein.
ENCLOSURES AND CERTIFICATION
All Models are enclosed in an investment cast, 316 Stainless Steel
enclosure, giving environmental protection to IP66 (NEMA 4X).
Ensure that the Model chosen is appropriate to the environment and
that codes of practice for the installation of electrical apparatus have
been followed.
4-387 Certified Intrinsically Safe when powered via a suitable Barrier
device or Isolator. The unit is rated
Ga Ex ia IIC T4 (Tamb = -20°C to +90°C)
Ga Ex ia IIC T5
Ex iaD 20 T120 (Tamb = -20°C to +90°C)
Ex iaD 20 T90
This model is suitable for use in Zone 0 Hazardous Areas when
installed in accordance with the proper Codes of Practice.
SPECIAL CONDITIONS OF SAFE USE (4-387 only)
1. The transmitter may not be capable of withstanding the
500V insulation test required by clause 6.3.12 of EN
60079-11 and this must be taken into account when
installing the apparatus
2. A conduit/cable gland or an integral cable when fitted to
the transmitter must provide a degree of protection of
R-387 Explosion-proof/Weather-proof and rated
And
This model is suitable for use in Zone 1/21 Hazardous Areas (Gas and
Dust) when installed in accordance with the proper Codes of Practice.
Particular attention should be given to the cable gland or conduit
attachment.
The instrument must be isolated from the power supply before the cover
is removed, and the cover must be screwed fully down (hand right) and
locked with the grub screw before power is restored.
at least IP6X
II 2 GD Ex tD A21 IP6X T85°C
II 2 GD Ex tD A21 IP6X T135°C (Tamb = -20°C to +90° C)
A-387 Weather-proof only. Suitable for outdoor use in all industrial
environments, including offshore.
F-387 Listed by Factory Mutual Research as being suitable for use in
Hazardous areas as follows:
Explosionproof Class I Division 1
Groups B, C & D
Dust Ignitionproof Class II & III Division 1
Groups E, F & G
Intrinsically Safe Class I, II & III Division 1
Groups A, B, C, D, E, F & G
Non-Incendive Class I, II & III Division 2
Groups A, B, C, D, F & G
ELECTRICAL ENTRY AND CONNECTION (Fig 1)
For reasons of Explosion containment, Explosion-proof approval is
confined to ranges 0 to 10 bar (160 psi) and above. Intrinsic Safety
operation are available over the full set of pressure ranges offered.
The instrument is designed for ease of electrical connection combined
with compact overall size, even with 2 mm2 (16 AWG) solid wire. Cable
inserted through threaded entry clears the terminal block and passes
out through the cover aperture, enabling termination and connection to
be carried out with minimum effort.
Cable to be braid, double-braid, or braid & foil screened.
Cable gland to terminate the cable screen through a 360° connection.
Ideally the gland would be made from the same material as the
instrument housing, 316 stainless steel. The instrument requires an
earth bond to the instrument enclosure.
MAINTENANCE
No maintenance is normally necessary or required on these
instruments. Should the cover be removed for adjustment, ensure that
the O-ring seal is not damaged. Light greasing is recommended.
Maintainance should only be conducted in a dry ambient environment
to prevent water ingress, which can cause damage to sensitive internal
components.
WARRANTY
This instrument is guaranteed against faulty workmanship and material
for a period of one year from the date of delivery. The company
undertakes to repair, free of charge, ex-works any instrument found to
be defective within the specified period provided the instrument has
been used within the specification in accordance with these instructions
and has not been misused in any way. Detailed notice of such defects
and satisfactory proof thereof must be given to the company
immediately after the discovery and the goods have to be returned free
of charge to the company, carefully packed and accompanied by a
detailed failure report.
To comply with health and safety requirements, the instrument must be
clean and safe to handle and accompanied by a formal statement to
that effect duly signed by an authorised officer of the user company.
Any instrument returned without certification will be quarantined and no
action will occur until cleared.
On ranges below 10 bar gauge (160 psi), it is recommended that the
cable incorporates a breather tube to permit pressure equalisation
during changing atmospheric conditions. This is not permitted with Exd
and FM Explosion-proof installations, but as these are limited to higher
pressures, any error introduced will be negligible. A suitable cable
gland must be fitted if the unit is to be wired with flexible or armoured
cable.
For Weather-proof and Intrinsically Safe units, the gland must seal to an
environmental rating not less than that of the instrument (IP66/NEMA
4X). In addition, for Exd and FM Explosion-proof units, it must be of a
type approved for the Zone/Division and Hazards applications, it must
be capable of withstanding a pull of 160 Newtons (36 pounds force).
Two optional threads are offered as standard for attachment of conduit
or gland.
002522-387-G
1

These are: Code 1 Female Thread M20 x 1.5 ISO
Code 2 Female Thread ½” NPT
WETTED PARTS
A variety of wetted parts is available, dependent upon the user’s needs
and, to some extent, on the pressure range required.
Code S For pressure ranges 10 bar (160 psi) and upwards, the
standard combination is a diaphragm of 15-5 PH or 17-4 PH stainless
steel, mounted on a pressure entry of 316 stainless steel. This offers
an optimum combination of high accuracy with corrosion resistance.
Thin-film strain gauge sensors are bonded directly to the ‘dry’ side of
the diaphragm and are laser-trimmed for accuracy and stability.
Maximum Working Pressure 2 x Upper Range Limit.
Code T Monel diaphragm and pressure entry. The low chemical
reactivity of this Nickel-copper alloy allows the instrument to be used
with chemicals that attack stainless steel. Its tensile strength limits the
amount of overpressure the instrument can take without suffering a
permanent shift in calibration. Maximum Working Pressure 1.5 x Upper
Range Limit compatible with the requirements of NACE.
Code U Hastelloy diaphragm and pressure entry. This offers the
best chemical resistance, but performance limits apply as to NACE and
Monel units. Maximum Working Pressure 1.5 x Upper Range Limit
compatible with the requirements of NACE.
Code C Hastelloy diaphragm and annealed 316 Stainless Steel
pressure entry. This offers the chemical resistance of Hastelloy on the
critical measuring parts, but uses SS for the more massive Pressure
Connection. This is the recommended version for NACE applications.
Performance limits apply as Monel units. Maximum Working Pressure
1.5 x Upper Range Limit.
Code R From 0 to 1 bar up to 0 to 10 bar, the sensor is a
piezoresistive silicon sensor protected by a 316 stainless steel
diaphragm. Maximum Working Pressure 2 x Upper Range Limit.
While a limited amount of advice can be given regarding suitability of
the wetted-parts options available, the wide range of chemical
processes to which Delta Controls Transmitters/transducers are applied
requires that the final decision for compatibility must lie with the user.
RANGES AND UNITS OF MEASURE
Definitions.
Upper Range Limit (URL). The maximum pressure to which the 20
mA output may correspond. In effect, this is recommended as the
maximum pressure that may continuously be applied to the instrument.
Upper Range Value (URV). The pressure which, according to the
setting of the instrument, corresponds to 20 mA output. For this range
of instruments, it will lie between 25% and 100% of the URL (4:1 turn
down).
Maximum Working Pressure. The pressure that may be occasionally
applied during test or abnormal conditions without detriment to the
performance of the instrument. Continuous operation above the URL,
particularly if the pressure is cyclic, will shorten the useful life of the
instrument and should be avoided
OUTPUT SIGNAL (Fig 2)
The transmitters/transducers use the standard 4 to 20 mA two wire
system in which the power supply, transmitter and load are in series.
This means, therefore, that for a constant voltage at the power supply,
as the signal level rises, the drop across the load reduces the voltage
available at the transmitter, which should at all times lie between 12V
and 36V. The attached load/voltage diagram shows the permitted
range of supply voltage for satisfactory operation of the instrument.
On intrinsically safe versions the maximum voltage is 28V DC.
Two levels of insulation can be offered:
Code 6 50 VDC maximum between electrical circuits
and earth (Ground).
Code M 500 V ac test between electrical circuits
and earth (Ground).
Where the instruments are certified Intrinsically Safe for use in
hazardous areas, they must be powered from a suitable source in
accordance with the System Certificate or Control Drawing. Where
Zener Barriers are used on Code 6 Signal Option, the instrument must
be earthed using the terminal provided with a conductor not less than 4
mm2 cross section and a total resistance to earth not exceeding 1 ohm.
If a galvanically isolated repeater / power supply is employed, or Signal
Code M is specified, no such earth is necessary.
While the instruments have high resistance to EM and RF interference,
it is strongly recommended that for long cable runs, the instrument
leads be screened.
For RF suppression to be fully effective, the instrument enclosure
should be grounded.
PROCESS CONNECTIONS
Ensure that the pressure range and maximum working pressures
selected are compatible with the expected pressures in the system.
The method of installation should ensure that very high temperature
media are not allowed in direct contact with the instrument by fitting an
adequate length of impulse line or a syphon. Precautions should also
be taken so that under low temperature conditions the process medium
cannot freeze within the instrument sensor. The instrument may be
mounted in any position and is normally self supporting by the pipe
work. The pressure connector should be tightened using a 45 mm (1
¾”) AF spanner on the hexagon provided, and the appropriate spanner
on the pipe work connector.
DO NOT USE A COMPRESSION WRENCH ON THE INSTRUMENT
BODY.
Code J ½” NPT external.
Code N G1/2A to ISO 228 (½” BSP Parallel External spigotted)
Note: Codes J & N are subject to a maximum average pressure of 1200
bar / 17500 psi or the value given in ‘wetted parts’ which ever is less.
Code V Nominal ¼” HP Cone and thread. This fitting is recommended
for pressures over 10, 000 psi (690 bar).
A wide range of alternative connectors is available; refer to contract
specification if necessary.
ADJUSTMENT
The instruments have fine adjustment for zero and span, plus a range
adjustment giving 4:1 turn-down from the nominal range, i.e. the range
0 to 10 bar (0 to 160 psi) may be re-ranged down to 0 to 2.5 bar (0 to
36 psi).
Range, span and zero controls are accessible by removal of the
threaded lid (refer to fig 3) first loosening the grub screw.
Disconnection of the electrical wiring is not necessary for the
functioning of the instrument, but proper site practices should be
followed when working on an instrument which is ‘live’ with respect to
power or process. For example, under no circumstances may an
Explosion-proof instrument operating in a Zone 1 / Division 1
Hazardous area have its lid removed when the electrical circuit is live
without a permit.
002522-387-G
2