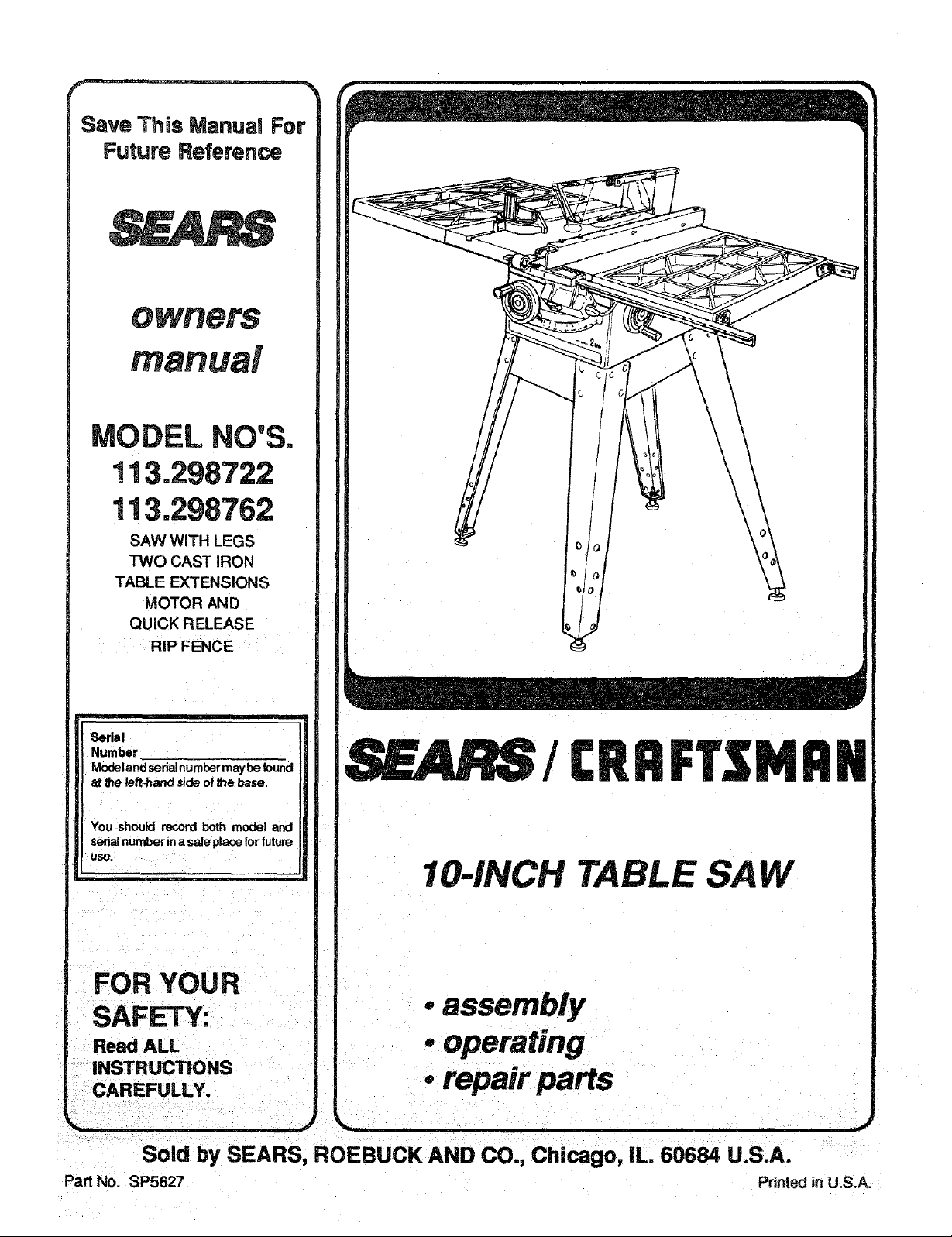
Save This Uanuam For
Future Reference
MODEL NO'S,
113o298722
113.298762
SAW WITH LEGS
TWO CAST IRON
TABLE EXTENSIONS
MOTOR AND
QUICK RELEASE
RiP FENCE
Serial
Number
Modelandserialnumbermaybefound
at theleft-handsideofthe base.
You should record both model and
serial number in a sale place for future
use.
SEAFW / CRRFTSMRH
IO.INCH TABLE SAW
FOR YOUR
SAFETY:
Read ALL
INSTRUCTIONS
CAREFULLY.
_,, illll
Sold by SEARS, ROEBUCK AND CO., Chicago, IL. 60684 U.S.A.
Part No. SP5627 Printed in U.S.A.
• assembly
ooperating
° repair parts
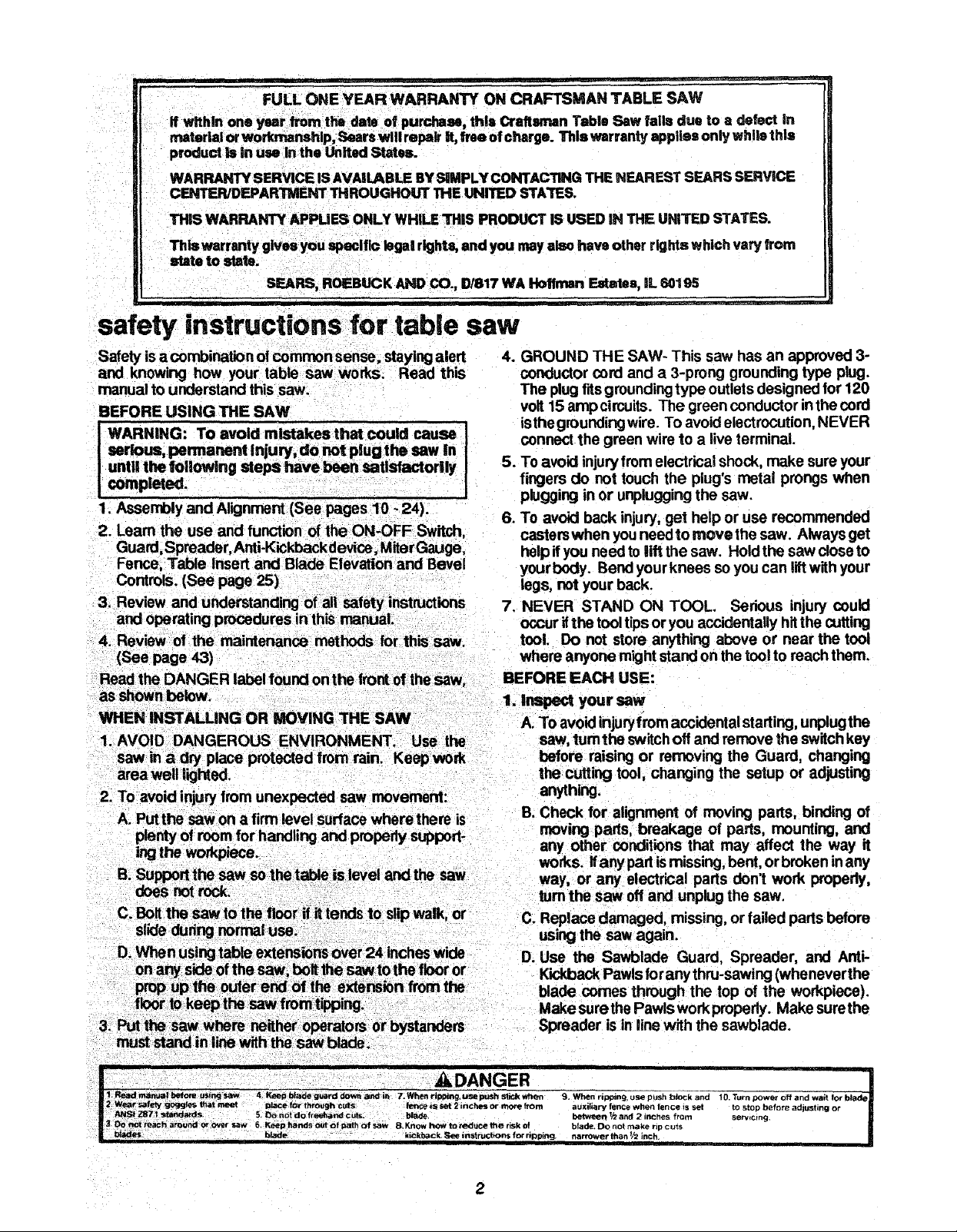
FULLONEYEARWARRANTYONCRAFTSMANTABLESAW
Ifwlth|noneyearfromthedaleof purchase,thisCraftsmanTableSawfallsdueto a defect in
mstedal orwo_manshlp, Sears will repair it, free ofcharge. This warrantyapplies onlywhile this
product is in use inthe United States.
WARRANTYSERVICE IS AVAILABLE BYSIMPLY CONTACTINGTHENEAREST SEARS SERVICE
CENTER/DEPARTMENT THROUGHOUT THE UNITED STATES.
THIS WARRANTY APPLIES ONLY WHILE THiS PRODUCTiS USEDIH THE UNITED STATES.
This warranty gives you specific legalrights, and you mayalso have other rightswhich vary from
state to state.
SEARS, ROEBUCK AND CO., D/817 WA Hoffman Estales, IL 60195
v .....
safety instructions for table saw
Safety isa combination of common sense, staying alert
and knowing how your table saw works. Read this
manual to understand this saw.
BEFORE USING THE SAW
serious, permanent Injury, do not plug the saw In
until the following steps have been satisfactorily
completed.
Guard, Spreader, Anti-Kickbackdevice, Miter Gauge,
Fence, Table Insert and Blade Elevation and Bevel
Controls. (See page 25)
4. Review of the maintenance methods for this saw. tool. Do not store anything above or near the tool
(See page 43) where anyone might stand on the tool to reach them.
Read the DANGER label found onthe front of the saw, BEFORE EACH USE:
4. GROUND THE SAW- This saw has an approved 3-
conductor cord and a 3-prong grounding type plug.
The plugfitsgrounding type outletsdesig ned for 120
volt 15 amp circuits. The green conductor inthe cord
isthegrounding wire. To avoid electrocution, NEVER
connect the green wire to a live terminal.
5. To avoid injuryfrom electrical shock, make sure your
fingers do not touch the plug's metal prongs when
plugging in or unpluggingthe saw.
6. To avoid back injury, get help or use recommended
casterswhen you need to move the saw. Always get
help if you need to lift the saw. Hold the saw close to
yourbody. Bend your knees soyou can liftwith your
legs, not your back.
7. NEVER STAND ON TOOL. Serious injury could
occur ifthe tooltips or you accidentally hitthe cutting
2. To avoid injury from unexpected saw movement:
anything.
B. Check for alignment of moving parts, binding of
A. Put the saw on a firm level surface where there is moving parts, breakage of parts, mounting, and
i
• _ua r_j . p gL,_rd down and i_ 7. When rtppixtg.use push stick when
II:_ _ goggles that meet place f_r through cut_ fence ,Isset 2 _nches or more from
ANSI 2:871 standa_s. 5. Do not do freehamd cuts. bla6_.
E 3. _notDotrot macfi around Or over saw 6. Keep hands out of path of saw 8. Know how to reduce the risk af
9. When riPPing, use push blOCk and 10. Turn _0owex off and walt fo_ blade
auxiliaw fence wherl fence _s set to stop before adjusting or
between V2 and 2 irt_hes from
blade. Do not nlake rip cuts |
narrower than _/2 inch __
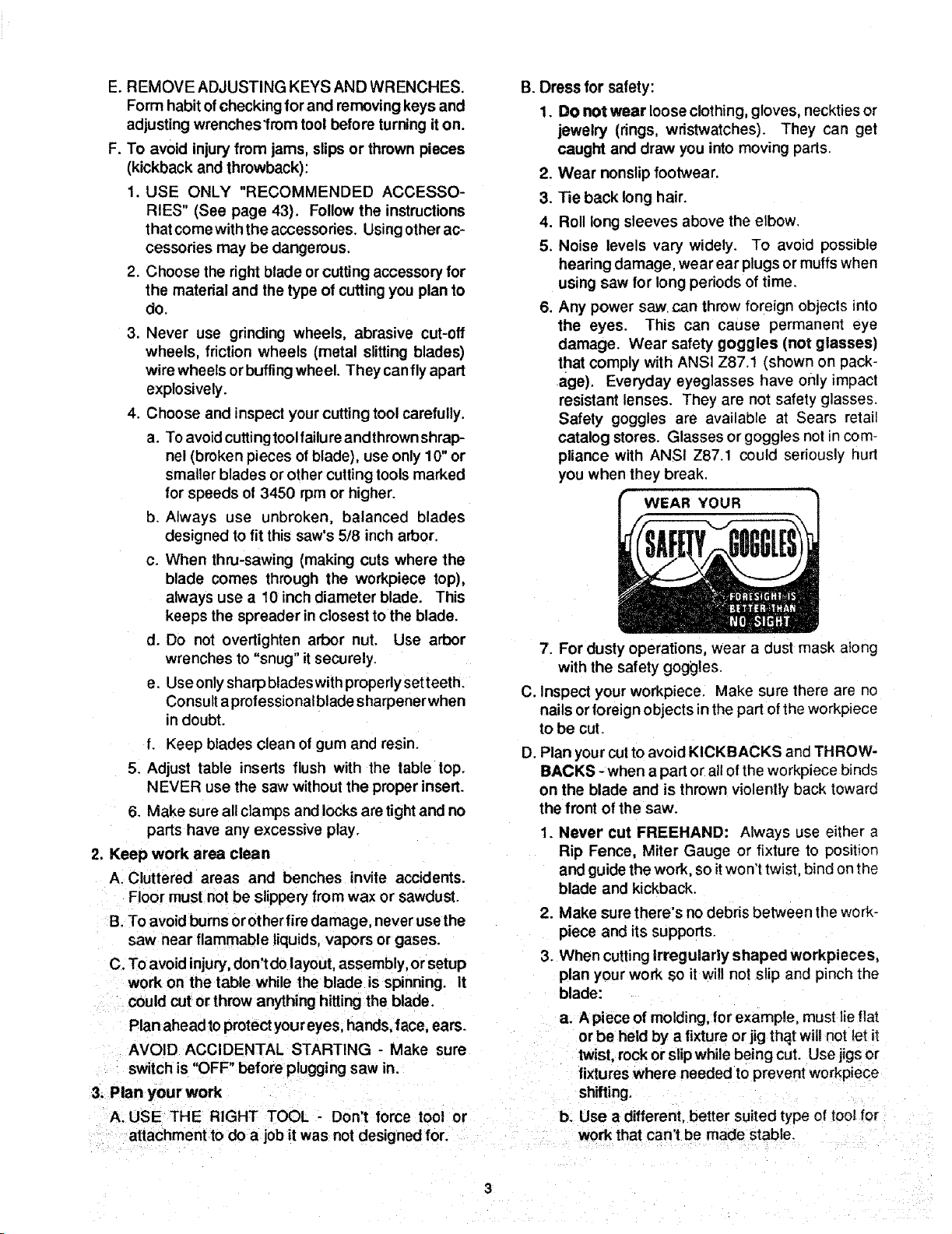
E. REMOVE ADJUSTING KEYS AND WRENCHES.
Form habitof checking for and removing keys and
adjusting wrencheslrem tool before turning it on.
F. To avoid injury from jams, slips or thrown pieces
(kickback and throwback):
1. USE ONLY "RECOMMENDED ACCESSO-
RIES" (See page 43). Follow the instructions
that come with the accessories. Using other ac-
cessories may be dangerous.
2. Choose the rightblade orcutting accessory for
the material and the type of cutting you plan to
do.
3. Never use grinding wheels, abrasive cut-off
wheels, friction wheels (metal slitting blades)
wire wheels orbuffing wheel. They canfly apart
explosively.
4. Choose and inspect your cutting tool carefully.
a. To avoidcuttingtoolfailureand thrownshrap-
nel (broken pieces ofblade), use only 10"or
smaller blades or other cutting tools marked
for speeds of 3450 rpm or higher.
b. Always use unbroken, balanced blades
designed to fit this saw's 5/8 inch arbor.
c. When thru-sawing (making cuts where the
blade comes through the workpiece top),
always use a 10 inch diameter blade. This
keeps the spreader in closest to the blade.
d. Do not overtighten arbor nut. Use arbor
wrenches to "snug"it securely.
e. Use onlysharpbladeswith properly setteeth.
Consulta professional bladesharpenerwhen
in doubt.
f. Keep blades clean of gum and resin.
5. Adjust table inserts flush with the table top.
NEVER use the saw without the proper insert.
6. Make sure all clamps and locksare tight and no
parts have any excessive play.
2. Keep work area clean
A. Cluttered areas and benches invite accidents.
Floor must not be slippery from wax or sawdust.
B. To avoid burnsor otherfiredamage, never usethe
saw near flammable liquids, vapors or gases.
C. To avoid injury,don't do layout, assembly, or setup
work on the table while the blade is spinning. It
could cut or throw anything hitting the blade.
Plan ahead to protectyoureyes, hands,face, ears.
AVOID ACCIDENTAL STARTING - Make sure
switch is "OFF" before plugging saw in.
3. Plan your work
A. USE THE RIGHT TOOL - Don't force toot or
attachmentto do a jobit was not designed for.
B. Dress for safety:
1. Do not wear looseclothing, gloves, neckties or
jewelry (dngs, wristwatches). They can get
caught and draw you into moving parts.
2. Wear nonslip footwear.
3. Tie back long hair.
4. Roll long sleeves above the elbow.
5. Noise levels vary widely. To avoid possible
hearing damage, wear ear plugsor muffs when
using saw for long periods of time.
6. Any power saw. can throw foreign objects into
the eyes. This can cause permanent eye
damage. Wear safety goggles (not glasses)
that comply with ANSI Z87.1 (shown on pack-
age). Everyday eyeglasses have only impact
resistant lenses. They are not safety glasses.
Safety goggles are available at Sears retail
catalog stores. Glasses or goggles not in com-
pliance with ANSI Z87.1 could seriously hurt
you when they break.
WEAR YOUR
7. For dusty operations, wear a dust mask along
with the safety goggles.
C. Inspect your workpiece. Make sure there are no
nails or foreign objects in the part of the workplece
to be cut.
D. Plan your cut to avoid KICKBACKS and THROW-
BACKS - when a part or all of the workpiece binds
on the blade and is thrown violently back toward
the front of the saw.
1. Never cut FREEHAND: Always use either a
Rip Fence, Miter Gauge or fixture to position
and guide the work, so itwon't twist, bind on the
blade and kickback.
2. Make sure there's no debris between 1ne work-
piece and its supports.
3. When cutting Irregularly shaped workpieces,
plan your work so it will not slip and pinch the
blade:
a. A piece of molding, for example, must lieflat
or be held by a fixture or jig that wiU not let it
twist, rock or slip while being cut. Use jigs or
fixtures where needed to prevent workpiece
shifting.
b. Use a different, better suited type of toot for
work that can't be made stable.
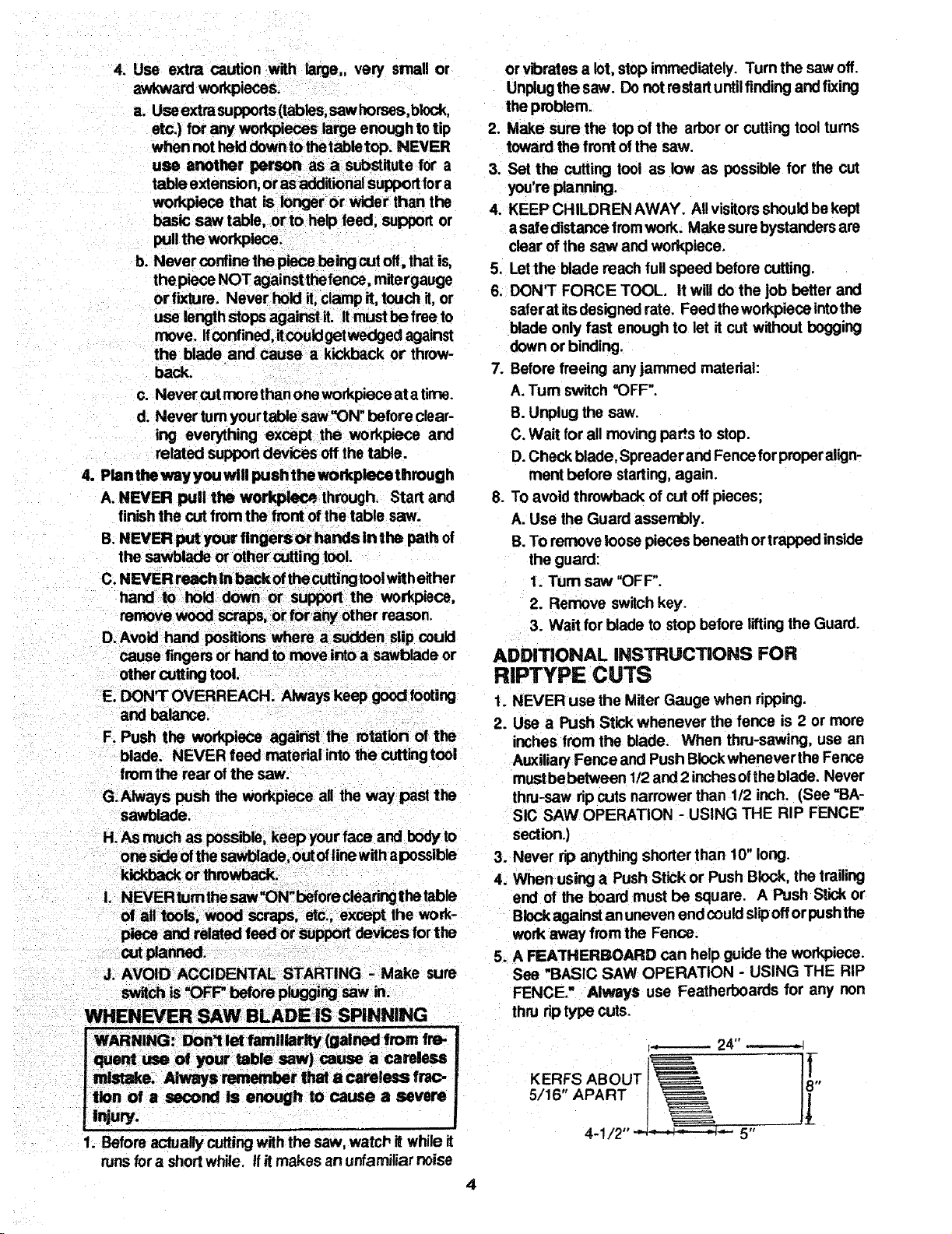
4. Use extra caution with large,, very small or
awkwardworkpisces.
a. Use extra supports(tables, sawhorses,block,
etc.) for any workpieces large enough totip
when not hell down to thetable top. NEVER
uSe another person as a substitute for a
table extension, or as additional support fora
workpiece that is longer or wider than the
basic saw table, orto helpfeed, support or
pull the workpisce.
b. Never confine the piece being cut off, that is,
the piece NOT againstthe fence, mitergauge
or fixture. Never hold it,clamp it,touch it, or
use length stops against it. Itmust be free to
move. Ifconfined,itcouldgetwedged against
the blade and cause a kickback or throw-
back.
c. Never cutmorethan one workpiece at a time.
d. Never turnyourtable saw"ON" before clear-
ing everything except the workpiece and
related support devices off the table.
4, Planthawayyouwill pushtheworkplecethrough
A. NEVER pull the workpleo_ through. Start and
finishthe cut from the front of the table saw.
B. NEVER put your fingers or hands in the path of
the sawblade or other cutting tool.
C. NEVER reach In back ofthe cuttingtoolwith either
hand to hold down or support the workpiece,
remove wood scraps, or for any other reason.
D. Avoid hand positions where a sudden slip could
cause fingers or handto move into a sawblade or
other cutting tool.
E. DON'T"OVERREACH. Always keep good footing
and balance.
F. Push the workpisce against the rotation of the
blade. NEVER feed material intothe cuttingtool
from the rear ofthe saw.
G. Always push the workpiece all the way past the
sawblade.
H. As much as possible,keep your face and body to
one skJeofthe sawblade, outof line with apossible
kickback or throwback.
I. NEVERtum the saw =ON" before cieadngthe table
of all tools, wood scraps, etc., except the work-
piece and related feed orsupport devices for the
cutp nned.
J. AVOID ACCIDENTAL STARTING - Make sure
switch is =OFF" before plugging saw in.
WHENEVER SAW BLADE iS SPINNING
or vibrates a lot,stop immediately. Turn the saw off.
Unplugthe saw. Do not restart untilfinding andfixing
the problem.
2. Make sure the top of the arbor or cutting tool turns
toward the front of the saw.
3. Set the cutting tool as low as possible for the cut
you're planning.
4. KEEP CHILDREN AWAY. All visitorsshouldbe kept
a safe distance fromwork. Make surebystanders are
clear of the saw and workplece.
5. Let the blade reach full speed before cutting.
6. DON'T FORCE TOOL. It will do the job better and
saferat its designedrate. Feed theworkpiece intothe
blade only fast enough to let it cut without bogging
down or binding.
7. Before treeing any jammed material
A. Turn switch "OFF".
B. Unplug the saw.
C. Wait for all movingpars to stop.
D. Check blade, Spreader and Fence forproperalign-
ment before starting, again.
8. To avoid throwback of cut off pieces;
A. Use the Guard assembly.
B. To remove loose pieces beneath ortrapped inside
the guard:
1. Turn saw "OFF".
2. Remove switch key.
3. Wait for blade to stop before liftingthe Guard.
ADDITIONAL INSTRUCTIONS FOR
RIPTYPE CUTS
1. NEVER use the Miter Gauge when ripping.
2. Use a Push Stick whenever the fence is 2 or more
inches from the blade. When thru-sawing, use an
AuxiliaryFence and Push Blockwhenever the Fence
mustbebetween 1/2 and2 inchesofthe blade. Never
thru-saw ripcuts narrower than 1/2 inch. (See =BA-
SIC SAW OPERATION - USING THE RIP FENCE"
section.)
3. Never rip anything shorter than 10" long.
4. When using a Push Stick or Push Block, the trailing
end of the beard must be square. A Push Stick or
Blockagainst an uneven end could slipofforpushthe
work away from the Fence.
5. A FEATHERBOARD can help guide the workpiece.
See "BASIC SAW OPERATION - USING THE RIP
FENCE." Always use Featherboards for any non
thru riptype cuts.
WARNING: Don't let familiarity (gained from fie- I
tion of a second Is enough to cause a Severe
Injury.
1. Before actually cuttingwith the saw, watcl_it while it
runsfor a shortwhile, if it makes an unfamiliar noise
J
4
+++o+,
5/16" APART
4-1/2' +- 5"
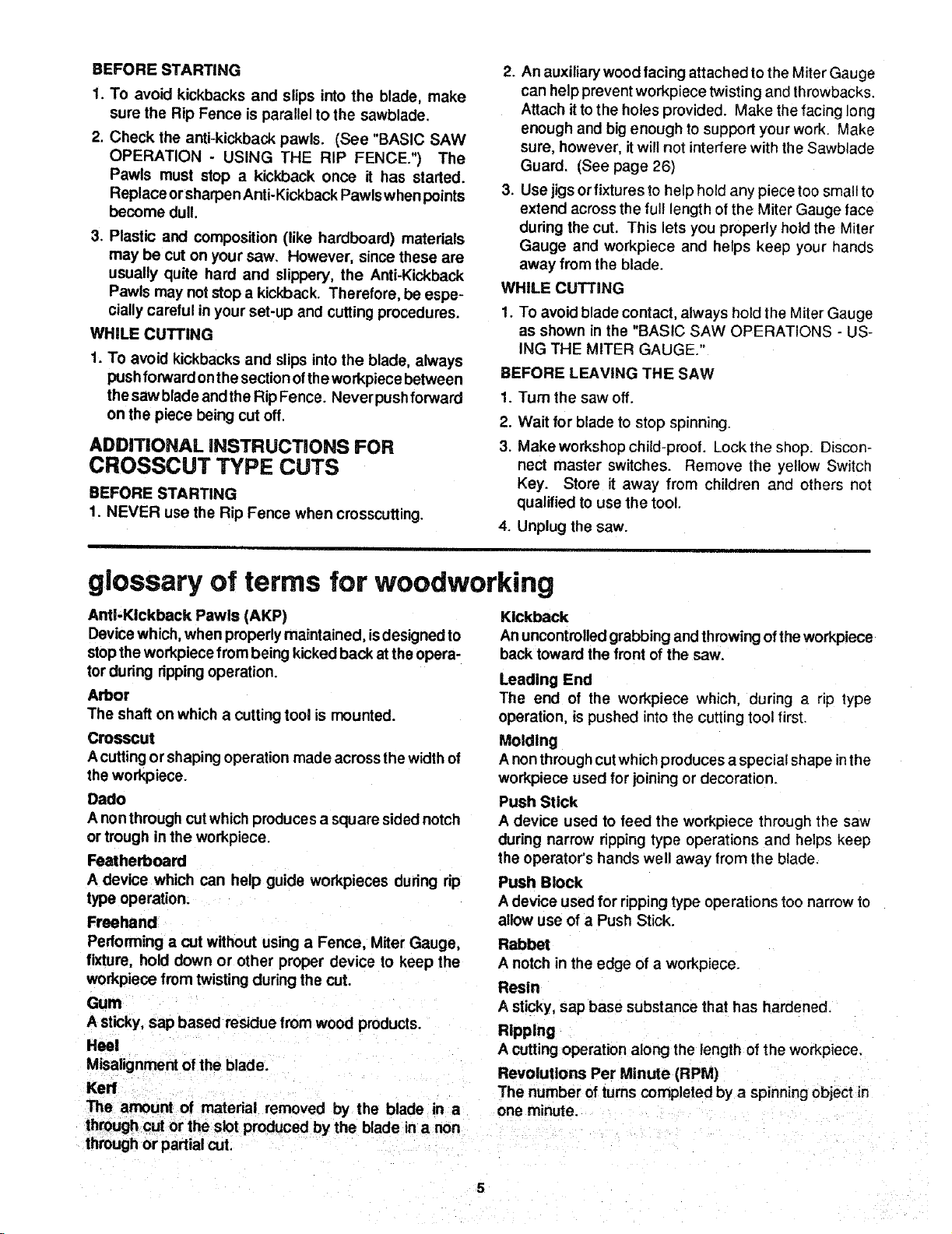
BEFORE STARTING
1. To avoid kickbacks and slips into the blade, make
sure the Rip Fence is parallel to the sawblade.
2. Check the anti-kickback pawls. (See "BASIC SAW
OPERATION - USING THE RIP FENCE.") The
Pawls must stop a kickback once it has started.
Replace orsharpen Anti-KickbackPawls when points
become dull.
3. Plastic and composition (like hardboard) materials
may be cut on your saw. However, since these are
usually quite hard and slippery, the Anti-Kickback
Pawls may notstop a kickback. Therefore, be espe-
cially careful in your set-up and cutting procedures.
WHILE CUTTING
1. To avoid kickbacks and slips into the blade, always
pushforward onthe section ofthe workpiece between
the saw blade and the Rip Fence. Neverpushforward
on the piece being cut off.
ADDITIONAL iNSTRUCTiONS FOR
CROSSCUT TYPE CUTS
BEFORE STARTING
1. NEVER use the Rip Fence when crosscutting.
2. An auxiliarywood facing attached to the Miter Gauge
can help prevent workpiece twisting and throwbacks.
Attach it to the holes provided. Make the facing long
enough and big enough to support your worK. Make
sure, however, itwill not interfere with the Sawblade
Guard. (See page 26)
3. Use jigs or fixtures to help hold any piece too small to
extend across the full length of the Miter Gauge face
during the cut. This lets you properly hold the Miter
Gauge and workpiece and helps keep your hands
away from the blade.
WHILE CUTTING
1. To avoid blade contact, always hold the Miter Gauge
as shown in the "BASIC SAW OPERATIONS - US-
ING THE MITER GAUGE."
BEFORE LEAVING THE SAW
1. Turn the saw off.
.
Wait for blade to stop spinning.
3.
Make workshop child-proof. Lock the shop. Discon-
nect master switches. Remove the yellow Switch
Key. Store it away from children and others not
qualified to use the tool.
4. Unplug the saw.
glossary of terms for woodworking
Anti-Kickback Pawls (AKP)
Device which, when properly maintained, isdesigned to
stopthe workpiece from being kicked back at the opera-
tor during rippingoperation.
Arbor
The shaft on which a cutting tool is mounted.
Crosscut
Acuttingor shapingoperation made across the width of
the workpiece.
Dado
A non through cut which produces a square sided notch
or trough inthe workpiece.
Featherboard
A device which can help guide workpieces during rip
type operation.
Freehand
Performing a cut without using a Fence, Miter Gauge,
fixture, hold down or other proper device to keep the
workpiece from twisting during the cut.
Gum
A sticky, sap based residue from wood products.
Heel
Misalignment of the blade.
Kerr
The amount of material removed by the blade in a
throughcut or the slot produced by the blade in a non
through or partial cut.
KIckback
Anuncontrolled grabbing and throwing ofthe workpiece
back toward the front ofthe saw.
Leading End
The end of the workpiece which, during a rip type
operation, is pushed into the cuttingtool first.
Molding
Anon through cutwhich produces a special shape inthe
workpiece used for joining or decoration.
Push Stick
A device used to feed the workpiece through the saw
during narrow rippingtype operations and helps keep
the operator's hands well away from the blade.
Push Block
A device usedfor ripping type operations too narrow to
allow use of a Push Stick.
Rabbet
Anotch in the edge of a workpiece.
Resin
Asticky, sap base substance that has hardened.
Ripping
A cutting operation along the length of the workpiece,
Revolutions Per Minute (RPM)
The number of turns completed by a spinning object in
one minute.
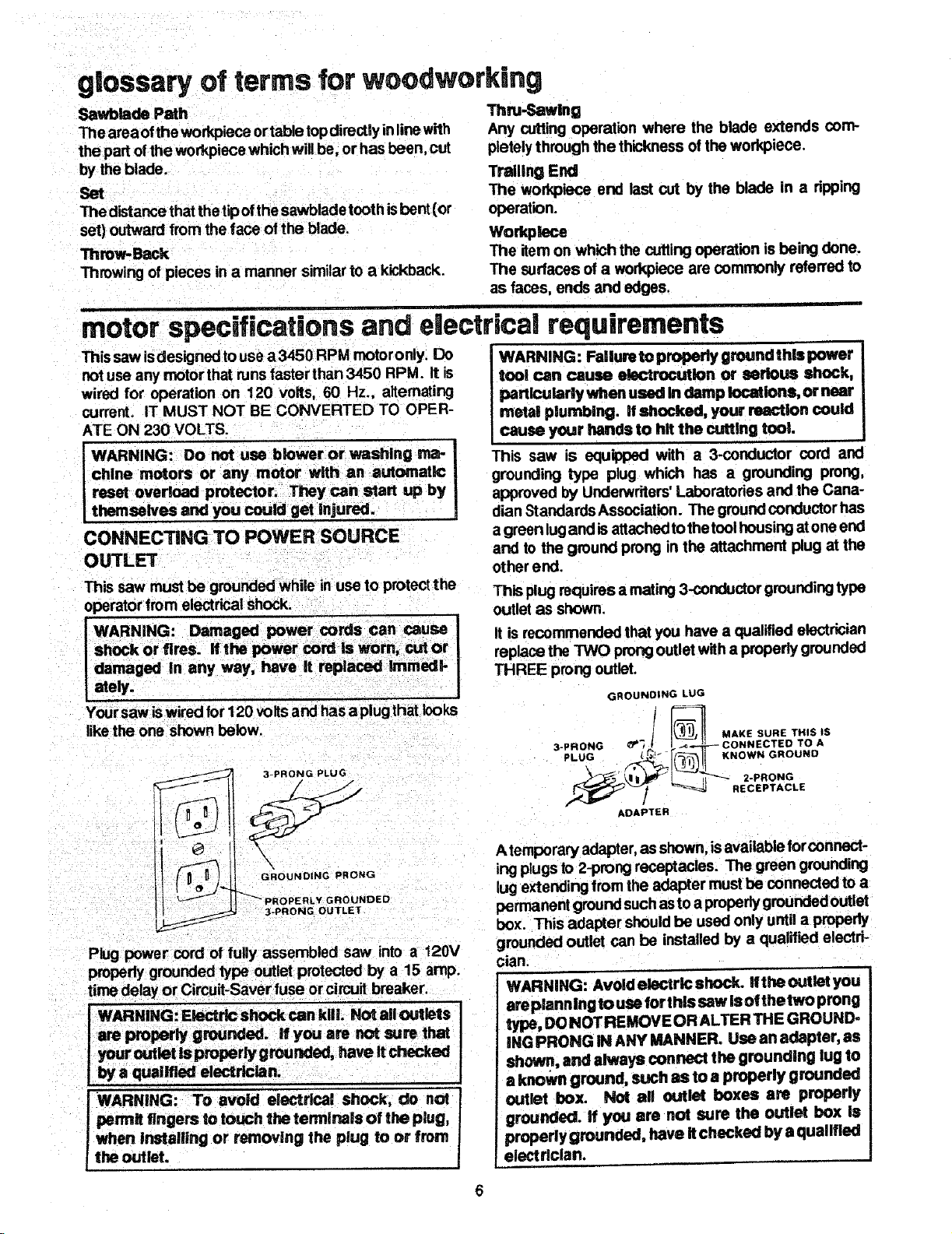
glossary of terms for woodworking
Sawbisde Path
The area ofthe workpiece ortable topdirectly inlinewith
the part ofthe workpiece whichwill be, orhas been, cut
by theblade.
Set
Thedistance that thetip of the sawblade tooth isbent(or
set) outward from the face of the blade.
Throw-Back
Throwing of pieces in a manner similar to a kickback.
Thru-Sawing
Any cutting operation where the blade extends com-
pletelythrough the thickness of the workpiece.
Trailing End
The workplace end last cut by the blade in a ripping
operation.
Workploce
The item on which the cuttingoperation is being done.
The surfaces of a workplece are commonly referred to
as faces, ends and edges.
ii
motor
Thissawisdesignadtouse a3450RPM motoronly. Do
not use any motorthat runsfaster than 3450 RPM. It is
wired for operation on 120 volts, 60 Hz., alternating
current. IT MUST NOT BE CONVERTED TO OPER-
ATE ON 230 VOLTS.
WARNING: Do not use blower or washing
chine motors or any motor with an automatic
reset overload protector. They can start up by
themselves and you could get Injured.
CONNECTING TO POWER SOURCE
OUTLET
This saw must be grounded while in use to protectthe
operator from electrical shock.
shock or fires. If the power cord is worn, cut or
damaged In any way, have It replaced immedF
JWARNING: Damaged power cords can cause
stely.
Yoursaw iswired for120 volts and has a plugthat looks / _- -
like the one shown below. J J"_,' !I MAKESURETHISIS
specifications and eiectrica! requirements
WARNING: Failure to properly ground this power
tool can cause electrocution or serious shock,
partlcuisrly when used In damp locations, or near
meta! plumbing. If shocked, your reaction could
cause your hands to hit the cutting tool.
This saw is equipped with a 3-conductor cord and
grounding type plug which has a grounding prong,
approved by Underwriters' Laboratories and the Cana-
dian StandardsAssociation. The groundconductor has
a green lugand isattachedto the toolhousing atone end
and to the ground prong in the attachment plug at the
other end.
This plug requiresa mating 3-conductor grounding type
outlet as shown.
It isrecommended that you have a qualified electrician
replace the TWO prong outlet witha properly grounded
THREE prong outlet.
GROUNDING LUG
3-PRONG _'_ _ _,_.-._-- CONNECTED TO A
\
/fl g/
Plug power cord of fully assembled saw into a 120V
properly grounded type outlet protected by a 15 amp.
time delay or Circuit-Saver fuse or circuit breaker.
your outlet Is properly g rounded, have It checked
by a qualified electrician.
WARNING: To avoid electrical ShOCk, do not
permit fingers to touch the terminals of the plug,
when Installing or removing the plug to or from
the outlet.
GROUNDING PRONG
PROPERLY GROUNDED
3-PRONG OUTLET
ADAPTER
Atemporary adapter, as shown, isavailable forconnect-
ing plugs to 2-prong receptacles. The green grounding
lug extending from the adapter mustbe connected to a
permanent ground suchas to a properlygrounded outlet
box. This adapter shouldbe used only until a properly
grounded outlet can be installed by a qualified electri-
cian.
WARNING: Avold electric shock, lftheoutlet you
are planning to use for this saw isof the two prong
type, DO NOT REMOVE OR ALTER THE GROUND-
ING PRONG IN ANY MANNER. Use an adapter, as
shown, and always connect the grounding lug to
a known ground, such as to a properly grounded
outlet box. Not all outlet boxes are properly
grounded, ff you are not sure the outlet box Is
properly grounded, have It checked by a qua llfled
eisctrlclan.
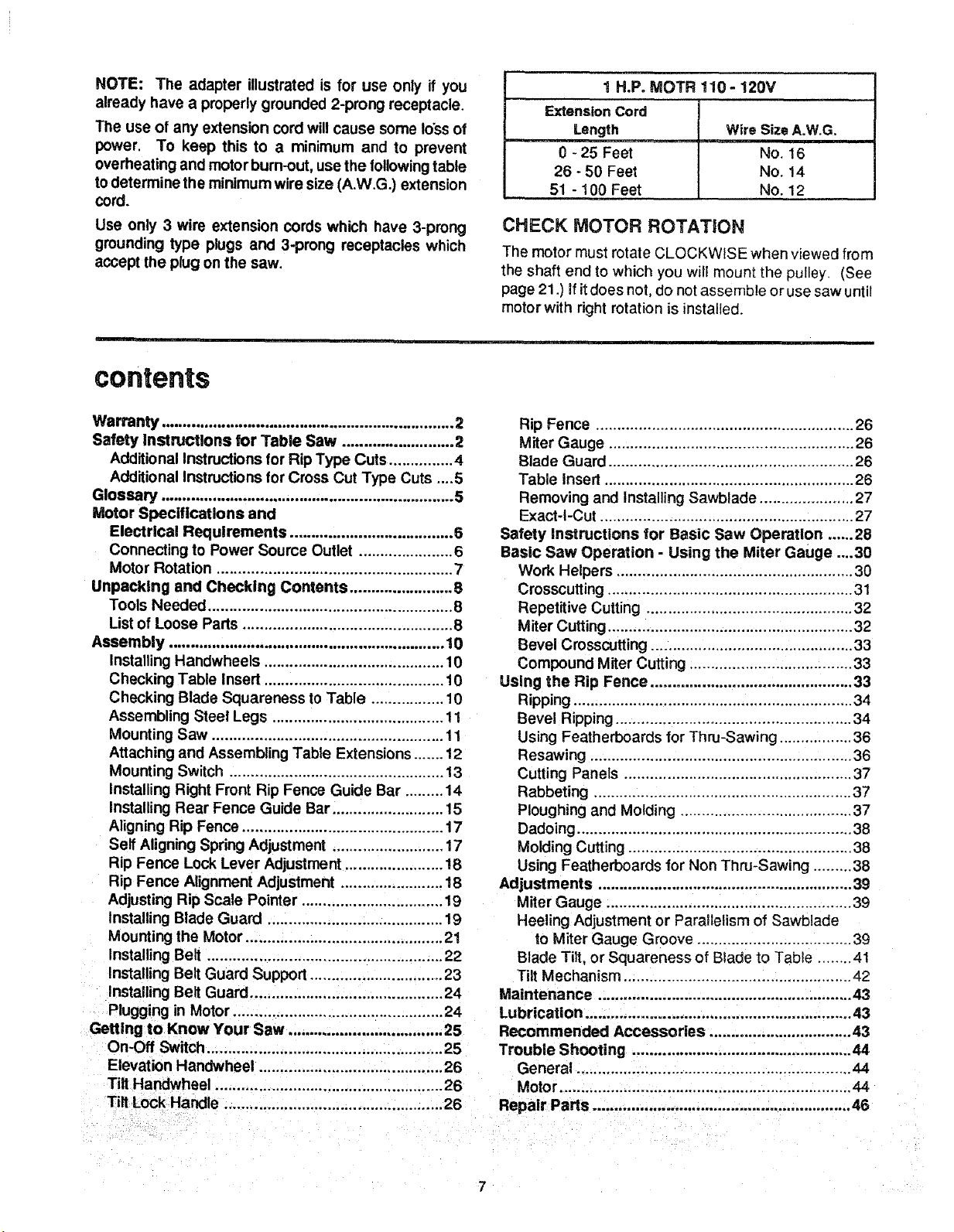
NOTE:Theadapterillustratedisfor use only if you
already have a properly grounded 2-prong receptacle.
The use of any extension cord will cause some loss of
power. To keep this to a minimum and to prevent
overheating and motor burn-out, use the followingtable
todetermine the minimum wire size (A.W.G.) extension
cord.
Use only 3 wire extension cords which have 3-prong
grounding type plugs and 3-prong receptacles which
accept the plug on the saw.
contents
1 H.P. MOTR 110- 120V
Extension Cord
Length Wire Size A.W.G.
0 - 25 Feet No. 16
26 -50 Feet No. 14
51 - 100 Feet No. 12
CHECK MOTOR ROTATION
The motor must rotate CLOCKWISE when viewed from
the shaft end to which you will mount the pulley. (See
page 21.) If it does not, do not assemble or use saw until
motor with right rotation is installed.
Warranty.................................................................... 2
Safety instructions for Table Saw .......................... 2
Additional Instructions for Rip Type Cuts ............... 4
Additional Instructions for Cross Cut Type Cuts ....5
Glossary .................................................................... 5
Motor Specifications and
Electrical Requirements ...................................... 6
Connecting to Power Source Outlet ...................... 6
Motor Rotation ....................................................... 7
Unpacking and Checking Contents ........................ 8
Tools Needed ......................................................... 8
List of Loose Parts ................................................. 8
Assembly ................................................................ 10
Installing Handwheels .......................................... 10
Checking Table Insert .......................................... 10
Checking Blade Squareness to Table ................. 10
Assembling Steel Legs ........................................ 11
Mounting Saw ...................................................... 11
Attaching and Assembling Table Extensions ....... 12
Mounting Switch .................................................. 13
Installing Right Front Rip Fence Guide Bar ......... 14
Installing Rear Fence Guide Bar .......................... 15
Aligning Rip Fence ............................................... 17
Self Aligning Spring Adjustment .......................... 17
Rip Fence Lock Lever Adjustment ....................... 18
Rip Fence Alignment Adjustment ........................ 18
Adjusting Rip Scale Pointer ................................. 19
Installing Blade Guard ......................................... 19
Mounting the Motor .............................................. 21
Installing Belt ....................................................... 22
Installing Belt Guard Support ............................... 23
Installing Belt Guard ............................................. 24
Plugging in Motor ................................................. 24
Getting to Know Your Saw .................................... 25
On-Off Switch ....................................................... 25
Elevation Handwheel ........................................... 26
Tilt Handwheel .................................................... 26
Tilt Lock Handle ................................................... 26
Rip Fence ............................................................ 26
Miter Gauge ......................................................... 26
Blade Guard ......................................................... 26
Table Insert .......................................................... 26
Removing and Installing Sawblade ...................... 27
Exact-I-Cut ........................................................... 27
Safety Instructions for Basic Saw Operation ...... 28
Basic Saw Operation - Using the Miter Gauge ....30
Work Helpers ....................................................... 30
Crosscutting ......................................................... 31
Repetitive Cutting ................................................ 32
Miter Cutting ......................................................... 32
Bevel Crosscutting ............................................... 33
Compound Miter Cutting ...................................... 33
Using the Rip Fence ............................................... 33
Ripping ................................................................. 34
Bevel Ripping ....................................................... 34
Using Featherboards for Thru-Sawing ................. 36
Resawing ............................................................. 36
Cutting Panels ..................................................... 37
Rabbeting ............................................................ 37
Ploughing and Molding ........................................ 37
Dadoing ................................................................ 38
Molding Cutting .................................................... 38
Using Featherboards for Non Thru-Sawing ......... 38
Adjustments ........................................................... 39
Miter Gauge ......................................................... 39
Heeling Adjustment or Parallelism of Sawblade
to Miter Gauge Groove ................................... 39
Blade Tilt, or Squareness of Blade to Table ........ 41
Tilt Mechanism ..................................................... 42
Maintenance ........................................................... 43
Lubrication....: ......................................................... 43
Recommended Accessories ................................. 43
Trouble Shooting ................................................... 44
General ................................................................ 44
Motor .................................................................... 44
Repair Parts ............................................................ 46
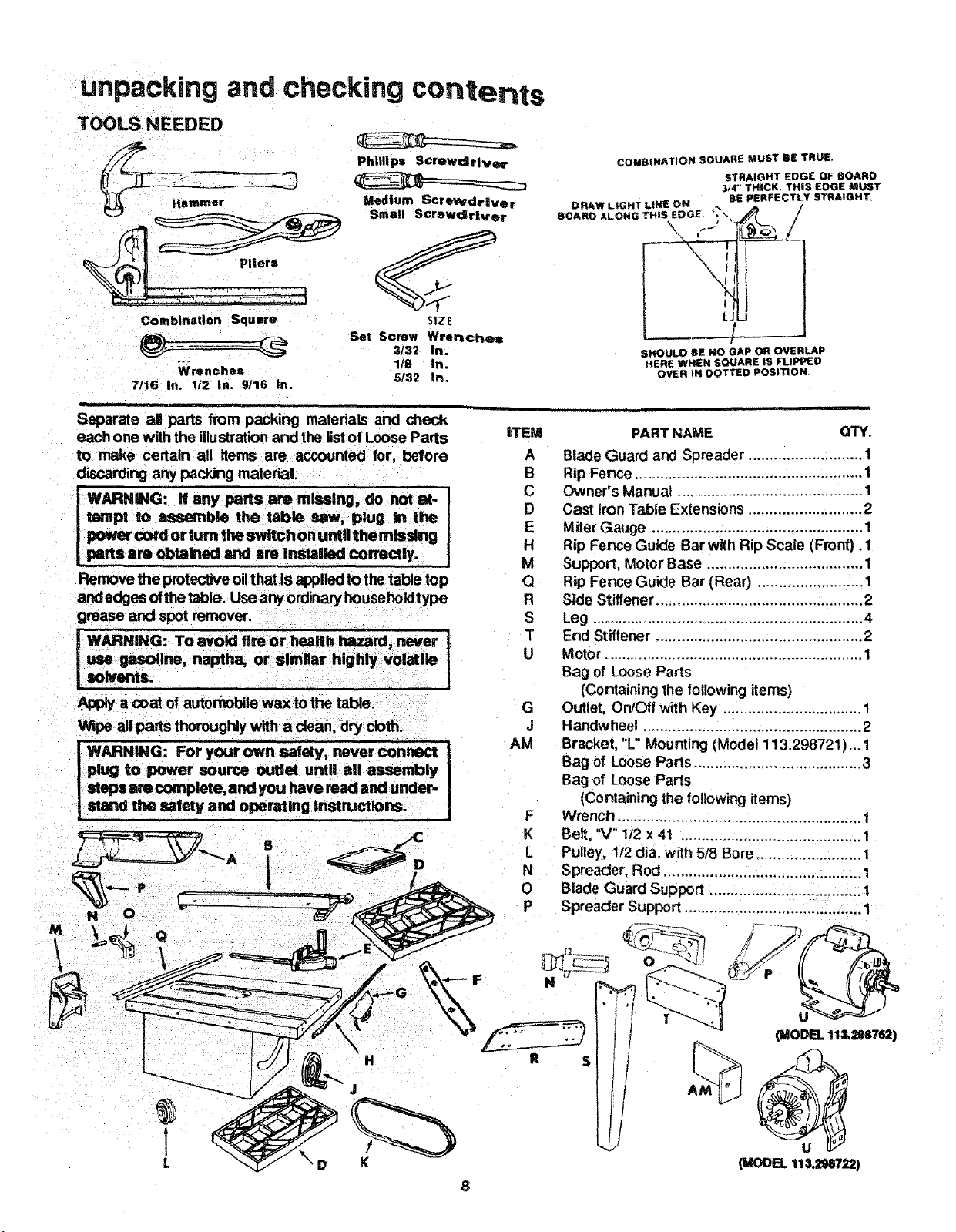
unpacking and checking contents
TOOLS NEEDED
Phillips Screwdriver
Medium Scra_dr|ver
Small Screwdriver
Plier
Combination Square
Set Screw Wrenches
Wrenchea
7/16 in, 1/2 in. 91"16 In.
r
Separate all parts from packing materials and check
each one with the illustrationand the listof Loose Parts
tO make certain all items are accounted for, before
discarding any packing material.
tempt to assemble the table saw, plug in the
power cord or turn the switch on until the missing
I WARNING: ff any parts are missing, do not at-
parts are obtained and are in_alle,(:l correctly.
Remove the protective oilthat isappliedto the table top
andedges of thetable. Use any ordinaryhouseholdtype
grease and spot remover.
use gasoline, naptha, or similar highly volatile
WARNING: To avoid fire or health hazard, never ]
Apply a coat of automobile wax to the table.
Wipe all parts thoroughly with a clean, dry cloth,
plug to power source outlet until all assembly
stepsarecomplete, aad you have mad and under-
WARNING: For your own safety, never con_ !
stand the safety and operating Instructions.
SIZE
3/32 In.
1/8 In.
5/32 In.
isolvents.
!
ITEM
A
B
C
D
E
H
M
Q
R
S
T
U
G
J
AM
F
K
L
N
O
P
COMBINATION SQUARE MUST BE TRUE,
STRAIGHT EDGE OF BOARD
3, 4" THICK. THIS EOGE MUST
DRAW LIGHT LINE ON _
BOARD ALONG THIS EDGE ; '_ _ /
BE PERFECTLY STRAIGHT.
L_ /
SHOULD BE NO GAP OR OVERLAP
HERE WHEN SQUARE IS FLIPPEO
OVER IN OOTTED POSITION.
PARTNAME QTY.
Blade Guard and Spreader ........................... 1
Rip Fence ...................................................... 1
Owner's Manual ............................................ 1
Cast Iron Table Extensions ........................... 2
Miter Gauge .................................................. 1
Rip Fence Guide Bar with Rip Scale (Front]. 1
Support, Motor Base ..................................... 1
Rip Fence Guide Bar (Rear) ......................... 1
Side Stiffener ................................................. 2
Leg ................................................................ 4
End Stiffener ................................................. 2
Motor ............................................................. 1
Bag of Loose Parts
(Containing the followingitems)
Outlet, On/Off with Key ................................ 1
Handwheel .................................................... 2
Bracket, "L" Mounting (Model 113.298721) ... 1
Bag of Loose Parts ........................................ 3
Bag of Loose Parts
(Containing the following items)
Wrench .......................................................... 1
Belt, "V" 1/2 x 41 ........................................... 1
Pulley, 112dia. with 5/8 Bore ......................... 1
Spreader, Rod ............................................... 1
Blade Guard Support .................................... 1
Spreader Support .......................................... 1
il/ ..........
14
£@
(MODEL 11_L29B762)
H
J
u
(MODEL 113.298722 i
8
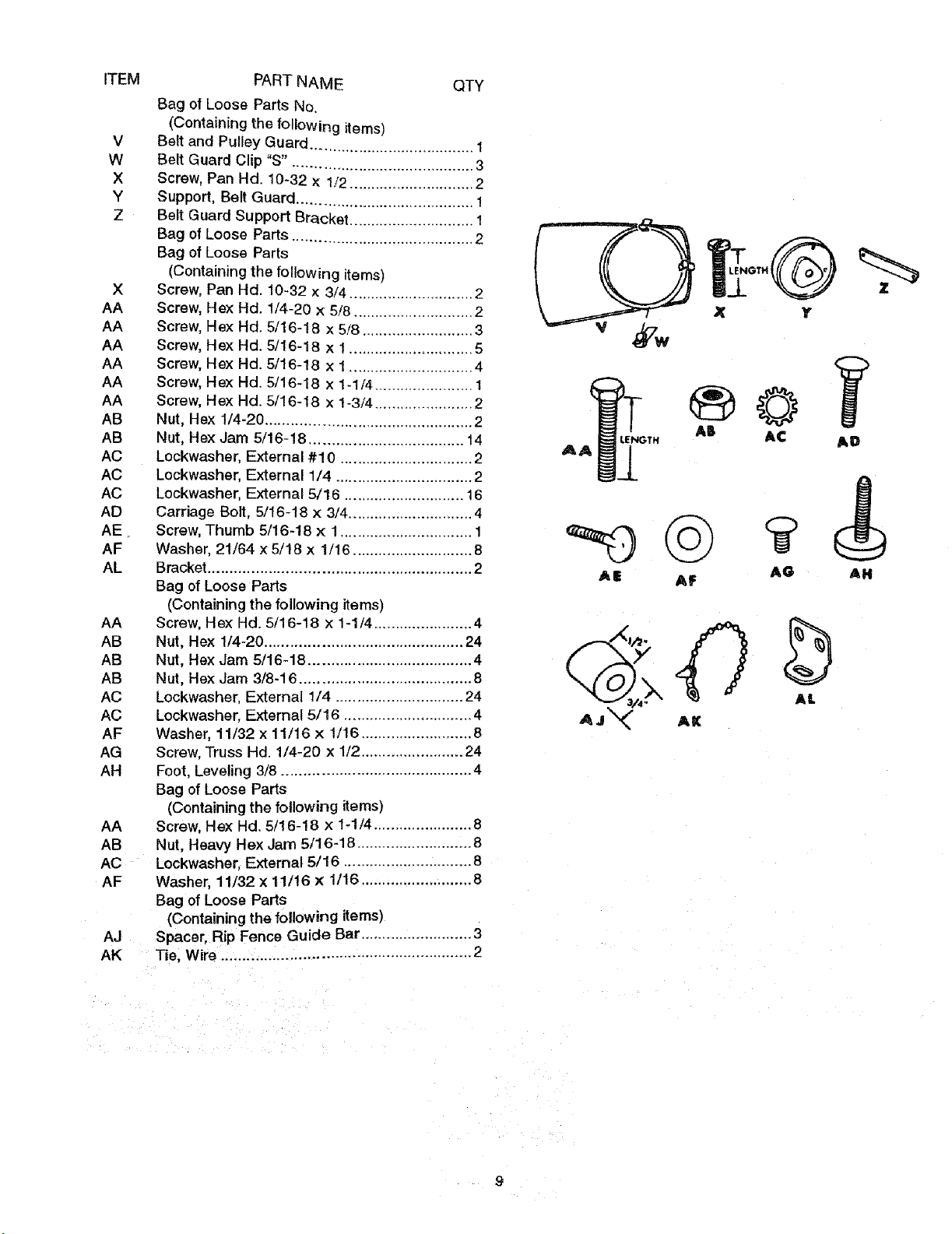
ITEM PARTNAME QTY
BagofLoosePartsNo.
(Containingthefollowingitems)
V BeltandPulleyGuard......................................1
W BeltGuardClip"S". ......................................... 3
X Screw, Pan Hd. 10-32 × 1/2 ............................. 2
Y Support, Belt Guard ......................................... 1
Z Belt Guard Support Bracket ............................. 1
Bag of Loose Parts .......................................... 2
Bag of Loose Parts
(Containing the following items)
X Screw, Pan Hd. 10-32 × 3/4 ............................. 2
AA Screw, Hex Hd. 1/4-20 × 5/8 ............................ 2
AA Screw, Hex Hd. 5/16-18 x 5/8 .......................... 3
AA Screw, Hex Hd. 5/16-18 x 1............................. 5
AA Screw, Hex Hd. 5/16-18 x 1 ............................. 4
AA Screw, Hex Hd. 5/16-I8 x 1-1/4 ....................... 1
AA Screw, Hex Hd. 5/16-18 x 1-3/4 ....................... 2
AB Nut, Hex 1/4-20 ................................................ 2
AB Nut, Hex Jam 5/16-18 .................................... 14
AC Lockwasher, External #10 ............................... 2
AC Lockwasher, External 1/4 ................................ 2
AC Lockwasher, External 5/16 ............................ 16
AD Carriage Bolt, 5/16-18 × 3/4 ............................. 4
AE .. Screw, Thumb 5/16-18 × 1............................... 1
AF Washer, 21/64 x 5/18 x 1/16 ............................ 8
AL Bracket ............................................................. 2
Bag of Loose Parts
(Containing the following items)
AA Screw, Hex Hd. 5/16-18 x 1-1/4 ....................... 4
AB Nut, Hex 1/4-20 .............................................. 24
AB Nut, Hex Jam 5/16-18 ...................................... 4
AB Nut, Hex Jam 3/8-16 ........................................ 8
AC Lockwasher, External 1/4 .............................. 24
AC Lockwasher, External 5/16 .............................. 4
AF Washer, 11/32 x 11/16 x 1/16 .......................... 8
AG Screw, Truss Hd. 1/4-20 x 1/2........................ 24
AH Foot, Leveling 3/8 ............................................ 4
Bag of Loose Parts
(Containing the following items)
AA Screw, He× Hd. 5/16-18 x 1-1/4 ...................... 8
AB Nut, Heavy Hex Jam 5/16-18 .......................... 8
AC Lockwasher, External 5/16 .............................. 8
AF Washer, 11/32 x 11/16 x 1/16 .......................... 8
Bag of Loose Parts
(Containing the following items)
AJ Spacer, Rip Fence Guide Bar .......................... 3
AK Tie, Wire .......................................................... 2
A| AF
AK
AG
AH
AL
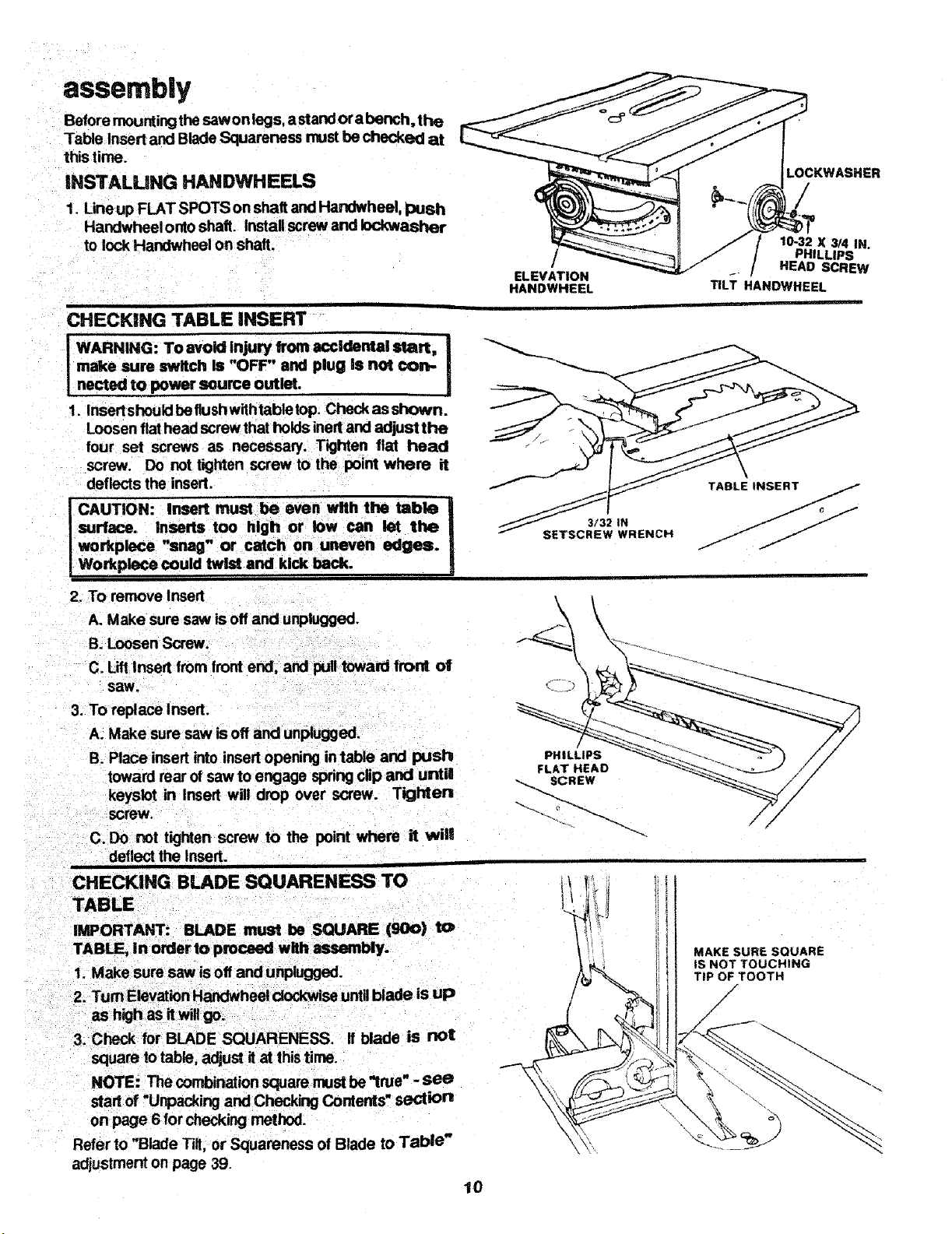
assembly
Before mountingthe saw on legs, a standor a bench, the
Table Insert and Blade Squareness must be checked at
tt_s time.
INSTALUNG HANDWHEELS
1. Line up FLAT SPOTS on shaft and Handwheel, Push
Handwheelonto shaft. Install screw and Iockwasher
to lockHandwheel on shaft.
CHECKING TABLE INSERT
make sure switch Is "OFF" and plug is not con-
i WARNING: To avoid Injury lrom accidental _rt,
nected to power source outlet.
1. Insert shouldbeflushwithtabletop, Chsck as shown.
Loosen flat head screw thatholds inert and adjust the
four set screws as necessary. Tighten flat head
screw. Do not tighten screw to the point where it
deflects the insert.
CAUTION: Insert must be even with the table
surface, inserts too high or low can let the
workplece "snag" or catch on uneven edges.
Workplece could twist and kick back.
2. To remove Insert
A. Make sure saw is off and unplugged.
B. Loosen Screw.
C. Lift Insert from front end, and pull toward front of
saw.
3. To replace Insert.
A. Make sure saw is off and unplugged.
B. Place insert into insert opening in table and push
toward rearof saw to engage springclip and until
keyslot in Insert will drop over screw. Tigl'ten
screw.
C. Do not tighten screw to the point where it will
deflect the Insert.
CHECKING BLADE SQUARENESS TO
TABLE
IMPORTANT: BLADE must be SQUARE (90o) "¢_
TABLE, in order to proceed with assembly.
1. Make sure saw is off and unplugged.
2. TurnElevation Handwheel clockwiseuntil blade is up
as highas it willgo.
3. Check for BLADE SQUARENESS. ff blade is not
square to table, adjust itat thistime.
NOTE: The combinationsquare mustbe "true" - see
start of *Unpacking and Checking Contents" section
on page 6 for checking method.
Refer to "Blade Tilt, or Squareness of Blade to Table"
adjustment on page 39.
10
LOCKWASHER
10-32 X 314 IN.
/ PHILLIPS
ELEVATION TIL'F HANDWHEEL
HANDWHEEL
i1
MAKE SURE SQUARE
IS NOT TOUCHING
TIP OF TOOTH
/
/
/
HEAD SCREW
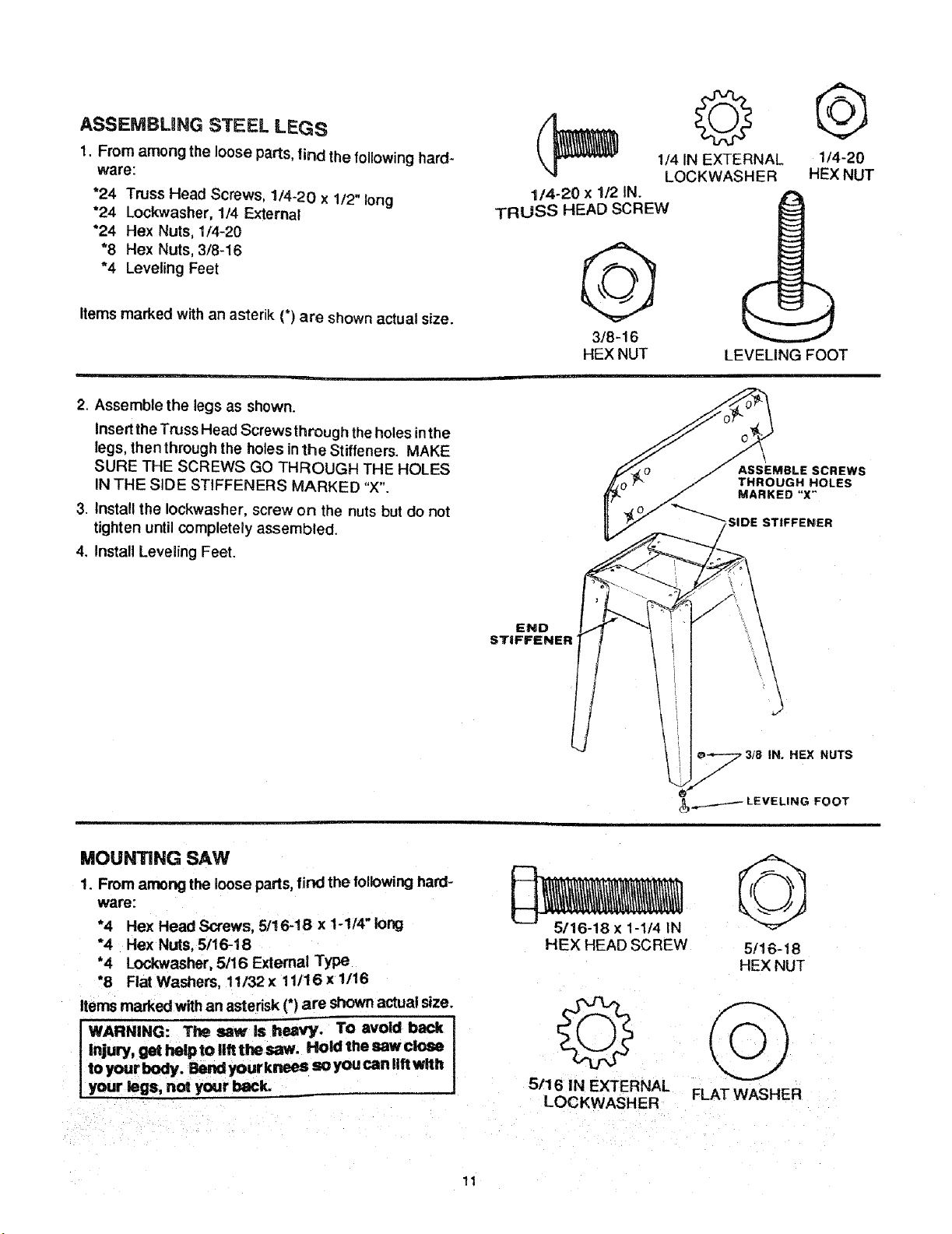
ASSEMBLRNG STEEL LEGS
1. From among the loose parts, find the following hard-
ware:
*24 Truss Head Screws, 1/4-20 x 1/2" long
*24 Lockwasher, 1t4 External
*24 Hex Nuts, 1/4-20
*8 Hex Nuts, 3/8-16
*4 Leveling Feet
Items marked with an asterik (*) are shown actual size.
2. Assemble the legs as shown.
insert the Truss Head Screws through theholes in the
legs, then through the holes in the Stiffeners. MAKE
SURE THE SCREWS GO THROUGH THE HOLES
IN THE SIDE STIFFENERS MARKED "X".
3. Install the Iockwasher, screw on the nuts but do not
tighten until completely assembled.
4. Install Leveling Feet.
© G
114IN EXTERNAL 1/4-20
LOCKWASHER HEX NUT
114-20 x 1/2 IN.
TRUSS HEAD SCREW
318-16
HEX NUT LEVELING FOOT
ASSEMBLE SCREWS
THROUGH HOLES
MARKED"X"
SIDE STIFFENER
MOUNTING SAW
1. From among the loose parts, find the following hard-
ware:
*4 Hex Head Screws, 5/16-18 x 1ol14"!ong
*4 Hex Nuts, 5t16-18
*4 Lockwasher, 5/16 External Type
*8 Flat Washers, 11/32x 11/16 x 1/16
Items marked with an astedsk (*) are strewn actual size.
WARNING: The saw Is heavy. To avoid back
Injury, get help to lift the saw. Hold the saw close
to your body. Bend your knees so you can liftwith
your legs, not your back.
t
END
STIFFENER
HEX HEAD SCREW
Q
5116 IN EXTERNAL
LOCKWASHER
IN. HEX NUTS
5tt6-18
HEX NUT
FLAT WASHER
!1
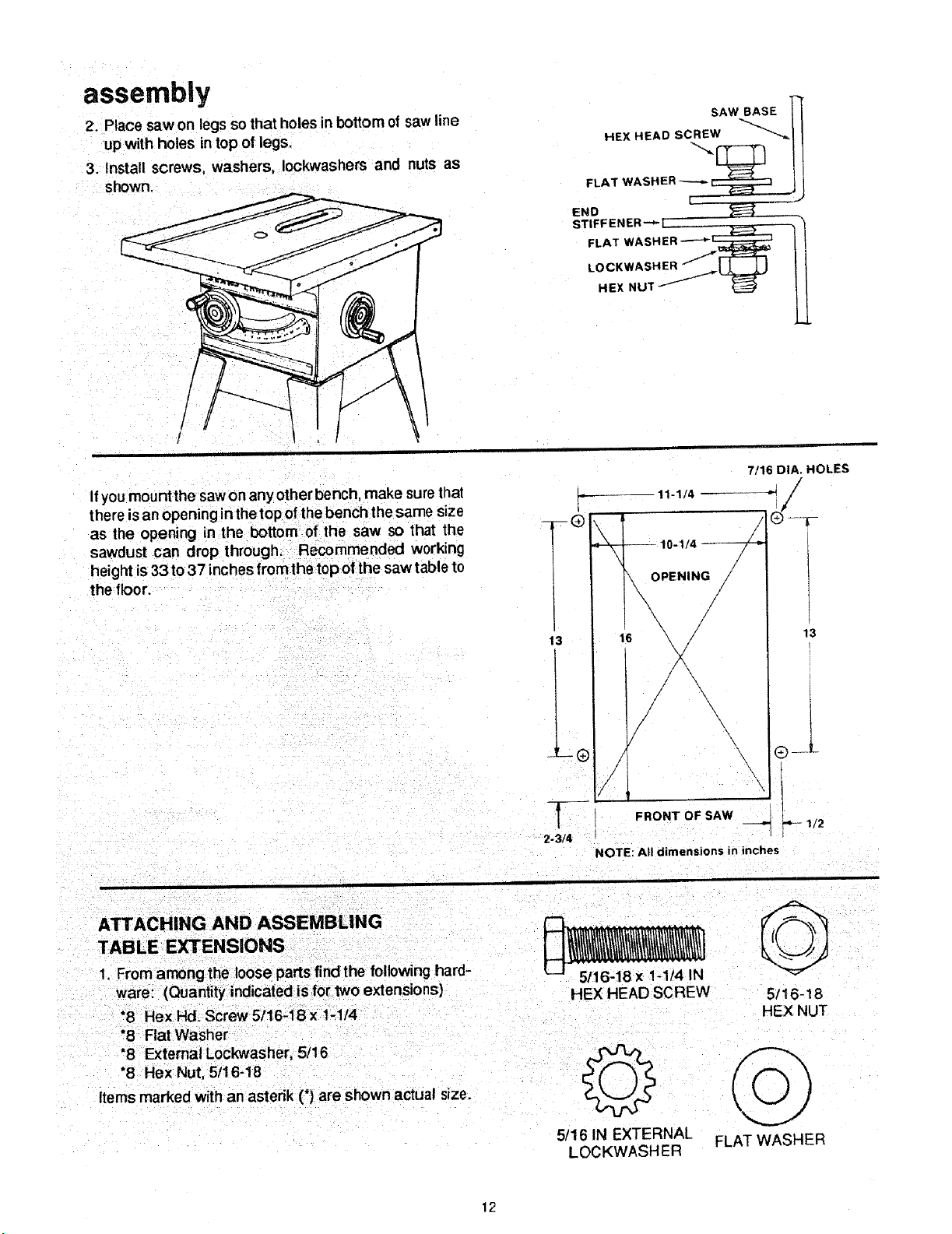
assembly
2. Place saw on legs sothat holesin bottom of saw line
up with holes in top of legs.
3. Install screws, washers, Iockwashers and nuts as
shown.
/
/
/
Ifyou mount the saw on any other bench, make sure that
there is an opening in the top ofthe bench the same size
as the opening in the bottom of the saw so that the
sawdust can drop through_ Recommended working
height is 33 to 37 inches fromthetopof the saw table to
the floor.
SAW._ IBASE t
HEX HEAD SCREW "'--_l
FLAT WASHER __
END _ .
STIFFENER-_i __ , "1
LOCKWASHER ""_' ' '
F
@
7-
7/16 DIA. HOLES
/
ATTACHING AND ASSEMBLING
TABLE EXTENSIONS
1. Fromamongthe loose parts findthe following hard-
ware: (Quantity indicated isfor two extensions)
*8 Hex Hd. Screw 5/16-18 x 1-1/4
*8 Flat Washer
*8 External Lockwasher, 5/16
"8 Hex Nut, 5t16-18
Items marked with an asterik (*) are shown actual size.
13 16
I ,
2-3/4
HEX HEAD SCREW
I ,
/" \\ __
FRONT OF SAW --'_ 1/2
NOTE: All dimensions in inches
O
/
\ ®
@
5t16-18
HEX NUT
12
5/16 IN EXTERNAL
LOCKWASH ER
FLAT WASHER
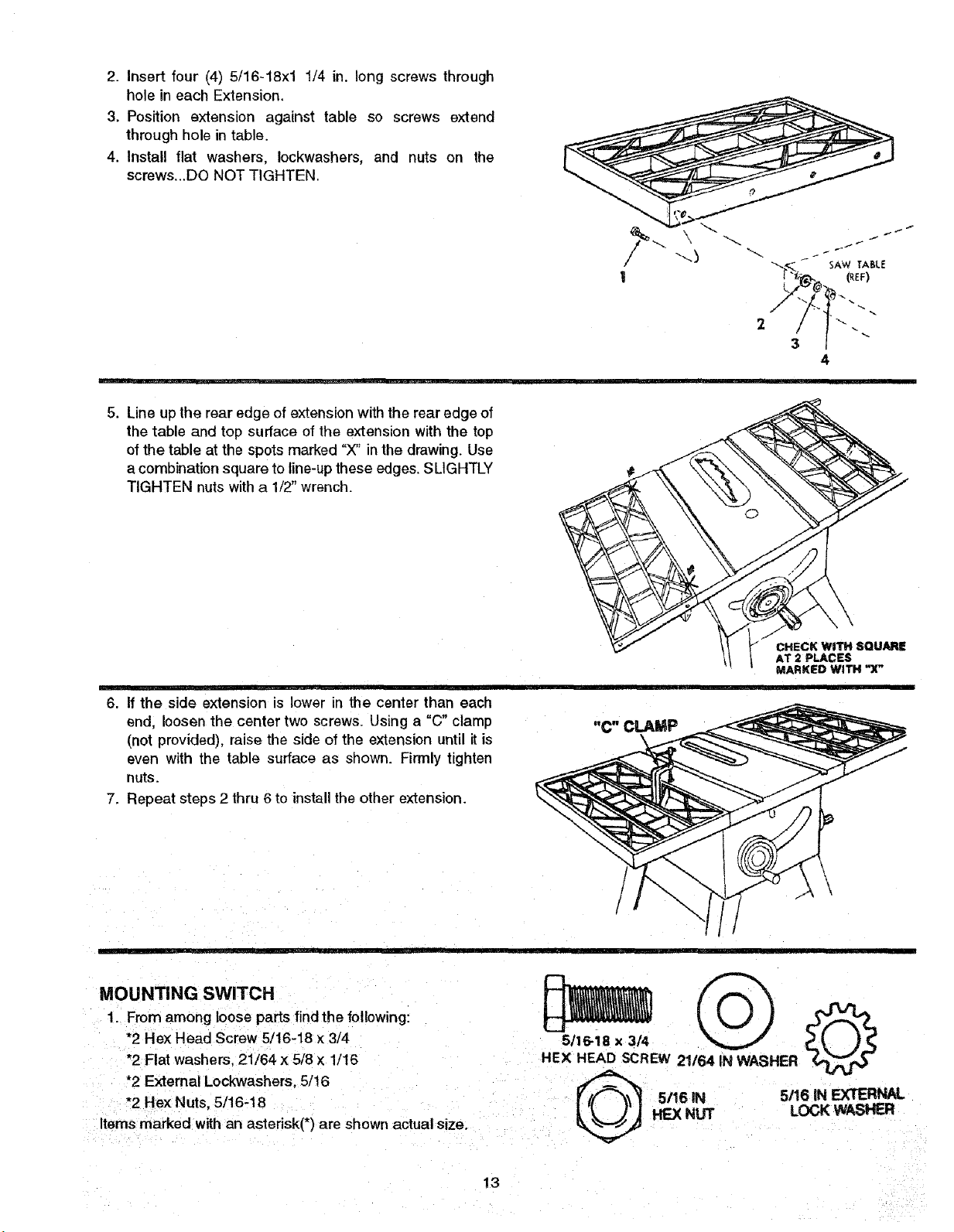
2. Insert four (4) 5/16-18xl 114 in. long screws through
hole in each Extension.
3. Position extension against table so screws extend
through hole in table.
4. Install flat washers, Iockwashers, and nuts on the
screws...DO NOT TIGHTEN.
5. Line up the rear edge of extension with the rear edge of
the table and top surface of the extension with the top
of the table at the spots marked "X" in the drawing. Use
a combination square to line-up these edges. SLIGHTLY
TIGHTEN nuts with a 1/2" wrench.
!
6. If the side extension is lower in the center than each
end, loosen the center two screws. Using a "C" clamp
(not provided), raise the side of the extension until it is
even with the table surface as shown. Firmly tighten
nuts.
7. Repeat steps 2 thru 6 to install the other extension.
I I
MOUNTING SWITCH
1. From among loose parts findthe following:
*2 Hex Head Screw 5/16-18 x 3/4
*2 Flat washers. 21/64 x 5/8 x 1/16
*2 External Lockwashers, 5/16
*2 Hex Nuts, 5/16-18
Items marked with an asterisk(*) are shown actual size.
CHECK WITH SQUARE
AT 2 PLACES
MARKED WiTH "X"
"C" CLAMP
5116-18x 3/4
HEX HEAD SCREW21164 IN WASHER
HE)( NUT LOCK WASHER
5/16 iN 5/16 IN EXTERNAL
13
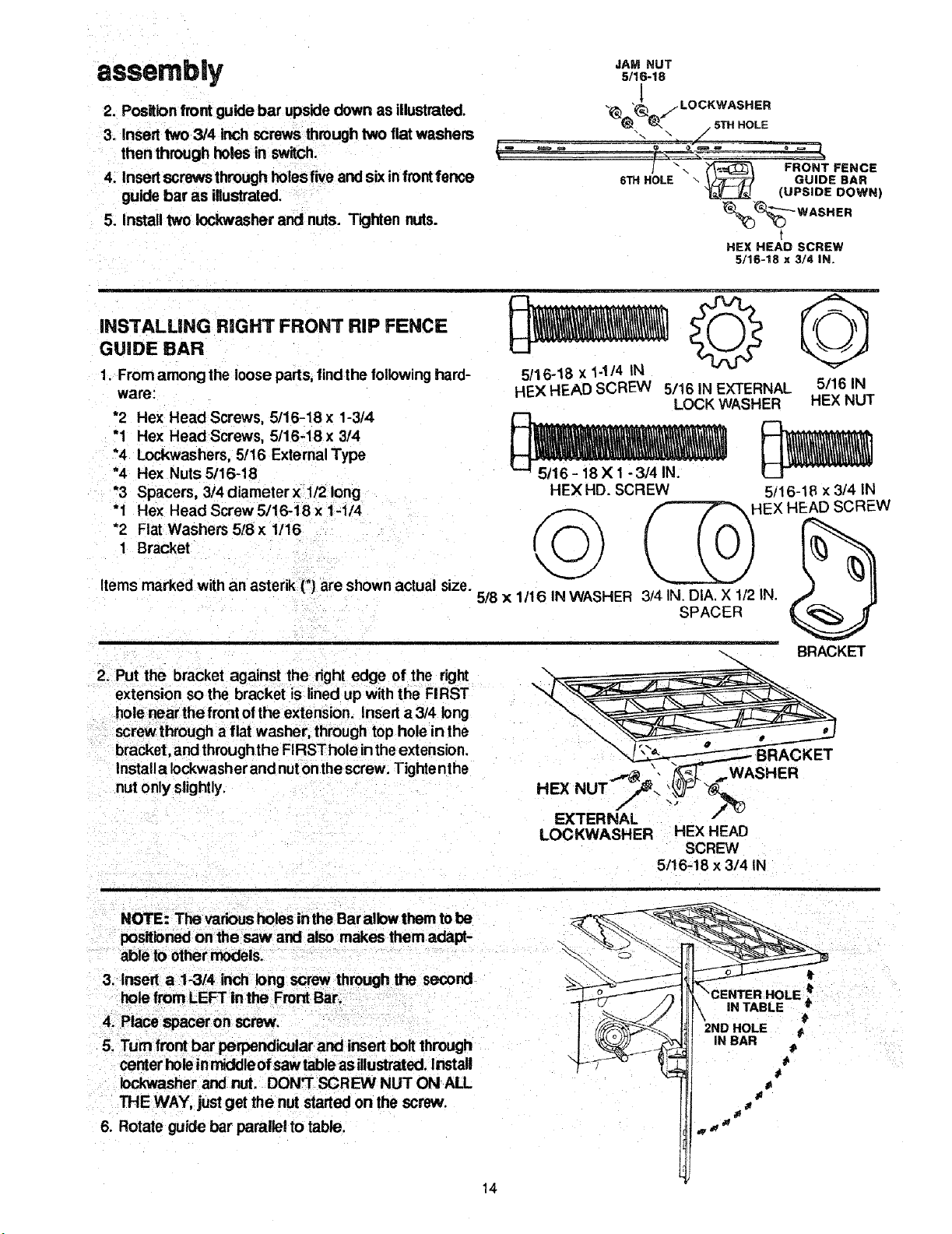
assembly
2. Position front guide bar upside down as illustrated.
3. Insert two 3/4 inch screws through two flat washers
then through holes in switch.
4. Insert screws through holesfive and six infrontfence
guide bar as illustrated.
5. Install two Iockwasher and nuts. Tighten nuts.
iNSTALLiNG RIGHT FRONT RIP FENCE
GUIDE BAR
1. From among the loose parts, findthe followinghard-
ware:
*2 Hex Head Screws, 5/16-18x 1-3/4
"1 Hex Head Screws, 5/16-18x 3/4
*4 Lockwashers, 5/16 External Type
*4 Hex Nuts 5/16-18
"3 Spacers, 3/4 diameterx 1/2 long
"1 Hex Head Screw 5/16-18 x 1-1/4
*2 Flat Washers 5/8 x 1/16
1 Bracket
Items marked withan asterik (*) are shown actual size.
JAM NUT
5/16-18
1 LOCKWASHER
_/" 7 5TH HOLE
J _'\ _ FRONT FENCE
6TH HOLE ',- \_.__-_ GUIDE BAR
%%"_""- W ASH E R
HEX HEAD SCREW
5/16-18 x 3/4 IN.
5/16-18 x 1-t/4 IN
HEX HEAD SCREW 5/16 IN EXTERNAL
LOCK WASHER
HEX HD. SCREW 5/16-18 x 3/4 IN
HEX HEAD SCREW
5/8 x 1/16 IN WASHER 314IN. DIA. X 112IN.
SPACER
(UPSIDE DOWN)
5/16 IN
HEX NUT
=
2. Put the bracket against the right edge of the right "_ -- ---"--_
extension so the bracket is lined up with the FIRST
hole near the front ofthe extension. Insert a 3/4 long
screw through a flat washer, through top hole in the
bracket, and throughthe FIRST hole inthe extension.
Installa lockwasherand nuton thescrew, Tightenthe T_,,_ _, _/_ _ 1WASHER
nut only slightly.
EXTERNAL
LOCKWASHER HEX HEAD
SCREW
5/16-18 x 3/4 IN
NOTE: The variousholes in the Bar allowthem to be
positionedon the saw and also makes them adapt-
able to other models.
3. Insert a 1-314 inch long screw through the second
holefrom LEFT Inthe Front Bar.
5. Turn front bar perpendicular and insert bolt through
_'CENTER HOLE :
'\ IN TABLE
2ND HOLE
IN BAR
center holein middleof saw table as illustrated. Install
lockwasher and nut. DON'T SCREW NUT ON ALL
THE 'NAY, just get the nut started on the screw.
6. Rotate guide bar parallel to table.
_f
BRACKET
t
;P
14
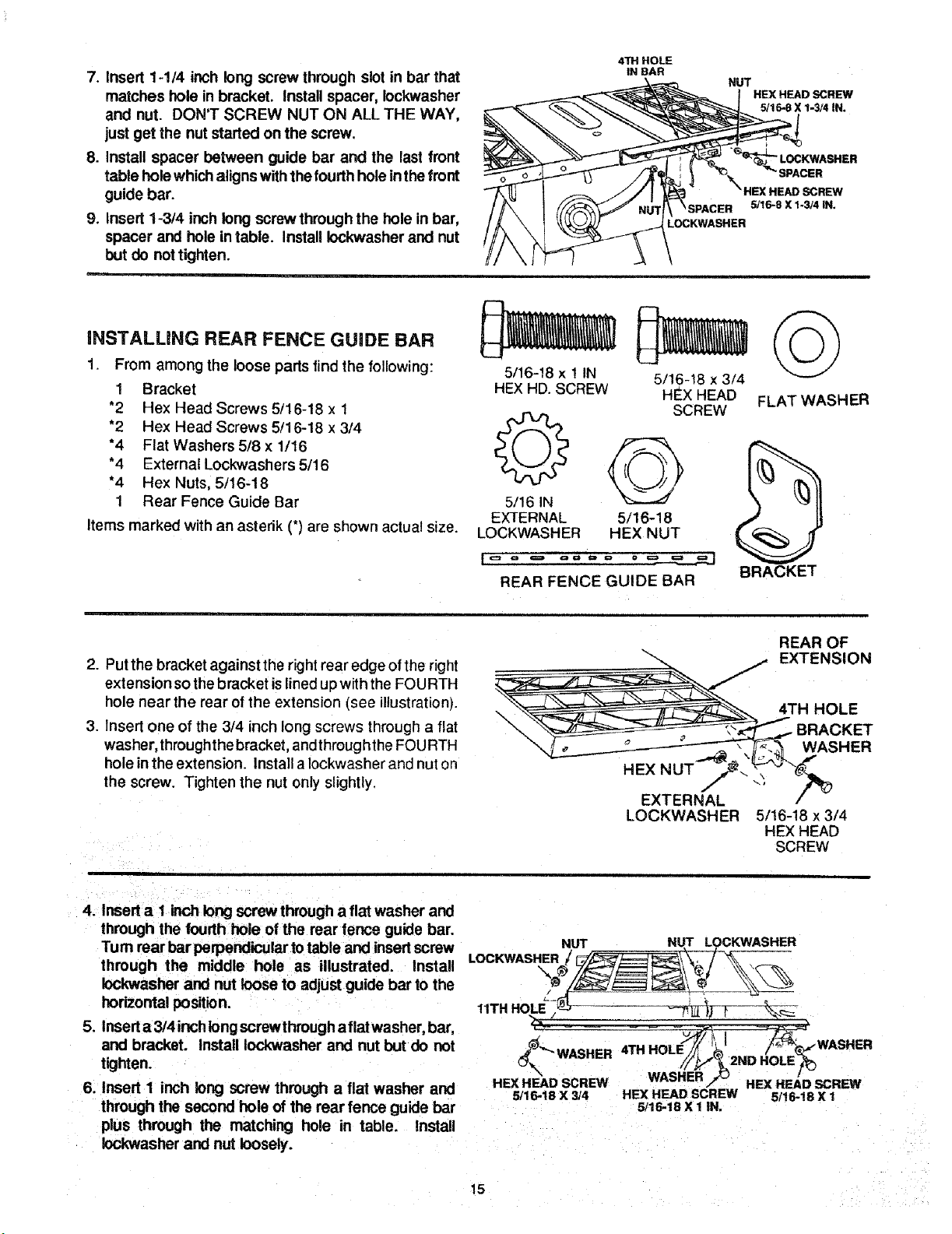
7. Insert 1-1/4 inch long screw through slot in bar that
matches hole in bracket. Install spacer, Iockwasher
and nut. DON'T SCREW NUT ON ALL THE WAY,
just get the nut started on the screw.
8. Install spacer between guide bar and the last front
table hole whichaligns with thefourth hole inthe front
guide bar.
9. Insert 1-3/4 inch long screw through the hole inbar,
spacer and hole intable. Install Iockwasher and nut
but do nottighten.
iNSTALLiNG REAR FENCE GUIDE BAR
4TH HOLE
IN BAR
LOCKWASHER
NUT
HEX HEAD SCREW
5/16-8 X 1-3/4 IN.
5/16-8 X 1-3/4 IN.
scREW
1. From among the loose parts find the following:
1 Bracket
*2 Hex Head Screws 5/16-18 x 1
*2 Hex Head Screws 5/16-18 x 3/4
*4 Flat Washers 5/8 x 1/16
*4 External Lockwashers 5/16
*4 Hex Nuts, 5/16-18
1 Rear Fence Guide Bar
Items marked withan astedk (*) are shown actual size.
2. Put the bracket against theright rear edge of the right
extension so the bracket is lined up with the FOURTH
hole near the rear of the extension (see illustration).
3. Insert one of the 3/4 inch long screws through a flat
washer, through the bracket, and through the FOURTH
hole in the extension. Install aIockwasher and nut on
the screw. Tighten the nut only slightly.
5/16-18 x ! IN
HEX HD. SCREW
5/16-18 x 3/4
HEx HEAD FLATWASHER
5/16 IN
EXTERNAL 5/16-18
LOCKWASHER HEX NUT
REAR FENCE GUIDE BAR BRACKET
REAR OF
EXTENSION
_ 4TH HOLE
_ \_/_ WASHER
LOCKWASHER 5/16-18 x 3/4
HEX HEAD
SCREW
4. Insert a 1 inch long screw through a flat washer and
through the fourth hole of the rear fence guide bar.
Turn rear bar perpendicular totable and insertscrew
through the middle hole as illustrated. Install
Iockwasher and nut loose to adjust guide bar to the
horizontal position.
5. Insert a 3/4 inchlong screwthrough a flat washer, bar,
and bracket. Install Iockwasher and nut but do not
tighten.
6. Insert 1 inch long screw through a flat washer and
through the second hole of the rear fence guide bar
plus through the matching hole in table. Install
Iockwasher and nut loosely.
LOCKWASH_UT _,:OC \KWA_
11TH HOLE_,.,I-_._ "-7_'''_-_------_-Vj-_T-_ -
HEX HEAD SCREW WASHER i HEX HEAD SCREW
5/16-18 X 3/4 HEX HEAD SCREW 5/16-18 X 1
15
5/16-18 X 1 IN.
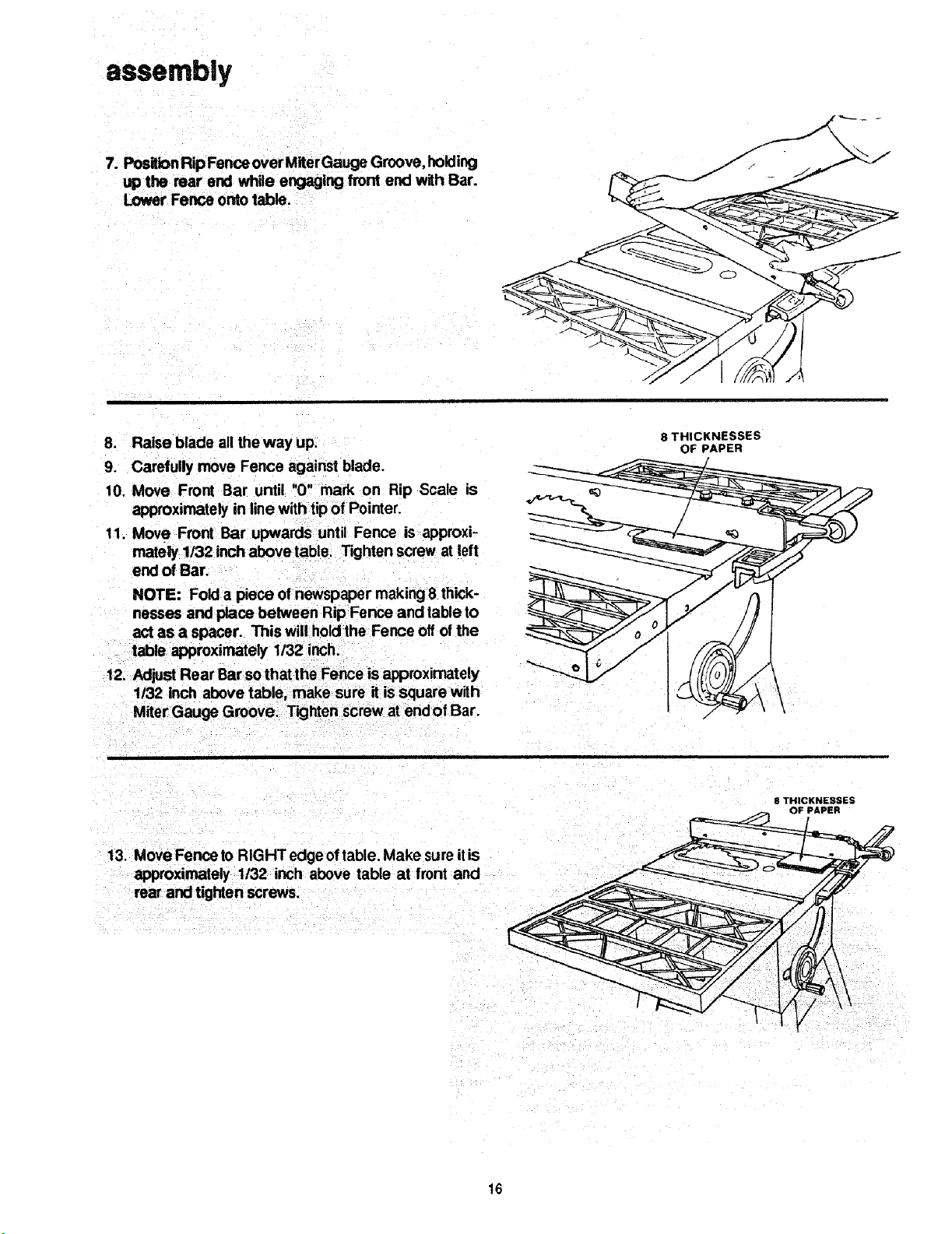
assembly
7. Position Rip Fence over Miter Gauge Groove, holding
up the rear end while engaging front end with Bar.
Lower Fence onto table.
8. Raise blade all the way up,
9. Carefully move Fence against blade.
t0, Move Front Bar until "0" mark on Rip Scale is
approximately in line withtip of Pointer.
11. Move Front Bar upwards until Fence is approxi-
mately 1/32 inch above table, Tighten screw atleft
end of Bar.
NOTE: Fold a piece of newspaper making 8 thick-
nesses and place between Rip Fence and table to
act as a spacer. This will hold the Fence offof the
table approximately 1/32 inch.
12. Adjust Rear Barso thal the Fence is approximately
1132 inch above table, make sure it issquare with
MiterGauge Groove. Tighten screw atend of Bar.
13. Move Fence to RIGHT edge of table. Make sure it is
approximately 1/32 inch above table at front and
rear and tighten screws.
8THICKNESSES
OF PAPER
o
8 THICKNESSES
OF PAPER
t6
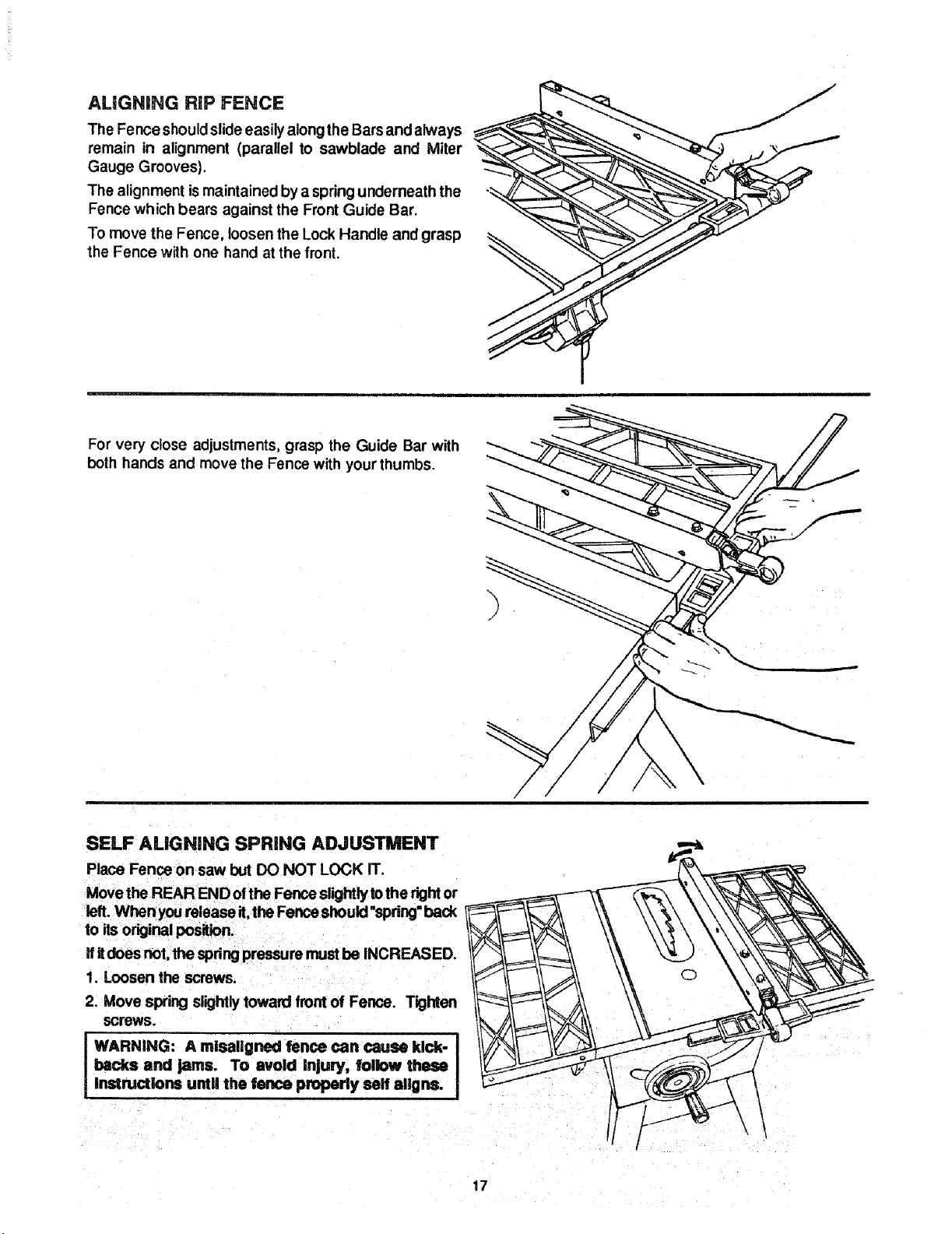
ALIGNING RiP FENCE
The Fence should slideeasily alongthe Bars and always
remain in alignment (parallel to sawblade and Miter
Gauge Grooves),
The alignment ismaintained by a springunderneath the
Fence which bears against the Front Guide Bar.
To move the Fence, loosen the Lock Handle and grasp
the Fence with one hand at the front.
For very close adjustments, grasp the Guide Bar with
both hands and move the Fence with your thumbs.
SELF ALIGNING SPRING ADJUSTMENT
Place Fence on saw but DO NOT LOCK IT.
Move the REAR END ofthe Fence slightlytothe rightor
left.When yourelease it,the Fence should "spring"back
to its originalposition.
ifitdoes not, the spring pressure must be INCREASED,
1. Loosen the screws.
2. Move spring slightly toward frontof Fence. Tighten
screws.
\
backs and jams. To avoid injury, follow these
instructions until the fence properly self aligns.
17