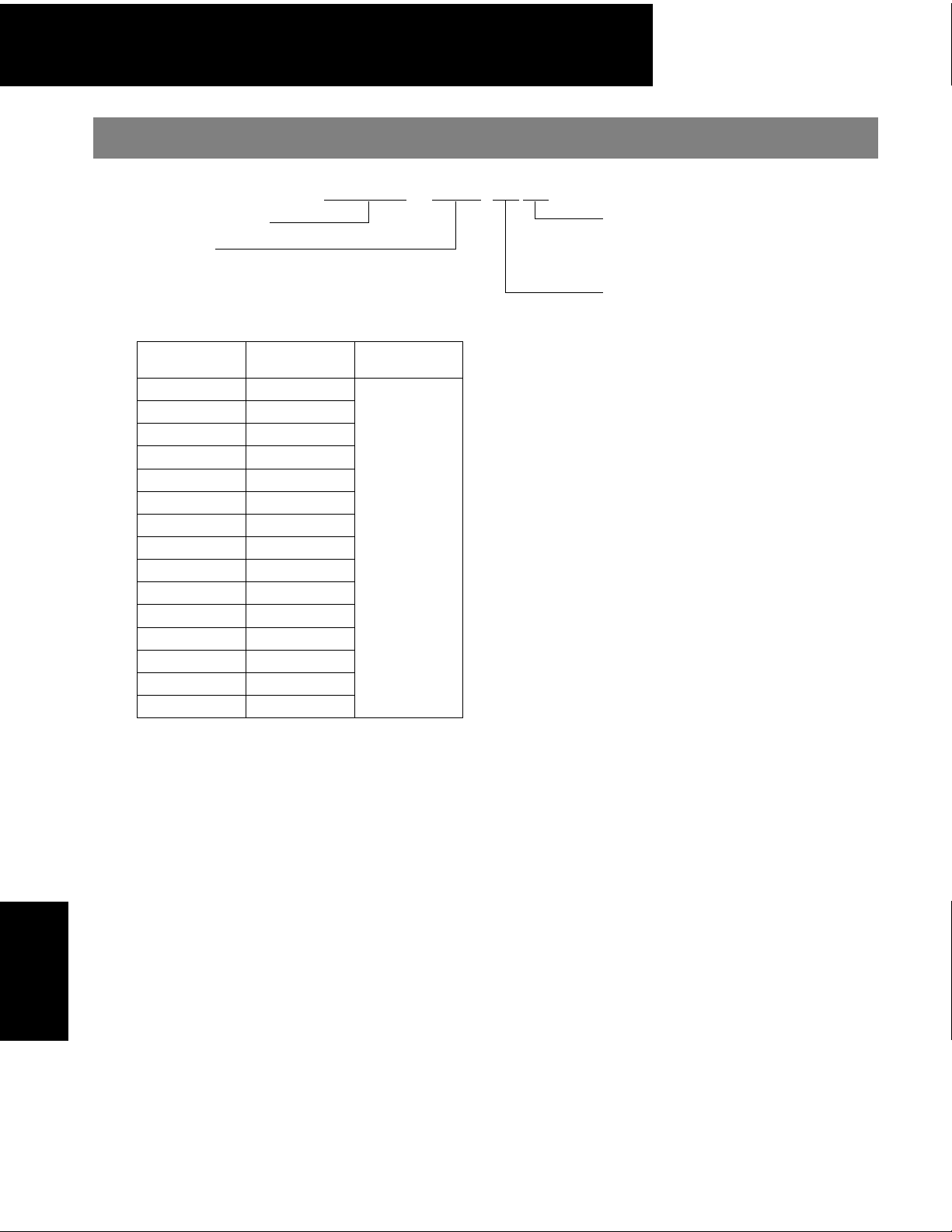
400V Sigma II Servo Systems
Model Number Designation
Sigma II Series
SGDH Servo Amplifier
Rated Output
Amplifier
Model
05 0.5 (.67)
10 1.0 (1.3)
15 1.5 (2.0)
20 2.0 (2.7)
30 3.0 (4.0)
50 5.0 (6.7)
60 6.0 (8.0)
75 7.5 (10)
1A 11 (15)
1E 15 (20)
2B 22 (30)
3Z 30 (40)
3G 37 (50)
4E 45 (60)
5E 55 (74)
Capacity
kW (HP)
SGDH - D E
Model
E: Speed, Torque, and
Position Control
Power Supply
D: 400V
AC Supply
Phases
3
Servo Amplifiers
SGDH
164

400V Sigma II Servo Systems
SGDH Amplifier Ratings and Specifications
Supply
Input Power
Control Mode
Feedback
Location
Basic Specifications
Structure
Performance
Main Circuit
Control Circuit
Ambient/Storage Temperature
Ambient/Storage Humidity
Vibration/Shock Resistance
Speed Control Range
Load Regulation
**
Voltage
Regulation
Speed
Temperature
Regulation
Regulation
Frequency Characteristics
Accel/Decel Time Setting
Reference Voltage
Input Impedance
Speed
Reference
Circuit Time Constant
Reference Voltage
Input Impedance
Torque
Reference
Circuit Time Constant
Rotation Direction
Selection
***
***
Three-phase 380 to 480Vac +10% to -15%, 50/60 Hz.
1. 24VDC ±10% to ±15%, 1A (maximum)
2 . 24V
Note: For 22 to 55kW units only, the power supply for the optional dynamic brake
(DB) contactor is made from the control circuit power supply. If DB operation is necessary when the power interruption occurs, maintain the DC24V while the DB operates. If 5 times inertia is attached and a standard DB resistor is used, DB operation
time is approximately 2 to 5 seconds.
Three-phase, full-wave rectification IGBT PWM (sinusoidal commutation)
Serial incremental encoder, absolute encoder
*
0 to 55°C / -20 to 85°C
90% or less (no-condensing)
1. 4.9m/s2 / 19.6m/s2 for 500W to 15kW units
2 . 9.8m/s
Cyclic shock resistance is 29m/s
Base mounted (duct ventilation available as option) and flat mount type
1 : 5000 (The lowest speed of the speed control range is the speed at which the
servomotor will not stop with a rated torque load.)
0% to 100%: 0.01% max. (at rated speed)
Rated voltage ±10% : 0% (at rated speed)
25 ± 25°C : 0.1% maximum (at rated speed)
400Hz (at JL = JM)
Note: 100 Hz (J
0 to 10s (Can be set individually for acceleration and deceleration).
±6VDC (variable setting range: ±2 to ±10VDC) at rated speed (forward rotation with
positive reference); input voltage: ±12V (maximum)
Approximately 14kΩ
—
±3VDC (Variable setting range: ±1 to ±10V) at rated torque (forward rotation with
positive reference), input voltage: ±12V
Approximately 14kΩ
Approximately 47μs
Uses P control signal
±10%, 40W for 22 to 55kw units
DC
2
(1G) / 49m/s2 (5G) for 22 to 55kW units
= JM) for 22 to 55kW systems
L
2
(3G)
DC
(maximum)
Speed Selection
Reference
Speed/Torque Control Mode
Notes: * Use the servo amplifier within the ambient temperature range. When enclosed, the temperatures inside the cab-
Contact Speed
Input Signal
inet must not exceed the specified range.
** Speed regulation is defined as follows:
Speed regulation
*** Forward is clockwise viewed from the non-load side of the servomotor, (counterclockwise viewed from the load
and shaft end).
no-load motor speed - full-load motor speed()
-------------------------------------------------------------------------------------------------------------------------x100%=
Forward/reverse rotation current limit signals are used (first to third speed selection). When both signals are OFF, the motor stops or enters another control mode.
rated motor speed
SGDH
Servo Amplifiers
165

400V Sigma II Servo Systems
Ratings and Specifications (cont’d)
Bias Setting 0 to 450rpm (setting resolution: 1rpm)
Feed-forward Compensation 0 to 100% (setting resolution: 1%)
Position Complete Width Setting 0 to 250 reference units (setting resolution: 1 reference unit)
Performance
Sign + pulse train, 90° phase difference 2-phase pulse (phase A + phase B), or
CCW + CW pulse train
+12V (With built-in 1kW resistor)
Phases A, B and C: Line driver output
Phase S: Line driver output (Only when absolute encoder is used)
Servo ON, P control (or forward/reverse rotation in contact input speed control
mode), forward rotation prohibited (P-OT), reverse rotation prohibited (N-OT),
alarm reset, forward rotation current limit, and reverse rotation current limit (or
contact input speed control)
Input
Signal
Positioning Control Mode
I/O Signals
Control SIgnal CLEAR (input pulse form identical to reference pulse)
Built-in Open Collector Power Sup-
ply
Output Form
Output
Frequency Dividing Ratio Any
Position
Sequence Input
Type
Pulse Buffer Line driver (+5V level), open collector (+5V or +12V level)
Signal
Reference
Pulse Frequency Maximum 500/200kpps (line driver/open collector)
*
— Servo alarm, 3-bit alarm codes
Sequence
Dynamic Brake (DB) Activated at main power OFF, servo alarm, servo OFF or overtravel
Regenerative Processing
Overtravel (OT) Prevention
Protection
LED Display POWER, CHARGE, five 7-segment LEDs (built-in digital operator functions)
Analog Monitor (5CN)
Built-in Functions
Servo Amplifiers
SGDH
Communication
Others
Configurable: (Any 3 of these sig-
Output
nals)
Interface
1 : N Communication N can be up to 14 when RS-422A port is used.
Axis Address Setting Set via user parameters
Functions
Positioning complete (speed coincidence), servomotor rotating, servo ready,
current limit, brake release, warning, and near position signals
Incorporated. For 6 to 55 kW units, external regenerative resistor must be
mounted.
Motor decelerates or coasts to a stop, or is stopped by a dynamic brake. This
requires optional dynamic brakes for 22 to 55kW units.
Overcurrent, overload, regenerative error, main circuit voltage error, heat sink
overheat, power open phase, overflow, overspeed, encoder error, encoder disconnected, overrun, CPU error, parameter error.
Built-in analog monitor connector to observe speed, torque, and other reference
signals
Speed: 1V/1000rpm
Torque 1V/rated torque
Pulses remaining: 0.05V/reference units or 0.05V/100 reference units
Digital operator (mount type or hand-held)
RS422A port such as person computer (RS-232C port can be used if some conditions are met).
Status display, user constant setting, monitor display, alarm traceback display,
jogging, autotuning, speed/torque reference signals, other graphing functions,
etc.
Reverse rotation connection, home position search, automatic servomotor ID,
DC reactor connection terminal for high power supply frequency control.
Note: * The built-in open collector power supply is not electrically isolated from the control circuit in the servo amplifier.
166