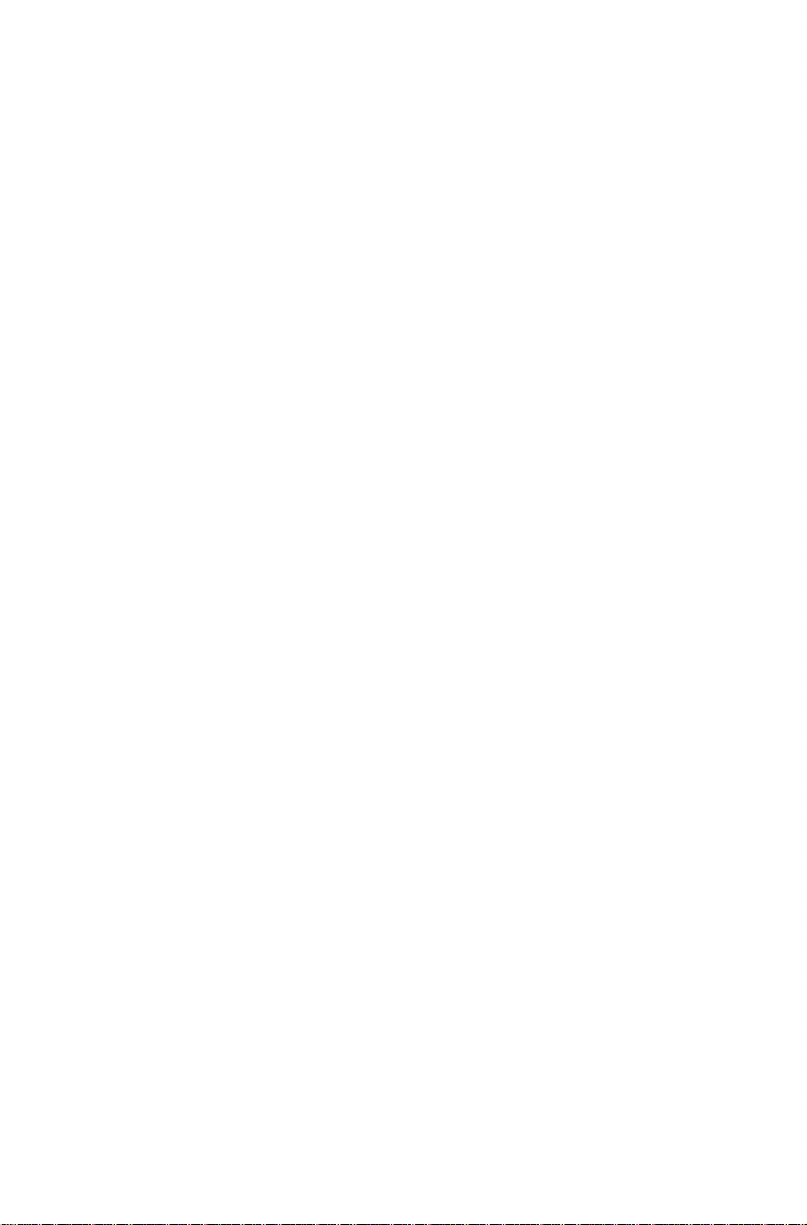
•
::E:
U
en
CC
--
en
~
en
-
Z
Z
UI
en
~,
~
en
::l
a::
~
:::E
tJ
-
Q
m
0
0
Z
0
a:a
~
·0
0
~
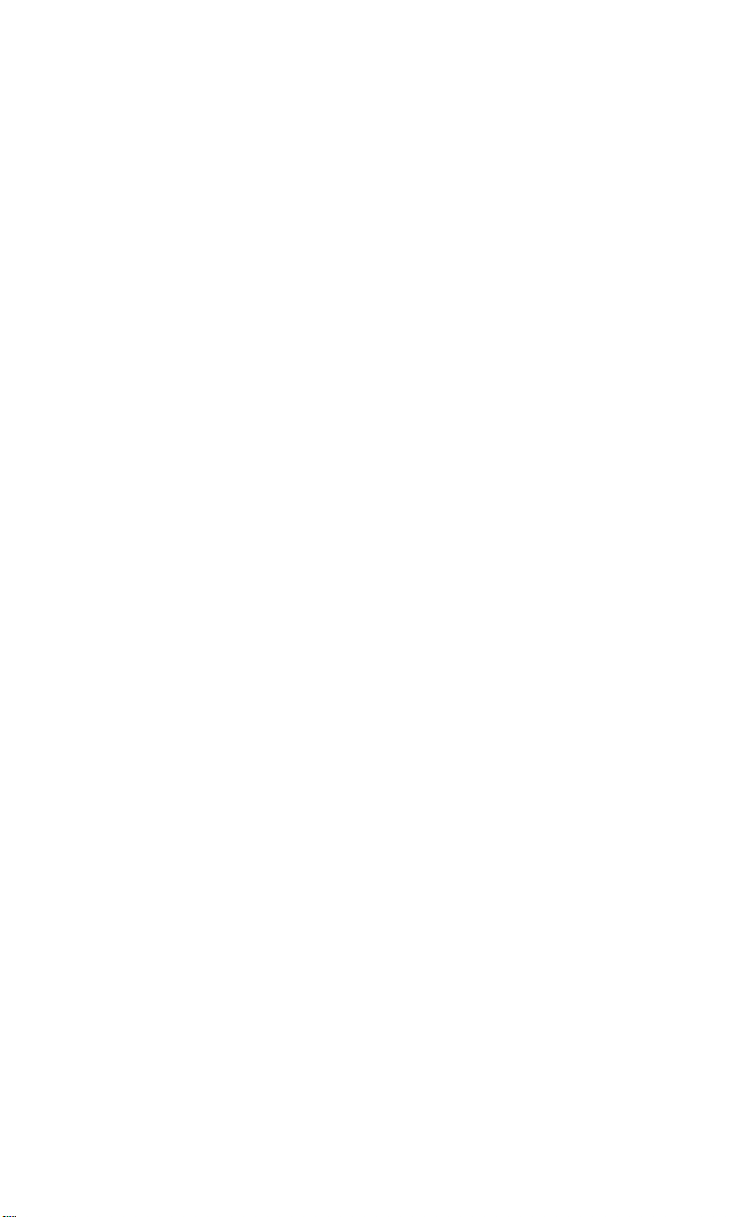
Foreword
This book was written with the object of enabling the
owner to maintain his car in perfect condition throughout
(
its life.
The Cobra 427 Chassis is designed and built at the
A.C. Factory, England, and like all other machinery of
advanced design needs regular care and attention to give
maximum results.
direction will be amply repaid by ultimate performance.
Shelby America Inc. are responsible for the conception of the
427 chassis, and in America for the fitting of the engine, and
gear box, manufactured by the Ford Motor Company of
America.
A.C. Cars were happy to co-operate to produce a sports car
of outstanding achievement.
6501 WEST IMPERIAL HIGHWAY,
LOS ANGELES, CALIFORNIA 90009
A
little time spent now and then in this
SHELBY AMERICA INC.,
Tel. 213674-1961
A.C. CARS LTD.
Registered Officeand Works:
THAMES DITTON, SURREY, ENGLAND
Telegrams:
(
"Autocarrier, Thames Ditton"
PRICE
Telephone:
Emberbrook 5621
40s.
A.T.G.
Reprint #1 1990

USEFUL INFORMATION
DIMENSIONS
Wheel Base:
Track:
Overall Length:
Width:
Height:
Weight:
Tyres:
Petrol Tank Capacity:
Electrical Equipment:
Capacity of Engine Sump:
Capacity of rear Axle:
Rear Axle Ratio:
Capacity of Gear Box:
Capacity of Radiator:
Chassis Number located on :
Engine Number stamped on:
IMPORTANT NOTE
Do not fit tyres of odd size to the rear wheels of the car. Running
the car in this condition may cause damage to the differential.
The engine of the car must pot be run with one rear wheel off the
ground with the car in gear. Under these conditions the
differential will drive the car off the jack.
It is possible to drive the transmission by raising both wheels clear
of the ground and running the engine with the car in gear.
The limited slip differential mainly when hot causes a certain amount
of grabbing when the car is making slight or sharp turns at low speeds.
This is a normal function with the
90"
Front: 53·96 Standard and Racing.
Rear: 53 Standard-55·1/8 Racing.
12'
lOt"
5' 5t"
2'
11"
Top of Scuttle--4' 1" Highest
Point on Soft Top.
21501bs.
8·15x15"
15 Imp. galls, 18 U.S. galls.
12 volt.
427 engine 6 U.S. quarts, 5 Imp. quarts.
289-6t Imp. pints, including Filter-
7iU.S. pints.
2t Imp. pints, 3 U.S. pints,
3·54 or
2t Imp. pints 289I3 Imp. pints 427.
24 Imp. pints 289I28 Imp. pints approx.
427.
Front Left or Right Wishbone Flange.
Engine Flange below rear L.H. spark
plug and on Bulkhead plate.
3·31to1
"Powr-Lok"
differential system.
1-4
litres.
"Powr-Lok'
COOLING SYSTEM
If the water level in the radiator header tank is to be checked while
the engine is hot, the pressure in the cooling system must first be released
by half turning the header tank filler cap. This permits pressure to be (
released through the overflow. It is dangerous to completely remove the
filler cap when the engine is hot without releasing the pressure as described.
Cars with aluminium radiators are fitted with a water bleed valve to
the cooling system. This must be removed in conjunction with the header
tank filler cap when topping up with water. The system is.full when water
commences to flow from the bleed valve aperture.
It is advisable to run the engine a few minutes with the bleed valve
and filler cap removed after topping up with water, this will ensure there
are no air locks left in the system.
After running the engine, the water height should again be checked
and added to if necessary. Where there is 'no bleed valve fitted the engine
should be run with the header tank filler cap removed following the same
procedure.
IMPORTANT
2
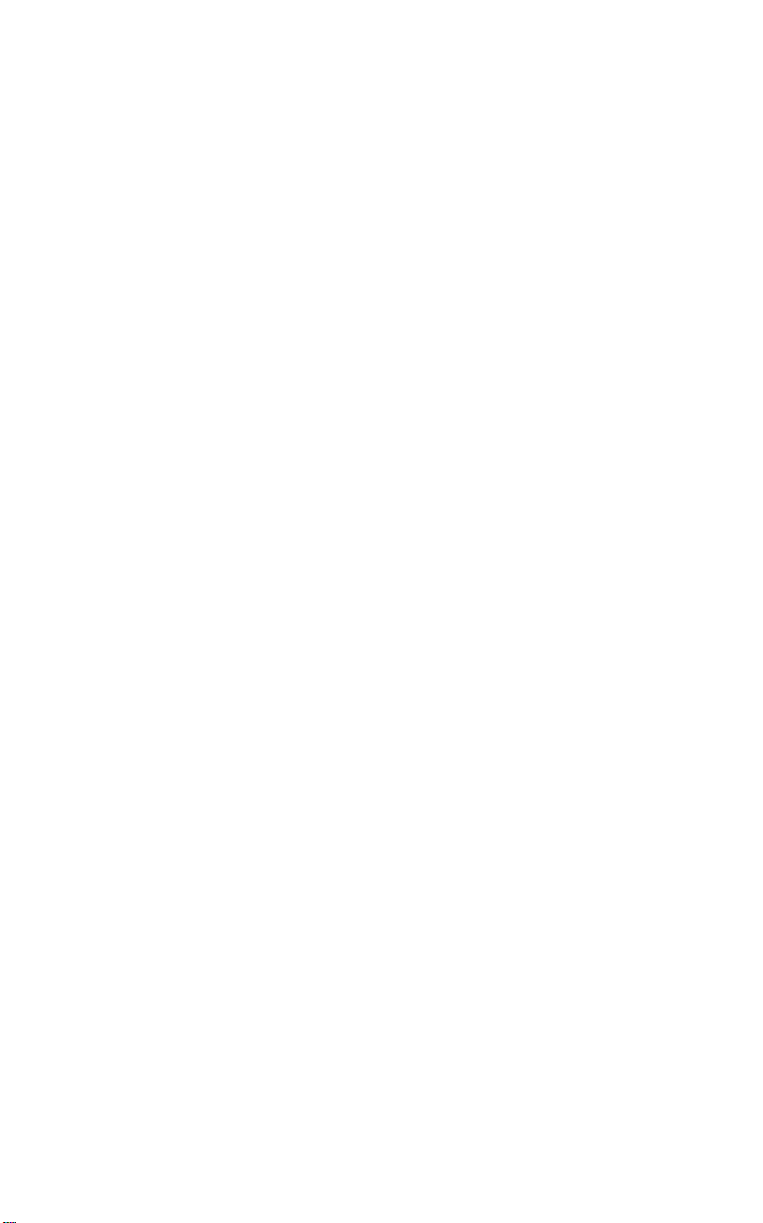
PROPELLER SHAFT AND
HALF SHAFTS
These units are manufactures by Messrs. Hardy Spicer to exceedingly
fine limits and are balanced to give freedom from vibration at all speeds.
The needle type universal joints will give long and satisfactory service
provided normal servicing is given, including greasing. Three such
greasing points are provided on each wheel drive shaft, one on each spider
and one on the slip splined joint. Two are provided on the propeller shaft
spiders. Lubrication is best carried out when the car is raised from the
(
ground and positioning of the shaft is necessary to allow the grease gun
to be applied. Attention every 2,000-3,000 miles will suffice.
Messrs. Hardy Spicer provide replacement Universal Joint Sets, these
consisting of a spider, four bearing races with needle rollers and snap rings.
In dismantling the Universal Joint observe the positions, this is so that
the yokes may be assembled in their original balance order.
Remove the spring clips and push or drive the spider to one side, this
will allow the race and needle bearing to come away. Reverse the proce-
dure to remove the other bearing. The spider with one end of the yoke
can then be removed. This procedure should be repeated to release the
spider itself.
In assembly, apply grease to retain the needles in the races and observe
that the sliding yoke is fitted to the correct splines. The yoke arms being
in line with each other.
Propeller Shaft Unit Order Number D.66976
Half Shaft Unit Order Number 55-0107jKR
I350YSA
(
3
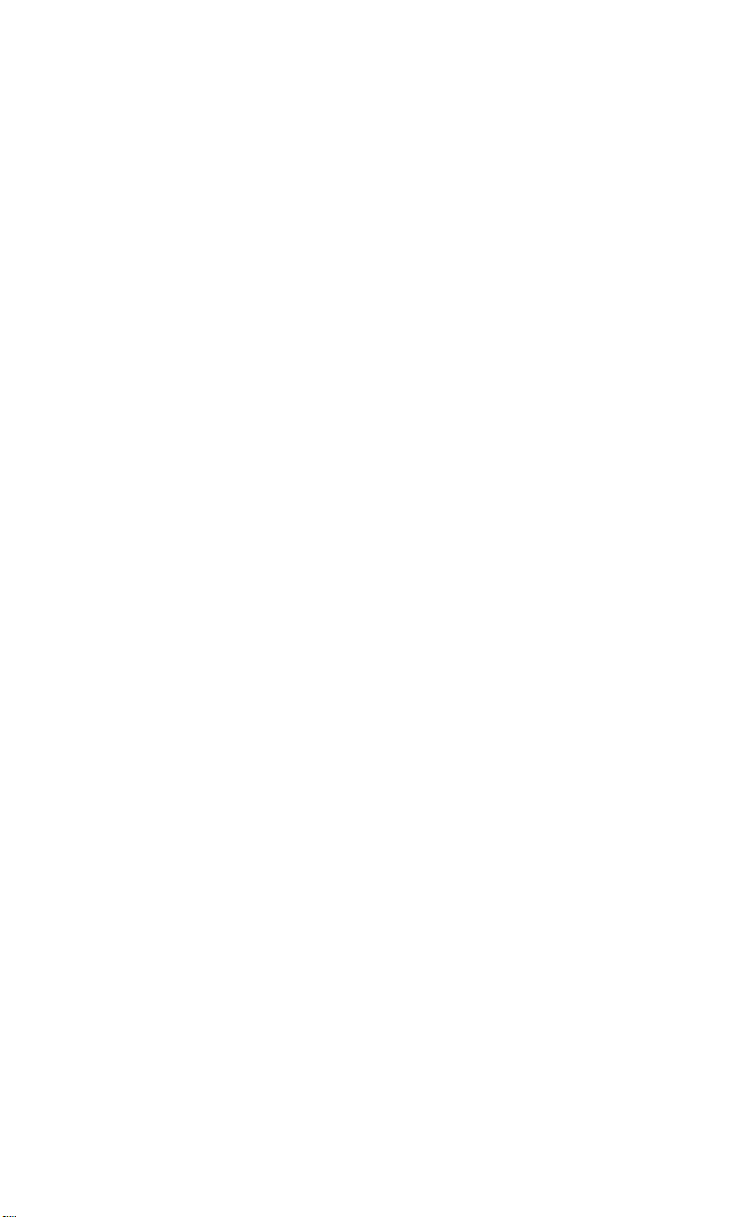
SALISBURY DIFFERENTIAL
UNIT 4HU
REMOVING THE
COBRA DIFFERENTIAL ASSEMBLY COMPLETE
The differential casing is supported on three rubber mountings. Two
of these are hanger bearings and are located on either side of the differential
casing, the front bearing is mounted on the nose of.the differential.
Unbolt the drive shaft flanges to the road wheels and the rear flange
on the propeller shaft. Remove the front mounting bolts, and support (
the weight of the differential with a jack or block.
Remove the two side hanger mountings, it may be necessary to rotate
the differential assembly when withdrawing the unit from the chassis.
DIFFERENTIAL MOUNTING
PART NUMBERS
FRONT SUPPORT CASTING C-66091
Metalistic Mounting 13/1121 D-63784
Distance Piece D-66202
Washer Internal Shake Proof
~" B.S.F. Bolts 2i" long (Hex.)
,'0"
U.N.C. Bolts 1i"long D-66198
Support packing D-66196
SIDE SUPPORT CASTINGS
Metalistic Mounting
Support Bolt with Self Locking Nut
i
B.S.F. 7" D-66208
,{" U.N.C. Bolts
11"
long D-66199
f'
D-66534
13/860 D-63503
D-63503
(1)
(2)
(1)
(2)
(2)
(4)
(4)
(2)
(4)
(2)
(4)
(
)
4
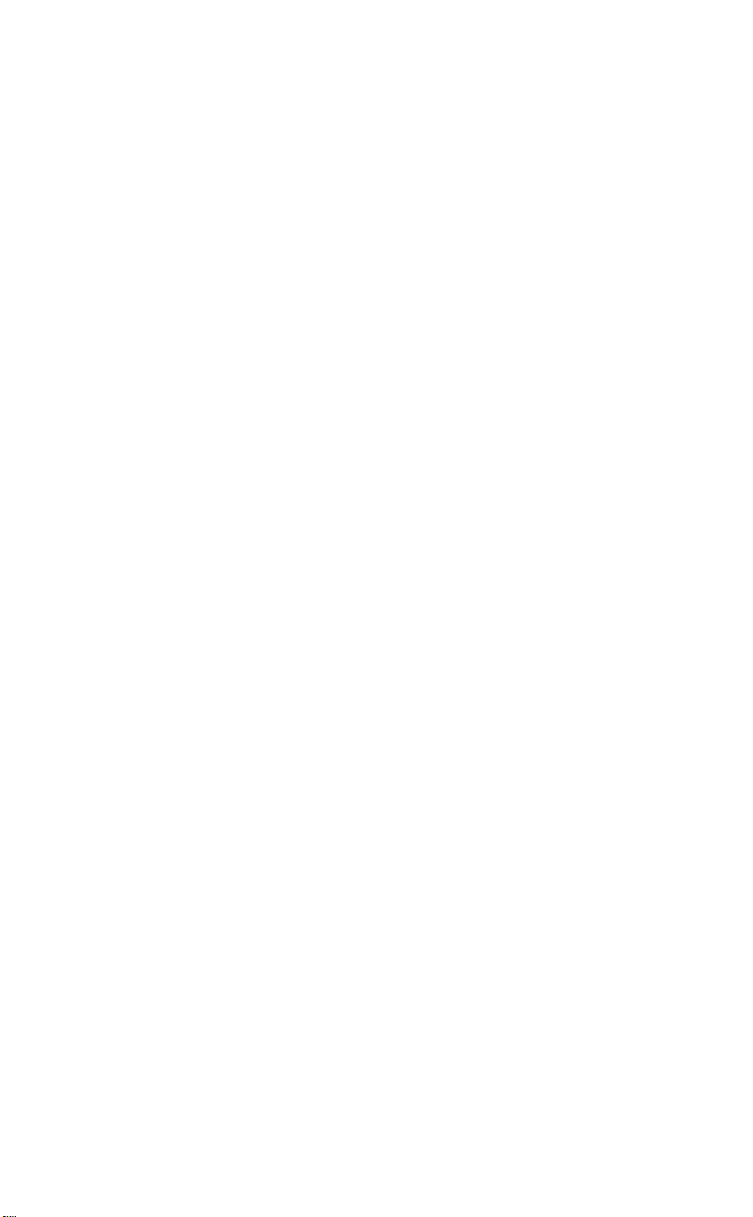
THE SALISBURY "POWR-LOK"
DIFFERENTIAL UNIT
WHY LIMITED SLIP DIFFERENTIALS ARE NEEDED
The purpose of a conventional differential is to provide equal torque
division between the two road wheels whilst compensating for the difference
in speed between the wheels when cornering. Since equal torque division
is obtained at all times, the total torque transmitted is limited by the
wheel with least adhesion. Whilst the limitation in performance of the
conventional differential has been noticeable in the past when driving on
(
ice or snow, these same factors are now assuming greater importance, due
to the trend towards a lighter weight on the axle, combined with greater
torque output from the engine. The Limited Slip Differential propor-
tions the torque so that, at all times, the wheel with greater adhesion will
transmit the greater portion of the torque available, whilst maintaining
the necessary differential action on cornering.
POWR-LOK
The Powr-Lok design combines excellent performance with low
initial cost and durability, and it is important to note that no other
assembly combines these advantages to the same degree. In operation, the
Powr-Lok combines the basic elements of the conventional differential
with the restraint of friction clutches which provide the necessary torque
bias. These basic features have been incorporated in a number of alter-
native designs but the Powr-Lok is unique in combining three alternative
methods of loading which are supplementary and provide the necessary
desirable qualities.
CONSTRUCTION
The cross pins which carry the pinion mates are so constructed that
there is clearance at the intersection to permit relative movement between
the two parts, each shaft having milled cam flats located in vee slots in the
differential case halves. The pinion mates have shoulders engaging
abutment faces on the clutch rings mounted adjacent to the differential
side gears. The clutch rings and side gears have common splines locating
on the axle shaft and the clutch rings are additionally provided with splined
hubs carrying the alternative internally splined clutch plates. The
remainder of the clutch plates are provided with 4 external lugs locating
in slots in the differential case halves. All clutch plates are specially
(
treated to obtain the desired friction characteristics and are flat with the
exception of one plate for each assembly which is dished to provide a
Belleville spring.
5
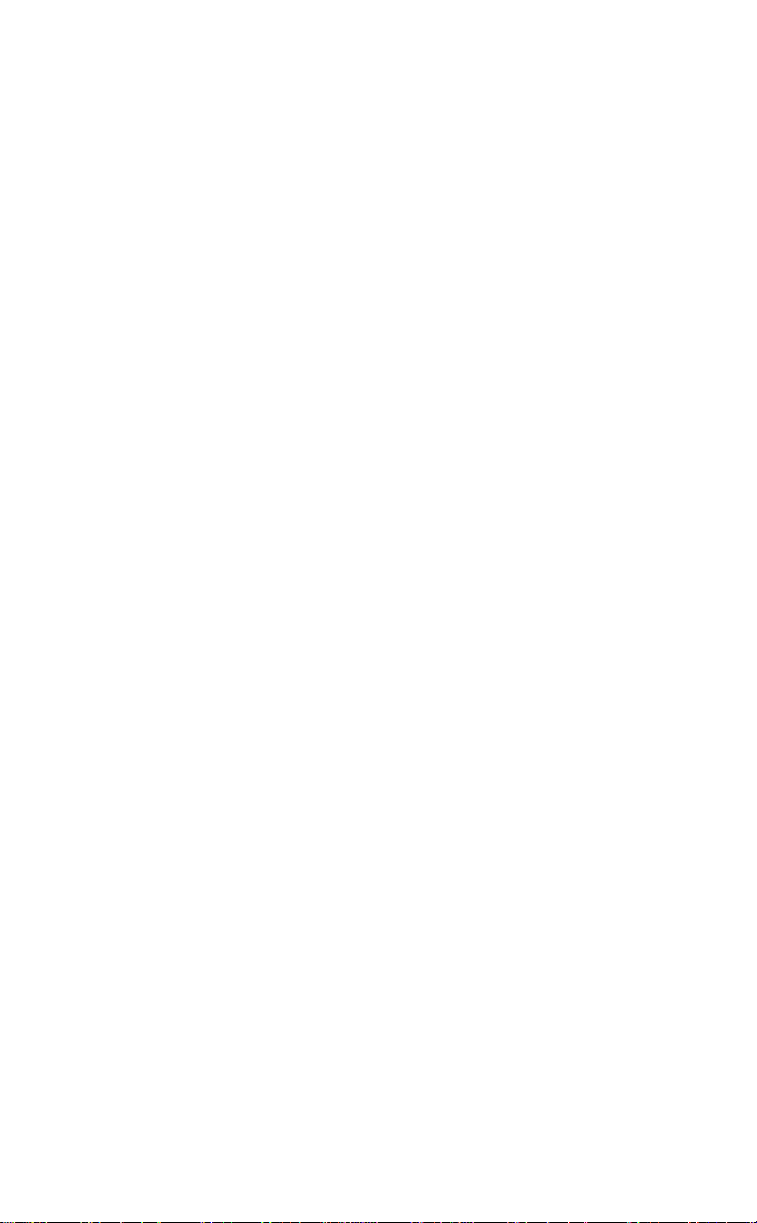
FRICTION CLUTCH LOADING
The loading of the friction clutches is effected by three different
methods-
1. Belleville Spring. Since one of the plates in each clutch pack is
dished to form a Belleville spring, the clutches are under a certain amount
of pressure at all times and there is, therefore, effective restraint of free
differential action, even if one wheel is clear of the ground. This point is
of great importance, since the other means of loading are dependent
the degree of re-action at the axle shafts.
on
SECTIONS OF T HE TV~O )
/ PLATES ~
{
~ tll~··
PRELOADING OBTAINED
BY USING DISHED PLATE
LOADING OF FRICTION CLUTCHES BY BElLEVILLE SPRING
2. The Separating Forces of the Differential Gears. As described, the
differential side gear abuts against the side gear ring and the axial loading,
due to the separating forces of the differential gears, is therefore transmitted
to the clutch pack and this loading will be directly proportional to the
torque transmitted by the gears.
THE SIDE GEAR RING LOADS
THE CLUTCH PACK AGAINST
THE DIFFERENTIAL CASE
DISHED BELLEVIL LE CLUTCH
~\~"
•. ~t: ~
J
!O
®
PRELOADING OBTAINED
BY USING DISHED PLATE
THE SIDE GEAR RING LOADS
THE CLUTCH PACK AGAINST
THE DIFFERENTIAL CASE
THE LOAD IS TRANSFERr,ED
TO THE SIDE GEAR RING
ADING DUE TO SEPARATING FORCES OF DIFFERENTIAL GEARS
THE LOAD ISTRANSFERRED
TO THE SIDE GEAR RING
6
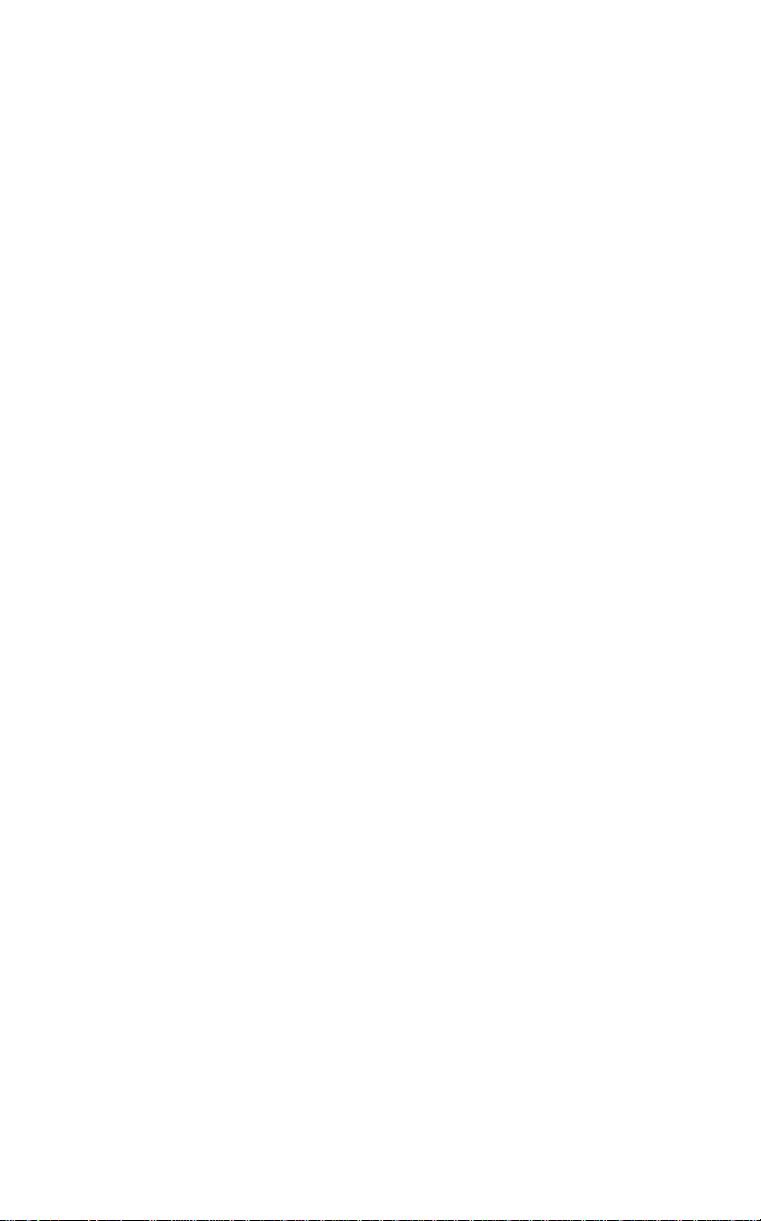
3. Carn Loading. The cam faces of the cross pins which engage vee
slots in the differential case halves, impose a loading on the cross pins
along the axis of the differentia! when torque is transmitted bythe differen-
tia! assembly. This re-action is transmitted to the side gear clutch rings
through the abutment shoulders on the differential pinion mates.
THE PINION MATE SHOULDER
TRANSFERS THE LOAD TO
THE SIDE GEAR RING
THE SIDE GEAR RING LOADS
THE CLUTCH PACK AGAINST
THE DIFFERENTIAL CASE
(
(~
THE SIDE GEAR RING LOADS
THE CLUTCH PACK AGAINST
THE DIFFERENTIAL CASE
CAM LOADING
OF
FRICTION CLUTCHES
CROSS-PIN MOVES UP THE RAMP OF
THE V-SLOT IN THE DIFFERENTIAL
CASE
OPERATION
Under all normal driving conditions, the optimum balance between
free differential action and frictional restraint of same is obtained due to
the loading of the friction clutches by the combination of the differential
gear separating forces and the cross pin cam loading. Since both these
methods of loading are proportional to the torque transmission, there will
be appropriate division of torque between the clutches and the differential
gears. Under extreme conditions, however, when one wheel is on a
surface giving extremely low or zero adhesion, it is necessary to provide
additional torque bias, since the loading provided by the cam and gear
forces depends upon there being a minimum degree of re-action at each
axle shaft In these circumstances, effective action is provided by the
loading of the clutch packs by the Belleville springs.
It should be emphasized that the Powr-Lok design is unique, since
the supplementary cam loading, in addition to the pressure on the clutch
packs from the differential gears, makes it possible to use the minimum
(
number of clutch plates, resulting in a compact assembly. It is also possi-
ble to utilize plates with comparatively low friction characteristics which
can be maintained throughout the service life of the unit, hence the claim
for durability.
POWR-LOK
Will prevent a vehicle from becoming immobile when one driving wheel
loses traction.
Provides vehicle stability under adverse road conditions.
Controls wheel spin and resultant shock loads.
Reliable and effective throughout the service life of the vehicle.
7

I
~
00
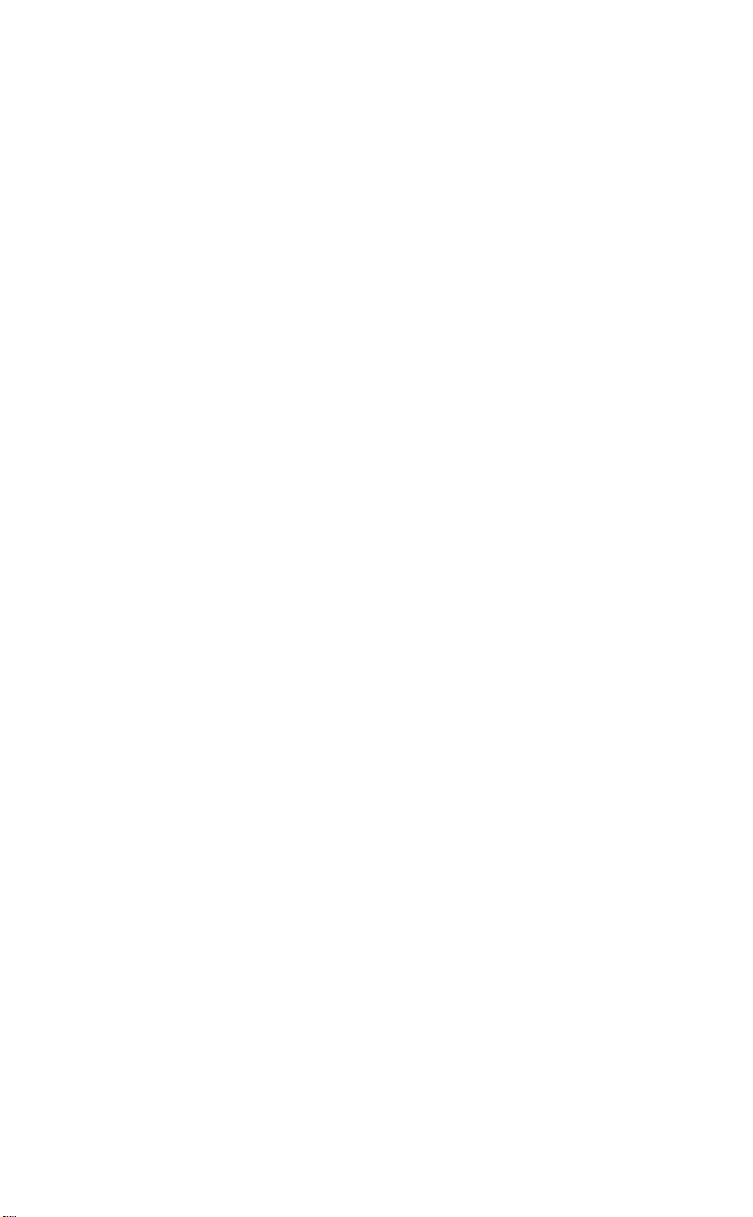
DIFFERENTIAL
PART NUMBERS
1. Front Differential Flange
2. Oil Thrower
3. Oil Seal
4. Seating Washer
5. Oil Thrower
6. Timkin Taper Roller Bearing
7. Differential Casing
(
S. Timkin Taper Roller Bearing
9. Distance Piece
10. Sealing Ring
11. Spring Washer
12. Casing retaining bolt
13. Metal Retaining Washer
14. Retaining Nut
15. Flange Tab Washer
16. Inner Drive Shaft
17. Inner Drive Shaft Retaining Casing
18. Oil Seal
19. Timkin Taper Roller Bearing
KA-2-1-GBll
2HA-021
2HA-019
2HA-020
4HA-036
2HA-022
4HU-004-12
2HA-023
4HU-018
4HA-079-2
7LW-13
7B-NC 44
16W-28
4HU-089-1
4HU-091-1
4HU-005-4
4HU-014-1
4HA-079-1
4HU-025
REAR AXLE
Service tools recommended by Salisburys Ltd.
SERVICE TOOL LIST
Tool No. Description
SE.lOI Universal Dial Test Indicator, Catalogue No. 160, supplied by
SE.103 Pinion and Differential Bearing Cone Puller.
SE.105 Pinion Bearing Cup Extractor.
SE.106 Bearing Cup Installation Tool.
SE.107 Pinion Cone Setting Gauge.
SE.lOS Pinion Oil Seal Installation Collar.
Churchill&Co., Ltd., Great South West Road, Bedfont, Middlesex.
J.
E. Baty&Co., Ltd., 39 Victoria Street, London, S.W.I.
Complete sets of Service Tools are available from Messrs. V. L.
SERVICE DATA
f
( Pinion Drop "A" ...
fa) Mounting Distance
f'I'
(b) Gear Bolts Lbs. Ft. ...
Model
Zero Cone Setting "B"
l
C/L to Brg. Housing "D"
Shaft
Torque Spanner Setting, Drive...
Diff. Preload Shim Allowance ...
Backlash ... ... . .. As etched on Drive Gear (Minimum '004")
l
Pinion Bearing Preload ... 8-I2 Ibs. in all Models
unit indicated above.
EndFio", ... ...
Service data concerning the 4H U differential is the same as the
REFER TO PAGE 38 FOR RECOMMENDED OILS.
"C'
6HA HA
1·000" ',250"
...
2·000"
...
3·375"
...
4·193"
...
4·183"
,006" to ,008" all Models
40-50 40-50
,005" all Models
9
2'125" 2·250" 2·625" 2750"
3·625" 3·937" 4·312" 4·625"
4·848" 5·130" 5·505"
4·838" 5·120" 5·495"
3HA
1·375" 1·500" 1·750" 1·750"
f'
50-60
n,"
70-80
4HA 2HA
5-818"
5·808" 6·121"
f'
50-60
k"
70-80
5HA
2'968"
4·906"
6·131"
40-50 70-80
4HA
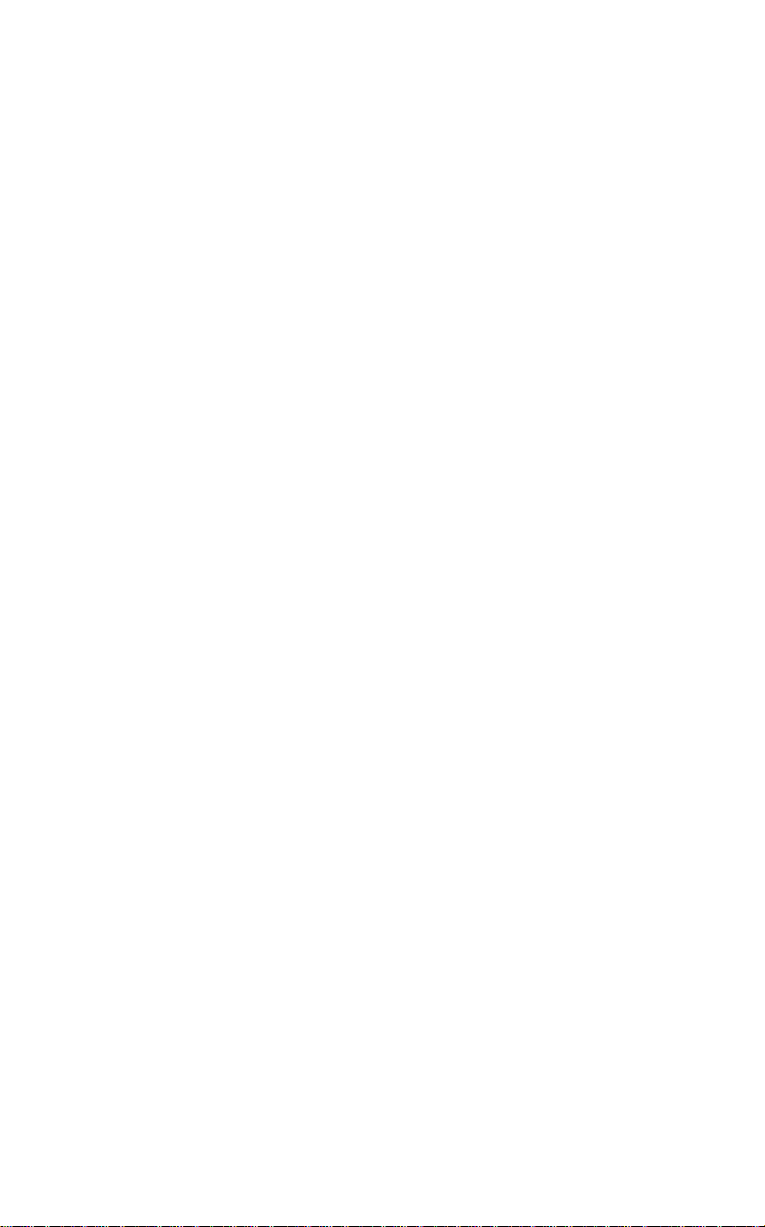
REMOVAL
TO REMOVE CALIPER-REAR BRAKES
1. Remove rear wheel.
2. Remove split pin and clevis pin from nandbrake abutment. Fig. 18.
(D.66053).
3. Remove wireon two caliper holding Bolts. Fig. 22.
4. Remove caliper holding bolts. Fig. 22 (D.6648I).
5. The caliper must be suspended from the wishbone to prevent damage
to the hydraulic brake pipe. (
6. lfthe banjo bolt, Fig. 23(376102W)is removed and the hydraulicpipe
isdisconnected, care must be taken that brake fluid is not permitted to
drop on car paintwork.
7. It will be necessary to bleed the brakes if the hydraulic brake pipe is
disconnected.
Note: Refer to rear hub drawing when carrying out this operation.
Page 11.
TO DISMANTLE REAR HUB AND UPRIGHT
1. Remove caliper holding bolts Fig. 22(D66481) and suspend caliper
wire from chassistubing.
2. Disconnect parking brake cable from the abutment Fig. 18(D66053)
on upright.
3. Disconnect four holding bolts on drive shaft outer flange Fig. 15
(4HU-077-2).
4. Disconnect top wishboneupper ball joint, RBJ-76. Fig. 2, page 15.
5. Loosen the two
tap out holding pin, Fig. 6, page 15 (D.66851).
NOTE: Before undertakingthe above operation, the disc and hubshouldbe
supportedby wire from a chassis tube.
If the hydraulic brake pipes are disconnected from the caliper
willbenecessaryto bleedthe brakes.
-!a"
cramp bolts on the lower wishbone outer end and
OF
REAR HUB
by
it
10
(
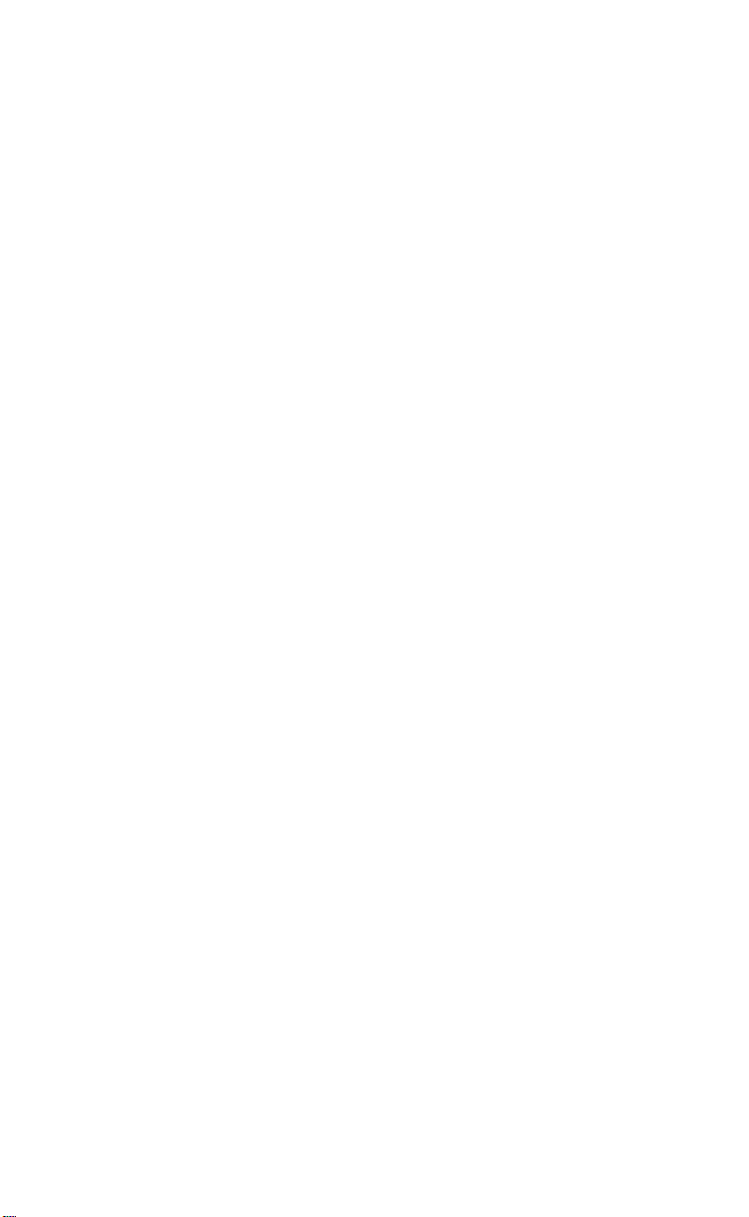
REAR HUB AND CALIPER DRA WINGS
--®
(
2.1
STANDARD
(,~\.----------- ' <,
~---
9
~
~
(
,https://manualmachine.com/
0---
https://manualmachine.com///
8
2
RACING
11
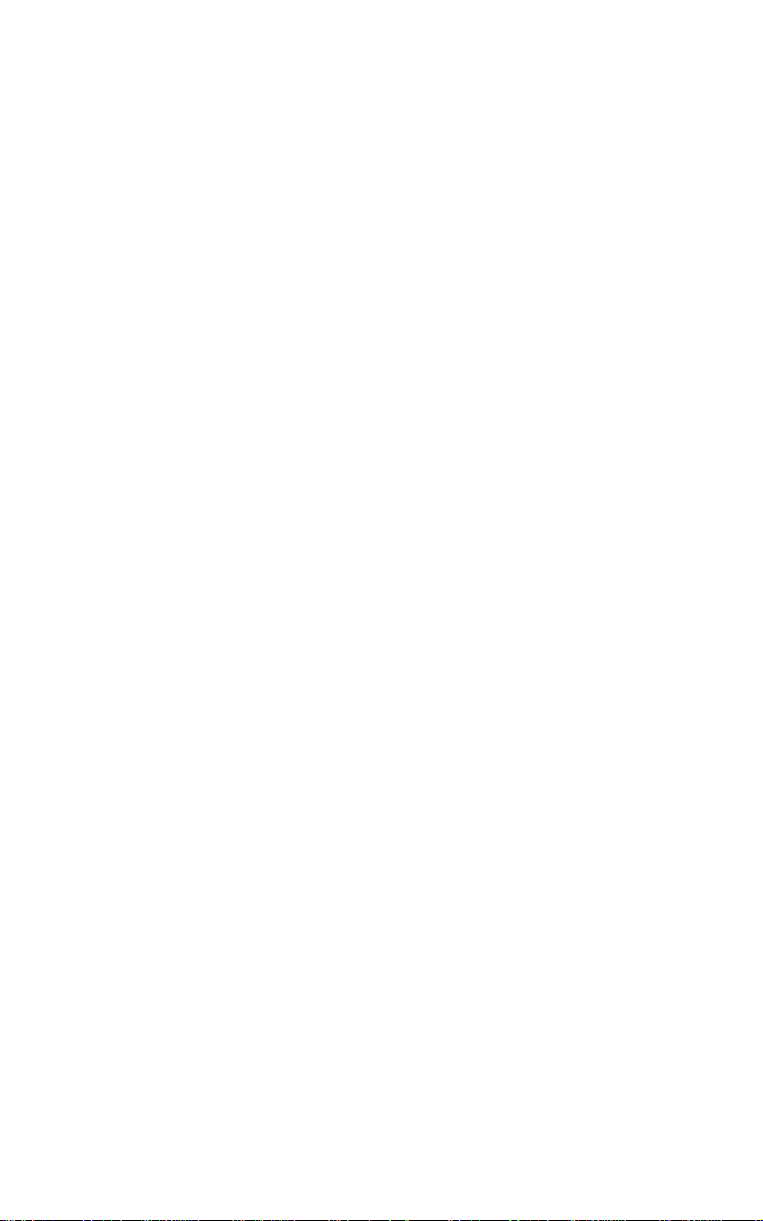
REAR HUB PART NUMBERS (STANDARD)
1. Rear Carrier
2: Hub Flange Bolt
3. Rear Hub
4. Rear Disc
5. Drive Pegs
6. Drive Peg Nuts
7. Oil Seal Outer "Burtonwood"
8. Oil SealInner "Burtonwood"
9. Spacer
10. Cone Outer "Timkin"
11. Cone Inner "Timkin"
12. Cup "Tirnkin"
13. Distance PieceLarge
14. Distance PieceSmall
15. Flange "Salisbury"
16. Washer "Salisbury"
17. Lock Washer
18. Handbrake abutment
19. Flange Bolt
20. Flange Nut
21.
Caliper 12/3 Girling
22. Caliper Bolt
23. Banjo Bolt Girling
24. Flexible Hydraulic Pipe
25. Connecting Gasket
26. Banjo
27. Banjo Gasket
-!an
B.S.F. High Tensile
-!on
B.S.F. Self-locking nut
It"
B-669I2-3
66074
C-66858-9
B.66908
ShelbyAmerican Inc.
ShelbyAmerican Inc.
275-3346-10
187-318
D-66871
2774X
2788A
2720
D-66872
67184
4-HU-077-2
16W-28
Salisbury 4-HU-091-1
D-66053
64032764/5
D-6648
I
376102W
3700634W
378711
64474288
378700
(
REAR HUB PART NUMBERS (RACING)
1. Rear Carrier
2. Hub Flange Bolt
3. Rear Hub
4. Rear Disc
5. Wheel Drive Pegs
6. Drive Peg Nuts
7. Oil SealOuter "Buttonwood"
8. Oil Seal Inner "Buttonwood"
9. Spacer
10. Cone Outer
II. Cone Inner "Timkin"
12. Cup "Tirnkin"
13. Distance Piece "Large"
14. Distance Piece·"Small"
15. Flange "Salisbury"
16. Washer "Salisbury"
17. Lock Washer
18. Handbrake Abutment
19. Flange Bolt :." B.S.F.
20. Flange Nut
21. Caliper ORA Girling
22.
Caliper Bolt
23. Banjo Bolt Girling
"Timkin"
-!o"
It"
B.S.F. Self-locking
High Tensile
12
B-66914-5
66074
C-66860
B-66909
ShelbyAmerican Inc.
ShelbyAmerican Inc.
275-3346-10
187-318
D-66871
2774X
2788A
2720
D-66872
67184
4-HU-077-2
16-W-28
4-HU-091-1
D-66053
64032772/3
D-66365
376102W
(
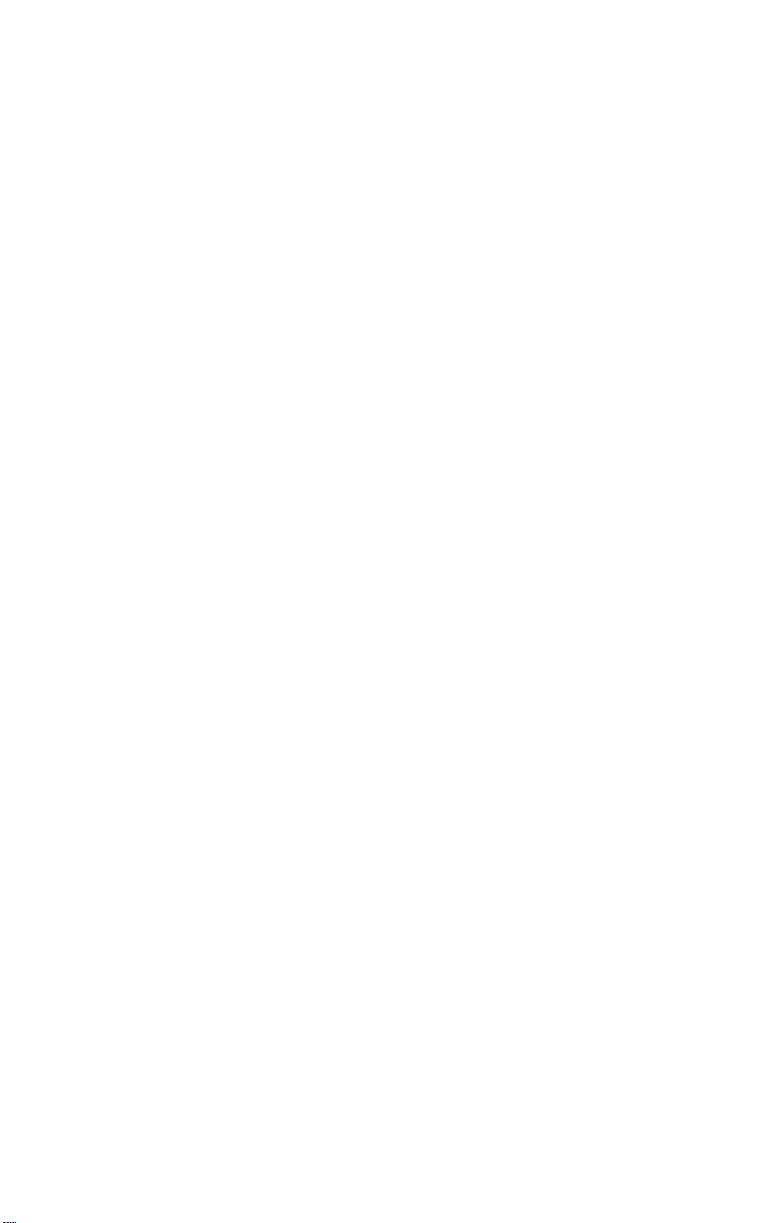
24. Flexible Hydraulic Pipe
25. Connecting Gasket
26. Banjo
27. Banjo Gasket
TO REMOVE REAR WHEEL BEARINGS
1. Remove locking washer Fig. 17 (Salisbury 4-HU-091-l).
2. Undo and remove Hub Flange Bolt, Fig. 2 (66074).
(
3. Remove spacer washer, Fig. 16(16W-28).
4. Remove drive flange, Fig. 15 (Salisbury 4-HU-077-2). This is a very
tight fit and can only be removed with a press of a draw.
5. The hub carrier Fig. 1 (B-66912-3) will then lift away with the two
oil seals Fig. 7 (Burtonwood 275-3346-10), Fig. 8 (Burtonwood
187-318), both bearing cups Fig. 12 (Tirnkin 2720) and the inner
bearing cone Fig. 11 (Tirnkin 2788A).
6. The outer bearing cone Fig.l0 (Timkin 2774X)will remain on the inner
hub shaft Fig. 3 (C-66858-9) with one large spacer Fig. 13 (D-66872),
and one small distance piece Fig. 14(67184), the spacers will lift away
without difficulty but the outer bearing Fig. 10 (Timkin 2774X) then
exposed will require a draw to facilitate removal.
7. The distance spacer Fig. 9 (D.66871) will lift away without trouble
when the bearing is removed.
8. The bearing outer cups Fig. 12 (Timkin 2720) and oil seals .Fig. 7
(Burtonwood 275-3346-10) and Fig. 8 (Burtonwood 187-318), which
will have remained with the hub carrier Fig. 1 (B-66912-3) may be
tapped out with a drift.
Note: There should be ·1000 vertical float when the hub is assembled; the
smaller distance piece mentioned above Fig. 14 (67184) measures
between ·150 to ·170 according to the amount of hub float; care
should be taken that the ·1000 vertical float is maintained when
the hub is reassembled.
Note: Part numbers quoted above are for a standard hub, racing part
numbers are on page 12.
2700634W
378711
64474288
378700
REFER TO REAR HUB DRAWING WHEN CARRYING OUT
THIS OPERATION, PAGE 11
(
13
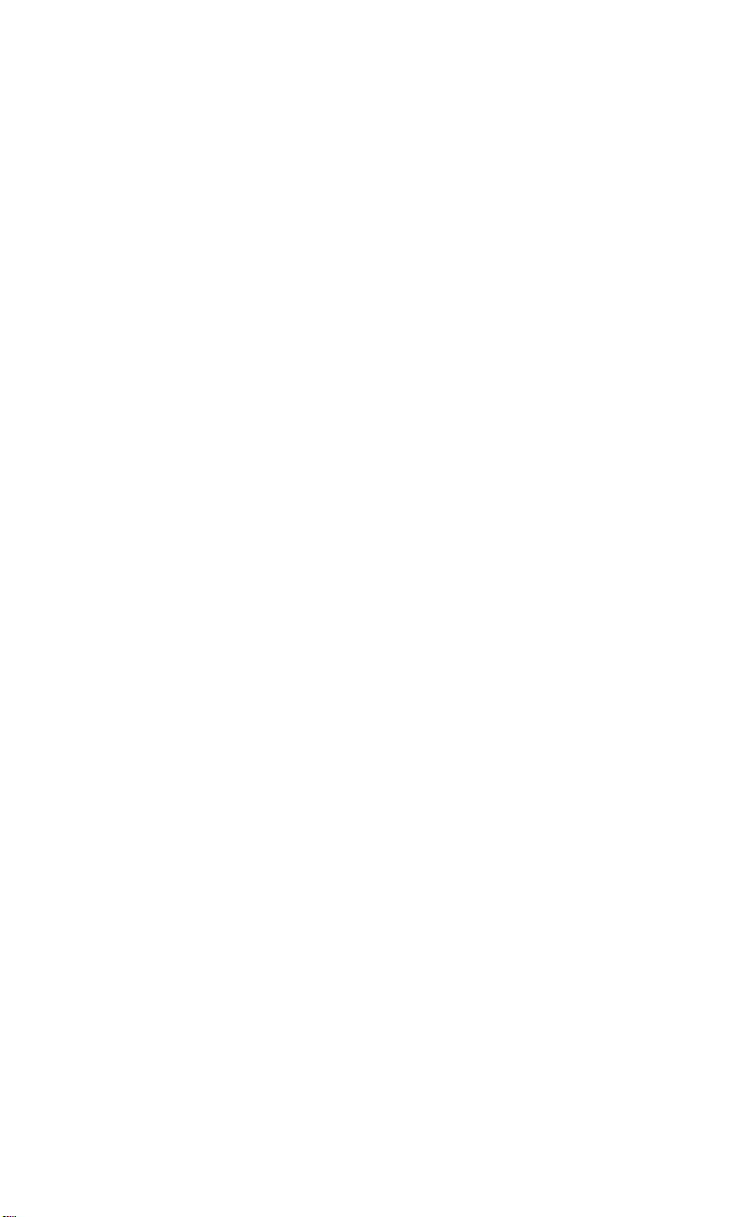
SUSPENSION UNITS
Upper Rear Wishbone Assembly (Photograph page
Wishbone Welded Assembly C.66823 (Fig. 1 photograph)
Spherical Bearing Joint to Rear Vertical Link (Fig. 2 photograph)
Spherical Bearing Rod End RBJ-76 (Fig. 2)
Lock Nuti"B.S.F. (Fig. 2)
Rubber Dust Shield
Spacer R.R.W.8 (Fig. 2)
1"B.S.F.
2i"
R.R.S8
Bolt (Fig. 2)
(Fig. 2)
IS)
1" B.S.F. Self-locking nut (Fig. 2)
Upper Rear Wishbone Assembly Inner Bushes (Fig. 13 photograph)
Bush Metalastic 13/935 (Fig. 13)
Special Bolt D-67179 (Fig. 13)
i"
B.S.F. Self-locking Nut (Fig. 13)
Wishbone Pivot Cup D-66819 (Fig. 13)
Lower Rear Wishbone Assembly (Fig. 10 photograph)
Welded assembly Number B-66881-2
Inner Lower Wishbone Bearing (Fig. If)
Adjusting Nut D-66829 (Fig. 11)
Sleeve D-66828 (Fig. 11)
o
Ring (Superfect) S.H.96-307 (Fig. 11)
Spherical Bearing (Rose) RBJ-210 (Fig. 11)
Circlip (Anderton) NAM-1300 (Fig. II)
Wishbone Pin and Bearings (Fig. 6 photograph)
Nylon bushes 12DU-16 (Fig. 6)
Rubber and metal seals 07S-IOO-SBW (Fig. 6)
Clamp Bolts
Chrome Pin D-668S1 (Fig. 6)
Rear Suspension Trailing Link (Fig. 8 photograph) 66877C
Trailing Link to Wishbone Bearing (Fig. 7)
Spherical Bearing and Circlip RBJ-20S/Seeger Circ1ip
3" Bolt (Fig. 7)
Two packing pieces (Fig. 7)
-!;,",
Ii",
!i"
nut (Fig. 6)
!i"
int. (Fig. 7)
1"Locking Nut (Fig. 7)
Trailing Link to Chassis Bearing (Fig. 9 photograph)
Spacer R.R. W.8 (Fig. 9)
Rubber Dust Seal R.R.S.8 (Fig. 9)
Spherical Bearing End Rod R.B.J.76 (Fig, 9)
i"
B.S.F. Lock Nut (Fig. 9)
S"
Bolt Xj-" (Fig. 9)
j-"
Locking Nut (Fig. 9)
Two packing pieces (Fig. 9)
Ruhber Bushes-Metalastic 13/1667, or Silentbloc E2088 (Fig. 9)
(
(
14
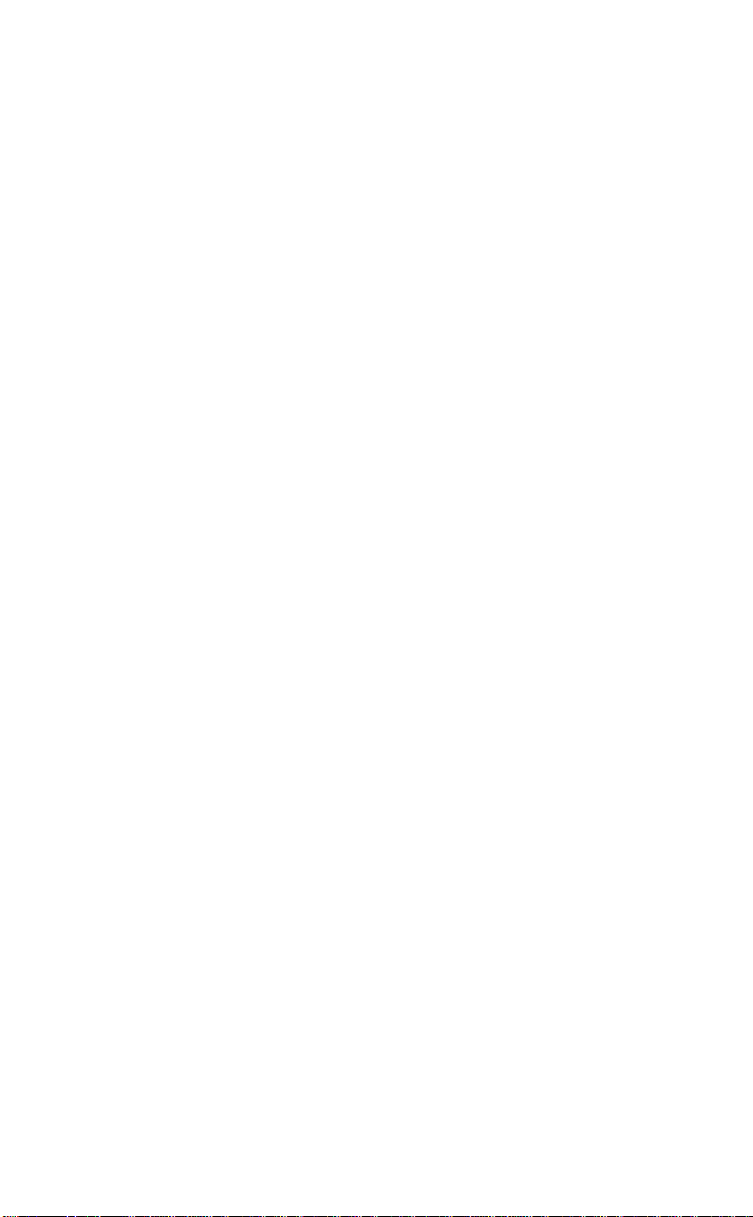
REAR SUSPENSION UNITS
1. Rear upper wishbone.
2. Upper Wishbone to rear upright spherical ball joint.
3. Rear brake caliper.
4. Shock absorber bottom mounting, reference to page 36.
5. Nylon bushes rubber and metal seals.
6. Chrome pin.
7. Trailing link, to lower wishbone, bearing.
( 8. Trailing link.
9. Trailing link to chassis bearing.
10. LOwerrear wishbone.
11. Lower wishbone inner bearing.
12. Differential front support, reference to page 4.
13. Upper wishbone inner bushes.
14. Differential side hanger bearings, refer to page 4.
15. Shock absorber top mounting refer to page 36.
Note:
Part numbers for suspension units above-are itemised on page 14.
Shock absorber bearings page 36.
(
15
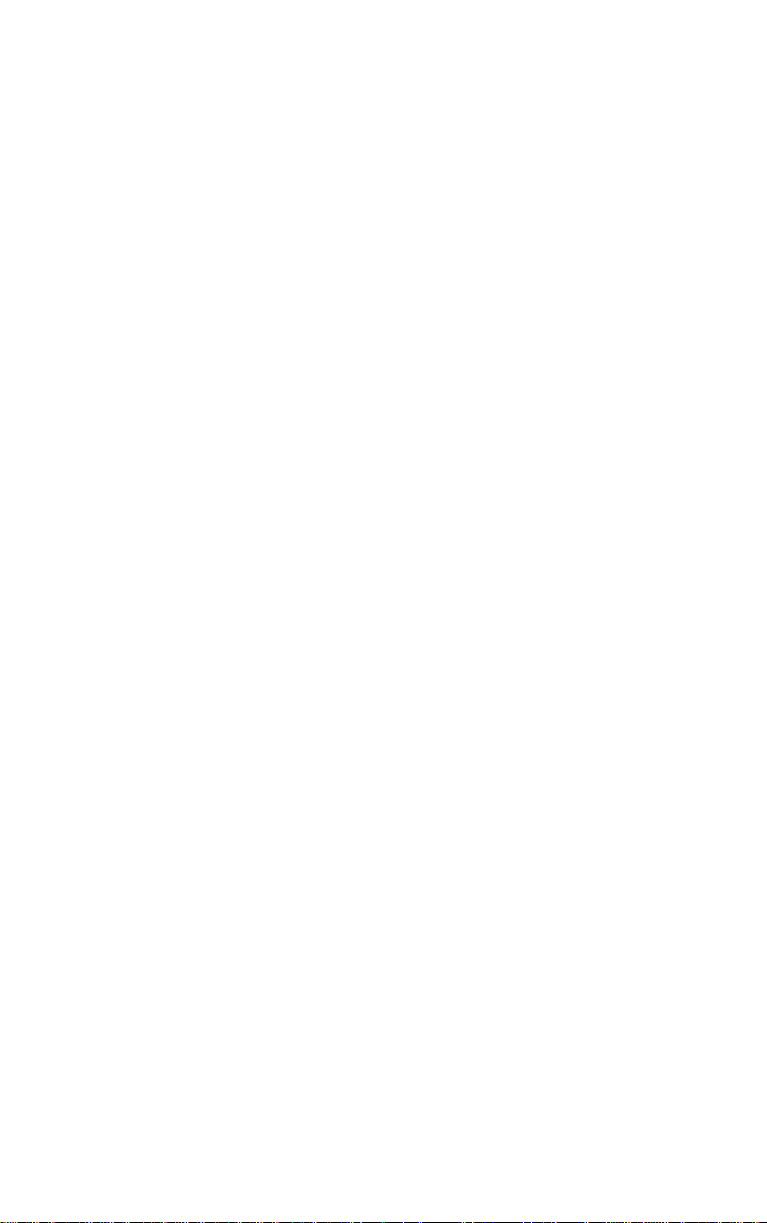
REAR
The rear suspension is comprised of an upper wishbone Fig. I
(C-66823) which is suspended from the chassis by rubber bushes Fig. 13,
page 15, (13/935) held in place byi"bolts {O-67I79) and cup washers
diameter (D-668I9).
The bolts are inserted from inside theVof the wishbone with the cup
washers inserted from outside, the assembly is retained byi"locking nuts.
The outboard end of the upper wishbone comprises at"metal ball
joint Fig. 2 (RBJ-76), and two packing washers, to which the rear upright
is attached by a
and the rubber gaitered and requires no attention.
Above items detailed on page 14, under Upper Rear Wishbone
Assembly.
t"
x
2f' bolt andt"self locking nut, the ball joint is sealed
SUSPENSION
Upper Unit
i"
REAR
The lower rear suspension unit comprises a narrow angle wishbone
Fig. 10 (B-66881-2) page 15, with the triangle point chassis mounted, and a
radius arm Fig. 8 (66877C), chassis located at the leading end Fig. 9, with the
trailing end attached to the outer wishbone Fig. 7, page IS, this arm accepts
braking and accelerating forces, all points of rear suspension are sealed
on assembly, and do not require any further attention.
The inner wishbone bearing Fig.
joint (RBJ-21O), two circlips, a steel tube threaded at the ends, a
bolt with locking nut. Attached to the threaded tube are two adjusting
nuts, the positioning of which determines the running angle of the rear
wheeL
The base of the rear upright is attached to the outer part of the wish-
bone by a chrome pin Fig. 6 (D·6685
Fig. 5 (12Du-16), inserted in the wishbone Fig.to(B·66881-2), the chrome
pin is retained in position by clamp bolts
of the upright, each bearing is sealed against dirt and dust by rubber and
metal seals.
This bearing does not require attention.
The trailing link Fig. 8 (66877C) is attached to the wishbone.by a
t"
ball joint Fig. 7 (RBJ-205), lubricated and sealed, a 3" bolt, two packi nd
pieces and
should not be touched.
lubricated and sealed ball joint Fig. 9 (RBJ·76), operating in conjunction
with two chassis mounted rubber bushes Fig.9(13/1667), a
t"
locking nut and two packing pieces complete the assembly.
Assembly and Rear Suspension Trailing Link.
-!"
locking nut. This bearing is grease packed and sealed and
The leading end of the radius arm is attached to the chassis by a
Above items detailed on page
SUSPENSION
Lower Unit
II
comprises a sealed metal ball
I),
which runs through nylon bushes
f.,",
If' and
14,
under Lower Rear Wishbo ne
16
f,;"
nut at the base
y
x
5" bolt,
in
X
4"
(
r'
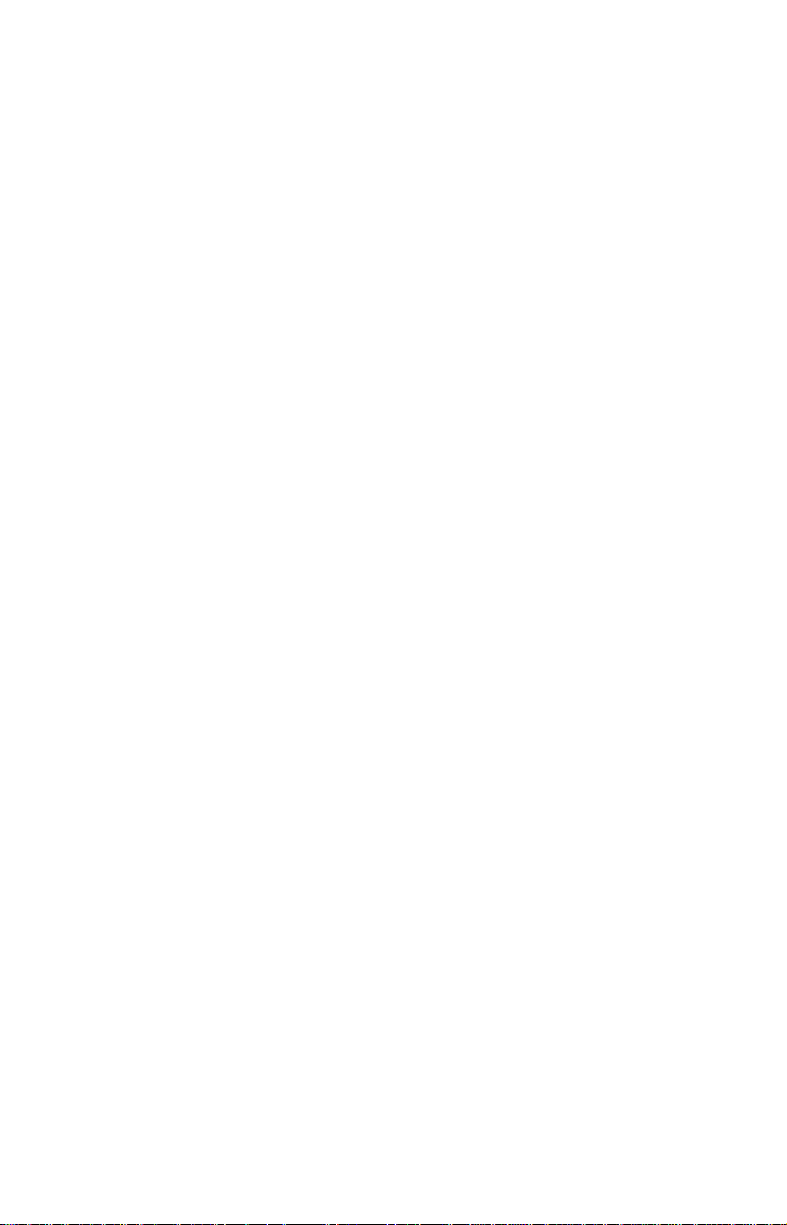
REMOVAL OF FRONT HUB
Castor Angle 3°
Camber Angle front Nil
Camber Angle rear 2° Neg.
Toe in front wheels
King PiHinclination 11°
*/1
TO REMOVE CALIPER FRONT
BRAKES
1. Remove front road wheel.
2. Remove caliper bolt locking wire, Fig. 23.
3. Undo and remove the two 16j3P caliper holding bolts, Fig. 21
(D.66483)
4. The caliper, Fig. 22, must be suspended from the wishbone to prevent
damage to the hydraulic brake pipe when the holding bolts are
disconnected.
5. If
the
hydraulic brake pipe is disconnected Fig. 25 (64474288) care
must be taken that brake fluid is not permitted to drop on the car body
work.
6. It will be necessary to bleed the brakes as indicated on page 34, if the
hydraulic brake pipe is disconnected.
7. When removing the caliper it will assist if reference is made to the
front hub and caliper drawings, page 18.
TO REMOVE FRONT VERTICAL
LINK
1. Unbolt caliper, Fig. 22 (I6j3P), and suspend by wire from chassis tube.
2. Remove locking nut and wire from inside top wishbone, Fig. 1, page 23,
and pull top of vertical link away. Fig. 2 (C.66813)-pages 18and 23.
(
3. Remove with ring spanner, the locking nut visible at the base of the
vertical link, and pull lower ball joint taper away, Fig. 3, page 23.
4. To remove the lower ball joint from the wishbone, remove the two
wired cap holding bolts together with the cap, the ball joint will then
withdraw through the base of the wishbone. Fig. 3, page 23.
5. The top ball joint may be removed from the upper wishbone tongue
upon removal ofthe selflocking nut. Fig. 2,page 23.
Reference should be made to the photographs illustrating the
composition of the upper and lower ball joints, page 22, before undertak-
ing verticle link removal.
The upper ball joint is a taper fit, and will require tapping to remove.
17
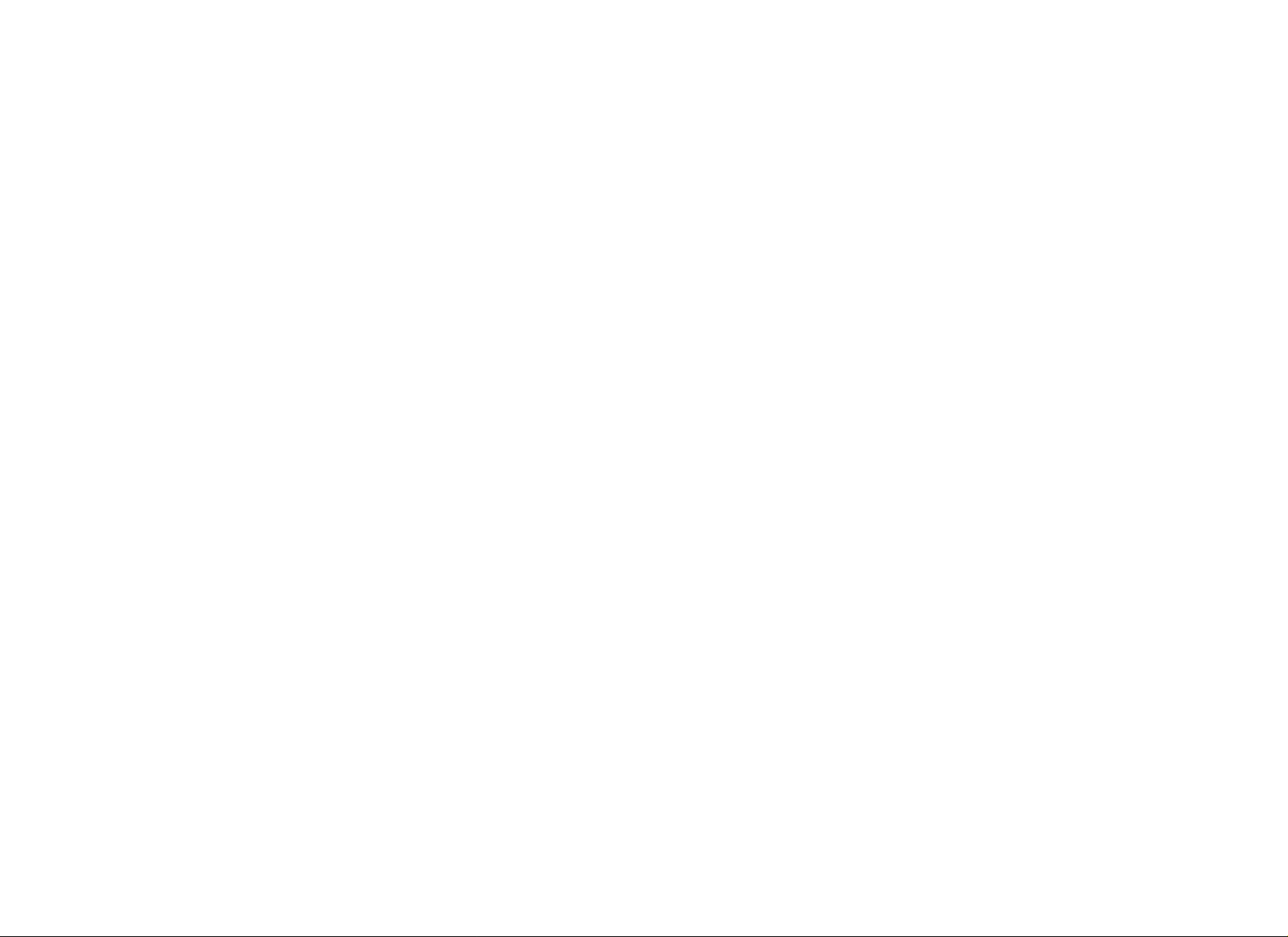
27
FRONT HUB AND CALIPER
DRAWINGS
••
®--
@ - ~\ ~
@
~ (14'i15
I
STANDARD
&
<.
,~
®--
~ ~~;~
(
6
13
if'l
16
RACING
18
14
I
~
~I
>-<
15
(
)
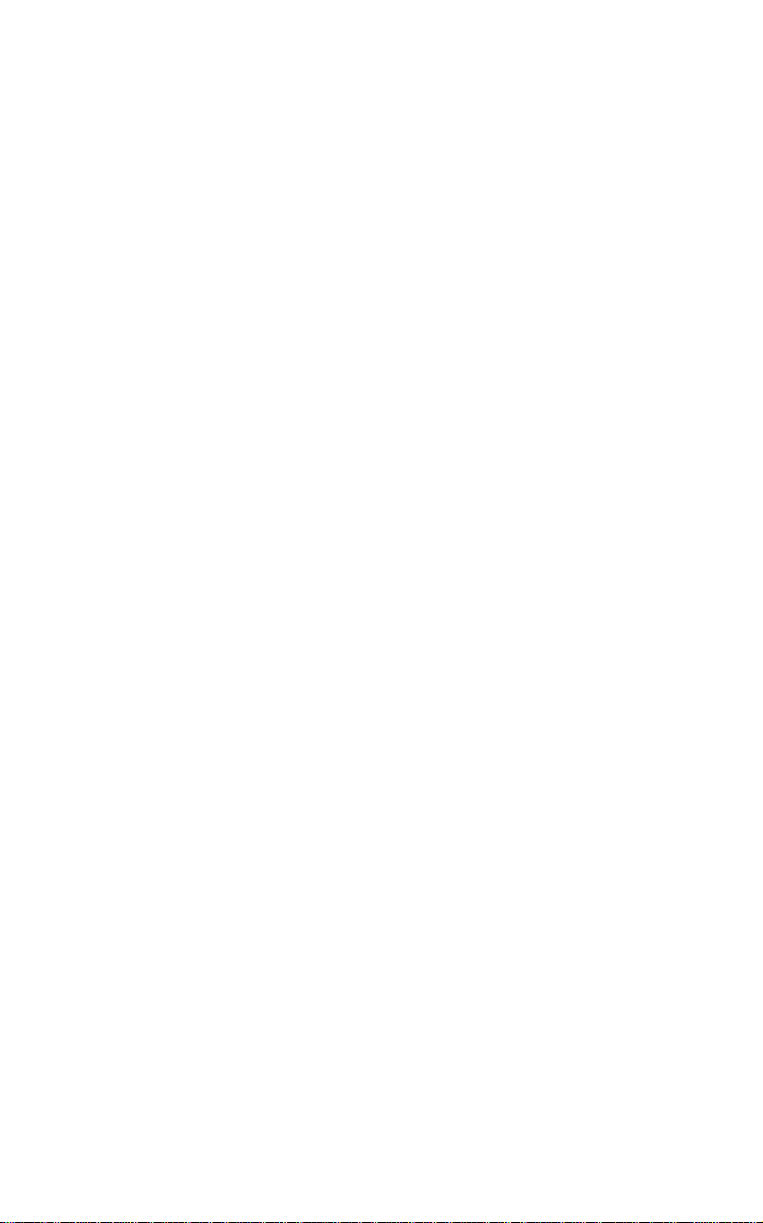
FRONT HUB PART NUMBERS (STANDARD)
1. Wheel Dunlop
2. Vertical Link C-668 I3
3. Stub Axle D-66821
4. Hub C-66852-3
5. OuterBearingConejOuterBearingCup LM.l1949-LM.1l91O
6. InnerBearingConejlnnerBearingCup LM.67048-LM.67010
7. Sealing Disc D-66445
8. D-Washer D-66446
9.
-?O"
dia. B.S.F. Slotted Nut FN.309
(
10. CotterPintHdia.lt"LG U.704
11. Washer
12. i"dia. B.S.F. Self locking nut
·13. Disc B-6691O
14.
io"
15.
io"
16. Hub nut SK-686
17. Steering Arm C-66460-1
18.
i"
19.
i"
20.
0
21. Caliper bolt D-66483
22. Caliper 16j3P 64032770-1
23.
-h-"
24. Gasket 378700
25. Banjo 64474288
26. Bolt 376102W
27. Flexible hose Girling Long 3700634W
28. Gasket 378711
29. Hub Dust Plug 67197
-tV
J.D. 1H" O.D. x 8G
dia. B.S.F. boltxIt" HT
dia. B.S.F. Self-locking nut
dia.
B.S.F. Bolt 2" long
dia. B.S.F. self-locking nut
Ring D-1614 M
dia. Soft locking wire
FRONT HUB PART NUMBERS (RACING)
1.
Wheel
2; Vertical Link
3. Stub Axle
4. Hub
5. Outer Bearing Cone/Outer Bearing Cup
6. Inner Bearing Cone/Inner Bearing Cup
7. Sealing Disc Nilos
(
8. D-washer
9.
-?o"
dia. B.S.F. Slotted Nut
10. Cotter Pin t" dia. If'long
11.
Washer
12.r dia. B.S.F. Self locking nut
13. Disc
14.
i"
15. Wheel Peg
16. Hub nut
17. Steering Arm
18.
r
19.
i"
-tt-"
1.
D. IH"O.D.x8G
U.N.F. Peg nut
dia. B.S.F. Bolt 2" long
dia. B.S.F. Self locking nut
19
Shelby American
C-66813
D-6682l
C-66854-5
LM.11949-LM.II910Timkin
LM.67048-LM.67010Timkin
D-66445
D.-66446
FN.309
0.704
B-66911
Shelby American
Shelby American
C-66849-50 Shelby American
C-67023-4
FB.106/16