
Manual, complete
745-34
Sewing unit for runstitching of piped flap
and welt pocket openings and pocket corners
Working methods: A, B, D, F
Operating Instructions
Installation Instructions
Service Instructions
Instructions for Programming DAC
1
2
3
4
Postfach 17 03 51, D-33703 Bielefeld • Potsdamer Straße 190, D-33719 Bielefeld
Telefon + 49 (0) 5 21 / 9 25-00 • Telefax + 49 (0) 5 21 / 9 25 24 35 • www.duerkopp-adler.com
Ausgabe / Edition: 01/2004 Printed in Federal Republic of Germany Teile-Nr./Part.-No.: 0791 745161
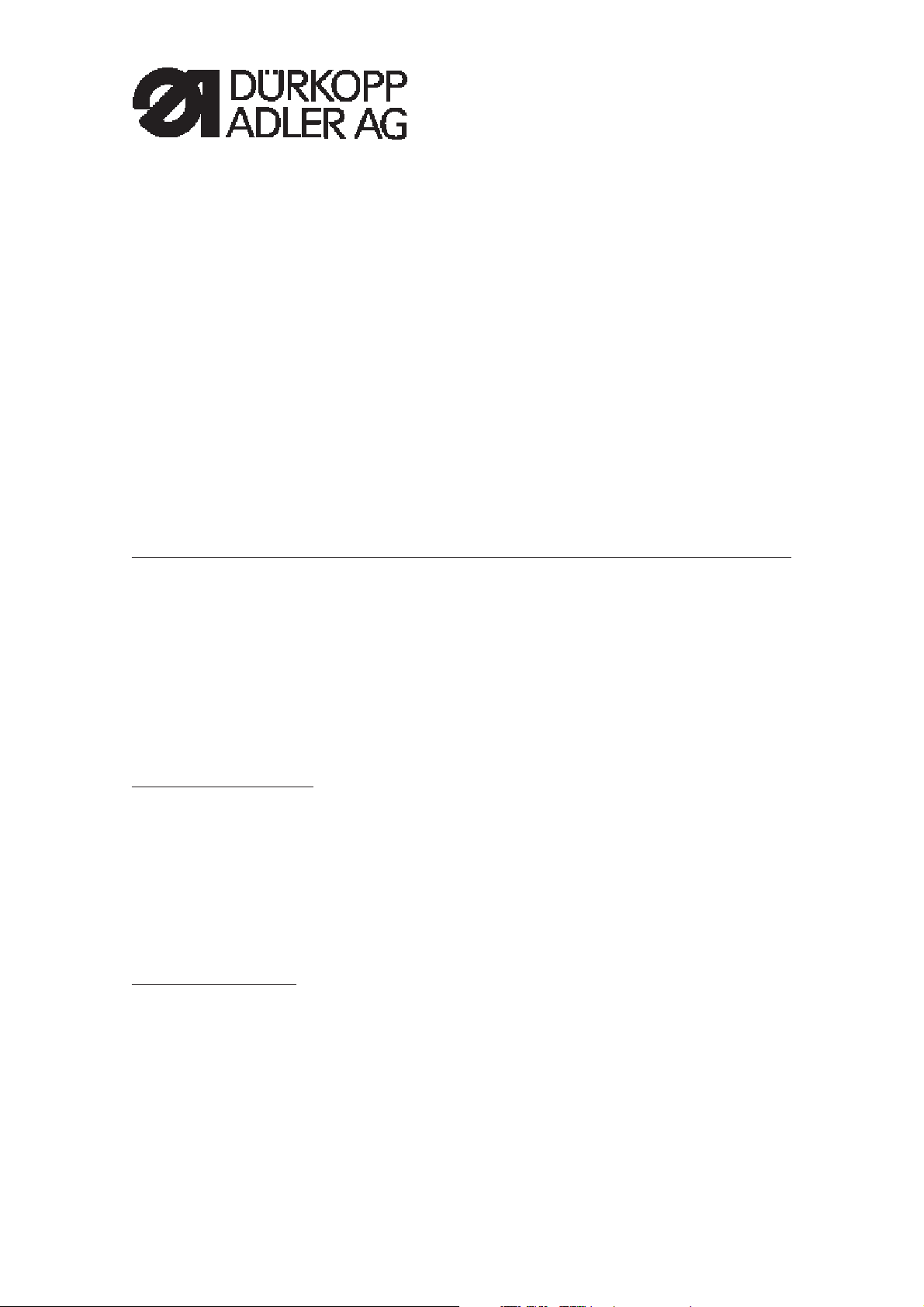
745 - 34
Manual, complete
Summary
Operating Instructions
Installation Instructions
Service Instructions
Instructions for Programming DAC
Interconnection-diagram
9870 745100 B
9870 745115 B
9870 745116 B
9870 001018 B
Pneumatic circuit plan
9770 745003
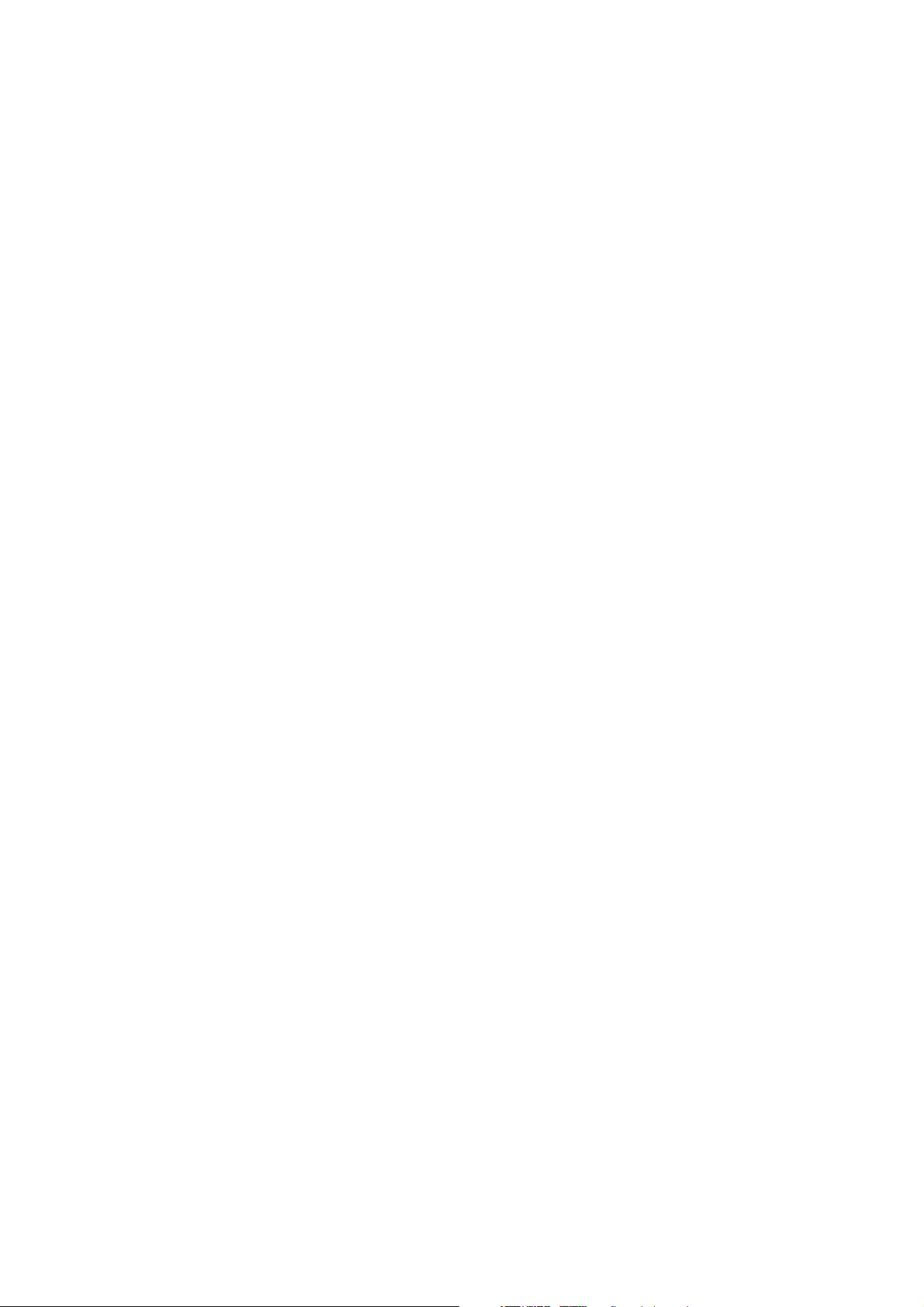
Index Page:
Part 2: Installation Instructions 745-34
1. Scope of delivery .............................................. 3
2. General notes ................................................ 3
3. Installing the sewing unit
3.1 Transport ................................................... 4
3.2 Removing the security devices ...................................... 5
3.3 Setting the working height ......................................... 6
3.4 Adjusting the foot pedals .......................................... 7
4. Attaching the machine parts removed for shipping
4.1 Thread reel holder .............................................. 8
4.2 Cylinder for pick-up folder stroke ..................................... 9
4.3 Workpiece boxes .............................................. 10
4.4 Fastening the holder for control panel, bobbin winder and right-hand tray............. 11
4.5 Table extension (optional equipment) .................................. 12
4.5.1 Table extension for working method with bundle clamp carriage .................. 12
4.5.2 Table extension for stacking to the side for 745-34 A and 745-34 D ................ 13
4.6 Throw-over stacker (optional equipment) ................................ 14
5. Electrical connection
5.1 Connecting the control panel DAC II C .................................. 16
5.2 Connecting the external bobbin winder ................................. 16
5.3 Making the mains connection ....................................... 16
5.4 Checking the nominal voltage ....................................... 17
5.5 Checking the nominal voltage of the vacuum device (optional equipment) ............ 18
5.6 Direction of rotation of the sewing motor ................................ 18
6. Pneumatic connection .......................................... 19
7. Connection to the factory-own vacuum unit ............................. 20
8. Oil lubrication................................................ 21
9. Commissioning............................................... 22
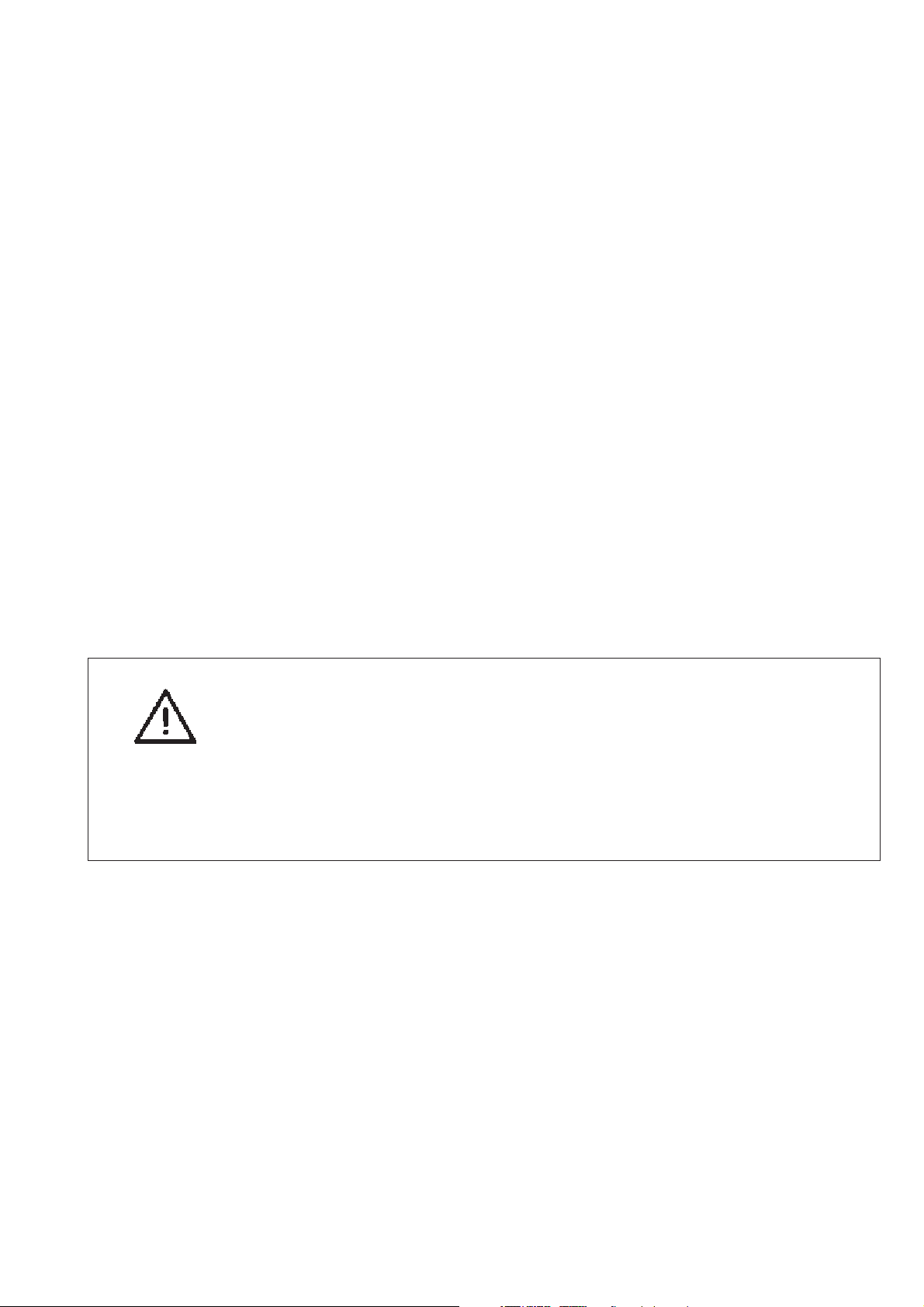
1. Scope of delivery
–
Basic sewing unit for runstitching of piped, flap and welt pocket
openings with rectangular and slanted pocket corners, consisting
of:
–
Height-adjustable stand
–
Step motors for sewing drive, material feed, length adjustment
of the corner incision device
–
Twin needle lockstitch machine
–
DAC II C control with control panel
–
Laser marking lamps
–
Sewing light
–
Compressed air maintenance unit with compressed air pistol
–
Thread reel holder
–
Workpiece boxes for additional parts to the left of the operator
and underneath the table top
–
Tools and small parts in the accessories
–
Feeding and sewing equipment according to the working
method
–
Optional equipment
2. General notes
ATTENTION !
The sewing unit must only be assembled by trained specialist staff.
Any work on the electrical equipment of the sewing unit must
only be carried out by electricians or correspondingly instructed
persons.
The mains plug must be pulled out.
The enclosed operating instructions of the step motor manufacturer
have to be observed in any case.
3
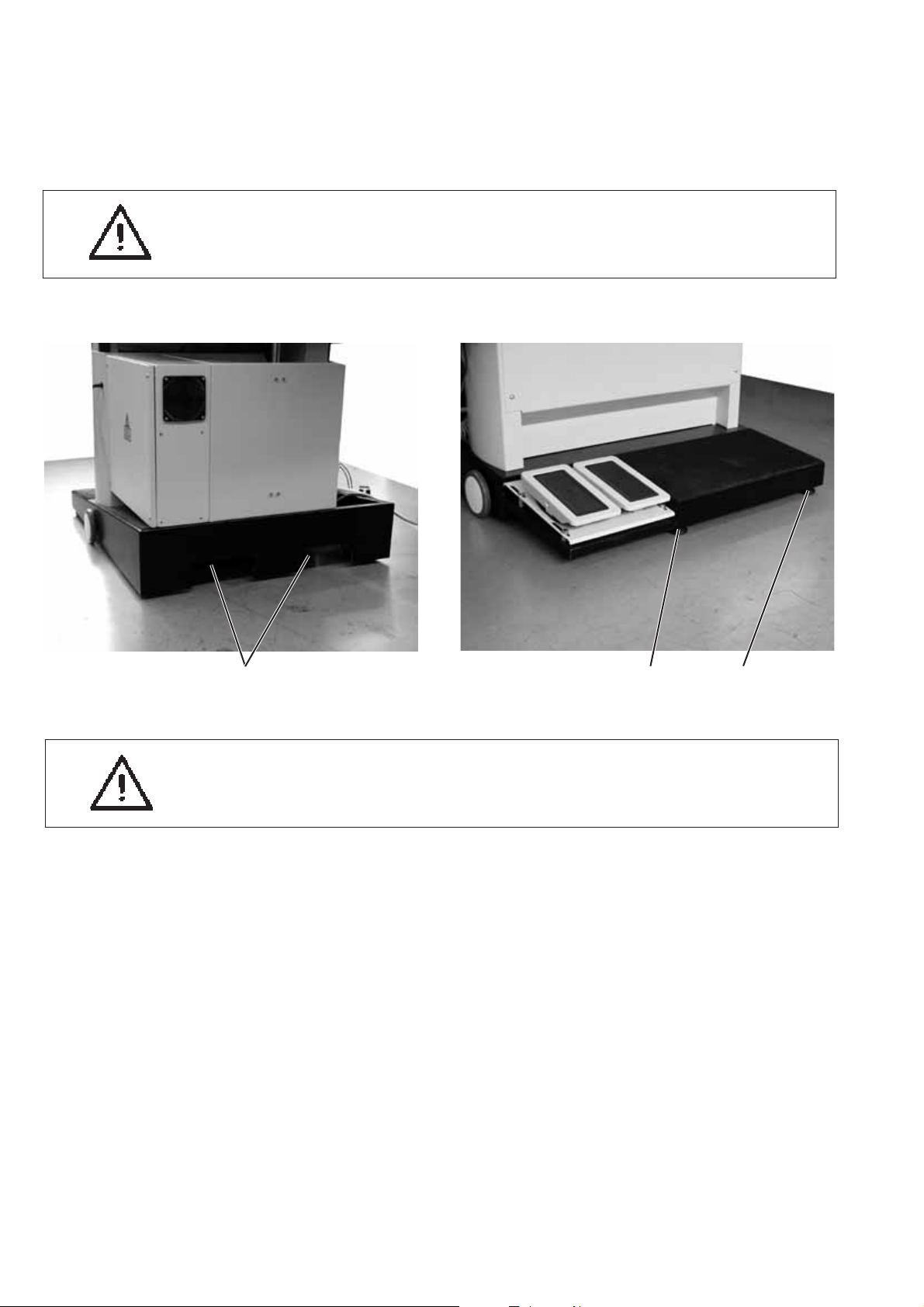
3. Installing the sewing unit
3.1 Transport
For in-house transport the stand is equipped with four castors.
ATTENTION !
Do not lift the sewing unit at the table tops.
Use an elevating platform truck or a forklift truck.
1
ATTENTION!
Before commissioning the sewing unit screw out the stand feet 2 and 3
until a secure footing is achieved.
Lifting the sewing unit
–
Push the elevating platform truck or the forklift forks into the
openings 1 at the back of the sewing unit.
Rolling the sewing unit
–
For transport purpose unfasten the stand feet 2 and 3 by turning
them to the right.
–
After transport secure the sewing unit by turning the stand feet 2
and 3 to the left.
23
4
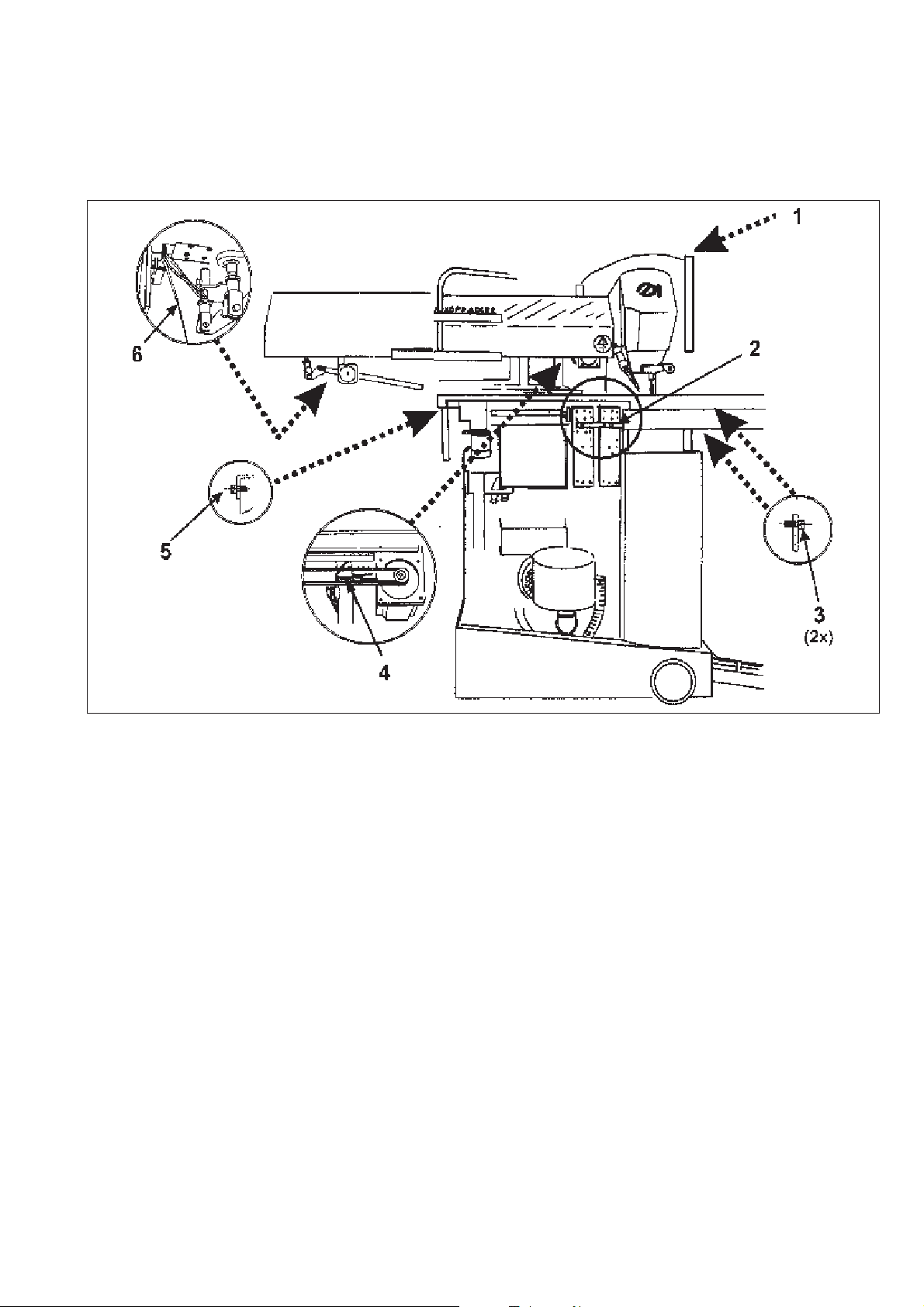
3.2 Removing the securing devices
Before installing the sewing unit all six securing devices have to be
removed.
If the sewing unit has to be transported to another place, please use
the securing devices again.
5
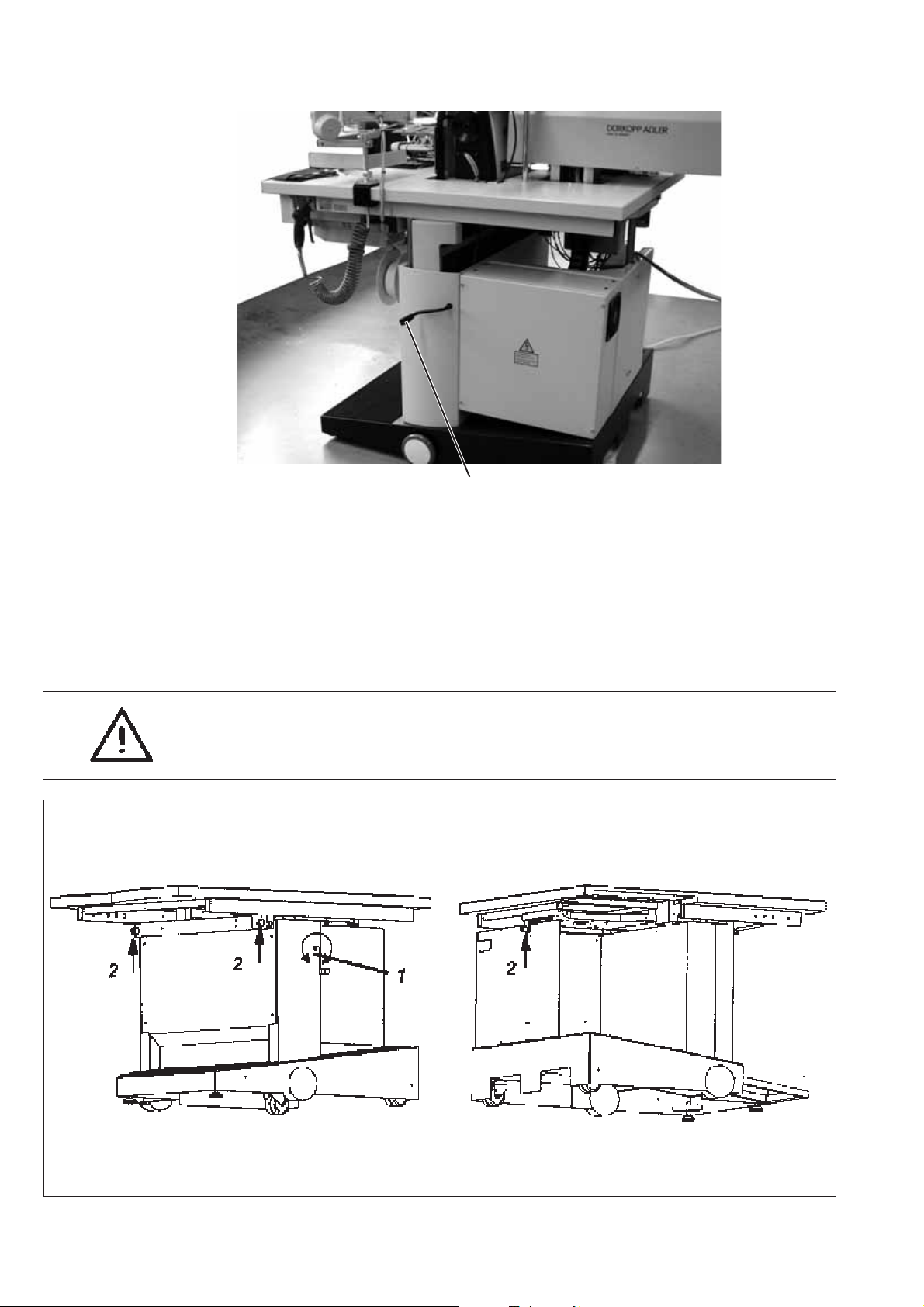
3.3 Setting the working height
1
The working height can be set between 77 cm and 108 cm
(measured up to the upper edge of the table top).
The sewing unit is set to the lowest working height of 77 cm by the
manufacturer.
–
Turn the table top to the desired height with crank 1.
–
To the right = Table top higher
–
To the left = Table top lower
ATTENTION: Danger of breakage !
Crank 1 must not be actuated before the 3 securing screws 2 have
been removed.
6