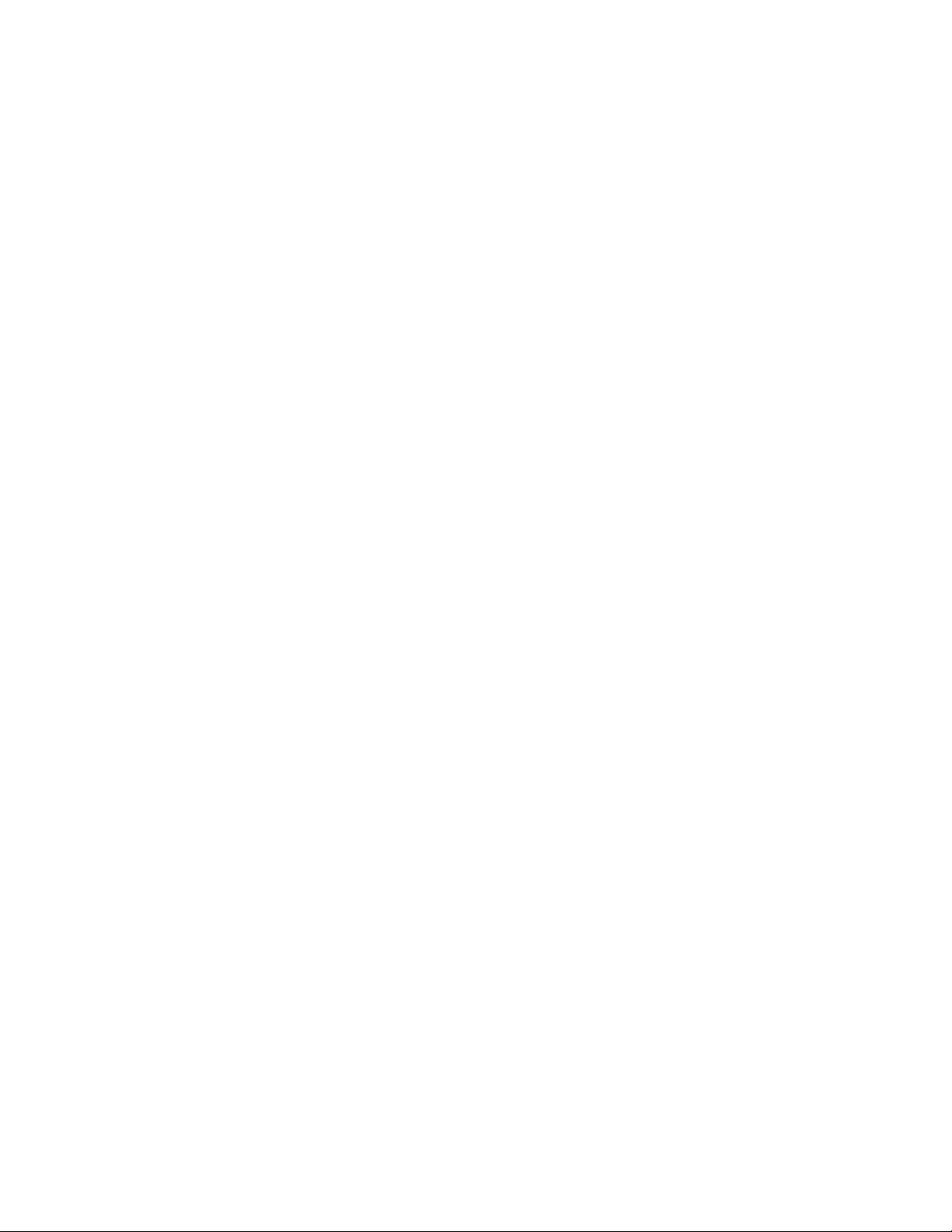
XLS 3U SERIES
CIRCUIT DESCRIPTION AND SERVICE NOTES
INTRODUCTION
These notes are intended to assist maintenance and service of the XLS 3-rack-space family of amplifiers. Please
refer to the relevant schematic diagrams and system diagram while reading this document.
The component references of the two amplifier channel electronics are appended "A" and "B" respectively. Shared
circuitry (such as that of the protection system) has no suffix. This document will refer to channel A references
only. Operation of channel B is identical except where explicitly noted. Voltage values in bold mentioned in the
text are test voltages which may be used for diagnostic purposes. Please read the surrounding text which
explains circuit operation and may qualify such measurements.
MECHANICAL CONSTRUCTION
The mechanical structure of the amplifier comprises three main components: chassis, front panel and cover.
The one-piece chassis incorporates rear panel, side panels, bottom cover and transformer mount.
The main PCB is fixed to the chassis using 4 M4x16 screws with insulating washers through the main
heatsinks and 4 M4x8 screws for the edges of the board, one of which connects the chassis electrically to 0V on
the PCB.
There are two heatsinks secured to the board with 3x No6 / 5/16" pozi pan 'B' point self tapping screws and 3x
M3.5 shakeproof washers each. Output devices are bare mounted (with zinc oxide heatsink paste) to the heatsinks with 2x No6 / 5/16" pozi pan 'B' point self tapping screws each. CAUTION: The heatsinks are LIVE at up to
+95VDC on one AND -95VDC on the other.
The plugable input module and output module are secured using 4x No4 / 8 plastite screws and 4x M3 / 8 screws
respectively.
The mechanical integrity of the amplifier is realised when the substantial frontpanel is fitted using 4x M4 /10
Flange Pozi Black screws at the sides and 2x M4 nuts behind the front. The cover is secured using 6x #8 / 3/8"
Flange Pozi Black self tapping screws.
All internal wiring is plugable to allow quick removal of main PCB for repairs and servicing.
CIRCUIT DESCRIPTION
Input Stage
The input stage is built around one half of a TL072 dual operational amplifier, IC1A on the input board,
configured as a unity-gain differential amplifier. Its correct operation depends on both of its input terminals being
correctly terminated and, therefore, any gain errors around this stage may be a result of a faulty cable termination
within the mating XLR connectors. There is no provision for trimming Common-Mode Rejection (CMR) but
checking this can easily eliminate the input stage in the search for a fault.
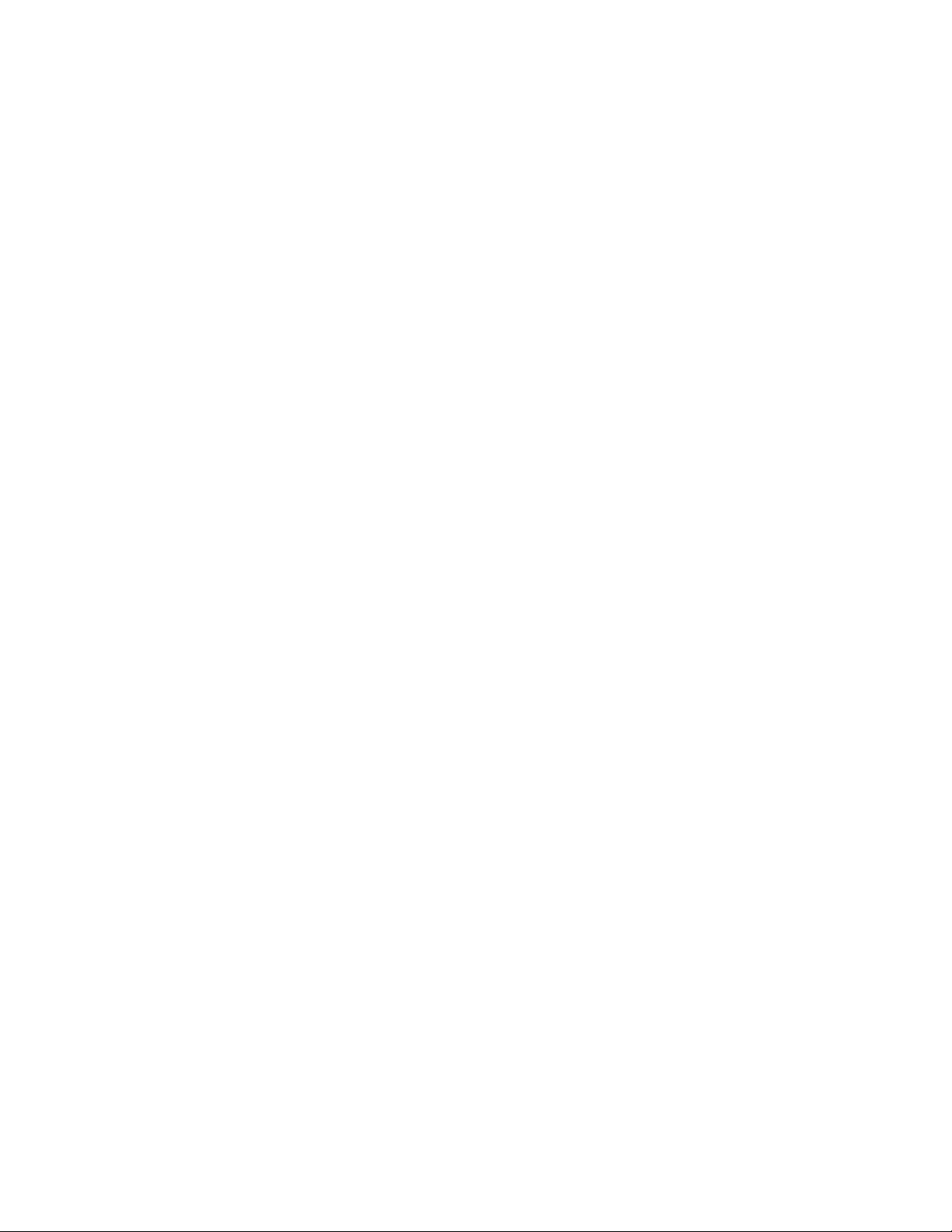
CMR checkout procedure is as follows :
Inject a common-mode test signal at 1kHz and +4dBu to the channel under test. The common-mode test signal of
the Audio Precision test system is suitable, otherwise connect the signal to both pins 2 & 3 via 56 Ohm or 47
Ohm resistors. Observe the amplifier output (with level control at maximum) which should be less than -9dBu.
Power for the input stage is derived from the main +HT and -HT supplies via 1W resistors R24 and R25
and shunt regulated to a nominal +18V, -18V by ZD3 and ZD4 respectively, all located on the main PCB. The output of the input differential amplifier is fed via DC blocking capacitor C7A and 100R “Build-out" resistor R10A to
pin 5 of Header 2 (channel B - pin 2 of Header 3) and then exits the input board.
If LK1,2,3,4 are present and intact then the signal travels back onto the input board via pin 4 of Header 2 (channel
B - pin 5 of Header 3).
Sub-Sonic filter and Clip Limiter
The Sub-Sonic filter is based around the other half of the TL072 dual operational amplifier, IC1A on the
input board, configured as a Sallen & Key unity gain 2nd order Butterworth high pass filter. The two-pole threeposition switch, SW1A, selects the following -3dB cutoff frequencies:
1) 30Hz: only C8A and C10A connected;
2) 15Hz: C11A and C12A connected in parallel with C8A and C10A respectively;
3) Off position: C14A bypassing C8A and C10A.
Limiter switch SW2 in its OFF position shorts R2A and disconnects LDR1A to turn the Clip Limiter off.
In its ON position, SW2 connects R2A and LDR1A as a light-dependent voltage divider, controlling the
level of the input signal. LDR1A faces LED2A, which is lit when the amplifier reaches about 1dB below clip (at the
same time as the clip LED at the front). Because the resistance of LDR1A reduces as its cell area is illuminated,
pushing the amplifier into clip will, therefore, cause the input signal to be reduced at the R2A -LDR1A divider.
Thus the amplifier is Clip Limited.
The output of the filtering/limiting op-amp is AC coupled by C13A and built out by R11A, and continues to pin 3
of Header 2 (ch. B pin 4 of Header 3), at which point it re-enters the main board and makes its way to pin 1 of
CN2A, a three-pin header making connection by wire to the level potentiometers: pin 1 is Top, pin 2 is Wiper, pin
3 is Bottom. The signal emerges from pin 2 and is fed to the input of the Power Amplifier.
POWER AMPLIFIER
The power amplifier consists of a fairly conventional Class A driver stage driving a Class AB bipolar output stage.
Each stage will be dealt with individually.
Class A Driver
The input signal returned from the level control is fed via DC blocking capacitor C7A and R8A. DC bias
current for the Class A input stage is supplied via R9A, while 33pF capacitor C54A prevents any extreme high frequency input signals from reaching the power amplifier and also provides a low source impedance at high frequencies to ensure frequency stability.
The first stage of the class A driver consists of Q1A and Q2A configured as a long-tailed pair differential
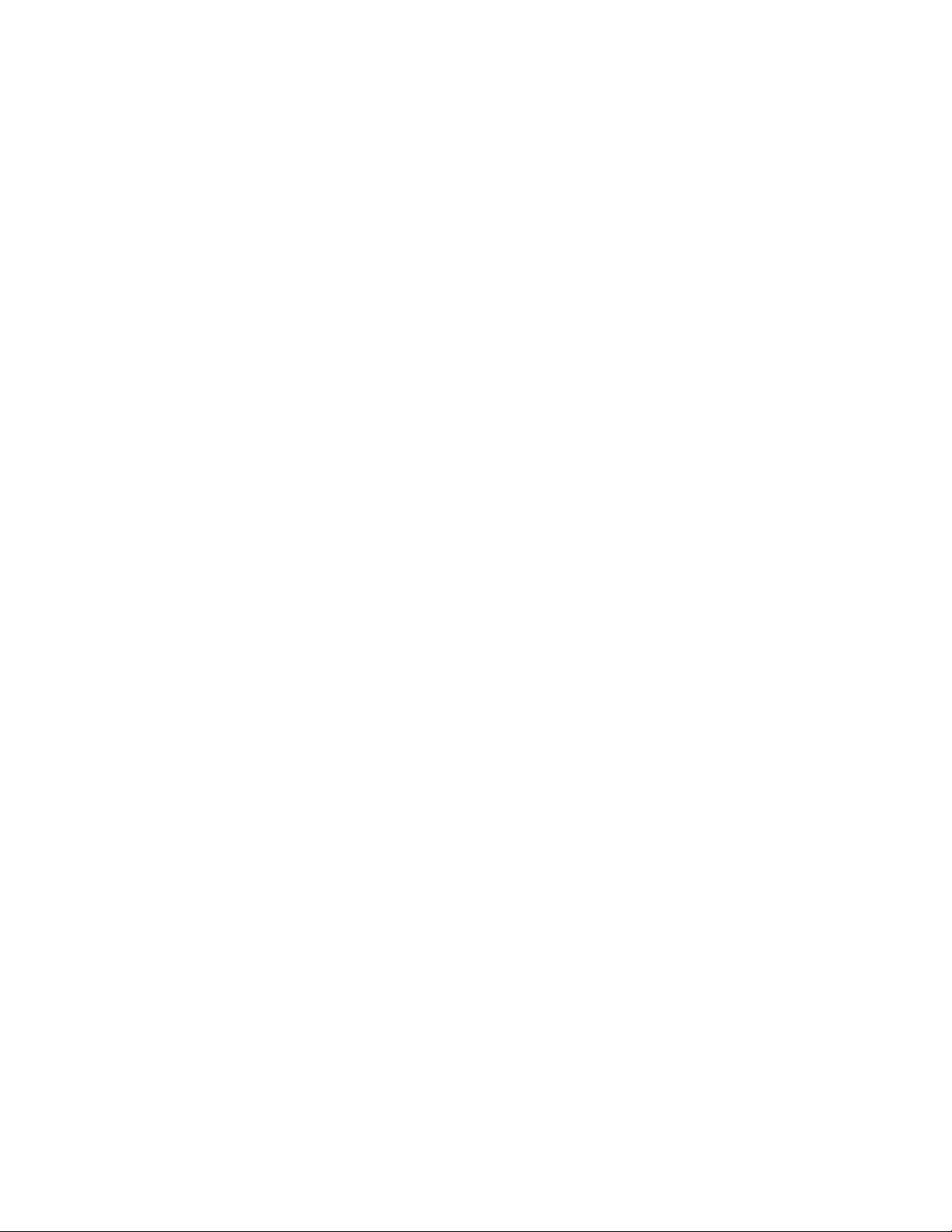
amplifier. Emitter resistors R10A and R11A de-sensitise the performance of the input stage to parameter variations of the two input transistors. The quiescent current for the input stage is delivered by current source Q3A.
Diodes D1A and D2A provide a reference voltage of approximately 1.2V, which is applied to the base of Q3A.
Approximately half of this (0.6V) will then appear across R13A (220R), which then sets the current, sourced from
Q3A collector at approximately 2.7mA. In the quiescent state half of this current is driven through Q1A and Q2A.
Hence the voltage dropped across emitter resistors R10A and R11A will be approximately equal at 135mV.
Overall voltage feedback of the amplifier is derived through R18A and R17A. R57A and C20A provide
local feedback around the Class A section only to define the dominant pole of the amplifier. C56A connected in
series with R66A gives 100% DC feedback to minimize any DC offset at the output. The reulting feedback signal
is applied to the base of TR53A.
The collector currents of Q1A and Q2A are fed via D3A and D4A to R15A and R16A respectively.
Hence, in the quiescent state, R15A and R16A should each exhibit a voltage drop of 1.35V or so.
Under normal conditions, the signals at the bases of Q1A and Q2A will be identical. However, under fault conditions, such as a DC offset at the output, the base voltages will become offset also. For example, in the event of a
large DC offset of +50V at the output, a positive DC voltage will appear at the feedback point and hence at the
base of Q2A. Although this would, in theory, be the full +50V, owing to C11A being rated at only 25V, the voltage
will, in practice, be somewhat lower. However, the important issue is that the voltage is positive. In the event the
voltage is negative this indicates that the feedback network is faulty (most likely R18A itself).
The voltage at Q2A base being positive while the base of Q1A is close to 0V will then reverse bias Q2A
base-emitter hence turning off the transistor. Hence, no voltage should appear across R11A and R16A
while double the normal voltage will appear across R10A and R15A (270mV and 2.7V respectively).
Should this not be the case, it indicates a fault in the input stage itself.
The output of the input long-tailed-pair (i.e. the voltages at the anodes of D3A and D4A) are fed to a second longtailed pair Q4A and Q5A. The bias current for this stage is set by resistor R19A thus: D3A drops approximately
the same voltage as the base-emitter junction of Q4A; the same can be said of D4A and the base-emitter junction
of Q4A; therefore the voltage across R19A is approximately equal to the voltage across R15A and/or R16A, i.e.
1.35V. This sets a current of about 6.75mA split between Q4A and Q5A. C12A and C13A provide a little Miller
Feedback around Q4A and Q5A respectively. These capacitors can be important to the stability of the amplifier but
do not define the dominant pole. It should also be noted that either of these capacitors becoming "leaky" (difficult
to measure in circuit) will result in a DC offset at the output.
The collector of Q5A drives the output stage in conjunction with the collector of Q7A while the collector
of Q4A drives current mirror Q6A/Q7A via R20A. In the quiescent state R20A will show a voltage drop of around
67.5V, and the current mirror emitter resistors R23A R24A and will show equal voltage drops of 160mV. Hence,
for the same +50V DC offset, described earlier, one would expect no voltage drop across any of R20A, R23A or
R24A, indicating that the feedback is attempting to correct the fault. Likewise, for a negative DC offset one would
expect these voltages to be twice their usual value. If this is not the case then the second stage (Q4A-Q7A) is at
fault.
The collectors of Q5A and Q7A are joined to form the output of the class A driver by the Vbe multiplier:
R22A, R21A and Q8A(mounted on the heatsink), bypassed at AC by C15A, which sets the output stage