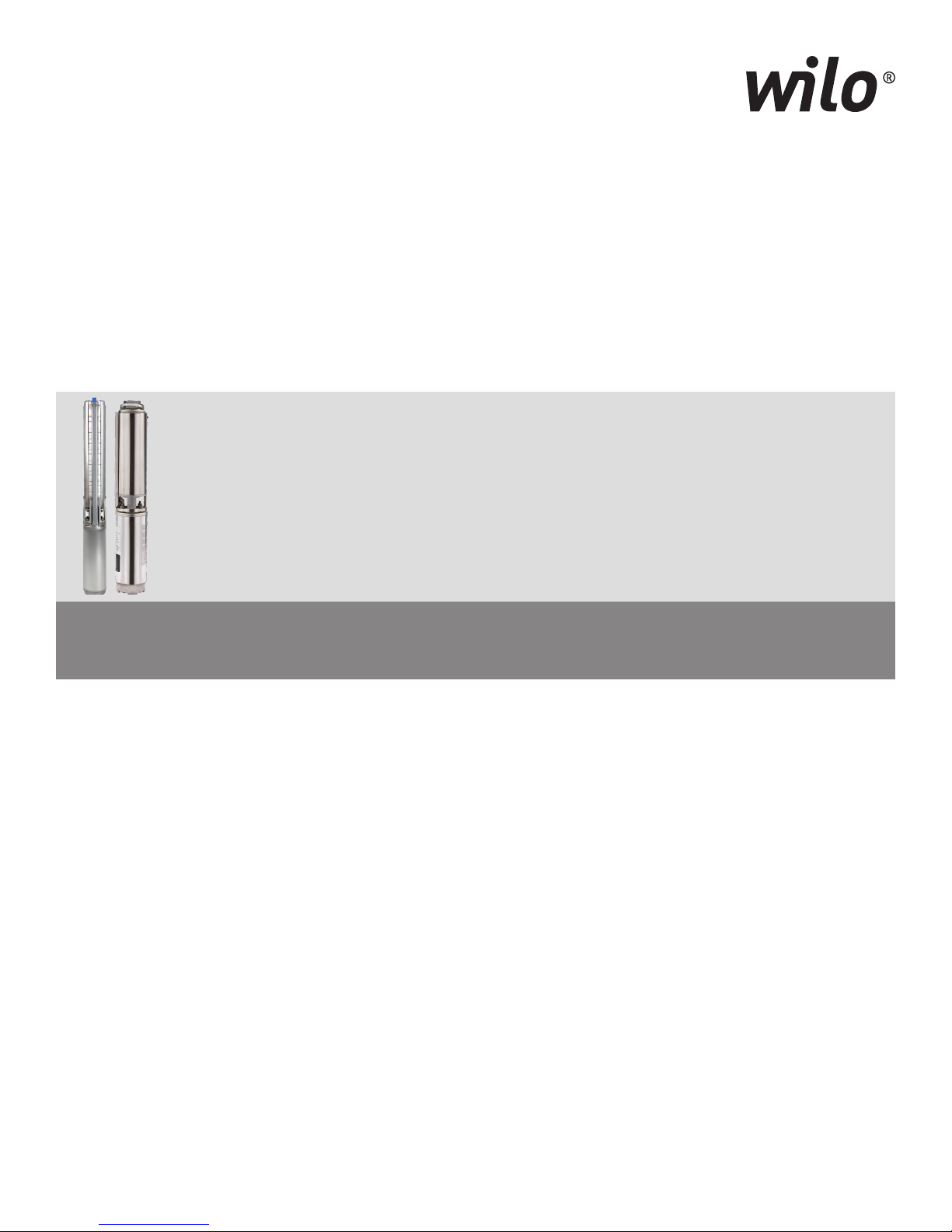
Wilo TWI & TWU
4” Submersible Well Pumps
Installation and operating instructions
50-18-002-0817
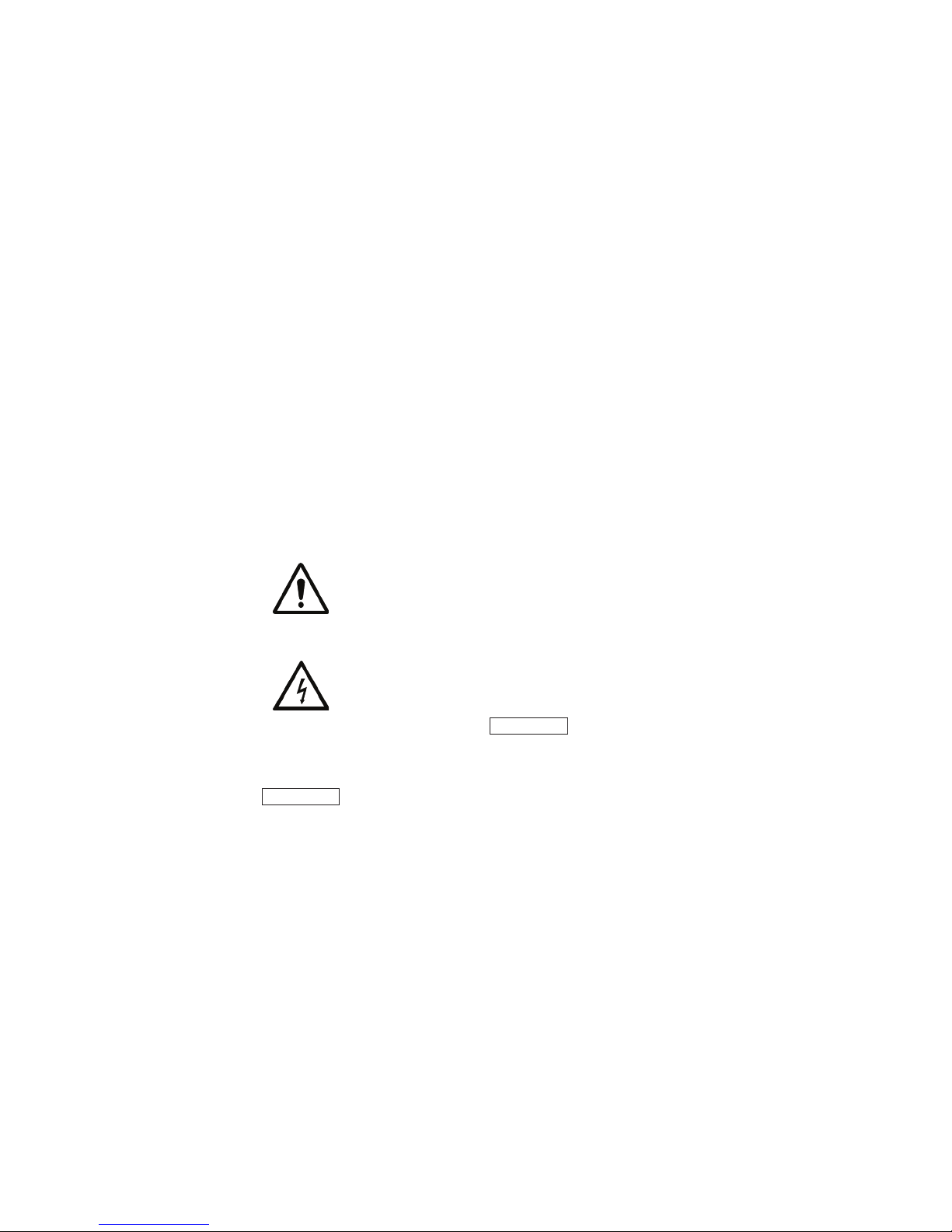
1 General Information
2.4 Safety precautions for the operator
1.1 Uses
Submersible pumps of the TWI series are suitable for
drawing groundwater from deep wells, for industrial use and
for supplying water.
1.2 Product Range
1.2.1 Rating Range
1.2.2 Technical Characteristics
• Temperature range: 38°F to 85°F
• Max. Flow rate: 115 GPM
• Max. immersion depth: 900 Ft.
• Maximum permissible sand content: 50 g/ml
• Pressure pipe connection: 1” to 2”, depending on size
of pump
• Max. pump lift: to 1300 ft, depending on size of pump
1 Safety
2.0 Danger symbols used in these operating instructions
Safety precautions in these operating instructions which, if
not followed, could cause personal injury are indicated by
the symbol:
Existing regulations for the prevention of accidents must
be followed. Dangers caused by electrical energy are to be
excluded. Directives issued by the local electrical code and
the local electricity supply companies are to be observed.
2.5 Safety information for inspection and assembly
The operator must ensure that all inspection and installation
work is carried out by authorised and qualied specialists
who have carefully studied these instructions. Work on
the pump/machinery should only be carried out when the
machine has been brought to a standstill.
2.6 Unauthorized modication and manufacture of spare
parts
Alterations to the pump or installation may only be carried
out with the manufacturer’s consent. The use of original
spare parts and accessories authorised by the manufacturer
will ensure safety. The use of any other parts may invalidate
claims invoking the liability of the manufacturer for any
consequences.
2.7 Unauthorized operating methods
The operating safety of the pump or installation supplied
can only be guaranteed if it is used in accordance with
paragraph 1 of the operating instructions. The limiting
values given in the catalogue or data sheet must neither be
exceeded nor allowed to fall below those specied.
when warning of electric voltage with
The following symbol is used to indicate that by ignoring
the relevant safety instructions, damage could be caused to
the pump/machinery and its functions:
ATTENTION!
2.2 Staff Training
The personnel installing the pump must have the
appropriate qualications for this work.
2.3 Risks incurred by failure to comply with the safety
precautions
Failure to comply with the safety precautions could result in
personal injury or damage to the pump or installation.
Failure to comply with the safety precautions could also
invalidate any claims for damages.
In particular, lack of care may lead to problems such as:
• Failure of important pump or machinery functions,
• Personal injury due to electrical, mechanical and
bacteriological causes.
• Damage to property.
3 Transport and interim storage
Upon delivery, please check that the device has survived
the journey undamaged. If you nd any damage, the normal
routine measures are to be initiated with the shipping
company.
ATTENTION!
During transport and in storage the pump must be
protected against moisture, frost and mechanical damage.
Store horizontally in shockproof places.
4 Product and accessory description
4.1 Pump
• Multistage submersible pump with radial or semi-axial
impellers, depending on size of pump, for use in 3” & 4”
bore- holes.
• With built-in check valve.
4.2 Motor
• Consult motor manufacturer’s documentation for more
information.
2 50-18-002-0817
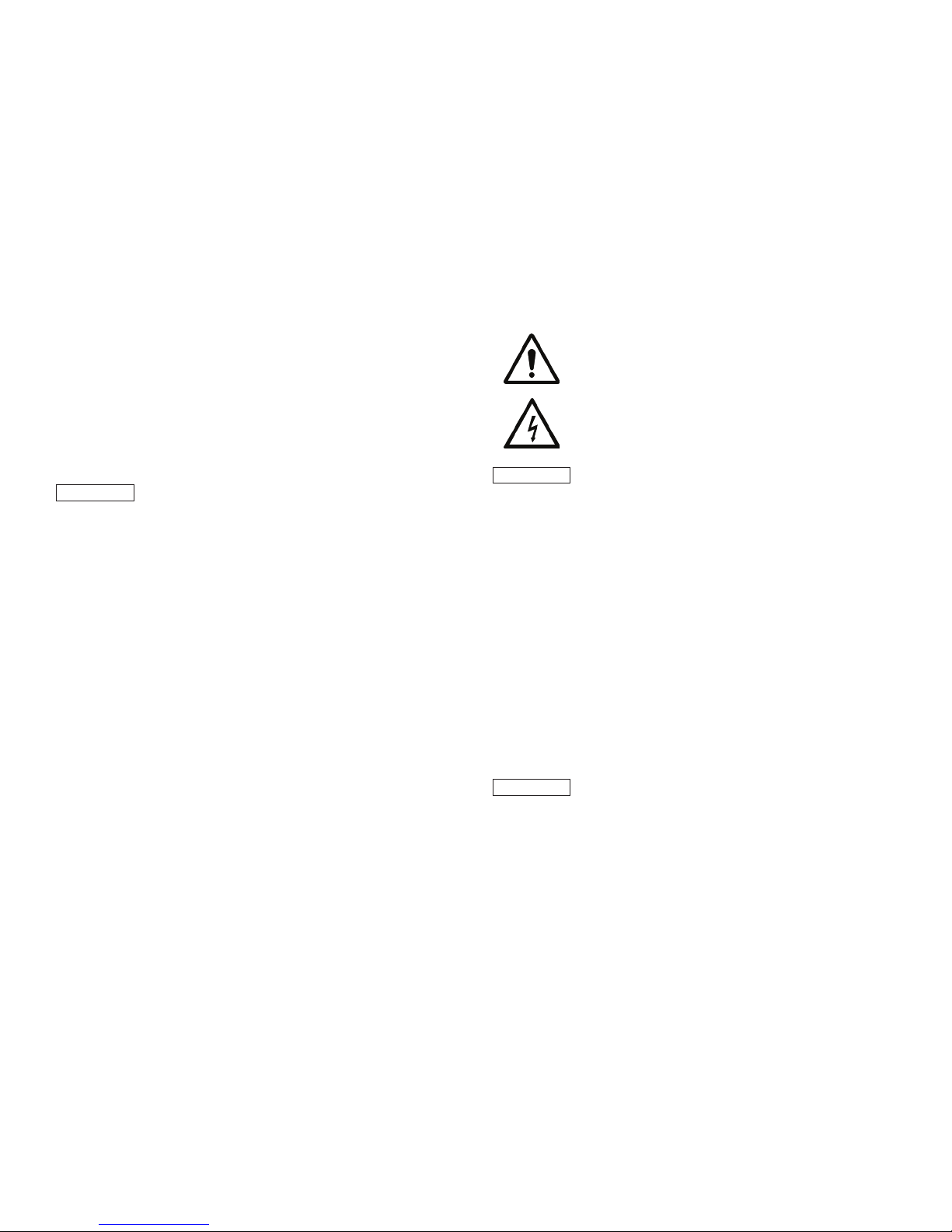
4.3 Accessories
5.3 Electrical Connection
Accessories must be ordered separately.
• Switching/controlling equipment (motor protection +
pump control) assembly
• Float
• Shut-off valves
• Manometer
• Safety valve
• Dry-run
• Electrodes
• Float switch
• Motor cable as assembly (incl. plug)
• Heat-shrink cable connections
• Steel cable (stainless steel)
• Pressure vessel
• Cooling-shroud (stainless steel/PVC)
• Etc.
1 Assembly / Installation
The pump can be operated either vertically or horizontally
(for horizontal position only with a cooling-shroud).
5.1 Assembly
ATTENTION!
• The bore-holes or pump stations must be created/
arranged in accordance with the generally applicable
technical rules.
• Please ensure that the ow of water in the bore-hole or
well is sufcient for the capacity of the pump.
• Ensure that the pump never runs dry and make sure that
even in dry periods the water level never falls below the
pump’s check valve (uppermost position).
In the case of installation in a deep well (well shaft diameter
greater than a bore-hole), a reservoir, horizontal installation
or in a deep well, a cooling-shroud (accessory) must be
tted to the unit to ensure the motor is properly cooled (g.
2, pos.
A).
• It must be ensured that the well shaft in the bore-hole
has a constant internal diameter to allow the pump to be
lowered freely for the entire depth of the shaft.
• Never raise or lower the pump by the electric cable.
• The electrical connection and extension of the motor
cable must take place before the pump is lowered and be
tested/measured to ensure they are working.
• The nal installation position must be guaranteed such
that the pump sits at least 1 foot above the bottom of
the bore-hole or well (g. 1).
• The rating plate must be afxed in the immediate vicinity
of the well head to allow access at all times to the unit’s
technical data.
• Before lowering (and while lowering in deep bore-holes)
the insulation resistance of
• The motor and cable must be measured several times
(min. 2 M).
Electrical work must be carried out by a qualied contractor
strict compliance with local regulations.
The maximum cable length depends on the nominal motor
current and the permissible drop in voltage over the entire
cable length. Consult motor manufacturer’s documentation
for more information.
A faulty electrical connection will result in damage to the
motor.
6 Operation
6.1 Controlling the direction of rotation in 3-phase
installations:
To determine the correct direction of rotation for the pump,
only the shutoff pressure at the well head needs to be
checked, taking into account that the correct motor
direction of rotation generates the greater pressure.
• To rectify an incorrect direction of rotation swap any
two phases in the switchbox or motor protection switch.
ATTENTION!
See motor manufacturer’s documentation for more
information.
6.2 Operation
The pump must never run while dry, not even for brief
periods.
7 Maintenance
Before carrying out any maintenance work, switch off the
pump and ensure that it cannot be switched on again by
unauthorized people. Never carry out work on a running
pump.
No special maintenance is required during normal operation.
7.1 Spare parts
ATTENTION!
Please contact Wilo Customer Service directly for spare
parts, standard replacements or repairs to the hydraulic
pump parts.
5.2 Hydraulic connections (see g. 1)
• Connections to pipes. 1” through 6” depending on size
of pump. In the case of larger types (8” / 10”), the pump
is only connected directly to the pipework.
• It is recommended that a check valve be tted every
200 Feet to the surface of the borehole.
3Wilo TWI - Installation and Operation Manual