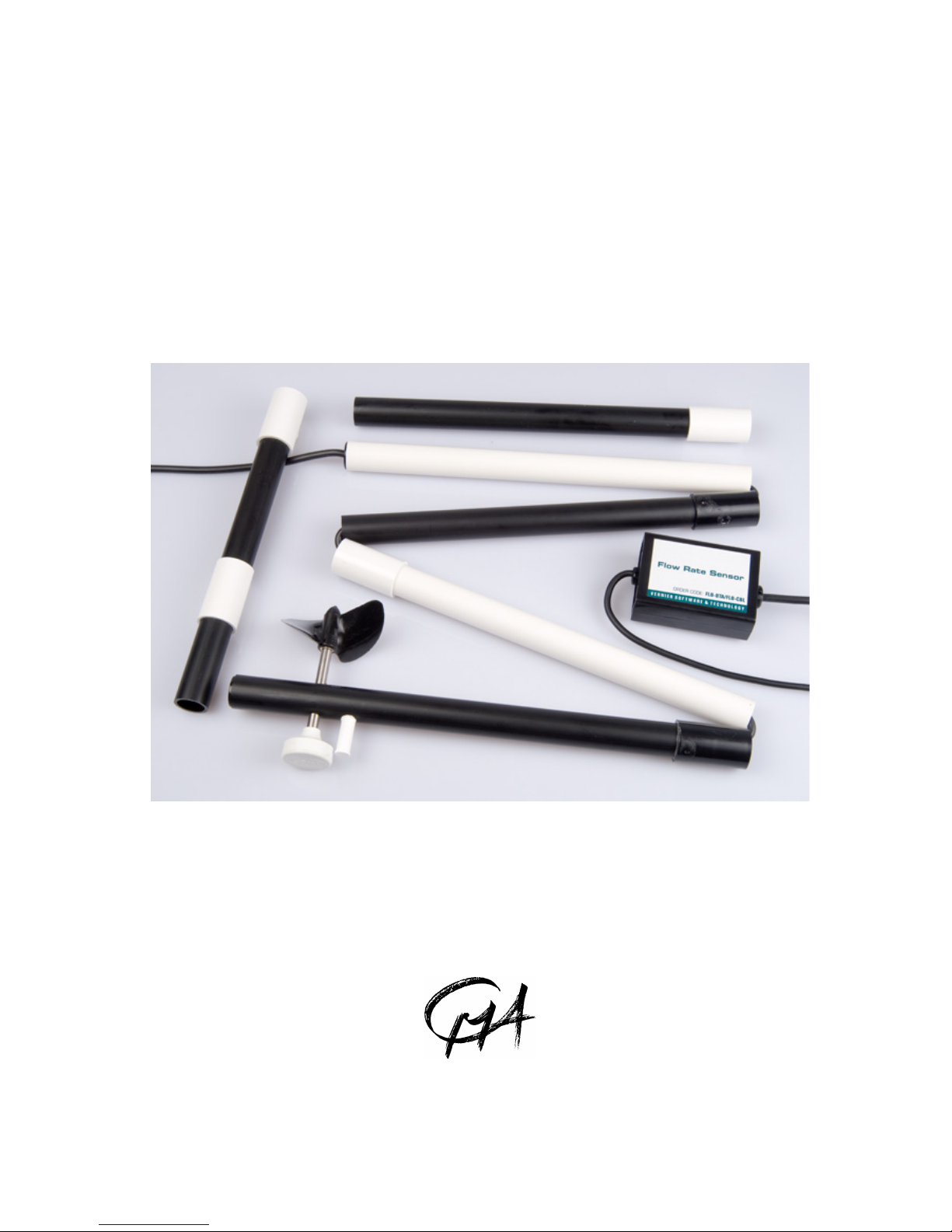
FLOW RATE SENSOR 0387I
0 .. 4 M/S
User’s Guide
CENTRE FOR MICROCOMPUTER APPLICATIONS
http://www.cma-science.nl
Figure 1. The Flow rate sensor 0387i

Description
The Flow rate sensor 0387i measures the velocity of flowing water. It can be used to
study the discharge, flow patterns, and sediment transport of flowing water.
The Flow rate sensor is equipped with impeller rod with 5-meter cable. To assemble
the sensor, simply unfold the four sections of the impeller rod and slide them
together. Connect the rods to one another with a small push.
The sensor is delivered with three riser rods (short, medium, and long). The total
length of the impeller rod, including all 3 risers, is 1.5 m.
When the Flow rate sensor is placed in a
stream, water flows against the blades of the
impeller, causing it to turn. The faster the
water flows, the faster the impeller turns. A
bar magnet rotating with the impeller triggers a
reed switch with each half rotation. The switch
sends a pulse to the signal conditioning box,
where the pulses are converted into a voltage
signal that is proportional to flow rate.
The Flow rate sensor is equipped with a BTplug and can be connected to the following
CMA interfaces: €Lab, CoachLab II/II+ and
ULAB. Furthermore the sensor can be used
with Texas Instruments CBL™, CBL2™ and
Vernier LabPro.
Sensor specifications
The Flow rate sensor has a memory chip (EEPROM) with information about the
sensor. Through a simple protocol (I2C) the sensor transfers its data: name, quantity,
unit and calibration to the interface1.
Storage and Maintenance of the Flow rate sensor
When you have finished using the Flow rate sensor, simply rinse it with clean water
and dry it using a paper towel or cloth. The probe can then be folded up and stored.
To prolong the life of your Flow rate sensor, we recommend that the moving parts of
the impeller rod be lubricated, after every few field uses.
When using the impeller rod, avoid hitting the impeller blade on rocks and other
hard surfaces. If the impeller blade is bent, it will decrease the accuracy of the
sensor.
1
This is valid for the following interfaces: CMA €Lab, BT inputs of CoachLab II/II+ and ULAB,
TI CBL™and CBL2™, and Vernier LabPro.
Figure 2.
Left: the sensor impeller
Right: the sensor bar magnet with reed
switch.
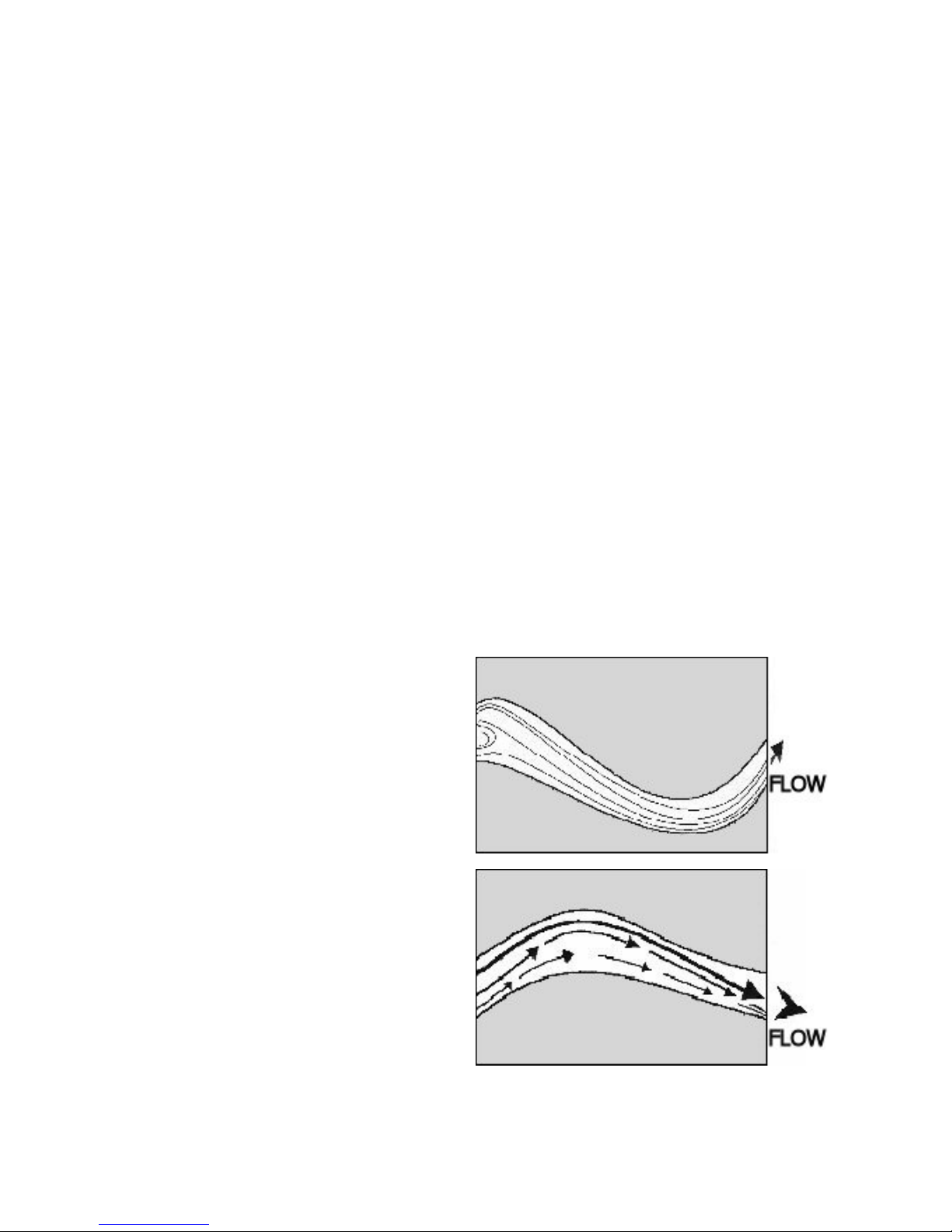
Examples of experiments
The Flow rate sensor can be used in the following experiments:
• Calculating Discharge
Stream flow or discharge is the volume of water that moves through a specific
point in a stream during a given period of time. To determine discharge, a
cross-sectional area of the stream or river is measured. Then, the velocity of the
stream is measured using a Flow rate sensor. The discharge can then be
calculated by multiplying the cross-sectional area by the flow velocity.
• Determining sediment transport rate for a stream or other body of water
The amount of sediment and maximum particle size that can be transported by
moving water is related to the flow velocity. Therefore, flow velocity data
obtained using the Flow rate sensor can be used to determine what size particles
will stay in motion at a particular flow velocity. For a given flow velocity there is
a range of behavioral possibilities for sediment particles lying on the bed, or
entrained within the flow, of a stream. For example, at a measured flow velocity
of 1 m/s, silt and sand (though not compacted clay) will be eroded from the
stream bed and transported downstream. At the same velocity, all sediment
particles between 10 mm and 100 mm that were already in motion will continue
in motion. Particles greater than 100 mm will be deposited. Thus, a Flow rate
sensor can be a valuable observational tool when used in sediment transportation
studies.
• Measuring and comparing flow rate at various locations in a stream
Using the Flow rate sensor, it is
possible to map flow characteristics
of a stream by taking measurements
at different spots and depths. To
understand the flow characteristics
within streams of moving water, it is
helpful to construct Stream Lines
and Vector Lines.
The first illustration shows how
Stream Lines depict possible paths
of a single fluid particle.
Vector Lines represent both the flow
rate and direction. The longer and
broader the line, the greater the flow
velocity. Vector Lines convey useful
information about the stream flow
characteristics.

Procedure for Measuring Stream Flow
1. Site Selection
• Always follow safety precautions when entering the stream. If the water is too
deep or swift, select another site. Never venture out into the stream alone without
another person available to assist you in case of emergency.
• Select two sites within a 50 m stretch of the
stream that are as far apart as possible and
are representative of the stream as a whole.
Avoid sites with bends or breaks in the
stream caused by rocks or sandbars. Try to
choose a site where some flow can be
observed. One site can have a swift flow
similar to that found in a riffle. The second
site can have a moderate or slow flow like
that found after a pool. It is not necessary
for both sites to be the same.
• At each site, you are going to take a cross
section of the stream and measure its width
and depth. Try to select a cross section that
is shallow enough to measure depth with a
meter stick and easy to cross. To measure
stream flow using the Flow rate sensor,
avoid sites where the stream depth is less
than 10 cm.
• The Flow rate sensor is equipped with a 5 m
cable. This enables you to take
measurements up to 4 meters away from the
shore without carrying the interface out into
the stream.
If the stream is wider than 4 meters, monitor
the stream flow out from one shore line, then have the person holding the
interface switch to the other side of the stream. This should reduce the chances of
dropping the equipment into the water and damaging it.
2. Measuring a Stream Cross Section
• Using measuring tape, determine the width of the stream cross section in meters
and record the measurement on a data sheet. Divide the cross section into six
equally spaced sections.

• Using a meter stick, measure the depth of the stream in
meters at each of the equally spaced points along the cross
section. Record the depth and the distance out from one
shore edge, in meters, on a data sheet. Always measure from
the same shore. Be sure to include both the initial distance
and depth and the final distance and depth.
3. Measuring Flow Velocity
• Connect the Flow rate sensor to your datalogger.
If you use the computer with an interface position it safely
away from the water.
• Submerge the impeller of the Flow rate sensor to about
40% of the depth measured at each section. If the section is
shallow enough, use the plastic risers that are included with
the Flow rate sensor to support the sensor on the stream
bed. The risers make it easier to keep the impeller of the
sensor in the same spot and oriented in the same direction.
• Point the impeller of the sensor upstream (as shown below)
and place it into the flow. Hold the sensor in place for 10 seconds while data are
being collected. Repeat the measurement for each of the remaining sections.
1 2
3
4
5 76
Initial
distance
Initial
depth
= 0
= 0
Final
distance
Final
depth
= 0
= Stream width

4. Calculating Stream Cross section
• Create a graph of stream depth vs. distance from the shore.
• Integrate the data. The integral value will give you the cross-sectional area of the
stream.
5. Determining Discharge
• Calculate the average velocity for each site.
• To calculate the discharge or stream flow, multiply the average stream velocity
by the cross-sectional area. Repeat for Site 2.
Additional tips
1. The plastic risers that come with the Flow rate
sensor can be very helpful in keeping the
sensor at the same orientation while taking
measurements. When using the risers, simply
place the bottom of the sensor rod against the
stream bottom. If you are unsure which riser to
use, start with the medium riser first and gauge
the depth from there.
2. When students are selecting sites to take flow
measurements, they should choose a site where
the stream is not split by rocks, partially
submerged obstructions, or sand bars.
3. The impeller of the Flow rate sensor should always be pointing into the flow
when measurements are being made. Students need to stand on the shore when
taking measurements close to the shore, or stand as far downstream as possible
from the sensor when placing the sensor in deeper water.
4. Because stream flow is easily affected by weather conditions, it is important that
good notes concerning date, time, and weather be taken whenever flow
measurements are made.

Calibration
The output of the Flow rate sensor is linear with respect to the flow velocity.
To collect data you can:
1. Use the calibration supplied by the sensor EEPROM memory.
2. Use the calibration supplied in the standard sensor library of the Coach program.
The name of the Flow rate sensor in the
standard sensor library of the Coach
program is
Flow rate sensor (0387i) (CMA) (0..4 m/s).
Figure 3.
Default calibration graph of the Flow
rate sensor (used in the standard Coach
library and sensor memory)
Flow (m/s)= 0.8 * V
out
(V)
Coefficients of the calibration function:
a= 0.8; b= 0.

0 - 4.0 m/s (0 – 13 ft/s)
Flow (m/s) = 0.8 * V
out
(V)
Resolution using 12 bit A/D converter
±1% of full-scale reading
98% of full-scale reading in 5 seconds, 100% of
full-scale in 15 seconds
Temperature range (can be placed in)
Sensor information for
Auto-ID and calibration
Right-hand BT (British Telecom) connector
Warranty:
The 0387i Flow rate sensor is warranted to be free from defects in materials and
workmanship for a period of 12 months from the date of purchase provided that it
has been used under normal laboratory conditions. This warranty does not apply if
the sensor has been damaged by accident or misuse.
Note: This product is to be used for educational purposes only. It is not appropriate
for industrial, medical, research, or commercial applications.
Rev. 1/11/12