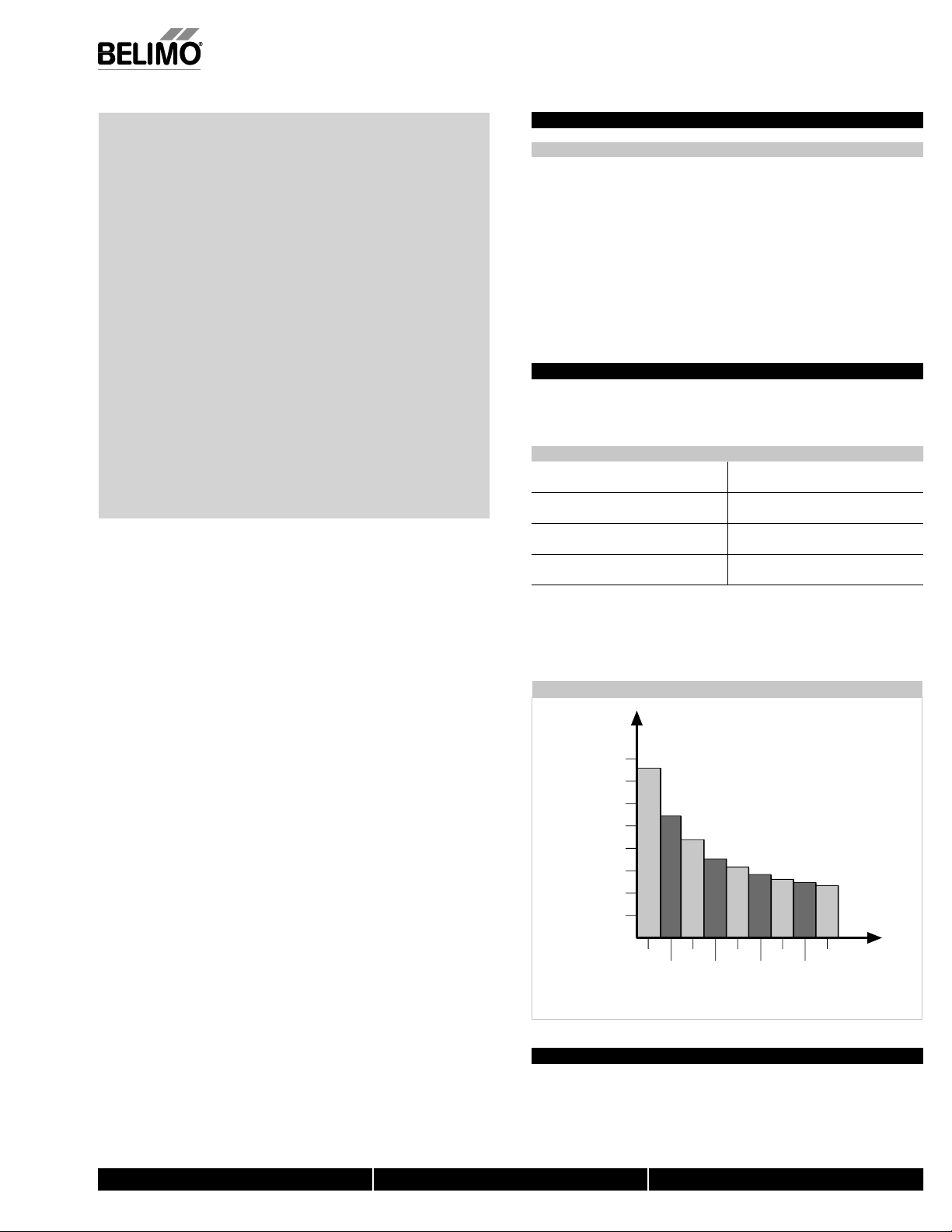
able of Content
...............................................................
........................................................
..............................................
PAGE
General Mountin
Standard
Reversible Clamp ...............................................
Lin
................................................................. 272
Rotary ................................................................. 273
Retrofit Brackets
Operation
Electrical
Mechanical ......................................................... 277
Wiring
General
Accessories
Startup and Checkout
270
271
75
27
278
282
nstallation and Operatio
Non-Spring Retur
General Information
Preliminary Steps
. Belimo actuators with NEMA 1 or NEMA 2 ratings should be mounted indoors in
a dry, relatively clean environment free from corrosive fumes. If the actuator is
mounted outdoors, a protective enclosure must be used to shield the actuator.
. For new construction work, order dampers with extended shafts. Instruct the
installing contractor to allow space for mounting the Belimo actuator on the shaft.
For replacement of existing gear train actuators, there are two options:
. From a performance standpoint, it is best to mount the actuator directly onto the
damper shaft.
. If the damper shaft is not accessible, mount the non-spring return actuator with
a ZG-NMA or ZG-GMA crank arm kit, and a mounting bracket (ZG-100, ZG-101,
ZG-103, ZG-104
Determining Torque Loading and Actuator Sizing
amper torque loadings, used in selecting the correct size actuator, should be pro
vided by the damper manufacturer. If this information is not available, the following
eneral selection guidelines can be used
amper Type
Opposed blade, without edge seals, for
ht close-off application
non-ti
Parallel blade, without edge seals, for
non-ti
ht close-off application
pposed blade, with edge seals, for tight
close-off application
Parallel blade, with edge seals, for tight
close-off application
he above torque loadings will work for most applications under 2 in. w.g. static
ressure or 1000 FPM face velocity. For applications between this criteria and 3 in.
w.g. or 2500 FPM, the torque loading should be increased by a multiplier of 1.5. If
the application calls for higher criteria up to 4 in. w.g. or 3000 FPM, use a multiplier
of 2.0
orque Loading
in-lb/sq. ft
4 in-lb/sq. ft
5 in-lb/sq. ft
7 in-lb/sq. ft
Torque Loading Char
, Inc.
USA
140
120
100
e. © Belimo Aircontrols
80
60
40
ect to chan
20
Damper Area (sq. ft.)
0
2
M40024 - 05/10 - Sub
Torque Loading (in-lb/ sq. ft.)
46810
3
579
Multiple Actuator Mounting
f more torque is required than one GM can provide, GM24B, GMB24-SR or GMX24-
FT may be installed on the same shaft
800-543-9038 USA 866-805-7089 CANADA 203-791-8396 LATIN AMERICA
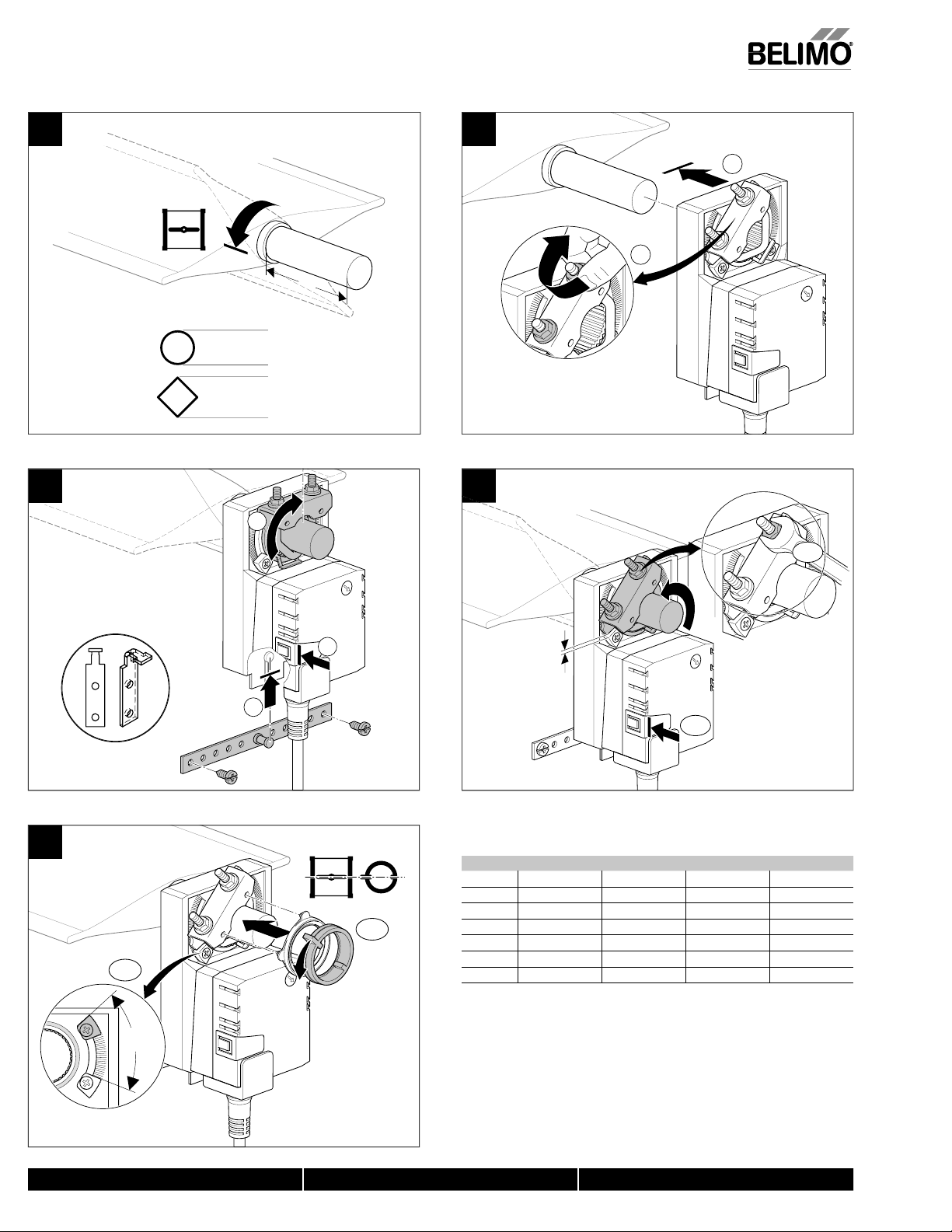
Installation Instructions
uick-Mount Visual Instructions for Mechanical Installatio
1
3
A
B
2
1
2
C
4
1
D
2
10
LM Universal
Mounting Bracket
5
1
5°
2
1
EE NEXT PAGE FOR STANDARD MOUNTING INSTRUCTION
LM
LMQ
1
2
NM
AM
AMQ
* LMB standard clamp has max 5/8” diameter. Accessory clamp K-LM20 can be
** Shorter with reversible clamp for NMB, AMB, and GMB.
1/4” to
1/2” to 1.05”3/8” to 11/16”1.5
1/2” to 1.
1/2” to 1.05”3/8” to 11/16”1.5” 6 to 7 ft-l
1/2” to 1.
1/2” to 1.05”7/16” to 11/16”1.5
2” to 1.
mounted for sizes u
elf-centers on the following diameter shafts: 1/2” (default), 3/4” and 1.05”. GM
clamps have an insert that self-centers on 3/4” diameter
to 3/4” diameter. NM and AM clamps have an insert that
” to 9/16”1.
” to 11/16”1.
” to 11/16”1.5”
7/16” to 11/16”1.
**
4 to 5 ft-l
6 to 7 ft-l
7 ft-l
7 ft-l
6 to 7 ft-l
7 ft-l
M40024 - 05/10 - Subject to change. © Belimo Aircontrols (USA), Inc.
800-543-9038 USA 866-805-7089 CANADA 203-791-8396 LATIN AMERICA
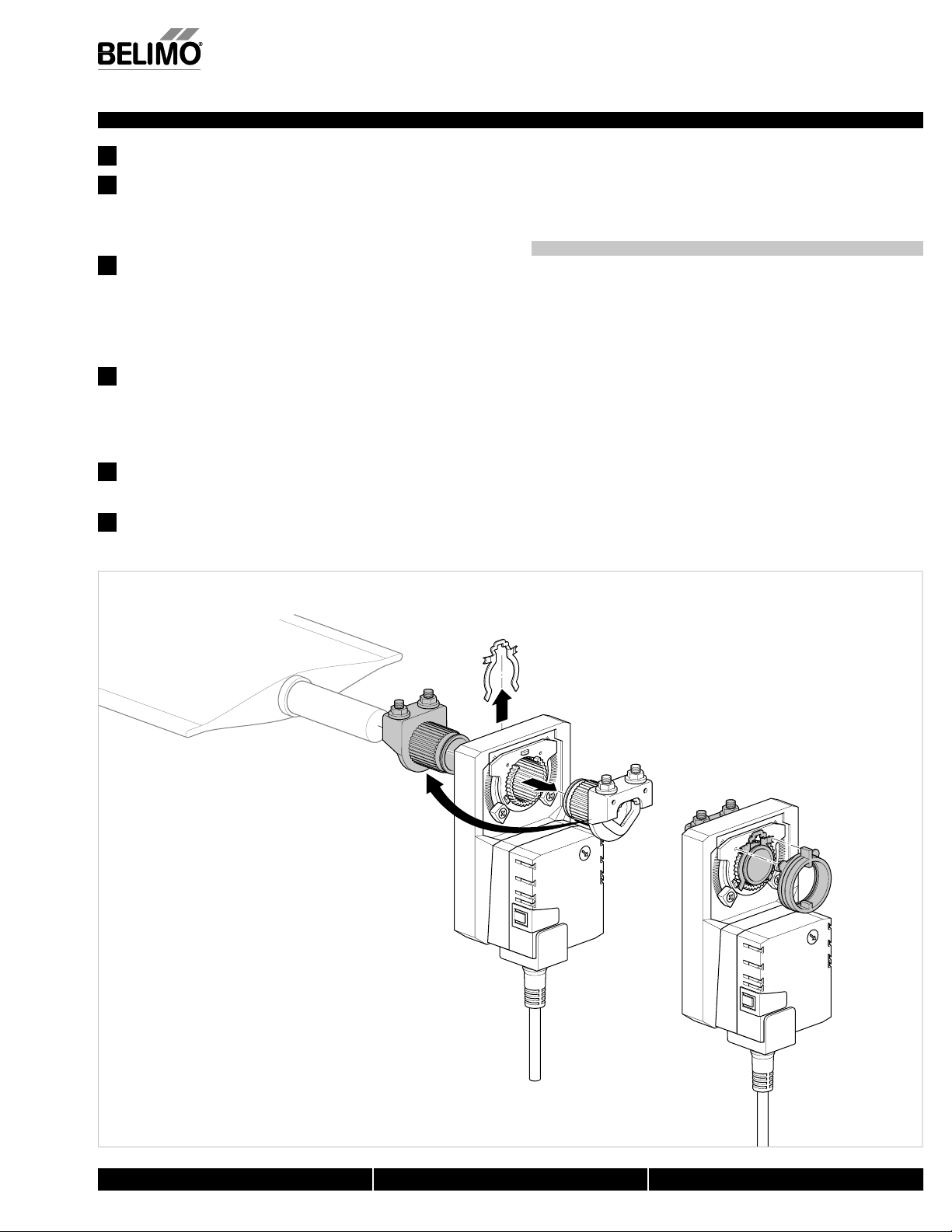
Standard Mounting
ounting Installatio
eversible Clamp Quick Mount (NM, AM, GM
1
Turn the damper shaft until the blades are fully closed
2
Slip the actuator’s universal clamp over the damper shaft. Make sure that
uct and the controls on the cover are access
t
mounting position
Hand tighten the two nuts on the actuators universal clamp.
3
Disengage the actuator gear train by pressing the manual override button
and rotate the clamp until centered.
Slide the anti-rotation strap up under the actuator so it engages the
actuator at the center cutout. Bend the bracket as needed to support the rear
of the actuator. Secure to ductwork with self-tapping screws (No. 8 recom
mended)
4
Loosen the nuts on the universal clamp. Press the manual override
utton and rotate the clamp to about 5° from the closed position (1/16 to 1/8”
etween stop and clamp).
Tighten the two nuts on the universal clamp with a 10 mm wrench (see
table for required torque)
5
Snap on the refl ective position indicator
Adjust end-stops, if required
6
Mount actuators indoors. If mounted outdoors, use approved protective enclosure.
e. Place the actuator in the
he damper is now fully closed but the actuator is 5° from fully closed. This is called
“pre-loading” the actuator. When the actuator is powered and sent to the closed
osition: it will put its full torque on the shaft compressing the edge and blade seals.
his ensures that the damper will meet its leakage rating. The actuator is electroni
ally protected from overload and will not be damaged.
Testing the Installation Without Powe
. Disengage the gear train with the manual override button and move the shaft
from closed to open to closed. Ensure that there is no binding and that the
damper goes fully open and closes with 5° of actuator stroke left
. Correct any problems and retest.
, Inc.
USA
e. © Belimo Aircontrols
ect to chan
M40024 - 05/10 - Sub
800-543-9038 USA 866-805-7089 CANADA 203-791-8396 LATIN AMERICA