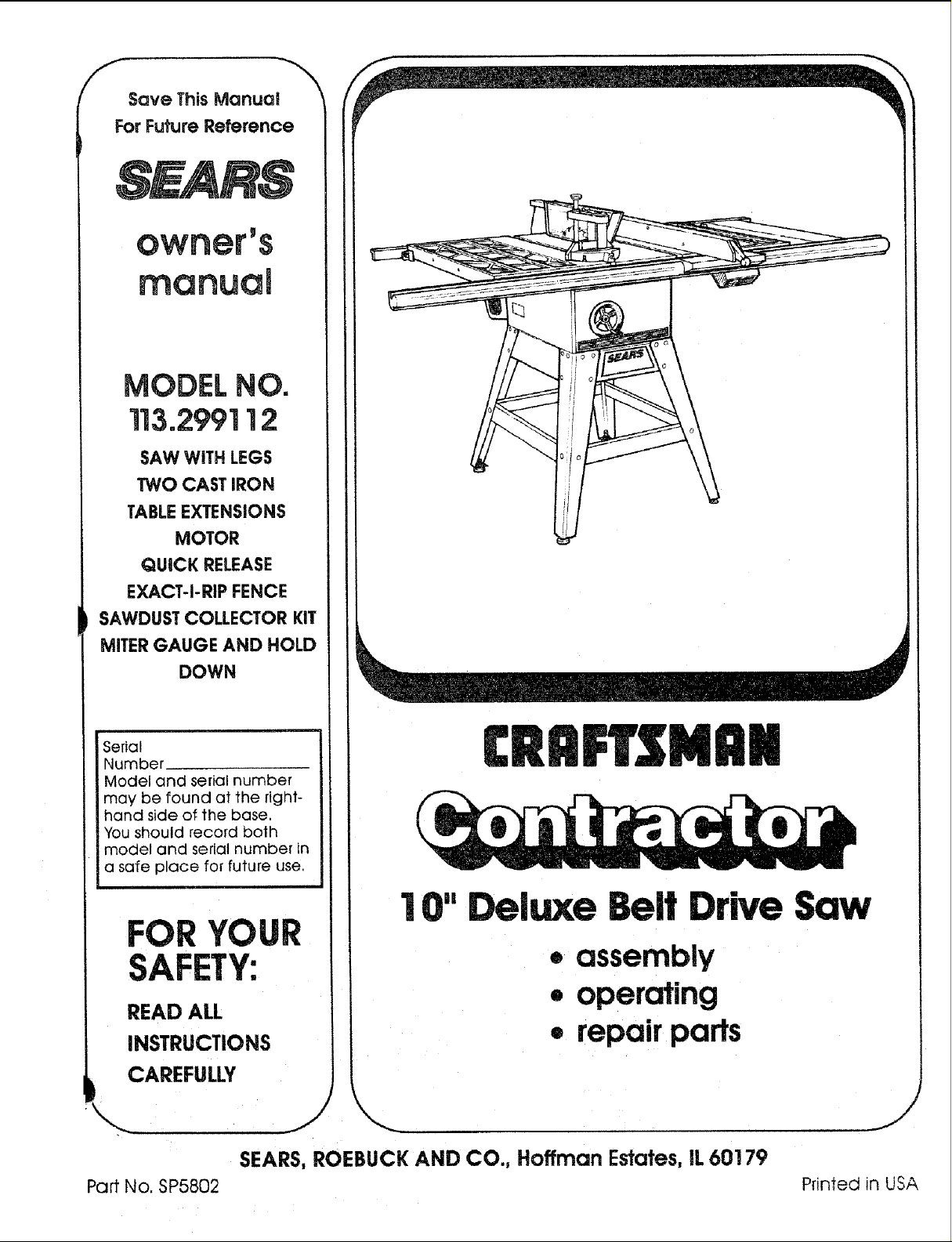
F
Save ThisManual
For FutureReference
MODEL NO.
113.299112
SAW WITH LEGS
TWO CAST IRON
TABLEEXTENSIONS
MOTOR
QUICK RELEASE
EXACT-i-RIP FENCE
SAWDUST COLLECTOR KIT
MITERGAUGE AND HOLD
DOWN
Seria!
Number
Model and serial number
may be found at the right-
hand side of the base.
You should record both
model and serial number in
a safe place for future use.
YOUR
SAFETY:
READ ALL
INSTRUCTIONS
CAREFULLY
,,...
SEARS, ROEBUCK AND CO., Hoffman Estates, IL 60179
Part No. SP5802
[RRFTZMRN
I 0" Deluxe Belt Drive Saw
• assembly
• operating
• repair parts
J
Printed in USA
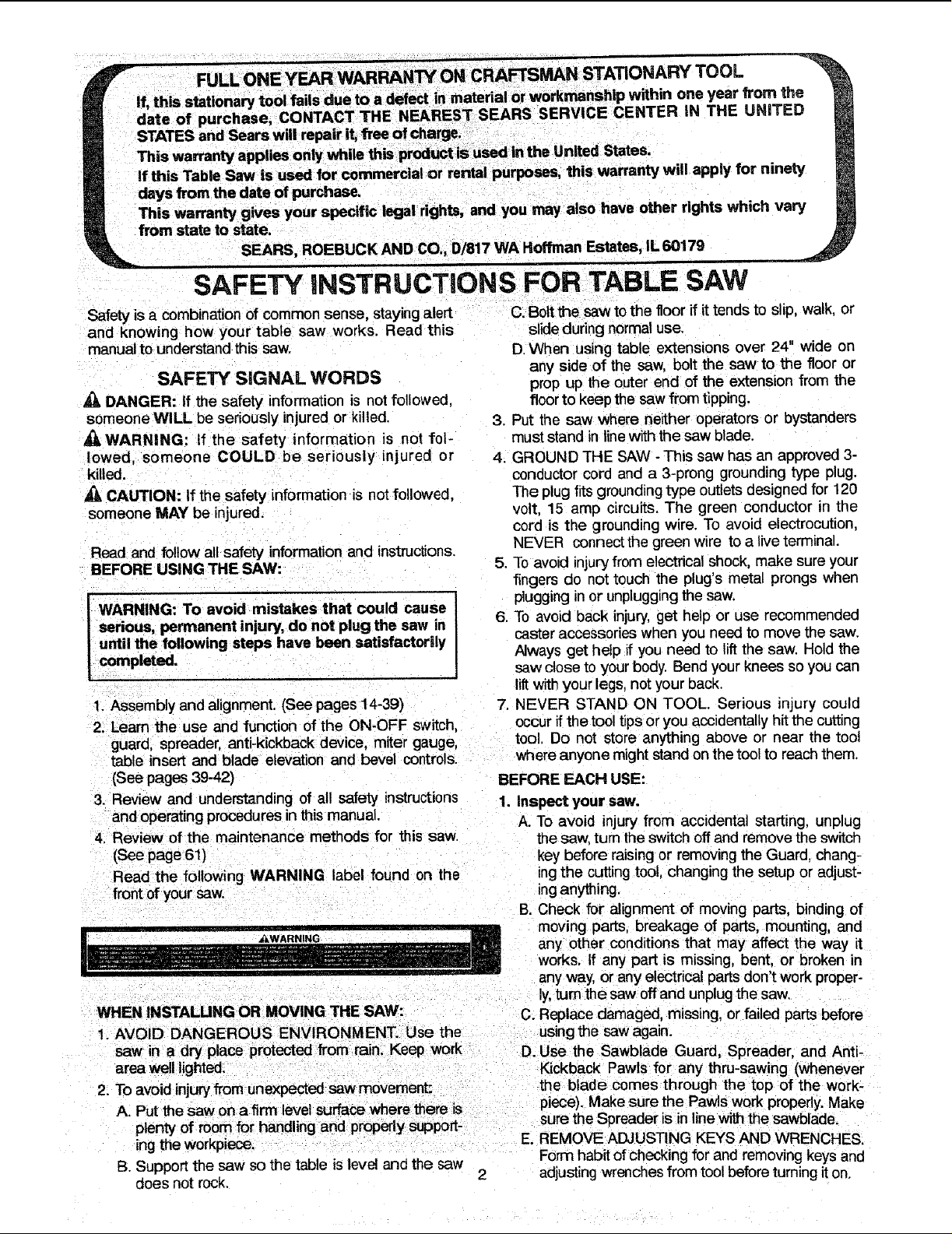
FULL ONE YEAR
STATES and Sears will repair it, free of charge.
This warranty applies only while this product is used in the United States.
If lJhisTable Saw is used for commercial or rental purposes, this warranty will apply for ninety
days from the date of purchase.
This warranty gives your specific legal rights, and you may also have other rights which vary
from state to state.
SEARS, ROEBUCK AND CO., D/817 WA Hoffman Estates, IL 60179
SAFETY iNSTRUCTiONS FOR TABLE SAW
Safety is a combination of common sense, staying alert
and knowing how your table saw works. Read this
manual to understand this saw.
SAFETY SIGNAL WORDS
DANGER: If the safety information is not followed,
someone WILL be seriously injured or killed
WARNING: If the safety information is not fol-
lowed, someone COULD be seriously injured or
killed.
CAUTION: If the safety information is notfollowed,
someone MAY be injured.
Read and follow all safety informationand instructions.
BEFORE USING THE SAW:
WARNING: To avoid mistakes that could cause
serious, permanent injury, do not plug the saw in
until the following steps have been satisfactorily
completed.
1. Assembly and alignment. (See pages 14-39)
2. Learn the use and function of the ON-OFF switch,
guard, spreader, anti-kickback device, miter gauge,
table insert and blade elevation and bevel controls.
(See pages 39-42)
3. Review and understanding of all safety instructions
and operating procedures inthis manual. A. To avoid injury from accidental starting, unplug
4. Review of the maintenance methods for this saw.
(See page 61)
Read the following WARNING label found on the
front of your saw.
WHEN INSTALUNG OR MOVING THE SAW':
1. AVOID DANGEROUS ENV RONMENT. Use the
saw n a dry place protected from rain. Keep work
................. where there is piece} Make sure the Pawlsworkproperly Make
A. _'u[ me saw on a nrm _evelsun_,uu ' . . . . "
-len'" of room for handlin" and -roDerl,, su'_'_rt sure the Spreader is in hnewiththe sawblade.
ij [y t.j H u H y I-,v_, -
ingthe workpiece. E. REMOVE ADJUSTING KEYS AND WRENCHES.
B. Support the saw so the table is level and the saw
does not rock. 2 adjusting wrenchesfrom tool before tuming iton.
C: Bolt the saw to the floor if it tends to slip, walk, or
slide during normal use.
D.When using table extensions over 24" wide on
any side of the saw, bolt the saw to the floor or
prop up the outer end of the extension from the
floor to keep the saw from tipping.
3. Put the saw where neither operators or bystanders
must stand in line with the saw blade.
4. GROUND THE SAW - This saw has an approved 3-
conductor cord and a 3-prong grounding type plug.
The plug fits grounding type outlets designed for 120
volt, 15 amp circuits. The green conductor in the
cord is the grounding wire. To avoid electrocution,
NEVER connect the green wire to a live terminal.
5. To avoid injury from electrical shock, make sure your
fingers do not touch the plug's metal prongs when
plugging in or unplugging the saw.
6. To avoid back injury, get help or use recommended
caster accessories when you need to move the saw.
Always get help if you need to lift the saw. Hold the
saw close to your body. Bend your knees so you can
lift withyour legs, not your back.
7. NEVER STAND ON TOOL. Serious injury could
occur if the tool tips or you accidentally hit the cutting
tool. Do not store anything above or near the tool
where anyone might stand on the tool to reach them.
BEFORE EACH USE:
1. Inspect your saw.
the saw, turn the switch off and remove the switch
key before raising or removing the Guard, chang-
ingthe cutting too!, changing the setup or adjust-
ing anything.
B. Check for alignment of moving parts, binding of
moving parts, breakage of parts, mounting, and
any other conditions that may affect the way it
works. If any part is missing, bent, or broken in
any way, or any electrical parts don't work proper-
ly.turn the saw off and unplug the saw.
C. Replace damaged, missing, or failed parts before
using the saw again.
D. Use the Sawblade Guard, Spreader, and Anti-
Kickback Pawls for any thru-sawing (whenever
the blade comes through the top of the work-
Form habit of checking for and removing keys and
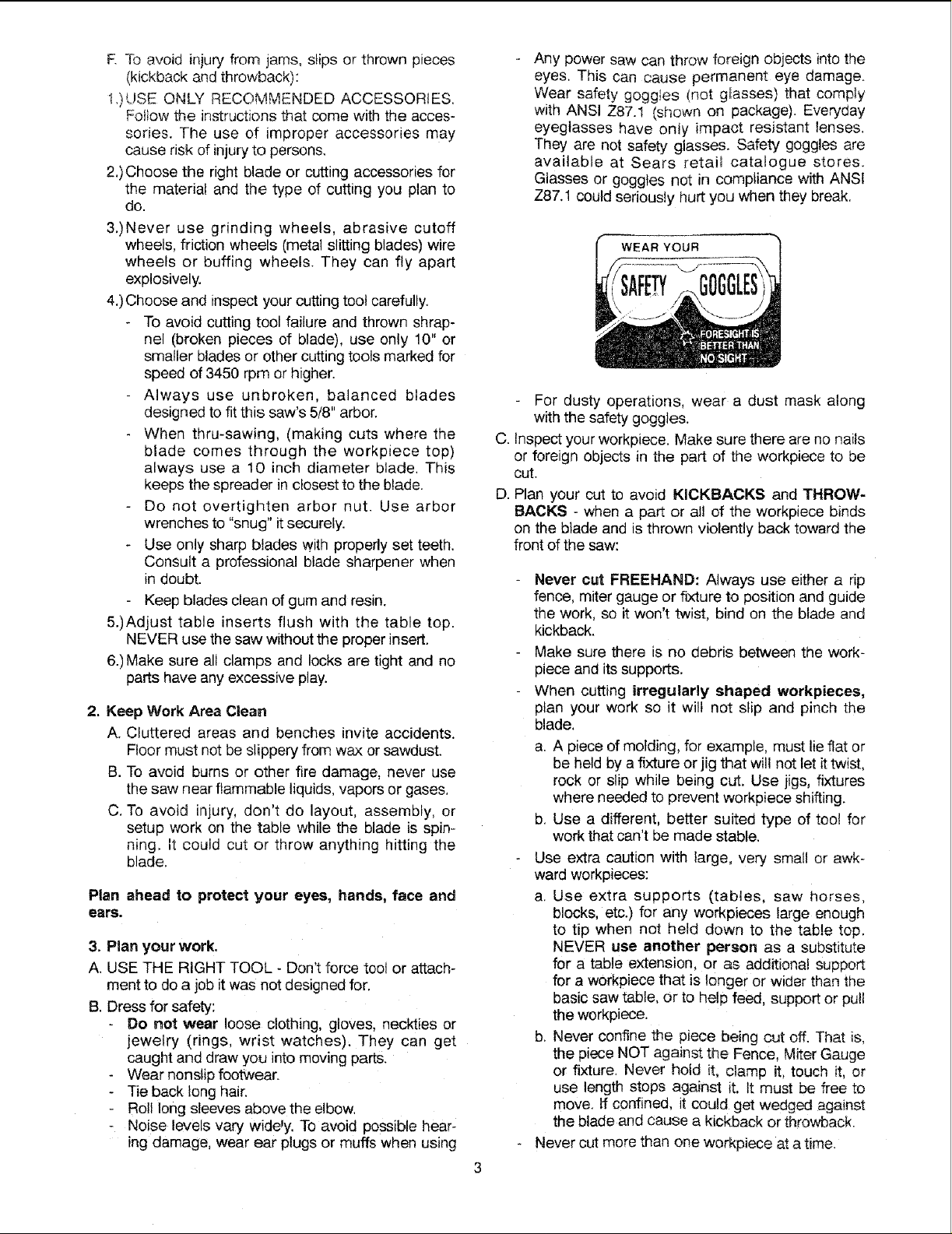
R [b avoidinjuryfrom jams, slips or thrown pieces
(kickback and throwback):
1.)USE ONLY RECOMMENDED ACCESSORIES.
Follow the instructions that come with the acces-
sories. The use of improper accessories may
cause risk of injury to persons.
2,)Choose the right blade or cutting accessories for
the material and the type of cutting you plan to
do.
3.)Never use grinding wheels, abrasive cutoff
wheels, friction wheels (metal slitting blades) wire
wheels or buffing wheels. They can fly apart
explosively.
4.)Choose and inspect your cutting tool carefully.
To avoid cutting tool failure and thrown shrap-
nel (broken pieces of blade), use only 10" or
smaller blades or other cutting tools marked for
speed of 3450 rprn or higher.
Always use unbroken, balanced blades
designed to fit this saw's 5/8" arbor.
When thru-sawing, (making cuts where the
blade comes through the workpiece top)
always use a 10 inch diameter blade. This
keeps the spreader inclosest to the blade.
Do not overtighten arbor nut. Use arbor
wrenches to "snug" it securely.
Use only sharp blades with properly set teeth.
Consult a professional blade sharpener when
in doubt.
Keep blades clean of gum and resin.
5.)Adjust table inserts flush with the table top.
NEVER use the saw without the proper insert.
6.) Make sure all clamps and locks are tight and no
parts have any excessive play.
2. Keep Work Area Clean
A. Cluttered areas and benches invite accidents.
Floor must not be slippery from wax or sawdust.
B. To avoid burns or other fire damage, never use
the saw near flammable liquids, vapors or gases.
C. To avoid injury, don't do layout, assembly, or
setup work on the table while the blade is spin-
ning. It could cut or throw anything hitting the
blade.
Plan ahead to protect your eyes, hands, face and
ears.
3, Plan your work.
A. USE THE RIGHT TOOL - Don't force tool or attach-
ment to do a job it was not designed for.
B. Dress for safety:
Do not wear loose clothing, gloves, neckties or
jewelry (rings, wrist watches). They can get
caugllt and draw you into moving parts.
Wear nonshp footwear.
Tie back long hair.
Roll long sleeves above the elbow.
Noise levels vary widely. To avoid possible qear-
_ngdamage, wear ear plugs or muffs when using
Any power saw can throw foreign objects into the
eyes. This can cause permanent eye damage.
Wear safety goggies (not gtasses) that comply
with ANSI Z87.1 (shown on package). Everyday
eyeglasses have only impaot resistant lenses.
They are not safety glasses. Safety goggles are
available at Sears retail catalogue stores.
Glasses or goggles not in compliance with ANSI
Z87.1 could seriously hurt you when they break.
WEAR YOUR
SAFE
For dusty operations, wear a dust mask along
with the safety goggles.
C. Inspect your workpiece. Make sure there are no nails
or foreign objects in the part of the workpiece to be
cut.
D. Plan your cut to avoid KICKBACKS and THROW-
BACKS - when a part or all of the workpiece binds
on the blade and is thrown violently back toward the
front of the saw:
Never out FREEHAND: Always use either a rip
fence, miter gauge or fixture to position and guide
the work, so it won't twist, bind on the blade and
kickback.
Make sure there is no debris between the work-
piece and its supports.
When cutting irregularly shaped workpieces,
plan your work so it wilt not slip and pinch the
blade.
a. A piece of molding, for example, must lie flat or
be held by a fixture or jig that wil! not let it twist,
rock or slip while being cut. Use jigs, fixtures
where needed to prevent workpiece shifting.
b. Use a different, better suited type of tool for
work that can't be made stable.
Use extra caution with large, very small or awk-
ward workpieces:
a. Use extra supports (tables, saw horses,
blocks, etc.) for any workpieces large enough
to tip when not held down to the table top.
NEVER use another person as a substitute
for a table extension, or as additiona! support
for a workpiece that is longer or wider than the
basic saw table, or to help feed, support or pull
the workpiece
b. Never confine the piece being cut off. That is,
the piece NOT against the Fence, Miter Gauge
or fixture. Never hold it, clamp it, touch it, or
use length stops against it. It must be free to
move. If confined, it could get wedged against
the blade and cause a kickback or throwback.
Never cut more than one workpiece at a time.
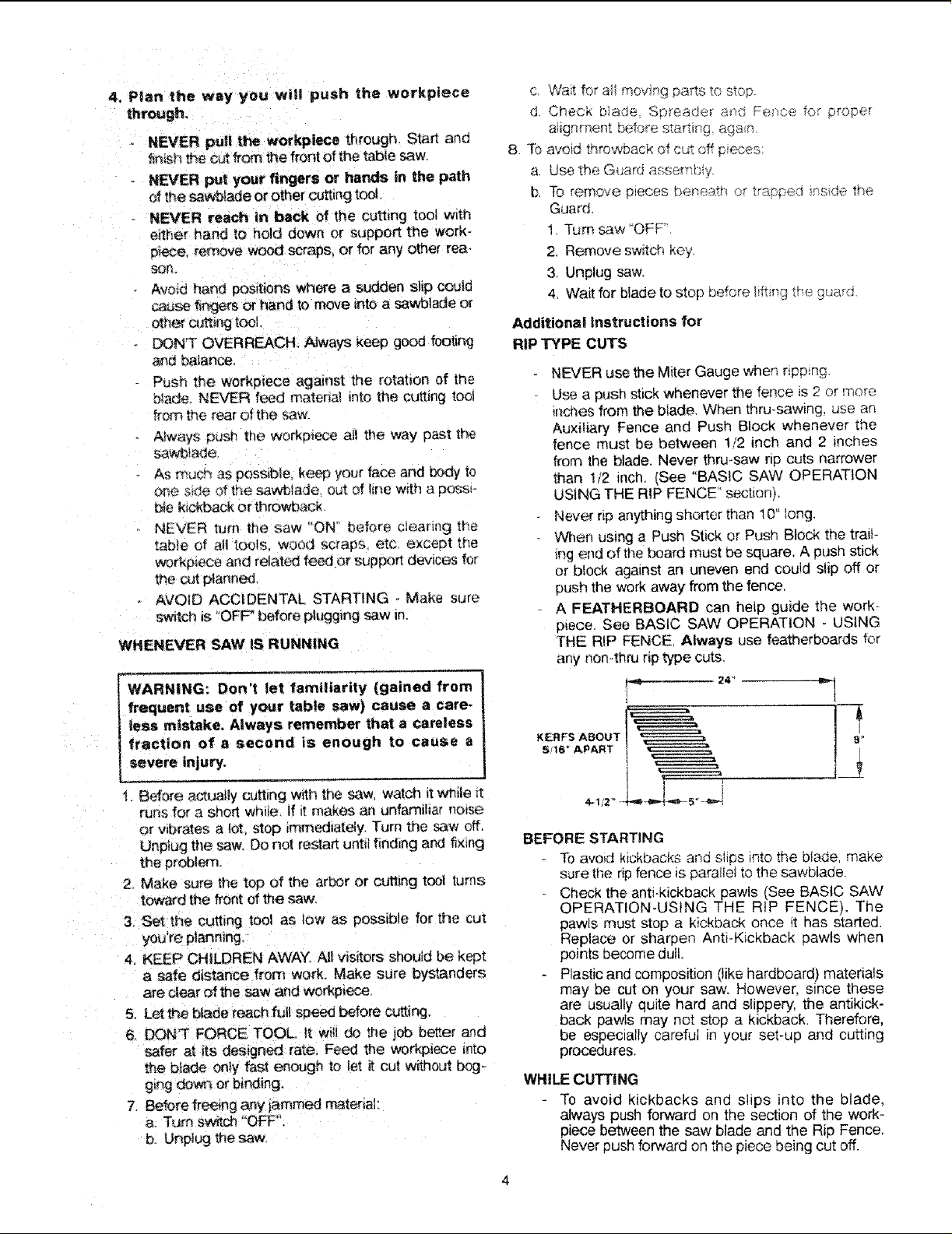
4. Plan the way you wlll push the workplece
through.
NEVER pull the workplece through. Start and
finish _e clot from the front of the table saw.
NEVER put your fingers or hands in the path
of the sawt_ade or other cutting too!.
NEVER reach in back of the cutting tool with
e_ther hand to hold down or support the work-
p_ece remove wood scraps, or for any other rea-
son.
Avoid hand pos_ons where a sudden s!ip could
cau_ fingers or hand to move _nto a sawblade or
oth,_" cutt=ng tO01
DON_ OVERREACH. AJways Keep good footing
an_ batance.
Push the workp_ece against the rotation of the
b_ade. NEVER feed materia! into the cutting tool
from tt_e rear of the saw.
Nways push the workp_ece all the way past the
As much as moss_bteoke_,_ your face and body to
one s_de of the _wbtade out of lille with a poss_-
t_e kickback or throwback
NEVER turn the saw "ON' before clearing the
tabte of atl tools, wood scraps etc exceot the
workp_ece and related fc_l or support devtce.s for
me cut ptanned
AVOID ACCIDENTAL, STARTING o Make sure
switch is "OFF" before plu.cLqing saw in.
WHENEVER SAW IS RUNNING
c Wa_tfor all moving parts to stop.
u, Check biade. Spreader a_d Fe_sce re: proper
a_gnrnent before slar_ir_g, _._f_an
8. To avoid throwback of cut off p;e,ces:
a. Use _ne G_4ard assemby.
h. To remove pt6wsesbeneath or trappecl ms,de the
Guard.
Turn saw "OFFL
2 Remove switch key.
3 Unplug saw,
4. Wa_t for blade to stop before !_fl_n9 the 9_sard.
Additional Instructions for
RiP TYPE CUTS
NEVER use the Miter Gauge when npp_ng,
Use a push stick whenever the fence is 2 or more
inches from the blade When thru-sawing, use an
Auxiliary Fence and Push Block whenever the
fence must be between 1/2 inch and 2 inches
from the blade, Never thru-saw rip cuts narrower
_an 1/2 inch. (See "BASIC SAW OPERATION
USING THE RIP FENCE' section),
Never rip anything shorter than 10" tong,
When using a Push Stick or Push Block the trail-
_ngend of the board must be square, A push stick
or block against an uneven end could slip off or
push the work away from the fence,
A FEATHERBOARD can hetp guide the work-
p_ece See BASIC SAW OPERATION - USING
THE RiP FENCE. Always use featherboards for
any non4f_ru rip type cuts.
WARNING: Don't let familiarity (gained from
frequent use of your table saw) cause a care-
_ess mistake. Always remember that a careless
fraction of a second is enough to cause a
severe injury.
t. Baler÷ aclualiy cutting w_th the saw, watc_ it while _t
runs for a short wh_ie If i! makes an unfarnihar no_se
or vibrates a tot, stoo immediately. Turn the ,_w eft,
Unplug the saw, Do not restart unt_tfinding and fixing
the problemo
2. Make sure the top of the arbor or cu11_ng tool turns
toward the front of the saw.
3, Set the cutting tool as tow as possible for the cuz
you're planning.
4. KEEP CHILDREN AWAY. All ws_tors should be kept
a safe distance from work. MaKe sure bystanders
are c4ear of the saw and workp_ece
5. Let, #_e blade reach full sp_ before cutting,
& DON'T FORCE TOOL. !t wilt do the job be_er and
safer at _ts designed rate. Feed the workp_ece rote
the b{ade only fast enougr_ to let it cut without bog-
g_ng down or binding.
7. Before freeing any jammed material:
a Turn switch "OFF".
b Unplug the saw
24 _
KERFS ABOUT
5/16" APART
9
BEFORE STARTING
-[b avoid kickbacks and slips into the blade, make
sure the rip fence is parallel to the sawblade.
Check the anti-kickback pawls (See BASIC SAW
OPERATION-USING THE RiP FENCE). The
pawls must stop a kickback once it has started.
Replace or sharpen Anti*Kickback pawls when
points become dull.
Plastic and composition (like hardboard) materials
may be cut on your saw. However, since these
are usually quite hard and slippery, the antikick-
back pawls may not stop a kickback. Therefore,
be especially careful in your set-up and cutting
procedures.
WHILE CUTTING
To avoid kickbacks and slips into the blade,
always push forward on the section of the work-
piece between the saw blade and the Rip Fence.
Never push forward on the piece being cut off.
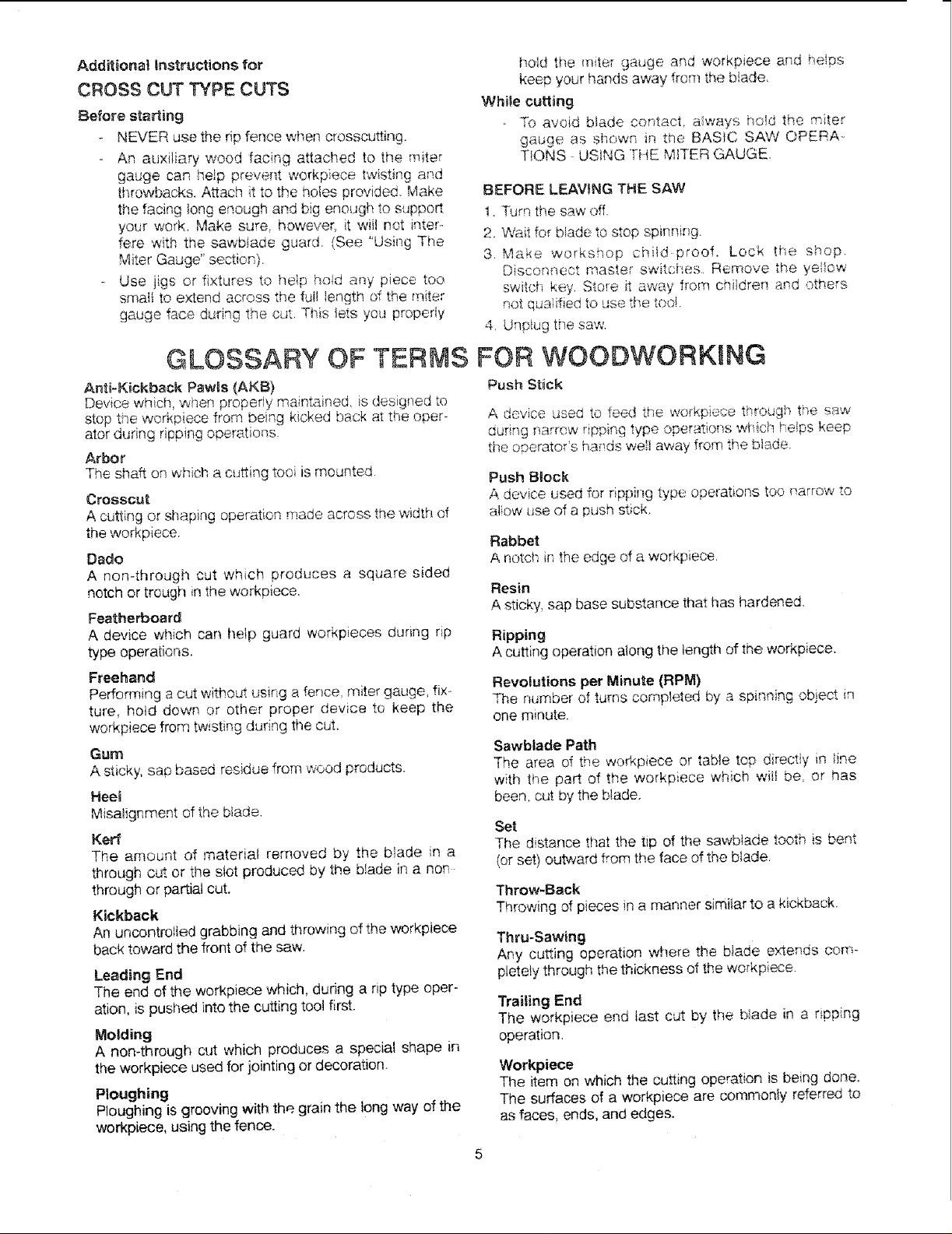
Addi_lona! Instructions for
CROSS CUT TYPE CUTS
Before starting
NEVER use the rip fence wt_en crosscutting.
An atJxiliary wood facing attached to the miter
gauge can heip prevent workpiece twisting and
throwbacks. Attach t to the i_oles provided. Make
the facing tong enough and big e,qo_gh to support
your work. Make sure however, it wii! not inter..
fore with the sawb_ade guard. (See "Using The
Miter Gauge" section),
Use jigs or fixtures to help hoid any piece too
smait to extend across the futl length d the miter
gauge face duriT_g 1he cu_ Th}s _ets yo_.,,properly
GLOSSARY OF TERMS FOR WOODWORKmNG
Anti-Kickback Paw_s (AKB)
Device which, when properly maintained, is desigried to
stop the workpiece from be}ng kicked back at the oper-
ator during ripping operations.
Arbor
The shaft on which a c_Jtti,qgtoo; is mounted
CrOSSCUt
A cutting or shaping operation made across tb,e width of
the workpiece,
Dado
A non-through cut which produces a square sided
notch or trough in the workpiece,
Featherboard
A device which can help guard workpieces during rip
type operations.
Freehand
Performing a cut without usir_ga fence, miter gauge, fix_
ture, hold down or other proper device to keep the
workpiece from twisting during the cut.
Gum
A sticky, sap based residue from wood products.
Heet
Misalignment of the b_ade.
Kerr
The amount of materia_ removed by the blade in a
tllrough cut or the slot produced by the bIade in a non
through or partial cut.
Kickback
An uncontrolled grabbing and throwing of the workpiece
back toward the front of the saw.
Leading End
The end of the workpiece which, dudng a rip type oper-
ation, is pushed into the cutting too! first.
Molding
A non-through cut which produces a special shape in
the workpiece used for jointing ordecoration.
Ploughing
Ploughing is grooving with the grain the long way of the
workpiece, using the fence,
ho_d the mi_er gauge and workp_ece ar_,d heips
keep your hands away from the b!ade
White cutting
fb avoid blade contact, aiways ho!d the miter
gauge as shown in the BASIC SAW OPERA-.
]'tONS USING file M_TER GAUGE.
BEFORE LEAVING THE SAW
1. Turn the saw off
2. Wait for b{ade to stop spirlnir_g
3. Make workshop child proof. Lock tt-;e shop.
Discon,qeot master switches Remove the yel_ow
switch key. Store it away from childre_ and others
not qua;fled to use the toei.
4, Unp}ug [iqe saw,
Push Stick
A dev,,ce used to feed the wo_kpiece throu#h the saw
during r_,arrow ripping type operations which helps keep
the operator's hands well away from the blade.
Push BRock
A devce used for rippir_g type operations toe _arrow to
a_iow use of a push stick,
Rabbet
A notch i_ the _lge of a workpiece.
Rea{n
A sticky, sap base substance that has hardened
Ripping
A cutting operation along the lengthof the workpiece.
Revolutions per Minute (RPM)
The number of turns completed by a spinning object in
one minute.
Sawblade Path
The area of the workpiece or tab}e top directiy in line
with tiqe part of tb.eworkpiece which wi!! be, or has
been cut by the blade.
Set
The distance that the tip of the sawblade _ooth is be_t
(or set) outward from the face of the b_ade
Throw-Back
Throwing of pieces in a manner similar to a kickback.
Thru-Sawing
Any cutting operation where the blade e×!ends com-.
pietety through the thickness of the workpiece.
Trailing End
The workpiece end tast cut by the blade in a ripping
operation.
Workpiece
The item on which the cutting operation is being done.
The surfaces of a workpiece are commonly referred to
as faces, ends, and edges.
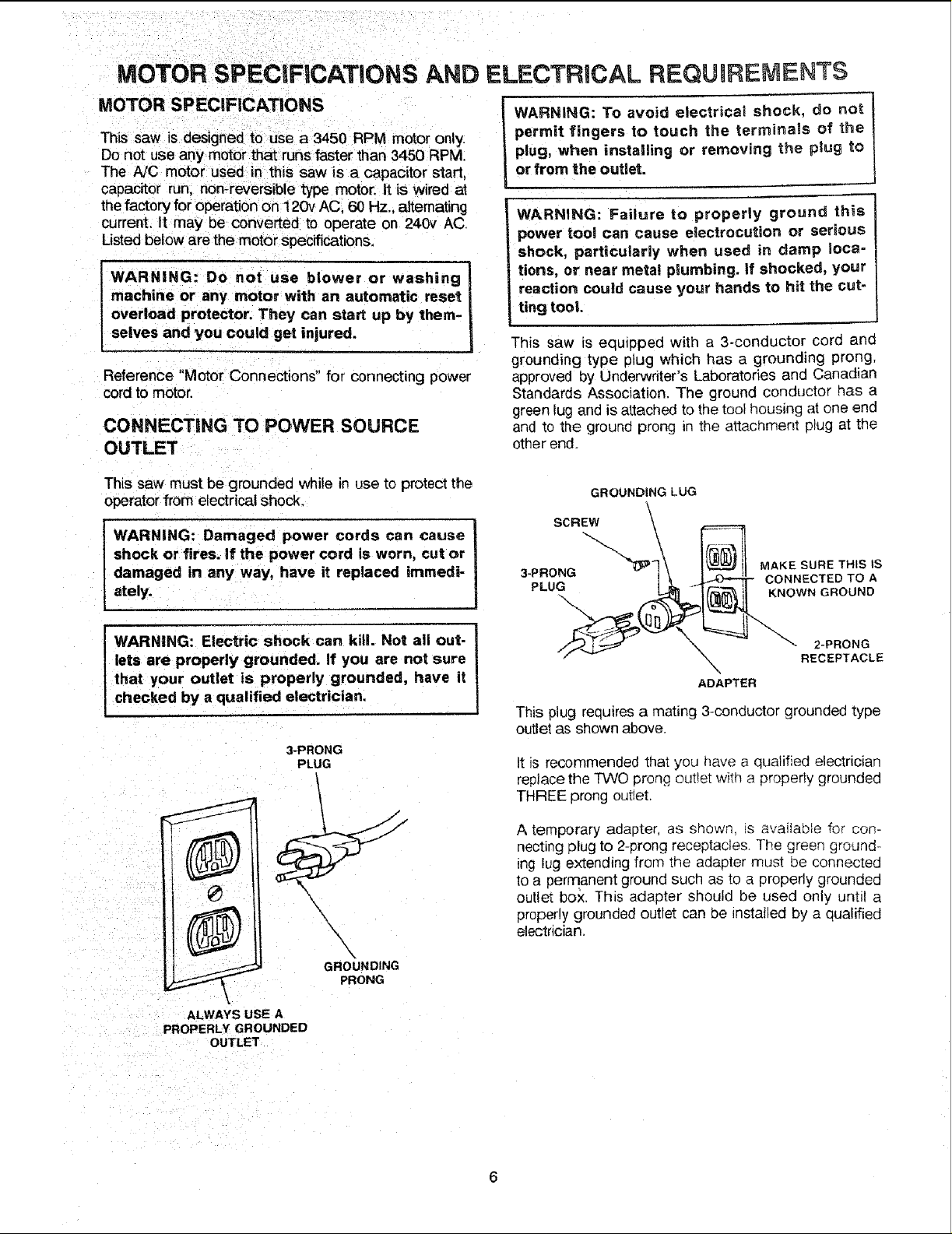
MOTOR SPECIFICATIONS AND ELECTRICAL REQUIREMENTS
MOTOR SPECIFICATIONS
This saw is designed to use a 3450 RPM motor only.
Do not use any motor that runs faster than 3450 RPM.
The A/C motor used in this saw is a capacitor start.
capacitor run, non-reversible type motor, it is wired at
the factory for operation on 120v AC, 60 Hz., alternating
current. It may be converted to operate on 240v AC
Listed below are the motor specifications.
not
machine or any motor with an automatic reset
overload protector. They can start up by them-
I WARNING: Do use blower or washing
selves and you could get injured.
Reference "Motor Connections" for connecting power
cord to motor.
CONNECTING TO POWER SOURCE
OUTLET
This saw must be grounded while in use to protect the
operator from electrical shock.
WARNING: Damaged power cords can cause
shock or fires. If the power cord is worn, cut or
damaged in any way, have it replaced immedi-
ately.
WARNING: To avoid electrical shock, do not
permit fingers to touch the terminals of the
plug, when installing or removing the plug to
or from the outlet.
WARNING: Failure to properly ground this
power tool can cause electrocution or serious
shock, particularly when used in damp loca-
tions, or near metal plumbing, if shocked, your
reaction coutd cause your hands to hit the cut-
ting tool
This saw is equipped with a 3-conductor cord and
grounding type Dlug which has a grounding prong,
approved by Underwriter's Laboratories and Canadian
Standards Association. The ground conductor has a
green lug and isattached to the tool housing at one end
and to the ground prong in the attachment plug at the
other end.
GROUNDING LUG
SCREW \
WARNING: Electric shock can kill Not all out-
lets are properly grounded. If you are not sure
that your outlet is properly grounded, have it
checked by a qualified electrician.
3-PRONG
PLUG
g)
\
\
x
GROUNDING
PRONG
ALWAYS USE A
PROPERLY GROUNDED
OUTLET
\.
ADAPTER
This plug requires a mating 3-conductor grounded type
outlet as shown above.
It is recommended that you nave a qualified electrician
replace the TWO prong outlet w_tna properly grounded
THREE prong outlet.
A temporary adapter, as shown, is available for con-
necting plug to 2-prong receptacles. The green ground-
ing lug extending from the adapter must be connected
to a pen_anent ground such as to a properly grounded
outlet box. This adapter should be used only until a
properly grounded outlet can be installed by a qualified
electrician.
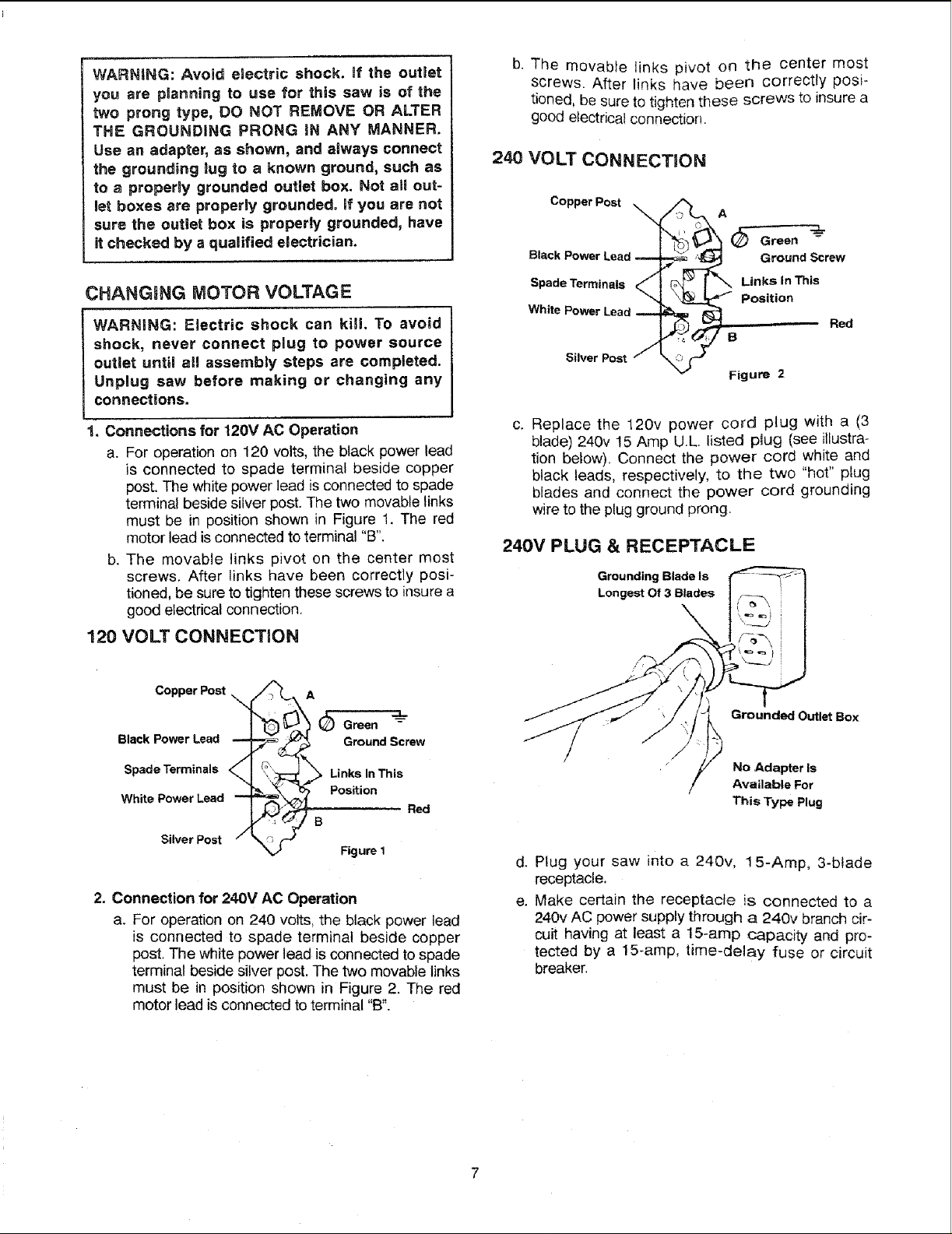
WARNING: Avoid electric shock, tf the outlet
you are planning to use for this saw is of the
two prong type, DO NOT REMOVE OR ALTER
THE GROUNDING PRONG iN ANY MANNER.
Use an adapter, as shown, and always connect
the grounding lug to a known ground, such as
to a properly grounded outlet box. Not all out-
let boxes are properly grounded, if you are not
sure the outlet box is properly grounded, have
it checked by a qualified electrician.
CHANGING MOTOR VOLTAGE
WARNING: Electric shock can kill. To avoid
shock, never connect plug to power source
outlet until all assembly steps are completed.
Unplug saw before making or changing any
connections.
1. Connections for 120V AC Operation
a. For operation on 120 volts, the black power lead
is connected to spade terminal beside copper
post. The white power lead is connected to spade
terminal beside silver post. The two movable links
must be in position shown in Figure 1. The red
motor lead isconnected to terminal "B".
b. The movable links pivot on the center most
screws, After links have been correctly posi-
tioned, be sure to tighten these screws to insure a
good electrical connection,
120 VOLT CONNECTION
b. The movable links pivot on the center most
screws. After links have been correctly posi-
tioned, be sure to tighten these screws to insure a
good electrical connectior_.
240 VOLT CONNECTION
Copper Post
Black Power Ground Screw
Spade Terminals Links in This
White Power Lead
Silver Post
A
Position
B
Figure 2
c. Replace the 120v power cord plug with a (3
blade) 240v 15 Amp U.L. listed plug (see illustra-
tion below). Connect the power cord white and
black leads, respectively, to the two "hot" plug
blades and connect the power cord grounding
wire to the plug ground prong.
240V PLUG & RECEPTACLE
Grounding Blade Is
Longest Of 3 Blades
Red
Copper Post A
Green _-
Black Power Lead Ground Screw
Spade Terminals Links In This
White Power Lead
Silver Post
Position
Red
B
Figure I
2. Connection for 24.0V AC Operation
a. For operation on 240 volts, the black power lead
is connected to spade terminal beside copper
post. The white power lead is connected to spade
terminal beside silver post. The two movable links
must be in position shown in Figure 2. The red
motor lead is connected to terminal "B".
Grounded Outlet Box
No Adapter Is
Available For
This Type Plug
d. Plug your saw into a 240v, 15-Amp, 3-blade
receptacle.
e. Make certain the receptacle is connected to a
240v AC power supply through a 240v branch cir-
cuit having at least a 15-amp capacity and pro-
tected by a 15-amp, time-delay fuse or circuit
breaker.
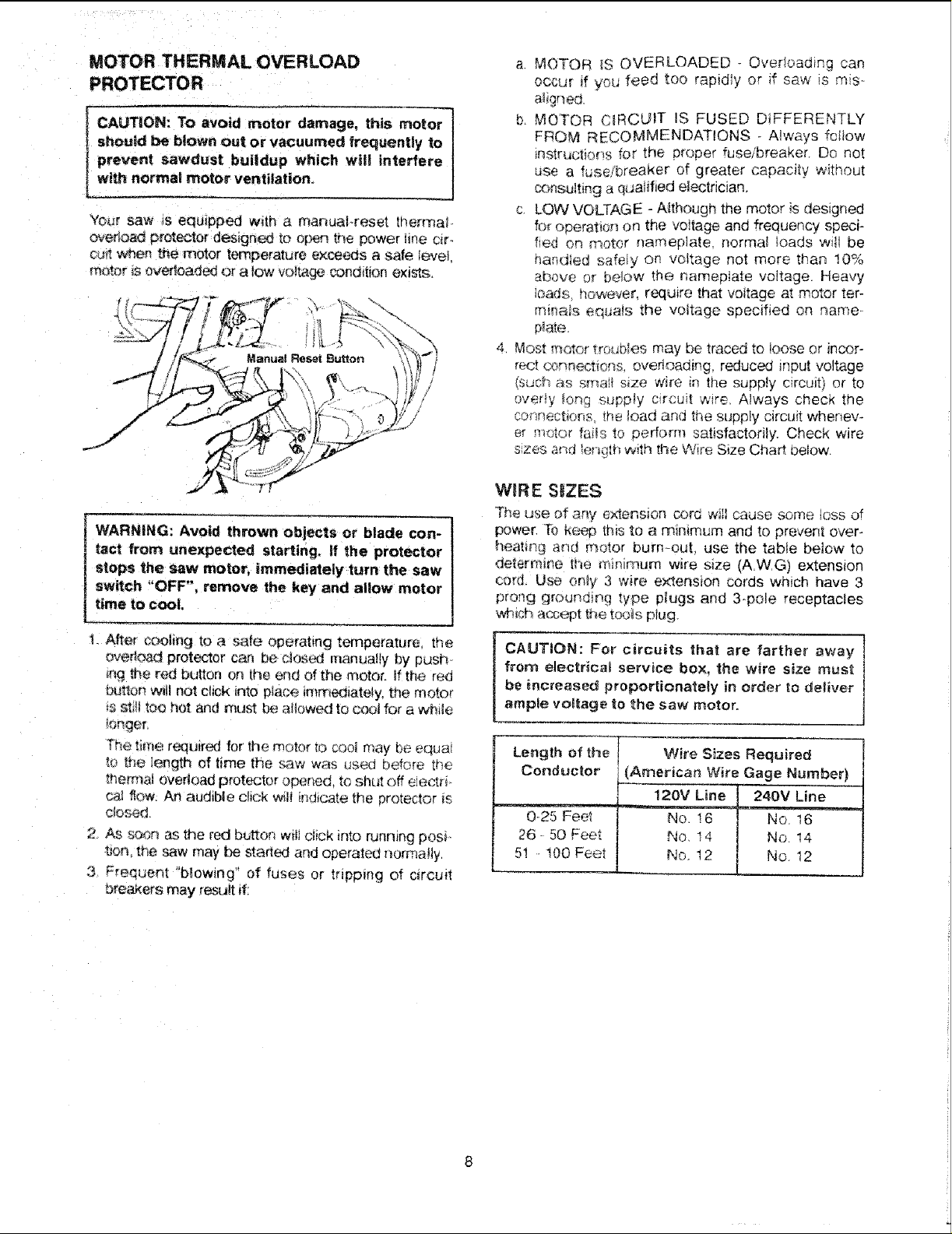
MOTOR THERMAL OVERLOAD
PROTECTOR
I CAUTION: TO avoid damage, this motor
shoued be blown out or vacuumed frequently to
prevent sawdust buildup which will interfere
I with n_ormal motor ventilation,
Your saw _s equipped w_th _ mar'_uaFreset thermal
over_a_ protector designed to open tr_e power line c_r.
cu_ w_en me motor temperature exce6_s a safe teveL
m_or $ overloaded el a low vo_ta_ cona_t_on exls'_.
nr_ot--or
a. MOTOR tS OVERLOADED - Overioading can
0ccu[ if yet,; feed too rapidly or if sew is mis_
a_igr_ecL
b MOTOR C_RCL_IT IS FUSED DIFFERENTLY
FROM RECOMMENDATIONS - A!ways fotlow
instructions for the proper fuseibreaker. Do not
use a fusefbreaker of greater capacity without
_msu_ting a qualified electrician.
c, LOW VOLTAGE -Aithough the motor is designed
fo_operation on the voitage and frequency speci-
fied on motor nameplate normal loads wilt be
har_died safely on voltage not more than 10%
above or below the namepiate voltage. Heavy
bads, i_owever, require that voltage a[ motor teF
m,inais equa!s the voltage specified on name
p_ate.
4. Most _otor troubles may be traced to loose or incor-
reel cormect_ons, overloading, reduced input voltage
(such as small size wire in the supply circuit) or to
overly _ong sup_'31y circuit wire, Always check the
cofinections the toad and the supply circuit whenev-
er motor fails to perform satisfactorily. Check wire
szes and ler_gthwith the Wire Size Chart below.
W_RE S_ZES
The use of any extension cord Will cause some !oss of
power, To keep this to a minimum and to prevent over-
heating ar_d motor burn-out_ use the table beiow to
determine ti_e minim{Kn wire size (AW, G) extension
co_J Use or_y 3 w_re extension cords which have 3
prong gK._ur_dir]g type plugs and 3_pole receptacles
,,_ff,icha_ept the toots plug
t. After cooling [o a safe operahng temperature, the
eve#earl protector can be c_es_ manually by push.
{t_g the red button on the end of the motor, if the red
buttO_ W_t not click into place immed_ate{y, the moto_
_ss£!_too hot and must be allowed] to cool for a while
_onqer.
Th_._brae required for the motor to cooi may be equal
_o _t_e;ength of time the _3w was useu before t_e
thermal overload protector opened, to shut off eiectri*
ca_ ,'lew. An audible click wilt _nd_catethe pretec[or is
CiOSed
2 As s_,_n as the re4dbutton w_!tdick _nto running posi-
t_ the saw may be started and operated norma!ty,
3 Frequent "b_owing" of fuses or tripping of c_rcu_t
breakers may result if.
CAUTION: For circuits that are farther away
from electrical service box, the wire size must
be _ncreased proportionately in order to de_iver
ample voltage tO the saw motor.
Length of the
Cor_ductor
0-25 Feet
26 50 Feet
5i - t00 Feet
Wire Sizes Required
(A_erican Wire Gage Number)
120V L_ne 240V Line
No. 16 No. 16
No_ 14 No. 14
No. 12 No. 12
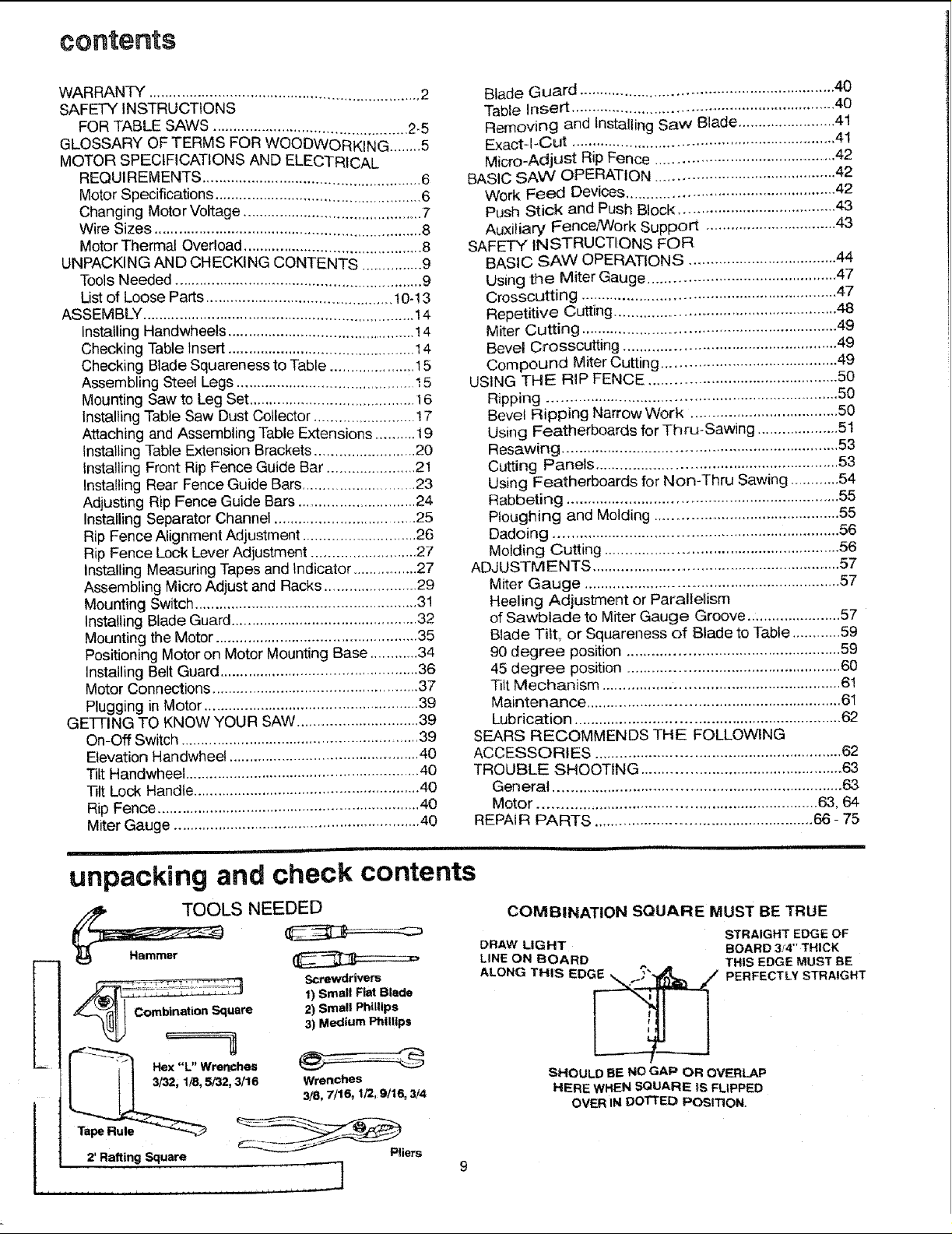
contents
WARRANTY
SAFETY INSTRUCTIONS ............................... z
FOR TABLE SAWS ........................... 2-5
GLOSSARY OF TERMS FOR WOODWORKIN'GI: .,.5
MOTOR SPECIFICATIONS AND ELECTRICAL
REQUIREMENTS ...................................................... 6
Motor Specifications ................................................... 6
Changing Motor Voltage ............................................ 7
Wire Sizes .................................................................. 8
Motor Thermal Overload ............................................ 8
UNPACKING AND CHECKING CONTENTS ...............9
Tools Needed ............................................................. 9
List of Loose Parts .............................................. t0-13
ASSEMBLY ................................................................... 14
Installing Handwheels ............................................... ! 4
Checking Table Insert ............................................. 14
Checking Blade Squareness to Table ......................15
Assembling Steel Legs ............................................ 15
Mounting Saw to Leg Set......................................... 16
Installing Table Saw Dust Collector ....................... ! 7
Attaching and Assembling Table Extensions ...........t 9
Installing Table Extension Brackets ..........................20
Installing Front Rip Fence Guide Bar ......................21
Installing Rear Fence Guide Bars........................... 23
Adjusting Rip Fence Guide Bars ............................ 24
Installing Separator Channel ....................................25
Rip Fence Alignment Adjustment ............................ 26
Rip Fence Lock Lever Adjustment .......................... 27
Installing Measuring Tapes and Indicator ................27
Assembling Micro Adjust and Racks ....................... 29
Mounting Switch ....................................................... 31
Installing Blade Guard .............................................. 32
Mounting the Motor .................................................. 35
Positioning Motor on Motor Mounting Base ............34
Installing Belt Guard ................................................. 36
Motor Connections ................................................... 37
Plugging in Motor ..................................................... 39
GE'I-FING TO KNOW YOUR SAW.............................. 39
On-Off Switch ........................................................... 39
Elevation Handwheel ............................................... 40
Tilt Handwheel .......................................................... 40
-I]lt Lock Handle ........................................................ 40
Rip Fence ................................................................. 40
Miter Gauge ............................................................. 40
i ==,== =,1= = = , ==H,r
Blade Guard ............................................................. 40
Table Insert ............................................................... 40
Removing and Installing Saw Blade ........................41
Exact-l-Cut ................................................................ 41
Micro-Adjust Rip Fence ............................................ 42
BASIC SAW OPERATION .................................... 42
Work Feed Devices .................................................. 42
Push Stick and Push Block ...................................... 43
Auxiliary Fence/Work Support ................................ 43
SAFETY INSTRUCTIONS FOR
BASIC SAW OPERATIONS .................................... 44
Using the Miter Gauge ............................................. 47
Crosscutting ............................................................. 47
Repetitive Cutting ...................................................... 48
Miter Cutting .............................................................. 49
Bevel Crosscutting ................................................... 49
Compound Miter Cutting .......................................... 49
USING THE RIP FENCE ............................................. 50
Ripping ...................................................................... 50
Bevel Ripping Narrow Work .................................... 50
Using Featherboards for Thru-Sawing ....................51
Resawing .................................................................. 53
Cutting Panels .......................................................... 53
Using Featherboards for Non-Thru Sawing ............54
Rabbeting .................................................................. 55
Ploughing and Molding ............................................ 55
Dadoing .................................................................... 56
Molding Cutting ........................................................ 56
ADJUSTMENTS ............................................................ 57
Miter Gauge ............................................................. 57
Heeling Adjustment or Parallelism
of Sawblade to Miter Gauge Groove .......................57
Blade Tilt, or Squareness of Blade to Table ............59
90 degree position .................................................... 59
45 degree position ................................................... 60
Tilt Mechanism ......................................................... 61
Maintenance ............................................................. 61
Lubrication ................................................................. 62
SEARS RECOMMENDS THE FOLLOWING
ACCESSORIES ........................................................... 62
TROUBLE SHOOTING ................................................ 63
General ..................................................................... 63
Motor ................................................................... 63, 64
REPAi R PARTS ..................................................... 66 - 75
unpacking and check contents
OLS NEEDED
Screwdrivers
1) Small Flat Blade
mbination Square
E
_. r 2' Rafting Square J
2) Small Philltps
3) Medium Phillips
Pliers
COMBINATION SQUARE MUST BE TRUE
DRAW LIGHT
LINE ON BOARD
ALONG THIS EDG_
SHOULD BE NO GAP OR OVERLAP
HERE WHEN SQUARE IS FLIPPED
OVER IN DoI-rED POSITION,
STRAIGHT EDGE OF
BOARD 3f4" THICK
THIS EDGE MUST BE
PERFECTLY STRAIGHT
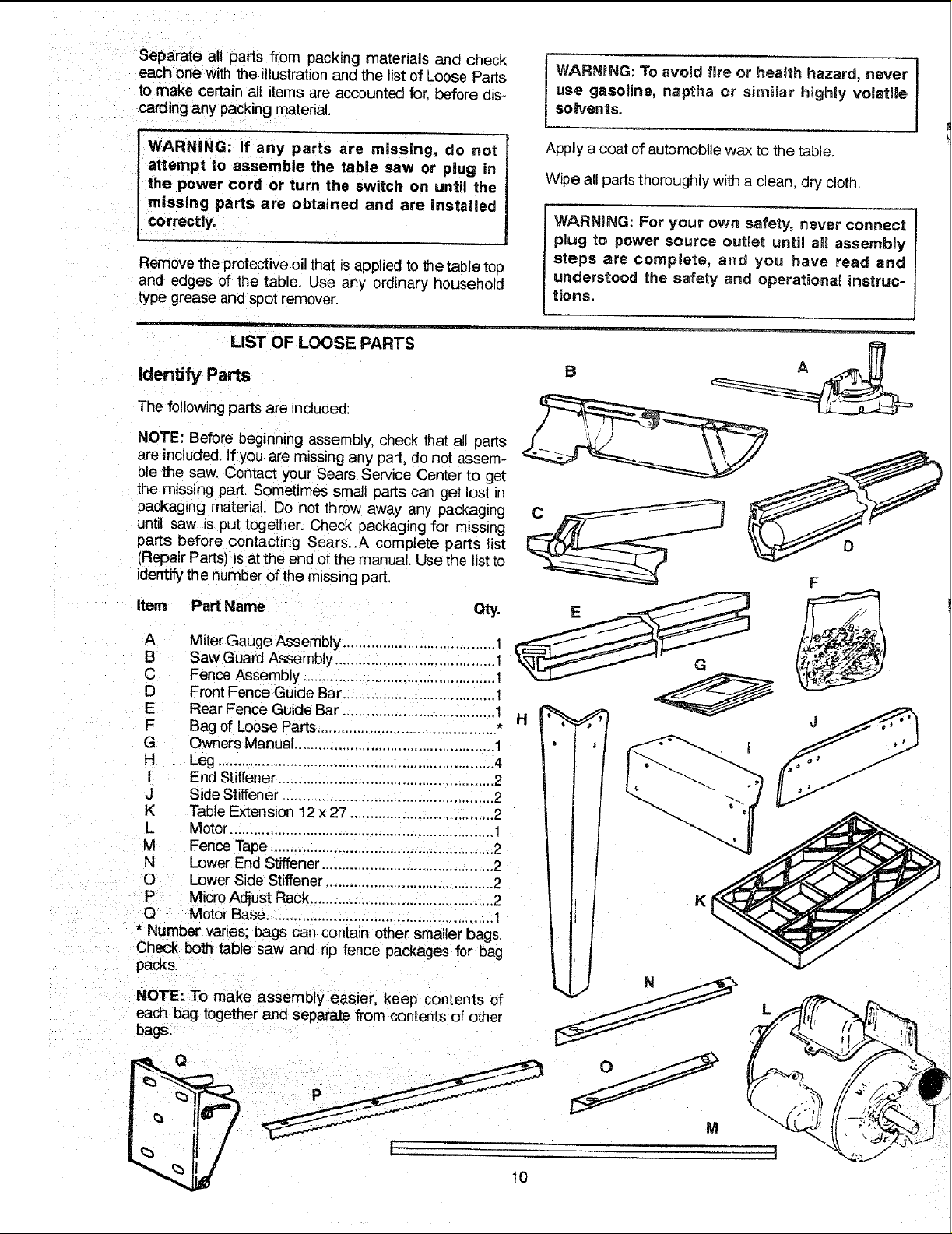
Separate all parts from packing materials ana check
each one with the illustration and the list of Loose Parts
to make certain all items are accounted for. before dis-
carding any packing material.
use gasoline, naptha or simiJar highly volatile
j WARNING: To avoid fire or health hazard, never J
so,vents.
i
I
' WARNING: If any parts are missing, do not J
attempt to assemble the table saw or plug in
the power cord or turn the switch on until the
missing parts are obtained and are instaUed
correctly.
Remove the protective oil that is appliedto the table top
and edges of the table. Use any ordinary household
type grease and spot remover.
LIST OF LOOSE PARTS
Identify Parts
The following parts are included'.
NOTE: Before beginning assembly, check that all parts
are included,If you are missing any part, do not assem-
ble the saw. Contact your Sears Service Center to get
the missing part, Sometimes small parts can get lost _n
packaging material. Do not throw away any packaging
until saw is put together. Check _ackaging for missing
parts before contacting Sears.,A corn plete parts list
(Repair Parts) Isat the end of the manual. Use the list to
identifythe number of the missing part.
Apply a coat of automobile wax to the table.
Wipe allparts thoroughly with aclean, dry cloth,
f
WARNING: For your own safety, never connect
plug to power source outlet until all assembly
steps are complete, and you have read and
understood the safety and operational instruc-
tions.
F
Item Part Name
A Miter Gauge Assembly .................................... 1
B Saw Guard Assembly ........................................
C Fence Assembly ................................................ 1
D Front Fence Guide Bar...................................... 1
E Rear Fence Guide Bar ...................................... 1
F Bag of Loose Parts ............................................. *
G Owners Manual .................................................. 1
H Leg ..................................................................... 4
I End Stiffener ...................................................... 2
J Side Stiffener ..................................................... 2
K Table Extension 12 x 27 .................................... 2
L Motor .................................................................. 1
M Fence Tape ........................................................ 2
N Lower End Stiffener ........................................... 2
O Lower Side Stiffener .......................................... 2
P MicroAdjust Rack .............................................. 2
Q Motor Base ........................................................ 1
• Number varies; bags can contain other smaller bags.
Check both table saw and rip fence packages for bag
packs,
NOTE: To make assembly easier, keep contents of
each bag together and separate from contents of other
bags.
Q
M
I t
10
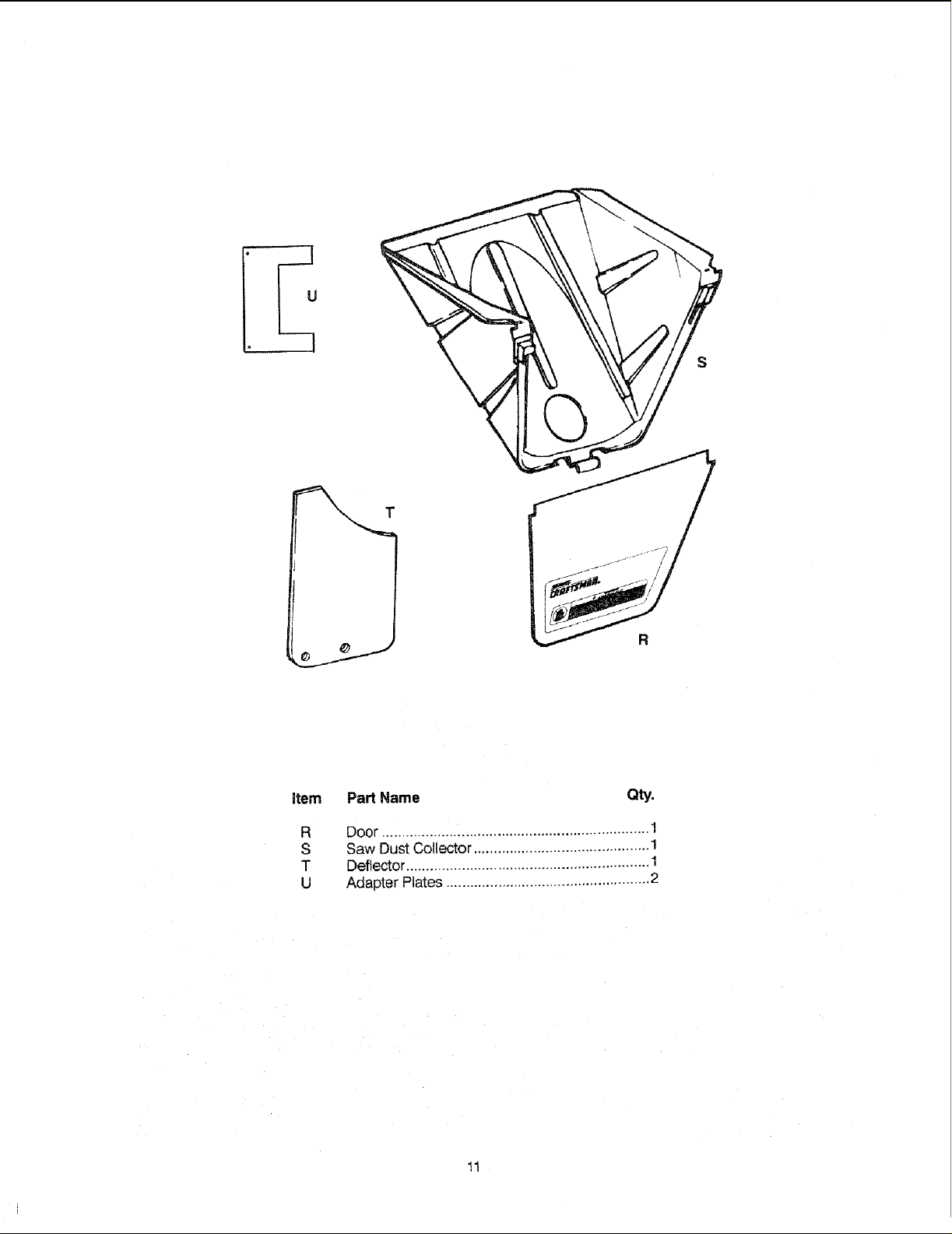
___d
I°
--q
T
item Part Name Qty.
R
Door ................................................................... 1
Saw Dust Collector ........................................... 1
S
Deflector ............ 1
T
U
Adapter Plates .................................................. 2
11
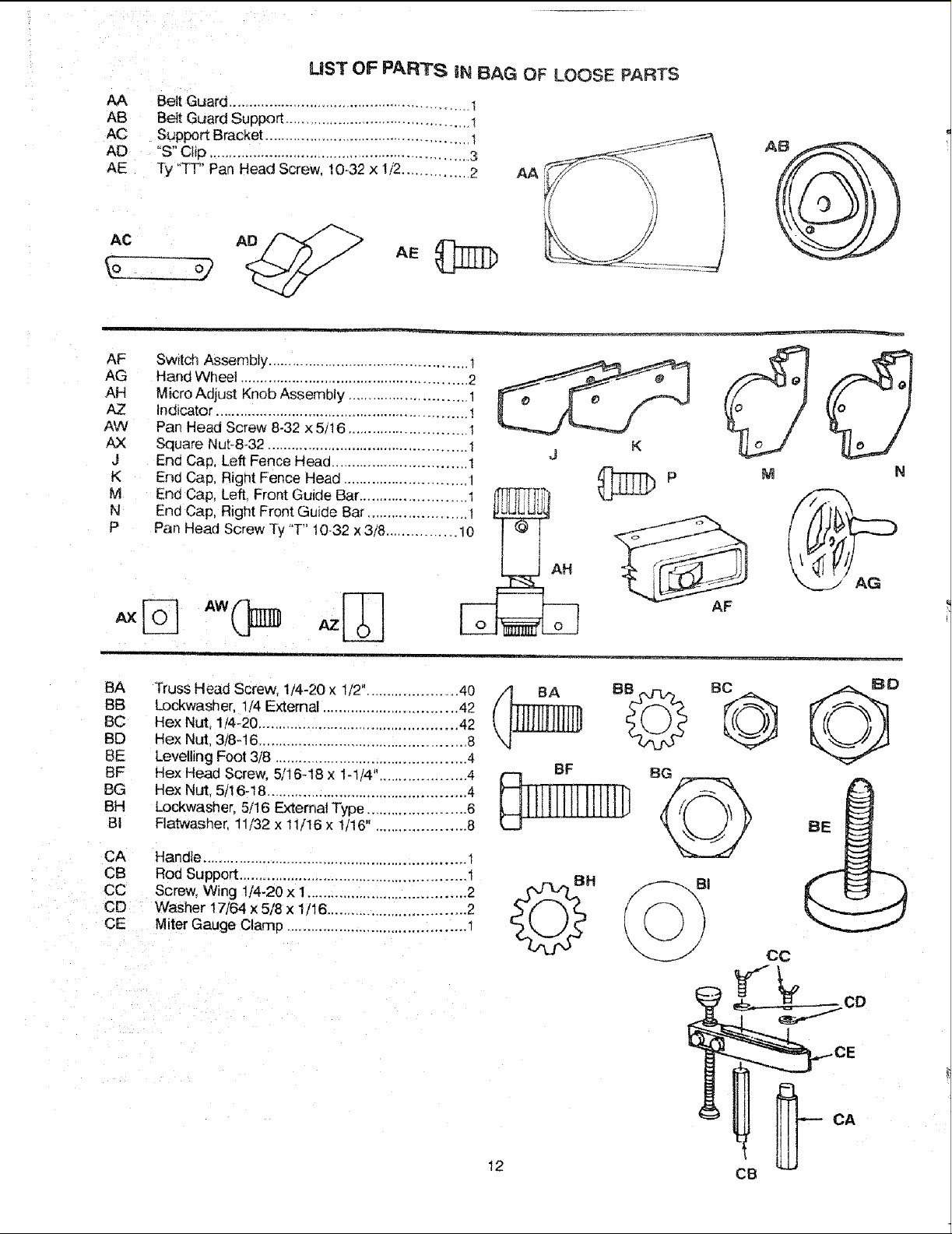
UST OF PARTS iN BAG OF LOOSE PARTS
AA Belt Guard ........................................................... t
AB Belt Guard Support ............................................. !
AC Support Bracket ................................................. 1
AD "S" Clip ................................................................ 3
AE Ty "TT' Pan Head Screw, 10-.32x 1/'2.................2 AA
AC AD
AF Switc_'lAssembly ................................................
AG Hand Wheel ....................................................... 2
AH Micro Adjust Knob Assembly ............................ I
AZ indicator ............................................................. 1
AW Pan Head Screw 8-32 x 5/16 ............................ 1
AX Square Nut-8-32 ................................................ 1
J End Cap, Left Fence Head ................................ 1
K End Cap, Right Fence Head ............................. 1
M End Cap, Left, Front Guide Bar......................... 1 _
N End Cap, R ght Front Guide Bar ............ t
J
K
M
BA Truss Head Screw, 1/4-20 x 1/2"...................... 40
BB Lockwasher, t/4 External .............................. 42
BC Hex Nut 1_4_20............................................ 42
BD Hex Nut, 3/8-16 .................................................. 8
BE Levelling Foot 3/8 .............................................. 4
BF Hex Head Screw. 5/16-18 x 1-1.'4".................... 4
BG Hex Nut. 5/16-18 ................................................ 4
BH Lockwasher, 5/16 External Type ....................... 6
BI Flatwasher. 11/32 x 11/16 x 1/16", .................... 8
CA Handle ................................................................ 1
CB Rod Support ....................................................... !
CC Screw, Wing 1/4-20 x 1...................................... 2
CD Washer 17/64 x 5/8 x 1/16 ................................. 2
CE Miter Gauge Clamp ........................................... 1
I!
AG
AF
BE
CC
12
CA
CB
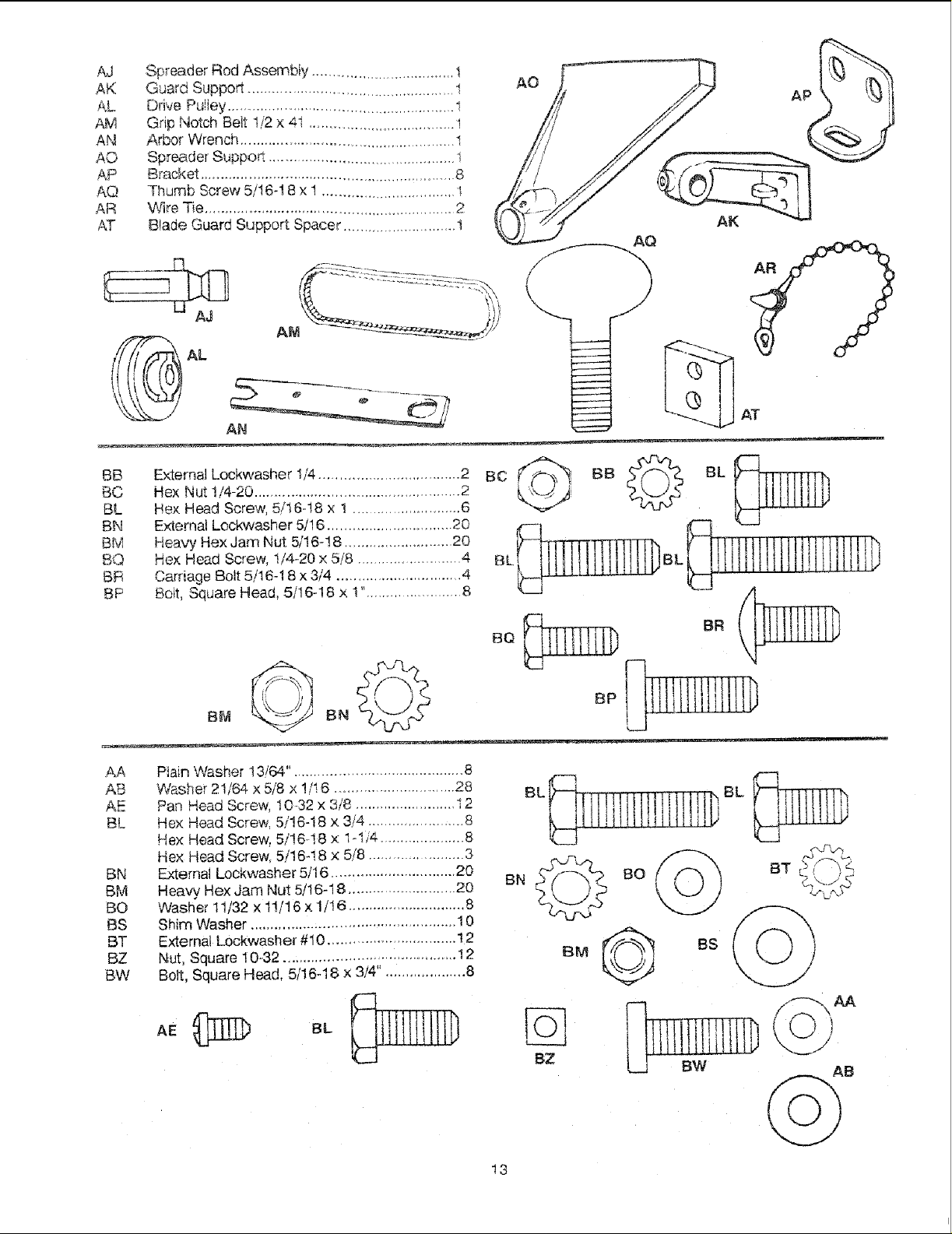
AJ SpreaderRodAssembly...................................1
AK GuardSupport..................................................l
AL DrivePuley.......................................................1
AM GripNotchBelt112x41.......................................1
AN ArborWrench.....................................................1
AO SpreaderSuppo_.............................................1
AP Bracket.............................................................8.
AQ ThumbScrew5/!648x 1................................I
AR WireTie..............................................................2
AT BIadeGuardSupportSpacer...........................!
AO
AK
AQ
AT
BC
BL
BN
BM
.o oc©
BQ BL
BR
BP
AA Piain Washer 13164".......................................... 8
AB Washer 21/64 x 5/8 x !/16 ............................ 28
AE Pan Head Screw, 10-32 x 3/8 ......................... 12
BL Hex Head Screw, 5/16-18 x 3/4 ...................... 8
BN External Lockwasher5/16 ............................... 20
BM Heavy. Hex Jam Nut 5/16-18 ......................... 20
BO VVasher 11/32 x tlr16 x 1/16 ............................. 8
BS Shim Washer ................................................... 10
BT External Lockwasher #10 .............................. 12
BZ Nut, Square 10-32 ....................................... 12
BW Bolt, Square Head. 5116-18 x 3/4". ................... 8
External Lockwasher 1/4.................................... 2
Hex Nut 1/4-20 .................................................. 2
Hex Head Screw, 5/t6-18 x 1 ............................6
External Lockwasher 5/16 ............................... 20
Heavy Hex Jam Nut 5/!6-18 .......................... 20
Hex Head Screw, 1/4-20 x 5/8 ......................... 4
Carriage Bolt 5/!6-18 x 3/4 ............................... 4
Bolt, Square Head, 5/16-18 x I "........................ 8
BQ _ BR __
Hex Head Screw, 5/16-t8 x 1-I14 .....................8
Hex Head Screw, 5/16-!8 x 5/8 ...................... 3
BN
.© os )
lilllt i p,BL
13
8Z
L_t BW
AB
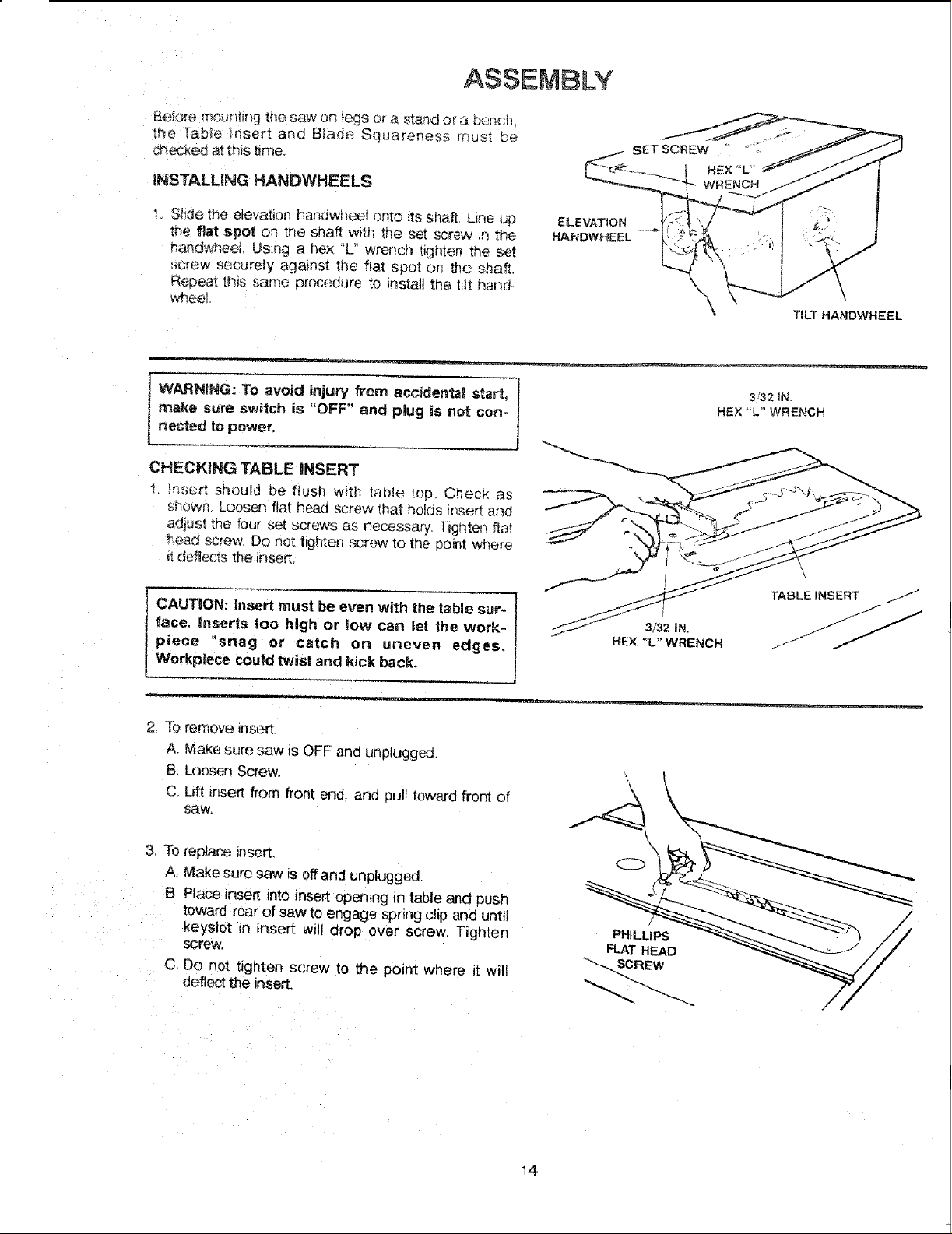
ASSEMBLY
Before mounting the saw on tegs or a stand or a bench,
the Table _nsert and Btade Squareness must be
Choked atthis time.
INSTALLING HANDWHEELS
1. Stide t,_e _evation bandy,heel onto its shaft. Line up
the flat spot on the shaft with the set screw in the
ELEVATION
HANDWHEEL
handv,dseol.Using a hex "L_Iwrench tighten the set
screw securely against the flat spot on the shaft,.
Repeat this same proco-xJureto instaJl the ti_t hand-
wheek
I WARNtNG: To avoid injury from accidental start, 3732_N.
I make sure switch is "OFF" and plug is not con- HEX "'L"WRENCH
t netted to power.
\ TILT HANDWHEEL
CHECKING TABLE iNSERT
_nsert should be flush with tabie top Chec_ as
shown Loosen flat head screw that holds insert and
adjus! the four set screws as necessary [ighten flat
r'_ead screw Do not tighten screw to the point where
_tdeflects the inse£
CAUTION: insert must be even with the table sur-
face. inserts too high or low can let the work-
piece "snag or catch on uneven edges.
Workplece could twist and kick back.
2 To remove insert,
A. Make sure saw _sOFF an(] unplugged.
B Loosen Screw.
C, Luft =nsert from front end, and _ull toward front of
SaW.
3. To replace insert,
A Make sure saw is off and unplugged.
B. Place insert into insert opening m table and push
toward rear of saw to engage spring clip and until
keyslot =n insert will drop over screw. Tigl_ten
screw.
C, Do not tighten screw to the point where it will
deflect the insert.
/
PHILLIPS
FLAT HEAD
SCREW
14
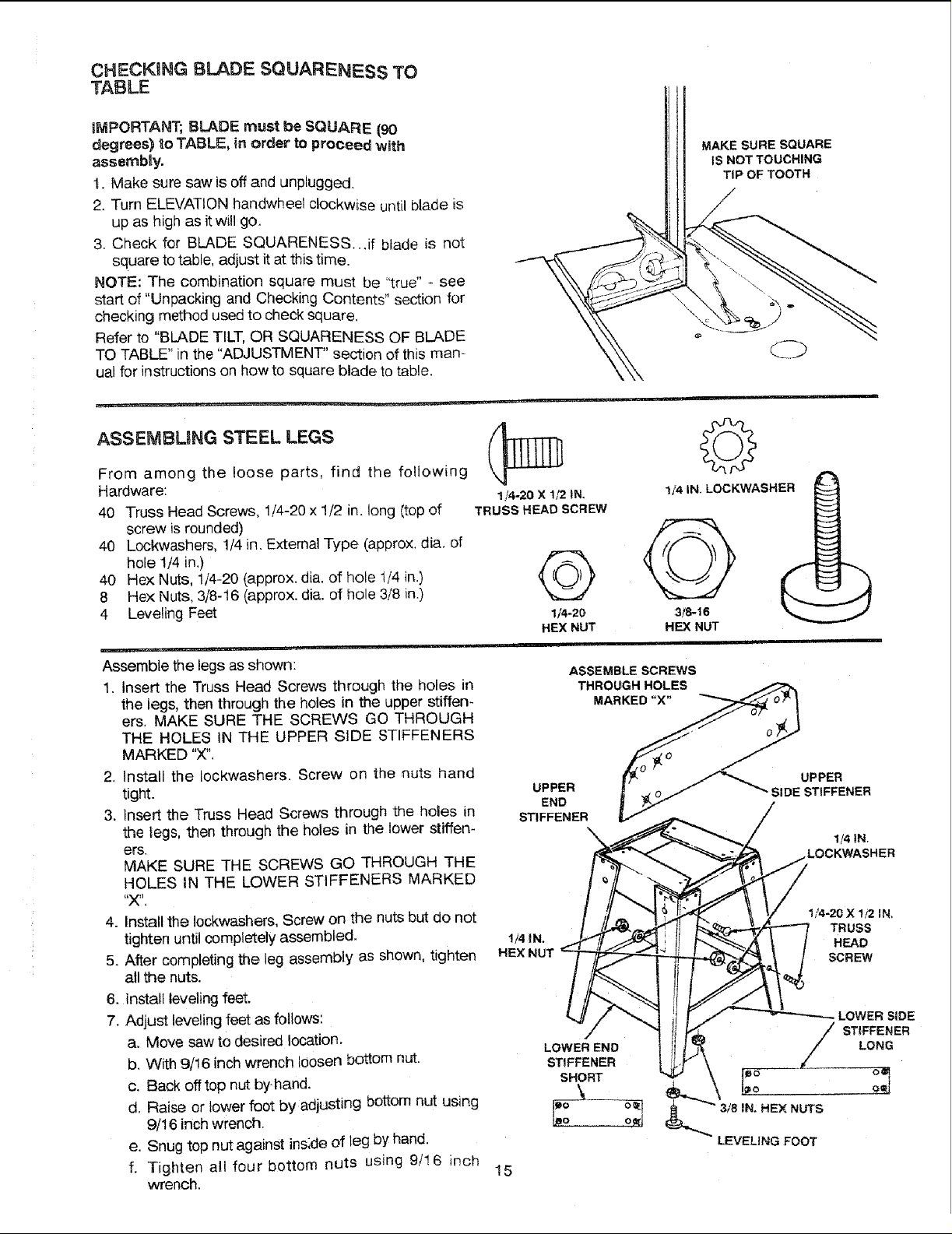
CHECKgNG BLADE SQUARENESS TO
TABLE
IMPORTANT; BLADE must be SQUARE (90
degrees) to TABLE, in order to proceed with
assemblly.
1. Make sure saw is offand unplugged,
2. Turn ELEVATION handwheel clockwise until blade is
up as high as it will go,
3, Check for BLADE SQUARENESS..,if blade is not
square to table, adjust it at thistime,
NOTE: The combination square must be "true" - see
start of "Unpacking and Checking Contents" section for
checking method used to check square.
Refer to "BLADE TILT, OR SQUARENESS OF BLADE
TO TABLE" in the "ADJUSTMENT" section of this man-
ual for instructions on how to square blade to table.
ASSEMBLING STEEL LEGS
From among the loose parts, find the following
Hardware:
40 Truss Head Screws, 1/4-20 x !/2 in. long Itop of
screw is rounded)
40 Lockwashers, 1/4 in. External Type (approx. diG, of
hole 1/4 in.)
40 He× Nuts, 1/4-20 (approx. diG.of hole 1/4 in.)
8 Hex Nuts, 3/8-16 (approx. diG.of hole 3/8 in.)
4 Leveling Feet
....... i== I,i .
Assemble the legs as shown:
1. Insert the Truss Head Screws through the holes in
the legs, then through the holes in the upper stiffen-
ers. MAKE SURE THE SCREWS GO THROUGH
THE HOLES IN THE UPPER SIDE STIFFENERS
MARKED "X".
2. Install the Iockwashers. Screw on the nuts hand
tight.
3. Insert the Truss Head Screws through the holes in
the Legs,then through the holes in the lower stiffen-
ers.
MAKE SURE THE SCREWS GO THROUGH THE
HOLES IN THE LOWER STIFFENERS MARKED
1/4-20 X 1/2 IN.
TRUSS HEAD SCREW
©
1/4-20
HEX NUT
MAKE SURE SQUARE
IS NOT TOUCHING
TIP OF TOOTH
1/4 IN. LOCKWASHER
___
HEX NUT
4. Install the Iockwashers, Screw on the nuts but do not
tighten until completely assembled,
5. After completing the leg assembly as shown, tighten
all the nuts.
6. install leveling feet.
7. Adjust leveling feet as follows:
a. Move saw to desired location.
b. With 9/! 6 inch wrench loosen bottom nut,
c. Back offtop nut byhand.
d, Raise or lower foot by adjusting bottom nut using
9/16 inch wrench.
e. Snug top nut against ins;de of leg by hand.
f. Tighten all four bottom nuts using 9/16 inch
wrench,
15
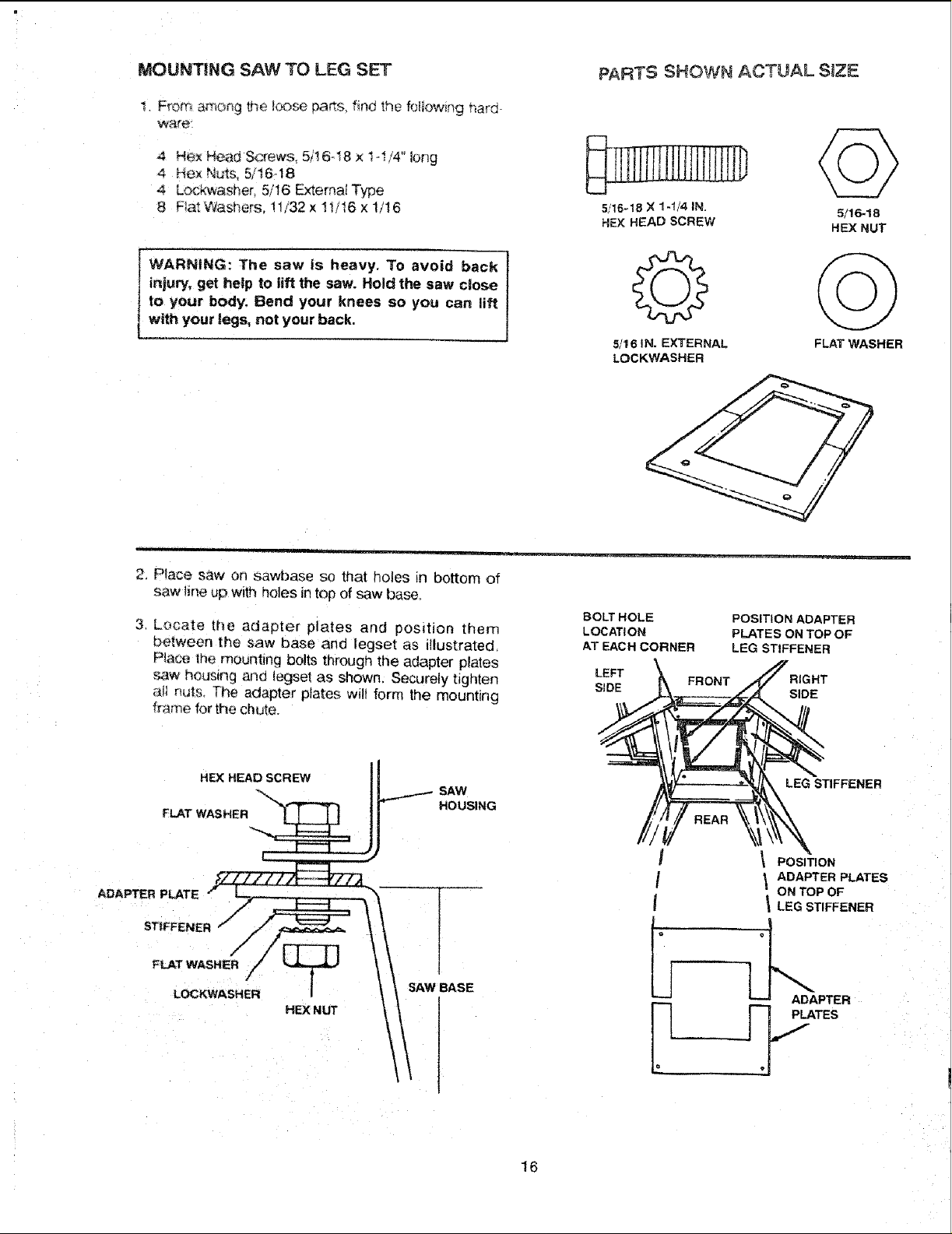
MOUNTING SAW TO LEG SET
I. From a_o_g the tcx_se pa_s, find the following hard
water
4 Hex Head Screws, 5/16..18 x t-I/4" long
4 Hex ,_quts,5/16.18
4 Lockwasher, 5/16 External Type
8 Flat Washers, !1/32 x t!/16 x 1/16
WARNING: The saw is heavy. To avoid back
injury, get help to lift the saw. Hold the saw close
to your body; Bend your knees so you can lift
with your legs, not your back.
PARTS SHOWN ACTUAL S_ZE
5/16-18 ;41-t/4 IN.
HEXHEAD SCREW
5/16 IN. EXTERNAL
LOCKWASHER
5/16-18
HEX NUT
FLATWASHER
2, Place saw or_ sawbase so that holes in bottom of
saw line up w_th holes in top of saw base.
3, Locate tt_e adapter plates and position them
between the _aw base and legset as illustrated.
Place, the mountin¢l bolts through the adapter plates
.saw houstng an(] legset as shown. Securely tigi_ten
a_ nuts. The adapter plates wi!t form the mounting
tr;_me for the chute.
BOLT HOLE
LOCATION
AT EACH OORNER
LEFT
SIDE SIDE
o
POSITION ADAPTER
PLATES ON TOP OF
LEG STIFFENER
FRONT RIGHT
_ADAPTER
LEG STIFFENER
POSITION
ADAPTER PLATES
ON TOP OF
LEG STIFFENER
PLATES
16
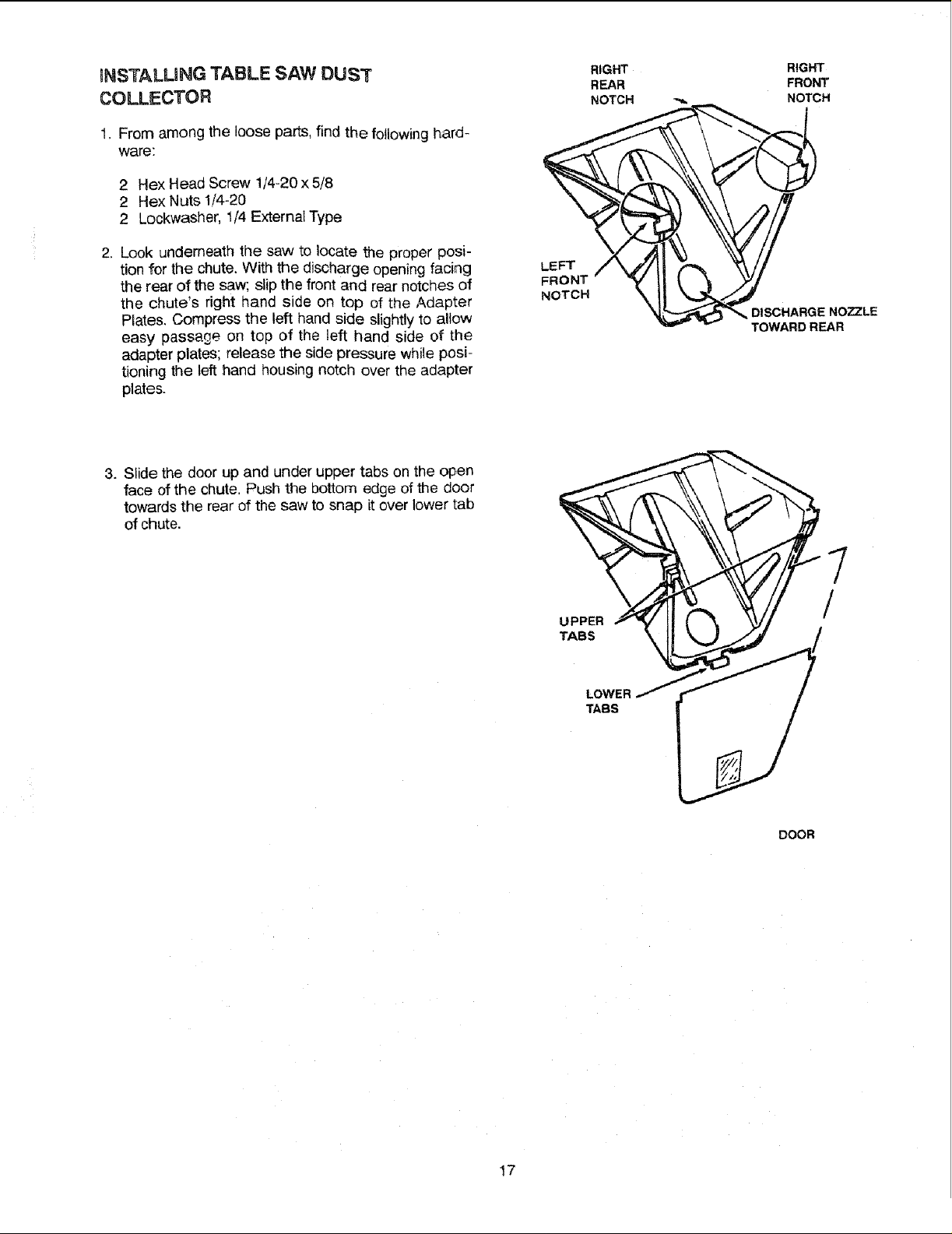
mNSTA.LLING TABLE SAW DUST
COLLECTOR
1. From among the loose parts, find the following hard-
ware:
2 Hex Head Screw 1/4-20 x 5/8
2 Hex Nuts 1/'4-20
2 Lockwasher, t/4 External Type
RIGHT RIGHT
REAR FRONT
NOTCH _ NOTCH
2, Look underneath the saw to locate the proper posi-
tion for the chute. With the discharge openingfacing
the rear of the saw; slip the front and rear notches of
the chute's right hand side on top of the Adapter
Plates. Compress the left hand side slightly to allow
easy passage on top of the left hand side of the
adapter plates; release the side pressure while posi-
tioning the left hand housing notch over the adapter
plates.
3. Slide the door up and under upper tabs on the open
face of the chute. Push the bottom edge of the door
towards the rear of the saw to snap it over lower tab
of chute.
LEFT
FRONT
NOTCH
DISCHARGE NOZZLE
TOWARD REAR
UPPER
LOWER _
TABS
17
DOOR
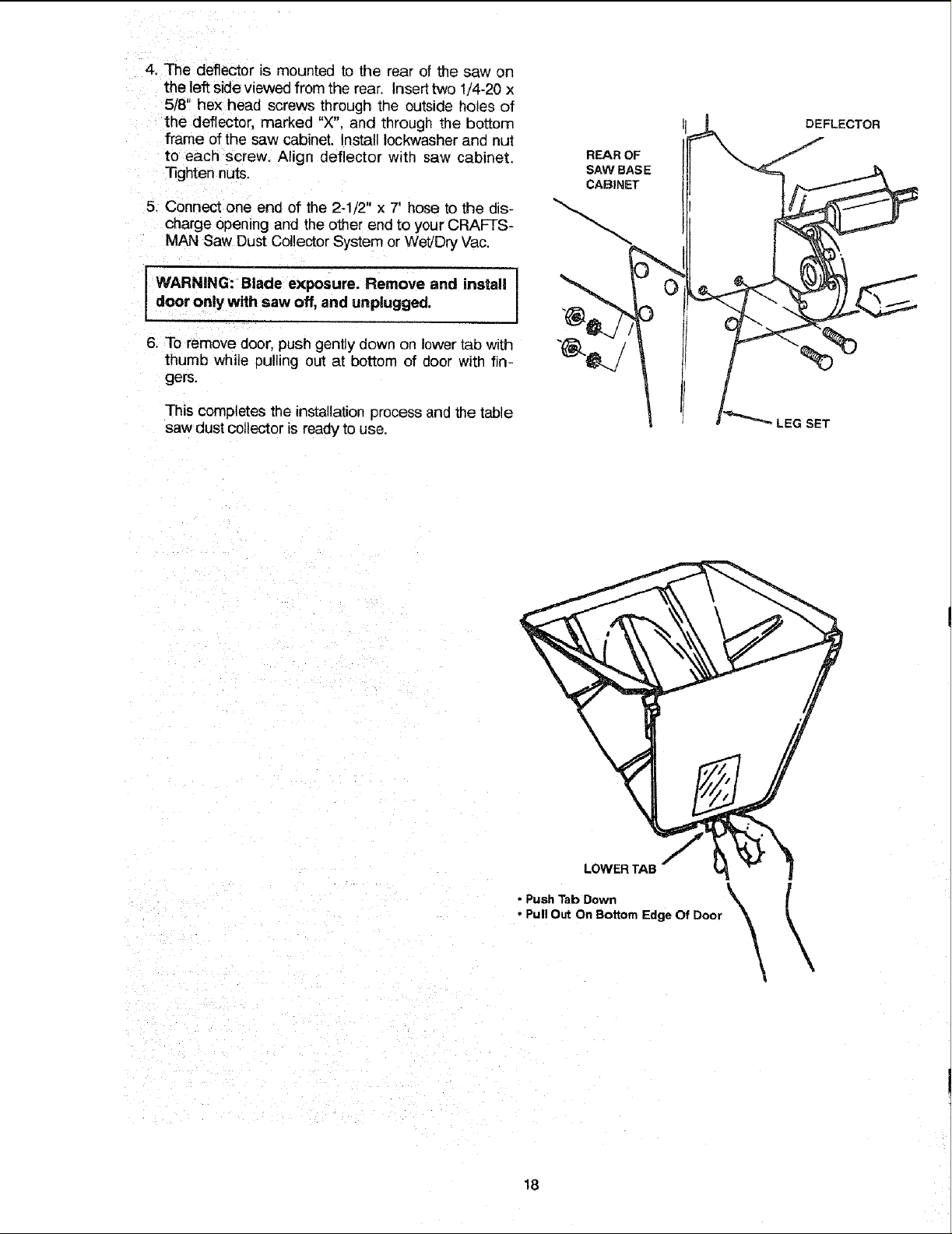
4.Thedeflectorismountedtotherearofthesawon
theleftsideviewedfromtherear.Inserttwo1/4-20x
5/8"hexheadscrewsthroughtheoutsideholesof
thedeflector,marked"X".andthroughthebottom
frameofthesawcabinet.InstallIockwasherandnut
to eachscrew.Aligndeflectorwithsawcabinet.
"l]ghtennuts.
5.Connectoneendofthe2-1/2"x7'hosetothedis-
chargeopeningandtheotherendtoyourCRAFTS-
MANSawDustCollectorSystemorWet/DryVac.
I WARNING: Blade exposure. Remove and install J
door only with saw off, and unplugged,
6. To remove door, push gently down on lower tab with
thumb while Dulling OUtat bottom of door with fin-
gers.
REAR OF
SAW BASE
CABINET
0
This completes the installation process and the table
saw dust collector is ready to use.
LEG SET
LOWER TAB
• Push Tab Down X
• Pull Out On Bottom Edge Of Door
18
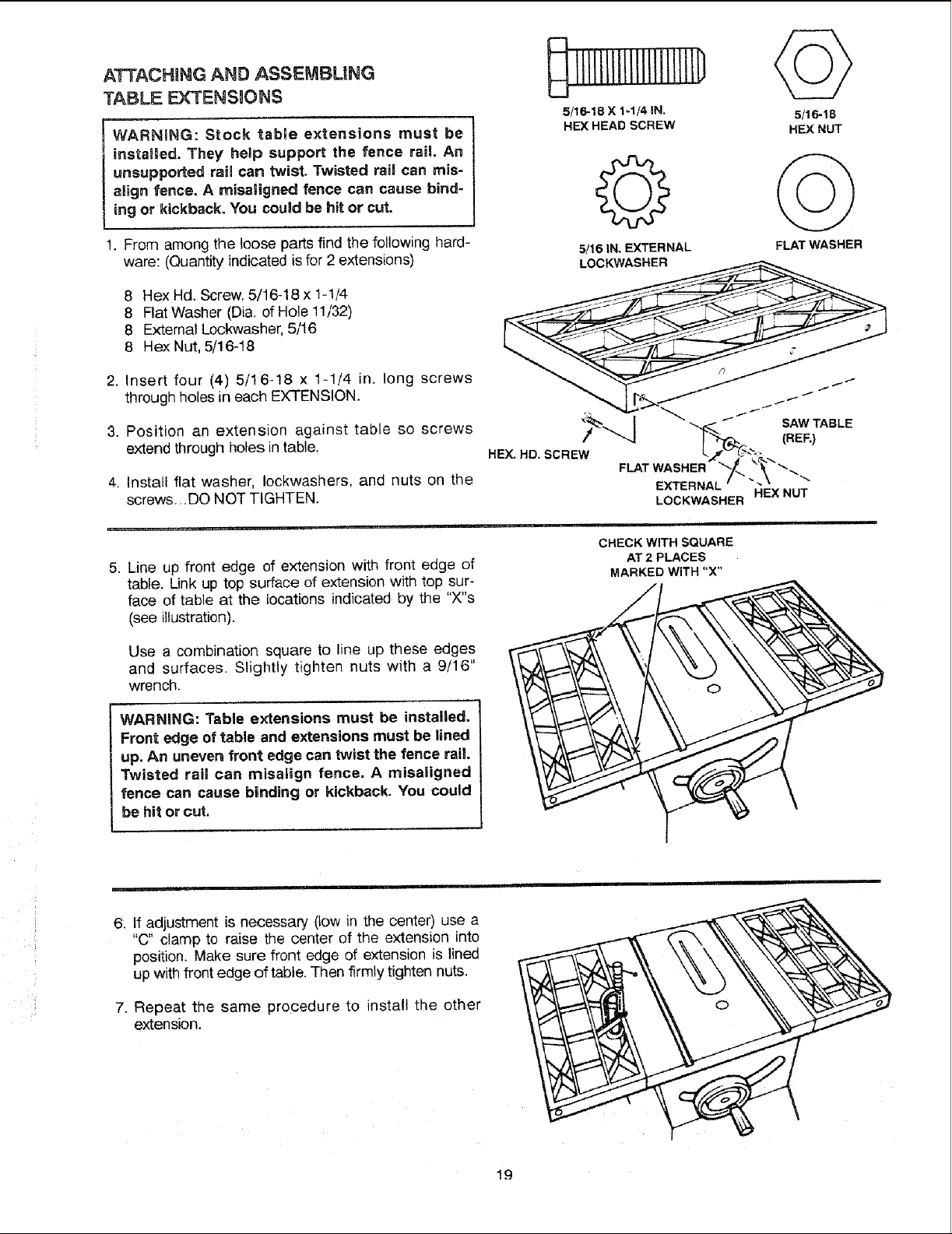
ATTACHmNG AND ASSEMBUNG
TABLE EXTENSmONS
WARNING: Stock table extensions must be
installed. They hetp support the fence rail. An
unsupported rail can twist. Twisted rail can mis-
aiign fence. A misaligned fence can cause bind-
ing or kickback. You could be hit or cut.
1111111111111i!111111)
5/16-18 X 1-1/4 IN.
HEX HEAD SCREW
5/16-18
HEX NUT
Q
1. From among the loose parts find the following hard-
ware: (Quantity indicated is for 2 extensions)
8 Hex Hd. Screw. 5/16-18 x 1-!/4
8 Flat Washer (Dia. of Hole 11/32)
8 External Lockwasher, 5/16
8 Hex Nut, 5/16-18
2. Insert four (4) 5/16-18 x 1-1/4 in. long screws
through holes in each EXTENSION.
3. Position an extension against table so screws
extend through holes in table.
4. Install flat washer, Iockwashers, and nuts on the
screws... DO NOT TIGHTEN.
.
Line up front edge of extension with front edge of
table. Link up top surface of extension with top sur-
face of table at the locations indicated by the "X"s
(see illustration).
Use a combination square to line up these edges
and surfaces. Slightly tighten nuts with a 9/16"
wrench.
5/16 IN. EXTERNAL
CHECK WITH SQUARE
AT 2 PLACES
MARKED WITH "X"
FLAT WASHER
WARNING: Table extensions must be installed.
Front edge of table and extensions must be lined
up. An uneven front edge can twist the fence rail.
Twisted rail can misaiign fence. A misaligned
fence can cause binding or kickback. You could
be hit or cut.
6: If adjustment is necessary (tow in the center) use a
"C" clamp to raise the center of the extension into
position. Make sure front edge of extension is lined
up with front edge of table. Then firmly tighten nuts.
7. Repeat the same procedure to insta!l the other
extension.
19
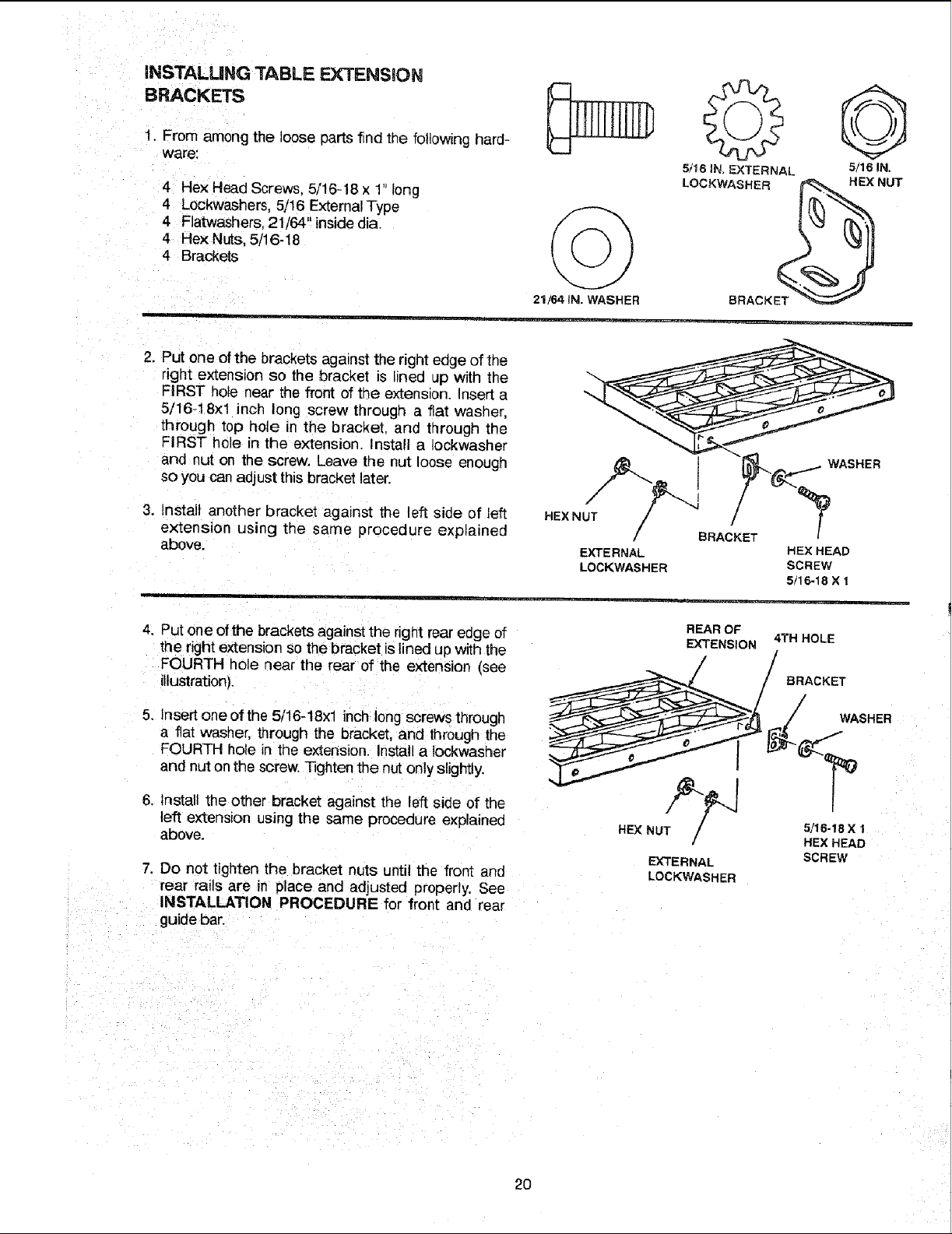
iNSTALLiNG TABLE EXTENSION
BRACKETS
1. From among the loose parts find the following hard-
ware:
4 Hex Head Screws. 5/16-18x 1" long
4 Lockwashers, 5/16 External Type
4 Flatwashers. 21/64" inside dia.
4 Hex Nuts, 5/16-18
4 Brackets
2. Put one ofthe brackets against the rightedge of the
right extension so the bracket is lined up with the
FIRST hole near the front of the extensior Inserta
5/16-18xl inct_ long screw through a fiat washer,
through top hole in the bracket, and through the
FIRST hole in the extension. Install a Iockwasher
and nut on the screw. Leave the nut loose enough
so you can adjust this bracket later.
5/16 IN, EXTERNAL 5/16 IN.
21/64 IN. WASHER
3. tnstalt another bracket against the left side of left
extension using the same procedure explained
above.
4. Put one of the brackets against the right rearedge of
the right extension so the bracket is lined up with the
FOURTH hole near the rear of the extension (see
illustration).
5. Insert one of the 5/16-18xl inch long screws through
a fiat washer, through the bracket, and through the
FOURTH hole in the extension. Install a Iockwasher
and nut on the screw. Tighten the nut only slightly.
6. Install the other bracket against the left side of the
left extension using the same procedure explained
above.
7. Do not tighten the bracket nuts until the front and
rear rails are in place and adjusted properly. See
INSTALLATION PROCEDURE for front and rear
guide bar.
HEX NUT /
/ BRACKET
EXTERNAL HEX HEAD
LOCKWASHER SCREW
REAR OF
EXTENSION 4TH HOLE
HEX NUT_/_
EXTERNAL
LOCKWASHER
5tl 6-18 X 1
BRACKET
WASHER
5/16-18 X 1
HEX HEAD
SCREW
2O
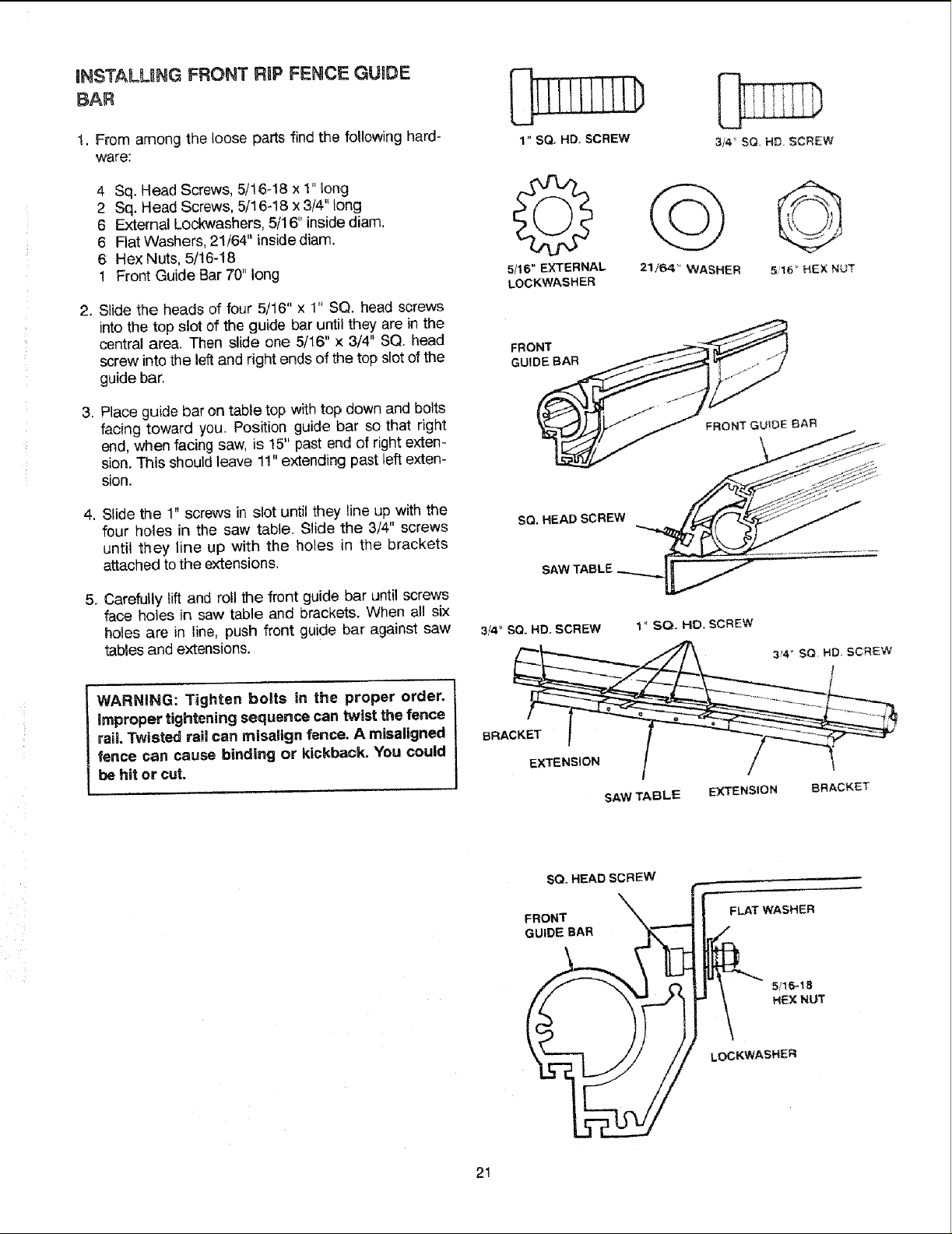
RNSTALLUNG FRONT RIP FENCE GUIDE
BAR
1. From among the loose parts find the following hard-
ware:
4 Sq. Head Screws, 5/16-18 x 1" long
2 Sq. Head Screws, 5/16-18 x 3/4" long
6 External Lockwashers, 5/16" inside diam.
6 Flat Washers, 21/64" inside diam.
6 Hex Nuts, 5/16-18
1 Front Guide Bar 70" long
,
Slide the heads of four 5/16" x 1" SQ. head screws
into the top slot of the guide bar until they are in the
central area. Then slide one 5/16" x 3/4" SQ, head
screw into the left and right ends of the top slot of the
guide bar,
,
Place guide bar on table top withtop down and bolts
facing toward you. Position guide bar so that right
end, when facing saw, is 15" past end of right exten-
sion. This should leave 11" extending past left exten-
sion.
4.
Slide the 1" screws in slot until they line up with the
four holes in the saw table. Slide the 3/4" screws
until they line up with the holes in the brackets
attached to the extensions,
1" SQ, HD. SCREW
5/16" EXTERNAL
LOCKWASHER
SQ. HEADSCREW
21164" WASHER
.
Carefully lift and roll the front guide bar until screws
face holes in saw table and brackets. When all six
holes are in line, push front guide bar against saw
tables and extensions.
WARNING: Tighten bolts in the proper order.
improper tightening sequence can twist the fence
rail Twisted rail can misalign fence, A misaligned
fence can cause binding or kickback. You could
be hit or cut.
3/4" SO, HD. SCREW 1" SQ, HD. SCREW
SAW TABLE
SO. HEAD SCREW
FRONT
GUIDE BAR
EXTENSION
FLAT WASHER
8RACKET
511_1B
HEX NUT
LOCKWASHER
2!
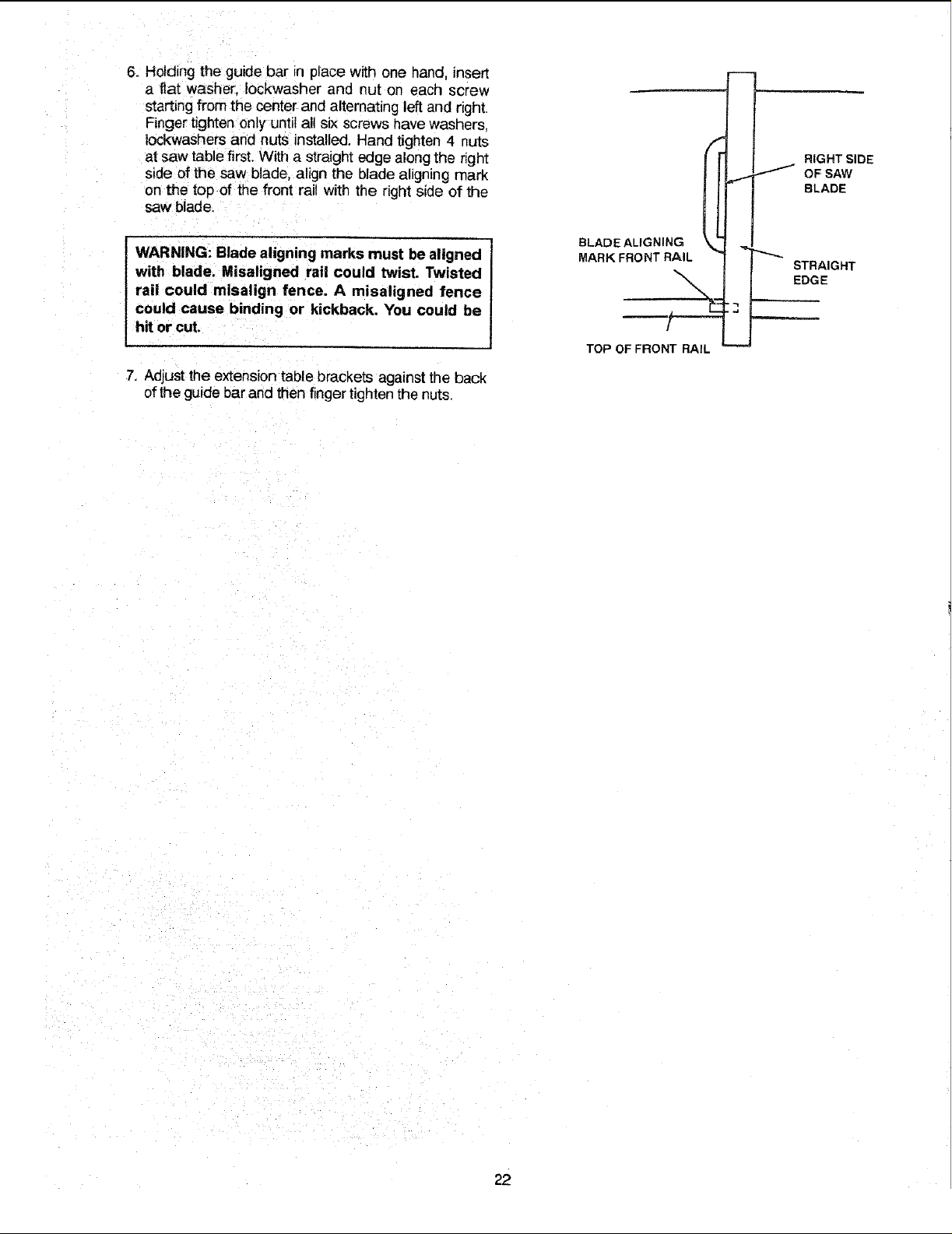
6. Holding the guide bar in place with one hand, insert
a flat washer, Iockwasher and nut on each screw
starting from the center and alternating left and right.
=inger tighten only until all six screws nave washers.
lockwashers and nuts installed. Hand tighten 4 nuts
at saw table first. With a straight edge along the right
side of the saw blade, align the blade aligning mark
on the top of the front rail with the right side of the
saw blade.
RIGHT SIDE
OFSAW
BLADE
WARNING: Blade aligning marks must be aligned I
with blade. Misaligned rail could twist. Twisted
rail could misalign fence. A misaligned fence
could cause binding or kickback. You could be
hit or cuL
7. Adjust the extension table brackets against the back
of the guide barand then finger tighten the nuts.
!
BLADE ALIGNING
MARK FRONT RAIL
TOP OF FRONT RAIL
STRAIGHT
EDGE
.J
22
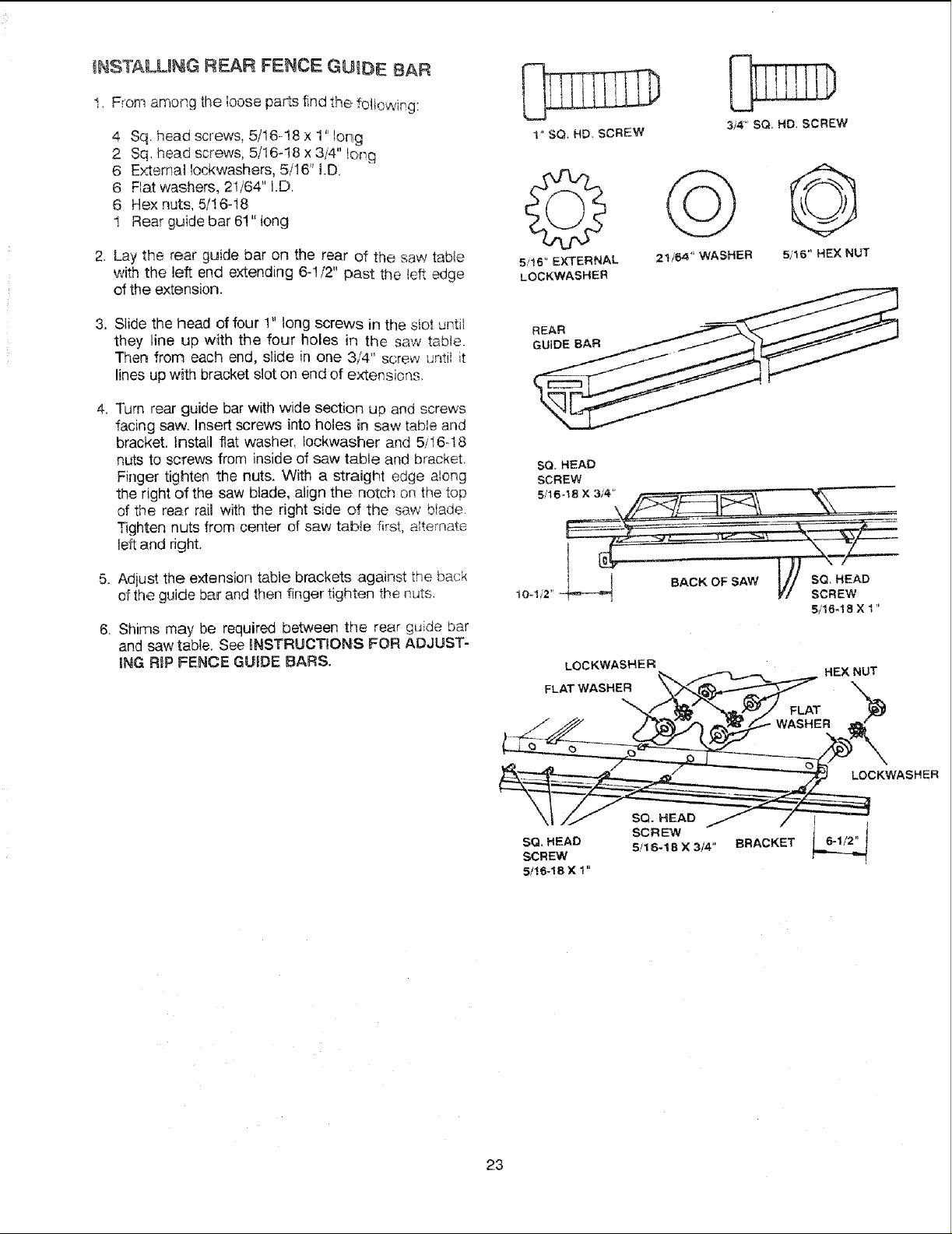
tNSTALU_G REAR FENCE GUIDE BAR
I. From among tt_e _ooseparts find the following:
4 Sq. head screws, 5/16--18 x 1" long
2 Sq. head screws, 5/16-18 x 3/4" torT,q
6 Externat lockwashers, 5/16" I.D.
6 Flat washers, 21/64" I.D.
6 Hex nuts, 5/!6-18
1 Rear guide bar 6!" tong
3i4" SQ, HD. SCREW
2. Lay the rear guide bar on the rear of the saw table
with the left end extending 6-1/2" past the le_ edge
of the extension.
3, Slide the head of four 1" long screws in the siot until
they line up with the four holes in the saw tabMe.
Then from each end, slide in one 3,/4" screw untii it
lines up with bracket slot on end of extensions,
4. Turn rear guide bar with ,,vide section up and screws
facing saw. Insert screws into holes in saw table and
bracket. Install flat washer, lockwasher and 5/16-t8
nuts to screws from inside of saw table and bracket.
Finger tighten the nuts. With a straight edge along
the right of the saw blade, align the notch on the top
of the rear rail with the right side of the saw btade.
Tighten nuts from center of saw tab!e first, alternate
left and right.
5. Adjust the extension table brackets against the back
ofthe guide bar and then finger tighten the nuts.
6. Shims may be required between the rear guide bar
and saw table. See INSTRUCTIONS FOR ADJUST-
ING RIP FENCE GUIDE BARS.
5/t6" EXTERNAL 2t/64 '! WASHER 5/16" HEX NUT
LOCKWASHER
SQ HEAO
SCREW
5/16-
5/16-18 X 1"
LOCKWASHEP;
FLAT WASHER _,,._ HEX _T
SQ. HEAD 511 6-! B X 3/4" BRACKET
SCREW
5/16-18 X 1"
SCREW
23