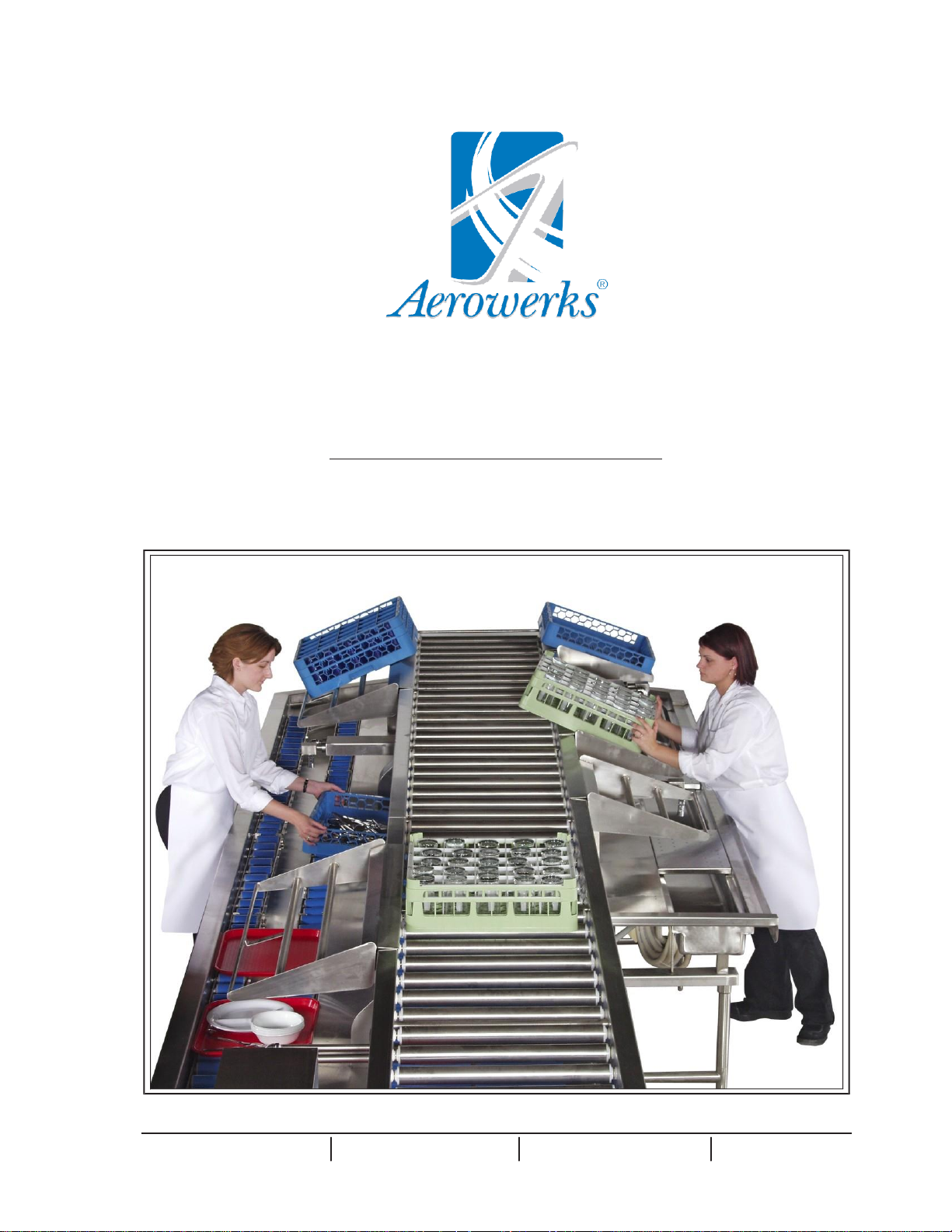
Fax : (905)-363-6998
- 1 -
INSTRUC TION MANUAL FOR MODEL PRC
POWER ROLLER CONVEYOR
Aerowerks©2017
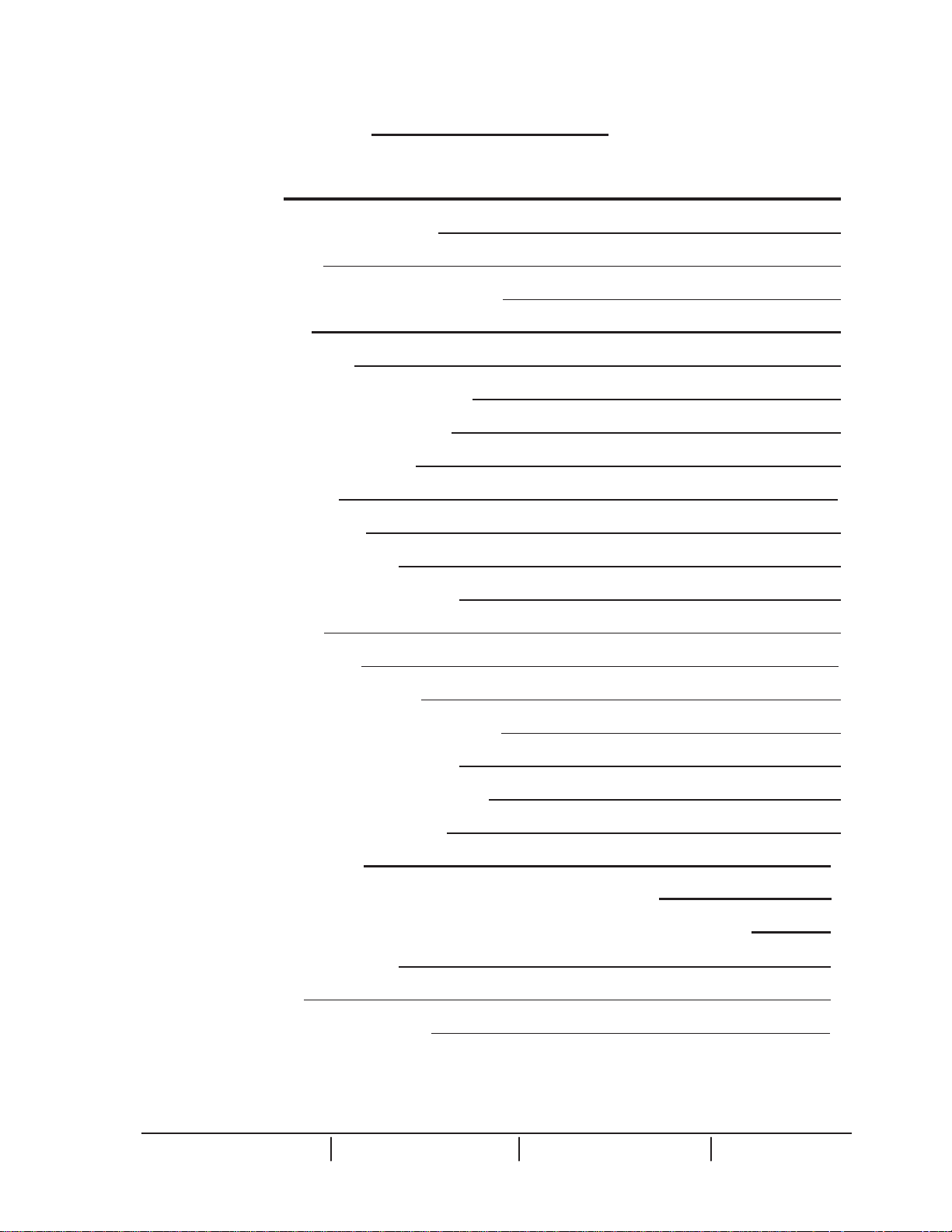
Fax : (905)-363-6998
- 2 -
TABLEOFCONTENTS
1. OPERATION 3
1.1. GENERAL DESCRIPTION 3
1.2. OPERATION 3
1.2.1. GENERAL INSTRUCTIONS 3
2. MAINTENANCE 4
2.1. CHAIN TAKEUP 4
2.1.1. GEAR MOTOR TAKEUP 4
2.1.2. CHAIN LINK TAKEUP 4
2.2. ELECTRICAL SYSTEM 5
2.3. LUBRICATION 6
2.3.1. BUSHINGS 6
2.3.2 GEAR MOTOR 6
2.4. MAINTENANCE SCHEDULE 6
2.4.1. DAILY 6
2.4.2. MONTHLY 6
2.4.3. SEMI-ANNUALLY 7
2.5. REPLACING FRAME BUSHINGS 7
2.6. REPLACING GEAR MOTOR 7
2.7. REPLACING ROLLER SHAFTS 8
2.8. REPLACING SPROCKETS 9
3. TROUBLESHOOTING 10
4. MODEL PRC- POWERED ROLLER CONVEYOR PARTS 11
5. WARRANTY FOR MODEL PRC- POWERED ROLLER CONVEYOR 13
5.1. WARRANTY PERIOD 13
5.2. GENERAL 13
5.3. WARRANTY COVERAGE 13
Aerowerks©2017
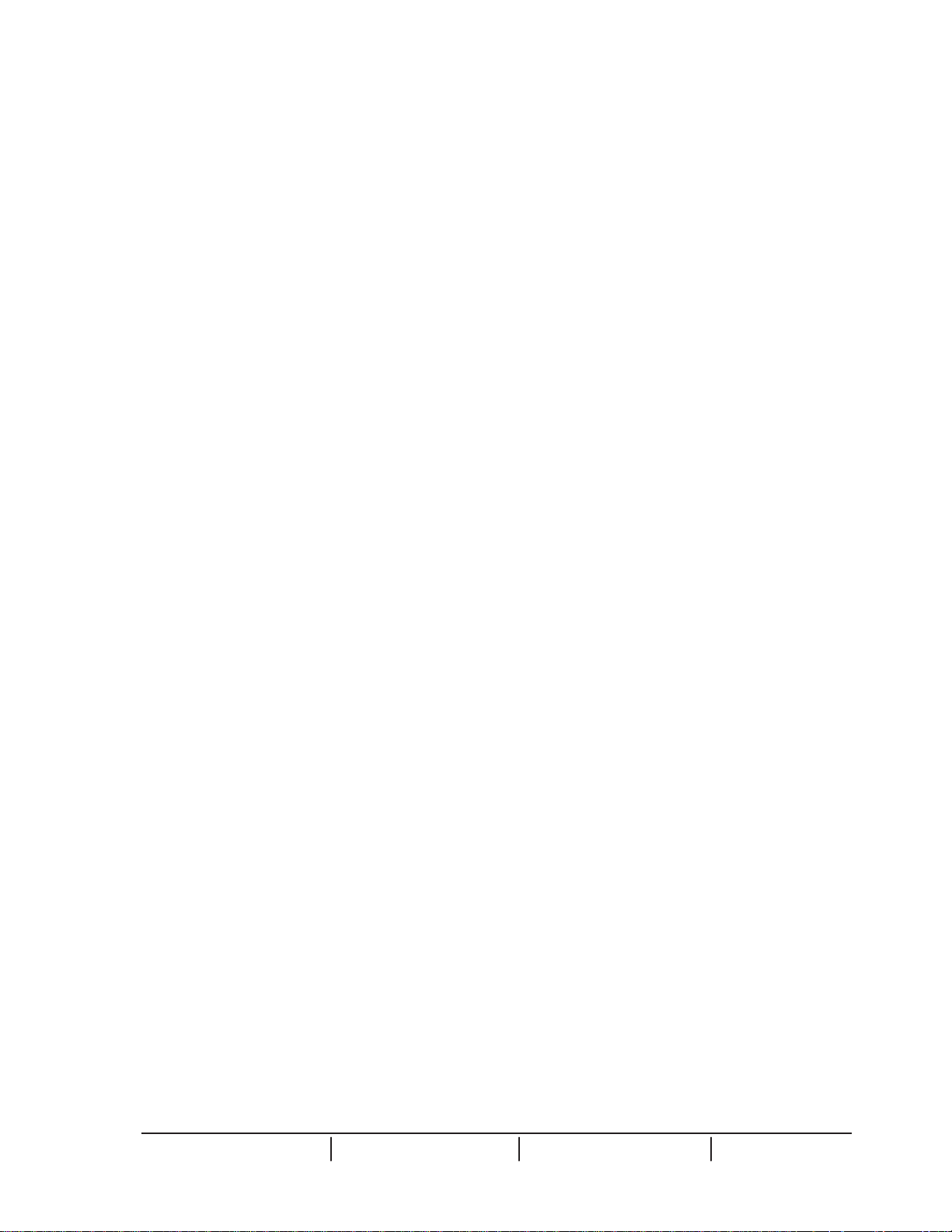
Fax : (905)-363-6998
- 3 -
INSTRUCTION MANUAL FOR MODEL PRC- POWER ROLLER
1. OPERATION
1.1. GENERAL DESCRIPTION
The Power Roller Conveyor usually forms an integral part of the scrapping table. Its
function is to convey 20” x 20” dish racks to the gravity roller conveyor or directly to the
dishwasher. This conveyor has been custom designed to suit your application. Do not
use this conveyor to convey items other than 20” x 20” dish racks.
The low-pressure accumulation principle treats each roller as an individual unit. Hence
when the racks get accumulated, the rollers underneath them stop turning where as the
remaining rollers will continue to function.
1.2. OPERATION
1.2.1. GENERAL INSTRUCTIONS
1. Turn the 'MAIN DISCONNECT' switch on the main control panel to “ON” position.
2. Push the green 'START' button marked 'Rack Conveyor'. Some systems may have
auxiliary push button stations located in other required areas.
3. To shut down the conveyor, push the red 'STOP' button marked 'Rack Conveyor'.
Then turn the 'MAIN DISCONNECT' switch to 'OFF'.
Note: Power rollers run at constant speed at low pressure driving force, allowing
accumulation to take place without having to stop the conveyor.
Aerowerks©2017
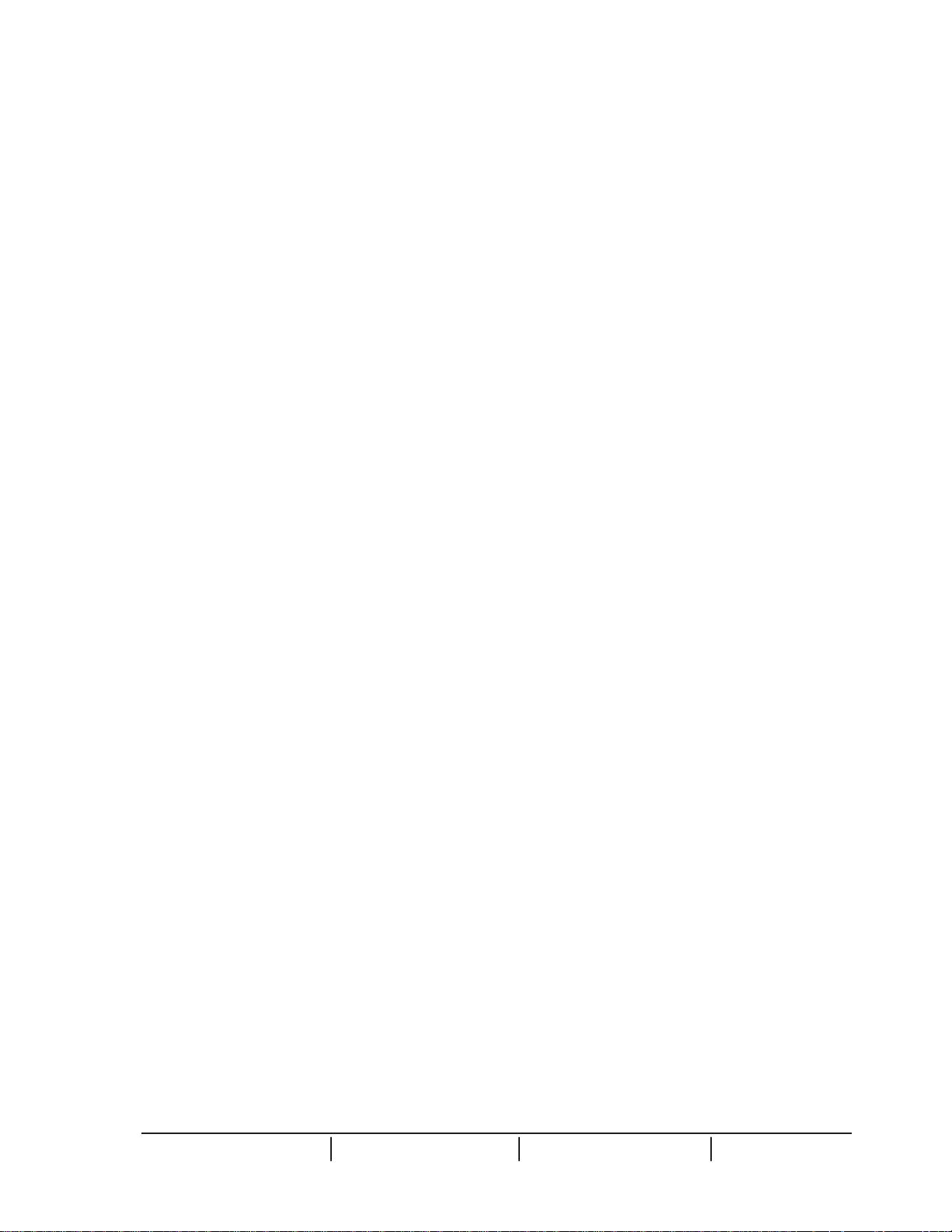
Fax : (905)-363-6998
- 4 -
2. MAINTENANCE
2.1. CHAIN TAKEUP
Generally the drive chain does not need any replacement. However, it requires time-totime adjustment to remove the slack developed in the chain due to the tension. This can
be accomplished either by moving the gear motor away from its initial position or by
removing a few links from the chain. The first method is recommended for the small
adjustments where as the second method is ideal choice for the large adjustments.
2.1.1. GEAR MOTOR TAKEUP
1. Disconnect the power to avoid accidental starting.
2. Remove the drive housing
cover.
3. Loosen the gear motor mounting bolts and gently lower the gear
motor.
Since the drive sprocket mounted the motor shaft, lowering the motor reduces
the slack in the chain.
4. Tighten the gear motor mounting bolts.
5. Run the system to make sure that the chain take-up is adequate and conveyor
operation is smooth.
6. Turn off the power and replace the side covers.
2.1.2. CHAIN LINK TAKEUP
1. Disconnect the power to avoid accidental starting.
2. Remove the drive housing cover.
3. Disconnect the chain preferably at the location of the removable link.
If it is hard to locate this link, use a chain breaker to disconnect at any other link.
Estimate the number of links required to be removed to eliminate the slack.
4. Remove the access links from the chain.
5. Reconnect the ends and turn on the power.
Aerowerks©2017
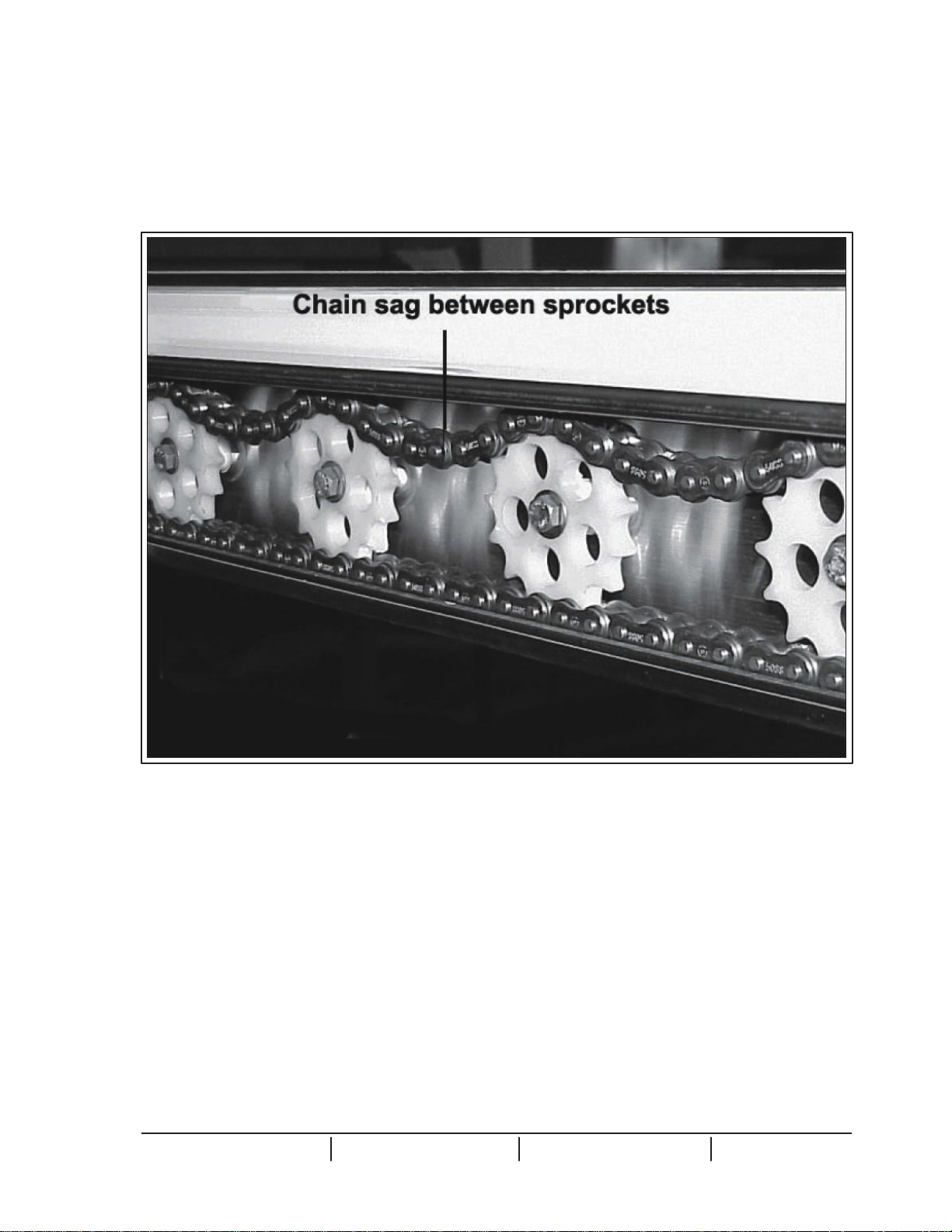
Fax : (905)-363-6998
- 5 -
6. Run the system to make sure that the chain take-up is adequate and the conveyor
operation is smooth.
7. Turn off the power and replace the drive housing cover.
The electrical system control unit contains all relays, starters and other devices required
for the operation of conveyor control. There may be some auxiliary start-stop stations in
addition to the main control panel. Check the schematic for details. The main control
panel is NOT waterproof. Under no circumstances shall the control panel be hosed down
with water, during cleaning.
All fuses are sized individually for control or power circuit. Refer to electrical wiring
schematics when replacing fuses.
Figure 1.0 Normal Chain Sag between Plastic Sprockets
2.2. ELECTRICAL SYSTEM
Aerowerks©2017