
INDUSTRIAL
SEWING
riNEST
STYLES
63400
63400
63400
QUALI
®
TY
LB
LC
LV
MACHINES
-
'
u
CATALOG
No.
121
LB
CL
ASS
STREAMLINED
HIGH
SPEED
LOCKSTITCH
WITH
PNEUMATIC
"K
LIPP
UNION SPECIAL
CHICAGO
63400
MACHINES
-
IT~
THREAD
TRIMMER
CORPORATION
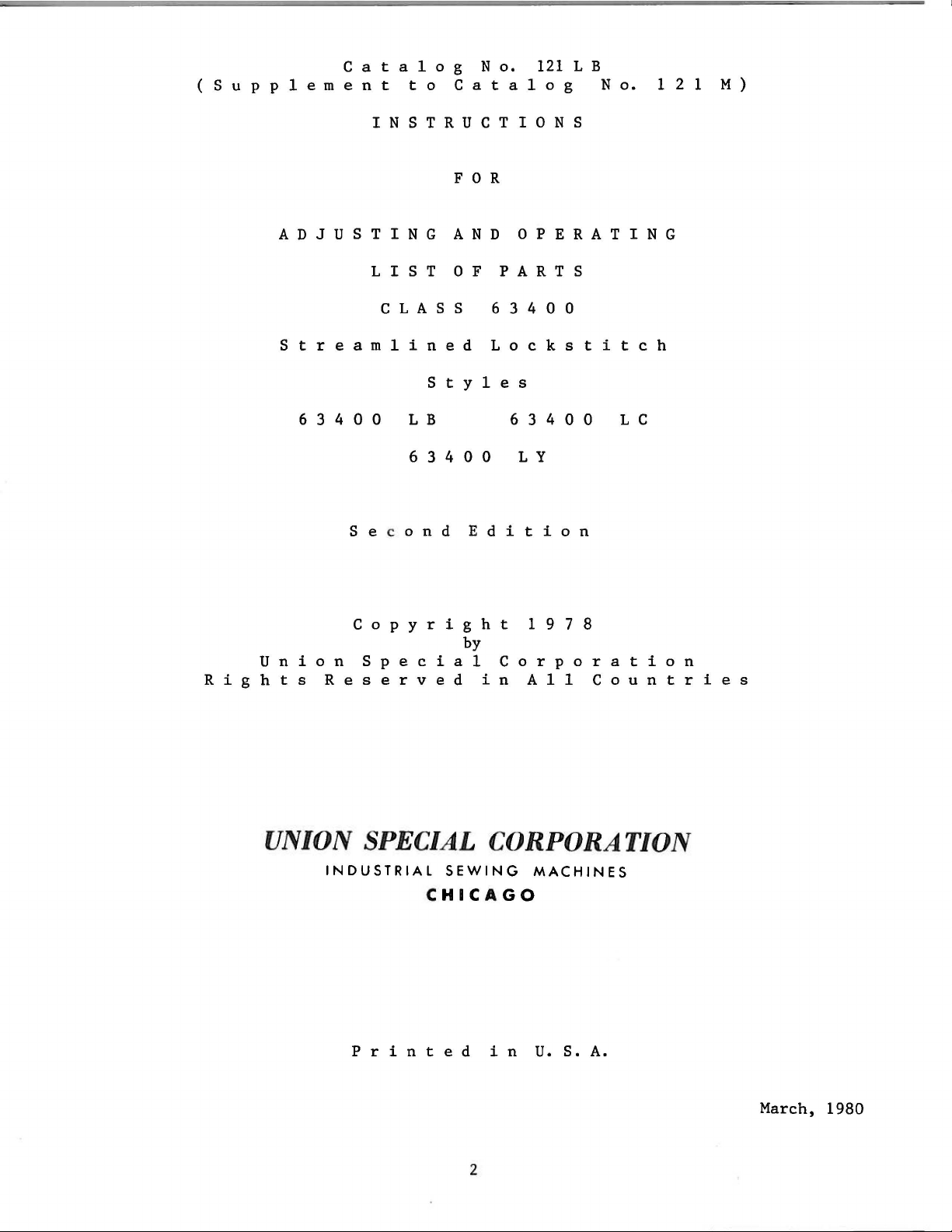
C a t a 1 o g N
o.
121 L B
( S u p p 1 e m e n t t o C a t a 1 o g N
I N S T R U C T I 0 N S
F 0 R
o.
1 2 1 M )
e
am
T I N G
L I
S T 0 F
L A S s
C
1 i
n e d L o c k s
s
AND
t y 1
A D J U S
t r
S
6 3 4 0 0 L B 6 3 4 0 0
6 3 4 0 0
S e c o n d E d i t i o n
0 P E R A T
PART
6 3 4 0 0
e s
L y
S
t i
I N G
t c h
L C
C o p y r i g h t 1 9 7 8
by
U n i o n S p e c i a 1 C o r p o r a t i o n
R i g h t s R e s e r v e d i n A 1 1 C o u n t r i e s
UNION SPECIAL CORPORATION
INDUSTRIAL
P r i n t e d i n
SEWING
CHICAGO
2
MACHINES
U.
S.
A.
March,
1980
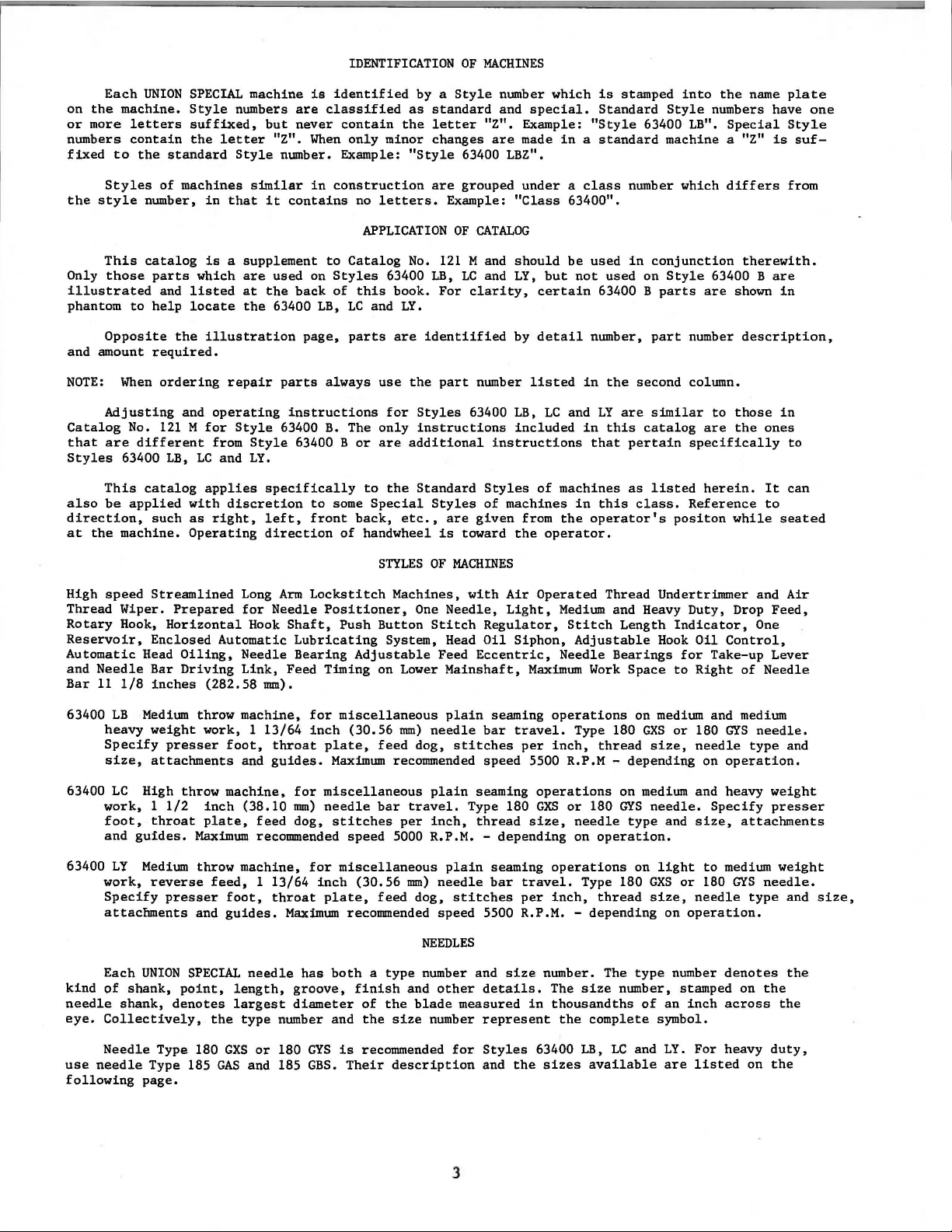
Each
on
the
or
more
numbers
fixed
UNION
machine.
letters
contain
to
the
SPECIAL
Style
suffixed,
the
standard
machine
numbers
letter
Style
IDENTIFICATION
is
identified
are
but
"Z".
classified
never
contain
When
number. Example:
only
by a Style
as
the
minor
"Style
OF
standard
letter
changes
63400 LBZ".
MACHINES
number
and
special.
"Z".
Example:
are
made
which
is
stamped
Standard
"Style
in a standard
into
Style
63400 LB".
numbers have
machine a "Z"
the
name
Special
is
plate
one
Style
suf-
Styles
the
style
This
Only
those
illustrated
phantom
Opposite
and
amount
NOTE:
Catalog
that
Styles
also
direction,
at
High
Thread
Rotary
Reservoir,
Automatic
and
Bar
When
Adjusting
are
63400
This
be
the
machine.
speed
Wiper.
Hook,
Needle
11
1/8
of
number,
catalog
parts
and
to
help
required.
ordering
No.
121 M for
different
LB,
catalog
applied
such
Streamlined
Prepared
Horizontal
Enclosed
Head
Bar
inches
machines
in
that
is a supplement
which
listed
locate
the
and
with
as
Operating
Oiling,
Driving
are
at
the
illustration
repair
operating
Style
from
LC
and
applies
discretion
right,
Long
for
Automatic
Needle
Link,
(282.58
similar
Style
LY.
left,
direction
Hook
mm).
in
it
used
the
63400
parts
63400 B. The
specifically
Arm
Needle
Shaft,
Feed Timing on Lower
construction
contains
to
Catalog
on
Styles
back
of
LB,
LC
page,
parts
always
instructions
63400 B
to
some
front
of
Lockstitch
Positioner,
Push
Lubricating
Bearing
no
letters.
APPLICATION
No.
63400
this
book.
and
LY.
are
identiified
use
the
for
Styles
only
or
to
back,
handwheel
Adjustable
instructions
are
additional
the
Standard
Special
etc.,
STYLES
Machines,
One
Button
System, Head
are
grouped
Example:
OF
CATALOG
121
M and
LB,
LC
For
clarity,
part
number
63400
Styles
are
given
is
toward
OF
MACHINES
with
Needle,
Stitch
Feed
Eccentric,
Mainshaft,
under a class
"Class
should
and
LY,
certain
by
detail
listed
LB,
included
instructions
Styles
of
Regulator,
Oil
of
machines
from
the
Air
Operated
Light,
Siphon,
Maximum
63400".
be
used
but
not
number,
in
LC
and
in
that
machines
in
the
operator's
operator.
Medium
Stitch
Adjustable
Needle
Work
number which
in
used
on
63400 B
the
second
LY
are
this
catalog
pertain
as
this
class.
Thread
and Heavy
Length
Bearings
Space
differs
conjunction
Style
parts
part
similar
listed
Undertrtmmer
Hook
63400
are
number
column.
to
are
specifically
herein.
Reference
positon
Duty,
Indicator,
Oil
Control,
for
Take-up
to
Right
from
therewith.
Bare
shown
in
description,
those
in
the
ones
to
It
can
to
while
Drop
of
seated
and
Feed,
One
Lever
Needle
Air
63400
LB
heavy
Specify
size,
63400
LC
work, 1 1/2
foot,
and
63400
LY
work,
Specify
attachments
Each
kind
of
needle
eye.
Collectively,
Needle
use
needle
following
Medium
weight
attachments
High
throat
guides.
Medium
reverse
UNION
shank,
shank,
Type 180
Type 185
page.
throw
work, 1 13/64
presser
throw
inch
plate,
Maximum
throw
feed, 1 13/64
presser
and
SPECIAL
point,
denotes
the
machine,
foot,
and
machine,
(38.10
feed
recommended
machine,
foot,
guides.
needle
length,
largest
type
GXS
or
GAS
and 185
throat
guides.
for
mm)
dog,
throat
Maximum
has
groove,
diameter
number
180
GYS
GBS.
for
miscellaneous
inch
(30.56
plate,
Maximum
miscellaneous
needle
for
inch
plate,
bar
stitches
speed
miscellaneous
(30.56
feed
recommended
both a type
finish
of
and
the
is
recommended
Their
mm)
feed
needle
dog,
recommended
plain
travel.
per
inch,
5000 R.P.M. -
mm)
needle
dog,
speed
NEEDLES
number and
and
the
other
blade
size
number
description
plain
bar
stitches
speed
seaming
Type 180
thread
plain
seaming
bar
stitches
5500 R.P.M. -
details.
measured
represent
for
Styles
and
seaming
travel.
per
5500 R.P.M -
operations
GXS
size,
depending
travel.
per
size
number. The
in
63400
the
sizes
operations
Type 180
inch,
operations
inch,
The
thousandths
or
needle
on
Type 180
depending
size
the
complete
LB,
available
thread
180
operation.
thread
LC
on medium and medium
GXS
or
180
size,
depending
on medium and
GYS
needle.
type
and
on
light
GXS
size,
on
type
of
and
number
an
symbol.
LY.
are
number, stamped on
GYS
needle
on
operation.
heavy
Specify
size,
to
medium
or
180
needle
operation.
denotes
inch
across
For
heavy
listed
attachments
GYS
needle.
type
weight
presser
needle.
type
the
duty,
on
the
and
weight
and
the
the
size,
3
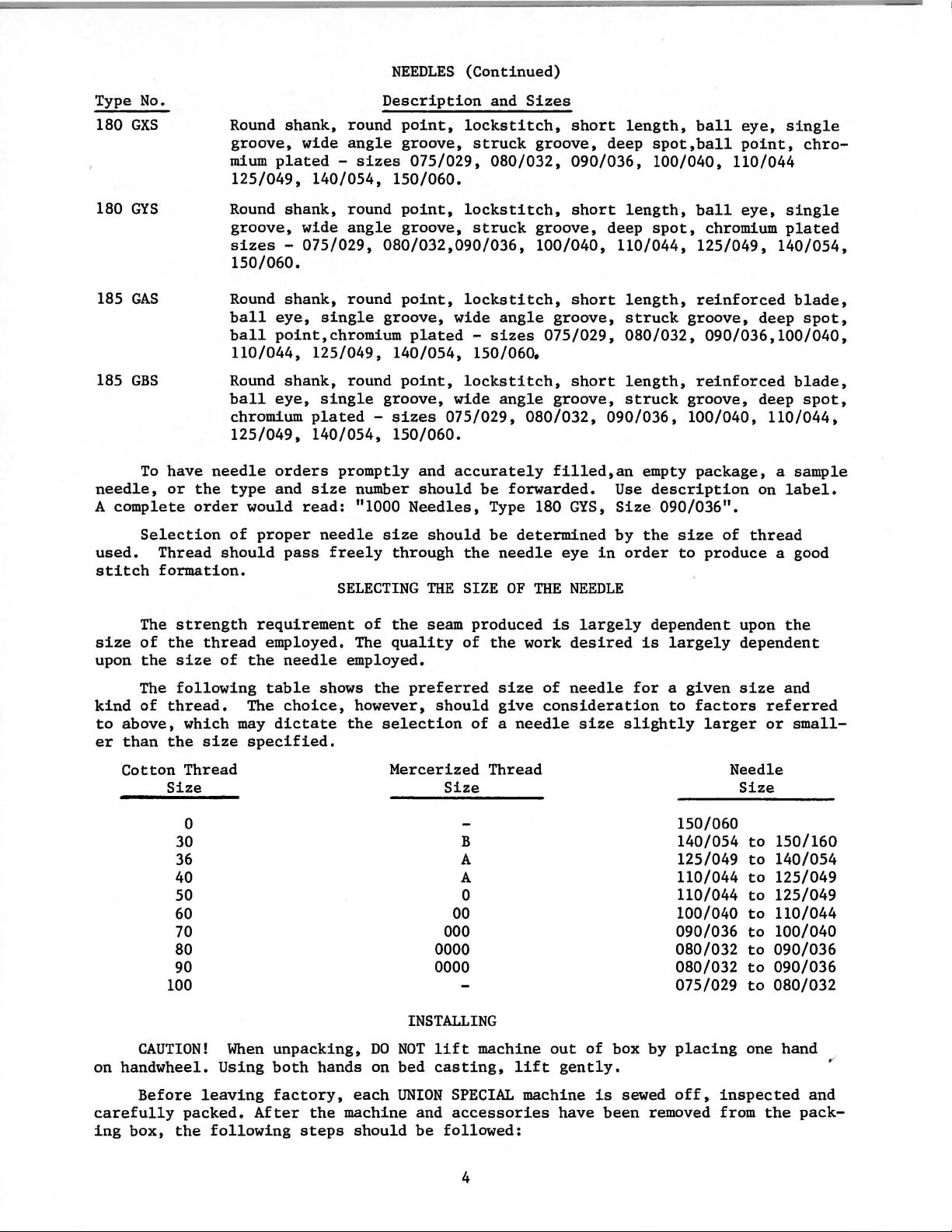
NEEDLES
(Continued)
Type No.
180
GXS
180
GYS
185
GAS
185
GBS
To
needle,
A
complete
Selection
used.
stitch
Round
groove,
mium
125/049,
Round
groove,
sizes -075/029,
150/060.
Round
ball
ball
110/044, 125/049,
Round
ball
chromium
125/049,
have
needle
or
the
type
order
of
Thread
formation.
should
shank,
wide
plated -sizes
140/054,
shank,
wide
shank,
eye,
single
point,chromium
shank,
eye,
single
plated -sizes
140/054,
orders
and
size
would
proper
pass
read:
needle
freely
Description
round
angle
round
angle
round
round
promptly
SELECTING
point,
groove,
075/029, 080/032,
150/060.
point,
groove,
080/032,090/036,
point,
groove,
plated -sizes
140/054,
point,
groove,
150/060.
and
number
"1000
should
Needles,
size
through
lockstitch,
lockstitch,
lockstitch,
wide
lockstitch,
wide
075/029,
accurately
should
the
THE
SIZE
and
Sizes
struck
struck
angle
150/060.
angle
080/032,
be
forwarded.
Type 180
be
determined
needle
OF
short
groove,
090/036,
short
groove,
100/040,
short
groove,
075/029, 080/032,
short
groove,
filled,an
GYS,
eye
THE
NEEDLE
length,
deep
length,
deep
110/044,
length,
struck
length,
struck
090/036,
empty
Use
Size
by
the
in
order
spot,ball
100/040,
spot,
description
090/036".
ball
eye,
single
point,
110/044
ball
eye,
chromium
125/049, 140/054,
reinforced
groove,
090/036,100/040,
reinforced
groove,
100/040,
package, a sample
size
of
thread
to
produce
chro-
single
plated
blade,
deep
spot,
blade,
deep
spot,
110/044,
on
label.
a good
The
size
of
upon
the
The
kind
of
to
above,
er
than
Cotton
CAUTION!
on
handwheel.
strength
the
thread
size
following
thread.
which
the
size
Thread
Size
0
30
36 A
40
50
60
70
80 0000
90
100
requirement
employed. The
of
the
table
The
may
dictate
specified.
When
unpacking,
Using
both
needle
shows
choice,
hands
of
the
quality
employed.
the
preferred
however,
the
selection
Mercerized
INSTALLING
DO
NOT
on bed
seam
should
Size
000
0000 080/032
lift
casting,
produced
of
the
size
give
of a needle
Thread
B 140/054
A 110/044
0
00
machine
is
largely
work
desired
of
needle
consideration
size
out
lift
gently.
of
dependent
is
largely
for a given
to
slightly
150/060
125/049
110/044
100/040
090/036
080/032
075/029
box by
placing
factors
larger
upon
the
dependent
size
and
referred
or
Needle
Size
to
150/160
to
140/054
to
125/049
to
125/049
to
110/044
to
100/040
to
090/036
to
090/036
to
080/032
one hand
small-
Before
carefully
ing
box,
leaving
packed.
the
following
factory,
After
the
machine and
steps
each
should
UNION
be
SPECIAL
accessories
followed:
4
machine
have
is
been
sewed
off,
removed from
inspected
the
and
pack-
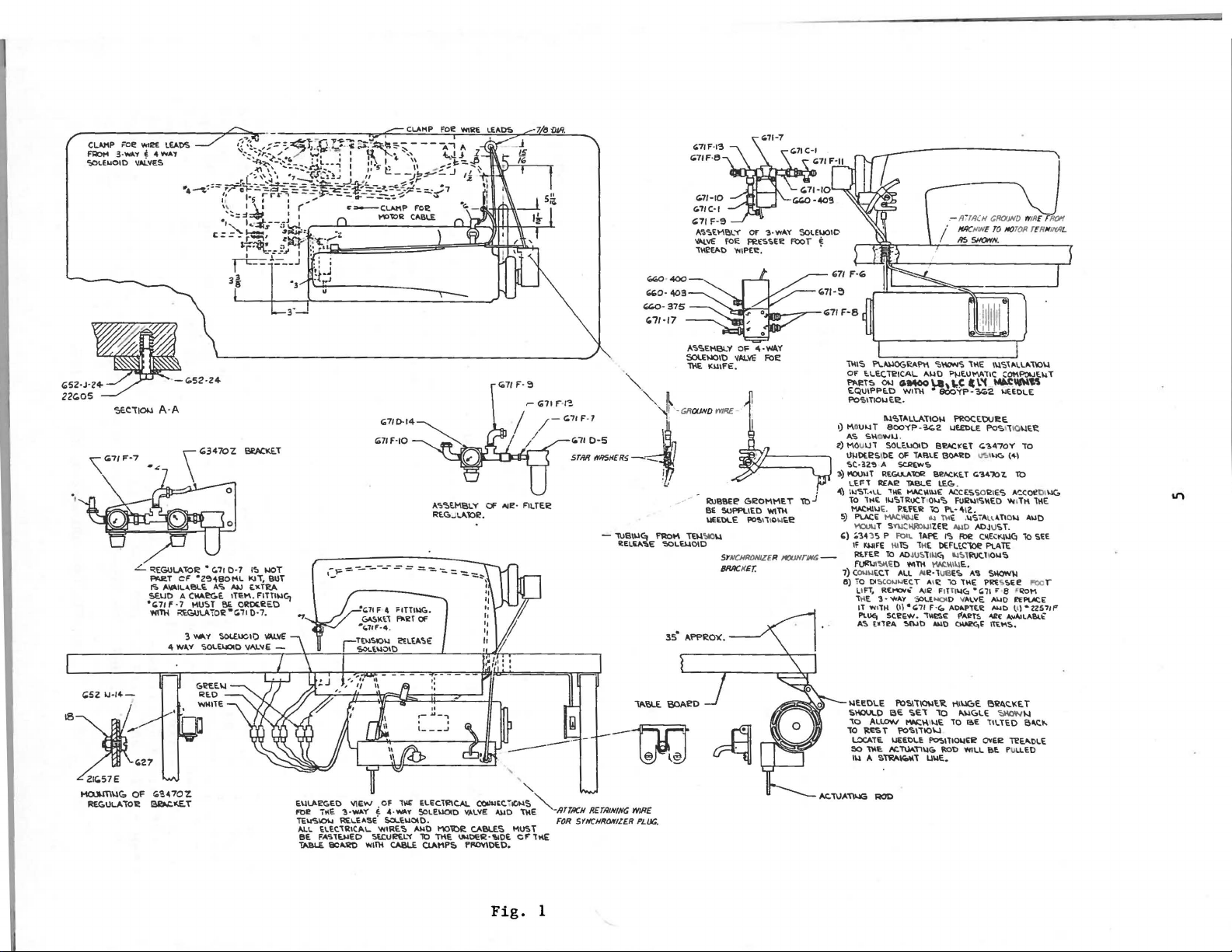
CLIIIIP
Foe
fA:>tt
':IOI..Et.aOI D vlti..VES
"'2E
3 ·
WAY
£ 4 'I¥Al
LEADS
<071F·I3
t;71 F·S
717
<;71
F· ll
Ee
R
lf()tJNf/116
SOlEIJOIO
RX>T
j
-10
<103
t
1111<;.
1'\.~EA!'>\
OF
ELECTeiCAL
PII.ET"'
01.1
EQUII'PE.O
Po'>ITIOIJt£!..
1\.I':>TI'\.\.Al\ON
1)
MO
U'-IT
""'
"'>\CWU.
Z)
MOUIJl
liiiDteS\tlE
SC·3Z~
A SCREWS
~)
MOOI.IT
REGUlA10R
LEF 1 R£-'11 ll<BI..E LE.(; .
IIJST.•lL
'I)
To
1"E
MA.C>III.I
t . P.
S)
PLI<Cii:
YOW
T
')
;3~
35 P
IF
....
-
FE
=~'!»\~[)
7)
C
OO<IJ
EC.T
8)
TO
DI
~COtJ~
L\
f:'T
, RO"'rtti
ll<t 3 •
IT W•TH
PLUEi
AS t•TI!A.
.-
lr!II(H
!IRC
JIIHE TO
•
/
RS
SHOWN
<;.\lOWS
11\E 1\.1';11<ll1<110\.l
A.IJ[) I'IJE\l"""11C
~Melo~\\.~t\.'(
WIT)\
BOo'fP-~2
eoo.,-P-~Z
SOLE.IJOIO
OF
'liE
MAC\III.IE
IIJ<;.H~UCT
EH.R
MA.C""'E
S
YIJC~IJI
fOOL
wr.; 1HE I>EFLtC10e PlATE
AOV:,
ALL
EC.T AI
"'"' •.;cu
(1\ • <071 F·c;.
sceew.
~[)
~ttliJ~E.
\JEEOLE
B~~ET
TABLE 130AeD
81!/loCKE.T
~"3470l.
A.CCESS
•
O"<;,
FU21o11'>\\tD
TO
Pl.·
~12.
o1.1
1\<
E ,\,jSo
ZE~
A>lD
TA.PE
-">JUST.
,.,_
RlE
~li~~~~~:I!\KIIOIJ"'
,.
~·1
\JS
E.,_
A~
~
10
l~E ~~S
"~C2' Ftlt'
\.l~
•
"'O
D V
,O.lVE
A!>t.I'Re
'"~"
,.
..
.,~
A.IJO
c...ec,• tlO<::O.
t;7HO
C#71C·I
~
t;71
F-9
.a.'>'>EK!ILY
1/Ai.l/€
11\I?EAD
~-375
1<.71
· 17
,a.';<;.El'ISLY
SOlEWOIO
"''"~''"'"..__
22~05
SECTIQI..l
A-A
L
~EGULA.TOR
~T
F..
,0.\ll.ILA.Bl.E.
·~~~
_:
'MlH
REGULA.Toe•c;7, o -7.
4WA.'f
---------------~
~E.T
.0.'>'1>E.I-I8LY
RtG~LA.TOI!
•
C.71
0 · 7
I~
CF
"Z'!l"BO!<L
A<;.
~~E&'T~~~~~c
1W
IJOT
I<JT,
EXT~
BUT
1
t~l=-::.-------=-=
.::::.-::,.
.
cr'
,..
...
7, f ·
!l
,-
"'I!·
Gi11 F·l'!.
/
FllTEI?
-1<.71F
1<.710
STIIJl
~
· 7 1
· 5
IYRSJI(RS
--
- l\JBII-IGt FRo>\ Tei.I
RELSASE
"t\o\E
-
"'
·
"'~
-GROOND
! '
SOLWOID
or
FOE
PRES'>U~
'HIPE'e. •
OF
"-~'f
~llJ..\1€
KU\f'€
.
WIRE
•J.'
f-----..,
!all!&
f.'
<;11!01"\l'IE. T TO
BE
SUI'f'I.IED
\IEEt".E I'OSii tOIJ
'OI0
\.1
SY
NOIRON!ZE
BRI/CKET.
?.·wA.Y
FOR
WITh
t;ROUND WJR£7fit:Jif
110
701<
fERJivrRL
.
~01'\PoutiJT
~~1.'\
IJ~EOLE
Po.,_I\IO
~U:
~"?.470'1'
TO
~\..C.
("\
TO
02 1
E.,_
A.~Cat!DIIJ(;
..,ITH
l~E
A.L<A.TIO>J
A.IJ[)
QlE<:I<I\l{:o
To
SEE
'i»>IWII
~Ee
,1\
Plt)O
F'
8 1
Qot'\
AIJD
IIEPUCE
,..., Vl.lZS71F
""'•
A.""'LA.Bl.-
ll'\
T
GI!EE\.1
<03"70Z
~to
WHITE.
E.\JLA.EGEO
>ne
T~E
?. ·
Te\6\0\.1
Ri.I.EASE.. SO...EIJOI[).
llJ..L
ELE<:lltiCAL. WIRE'!\
BE.
FA.'>lE.»ED
TI.BLE 80A.Rtl
VIEW
WA'f
OF
i " ·
5U:UI<!E.L'<
WIT\\
c...aLE
l\4£
WAY
ELEC.ll11c...L
50LE\JOIO
-""0
l'lO"Il:>R
10
~E
CLI<11P'!\
OlolNtC.
V,.LVE
"-110
CA.6l£.<;. MU'ST
INI:i£R·'!oiOE
I'I!OVIOEO.
Fig.
,,
TICIJS
eF
TilE
~
1KE:
1
IITTIICH
FOR
~sz
u-1+-
18j
,
<0'2.7
ZIC.57E
MOJ.ITI\.IG.
OF
RE.GU~"TO'e
~I<.E.T
lAI!U.
-oo
IIETII!N/NG
SrlfCHIIOII'IZ£R PLUG.
WJIIE
'60Af.'0
I.IEEDLE I'OSI"t\0\.IE'il ~~~E
S~O
ee.
"'ET
iO
UIJE.
TO
!tOll
"-\.l<i.LE
BE
WILL !lot PULLED
iO
ALI.DW
lO
'ltES l 1'0"'1"110\..l
l..OCJI.TE.
\JEEDLE f'O!.ITI0\1;1'!
SO
TI<E.
K.TUI\n\lc;.
I~
A
s"I'R,o."-111
ROD
Mot\oC~I'-IE
Bl!o\C:.l<ET
"""""'
liLTEO
OVE12
TeE.A.t>LE
\.!
B":"-
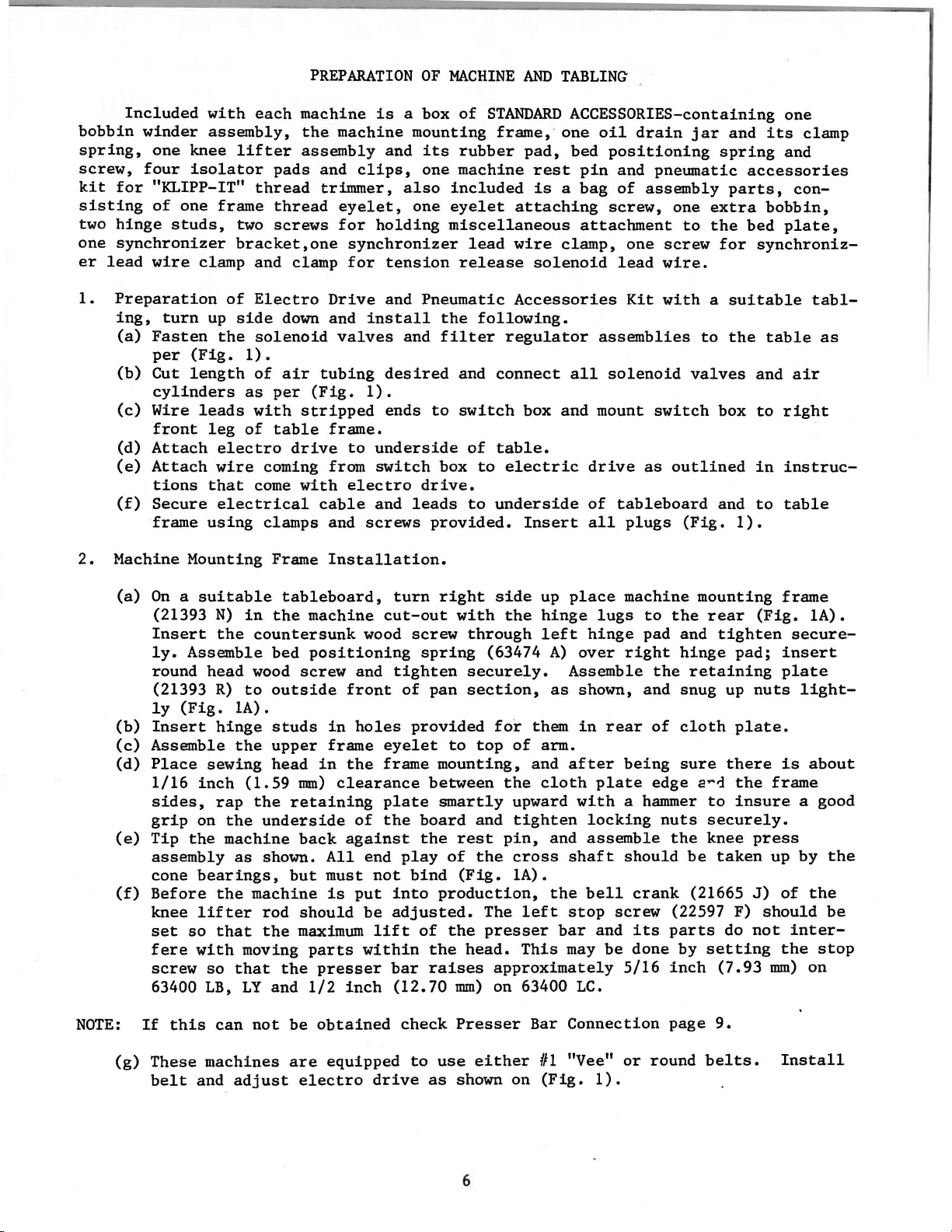
PREPARATION
OF
MACHINE
AND
TABLING
Included
bobbin
spring,
screw,
kit
for
sisting
two
hinge
one
synchronizer
er
lead
1.
Preparation
ing,
(a)
(b)
winder
one
four
"KLIPP-IT"
of
wire
Fasten
per
Cut
with
assembly,
knee
lifter
isolator
one
frame
studs,
two
bracket,one
clamp and clamp
of
turn
up
side
the
(Fig.
length
cylinders
(c)
Wire
(d)
Attach
(e)
Attach
(f)
2.
Machine Mounting Frame
leads
front
tions
Secure
frame
leg
electro
wire
that
electrical
using
each
machine
the
assembly
pads
and
thread
thread
screws
Electro
down
solenoid
1).
of
air
tubing
as
per
(Fig.
with
of
stripped
table
drive
coming from
come
with
cable
clamps and
is
machine
and
clips,
trimmer,
eyelet,
for
holding
synchronizer
for
tension
Drive
and
and
install
valves
desired
1).
ends
frame.
to
underside
switch
electro
and
screws
Installation.
a box
of
mounting
its
rubber
one
machine
also
one
included
eyelet
miscellaneous
release
Pneumatic
the
and
filter
and
to
switch
box
drive.
leads
provided.
STANDARD
frame,
pad,
rest
attaching
lead
wire
Accessories
following.
regulator
connect
box and mount
of
table.
to
electric
to
underside
Insert
ACCESSORIES-containing one
one
oil
bed
pin
is a bag
attachment
clamp,
solenoid
assemblies
all
drive
of
all
drain
positioning
and
of
screw,
one
lead
Kit
solenoid
as
tableboard
plugs
jar
and
spring
pneumatic
assembly
one
screw
to
parts,
extra
the
for
wire.
with a suitable
to
the
valves
switch
box
outlined
and
(Fig.
its
clamp
and
accessories
con-
bobbin,
bed
plate,
synchroniz-
table
and
air
to
right
in
instruc-
to
table
1).
tabl-
as
NOTE:
(a)
On a suitable
(21393
Insert
ly.
round
(21393
ly
(Fig.
(b)
Insert
(c)
Assemble
(d)
Place
1/16
sides,
grip
(e)
Tip
assembly
cone
(f)
Before
knee
set
fere
screw
63400
If
this
tableboard,
N)
in
the
the
countersunk
Assemble bed
head
wood
R)
to
outside
1A)
•
hinge
sewing
inch
rap
on
the
machine
bearings,
the
lifter
so
that
with
so
LB,
can
the
(1.59
the
the
underside
as
shown.
machine
rod
the
moving
that
LY
not
studs
upper
head
retaining
but
the
and
be
machine
wood
positioning
screw
and
front
in
holes
frame
in
the
mm)
clearance
of
back
against
All
end
must
is
put
should
be
maximum
parts
within
presser
1/2
inch
obtained
turn
cut-out
screw
tighten
of
provided
eyelet
frame
plate
the
play
not
bind
into
adjusted.
lift
bar
(12.70
check
right
with
through
spring
securely.
pan
section,
to
top
mounting,
between
smartly
board
the
rest
of
and
the
(Fig.
production,
The
of
the
presser
the
head.
raises
mm)
Presser
side
up
place
the
hinge
left
hinge
(63474
A)
over
Assemble
as
shown, and snug up
for
them
in
of
arm.
and
after
the
cloth
upward
tighten
pin,
cross
with
and
shaft
locking
assemble
1A).
the
bell
left
stop
bar
This
may
approximately
on 63400
Bar
Connection
LC.
machine
lugs
right
rear
being
plate
a hammer
should
screw
and
be
5/16
to
the
pad and
the
of
edge
nuts
the
crank
(22597 F)
its
parts
done
inch
page
mounting
rear
tighten
hinge
retaining
cloth
sure
there
a~1
to
securely.
knee
be
taken
(21665
do
by
setting
(7.93
9.
(Fig.
pad;
nuts
plate.
the
frame
insure
press
up
J)
should
not
mm)
frame
1A).
secureinsert
plate
light-
is
about
a good
by
of
the
interthe
stop
on
the
be
(g)
These
belt
machines
and
adjust
are
equipped
electro
drive
to
as
use
either
shown on
6
Ill
(Fig.
"Vee"
1).
or
round
belts.
Install
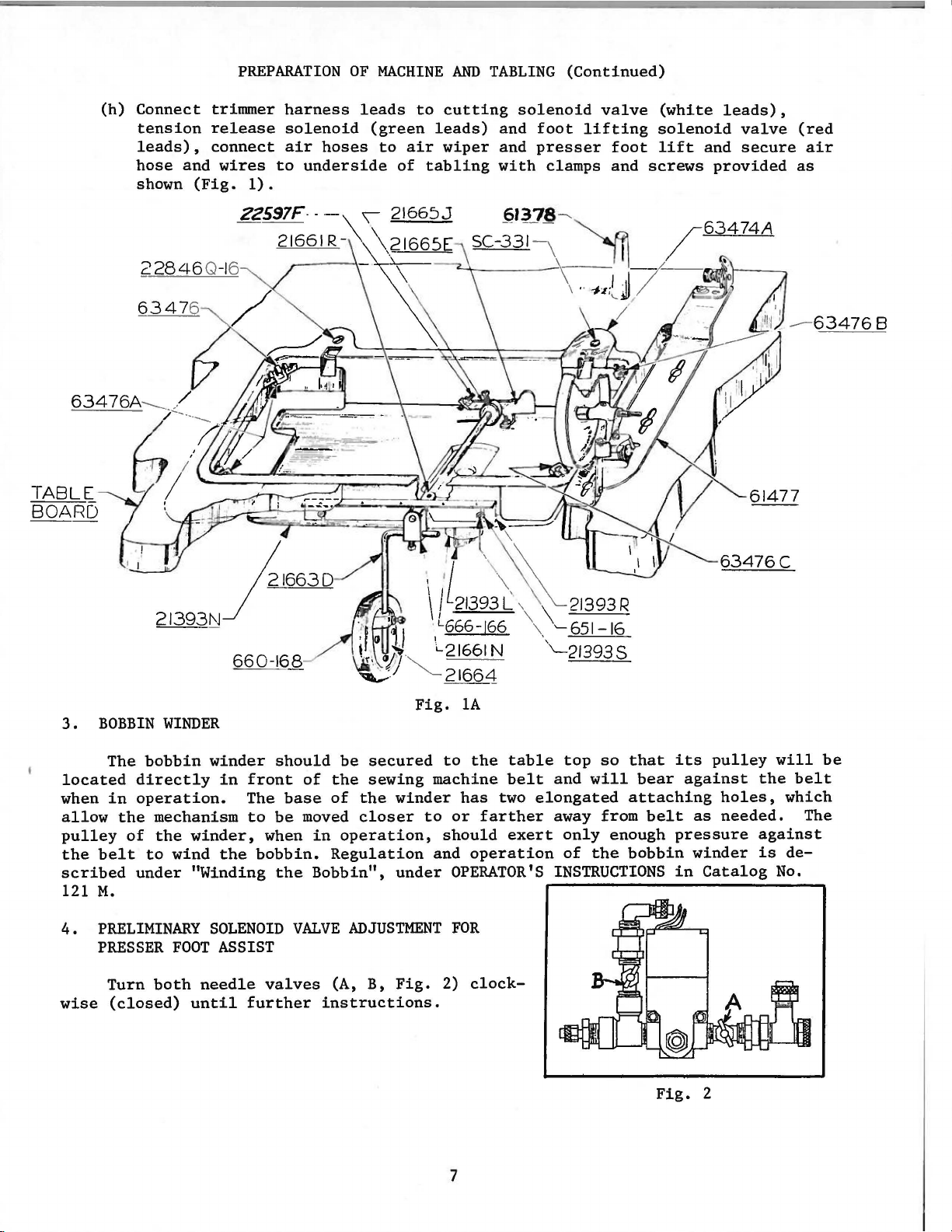
(h)
Connect
tension
leads),
hose
and
shown
PREPARATION
trimmer
release
connect
wires
(Fig.
1) .
22597F---
harness
solenoid
air
hoses
to
underside
OF
MACHINE
leads
(green
to
air
of
AND
to
cutting
leads)
wiper
tabling
TABLING
solenoid
and
foot
and
presser
with
clamps and
(Continued)
valve
lifting
foot
screws
(white
solenoid
lift
and
provided
leads),
valve
secure
(red
air
as
TABLE
BOARD
---
3.
22846Q-1
6347
BOBBIN
6
6
" }
213931\J
660-168
WINDER
216630
Fig.
61477
1A
The
located
when
allow
pulley
scribed
4.
wise
in
the
of
the
belt
121
M.
PRELIMINARY
PRESSER
Turn
(closed)
bobbin
directly
operation.
mechanism
the
winder,
to
wind
under
FOOT
both
"Winding
needle
until
winder
in
the
SOLENOID
ASSIST
should
front
The
to
be
when
bobbin.
the
valves
further
of
the
base
of
moved
in
Regulation
Bobbin",
VALVE
(A, B,
instructions.
be
secured
sewing
the
closer
operation,
ADJUSTMENT
machine
winder
to
under
Fig.
to
the
has
two
or
farther
should
and
operation
OPERATOR'S
FOR
2)
clock-
7
table
belt
exert
top
and
elongated
away from
only
of
INSTRUCTIONS
so
will
enough
the
that
its
bear
attaching
bobbin
belt
pressure
in
Fig.
against
as
winder
pulley
holes,
needed.
Catalog
2
will
the
belt
which
The
against
is
de-
No.
be
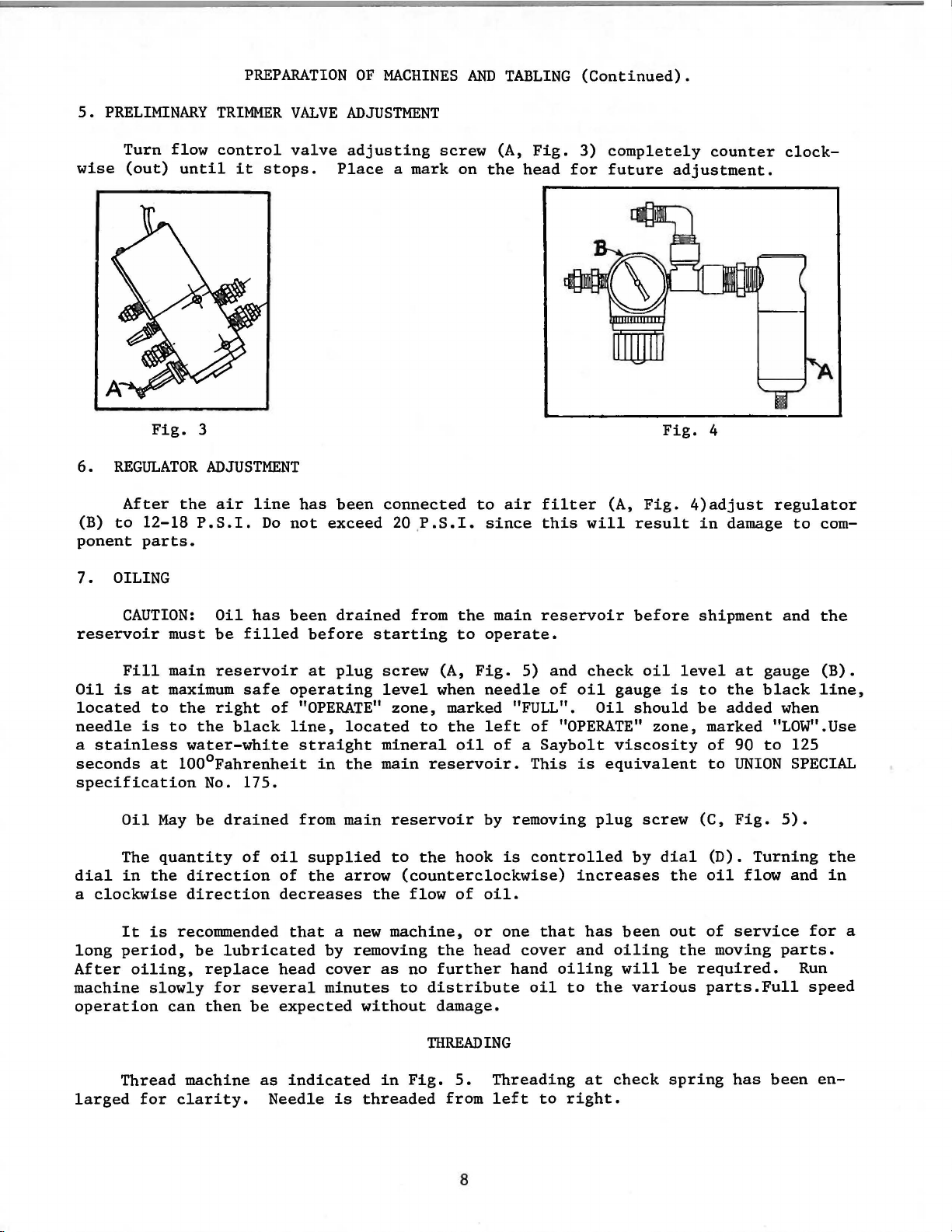
5.
PRELIMINARY
PREPARATION
TRIMMER
VALVE
OF
MACHINES
ADJUSTMENT
AND
TABLING
(Continued).
Turn
wise
6.
(B)
ponent
7.
(out)
REGULATOR
After
to
OILING
flow
until
Fig.
the
12-18
parts.
control
it
stops.
3
ADJUSTMENT
air
line
P.S.I.
Do
valve
has
not
exceed 20.
adjusting
Place
been
connected
screw
a mark on
P.S.I.
(A,
the
to
since
air
Fig.
head
filter
this
3)
completely
for
future
(A,
will
adjustment.
Fig.
Fig.
result
counter
4
4)adjust
in
damage
clock-
regulator
to
com-
CAUTION:
reservoir
Fill
Oil
is
at
located
needle
a
stainless
seconds
specification
dial
a
clockwise
long
After
machine
operation
to
is
at
Oil
May
The
quantity
in
the
It
is
period,
oiling,
slowly
Oil
has
must
main
maximum
can
be
filled
reservoir
safe
the
right
to
the
black
water-white
100°Fahrenheit
No.
175.
be
drained
of
direction
direction
recommended
be
lubricated
replace
for
several
then
be
been
before
at
operating
of
"OPERATE"
line,
straight
in
from
oil
supplied
of
the
decreases
that
by
head
expected
cover
minutes
drained
starting
plug
a new
screw
level
located
mineral
the
main
main
arrow
the
removing
as
without
from
zone,
reservoir
to
(counterclockwise)
flow
machine,
no
to
the
main
to
operate.
(A,
Fig.
when
to
reservoir.
the
the
further
distribute
damage.
THREADING
needle
marked "FULL".
the
left
oil
of a Saybolt
by
removing
hook
of
oil.
or
head
is
one
hand
cover
reservoir
5)
and
of
oil
of
"OPERATE"
This
oil
is
controlled
increases
that
has
and
oiling
to
before
check
Oil
plug
the
oil
gauge
should
viscosity
equivalent
screw
by
been
oiling
will
various
level
is
zone,
dial
the
out
the
be
shipment
at
to
the
be
added
marked "LOW".Use
of
90
to
UNION
(C,
Fig.
(D).
oil
of
service
moving
required.
parts.Full
and
gauge
black
when
to
5).
Turning
flow
parts.
the
(B).
line,
125
SPECIAL
the
and
in
for
Run
speed
a
Thread
larged
for
machine
clarity.
as
indicated
Needle
is
threaded
in
Fig.
5.
from
8
Threading
left
to
at
right.
check
spring
has
been
en-
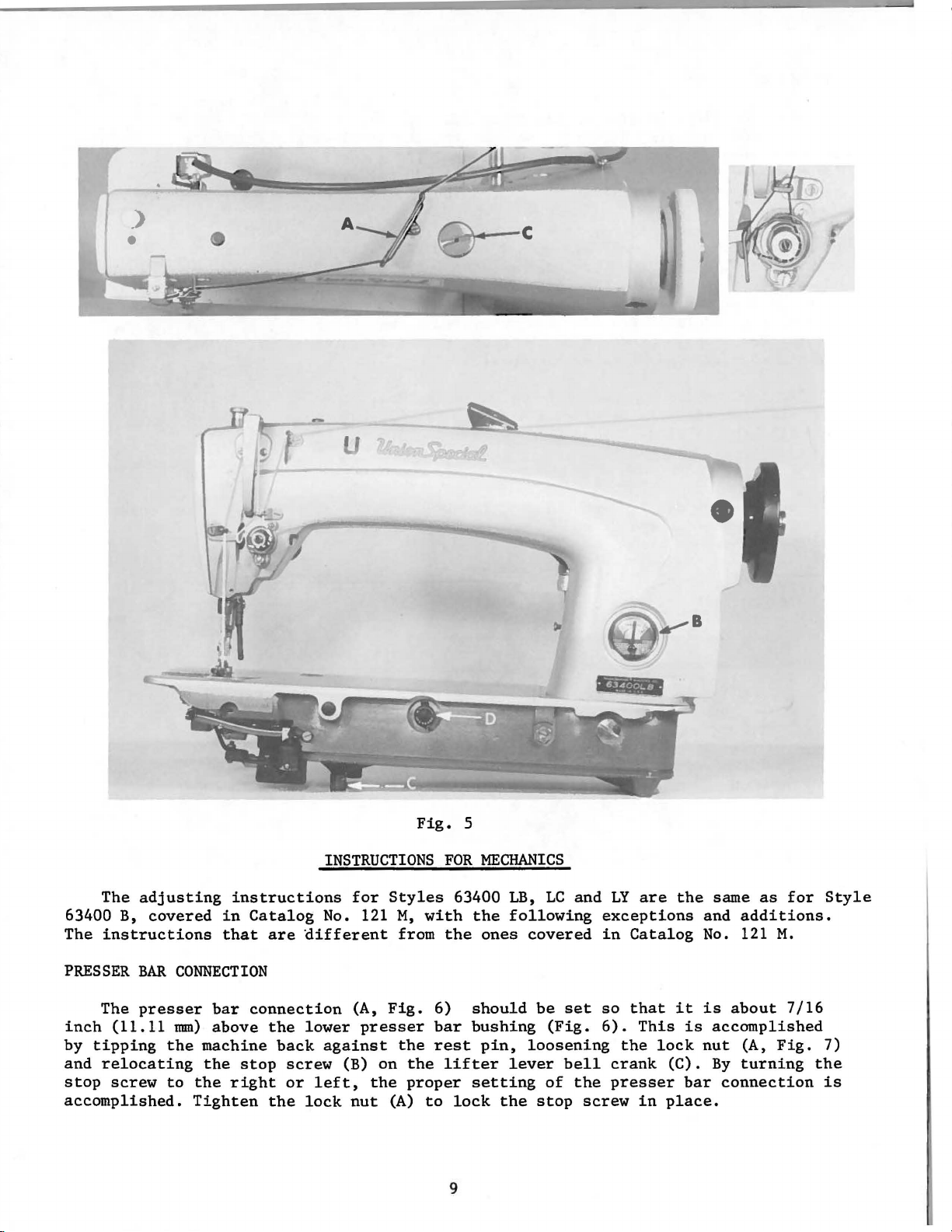
Fig.
5
The
adjusting
63400 B,
The
PRESSER
The
inch
by
tipping
and
relocating
stop
accomplished.
covered
instructions
BAR
presser
(11.11
the
screw
to
instructions
in
Catalog
that
are
CONNECTION
bar
connection
mm)
above
machine
the
the
Tighten
the
stop
right
the
different
lower
back
screw
or
lock
INSTRUCTIONS
for
Styles
No. 121
against
(B)
left,
(A,
Fig.
presser
on
the
nut
(A)
M,
with
from
the
the
proper
to
FOR
63400
the
6)
bar
rest
lifter
lock
the
should
bushing
setting
MECHANICS
LB,
LC
following
ones
pin,
covered
be
loosening
lever
the
stop
(Fig.
bell
of
9
and
exceptions
in
set
so
6).
the
screw
LY
are
Catalog
that
This
the
lock
crank
presser
in
the
same
and
No. 121
it
is
is
accomplished
nut
(C).
By
bar
place.
as
for
additions.
M.
about
connection
7/16
(A,
Fig.
turning
Style
7)
the
is
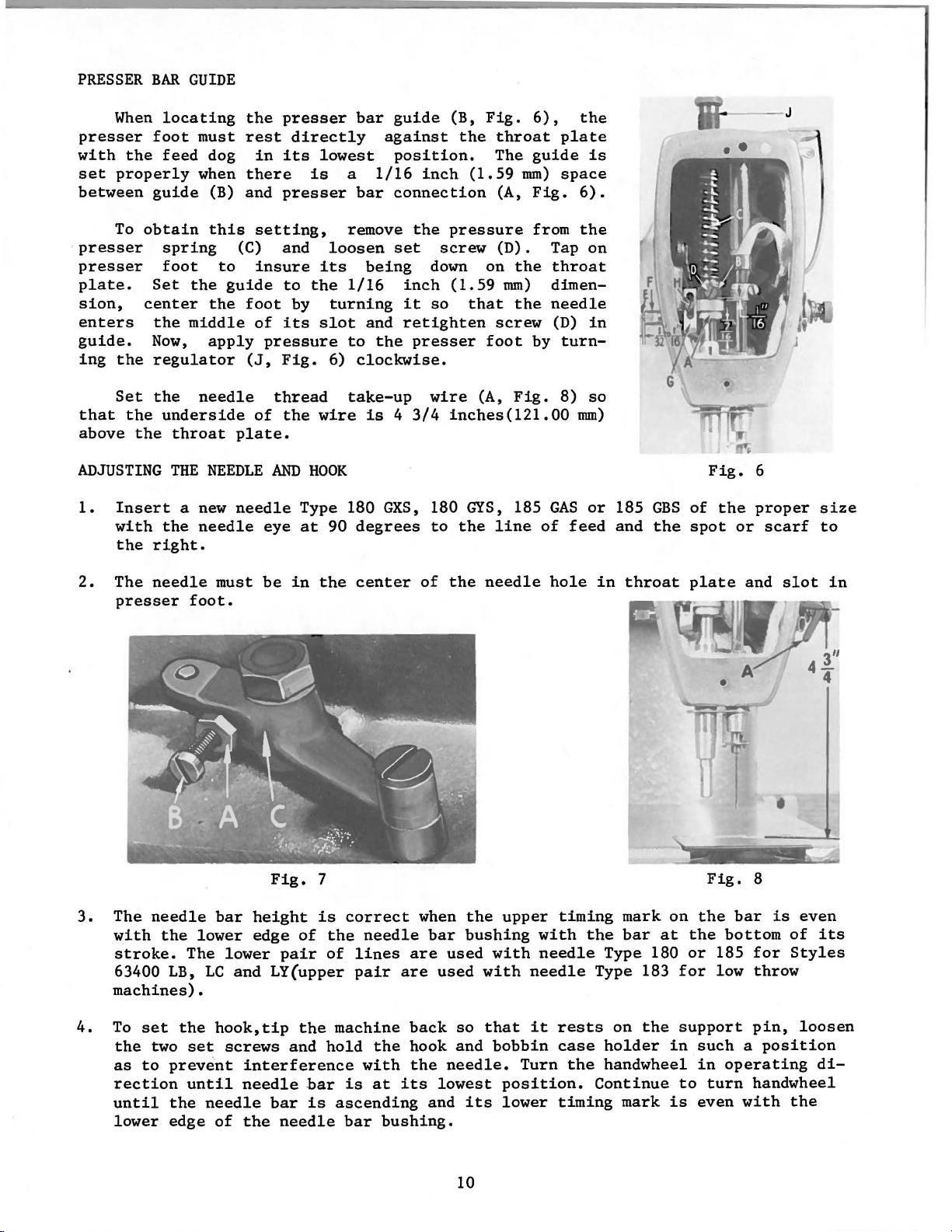
PRESSER
BAR
GUIDE
When
presser
with
set
between
foot
the
properly
guide
To
obtain
presser
presser
plate.
sion,
enters
guide.
ing
that
above
the
Set
the
the
Set
center
the
Now,
regulator
the
ADJUSTING
1.
Insert
with
the
right.
locating
must
feed
dog
when
(B)
this
spring
foot
the
to
guide
the
middle
apply
needle
underside
throat
THE
NEEDLE
a
new
the
needle
the
presser
rest
directly
in
its
there
and
presser
setting,
(C) and
insure
to
foot
by
of
its
pressure
(J,
Fig.
thread
of
the
plate.
AND
needle
eye
bar
lowest
is
a
bar
remove
loosen
its
being
the
1/16
turning
slot
and
to
6)
clockwise.
take-up
wire
HOOK
is 4 3/4
Type 180
at
90
degrees
guide
against
position.
1/16
inch
connection
the
set
down
inch
it
so
retighten
the
presser
wire
GXS,
180
to
(B,
Fig.
the
throat
The
guide
(1.59
(A,
mm)
Fig.
pressure
screw
(1.59
that
(D).
on
the
mm)
the
screw
foot
by
(A,
Fig.
inches(121.00
GYS,
the
185
line
6),
plate
space
from
Tap
throat
dimenneedle
(D)
turn-
8)
GAS
of
the
is
6).
the
on
in
so
mm)
or
feed
185
and
GBS
the
Moli-----
Fig.
of
spot
the
6
proper
or
J
scarf
size
to
2.
The
presser
3.
The
with
stroke.
63400
machines).
4.
To
the
as
rection
until
lower
needle
needle
the
LB,
set
two
to
prevent
the
edge
foot.
lower
The
the
set
until
must
be
Fig.
bar
height
edge
lower
LC
pair
and LY(upper
hook,tip
screws
interference
needle
needle
of
the
bar
needle
in
of
the
and
bar
is
the
center
7
is
correct
the
needle
of
lines
pair
machine
hold
with
is
ascending
bar
of
when
are
are
back
the
hook and
the
at
its
bushing.
the
bar
used
used
so
needle.
lowest
and
needle
the
upper
bushing
with
with
that
bobbin
position.
its
lower
hole
with
needle
needle
it
Turn
in
timing
the
Type 183
rests
case
the
Continue
timing
throat
mark
bar
on
at
Type 180
for
on
the
support
holder
in
handwheel
to
mark
is
plate
the
the
or
Fig.
bar
bottom
185
low
and
8
is
for
throw
pin,
slot
even
of
Styles
loosen
such a position
in
operating
turn
handwheel
even
with
the
in
its
di-
10
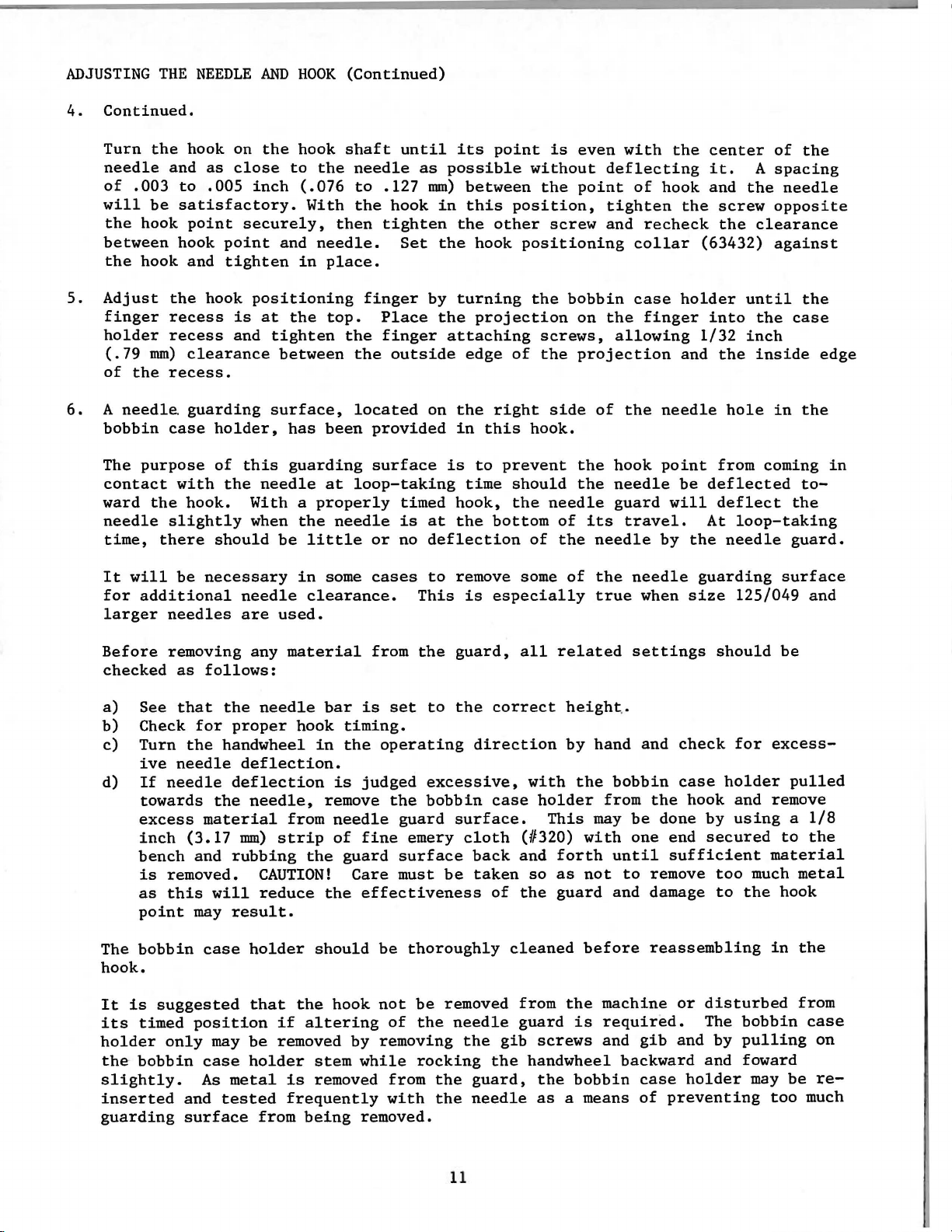
ADJUSTING
4.
Continued.
THE
NEEDLE
AND
HOOK
(Continued)
5.
6.
Turn
needle
of
will
between
Adjust
finger
holder
of
A
bobbin
The
contact
ward
needle
time,
It
for
larger
.003
the
the
(.79
the
needle
will
the
be
hook
hook and
mm)
purpose
the
there
additional
hook on
and
as
close
to
.005
satisfactory.
point
hook
the
recess
recess
clearance
recess.
guarding
case
with
hook.
slightly
be
needles
securely,
point
tighten
hook
is
and
holder,
of
this
the
should
necessary
needle
are
the
hook
shaft
to
the
needle
inch
positioning
With a properly
when
(.076
and
in
at
the
tighten
between
surface,
has
guarding
needle
the
be
in
used.
to
With
the
then
needle.
place.
finger
top.
the
the
located
been
provided
surface
at
loop-taking
needle
little
clearance.
some
or
cases
until
as
.127
hook
tighten
Set
Place
finger
outside
timed
is
no
This
its
point
possible
mm)
between
in
this
the
other
the
hook
by
turning
the
projection
attaching
edge
on
the
right
in
this
is
to
time
hook,
at
the
bottom
deflection
to
remove some
is
especially
is
without
the
position,
screw
positioning
the
screws,
of
the
side
hook.
prevent
should
the
needle
of
of
the
even
with
deflecting
point
tighten
and
bobbin
on
the
allowing
projection
of
the
the
hook
the
needle
guard
its
travel.
needle
of
the
true
the
of
hook
recheck
collar
case
finger
needle
point
will
by
needle
when
center
it.
and
the
screw
the
(63432)
holder
into
1/32
and
the
from
be
deflected
deflect
At
the
guarding
size
of
A
spacing
the
needle
opposite
clearance
against
until
the
case
inch
inside
hole
needle
in
coming
the
loop-taking
guard.
surface
125/049
the
the
edge
the
in
to-
and
Before
checked
a)
See
b)
Check
c)
Turn
ive
d)
If
towards
excess
inch
bench
is
as
point
The
bobbin
hook.
It
is
suggested
its
timed
holder
the
bobbin
slightly.
inserted
guarding
removing
as
follows:
that
needle
needle
removed.
this
only
the
for
the
handwheel
the
material
(3.17
and
will
may
case
position
may
case
As
metal
and
tested
surface
any
material
needle
proper
deflection.
deflection
mm)
rubbing
result.
hook
needle,
from
strip
CAUTION!
reduce
holder
that
the
if
be
removed
holder
is
frequently
from
bar
timing.
in
the
is
remove
needle
of
the
guard
Care
the
should
hook
altering
by
stem
removed
being
from
the
is
set
to
operating
judged
fine
effectiveness
be
not
removing
while
removed.
excessive,
the
bobbin
guard
emery
surface
must
thoroughly
be
of
the
rocking
from
the
with
the
be
removed
guard,
the
correct
direction
case
surface.
cloth
back
taken
of
needle
the
gib
the
guard,
needle
all
related
height
by
with
holder
This
(#320)
and
forth
so
as
the
guard
cleaned
from
guard
the
screws
handwheel
the
as
a means
hand
the
bobbin
from
may
with
until
not
and damage
before
machine
is
required.
and
bobbin
settings
..
and
check
case
the
be
done
one
end
sufficient
to
remove
reassembling
or
gib
and
backward
case
holder
of
preventing
should
holder
hook
and
by
using a 1/8
secured
too
to
disturbed
The
by
and
for
excess-
remove
material
much
the
in
bobbin
pulling
foward
may
too
be
pulled
to
the
metal
hook
the
from
case
be
much
on
re-
11
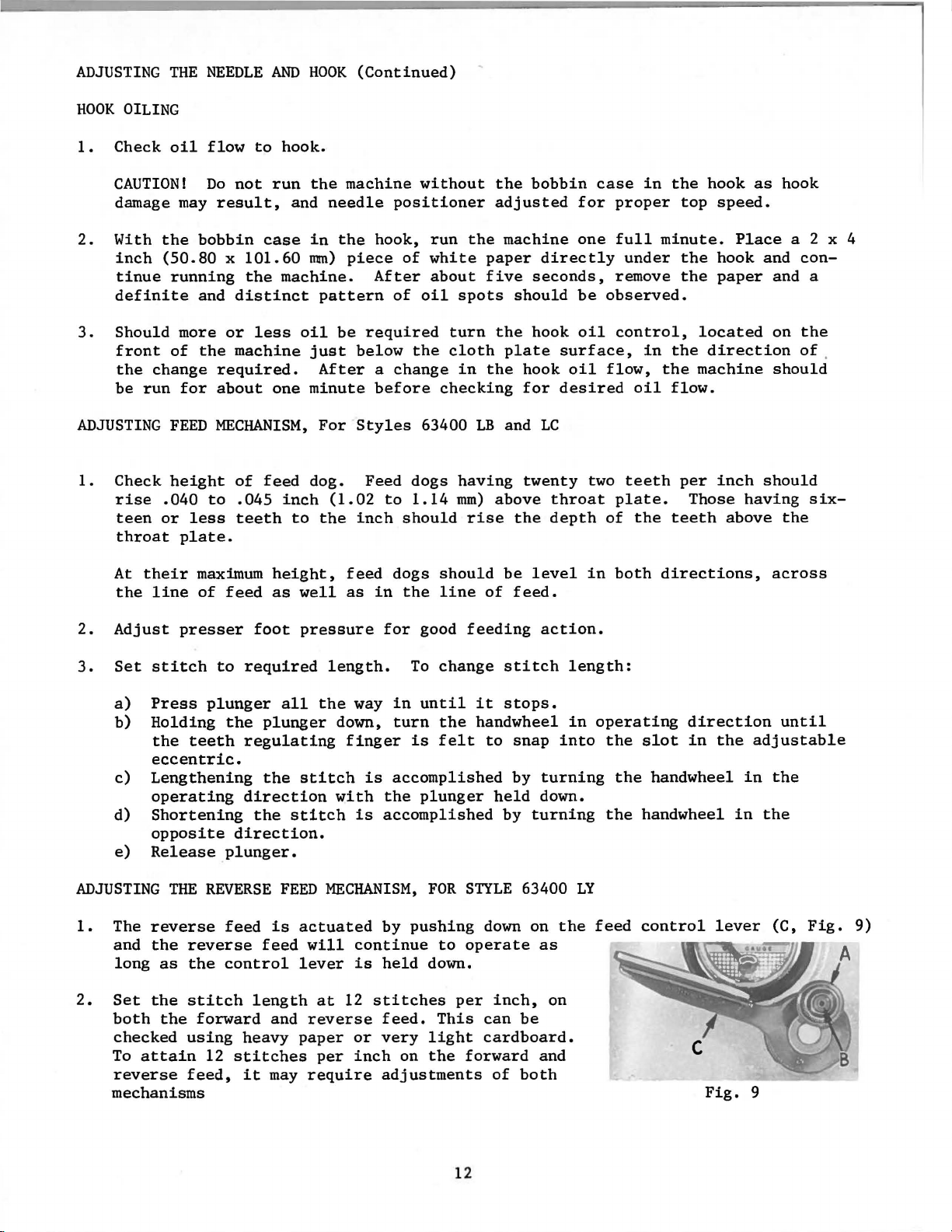
ADJUSTING
THE
NEEDLE
AND
HOOK
(Continued)
HOOK
ADJUSTING
1.
Check
CAUTION!
2.
3.
1.
OILING
damage
With
inch
tinue
definite
Should
front
the
change
be
run
Check
rise
teen
throat
oil
flow
Do
may
the
bobbin
(50.80 x 101.60
running
and
more
of
the
for
FEED
height
.040
or
less
plate.
to
hook.
not
run
result,
case
the
machine.
distinct
or
less
machine
required.
about
MECHANISM,
to
of
feed
.045
teeth
one
inch
the
machine
and
needle
in
the
hook,
mm)
piece
After
pattern
oil
be
required
just
below
After a change
minute
For
dog.
to
the
Styles
(1.02
inch
before
Feed
to
without
positioner
run
of
white
about
of
oil
spots
turn
the
cloth
in
checking
63400
dogs
1.14
should
having
mm)
the
paper
five
the
LB
rise
the
bobbin
adjusted
machine
directly
seconds,
should
the
hook
plate
hook
for
and
LC
twenty
above
the
throat
depth
case
for
one
be
observed.
oil
surface,
oil
flow,
desired
two
of
in
proper
full
minute.
under
remove
control,
in
the
oil
teeth
plate.
the
the
top
the
the
located
the
machine
flow.
per
Those
teeth
hook
as
speed.
Place
hook and
paper
direction
inch
should
having
above
hook
a 2 x 4
con-
and a
on
the
of
should
six-
the
.
At
their
the
line
2.
Adjust
3.
Set
stitch
a)
Press
b)
Holding
the
eccentric.
c)
Lengthening
operating
d)
Shortening
opposite
e)
Release
ADJUSTING
1.
The
reverse
and
the
long
2.
Set
the
both
checked
To
attain
reverse
mechanisms
presser
THE
reverse
as
stitch
the
using
feed,
maximum
of
feed
to
plunger
the
teeth
direction.
plunger.
REVERSE
feed
the
control
forward
12
stitches
height,
as
well
foot
required
regulating
direction
the
length
heavy
it
pressure
all
plunger
the
stitch
stitch
FEED
is
actuated
feed
will
lever
and
reverse
paper
may
require
feed
as
length.
the
down,
finger
with
MECHANISM,
at
12
per
dogs
in
for
way
in
turn
is
accomplished
the
is
accomplished
by
continue
is
held
stitches
feed.
or
very
inch
on
adjustments
should
the
line
good
To
change
until
the
is
felt
plunger
FOR
pushing
to
down.
This
light
the
be
of
feeding
stitch
it
stops.
handwheel
to
by
held
by
STYLE
down
operate
per
inch,
can
cardboard.
forward
of
level
feed.
action.
snap
turning
down.
turning
63400
on
as
be
and
both
length:
in
into
the
on
in
both
operating
the
the
the
LY
feed
directions,
direction
slot
in
handwheel
handwheel
control
lever
Fig.
the
adjustable
in
in
9
across
until
the
the
(C,
12
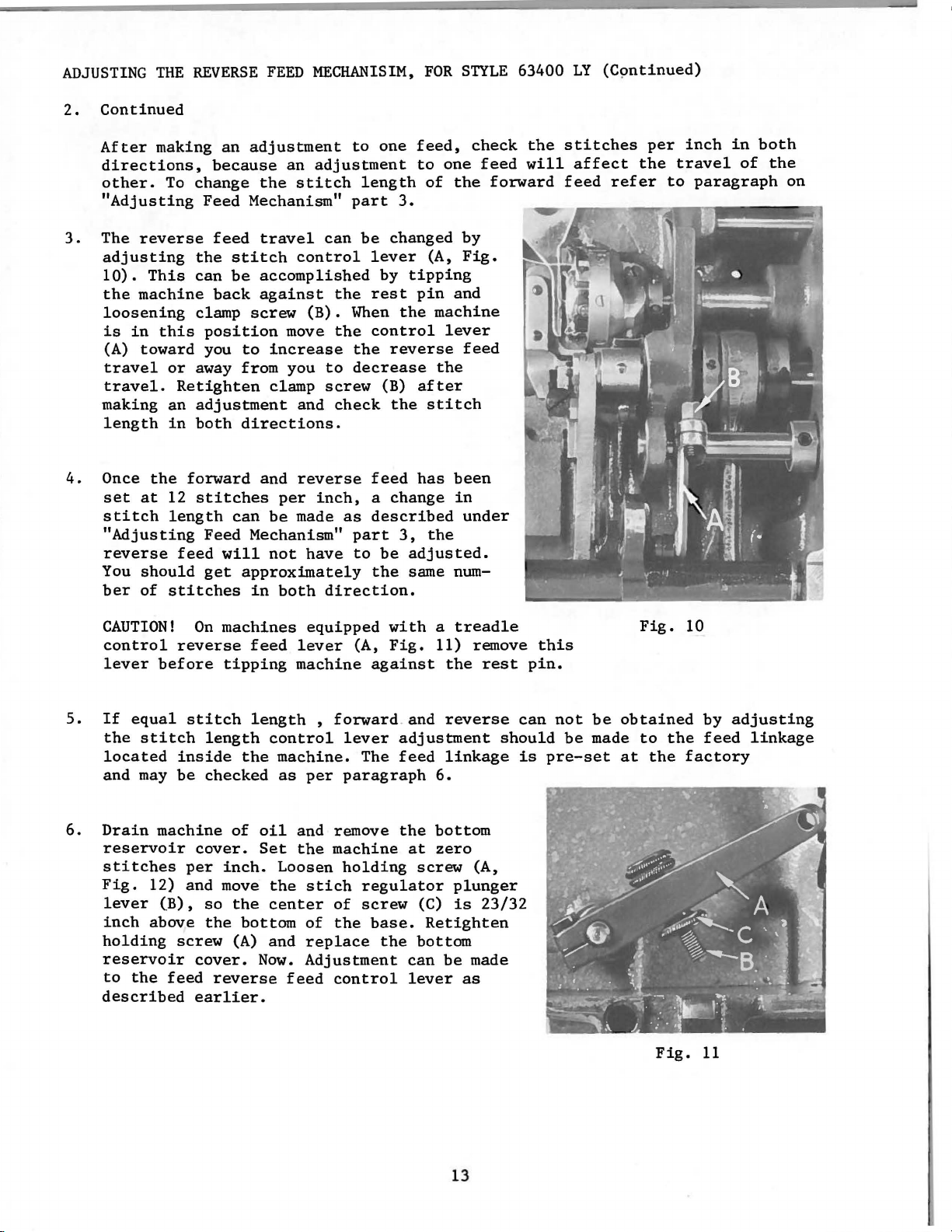
ADJUSTING
2.
Continued
THE
REVERSE
FEED
MECHANISIM,
FOR
STYLE
63400
LY
(Cpntinued)
After
directions,
other.
"Adjusting
3.
The
adjusting
10).
the
loosening
is
(A)
travel
travel.
making
length
4.
Once
set
stitch
"Adjusting
reverse
You
ber
making
To
reverse
This
machine
in
this
toward
or
Retighten
an
in
the
at
12
length
feed
should
of
stitches
an
adjustment
because
change
Feed Mechanism"
feed
the
stitch
can
be
back
clamp
position
you
away from you
adjustment
both
directions.
forward
stitches
can
Feed Mechanism"
will
get
an
the
stitch
travel
control
accomplished
against
screw
move
to
increase
clamp
and
and
reverse
per
be
made
not
approximately
in
both
to
one
feed,
adjustment
length
part
can
the
(B).
When
the
to
screw
check
inch, a change
as
have
direction.
3.
be
changed
lever
by
tipping
rest
the
control
the
reverse
decrease
(B)
the
feed
described
part
3,
to
be
adjusted.
the
same num-
to
one
of
the
(A,
pin
and
machine
lever
the
after
stitch
has
been
in
the
check
feed
forward
by
Fig.
feed
under
the
will
stitches
affect
feed
refer
per
the
inch
travel
to
paragraph
in
of
both
the
on
5.
6.
CAUTION!
control
lever
If
the
located
and
Drain
reservoir
stitches
Fig.
lever
inch
holding
reservoir
to
described
before
equal
stitch
may
machine
12) and move
(B),
above
the
feed
On
machines
reverse
tipping
stitch
length
inside
be
checked
cover.
per
inch.
so
the
screw
cover.
reverse
earlier.
equipped
feed
lever
machine
length , forward
control
the
of
oil
Set
the
center
bottom
(A)
and
Now.
machine.
as
Loosen
the
feed
lever
per
paragraph
and remove
the
machine
holding
stich
of
of
the
replace
Adjustment
control
with a treadle
(A,
Fig.
against
and
adjustment
The
feed
the
at
screw
regulator
screw
base.
the
(C)
Retighten
bottom
can
lever
11) remove
the
rest
reverse
should
linkage
6.
bottom
zero
(A,
plunger
is
23/32
be
made
as
this
pin.
can
is
not
be
be
made
pre-set
Fig.
obtained
to
the
at
the
Fig.
10
by
adjusting
feed
factory
11
linkage
13
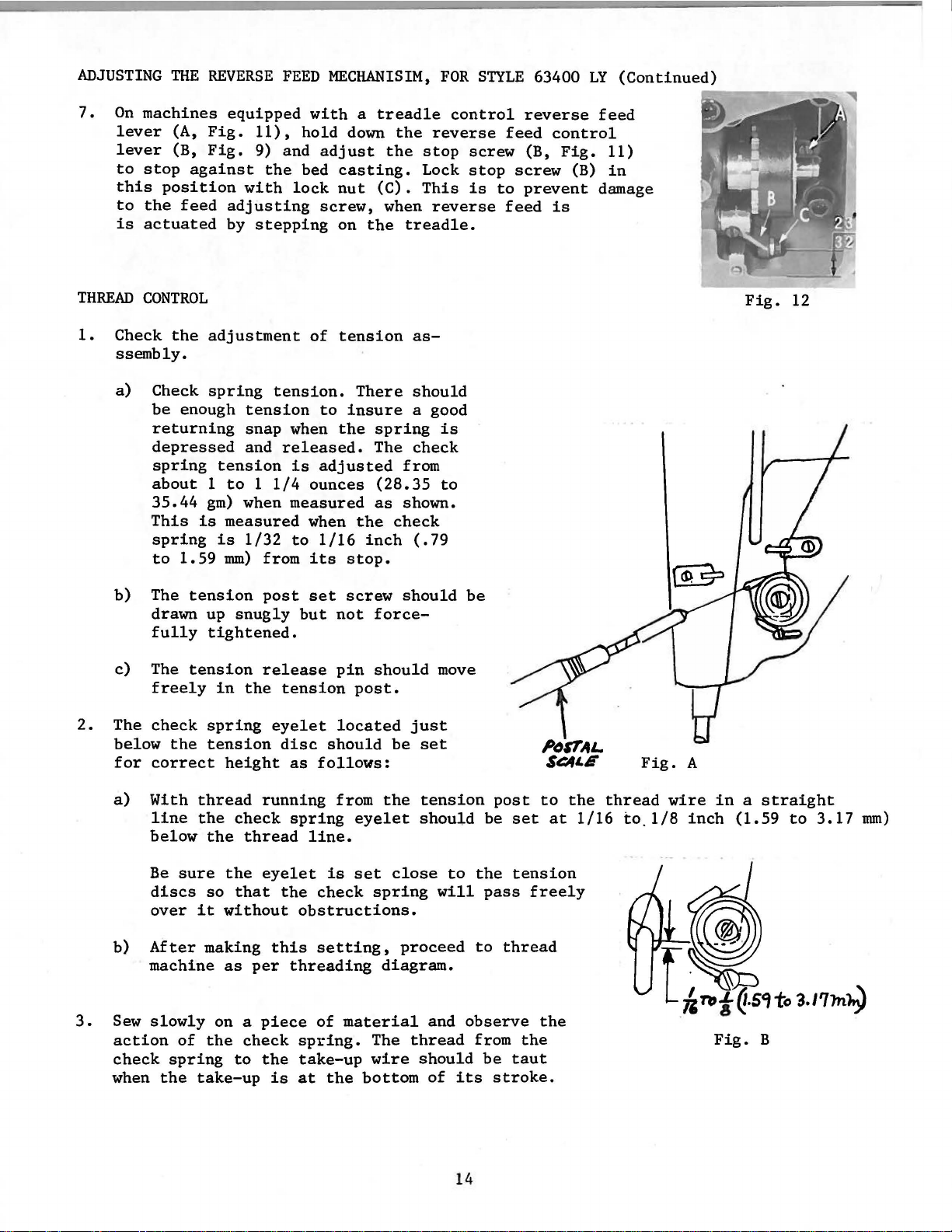
ADJUSTING
7.
On
machines
lever
lever
to
stop
this
to
the
actuated
is
THE
REVERSE
(A,
Fig.
(B,
Fig.
against
position
feed
FEED
equipped
11),
9) and
the
with
adjusting
by
stepping
MECHANISIM,
with a treadle
hold
down
bed
lock
adjust
casting.
nut
screw,
on
the
(C).
when
the
the
reverse
stop
Lock
This
reverse
treadle.
FOR
STYLE
control
screw
stop
is
feed
screw
to
feed
63400
reverse
control
(B,
Fig.
(B)
prevent
is
LY
(Continued)
feed
11)
in
damage
THREAD
1.
Check
ssembly.
a)
b)
c)
2.
The
below
for
CONTROL
the
adjustment
Check
be
returning
depressed
spring
spring
enough
tension
tension.
tension
snap
and
about 1 to 1 1/4
35.44
This
spring
to
The
drawn up
fully
The
freely
check
correct
is
1.59
tension
tension
the
gm)
when
measured
is
1/32
mm)
from
post
snugly
tightened.
release
in
the
spring
eyelet
tension
height
of
tension
to
when
the
released.
is
adjusted
ounces
measured
when
to
1/16
its
set
but
not
pin
tension
located
disc
as
follows:
should
There
insure
spring
The
(28.35
as
the
inch
stop.
screw
force-
should
post.
as-
should
a good
check
from
shown.
check
(.79
should
just
be
set
is
to
move
be
Fig.
A
Fig.
12
a)
3.
With
below
Be
discs
over
b)
After
machine
Sew
slowly
action
check
when
line
spring
the
thread
the
the
sure
so
it
making
of
the
take-up
check
thread
the
that
without
as
per
on a
check
to
running
spring
line.
eyelet
the
check
obstructions.
this
setting,
threading
piece
of
spring.
the
take-up
is
at
from
eyelet
is
set
material
the
bottom
the
tension
should
close
spring
proceed
diagram.
The
thread
wire
should
to
will
and
of
post
be
the
pass
to
observe
from
be
its
stroke.
to
set
tension
freely
thread
the
the
taut
at
14
the
1/16
thread
to.1/8
wire
inch
in a straight
(1.59
Fig.
to
B
3.17
mm)