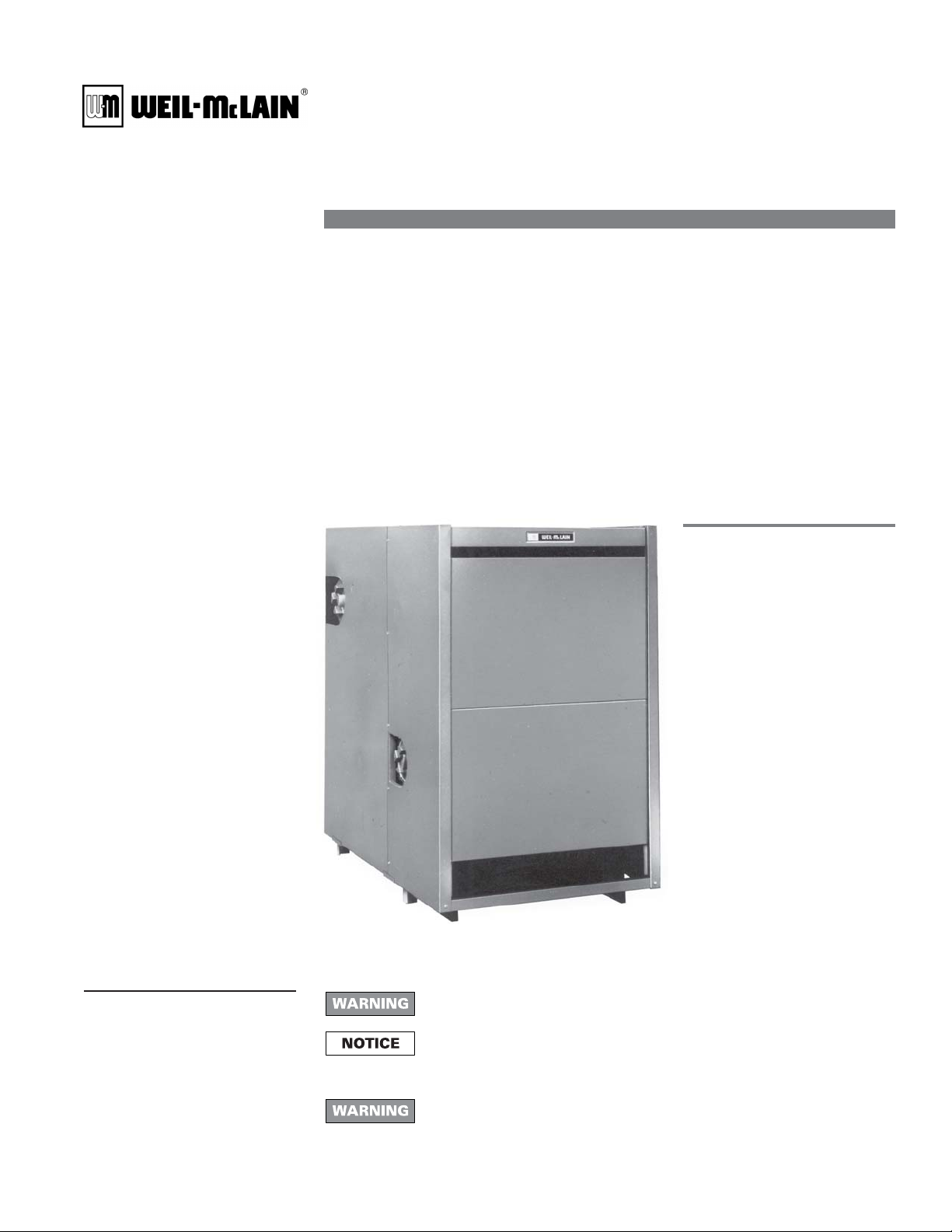
LGB
Gas–fired boiler
Control Supplement
LGBLGB
LGB
LGBLGB
-6 -6
-6
-6 -6
LGB LGB
toto
LGB
to
toto
LGB LGB
-23-23
-23
-23-23
Series 2 – Natural gas
Universal Control System
Contents
I. Installation ..................... 2
II. Gas piping ...................... 4
III. Wiring ............................ 5
Sequence of operation ....... 5
Wiring procedure ............... 8
IV.Operating instructions . 9
V. Verification testing ..... 10
VI.Parts list....................... 11
These terms are used throughout this
manual to bring attention to the
presence of hazards of various risk
levels or to important information
concerning the life of the product.
Indicates presence of hazards that can cause severe personal injury, death or
substantial property damage.
Indicates special instructions on installation, operation or maintenance that
are important but not related to personal injury or property damage.
This Control Supplement must only be used by a qualified installer/service
technician. Read these instructions completely before beginning the
installation. Failure to follow these instructions can cause severe personal
injury, death or substantial property damage.
Part Number 550-141-916/0304
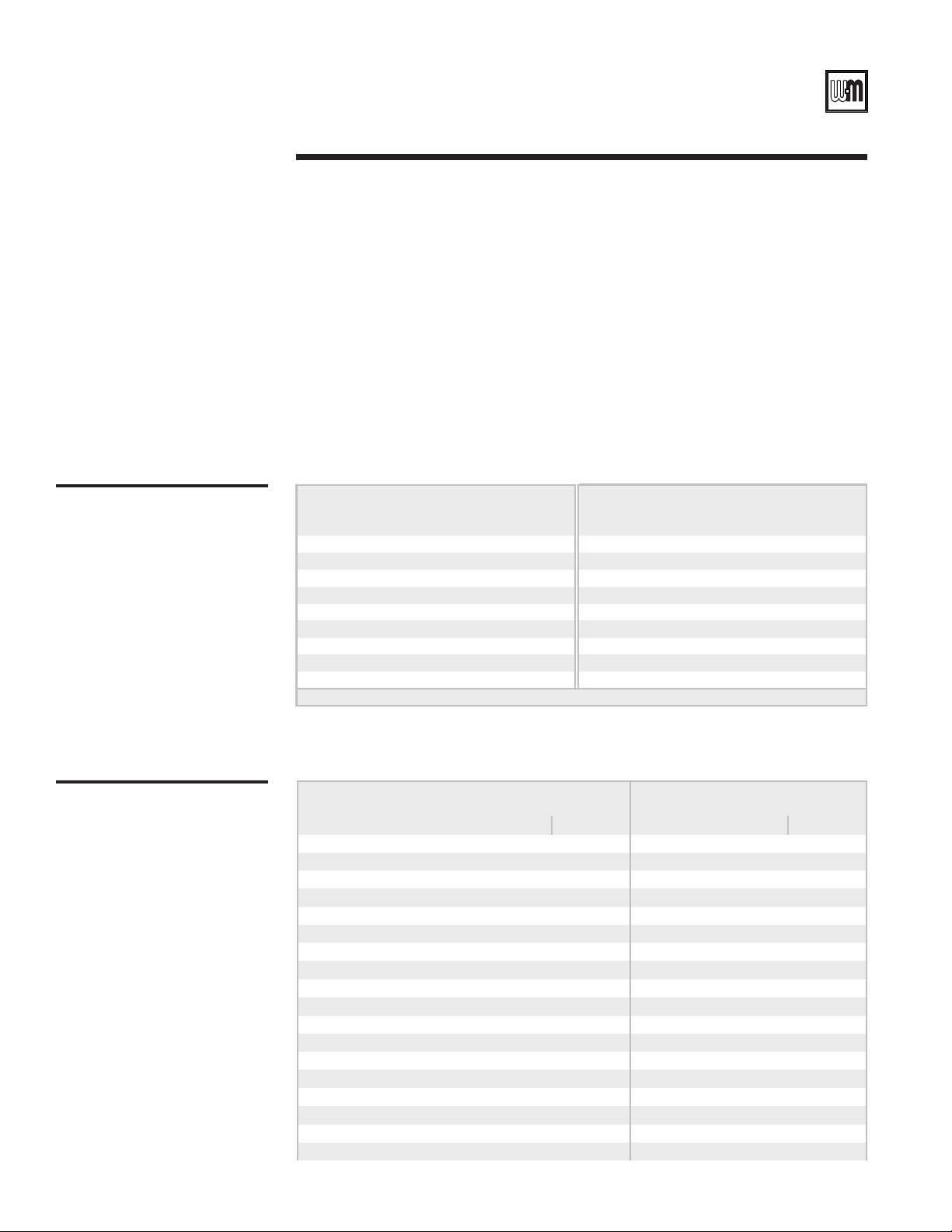
LGB-6 to LGB-23
I Installation
1. Assemble pilot burner and flame sensor to main burners with pilot brackets. See Figures 1
and 2 (page 3). Install ground wiring as shown in Figures 1 and 2 (page 3).
2. Reinstall burner assemblies. See Table 1, below for pilot burner and flame sensor locations.
3. Install gas controls and ignition control panel as shown in Table 2, below and Figure 5 on
page 10.
4. LGB-21 through LGB-23 require High Gas Pressure Switch Control Carton - 7" and 5" W.C.
Attach pressure switch to interior jacket panel. See Figure 5 on page 10.
5. Canada only - mount rating plate on interior jacket panel.
Series 2 – Control Supplement
Table 1
Pilot burner and flame sensor
locations
Table 2
Gas control arrangement
Boiler
Model
Number
LGB-6 2--9--LGB-15 2161327
LGB-7 2--11--LGB-16 2181529
LGB-8 2--13--LGB-17 2181531
LGB-9 2--15--LGB-18 2201633
LGB-10 2--16--LGB-19 2201634
LGB-11 2--16--LGB-20 2221636
LGB-12 2--16--LGB-21 2221636
LGB-13 2141123LGB-22 2241638
LGB-14 2161325LGB-23 2241638
* From le f t burner
Boiler
Model
Number
LGB-6 A and B 1" -- A and B 1 ¼" --
LGB-7 A and B 1" -- A and B 1 ¼" --
LGB-8 C and D 1" -- C and D 1 ¼" --
LGB-9 C and D 1" -- C and D 1 ¼" --
LGB-10 E, F and G 1 ¼" -- E 1 ½" --
LGB-11 E, F and G 1 ¼" -- F and G 2" --
LGB-12 E, F and G 1 ¼" -- F and G 2" --
LGB-13 H 1"1"H1 ¼"1 ¼"
LGB-14 I 1"1"I 1 ¼"1 ¼"
LGB-15 J 1"1"J 1 ¼"1 ¼"
LGB-16 J 1"1"J 1 ¼"1 ¼"
LGB-17 J 1"1"J 1 ¼"1 ¼"
LGB-18 K 1 ¼" 1" K 1 ½" 1 ¼"
LGB-19 L 1 ¼" 1 ¼" M 1 ½" 1 ½"
LGB-20 L 1 ¼" 1 ¼" N 2" 1 ½"
LGB-21 L1 ¼"1 ¼"O2"2"
LGB-22 L1 ¼"1 ¼"O2"2"
LGB-23 L1 ¼"1 ¼"O2"2"
Flame Sensor* Pilot Burner*
No. 1 No. 2 No. 1 No. 2 No. 1 No. 2 No. 1 No. 2
7"
W.C.
Carton
Inlet Pipe Size
Left base Right base Left base Right base
Boiler
Model
Number
Flame Sensor* Pilot Burner*
5"
W.C.
Carton
Inlet Pipe Size
2
Part Number 550-141-916/0304
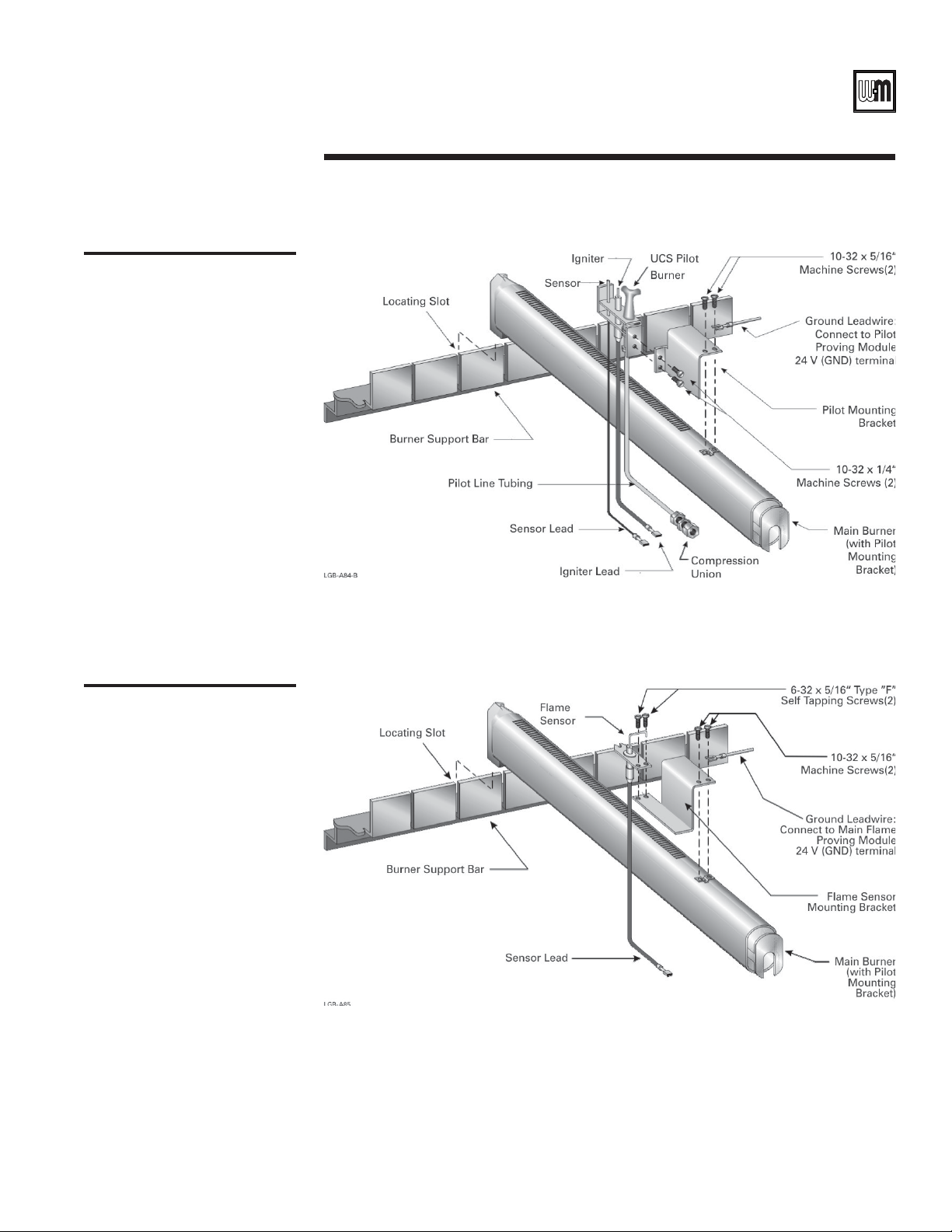
I Installation – continued
Figure 1
Pilot burner assembly, typical
Universal Control System – Natural gas
Figure 2
Main flame sensor assembly
Part Number 550-141-916/0304 3
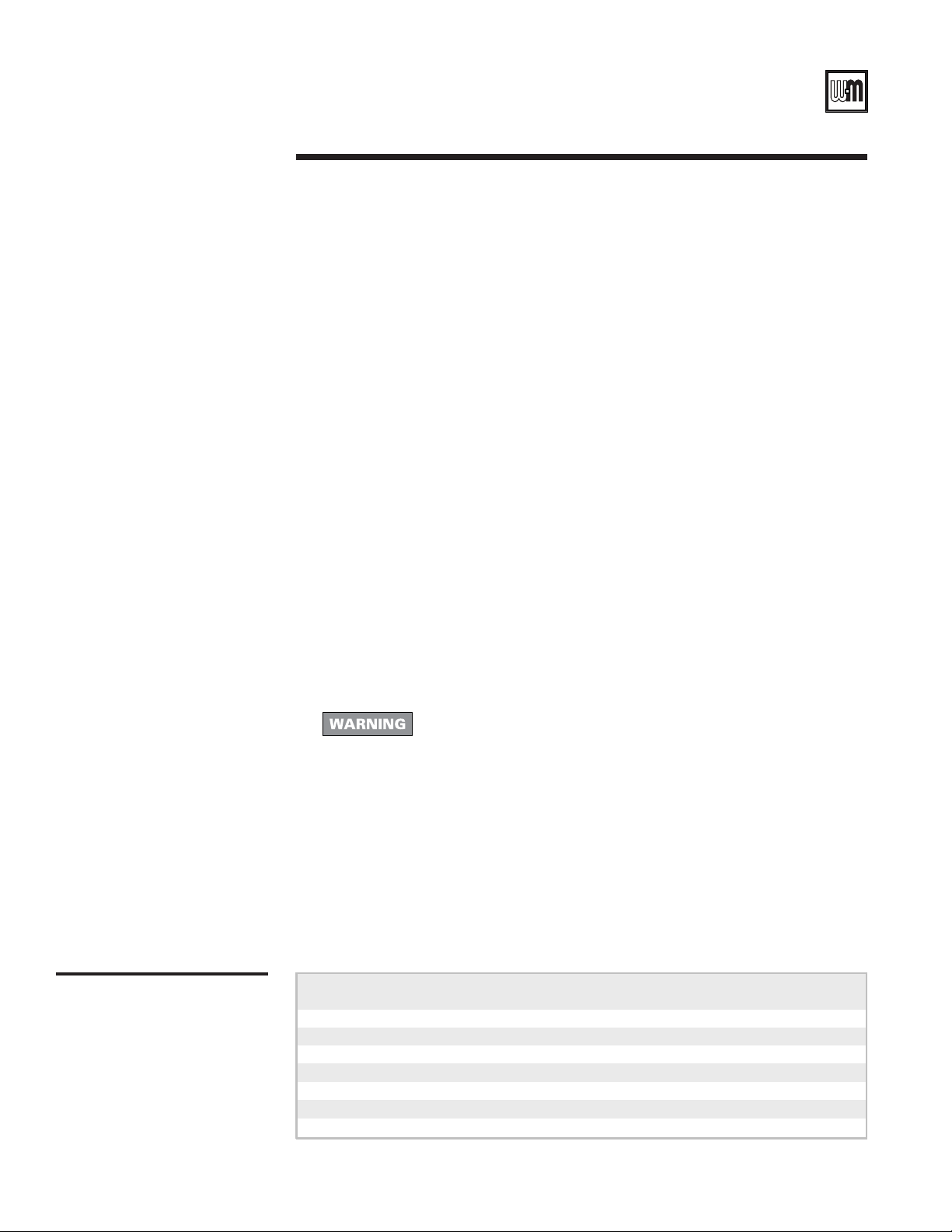
LGB-6 to LGB-23
II Gas piping
1. Size gas piping considering —
a. Diameter and length of gas supply piping.
b. Number of fittings.
c. Maximum gas consumption (including any possible future expansion).
d. Allowable pressure drop from gas meter outlet to boiler. For pressure drops, see
ANSI-Z223.1 – latest edition. Canadian installations must comply with B149.1 or
B149.2 Installation Code.
2. Size natural gas piping from Table 3, below. Size piping to provide proper inlet pressure to
gas valve when operating at rated input.
a. Inlet gas pressure to manual main shut-off gas valve —
minimum 7" W.C. standard (5" on special order) – maximum 13" W.C.
b. If pressure to gas valve exceeds 13" W.C., install positive dead-end lockup gas pressure
regulator upstream of hand valve.
c. To obtain approximate cubic feet per hour, divide input (BTU/HR) by 1000.
3. Remove gas supply knockout disc from jacket panel.
4. Follow good piping practices.
5. Pipe joint compound (pipe dope) must be resistant to corrosive action of liquefied
petroleum gases. Apply sparingly only to male threads of pipe joints.
6. Install drip leg at inlet of gas connection to boiler. Where local utility requires, extend drip
leg to floor.
7. Install ground joint union when required for servicing.
8. Support piping by hangers, not by boiler or its accessories.
9. Purge all air from supply piping.
10. Before operating boiler, check boiler and its gas connections for leaks.
Do not check for gas leaks with an open flame – BUBBLE TEST. Failure to
use bubble test or test for leaks can cause severe personal injury, death or
substantial property damage.
a. Close manual main shut-off valve during any pressure testing at less than 13" W.C.
b. Disconnect boiler and gas controls from gas supply piping during any pressure test
greater than 13" W.C.
11. Set gas pressure switch as follows or to local inspector’s requirements (LGB-21 through
LGB-23 only):
a. High – 14" W.C.
12. Canada only - manual main shut-off valve must be identified by installer.
Series 2 – Control Supplement
Table 3
Natural gas supply pipe sizing
4
Pipe
Size
1 ¼" 1,050 730 590 500 440 360 305 250
1 ½" 1,600 1,100 890 760 670 545 460 380
2" 3,050 2,100 1,650 1,450 1,270 1,020 870 710
2 ½" 4,800 3,300 2,700 2,300 2,000 1,650 1,400 1,130
3" 8,500 5,900 4,700 4,100 3,600 2,900 2,500 2,000
4" 17,500 12,000 9,700 8,300 7,400 6,000 5,100 4,100
*Include measured length of gas supply piping and allowance in feet for number and size of fittings.
*Pipe length, in feet (Natural Gas capacities, listed in MBH)
10 20 30 40 50 75 100 150
Part Number 550-141-916/0304