
IDENTIFICATION
OF
MACHINE
Each
the
name
Standard
"Z".
only
Style
which
63400
used
but
clarity,
parts.
number,
NOTE:
column.
Example:
minor
number.
Styles
differs
".
This
in
not
Opposite
Union
plate
Style
catalog
conjunction
used
certain
description
When
Special
on
numbers
"Style
changes
Example:
of
machines
from
on
Style
the
ordering
machine
the
machine.
have
one
63400
are
the
style
is a supplement
therewith.
63400 B are
63400 B parts
illustration
and
KS".
made
similar
repair
in a standard
"Style
number,
APPLICATION
pages,
amount
is
Style
or
Special
63400
in
to
Only
illustrated
are
required.
parts
identified
numbers
more
letters
Style
machine, a "Z"
KSZ".
construction
in
that
OF
Catalog
those
shown
the
always
No.
parts
in
parts
use
by a Style
are
classified
suffixed,
numbers
are
grouped
it
contains
CATALOG
121 M
which
and
listed
phantom
are
identified
the
part
number
as
but
contain
is
no
letters.
(Second
are
used
at
the
to
help
number
which
standard
never
the
suffixed
under a class
Edition)
back
locate
by
contain
letter
Example:
on
of
detail
listed
is
to
and
Style
this
the
number,
in
stamped
and
special.
the
"z".
the
Standard
number
"Class
should
63
400 KS,
book.
63400
the
second
into
letter
When
be
For
KS
part
Adjusting
Catalog
in
this
instructions
in.
class.
from
handwheel
High
to
Rear
Positioner,
zontal
servoir
Oil
Needle
Lower
63 400 KS
No.
catalog
The
catalog
It
can
Reference
the
Speed
of
Hook
Enclosed
Control,
Bearings
Main
tions
travel.
feed
dog,
guide.
and
121 M
are
that
pertain
applies
also
be
applied
operator's
is
toward
Streamlined
Needle,
One
Needle,
Shaft,
Automatic
Automatic
for
Shaft,
For
attaching
on
medium
Type
stitches
Maximum
operating
(Second
the
ones
specifically
specifically
to
direction,
position
the
operator.
Long
Thread
Medium
Push
Maximum
180
Button
Head
Take-up
sleeve
to
medium
GXS
per
recommended
instructions
Edition)
that
are
with
discretion
such
while
STYLES
Arm
Undertrimmer
Lubricating
or
inch,
and
Stitch
Oiling,
Lever
Work
facings
180
thread
Lockstitch
heavy
GYS
for
or
Style
different
to
Style
to
the
to
as
right,
seated
OF
Heavy
Regulator,
System,
Needle
and
Needle
Space
to
work
weight
needle.
size,
speed
Style
63400
from
63400
Standard
some
at
MACHINES
Machine,
and
Duty,
to
Right
5500
63400
B.
Style
KS.
Style
Special
left,
the
machine.
Thread
Drop
Stitch
Head
Bearing
Bar
of
and
dress
material.
Specify
needle
R.
P.
KS
The
only
63400
of
Styles
front,
with
Wiper,
Feed,
Length
Oil
Adjustable
Driving
Needle
shirts
1
presser
type
and
M. -
are
similar
instructions
B,
or
machines
of
machines
back,
Operating
Top
Driven
Prepared
Rotary
Indicator,
Siphon,
Link,
Bar
11
and
13/64
foot,
size,
depending
to
those
included
are
additional
as
listed
etc.,
Adjustable
Feed
Feed
1/8
similar
inch
attachment
are
direction
Roller
for
Hook,
One
Eccentric,
Timing
Inches.
needle
throat
on
operation.
in
here-
in
this
given
of
Feed
Needle
Hori-
Re-
Hook
on
opera-
bar
plate,
and
3
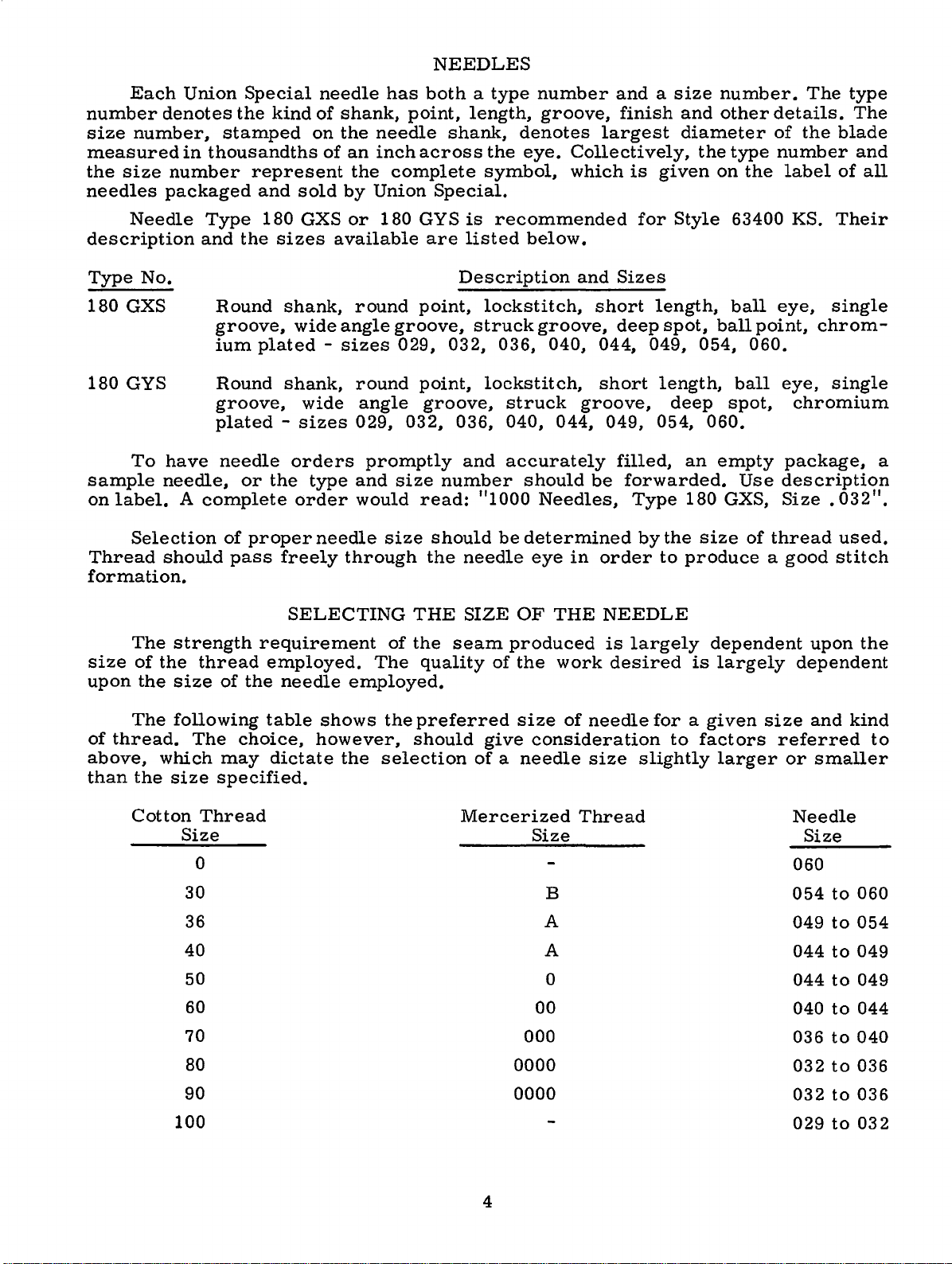
NEEDLES
Each
number
size
measured
the
needles
description
Type
180
180
sample
on
label.
Thread
formation.
denotes
number,
size
number
packaged
Needle
No.
GXS
GYS
To
have
needle,
Selection
should
Union
in
A
Special
the
stamped
thousandths
represent
and
Type
and
the
Round
groove,
ium
plated -sizes
Round
groove,
plated -sizes
needle
or
complete
of
proper
pass
kind
180
sizes
shank,
shank,
the
freely
needle
of
on
of
sold
GXS
available
wide
wide
orders
type
order
needle
has
shank,
the
needle
an
inch
the
complete
by
Union
or
180
round
angle
round
angle
029,
promptly
and
would
size
through
both a type
point,
shank,
across
Special.
GYS
is
are
listed
Description
point,
groove,
029, 032,
point,
groove,
032,
size
number
read:
should
the
036,
and
needle
number
length,
the
symbol,
lockstitch,
struck
lockstitch,
"1000
groove,
denotes
eye.
recommended
below.
groove,
036, 040, 044,
struck
040, 044,
accurately
should
Needles,
be
determined
eye
and a size
finish
largest
Collectively,
which
and
groove,
in
is
for
Sizes
short
deep
short
049,
filled,
be
forwarded.
Type
by
order
given
length,
spot,
049,
length,
deep
054,
the
to
number.
and
other
diameter
the
on
Style
ball
054,
060.
an
empty
180
GXS,
size
produce a good
type
the
63400
ball
point,
060.
ball
spot,
Use
of
thread
details.
of
number
label
KS.
eye,
eye,
chromium
package,
description
Size . 032".
The
the
single
chrom-
single
type
The
blade
and
of
all
Their
used.
stitch
a
The
size
upon
The
of
thread.
above,
than
the
Cotton
of
the
the
which
size
SELECTING
strength
thread
size
following
The
Thread
Size
0
30
36
40 A
50
60
70
80
requirement
employed.
of
the
needle
table
choice,
may
specified.
dictate
employed.
shows
however,
the
THE
of
the
The
quality
the
preferred
should
selection
SIZE
seam
Mercerized
OF
produced
of
the
size
give
of a needle
000
0000
THE
consideration
Size
B
A
0
00
work
of
needle
size
Thread
NEEDLE
is
largely
desired
dependent
is
for a given
to
factors
slightly
largely
size
larger
upon
dependent
and
referred
or
smaller
Needle
Size
060
054
to
049
to
044
to
044
to
040
to
036
to
032
to
the
kind
to
060
054
049
049
044
040
036
90
100
0000
4
032
029
to
to
036
032

IDENTIFYING
PARTS
Where
Parts
which
appear.
OF
replacement
listed
Each
bled
with
cular
throat
too
distinguish
Part
IMPORTANT!
MACHINE
The
arrangement
Exploded
in
this
plate
position.
their
view
plate,
the
construction
small
numbers
presents a sector
part
being
for a complete
one
part
represent
ON
FOR
parts
view
catalog
On
feed
WHICH
for
plates
and
the
page
numbers,
shown.
dog,
of
Style
and
permits,
from
ALL
ORDERING
this
at
Style
opposite
descriptions
Following
presser
another
the
ORDERS,
PART
catalog
63 400 KS.
the
back
63400 B covered
of
the
catalog
same
IS
ORDERED.
OF
is
cover
machine,
the
illustration
and
the
foot
each
part,
PLEASE
exploded
part
stamping
that
is
similar.
regardless
REPAIR
to
facilitate
the
differences
in
parts
the
number
combinations
is
stamped
are
identified
in
of
INCLUDEPARTNAMEANDSTYLE
PARTS
easy
Catalog
being
will
view
No.
be
of
pieces
plates,
available
with
its
by
letter
appearance.
the
catalog
and
accurate
between
121 M
aligned
found a listing
are
the
(Second
as
in
required
plates
for
these
part
Standard
number.
symbols
in
which
ordering
Edition).
their
assem-
of
the
in
the
covering
machines.
Style
parts
parti-
they
of
the
Numbers
the
position
in
ordering
exploded
Sub-assemblies,
or a solid
can
be
furnished
description
32
33
34
35
36
29480
63458 H
37
Success
Union
ation,
to
Maximum
the
Special
its
most
in
the
of
the
part
parts.
view
660-360
670
670
line
of
plate
box
for
the
FM
G-18
G-23
main
660-347
USE
in
the
Needles
subsidiaries
approved
efficiency
first
Always
carries
on
operation
column
in
the
which
the
picture
repairs,
sub-assembly.
Rotary
GENUINE
and
and
scientific
and
durability
are
reference
illustration.
use
the
part
a
reference
are
sold
plate.
are
indicated
Tension
Rotary
RotarySolenoid---------------------------------
Female
Male
SolenoidLeadCover
of
Repair
authorized
Solenoid
Connector
Wire
NEEDLES
these
Parts
principles,
are
Reference
number
number
complete,
Component
Example:
Release
Terminal
AND
machines
as
distributors.
assured.
numbers
listed
or
by
indenting
Solenoid
Cover
Sleeve,
----------------------------
----------------------------
REPAIR
can
furnished
and
are
only,
numbers
in
for
each
by
separate
parts
their
Assembly
-------------------------green
PARTS
be
secured
by
the
They
made
should
the
second
part a vail
part,
of
sub-assemblies,
descriptions
-----------------
Union
are
with
and
merely
never
column.
able
are
------------
only
Special
designed
utmost
indicate
be
for
in a bracket
which
under
with
genuine
Corpor-
according
precision.
used
Each
sale.
the
1
1
1
2
2
1
Genuine
parts
guarantee
are
needles
stamped
of
the
highest
are
with
packaged
the
Union
quality
with
Special
in
materials
labels
trade
5
marked
mark.
and
workmanship.
~
Each
•
trade
Genuine
mark
repair
is
your
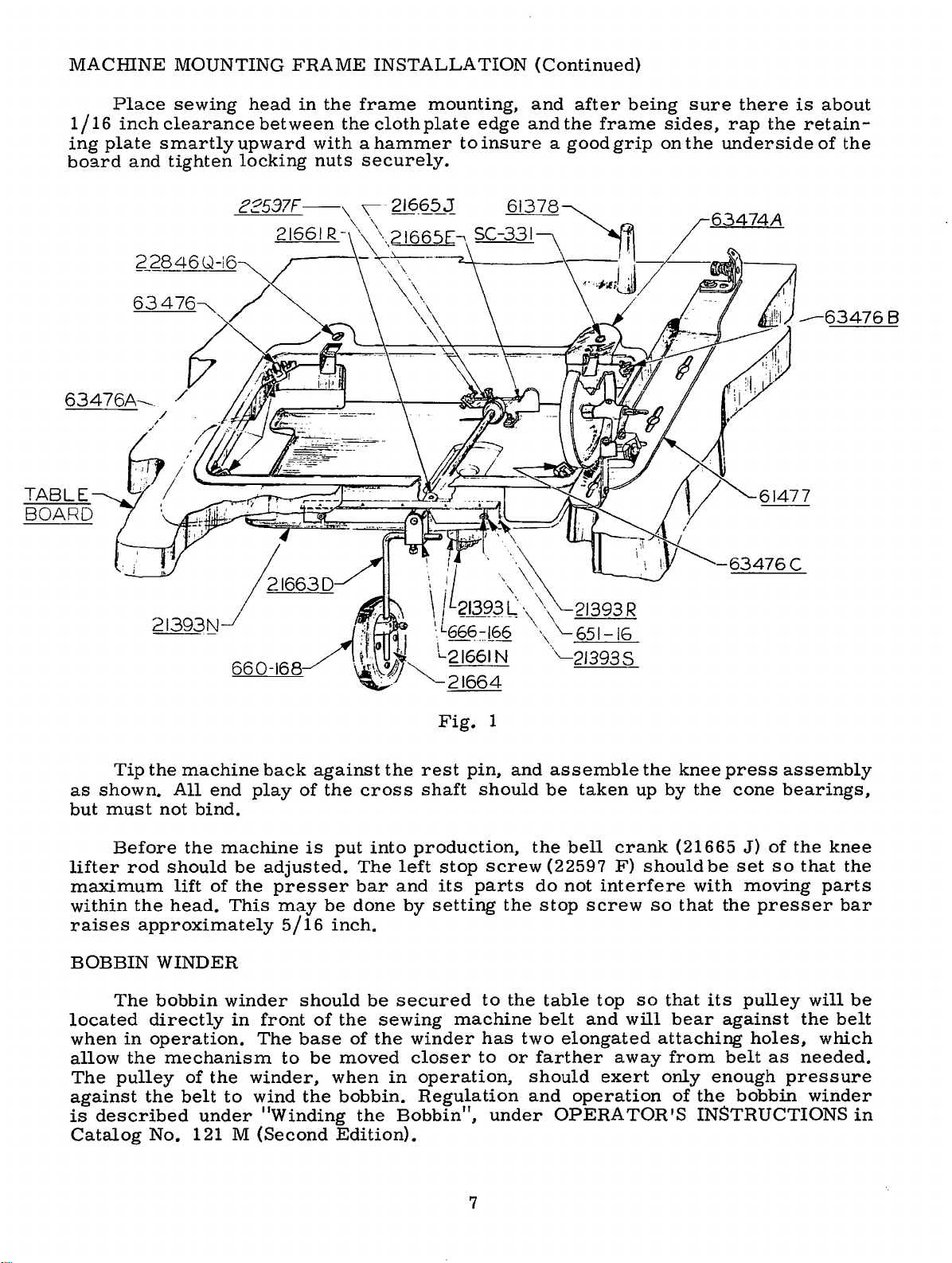
MACHINE
MOUNTING
FRAME
INSTALLATION
(Continued)
1/16
ing
plate
board
Place
inch
and
sewing
clearance
smartly
tighten
head
between
upward
locking
in
the
frame
the
cloth
with a hammer
nuts
securely.
mounting,
plate
edge
to
insure a good
and
and
after
the
being
frame
grip
sure
sides,
on
the
there
rap
the
underside
-63476C
is
about
retain-
of
the
Tip
as
shown.
but
must
Before
lifter
rod
maximum
within
raises
the
approximately
BOBBIN
The
located
when
allow
The
in
the
pulley
against
is
described
Catalog
the
machine
All
end
not
bind.
the
should
lift
of
head.
WINDER
bobbin
directly
operation.
mechanism
of
the
the
belt
under
No.
121 M
back
play
machine
be
adjusted.
the
presser
This
may
5/16
winder
in
front
The
to
winder,
to
wind
"Winding
(Second
against
of
the
is
put
be
inch.
should
of
the
base
be
moved
when
the
bobbin.
Edition).
cross
into
The
bar
done
be
sewing
of
the
the
Fig.
the
rest
shaft
production,
left
stop
and
its
by
setting
secured
winder
closer
in
operation,
Regulation
Bobbin",
1
pin,
and
should
screw
parts
the
to
the
machine
has
to
or
under
assemble
be
the
(22597
do
not
stop
table
belt
two
elongated
farther
should
and
OPERA
taken
bell
crank
F)
interfere
screw
top
and
will
away
exert
operation
TOR'S
the
knee
up
by
(21665
should
so
that
so
that
bear
attaching
from
only
of
press
the
be
with
the
its
against
belt
enough
the
cone
assembly
bearings,
J)
of
set
so
moving
presser
pulley
holes,
as
pressure
bobbin
the
that
parts
will
the
which
needed.
winder
INSTRUCTIONS
knee
the
bar
be
belt
in
7
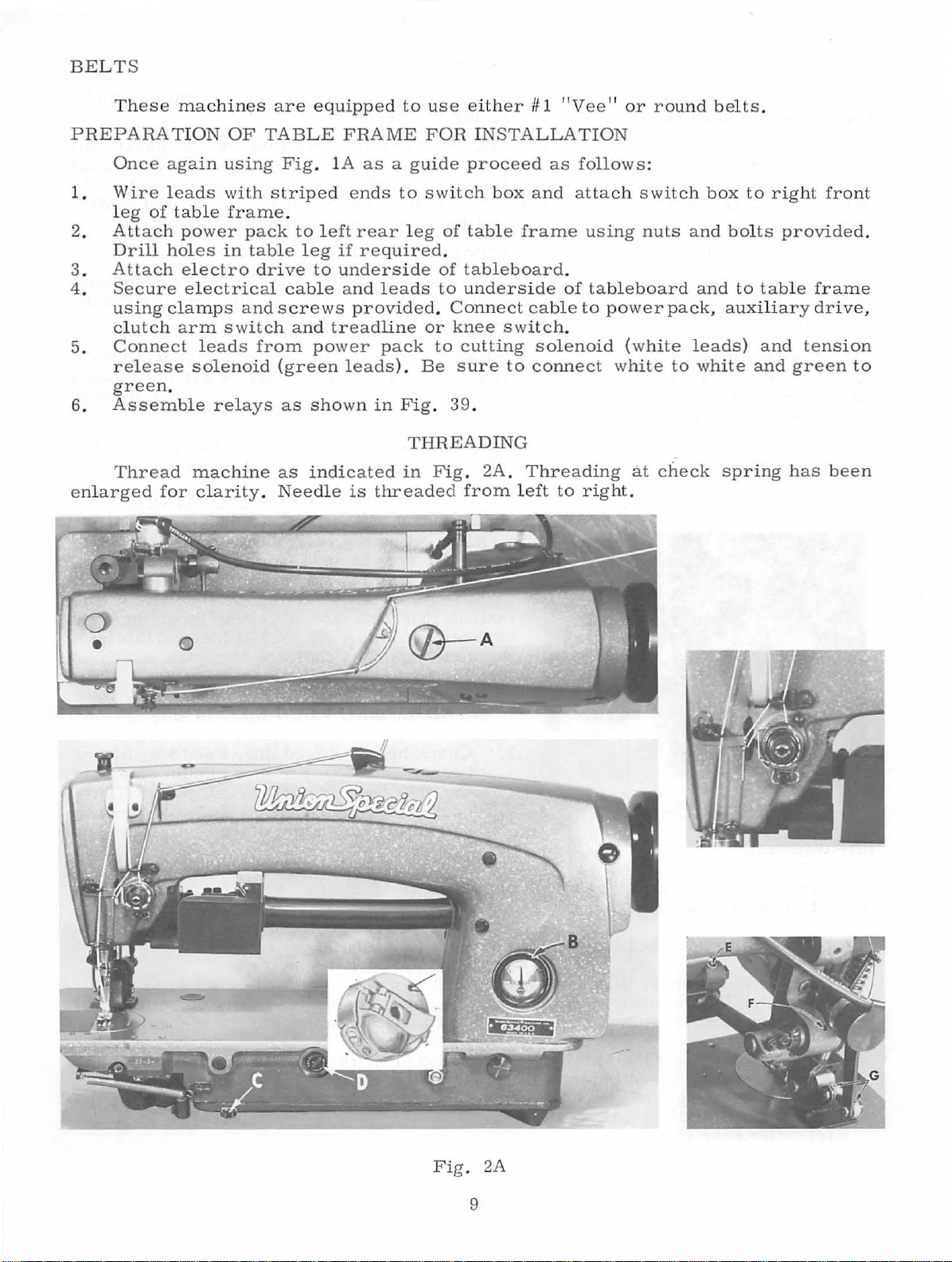
BELTS
Th
ese
machines
PREPARATION
Once
1.
Wi
l
2. A
Drill
3.
Attach
4.
Secure electrical
using
clutch
5.
Connect
release
green
6.
Assemble relays
Thread
enlarg
eg
tt
ed
re
of
ach
again
leads
tab
power
holes
electro
clamps
arm
leads
solenoid (green
.
machine
for
clarity.
OF
TAB
using
with
stri
le
frame.
pack
in
table
drive
and
switch and
from
are
equipped
LE
Fig
.
ped
to
left
leg
to
cable
screws
power
as
shown
as
indicated
Needle
FRAME
lA
as a guide
ends
to
rear leg
if
required
underside
and leads
to use
either
FOR
proceed
switch
of
tab
.
of
tableboard
to
und
provided. Connect
tread
line or
pack
leads).
in
Fig
Be
.
knee
to
cutting
sure
39.
THREADING
in
Fig.
is
threaded
from
# 1 "Vee
11
INSTALLATION
as
follows:
box
and
attach
le
frame
using
.
erside
switch
cab
of
tableboard
l e
to
power
.
solenoid (white
to
connect
2A.
Threading
left
to
right.
or
round
switch
nuts
pack, auxiliary drive,
white
to
at
check spring
belts
box
and
bolts
and to
leads)
white
.
to
table
and
and
right
front
provided
frame
tension
green
has
been
.
to
Fig
. 2A
9
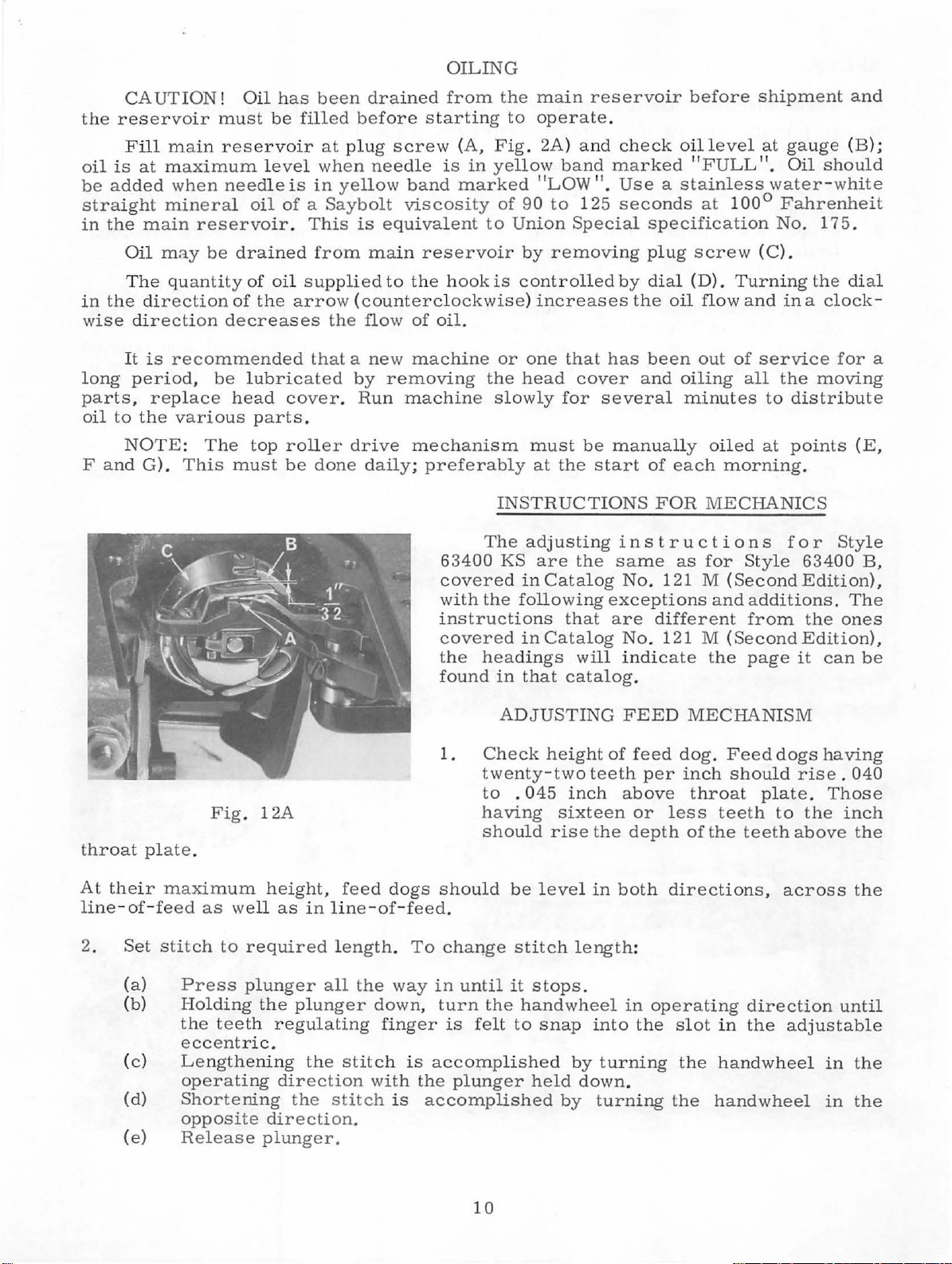
OILING
CAUTION!
the
reservoir
Fill
oil
is
be
added
straight
in
the
Oil
The
in
the
wise
long
parts,
oil
F
direction
It
period,
to
NOTE:
and
main
at
maximum
when
mineral
main
direction
is
the
G).
reservoir.
may
be
quantity
recommended
replace
various
The
This
Oil
has
been
must
reservoir
be lubricated
be
level
needle
drained
of
decreases
head
must
is
oil
of a Saybolt
of
oil
the
arrow (counterclockwise)
cover. Run machi
parts
top
roller
be
filled
at plug
when
in
This
from
supplied
that a new
.
done
drained
before
yellow
is
the
flow
by
drive
daily;
starting
screw (A,
needle
band
viscosity
equivalent
main
reservoir
to
the
of
machine
removing
mechanism
preferably
from
is
hook
oil.
63400
covered
with
instructions
covered
the
found
the
main
to
operate.
Fig.
2A)
in
yellow
marked ''LOW".
of
90
to
to
Union
by
removi
is
controlled
increases
or
one
the
head
ne slowly
must
at
INSTRUCTIONS
The
adjusting
KS
are
in
Catalog
the
following
in
Catalog
headings
in
that
reservoir
and
band
125
Special
that
cover
for
be
the
start
the
that
will
catalog
before
check oil
marked "FULL". Oil
Use a stainless
seconds
specification
ng
plug
by
dia
the
has
been
and
several
manually oiled
of
FOR
instructions
same
No
. 1
exceptions
are
different
No
. 121 M
indicate
.
level at gau
at
screw
l (D).
oil
flow
out
oiling
minutes
each
MECHANICS
as
for
21
M (
the
100°
Turning
and
of
all
morning
Sty
Second
and
additions.
from
(Second
page
shipment
water-white
Fahrenheit
No.
(C).
in a clock
service
the
to
at
le
and
ge
(B);
should
175.
the dial
for
moving
distribute
points
.
for
63400
Edition),
the
Edition),
it
(E,
Sty
The
ones
can
-
a
l e
B,
be
throat
At
line-of-feed
2.
their
Set
(a)
(b)
(c)
(d)
(e)
plate.
maximum
stitch
Fig.
as
Press
Holding
the
eccentric.
Lengthening
operating
Shortening
opposite
Release
well
to
required
plunger
teeth
12A
height,
the
regulating
direction.
plunger.
feed
as
in
line-of-feed.
length. To
all
plunger
the
stitch
direction
the
stitch
the
down,
finger
with
1.
dogs
should
change
way
in
until
turn
is
is
accomplished
the
plunger
is
accomplished
ADJUSTING
Check
twenty-two
to . 045
having
should
the
felt
height
rise
be
level
stitch
it
stops
handwheel
to
snap
held
of
teeth
inch
sixteen
the
in
length:
.
into
by
turning
down
by
turning
FEED
feed
per
above
or
depth
both
in
operating
the
.
MECHANISM
dog.
Feed
inch
should
throat
less
of
the
directions,
slot
the
the
plate.
teeth
teeth
direction
in
the
handwheel
handwheel
dogs
having
rise.
Those
to
the
above
across
until
adjustable
in
in
040
inch
the
the
the
the
10
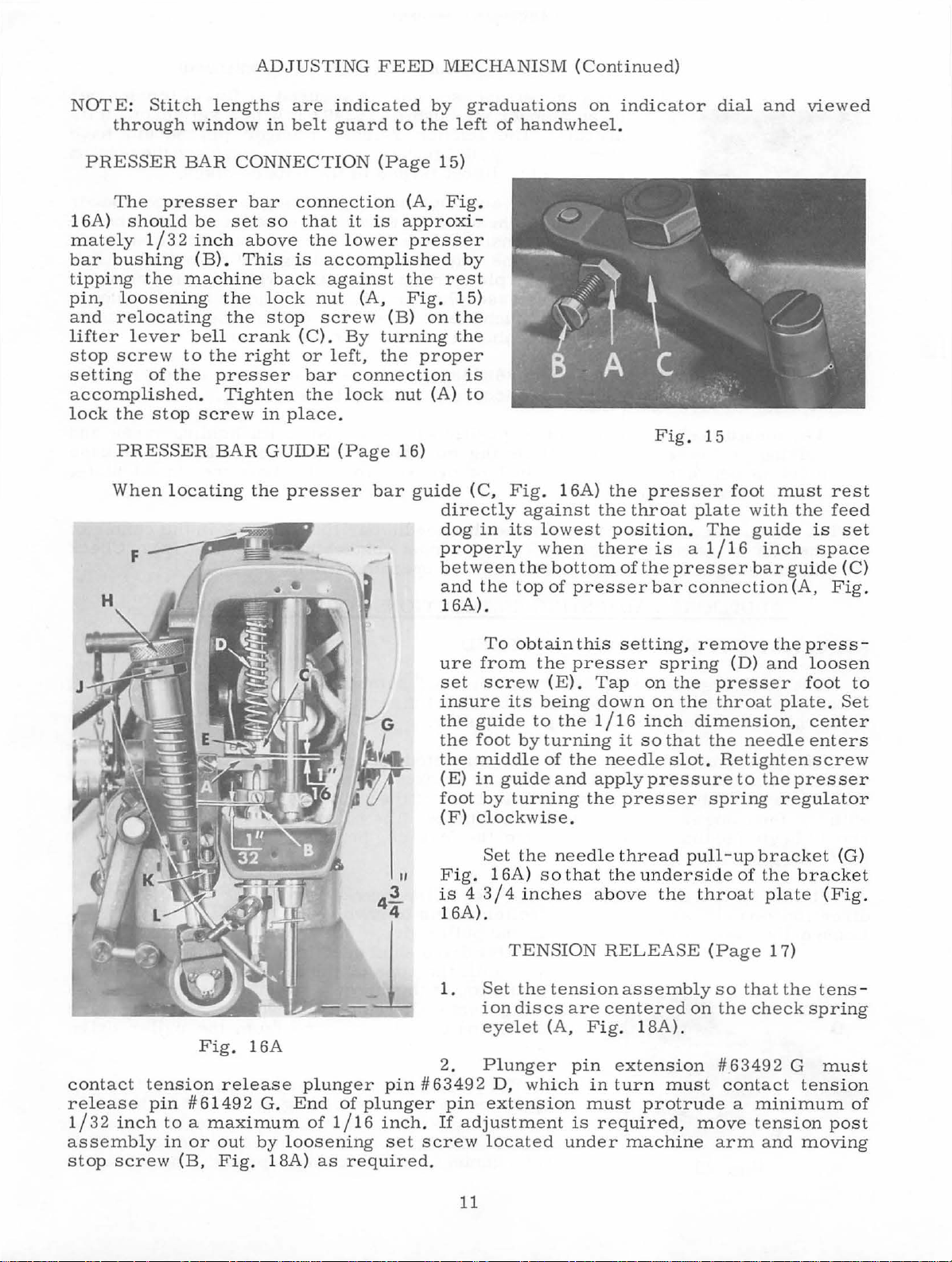
ADJUSTING
FEED
MECHANISM
(Continued)
NOTE:
Stitch
through
PRESSER
The
16A)
mately
bar
bushing
tipping
pin,
and
lifter
stop
setting
presser
should
1/32
the
loosening
relocati
lever
screw
of
accomplished
lock
the
stop
PRESSER
When
lengths
window
BAR
be
set
inch
(B).
machine
the
ng
the
bell
to
the
the
presser
.
Tighten
screw
BAR
locating
are
indicated
in
belt
guard
to
CONNECTION (Page
bar
above
This
crank
right
connection
so
that
it
the
low
is
accomp
back
against
lock nut (A,
stop
screw
(C).
or
By
left,
bar
the
lock
in
place.
GUIDE
the
presser
(Page
(A,
is
approx
er
presser
lished
the
Fig.
(B)
turning
the
proper
connection
nut
16)
bar
guide
by
the
left
15)
Fig.
by
rest
15)
on
the
the
(A)
directly
dog
properly
between
and
16A).
graduations
of
handwheel.
i-
is
to
(C,
Fig.
against
in
its lowest
wh
the
bottom
the
top
of
on
16A)
en
presser
indicator
Fig.
the
presser
the
throat
plate
position. The
there
of
is
the
bar
presser
a 1
connection
15
dial
foot
/16
and
must
with
guide
inch
bar
viewed
the
is
space
guide
(A,
rest
feed
set
(C)
Fig
.
contact
release
1
/32 inch
assembly
stop
screw
Fig. 16A
tension
release
pin #61492
to a maximum
in
or
out
(B,
Fig.
plunger
G.
End
of plun
of
1/ 16
by loosening
18A)
as
required.
ure
set
insure
the
the
the
(E)
foot
(
F)
F ig.
is 4 3 I 4
16
1.
2.
pin
#63492
ger
pin
inch.
set
If
screw located
To
obtain
from
the
screw (E). Tap
its
being
guide
foot
middle
in
by
to
by
guide
turning
the
turning
of
the
and
clockwise.
Set
the
needle
16
A)
so
that
inches
A).
TENSION
Set
the
tension
ion
discs
eyelet
are
(A,
Plunger
D,
which in
extension
adjustment
under
this
setting,
presser
down
1 I
needle
app
the
spring
on
on
16
inch
it
so
ly
pressure
presser
the
the
that
slot. Retighten
thread
the und
above
erside
the throat
RELEASE (Page
assemb
centered
Fig
. 18A) .
pin
extension
turn
must
is
required,
must
protrude a minimum
mac
hine arm and
remove
(D)
presser
throat
dim
ension, center
the
needle
to
the
spring
pull-up
bracket
of
the
plate (Fig
ly
so
that
on
the
check
#63492
contact
move
tension
the
press
and
loosen
foot
plate.
ente
screw
presser
regulator
bracket
1 7)
the
tens
spring
G
tens
moving
-
to
Set
rs
(G)
.
-
must
ion
of
post
11
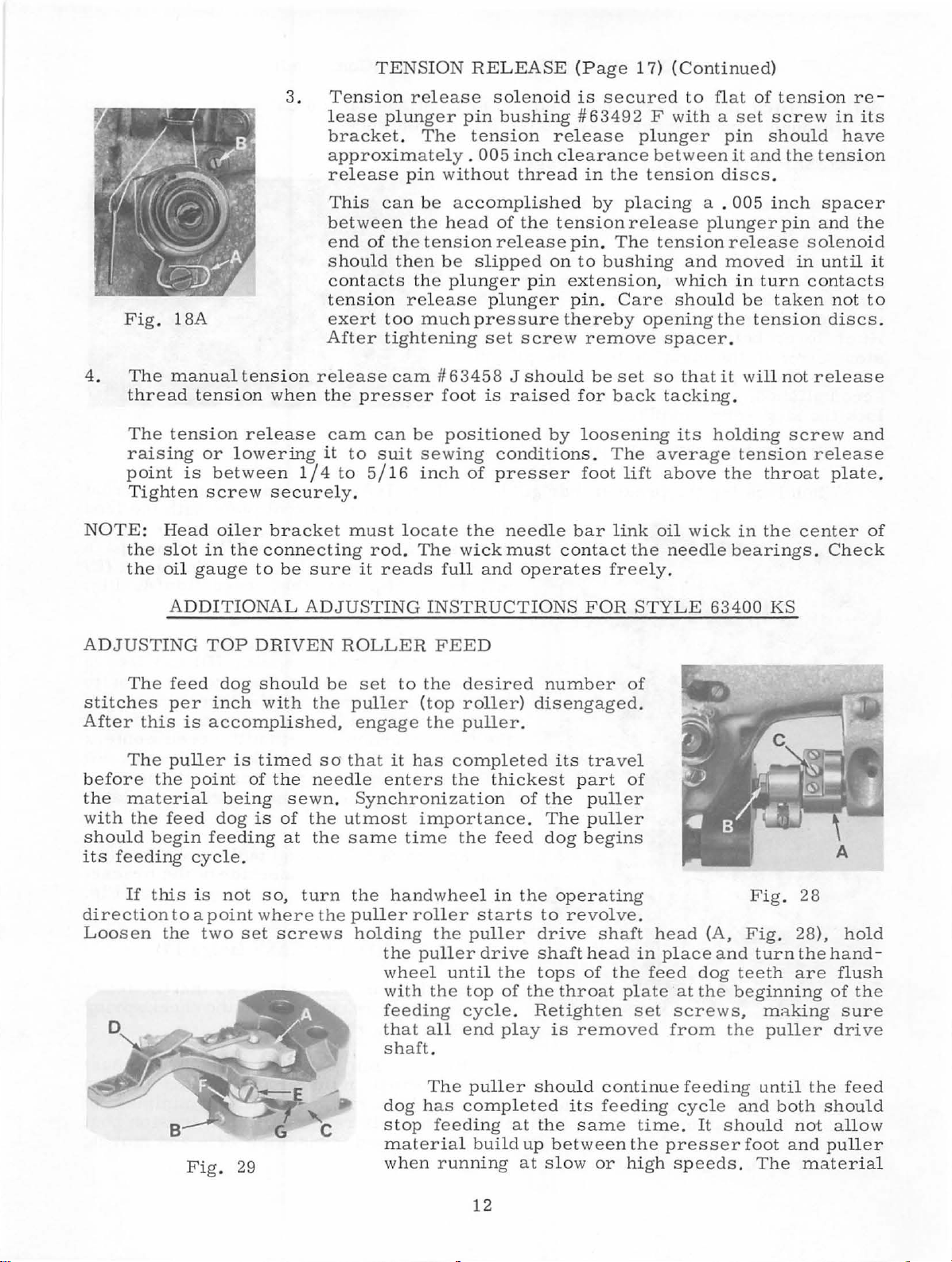
3.
Tension
l
ease
bracket.
approximately
release
TENSION
release
plunger
The
pin
without
RELEASE
solenoid
pin
bushing
tension
.
005
inch
thread
(Page
is
#63492 F with a set
release
clearance
in
1 7)
secured
plunger
between
the
tension
(Continued)
to flat
pin
it
discs
of
tension
screw
should
and
.
the
re-
in
its
have
tension
Fig.
4.
NOTE:
ADJUSTING
18A
The
manual
thread
The
tension
raising
point
Tighten
the
the
is
Head
slot
oil
ADDITIONAL ADJUSTING
tens
tension
or
lowering
between
screw
oiler
in
the
gauge
TOP
ion
when
release
1/4
securely.
bracket
connecting
to
be
sure
DRIVEN
This
between
end
should
contacts
tension
exert
After
release
the
presser
cam
it
to
to
must
it
ROLLER
can
be
the
of
the
tension
then
the
release
too
much
tightening
cam#
can
be
suit
sewing
5/16
rod.
inch
locate
The
reads
INSTRUCTIONS
accompli
head
be
slipped
plunger
plunger
pressure
set
63458 J should
foot
is
positioned
of
the
wick
full
and
FEED
shed
of
the tension
release
pin
screw
raised
conditions. The
presser
needle
must
operates
by
pin.
on
to
bushing
extension,
pin.
thereby
remove
be
for
by
loosening
foot
bar
contact
FOR
placing
release
The
Care
opening
set
so
back
lift
link
the
freely.
STYLE
a . 005 inch
plunger
tension
and
which
should
spacer.
that
tacking.
its
average
above
oil
wick
need
le
63400
release
moved
in
turn
be
the
tension
it
will
holding
tension
the
throat
in
the
bearings.
pin
in
taken
not
screw
center
KS
spacer
and
the
solenoid
until
contacts
release
release
it
not
to
discs.
and
plate.
of
Check
The
stitches
After
before
the
with
should
its
direction
Loosen
this
The
material
the
feeding
If
feed
per
is
puller
the
point
feed
begin
cycle
this
is
to a point
the
Fig.
dog
should
inch
accomplished,
feeding
two
is
being
dog
.
not
set
29
of
is
with
timed
the
sewn.
of
at
so,
turn
where the
screws
be
set
the
puller
engage
so
that
it
needle
the
the
enters
Synchronization
utmost
same
the
handwheel
puller
holding
the
wheel
with
feeding
that
shaft.
dog
stop
material
when
to
the
desired
(top
roller)
the
puller.
has
completed
the
importance.
time
roller
the
puller
until
the
all
The
has
feeding
running
the
top
cycle.
end
completed
thickest
feed
in
starts
puller
drive
the
of
play
puller
build
number
disengaged.
its
part
of
the
The
dog
the
operating
to
revolve.
drive
shaft
tops
the
throat
Retighten
is
removed
shou
ld
its
at
the
same
up
between
at
slow
of
travel
of
puller
puller
begins
shaft
head
of
the
plate
continue
feeding
or
high
in
feed
set
time
the
head
place
dog
at
the
screws,
from
feeding
cycle
.
It
presser
speeds.
Fig
(A,
Fig
and
teeth
beginning
the
and
shou
foot
. 28
. 28),
turn
the
are
m;:tking
puller
until
both
ld
not
and
The
material
hand-
flush
of
sure
drive
the
should
allow
puller
hold
the
feed
12
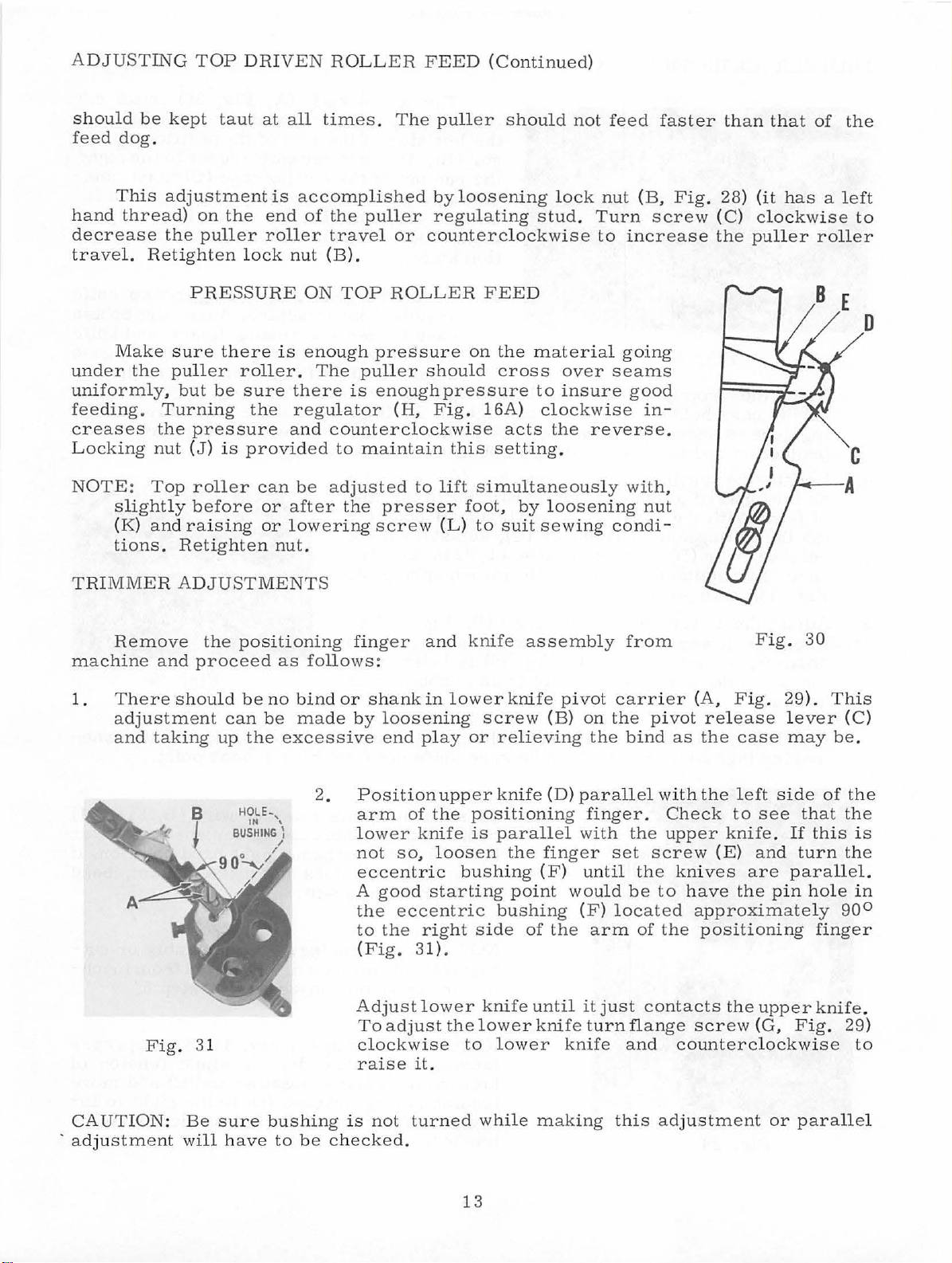
ADJUSTING
TOP
DRIVEN
ROLLER
FEED
(Continued)
should
feed
hand
decre
travel.
under
be
dog.
This
thread)
ase
Retighten
Make
the
kept
adjustment
the
sure
puller
uniformly,
feeding.
creases
Locking
Turning
the
nut
NOTE: Top
slightly
(
K)
and
tions. Ret
taut
at
is
on
the
end
puller
roller
lock
PRESSURE
there
is
roller. The
but
be
sure
the
pressure and
(J)
is
provided
roller
before
raising
ighten
can
or
or lowering
nut.
all
times.
accomplished
of
the
puller
travel
nut
(B).
ON
TOP
enough
pressure
puller
there
is
enoughpressure
regulator
counterclockwise
to
maintain this
be
adjusted
after
the
screw
The
puller
by
loosening
regulating
or
counterclockwise
ROLLER
on
should
(H,
Fig.
to
lift simult
presser
foot,
(L)
should
FEED
th e
cross
16A)
acts
setting
by
to suit
not
lock
stud.
Turn
to
material
over
to
insure
clockwise
the
reverse.
.
aneously
loosening
sewing
feed
nut
increase
going
seams
good
with
condi-
faster
(
B,
screw
in-
nut
Fig.
,
than
28) (
it
(C)
clockwise
the
puller roll
that
of
has a left
the
to
er
D
TRIMMER
Remove
machine
1.
Th
ere
adjustment
and
taking
F ig. 31
ADJUSTMENTS
the
positioning
and
proceed
should
can
up
be
the
no
be
finger
as
follows:
bind
or
made
by
excessive
2.
lower
A
Adjust
and
shank
in
loosening
end play
Position
arm
of
knife
not
so,
eccentric
good
the
to
(Fi
starting
eccentric
the
right
g.
31).
lower
To
adjust
clockwise
raise it.
knife
lower
or
upp
er knif
the
positioning
is
loos
en
bushing
side
the
lower
to lower
assembly
knife pivot
screw
relieving
e (D)
parallel
the
finger
(F)
point
bushing
of
knife
until
knife turn
from
carrier
(B)
on
the
pivot
the
bind
parallel
finger.
with
the
set
screw (E)
until the knives
wo
uld
be
(F)
loca
the
arm
of
it
just
contacts
flange
knife
and
Fig
(
A,
Fig.
release
as
the
case
with the left
Check
upper
knife
to
side
see
.
and
are paralle
to
have
ted
the
the pin hole
approximate
positioning
the
upper
screw
(G,
counterclockwise
.
30
29).
lever
may
that
If
th
turn
ly
finger
knife.
Fig.
This
be.
of
is
90°
(C)
the
the
is
the
l.
in
29)
to
CAUTION:
·
adjustment will
Be
sure
have
bushing
to
be
is
not turned
checked.
while
making
13
this adjustm
ent
or
parallel