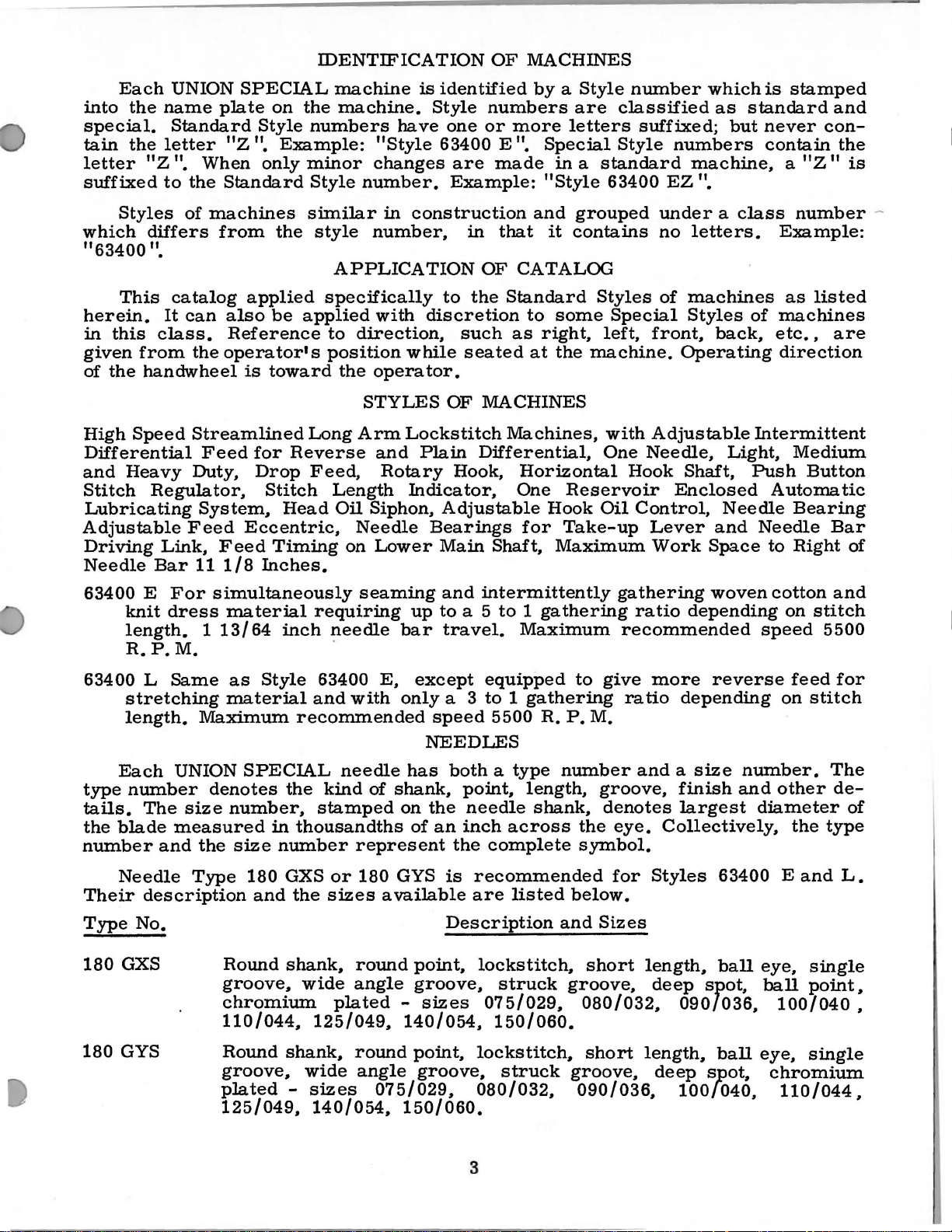
IDENTIFICATION
OF
MACHINES
Each
into
the
name
special.
tain
the
letter
letter
suffixed
"Z
to
Styles
which
11
63400
differs
11
•
This
herein.
in
this
given
of
the
High
It
class.
from
handwheel
Speed
Differential
and
Heavy
Stitch
Regulator,
Lubricating
Adjustable
Driving
Needle
Link,
Bar
UNION
SPECIAL
plate
Standard
•
When
the
Standard
of
machines
"Z
11
from
catalog
can
also
Reference
the
operator's
Streamlined
Feed
Duty,
System,
Feed
Feed
111/8
on
the
Style
11
•
only
numbers
Example:
minor
Style
similar
the
style
applied
be
applied
is
toward
Long
for
Reverse
Drop
Feed,
Stitch
Head
Eccentric,
Timing
Inches.
machine
machine.
is
Style
have
"Style
changes
number.
in
construction
number,
APPLICATION
specifically
with
to
direction,
position
the
opera
discretion
while
tor.
STYLES
Arm
Lockstitch
and
Plain
Rotary
Length
Oil
Needle
on
Indicator,
Siphon,
Bearings
Lower
identified
numbers
one
or
more
63400
are
E ".
made
Example:
in
that
OF
CATALOG
to
the
Standard
such
as
seated
OF
MACHINES
Machines,
Differential,
Hook,
One
Adjustable
Main
Shaft,
by a Style
are
letters
Special
in a standard
"Style
and
grouped
it
contains
Styles
to
some
right,
at
the
machine.
Horizontal
Reservoir
Hook
for
Oil
Take-up
Maximum
number
classified
suffixed;
Style
63400
under a class
no
of
Special
left,
One
with
front,
Adjustable
Needle,
Hook
Control,
Lever
Work
which
as
numbers
machine,
EZ
".
letters.
machines
Styles
back,
Operating
Shaft,
Enclosed
Needle
and
Space
is
stamped
standard
but
never
contain
a
Example:
as
of
machines
etc.,
direction
Intermittent
Light,
Push
Automatic
Needle
to
and
con-
the
11
"Z
is
number
listed
are
Medium
Button
Bearing
Bar
Right
of
-
63400 E For
knit
dress
length. 1 13/64
R.P.M.
63400 L Same
stretching
length.
Each
type
number
tails.
the
blade
number
Needle
Their
Type
180
No.
GXS
The
description
Maximum
UNION
size
measured
and
the
Type
simultaneously
material
requiring
inch
as
Style
material
63400
and
recommended
SPECIAL
denotes
number,
size
Round
groove,
180
and
the
stamped
in
thousandths
number
GXS
the
shank,
wide
chromium
110/044,
125/049,
seaming
needle
.
with
needle
kind
represent
or
180
sizes
round
angle
plated
up
bar
E,
except
only
has
of
shank,
on
of
GYS
available
point,
groove,
-
sizes
140/054,
and
intermittently
to
a 5
to 1 gathering
travel.
equipped
a 3
to 1 gathering
speed
5500
NEEDLES
both a type
point,
the
needle
an
inch
the
complete
is
recommended
are
Description
lockstitch,
struck
075/029, 080/032, 090/036,
150/060.
Maximum
R.
P.M.
number
length,
shank,
across
listed
and
groove,
gathering
to
give
groove,
denotes
the
eye.
symbol.
for
below.
Sizes
short
woven
ratio
depending
recommended
more
ratio
reverse
depending
and a size
finish
largest
Collectively,
Styles
length,
deep
63400 E and
ball
spot,
cotton
on
speed
feed
on
number.
and
other
diameter
the
eye,
ball
100/040,
and
stitch
5500
for
stitch
The
de-
of
type
L.
single
point,
180
GYS
I
Round
groove,
plated
125/049,
shank,
wide
-
sizes
140/054,
round
angle
075/029,
point,
groove,
150/060.
lockstitch,
struck
080/032,
3
short
groove,
090/036,
length,
deep
100/040,
ball
spot,
eye,
single
chromium
110/044,
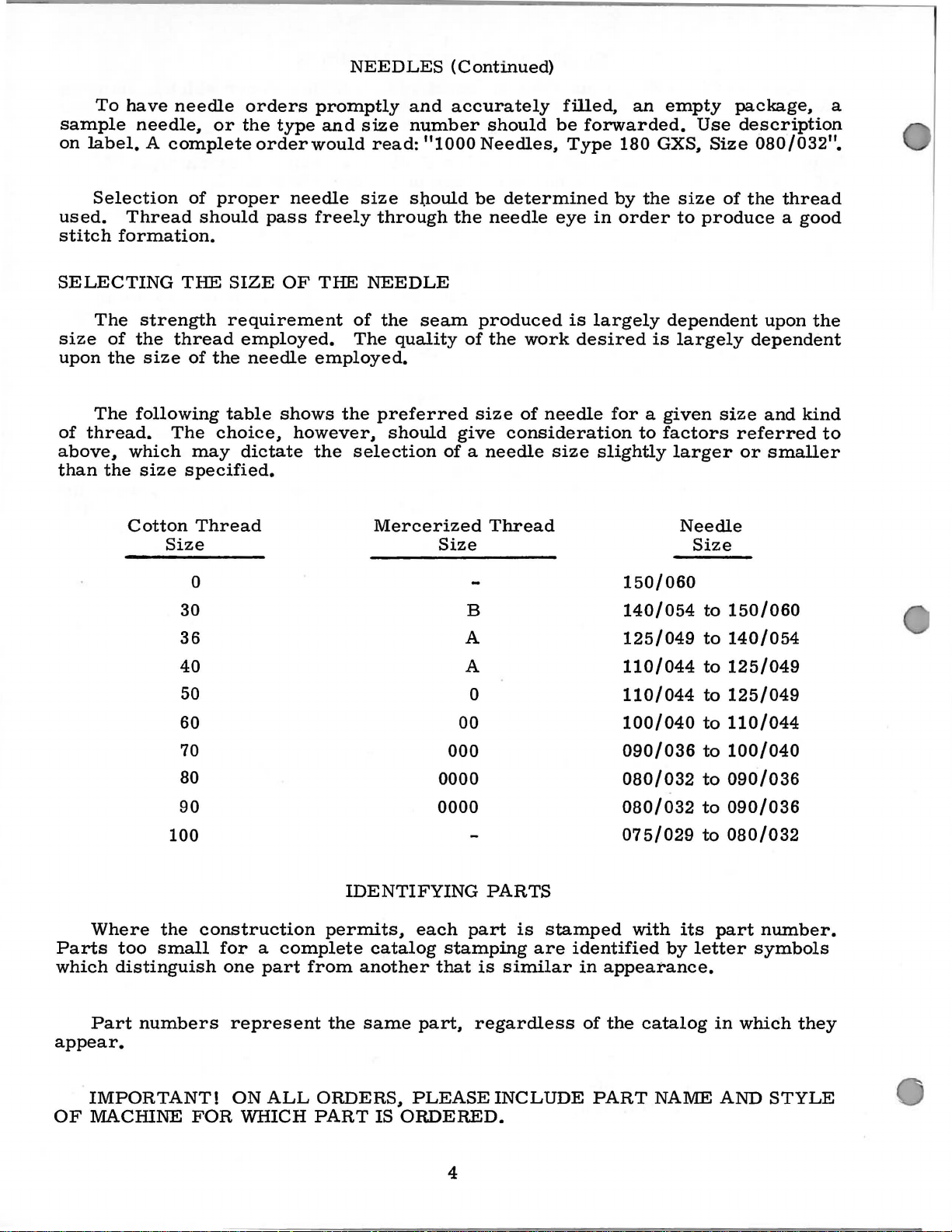
To
have
sample
on
label. A complete
needle
needle,
or
orders
the
type
order
NEEDLES
promptly
and
size
would
read:
(Continued)
and
accurately
number
"1000
should
Needles,
filled,
be
forwarded.
Type
an
180
empty
GXS,
package,
Use
Size
a
description
080/032".
Selection
used.
stitch
Thread
formation.
SELECTING
The
strength
size
upon
of
above,
than
of
the
the
The
following
thread.
which
the
size
size
Cotton
of
proper
should
THE
thread
of
the
The
choice,
may
specified.
Thread
Size
0
30
36
needle
pass
SIZE
freely
OF
requirement
employed.
needle
table
employed.
shows
however,
dictate
the
THE
the
size
sl;lould
through
NEEDLE
of
the
The
quality
preferred
should
selection
Mercerized
be
the
seam
produced
of
size
give
of a needle
Size
B
A
determined
needle
eye
is
the
work
of
needle
consideration
size
Thread
by
in
order
largely
desired
for a given
slightly
150/060
140/054
125/049
the
size
to
dependent
is
largely
to
factors
larger
Needle
of
the
thread
produce a good
upon
the
dependent
size
and
kind
referred
or
smaller
Size
to
150/060
to
140/054
to
Where
Parts
which
too
distinguish
Part
appear.
IMPORTANT!
OF
MACHINE
40
50
60
70
80
90
100
the
construction
small
numbers
FOR
IDENTIFYING
permits,
for a complete
one
part
from
represent
ON
ALL
WHICH
the
ORDERS,
PART
catalog
another
same
PLEASE
IS
ORDERED.
000
0000
0000
each
stamping
that
part,
A
0
00
PARTS
part
is
similar
is
regardless
INCLUDE
stamped
are
identified
in
110/044
110/044
100/040
090/036
080/032
080/032
075/029
with
appearance.
of
the
catalog
PART
to
to
to
to
to
to
to
its
by
letter
NAME
125/049
125/049
110/044
100/040
090/036
090/036
080/032
part
number.
symbols
in
which
AND
they
STYLE
4
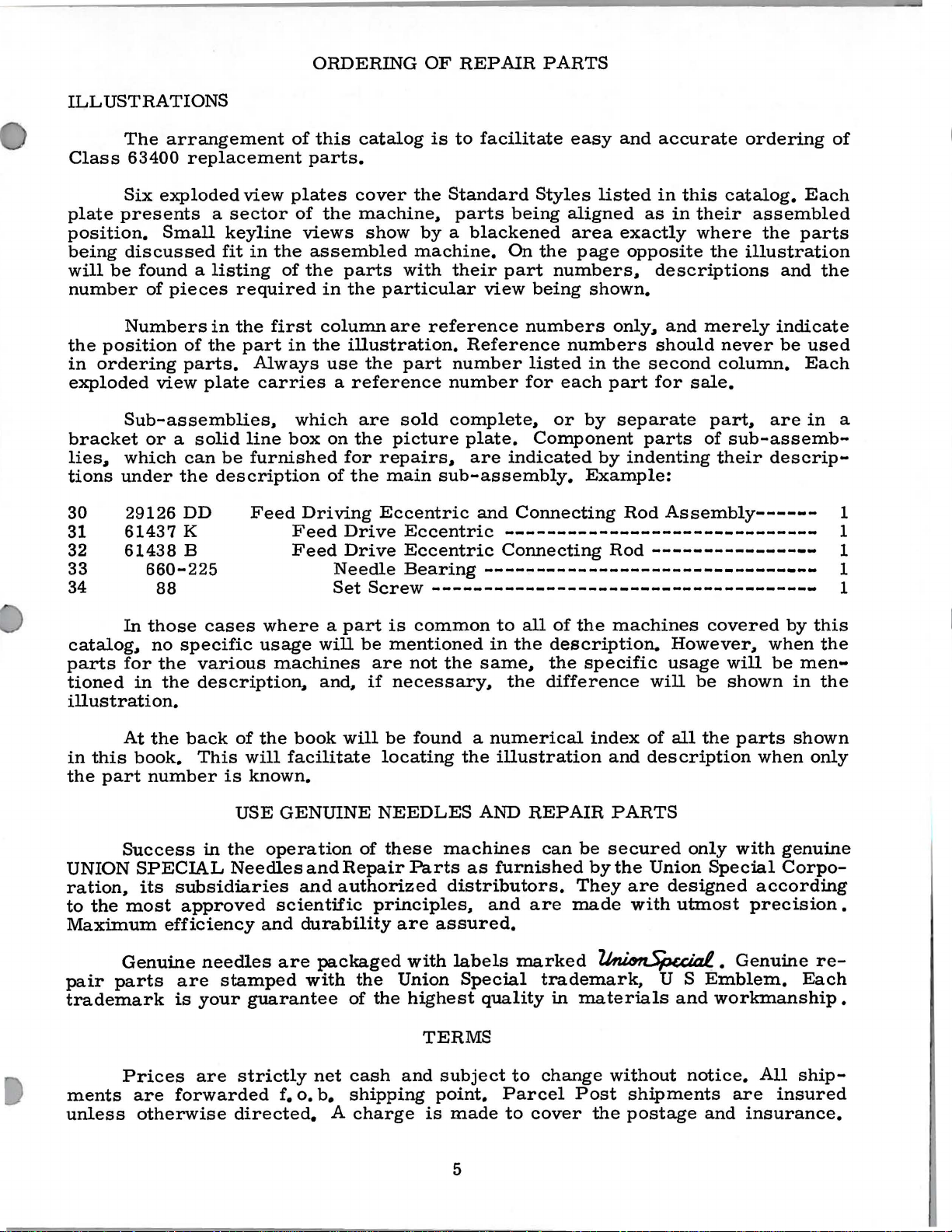
ILLUSTRATIONS
The
arrangement
Class
plate
position.
being
will
number
63400
Six
replacement
exploded
presents
Small
discussed
be
found a listing
of
pieces
a
view
sector
keyline
fit
in
required
ORDERING
of
this
parts.
plates
of
the
views
the
assembled
of
the
in
catalog
cover
machine,
show
parts
the
particular
OF
REPAIR
is
to
facilitate
the
Standard
parts
by a blackened
machine.
with
their
On
part
view
PARTS
Styles
being
the
being
easy
and
listed
aligned
area
exactly
page
numbers,
shown.
accurate
in
this
as
in
opposite
descriptions
catalog.
their
where
the
ordering
Each
assembled
the
parts
illustration
and
the
of
Numbers
the
position
in
ordering
exploded
view
Sub-assemblies,
bracket
lies,.
tions
30
31
32
33
34
catalog,.
parts
tioned
or a solid
which
under
29126
61437
61438
660-225
88
In
those
no
for
the
in
illustration.
At
the
in
this
book.
the
part
number
in
of
the
parts.
plate
can
the
description
DD
K
B
cases
specific
various
the
description,
back
This
the
first
part
Always
carries
line
be
furnished
Feed
where a part
usage
machines
of
the
will
is
known.
column
in
the
use
a
which
box
on
of
Driving
Feed
Feed
Needle
SetScrew-------------------------------------
will
and,
book
will
facilitate
are
reference
illustration.
the
part
reference
are
sold
the
picture
for
repairs,
the
main
Eccentric
Drive
Drive
Eccentric------------------------------
Eccentric
Bearing
is
common
be
mentioned
are
not
if
necessary,
be
found a numerical
locating
numbers
Reference
number
number
complete,
plate.
are
indicated
numbers
listed
for
each
or
Component
sub-assembly.
and
Connecting
Connecting
--------------------------------
to
all
of
in
the
description.
the
same,
the
illustration
the
the
difference
only,
in
the
part
by
separate
by
indenting
Example:
Rod
Rod
the
machines
specific
index
and
and
merely
should
second
for
never
column.
sale.
part,
parts
of
sub-assemb-
their
Assembly------
----------------
covered
However,
will
of
usage
all
be
the
will
shown
description
are
descrip-
when
be
parts
when
indicate
be
used
Each
in
by
this
the
men-
in
the
shown
only
a
1
1
1
1
1
USE
Success
UNION
ration,
to
the
SPECIAL
its
most
Maximum
Genuine
pair
parts
trademark
in
the
Needles
subsidiaries
approved
efficiency
needles
are
stamped
is
your
GENUINE
operation
and
and
scientific
and
durability
are
packaged
with
guarantee
NEEDLES
of
these
Repair
Parts
authorized
principles,
are
with
the
Union
of
the
highest
AND
machines
as
furnished
distributors.
and
assured.
labels
marked
Special
quality
REPAIR
can
are
trademark,
in
TERMS
ments
unless
Prices
are
otherwise
are
strictly
forwarded
directed.
f.
o.
net
b.
A
cash
and
shipping
charge
subject
point.
is
made
5
to
change
Parcel
to
cover
PARTS
be
secured
by
the
They
made
are
with
~.
materials
without
Post
shipments
the
postage
only
Union
designed
utmost
U S
and
notice.
with
genuine
Special
Corpo-
according
precision.
Genuine
Emblem.
Each
workmanship.
All
ship-
are
insured
and
insurance.
re-
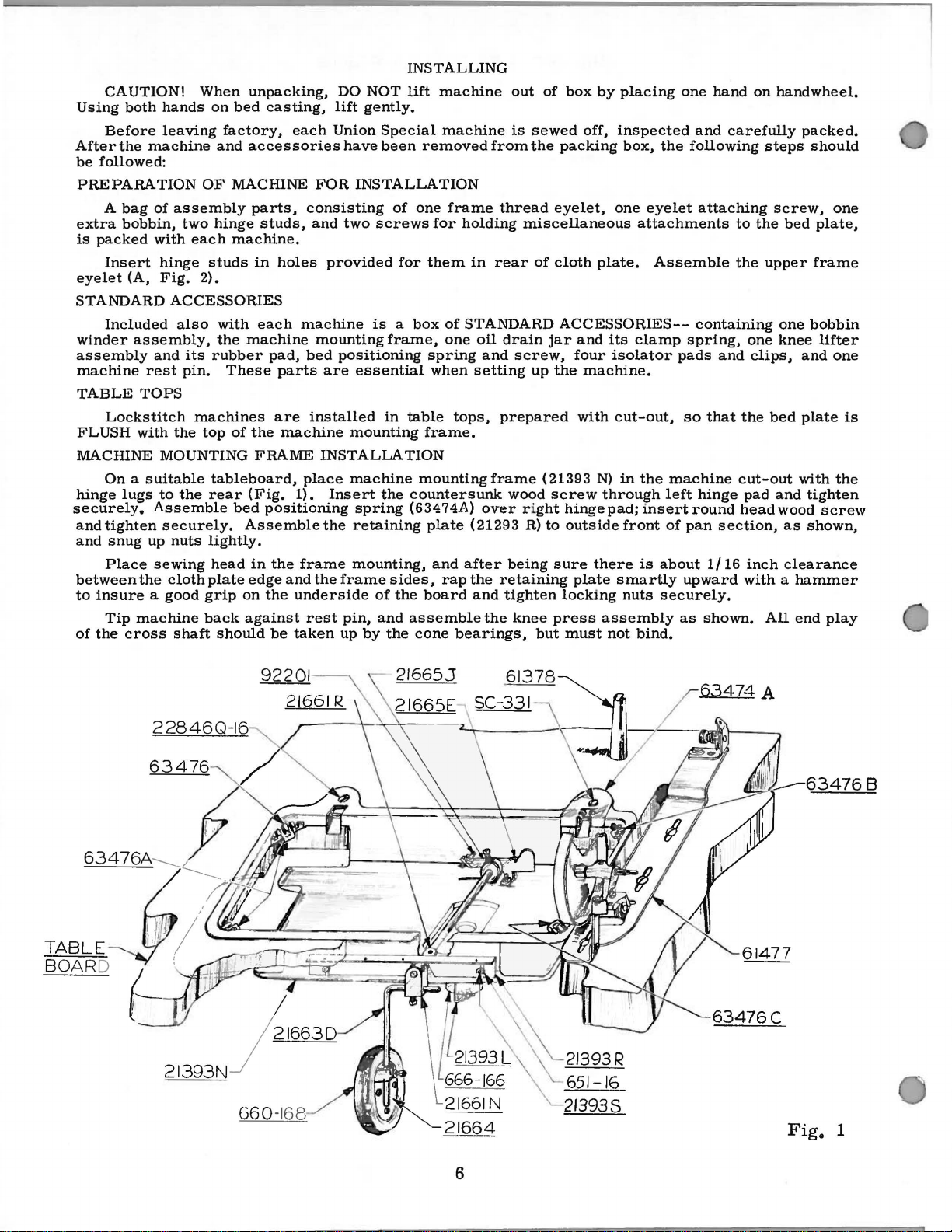
CAUTION!
Using
After
be
PREPARATION
extra
is
eyelet
STANDARD
winder
assembly
machine
TABLE
FLUSH
MACHINE MOUNTING
hinge
securely.
and
and
between
to
of
both
Before
the
machine
followed:
A
bag
bobbin,
packed
Insert
(A,
Included
assembly,
rest
TOPS
Lockstitch
with
On a suitable
lugs
tighten
snug
up
Place
the
insure a good
Tip
machine
the
cross
When
hands
leaving
of
with
hinge
Fig.
and
to
Assemble
securely.
sewing
on
factory,
and
OF
MACHINE
assembly
two
hinge
each
machine.
studs
2).
ACCESSORIES
also
with
the
its
rubber
pin.
These
machines
the
top
of
tableboard,
the
rear
bed
nuts
lightly.
head
cloth
plate
grip
back
shaft
should
unpacking,
bed
casting,
each
accessories
parts,
studs,
in
holes
each
machine
the
FRAME
(Fig.
Assemblethe
in
edge
on
against
machine
pad,
parts
are
machine
1).
positioning
the
frame
and
the
underside
be
taken
DO
NOT
lift
gently.
Union
FOR
consisting
and
provided
mounting
bed
are
installed
INSTALLATION
place
Insert
the
rest
Special
have
been
INSTALLATION
of
two
screws
for
is a box
frame,
positioning
essential
in
mounting
machine
the
spring
retaining
mounting,
frame
up
pin,
by
sides,
of
and
the
the
INSTALLING
lift
machine
machine
removed
one
for
them
spring
when
table
frame.
mounting
countersunk
(63474A)
plate
and
rap
board
assemblethe
cone
from
frame
holding
in
rear
of
STANDARD
one
oil
and
setting
tops,
frame
over
(21293
after
the
and
bearings,
out
of
is
sewed
the
packing
thread
drain
prepared
retaining
tighten
eyelet,
miscellaneous
of
cloth
ACCESSORIES--
jar
screw,
up
the
(21393
wood
screw
r i
ght
R)
to
being
sure
locking
knee
press
but
box
by
placing
off,
inspected
box,
one
plate.
and
its
four
isolator
machine.
with
cut-out,
N)
in
through
hingepad;insertround
outside
plate
must
front
there
smartly
nuts
assembly
not
one
and
the
following
eyelet
attachments
clamp
the
is
bind.
attaching
Assemble
containing
spring,
pads
so
machine
left
hinge
of
pan
about
upward
securely.
as
hand
on
carefully
to
the
the
one
and
clips,
that
the
cut-out
pad
head
section,
1/16
inch
with a hammer
shown.
handwheel.
packed.
steps
should
screw,
bed
plate,
upper
All
frame
one
bobbin
knee
and
bed
plate
with
and
tighten
wood
as
shown,
clearance
end
lifter
screw
one
one
is
the
play
TABLE
BOARD
22846Q-16
63476
21393N
J
660
I
21663D
-168
63474
A
6
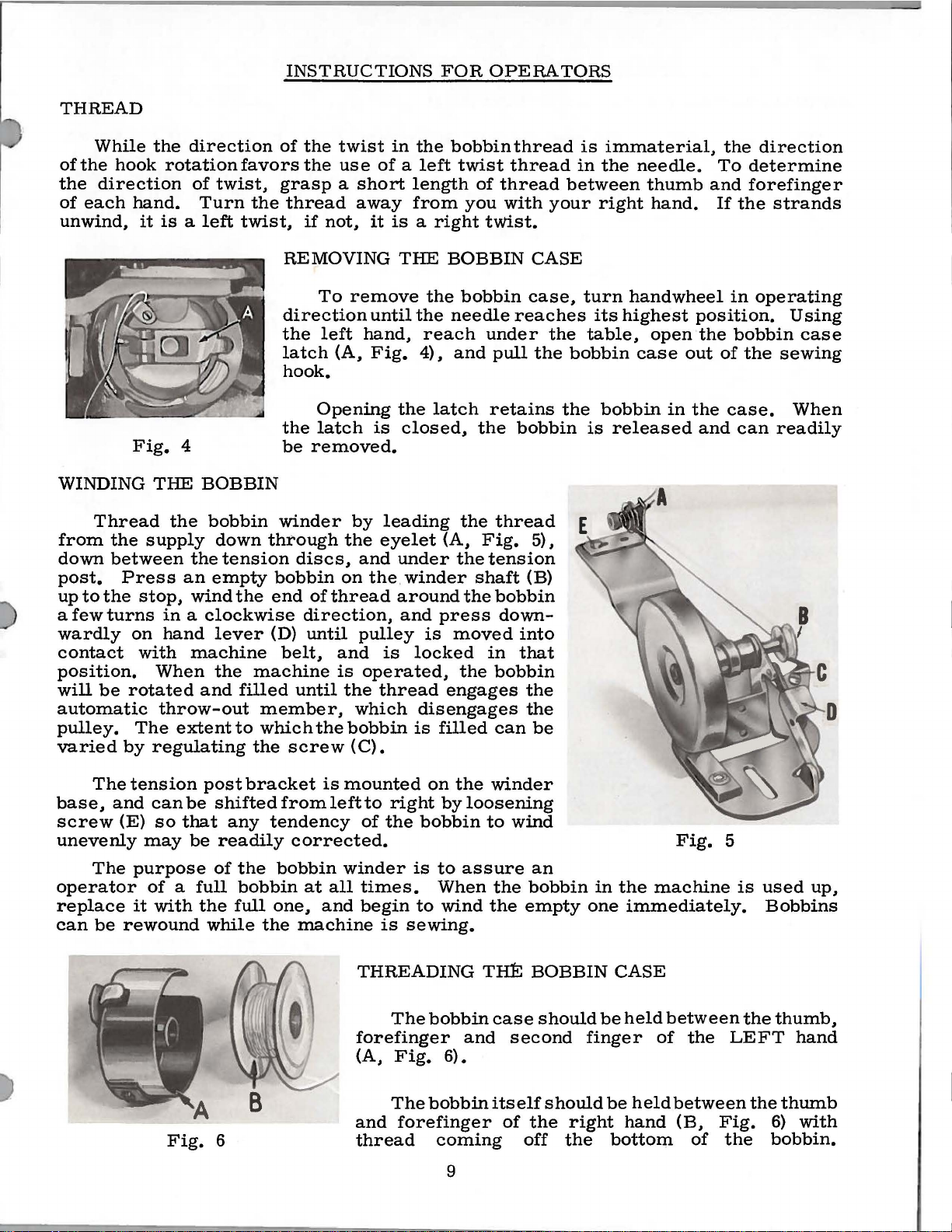
THREAD
INSTRUCTIONS
FOR
OPERA
TORS
While
ofthe
the
of
unwind,
WINDING
from
down
post.
up
a
wardly
contact
position.
will
automatic
pulley.
varied
direction
each
Thread
the
between
to
the
few
turns
be
hook
hand.
Fig.
Press
on
rotated
by
the
direction
rotation
of
twist,
Turn
it
is a left
4
THE
supply
stop,
with
The
regulating
BOBBIN
the
bobbin
down
the
tension
an
empty
wind
in a clockwise
hand
When
throw-out
lever
machine
the
and
extent
of
favors
grasp a short
the
thread
twist,
REMOVING
direction
the
latch
hook.
the
be
winder
through
discs,
bobbin
the
end
(D)
belt,
machine
filled
to
until
member,
which
the
screw
the
twist
the
use
away
if
not,
it
To
remove
until
left
hand,
(A,
Fig.
Opening
latch
removed.
of
direction,
until
the
is
by
the
and
on
the. winder
thread
pulley
and
is
operated,
the
which
bobbin
(C).
in
the
of a left
length
from
is a right
THE
the
the
reach
4),
the
latch
closed,
leading
eyelet
under
around
and
press
is
is
locked
thread
disengages
is
filled
bobbin
twist
of
thread
you
tWist.
BOBBIN
bobbin
needle
under
and
pull
retains
the
the
thread
(A,
Fig.
the
tension
shaft
the
bobbin
down-
moved
in
the
bobbin
engages
can
thread
thread
with
CASE
case,
reaches
the
bobbin
5),
(B)
into
that
the
the
be
is
in
between
your
turn
the
table,
bobbin
the
is
immaterial,
the
needle.
thumb
right
its
bobbin
hand.
handwheel
highest
open
case
released
position.
the
out
in
the
and
the
To
and
If
in
bobbin
of
case.
the
the
can
direction
determine
forefinger
strands
operating
Using
case
sewing
When
readily
The
base,
screw
unevenly
operator
replace
can
and
(E)
The
be
rewound
tension
can
so
may
purpose
of a full
it
with
be
that
be
Fig.
post
shifted
any
readily
of
the
while
6
bracket
from
tendency
the
bobbin
bobbin
full
one,
the
is
mounted
leftto
of
corrected.
winder
at
all
times.
and
begin
machine
THREADING
forefinger
(A,
and
thread
on
right
the
bobbin
is
to
When
to
is
sewing.
The
bobbin
Fig.
The
bobbin
forefinger
coming
the
by
loosening
assure
wind
Tim
and
6).
9
winder
to
wind
the
bobbin
the
empty
BOBBIN
case
second
itself
of
the
off
an
should
should
in
one
finger
right
the
the
machine
immediately.
CASE
be
held
between
of
be
held
between
hand
botto:r:p.
Fig.
the
(B,
of
5
is
the
LEFT
Fig.
the
used
Bobbins
thumb,
hand
the
thumb
6)
bobbin.
up,
with
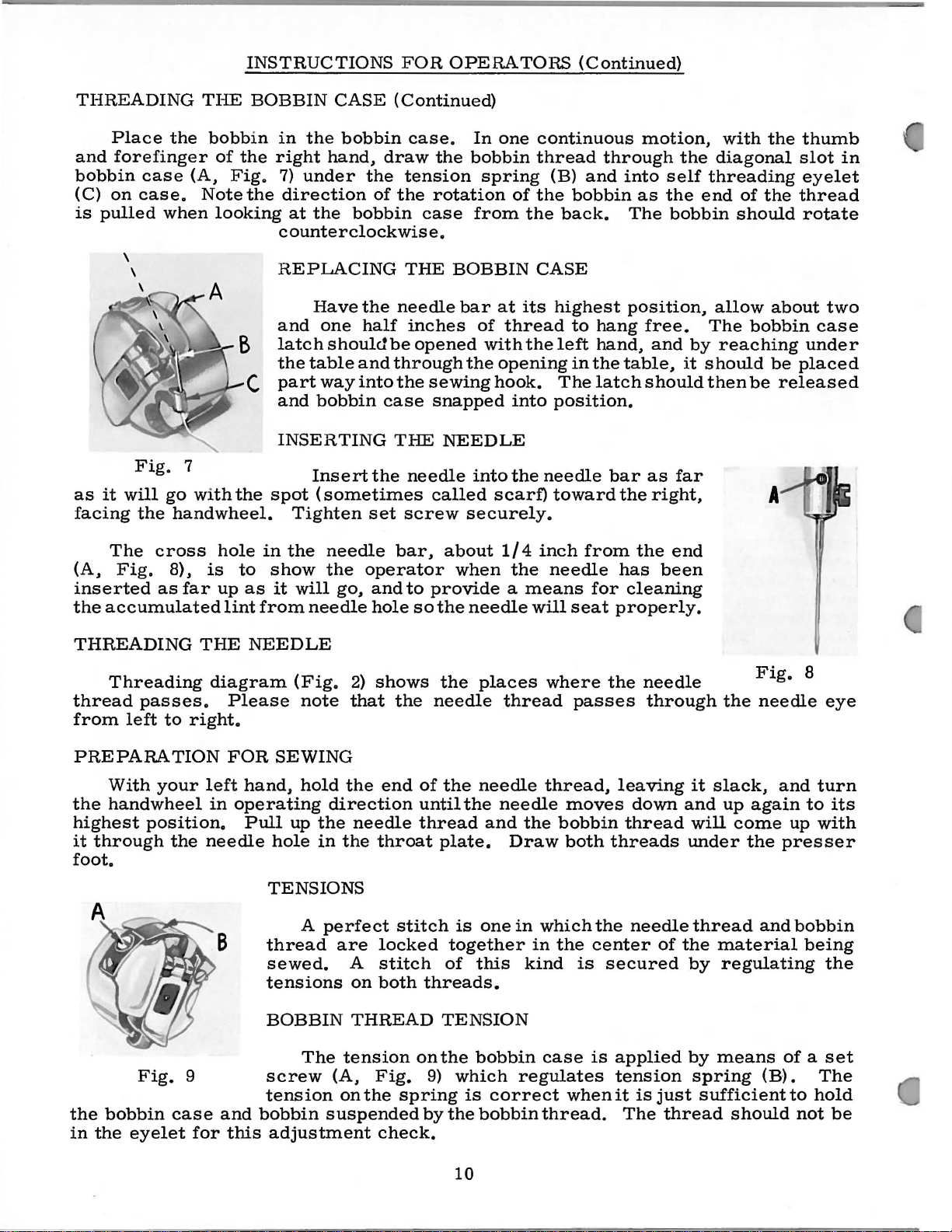
INSTRUCTIONS
FOR
OPERA
TORS
(Continued)
THREADING
Place
and
forefinger
bobbin
(C)
on
is
pulled
as
it
facing
The
(A,
Fig.
inserted
the
accumulated
case
case.
Fig.
will
the
the
when
go
handwheel.
cross
8),
as
THE
(A,
Note
7
with
far
BOBBIN
bobbin
of
the
Fig.
the
looking
C
the
hole
is
to
up
as
lint
CASE
in
the
bobbin
right
7)
counterclockwise.
REPLACING
and
latch
the
part
and
INSERTING
spot
in
show
it
from
hand,
under
direction
at
the
Have
one
should
table
way
bobbin
Insert
(sometimes
Tighten
the
needle
the
will
go,
needle
the
of
bobbin
the
half
and
into
the
set
operator
and
hole
(Continued)
case.
draw
tension
the
case
THE
needle
inches
be
opened
through
the
case
THE
needle
screw
bar,
to
so
In
the
bobbin
rotation
from
BOBBIN
bar
the
sewing
snapped
NEEDLE
into
called
securely.
about
when
provide a means
the
needle
one
spring
of
at
of
thread
with
opening
hook.
into
the
scarf)
1/4
the
continuous
thread
(B)
and
the
bobbin
the
back.
CASE
its
highest
to
the
left
in
The
position.
needle
toward
inch
from
needle
for
will
seat
through
into
as
The
position,
hang
hand,
the
table,
latch
bar
the
the
has
cleaning
properly.
motion,
the
self
the
bobbin
free.
and
by
it
should
as
far
right,
end
been
with
diagonal
threading
end
of
should
allow
The
bobbin
reaching
should
then
be
the
thumb
slot
eyelet
the
thread
rotate
about
under
be
placed
released
A
in
two
case
THREADING
Threading
thread
from
PREPARATION
the
highest
it
through
foot.
the
in
passes.
left
With
handwheel
bobbin
the
your
position.
Fig.
eyelet
to
the
case
right.
9
for
THE
diagram
Please
FOR
left
hand,
in
operating
Pull
needle
B
and
this
NEEDLE
(Fig.
note
SEWING
hold
up
the
hole
TENSIONS
thread
sewed.
tensions
BOBBIN
screw
tension
bobbin
adjustment
in
A
The
2)
shows
that
the
the
end
direction
needle
the
throat
perfect
are
tension
(A,
on
suspended
stitch
locked
A
stitch
on
both
THREAD
Fig.
the
check.
the
needle
of
until
thread
plate.
threads.
TENSION
on
the
9)
spring
by
places
the
needle
the
and
is
one
together
of
this
bobbin
which
is
correct
the
bobbin
where
thread
thread,
needle
the
Draw
in
which
in
kind
case
regulates
thread.
passes
moves
bobbin
both
the
the
center
is
is
when
the
needle
through
leaving
down
thread
threads
needle
of
secured
applied
tension
it
is
just
The
it
and
will
under
thread
the
by
by
spring
sufficient
thread
Fig.
the
needle
slack,
up
material
regulating
means
should
and
again
come
the
and
(B).
8
eye
turn
to
its
up
with
presser
bobbin
being
the
of a set
The
to
hold
not
be
10
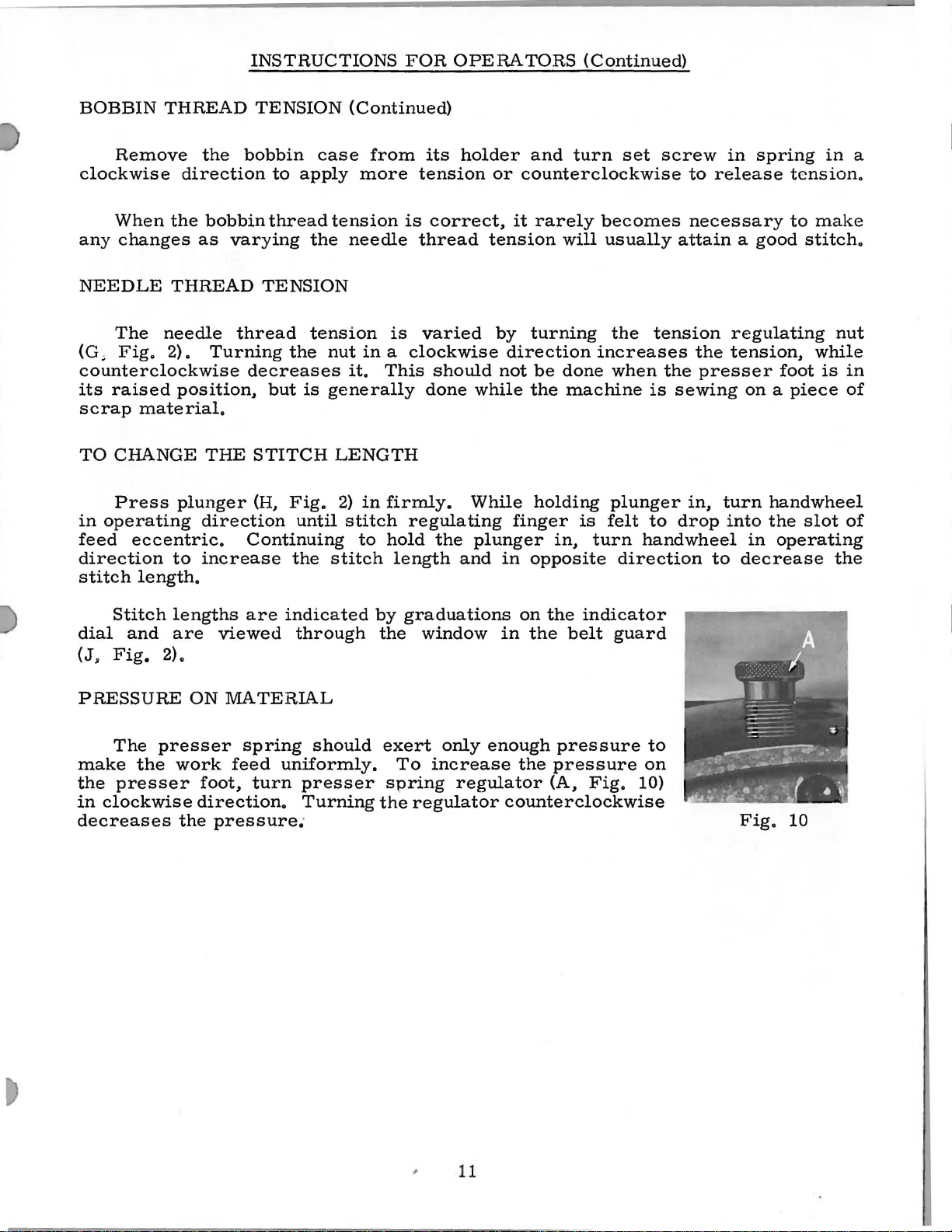
INSTRUCTIONS
FOR
OPERA
TORS
(Continued)
BOBBIN
Remove
clockwise
When
any
NEEDLE
The
(G,
THREAD
the
changes
THREAD
needle
Fig.
2).
the
direction
bobbin
as
Turning
counterclockwise
its
raised
scrap
TO
CHANGE
Press
in
operating
feed
direction
stitch
position,
material.
THE
plunger
direction
eccentric.
to
increase
length.
TENSION
bobbin
to
thread
varying
TENSION
thread
the
decreases
but
STITCH
(H,
Fig.
until
Continuing
the
case
apply
tension
the
tension
nut
is
generally
LENGTH
2)
stitch
(Continued)
from
more
needle
is
is
its
tension
correct,
thread
varied
in a clockwise
it.
This
should
done
in
firmly.
stitch
to
regulating
hold
the
length
holder
or
tension
by
not
while
While
plunger
and
in
and
turn
set
counterclockwise
it
rarely
turning
direction
be
the
holding
finger
in,
opposite
becomes
will
usually
the
increases
done
when
machine
plunger
is
felt
turn
direction
screw
to
release
necessary
attain a good
tension
the
the
presser
is
sewing
in,
to
drop
handwheel
to
in
spring
regulating
tension,
foot
on a piece
turn
handwheel
into
the
in
operating
decrease
in
tension.
to
make
stitch.
nut
while
is
in
of
slot
of
the
a
Stitch
dial
(J~
and
Fig.
2).
PRESSURE
The
presser
make
the
in
the
presser
clockwise
decreases
lengths
are
viewed
ON
work
foot,
direction.
the
pressure.
are
indicated
through
MATERIAL
spring
feed
turn
should
uniformly.
presser
Turning
·
by
graduations
the
window
exert
To
increase
spring
the
regulator
only
enough
regulator
on
the
indicator
in
the
belt
guard
pressure
the
pressure
(A,
Fig.
counterclockwise
to
on
10)
Fig.
10
11
;
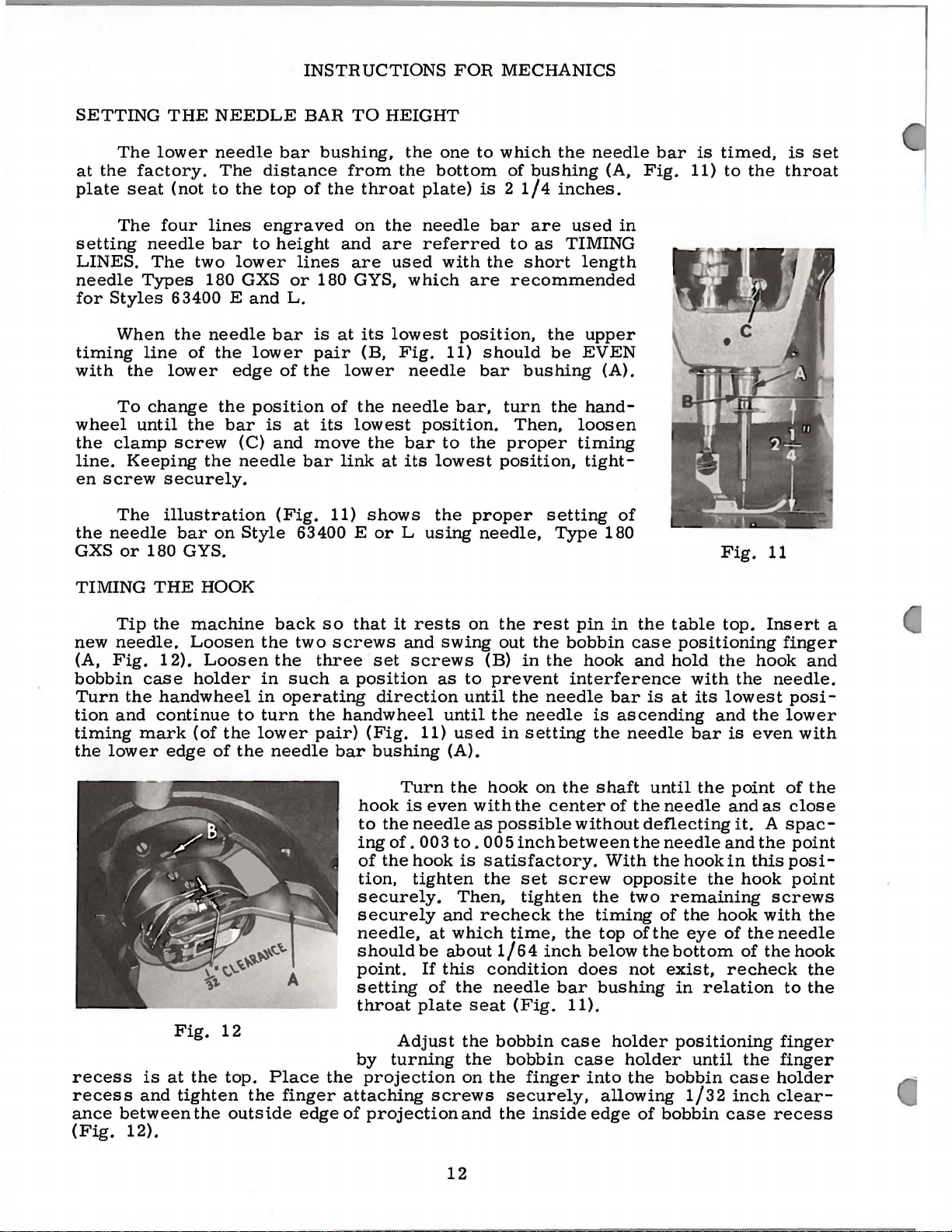
INSTRUCTIONS
FOR
MECHANICS
SETTING
The
at
the
factory.
plate
setting
LINES.
needle
for
timing
with
wheel
the
line.
en
the
GXS
seat
The
Types
Styles
When
the
To
until
clamp
Keeping
screw
The
needle
or
line
180
THE
lower
four
needle
The
lower
change
securely.
illustration
NEEDLE
needle
The
(not
to
lines
bar
two
180 GXS
63400 E and
the
needle
of
the
the
the
screw
the
bar
on
GYS.
the
to
lower
lower
edge
position
bar
(C)
needle
Style
BAR
bar
bushing,
distance
top
of
the
engraved
height
lines
or
180 GYS,
L.
bar
is
pair
of
the
is
at
its
and
move
bar
(Fig.
63400 E
TO
from
and
are
at
lower
of
lowest
link
11)
throat
on
its
(B,
the
the
shows
HEIGHT
the
one
the
bottom
plate)
the
needle
are
referred
used
lowest
needle
at
or L using
which
Fig.
needle
position.
bar
its
lowest
the
with
position,
11)
bar,
to
to
which
of
bushing
is 2 1/4
bar
are
to
the
short
are
recommended
should
bar
bushing
turn
Then,
the
proper
position,
proper
needle,
the
inches.
as
TIMING
the
be
the
setting
Type
needle
(A,
used
length
upper
EVEN
(A).
handloosen
timing
tight-
180
in
of
bar
Fig.
is
11)
timed,
to
the
Fig.
is
throat
11
set
TIMING
Tip
new
needle.
(A,
Fig.
bobbin
Turn
tion
timing
the
recess
recess
ance
(Fig.
the
and
lower
between
12).
THE
the
machine
Loosen
12).
case
mark
is
and
holder
handwheel
continue
(of
edge
Fig.
at
the
tighten
the
HOOK
Loosen
to
the
of
the
12
top.
outside
back
the
the
in
in
turn
lower
needle
Place
the
so
two
three
such a position
operating
the
pair)
the
finger
edge
that
it
screws
set
direction
handwheel
(Fig.
bar
bushing
Turn
hook
to
the
ing
of.
of
the
tion,
securely.
securely
needle,
should
point.
setting
throat
Adjust
by
turning
projection
attaching
of
projection
rests
and
swing
screws
as
until
11)
is
even
needle
003
hook
tighten
and
at
be
If
this
of
plate
screws
on
the
out
(B)
to
prevent
until
the
used
(A).
the
hook
with
as
possible
to.
005
is
satisfactory.
the
Then,
recheck
which
about
condition
the
seat
the
the
on
the
and
1/64
needle
bobbin
the
rest
the
in
the
the
needle
needle
in
setting
on
the
center
inch
between
set
screw
tighten
the
time,
inch
bar
(Fig.
case
bobbin
finger
securely,
inside
pin
in
the
bobbin
hook
interference
the
without
the
does
11).
case
case
and
bar
is
ascending
the
needle
shaft
of
the
the
With
opposite
the
two
timing
top
of
below
not
bushing
holder
holder
into
the
allowing
edge
deflecting
the
of
table
positioning
hold
with
is
at
its
bar
until
the
needle
needle
the
hook
remaining
of
the
the
eye
bottom
exist,
in
positioning
until
bobbin
1/32
bobbin
top.
the
hook
the
lowest
and
the
is
even
point
and
it. A spac-
and
in
this
the
hook
hook
of
the
of
recheck
relation
the
case
inch
case
Insert
finger
needle.
posi-
lower
of
as
close
the
point
posi-
point
screws
with
needle
the
to
finger
finger
holder
clear-
recess
a
and
with
the
the
hook
the
the
12