
TABLEOFCONTENTS
Page
5.0
6.0
~Aintenance
4.7
4.8
4.9
4.10
4.11.
4.12
4.13
4.14
Carrier
Index
Drive
Head Load
Front
Front
Stepper
Head/Carriage
Level. 2
Assembly
Lamp
Motor Assembly (on Motor
Lever
Bezel
Assembly
PARTS/ASSEMBLIES
TEST
POINT/CONNECTOR
Assembly (on Motor
Solenoid
Assembly
PHYSICAL
PIN
LOCATIONS
ASSIGNMENTS
Control
Control
PWB)
PWB)
15
16
17
18
21
U
23
24
30
35 .
7.0
8.0
9.0
10.0
SPARE
PARTS
SCHEMATIC
EXPLODED
USINGACLEANING
LIST
DIAGRAMS
VIEW
DISK
38
39
42
43

1.0
INTRODUCTION
This
DATA
Included
ment
engineers.
2.0
MAINTENANCE
The
supplies,
2.1
Maintenance
Phillips
manual
YD-380
is
procedures,
following
test
Screwdriver
describes
two
sided,
information
and
TOOLS
Tools
TOOL
AND
tables
equipment and
List
the
high
also
TEST
list
(for
maintenance
density,
on
service
adjustment
EQUIPMENT
the
maintenance
exerciser
M3)
and
5.25
checks,
instructions
tools,
for
Y-E
141034-01
operation
inch
Floppy
removal and
for
maintenance
the
YO-38D.
DATE
PIN
of
the
Disk
replace-
customers'
Y-E
Drive.
Phillips
Flat
Cutters
Needle Nose
Tweezers
CE
Disk
Cleaning
Wrench
Hex
Wrench
Hex
Screwdriver
Head
Disk
Screwdriver
Pliers
1.27
1.5
mm
mm
(for
M2.6)
141627-01
141035-01
141039-01
141040-01
141042-01
145173-01
145174-01
140266-03
140266-01

2.2
Maintenance
Supplies
2.3
Tie
Wrap
Test
Equipment
Test
Multimeter
Electronic
Oscilloscope*
*
For
Supplies
(TY-23M,
Equipment
Counter*
use
at
Kitagawa)
Maintenance
Level
Y-E
DATA
031005-01
2
PIN
2.4
Exerciser
Equipment
Exerciser
Y-E
DATA
YD-164T
PIN
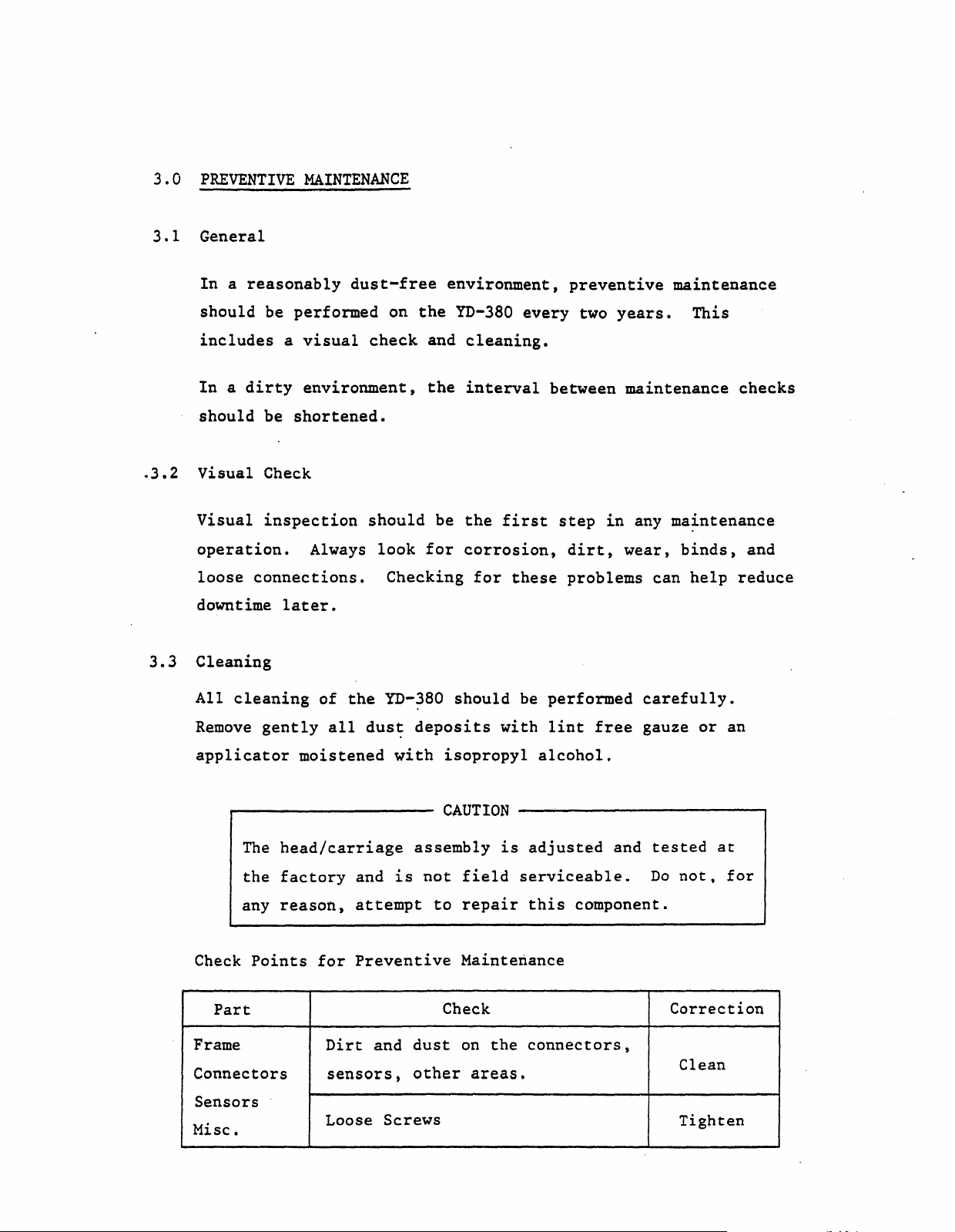
3
.0
PREVENTIVE
MAINTENANCE
.
3.2
3.3
3.1
General
Inareasonably
should
includes
Inadirty
should
Visual
Visual
operation.
loose
downtime
be
performed
a
visual
environment,
be
shortened
Check
inspection
Always
connections.
later.
Cleaning
dust-free
on
check
•
should
look
Checking
environment,
the
YD-380
and
cleaning.
the
interval
be
the
for
corrosion,
for
every
first
these
preventive
two
between
step
dirt,
problems
maintenance
years.
maintenance
in
any
ma~ntenance
wear,
can
This
binds,
help
checks
and
reduce
All
cleaning
Remove
gently
applicator
The
the
any
Check
Points
Part
Frame
Connectors
Sensors
Misc.
of
the
all
dus~
moistened
head/carriage
factory
reason,
for
Dirt
and
attempt
Preventive
and
sensors,
Loose
YD-380
deposits
with
assembly
is
not
dust
other
Screws
should
isopropyl
CAUTION
field
to
repair
Maintenance
Check
the
on
areas.
be
performed
with
lint
alcohol.
is
adjusted
serviceable.
this
connectors,
carefully.
free
and
gauze
tested
Do
component.
or
an
at
not,
for
Correction
Clean
Tighten

4.0
SERVICE
CHECKS,
REPLACEMENTS
AND
ADJUSTMENTS
This
assemblies
two
Levell:
Level
Level
chapter
maintenance
2:
1
4.1
4.2
4.3
4.4
4.5
4.6
Level 2
4.7
contains
listed
Can
be
Special
PWB
Index
Track
Write
Media
In
Use
Carrier
below.
levels:
performed
training
Sensor
00
Sensor
Protect
Sensor
Lamp
detailed
Note
Sensor
maintenance
that
without
and
tools
the
list
special
required.
procedures
is
separated
training
or
for
the
into
tools.
Note:
4.8
4.9
4.10
4.11
4.12
4.13
4.14
Index
Drive
Head Load
Front
Front
Stepper
Head/Carriage
Refer
Chapter
Chapter9for
to
Lamp
Motor (on Motor
Lever
Bezel
Chapter
6
for
(on Motor
Solenoid
Assembly
5
for
Test
Exploded View.
Points/Connector
Control
Control
Parts/Assemblies
PWB)
PWB)
Pin
Locations,
Assignments and
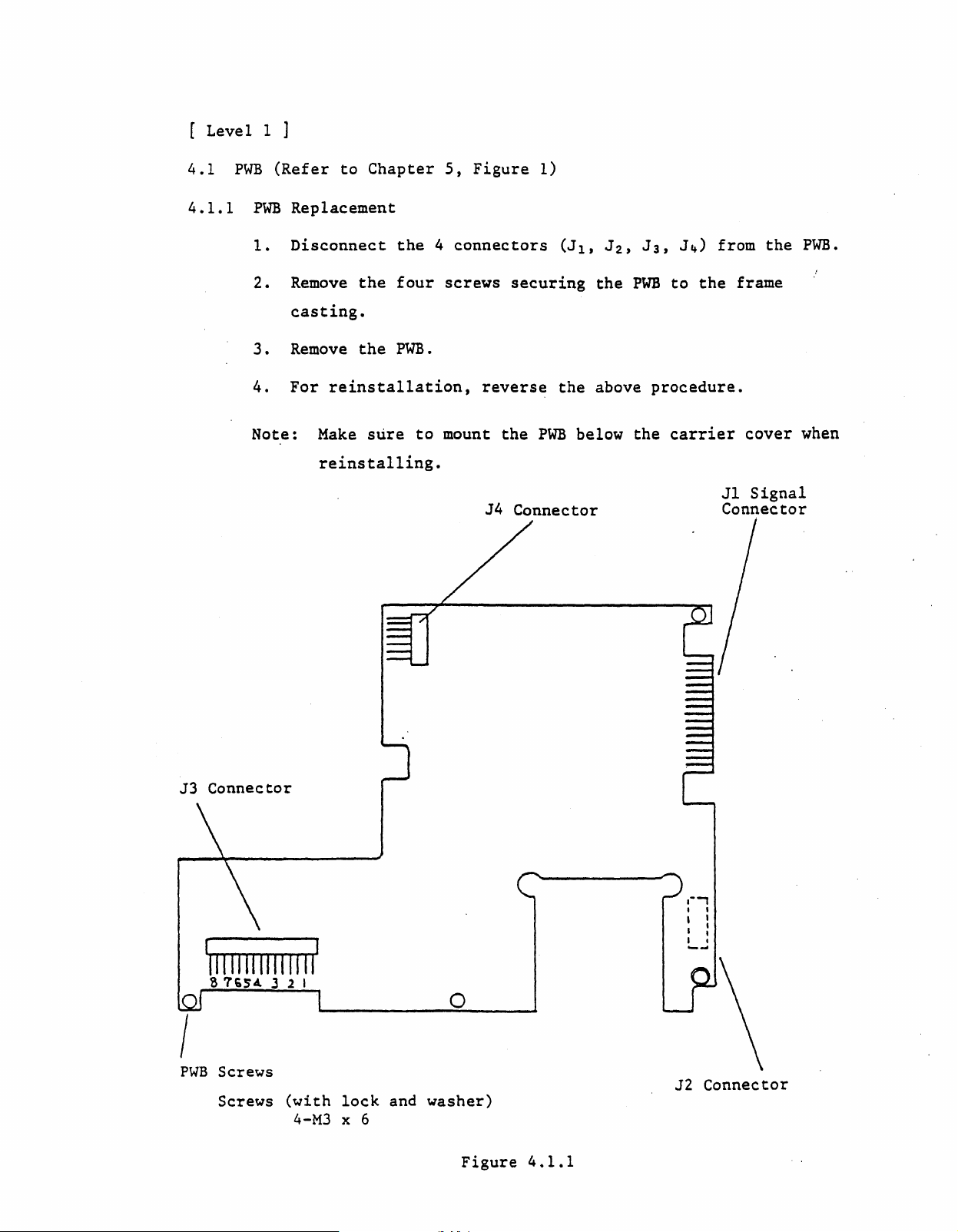
[
Levell]
4.1
4.1.1
PWB
PWB
1.
2.
3.
4.
Note:
(Refer
Replacement
Disconnect
Remove
casting.
Remove
For
to
reinstallation,
Make
reinstalling.
Chapter
the
the
four
the
PWB.
sure
5,
4
connectors
screws
to
mount
Figure
securing
reverse
the
J4
1)
(J1,
the
PWB
below
Connector
J2'
the
PWBtothe
above
the
J3,
J4)
procedure.
carrier
from
the
frame
cover
Jl
Signal
Connector
PWB.
when
J3
Connector
I
PWB
Screws
Screws
(with
4-M3
lock
x 6
and
o
washer)
Figure
4.1.1
,--,
I ,
, I
, :
I ,
--
J2
Connector