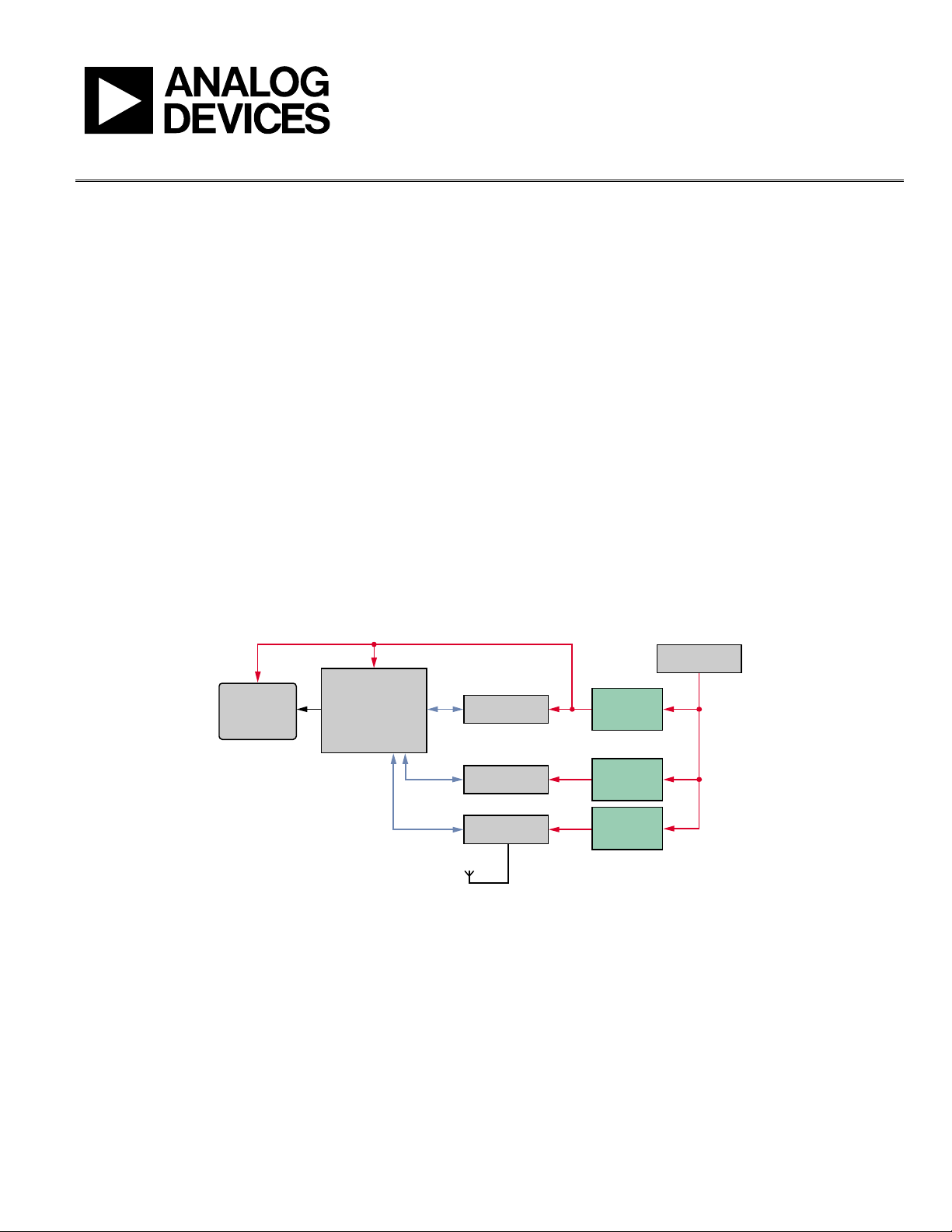
AN-1149
MEMORY
V
DD
MICROPROCESSOR
LCD DISPLAY
BUCK
REGULATOR
ADP2139
SENSOR
BATTERY
Li-Ion
1.8V
3.6V
3.3V
RF PA
BUCK-BOOST
REGULATOR
ADP2503
BUCK-BOOST
REGULATOR
ADP2504
3.0V TO 4.2V
10542-001
One Technology Way • P. O. Box 9106 • Norwood, MA 02062-9106, U.S.A. • Tel: 781.329.4700 • Fax: 781.461.3113 • www.analog.com
How to Apply DC-to-DC Step-Down/Step-Up (Buck/Boost) Regulators
by Ken Marasco
INTRODUCTION
DC-to-DC switching converters are used to change one dc
voltage to another efficiently. High efficiency dc-to-dc
converters come in three basic topologies: step-down (buck),
step-up (boost), and step-down/step-up (buck/boost).
The buck converter is used to generate a lower dc output
voltage, the boost converter is used to generate a higher dc
output voltage, and the buck/boost converter is used to generate
an output voltage less than, greater than, or equal to the input
voltage.
This application note focuses on how to successfully apply
buck/boost dc-to-dc converters. Buck and boost converters are
described individually in the AN-1125 Application Note, How
to Apply DC-to-DC Step-Down (Buck) Regulators, and the
AN-1132 Application Note, How to Apply DC-to-DC Step-Up
(Boost) Regulators.
Figure 1 shows a typical low power system powered from a
single-cell lithium ion (Li-Ion) battery. The battery’s usable
output varies from about 3.0 V when discharged to 4.2 V when
fully charged. The system ICs require 1.8 V, 3.3 V, and 3.6 V for
optimum operation. Whereas the lithium ion battery starts at
4.2 V and ends at 3.0 V, a buck/boost regulator can supply a
constant 3.3 V, and a buck regulator or low dropout (LDO)
regulator can supply 1.8 V, as the battery discharges. A buck
regulator or LDO can conceivably be used for the 3.3 V while
the battery voltage is above 3.5 V, but the system would cease to
operate when the battery voltage drops below 3.5 V. Allowing
the system to be turned off prematurely reduces the system’s
operating time before the battery must be recharged.
Figure 1. Typical Low Power Portable System
Rev. 0 | Page 1 of 8
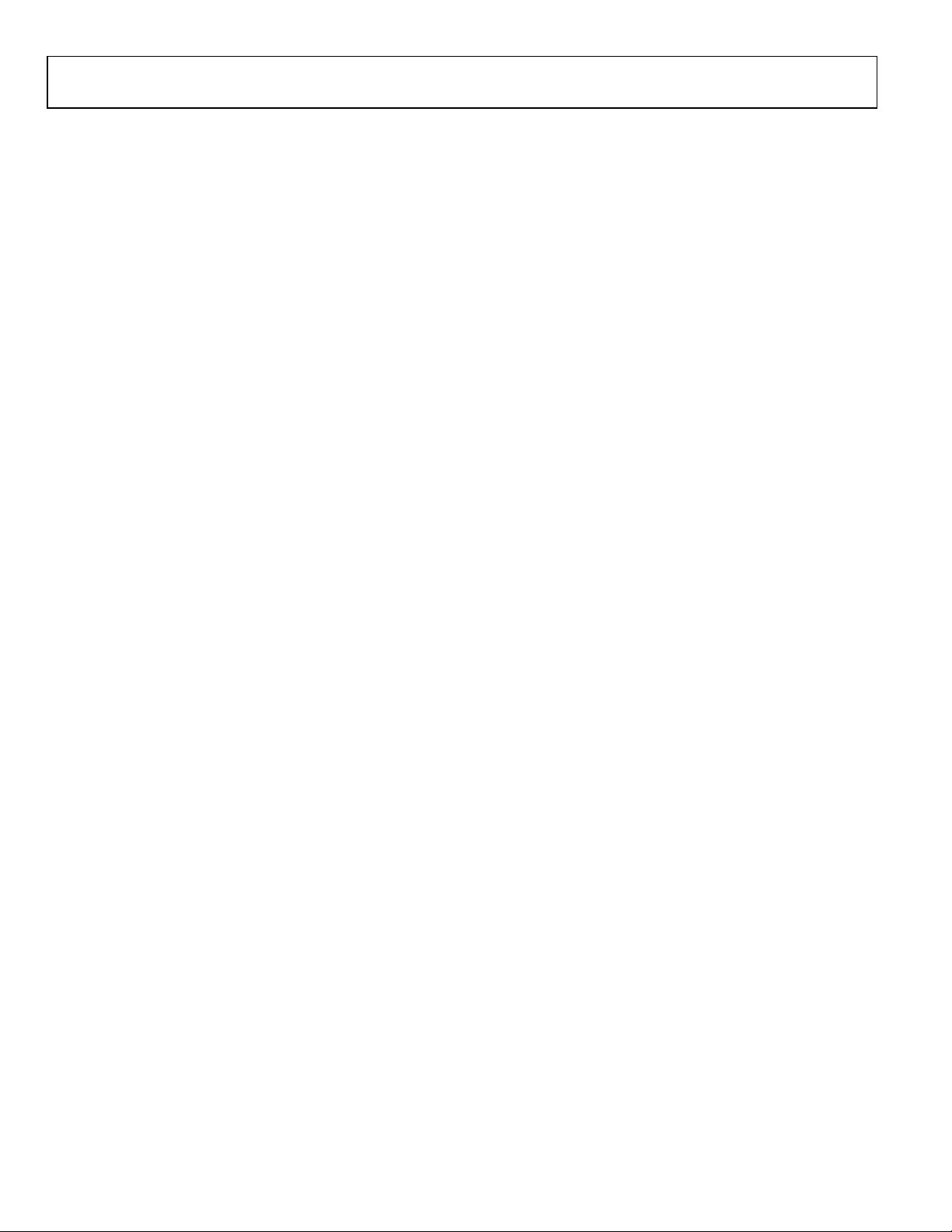
AN-1149 Application Note
TABLE OF CONTENTS
Introduction ...................................................................................... 1
Revision History ............................................................................... 2
Buck/Boost Regulators ..................................................................... 3
Buck/Boost Regulators Improve System Efficiency ..................... 5
Buck/Boost Regulator Key Specifications and Definitions ......... 6
Output Voltage Range Options ................................................... 6
Ground or Quiescent Current .................................................... 6
Shutdown Current ........................................................................ 6
REVISION HISTORY
4/12—Revision 0: Initial Version
Soft Start .........................................................................................6
Switching Frequency .....................................................................6
Thermal Shutdown (TSD) ...........................................................6
Buck/Boost DC-to-DC Switching Converters Operate at
MHz ................................................................................................7
Conclusion..........................................................................................8
References .......................................................................................8
Rev. 0 | Page 2 of 8
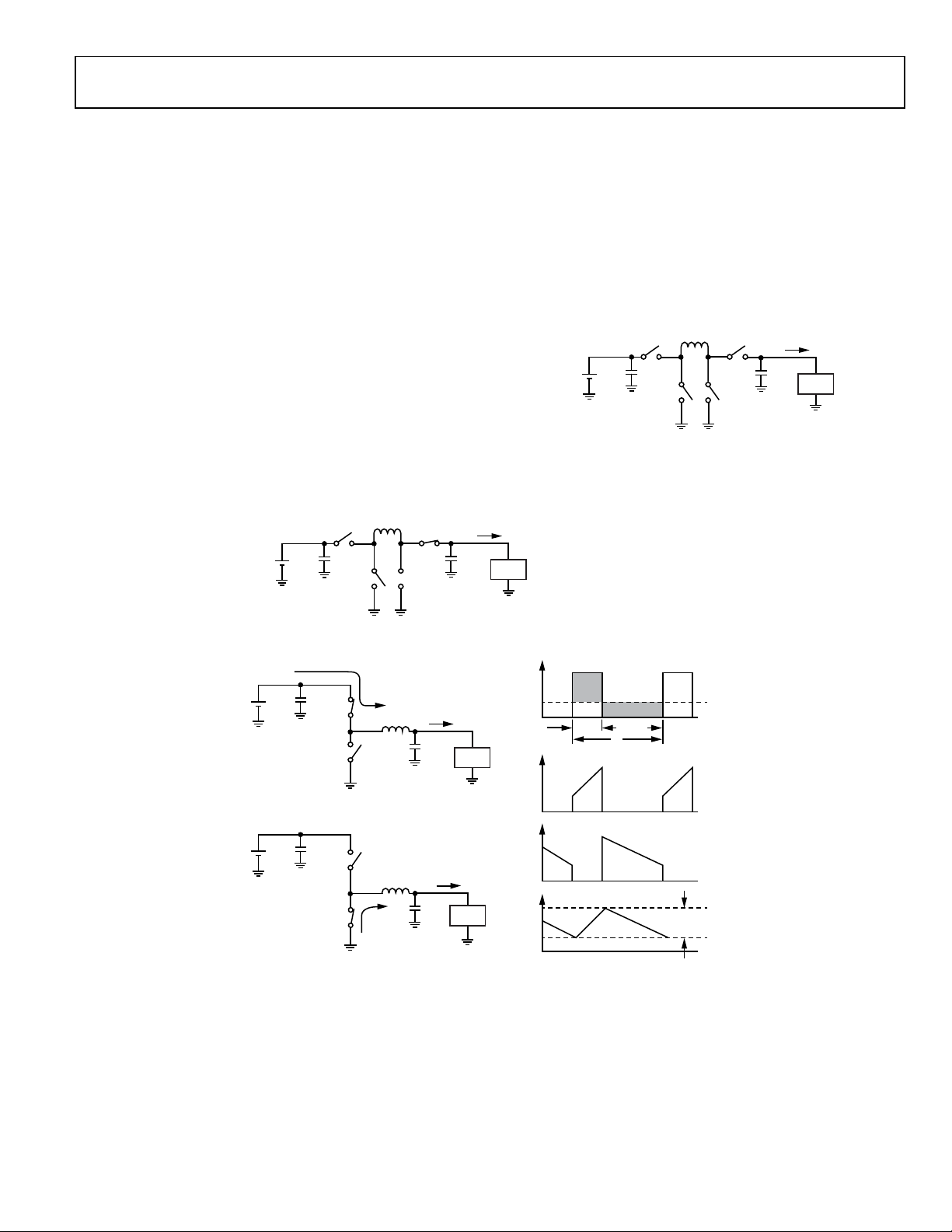
Application Note AN-1149
BUCK/BOOST REGULATORS
Buck/boost regulators contain four switches, two capacitors,
and an inductor, as shown in Figure 2. Current low power, high
efficiency buck/boost regulators reduce losses and improve
efficiency by actively operating only two of the four switches
when operating in buck or boost mode.
When V
is greater than V
IN
, Switch C is open and Switch D
OUT
is closed. Switch A and Switch B operate as in a standard buck
regulator, as shown in Figure 3.
When V
is less than V
IN
, Switch B is open and Switch A is
OUT
closed. Switch C and Switch D operate as in a boost regulator,
as shown in Figure 4. The most difficult operating mode is
when V
is in the range of V
IN
± 10% and the regulator enters
OUT
the buck/boost mode. In buck/boost mode, the two operations,
buck and boost, take place during a switching cycle. Care must
be taken to reduce losses, optimize efficiency, and eliminate
instability due to mode switching. The objective is to maintain
voltage regulation with minimal current ripple in the inductor
to guarantee good transient performance.
L
+
V
IN
–
A
C
IN
BC
D
I
C
OUT
At high load currents, the buck/boost uses voltage or currentmode, fixed frequency pulse-width modulation (PWM) control
for optimal stability and transient response. To ensure the
longest battery life in portable applications, a power save mode
reduces the switching frequency under light load conditions.
For wireless and other low noise applications where variablefrequency power save mode may cause interference, the
addition of a logic control input to force fixed frequency PWM
operation under all load conditions is included.
L
+
IN
–
A
C
IN
BC
Figure 2. Buck/Boost Converter Topology
I
LOAD
D
C
OUT
LOAD
V
OUT
LOAD
LOAD
V
OUT
10542-002
IN BUCK MODE SWITCH C IS O PEN AND SWIT CH D IS CLOSED.
I
+
IN
–
TYPICAL BUCK
OPERATION
+
IN
–
C
IN
PWM ON
C
IN
PWM OFF
A
A
V
SW
B
A
V
SW
B
I
B
I
LOAD
L
C
I
L
C
OUT
LOAD
OUT
LOAD
LOAD
V
OUT
V
OUT
Figure 3. Buck Mode When V
V
I
LOAD
PWM
OUT
MODULATIO N
t
OFF
T
∆I
LOAD
V
OUT
10542-003
SW
t
ON
I
A
I
B
> V
IN
Rev. 0 | Page 3 of 8