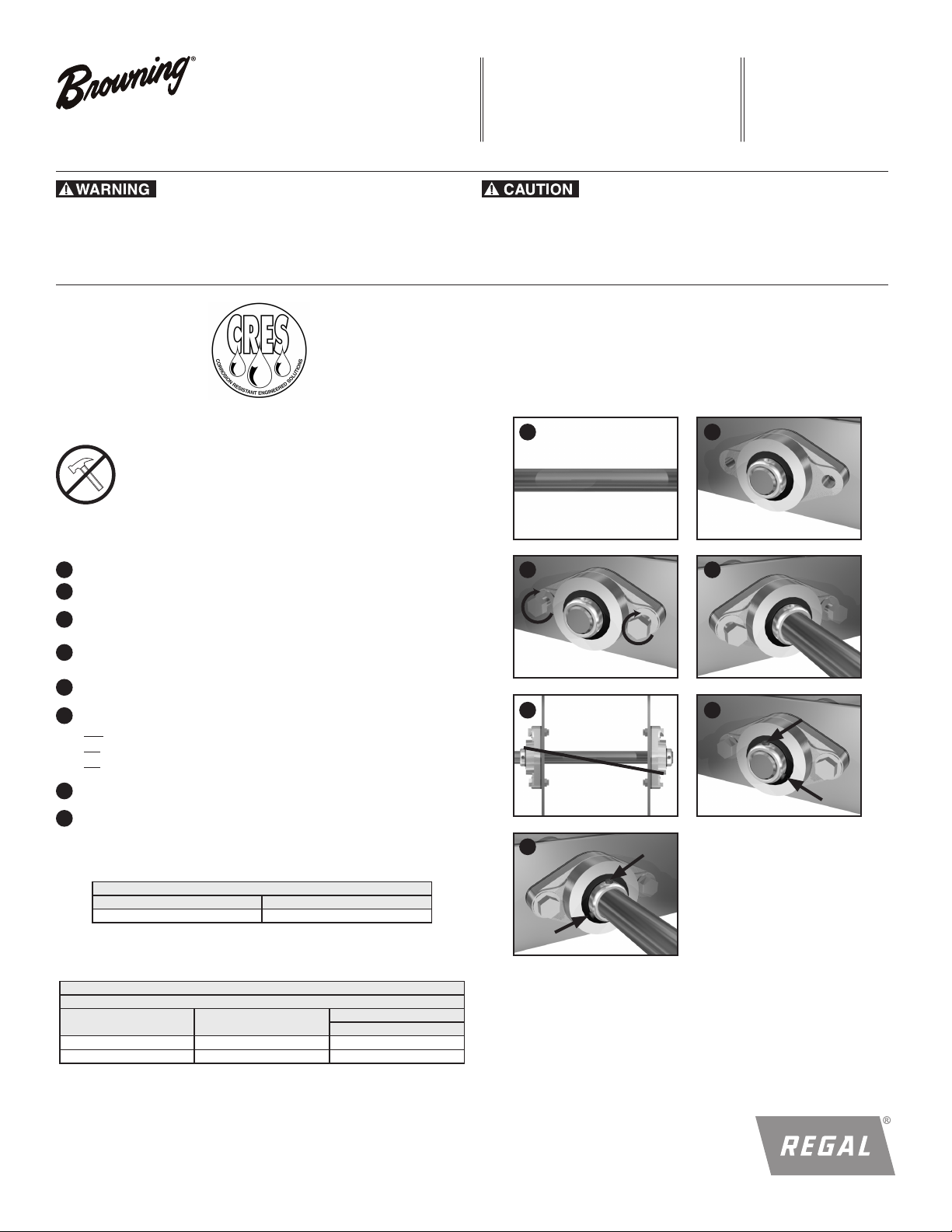
Ball Bearing Installation Instructions
CRES SS
F O R M
PN 784370, PS-740-0001
9564E
Revised
August 2016
• Read and follow all instructions carefully.
• Disconnect and lock-out power before installation and maintenance.
Working on or near energized equipment can result in severe injury or death.
• Do not operate equipment without guards in place. Exposed equipment can
result in severe injury or death.
NOTICE
• These bearings are designed for maximum permissible static
misalignment of ± 2 degrees. Installation, handling or operation of the
bearing in excess of the maximum of ± 2 degrees can cause reduction
in bearing performance and may lead to equipment failure.
• Do not strike or hammer on any component of the bearing
and/or shaft. Impact can result in damage to the bearing that may cause
reduction in bearing performance and may lead to equipment failure.
Ensure shafting is clean and within spec. See Table 1 below. Remove all burrs.
1
Place first bearing onto shaft. Do not hammer.
2
Install bolts and stainless steel washers (if used). Tighten down housing
3
mounting bolts.
Repeat steps 2-4 for the second bearing but do not tighten down housing
4
mounting bolts yet.
Align bearings and shaft. Shaft should be within ±2 degrees. Set screws on
5
both bearings should face the same direction. Tighten mounting bolts.
Bearing one - set screw tightening directions:
6
Half - Tighten set screw “A” to 1/2 the recommended torque in Table 2 below.
Full- Tighten set screw “B” to the full recommended torque in Table below.
Full - Tighten set screw “A” to the full recommended torque in Table.
Repeat tightening of the set screws in step 6 for the second bearing. Set
7
screws on both bearings should face the same direction.
8
Rotate bearing several times. Look, feel and listen for anything unusual.
• Periodic inspections should be performed. Failure to perform proper maintenance
can result in premature product failure and personal injury.
1 2
No Hammers!
3 4
Do Not Tighten
Tighten Bolts!
5 6
Align Shaft Within 2º
Tighten Bolts!
Bolts Yet!
A
B
TABLE 1
TABLE 2
SET SCREW
SHAFT DIAMETER (IN.) SHAFT TOLERANCE (IN.)
1/2” to 1 15/16” Plus .0000 to minus .0005
CRES SS: SPS-S, SF2S-S, SF4S-S, STBS-S, VS-S (INSERT)
DIAMETER
1/4 1/8 35-45
5/16 5/32 75-100
SHAFT TOLERANCES
SETSCREW TORQUE
HEX SIZE
ACROSS FLATS
TORQUE
(IN-LBS.)
7
A
B
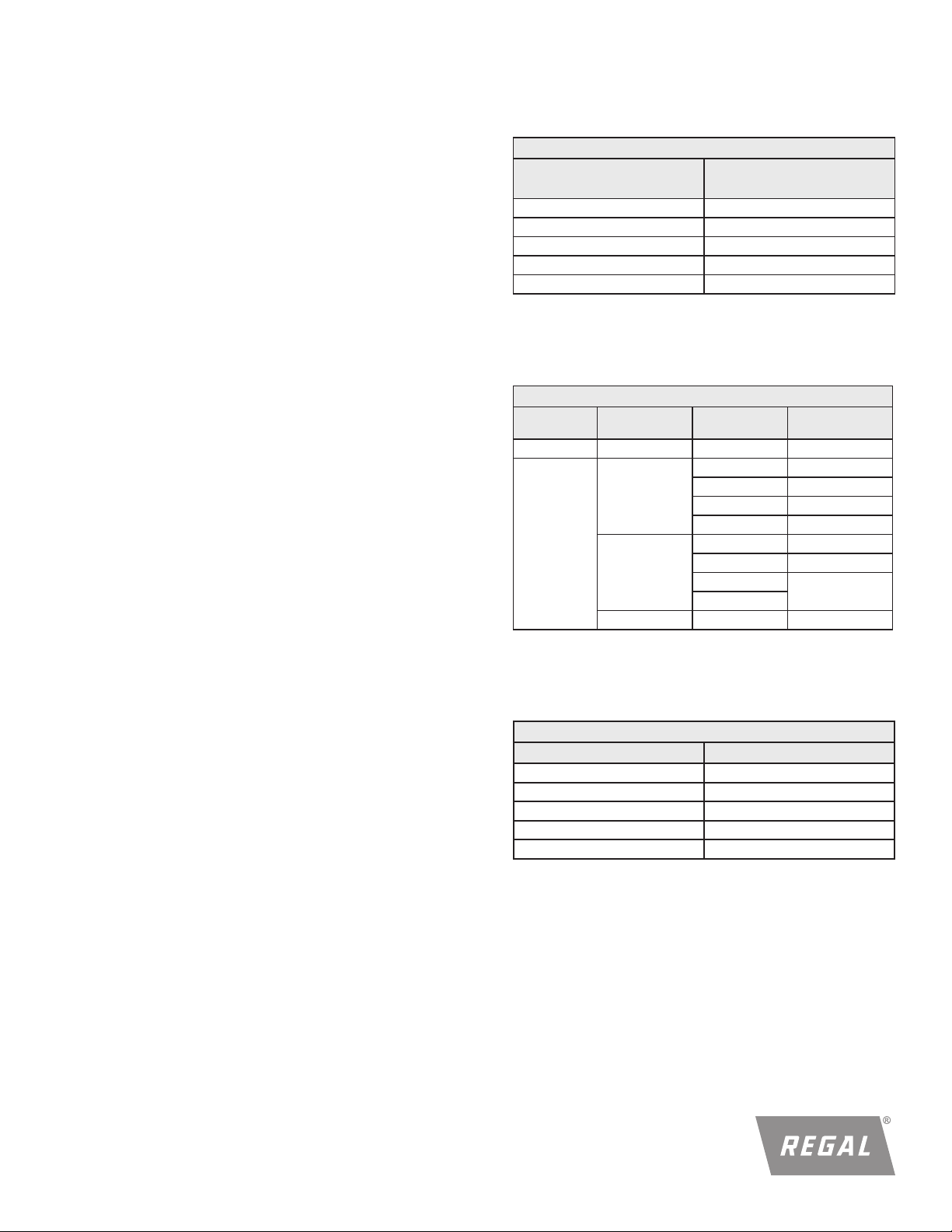
LUBRICATION:
All Browning CRES SS Ball Bearings are delivered with a
high quality food grade grease with an EP additive. The
bearing is ready for use with no initial lubrication required.
The grease consists of an aluminum complex, mineral oil,
and NLGI grade 2 consistency.
Compatibility of grease is critical; therefore consult with
Application Engineering and your grease supplier to
insure greases are compatible. For best performance it
is recommended to relubricate with aluminum complex
thickened grease with a comparable NLGI consistency and
base oil properties.
TABLE 3
GREASE CHARGE FOR RELUBRICATION
SHAFT SIZE GREASE CHARGE (MASS - OUNCES)
3/4 0.05
1 0.06
1 3/16 - 1 1/4S 0.12
1 1/4 - 1 7/16 0.18
1 1/2 0.27
Relubricatable Browning bearings are supplied with
grease fittings or zerks for ease of lubrication with hand or
automatic grease guns. Always wipe the fitting and grease
nozzle clean.
Caution: If possible, it is recommended to lubricate the
bearing while rotating, until grease purge is seen from the
seals. If this is not an option due to safety reasons, follow
the alternate lubrication procedure below.
ALTERNATE LUBRICATION PROCEDURE:
Stop rotating equipment. Add one half of the
recommended amount shown in Table 3. Start the bearing
and run for a few minutes. Stop the bearing and add the
second half of the recommended amount. A temperature
rise after lubrication, sometimes 30°F (17°C), is normal.
Bearing should operate at temperatures less than 200°F
(94°C) and should not exceed 250° (121°C) for intermittent
operation. For lubrication guidelines, see Tables 4 and 5.
Note: Table 4 is a general recommendation. Experience
and testing may be required for specific applications.
Note: Grease charges in Table 3 are based on the use of
aluminum complex thickened grease with a NLGI grade 2
consistency.
TABLE 4
RELUBRICATION RECOMMENDATIONS
ENVIRONMENT TEMPERATURE (°F)
Dirty -20 to 200 0 - 100% Daily to 1 Week
-20 to 125
Clean
125 to 175
175 to 200 0 - 100% Daily to 1 Week
SPEED
(% CATALOG MAX)
0 - 25% 4 to 10 Months
26 - 50% 1 to 4 Months
51 - 75% 1 Week to 1 Month
76 - 100% Daily to 1 Week
0 - 25% 2 to 6 Weeks
26 - 50% 1 Week to 1 Month
51 - 75%
76 - 100%
Daily to 1 Week
TABLE 5
MAXIMUM OPERATIONAL SPEED
SHAFT SIZE SPEED (RPM)
3/4 2000
1 2000
1 3/16 - 1 1/4S 2000
1 1/4 - 1 7/16 1750
1 1/2 150 0
FREQUENCY
Regal and Browning are trademarks of Regal Beloit Corporation or one of its affiliated companies.
©2016 Regal Beloit Corporation, All Rights Reserved. MCIM16047E • Form 9564E • Printed in USA