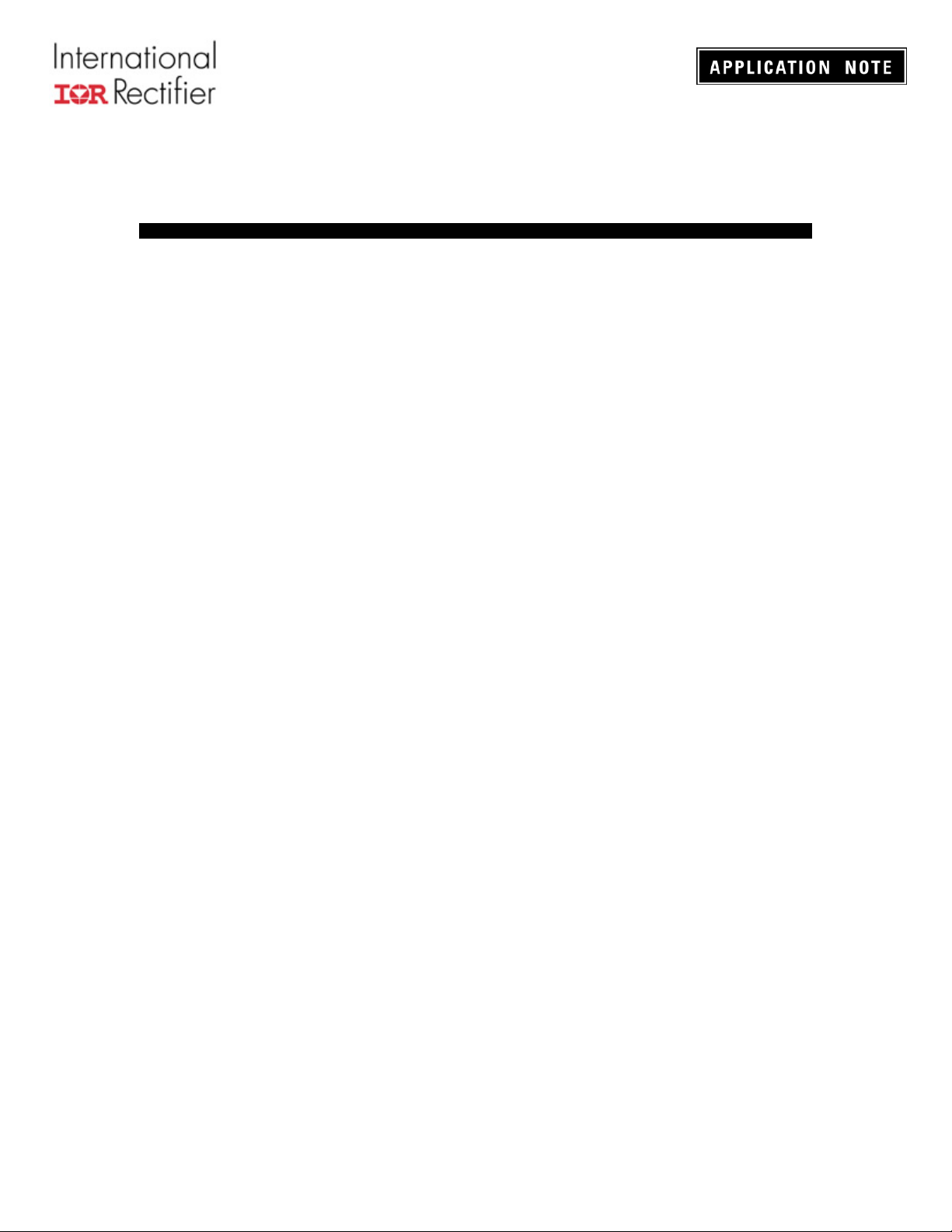
Application Note AN-1027
ADD-A-Pak Module Mounting Instructions
Table of Contents
Page
Heat Preparation..................................................................................2
Visual Inspection..................................................................................2
Thermal Compound .............................................................................2
Module Fastening.................................................................................2
Electrical Connection ...........................................................................2
This application note discusses the proper mounting and exchanger surface preparation,
important to optimize the heat transfer from module to heatsink and maintain the contact thermal
resistance value specified on the data sheet.
www.irf.com
AN-1027
1
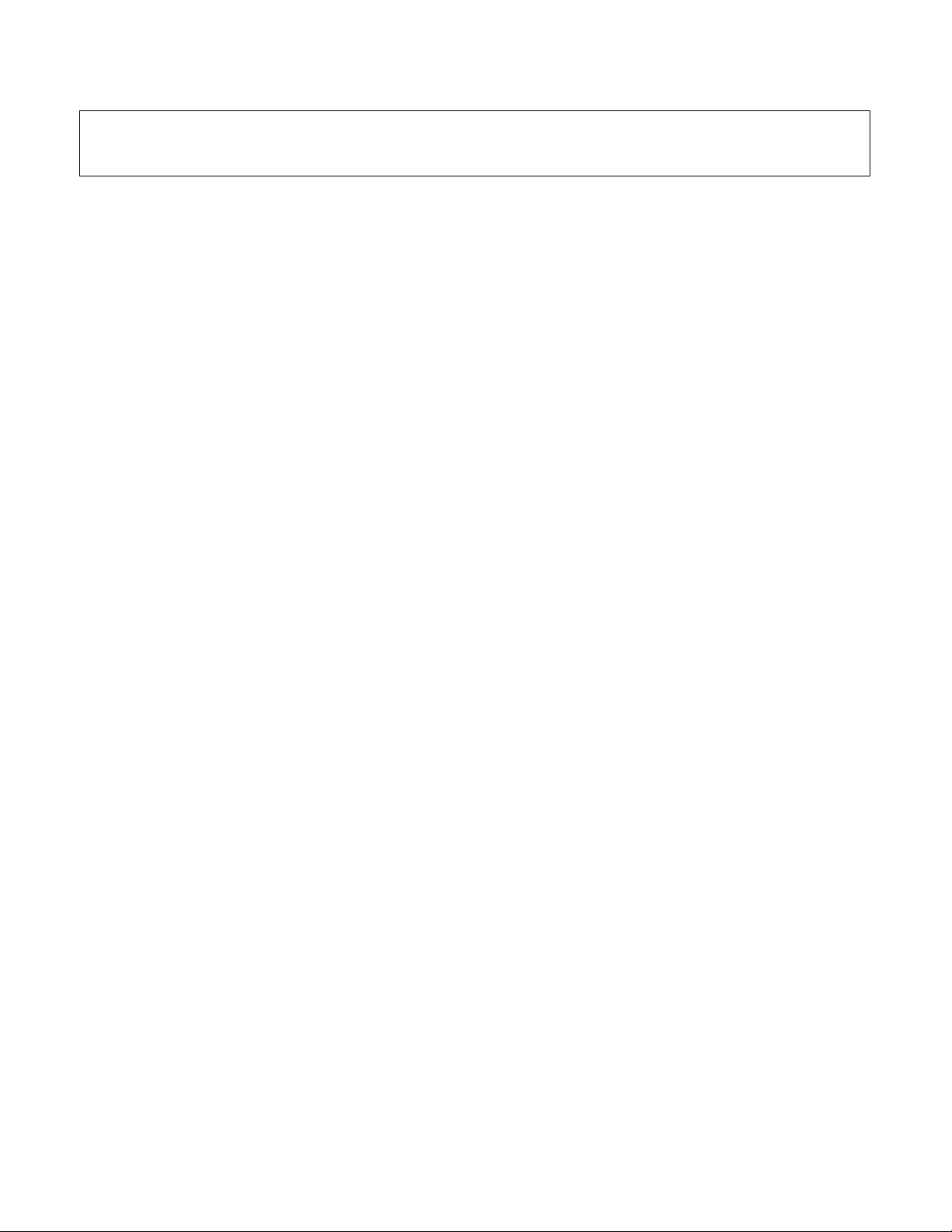
Application Note
ADD-A-Pak Module Mounting Instructions
Proper mounting and exchanger surface
preparation are generally very important to
optimize the heat transfer from module to
heatsink and maintain the contact thermal
resistance value specified on the data sheet.
The following procedure is recommended:
Heatsink Preparation
The contact surface of heatsink must be flat,
with unevenness remaining after grinding those
areas must be less than 20um; the roughens
less than 10um
In general, a milled or machined surface is
satisfactory if prepared with tools in good
working condition.
The heatsink mounting surface must be clean,
with no dirt, corrosion, or surface oxides. It is
very important to keep the mounting surface
free from particles exceeding in thickness
0.05mm (2 mils), provided thermal compound
is used.
Visual Inspection
Inspect the power module to insure that the
contact surface of the base is clean, that here
are no lumps or bulges on the base plate that
could damage the base or reduce heat transfer
across the surfaces.
Thermal Compound
Coat uniformly the heatsink mounting surfaces
and power module base plate with a good
quality thermal compound. Do not exceed with
the compound, a very thin layer (around
100µm) is sufficient.
A good thermal grease is the Dow Corning 340
Apply uniform pressure on the package to force
the compound to spread over the entire contact
area.
Module Fastening
Bolt the module to the heatsink using the two
fixing holes. The recommended torque is 5 Nm
± 10%.
An even amount of torque should be applied
for each individual mounting screw.
A torque wrench, accurate in the specified
range, must be used in mounting module, in
order to achieve optimum results. The
mounting screws must be tightened in
sequence.
After a period of about 3 hours, recheck the
torque with a final tightening in opposite
sequence to allow the spread of the compound.
Electrical Connection
Tighten the M5 screws to the power terminals
applying a torque of 3 Nm ± 10% avoiding any
pressure on the module.
The gate and auxiliary cathode connections
should be made via the flying leads as
supplied. If International Rectifier hardware is
not available, use only fast-on connectors
2.8mm x 0.8mm. The length of the flying leads
should be kept as short as is physically
possible.
Gate circuit return connection should always be
accomplished by way of the auxiliary cathode
connection.
AN-1027
© 2002 International Rectifier