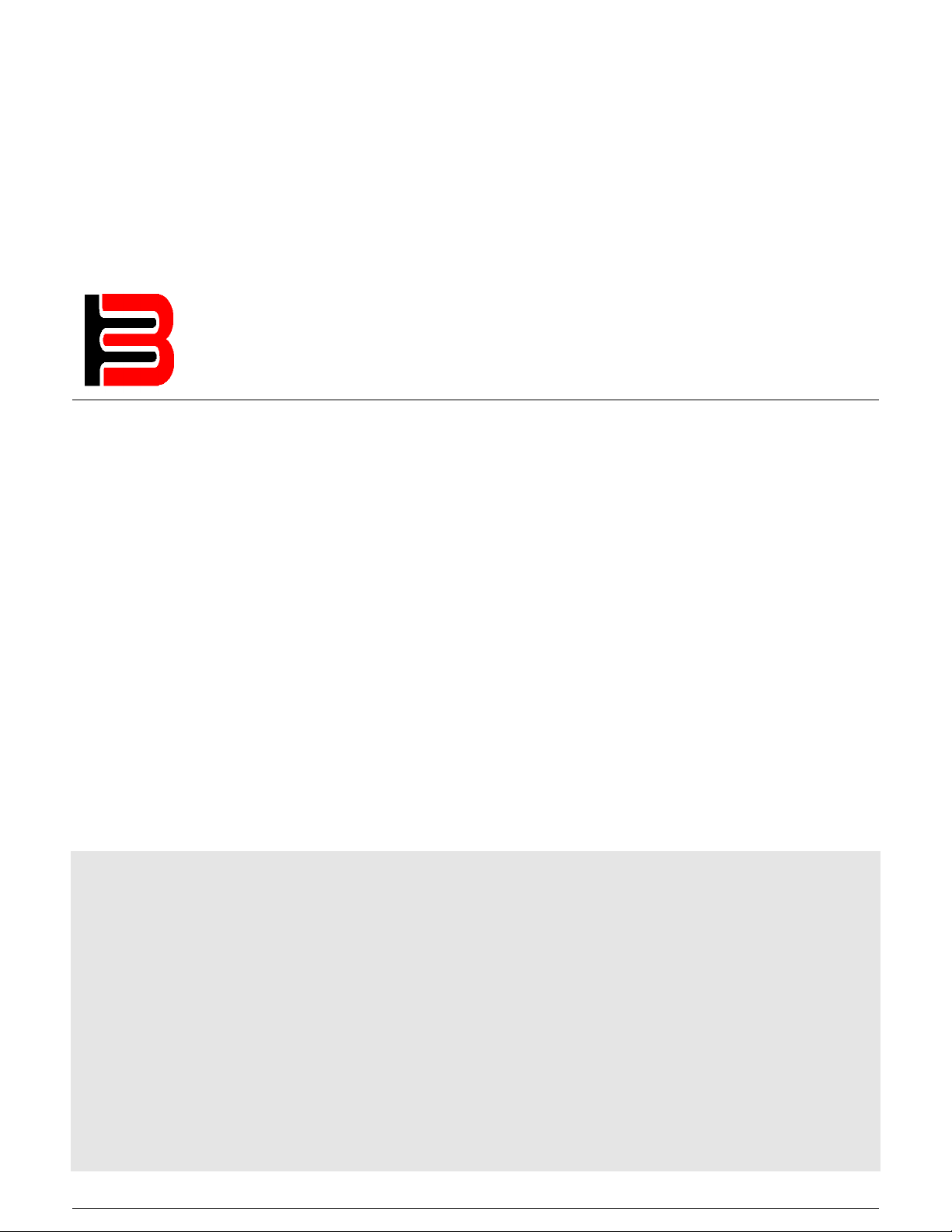
BRYAN STEAM LLC
Installation and Operating Service Manual
Form 2143
Date: 4/3/03
Repl: 2/1/99
BOILER FEED
SYSTEM
0
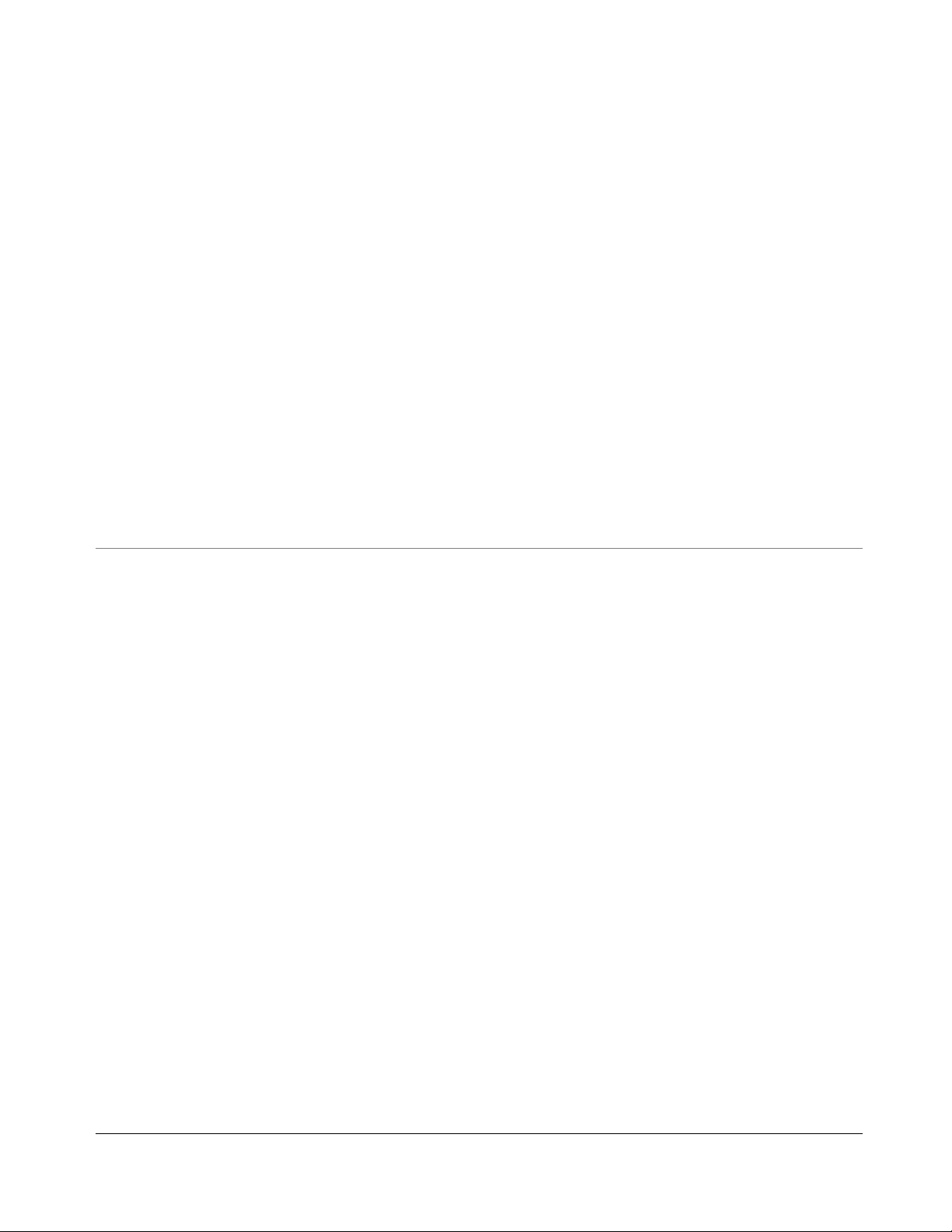
INSTALLATION AND OPERATION SERVICE MANUAL
BOILER FEED SYSTEM
Bryan Steam LLC
783 North Chili Avenue * Peru, IN 46970
Phone 765.473.6651 • Fax 765.473.3074
bryanboilers@iquest.net Internet: www.bryanboilers.com
E-mail:
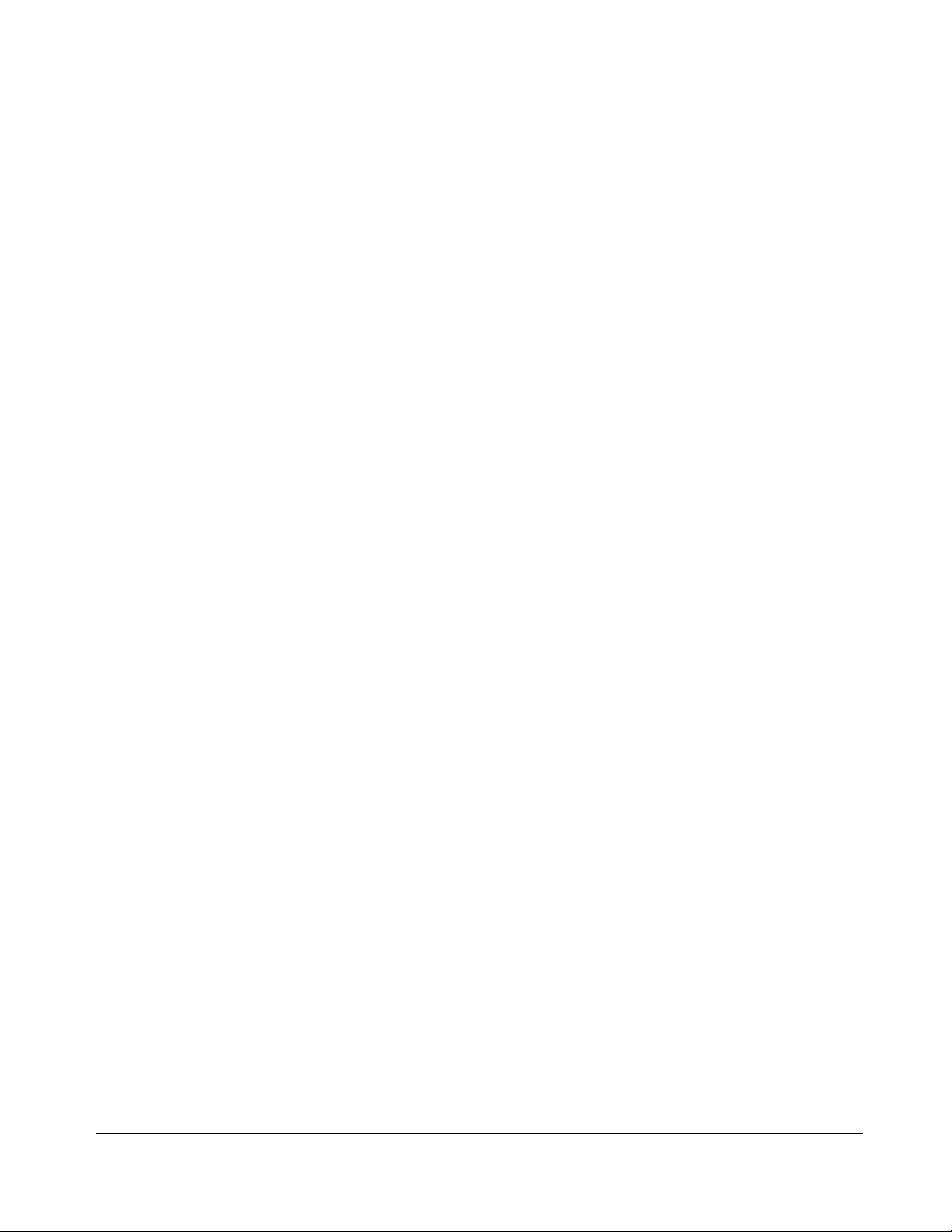
MODEL IDENTIFICATION & DESIGNATION
Boiler F eed System
A – H - FS – 15 – 12 – 50 – D
A = LINING
BLANK – NO LINING
A – APEXIOR LINING
B – GALVANIZED LINING
H = TANK POSITION
H – HORIZONTAL TANK POSITION
V – VERTICAL TANK POSITION
C - COMPACT
FS = FEED SYSTEM (TS – TRANSFER SYSTEM)
“15” = BOILER RELIEF VALVE SETTING
“12” = MAX. BOILER HP
“50” = TANK SIZE (GALLONS)
“D” = NO. OF PUMPS
S – SIMPLEX PUMPS
D – DUPLEX (2) PUMPS
T – TRIPLEX (3) PUMPS
Q – QUADRAPLEX (4) PUMPS
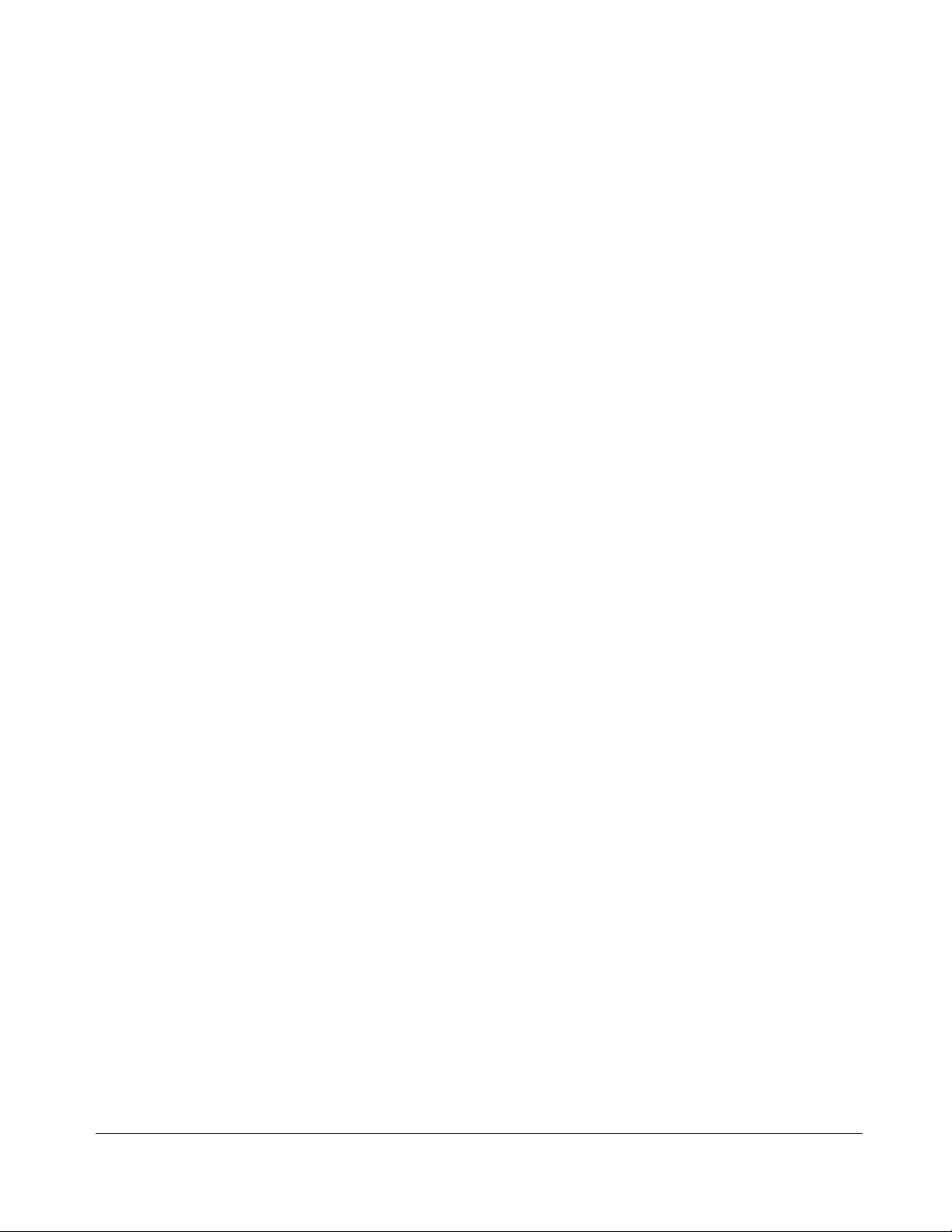
Table of Contents
SECTION 1 –
INSTALLATION INSTRUCTIONS
1.1 FOUNDATION......................................................................................................... 1
1.2 CLEARANCE........................................................................................................... 1
1.3 UNCRATING THE FEED SYSTEM........................................................................... 2
1.4 BOILER FEED SYSTEM CONNECTIONS................................................................. 2-3
1.5 FEED SYSTEM ACCESSORY EQUIPMENT.............................................................. 4-5
1.6 PROCEDURES TO BE FOLLOWED BEFORE PLACING
FEED SYSTEM IN OPERATION............................................................................... 5
SECTION 2 –
START – UP
2.1 LIMIT TEST ............................................................................................................ 6-7
2.2 OPERATING INSTRUCTIONS................................................................................. 8
2.3 MAINTENANCE SCHEDULE ................................................................................... 8
SECTION 3 –
SHUTDOWN AND RE-START
3.1 REQUIRED PRECAUTIONS DURING TEMPORARY USE........................................ 9-10
3.2 CLEANING THE BOILER AND SYSTEM – NEW SYSTEMS..................................... 10
3.3 SYSTEM CLEAN – OUT........................................................................................... 10
3.4 REPLACEMENT BOILER SYSTEM INSTALLATION:
PROTECTION AGAINST CORROSION & SEDIMENT .............................................. 10-11
3.5 BOILER WATER TREATMENT................................................................................ 11
3.6 SUGGESTED MAINTENANCE SCHEDULE.............................................................. 12
3.7 IDLE BOILER SYSTEMS CARE & LAY-UP .............................................................. 12-13
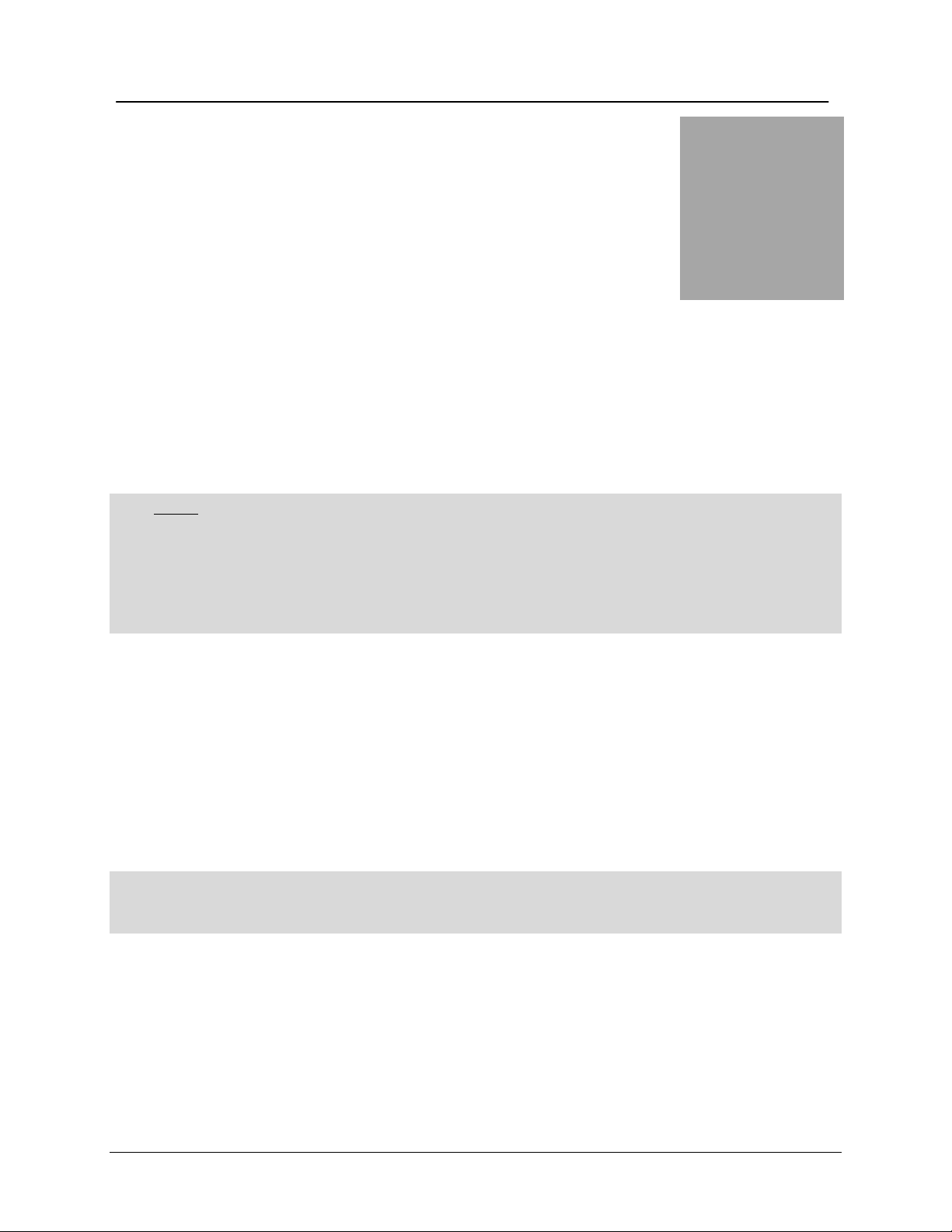
BOILER FEED SYSTEM
DATE: 4/3/03
REP:2/1/99
Section
1
Installation Instructions –
Boiler Feed System
Note: Please read the entire instruction manual before attempting installation.
Insurance and local or state regulatory codes may contain additional or more stringent
requirements than those contained in this manual. Installation must conform to these codes and
any other authority having jurisdiction.
Appropriate sections of the National Electric Code and ASME Code should be consulted and
followed.
1.1 FOUNDATION
Before uncrating, the location should be prepared. The boiler feed system should set upon a good
level concrete floor. If the unit is not level or the floor is not in good condition, a concrete
foundation should be built, the dimensions being larger than the outside dimensions of the boiler
feed system base.
1.2 CLEARANCES
NOTE
Adhere to all applicable local codes and NEC regarding system feed system installation and
clearances.
The unit may need room for service accessibility and clearances for piping and electrical
connections. Local codes must be applied to specific installations and the minimum clearances
established accordingly. If an electrical panel is supplied, the NEC requires a 36” service
entrance in front of the electrical panel.
1.3 UNCRA TING THE BOILER FEED SYSTEM
Leave the packaging material used for crating in place until ready for installation. The crating is
not designed for outdoor storage; therefore the unit should be stored inside. Uncrate the boiler
1
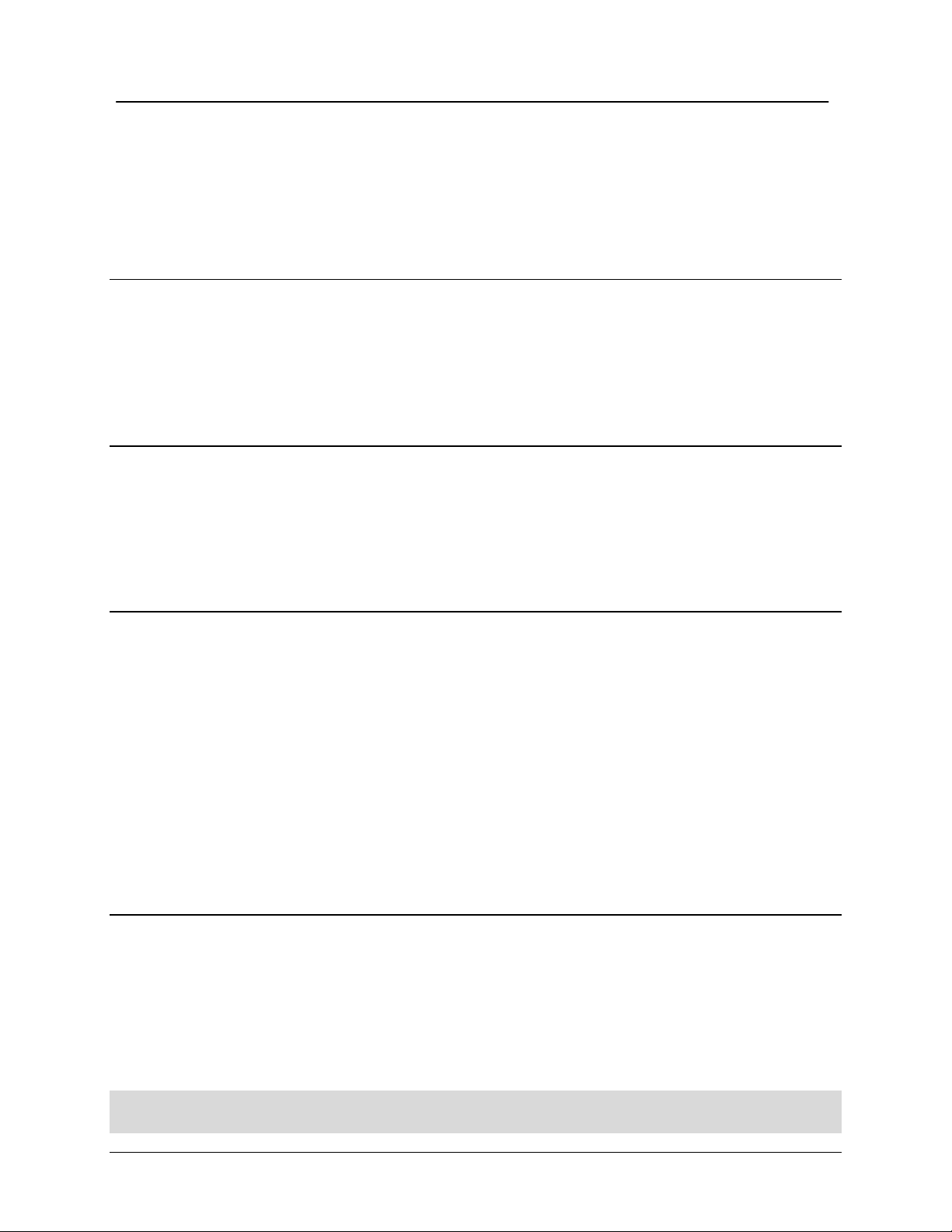
BOILER FEED SYSTEM
DATE: 4/3/03
REP:2/1/99
feed system near its permanent location. Before installation, take inventory of items that were
shipped loose so they will not be misplaced.
1.4 BOILER FEED SYSTEM CONNECTIONS
1.4.1 GENERAL
Maintain clearances as shown on the dimensional drawing for servicing and as referenced in
N.E.C. All piping should be designed and installed to avoid any loadings on the feed
system connections or piping. Install pump discharge piping so that accessibility and
maintenance on the pumps can be done with ease and that pumps can be removed for service if
required.
1.4.2 MANUAL MAKE UP WATER CONNECTION
There are two connections supplied for make-up water on the HFS system and one connection on
the CFS model. A manual fill connection (top center) is supplied for a by-pass around the
standard make-up water connection (HFS only). The standard make up water connection is
located on the side of the unit and is tied in directly with a level control to maintain minimum level
of water in the vessel.
1.4.3 CONDENSATE RETURN CONNECTION
The condensate return connection is located on top of the tank. All condensate returns should be
piped to this connection for entrance into the feed system. Since this vessel is an atmospheric
tank the condensate returns coming back should be of low pressure and will be introduced to
atmospheric conditions once entering the tank. If high-pressure returns are required to return to
this tank, they should be reduced to a low pressure before entrance. A steam pre-heater
assembly (optional) may have been supplied with the unit. This connection is for high-pressure
steam and is reduced and controlled via a pressure/temperature regulating valve and enters the
tank through a sparge tube. This has been sized based on specific conditions given at the time of
ordering. For proper operation and maintenance of the valve and proper installation, please
reference the valve manufacturer’s instructions supplied with the unit. This connection is used to
preheat the water in the tank and is controlled based on a temperature pilot, with the sensor
located in the tank.
1.4.4 VENT CONNECTIONS
There are two vent connections supplied on the HFS unit and one on the CFS unit that should not
be reduced. One is a 3” vent connection and the other is labeled “blowout opening” on the HFS
model only. The tank vent connection must be vented to the atmosphere and piped to a safe
discharge location for hot temperatures. The blowout opening is designed as an additional safety
condition against having pressure in the tank. The blowout opening has a neoprene rubber
stopper installed so if pressure is built up in the tank, the stopper will blow out of the connection
relieving the pressure in the tank.
NOTE:
The tank should never, under any circumstances, be installed to become pressurized.
2