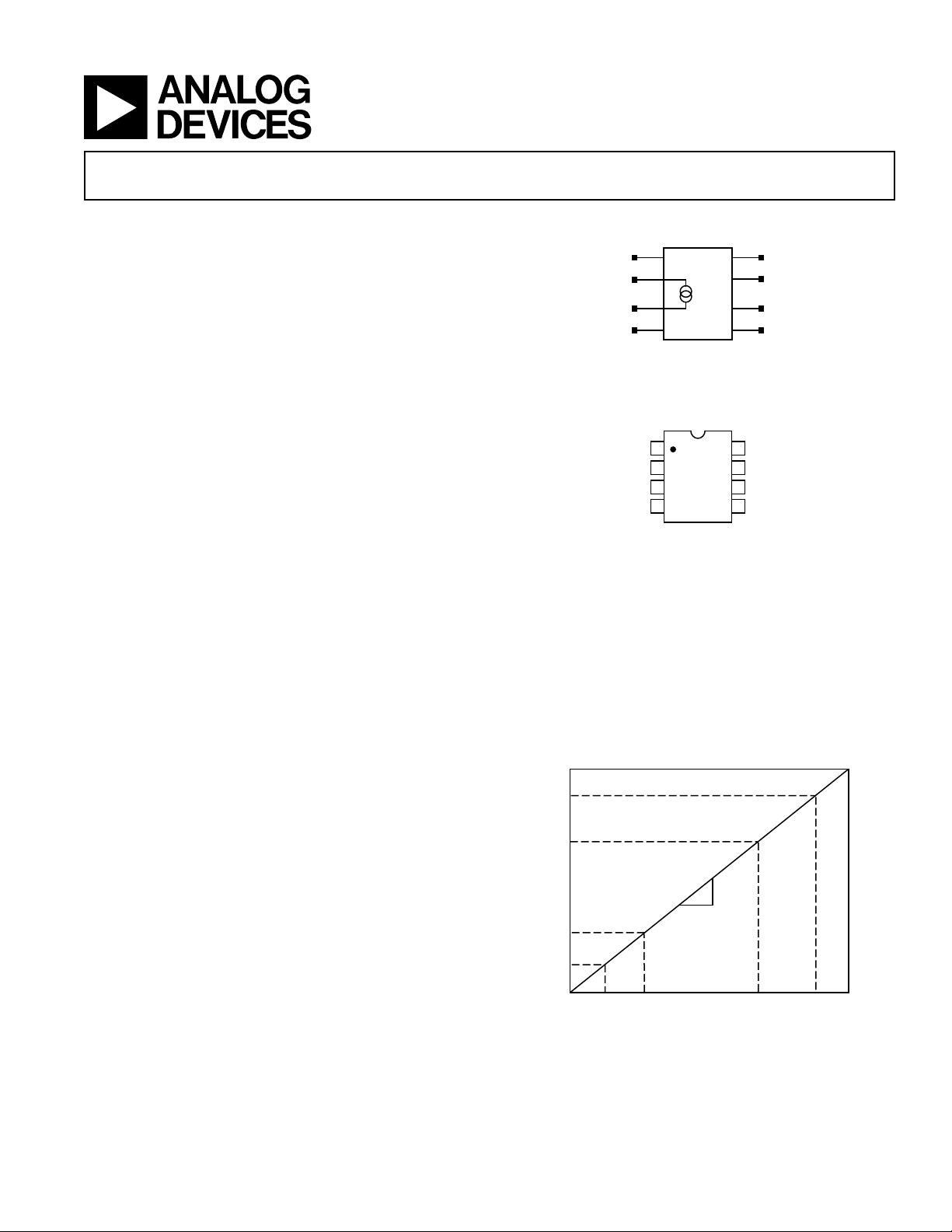
Low Cost, Current Output
378
343
273
248
1A/K
–45 –25 0 70 105 125
TEMPERATURE – ⴗC
I
OUT
– A
Temperature Transducer
FEATURES
Operating Temperature Range: –40ⴗC to +105ⴗC
Single-Supply Operation: 4 V to 30 V
Excellent Repeatability and Stability
High Level Output: 1 A/K
Monolithic IC: Temperature In/Current Out
Minimal Self-Heating Errors
APPLICATIONS
Appliance Temperature Sensor
Automotive Temperature Measurement and Control
HVAC System Monitoring
Industrial Temperature Control
Thermocouple Cold Junction Compensation
GENERAL DESCRIPTION
The TMP17 is a monolithic integrated circuit temperature transducer that provides an output current proportional to absolute
temperature. For a wide range of supply voltages, the transducer
acts as a high impedance temperature dependent current source
of 1 µA/K. Improved design and laser wafer trimming of the
IC’s thin-film resistors allow the TMP17 to achieve absolute
accuracy levels and nonlinearity errors previously unattainable
at a comparable price.
The TMP17 can be employed in applications from –40ⴗC to
+105ⴗC where conventional temperature sensors (i.e., thermistor,
RTD, thermocouple, diode) are currently being used. Expensive
linearization circuitry, precision voltage references, bridge
components, resistance measuring circuitry, and cold junction
compensation are not required with the TMP17.
The TMP17 is available in a low cost SOIC-8 surface-mount
package.
TMP17
*
FUNCTIONAL BLOCK DIAGRAM
PACKAGE DIAGRAM
SOIC-8
NC
1
V+
2
TOP VIEW
V–
3
(Not to Scale)
NC
4
NC = NO CONNECT
NC
8
NC
7
NC
6
NC
5
4. The high output impedance of the TMP17 provides greater
than 0.5ⴗC/V rejection of supply voltage drift and ripple.
5. Laser wafer trimming and temperature testing ensures that
TMP17 units are easily interchangeable.
6. Initial system accuracy will not degrade significantly over time.
The TMP17 has proven long term performance and repeatability advantages inherent in integrated circuit design and
construction.
PRODUCT HIGHLIGHTS
1. A wide operating temperature range (–40ⴗC to +105ⴗC) and
highly linear output make the TMP17 an ideal substitute for
older, more limited sensor technologies (i.e., thermistors, RTDs,
diodes, thermocouples).
2. The TMP17 is electrically rugged; supply irregularities and
variations or reverse voltages up to 20 V will not damage
the device.
3. Because the TMP17 is a temperature dependent current
source, it is immune to voltage noise pickup and IR drops in
the signal leads when used remotely.
*Protected by U.S. Patent No. 4,123,698
REV. A
Information furnished by Analog Devices is believed to be accurate and
reliable. However, no responsibility is assumed by Analog Devices for its
use, nor for any infringements of patents or other rights of third parties that
may result from its use. No license is granted by implication or otherwise
under any patent or patent rights of Analog Devices. Trademarks and
registered trademarks are the property of their respective companies.
Figure 1. Transfer Characteristic
One Technology Way, P.O. Box 9106, Norwood, MA 02062-9106, U.S.A.
Tel: 781/329-4700 www.analog.com
Fax: 781/326-8703 © 2003 Analog Devices, Inc. All rights reserved.
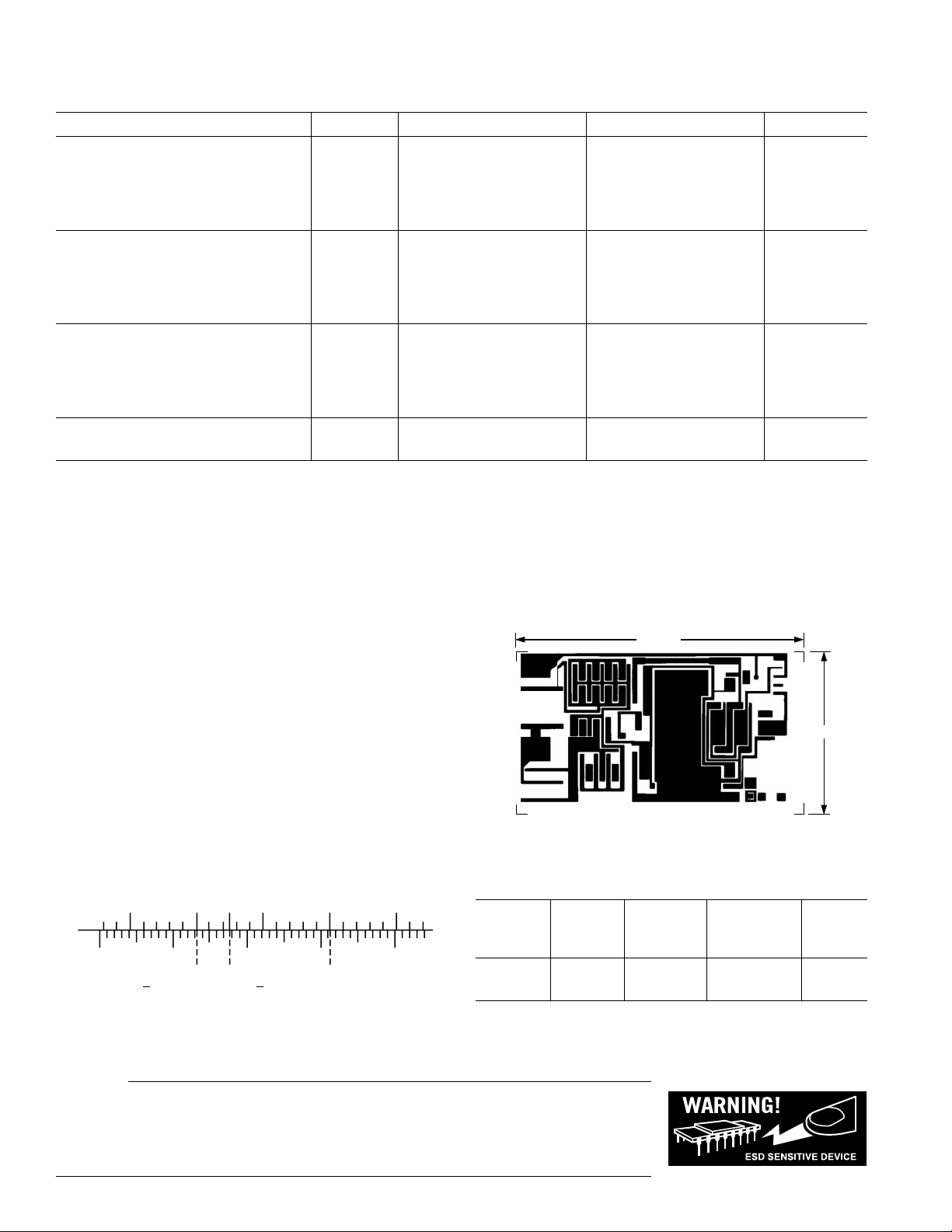
TMP17F/G–SPECIFICATIONS
(VS = 5.0 V, –40ⴗC ≤ TA ≤ 105ⴗC, unless otherwise noted.)
Parameter Symbol Conditions Min Typ Max Unit
ACCURACY
TMP17F T
TMP17G T
A
A
= 25ⴗC
= 25ⴗC
1
1
± 2.5 ⴗC
± 3.5 ⴗC
TMP17F Over Rated Temperature ± 3.5 ⴗC
TMP17G Over Rated Temperature ± 4.5 ⴗC
POWER SUPPLY REJECTION RATIO
4 V < VS < 5 V PSRR 0.5 ⴗC/V
5 V < V
15 V < VS < 30 V PSRR 0.3 ⴗC/V
Nonlinearity Over Rated Temperature
< 15 V PSRR 0.3 ⴗC/V
S
2
0.5 ⴗC
OUTPUT
Nominal Current Output TA = 25ⴗC (298.2 K) 298.2 µA
Scale Factor Over Rated Temperature 1 µA/ⴗC
Repeatability Note 3 0.2 ⴗC
Long Term Stability TA = 150ⴗC for 500 Hrs
4
0.2 ⴗC/month
POWER SUPPLY
Supply Range +V
NOTES
1
An external calibration trim can be used to zero the error @ 25ⴗC.
2
Defined as the maximum deviation from a mathematically best fit line.
3
Maximum deviation between 25ⴗC readings after a temperature cycle between –40 ⴗC and +105ⴗC. Errors of this type are noncumulative.
4
Operation at 150ⴗC. Errors of this type are noncumulative.
Specifications subject to change without notice.
S
430V
ABSOLUTE MAXIMUM RATINGS*
Maximum Supply Voltage . . . . . . . . . . . . . . . . . . . . . . . . .30 V
Operating Temperature Range . . . . . . . . . . . –40ⴗC to +105ⴗC
Maximum Forward Voltage (1 to 2) . . . . . . . . . . . . . . . . . 44 V
Maximum Reverse Voltage (2 to 1) . . . . . . . . . . . . . . . . . . 20 V
Dice Junction Temperature . . . . . . . . . . . . . . . . . . . . . . 175ⴗC
Storage Temperature Range . . . . . . . . . . . . . –65ⴗC to +160ⴗC
Lead Temperature (Soldering, 10 sec) . . . . . . . . . . . . . 300ⴗC
*Stresses above those listed under Absolute Maximum Ratings may cause perma-
nent damage to the device. This is a stress rating only and functional operation at
or above this specification is not implied. Exposure to the above maximum rating
conditions for extended periods may affect device reliability.
TEMPERATURE SCALE CONVERSION EQUATIONS
K +223ⴗ +273ⴗ +298ⴗ +323ⴗ +373ⴗ +423ⴗ
ⴗC –50ⴗ 0ⴗ +25ⴗ +50ⴗ +100ⴗ +150ⴗ
ⴗF –100ⴗ 0ⴗ +100ⴗ +200ⴗ +300ⴗ
+32ⴗ +70ⴗ +212ⴗ
5
ⴗC = (ⴗF – 32) ⴗF = ⴗC + 32 K = ⴗC + 273.15
9
9
5
METALLIZATION DIAGRAM
62mils
V+
37mils
V–
ORDERING GUIDE
Max Cal Max Error Nonlinearity
Error –40ⴗC to –40ⴗC to Package
Model @ +25ⴗC +105ⴗC +105ⴗC Option
TMP17FS 2.5ⴗC 3.5ⴗC 0.5ⴗCR-8
TMP17GS 3.5ⴗC 4.5ⴗC 0.5ⴗCR-8
CAUTION
ESD (electrostatic discharge) sensitive device. Electrostatic charges as high as 4000 V readily
accumulate on the human body and test equipment and can discharge without detection. Although the
TMP17 features proprietary ESD protection circuitry, permanent damage may occur on devices
subjected to high energy electrostatic discharges. Therefore, proper ESD precautions are recommended
to avoid performance degradation or loss of functionality.
REV. A–2–
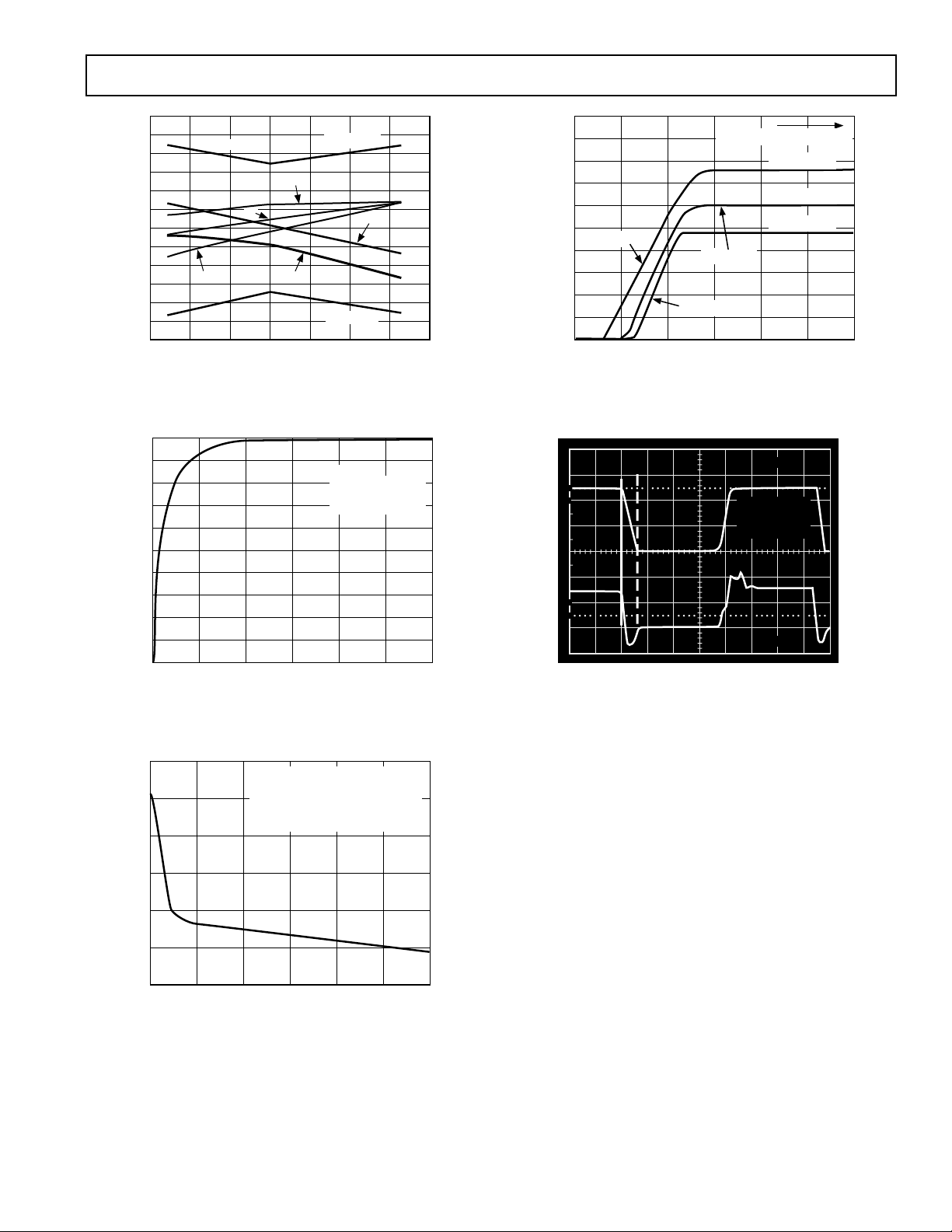
Typical Performance Characteristics–TMP17
6
5
4
3
2
1
0
–1
–2
–3
TEMPERATURE ERROR – ⴗC
–4
–5
–6
–50 125–25
V+ = +5V
2
4
0255075100
TEMPERATURE – ⴗC
MAX LIMIT
1
3
5
MIN LIMIT
TPC 1. Accuracy vs. Temperature
100
90
80
70
60
50
40
30
PERCENT OF CHANGE – %
20
10
0
0305
10 15 20 25
TIME – sec
V+ = +5V
SOIC PACKAGE
SOLDERED TO
0.5" ⴛ 0.3" Cu PCB
TPC 2. Thermal Response in Stirred Oil Bath
500
450
400
350
300
250
200
150
OUTPUT CURRENT – A
100
50
TA = +105ⴗC
0
061
2345
SUPPLY VOLTAGE – V
CONSTANT I
TA = +25ⴗC
TA = –40ⴗC
TPC 4. V-I Characteristics
100
90
10
0%
VIN = 0V TO 5V
= 1k⍀
R
L
= 25ⴗC
T
A
200mV
TPC 5. Output Turn-On Settling Time
I
I
I
2µs
OUT
OUT
OUT
OUT
UP TO 30V
= 378A
= 298A
= 233A
60
50
40
30
20
TIME CONSTANT – sec
10
0
0 600100
TRANSITION FROM ⴙ100ⴗC STIRRED
BATH TO FORCED ⴙ25ⴗC AIR
Vⴙ = ⴙ5V
SOIC PACKAGE SOLDERED
TO 0.5“ ⴛ 0.3” Cu PCB
200 300 400 500
AIR VELOCITY – FPM
TPC 3. Thermal Time Constant in Forced Air
REV. A –3–