
INSTALLATION INSTRUCTIONSOWNER’S GUIDE &
Transom or Trolling Motor Mount
CHIRP or Adjustable Wide-beam Transducer
Models: P48W, TM130M, TM150M, TM210H
U.S. Patent 7,961,522. UK 2 414 077. U.S. Patents Pending
Follow the precautions below for optimal
product performance and to reduce the risk of
property damage, personal injury, and/or death.
WARNING: Always wear safety goggles and a dust
17-499-01 rev. 06 01/18/13
mask when installing.
WARNING: When the boat is placed in the water,
immediately check for leaks around the screws and
any other holes drilled in the hull.
CAUTION: P48W—Operate at 200 kHz only.
Operating at any other frequency will permanently
damage the transducer and/or the echosounder.
CAUTION: CHIRP transducer—Always operate the
transducer in water. Operating in air will allow the
transducer to overheat resulting in failure.
CAUTION: Never pull, carry, or hold the transducer by
its cable; this may sever internal connections.
CAUTION: Never strike the transducer with anything
except the palm of the hand to release it.
CAUTION: Never use solvents. Cleaner, fuel, sealant,
paint and other products may contain solvents that can
damage plastic parts, especially the transducer’s face.
Record the information found on the cable tag for future reference.
Part No._________________Date___________Frequency________kHz
P48W
TM150M
Applications
• Recommended for boat up to 7m (22’) long
• Not recommended for boats with large inboard engine(s)
• P48W—Not recommended for stepped transoms because the
transducer will be difficult to adjust.
• Vertically orients sound beam on hull with deadrise angle up to 22°
• Adjusts to transom angles from 2° – 22°
• Requires 89mm (3-1/2") of headroom to install
• Bracket protects sensor from frontal impact only
• P48W or TM150M—Trolling motor fitting adapts transducer for
use with a trolling motor or optional Portable Mount Kit
Transom Mount
Attaching the Bracket to the Transducer
1. Insert the sensor’s pivot posts into the recesses on the sides of
the bracket (see Figure 1).
2. Press the two nuts into the slots in the back of the bracket.
3. Align the holes in the sensor, bracket, and nuts. Insert the two
machine screws capturing the nuts. Tighten the machine screws
until the sensor will stay in the “up” (released) position unaided.
IMPORTANT: Read the instructions completely
before proceeding with the installation. These
instructions supersede any other instructions in your
instrument manual if they differ.
Tools & Materials
Safety goggles
Dust mask
Phillips screwdrivers
Pencil
Electric drill
Drill bits:
Bracket holes 4mm, #23, or 9/64"
Transom hole (optional) 18mm, 11/16", or 3/4"
24 mm or 15/16" or 1"
Cable clamp holes 3mm or 1/8"
Masking tape
Angle finder (some installations)
Marine sealant (suitable for below waterline)
Straight edge
Grommet(s) (some installations)
Cable ties (some installations)
Band clamp
Water-based anti-fouling paint (mandatory in salt water)
(trolling motor mount) Measure before purchasing ( Figure 9)
(Raymarine only)
Mounting Location
CAUTION: Do not mount in line with or near water intake or
discharge openings or behind strakes, fittings, or hull irregularities
that will disturb the water flow.
CAUTION: Do not mount the sensor where the boat may be
supported during trailering, launching, hauling, or storage to avoid
damaging the transducer’s face.
pivot post (2)
bracket
sensor
Figure 1. Attaching the bracket to the transducer
recess (2)
Copyright © 2008 Airmar Technol ogy Corp.
machine
screw (2)
slot (2)
nuts
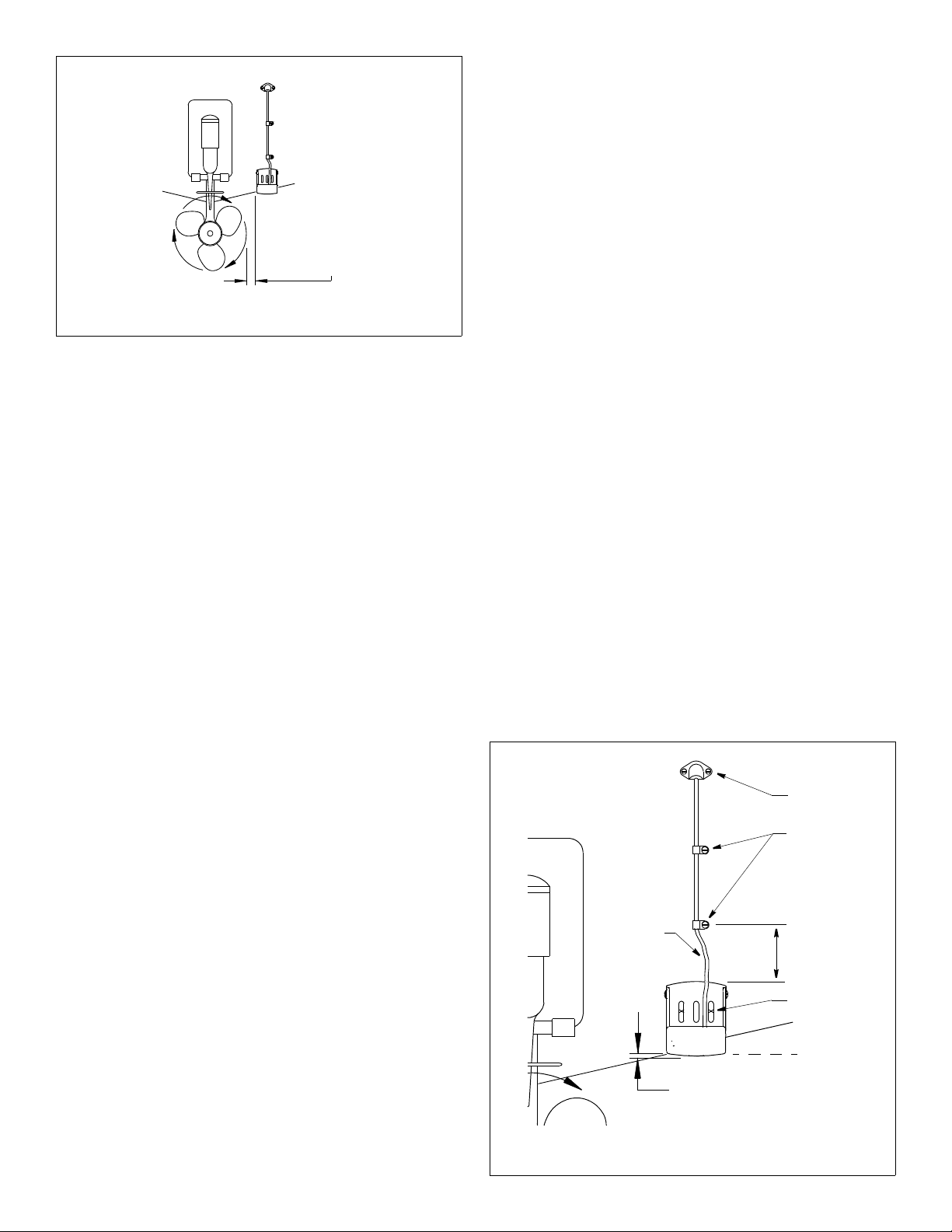
NOTE: Starboard
side of hull where
propeller blades are
moving downward is
preferred.
75mm (3")
minimum beyond
swing radius
Figure 2. Mounting location on single drive boat
Copyright © 2008 Airmar Technolog y Corp.
• For the best performance, the transducer’s face must be in contact
with smooth water. To identify an area of “clean” water, observe
the water flow off the transom while the boat is underway.
• Allow headroom space above the bracket for it to release and
rotate the sensor upward.
• Mount the sensor as close to the centerline (keel) of the boat as
possible to ensure the transducer’s face remains in the water
when the boat is turning.
• Single drive boat—Mount at least 75mm (3") beyond the
swing radius of the propeller, so the water passing over the
transducer does not cause a flow disturbance to the propeller
(see Figure 2). The starboard side where the propeller blades
are moving downward is preferred.
• Twin drive boat—Mount the sensor between the drives.
Hole Drilling
CAUTION: To prevent drilling too deeply, wrap masking tape
around the bit 22mm (7/8") from the point.
NOTE: Fiberglass hull—Minimize surface cracking by running
the drill in reverse until the gelcoat is penetrated.
1. At the selected location, position the sensor, so it projects 3 mm
(1/8") below the bottom edge of the transom (see Figure 3).
2. Being sure the bottom of the sensor is parallel to the waterline,
mark the location of the screw holes with an “X” in the center of
the two outer most slots.
3. Using a 4mm, #23, or 9/64" drill bit, drill two holes 22 mm (7/8")
deep at the locations indicated.
• Small aluminum and fiberglass boats (20° transom angle)—
Use the 9° shim with the taper up (see Figure 4). If your boat is
capable of speeds above 20kn (28MPH), install the bracket
with only the 4.5
° shim, taper up.
• If you are unsure about using the shim(s)—Experiment with
the shims by following the instructions “Mounting & Adjusting.”
Mounting & Adjusting
CAUTION: Do not position the leading edge of the sensor lower
than the trailing edge because aeration will occur.
CAUTION: Do not position the sensor deeper into the water than
necessary to avoid increasing drag, spray, and water noise and
reducing boat speed.
1. Apply marine sealant to the threads of two, #10 x 1-1/4", selftapping bracket screws to prevent water seepage into the
transom. Be sure the nuts are in the slots in the back of the
bracket and any shim(s) is in place (see Figure 1). Screw the
sensor to the hull (see Figure 5). Do not tighten the screws
completely at this time.
2. Using a straight edge, sight the underside of the sensor relative to
the underside of the hull (see Figure 4). The trailing edge of the
sensor must be 1 – 6mm (1/16 – 1/4") below the leading edge.
3. Using the vertical adjustment space in the bracket slots, slide
the sensor up or down until the bottom left corner of the sensor
projections 0 – 3mm (0 – 1/8") below the bottom of the hull (see
Figure 3). When you are satisfied with the position of the
sensor, tighten the two bracket screws.
Testing on the Water
1. With the beam angle factory-set to 90°, become familiar with
your echosounder’s performance at a speed of 4kn (5MPH).
2. Gradually increase the boat speed and observe the gradual
decline in performance due to turbulent water flowing over the
sensor’s active surface.
cable cover
cable clamp
Compensating for Transom Angle: Shims
For the best performance, the transducer beam must be aimed
straight at the bottom. Since the transom of most boats is angled,
the bracket must compensate for it. Measure the transom angle of
the boat with an angle finder.
• Standard transom (13
designed for a standard 13
needed for this installation. If your boat is capable of speeds
above 20kn (28MPH), install the bracket with the 4.5° shim,
taper down (see Figure 4).
• Stepped transom and jet boats (3
shim with the taper down (see Figure 4). If your boat is capable of
speeds above 20kn (28 MPH), install the bracket with both the 9
° shims, taper down. Install the 4.5° shim against the
and 4.5
transom after shaving the interfering portion of the rails and lower
bump. Place the 9
2
° transom angle)—The bracket is
° transom angle. The 9° shim is not
° transom angle) —Use the 9°
°
° shim and bracket assembly on top.
allow 76mm
(3”) of slack
to adjust
beam angle
Hull projection
0– 3 mm (0–1/8")
Figure 3. Vertical adjustment and cable routing
Copyright © 2008 - 2012 Airmar Techno logy Corp.
50mm (2")
screw (2)
location
parallel to
waterline