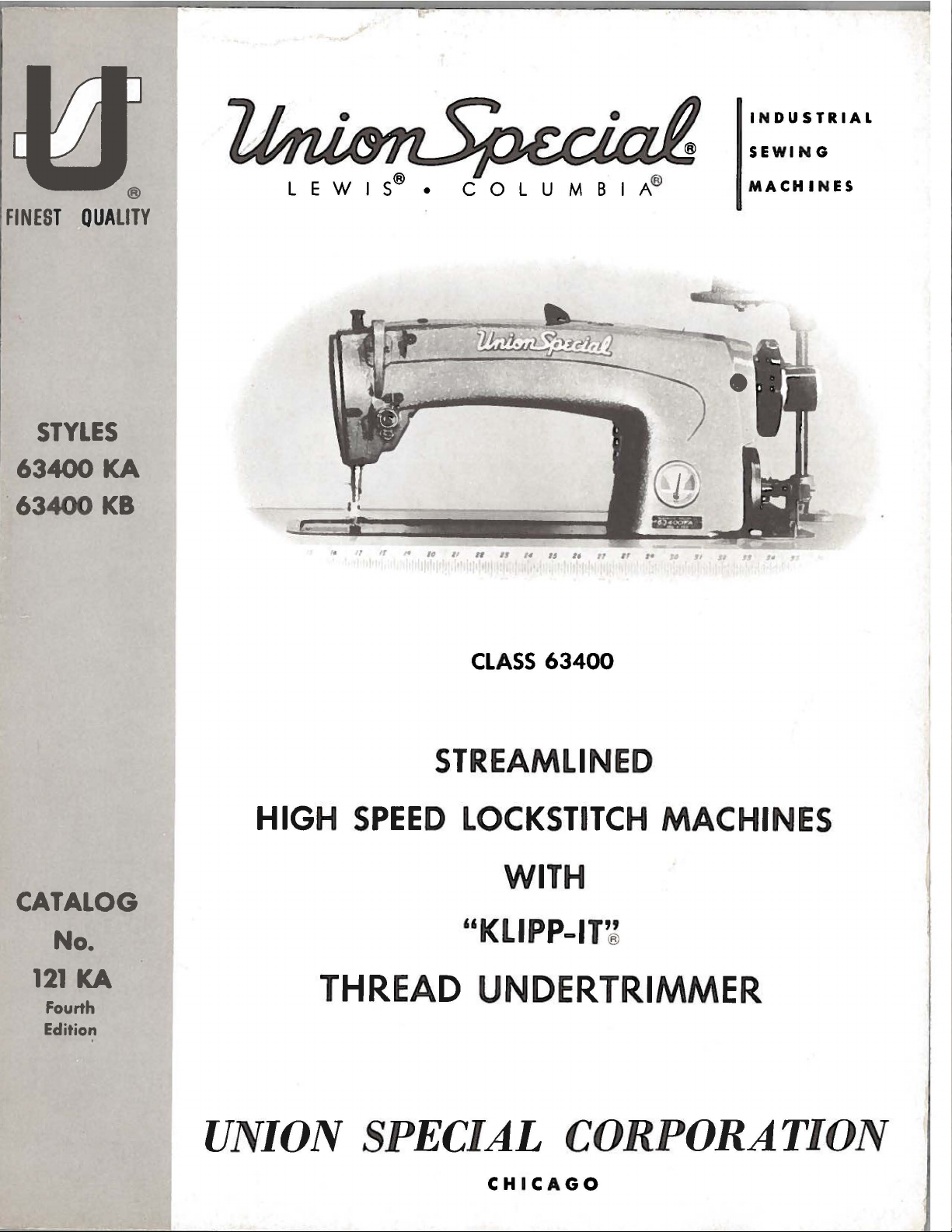
I N
DUSTRIAL
FINEST QUA
STYLES
63400
63400
LITY
KA
KB
®
ltnum~
L E W I
S®
• C 0 L U M B I A®
SE WI N G
M
ACHI
N ES
CATALOG
No.
121
KA
Fourth
Edition
HIGH
THREAD
STREAMLINED
SPEED
CLASS
LOCKSTITCH
63400
MACHINES
WITH
"KLIPP-IT
~
UNDERTRIMMER
UNION SPECIAL
CH
I C A
CORPORATION
GO

C a t a 1 o g N
( S u p p 1 e m e n t t o C a t a 1 o g N
o.
1 2 1 K A
I N S T R U C T I 0 N S
F 0 R
A D J U S T I N G A N D 0 P E R A T I N G
L I S T 0 F P A R T S
C
L A S S 6 3 4 0 0
S t r e a m 1 i n e d L o c k s t i t c h
S t y 1 e s
6 3 4 0 0 K A 6 3 4 0 0 K B
o.
1 2 1 M )
F o u r t h E d i t i o n
C o p y r i g h t 1 9 6 7 & 1 9 7 8
b y
U n i o n S p e c i a 1 C o r p o r a t i o n
R i g h t s R e s e r v e d i n A 1 1 C o u n t r i e s
UNION
SPECIAL CORPORATION
INDUSTRIAL
SEWING
MACHINES
CHICAGO
P r i n t e d i n
U.
S.
A.
2
March,
1981
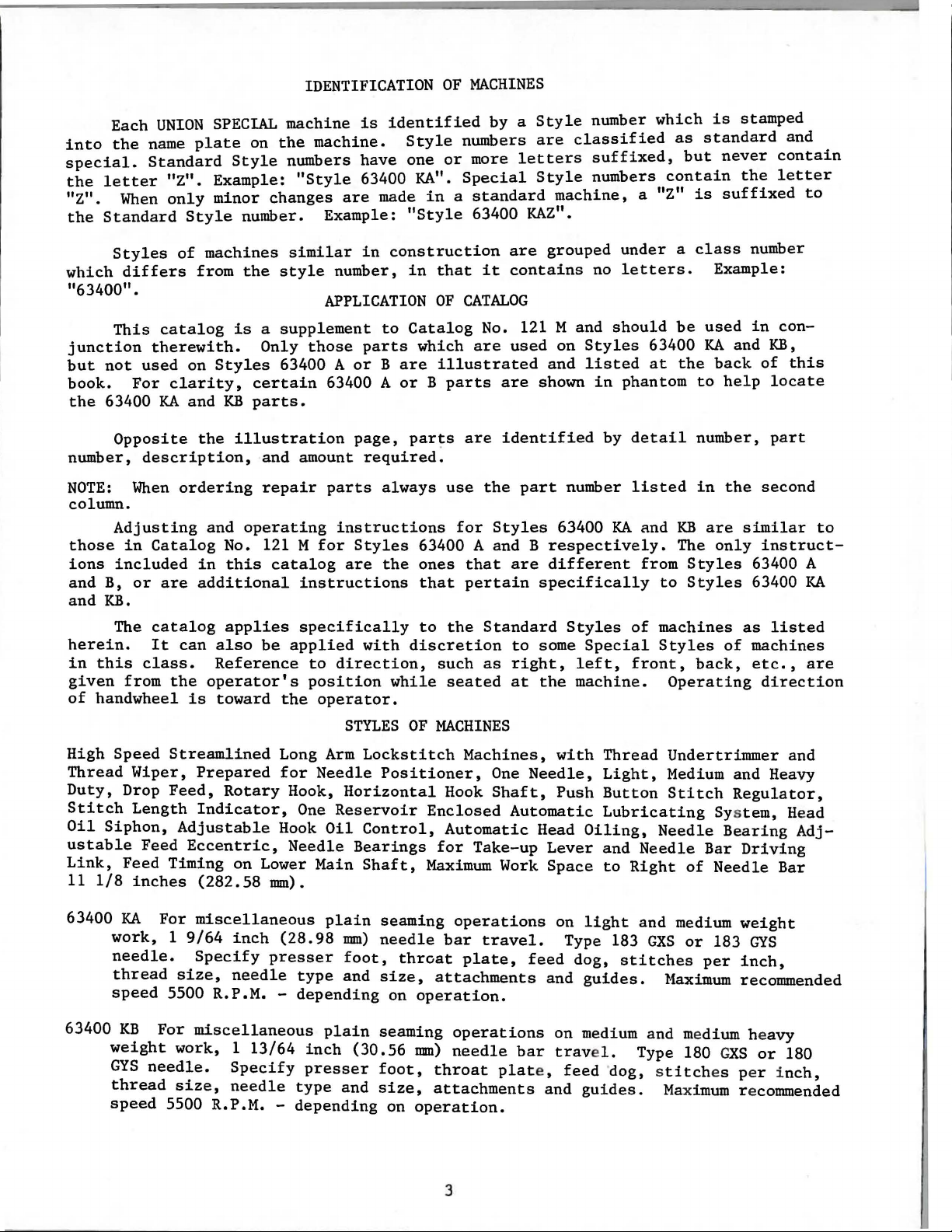
Each
into
the
special.
the
letter
"Z".
the
Standard
name
Standard
When
UNION
plate
"Z".
only
Style
IDENTIFICATION
SPECIAL
Style
Example:
minor
machine
on
the
numbers
changes
machine.
"Style
number. Example:
is
have
63400
are
identified
Style
one
KA".
made
in a standard
"Style
OF
MACHINES
by a
numbers
or
more
Special
63400
Style
are
letters
Style
machine,
KAZ".
number
classified
suffixed,
numbers
a "Z"
which
as
but
contain
is
is
stamped
standard
never
the
suffixed
and
contain
letter
to
Styles
which
differs
"63400".
This
junction
but
not
book.
the
63400
Opposite
number,
NOTE:
column.
Adjusting
those
ions
in
included
and B,
and
KB.
The
herein.
in
this
given
of
from
handwheel
of
machines
from
catalog
therewith.
used
on
For
clarity,
KA
and
the
description,
When
ordering
and
Catalog
in
or
are
additional
catalog
It
can
class.
the
operator's
is
similar
the
style
is a supplement
Only
Styles
those
63400 A
certain
KB
parts.
illustration
and amount
repair
operating
No. 121 M
this
for
catalog
instructions
applies
also
Reference
specifically
be
applied
to
position
toward
the
operator.
in
construction
number,
in
APPLICATION
to
Catalog
parts
which
or B are
63400 A
page,
or B parts
par~s
required.
parts
always
instructions
Styles
are
63400 A and B
the
ones
that
to
with
discretion
direction,
while
that
it
OF
CATALOG
No.
are
illustrated
are
are
identified
use
the
for
Styles
that
pertain
the
Standard
such
as
seated
are
grouped
contains
121 M and
used
on
and
shown
part
number
63400
respectively.
are
different
specifically
Styles
to
some
right,
at
the
under a class
no
letters.
should
Styles
listed
in
phantom
by
detail
listed
KA
of
Special
left,
front,
machine.
be
63400
at
the
and
KB
The
from
Styles
to
Styles
machines
Styles
Operating
number
Example:
used
KA
and
back
to
help
number,
in
the
are
similar
only
as
of
back,
in
con-
KB,
of
this
locate
part
second
instruct63400 A
63400
KA
listed
machines
etc.,
are
direction
to
High
Speed
Thread
Duty,
Stitch
Oil
Siphon,
ustable
Link,
11
1/8
63400
KA
work, 1 9/64
needle.
thread
speed
63400
KB
weight
GYS
thread
speed
STYLES
Wiper,
Drop
Length
Feed
Streamlined
Prepared
Feed,
Rotary
Indicator,
Adjustable
Eccentric,
Long
for
Hook,
One
Hook
Needle
Arm
Needle
Horizontal
Reservoir
Oil
Feed Timing on Lower Main
inches
needle.
(282.58
For
miscellaneous
inch
Specify
size,
needle
5500 R.P.M. -
For
miscellaneous
work, 1
Specify
size,
needle
5500 R.P.M. -
mm).
(28.98
presser
13/64
plain
mm)
foot,
type
and
depending
plain
inch
presser
type
and
depending
OF
Lockstitch
Positioner,
Control,
Bearings
Shaft,
seaming
needle
throat
size,
on
operation.
seaming
(30.56
mm)
foot,
size,
on
operation.
MACHINES
Machines,
One
Hook
Shaft,
Enclosed
Automatic
for
Take-up
Maximum
Work
operations
bar
travel.
plate,
attachments
operations
needle
throat
plat
attachments
with
Needle,
Push
Automatic
Head
Lever
Space
on
Type 183
feed
dog,
and
Thread
Light,
Button
Lubricating
Oiling,
and
to
light
stitches
guides.
Undertrimmer
Medium and Heavy
Stitch
Needle
Needle
Right
of
and medium
GXS
or
Maximum
on medium and medium heavy
bar
travel.
e ,
feed
and
guides.
Type 180 G
dog, stitch
Maximum
Regulator,
Sy
stem, He
Bearing
Bar
Driving
Needle
weight
183
GYS
per
inch,
recommended
XS
or
es per i
r ecommended
and
ad
Adj-
Bar
180
nch,
3
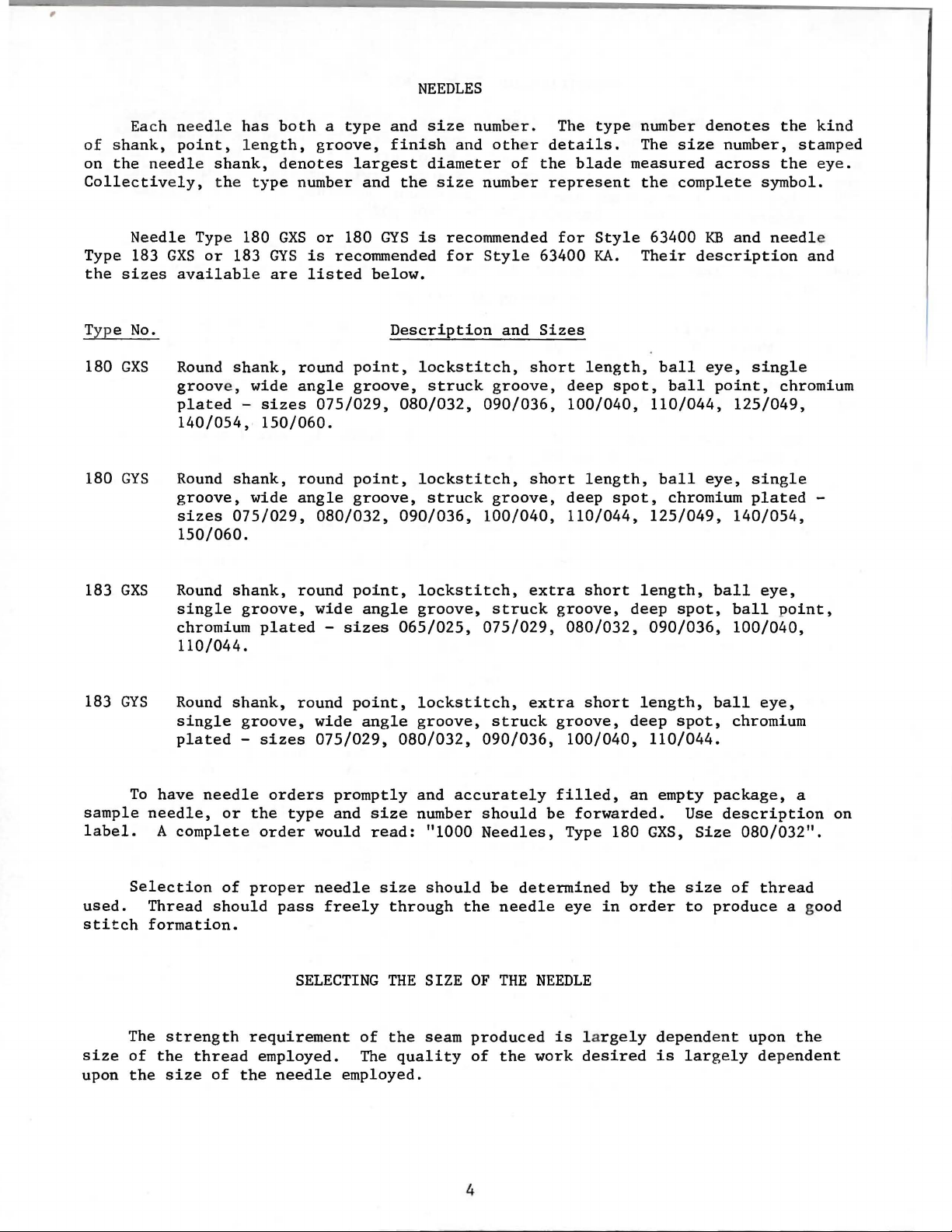
Each
needle
of
shank,
on
the
Collectively,
point,
needle
has
length,
shank,
the
type
both a type
groove,
denotes
number and
largest
NEEDLES
and
size
finish
diameter
the
and
size
number.
other
of
number
The
type
details.
the
blade
represent
number
The
size
measured
the
complete
denotes
number,
across
the
stamped
the
symbol.
kind
eye.
Needle
Type 183
the
sizes
Typ e
180
180
183
No.
GXS
GYS
GXS
Type 180
GXS
or
183
GYS
available
Round
groove,
plated -sizes
140/054,
Round
groove,
sizes
150/060.
Round
single
chromium
110/044.
are
shank,
wide
150/060.
shank,
wide
075/029,
shank,
groove,
plated
GXS
or
180
GYS
is
recommended
is
recommended
listed
round
angle
075/029, 080/032, 090/036,
round
angle
080/032,
round
wide
-
below.
Description
point,
groove,
point,
groove,
point,
angle
sizes
for
lockstitch,
struck
lockstitch,
struck
090/036,
lockstitch,
groove,
065/025,
Style
groove,
groove,
100/040,
struck
075/029,
and
63400
Sizes
short
short
extra
for
Style
KA.
length,
deep
100/040,
length,
deep
110/044,
short
groove,
080/032,
Their
spot,
spot,
length,
deep
63400
ball
110/044,
ball
125/049,
090/036,
KB
description
eye,
ball
eye,
chromium
spot,
and
single
point,
125/049,
single
plated
140/054,
ball
ball
100/040,
needl
and
chromium
eye,
point,
e
-
183
GYS
sample
label.
used.
stitch
size
upon
Round
single
plated -sizes
To
have
needle,
A
complete
Selection
Thread
formation.
The
strength
of
the
the
size
shank,
needle
or
of
should
thread
of
round
groove,
the
order
proper
requirement
employed.
the
wide
075/029,
orders
type
would
needle
pass
SELECTING
needle
point,
angle
promptly
and
size
read:
freely
of
The
employed.
lockstitch,
groove,
080/032,
and
number
size
through
THE
the
quality
accurately
"1000
should
the
SIZE
seam
extra
struck
090/036,
should
Needles,
be
determined
needle
OF
THE
produced
of
the
short
groove,
100/040,
filled,
be
forwarded.
Type 180
eye
NEEDLE
is
l a
work
desired
deep
an
by
in
order
rgely
length,
spot,
110/044.
empty
Use
GXS,
Size
the
size
to
dependent
is
largely
ball
package,
produce
eye,
chromium
description
080/032".
of
thread
upon
dependent
a
on
a good
the
4
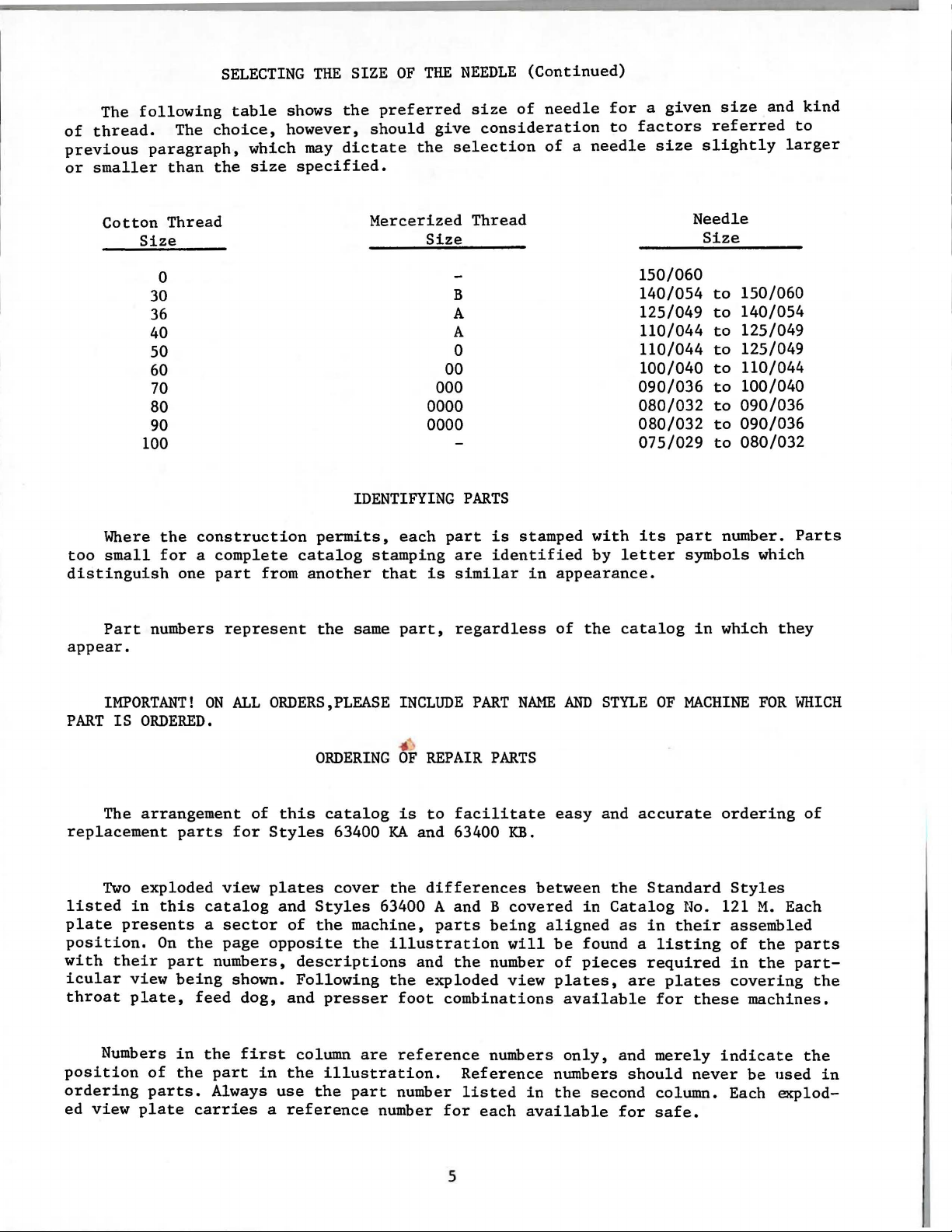
The
of
thread.
previous
or
smaller
following
The
paragraph,
than
SELECTING
table
choice,
which
the
size
THE
shows
however,
the
may
dictate
specified.
SIZE
preferred
should
OF
THE
give
the
NEEDLE
size
of
consideration
selection
(Continued)
needle
of a needle
for a given
to
factors
size
size
referred
slightly
and
larger
kind
to
Cotton
Size
100
Where
too
small
distinguish
Part
appear.
Thread
0
30
36
40
50
60
70
80
90
the
construction
for a complete
one
part
numbers
represent
from
permits,
catalog
another
the
Mercerized
Size
00
000
0000
0000
IDENTIFYING
each
part
stamping
that
is
same
part,
Thread
B
A
A
0
PARTS
is
stamped
are
identified
similar
regardless
in
appearance.
of
the
with
by
150/060
140/054
125/049
110/044
110/044
100/040
090/036
080/032
080/032
075/029
its
letter
catalog
Needle
Size
to
to
to
to
to
to
to
to
to
part
number.
symbols
in
which
150/060
140/054
125/049
125/049
110/044
100/040
090/036
090/036
080/032
Parts
which
they
IMPORTANT!
PART
replacement
listed
plate
position.
with
icular
throat
position
ordering
ed
IS
The
Two
in
presents
their
view
plate,
Numbers
view
ORDERED.
arrangement
exploded
of
parts.
plate
this
On
part
ON
parts
catalog
a
the
being
feed
in
the
the
carries
ALL
ORDERS,PLEASE
of
for
Styles
view
sector
page
numbers,
part
Always
plates
opposite
shown.
dog,
first
in
a
ORDERING
this
catalog
63400
cover
and
Styles
of
the
descriptions
Following
and
presser
column
the
illustration.
use
the
reference
INCLUDE
•
OF
REPAIR
is
to
KA
and 63400
the
differences
63400 A and B
machine,
the
are
part
number
parts
illustration
and
the
exploded
foot
reference
number
PART
N.M1E
PARTS
facilitate
KB.
between
covered
being
will
the
number
view
combinations
numbers
Reference
listed
for
each
in
available
AND
easy
in
aligned
be
found a
of
pieces
plates,
available
only,
numbers
the
second
STYLE
and
accurate
the
Catalog
as
are
and
should
for
OF
MACHINE
Standard
l~o.
in
their
listing
required
plates
for
these
merely
never
column. Each eKplodsafe.
FOR
ordering
Styles
121
M.
assembled
of
the
in
the
covering
machines.
indicate
be
used
WHICH
of
Each
parts
part-
the
the
in
5
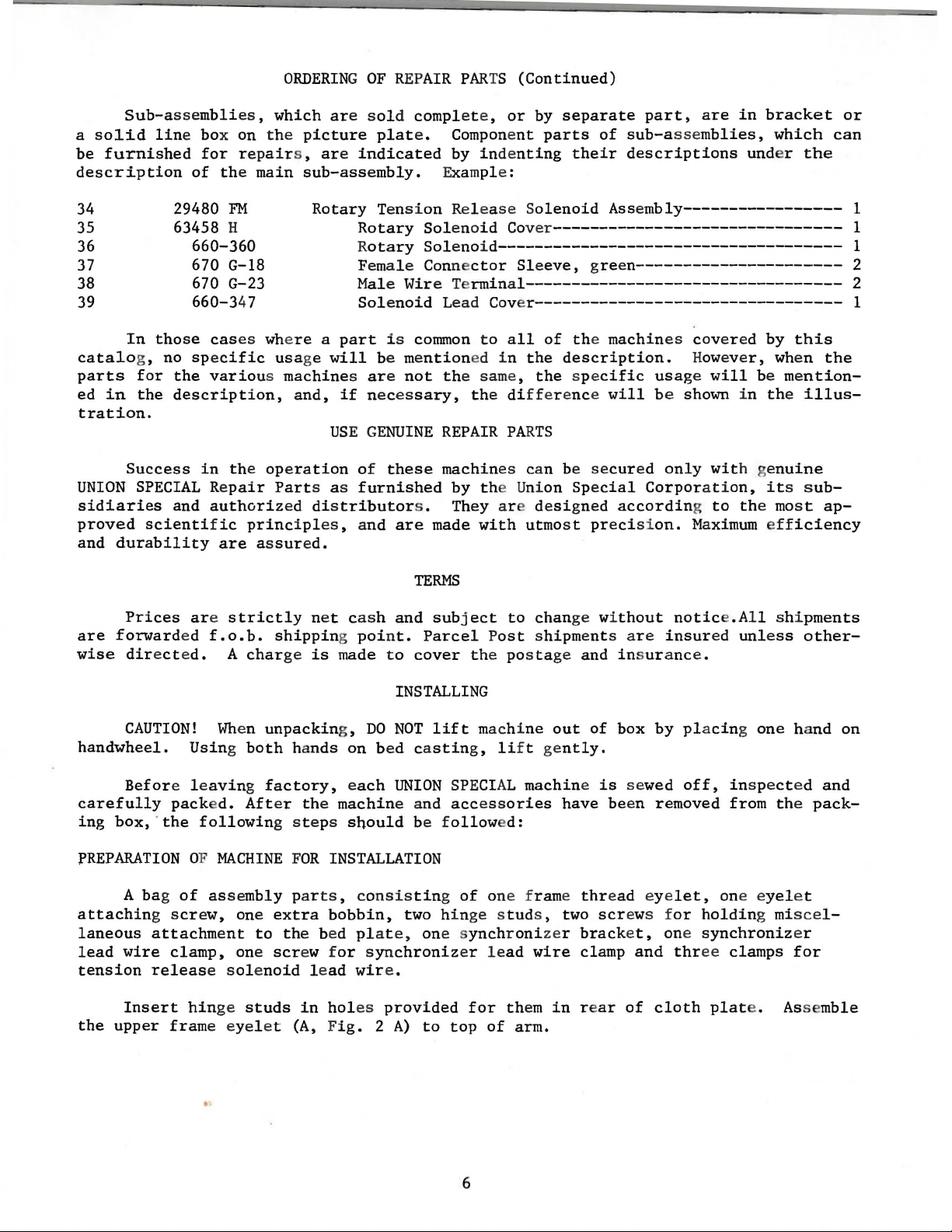
ORDERING OF REP
AIR
PAR
TS
(Continued)
Sub-a
a
solid
be
furnished
description
34
35
36
37
38
39
In
catalo
parts
ed
tration.
UNION
sidiaries
proved
and
g , no spe
for
in
the
Success
SPECIAL Repair
scientific
durability
sse
mblies,
lin
e bo x on the
for
of the
29480
63458 H
those
the
description,
and
FM
660-360
670 G-18
670 G-23
660-3
cas
cific
vario
in the ope
authoriz
are assured.
which are sold compl et e,
picture
repa i r s , are
main
sub-assembly. Exampl
Rotary
47
es whe
principles, a
re a part
usa
ge
will
us
machines are not the same ,
and,
ration
Part
s as
ed dis
plat
indicated
Tension
Rotary
R
otary
Fema l e
Male Wire Te
Solenoid Lead
i s
common
be me
if
necessary,
US
E G
ENUINE
of
these
furnished
tributor
nd
s . They ar e designed
are
e.
Sol
Sol
Connector Sle
ntion
or
by
separate
Component
by inde
Rel ea
eno
id Cover
eno i
d-------------------------------------
rminal----------------------------
Cover---------------------------------
t o
ed i n
the di
REPAIR PART
machin
by
th
made
with
parts
nting
e :
se Solenoid
-------------------------------
eve, green----------------------
all
of the machin
the
the
ffe
r ence
S
es
can be secur
Uni
on Spe
utmos t precisi
of
their
Asse
description.
spe
cific
will
cial
part,
sub-a
descriptions
mbly---------
usage will
be shown i n the
ed
Corpor
according to the mos t
on. Maximum
sse
es
only
are
mblies,
cov
er ed
Howeve
wit
at i
on,
in
bracket
which
under
-
-------
by
r, when
be me
h ge
nuine
i t s s
eff
-
-----
this
iciency
or
can
the
1
1
1
2
2
1
the
ntionillus-
ub-
ap-
Prices
are
forward
wise
handwheel.
carefully
ing
PREPARATION
attachin
laneous
lead
tension
the
directed.
CAUTION! When
Befor
box, 'the
A bag
wire
Insert
upper
e l e
packed.
g screw, one
attachment
clamp,
releas
fram
are strictly
ed
f.o.b.
A
char
Using both hands
aving factory, each
Aft
followin
OF
MACHINE FOR
of asse
hin
mbly parts, co
to the bed plat
one
e sole
e eyel et
ge
noid
studs
ne t cash
shipping point.
ge
is made
unpackin
er the
g s t eps
extra
scr
ew f
l e
in
(A, Fig.
TERMS
and
subject
Parcel Post
t o
cover the postage
INSTALLING
g ,
DO
NOT
lift machine
on bed ca
machin
should
INSTALLATION
nsis
bobbin,
or synchroniz
ad
wir
hol
es
provided
2
stin
UNION
e and
be f
ting of one
two hi nge s
e,
one s
e .
A)
to
to
chan
shipments ar e
out
g, lif t gently.
SPECIAL
acc
ollowed:
ynchronizer
er lead
for them
top
machine is sewed
ess
ories
f rame
tud
s , two
wire
in
of
arm.
ge without
and insuranc e .
of
box
have been removed from the
thr
ead eye
scr
bracket,
clamp
r e
ar
of
by pla
ews f
and
cloth
notice.A
insur
ed
cing one
off,
let,
or
holdin
one
synchroniz
thr
ee
plat
l l shi
unless
in
spected
one e
g mi
clamps
e .
yel
Assemble
pments
other-
hand
and
pack-
et
sce
ler
for
on
6
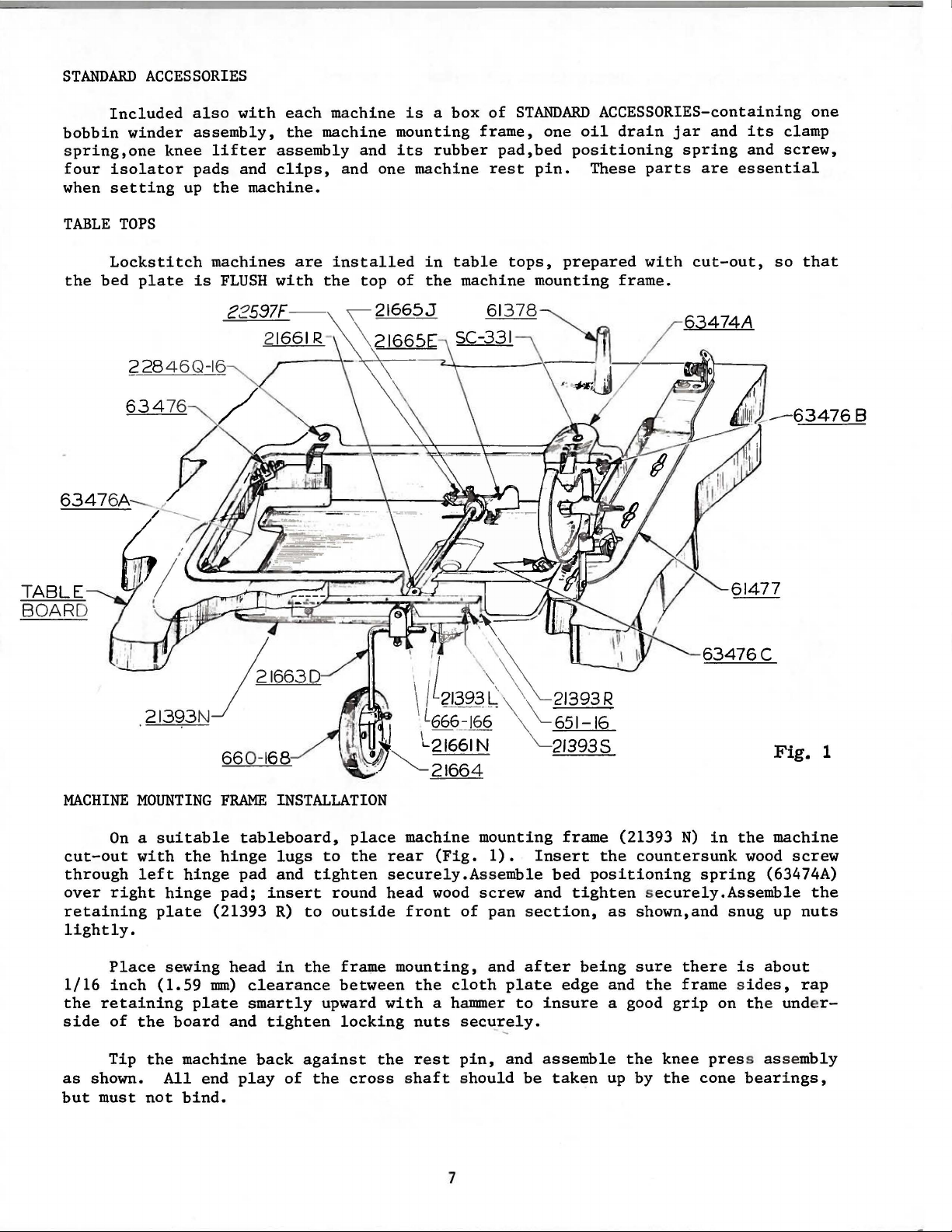
STANDARD
ACCESSORIES
Included
bobbin
spring,one
four
when
TABLE
the
6347
winder
isolator
setting
TOPS
Lockstitch
bed
228
634
6A
knee
plate
46Q-16
76
also
with
assembly,
lifter
pads
up
is
and
the
machines
FLUSH
each
the
assembly
clips,
machine.
are
with
machine
machine
and
and one machine
installed
the
top
is
mounting
its
in
of
the
a box
rubber
table
machine
of
STANDARD
frame,
pad,bed
rest
tops,
ACCESSORIES-containing
one
oil
positioning
pin.
mounting
These
prepared
drain
parts
with
frame.
jar
spring
are
cut-out,
and
essential
its
and
clamp
screw,
so
that
one
TABLE
BOARD
MACHINE
cut-out
through
over
retaining
lightly.
1/16
the
side
MOUNTING
On a suitable
with
right
Place
inch
retaining
of
left
plate
(1.59
the
the
hinge
hinge
sewing
plate
board
FRAME
tableboard,
hinge
pad
pad;
(21393
head
mm)
clearance
smartly
and
INSTALLATION
place
lugs
to
the
and
tighten
insert
R)
in
tighten
round
to
outside
the
upward
frame
between
locking
machine
rear
securely.A
head
with
(Fig.
wood
front
mounting,
the
cloth
a hammer
nuts
mounting
1).
Insert
sse
mble
screw
of
pan section,
and
plate
sec~~ely.
and
after
to
bed
insure
frame
tighten securely.Assemble
edge
(21393
the
countersunk
positioning
as
shown,and
being
sure
and
the
a good
N)
in
the
wood
spring
snug
there
frame sides,
grip
is
on the und e
about
Fig.
machine
(63474A)
up
1
screw
the
nuts
rap
r-
Tip
the
as
but
shown.
must
All
not
machine
end
bind.
back
play
against
of
the
the
r e
st
pin,
cross shaft should
7
and
be
assemble
taken
the
up by
knee
the
press assembly
cone
bearings,
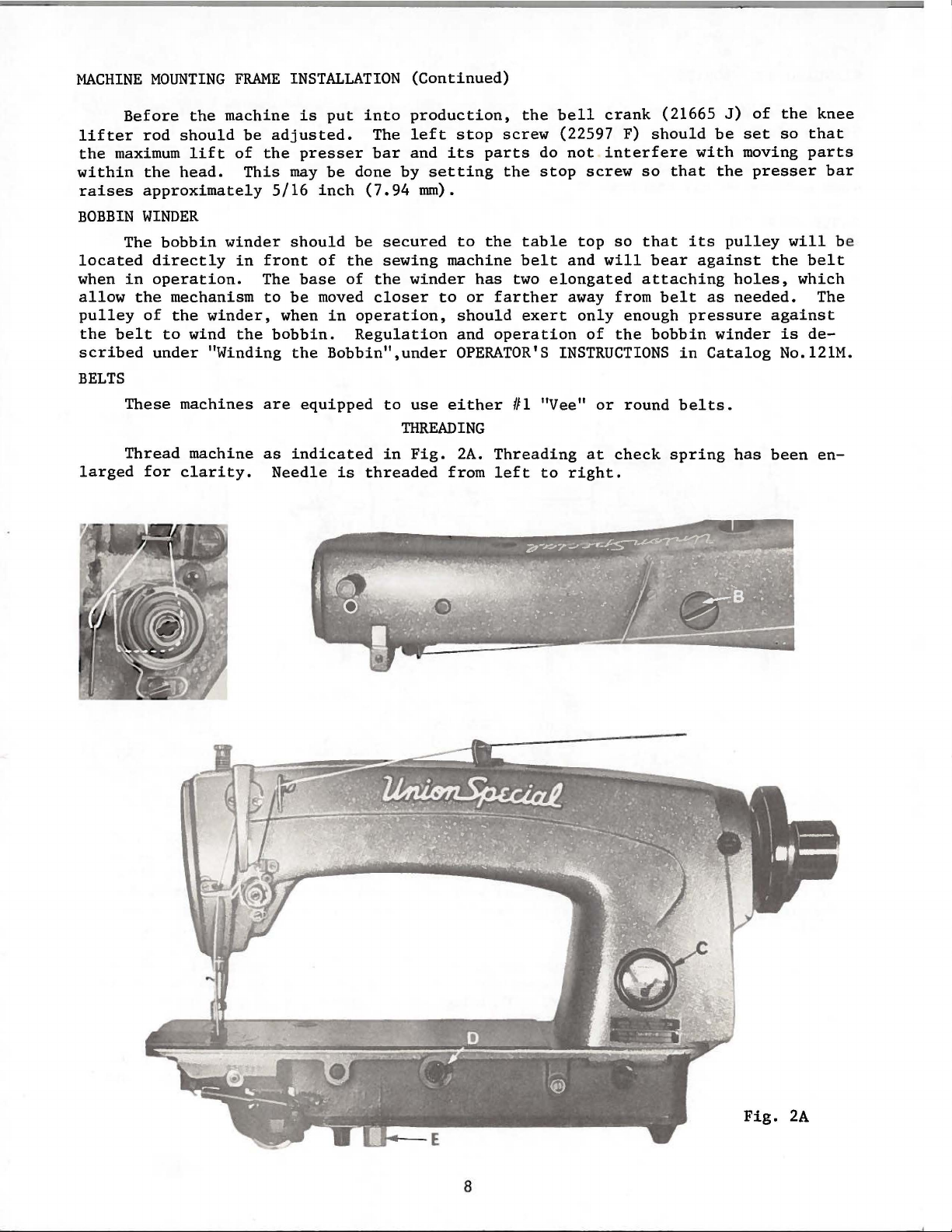
MACHINE
MOUNTING
FRAME
INSTALLATION
(Continued)
Before
lifter
the
maximum
within
raises
BOBBIN
The
located
when
allow
pulley
scribed
BELTS
larged
the
in
belt
These
Thread
the
machine
rod
should
lift
the
head.
approximately
WINDER
bobbin
directly
operation.
the
mechanism
of
the
to
under
for
winder
winder,
wind
"Winding
machines
machine
clarity.
be
of
This
in
the
is
adjusted.
the
presser
may
5/16
should
front
The
base
to
be
when
bobbin.
the
are
equipped
as
indicated
Needle
put
into
production,
The
left
bar
and
be
done
by
inch
of
moved
(7.94
be
secured
the
sewing
of
the
winder
closer
in
operation,
Regulation
Bobbin",under
to
use
THREADING
in
Fig.
is
threaded
stop
its
setting
mm).
to
machine
to
or
should
and
OPERATOR'S
either
2A.
from
the
screw
parts
the
the
table
belt
has
two
farther
exert
operation
Ill
Threading
left
bell
do
stop
elongated
"Vee"
to
crank
(22597 F)
not
interfere
screw
top
so
and
will
away from
only
enough
of
the
INSTRUCTIONS
or
round
at
check
right.
(21665
should
with
so
that
that
attaching
its
bear
belt
pressure
bobbin
in
belts.
spring
against
J)
of
be
set
moving
the
presser
pulley
holes,
as
needed.
winder
Catalog
has
the
knee
so
that
parts
bar
will
the
belt
which
The
against
is
de-
No.121M.
been
en-
be
8
Fig.
2A
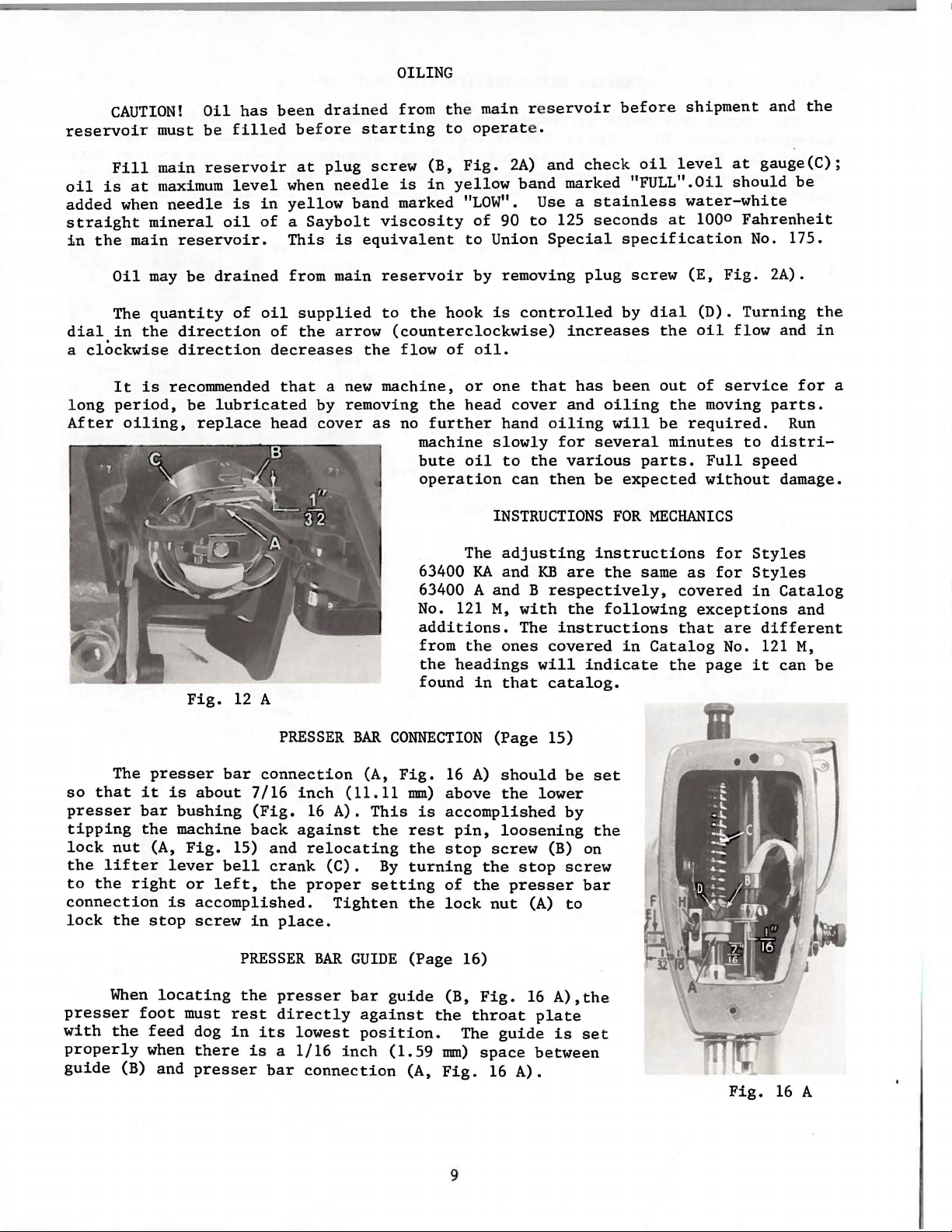
OILING
CAUTION!
reservoir
Fill
oil
is
added
straight
in
dial
a
long
After
when
the
Oil
The
in
clockwise
It
period,
oiling,
must
main
at
maximum
needle
mineral
main
reservoir.
may
quantity
the
direction
direction
is
recommended
Oil
be
reservoir
oil
be
drained
be
lubricated
replace
Fig.
has been
fill
ed bef
at
level
is
of
12
when
in
yellow
of a Saybolt
This
from main
oil
supplied
of
the
decreases
that a new
head
A
drain
ore
plug
needle
band
is
arrow
by
removing
cover
ed from the main re
starting
screw
marked
viscosity
equivalent
reservoir
to
(counterclockwise)
the
machine,
as
to
(B,
is
in
the
hook
flow
of
the
no
further
machine
bute
operation
63400
63400 A
No. 121
additions.
from
the
found
operat
Fig.
yellow
headings
2A)
"LOW".
of
90
to
Union
by
removing
is
oil.
or
one
head
hand
slowly
oil
to
INSTRUCTIONS
The
adjusting
KA
and
and B respectively,
M,
the
ones
in
that
servoir
e .
and
band
cover
can
with
The
marked "FULL".Oil
Use a
to
125
Special
controlled
increases
that
has
and
oiling
for
the
various
then
KB
are
the
instructions
covered
will
catalog.
before
check
plug
indicate
oil
stainless
seconds
specification
screw
by
dial
been
oiling
will
several
parts.
be
expected
FOR
MECHANICS
instructions
the
same
following
in
Catalog
shipment
level
water-white
at
1000
(E,
(D).
the
oil
out
of
the
moving
be
required.
minutes
Full
without
for
as
for
covered
exceptions
that
the
page
and
at
gauge(C);
should
Fahrenheit
No.
Fig.
2A).
Turning
flow
service
parts.
to
distri-
speed
Styles
Styles
in
Catalog
are
different
No.
121
it
can
the
be
175.
the
and
in
for
Run
damage.
and
M,
be
a
The
so
that
presser
tipping
lock
nut
the
lifter
to
the
right
connection
lock
the
When
presser
with
properly
guide
foot
the
(B) and
presser
it
is
bar
bushing
the
machine
(A,
lever
is
stop
locating
feed
when
bar
connection
about
Fig.
or
accomplished.
screw
must
dog
there
presser
7/16
(Fig.
back
15)
bell
left,
in
PRESSER
the
rest
in
is a 1/16
and
crank
the
directly
its
bar
PRESSER
inch
16
A).
against
relocating
(C).
proper
Tighten
place.
BAR
presser
lowest
connection
BAR
(A,
(11.11
This
the
By
setting
GUIDE
bar
against
position.
inch
CONNECTION
Fig.
16
A)
mm)
above
is
accomplished
rest
pin,
the
stop
turning
the
(Page 16)
guide
(1.59
(A,
of
lock
(B,
the
mm)
Fig.
9
the
the
Fig.
throat
The
space
(Page
should
the
lower
loosening
screw
stop
presser
nut
(A)
16
plate
guide
between
16
A).
15)
be
by
(B) on
screw
bar
to
A),the
is
set
set
the
Fig.
16
A
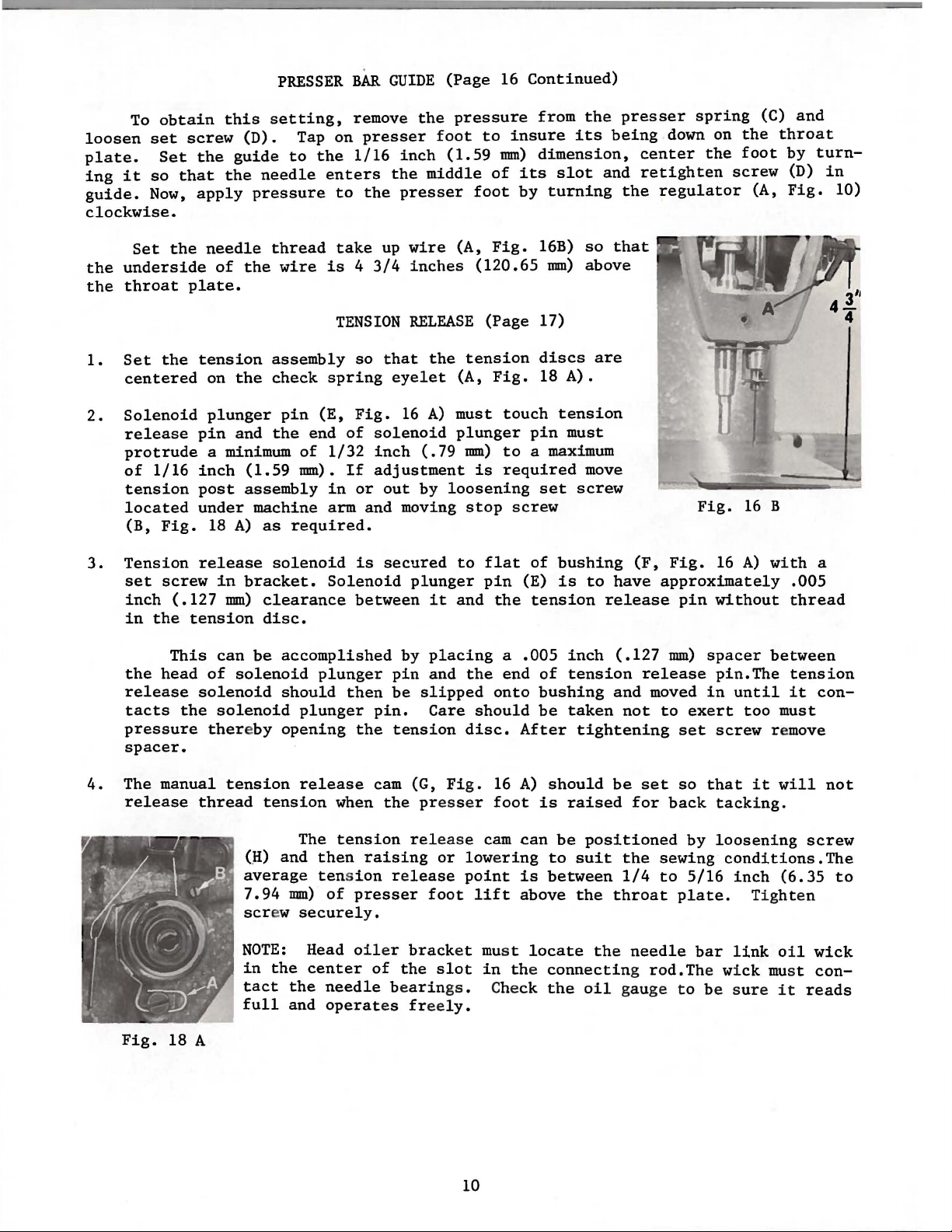
To
loosen
plate.
ing
guide.
clockwise.
the
the
set
it
so
Now,
Set
underside
throat
obtain
screw
Set
the
that
apply
the
plate.
this
(D).
guide
the
needle
of
the
PRESSER
setting,
Tap on
to
needle
pressure
thread
wire
BAR
remove
presser
the
1/16
enters
to
the
take
is 4 3/4
GUIDE
inch
the
presser
up
wire
inches
(Page
the
pressure
foot
(1.59
middle
to
foot
(A,
(120.65
16
Continued)
insure
mm)
of
its
by
Fig.
from
dimension,
16B)
the
its
slot
turning
so
mm)
above
being
and
that
presser
down on
center
retighten
the
regulator
spring
the
screw
(C)
the
foot
(A,
and
throat
by
turn(D)
Fig.
in
10)
1.
2.
3.
Set
the
centered
Solenoid
release
protrude
of
1/16
tension
located
(B,
Fig.
Tension
set
screw
inch
in
the
release
tacts
pressure
spacer.
(.127
the
This
head
the
tension
on
the
plunger
pin
and
a minimum
inch
post
under
release
tension
solenoid
(1.59
assembly
18
A)
in
bracket.
mm)
can
of
solenoid
solenoid
thereby
TENSION
assembly
check
the
machine arm
as
solenoid
clearance
disc.
be
spring
pin
(E,
end
of
of
1/32
mm).
required.
accomplished
should
opening
If
in
Solenoid
plunger
then
plunger
RELEASE
so
that
eyelet
Fig.
or
between
16
solenoid
inch
adjustment
out
and
moving
is
secured
plunger
by
pin
be
pin.
the
tension
the
tension
(A,
A)
must
plunger
(.79
mm)
by
loosening
stop
to
it
and
placing
and
the
slipped
Care
disc.
(Page 17)
discs
Fig.
is
flat
pin
onto
should
18
touch
pin
to a maximum
required
set
screw
of
(E)
the
tension
a
.005
end
of
bushing
be
After
are
A).
tension
must
move
screw
bushing
is
to
release
inch
tension
taken
tightening
(F,
have
(.127
release
and
not
Fig.
Fig.
approximately
mm)
moved
to
pin
exert
set
16
A)
without
spacer
pin.The
in
until
screw
16
B
with
between
too
remove
.005
thread
tension
it
must
a
con-
4.
The manual
release
Fig.
18 A
tension
thread
tension
(~)
and
average
7.94
mm)
scr
ew
NOTE:
in
the
tact
the
full
and
release
The
then
tension
securely.
Head
center
needle bearings. Che
operat
when
tension
raising
of
presser
oil
cam
(G, Fig.
the pres
rel
r e
lease
er
brack
of
the
es free
ease cam
or
foot
slot
ly.
16
ser
foot
lowe
ring
point
lift
et must
in the
10
A)
should
is
can
be
to
is
between
above
locate
connecting rod.Th
ck
the
be
raised
positioned
suit
the
throat
the
oil gau
the
1/4
set
for
back
sewing
to
needle
ge
so
that
tacking.
by
loosening
conditions.The
5/16
inch
plate.
bar
link
e wi
t o be su
it
will
(6.35
Tight
oi l
ck must
re
it
not
screw
to
en
wick
con-
reads
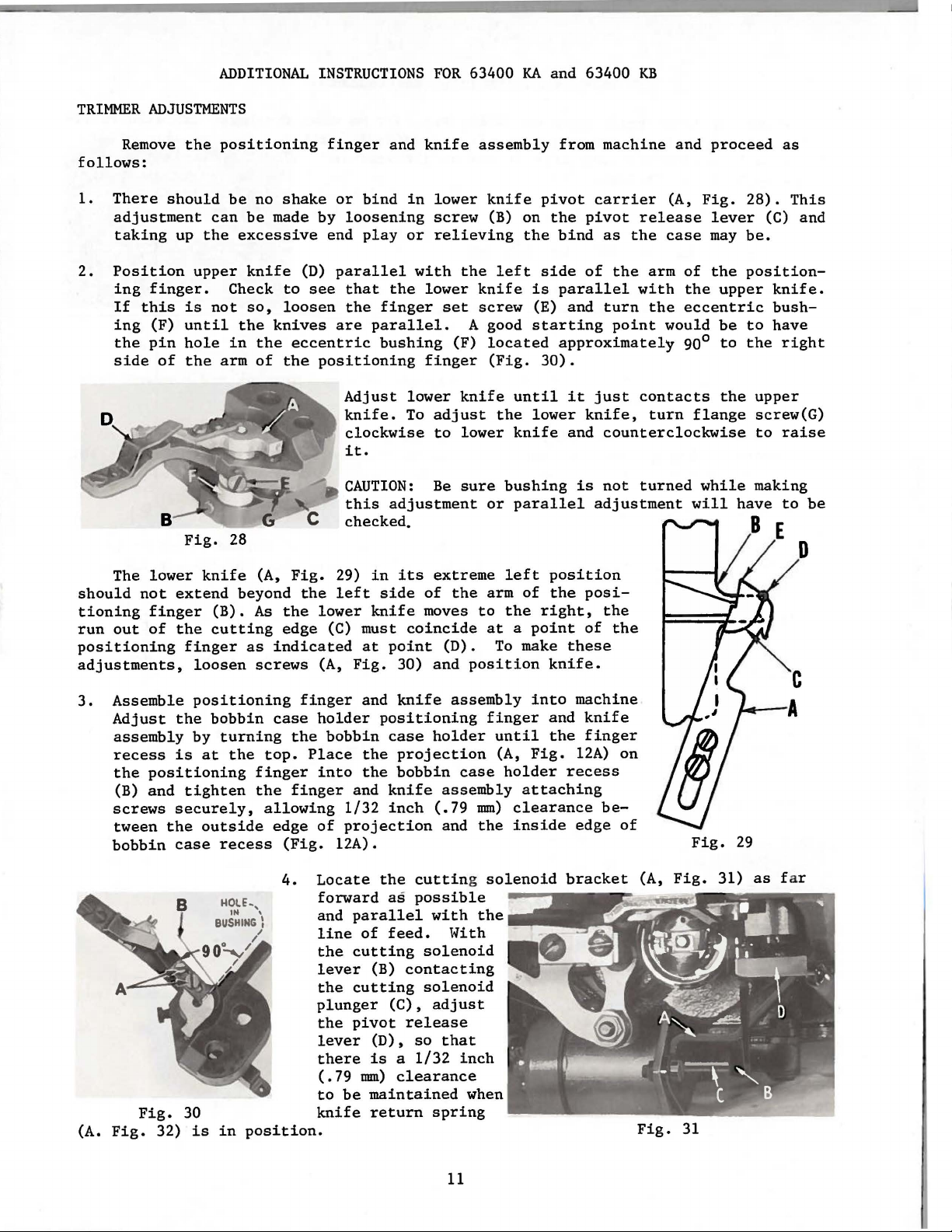
ADDITIONAL
INSTRUCTIONS
FOR
63400
KA
and 63400
KB
TRIMMER
follows:
1.
2.
should
tioning
run
positioning
adjustments,
ADJUSTMENTS
Remove
There
adjustment
taking
Position
ing
finger.
If
this
ing
(F)
the
pin
side
of
The
lower
not
finger
out
of
the
should
up
the
upper
is
until
hole
the
Fig.
knife
extend
the
finger
loosen
positioning
be
no
can
be
made
excessive
knife
Check
not
so,
the
knives
in
the
arm
of
28
(A,
beyond
(B).
As
cutting
as
indicated
screws
finger
shake
by
end
(D)
to
see
loosen
eccentric
the
positioning
Fig.
the
the
lower
edge
(C) must
(A,
and
or
bind
loosening
play
parallel
that
the
the
finger
are
parallel.
bushing
Adjust
knife.
clockwise
it.
CAUTION:
this
adjustment
checked.
29)
in
left
side
knife
at
point
Fig.
knife
in
lower
screw
or
relieving
with
lower
finger
lower
To
adjust
to
Be
its
extreme
of
moves
coincide
30)
and
the
set
A good
(F)
knife
lower
sure
the
(D).
position
assembly
knife
(B) on
knife
screw
located
(Fig.
or
arm
to
at a point
To
the
left
is
(E)
starting
until
the
lower
knife
bushing
parallel
left
of
the
make
pivot
side
30).
right,
from
machine
carrier
the
pivot
bind
as
the
of
the
parallel
and
approximately
it
knife,
and
is
position
the
posiof
these
knife.
with
turn
point
just
counterclockwise
not
adjustment
the
the
and
(A,
release
case
arm
of
the
the
eccentric
would
90°
contacts
turn
flange
turned
will
proceed
Fig.
lever
may
the
upper
be
to
the
while
have
as
28).
This
(C) and
be.
position-
knife.
bush-
to
have
the
right
upper
screw(G)
to
raise
making
to
D
be
3.
(A.
Assemble
Adjust
assembly
recess
the
positioning
(B)
and
screws
tween
bobbin
Fig.
the
Fig.
32)
positioning
the
bobbin
by
turning
is
at
the
tighten
securely,
outside
case
recess
30
is
in
finger
case
the
top.
finger
the
finger
allowing
edge
(Fig.
4.
position.
holder
bobbin
Place
into
1/32
of
projection
12A).
Locate
forward
and
line
the
lever
the
plunger
the
lever
there
(.79
to
be
knife
and
knife
positioning
case
the
projection
the
bobbin
and
knife
inch
the
as
parallel
of
feed.
cutting
(B)
contacting
cutting
(C),
pivot
mm)
release
(D),
is a 1/32
clearance
maintained
return
assembly
holder
case
assembly
(.79
mm)
and
the
cutting solenoid
possible
with
the
loli
th
solenoid
solenoid
adjust
so
that
inch
when
spring
finger
until
(A,
holder
attaching
clearance
inside
into
Fig.
machine
and
the
12A)
recess
edge
bracket
knife
finger
on
be-
of
(A,
Fig.
Fig.
Fig.
31
31)
29
as
f ar
11
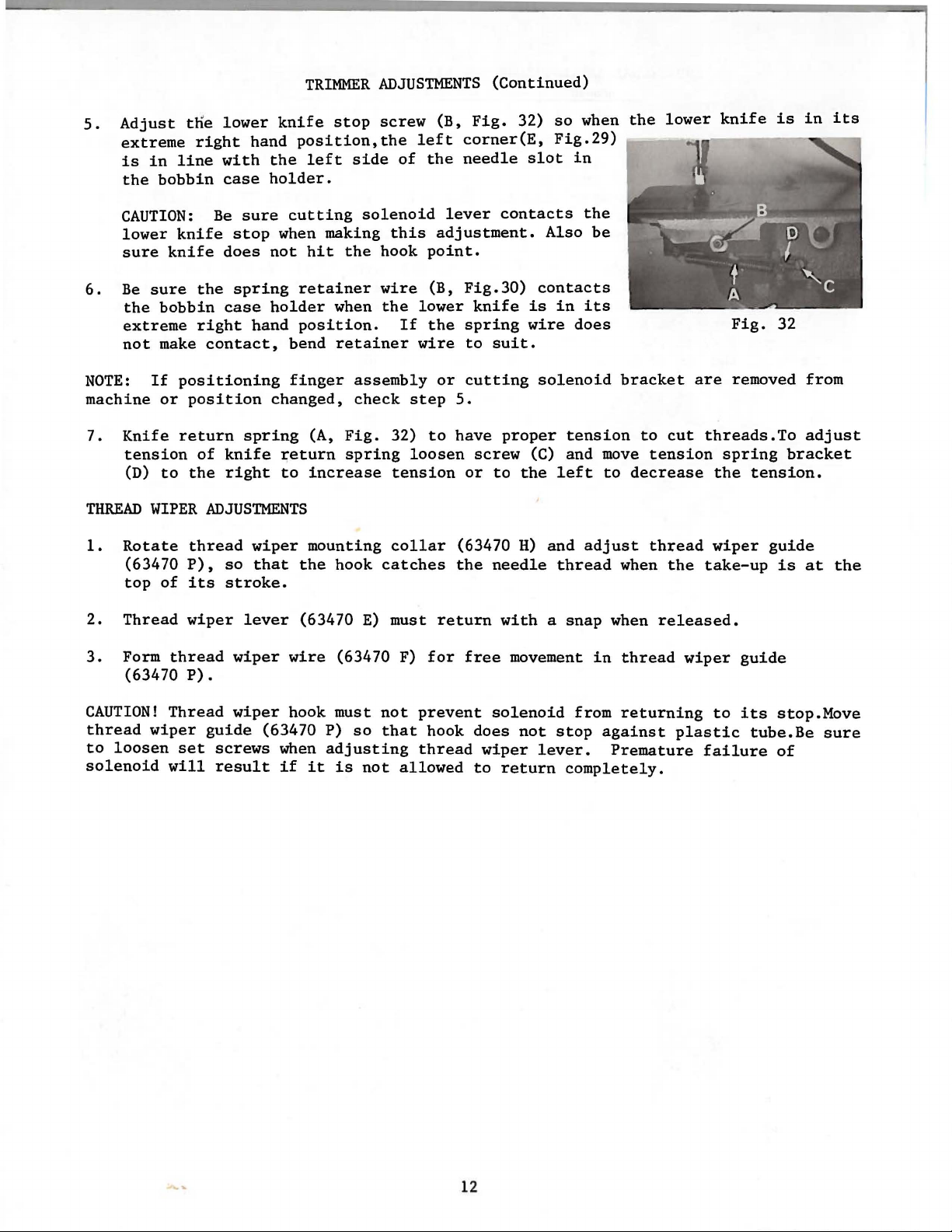
5.
Adjust
extreme
is
in
the
bobbin
t~e
right
line
lower
hand
with
case
TRIMMER
knife
position,the
the
left
holder.
ADJUSTMENTS
stop
screw
side
of
(B,
left
the
(Continued)
Fig.
32)
corner(E,
needle
slot
so
when
Fig.29)
in
the
lower
knife
is
in
its
CAUTION:
lower
sure
6.
Be
the
extreme
not
NOTE:
machine
7.
Knife
tension
(D)
THREAD
1.
Rotate
(63470
top
2.
Thread
3.
Form
(63470
knife
knife
sure
If
WIPER
the
bobbin
right
make
positioning
or
position
return
of
to
the
thread
P),
of
its
wiper
thread
P).
Be
sure
cutting
stop
when making
does
not
hit
spring
case
contact,
spring
knife
right
ADJUSTMENTS
so
stroke.
lever
wiper
holder
hand
bend
finger
changed,
return
to
wiper
that
wire
retainer
position.
(A,
increase
mounting
the
(63470
solenoid
this
the
hook
wire
when
the
If
retainer
assembly
check
Fig.
32)
spring
tension
collar
hook
catches
E)
must
(63470 F)
lever
adjustment.
point.
(B,
lower
the
wire
or
step
to
loosen
return
for
5.
have
(63470
the
contacts
Fig.30)
knife
spring
to
suit.
cutting
proper
screw
or
to
the
H)
needle
with a snap
free
movement
Also
contacts
is
in
wire
does
solenoid
tension
(C)
and
left
and
thread
the
be
its
bracket
move
to
adjust
when
when
in
thread
to
cut
tension
decrease
thread
the
released.
wiper
Fig.
are
removed from
threads.To
spring
the
tension.
wiper
take-up
guide
32
bracket
guide
is
adjust
at
the
CAUTION!
thread
to
solenoid
wiper
loosen
Thread
guide
set
will
wiper
screws
result
hook must
(63470 P)
when
if
adjusting
it
is
so
not
not
that
allowed
prevent
hook
thread
solenoid
does
wiper
to
return
not
from
stop
lever.
completely.
returning
against
Premature
to
plastic
failure
its
stop.Move
tube.Be
of
sure
12