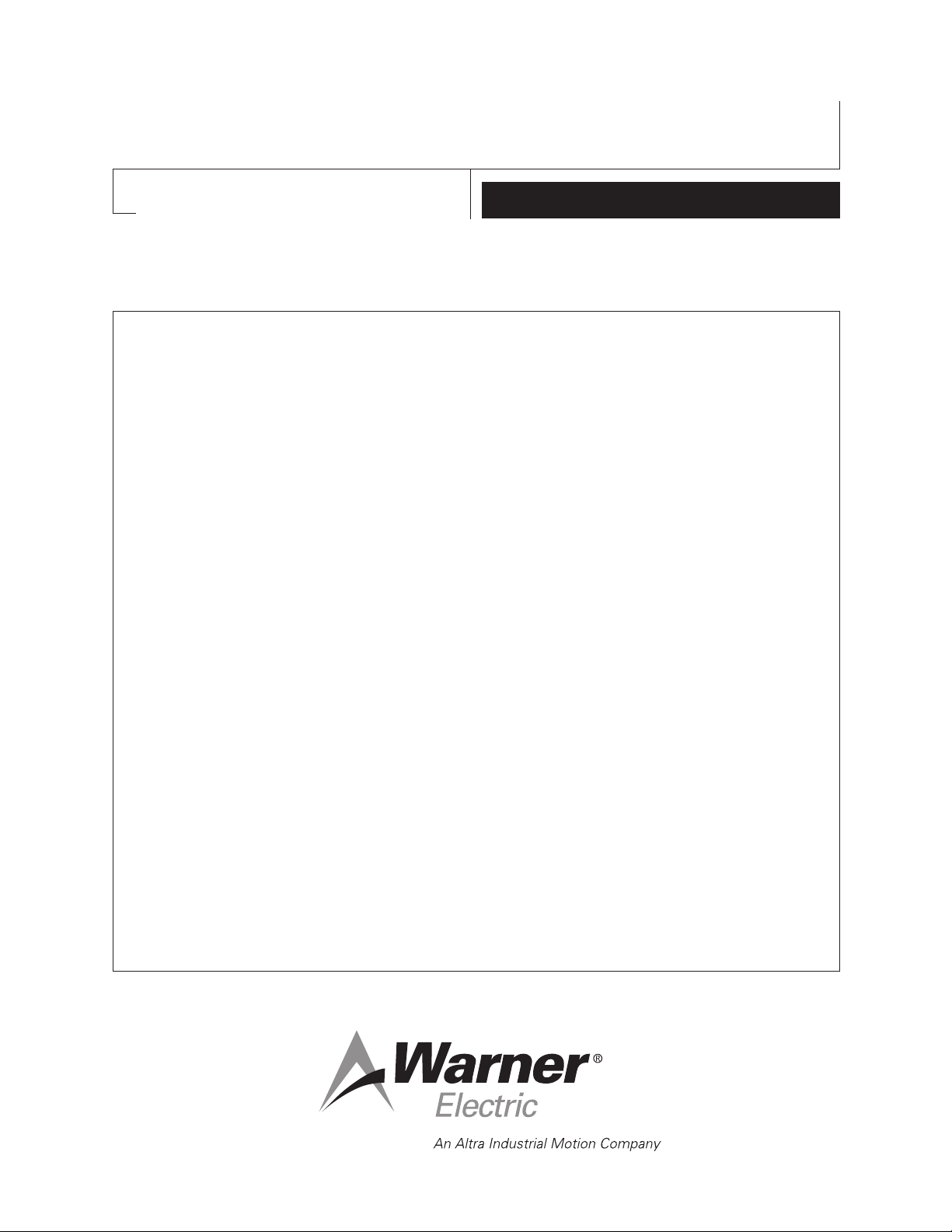
Electromagnetic Particle Clutches and Brakes
Models: POC, PHC-R, POB and PTB-BL3
P-223-1
819-0368
Installation Instructions
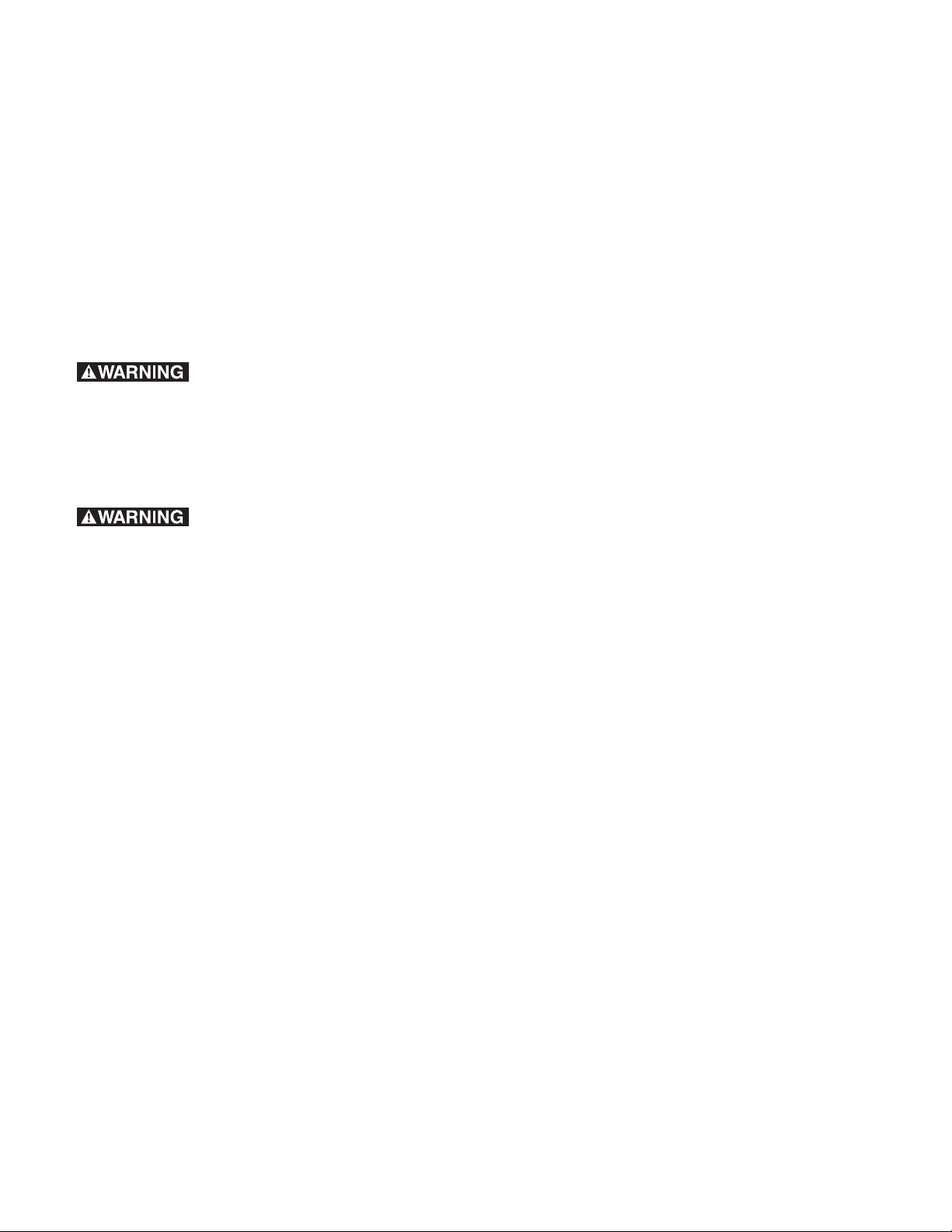
2
Warner Electric • 800-825-9050 819-0368
Contents
Introduction . . . . . . . . . . . . . . . . . . . . . . . . . . . 2
Installation Instructions . . . . . . . . . . . . . . . . 3-6
Electrical Data . . . . . . . . . . . . . . . . . . . . . . . . . 7
Overhung Load Data . . . . . . . . . . . . . . . . . . . 8
Start Up . . . . . . . . . . . . . . . . . . . . . . . . . . . . . . 9
Maintenance . . . . . . . . . . . . . . . . . . . . . . . . . . 9
Mechanical Data . . . . . . . . . . . . . . . . . . . . . . 10
Dimensions. . . . . . . . . . . . . . . . . . . . . . . . 11-16
Warranty . . . . . . . . . . . . . . . . . . . . . . Back Page
Introduction
This service manual provides information
required for installing, wiring, and maintaining
Warner Electric Magnetic Particle clutches and
brakes. Dimensions and specifications are also
included. The models covered in this service
manual include POC and PHC-R clutches and
POB and PTB brakes. For selection information,
please refer to your Warner Electric Tension
Control Sytems Catalog.
Warner Electric Magnetic Particle clutches and
brakes provide smooth and controllable torque
for a variety of torque and tension control applications. They also provide excellent performance for cycling and positioning applications.
Quick response is achieved by applying full
rated voltage. Lower voltage can be applied for
softer engagements. Extremely accurate tension
control can be achieved with an appropriate
Warner Electric tension control for electric
brakes and clutches.
Failure to follow these
instructions may result in product damage,
equipment damage, and serious or fatal
injury to personnel.
Make sure all power is turned
off to this equipment when installing, as
injury (or even death) may result from contact
with live wires or rotating shafts.
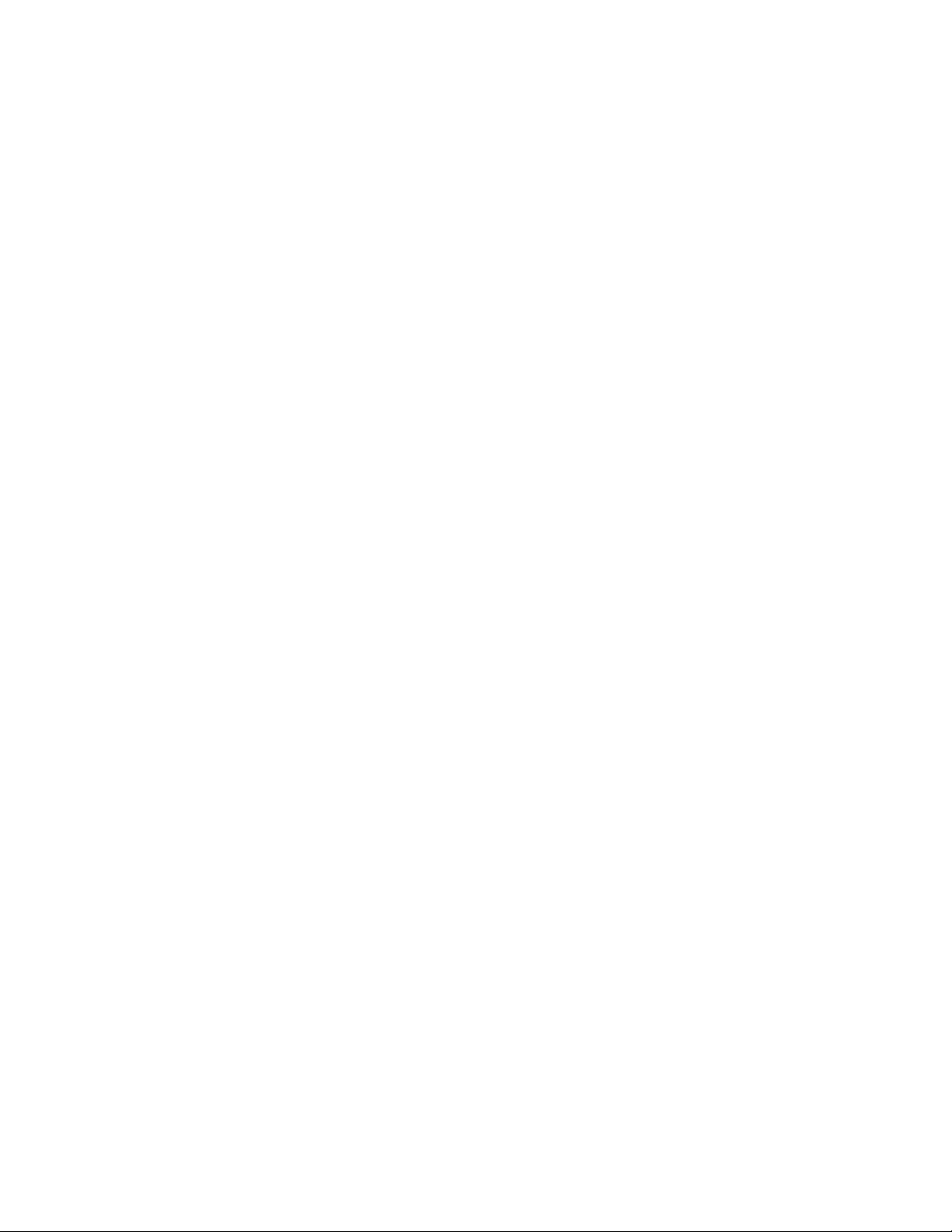
3
Warner Electric • 800-825-9050 819-0368
Installation Instructions
Introduction
Verify the model of your clutch or brake by
checking the label before proceeding with these
instructions. POC and PHC-R designate clutch
models and POB and PTB are brakes. All models of POC clutches are face mounted (except
size 80, which is foot mounted) and have male
input and output shafts. See Figures 1 and 2.
The PHC-R clutch is designed to be shaft
mounted and is ideal for "parallel shaft" applications. It has a hollow bore and slides on the output shaft. An input hub with flange is provided
for mounting a pulley or sprocket. An integral
fan rotates with the input for additional cooling.
See Figure 3.
POB and PTB-BL3 brakes are face mounted
with male input shafts. Like the POC's, only the
size 80 is foot mounted. The major difference
between PTB-BL3 and POB brakes is that PTBBL3's utilize a patented heat pipe cooling
method that provides heat dissipation several
times greater than conventional cooling. See
Figures 4, 5, and 6 for mounting information on
POB's and PTB-BL3's.
Pre-Mounting
Note: Unit performance can be affected by
prolonged exposure to humid environments.
Please store in a dry location.
Note: The equipment covered by this service
manual must be installed in accordance with
these instructions. Failure to do so may damage the equipment and void the warranty.
1. Remove the Magnetic Particle unit from its
shipping carton and inspect it thoroughly to
ensure that it has arrived in good condition.
When handling, please take care not to damage the unit’s lead wires or terminal block.
2. Check the input shaft/hub to make sure it
can be rotated by hand. On clutch assemblies, hold the output stationary while turning
the input. The powder inside the unit may
settle due to shock and vibration incurred
during shipping, making rotation difficult. This
is easily remedied by turning the unit upside
down and gently tapping the housing to
loosen the powder. Do not hit shaft. See
page 10 for nominal drag torque values.
3. Make sure the location chosen for mounting
will not expose the unit to water or oil. If
water or oil enters the powder cavity, performance may be affected. If the unit is
mounted next to a gearbox, special care
should be taken to prevent oil from working
its way into the unit.
4. If couplings are to be used in the drive system, the mounting surface must properly
locate the housing to ensure alignment is
within coupling tolerances.
5. When connections are made with pulleys or
sprockets, the overhung load must be verified to be within rating. See page 8 for allowable overhung load information.
Mounting
Note: Do not use excessive force when mount-
ing couplings, pulleys, or sprockets on shafts.
Note: For proper function, magnetic particle
units must be mounted so the shaft is horizontal.
Use the proper mounting method described for
the model being installed.
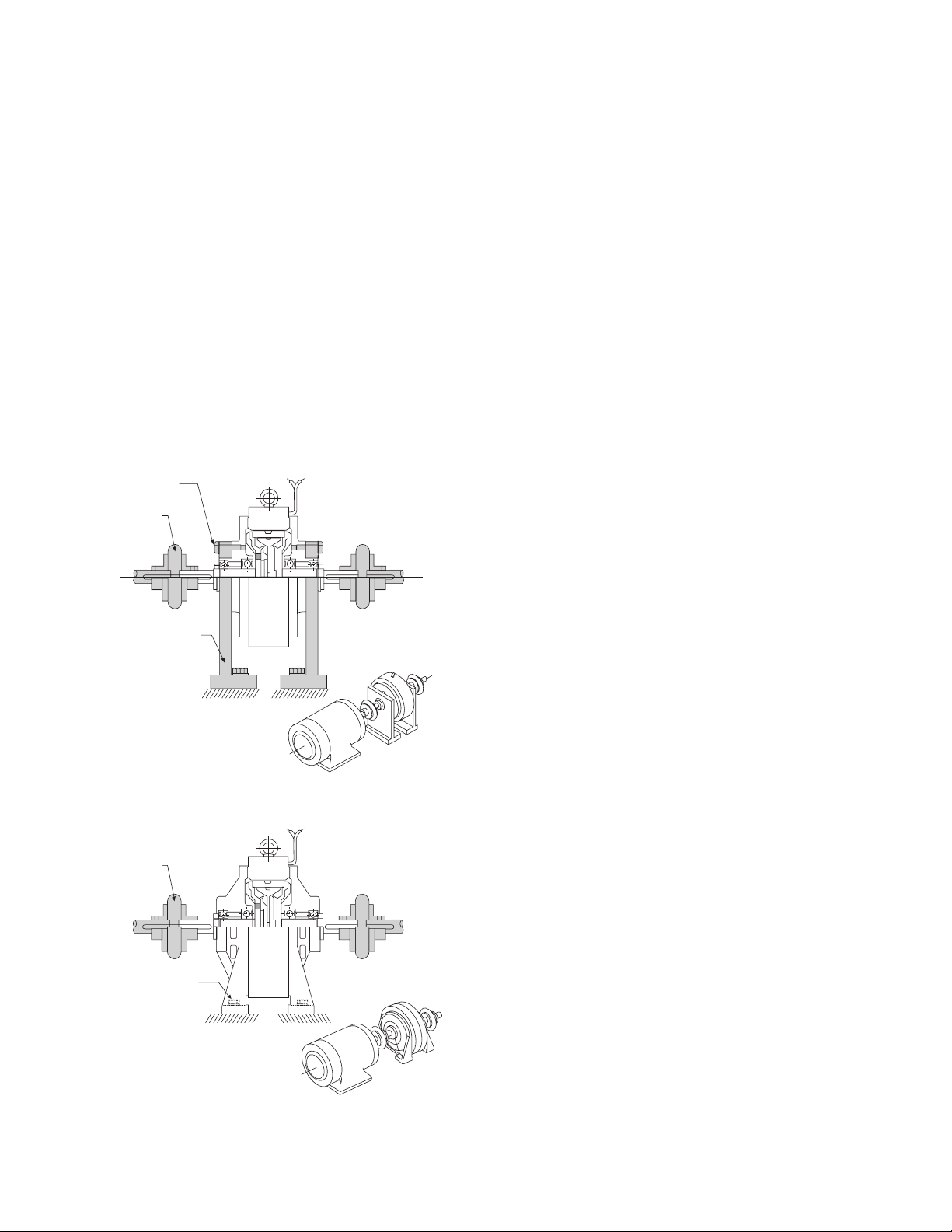
4
Warner Electric • 800-825-9050 819-0368
POC Clutches
For mounting dimensions, see pages 12-13 of
this service manual.
Step 1: Bolt Clutch in Place
Mount the clutch to a vertical surface, using
customer supplied fasteners. For models larger
than size 5, the housing must be secured on
both input and output sides. See Figure 1. A flat
horizontal mounting surface is required for foot
mounted size 80 clutches. See Figure 2.
Step 2: Make Mechanical Connections
Mount couplings, pulleys, or sprockets to the
male shafts per the manufacturers' recommendations. The pulleys, sprockets, and couplings
are customer supplied.
PHC-R Clutches
For mounting dimensions, please refer to page
11 of this service manual.
Step 1: Secure Clutch to Shaft
Slide the clutch on the shaft that is being driven
by the clutch. Secure the clutch with customer
supplied locking collars or other suitable means.
(Mounting the clutch on the shaft that is driving
the clutch is acceptable, but doing so increases
total load inertia.)
Step 2: Attach Antirotation Restraint
Since this is a shaft mounted unit with a stationary field supported by bearings, the field must
be restrained to prevent bearing drag from
pulling on the lead wires. Restraining device
must not preload the bearing.
The field can be restrained with a holding arm
attached to the tapped holes in the field housing
or with capscrews through a mounting bracket
as shown in Figure 3. If bolts are used, first
hand tighten the bolt just enough to take out the
clearance under the head of the capscrew. Then
tighten the locking nut while preventing the bolt
from turning.
Flexible Coupling
Mounting Bracket
Capscrews
Flexible Coupling
Capscrews
Figure 2*
POC-80 (Foot Mount)
*Note: Shaded items are customer supplied.
Figure 1*
POC Clutches (Except POC-80)
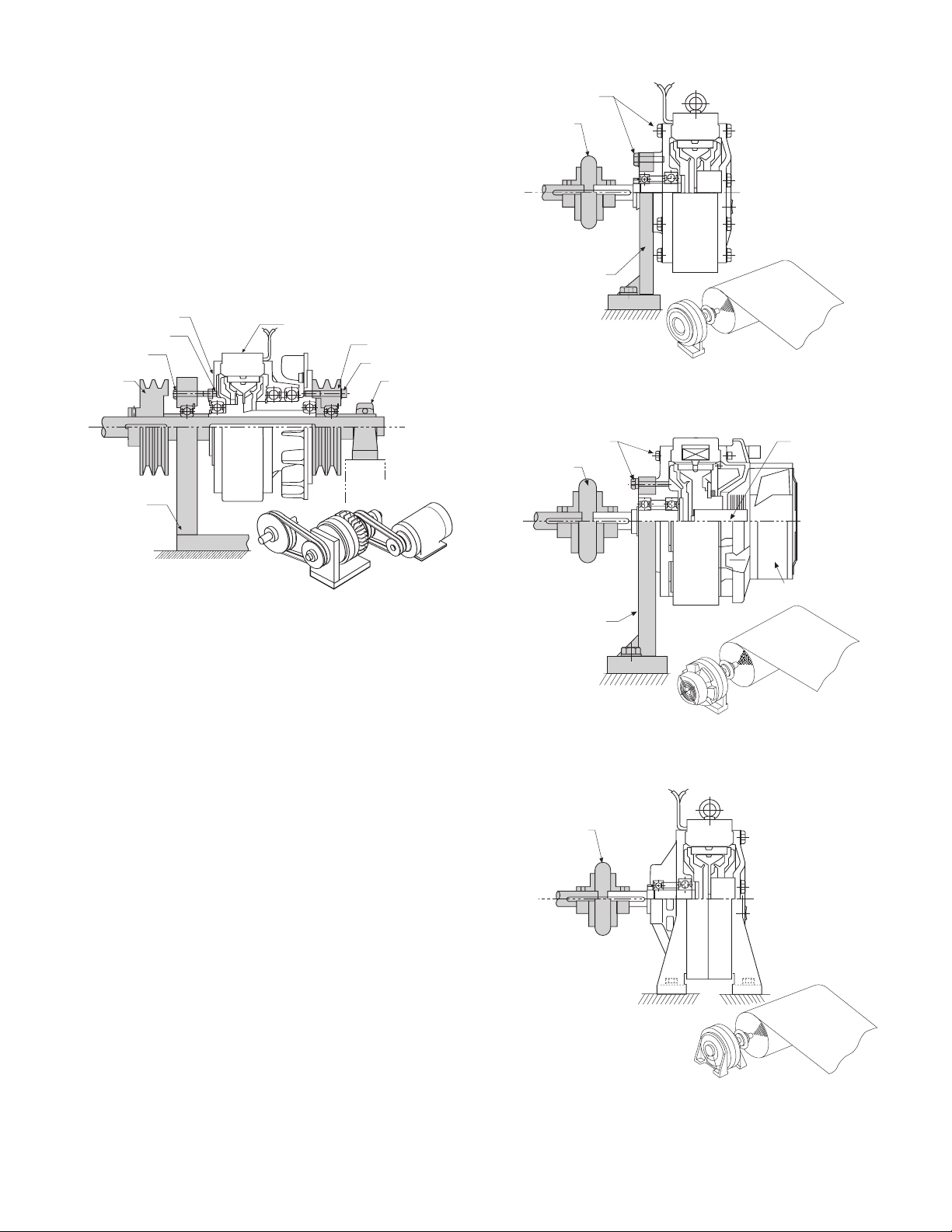
5
Warner Electric • 800-825-9050 819-0368
Step 3: Mount Pulley, Sprocket, or Coupling
Note: If a pulley or sprocket is to be attached
directly to the input hub, bearings should be
installed to support the pulley or sprocket as
shown in Figure 3.
Bolt the pulley, sprocket, or coupling to the
input hub of the clutch. The pulley, sprocket,
and bolts are customer supplied. Do not block
ventilation openings.
Figure 3*
PHC-R Clutches
POB and PTB-BL3 Brakes
For mounting dimensions, please refer to pages
14-16 of this service manual.
Step 1: Bolt Brake in Place
Mount the brake to a vertical surface using customer supplied fasteners. See Figures 4 and 5.
A flat horizontal mounting surface is required for
foot mounted POB size 80 brakes. See Figure 6.
Step 2: Make Mechanical Connections
Mount couplings, pulleys, or sprockets to the
male shafts per the manufacturers' recommendations. The pulleys, sprockets, and couplings
are customer supplied.
Capscrews
Output
Pulley
Mounting
Bracket
Locking
Nuts
Input Pulley
Capscrews
(Field Restraining)
Pillow Block
Field Housing
Ventilation Openings
Flexible
Coupling
Mounting
Bracket
Capscrews
Flexible
Coupling
Mounting
Bracket
Capscrews
Electric Blower
Single-Phase 110V
Heat Pipe
Figure 4*
POB Brakes (Except POB-80)
Figure 5*
PTB – BL3 Brakes
Figure 6*
POB-80 (Foot Mount)
*Note: Shaded items are customer supplied.
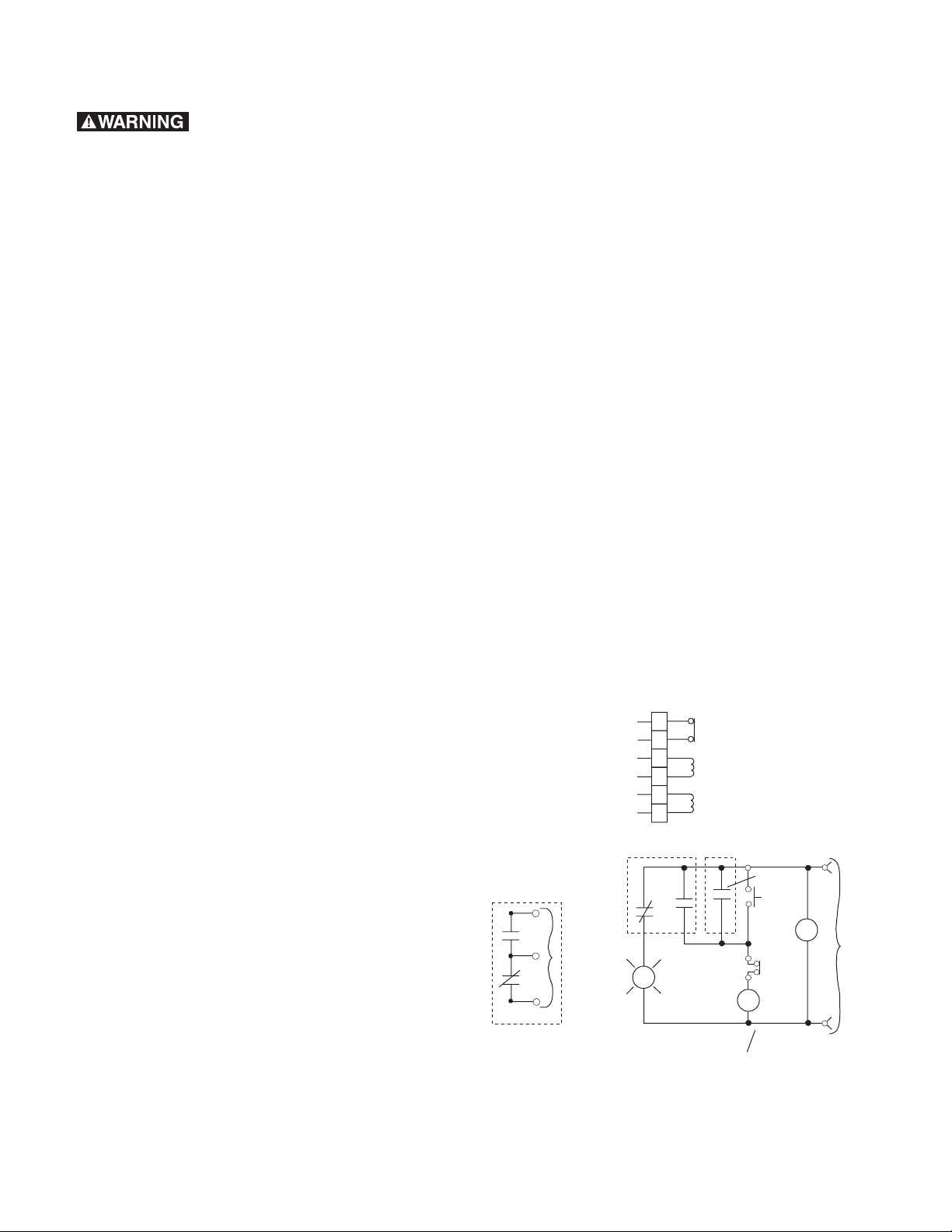
6
Warner Electric • 800-825-9050 819-0368
Electrical Connections
To avoid injury (or even death),
always make certain all power is off before
attempting to install or service the control or
any electrical equipment.
The clutch and brakes operate on DC voltage.
Warner Electric offers a full line of AC powered
controls to meet the needs of almost every
application. The service and installation instructions included with each Warner Electric control
show the proper electrical connections for the
units. Do not use the varistor supplied with the
unit if you are using a Warner Electric control.
Warner Electric controls have built in suppression.
Each PTB-BL3 brake has a cooling fan and a
thermal switch. Connect these items according
to Figure 7.
Use appropriate terminal connectors when
wiring to the terminal block. After connecting the
terminal, cover it with the attached rubber cap
so that no bare wire is exposed.
After wiring your Magnetic Particle clutch or
brake, confirm that the control circuit is functioning. Without rotating the input shaft, check
for voltage at the unit when the control output is
turned on. If appropriate, set the current for the
proper output. Your magnetic particle unit is
now ready for operation. For additional information on start up and maintenance, see page 9 of
this manual.
PTB-BL3 Wiring
The PTB-BL3 units are offered with a normally
closed thermal switch. This switch can be used
to protect the unit from overheating. It is not
recommended that this switch be connected in
series with the unit, because the opening of the
thermal switch on the output side of the control
may damage the control.
Figure 7 shows one possible way of using the
switch in a shutdown circuit. Under normal
operation, when power is applied to the circuit,
voltage is applied to the interval-on-relay, K
S
.
This momentarily closes contacts K
SA
. This in
turn applies voltage to relay K
T
. This double pole
double throw relay closes contacts K
TA1
, and
K
TB1
and opens contacts K
TA2
and K
TB2
. These
contacts will remain in this state unless power is
removed or the thermal switch opens. If the
switch opens, the thermal shutdown indicator
will be activated and the state of K
TB1
and /or
K
TB2
will shut down the system. After correcting
the cause of the thermal shutdown, the thermal
reset button will reset the shutdown circuit and
power up the system.
K
S =
Interval On Relay
K
T =
DPDT Relay
Man.
Thermal
Reset
Thermal
Switch
K
TA2
K
S
K
T
K
SA
Thermal
Shutdown
Indicator
R
S
2
S
1
Power
AC
or DC
To control
circuit
or other
shut down
method
K
TB2
K
TA1
K
TB1
Typical Shutdown Circuit
Note: Select relays with appropiate voltage rating for circuit.
S
S
M
M
C
C
DC24V
115 VAC
To alarm or
Shutdown circuit
Brake Coil
Fan Motor
Thermal Switch
Terminal Block Wiring
Figure 7
Wiring (PTB-BL3 Brake Only)

7
Warner Electric • 800-825-9050 819-0368
Electrical Data
Unit Size Voltage Resistance Amperes Watts Torque Build Up Torque Decay
[ohms @ 75° F (25°C)] [@ 75° F (25°C)] [@ 75° F (25°C)] (msec) (msec)
0.3 24 35.6 .674 16.2 78 6
0.6 24 21.1 1.14 27.4 84 9
1.2 24 20.6 1.16 28.0 147 16
2.5 24 15.8 1.52 36.5 175 21
524 8.80 2.74 65.7 271 28
10 24 9.00 2.68 64.2 448 43
20 24 7.20 3.34 80.3 536 66
40 24 5.10 4.66 112 680 100
80 24 4.30 5.57 134 1310 300
Note: Build up time equals time for torque to build to approximately 63.2% of steady state value
after a step change in voltage. Decay time equals time for current to drop to approximately 36.8%
of steady state value after a voltage change.
Fan Motor Data (PTB-BL3 Brake only)
Size Voltage Wattage
(single phase 60 hertz)
2.5 115 VAC 20
5115 VAC 38
10 115 VAC 38
20 115 VAC 38
Thermal Switch Data (PTB-BL3 Brake
only)
Type: Normally Closed
Current Rating: 24 VAC 18 A
115 VAC 18 A
230 VAC 13 A

8
Warner Electric • 800-825-9050 819-0368
Overhung Load Data
Note: Shaft extensions are not recommended.
When an overhung load (side load) is applied to
the shaft, verify that this load does not exceed
the maximum allowable. You will need to know
your operating speed and where your load is
applied to the shaft (See dimension 'A', Figure
8). For your speed, determine the speed coefficient from the coefficient table. Also, determine
the allowable overhung load from the chart
based on dimension 'A'. Multiply the load from
the chart times the speed coefficient to determine the allowable load for your application.
Figure 8
Overhung Load
Allowable Overhung Load
Type A R ARAR
(In.) (Lbs.) (In.) (Lbs.) (In.) (Lbs.)
POC/POB-0.3 .40 30 .50 28 .90 22
POC/POB-0.6 .40 45 .50 42 1.0 29
POC/POB-1.2 .40 52 .70 43 1.4 31
POC/POB-2.5 .40 88 .90 67 1.7 48
PTB2.5-BL3
POC/POB-5 .40 204 1.1 136 2.2 93
PTB-5BL3
POC/POB-10 .40 313 1.3 235 2.6 159
PTB-10BL3
POC/POB-20 .40 379 1.4 265 2.8 198
PTB-20BL3
POC/POB-40 .40 581 1.8 432 3.6 324
POC/POB-80 .40 860 2.2 648 4.3 498
Note: This table is based on 1000 rpm and
6000 hours bearing life. Also, this table
assumes that no thrust load is applied.
For most applications, the overhung load is
caused by pulleys or sprockets. The smaller the
pitch diameter (P.D.) of the pulley or sprocket,
the higher the belt tension, and therefore the
higher the overhung load. To determine the minimum pulley diameter for your application, use
the following equation:
Min. P.D.(in.) = 24 T K
C R
T - Torque (lb. ft.) This is the torque actually
being transmitted, not necessarily the maximum
torque capacity of the unit.
K - Safety factor for the tension in the type of
drive.
Use: 1.2 to 1.5 for sprockets
2 to 4 for belts
C - Speed coefficient from table.
R - Allowable Overhung Load from table.
Example: Determine the minimum sprocket
diameter that can be used on a POB-5.
Dimension A is 1.11 inches, required torque is
20 lb. ft. and the speed is 600 RPM.
Min. P.D.(in.) = 24 x 20 x 1.5
1.2 x 136
= 4.4 inch minimum P.D.
Speed Coefficient
Speed Speed Speed Speed
(rpm) coefficient (rpm) coefficient
50 2.74 1000 1.00
100 2.18 1200 0.95
200 1.72 1400 0.89
400 1.37 1600 0.86
600 1.20 1800 0.82
800 1.09 2000 0.80

9
Warner Electric • 800-825-9050 819-0368
Start Up
The powder in magnetic particle units sometimes settles during shipping and will need to be
redistributed. A simple run in procedure should
be performed to ensure proper performance.
Run in Procedure
Notes: 1. Before running in the unit, make
sure it does not bind. See step 2
(Page 3) of the Premounting instructions.
2. For clutches, the output must be
secured properly to prevent turning
if full torque is accidentally applied.
Set the control output voltage for 5 to 6 volts.
Turn off the control and run the input for one
minute. Then run the input at a speed close to,
but not exceeding, 1000 RPM. Cycle the unit at
5 or 6 volts for five seconds on and ten seconds
off. Repeat for 20 cycles.
When the powder is redistributed properly, the
torque will be consistent and proportional to
current.
Maintenance
Heat
Overheating occurs when the heat generated
exceeds the heat dissipation of the unit. Please
refer to the following table for maximum allowable surface temperatures.
Slip Applications
The heat generated is proportional to torque and
slip rpm. Care must be taken when adjusting
torque on the control to make sure that unit heat
dissipation capacity is not exceeded. Refer to
the sizing procedure in the catalog to make sure
the unit has adequate heat dissipation capability. Do not increase slip speed or torque without
verifying that the unit can dissipate the heat
generated.
Cycling Applications
In cycling applications, the speed and inertia of
the load and the frequency of starting and stopping determines the heat generated. Refer to the
selection procedure in the catalog to verify that
the unit can handle the thermal energy generated in your application. Do not increase the input
speed, cycle rate, or inertia without checking the
units ability to dissipate the heat generated.
Maximum Allowable Surface
Temperatures
Maximum
Cooling Allowable
Type System Temperature
POC/POB Natural 176° F
PHC-R Self-ventilated 176° F
PTB-BL3 Heat Pipe with Blower 194° F
Contamination
Do not expose the unit to water or oil. If water
or oil enters the powder cavity, the performance
of the unit may be affected. If the unit is mounted next to a gearbox, special care must be
taken to prevent oil from working its way into
the unit.

10
Warner Electric • 800-825-9050 819-0368
Mechanical Data
Part Nominal Nominal Drag Maximum Inertia
Model Number Torque Torque Speed Input Output Weight
(lb. ft.) (lb. ft.) (rpm) (lb. ft.2)(lb. ft.2)(lbs.)
POC 0.3 5401-270-211 2.1 .065 1800 .0128 .00477 5.5
POC 0.6 5401-270-221 4.3 .13 1800 .0173 .00570 7.9
POC 1.2 5401-270-231 8.6 .26 1800 .0304 .0104 12
POC 2.5 5401-270-241 18 .54 1800 .0973 .0387 22
POC 5 5401-270-251 36 1.1 1800 .0249 .114 38
POC 10 5401-270-261 72 2.2 1800 1.04 .437 77
POC 20 5401-270-271 144 4.3 1800 2.23 1.19 128
POC 40 5401-270-281 289 8.7 1800 5.93 3.08 220
POC 80 5401-270-291 578 17 1500 23.5 15.2 551
PHC-0.6R 5401-270-321 4.3 .13 1800 .0223 .00712 9.3
PHC-1.2R 5401-270-331 8.6 .26 1800 .0392 .0171 13
PHC-2.5R 5401-270-341 18 .54 1800 .126 .0494 22
PHC-5R 5401-270-351 36 1.1 1800 .323 .0138 38
PHC-10R 5401-270-361 72 2.2 1500 1.42 .617 95
PHC-20R 5401-270-371 144 4.3 1500 3.01 1.30 154
POB 0.3 5401-169-211 2.1 .065 1800 .0128 5.3
POB 0.6 5401-169-221 4.3 .13 1800 .0173 7.5
POB 1.2 5401-169-231 8.6 .26 1800 .0304 11.5
POB 2.5 5401-169-241 18 .54 1800 .0973 24.3
POB 5.0 5401-169-251 36 1.1 1800 .0249 35.3
POB 10 5401-169-261 72 2.2 1800 1.04 72.8
POB 20 5401-169-271 144 4.3 1800 2.23 106
POB 40 5401-169-281 289 8.7 1800 5.93 176
POB 80 5401-169-291 578 17 1500 23.5 573
PTB-2.5BL3 5401-169-141 18 .54 1800 .0973 24
PTB-5BL3 5401-169-151 36 1.1 1800 .249 38
PTB-10BL3 5401-169-161 72 2.2 1800 1.04 76
PTB-20BL3 5401-169-171 144 4.3 1500 2.23 114

PHC-R Dimensional Data
Note: All dimensions are nominal unless otherwise noted.
Bore Dimensions
Model A B C D E F G H I J K L
mm mm mm mm mm mm (in.) mm (in.) mm (in.) mm (in.) mm (in.) Thrd. Depth Bolt Thrd. Depth Bolt
(In.) (in.) (in.) (in.) (in.) Size mm Circle Size mm Circle
(in.) mm (in.) (in.) mm (in.)
PHC- 134 92 4 25.5 89 50.000
1.9685 50.000 1.9685 12.018 0.4731 4.028 0.1586 13.75 0.5413 M4 6 60 M4 6 60
0.6R (5.28) (3.62) (0.16) (1.00) (3.50) 49.975 1.9675 49.975 1.9675 12.000 0.4724 4.010 0.1579 13.50 0.5315 (0.24) (2.362) (0.24) (2.362)
PHC- 152 96 4 25 89 45.000
1.7717 70.000 2.7559 15.018 0.5913 5.028 0.1980 17.25 0.6791 M5 6 55 M4 8 80
1.2R (5.98) (3.78) (0.16) (0.98) (3.50) 44.975 1.7707 69.970 2.7547 15.000 0.5906 5.010 0.1972 17.00 0.6693 (0.24) (2.165) (0.31) (3.150)
PHC- 182 132 5 45 140 70.000
2.7559 70.000 2.7559 25.021 0.9851 7.035 0.2770 28.25 1.1122 M6 10 80 M6 9 80
2.5R (7.17) (5.20) (0.20) (1.77) (5.51) 69.970 2.7547 69.670 2.7429 25.000 0.9843 7.013 0.2761 28.00 1.1024 (0.39) (3.150) (0.35) (3.150)
PHC- 219 148 4 40 165 87.000
3.4252 87.000 3.4252 35.025 1.3789 10.035 0.3951 38.75 1.5256 M8 10 102 M8 10 102
5R (8.62) (5.83) (0.16) (1.57) (6.50) 86.965 3.4238 86.965 3.4238 35.000 1.3780 10.013 0.3942 38.50 1.5157 (0.39) (4.016) (0.39) (4.016)
PHC- 290 183.5 6 60 190 105.000
4.1339 110.000 4.3307 45.025 1.7726 12.043 0.4741 48.75 1.9193 M10 13 120 M8 10 120
10R (11.42) (7.22) (0.24) (2.36) (7.48) 104.965 4.1325 109.965 4.3293 45.000 1.7717 12.016 0.4731 48.50 1.9094 (0.51) (4.724) (0.39) (4.724)
PHC- 335 222 9 75 220 130.000
5.1181 130.000 5.1181 55.030 2.1665 15.043 0.5922 60.25 2.3720 M10 15 150 M10 13.5 150
20R (13.19) (8.74) (0.35) (2.95) (8.66) 129.960 5.1165 129.960 5.1165 55.000 2.1654 15.016 0.5912 60.00 2.3622 (0.59) (5.906) (0.53) (5.906)
Note: This is a stationary field clutch. The tapped holes "L" in the field are for securing the housing to prevent it from rotating.
See instaltion instructions.
Do not block ventilation openings when mounting.
11
Warner Electric • 800-825-9050 819-0368
PHC-R Dimensions
L (6 Holes)
B
C
A
E
F
30°
D
D
Input Hub
K
4mm
(.16 in.)
Ventilation
Opening
G
300 mm
(11.8 in.)
I
J
H

12
Warner Electric • 800-825-9050 819-0368
POC Dimensional Data
Note: All dimensions are nominal unless otherwise noted.
Shaft Dimensions L
Model A B C D E F G H I J K Depth No. of Bolt
mm mm mm mm mm mm mm inches mm inches mm inches mm mm Thread mm Holes Circle
(in.) (in.) (in.) (in.) (in.) (in.) (in.) (in.) Size (in.) mm
(in.)
POC-0.3 120 147 23 87 11 65 42.000
1.6535 10.000 0.3937 4.024 0.1584 4 2.5 M5 10 6 x 2 64
(4.72) (5.79) (0.91) (3.43) (0.43) (2.56) 41.975 1.6526 9.985 0.3931 4.012 0.1580 (0.16) (0.10) (0.39) (2.520)
POC-0.6 134 155 26 90 10 70 42.000
1.6535 12.000 0.4724
4.024 0.1584 4 2.5 M5 11 6 x 2 64
(5.28) (6.10) (1.02) (3.54) (0.39) (2.76) 41.975 1.6526 11.982 0.4717 4.012 0.1580 (0.16) (0.10) (0.43) (2.520)
POC-1.2 152 188 34.5 106 13 80 42.000
1.6535 15.000 0.5906 5.024 0.1978 53M6 136 x 2 64
(5.98) (7.40) (1.36) (4.17) (0.51) (3.15) 41.975 1.6526 14.982 0.5898 5.012 0.1973 (0.20) (0.12) (0.51) (2.520)
POC-2.5 182 227.5 43 123.5 15 93.5 55.000
2.1654 20.000 0.7874 5.024 0.1978 53M6 136 x 2 78
(7.17) (8.96) (1.69) (4.86) (0.59) (3.68) 54.970 2.1642 19.979 0.7866 5.012 0.1973 (0.20) (0.12) (0.51) (3.071)
POC-5 219 284 57 151 23 105 74.000
2.9134 25.000 0.9843 7.030 0.2768 74M6 136 x 2 100
(8.62) (11.18) (2.24) (5.94) (0.91) (4.13) 73.970 2.9122 24.979 0.9834 7.015 0.2762 (0.28) (0.16) (0.51) (3.937)
POC-10 290 348 67 192 25 142 100.000
3.9370 30.000 1.1811 7.030 0.2768 74M10 18 6 x 2 140
(11.42) (13.70) (2.64) (7.56) (0.98) (5.59) 99.965 3.9356 29.979 1.1803 7.015 0.2762 (0.28) (0.16) (0.71) (5.512)
POC-20 335 382 71 216 25 166 110.000
4.3307 35.000 1.3780 10.030 0.3949 8 4.5 M10 18 6 x 2 150
(13.19) (15.04) (2.80) (8.50) (0.98) (6.54) 109.965 4.3293 34.975 1.3770 10.015 0.3943 (0.31) (0.18) (0.71) (5.906)
POC-40 395 490 92 278 33 212 130.000
5.1181 45.000 1.7717 12.036 0.4739 8 4.5 M12 20 8 x 2 200
(15.55) (19.29) (3.62) (10.94) (1.30) (8.35) 129.960 5.1165 44.975 1.7707 12.018 0.4731 (0.31) (0.18) (0.79) (7.874)
* Air inlet for optional forced air cooling. Consult factory.

13
Warner Electric • 800-825-9050 819-0368
POC Dimensions
4x3/8 Conduit
C
E
F
D
B
E
C
A
G
G
J
K
H
I
Terminals
L
10°
10°
30°
L
Te rminals
300 mm
(11.8 in)
Output
Input
10°
10°
End View (POC 0.3) End View (POC-40)
POC – 80
Terminal blocks
560
(22.05)
515
(20.28)
275.0 10.83
274.5 10.81
()
25
(.98)
90
(3.54)
145
(5.71)
145
(5.71)
390
(15.35)
Output
6
(.24)
65.000 2.5591
64.970 2.5579
12
(.47)
18.036 .7101
18.018 .7094
()
()
645
(25.40)
Input
322.5
(12.70)
197.5
(7.78)
197.5
(7.78)
110
(4.33)
100
(3.94)
88
(346)
88
(346)
100
(3.94)
110
(4.33)
Ø480
(18.90)
90
(3.54)
140
(5.51)
140
(5.51)
350
(13.78)
4-Ø21 (.83)
90
(3.54)
90
(3.54)
322.5
(12.70)
End View (POC 0.6, 1.2,
2.5, 5.0, 10, 20)

14
Warner Electric • 800-825-9050 819-0368
POB Dimensions
30°
L
300 mm
(11.8 in)
L
4x3/8 Conduit*
C
E
F
D
B
A
I
J
H
K
G
Te rminals
10°
10°
Terminals
L
10°
10°
End View (POB-0.3)
End View (POB-40)
Terminal blocks
560
(22.05)
515
(20.28)
275.0 10.83
274.5 10.81
()
25
(.98)
90
(3.54)
90
(3.54)
145
(5.71)
145
(5.71)
390
(15.35)
6
(.24)
65.000 2.5591
64.970 2.5579
12
(.47)
18.036 .7101
18.018 .7094
(
)
(
)
485
(19.09)
322.5
(12.70)
197.5
(7.78)
162.5
(6.40)
53
(2.09)
88
(346)
100
(3.94)
110
(4.33)
Ø480
(18.90)
90
(3.54)
90
(3.54)
140
(5.51)
140
(5.51)
350
(13.78)
4-Ø21 (.83)
POB-80
End View (POB-0.6, 1.2,
2.5, 5.0, 10, 20)

15
Warner Electric • 800-825-9050 819-0368
POB Dimensional Data
Note: All dimensions are nominal unless otherwise noted.
Shaft Dimensions L
Model A B C D E F G H I J K Depth No. of Bolt
mm mm mm mm mm mm mm (in.) mm (in.) mm (in.) mm mm Thread mm Holes Circle
(in.) (in.) (in.) (in.) (in.) (in.) (in.) (in.) Size (in.) mm
(in.)
POB-0.3 120 105 23 75 11 64 42.000
1.6535 10.000 0.3937 4.024 0.1584 4 2.5 M5 10 6 64
(4.72) (4.13) (0.91) (2.95) (0.43) (2.52) 41.975 1.6526 9.985 0.3931 4.012 0.1580 (0.16) (0.10) (0.39) (2.520)
POB-0.6 134 109 26 76.5 10 66.5 42.000
1.6535 12.000
0.4724 4.024 0.1584 4 2.5 M5 11 6 64
(5.28) (4.29) (1.02) (3.01) (0.39) (2.62) 41.975 1.6526 11.982 0.4717 4.012 0.1580 (0.16) (0.10) (0.43) (2.520)
POB 1.2 152 130.5 34.5 89.5 13 76.5 42.000
1.6535 15.000 0.5906 5.024 0.1978 5 3.0 M6 13 6 64
(5.98) (5.14) (1.36) (3.52) (0.51) (3.01) 41.975 1.6526 14.982 0.5898 5.012 0.1973 (0.20) (0.12) (0.51) (2.520)
POB 2.5 182 155 43 103 15 88 55.000
2.1654 20.000 0.7874 5.024 0.1978 5 3.0 M6 13 6 78
(7.17) (6.10) (1.69) (4.06) (0.59) (3.46) 54.970 2.1642 19.979 0.7866 5.012 0.1973 (0.20) (0.12) (0.51) (3.071)
POB 5.0 219 189 57 122.5 23 99.5 74.000
2.9134 25.000
0.9843 7.030 0.2768
7 4.0 M6 13 6 100
(8.62) (7.44) (2.24) (4.82) (0.91) (3.92) 73.970 2.9122 24.979 0.9834 7.015 0.2762 (0.28) (0.16) (0.51) (3.937)
POB 10 290 233.5 67 155.5 25 130.5 100.000
3.9370 30.000 1.1811 7.030 0.2768 7 4.0 M10 18 6 140
(11.42) (9.19) (2.64) (6.12) (0.98) (5.14) 99.965 3.9356 29.979 1.1803 7.015 0.2762 (0.28) (0.16) (0.71) (5.512)
POB 20 335 263.5 71 180.5 25 155.5 110.000
4.3307 35.000 1.3780 10.030 0.3949 8 4.5 M10 18 6 150
(13.19) (10.37) (2.80) (7.11) (0.98) (6.12) 109.965 4.3293 34.975 1.3770 10.015 0.3943 (0.31) (0.18) (0.71) (5.906)
POB-40 395 330 92 224 33 191 130.000
5.1181 45.000 1.7717 12.036 0.4739 8 4.5 M12 20 8 200
(15.55) (12.99) (3.62) (8.82) (1.30) (7.52) 129.960 5.1165 44.975 1.7707 12.018 0.4731 (0.31) (1.18) (0.79) (2.520)

16
Warner Electric • 800-825-9050 819-0368
PTB Dimensions
K
J
L
M
A
I
G
F
E
C
B
D
H
Te rminal Block
Electric Blower,
Single-Phase 110 VAC
N
PTB Dimensional Data
Note: All dimensions are nominal unless otherwise noted.
Shaft Dimensions N
Model A B C D E F G H* I J K L M Depth Bolt
mm mm mm mm mm mm mm mm mm (in.) mm (in.) mm (in.) mm mm Thread mm Circle
(in.) (in.) (in.) (in.) (in.) (in.) (in.) (in.) (in.) (in.) Size (in.) mm
(in.)
PTB- 182 221.5 169.5 43 15 43 38 120 55.000
2.1654 20.000 0.7874 5.024 0.1978 53M613 78
2.5BL3 (7.17) (8.72) (6.67) (1.69) (0.59) (1.69) (1.50) (4.72) 54.970 2.1642 19.979 0.7866 5.012 0.1973 (0.20) (0.12) (0.51) (3.071)
PTB- 219 274.5 208 61.5 23 57 47 150 74.000
2.9134 25.000 0.9843 7.030 0.2768 74M6 13 100)
5BL3 (8.62) (10.81) (8.19) (2.42) (0.91) (2.24) (1.85) (5.91) 73.970 2.9122 24.979 0.9834 7.015 0.2762 (0.28) (0.16) (0.51) (3.937)
PTB- 290 335 257 61.5 25 67 56 150 100.000
3.9370 30.000 1.1811 7.030 0.2768 74M10 18 140
10BL3 (11.42) (13.19) (10.12) (2.42) (0.98) (2.64) (2.20) (5.91) 99.965 3.9356 29.979 1.1803 7.015 0.2762 (0.28) (0.16) (0.71) (5.572)
PTB- 335 352.5 269.5 61.5 25 71 60 150 110.000
4.3307 35.000 1.3780 10.030 0.3949 8 4.5 M10 18 150
20BL3 (13.19) (13.88) (10.61) (2.42) (0.98) (2.80) (2.36) (5.91) 109.965 4.3293 34.975 1.3770 10.015 0.3943 (0.31) (0.18) (0.71) (5.906)
* Adjacent symbol denotes shape of fan.

17
Warner Electric • 800-825-9050 819-0368

Warranty
Warner Electric LLC warrants that it will repair or replace (whichever it deems advisable) any
product manufactured and sold by it which proves to be defective in material or workmanship
within a period of one (1) year from the date of original purchase for consumer, commercial or
industrial use.
This warranty extends only to the original purchaser and is not transferable or assignable without
Warner Electric LLC’s prior consent.
Warranty service can be obtained in the U.S.A. by returning any defective product, transportation
charges prepaid, to the appropriate Warner Electric LLC factory. Additional warranty information
may be obtained by writing the Customer Satisfaction Department, Warner Electric LLC, 449
Gardner Street, South Beloit, Illinois 61080, or by calling 815-389-3771.
A purchase receipt or other proof of original purchase will be required before warranty service is
rendered. If found defective under the terms of this warranty, repair or replacement will be made,
without charge, together with a refund for transportation costs. If found not to be defective, you
will be notied and, with your consent, the item will be repaired or replaced and returned to you
at your expense.
This warranty covers normal use and does not cover damage or defect which results from
alteration, accident, neglect, or improper installation, operation, or maintenance.
Some states do not allow limitation on how long an implied warranty lasts, so the above limitation
may not apply to you.
Warner Electric LLC’s obligation under this warranty is limited to the repair or replacement of the
defective product and in no event shall Warner Electric LLC be liable for consequential, indirect,
or incidental damages of any kind incurred by reason of the manufacture, sale or use of any
defective product. Warner Electric LLC neither assumes nor authorizes any other person to give
any other warranty or to assume any other obligation or liability on its behalf.
WITH RESPECT TO CONSUMER USE OF THE PRODUCT, ANY IMPLIED WARRANTIES WHICH
THE CONSUMER MAY HAVE ARE LIMITED IN DURATION TO ONE YEAR FROM THE DATE OF
ORIGINAL CONSUMER PURCHASE. WITH RESPECT TO COMMERCIAL AND INDUSTRIAL
USES OF THE PRODUCT, THE FOREGOING WARRANTY IS IN LIEU OF AND EXCLUDES ALL
OTHER WARRANTIES, WHETHER EXPRESSED OR IMPLIED BY OPERATION OF LAW OR
OTHERWISE, INCLUDING, BUT NOT LIMITED TO, ANY IMPLIED WARRANTIES OF
MERCHANTABILITY OR FITNESS.
Some states do not allow the exclusion or limitation of incidental or consequential damages, so
the above limitation or exclusion may not apply to you. This warranty gives you specic legal
rights and you may also have other rights which vary from state to state.
Changes in Dimensions and Specifications
All dimensions and specications shown in Warner Electric catalogs are subject to change without
notice. Weights do not include weight of boxing for shipment. Certied prints will be furnished
without charge on request to Warner Electric.
Warner Electric LLC
31 Industrial Park Road • New Hartford, CT 06057
815-389-3771 • Fax: 815-389-2582
www.warnerelectric.com
P-223-1 819-0368 6/05 Printed in USA