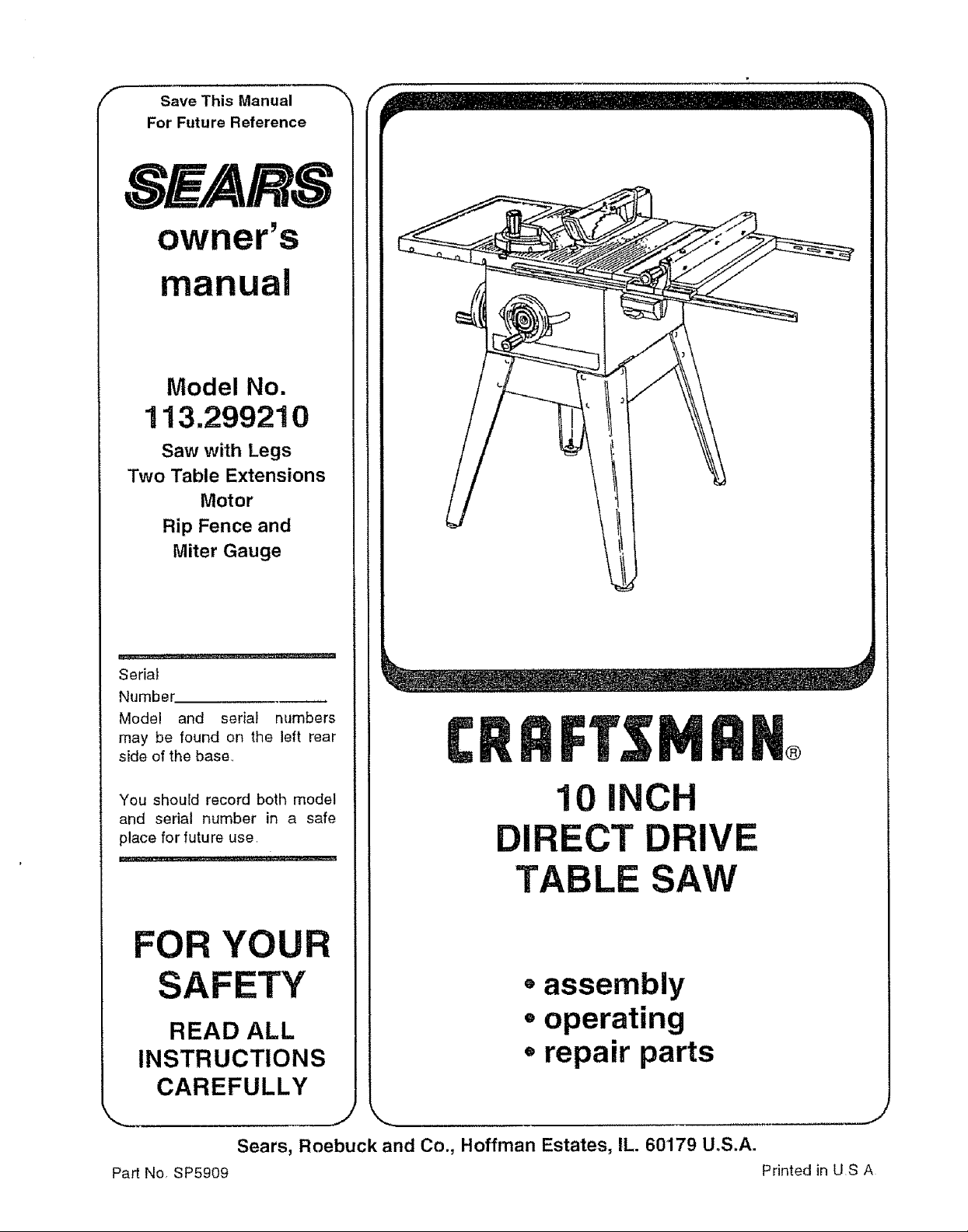
f
Save This Manual
For Future Reference
SEARS
owner's
manual
Model No.
113.299210
Saw with Legs
Two Table Extensions
Motor
Rip Fence and
Miter Gauge
Serial
Number.
Model and sedal numbers
may be found on the left rear
side of the base,
You should record both model
and serial number in a safe
place for future use,
FOR YOUR
READ ALL
INSTRUCTIONS
CAREFULLY
®
10 iNCH
DIRECT DRIVE
TABLE SAW
- assembly
. operating
orepair parts
J
Part No, SP5909
Sears, Roebuck and Co., Hoffman Estates, IL. 60179 U_S,A.
Printed in US A
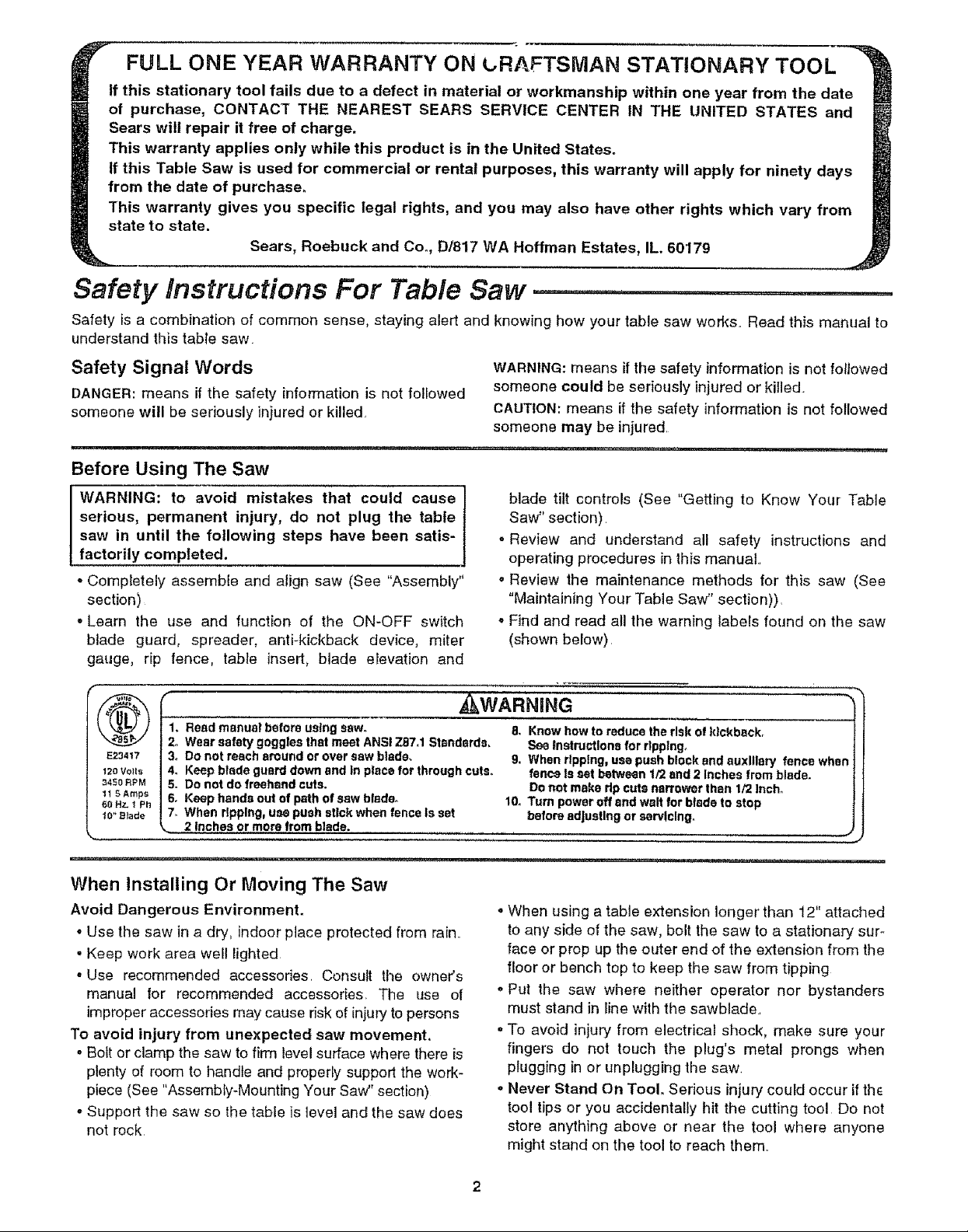
FULL ONE YEAR WARRANTY ON L,RAFTSNIAN STATIONARY TOOL
If this stationary tool fails due to a defect in material or workmanship within one year from the date
of purchase, CONTACT THE NEAREST SEARS SERVICE CENTER IN THE UNITED STATES and
Sears wilt repair it free of charge.
This warranty applies only while this product is in the United States.
If this Table Saw is used for commercial or rental purposes, this warranty will apply for ninety days
from the date of purchase.
This warranty gives you specific legal rights, and you may also have other rights which vary from
state to state.
Sears, Roebuck and Co°, D/817 WA Hoffman Estates, IL 60179 . .._
Safety Instructions For Table Saw
Safety is a combination of common sense, staying alert and knowing how your table saw works,, Read this manual to
understand this table saw
Safety Signal Words
DANGER: means if the safety information is not followed
someone will be seriously injured or killed
Before Using The Saw
WARNING: to avoid mistakes that could cause
serious, permanent injury, do not plug the table
saw in until the following steps have been satis-
factorily completed.
* Completely assemble and align saw (See "Assembly"
section)
° Learn the use and function of the ON-OFF switch
blade guard, spreader, anti-kickback device, miter
gauge, rip fence, table insert, blade elevation and
m
®
E23417
12o VoIts
3450 RP M
1 t 5 Amp._
60 Hz_ I Ph
I0" Blade
1, Read manual before usingsaw.
2. Wear safety gogglesthat meet ANSI Z87.1Standards,
' 3. DO not reach around or over saw blade.
4. Keepblade guard downend In place for throughcuts.
5. Do not do freehand cuts.
6. Keep hands out of path of saw blade°
7. When ripping,use push stickwhen fence Is set
2 Inches or more from blade.
WARNING: means if the safety information is not foUowed
someone could be seriously injured or killed,
CAUTION: means if the safety information is not followed
someone may be injured,
blade tilt controls (See "Getting to Know Your Table
Saw" section),
. Review and understand all safety instructions and
operating procedures in this manual.
, Review the maintenance methods for this saw (See
"Maintaining Your Table Saw" section)),
- Find and read all the warning labels found on the saw
(shown below),
, WARNING
8,, Know how toreduce therisk ofkickback,
See Instructions for ripping,
9. When rlpNng, usepush blockand auxiliary fence wher
fenceIs set between1/2end 2 Inches fromblade.
Donot make dp cutsnarrowerthan 1/2 ]nch_
l& Turn poweroff endwalt forbladeto stop
beforeadjustingor servicing.
When Installing Or Moving The Saw
Avoid Dangerous Environment.
• Use the saw in a dry, indoor place protected from rain,
• Keep work area well lighted
• Use recommended accessories Consult the owneCs
manual Ior recommended accessories, The use of
improper accessories may cause risk of injuryto persons
To avoid injury from unexpected saw movement.
. Bott or clamp the saw to firm level surface where there is
plenty of room to handle and properly support the work-
piece (See "Assembly-Mounting Your Saw" section)
° Support the saw so the table is level and the saw does
not rock
o When using a table extension longer than t2" attached
to any side of the saw, bolt the saw to a stationary sur_
face or prop up the outer end of the extension from the
floor or bench top to keep the saw from tipping
o Put the saw where neither operator nor bystanders
must stand in line wilh the sawblade,
° To avoid injury from electrical shock, make sure your
fingers do not touch the plug's metal prongs when
plugging in or unplugging the saw,
• Never Stand On Tool Serious injury could occur if the
tool tips or you accidentally hit the cutting tool Do not
store anything above or near the tool where anyone
might stand on the tool to reach them,
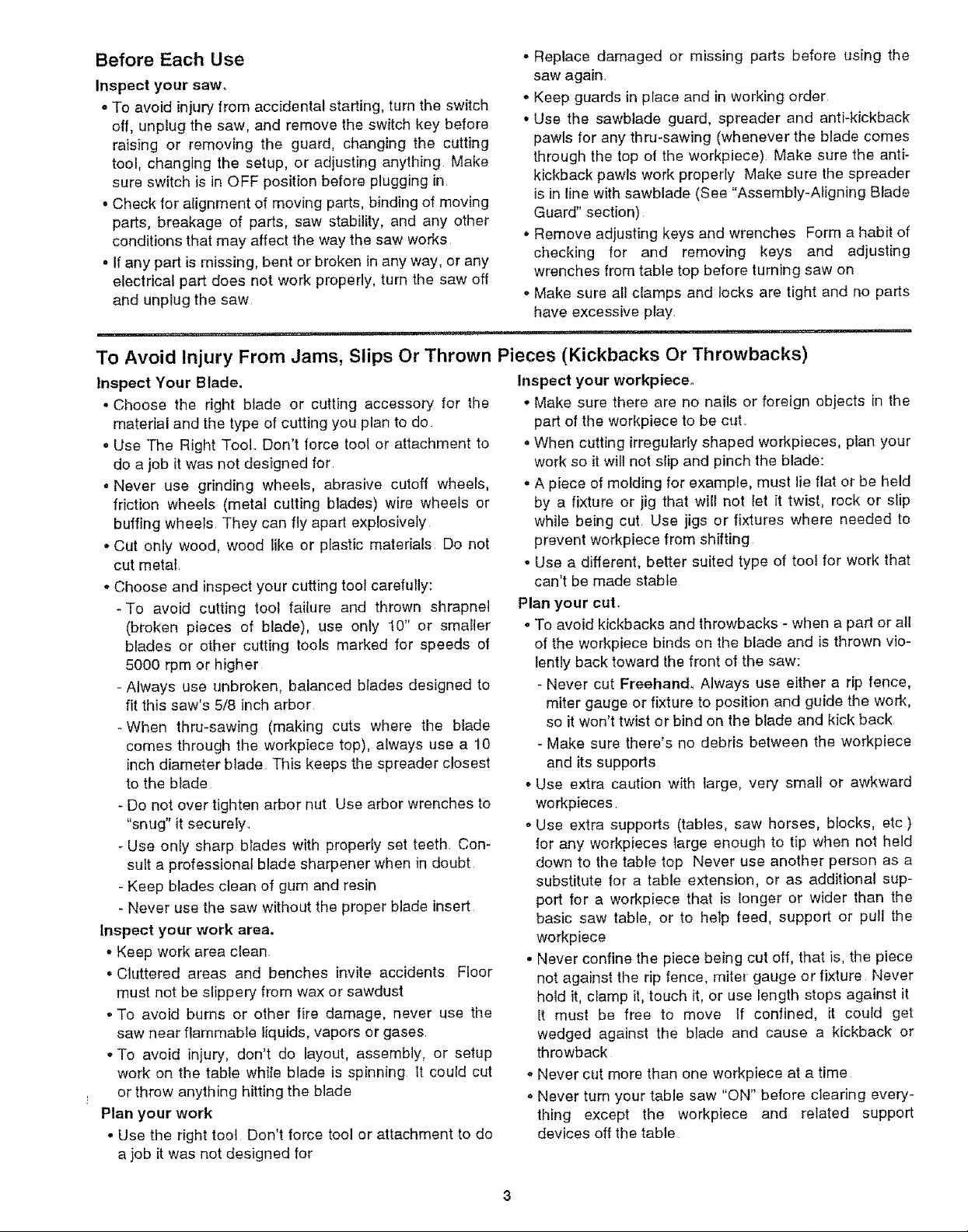
Before Each Use
Inspect your saw,
- To avoid injury from accidental starting, turn the switch
off, unplug the saw, and remove the switch key before
raising or removing the guard, changing the cutting
tool. changing the setup, or adjusting anything Make
sure switch is in OFF position before plugging in,
• Check for alignment of moving parts, binding of moving
parts, breakage of parts, saw stability, and any other
conditions that may affect the way the saw works
• If any part is missing, bent or broken in any way. or any
electrical part does not work properly, turn the saw off
and unplug the saw
° Replace damaged or missing parts before using the
saw again,
* Keep guards in place and in working order
. Use the sawblade guard, spreader and anti-kickback
pawls for any thru-sawing (whenever the blade comes
through the top of the workplace) Make sure the anti-
kickback pawls work properly Make sure the spreader
is in line with sawblade (See "Assembly-Aligning Blade
Guard" section)
° Remove adjusting keys and wrenches Form a habit of
checking for and removing keys and adjusting
wrenches from table top before turning saw on
o Make sure all clamps and locks are tight and no parts
have excessive play
To Avoid Injury From Jams, Slips Or Thrown Pieces (Kickbacks Or Throwbacks)
Inspect Your Blade. Inspect your workpieceo
• Choose the right blade or cutting accessory for the • Make sure there are no nails or foreign objects in the
material and the type of cutting you plan to do. part of the workpiece to be ctJt,
oUse The Right Tool. Don't lorce tool or attachment to . When cutting irregularly shaped workpieces, plan your
do a job it was not designed for work so it will not slip and pinch the blade:
. Never use grinding wheels, abrasive cutoff wheels, ° A piece of molding for example, must lie flat or be held
friction wheels (metal cutting blades) wire wheels or by a fixture or jig that will not let it twist, rock or slip
buffing wheels, They can fly apart explosively while being cut Use jigs or fixtures where needed to
• Cut only wood, wood like or plastic materials Do not prevent workpiece from shifting
cut metal • Use a different, better suited type of tool for work that
. Choose and inspect your cutting tool carefully: can't be made stable
-To avoid cutting tool failure and thrown shrapnel Plan your cut,
(broken pieces of blade), use only 10" or smaIler ° To avoid kickbacks and throwbacks - when a part or all
blades or other cutting tools marked for speeds of of the workpiece binds on the blade and isthrown vio-
5000 rpm or higher lently back toward the front of the saw:
- Always use unbroken, balanced blades designed to - Never cut Freehand. Always use either a rip fence,
fit this saw's 5/8 inch arbor miter gauge or fixture to position and guide the work,
- When thru-sawing (making cuts where the blade so it won't twist or bind on the blade and kick back
comes through the workpiece top), always use a 10 - Make sure there's no debris between the workpiece
inch diameter blade This keeps the spreader closest and its supports
to the blade - Use extra caution with large, very small or awkward
- Do not over tighten arbor nut Use arbor wrenches to workpieces,
"snug" it securely, o Use extra supports (tables, saw horses, blocks, etc)
- Use only sharp blades with properly set teeth. Corn for any workpieces {arge enough to tip when not held
suit a professional blade sharpener when in doubt down to the table top Never use another person as a
- Keep blades clean of gum and resin substitute for a table extension, or as additional sup-
- Never use the saw without the proper blade insert port for a workpiece that is longer or wider than the
Inspect your work area. workplace
,, Keep work area clean, • Never confine the piece being cut off, that is, the piece
. Cluttered areas and benches invite accidents Floor not against the rip fence, mitel gauge or fixture Never
must not be slippery from wax or sawdust hold it, clamp it. touch it, or use length stops against it
oTo avoid burns or other fire damage, never use the It must be free to move If confined, it could get
saw nearflammabte liquids, vapors or gases wedged against the blade and cause a kickback or
• To avoid injury, don't do layout, assembly, or setup throwback
work on the table while blade is spinning It could cut * Never cut more than one workpiece at a time
! or throw anything hitting the blade oNever tum your table saw "ON" before clearing every-
Plan yourwork thing except the workpiece and related support
• Use the right toot Don't force tool or attachment to do devices off the table
a job it was not designed for
basic saw table, or to help feed, support or pull the
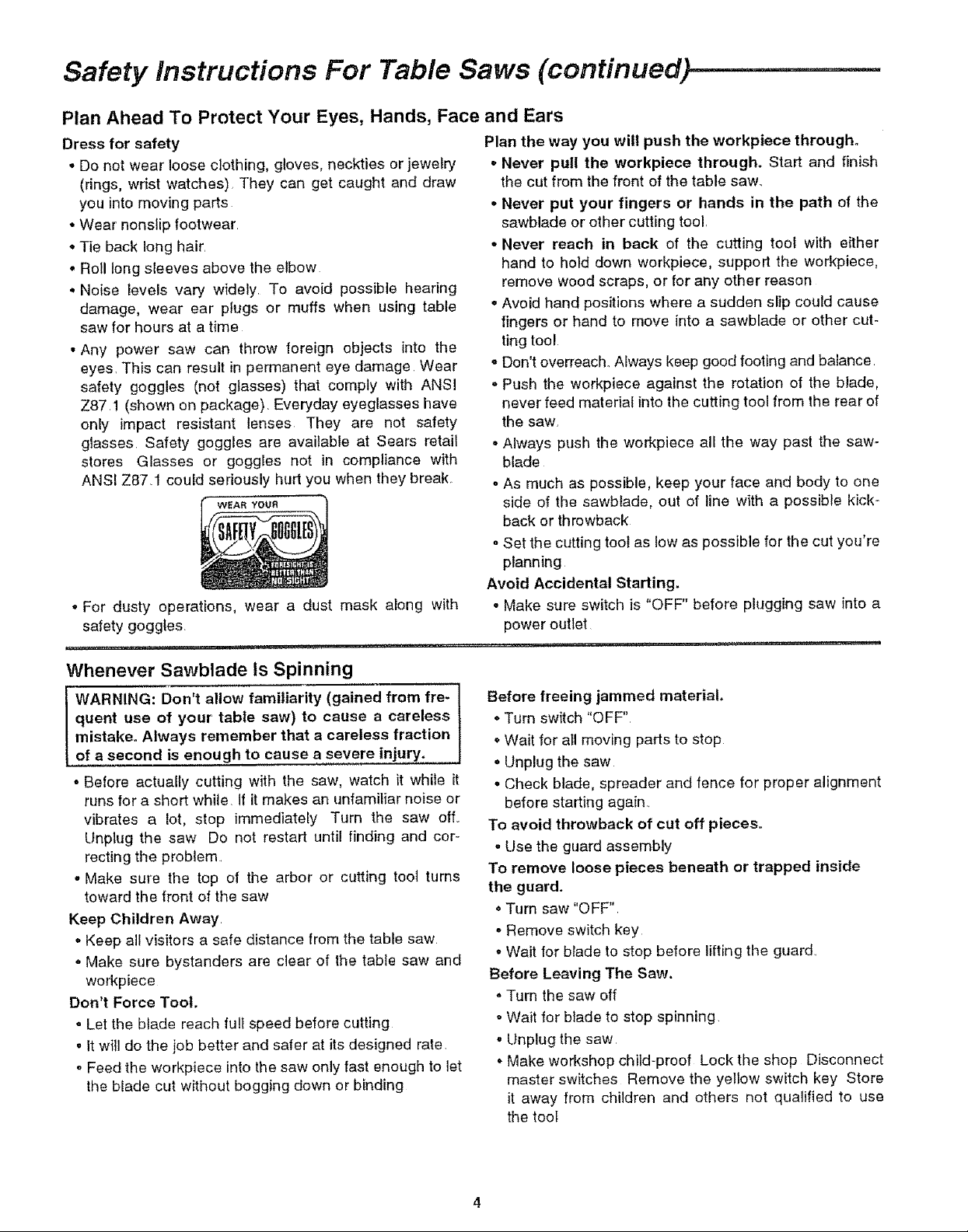
Safety Instructions For Table Saws (continued)
Plan Ahead To Protect Your Eyes, Hands, Face and Ears
Dress for safety
• Do not wear loose clothing, gloves, neckties or jewelry
(rings, wrist watches) They can get caught and draw
you into moving parts
• Wear nonslip footwear
. Tie back long hair,
• Roll long sleeves above the elbow
• Noise levels vary widely To avoid possible hearing
damage, wear ear plugs or muffs when using table
saw for hours at a time
• Any power saw can throw foreign objects into the
eyes, This can result in permanent eye damage, Wear
safety goggles (not glasses) that comply with ANSI
Z87 1 (shown on package), Everyday eyeglasses have
only impact resistant lenses They are not safety
glasses, Safety goggles are available at Sears retail
stores Glasses or goggles not in compliance with
ANSI Z87.1 could seriously hurt you when they break,
WEAR YOUR
° For dusty operations, wear a dust mask along with
safety goggles
Plan the way you will push the workpiece through°
- Never pull the workpiece through, Start and finish
the cut from the front of the table saw,,
• Never put your fingers or hands in the path of the
sawblade or other cutting tool,
° Never reach in back of the cutting tool with either
hand to hold down workpiece, support the workpiece.
remove wood scraps, or for any other reason
° Avoid hand positions where a sudden slip could cause
fingers or hand to move into a sawblade or other cut-
ting too!
• Don't overreach., Always keep good footing and balance
o Push the workpiece against the rotation of the blade,
never feed material intothe cutting tool from the rear of
the saw,
° Always push the workpiece all the way past the saw-
blade
° As much as possible, keep your face and body to one
side of the sawblade, out of line with a possible kick _
back or throwback
o Set the cutting tool as low as possible for the cut you're
planning
Avoid Accidental Starting.
- Make sure switch is "OFF" before pltJgging saw into a
power outlet
, ,,11........ H,, .... , i, ,,,1
Whenever Sawblade Is Spinning
WARNING: Don't allow familiarity (gained from fre-
quent use of your table saw) to cause a careless
mistake,. Always remember that a careless fraction
of a second is enough to cause a severe injury.
• Before actually cutting with the saw, watch it while it
runs for a short while if it makes an unfamiliar noise or
vibrates a lot, stop immediately Turn the saw off
Unplug the saw Do not restart until finding and cor-
recting the problem,
• Make sure the top of the arbor or cutting tool turns
toward the front of the saw
Keep Children Away,
o Keep all visitors a safe distance from the table saw.
o Make sure bystanders are clear of the table saw and
workpiece
Don't Force Toot.
• Let the blade reach fu!t speed before cutting
° It will do the job better and safer at its designed rate
oFeed the workpiece into the saw only fast enough to let
the blade cut without bogging down or binding
Before freeing jammed material.
o Turn switch "OFF"
l
Wait for aFImoving parts to stop
. Unplug the saw
° Check blade, spreader and fence for proper alignment
before starting again.
To avoid throwback of cut off pieces.
° Use the guard assembly
To remove loose pieces beneath or trapped inside
the guard.
oTurn saw "OFF"
° Remove switch key
- Wait for blade to stop before lifting the guard
Before Leaving The Saw.
- Turn the saw off
° Wait for blade to stop spinning
. Unplug the saw
• Make workshop child-proof Lock the shop Disconnect
master switches Remove the yellow switch key Store
it away from children and others not qualified to use
the took
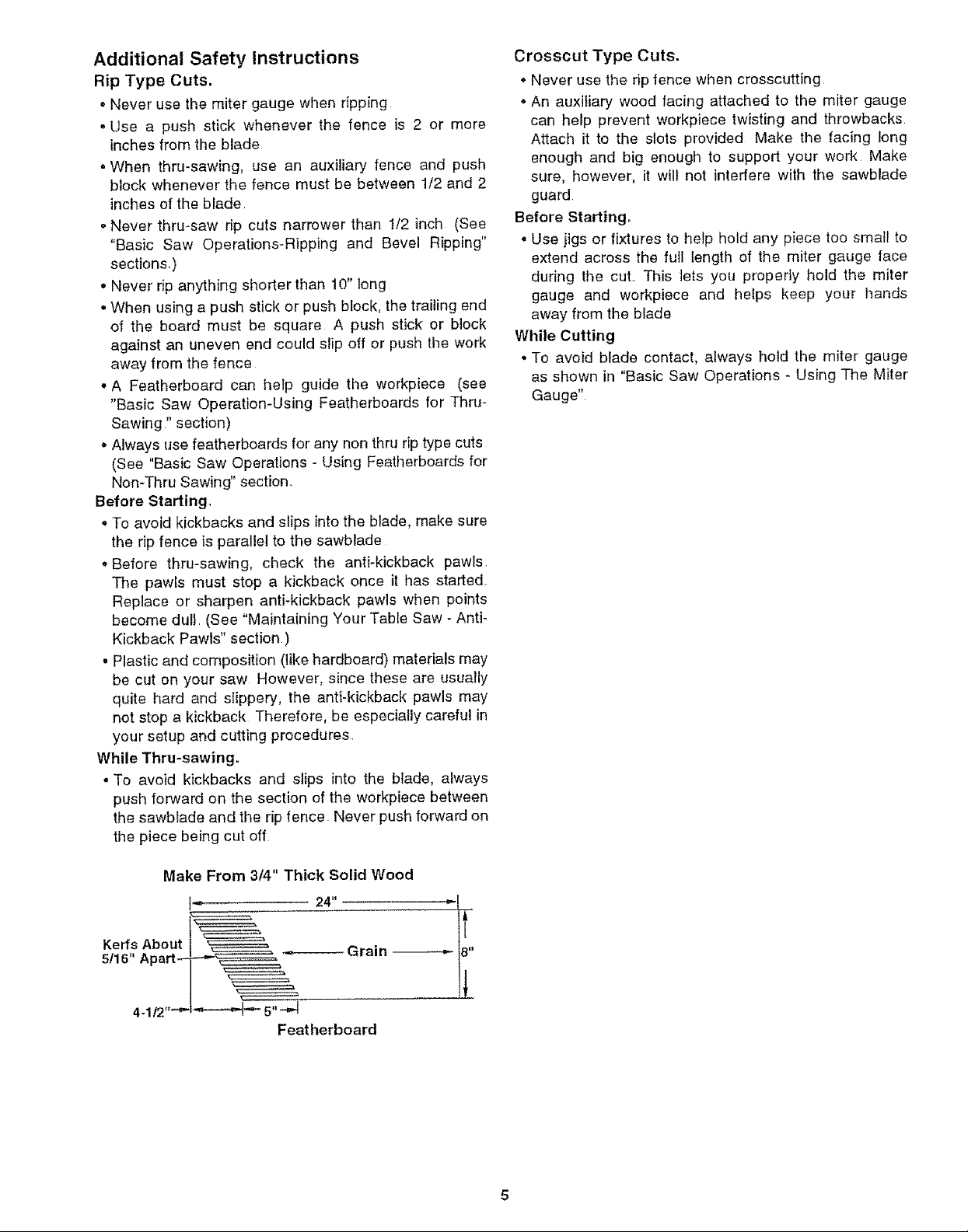
Additional Safety Instructions
Rip Type Cuts.
oNever use the miter gauge when ripping
oUse a push stick whenever the fence is 2 or more
inches from the blade
* When thru-sawing, use an auxiliary fence and push
block whenever the fence must be between 1/2 and 2
inches of the blade
oNever thru_saw rip cuts narrower than 1/2 inch (See
"Basic Saw Operations-Ripping and Bevel Ripping"
sections,)
• Never rip anything shorter than 10" long
. When using a push stick or push block, the trailing end
of the board must be square A push stick or block
against an uneven end could slip off or push the work
away from the fence
• A Featherboard can help guide the workpiece (see
"Basic Saw Operation-Using Featherboards for Thru-
Sawing" section)
oAlways use featherboards for any non thru rip type cuts
(See "Basic Saw Operations - Using Featherboards for
NomThru Sawing" section,
Before Starting,
o To avoid kickbacks and slips into the blade, make sure
the rip fence is parallel to the sawblade
oBefore thru-sawing, check the anti-kickback pawls
The pawls must stop a kickback once it has started.
Replace or sharpen antFkickback pawls when points
become dul} (See "Maintaining Your Table Saw - AntF
Kickback Pawls" section )
. Plastic and composition (like hardboard) materials may
be cut on your saw However, since these are usually
quite hard and sIippery, the anti-kickback pawls may
not stop a kickback Therefore, be especially careful in
your setup and cutting procedures,
While Thru-sawing.
• To avoid kickbacks and slips into the blade, always
push forward on the section of the workpiece between
the sawblade and the rip fence Never push forward on
the piece being cut off
Crosscut Type Cuts.
o Never use the rip fence when crosscutting
o An auxiliary wood facing attached to the miter gauge
can help prevent workpiece twisting and throwbacks
Attach it to the slots provided Make the facing long
enough and big enough to support your work Make
sure, however, it wilt not interfere with the sawblade
guard
Before Starting.
* Use jigs or fixtures to help hold any piece too small to
extend across the full length of the miter gauge face
during the cut. This lets you properly hold the miter
gauge and workpiece and helps keep your hands
away from the blade
While Cutting
° To avoid blade contact, always hold the miter gauge
as shown in "Basic Saw Operations - Using The Miter
Gauge"
Kerfs About
5116" Apart_
4.1/2,,-_-
Make From 3/4" Thick Solid Wood
24" _'i
it
Grain ----_
Featherboard
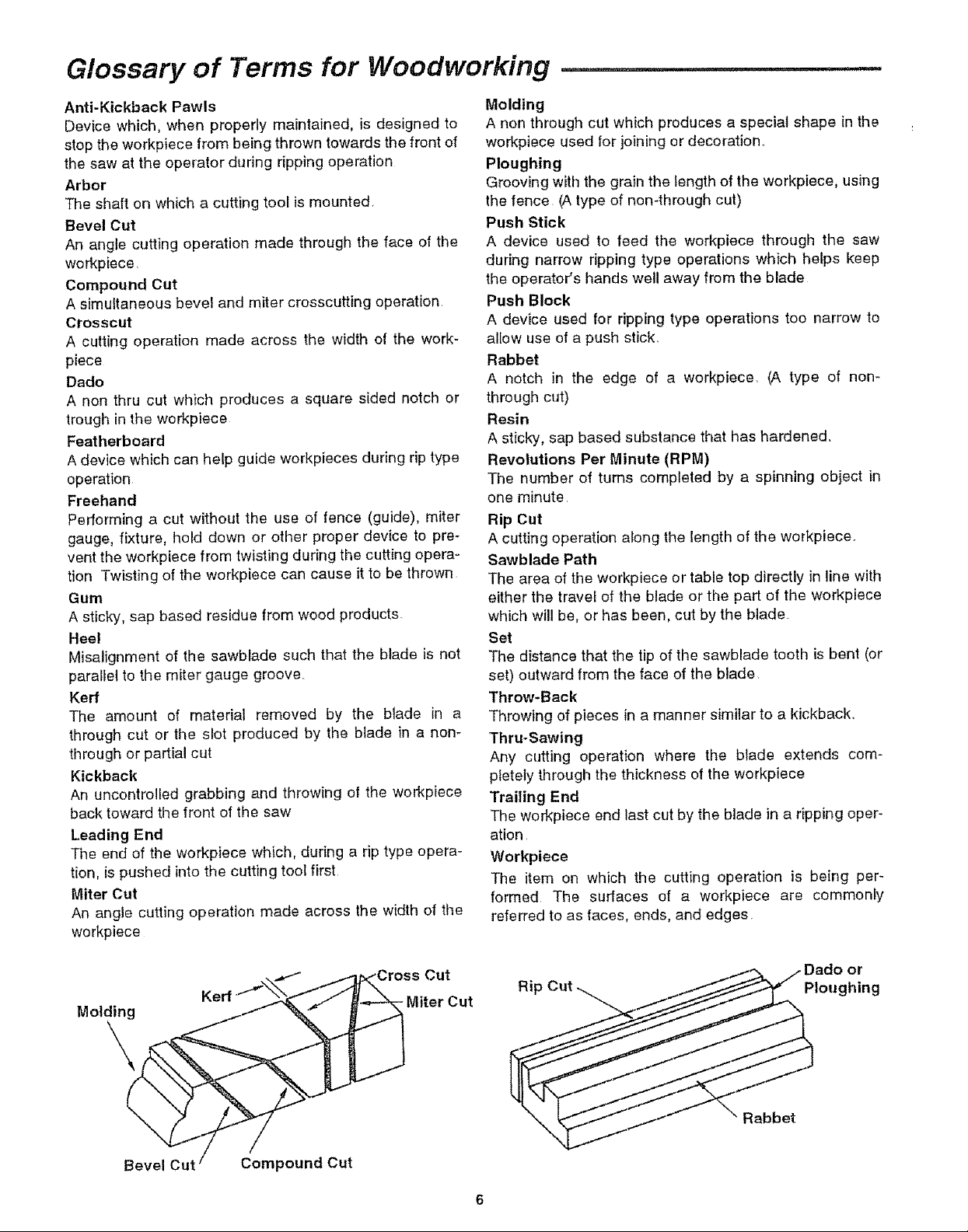
Glossary of Terms for Woodworking
Anti-Kickback Pawls
Device which, when properly maintained, is designed to
stop the workpiece from being thrown towards the front of
the saw at the operator during ripping operation
Arbor
The shaft on which a cutting tool is mounted
Bevel Cut
An angle cutting operation made through the face of the
workpiece,
Compound Cut
A simultaneous bevel and miter crosscutting operation
Crosscut
A cutting operation made across the width of the work-
piece
Dado
A non thru cut which produces a square sided notch or
trough in the workpiece
Featherboard
A device which can help guide workpieces during rip type
operation
Freehand
Performing a cut without the use of fence (guide), miter
gauge, fixture, hold down or other proper device to pre-
vent the workpiece from twisting during the cutting opera-
tion Twisting of the workpiece can cause it to be thrown
Gum
A sticky, sap based residue from wood products,
Heel
Misalignment of the sawblade such that the blade is not
parallel to the miter gauge groove,
Kerr
The amount of material removed by the blade in a
through cut or the slot produced by the blade in a non-
through or partial cut
Kickback
An uncontrolled grabbing and throwing of the workpiece
back toward the front of the saw
Leading End
The end of the workpiece which, during a rip type opera-
tion, is pushed into the cutting tool first
Miter Cut
An angle cutting operation made across the width of the
workpiece
Molding
A non through cut which produces a special shape in the
workpiece used for joining or decoration,,
Ploughing
Grooving with the grain the length of the workpiece, using
the fence (A type of non-through cut)
Push Stick
A device used to feed the workpiece through the saw
during narrow ripping type operations which helps keep
the operator's hands well away from the blade
Push Block
A device used for ripping type operations too narrow to
allow use of a push stick,
Rabbet
A notch in the edge of a workpiece, (A type of non-
through cut)
Resin
A sticky, sap based substance that has hardened,
Revolutions Per Minute (RPM)
The number of turns completed by a spinning object in
one minute
Rip Cut
A cutting operation along the length of the workpiece.
Sawblade Path
The area of the workpiece or table top directly in line with
either the travel of the blade or the part of the workpiece
which will be, or has been, cut by the blade.
Set
The distance that the tip of the sawblade tooth is bent (or
set) outward from the face of the blade,
Throw-Back
Throwing of pieces in a manner similar to a kickback,
Thru-Sawing
Any cutting operation where the blade extends com-
pletely through the thickness of the workpiece
Trailing End
The workpiece end last cut by the blade in a ripping oper-
ation
Workpiece
The item on which the cutting operation is being per-
formed The surfaces of a workpiece are commonly
referred to as faces, ends, and edges
Molding
\
Bevel Cut Compound Cut
Cut
)ado or
Ri Ploughing
Cut
Rabbet

Motor Specifications and Electrical Requirements 1
_ower Supply and Motor Specifications
WARNING: To avoid electrical hazards, fire haz-
ards or damage to the tool, use proper circuit pro-
tection. Your tool is wired at the factory for
operation using the voltage shown. Connect toot
to a power line with the appropriate voltage and a
15-amp branch circuit. Use a 15-amp time delay
type fuse or circuit breaker. To avoid shock or fire,
if power cord is worn or cut, or damaged in any
way, have it replaced immediately.
i ,,u ..............
General Electrical Connections
DANGER: To avoid electrocution:
1. Use only identical replacement parts when ser-
vicing, Servicing should be performed by a
qualified service technician.
2, Do not use in rain or where floor is wet.
This tool is intended for indoor residential use
.........only.
The A-C motor used inthis tool is a relay start, non-revers-
ible type, having the following specifications:
Rated HP 1
Voltage 110-120
Amperes 1t 5
Hertz (Cycles) 60
Phase Single
RPM 3450
Rotation of Shaft Counterclockwise
7
WARNING: Do not permit fingers to touch the ter- |
minals of plug when installing or removing the
plug to or from the outlet.
110-120 Volt, 60 Hz. Tool Information
NOTE: The plug supplied on your toof may not fit into the
outtet you are planning to use Your local electrical code
may require slightly different power cord plug connec-
tions if these differences exist refer to and make the
proper adjustments per your local code before your tool
isplugged in and turned on
In the event of a malfunction or breakdown, grounding
provides a path of least resistance for electric current to
reduce the risk of electric shock This toot is equipped
with an electric cord having an equipment-grounding con-
ductor and a grounding plug, as shown,, The plug must
be plugged into a matching outlet that is properly
installed and grounded in accordance with all local codes
and ordinances
Do not modify the plug provided, If it will not fit the outlet,
have the proper outlet installed by a qualified electrician
A temporary adapter may be used to connect this plug to
a 2-prong outlet as shown if a properly grounded three
prong outlet is not available,. This temporary adapter
should be used only until a properly grounded three
prong outlet can be installed by a qualified electrician
The green colored rigid ear', lug or the like, extending
from the adapter must be connected to a permanent
ground such as a properly grounded outfet box
Improper connection of the equipment-grounding con-
ductor can result in a risk of electric shock The conduc-
tor with insulation having an outer surface that is green
with or without yellow stripes is the equipment-grounding
conductor If repair or replacement of the electric cord or
plug is necessary, do not connect the equipment-ground-
ing conductor to a live terminal
If the grounding instructions are not completely under-
stood, or if you are in doubt as to whether the tool is prop-
erly grounded check with a qualified electrician or service
)ersonnel.
WARNING: If not properly grounded, this tool can
cause an electrical shock, particularly when used
in damp locations, in proximity to plumbing, or out
of doors_ If an electrical shock occurs there is the
potential of a secondary hazard, such as your
hands contacting the sawblade.
Properly
3-Prong Plug
Grounded
3-Prong Outlet
\ J
In 111
G!ounding
Prong
Make sure this
Grounding Lug _
Is Connected
to a Known
Ground
2-Prong
Outlet
NOTE: The adapter illustrated is for use only if you
already have a properly grounded 2-prong outlet
7
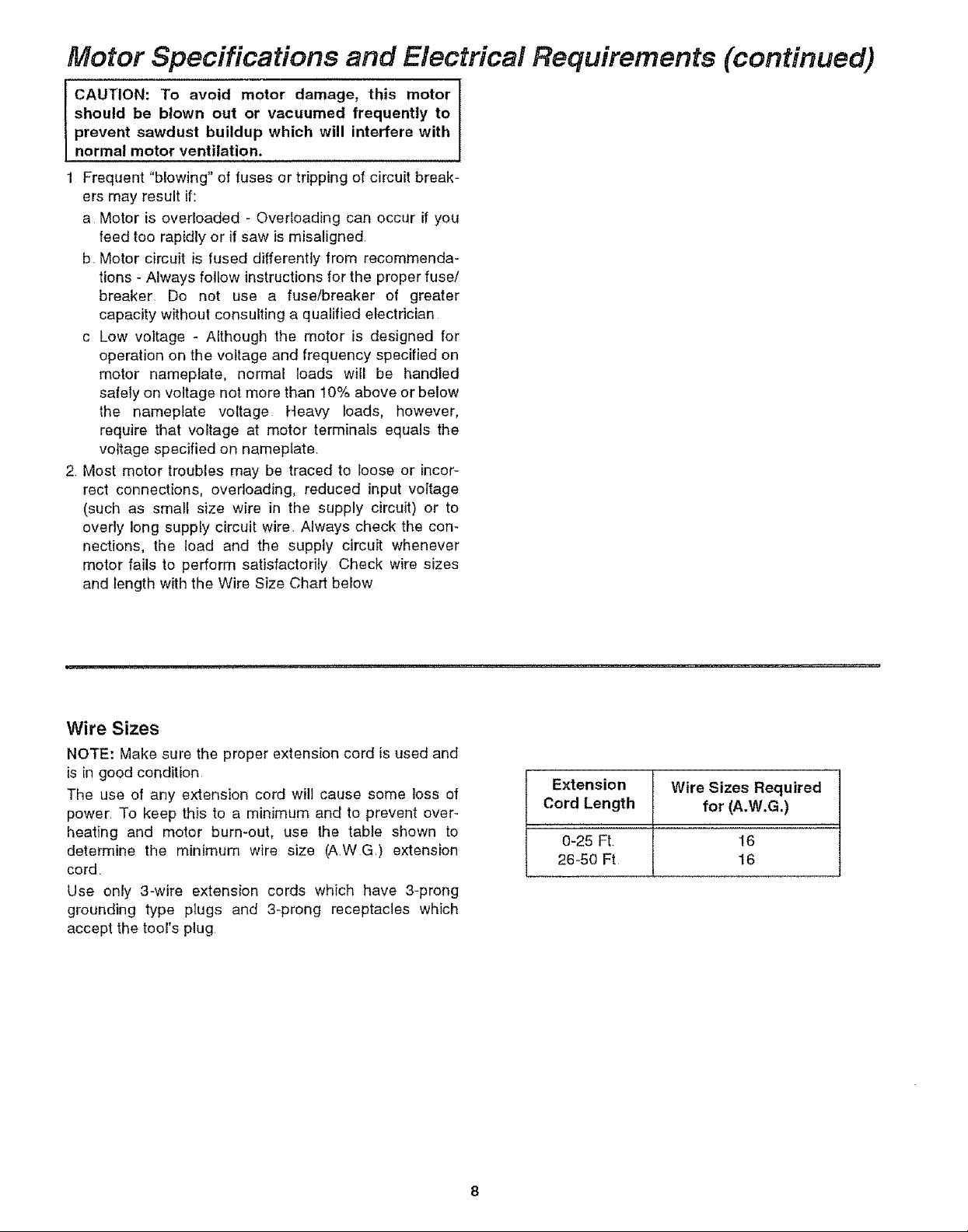
Motor Specifications and Electrical Requirements (continued)
CAUTION: To avoid motor damage, this motor
should be blown out or vacuumed frequently to
prevent sawdust buildup which will interfere with
normal motor ventilation,
1 Frequent "blowing" of fuses or tripping of circuit break-
ers may result if:
a Motor is overloaded - Overloading can occur if you
feed too rapidly or if saw is misaligned
b, Motor circuit is fused differently from recommenda-
tions - Always follow instructionsfor the proper fuse/
breaker Do not use a fuse/breaker of greater
capacity without consulting a qualified electrician
c Low voltage - Although the motor is designed for
operation on the voltage and frequency specified on
motor nameplate, normal loads will be handled
safely on voltage not more than 10% above or below
the nameplate voltage Heavy loads, however,
require that voltage at motor terminals equals the
voltage specified on nameplate,
2. Most motor troubles may be traced to loose or incor-
rect connections, overloading, reduced input voltage
(such as small size wire in the supply circuit) or to
overly long supply circuit wire, Always check the con-
nections, the load and the supply circuit whenever
motor fails to perform satisfactorily Check wire sizes
and length with the Wire Size Chart below
Wire Sizes
NOTE: Make sure the proper extension cord is used and
is in good condition
The use of any extension cord will cause some loss o!
power To keep this to a minimum and to prevent over-
heating and motor burn-out, use the table shown to
determine the minimum wire size (AWG,) extension
cord
Use only 3-wire extension cords which have 3-prong
grounding type plugs and 3-prong receptacles which
accept the tool's plug
Extension
Cord Length
0-25 Ft,
26-50 Ft
Wire Sizes Required
for (A.W.G.)
16
16
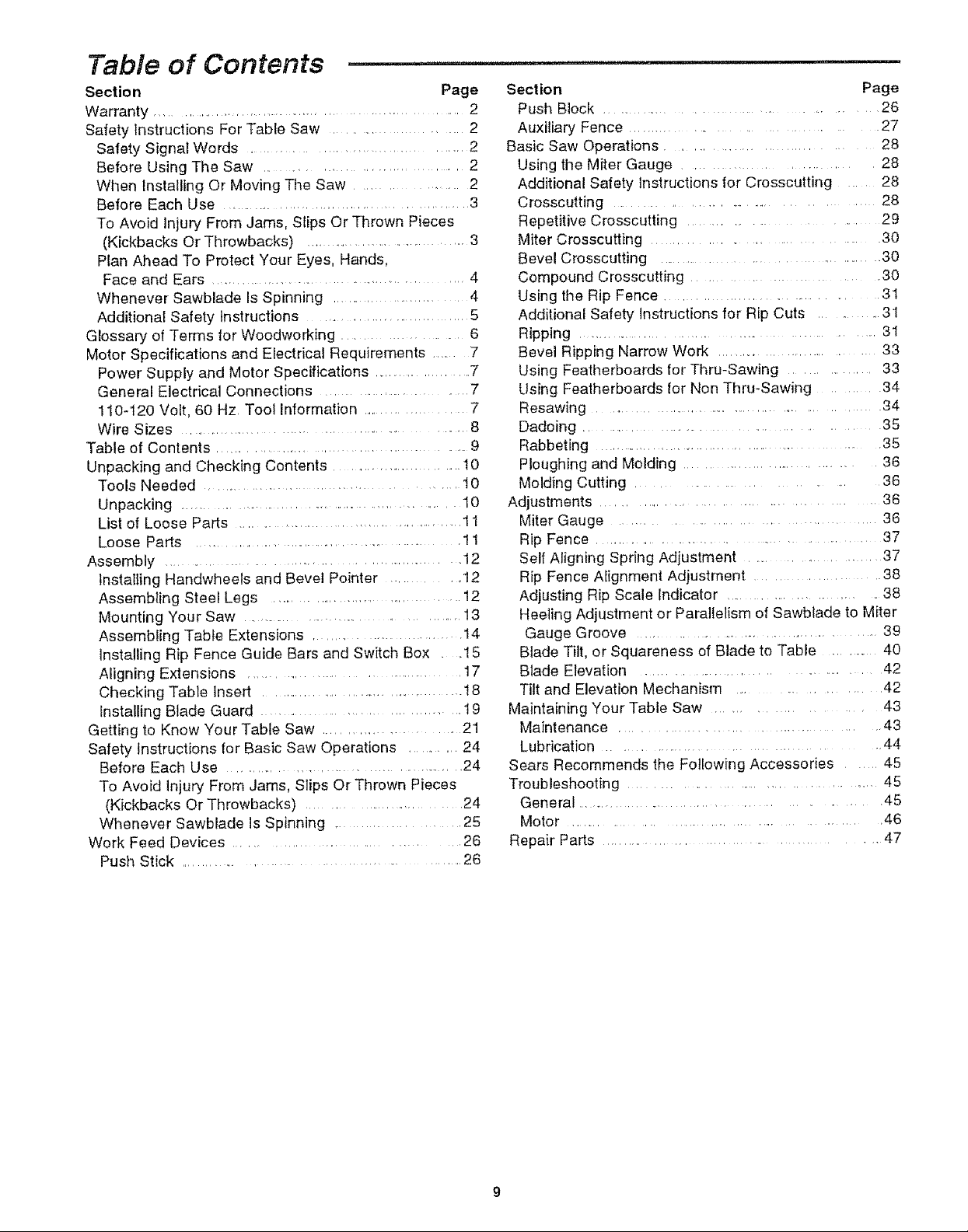
Table of Contents .......
Section Page
Warranty ................................................................................ 2
Safety Instructions For Table Saw .................... 2
Safety Signal Words ............................................... 2
Before Using The Saw ........................... 2
When Installing Or Moving The Saw ...................... 2
Before Each Use .......................................... 3
To Avoid Injury From Jams, Slips Or Thrown Pieces
(Kickbacks Or Throwbacks) .................................. 3
Plan Ahead To Protect Your Eyes, Hands,
Face and Ears ............................................................... 4
Whenever Sawblade Is Spinning .......................... 4
Additional Safety Instructions .......................... 5
Glossary of Terms for Woodworking ............................ 6
Motor Specifications and Electrical Requirements ......... 7
Power Supply and Motor Specifications ..................... 7
General Electrical Connections ................................... 7
110-f20 Volt, 60 Hz Tool Information ......................... 7
Wire Sizes .................................................................... 8
Table of Contents ............................................................ 9
Unpacking and Checking Contents ...................... 10
Tools Needed ................................... 10
Unpacking ................................................. 10
List of Loose Parts .......................................... 11
Loose Paris ........................................... 11
Assembly .............................................. 12
Installing Handwheels and Bevel Pointer ............... 12
Assembling Steel Legs .............................. 12
Mounting Your Saw ....................................... 13
Assembling Table Extensions .................................... 14
Installing Rip Fence Guide Bars and Switch Box , ,15
Aligning Extensions ................................................ 17
Checking Table Insert ........................................... 18
Installing Blade Guard ................................ 19
Getting to Know Your Table Saw ................................. 21
Safety Instructions for Basic Saw Operations ............ 24
Before Each Use ....................................... 24
To Avoid Injury From Jams, Slips Or Thrown Pieces
(Kickbacks Or Throwbacks) .................................. 24
Whenever Sawblade Is Spinning ............................ 25
Work Feed Devices ............................... 26
Push Stick ................................................................. 26
Section Page
Push Block ................................. 26
Auxiliary Fence .............................................. 27
Basic Saw Operations ........................ 28
Using the Miter Gauge ..................... 28
Additional Safety Instructions for Crosscutting ........ 28
Crosscutting ................................................... 28
Repetitive Crosscutting ................................... 29
Miter Crosscutting ............................ 30
Bevel Crosscutting ................................................... 30
Compound Crosscutting ...................................... 30
Using the Rip Fence .......................................... 31
Addilionai Safety Instructions for Rip Cuts ............. 31
Ripping .............................................. 31
Bevel Ripping Narrow Work .......................... 33
Using Featherboards for Thru-Sawing ............ 33
Using Featherboards for Non Thru-Sawing ....... 34
Resawing .................................................................. 34
Dadoing .................................... 35
Rabbeting ........................................... 35
Ploughing and Molding ............................ 36
Molding Cutting ..................................... 36
Adjustments .................................................... 36
Miter Gauge ..................................................... 36
Rip Fence ...................................... 37
Self Aligning Spring Adjustment .............................. 37
Rip Fence Alignment Adjustment .............. 38
Adjusting Rip Scale Indicator ...................... 38
Heeling Adjustment or Parallelism of Sawblade to Miter
Gauge Groove ............................... 39
Blade Tilt, or Squareness of Blade to Table ........ 40
Blade Elevation .................................. 42
Tilt and Elevation Mechanism ........................... 42
Maintaining Your Table Saw ........................... 43
Maintenance ................................... 43
Lubrication ...................................................... 44
Sears Recommends the Following Accessories ...... 45
Troubleshooting ........................................ 45
General ........................................ 45
Motor ................................................................. 46
Repair Parts ........................................ 47
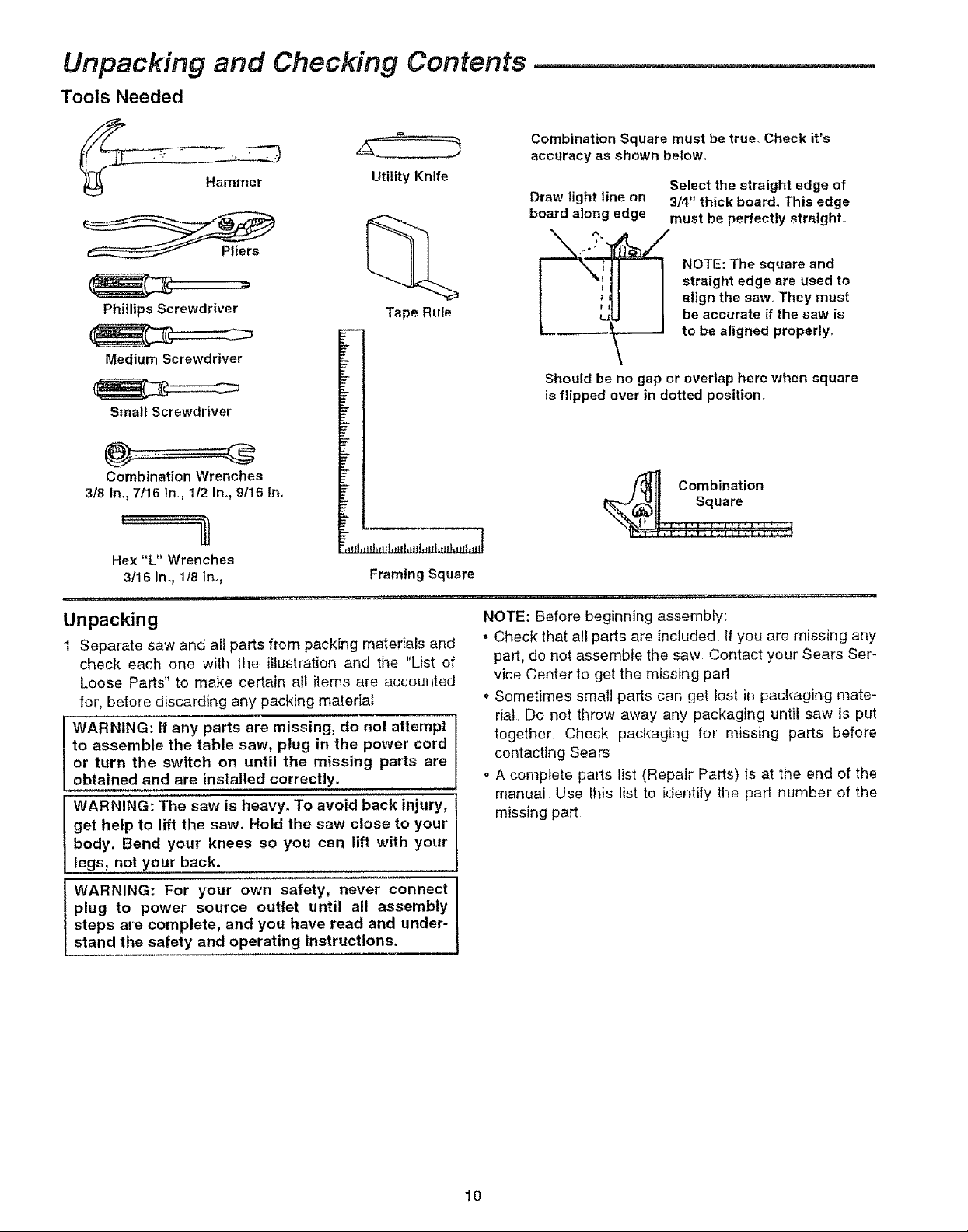
Unpacking and Checking Contents
Tools Needed
Utility Knife
Combination Square must be true. Check it's
accuracy as shown below.
Draw light line on
board along edge
Select the straight edge of
314" thick board. This edge
must be perfectly straight.
Phillips Screwdriver
Tape Rule
Medium Screwdriver
Small Screwdriver
Combination Wrenches
3!8 ino,7116 In,, 112 Ino,9/16 In.
Hex "L" Wrenches
3/16 In., 1/8 In,
Framing Square
Unpacking
1 Separate saw and all parts from packing materials and
check each one with the illustration and the "List of
Loose Parts" to make certain all items are accounted
for, before discarding any packing material
WARNING: If any parts are missing, do not attempt
to assemble the table saw, plug in the power cord
or turn the switch on until the missing parts are
obtained and are installed correctly.
WARNING: The saw is heavy° To avoid back injury,
get help to lift the saw. Hold the saw close to your
body. Bend your knees so you can lift with your
legs, not your back.
I i
LI
\
straight edge are used to
align the saw, They must
NOTE: The square and
be accurate if the saw is
to be aligned properly,
Should be no gap or overlap here when square
isflipped over in dotted position,
_., Combination
Square
,_',- ',i '.;: :'._ '.I_,t
NOTE: Before beginning assembly:
o Check that all parts are included If you are missing any
part, do not assemble the saw Contact your Sears Ser-
vice Center to get the missing part
o Sometimes small parts can get lost in packaging mate*
riat Do not throw away any packaging until saw is put
together Check packaging for missing parts before
contacting Sears
o A complete parts list (Repair Parts) is at the end of the
manual Use this list to identify the part number of the
missing part
WARNING: For your own safety, never connect
plug to power source outlet until all assembly
steps are complete, and you have read and under-
stand the safety and operating instructions.
10
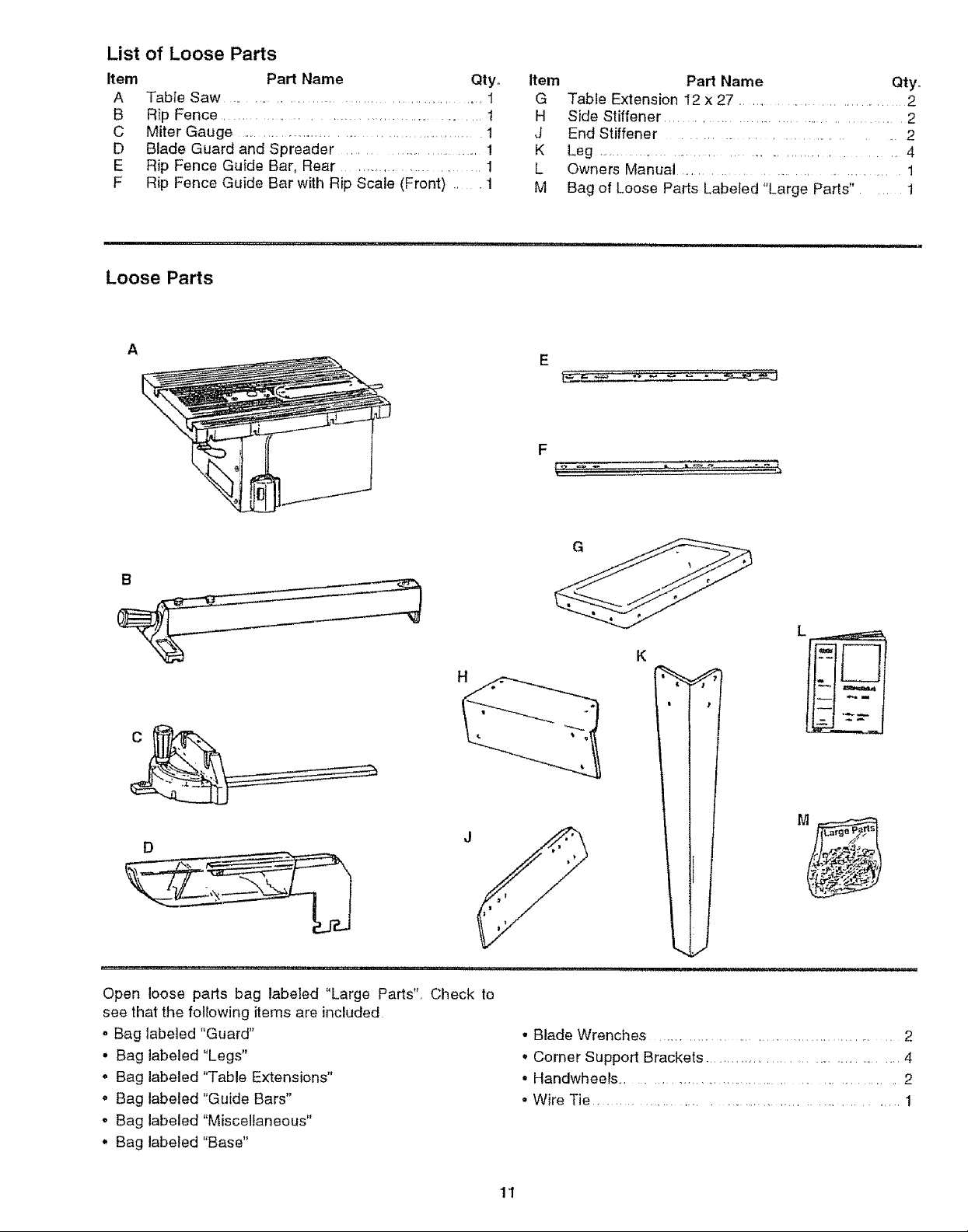
of Loose PartsList
Item Part Name Qtyo
A Tabte Saw ............................................................ 1
B Rip Fence .......................................... t
C Miter Gauge ................................................. 1
D Blade Guard and Spreader ................................. !
E Rip Fence Guide Bar, Rear .................. 1
F Rip Fence Guide Bar with Rip Scale (Front) ,1
Loose Parts
A
Item Part Name Qtyo
G Table Extension 12 x 27 ......................... 2
H Side Stiffener ...................................... 2
J End Stiffener ......................... 2
K Leg ............................................ 4
L Owners Manual ................................................ 1
M Bag of Loose Parts Labeled "Large Pads" ...... 1
E
F
_, _- . ,,_,,_o "_:__
B
C
Open loose parts bag labeled "Large Pads", Check to
see that the following items are included
o Bag labeled "Guard"
• Bag labeled "Legs"
o Bag labeled "Table Extensions"
o Bag labeled "Guide Bars"
• Bag labeled "Miscellaneous"
• Bag labeled "Base"
K
• Blade Wrenches ...................................... 2
• Corner Supped Brackets ......................................... 4
° Handwheels ..................................................................... 2
• Wire Tie ..................................................... 1
11
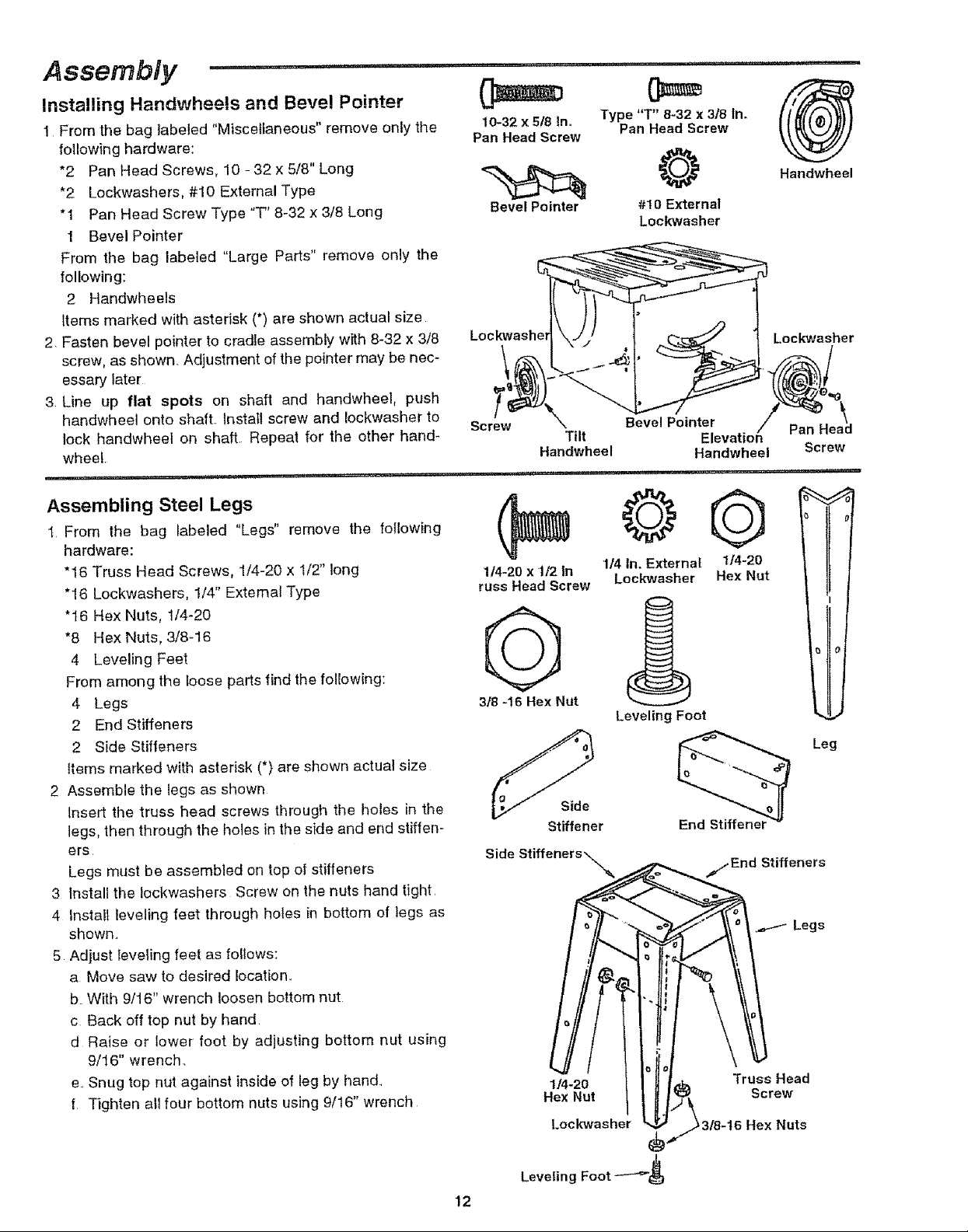
Assembly ................. '"
........ i,,i
= ..... PH.....,.H..,=...... =
Installing Handwheels and Bevel Pointer
1 From the bag labeled "Miscellaneous" remove only the
following hardware:
*2 Pan Head Screws, 10 - 32 x 5/8" Long
*2 Lockwashers, #10 External Type
"1 Par} Head Screw Type "T" 8-32 x 3/8 Long
1 Bevel Pointer
From the bag labeled "Large Parts" remove only the
following:
2 Handwheels
Items marked with asterisk (*) are shown actual size
2, Fasten bevel pointer to cradle assembly with 8-32 x 3/8
screw, as shown. Adjustment of the pointer may be nec-
essary later
3 Line up flat spots on shaft and handwheel, push
handwheel onto shaft.. Install screw and !ockwasher to
lock handwheel on shaft. Repeat for the other hand-
wheel
Assembling Steel Legs
t From the bag labeled "Legs" remove the following
hardware:
"16 Truss Head Screws, 1/4-20 x 1/Z' long
"16 Lockwashers, 1/4" External Type
"I6 Hex Nuts, 1/4-20
*8 Hex Nuts, 3/8-16
4 Leveling Feet
From among the loose parts find the following:
4 Legs
2 End Stiffeners
2 Side Stiffeners
items marked w{th asterisk (*) are shown actual size
2 Assemble the legs as shown
insert the truss head screws through the holes in the
legs, then through the holes in the side and end stiffen-
ers
Legs must be assembled on top of stiffeners
3 Install the Iockwashers Screw on the nuts hand tight.
4 Instal! leveling feet through hotes in bottom of legs as
shown.
5 Adjust teveling feet as follows:
a Move saw to desired location..
b. With 9/16" wrench loosen bottom nut
c Back off top nut by"hand
d Raise or lower foot by adjusting bottom nut using
9/16" wrench..
e..Snug top nut against inside of leg by hand..
f Tighten all four bottom nuts using 9/16" wrench
10-32 x 5/8 In.
Pan Head Screw
Bevel Pointer
Screw
1/4-20 x 112In
russ Head Screw
Tilt
Handwheel
Q
3/8-16 Hex Nut
Stiffener
Side Stiffeners'_
1/4-20
Hex Nut
Lockwasher
Type "T" 8-32 x 3/8 In.
Pan Head Screw
O Handwheel
#10 External
Lockwasher
Lockwasher
Bevel Pointer / Pan Head
Elevation
Handwheel Screw
0©
1/4 In. External 1/4-20
Lockwasher Hex Nut
Leveling Foot
.,,j End Stiffeners
Truss Head
Screw
Hex Nuts
Leg
12
Leveling Foot ----_
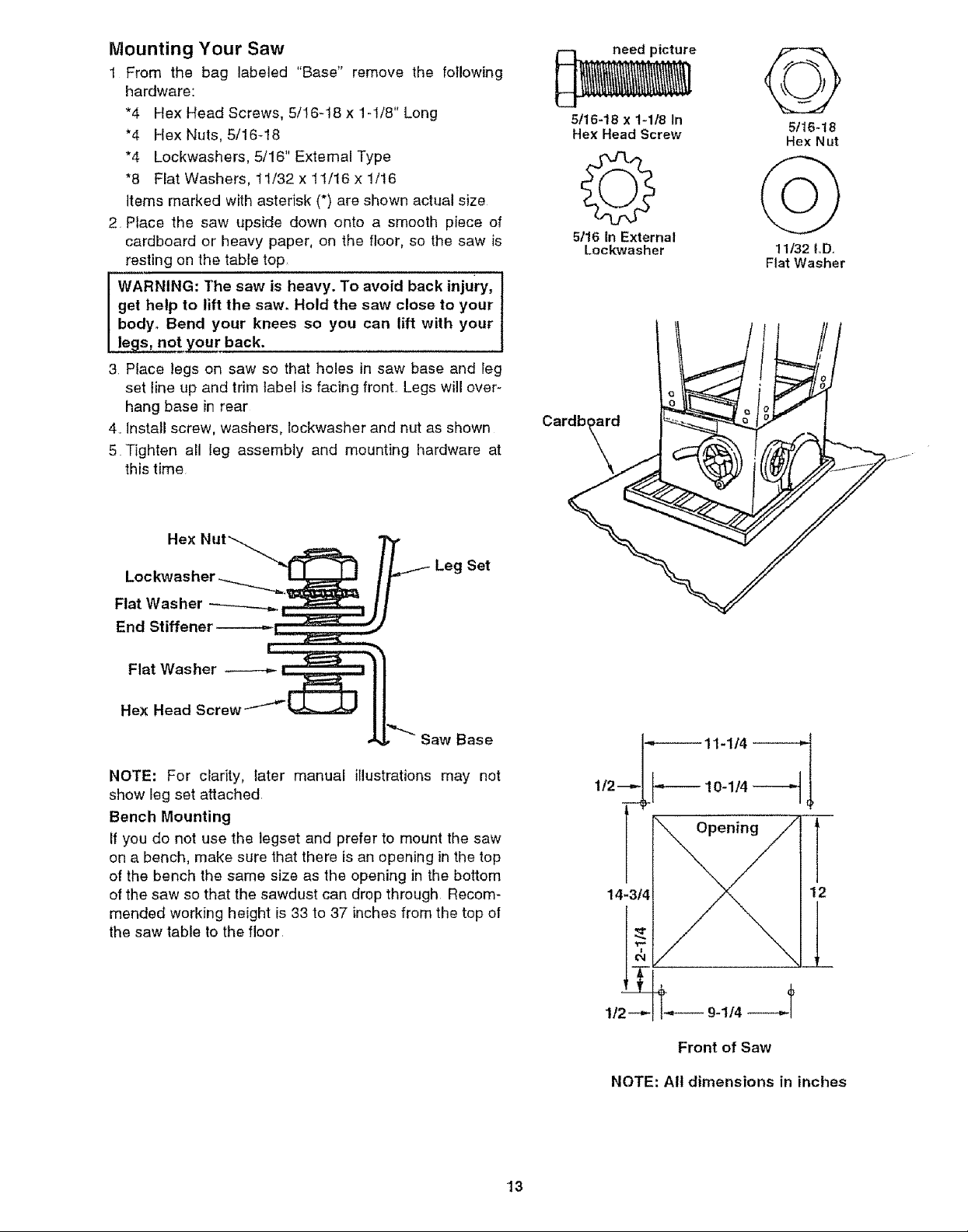
Mounting Your Saw
1 From the bag labeled "Base" remove the following
hardware:
*4 Hex Head Screws, 5/16-18 x 1-I/8" Long
*4 Hex Nuts, 5/16-18
*4 Lockwashers, 5/16" External Type
*8 Fiat Washers, tl/32 x 11/16 x 1/16
items marked with asterisk (*) are shown actual size
2 Place the saw upside down onto a smooth piece of
cardboard or heavy paper, on the floor, so the saw is
resting on the table top
WARNING: The saw is heavy. To avoid back injury,
get help to lift the saw. Hold the saw close to your
body. Bend your knees so you can lift with your
3. Place legs on saw so that holes in saw base and leg
set line up and trim label is facing front. Legs will over-
hang base in rear
4. Install screw, washers, lockwasher and nut as shown
5 Tighten all leg assembly and mounting hardware at
this time
5t16-18 x 1-1/8 In 5/16-18
Hex Head Screw Hex Nut
5/16 In External
Lockwasher 11/32 LD.
Flat Washer
Cardb,
Hex
Leg Set
Flat Washer
End Stiffener
Flat Washer
Hex Head Screw
Saw Base
NOTE: For clarity, later manual illustrations may not
show leg set attached
Bench Mounting
If you do net use the legset and prefer to mount the saw
on a bench, make sure that there is an opening in the top
of the bench the same size as the opening in the bottom
of the saw so that the sawdust can drop through Recom-
mended working height is 33 to 37 inches from the top of
the saw table to the floor
14-3/4
12
13
1/2--,-- _l
Front of Saw
NOTE: All dimensions in inches
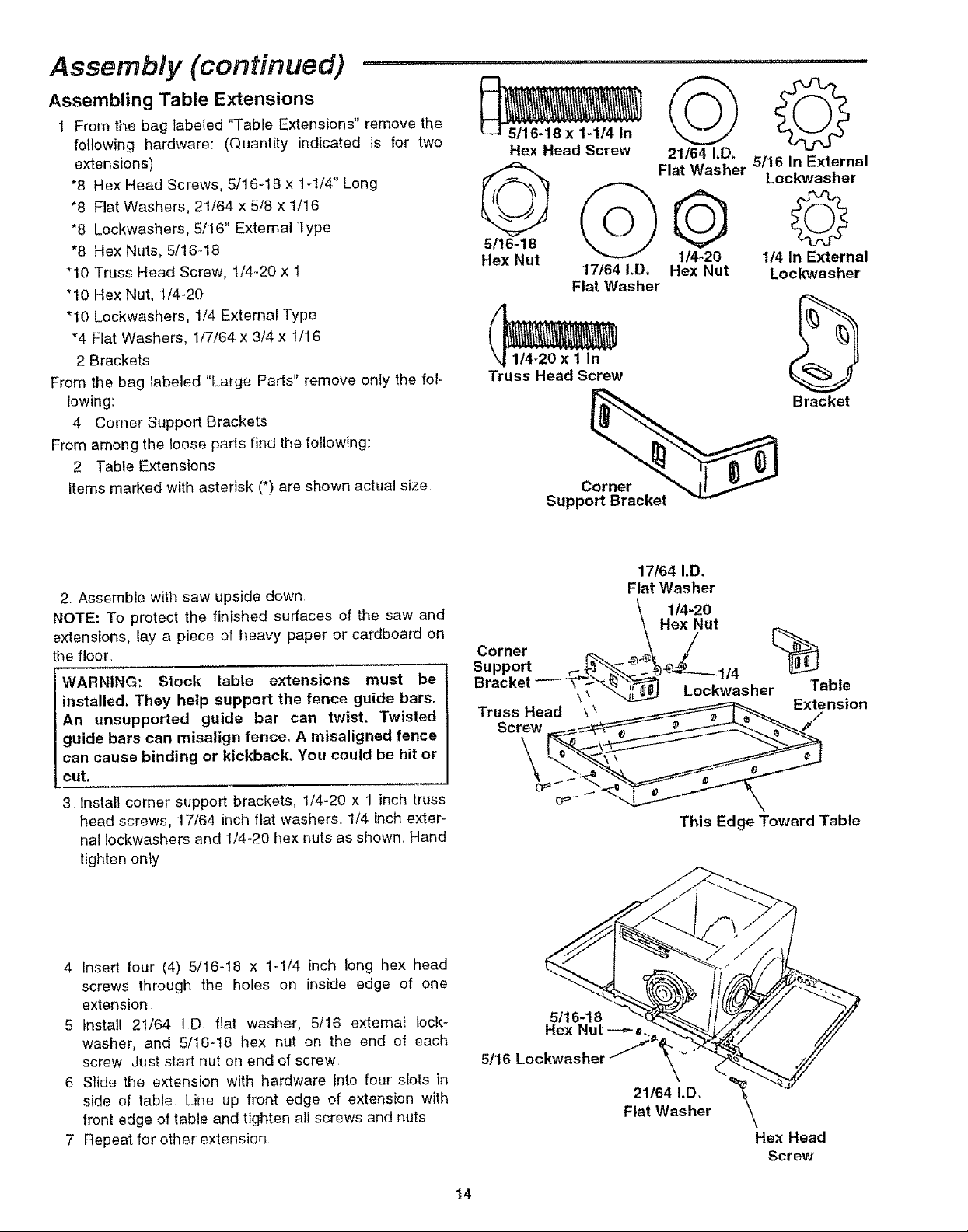
Assembly (continued)
Assembling Table Extensions
1 From the bag labeled "Table Extensions" remove the
following hardware: (Quantity indicated is for two
extensions)
*8 Hex Head Screws, 5/16-18 x 1-1/4" Long
*8 Flat Washers, 21/64 x 5/8 x 1/16
*8 Lockwashers. 5/16" External Type
*8 Hex Nuts, 5/16-18
"10 Truss Head Screw, 1/4-20 x 1
"10 Hex Nut, 1/4-20
"10 Lockwashers, 1/4 External Type
*4 Flat Washers, 1/7/64 x 3/4 x 1/16
2 Brackets
From the bag labeled "Large Parts" remove only the fol-
lowing:
4 Comer Support Brackets
From among the loose parts find the following:
2 Table Extensions
items marked with asterisk (*) are shown actual size
Hex Head Screw
0
5/16-18
Hex Nut
Truss Head Screw
@Q
17/64 I,D. Hex Nut
Flat Washer
s°ppc
.... i ................. ,,,
21_41,D.
Flat Washer
O
5/16 In External
Lockwasher
©
114 In External
Lock'washer
Bracket
2 Assemble with saw upside down
NOTE: To protect the finished surfaces of the saw and
extensions, lay a piece of heavy paper or cardboard on
the floor..
WARNING: Stock table extensions must be
installed. They help support the fence guide bars.
An unsupported guide bar can twist. Twisted
guide bars can misalign fence. A misaligned fence
can cause binding or kickback. You could be hit or
cut,
3 Install corner support brackets, 1/4-20 x 1 inch truss
head screws, 17/64 inch flat washers, 1/4 inchexter-
nal Iockwashers and 1/4-20 hex nuts as shown, Hand
tighten onty
4 insert four (4) 5/16-18 x 1-1/4 inch long hex head
screws through the holes on inside edge of one
extension
5 Instal! 21/64 ID fiat washer, 5/16 external lock-
washer, and 5/16-t8 hex nut on the end of each
screw Just start nut on end of screw
6 Slide the extension with hardware into four slots in
side of table Line up front edge of extension with
front edge of table and tighten all screws and nuts
7 Repeat for other extension
17/64 I.D.
Flat Washer
\ 1/4-20
\ Hex Nut
Corner _._\ / (_
support
Bracket ----__ Lockwasher Table
51'16Lock'washer
k' _'-4z.z_
This Edge Toward Table
5/16-18
Hex Nut _
21/64 I.D.
Flat Washer
Hex Head
Screw
t4
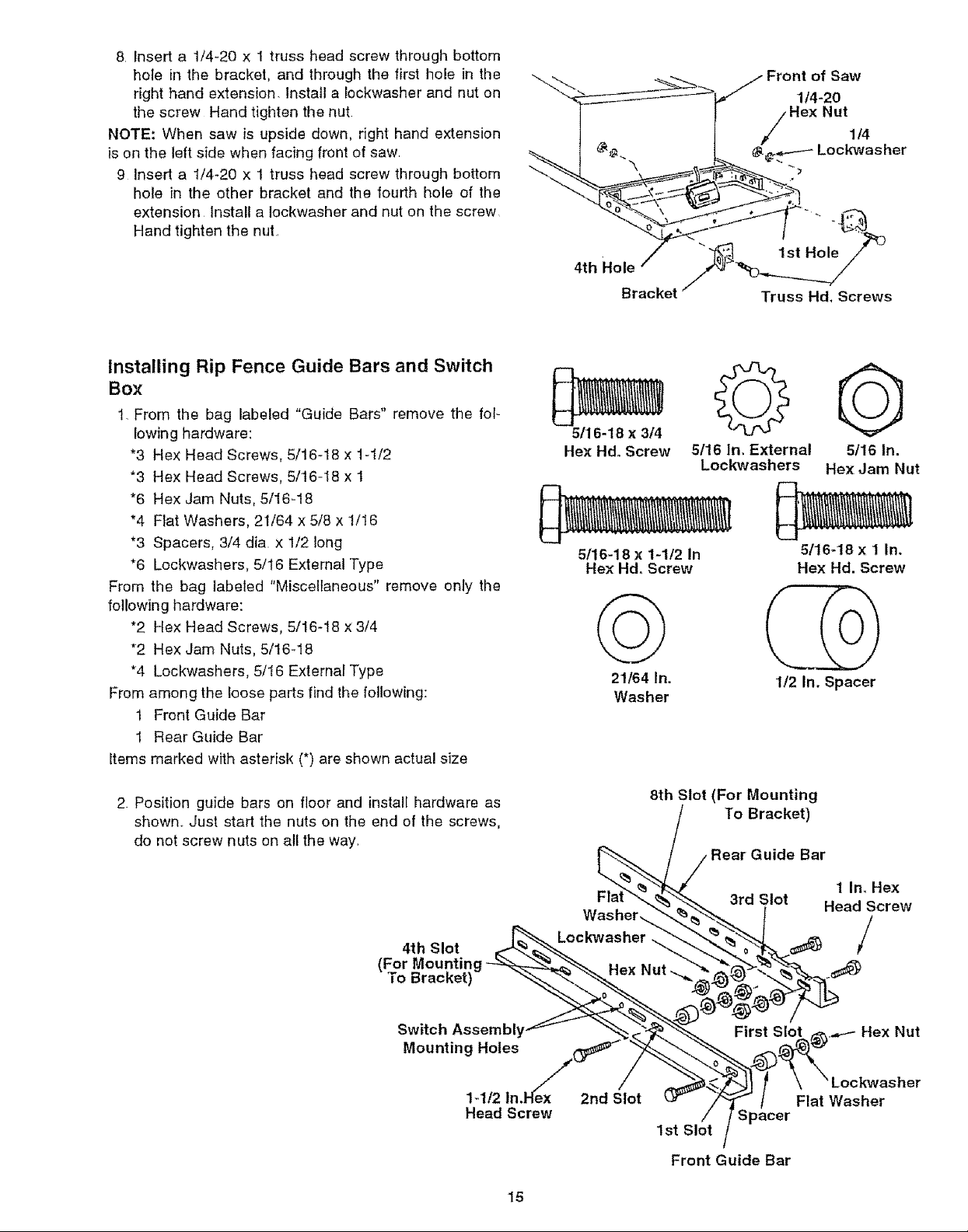
8 Inserta 1/4-20x 1trussheadscrewthroughbottom
holeinthebracket,andthroughthefirstholein the
righthandextension.Installa lockwasherandnuton
thescrewHandtightenthenut
NOTE:Whensawis upsidedown,righthandextension
isontheleftsidewhenfacingfrontofsaw
9 Inserta 1/4-20x 1trussheadscrewthroughbottom
holein the other bracket and the fourth hole of the
extension Install a Iockwasher and nut on the screw
Hand tighten the nut.
j Front of Saw
1/4-20
Hex Nut1/4
_ ¢._---- Lockwasher
1st Hole
Installing Rip Fence Guide Bars and Switch
Box
1. From the bag labeled "Guide Bars" remove the fol-
lowing hardware:
*3 Hex Head Screws, 5/16-18 x 1-t/2
*3 Hex Head Screws, 5/16-I8 x 1
*6 Hex Jam Nuts, 5/I6-18
*4 Flat Washers, 21/64 x 5/8 x 1/16
*3 Spacers, 3/4 dia, x 1/2 long
*6 Lockwashers, 5/16 External Type
From the bag labeled "Miscellaneous" remove only the
following hardware:
*2 Hex Head Screws, 5/16-18 x 3/4
*2 Hex Jam Nuts, 5/16-18
*4 Lockwashers, 5/t6 External Type
From among the loose parts find the following:
1 Front Guide Bar
1 Rear Guide Bar
Items marked with asterisk (*) are shown actual size
Bracket
5/16-18 x 3/4
Hex Hd. Screw
5116-18 x 1-1/2 In
Hex Hd. Screw
21164 In. 1/2 In. Spacer
Washer
Truss Hd. Screws
5/16 In. External
Lockwashers
G
5/16 In.
Hex Jam Nut
5/16-18 x 1 In.
Hex Hd. Screw
2. Position guide bars on floor and install hardware as
shown,. Just start the nuts on the end of the screws,
do not screw nuts on all the way,
(ForMounting __'_ Hex Nut __--_
ToBracko,
1-112 ln.Hex 2rid Slot t_'_ ._ / Flat Washer
Head Screw 1st SIo_t I Spacer
15
8th Slot (For Mounting
To Bracket)
/ Rear Guide Bar
• FI_ _ 3rd Slot Head'Screw
wasner.._ __ l
, ¢ 1 In Hex
Front Guide Bar
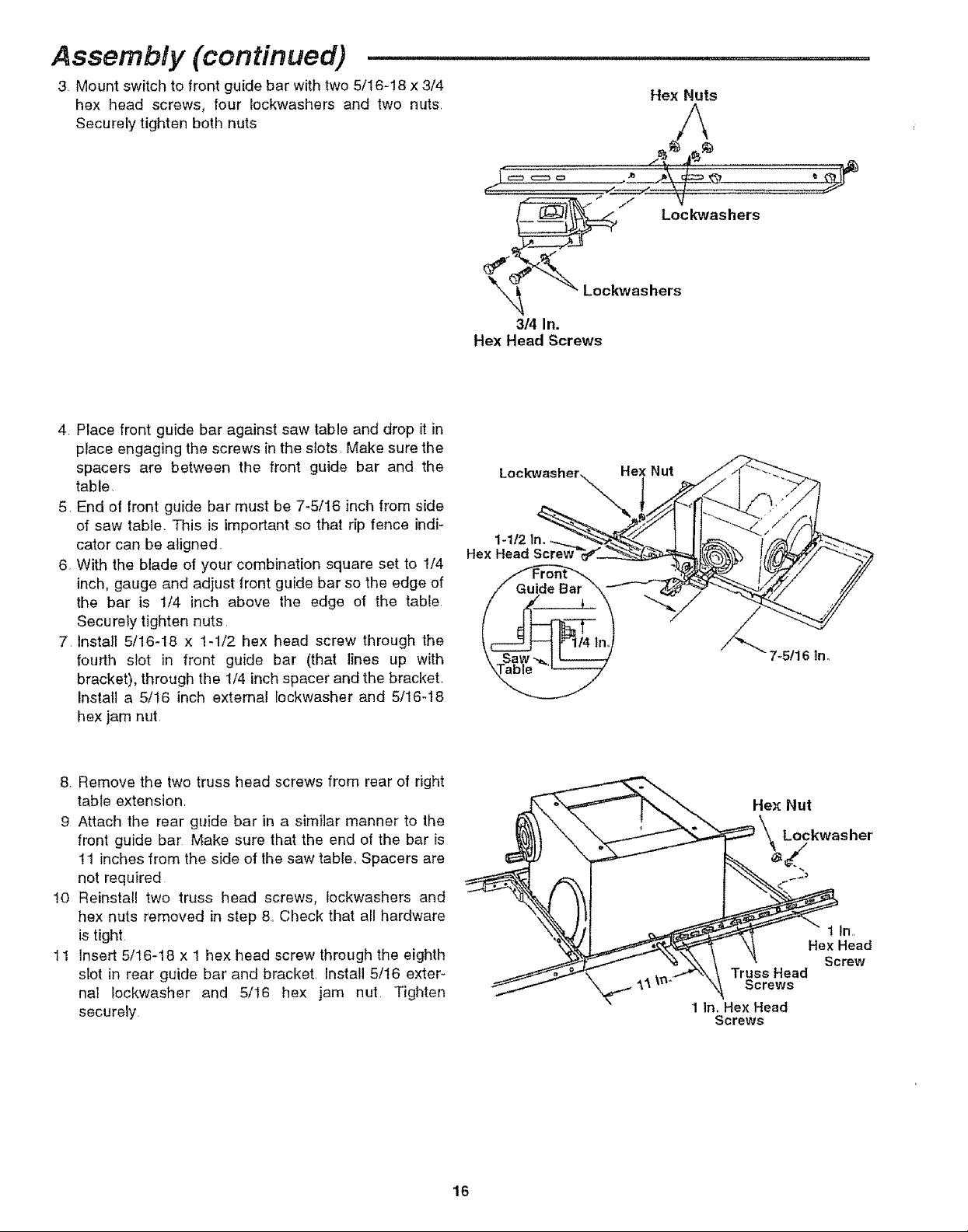
Assembly (continued)
3 Mount switch to front guide bar with two 5/16-!8 x 3/4
hex head screws, tour lockwashers and two nuts_
Securely tighten both nuts
4 Place front guide bar against saw table and drop it in
place engaging the screws in the slots, Make sure the
spacers are between the front guide bar and the
table
5 End of front guide bar must be 7-5/16 inch from side
of saw table, This is important so that rip fence indi-
cator can be aligned
6 With the blade of your combination square set to 1/4
inch, gauge and adjust front guide bar so the edge of
the bar is 1/4 inch above the edge of the table,
Securely tighten nuts,
7 Install 5/16-18 x 1-1/2 hex head screw through the
fourth slot in front guide bar (that lines up with
bracket), through the 1/4 inch spacer and the bracket,
Install a 5/16 inch external lockwasher and 5/16-t8
hex jam nut,
,, 1 Lockwashers
_'_ _ Loekwashers
3/4 In.
Hex Head Screws
Lockwasher Hex Nut
1-1/2In.
Hex Head Screw
@
Hex Nuts
7-5!16 |no
8. Remove the two truss head screws from rear of right
table extension,
9 Attach the rear guide bar in a similar manner to the
front guide bar Make sure that the end of the bar is
11 inches from the side of the saw table, Spacers are
not required
10 Reinstall two truss head screws, tockwashers and
hex nuts removed in step 8. Check that all hardware
is tight
11 insert 5/16-18 x 1 hex head screw through the eighth
slot in rear guide bar and bracket, Install 5/16 exter-
nal Iockwasher and 5/16 hex jam nut Tighten
securely
16
Hex Nut
Truss Head
Screws
1 In. Hex Head
Screws
Lockwas her'
t In,
Hex Head
Screw
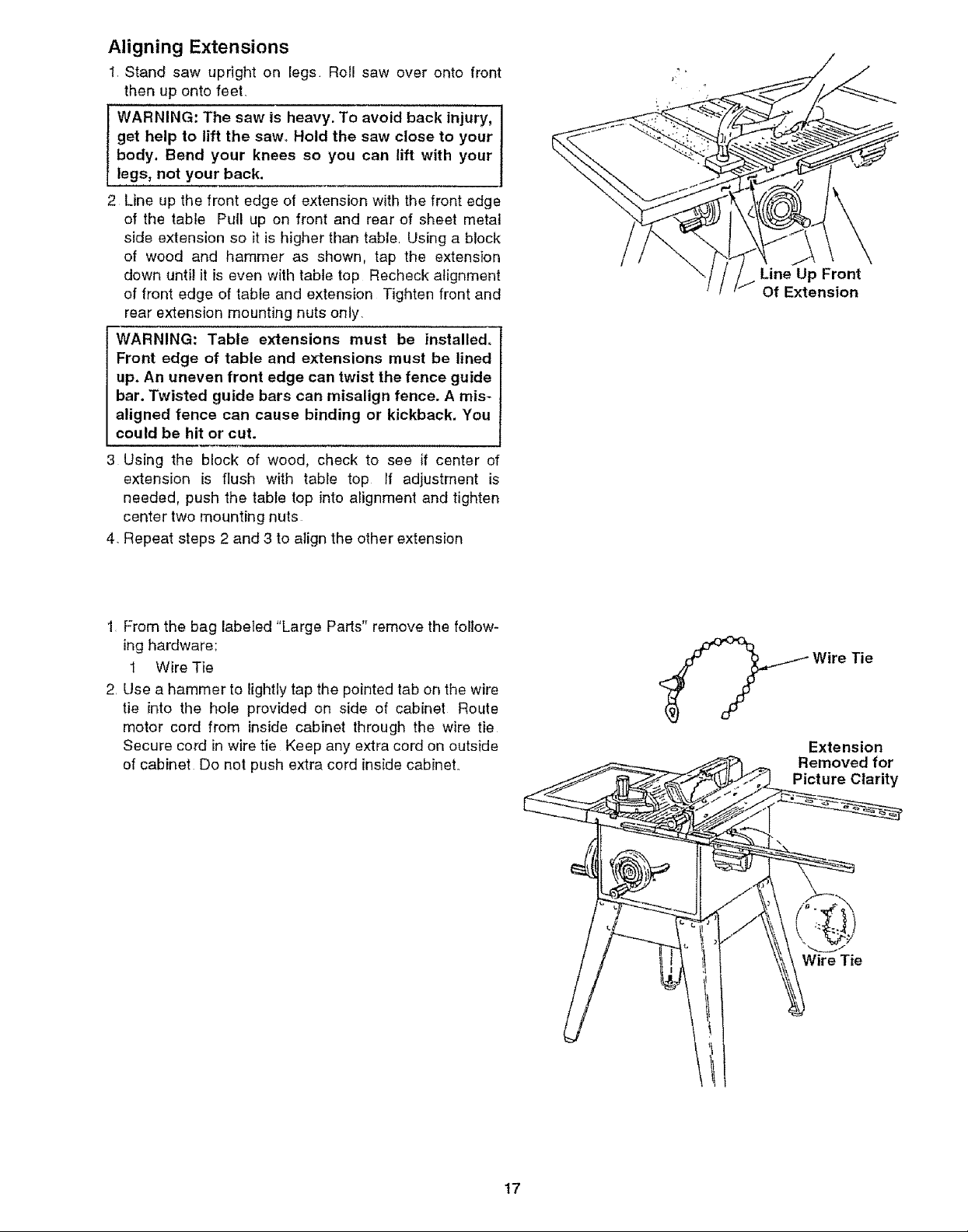
Aligning Extensions
1. Stand saw upright on legs Roll saw over onto front
then up onto feet,
WARNING: The saw is heavy. To avoid back injury,
get help to lift the saw. Hold the saw close to your
body. Bend your knees so you can lift with your
legs, not your back.
2 Line up the front edge of extension with the front edge
of the table Pul! up on front and rear of sheet metal
side extension so it is higher than table Using a block
of wood and hammer as shown, tap the extension
down until it is even with table top Recheck alignment
of front edge of table and extension Tighten front and
rear extension mounting nuts only,
WARNING: Table extensions must be installed,
Front edge of table and extensions must be lined
up. An uneven front edge can twist the fence guide
bar. Twisted guide bars can misalign fence. A mis-
aligned fence can cause binding or kickback. You
could be hit or cut.
3 Using the block of wood, check to see if center of
extension is flush with table top If adjustment is
needed, push the table top into alignment and tighten
center two mounting nuts
4, Repeat steps 2 and 3 to atign the other extension
Line Up Front
Of Extension
1 From the bag labeled "Large Parts" remove the follow-
ing hardware;
1 Wire Tie
2 Use a hammer to lightly tap the pointed tab on the wire
tie into the hole provided on side of cabinet Route
motor cord from inside cabinet through the wire tie
Secure cord in wire tie Keep any extra cord on outside
of cabinet Do not push extra cord inside cabinet,,
Tie
Extension
Removed for
Picture Clarity
Wire Tie
17