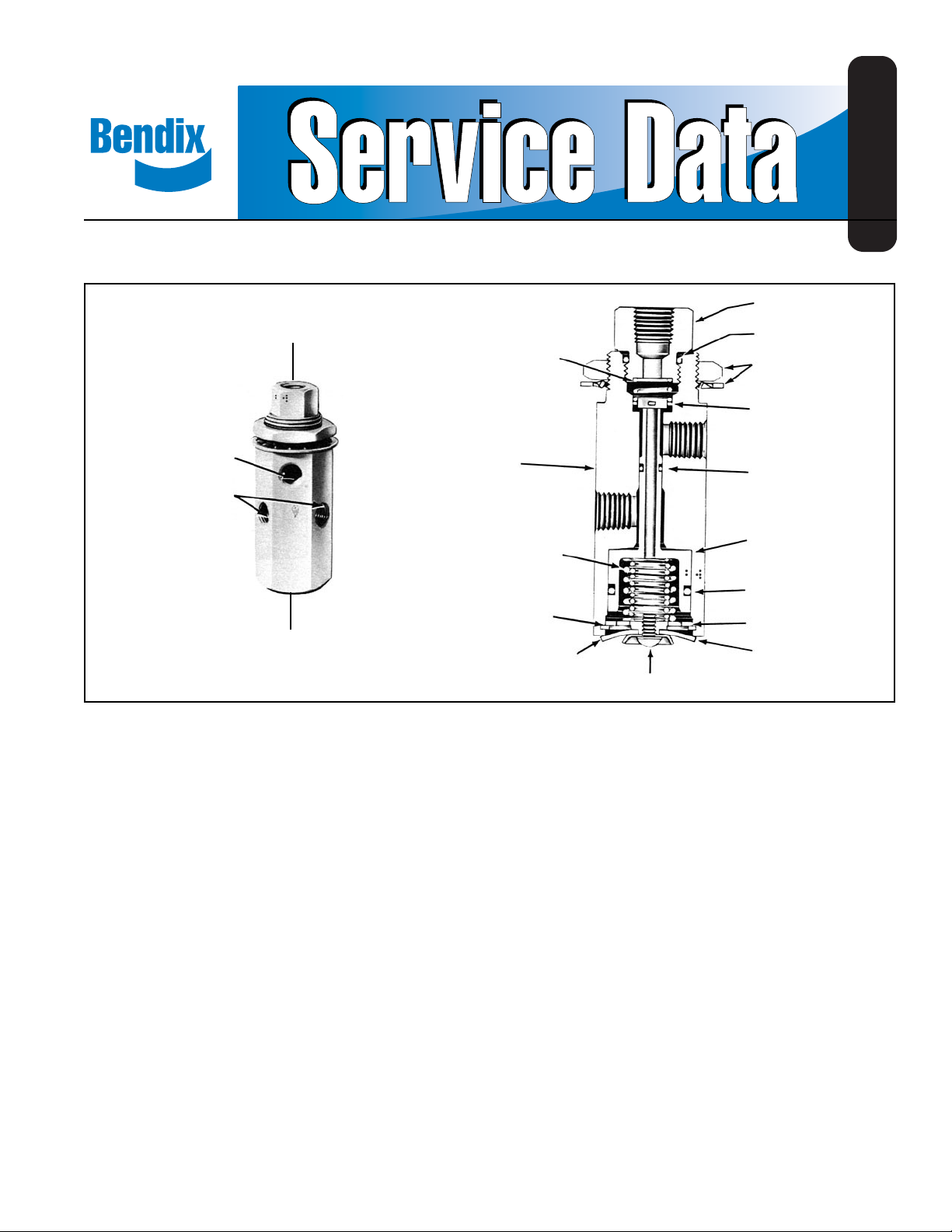
®
Bendix® TR-2™, TR-3™ & TR-4™ Inversion Valves
SD-03-4650
CAP NUT
SUPPLY PORT
INLET & EXHAUST
DELIVERY PORT (2)
CONTROL PORT (3)
PISTON SPRINGS
RETAINER RING
EXHAUST
DIAPHRAGM WASHER
FIGURE 1 - TR-2™ INVERSION VAL VE
DESCRIPTION
GENERAL
The TR-2™ & TR-3™ valves are normally open pilot-operated,
inverting, on-off, two-way valves. The TR-4™ valve is lever
operated. With normal operating pressure at both supply
and control ports, the delivery port will be exhausted to
atmosphere. As control pressure is reduced to the point
that the piston return spring or springs overcomes the force
on the control piston, the valve will deliver full supply pressure
at the delivery port.
TR-2™ INVERSION V AL VE
SEAL RING
VALVE SPRING
BODY
CAP SCREW
MOUNTING NUT
& LOCKWASHER
INLET & EXHAUST
VALVE
PISTON GROMMET
(SMALL)
PISTON
PISTON GROMMET
(LARGE)
COVER PLATE
EXHAUST
DIAPHRAGM
TR-3™ INVERSION V AL VE
Referring to Figure 2, the TR-3™ valve is similar in function to
the TR-2™ valve, but with a die cast body . Referring to Figure
3, some TR-3™ valve’s have an internal passage in the body
connecting supply pressure to control. The external control
port is permanently plugged in such valves.
TR-4™ INVERSION V AL VE
Referring to Figure 4, the TR-4™ valve is a TR-3™ valve with
the internal passage connecting supply and control plus a
manual lever control which permits the valve to be locked in
the open position.
Referring to Figure 1, the TR-2™ valve was used primarily in
early DD-3™ Safety Actuator control systems to apply air
pressure to the emergency diaphragm of the DD-3
actuator’s from a protected reservoir as control pressure is
released from the lock mechanism. The TR-2™ valve is
available in 11/4" bulk head mount only .
OPERATION
TR-2™ & TR-3™ INVERSION V AL VES
™
When sufficient air pressure is present in the control cavity
to overcome the setting of the piston return spring, the piston
is held away from the inlet valve which is held closed by the
inlet valve return spring. The delivery lines are vented to
atmosphere through the hollow exhaust stem of the piston.
When air pressure in the control cavity falls to a
1
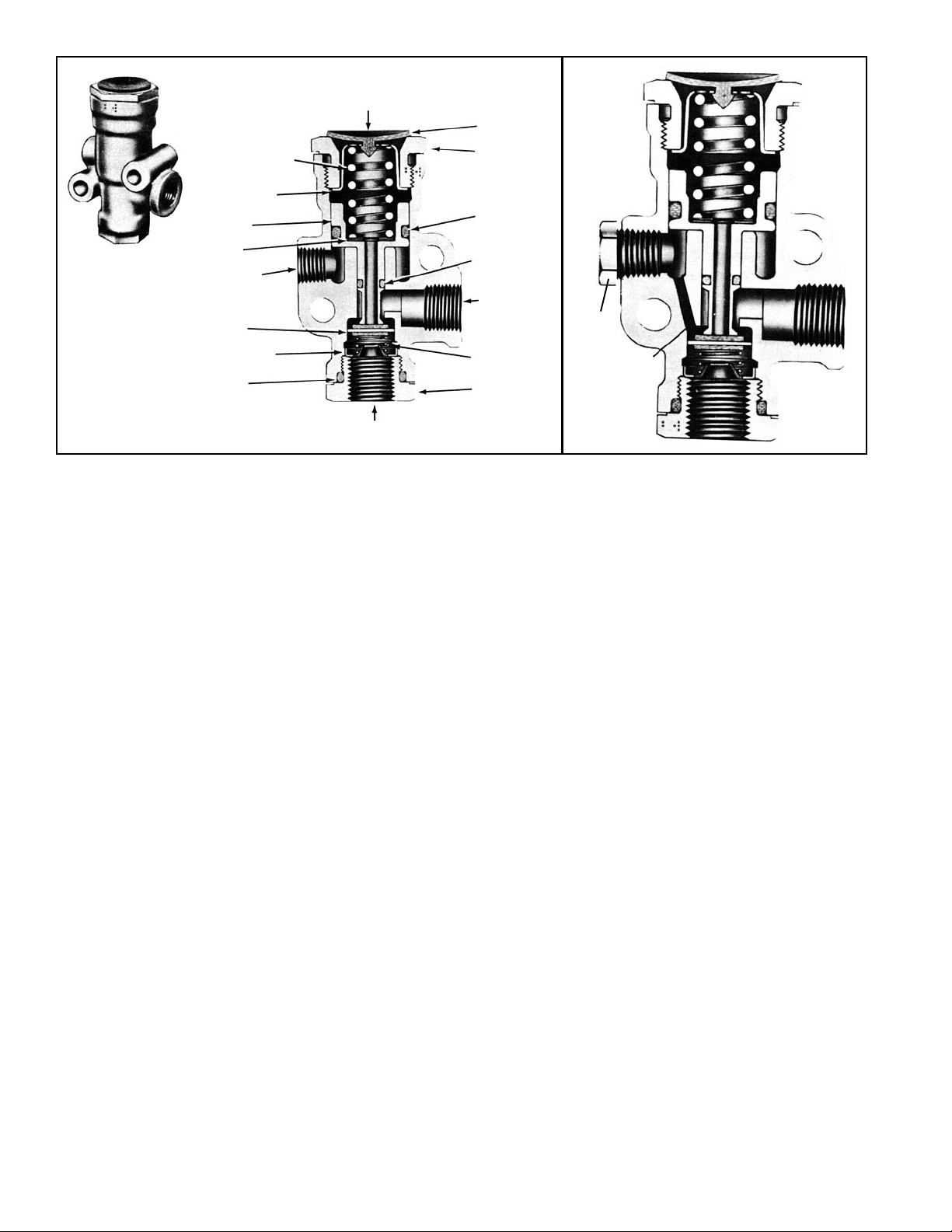
EXHAUST
DIAPHRAGM
PISTON SPRING
DIAPHRAGM
RETAINER
PISTON
SHIM
1/8” P.T.
CONTROL
INLET &
EXHAUST
VALVE
VALVE STOP
O-RING
1/4” P.T. SUPPLY
FIGURE 2 - TR-3™ INVERSION VAL VE FIGURE 3 - TR-3™ INVERSION VAL VE
predetermined pressure or is vented from the control cavity ,
EXHAUST
NUT
O-RING
O-RING
1/4” P.T.
DELIVERY
VALVE
SPRING
CAP
PIPE
PLUG
INTERNAL
PASSAGE
INTERNAL BLEED CONTROL
PREVENTIVE MAINTENANCE
the piston spring forces the piston against the inlet valve
closing the exhaust passage in the hollow piston stem.
Further travel of the piston opens the inlet valve allowing the
passage of air past the open inlet valve and out the delivery
port.
The TR-3™ valve with the internal control passage functions
the same as above except that the control pressure is always
the same as the supply pressure. Consequently , as supply
pressure builds up, when the pressure is great enough to
overcome the piston return spring, the delivery pressure will
be vented out the exhaust. On descending supply/control
pressure, as the piston return spring overcomes the control
pressure the valve will deliver the remaining supply pressure
at the delivery port.
Important: Review the Bendix Warranty Policy before
performing any intrusive maintenance procedures. A warranty
may be voided if intrusive maintenance is performed during
the warranty period.
No two vehicles operate under identical conditions, as a
result, maintenance intervals may vary. Experience is a
valuable guide in determining the best maintenance interval
for air brake system components. At a minimum, the
inversion valves should be inspected every 6 months or 1500
operating hours, whichever comes first, for proper operation.
Should the inversion valves not meet the elements of the
operational tests noted in this document, further investigation
and service of the valve may be required.
TR-4™ INVERSION V AL VE
The TR-4™ valve provides the same functions as the internal
passaged TR-3™ valve except the lever override gives the
operator the option of locking the valve in the open or delivery
position.
MOUNTING LOCATION
Care should be given to assure proper mounting location of
the valve with the exhaust pointed downward, mounted high
on the frame rail, and away from road spray and debris.
Unprotected or exposed exhaust ports can allow migration
of road contaminants into the valve, which may cause
accelerated wear or unintended operation.
2
OPERA TING AND LEAKAGE TESTS
NOTE: The following checks should be made with two
calibrated gauges or two gauges known to be
accurate. Depending upon installation, it may be
easier or necessary to completely remove the valve
to test properly .
Install one test gauge in a common control and supply line;
install the other gauge in the delivery port. Gradually apply
pressure to the common supply and control line. On
ascending pressure, note at what pressure exhaust occurs
and compare with vehicle manual. With air pressure present
in supply and control port, apply a soap solution around the
supply port cap nut. No leakage is permitted. Apply soap
solution to the delivery and exhaust ports. Leakage should
not exceed 100 SCCM or a 1" bubble in not less than 5
seconds. Excessive leakage would indicate a faulty o-ring
or inlet valve. Operate the manual control of the TR-4™ valve
and note that delivery and exhaust occur promptly .

PLUNGER
LEVER
PLUNGER SPRING
PISTON SPRING
VALVE STOP
FIGURE 4 - TR-4™ INVERSION VAL VE
Slowly decrease pressure in the control cavity and note at
what pressure delivery is made and compare with vehicle
manual.
NOTE: In the TR-3™ valve shown in Figure 3 and the TR-4
valve in Figure 4, control pressure is reduced by
decreasing supply air pressure because of the
internal passage connecting supply and control.
If the TR-2™, TR-3™ or TR-4™ inversion valve does not function
as described or leakage is excessive, it is recommended
that it be replaced with a new valve or remanufactured unit,
or repaired with genuine Bendix parts available at Bendix
outlets.
WARNING! PLEASE READ AND FOLLOW
THESE INSTRUCTIONS TO AVOID
PERSONAL INJURY OR DEATH:
When working on or around a vehicle, the following
general precautions should be observed at all times.
1. Park the vehicle on a level surface, apply the
parking brakes, and always block the wheels.
Always wear safety glasses.
2. Stop the engine and remove ignition key when
working under or around the vehicle. When
working in the engine compartment, the engine
should be shut off and the ignition key should be
removed. Where circumstances require that the
engine be in operation, EXTREME CAUTION should
be used to prevent personal injury resulting from
contact with moving, rotating, leaking, heated or
electrically charged components.
3. Do not attempt to install, remove, disassemble or
assemble a component until you have read and
COVER
PIN
SHIM
PISTON
O-RING
PLUGGED
INLET/EXHAUST
VALVE
O-RING
1/4” P.T. SUPPLY
LOCK NUT
COVER NUT
O-RING
1/4” P.T.
DELIVERY
VALVE
SPRING
CAP
thoroughly understand the recommended
procedures. Use only the proper tools and observe
all precautions pertaining to use of those tools.
4. If the work is being performed on the vehicle’s air
™
brake system, or any auxiliary pressurized air
systems, make certain to drain the air pressure from
all reservoirs before beginning ANY work on the
vehicle. If the vehicle is equipped with an AD-IS
air dryer system or a dryer reservoir module, be
sure to drain the purge reservoir.
5. Following the vehicle manufacturer’s
recommended procedures, deactivate the electrical
system in a manner that safely removes all electrical
power from the vehicle.
6. Never exceed manufacturer’s recommended
pressures.
7. Never connect or disconnect a hose or line
containing pressure; it may whip. Never remove a
component or plug unless you are certain all
system pressure has been depleted.
8. Use only genuine Bendix® replacement parts,
components and kits. Replacement hardware,
tubing, hose, fittings, etc. must be of equivalent
size, type and strength as original equipment and
be designed specifically for such applications and
systems.
9. Components with stripped threads or damaged
parts should be replaced rather than repaired. Do
not attempt repairs requiring machining or welding
unless specifically stated and approved by the
vehicle and component manufacturer.
10. Prior to returning the vehicle to service, make
certain all components and systems are restored
to their proper operating condition.
™
3

REMOV AL AND INST ALLA TION
REMOV AL
Block and hold vehicle by means other than air brakes. Drain
service and emergency or parking reservoirs. Disconnect
air lines from valve. Remove the mounting bolts, remove valve.
INST ALLATION
Remount valve securely using holes provided in body . Check
and clean air lines and reconnect.
DISASSEMBL Y
NOTE: Care should be taken if body is clamped in vise.
Excessive tightening can cause distortion of valve
body.
TR-2™ INVERSION V AL VE
1. Remove the cap nut with sealing ring, remove sealing ring
from cap nut.
2. Remove the inlet/exhaust valve spring and inlet/exhaust
valve.
3. Turn the valve over and remove the exhaust diaphragm
cap screw with lockwasher, then the diaphragm washer
and diaphragm.
4. With a pair of #1 Truarc pliers, remove the retainer ring.
Remove the cover plate and two (2) piston springs.
5. Remove the piston with grommets.
6. Remove the piston grommets.
TR-3™ INVERSION V AL VE
1. Remove the exhaust port cap nut and o-ring.
2. Remove the diaphragm retainer and piston spring.
3. Remove the shim washer or washers (if present).
4. Remove the piston from the valve body .
5. Remove the piston o-ring and exhaust stem o-ring.
6. Remove the supply cap nut and o-ring.
7. Remove the valve stop and spring.
8. Remove the inlet and exhaust valve.
TR-4™ INVERSION V AL VE
1. Press lever pin out of the lever and remove lever.
2. Remove the plunger and plunger return spring from cover.
3. Remove the cover nut lock nut.
4. Remove the cover nut and o-ring.
5. Remove the cover and shim washer or washers.
6. Remove the piston spring and piston from body .
7. Remove the piston and exhaust stem o-rings.
8. Remove the supply port cap nut and o-ring.
9. Remove the valve stop and valve return spring.
10. Remove the inlet and exhaust valve.
CLEANING AND INSPECTION
Wash all metal parts in a good cleaning solvent. Rubber
parts should be wiped clean.
Inspect all parts for signs of wear or deterioration. Check
the springs for cracks, corrosion, or distortion. Inspect the
piston and its exhaust seat, body bores, and inlet valve for
nicks, scratches, or burrs.
Replace all parts not considered serviceable during
inspection.
ASSEMBL Y
Before assembling the valve, lubricate the piston o-rings and
body bores with Bendix silicone lubricant such as BW650M
Bendix Pc. No. 291 126.
™
TR-2
INVERSION V AL VE
1. Install the piston grommets on piston.
2. Install the piston with grommets in valve body .
3. Position the piston springs, cover plate and retainer ring
in the piston in that order. Press the cover and ret ainer
down and with a pair of Truarc #1 pliers, snap the ring
into the body groove.
4. Install the diaphragm and diaphragm washer and secure
with cap screw.
5. Turn the inversion valve over and position the inlet and
exhaust valve in its bore.
6. Place the spring over inlet valve.
7. Install the sealing ring on cap nut. Install the cap nut with
sealing ring and tighten securely . T orque to approx. 125
in. lbs.
8. Using the mounting nut and lockwasher, install the valve
on vehicle.
TR-3™ INVERSION V AL VE
1. Install the inlet and exhaust valve in the body (supply
port).
2. Install the inlet valve spring and valve stop (center stop on
spring).
3. Install the o-ring on the supply cap nut and install and
tighten the cap nut. Torque to approx. 100 in. lbs.
4. Install the piston and exhaust stem o-ring on piston. Install
the piston in body .
5. Install the shim washer or washers (if present). Install the
piston spring.
6. Install the diaphragm retainer and exhaust diaphragm.
7. Install the o-ring on exhaust cap nut and install and tighten
the cap nut. Torque to approx. 275 in. lbs.
TR-4™ INVERSION V AL VE
1. Replace the inlet and exhaust valve.
2. Install the valve return spring and valve stop.
3. Install the o-ring on supply cap nut and install and tighten
the cap nut. Torque to approx. 100 in. lbs.
4. Install the piston and exhaust stem o-ring on the piston.
Install the piston in the body.
5. Install the piston spring.
6. Install the cover and washer or washers.
7. Replace the cover nut o-ring on the cover nut and install
and tighten the cover nut. Torque to approx. 275 in. lbs.
8. Install the plunger return spring and plunger.
9. Install the cover nut lock nut. T orque to approx. 100 in.
lbs.
10. Install lever and press the lever pin in to secure.
TESTING REBUIL T VAL VES
Perform operating and leakage tests as outlined in “Operating
and Leakage Tests” section.
4
BW1581 © 2004 Bendix Commercial Vehicle Systems LLC. All rights reserved. 4/2004 Printed in U.S.A.