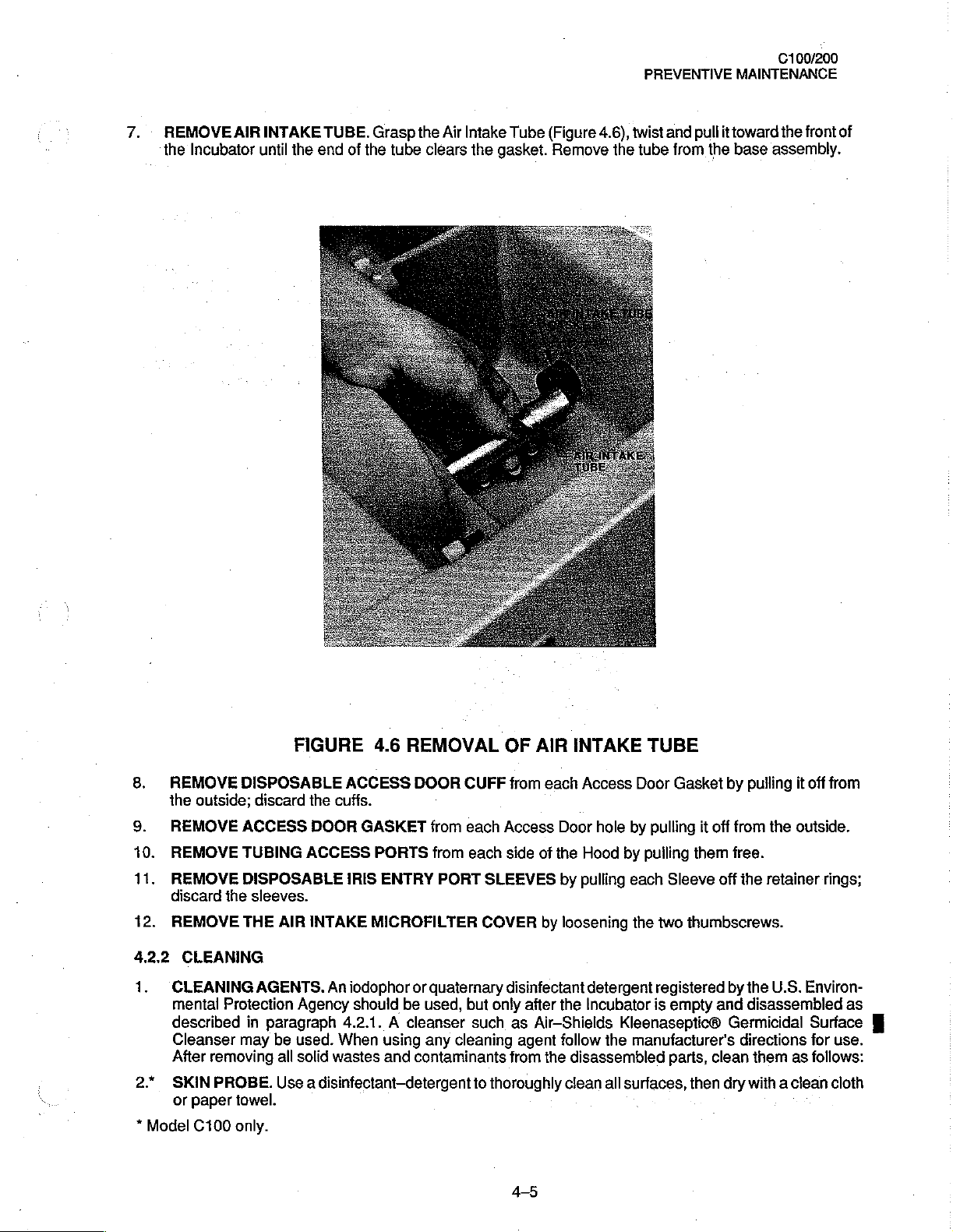
7.
REMOVEAIRINTAKE
the
Incubator
until
the
TUBE.
end
of
Grasp
the
tube
the
Air
clears
Intake
the
gasket.
Tube
(Figure
Remove
4.6),
twist
the
PREVENTIVE
and
pull
tube
from
MAINTENANCE
it
toward
the
base
C100/200
the
front
assembly.
of
8.
9.
10.
11.
12.
4.2.2
1.
2.*
*
Model
REMOVE
the
outside;
REMOVE
REMOVE
REMOVE
discard
REMOVE
CLEANING
mental
described
Cleanser
After
SKIN
or
the
CLEANING
Protection
removing
PROBE.
paper
C100
FIGURE
DISPOSABLE
discard
ACCESS
TUBING
DISPOSABLE
sleeves.
THE
AGENTS.
in
may
towel.
only.
the
DOOR
ACCESS
AIR
INTAKE
Agency
paragraph
be
used.
all
solid
Use a disinfectant—detergent
4.6
ACCESS
cuffs.
GASKET
PORTS
IRIS
ENTRY
MICROFILTER
An
iodophor
should
4.2.1. A cleanser
When
using
wastes
and
REMOVAL
DOOR
or
be
contaminants
CUFF
from
each
from
each
PORT
COVER
quaternary
used,
but
such
any
cleaning
to
OF
AIR
from
each
Access
side
of
SLEEVES
by
disinfectant
only
after
as
Air-Shields
agent
from
the
thoroughly
45
INTAKE
Access
Door
hole
by
the
Hood
by
by
pulling
loosening
the
follow
disassembled
clean
each
detergent
Incubator
Kleenaseptic®
the
all
surfaces,
TUBE
Door
Gasket
pulling
pulling
Sleeve
the
two
registered
is
empty
manufacturer's
parts,
by
it
off
from
them
free.
off
thumbscrews.
by
and
Germicidal
clean
then
dry
pulling
the
the
disassembled
directions
with a clean
the
retainer
U.S.
them
as
it
off
outside.
Environ-
Surface
for
follows:
from
rings;
as
use.
cloth
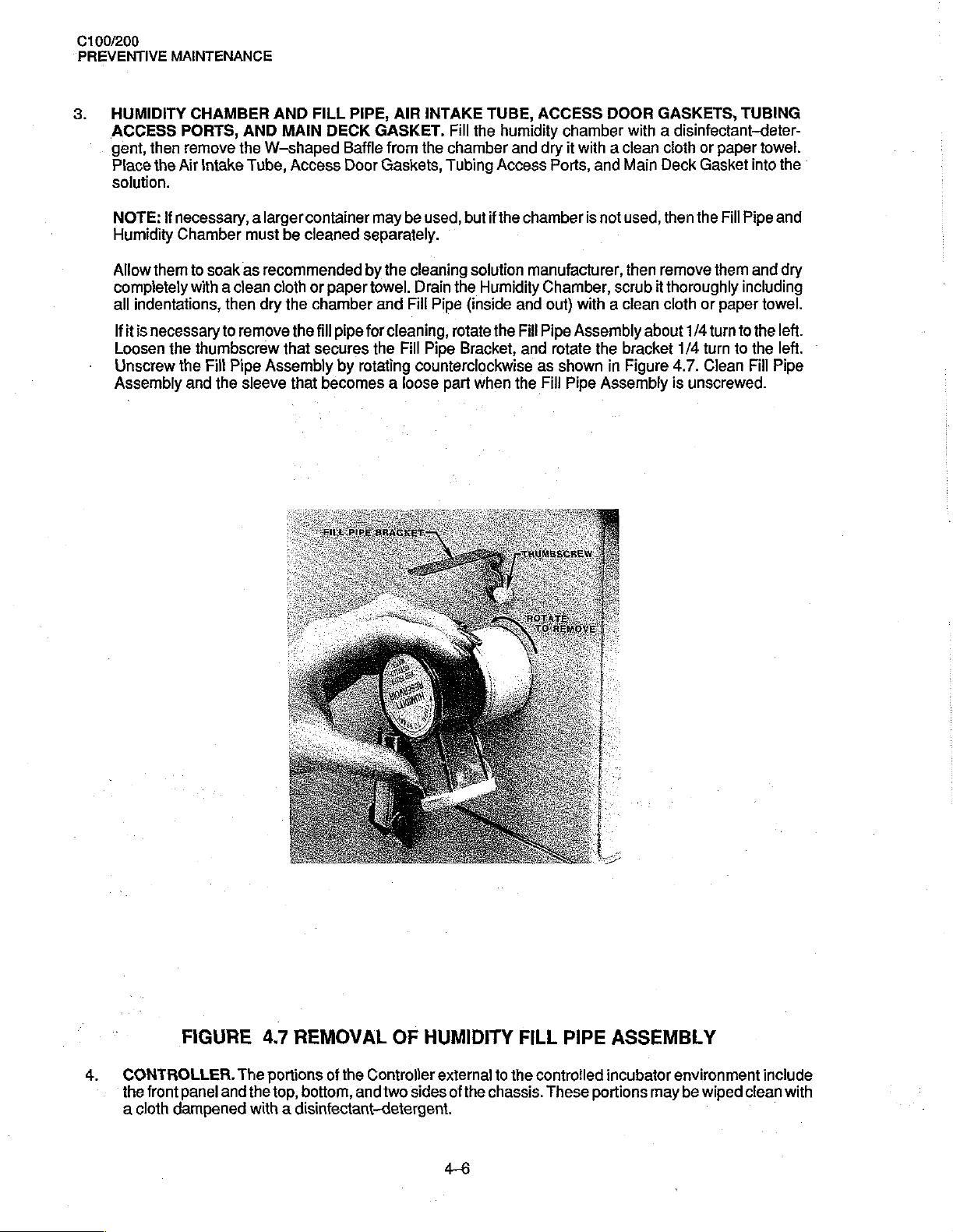
100/200
PREVENTIVE
3.
HUMIDITY
ACCESS
gent,
Place
solution.
MAINTENANCE
CHAMBER
PORTS,
then
remove
the
Air
AND
the
Intake
AND
MAIN
W-shaped
Tube,
FILL
DECK
Access
PIPE,
AIR
GASKET.
Baffle
from
Door
Gaskets, Tubing
INTAKE
Fill
the
chamber
TUBE,
the
humidity
Access
and
ACCESS
chamber
dry
it
with a clean
Ports,
DOOR
and
GASKETS,
with a disinfectant-deter-
cloth
Main
Deck
TUBING
or
paper
Gasket
towel.
into
the
*
NOTE:
Humidity
Allow
completely
all
Ifit
Loosen
Unscrew
Assembly
if
necessary, a larger
Chamber
them
indentations,
is
necessary
the
the
and
must
to
soak
as
recommended
with a clean
then
dry the
to
remove
thumbscrew
Fill
Pipe
Assembly
the
sleeve
container
be
cleaned
cloth
the
that
that
may
be
separately.
by
the
cleaning
or
paper
towel.
chamber
fill
secures
becomes a loose
pipe
for
by
rotating
and
Fill
cleaning,
the
Fill
used,
but
if
the
chamber
solution
Drain
the
Humidity
Pipe
(inside
rotate
Pipe
Bracket,
counterclockwise
part
when
manufacturer,
and
the
Fill
and
the
is
Chamber,
out)
with a clean
Pipe
Assembly
rotate
as
shown
Fill
Pipe
not
used,
then
scrub
about
the
bracket
in
Figure
Assembly
then
the
remove
it
thoroughly
cloth
them
or
1/4
turn
1/4
turn
4.7.
Clean
is
unscrewed.
Fill
Pipe
and
including
paper
to
the
to
the
Fill
and
dry
towel.
left.
left.
Pipe
-
4.
CONTROLLER.
the
a
front
cloth
FIGURE
panel
and
dampened
4.7
REMOVAL
The
portions
the
top,
with a disinfectant-detergent.
of
the
bottom, and
OF
HUMIDITY
Controller
two
external
sides
46
of
to
the
chassis.
FILL
the
controlled
These
PIPE
portions
ASSEMBLY
incubator
environment
may
be
wiped
include
clean
with
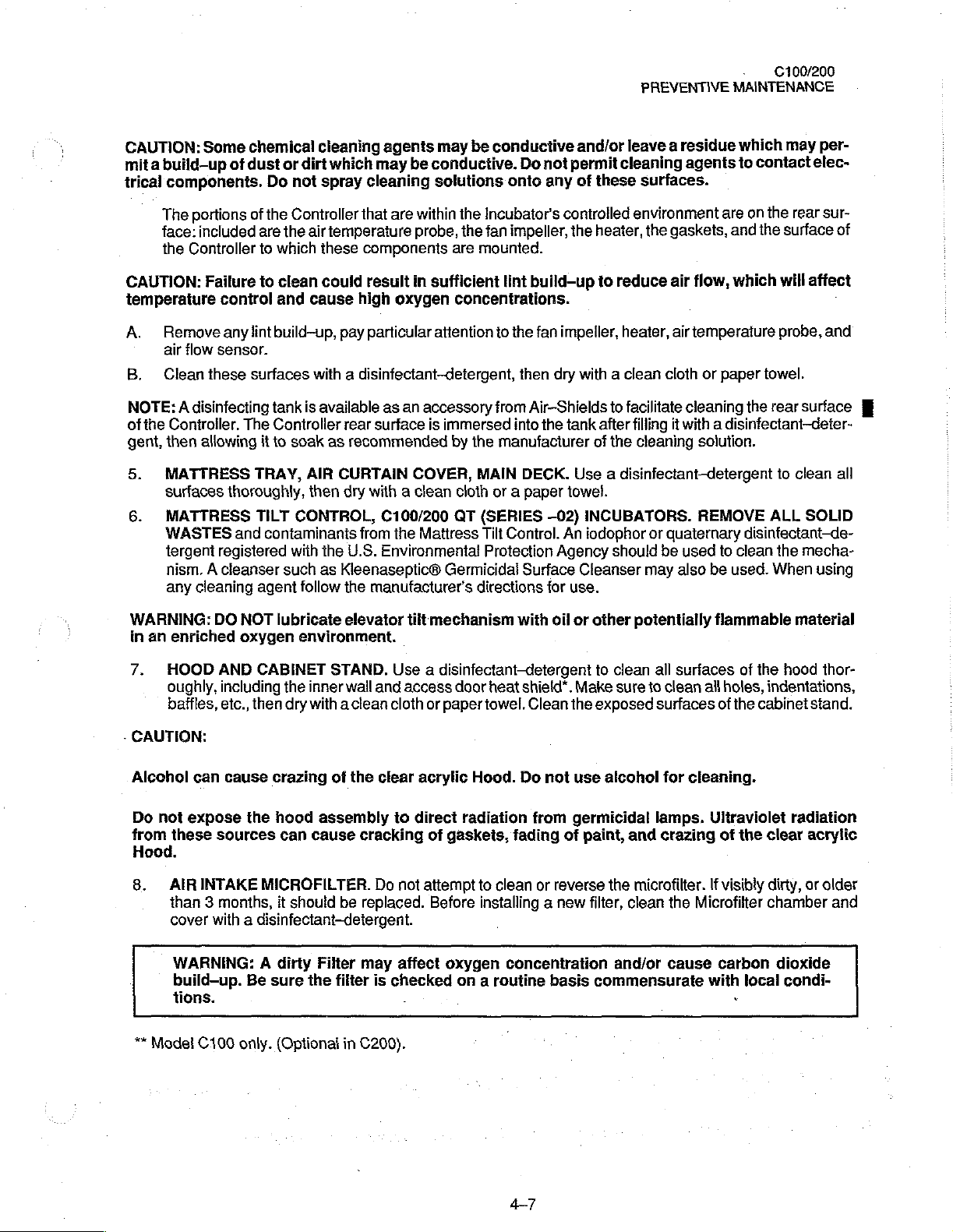
PREVENTIVE
-
C100/200
MAINTENANCE
CAUTION:
mita
trical
CAUTION:
temperature
A.
B.
NOTE: A disinfecting
ofthe
gent,
5.
6.
Some
chemical
build-up
components.
The
face:
the
Remove
air
Clean
Controller.
then
MATTRESS
surfaces
MATTRESS
WASTES
tergent
nism. A cleanser
any
of
dust
portions
included
Controller
flow
allowing
cleaning
of
Failure
control
any
lint
sensor.
these
surfaces
The
thoroughly,
and
registered
are the
to
to
it
TRAY,
TILT
agent
cleaning
or
dirt
which
Do
not
spray
the
Controller
air
temperature
which
these
clean
could
and
cause
build-up,
tank
Controller
to
soak
pay
with a disinfectant-detergent,
is
available
rear
as
recommended
AIR
CURTAIN
then
dry
CONTROL,
contaminants
with
the
U.S.
such
as
Kleenaseptic®
follow
the
agents
may
cleaning
that
are
components
result
high
particular
as
surface
with a clean
may
be
conductive.
solutions
within
probe,
in
sufficient
oxygen
attention
an
accessory
is
COVER,
immersed
C100/200
from
the
Mattress
Environmental
Germicidal
manufacturer's
be
conductive
Do
not
onto
any
the
Incubator's
the fan
are
concentrations.
by
cloth
QT
impeller,
mounted.
lint
build-up
to
the
fan
then
from
Air-Shields
into
the
manufacturer
MAIN
DECK.
or a paper
(SERIES
Tilt
Control.
Protection
Surface
directions
impeller,
dry
the
—02)
Agency
for
and/or
permit
of
controlled
the
with a clean
tank
Use a disinfectant-detergent
towel.
An
Cleanser
use.
leave a residue
cleaning
these
surfaces.
environment
heater,
to
after
of
the
reduce
heater,
cloth
to
facilitate
filling
the
cleaning
gaskets,
air
air
it
INCUBATORS.
iodophor
or
should
may
quaternary
be
which
agents
cleaning
with a disinfectant-deter-
to
are
and
flow,
which
temperature
or
paper
solution.
REMOVE
disinfectant-de-
used
to
clean
also
be
used.
may
contact
on
the
the
surface
will
probe,
towel.
the
rear
to
ALL
the
When
per-
elec-
rear sur-
of
affect
and
surface
clean
all
SOLID
mecha-
using
WARNING:
in
an
7.
-
CAUTION:
Alcohol
Do
not
from
Hood.
8.
**
Model
DO
NOT
lubricate
enriched
HOOD
oughly,
baffles,
expose
these
AIR
than 3 months,
cover
WARNING:
build-up.
tions.
oxygen
AND
including
etc.,
then
can
cause
the
sources
INTAKE
with a disinfectant-detergent.
Be
C100
only.
environment.
CABINET
crazing
hood
can
MICROFILTER.
it
A
dirty
sure
(Optional
STAND.
the
inner
dry
with a clean
of
assembly
cause
should
Filter
the
filter
be
elevator
Use a disinfectant-detergent
wall
and
cloth
the
clear
to
cracking
Do
not
replaced.
may
affect
is
checked
in
C200).
tilt
mechanism
access
or
paper
acrylic
direct
of
attempt
Before
oxygen
.
with
door
heat
shield*.
towel.
Hood.
radiation
gaskets,
on a routine
Do
fading
to
clean
installing a new
concentration
oil
Clean
not
from
or
reverse
basis
or
other
to
clean
Make
sure
the
exposed
use
alcohol
germicidal
of
paint,
and
the
filter,
clean
and/or
commensurate
potentially
all
to
clean
surfaces
for
lamps.
crazing
microfilter.
cause carbon
flammable
surfaces
all
of
cleaning.
Ultraviolet
of
If
visibly
the
Microfilter
with
of
the
holes,
indentations,
the
cabinet
the
clear
dirty,
chamber
dioxide
local
material
hood
thor-
stand.
radiation
acrylic
or
older
and
condi-
4-7
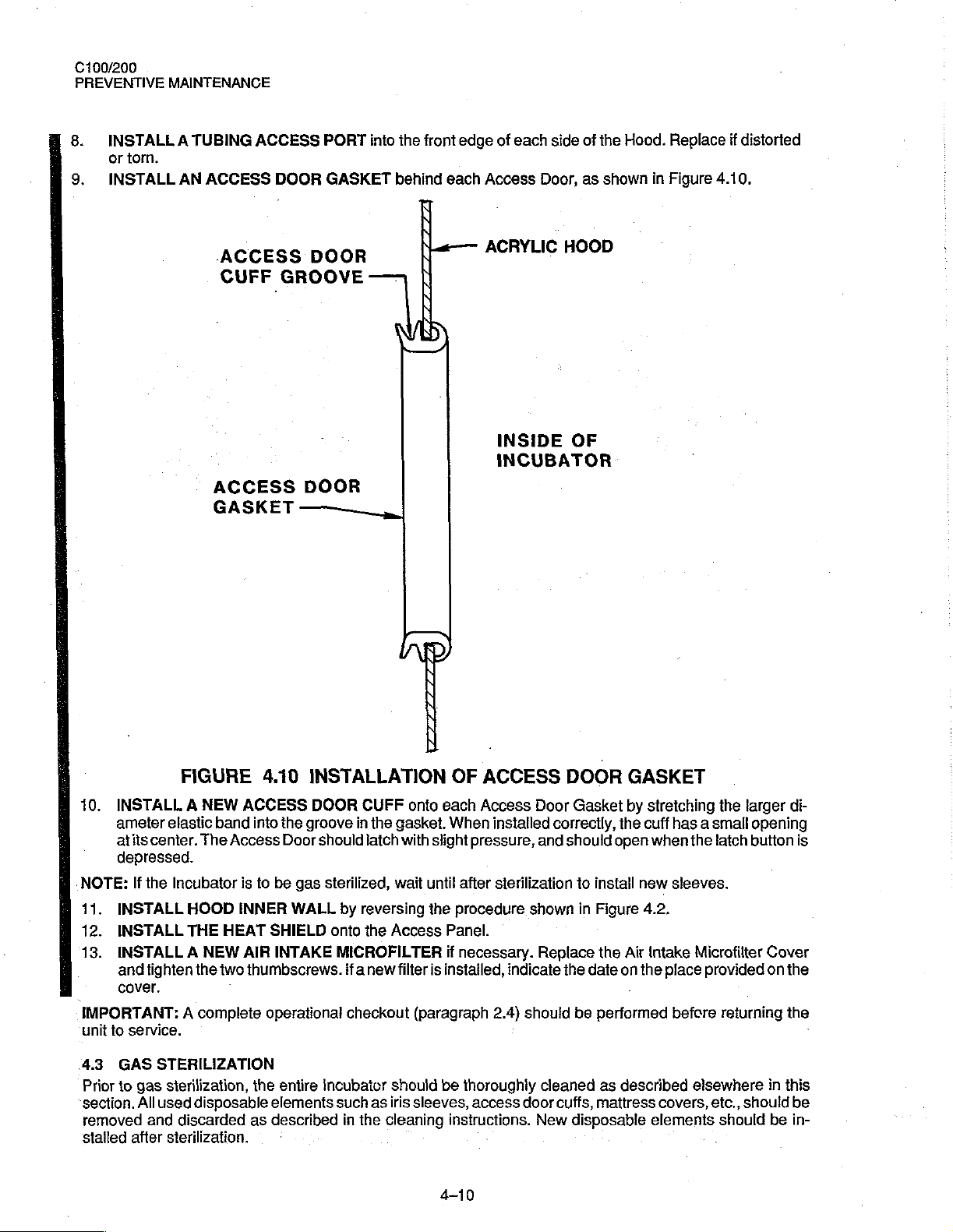
C100/200
PREVENTIVE
8.
INSTALL A TUBING
or
torn.
9.
INSTALL
MAINTENANCE
AN
ACCESS
ACCESS
DOOR
PORT
GASKET
into
behind
the
front
each
edge
Access
of
each
side
Door,
of
as
the
Hood.
shown
Replace
in
Figure
if
distorted
4.10.
ACCESS
CUFF
GROOVE
ACCESS
GASKET
DOOR
DOOR
——
„|
a
ACRYLIC
É
INSIDE
INCUBATOR
HOOD
OF
FIGURE
10.
INSTALL A NEW
ameter
atits
depressed.
NOTE:
11.
INSTALL
12.
INSTALL
13.
INSTALL A NEW
and
elastic
center.
If
the
tighten
Incubator
HOOD
THE
the
cover.
IMPORTANT: A complete
unit
to
service.
、4.3
GAS
STERILIZATION
Prior
to
gas
sterilization,
section.
removed
stalled
All
used
disposable
and
discarded
after
sterilization.
The
ACCESS
band
Access
is
INNER
HEAT
AIR
two
4.10
INSTALLATION
DOOR
into
the
groove
Door
should
to
be
gas
sterilized,
WALL
SHIELD
INTAKE
thumbscrews.
operational
the
entire
elements
as
described
onto
incubator
CUFF
onto
in
the
gasket,
latch
with
wait
by
reversing
the
Access
MICROFILTER
ifa
new
filter
checkout
such
in
the
(paragraph
should
as
iris
sleeves,
cleaning
OF
ACCESS
each
Access
When
installed
slight
pressure,
until
after
sterilization
the
procedure
Panel.
if
necessary.
is
instatled,
2.4)
be
thoroughly
access
instructions.
4-10
Door
correctly,
and
shown
Replace
indicate
:
should
cleaned
door
cuffs,
New
the
DOOR
Gasket
should
to
in
be
disposable
GASKET
by
the
open
install
Figure
the
Air
date
on
performed
as
described
mattress
stretching
cuff
has a small
when
the
new
sleeves.
4.2,
Intake
Microfilter
the
place
provided
before
elsewhere
covers,
elements
the
larger
opening
latch
button
returning
etc.,
shouldbe
should
di-
is
Cover
on
the
the
in
this
be
in-
・
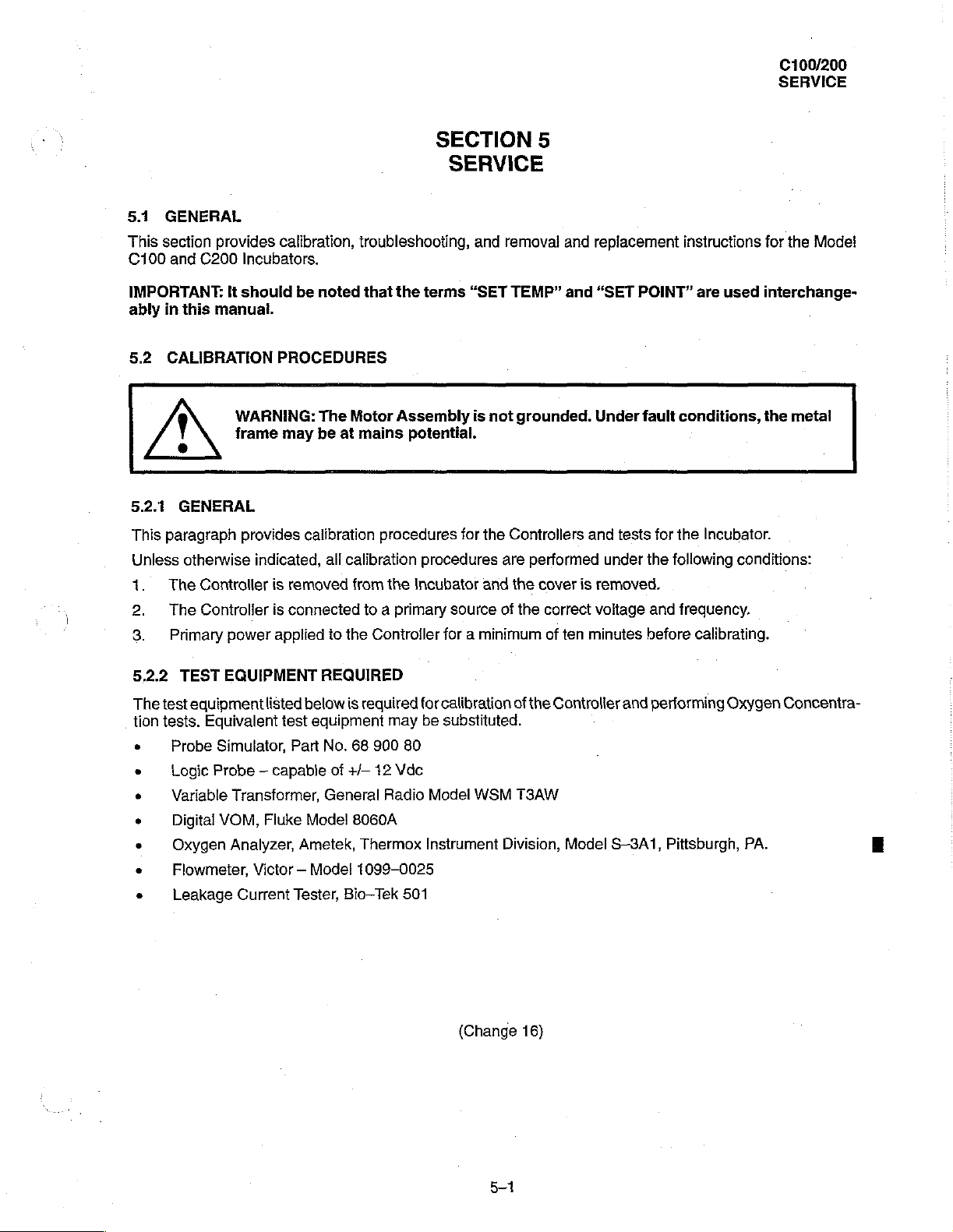
C100/200
SERVICE
5.1
GENERAL
This
section
C100
and
IMPORTANT:
ably
in
this
5.2
CALIBRATION
5.2.1
This
paragraph
Unless
1.
The
2.
The
3.
Primary
GENERAL
otherwise
provides
C200
Incubators.
It
should
manual.
WARNING:
frame
provides
indicated,
Gontroller
Controller
is
is
power
calibration,
be
noted
PROCEDURES
The Motor
may
be
at
calibration
all
calibration
removed
connected
applied
to
from
the
SECTION
SERVICE
troubleshooting,
that
the
terms
Assembly
mains
potential.
procedures
procedures
the
Incubator
to a primary
Controller
and
"SET
is
for
source
for a minimum
5
removal
TEMP”
not
grounded.
the
Controllers and
are
performed
and
the
cover
of
the
correct
of
and
replacement
and
“SET
Under
under
is
removed.
voltage and
ten
minutes
POINT"
fault
tests
the
before
instructions
are
conditions,
for
the
Incubator.
following
frequency.
calibrating.
for
the
used
interchange-
the
metal
conditions:
Model
5.2.2
The
test
tion
tests.
.
ㆍ
ο
.
ㆍ
.
.
TEST
EQUIPMENT
equipment
Equivalent
Probe
Simulator,
Logic
Probe — capable
Variable
Digital
Oxygen
Flowmeter,
Leakage
Transformer,
VOM,
Analyzer,
Current
REQUIRED
listed
below
test
equipment
Part
No.
of
General
Fluke
Model
Ametek,
Victor — Model
Tester,
Bio—Tek
is
required
may
68
900
+/—
12
Vdc
Radio
8060A
Thermox
1099-0025
for
calibration
be
substituted.
80
Model
Instrument
501
of
WSM
Division,
(Change
the
Controller
T3AW
16)
Model
and
performing
S-3A1,
Oxygen
Pittsburgh,
PA.
Concentra-
5-1
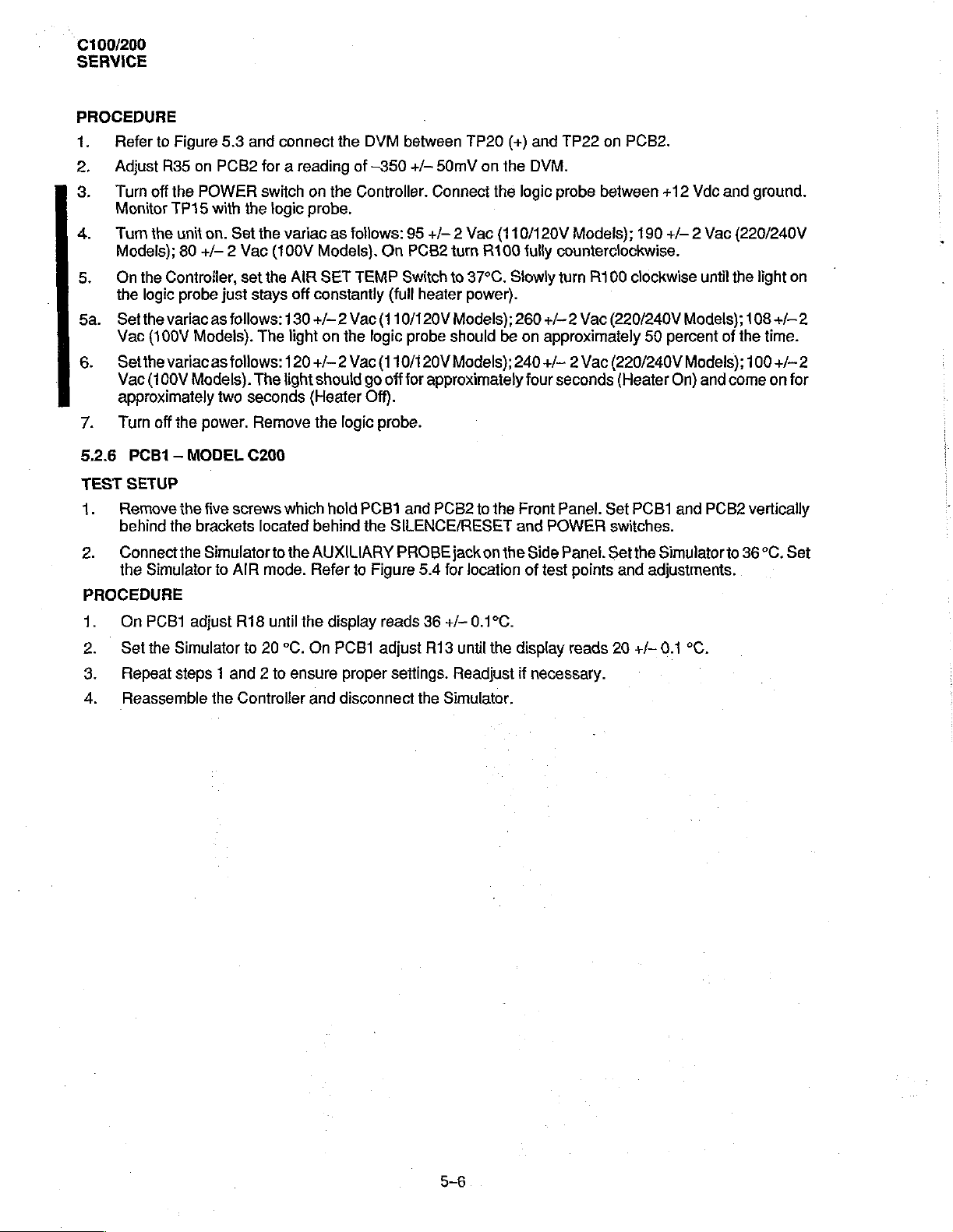
100/200
SERVICE
PROCEDURE
1.
Refer
2.
Adjust
3.
Turn
Monitor
4.
Turnthe
Models);
5.
Onthe
the
5a.
Setthe
Vac
6.
Setthevariacas
Vac
approximately
7.
Turn
5.2.6
TEST
1.
2.
PCB1—
SETUP
Remove
behind
Connect
the
PROCEDURE
to
Figure
R35
off
the
TP15
Controller,
logic
variac
(100V Models).
(100V
off
the
Simulator
on
POWER
with
unit
on,
80
+/— 2 Vac
probe
as
Models).
the
power.
MODEL
the
five
brackets
the
Simulator
to
5.3
PCB2
Set
set
just
follows:
follows:
two
screws
AIR
and
connect
for a
reading
switch
the logic
the
variac
(100V
the
AIR
stays
off
130
The
light
120
The
light
seconds
Remove
C200
which
located
to
the
mode.
the
DVM
of
—350
on
the
Controller.
probe.
as
follows:
Models).
SET
TEMP
constantly
+/—2
Vae
on
the
logic
+/-2
Vac
should
(Heater
the
behind
AUXILIARY
Refer
logic
høld
to
go
Off).
PCB1
the
Figure
.
between
+/—
50mV
Connect
95
+/— 2 Vac
On
PCB2
turn
Switch
(full
(110/120V
(110/120V
off for
probe.
SILENCE/RESET
PROBE
to
heater
Models);
probe
should
Models);
approximately
and
PCB2
jack
5.4
for
TP20
(+)
on
the
the
logic
(110/120V
R100
37°C.
Slowly
power).
260
be on
240
to
the
Front
and
on
the
location
and
TP22
on
DVM.
probe
between
Models);
fully
counterclockwise.
turn
R100
+/- 2 Vac
approximately
+/- 2 Vac
four
seconds
Panel.
POWER
Side
Panel.
of
test
(220/240V
(220/240V
Set
switches.
Set
points
(Heater
and
PCB2.
+12
Vde
190
+/— 2 Vac
clockwise
Models);
50
percent
Models);
On)
PCB1
and
the
Simulator
adjustments.
and
uniil
the
of
and
come
PCB2
to
ground.
(220/240V
light
on
108
+/—
2
the
time.
100
+/-
2
on
for
vertically
36
°C.
Set
1.
2.
3.
4
On
PCB1
adjust
Set
the
Simulator
Repeat
Reassemble
steps 1 and 2 to
R18
to
the
Controller
until
20
*C.
the
display
On
ensure
and
reads
PCB1
adjust
proper
disconnect
settings.
36
+/-0.1°C.
R13
until
Readjust
the
Simulator.
the
display
if
reads
necessary.
20
+/-
0.1
°C.
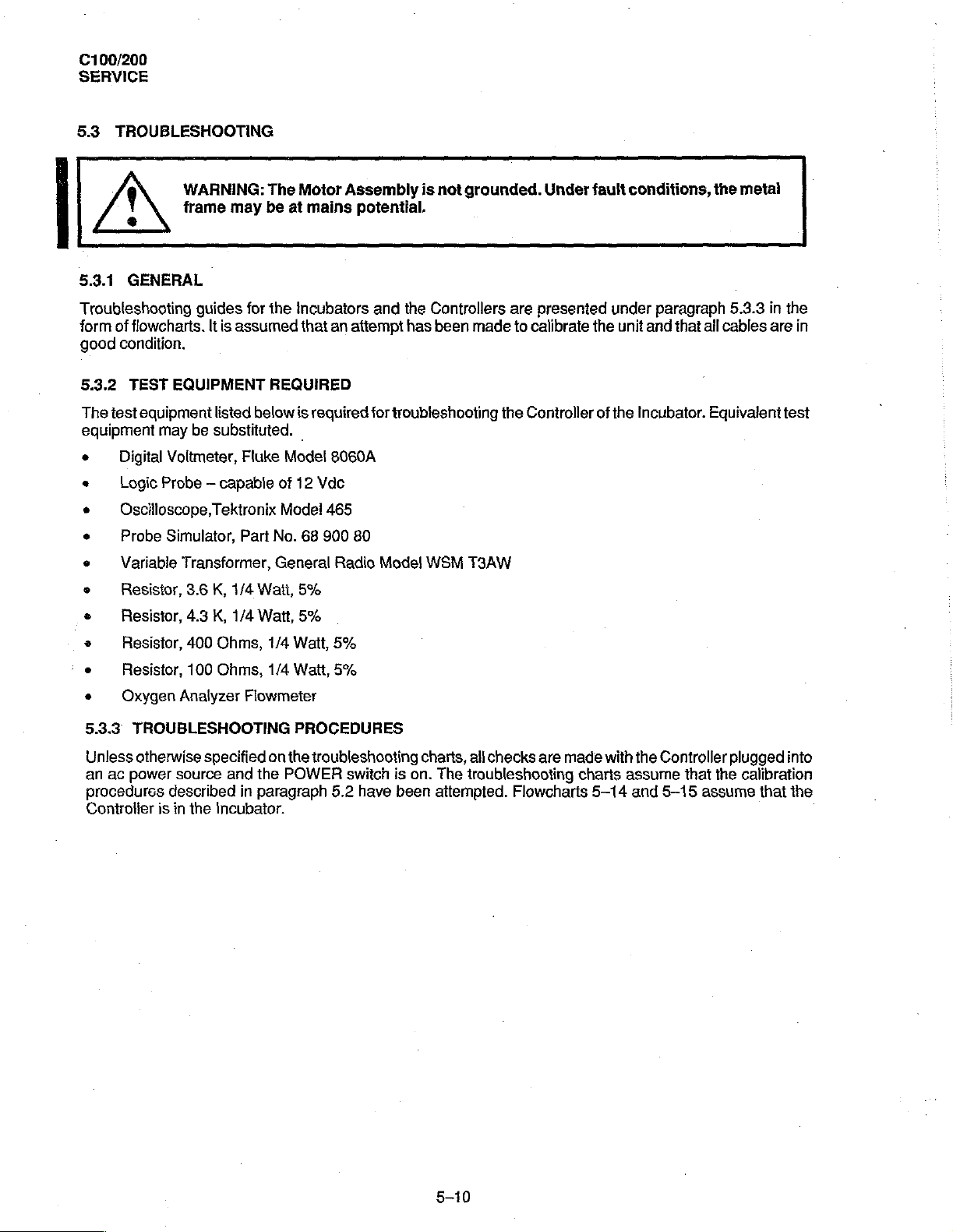
C100/200
SERVICE
5.3
TROUBLESHOOTING
WARNING:
frame
5.3.1
Troubleshooting
form
good
5.3.2
The
equipment
GENERAL
guides
of
flowcharts.
condition.
TEST
EQUIPMENT
test
equipment
may
be
e
Digital
.
‧
+
« © Variable
9
e
Voltmeter,
Logic
Probe — capable
Oscilloscope,Tektronix
Probe
Simulator,
Transformer,
Resistor,
Resistor,
3.6
4.3
The
may
be
at
for
the
lt
is
assumed
REQUIRED
listed
below
substituted.
Fluke
Model
of
Model
Part
No.
General
K,
1/4
Wat,
K,
1/4
Watt,
Motor
Assembly
mains
Incubators
that
is
|
12
68
5%
5%
poteniial.
an
attempt
required
8060A
Vdc
465
900
80
Radio
is
not
and
the
Controllers
has
been
for
troubleshooting
Model
WSM
grounded.
are
made
to
the
Coniroller
T3AW
Under
fault
presented
calibrate
the
conditions,
under
unit
and
of
the
Incubator.
the
paragraph
that
all
Equivalent
metal
5.3.3
cables
in
the
are
test
in
9
Resistor,
ㆍ
Resistor,
9
Oxygen
5.3.3
ап ac
TROUBLESHOOTING
Unless
procedures
Controller
otherwise
power
400
100
Analyzer
specified
source
described
is in
the
Ohms,
Ohms,
Incubator.
1/4
1/4
Flowmeter
on
and
the
in
paragraph
the
POWER
Watt,
5%
Watt,
5%
PROCEDURES
troubleshooting
switch
5.2
have
is
on.
been
charts,
all
checks
The
troubleshooting
attempted.
Flowcharts
are
made
charts
with
5-14
the
Controller
assume
and
5-15
that
assume
plugged
the
calibration
that
into
the
5-10