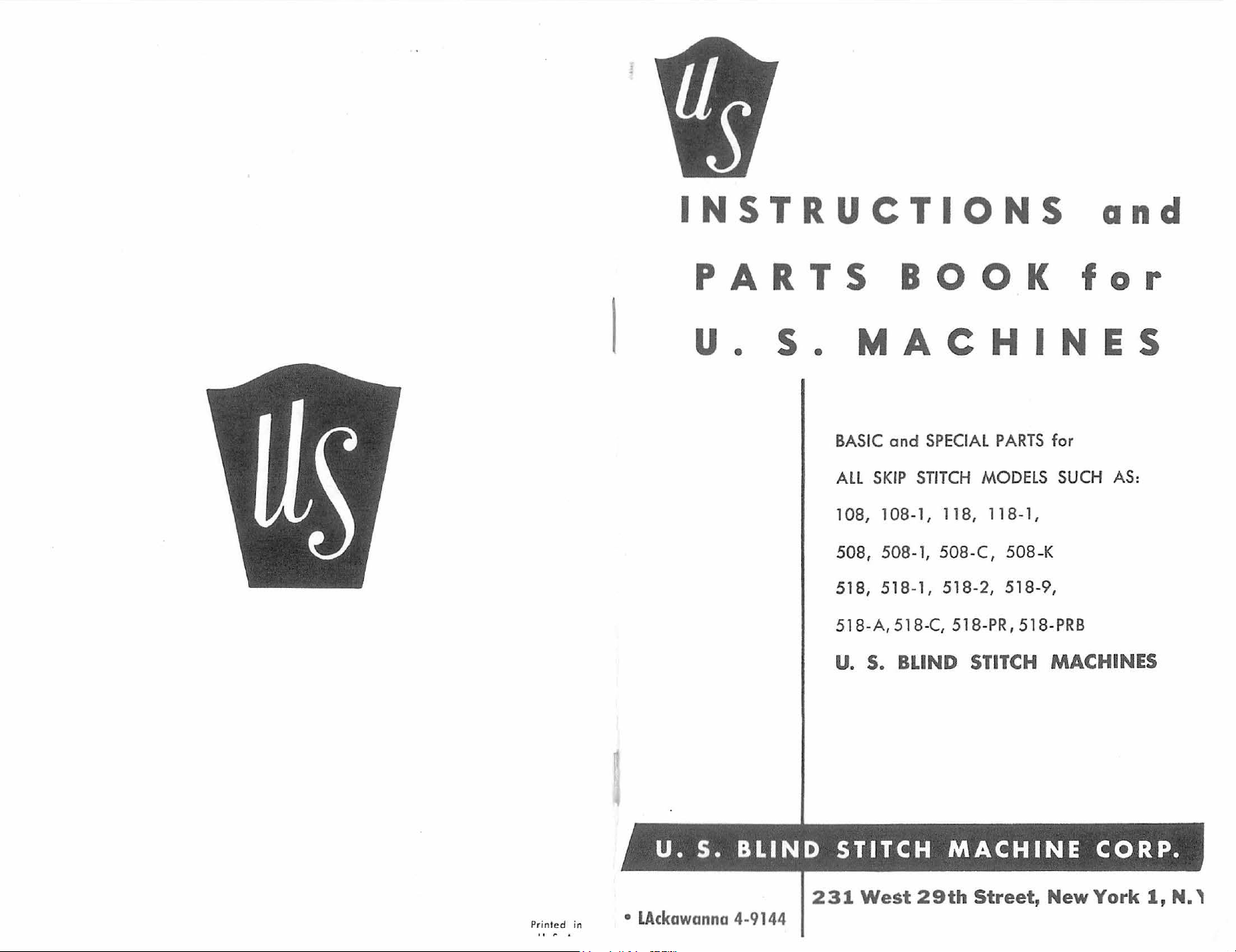
Pr
in
ted
in
INSTRUCTIONS
and
PARTS
BOOK
for
U.S.
MACHINES
BASIC
and
SPECIAL
PARTS
f
or
All
SK
IP
STITCH
MODELS
SUCH
AS
:
108,108
-
1,1
18,
118
-1,
508,
508
-
1,
508
-C, 5
08
-K
518,
518
-1,
518-2,
51
8-9
,
518-A,
518-C,
518
-
PR
, 518-
PRB
U. S.
BLIND
STITCH
MACHINES
U.
S.
BLIND
STITCH
MACHINE
CORP.
231
West
29th
Street,
New
York
1,
N.'
•
LAckawanna
4-9144
From the library of: Superior Sewing Machine & Supply LLC
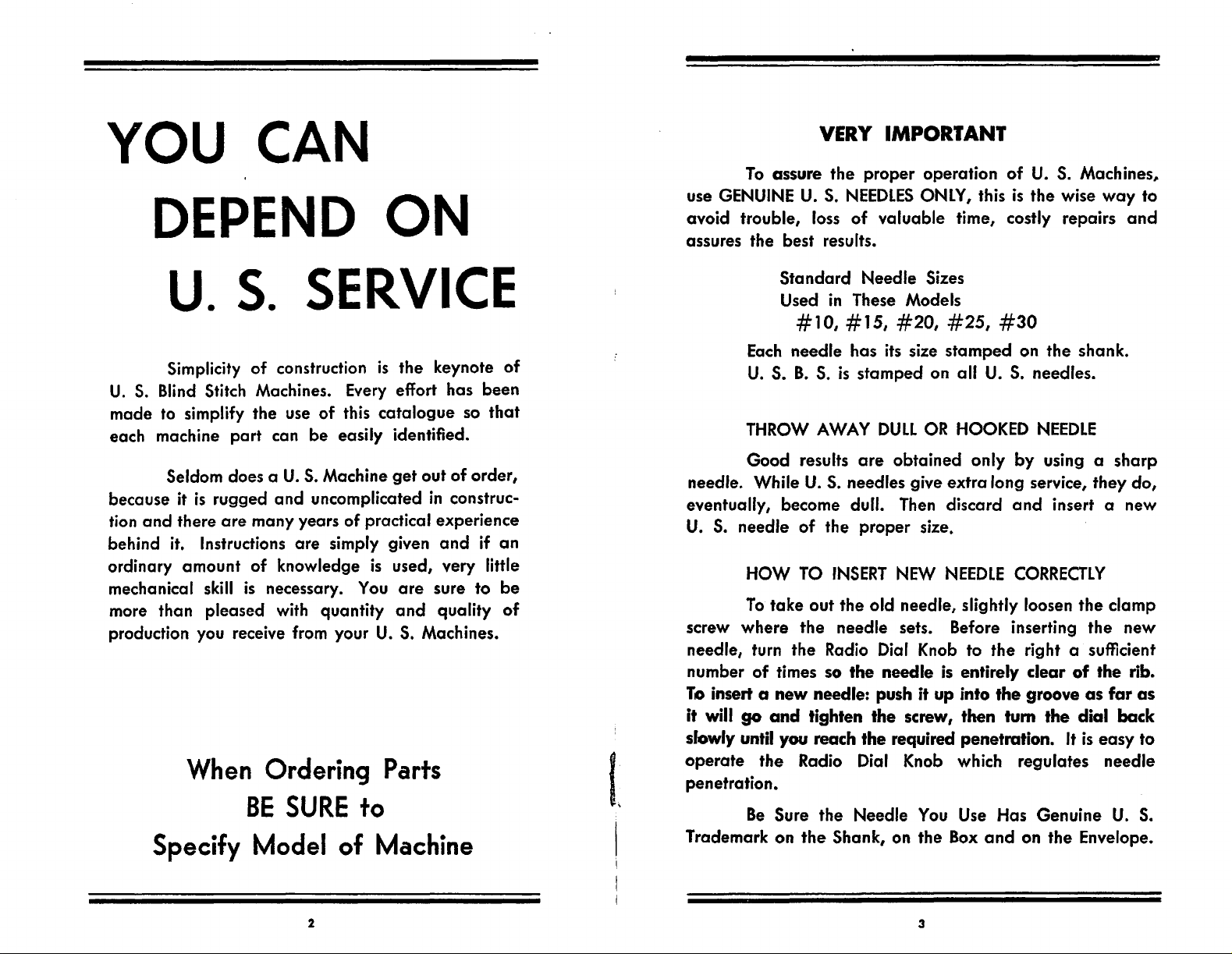
YOU
CAN
DEPEND
ON
U.
S.
SERVICE
Simplicity of construction
is
the
keynote
of
U.
S.
Blind
Stitch Machines. Every effort has been
mode to
simplify the use
of
this
catalogue
so
that
each machine port con
be
easily identified.
Seldom does
aU.
S. Machine
get
out
of
order,
because it
is
rugged
and
uncomplicated
in
construc-
tion
and
there
are
many years
of
practical experience
behind it. Instructions
are
simply given
and
if
an
ordinary
amount
of
knowledge
is
used, very little
mechanical skill
is
necessary.
You
are
sure to
be
more
than
pleased with quantity
and
quality
of
production you receive from your
U.
S. Machines.
When
Ordering Parts
BE
SURE
to
Specify
Model
of
Machine
2
t
I
VERY
IMPORTANT
To
assure
the
proper
operation
of
U.
S. Machines,.
use
GENUINE
U.
S.
NEEDLES
ONLY,
this
is
the
wise
way
to
avoid
trouble, loss
of
valuable time, costly repairs
and
assures the best results.
Standard
Needle Sizes
Used
in
These Models
# 10, # 15,
#20,
#25,
#30
Each needle has its size
stamped
on
the
shank.
U.
S.
B.
S.
is
stamped
on all
U.
S. needles.
THROW
AWAY
DULL
OR
HOOKED
NEEDLE
Good
results
are
obtained
only
by
using a
sharp
needle. While
U.
S. needles give
extra
long service,
they
do,
eventually, become dull. Then discard
and
insert a new
U.
S.
needle
of
the proper size.
HOW
TO
INSERT
NEW
NEEDLE
CORRECTLY
To
take
out
the
old needle, slightly loosen
the
clamp
screw where
the
needle sets. Before inserting the new
needle, turn
the
Radio Dial Knob to
the
right a sufficient
number
of
times
so
the
needle
is entirely clear
of
the
rib.
To
insert a
new
needle: push it up into
the
groove
as
far
as
it will
go
and
tighten
the
screw,
then
tum
the
dial
back
slowly until you reach
the
required penetration.
It
is
easy
to
operate
the
Radio Dial Knob which regulates needle
penetration.
Be
Sure the Needle
You
Use Has Genuine
U.
S.
Trademark on
the
Shank, on the
Box
and
on
the
Envelope.
3
From the library of: Superior Sewing Machine & Supply LLC
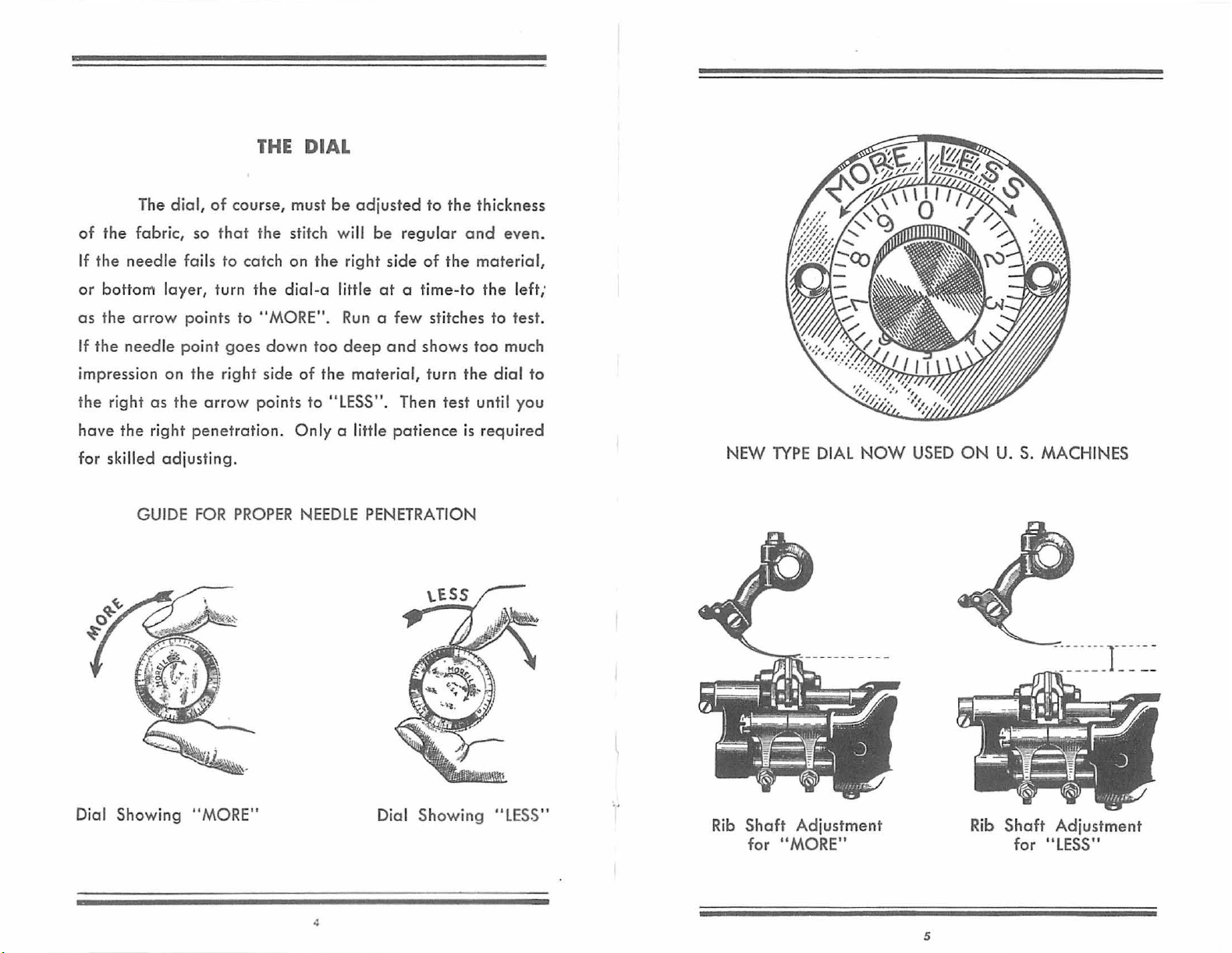
THE
DIAL
The
dial,
of
course,
must
be
adjusted
to
the
thickness
of
the
fabric,
so
that
the
stitch wi
ll
be
regular
and
even.
If
the
needle
fails
to
catch
on
the
right
side
of
the
material,
or
bottom
layer,
turn
the
dial
-a little
at
a
time
-
to
the
left;
as
the
arrow
points
to
"MORE".
Run
a
few
stitches
to
test.
If
the
needle
point
goes
down
too
deep
and
shows
too
much
impression
on
the
right
side
of
the
material,
turn
the
dial
to
the
right
as
the
arrow
points
to
"lESS".
Then
test
until
you
have
the
right
penetration.
Only
a little
patience
is
required
for skilled
adjusting.
GUIDE
FOR
PROPER
NEEDlE PENETRATION
Dial
Showing
"MORE"
Dial
Showin
g
"lESS"
NEW
TYPE
DIAl
NOW
USED
ON
U. S. MACHINES
Rib
Shaft
Adjustment
for
"MORE"
5
-.-
-.
..
·
1---
---
"
---
- -
--
--
Rib
Shaft
Adjustment
for
"lESS"
From the library of: Superior Sewing Machine & Supply LLC
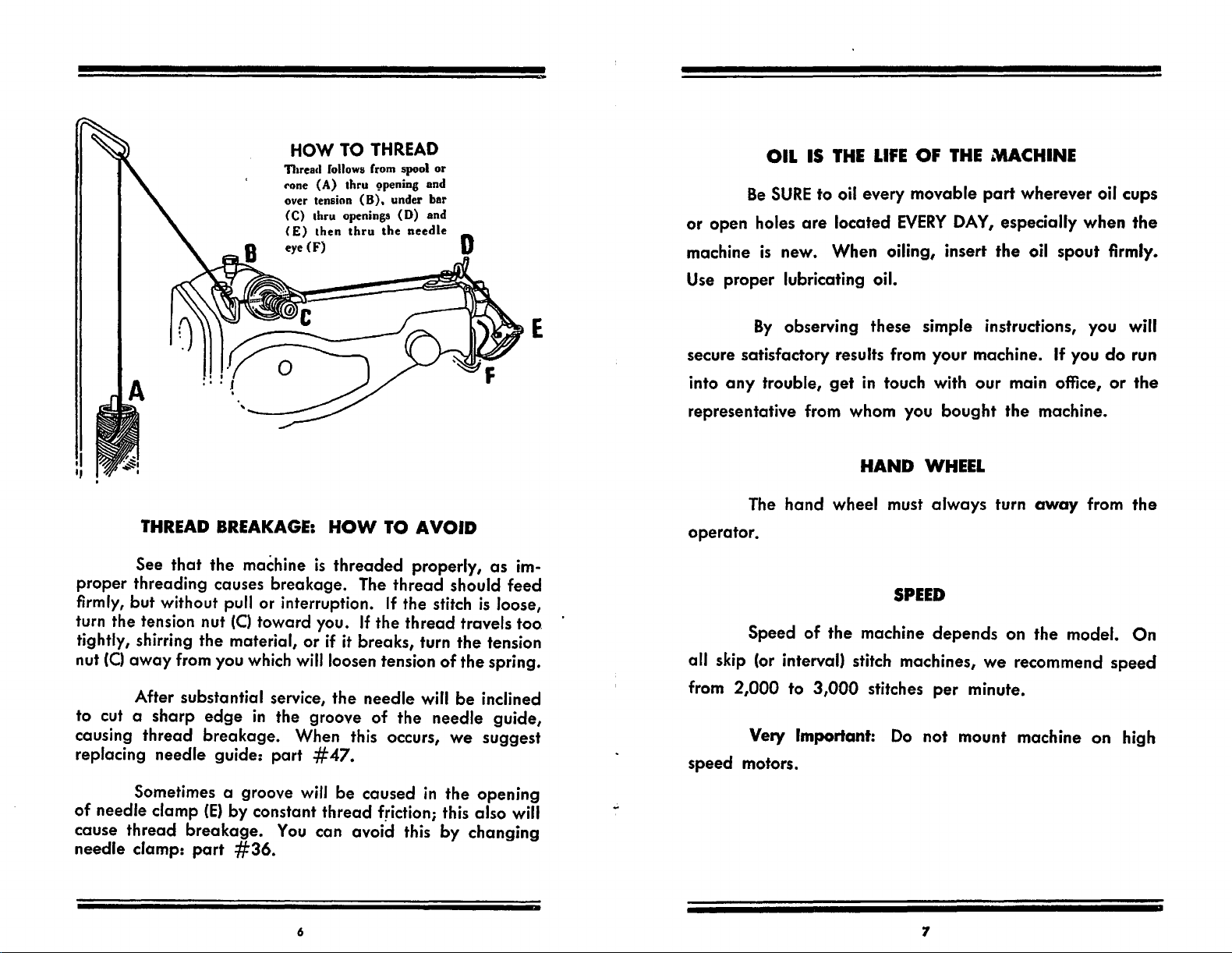
I
,,
HOW
TO THREAD
Thread
follows
from spool or
rone
(A)
thru 9pening and
over tension
(B),
under bar
(C)
thru openings (D) and
(E)
then
thru
the
needle
eye
(F)
THREAD
BREAKAGE:
HOW
TO
AVOID
E
See
that
the machine
is
threaded
properly,
as
im-
proper threading causes breakage. The
thread
should
feed
firmly, but without pull or interruption.
If
the stitch
is
loose,
turn the tension nut
(C)
toward you.
If
the
thread
travels too.
tightly, shirring the material, or
if
it breaks, turn
the
tension
nut
(C)
away
from you which
will
loosen tension
of
the
spring.
After substantial service, the needle
will
be
inclined
to cut a sharp
edge
in
the groove
of
the needle guide,
causing
thread
breakage.
When this occurs,
we
suggest
replacing needle guide:
part
#47.
Sometimes a groove will
be
caused
in
the opening
of
needle clamp
(E)
by
constant
thread
friction; this also will
cause
thread
breakage.
You
can avoid this
by
changing
needle
clamp:
part
#36.
6
.;.
OIL
IS
THE
LIFE
OF
THE
MACHINE
Be
SURE
to oil every movable
part
wherever oil cups
or
open holes
are
located
EVERY
DAY,
especially when
the
machine
is
new. When oiling, insert
the
oil spout firmly.
Use proper lubricating oil.
By
observing these simple instructions, you will
secure satisfactory results from your machine.
If
you
do
run
into
any
trouble,
get
in
touch with our main office,
or
the
representative from whom you
bought
the
machine.
HAND
WHEEL
The
hand
wheel must
always
turn
away
from
the
operator.
SPEED
Speed
of
the
machine
depends
on
the
model.
On
all skip (or interval) stitch machines,
we
recommend
speed
from
2,000
to
3,000
stitches
per
minute.
Very
Important:
Do
not mount machine on high
speed
motors.
7
From the library of: Superior Sewing Machine & Supply LLC
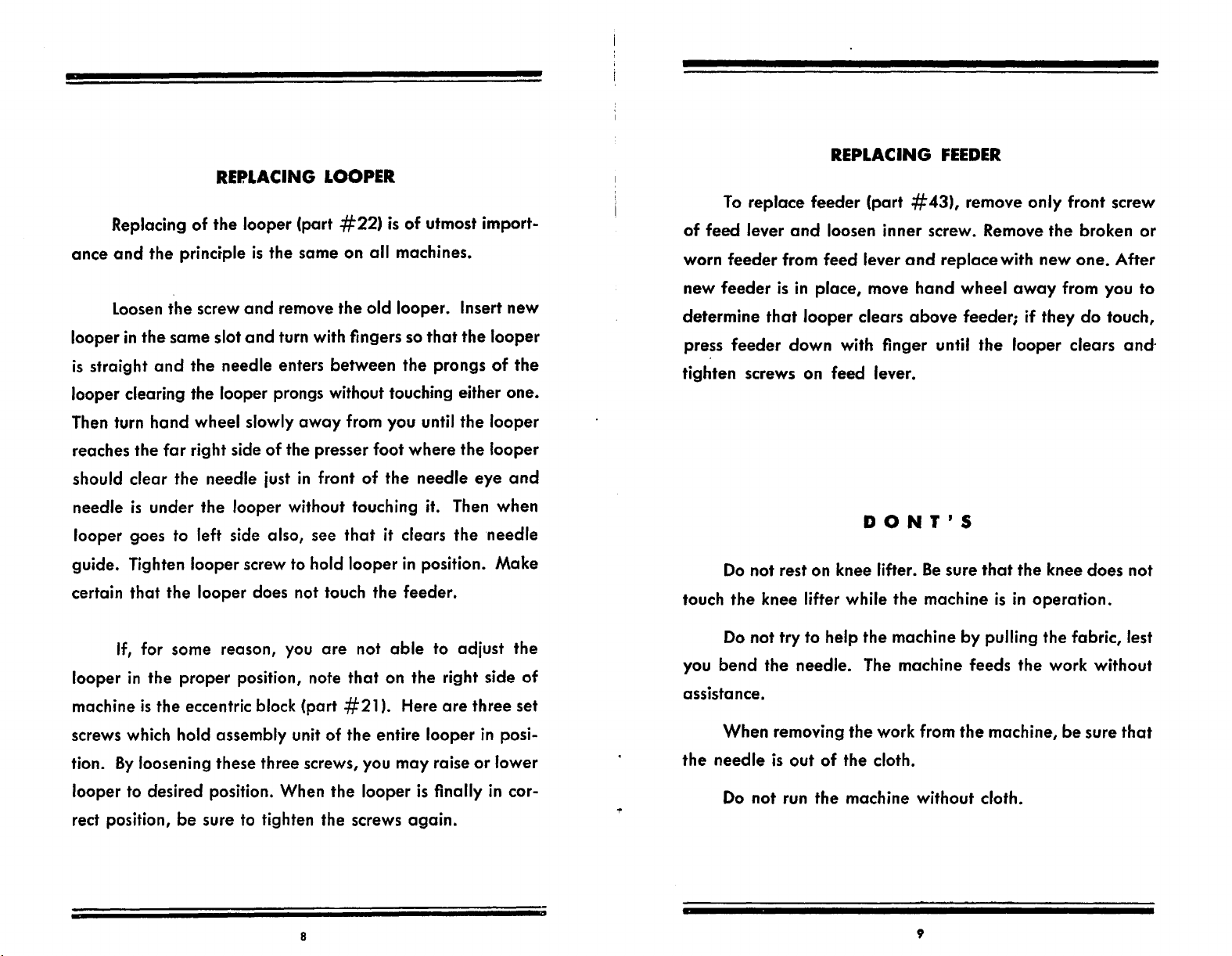
REPLACING LOOPER
Replacing
of
the
looper (part
#22)
is
of
utmost
importM
once
and
the princi-ple
is
the same on all machines.
Loosen
the
screw
and
remove the old looper. Insert new
looper
in
the
same
slot
and
turn with fingers so
that
the looper
is
straight
and
the
needle enters between the prongs
of
the
looper clearing the looper prongs without touching either one.
Then turn
hand
wheel slowly
away
from you until
the
looper
reaches the
far
right side
of
the presser foot where the looper
should clear the needle iust
in
front
of
the needle
eye
and
needle
is
under the looper without touching it. Then when
looper goes to left side
also, see
that
it clears the needle
guide. Tighten looper screw to hold looper
in
position. Make
certain
that
the looper does not touch the feeder.
If,
for some reason, you
are
not
able
to adiust the
looper
in
the proper position, note
that
on the right side
of
machine
is
the eccentric block (part
#21
).
Here
are
three set
screws which hold assembly unit of the entire looper
in
posiM
tion.
By
loosening these three screws, you may raise or lower
looper to desired position. When the looper
is
finally
in
cor-
rect position,
be
sure to tighten the screws
again.
8
,.
REPLACING
FEEDER
To
replace feeder (part
#43),
remove only front screw
of feed lever
and
loosen inner screw. Remove the broken
or
worn feeder from feed lever
and
replace with new
one.
After
new feeder
is
in
place, move
hand
wheel
away
from you to
determine
that
looper clears
above
feeder; if they
do
touch,
press feeder down with finger
until the looper clears and·
tighten screws on feed lever.
DO
NT'S
Do
not rest on knee lifter.
Be
sure
that
the knee
does
not
touch the knee lifter while the machine
is
in
operation.
Do
not try to help the machine by pulling the fabric, lest
you
bend
the needle. The machine feeds the work without
assistance.
When removing the work from the machine,
be
sure
that
the
needle
is
out
of
the cloth.
Do
not run the machine without cloth.
9
From the library of: Superior Sewing Machine & Supply LLC