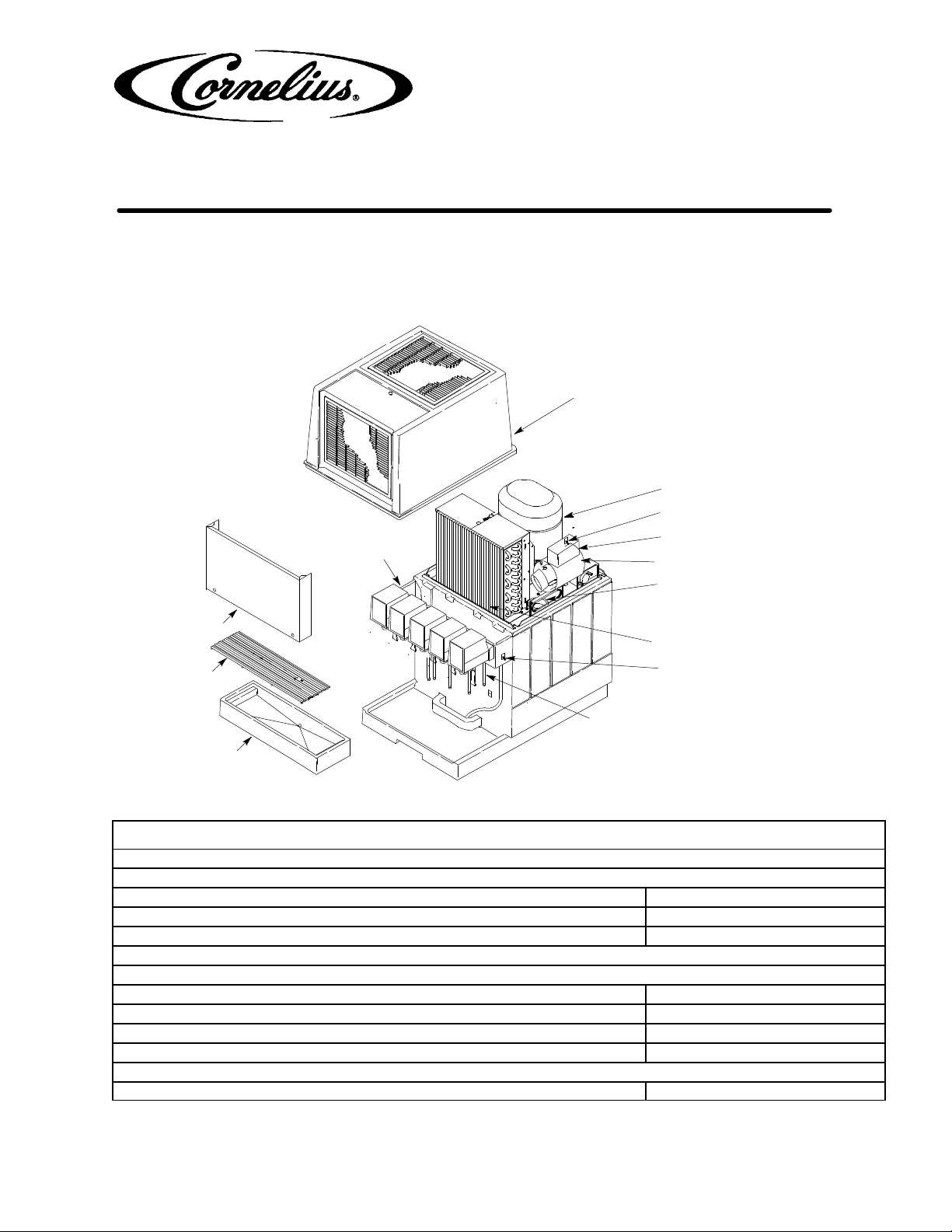
IMI CORNELIUS INC.
One Cornelius Place
Anoka, MN. 55303 -6234
Telephone(612) 421-6120
Facsimile (612) 422 -3232
INSTALLATION & MAINTENANCE MANUAL
COLD CARB VENTURE
This is the Installation and Maintenance Manual for the Venture Post-Mix Dispenser with cold carbonator and
1/4 H.P. refrigeration compressor. The Venture Dispenser may be installed on a front or rear counter. A full
Installatio/Service Manual (P/N 318832000) is available upon request.
HOOD
COMPRESSOR
CARBONAT ORSWITCH
DISPENSING VALVES
KEY-LOCK SWITCH
CONTROL BOX
WATER PUMP AND MOTOR
WATER FILL HOLE PLUG
FRONT
ACCESS PANEL
CUP
REST
SYRUP STAINLESS-
STEEL INLET TUBES
DRIP
TRAY
CONDENSER COIL
ON/OFF SWITCH
(ON 115 VOLT UNITS ONL Y)
FIGURE 1. PARTS IDENTIFICA TION
Design Data
Dimensions:
Width 16-1/4 inches
Height 27-5/8 inches
Depth 24-1/2 inches
Weights:
Shipping Weight (approx) 128 pounds
Dry Weight (approx) 107 pounds
Ice Bank Weight (approx) 30 pounds
Drop-In Refrigeration Assembly 66 pounds
Water Tank Capacity (no ice bank) approx 9-3/4 gallons
EIMI Cornelius Inc; 1995--98
Control Code B
Revised: January 16, 1998
June 6, 1995
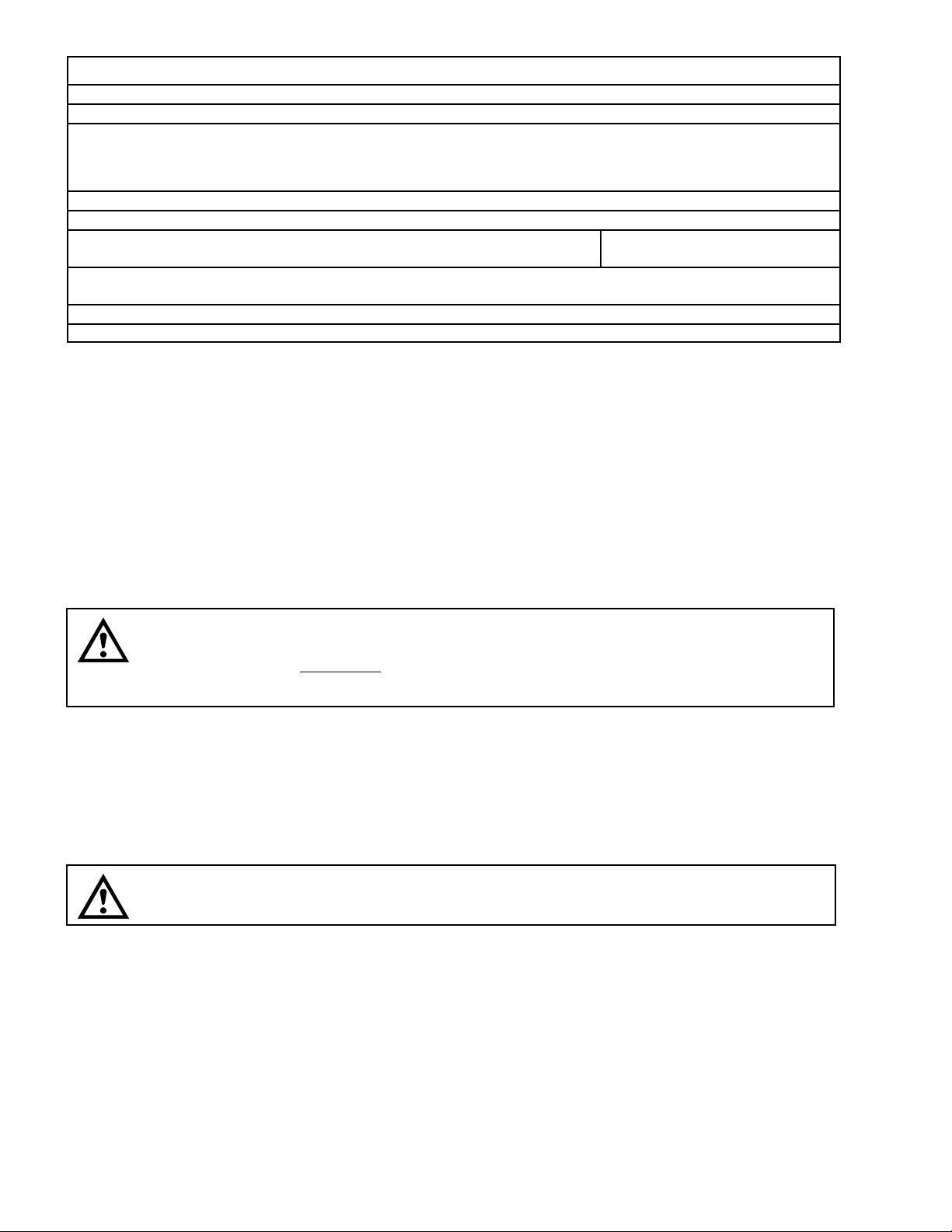
Design Data (cont’d)
Dispensing Rate: 12-oz. drinks 4/min. 40° F or below (see Note) *248
NOTE: *Approximate number of drinks dispensed 40° F or below 4@ 75° F syrup and water inlet tem-
perature and
75° F ambient.
Refrigeration Requirements:
Refrigerant Type and Amount See Unit
Nameplate
Ambient Operating Temperature 40° F to 120° F
Electrical Requirements: See Unit nameplate
UNPACKING AND INSPECTION
NOTE: The Unit was thoroughly inspected before leaving the factory and the carrier has accepted and
signed for it. Any damage or irregularities should be noted at the time of delivery (or not later than 15
days from date of delivery) and immediately reported to the delivering carrier. Request a written inspection report from Claims Inspector to substantiate any necessary claim. File claim with the delivering
carrier, not with IMI Cornelius Inc.
INSTALLATION
NOTE: Optional 4-inch Legs (P/N 31474400) that will elevate the Unit 4-inches above the countertop are
available. When ordering legs, order a quantity of four.
WARNING: To avoid possible fatal electrical shock or serious injury to the operator, it is
required that a GFCI (ground fault circuit interrupt) be installed in the electrical circuit for
the domestic Units. It is required that an ELCB (earth leakage circuit breaker) be installed in
the electrical circuit for the export Units
IMPORTANT: It is the responsibility of the Installer to ensure that the water supply system that is to be
connected to the dispensing equipment is provided with protection against back flow by an air gap as
defined in ANSI/ASME A112.1.2--1979; or an approved vacuum breaker or other such method as proved
effective by test.
Water pipe connections and fixtures directly connected to a potable water supply shall be sized,
installed, and maintained according to Federal, State, and local laws.
CAUTION: This Unit is intended for indoor installation only. Do not install this Unit in an
outdoor environment which would expose it to the outside elements.
Note: A minimum of 15-inches clearance must be maintained above the Unit to the nearest object
(shelf, cupboard, ceiling, etc.). The front grille of the Unit must be unobstructed to allow air to enter the
Unit hood.
The Unit must be located close to a permanent drain to connect the Unit drip tray drain hose.
The Unit must be installed near a properly grounded electrical outlet with proper electrical require-
ments.The electrical circuit must be properly fused (slow-blow type fuse) or the circuit must be connected through an equivalent HACR circuit breaker.The electrical outlet must be accessible for ease of
connecting and disconnecting the Unit power cord. No other electrical equipment should be connected to this circuit. REFER TO UNIT NAMEPLATE FOR THE REQUIRED POWER CIRCUIT OPERATING
VOLTAGE, HZ, AND THE MINIMUM CIRCUIT AMPACITY OF THE UNIT. ALL ELECTRICAL WIRING MUST
CONFORM TO NATIONAL AND LOCAL ELECTRICAL CODES.
2 318832013
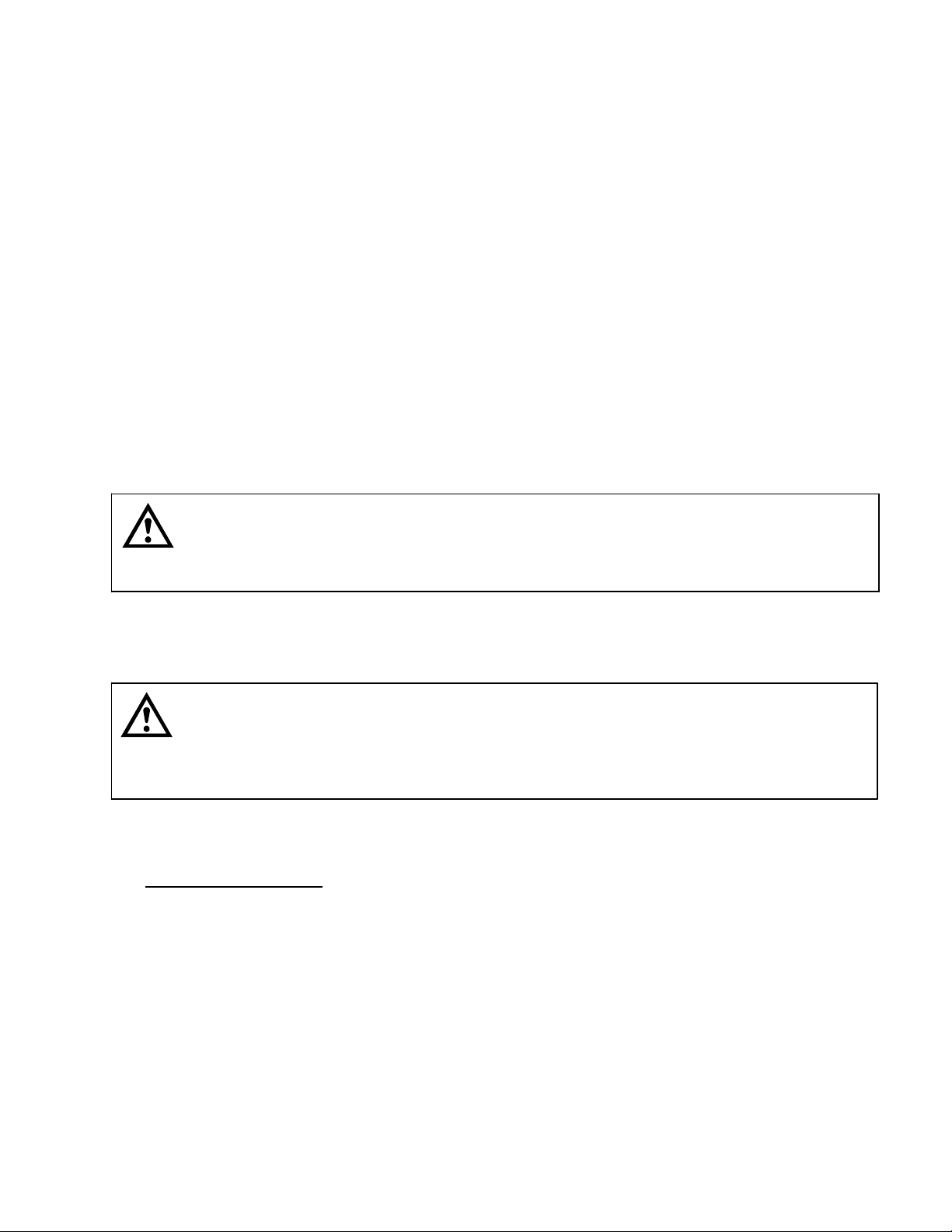
1. Install drain hose on Unit and secure with provided clamp.
2. Route drip tray drain tube down to and connect to permanent drain.
Note: The Unit syrup, water and CO2source tubes may either be routed in through opening in lower
back side of the Unit to location behind the front panel or tubes may be routed up through hole cut in
the countertop to inside of the Unit. Cut necessary hole in countertop if applicable.
3. Remove Unit front access panel (see Figure 1) for access to the Unit syrup connecting tubes and for routing water inlet tube to the water pump.
4. Route syrup source tubes (numbered for identification) up to and to inside of the Unit. Connect numbered
syrup source tubes to matching number labeled Unit syrup inlet tubes.
5. Route plain water source tube up to the Unit. Connect plain water source tube to water pump inlet on water
pump and motor assembly .
6. Route CO2source tube up to the Unit. Connect CO2source tube to labeled Unit CO2inlet tube.
7. Place Unit in operating position on the countertop. To meet NSF International (NSF) requirements, seal
Unit to countertop with silastic sealant, such as Dow Corning RTV 731 or equivalent.
8. Remove hood from Unit. Fill water tank with clean water until water runs out of overflow into the drip tray
pan. Use low-mineral-content water where a local water problem exists.
WARNING: The Unit must be electrically grounded to avoid possible fatal electrical shock
or serious injury to the operator. The Unit power cord is equipped with a three-prong plug.
If a three-hole (grounded) electrical outlet is not available, use an approved method to
ground the Unit.
9. Plug Unit power cord into electrical outlet.
10. Place Unit power switch in “ON” position. Refrigeration system will start and begin building an ice bank.
WARNING: CO2displaces oxygen. Strict attention must be observed in the prevention of
CO2(carbon dioxide) gas leaks in the entire CO2and soft drink system. If a CO2gas leak is
suspected, particularly in a small area, immediately ventilate the contaminated area before
attempting to repair the leak. Personnel exposed to high concentration of CO2gas will experience
tremors which are followed rapidly by loss of consciousness and suffocation.
11. Make sure primary and secondary CO2regulators adjusting screws are turned to the left (counterclockwise) until all tension is relieved from adjusting screws springs, then open the CO2cylinder shutoff valve.
12. Adjusting CO2regulators.
A. Adjust secondary CO2regulator for the dispenser integral carbonator to nominal 80-psig. INLET CO
PRESSURE TO CARBONATOR MUST NOT EXCEED 125-PSIG.
2
B. Sugar syrup tanks Secondary CO2regulator-- Adjust sugar syrup tanks secondary CO2regulator to a
minimum of 45-psig.
C. Low-calorie (diet) syrup tank secondary CO2regulator-- Adjust low-calorie (diet) syrup tank secondary
CO2regulator to 10-psig for syrup lines up to 30-feet in length. Syrup lines longer than 30-feet in length
may require a slightly higher setting of 12-psig maximum. Excessive CO2pressure may cause low-calorie
syrup carbonation resulting in a foamy drink being dispensed.
D. Bag-in-Box System syrup pumps--Adjust the Bag-in-Box system syrup pumps secondary CO2regulator
to 70-psig. DO NOT EXCEED MAXIMUM PRESSURE SPECIFIED ON THE SYRUP PUMPS.
13. Turn on water supply to the Unit. Check for water leaks and repair if evident.
3318832013