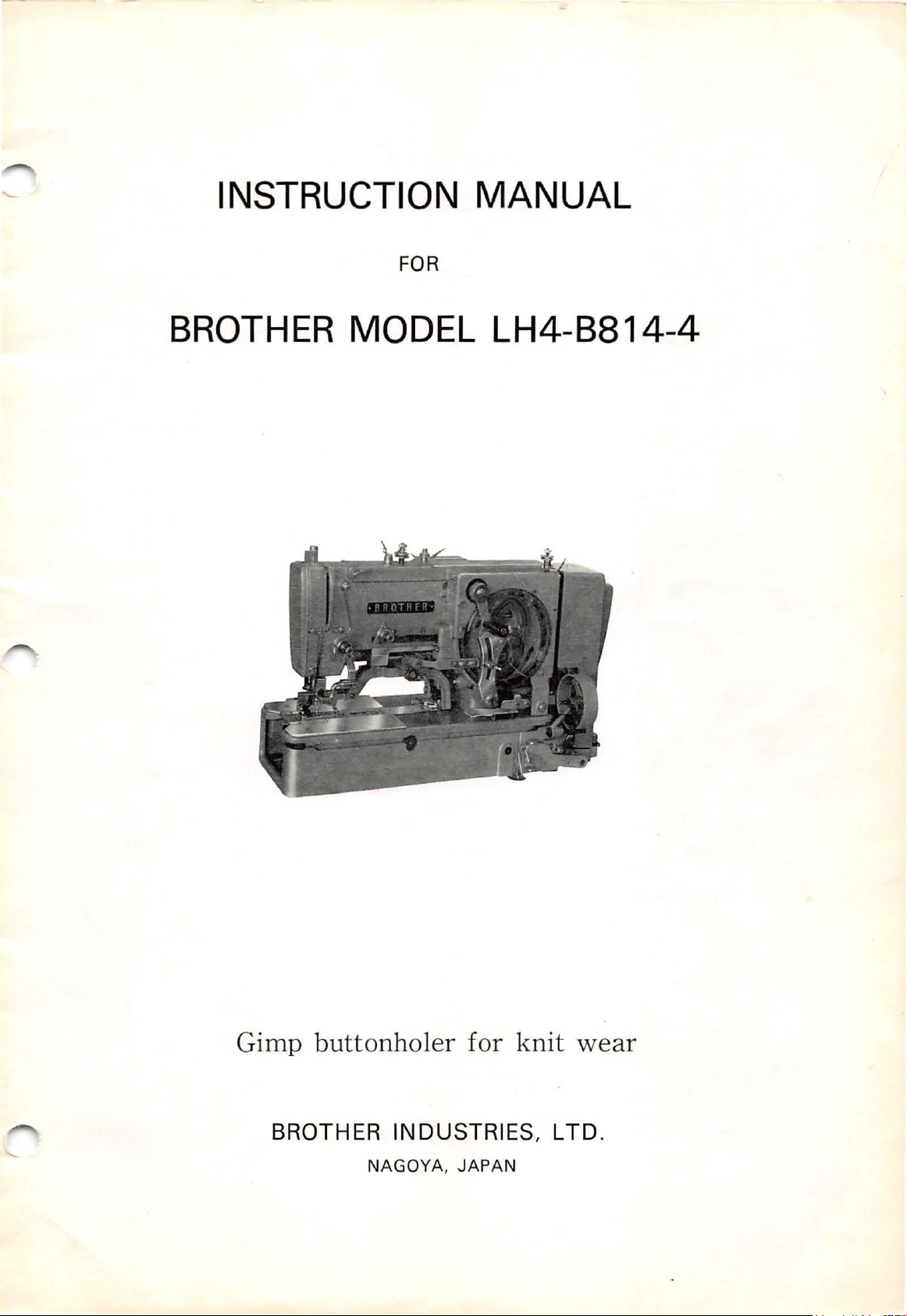
INSTRUCTION MANUAL
FOR
BROTHER MODEL
LH4-B814-4
Gimp buttonho l
BROTHER INDUSTRIES,
NAGOYA, JA
er
for
PAN
knit
LTD.
wear
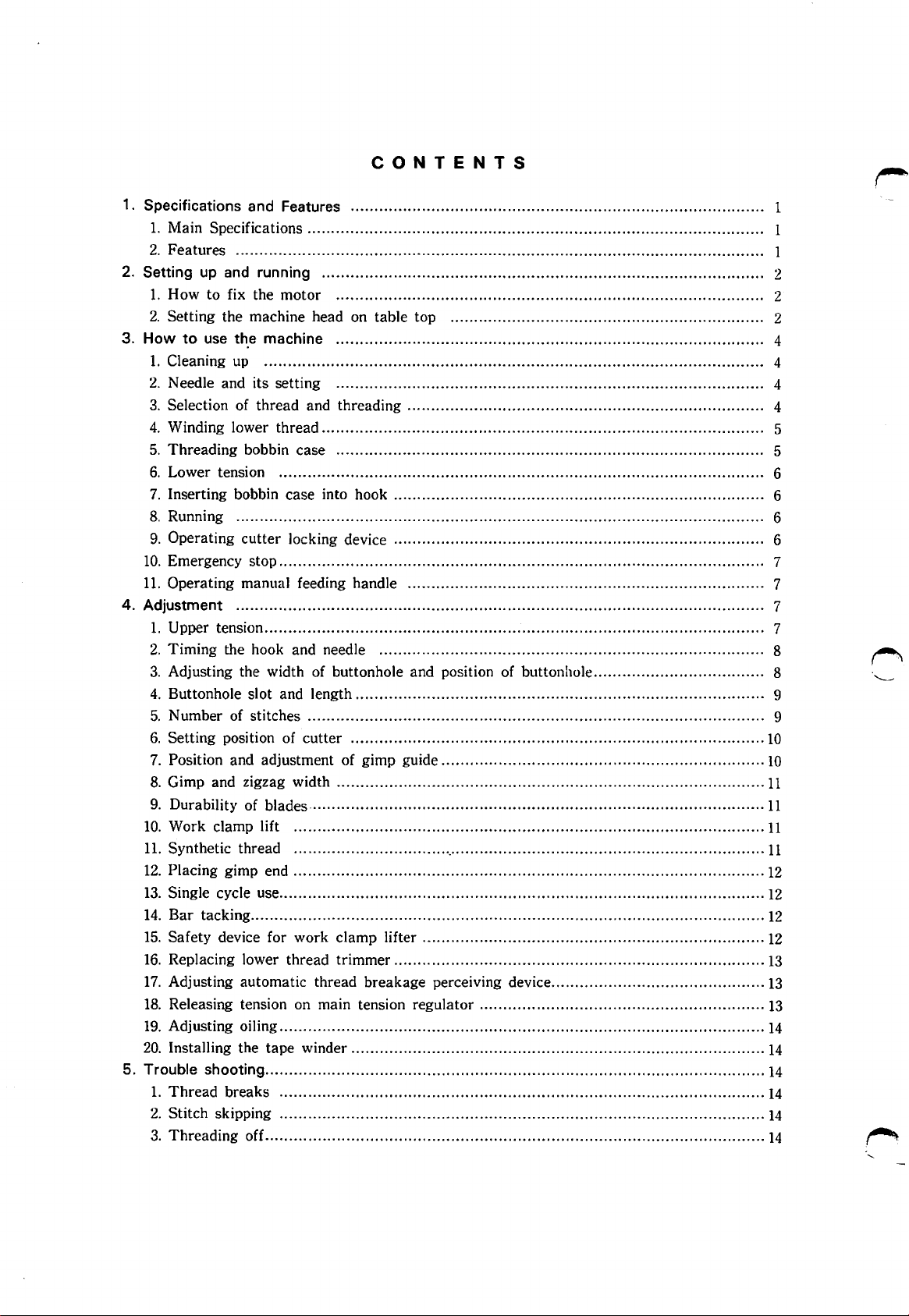
CONTENTS
1.
Specifications and Features ..................................................................................... ..
1.
Main
Specifications
2.
Features
2. Setting up and running ............................................................................................ .
1.
How
2.
Setting
How
3.
4. Adjustment .............................................................................................................. .
5. Trouble shooting .........................................................................................................
to
1.
Cleaning up
2.
Needle
3.
Selection of
4.
Winding lower
5.
Threading
6.
Lower
7.
Inserting bobbin
8.
Running
9.
Operating
10.
Emergency
11.
Operating
1.
Upper
2.
Timing
3.
Adjusting
4.
Buttonhole
5.
Number
6.
Setting
7.
Position
8.
Gimp
9. Durability of
10.
Work
11.
Synthetic
12.
Placing gimp end
13.
Single cycle
14.
Bar
15.
Safety
16.
Replacing lower
17.
Adjusting
18.
Releasing tension on
19.
Adjusting oiling
20.
Installing
1.
Thread
2.
Stitch
3.
Threading
.............................................................................................................
to
fix
the
the
machine
use
the machine ........................................................................................
and
its
thread
bobbin
tension
..............................................................................................................
cutter
stop
manual
tension
the hook
the
slot
of stitches
position of
and
and
zigzag width
clamp
thread
use
tacking
............................................................................................................
device for
automatic
the
breaks
skipping
off
...............................................................................................
motor
........................................................................................................
setting
thread
.....................................................................................................
case
locking device
.....................................................................................................
........................................................................................................
width of
and
adjustment
blades
lift
......................................................................................................
thread
......................................................................................................
tape
......................................................................................................
......................................................................................................
.........................................................................................................
.........................................................................................
head on
and
............................................................................................
case
into hook
feeding
and
needle
length
...............................................................................................
cutter
................................................................................................
...................................................................................................
....................................................................................................
...................................................................................................
work
thread
main
winder
table
top
.................................................................
.........................................................................................
threading
.........................................................................................
handle
buttonhole
.....................................................................................
.......................................................................................
of
..........................................................................................
clamp
trimmer
tension
.......................................................................................
..........................................................................
.............................................................................
.............................................................................
..........................................................................
................................................................................
and
position of
gimp
guide
....................................................................
lifter
........................................................................
..............................................................................
breakage
perceiving device
regulator
buttonhole
............................................................
..................................
.............................................
..
..
..
~
1
.
1
2
.
2
.
2
4
.
4
.
4
.
4
.
5
.
5
.
6
.
6
.
6
.
6
.
7
.
7
7
.
7
.
8
8
.
9
.
9
10
10
11
11
11
11
12
12
12
12
13
13
13
14
14
14
14
14
14
~
'---'

1.
SPECIFICATIONS
1. Main Specifications
AND
FEATURES
i\lodel
t-
--
Sub-class
Usc
Max
. sewing
Leng
th
'vVidth of buttonho le
T ape
winding
Feeding mecha nism
Butt
onhole stitch
!Ieight
O
ilin
g system
2. Featu
10
11) Bobbin wi
1
13) Th
14)
res
1) When the s
matically trimmed.
2)
Thi
s model is
3) Automatic lubricati
4)
It
can rai
5)
\Viele
worki
6)
A s
pecially select
7)
An
automatic knife lo
thread breakage.
8) Speciall
n
9)
It is ve
n
) Emergency ins
dur
breaka
2)
Presser
u
T his machi
lo
y design ed speed reduction mechanism enabl es
oisel
ess
ry easy
um
ber of s
ability
ge
foot can
e app
lic
pto 6mm
back and forth direction or le
of
buttonhole
spee
LI-!4-B81
d
2.8
4-4
00
spm (Used synthetic upper thr
i
de,·ice
es
of presser foot
ew
ing is clone and you press t
very
fast to sew and can be obt
on can a\·oicl the o
se
up the producti v ity as it ensures less
ng space can ensure easy sewi
ed belt makes no fine adjustment of belt tension.
ck ing ck·\·ice enabl
and l
ess vibra
to change the len
titches
tant
of
this machine and also can
of the i
nding
can be
able thickness
.
ne
IS equ
tion
works.
gth.
and amount
stop lever can guarant
mportant
clone
lift
upto
ipp
ed with adjustable
of
part
s.
even if machine s
1:~mm.
of
the m
ft
he treadle fo r clamp lift. the
ilin
g to t
es
widt
h of
oil.
aterials
and right.
Single needle lock stitch g
-
..J
Knitt
ed wear
3.300 spm
10mm-32mm (%"
2mm-
Automatic lu
ain
he machine
ng operation
to prevent the m
buttonhole
ee
the long
protec
lop
is ensured
rul
ers either
6mm (
Equipp
Upp
er & lower
147-360 stitch
13
mm
ed good qua
thread breaks and thread
.
s.
t t
he
s.
X,"-;),(.
ed
(%")
bri
lity bu
in
eve
ater
- l
es
ca lion
ead
,Y.(
ry
ials
imp
but
tonholer
or
materi al
")
")
thr
eads and gimp arc auto-
ttonhol
morn
es
ing.
from
s)
wit
h easy adj ustments.
off.
dama
ge
in case
-
-
-
of the
-- 1 -
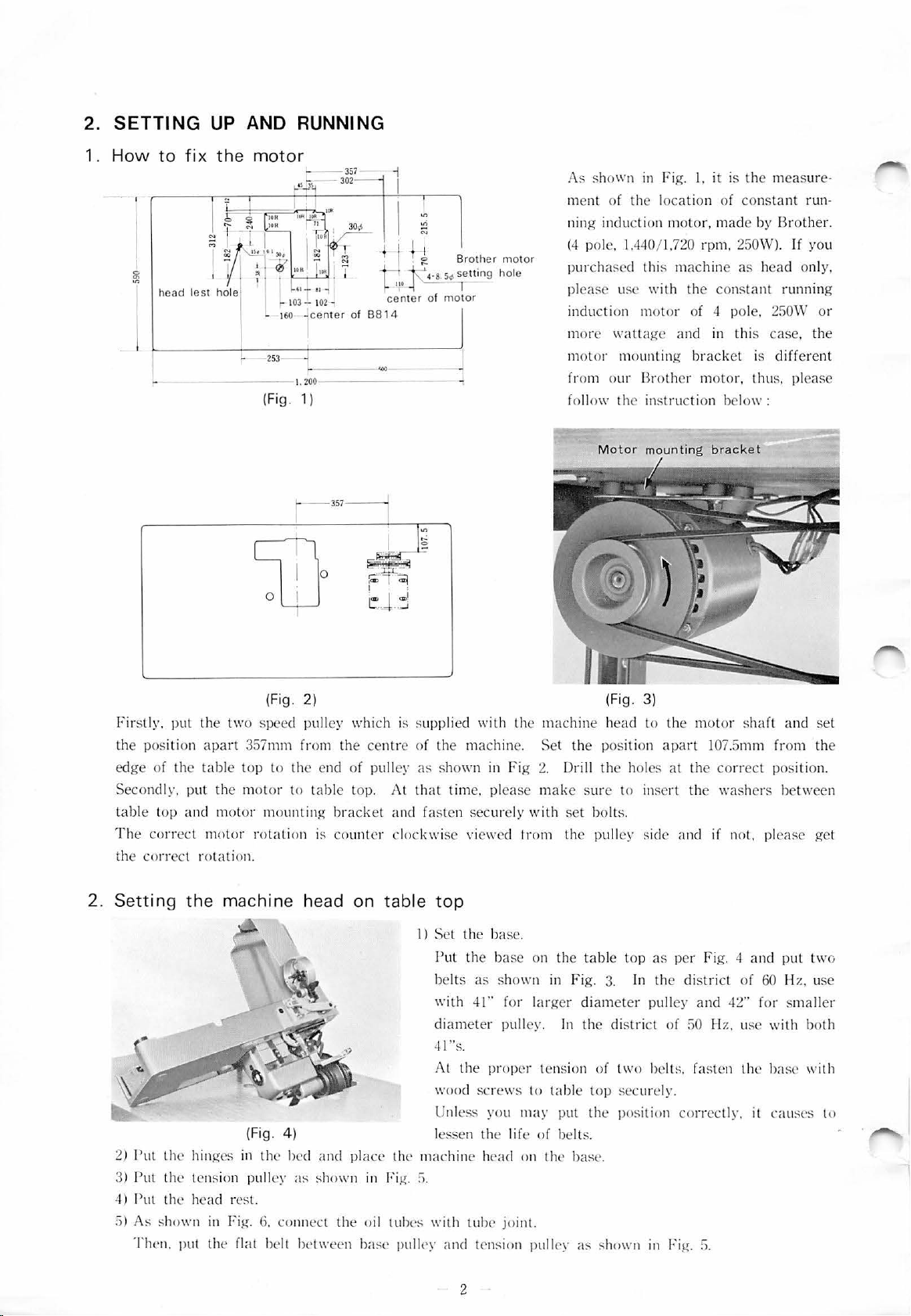
2.
SETTING
1.
How
~
- I
UP
AND RUNNING
to
fix
the
moto
r
As
sho
,,·n
in
Fig. I, it is
,
j I
~
~
Brother
motor
or
~
r
1
03 _ 102
-
160
ren
253
-
I.
200
(Fig. 1)
~
-
_
ter
357
of 88 1 4
_
-1
~
t
center
,.,.
-'
-s.s¢setting hole
4
110
.
of mot
ment
of
the location
ni
ng
induction
(4
pole. 1.440/1.720
purchas
pleas
indu
more
mot
f
follm,· the
ed this machine
e u
se
with
ction
motor
wattage and in thi s
or m
ounti
rom our
Brot
instruction
motor,
the con
of 4 p
ng b
her m
the
of
constant
mad
e by
rpm
, 250W). If yo u
as
head
stant running
ole
. 25
racket
otor.
below:
is
thus. please
measure-
run-
Brot
her.
on ly,
0W
or
case, the
diff
erent
~0
Fir
stly. put the two speed pulley whi c h is suppli
position
the
ed
ge
of
the
Secondly.
tab
le t
op
T
he corr
correct
the
2.
Setting the
2)
l'ut the hin
3) Put the tens ion
4)
Put
the
5)
As shown
Then.
oLW
(Fig.
2)
apa
rt 357mm from the centre of the m
table lop
put
the motor to table
and mo
ect
motor rot at ion 1s counter
rotation.
machine head on
ges
head res
in
put the flat belt bet
to th
tor
mounting
(Fig.
4 )
in the
pulle~·
t.
Fig. 6.
con
e end of pulley
bed
as shown
nect
bracket
and
the
ween
as shO\m
lop. At
place
in
oil tubes \\'i
base
that
and fasten securely
cloc
k wi
tab
le
I)
the
machine head
Fig. S.
pulle~·
ed
with the ma
ach
ine.
in
Fig
time
. pl
ease
se
viewed I rom the pulley side
chine head
Set the pos ition
2.
Drill the holes at the correct
mak
e su
with
set bolt
top
Set the base.
Put the base
belts
as show
"·
ith
41
diamet
er pulley. In
4l''s.
1\t the pr
wood screws
Un
les.<>
lessen
the
th
tube
and
tension
" f
or
oper tens
you
may
life
on
joint.
on th e t
n in Fig.
larger
diamete
the
ion of
to
table lop
put the
of
bel ts.
the
base.
pulle~
·
as shown
able top
(Fig. 3)
to
the
apart
re
to inse
s.
3.
district
two
securely.
position correctly.
rt the \\
and
as per
In the dis
r pulley
of
50 Hz. u
belts. f
111
Fig.
motor
107.5mm
·ashers
if not.
Fig
. 4 and put
tri
ct
and
42''
asten
5.
shaf
t and set
from
posit
ion.
between
please get
of
60 Hz, use
for
smaller
se
with
both
the base wi
it causes
the
two
th
to
2

6)
Put
the bobbin wmder a
be
tween
belt
the bobbin t
guide.
7)
Put
the be
lt
S)
Put
the flat belt to th e machine
line with indicator.
-
...
\
'
;+
I
(Fig.
5)
sse
mbl y as per Fig. 7.
and pull
hreads on bobbin
cover
ey.
Thi
\\'ith flat head screws.
s is b
ecause
actually.
pulle~·
(Fig.
6)
/\t
that
tim
e. please
you can get the even bob bin winding when you may wind
Th
e fine adjustment
and
push the tension le
can
wr
be
done
and
mak
rel
e sure to
at
the posi
ease
it
at
(F
be right
tion
of threa
the
pos
ig. 7)
ition
ang
le
d
111
(Fig.
8)
9) All
the
parts
takin
the dusts
above
procedures ar
g off the face
of pac
king
e c
ompleted.
plate. side
in transit. if any.
cove
then
r and be
(Figs 8.
pour
oil
into
the oil
lt
cover. Please also make sure
9)
- 3 -
(Fig.
9)
reservoir and oi l to the sliding
to
wipe
out
all
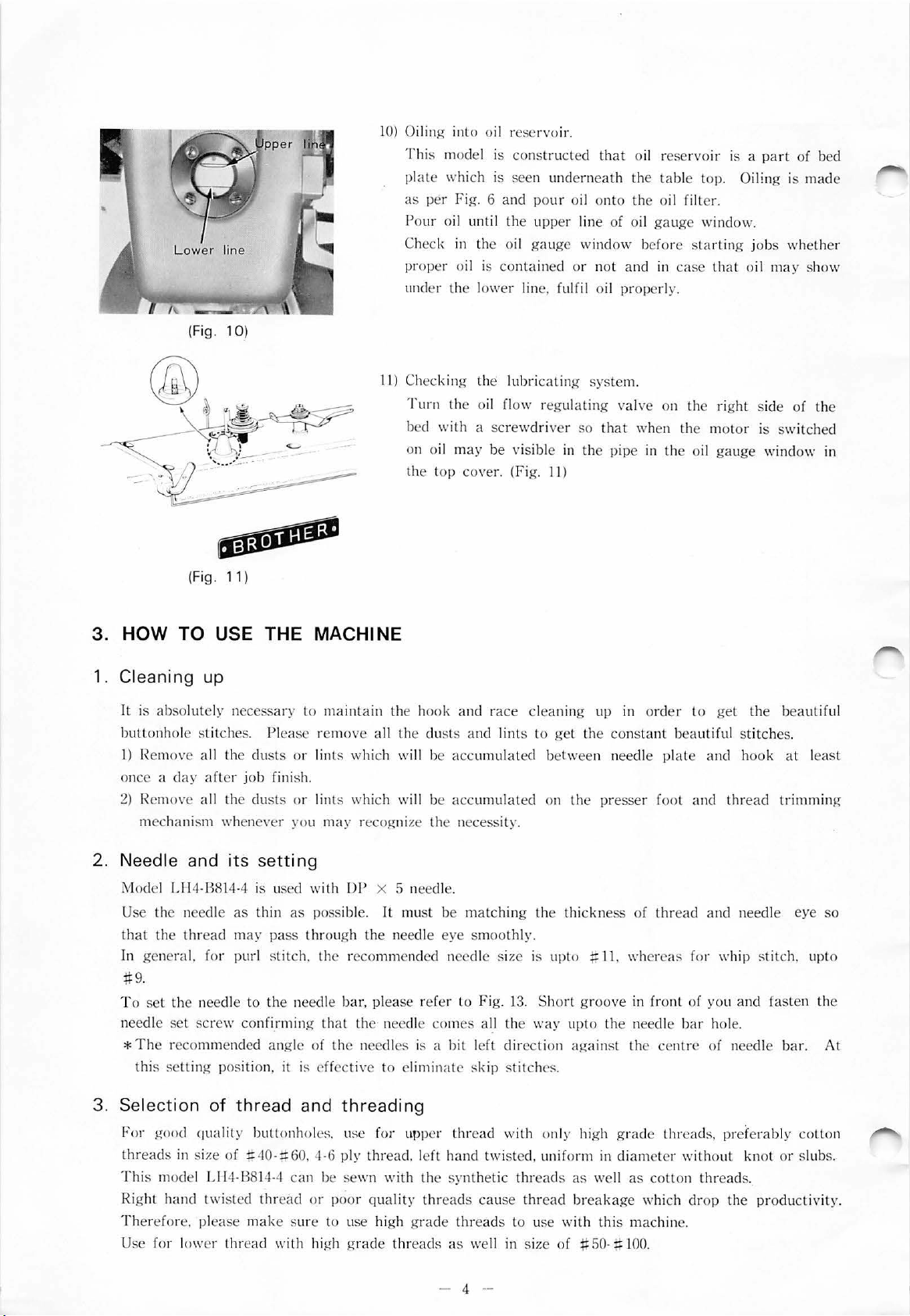
(Fig. 10)
10) Oiling
This
lat
e which is
p
as
per
Pour
Check
prop
er oil is
under
into
oil
model is
Fig. 6
oil until
in
the oil
the
lower
reservoir.
construc
seen underneath
and
the
conta
line, fulfil o
ted t
pour
oil
upper line
gauge
window b
ined or
hat oil
onto
of o
not
il
properly.
the
the o
il
and
reservoir
tab
le to
il
filt e
gauge
efore
in
case
p.
r.
window.
star
ting jobs
that
is a
part of
Oil!ng is
oil may sh
bed
made
whether
ow
@
~
.....
__
(Fig.
11 )
...
_ .
..
ll) Chec
3. HOW TO USE THE MACHINE
1. Cleaning up
It is
absolute
buttonhole stitche
1)
Remove all the
once a clay
2)
f~emo
mechanism
ly necessa
after
ve
all the dusts
\\'hen
ry to
maintain
s. Pl
ease remov
dust
s or lints which will be
job
finish.
or
eve
r you
e all the
lints which will be
may recognir.e
the hook
kin
,g
the l
ubricating
Turn
the oil flow regulating
bed \\'ith a
on o
il
top
Lhe
dusts
the
screwdriver
may
be
vis
cover.
and
accumulated betw
accumulated
necessity.
(Fig. 11)
rac
e cleaning
and lints
system
.
va lve
so
that when the
ible in the pipe in
up
in orde r to get
to get the con
een nee
on the
sta
dle pl
presser
on
the right
motor
the oil
nt
foot
gauge
beautiful stitches
ate
and
and
thread
side
is s
winclo\\' in
the
hook
trimm
of
the
witch
ed
beautiful
.
at
least
ing
2. Needle and its
Model
U
that
In
Lll
se
the needle
the
general.
4·B8l4-4 is used with DP x 5 needle.
thr
ead
for purl stitc
setting
as
thin
may
pass
as
possible.
thr
ough
h.
the recommend
the
It
must
needle
be
eye
ed nee
matching
smoothly
dle size is
the
.
upto
thickness
#9.
To set th e needle
eedle set sc rew
n
*Th
e r
ecomme
this
sell
ing position, it is
3. Selection
For
good
threads
Thi
Right
Theref
Use for l
in si
s model Ll l4-B81
hand
ore.
owe
quality
please
to
conf
nded
of
thread
buttonholes. usc for upper
ze
of :±40-#60.
twisted
mak
r thre
ad
the nee
angle
4-4
thread
dle bar,
irming that
and
can
or poor
e sure to use high
with high
the nee
of
the
needl
cffect
i\·e
threading
4·6 ply
be
sewn
grade threads
please refer to
dle com
es
is a bit le
to eliminate skip stitches.
thread. left
with
the synthetic threads
quality
threads
grade thr
es
thread
hand
as well
- 4
Fig.
13. Short
all the
ft
direction
with only high
tw i
sted,
cause
eads
to use
in size
--
way upto the need
uniform
thread breakage
with
of
of thr
ead
and
needle
±j:
11. \\·herea: for \\'hip stitch. upto
groove
against the centre of
as
#50-#
in f
ront
le
grade thr
in
diameter
well
as
cotto
\\'hich
this machine.
100.
of
you
and
bar
hole.
needle
eads, preferab
without knot
n th r
eads
..
drop
the
productivity.
eye
so
fasten th e
bar. At
ly
cotton
or slubs.

•
Threads
4.
Winding
and
gimp passes
lower
(pl
ease
thread
refer to Fig. 1
:1).
Upper threa
d
5_
Threading
To
thread
(Fig .
bobbin
on
the
14)
case
bobbin case. plea
For lower
c
otton thr
ance
To
4-S
push the l
of
maticall
by the sc rew.
se
refer to Fig. 15.
thread.
ead.
with synthetic
wind the th re
tim
es
around
ever to start to wind_ When suffici
threads will
y.
The
a.
it is r
but
it can be
threads as
ad
in bobbin. ple
the e
be
wnund. th e b
amount
b.
c &
ecomme
mpty bo
of
d.
nded to u
assured
well.
bbin
obb
threads
se
with
to
get
sew
ing pe
ase
refer to Fig. 1
counte
r clock wi
ent
in winder will stop
to be wound is
#50-#
rform-
4.
Wind
se,
amount
auto-
adjusted
100
and
(Fig.
(Fig.
15a
15b
)
(Fig.
)
15
- 5 -
c)
(Fig. 1
5d
)

6. Lower tension
7. Insert i
ng
(Fig. 16)
(Fig . 17)
bobb
machin
This
case.
ecia
Esp
thread.
thus
bobbin from idle r unning.
the t
hook and pull the l
adjust it. (See fig.
The
spring
grams
~·
in ca
se into
s
(N
so
hook
Please
th
in
lly, when
ther
with spring
ens
tension of lower thread is adju
and
by
pring, thu
OTE)
that
you n
refer to Fig.l 8
at
time
order to
e mu
st
be
used
with
special bobbin
you
may
use the synth
e causes
ion of lower
braking spring. Each tension as
thread
s s
tandard
Braking sprin
eed
, pl
ease
avo
idle
runn
ing of
actio
n in the bobbin
Therefo
thread.
ower
16)
retaining spring
tens
g is
no
adjustme
to inse
mak
e sure to pu ll the threa
id
thread
set the bobbin
thread.
ion is 30
correctly
nt
rt
jammin
re. when y
then ch
sted by
-35 gram
until it will
the bobbin
g.
etic
bobb
in in
case. it prevents
ou
eck
the
standard
and
20 grams by
s in
adjusted
be
case
d end to
and bobb
thread as
the bob
case ont
its tension
thread reta
befor
bin
want
is 10- 15
total.
e shipment.
out
of orde
into hoo
ward
to adju
o r
in
lower
case.
the
st
ota
ry
and
ining
braking
r.
k.
At
you
8. Running
When you will s
engaged
ac
m
The
dri ving
case
With
ma
his ma
T
clamp
if
to
(
in the s
hine from s
best
way
the pull
and cutt
left trea
chine.
chine is designed
ing foot is lifted
you depr
run,
and
OTE)
Plea
th
9. Operatin g
(I) On
(
2)
upp
On lower
tart
the
mach
ine. plea
topper cam.
tarting by the m
to compr
ey slowly to observe the
er then start to run.
dle pedal. you can lift the c
ess
right
left treadle p
se
e machine will n
cutt
er
thr
ead bre
thread
ehend the m
and
tread
be c
areful that when machine is going to
er l
ocking de
runnin
with safet
prevents the
le pe
dal
eda
l will not en
ot
aking
g o
ut
Unle
oto
on
stop.
or t rea
se
mak
e sure
ss
you
may
r. Fig 2
vic
0.
ach
ine mechan
respec
lamping
y dev ice. which pr
clamping
the
half
way
gage
e
h
rea
d b
With this model, LH4· 8 814-4, in
will be locked au
ll
be en
wi
the m
pr
eve
nt the materials from
tart. Fig 1
res
to
be normal sl
be acqu
tive move
in lifting cl
I
ac
aint
ism
thoroughl
foot
and
foo t from lifti ng
of left pedal en
}
. you
<1ng
hine st
gage
the
d in,
ops
9.
ed with th is machine, please r
ment
eve
amp
tomat
op pos
tllon, th
y, please
s.
At
with
right treadl e ped;-tl. you c
nts the machine
gagemen
ing foot whil e machine is runni ng.
sto
p if you will
can
ha,
·e machine
butt
onhole \\'It h
icall y
plea
se de
automaticall
damage
start the machi ne
first,
remove thr
up
while machine runs.
t, the
.
cutter.
case
and
in
pre
ss
y.
Wi
and
at
is, th e s
ead. need
from star
machine
depr
res
of ( 1) the cu
case of
the cu
th thi s step, it ensur
you can have machi ne
ting while the
ess left tr
ta rt wit hout c
tte
(2),
tter
stop leve
topp
efrai
by
le. bobbin
an start
Ther
will
not start
eadle peda
r m
ovement
as
the c
r until
er is
n th e
hand
the
efore,
l,
utting
utt
er
es
to
(Fig .
19)
. 6

10
. Emergency
stop
(F
ig.
20)
It
is
esse
ntial to stop the
the machine runs when the needle
the hoo k.
damage
In this case, de
and
rel
means th
ing the lever a nd will be reduced
lever.)
.
ease
at mac
Th
is preve
pr
ess down the emergency stop lever by ha nd
it. (
Thi
s ope ration of the emergency
hine
spee
mac
hine instantaneously
nts the machine and m
d will be reduced to 800 rpm by press·
breaks
to
even if
or thread jamming
ate
rials from
stop lever
zero by rel
eas
ing the
in
11. Operating
\\
'hen you wi
you would like to
clockwi se by means of this manual feeding handle at your desir
(NOTE)
manual
ll use
I.
At the repairin
st
opper which is on the condition of depressing the right treadle pedal. after turning the
pulley
startin
or
dep
2.
T he manual feeding handl e should
safe
is
correct angle.
feeding handle
the emergency
resta
rt the
mac
g of this machi
by hand. th
g to run.
ressing the cu
to
This ca
ope
rate the manual feeding handle at
stop
hine ju
ere cau
tte
r stop l
lever or when the thread brea k
st before the def
ne, on the conditi on th
ses
sometim
n be avoided by s
ever as
es
the cutter being operated to dr
show n
be used wh
4. ADJUSTMENT
1.
Upper
tension
age cau
ect
ive stitch .
ed position. Fig
tartin
g the machine from normal stop position
in
Fig. 19.
en the needle is apa rt from the material's. It
that pos
at
At
the
ition that
ses
during its ope ration.
that time. turn the feed
20.
stop
cam may
stop
op
ca m
at the
be off from
stops
machine
at
cam
the
T his machine
an
d no need to tension.
is
equipped with two t
(Fig. 2 1)
ens
ion regulator
on the upper plate and sub-tension is fixe
(l) Upper tension should be adju
it is pulled
T o check the t
manual feed ing handle
(2)
Tension spring stroke and its
T he s
sub-tension knob so
is pull
At tha t time. the tensio n 1s regu l
te
nsion knob so
is pulled downward.
s.
Upper tension is regulated by the tension of
as
per
fo'
ig. 21.
ens
ion is done by r
tr
oke of tension spri
as
ed
as per
fo'
ig. 2
as
to be 10- 15 gr
an
to
1.
- 7 -
d the spring tensio n
ste
d within
otating
d p
ress
ing the actu
adjustme
ng
is regul
be
5- 7mm when the upper thread
ams when
25-45
the
mac
ating trea
nt.
ated
by turning the
ated
by turning the sub-
the
gra ms when
upp
hine by the
dle peda
er
thr
ead
l.

2.
Timing
*Wh
is inco
turn
(Fig.
en the heig
rre
the upper tension
the
ct pos
hook
I
ht
ition.
I
8••
22
) (Fig.
of thread
loosen the scr
regulat
take·up s
ew
or a
sse
pring
and
mbly.
*Th
e threa
to correct tension as weak as possible.
*To
change the tension.
23.
f.'ig
and needle
d l al\e·
23)
up spri
ng mu
turn the stud screw.
st
be adjusted
1
3-
~\/·
(Fig.
24)
To
make adjustm
needle
When the needle comes up
1s
at the dis
comi
located
at behi
tan
3. Adjustin g the width
Fo
rward
ent
of
t1m111g
ng clown
ce
to
the ce
nd the cent re
of I.Hmm bet ween the
(Fig
26)
the h
ntr
e of needle plat
:~mm
fr
om its lowest pos
of needle. A t
of
buttonhol
ook
point
(I) T o
(2)
and needl
e.
that
of
hook
mak
screw
T o
mak
bar
clamp screw.
e and
(Fig. 25)
e.
please make sure
itio
n. it
is
correct timing
Lime. the correct height of needle
and the top
e adjustme
as per
e adjustme
position
Fig. 2:1.
nt
nt
f.'i
g. 26.
of
of
of
to
be
needle eye.
of
timing
needle
the
bar
buttonhole
at
height. loosen the needle
the
position
that the point
bar is cle
f.'ig 2-
1.
hook
. loosen the
of
of
hook
termin
the
ccl
set
::
l )
r
;-;
Bookwa<
WI
A li
ne
(I ) Needle
'
fhis ma
(2)
Adj
th
narro\\'
The width
If
hole \\'
B
line
(Fig.
swingi
chine s
usting z1gzag
e zigzag
you
er.
(Figs
\\·ill
llhout
width
of zigz
loo
d I
~
WI
ng.
bar
--WI
-W2-
27)
win
gs the needle
wid
th \
will
. 28.
29)
ag
and Lacking ca n be a
sen
consicler(lbly the
takin
g
lin
e
from right
'II
I and W
be \\'icier. and
2.
adjustin
vVi
turn
th
(F
ig .
28)
to left eith
WI
to
dju
sted
g sere\\'
er going fo
and W2 adju
left (counter-c lockwise). the zigzag
by
the
adj
for
bar tacki
8
(Fig.
rwa
rd
or
backward.
sti
ng screws. t
usting screws to be
ng. you can obtain the gi
urn
29)
f.'i
g.
27.
to right (clock
width
large
will
r or sm
mp
butto
wise).
be
(lller
n·
.
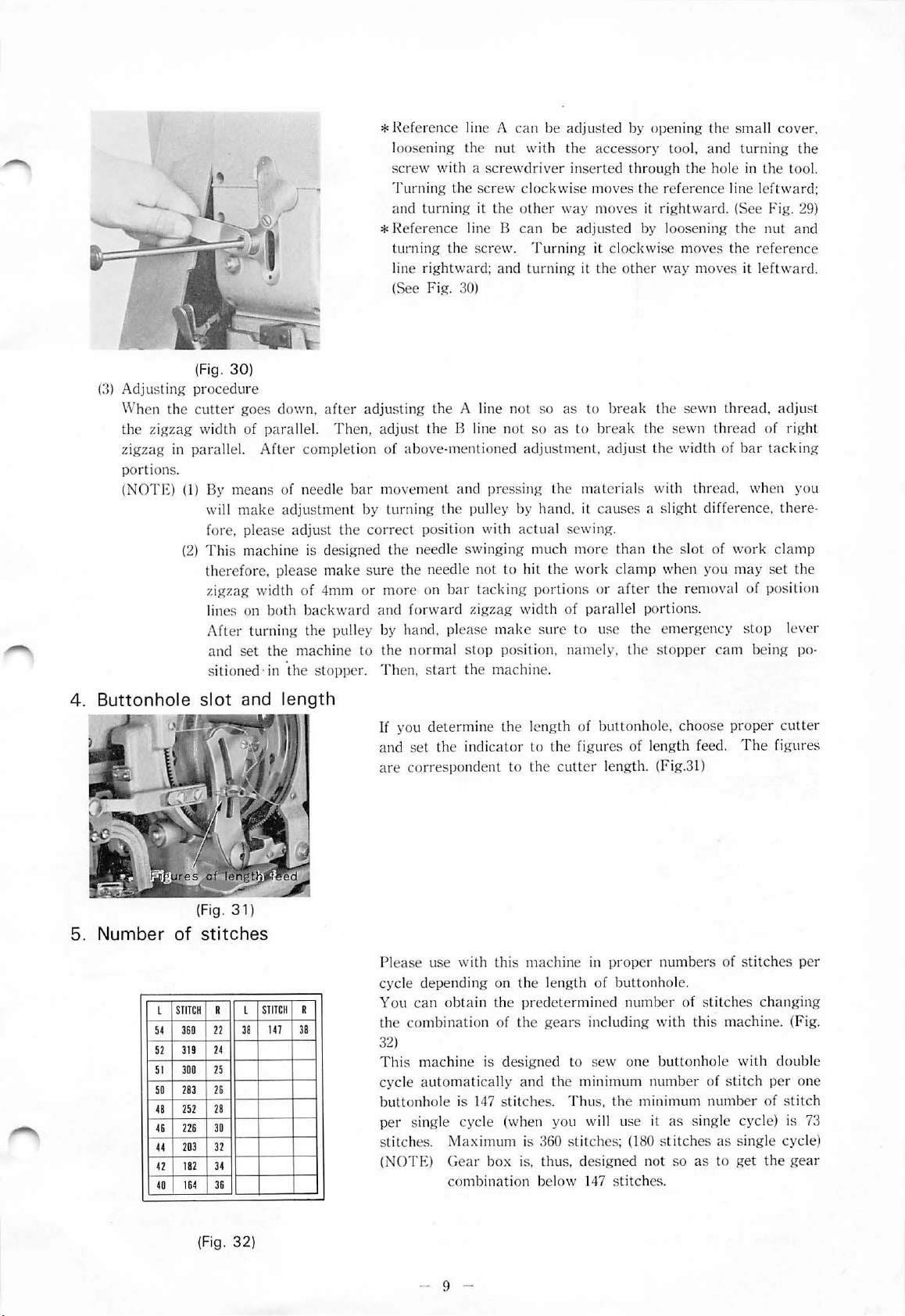
(3) Adjus
When t
the zi
zigza
portions.
(
T
OTE)
(Fig.
30)
ting procedure
he
cutter
goes
gzag width
g in paralle
(1) By me
(2)
l.
wi
ll
mak
fo
re.
Thi
s machine is designed the needle swinging much m
theref
zi
gzag
es
lin
/\ft
er
set
and
sitioned·
down,
after adju
of paralle
Aft
an
plea
ore, pl
width o f 4
on
turning
l. The
er
comp
letion of above
s of needle
e a
djus
tme
se
adjust
the correct position
ease mak
mm
both backward and
the pulley by hand , pl
the
machine to
in 'the stoppe
*
I
~cference
l
oose
screw
Turning the
and
*R
efe
line A can
ning
the nut
with
a s
screw
turn
ing it
renc
e line B can
turning the screw.
line rightwa
(S
ee
Fig. 30)
rd; and
sting the A line
n,
adjust
the
B line
-mentioned adjustment.
bar moveme
nt
by turning the pulley
nt
and
with
e sure the needl e not to
or
mor
e on
bar
tacl.;ing
forwa
rd zi
gzag
ease
the norm
r. The
al slop position, namely.
n, start
the
be
adju
with
the
crewdriver inserte
clockwi
the
other
not
not
pressing the
by
actual
se
moves
way
be
adjuste
Turning
turn
so
it cl
ing it the
as to break
so as to brea
mat
hand. it
sewi ng.
ore
hit
the
work
port
ions or after the removal
width of
mak
e sure to
machin
par
e.
sted by
accessory too
opening
l, and turning
the small
d through the hole in the too
the referenc e line
moves
it rig
d by l
ockwise
other way
the sewn
k the sewn thre
adju
st
the
erials wi th
causes
than
a slight
the slot
clamp whe
htward.
oosen
mov
moves it le
width
threa
n you
ing the nut
es the
diff
leftwa
(See Fig. 29)
referen
thread.
ad
of bar
d,
when you
erence. there-
of
work
may
of
allel por
use
tio
ns.
the
eme
rgen
the stopper ca
cy st
m be i
op
cove
ftward
adjust
of
rig
tac
clamp
set
pos
ition
lever
ng
r.
the
l.
rd;
and
ce
.
ht
king
the
po-
4.
Buttonhole
5. Number
54
52
51
50
48
46
44
42
l
40
slot
(Fig. 31)
of
stitches
S
TITCH
360
319
300
283
252
226
203
182
164
R l
22
24
25
26
28
30
32
34
36
and
STITCH
38
length
147
38
If you dete
and
are co
Pl
ease use
cycle
R
You c
co
the
rmine the length o f buttonhole,
se
t the
indicator
rre
spondent to the
with
depending
an
obtain
mbina
tion
to
the figu
cutter length. (Fig.3l)
this
machin
on the length
the pre
of
determ
the gear
res
of
e in
proper numb
of
buttonhole.
ined number
choose
length feed.
of stitches
prope
The figures
ers of stitch
chang
r c
es
utt
er
per
ing
s including wi th this machine. (Fig.
32)
This machin
cyc
le automatically
butt
onhole is 147
per single
tches. Maximum
sti
(NOTE)
e is desi
stitches.
cyc
le (when yo u w
Gear box
ombination
c
gne
d to sew one
and
the
minim
um
Thu
s, t
he mini
ill
use it as single
is 360 s
is, thus, d
titches; (180 stit
esigned
below 147 stitches.
buttonh
number
mum
not
so
ole with double
of
stit
ch per one
num
ber of s
cyc
ches
as
single
as to
get the
titch
le) is 73
cycle
gea
)
r
(Fig.
32)
-- 9 -