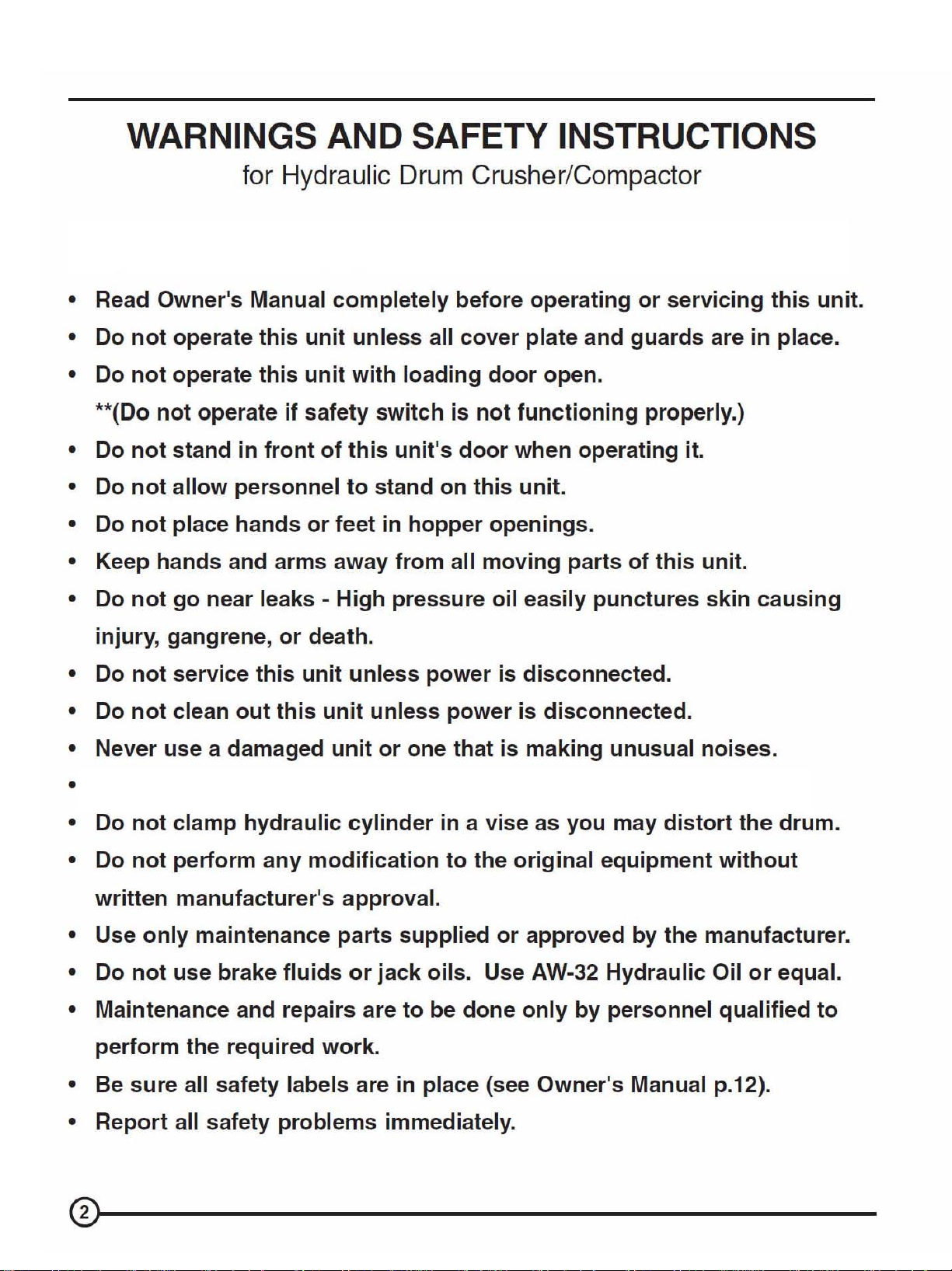
Do not change pressure relief valve setting on manifold.

OPERATING INSTRUCTIONS
The HDC-900 is equipped with a momentary contact control. This relieves the operator from having
to hold the "Start" button while the unit cycles.
Sequence of Operation:
In order to operate, the crusher must be prepared as follows: 1) place a drum insid e the crusher; 2)
close the door; 3) lock the door latch handle; 4) turn the key switch to the appropriate mode; 5) select
“CRUSH” or “COMPACT”; 6) pull out the Emergency Stop button; 7) momentary press the cycle “START”
button to activate the crush/compact cycle.
The direction of the platen's travel wi ll be determined by its starting position -- if it is fully raised to the
top of the cabinet, the platen will move down to crush a drum; otherwise, the cylinder will raise the platen
until it finally is all the way up and in its starting ("home") position, at which point the power unit will turn off.
Pressing the cycle start button again will cause the platen to move downward. The operator must hold the
button for a few seconds to latch the circuit.
When the crusher is in its "home" position and th e cycle start button is pressed, the cylinder pu shes
the platen down onto (or into) the drum. In ord er to achi eve a short cycle time, both sections of the pum p
in the power unit drive oil to the cylinder until the cylinder pressure reaches approximately 1000 PSI. At that
time, the higher-displacement sec tion recycles oil to the reservoir while the low-displacement, high-pressur e
section continues to pump oil to the cylinder, i.e. a typi cal High-Low circuit.
As the platen crushes or compacts the drum to a height of about 6 inches, the cylinder pressure
increases until it reaches the set-point of the appropriate pressure switch. The valve shifts to center and a
timer activates to control the period of decompression. Once the period ends the directional valve shifts
and reverses the direction of oil flow to the cylinder. Reversing the flow of oil raises the platen to its starting,
or "home" position. When the cylinder returns the platen a ll the way to the top of the cabi net, the power
unit turns off. At this point, the cabinet door can be opened to remove the drum.
If the unit needs to be stopped at any point during its cycle, the operator can depress the red
emergency stop button located on the control panel. This stops the motor and prevents the unit from
cycling any further. To return the platen to its starting ("home") position, pull the emergency stop button out
to release it and depress the cycle start button again. This will cause the platen to ascend back to the
starting position. To cycle the unit again, simply depress the cycle start button.
RESPONSIBILITIES OF OWNERS/USERS
It is the responsibility of the owner/user for the following:
1.) Inspected and maintain this product according to the guidelines in this manual.
2.) Any unit not in normal operating condition should immediately be removed from service and remain
out-of-service until it is returned to normal operating condition.
Unsafe conditions include, but are not limited to, the following: excessive hydraulic or air leakage, missing
pins, or fasteners, any cracked or deformed structural members, cut or frayed hydraulic, electric or air lines,
and damaged controls or safety devices. All repairs and maintenance must be performed by qualified
personnel.
3.) Unit should only be used by authorized personnel. All operators must read and understand all operating
procedures and safety guidelines in this manual prior to using the crusher for the first time.
4.) Operator should verify that all safety features function properly before each use.
5.) Any modifications to the unit must be approved in writing by the manufacturer.
Ordering Replacement & Spare Parts
Our company takes pride in using the finest available parts for our equipment. We are not responsible for
equipment failure resulting from the use of unapproved replacement parts. To order parts for your
equipment, contact Customer Service at the factory. In any correspondence with the factory please
include the Serial Number which is inscribed on the nameplate of the piece of equi pment. Use only the part
numbers provided in this Owner's Manual. When ordering parts for AC power units please indicate the
motor phase and voltage that the equipment is operating on. Ordering Replacement or Extra Parts.
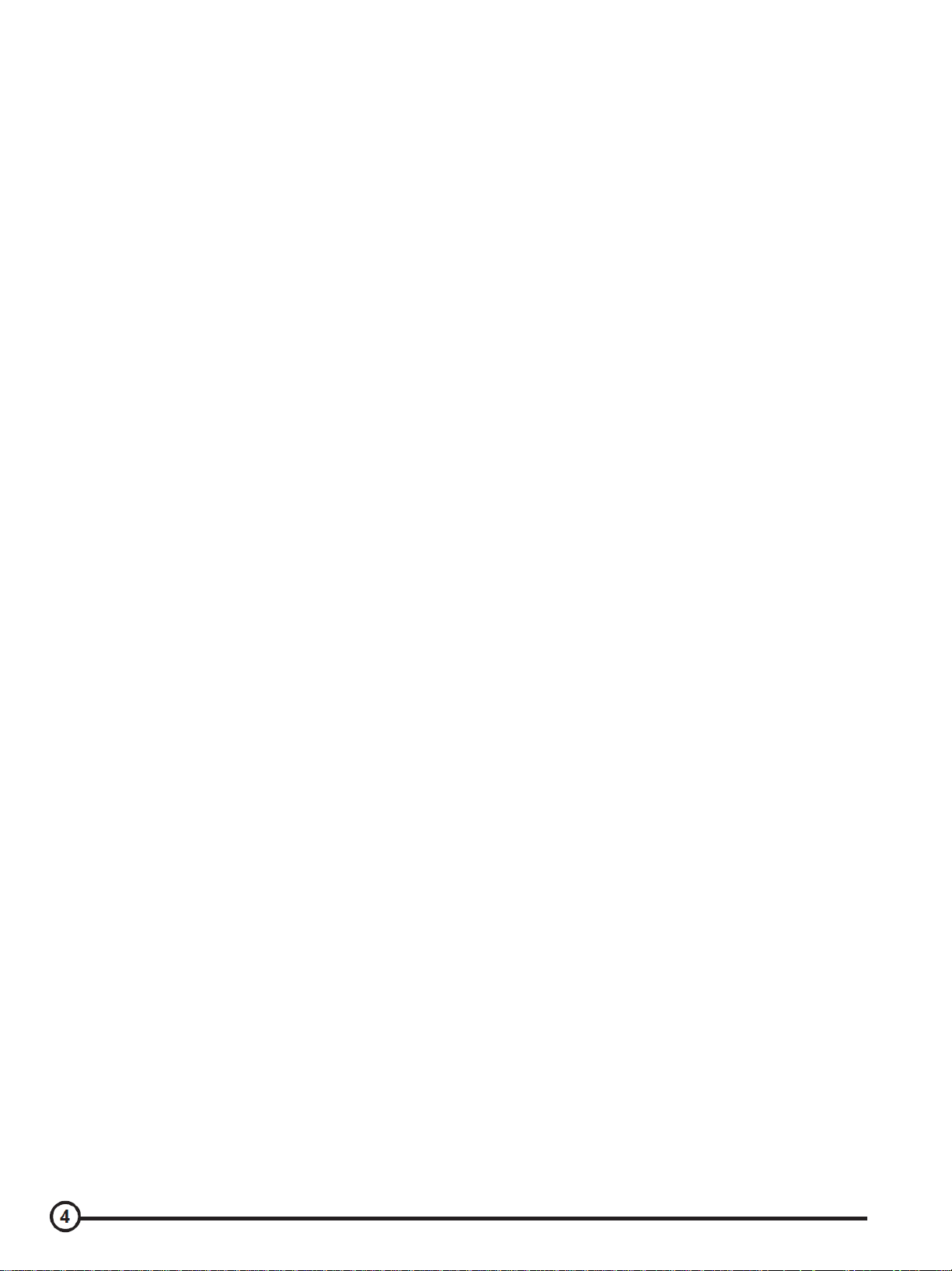
INSTALLATION INSTRUCTIONS
Read the entire manual before installing the crusher.
For installation you will need the following:
1.) A fork truck.
2.) Lag bolts, masonry drill, masonry bit, and wrench for lag bolt, grout, and steel shims.
3.) A power circuit with the specified voltage, including fuses and disconnect or circuit
breakers. (See p. 8-9). Reference NEC 70.
4.) Minimize voltage drop by using adequate wire size. Reference NEC 70.
Position the crusher with a fork truck by lifting the crusher via the fork tubes on the frame.
Read all warning labels on the unit and b e sure every label shown on page 12 is on the unit.
Anchor the crusher to the floor before using it for the first time.
Connect the power source as shown in electrical section.
Cycle the unit a few times; then check the oil and add more oil, if necessary. (See oil
specification on page 5).
LOADING INSTRUCTIONS
The Hydraulic Drum Crusher/Compactor (HDC-900) is designed to crush standard ribbed steel
drums of 55 gallon size or smaller. DO NOT use the crusher to compact smooth -walled drums,
i.e. drums that lack ribs. The crusher can be used to compact (standard ribbed) steel drums
that contain soft materials.
When loading the crusher, always apply these suggestions:
1.) Before using the crusher, confirm that the platen is properly installed;
2.) Carefully center the material/item to be crushed under the platen, because an offset or
uneven load might damage the cylinder rod;
3.) DO NOT fill drums with scrap metal, paint cans, etc. which w ill exceed the crushing
capacity of the unit and significantly damage the crusher.
NOTE: The crusher is designed to compact standard, ribbed steel drums. However, the crusher
might not compact a particular drum. It is also possible that the crusher might sustain minor
damage during the compaction process.
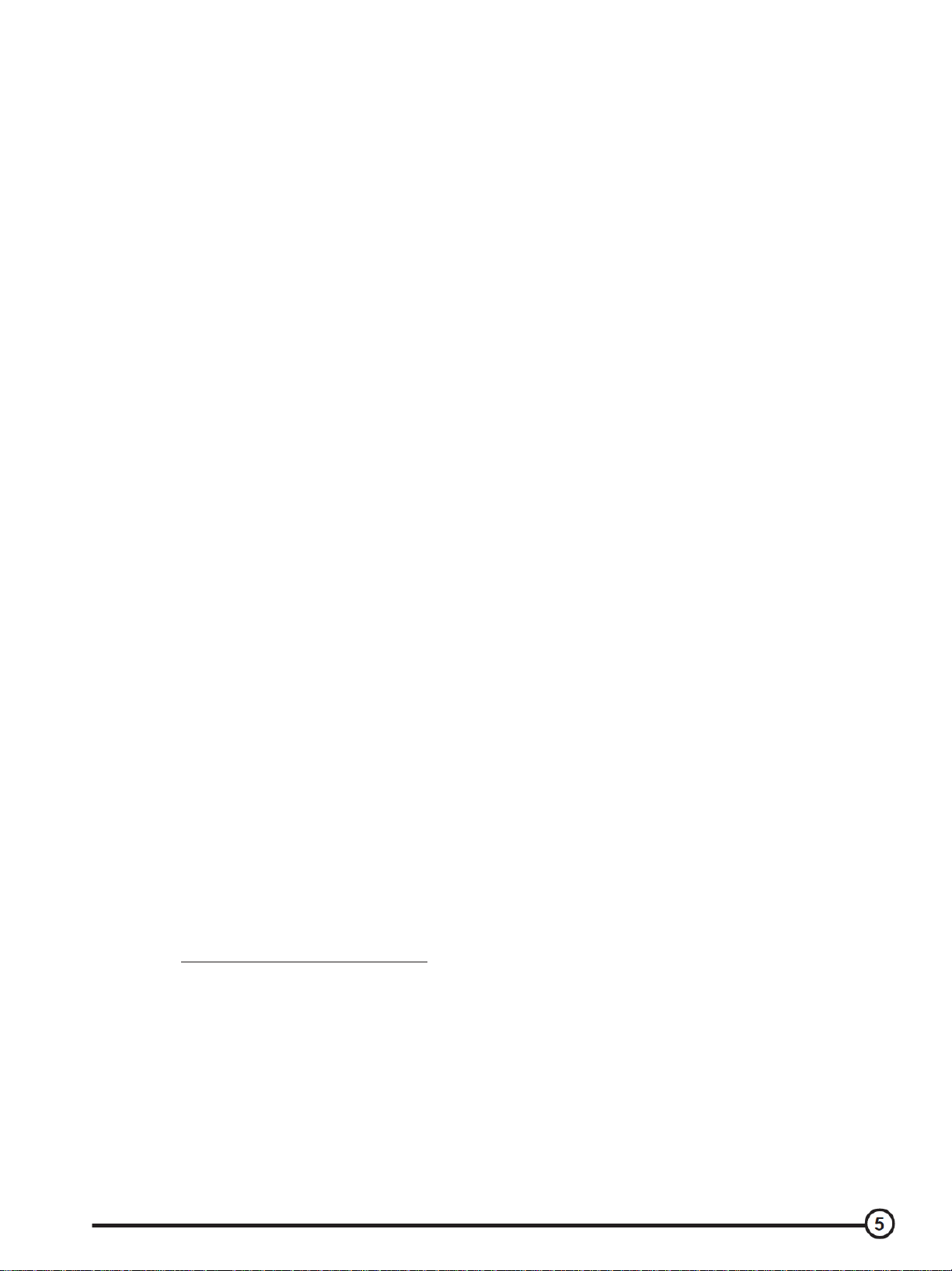
PERIODIC INSPECTIONS & MAINTENANCE INSTRUCTIONS
ALWAYS EMPTY THE CRUSHER BEFORE INSPECTING OR PERFORMING MAINTENANCE ON IT.
(A) Before each use, inspect the crusher and remove it from service if any of the following
issues are observed:
1.) Frayed wires;
2.) Oil leaks;
3.) Pinched or chafed hoses, loose fittings;
4.) Structural deformation of frame;
5.) Unusual noise or binding
(B) Monthly Inspections
1.) Check oil level. Oil should be 2" to 2½" below the top of the tank with the
cylinder in the fully retracted position. Add as necessary.
2.) Check for oil leaks.
3.) Check for worn or damaged hydraulic hoses, elect rical wires, and cords.
Repair as necessary.
4.) Cycle the crusher and listen for unusual noise.
5.) Make sure all warning labels are readable and in plac e according to the
diagram on p. 12.
6.) Remove dirt and debris.
(C) Yearly Inspection
Change the hydraulic oil at least once per year. However, because the oil
should be changed as soon as it darkens, looks milky, or becomes gritty, oil
changes might be required more frequently than every 12 months.
After draining the oil from the reservoir, flush the reservoir before refilling it.
If the oil looks milky, water is present and the oil should be changed
immediately.
Recommended hydraulic oil
: Purity ISO AW-32 Hydraulic fluid or equal.