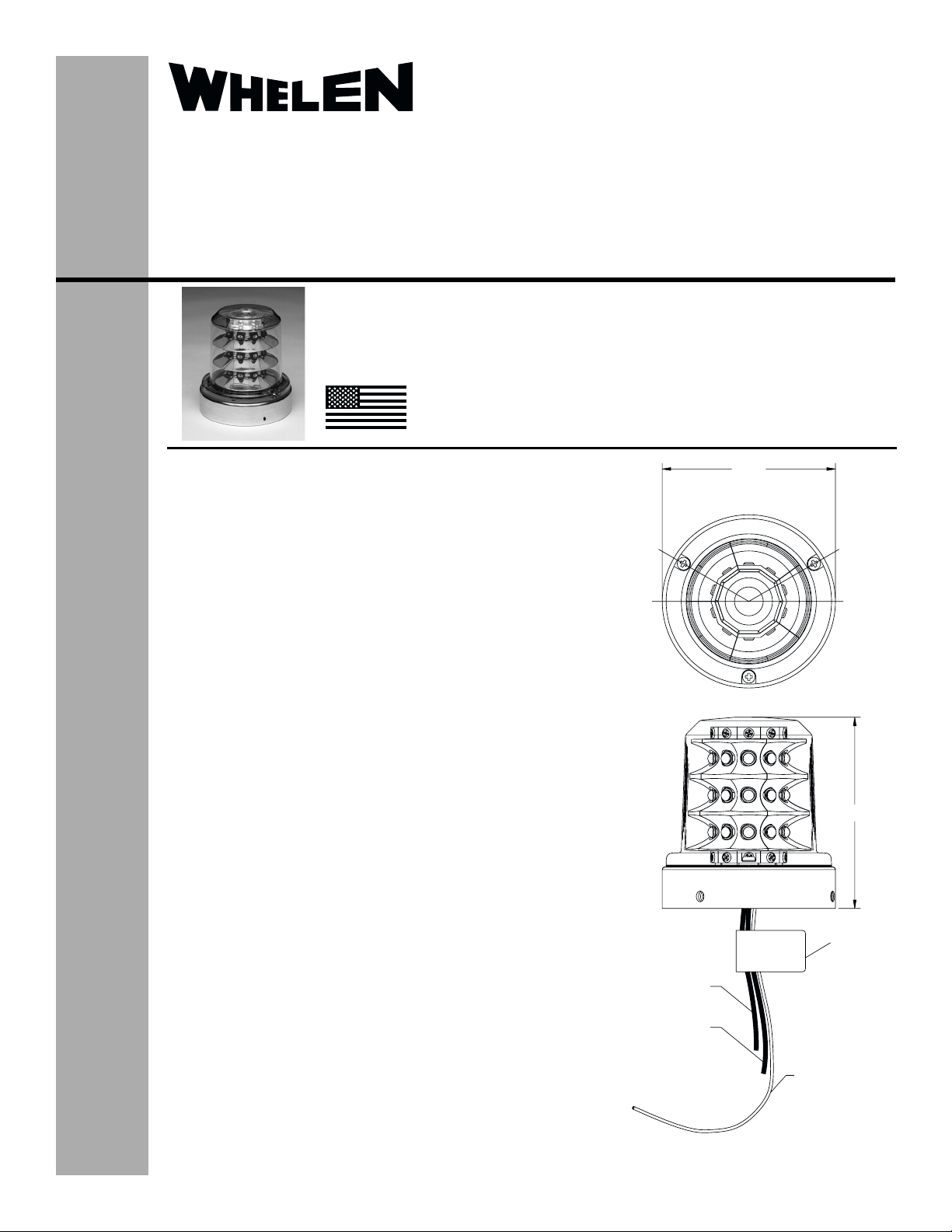
®
ENGINEERING COMPANY INC.
Route 145, Winthrop Road,
Chester, Connecticut 06412
Phone: (860) 526-9504
Fax: (860) 526-2009
Internet: www.whelen.com
Sales/Service e-mail: aviation@whelen.com
Installati on Guide:
Model 70900( )-series
Model 7090004
7090005
P/N:01-0770900-04
01-0770900-05
LED Flashing Anti-Collision
Light Assembly
TSO-C96a CLASS III
APPROVED
MADE IN THE U.S.A.
OPERATING INSTRUCTIONS:
Operational Voltage:. . . . . . . . . . . 14 / 2 8 VD C no m i n a l
Average Input Current:. . . . . . . . . 0.85 / 0.425 Amps
Peak Input Current:. . . . . . . . . . . . 4.5 / 2.25 Amps @ .25 Seconds
The Model 70900 series LED anti-collision light assembly meets the
requirements of FAR 91.205(c)(3).
CONTINUED AIRWORTHINESS: The 70900 series LED anti-collision
light assembly is designed with 10 vertical columns consisting of 3 LEDs
each. Should any one LED or any vertical column fail, the unit must be
repaired or replaced.
INSTALLATION PROCEDURES: The following information is to assist
in the installation of a Whelen LED Flashing Anti-collision Light System.
1. The installation procedure described in the following text will be
confined to a single light installation, but is identical for multiple light
installations.
2. Prepare the aircraft for means to secure the LED Flashing Anticollision Light assembly (see reference AC 43.13-2A, Ch. 9).
3. 14/28 VDC (+) and (-) ground leads equipped with an appropriate
sized breaker to be supplied to the LED Flashing Anti-collision Light
Assembly System. Both leads must be connected by an approved
FAA conne ct ion. Insure that the wire leads and the pressur e venting
tube are all clear of any obstructions and ty-wrap as required. The
pressure venting tube may be trimmed to minimum length of 1” from
base.
4. Install the light assembly by securing to aircraft using #6-3 2 x
3/8” (maximum length) approved hardware. NOTE: Lens mounting
screws installed at 5-7 in./lbs. of torque.
5. Check all avionics systems for interference from this installation.
6. A flight check should be performed by a properly certified pilot.
7. All inverted (bottom) mounted units shall require waterproofing of
the unused mounting holes. An application of single-part silicone
(RTV) or equivalent applied into mounting holes is recommended
(see illustration on page 2). Inverted and/or standard mounted units,
when necessary, may require waterproofing around any open area
where water could get in. Specifically, the lens to the flasher base
assembly, and the flashe r base assembly t o the a ircraft. Note: It is
permissable to drill a 1/8” hole in the center of the lens for bottom
mount units.
8. Update aircraft records, complete Form 337 and obtain FAA field
approval for installation.
Aviation
The conditions and tests required for TSO approval of this
article are minimum performance standards. It is the
responsibility of those installing this article either on or
within a specific type or class of aircraft to determine that
the aircraft installation conditions are within the TSO
standards. TSO articles must have separate approval for
installation in aircraft. The article may be installed only if
performed under 14 CFR part 43 or the applicable
airworthiness requirements.
3.66
4.04±.06
(+)14VDC Red 18GA
Teflon Wire 18”LG
or
(+)28VDC White 18GA
Teflon Wire 18”LG
(-)Ground Black 18GA
Teflon Wire 18”LG
MFG Label
Teflon Tube 18GA
(Pressure Venting)
©2003 Whelen Engineering Company Inc.
Form No.13828D (111505)
Page 1
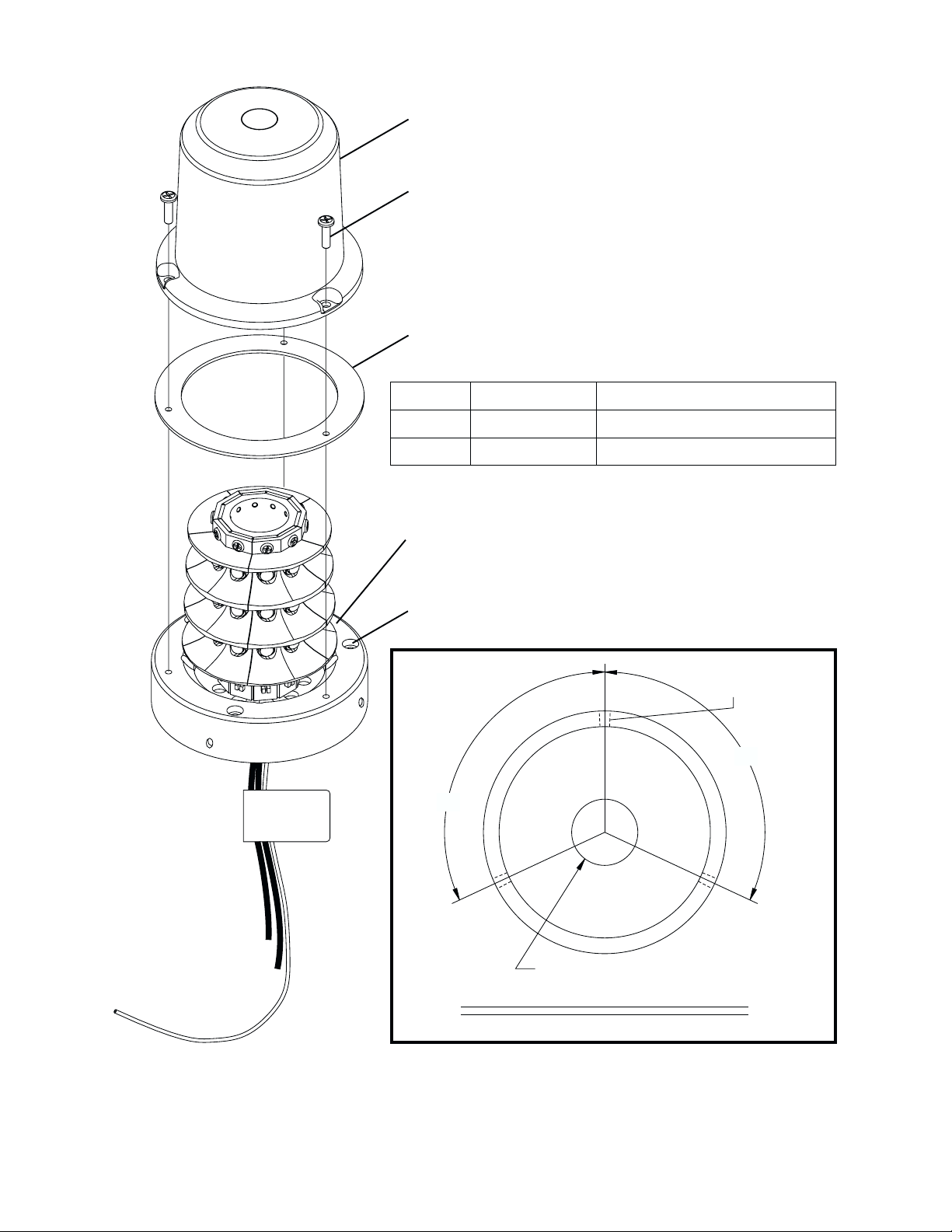
Lens
P/N: 68-4990257A30
Screw
P/N: 14-062216-05M
Gasket
P/N: 38-0250843-00
Model
7090004
7090005
LED Module
P/N : 01-0270918-01
(14V)
(28V): 01-0270918-03
“RTV” required after hardware installation
for inverted (bottom) mounted units
Part Number
01-0770900-04
01-0770900-05
115°
Description
14VDC, No Connector
28VDC, No Connector
(3) #6-32 x 3/8
Thread
115°
1.00” Clearance for wires
Typical Mounting Hole Pattern
Page 2