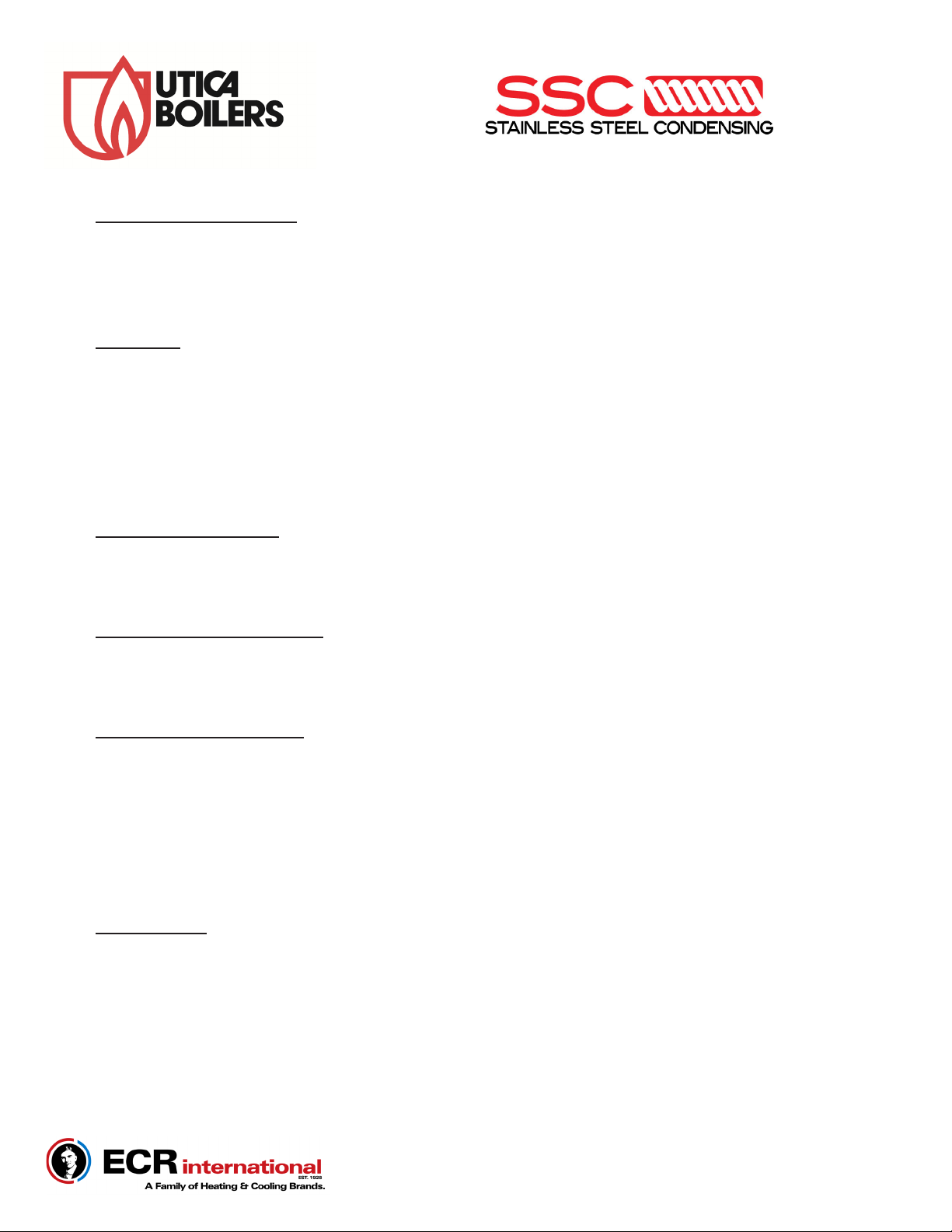
Suggested Specications Utica Boiler SSC Stainless Steel Boiler
1.0 General Requirements:
1.1 Provide and Install Boiler(s) in accordance with the plan drawings, written specications and
contract documents.
1.2 All work shall be performed in a neat workmanship like manner compliant with all local code
authorities.
2.0 Submittal
2.1 Product Data: Submit manufacturer’s technical product data, including rated capacities of selected
model, weights (shipping, installed and operating), installation and start-up instructions, and
furnished accessory information.
2.2 Shop Drawings: Submit manufacturer’s end assembly drawings indicating dimensions, connection
locations, and clearance requirements.
2.3 Wiring Diagrams: Submit manufacturer’s electrical requirements for the boiler including ladder
type wiring diagrams for interlock and control wiring.
3.0 Boiler Requirements
3.1 Boiler shall be a wall hung model. Boiler shall be gas red, condensing type with a minimum 95%
AFUE rating. Boiler shall be rated Energy Star Most Efcient. Optional oor mounting stand shall
be available from the manufacture. Boiler shall be factory re tested.
4.0 Acceptable Manufacturers
4.1 This specication is based on the Utica SSC boilers as manufactured by ECR International, Inc.
Equivalent units and manufacturers must meet all performance criteria for all fuel options, and will
be considered upon prior approval.
5.0 Certications & Listings
5.1 Boiler shall be certied by CSA
5.2 Boiler shall be constructed in accordance with the American Society of Mechanical Engineers
(ASME)
5.3 Boiler shall have an ASME H stamp that is applied to the Heat Exchanger. Each Heat Exchanger
shall be independently reviewed by an ASME authorized inspector. A copy of the inspection report
shall accompany the boiler. The boiler shall be rated for a maximum allowable working pressure
of 150 MAWP. The boiler shall be equipped with a 30 psi relief valve.
6.0 Construction
6.1 Boiler Heat Exchanger shall be a single tubular construction helical coil with laser welded ns. The
Heat Exchanger shall be constructed as one continuous piece of Stainless Steel Type 316 L coiled
tube. The ns shall be constructed of Stainless Steel Type 444 and laser welded onto the tube
utilizing a computer automated process. The Heat Exchanger shall be vertical mounted with a
counter ow of water and ue gases.
6.2 Burner Components
6.2.1 Gas Valve shall be negative regulation delivering the proper quantity of fuel based on the
speed of the combustion air blower. The valve shall be able to operate at gas supply inlet
pressures as indicated.
ECR International, Inc.
2201 Dwyer Avenue, Utica NY 13501
Tel: 1-315-797-1310
P/N 240010475 REV C, [04/2015]
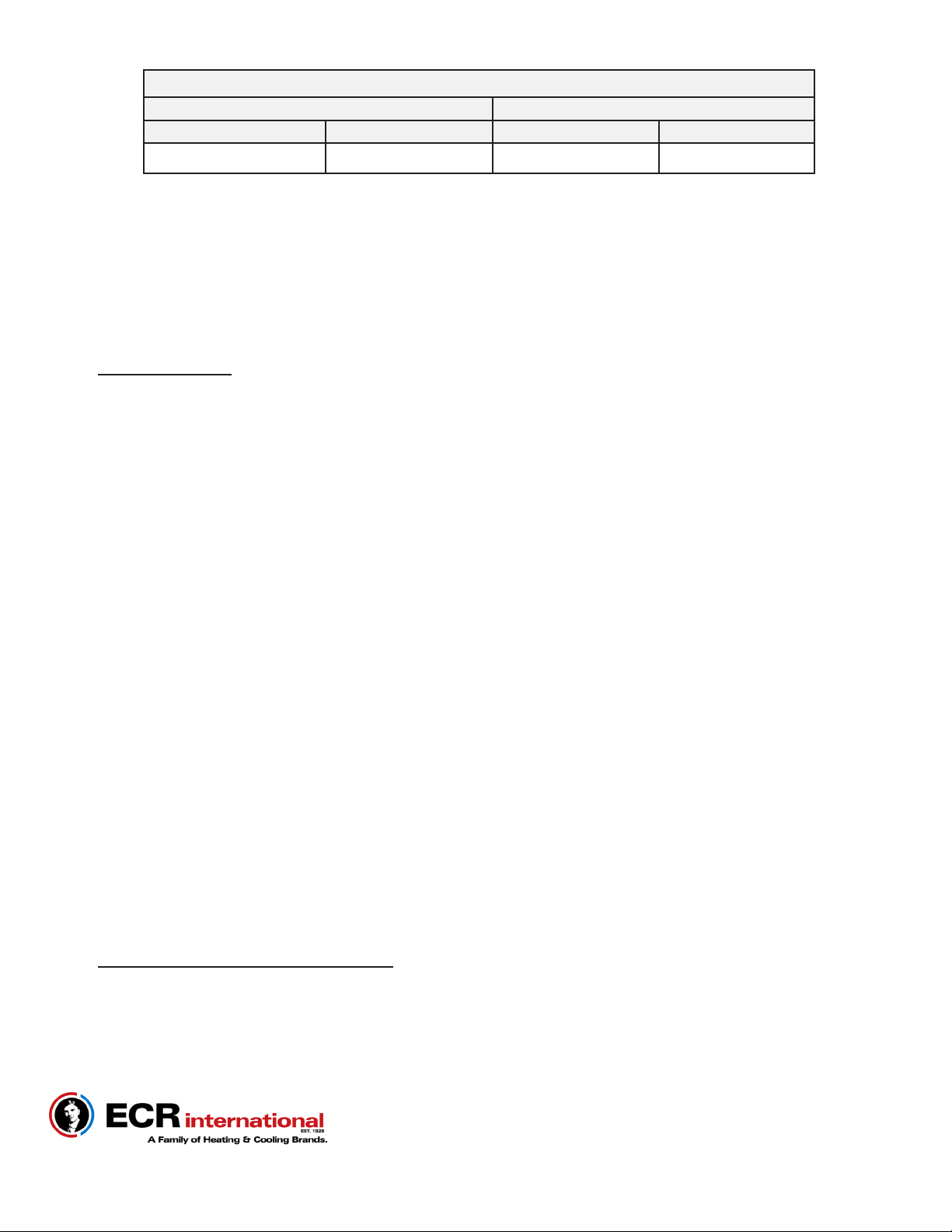
3.0" w.c. (0.7 kPa) 13.5" w.c. (3.3 kPa) 5.0" w.c. (1.2 kPa) 13.5" w.c. (3.4 kPa)
6.2.2 Combustion air blower shall be equipped with a variable speed blower to regulate the
amount of premix gas/air through the blower assembly and into the burner. The on board
control system shall regulate the speed of the blower to modulate the capacity of the boiler
from 20% input ring rate up to 100% input ring rate.
6.2.3 Gas Burner shall be constructed of a stainless steel mesh.
6.2.4 Ignition system shall consist of a direct spark igniter (DSI) and separate ame sensing rod.
7.0 Control System
7.1 Boiler Control System. Boiler shall feature an integrated modulating control. The control shall
sense the supply water, return water and outside air temperatures and adjusts the ring rate to
deliver the amount of heat needed to the structure.
Boiler Control System must consist of:
• Replaceable fuse /extra spare fuse shipped with the control.
• User interface with LCD screen display English text—boiler status indication .
Gas Supply Pressure
Natural Gas Propane
Min. Max. Min. Max.
• Function Programming Keys - Reset, Menu, Enter and arrow s (+ - ).
• Central Heating CH and Domestic Hot Water DHW set points. Domestic hot water priority
with programmable maximum priority time .
• Outdoor air sensor. Programmable reset curves and warm weather shutdown or xed
water temperature operation.
• Boost function temperature setting and adjustable boost time.
• Maximum power function to restrict ring rate in heat mode but allow full power in DHW
mode.
• Integral multiple boiler control capability up to 16 boilers. Requires an optional system
sensor
• Service reminder status display on the user interface with programmable settings in a
range of 1 to 999 days
7.1.1 The control system shall continuously monitor the boiler during operation and standby
modes. The control shall operate in such a manor to receive input data from the supply,
return and outdoor air temperature sensors and adjust the modulation rate accordingly.
7.1.2 The Boiler’s control system shall consist of the following safety devices factory installed
on the boiler: high limit temperature sensor, vent temperature sensor, heat exchanger
temperature limit, UL Listed, probe type Low Water Cut Off (LWCO).
8.0 Primary Secondary Piping System
8.1 The boiler shall be equipped with an internal primary loop and pump.
8.2 The internal primary loop piping system will contain a manually operated ball valve. The valve
shall be set by the factory in the full open position.
ECR International, Inc.
2201 Dwyer Avenue, Utica NY 13501
Tel: 1-315-797-1310
P/N 240010475 REV C, [04/2015]