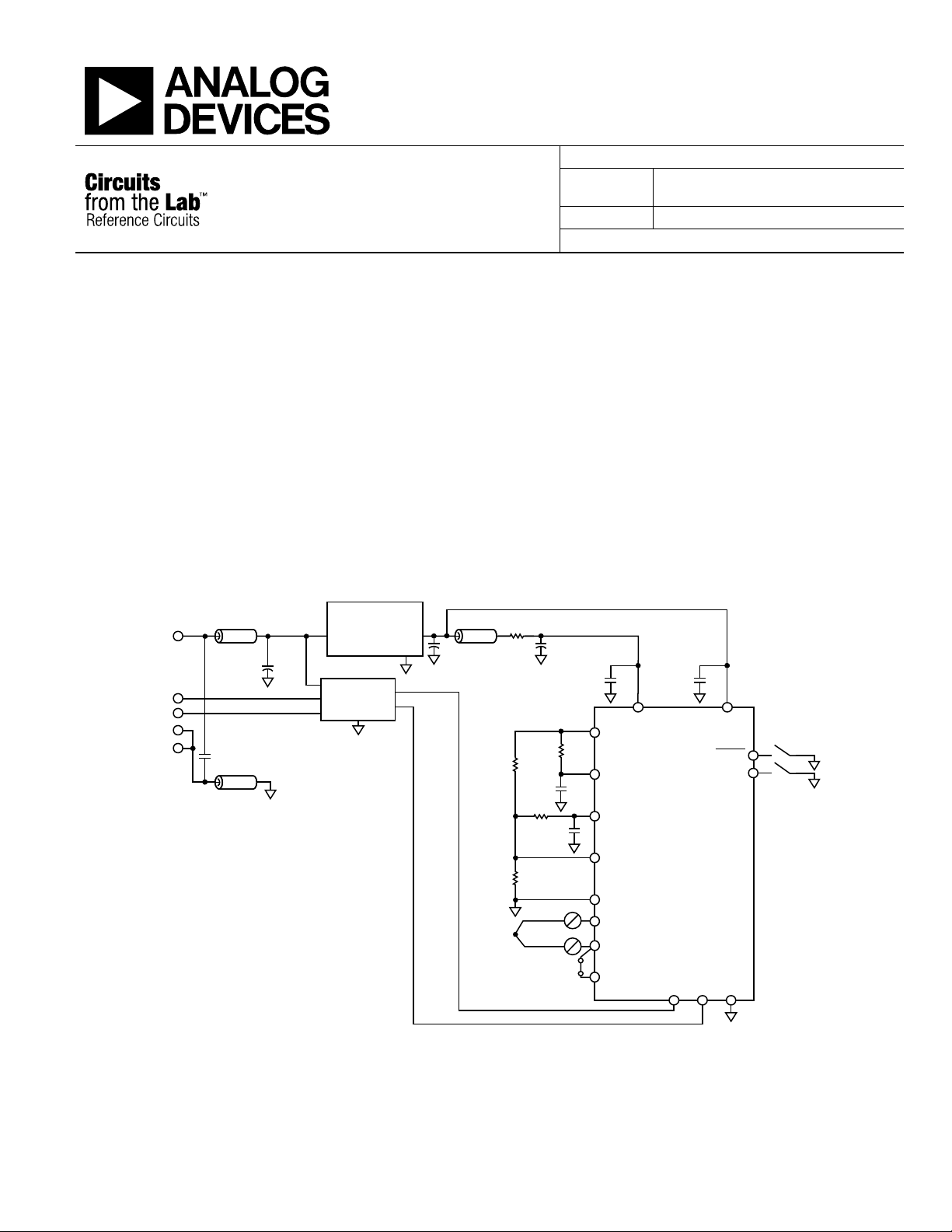
Rev. 0
Circuits from the Lab™ circuits from Analog Devices have been designed and built by Analog Devices
each circuit, and their function and performance have been tested and verified in a lab environment at
room temperature. However, you are solely responsible for testing the circuit and determining its
r your use and application. Accordingly, in no event shall Analog Devices
be liable for direct, indirect, special, incidental, consequential or punitive damages due to any cause
whatsoever connected to the use of any Circuits from the Lab circuits. (Continued on last page)
Fax: 781.461.3113 ©2012 Analog Devices, Inc. All rights reserved.
ADuCM360
AIN5/IEXC
AVDD IOVDD
AIN0
RxD
RxD
TxD
TxD
RESET
P2.2/BM
RESET
SD
V
REF
+
R
REF
V
REF
–
AIN1
5.6k
Ω
0.1%
100
Ω
PtRTD
AIN2
THERMOCOUPLE
JUNCTION
AIN3
J1
AIN7/VBIAS
AGND
09985-001
BEAD
3.3V
BEAD
USB HEADER
10Ω
10Ω
10Ω
0.01µF
0.01µF
0.1µF
4.7µF
4.7µF
0.1µF
10µF
IN
5V
D–
D+
GND
OUT
GND
ADP1720-3.3
FT232R
BEAD
FERRITE BE ADS :
1kΩ @ 100MHz
TAIYO Y UDE N
BK2125HS102-T
0.1µF
SHIELD
P0.2/SOUT
P0.1/SIN
Circuits from the Lab™ reference circuits are engineered and
tested for quick and easy system integration to help solve today’s
analog, mixed-signal, and RF design challenges. For more
information and/or support, visit www.analog.com/CN0221.
USB-Based Temperature Monitor Using the ADuCM360 Precision Analog
Microcontroller and an External Thermocouple
EVALUATION AND DESIGN SUPPORT
Circuit Evaluation Board
CN-0221 Evaluation Board (EVAL-ADuCM360TCZ)
Design and Integration Files
Schematics, Layout Files, Bill of Materials, source code for
ADuCM360
CIRCUIT FUNCTION AND BENEFITS
This circuit uses the ADuCM360/ADuCM361 precision analog
microcontroller in an accurate thermocouple temperature
monitoring application. The ADuCM360/ADuCM361 integrates
dual 24-bit sigma-delta (Σ-Δ) analog-to-digital converters (ADCs),
dual programmable current sources, a 12-bit digital-to-analog
Circuit Note
Devices Connected/Referenced
ADuCM360/
ADuCM361
ADP1720-3.3 Low Dropout Linear Regulator
converter (DAC), and a 1.2 V internal reference, as well as an ARM
Cortex-M3 core, 126 kB flash, 8 kB SRAM, and various digital
peripherals such as UART, timers, SPIs, and I
In the circuit, the ADuCM360/ADuCM361 is connected to a
thermocouple and a 100 Ω platinum resistance temperature
detector (RTD). The RTD is used for cold junction compensation.
In the source code, an ADC sampling rate of 4 Hz is chosen. When
the ADC input programmable gain amplifier (PGA) is configured
for a gain of 32, the noise-free code resolution of the ADuCM360/
ADuCM361 is greater than 18 bits.
Cortex-M3 Based Microcontroller with
Dual 24-Bit Σ-Δ ADCs
2
C interfaces.
Figure 1. ADuCM360/ADuCM361 as a Temperature Monitor Controller with a Thermocouple Interface (Simplified Schematic, All Connections Not Shown)
engineers. Standard engineering practices have been employed in the design and construction of
suitability and applicability fo
One Technology Way, P.O. Box 9106, Norwood, MA 02062-9106, U.S.A.
Tel: 781.329.4700
www.analog.com
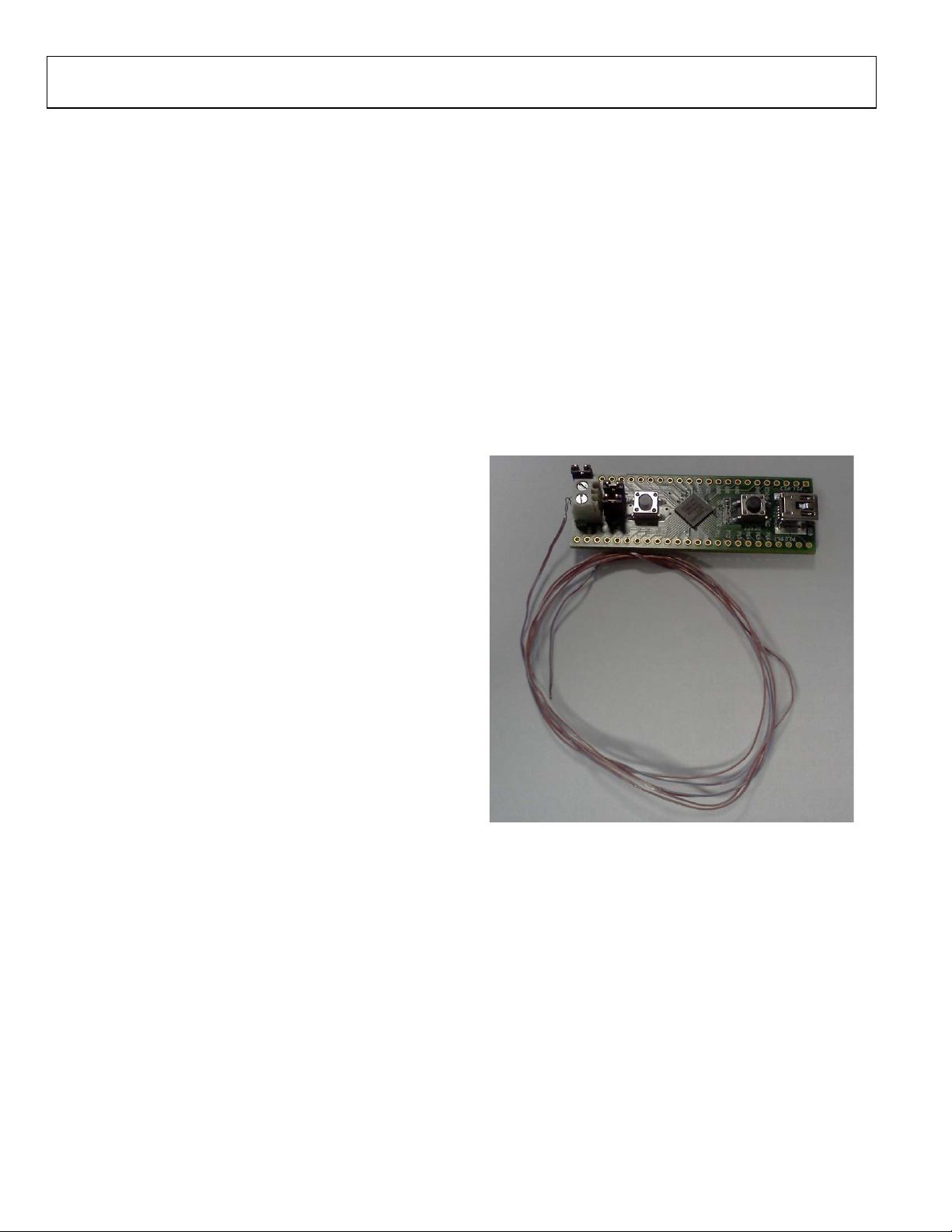
CN-0221 Circuit Note
CIRCUIT DESCRIPTION
The following features of the ADuCM360/ADuCM361 are used
in this application:
• A 24-bit Σ-Δ ADC with a PGA set for a gain of 32 in the
software for the thermocouple and RTD. The ADC1 was
switched continuously between sampling the thermocouple
and the RTD voltages.
• Programmable excitation current sources for forcing a
controlled current through the RTD. The dual current
sources are configurable in from 0 µA to 2 mA. For this
example, a 200 µA setting was used to minimize the error
introduced by the RTD self-heating.
• An internal 1.2 V reference for the ADC in the ADuCM360/
ADuCM361. It measures the thermocouple voltage; the
internal voltage reference was used due to its precision.
• An external voltage reference for the ADC in the
ADuCM360/ADuCM361. It measures the RTD resistance;
a ratiometric setup was used where an external reference
resistor (R
and VREF− pins.
• A bias voltage generator (VBIAS). The VBIAS function was
used to set the thermocouple common-mode voltage to
AVDD/2.
• The ARM Cortex-M3 core. The powerful 32-bit ARM core
with integrated 126 kB flash and 8 kB SRAM memory runs
the user code that configures and controls the ADC, processes
the ADC conversions from the RTD, and controls the
communications over the UART/USB interface.
• The UART was used as the communication interface to the
host PC.
• Two external switches are used to force the part into its
flash boot mode. By holding SD low and toggling the RESET
button, the ADuCM360/ADuCM361 enters boot mode
instead of normal user mode. In boot mode, the internal
flash can be reprogrammed through the UART interface.
Both the thermocouple and the RTD generate very small signals;
therefore, a PGA is required to amplify those signals.
The thermocouple used in this application is a Type T (copperconstantan) that has a temperature range of −200°C to +350°C.
Its sensitivity is approximately 40 µV/°C, which means that the
ADC in bipolar mode, with a PGA gain of 32, can cover the
entire temperature range of the thermocouple.
The RTD was used for cold junction compensation. The
particular one used in this circuit was a platinum 100 Ω RTD,
Enercorp PCS 1.1503.1. It is available in a 0805, surface-mount
package. This RTD has a temperature variation of 0.385 Ω/°C.
) was connected across the external VREF+
REF
Note that the reference resistor, R
5.6 kΩ (±0.1%).
The USB interface to the ADuCM360/ADuCM361 is implemented
with an FT232R UART to USB transceiver, which converts USB
signals directly to the UART.
In addition to the decoupling shown Figure 1, the USB cable itself
must have a ferrite bead for added EMI/RFI protection. The ferrite
beads used in the circuit were Taiyo Yuden, #BK2125HS102-T,
which have an impedance of 1000 Ω at 100 MHz.
Construct the circuit on a multilayer printed circuit board (PCB)
with a large area ground plane. Use proper layout, grounding,
and decoupling techniques to achieve optimum performance (see
Tutorial MT-031, Grounding Data Converters and Solving the
Mystery of "AGND" and "DGND," Tut o r ia l MT-101, Decoupling
Techni q u e s , and the ADuCM360TCZ Evaluation Board layout).
The PCB used for evaluating this circuit is shown in Figure 2.
Figure 2. EVAL-ADuCM360TCZ Board Used for this Circuit
, should be a precision
REF
Rev. 0 | Page 2 of 5