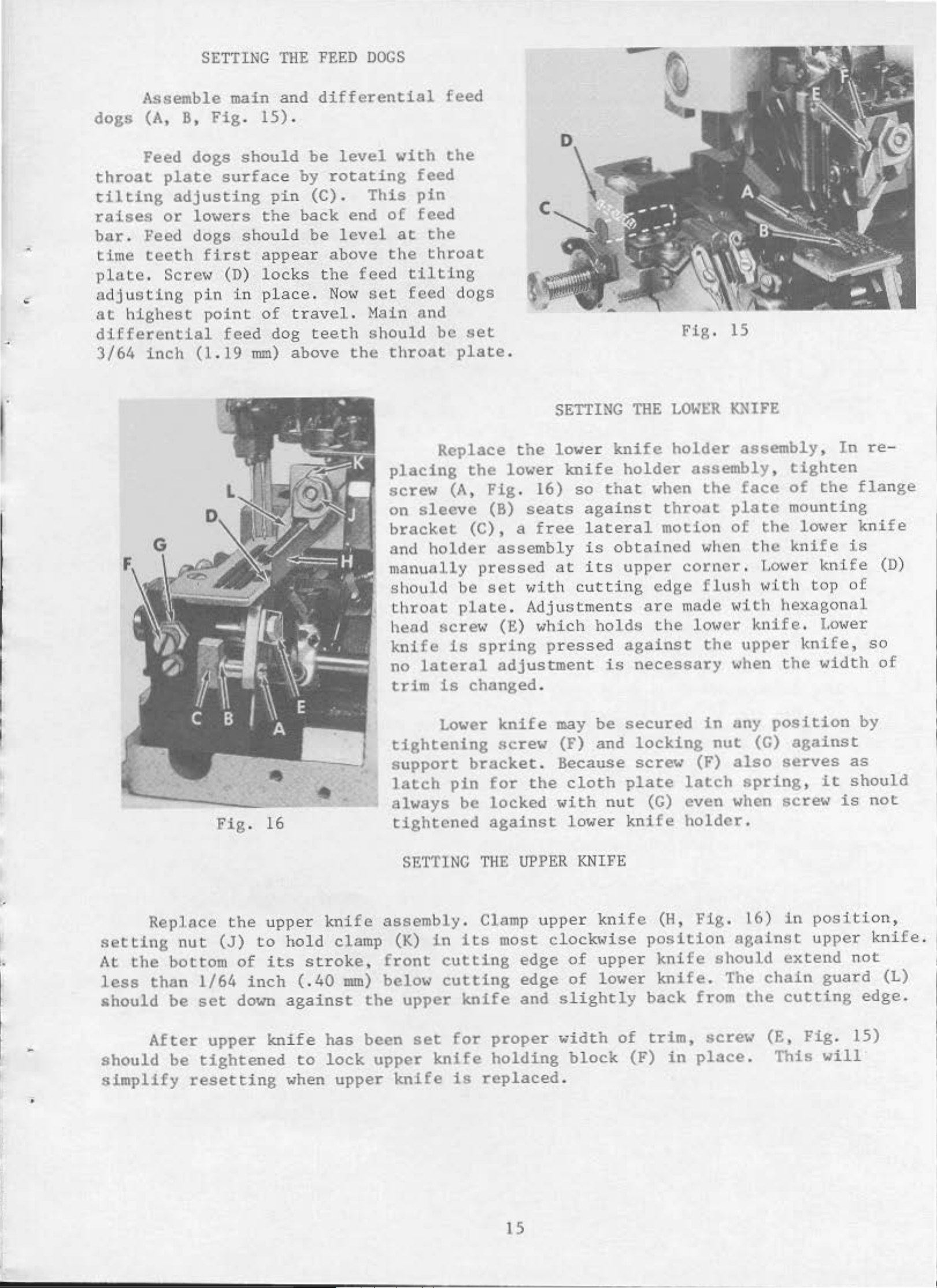
SETTING
THE
FEED
DOGS
Assemble main
dogs
(A,
8,
Feed
throat
tilting
raises
bar.
time
plate.
plate
adjusting
or
Feed dogs
teeth
Screw
adjusting
at
highest
differential
3/64
inch
Fig.
dogs
should
surface
lowers
shoul
first
(D)
pin
in
point
feed
(1.19
and
15).
pin
the
d
appear
l ocks t
plac
of
tra
dog t
mm)
above
differential
be
level
by
rotating
(C).
back
be
This
end
level
above
he
feed
e.
No
1~
set
vel.
eeth
Hain
should
the
with
feed
pin
of
feed
at
the
the
throat
tilting
feed
and
throat
feed
the
dogs
be
plate.
set
C
SETTING
THE
Fig
.
15
LOWER
KNIFE
Fig.
16
Replace
placing
screw
on
(A,
sleeve
bracket
and
holder
manually
should
throat
head
knife
no
lateral
trim
be
plate.
screw
is
is
Lower
tightening
support
latch
always
pin
be
tightened
the
the
(C),
lower
Fig
(B)
. 16)
seats
a
free
assembly
pressed
set vlit
Adjustments
(E)
which
spring
adjustment
changed.
knife
screw
bracket.
for
the
locked
against
lower
knife
so
that
against
lateral
is
at its
h cutt
holds
pressed
may
(F)
be
and
Because
cloth
1•ith
lower
knife
holder
when
throat
motion
obtained
upper
ing
edge
arc
the
against
is
necessary
secured
locking
screw
plate
nut
(G)
knife
holder
assembly,
the
plate
of
when
corner
flush
made
with
lower
the
in
nut
(F)
latch
even
holder.
assembly,
tighten
face
of
mounting
the
the
.
Lo1•er
lower
knife
with
hexagonal
knife.
upper
when
any
(G)
also
knife,
the
position
against
serves
spring,
when
sere<>'
In
the
knife
top
Lower
width
it
is
re-
flange
knife
is
(D)
of
so
of
by
as
should
not
SETTING
Replace
setting
At
the
less
should
nut
bottom
than
be
After
should
simplify
•
be
resetting
the
(J)
1/64
set
upper
upper
to
of
its
inch
down
knife
tightened
knife
hold
clamp
stroke,
( .
40
against
has
to
lock
when
upper
mm)
the
been
assembly.
(K)
front
below
in
cutting
cutting
upper
set
upper
knife
knife
THE
Clamp
its
knife
for
is
replaced
UPPER
upper
most
proper
holding
clock,.ise
edge
edge
and
KN
IFE
knife
of
upper
of
lower
slightly
width
of
block
.
(H,
position
knife
knife.
back
trim,
(F)
in
Fig.
analnst
should
The
from
screw
place.
16)
chain
the
(E,
in
position,
upper
extend
cutting
Fig.
This
not
guard
edge.
15)
will
knife.
(L)
15
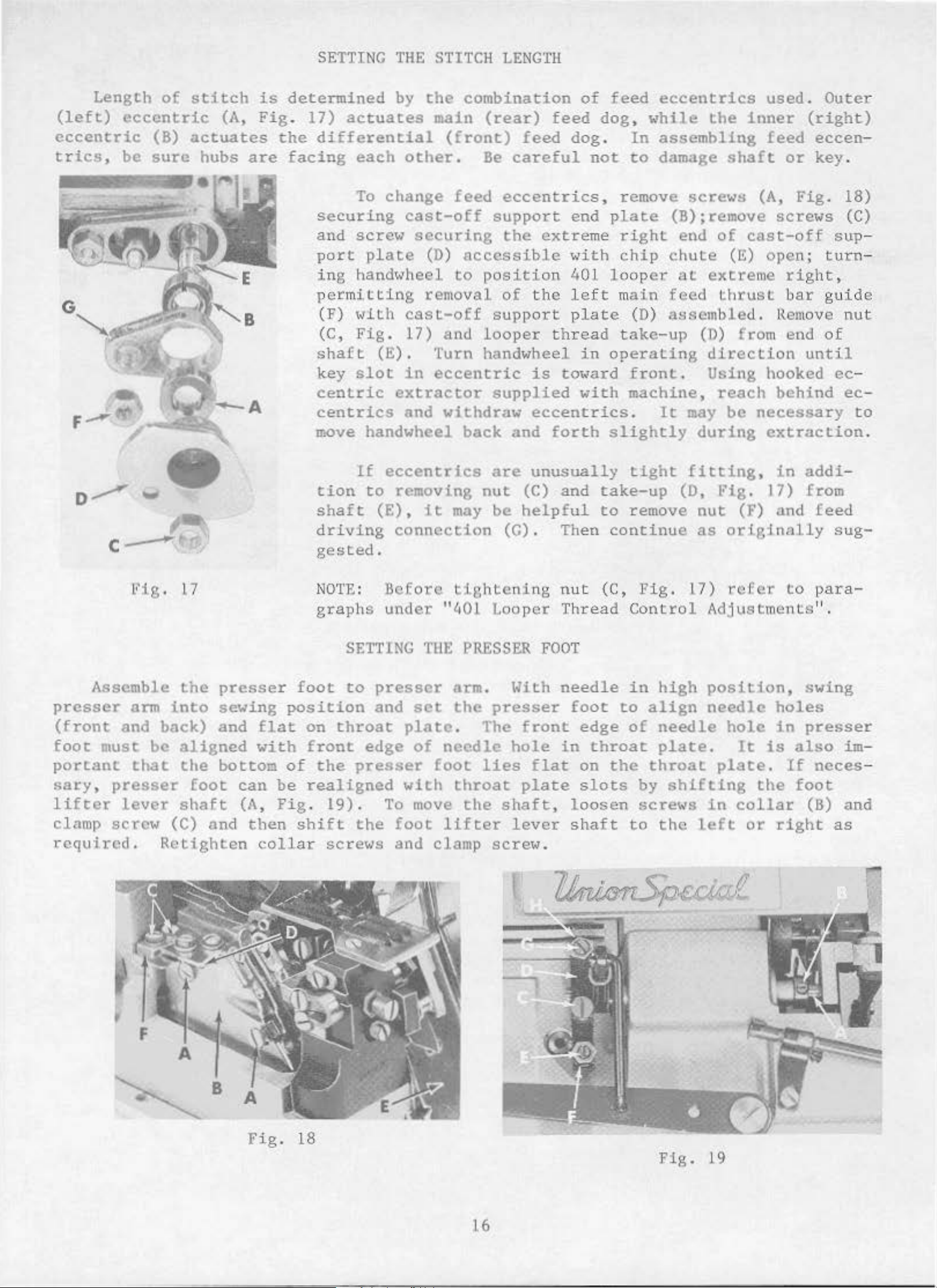
SETTING
THE
STITCH
LENGTH
Length
(left)
eccentric
eccentric
trics,
be
of
(B)
sure
stitch
(A,
actuates
hubs
are
is
determined
Fig. 17)
the
differential
facing
securing
and
port
ing
permitting
(F)
(C,
shaft
key
centric
centrics
move handwheel
by
actuates
each
To
other.
change
cast-off
screw
securing
plate
handwheel
IJith
Fig.
slot
cast-off
17)
(E).
in
extractor
and
the
(D)
removal
combination
main
(rear)
(front)
Be
feed
eccentrics
support
the
accessible
to
positio
of
supp
and
looper
feed
feed
careful
extre
n 401 l oop
the
ort
t h
dog.
end
w
left
plate
read
Turn handwheel i n
eccentric
is
tot<ard
supplied
withdraw
back
eccentrics
and
forth
of
feed
dog,
not
eccentrics
while
In
assembling
to
damage
the
shaft
, remove screwH (A,
plate
me
right
ith
chip
m
take-up
operating
with
slightly
ain
(D)
front.
machine,
.
(B); remove
end
chute
er
at
feed
a~semb!ed.
of
(E)
extreme
thrust
(D)
direction
Using hooked
reach
It
may
be
during
used.
inner
(right)
feed
or
Fig.
screws
cast-off
open;
right
bar
Remove
from end
until
behind
necessary
extraction.
Outer
eccen
key.
18)
(C)
sup
turn
,
guide
nut
of
ec
-
ec
-
-
-
-
to
D__.........
c-
Assemble
presser
(front
foot
portant
sary,
lifter
clamp
required.
and
must
presser
lever
screw
w
Fig
. 17
arm
into
back)
be
that
(C)
Retighten
the
presser
sewing
and
aligned
the
botton
foot
shaft
and
flat
with
can
(A,
then
collar
tion
shaft
driving
gested
NOTE:
graphs
SETTING
foot
to
position
on
throat
front
of
the
be
realigned
presser
Fig. 19).
shift
screws
If
eccentrics
to
removing
(E),
connection
.
Before
under
presser
and
plate.
edge
with
To
the
foot
and
it
"401
THE
set
of
needle
foot
move
lifter
clamp
may
are
nut
be
unusually
(C)
helpful
(G)
. Then
tightening
Lo
oper Thread
PRESSER
FOOT
arm. With
the
presser
The
front
hole
lies
throat
the
flat
plate
shaft
lever
screw
.
and
nut
needle
foot
edge
in
throat
on
slots
,
loosen
shaft
tight
take-up
to
remove
continue
(C,
l'ig.
Contro
in
high
to
align
of
needle
plate.
the
throat
by
screws
to
fitting,
(D,
nut
as
17)
Fig.
(F)
originally
rc
l Adjustments
position,
needle
hole
It
plate.
shifting
ln
collar
the
left
in
17) from
and
Eer co
holes
in
is
also
If
the
or
foot
right
addi-
feed
sug-
para".
swing
presser
im
-
neces
-
(6) and
as
F
A
~
B
Fig
. 18
16
Pig.
19
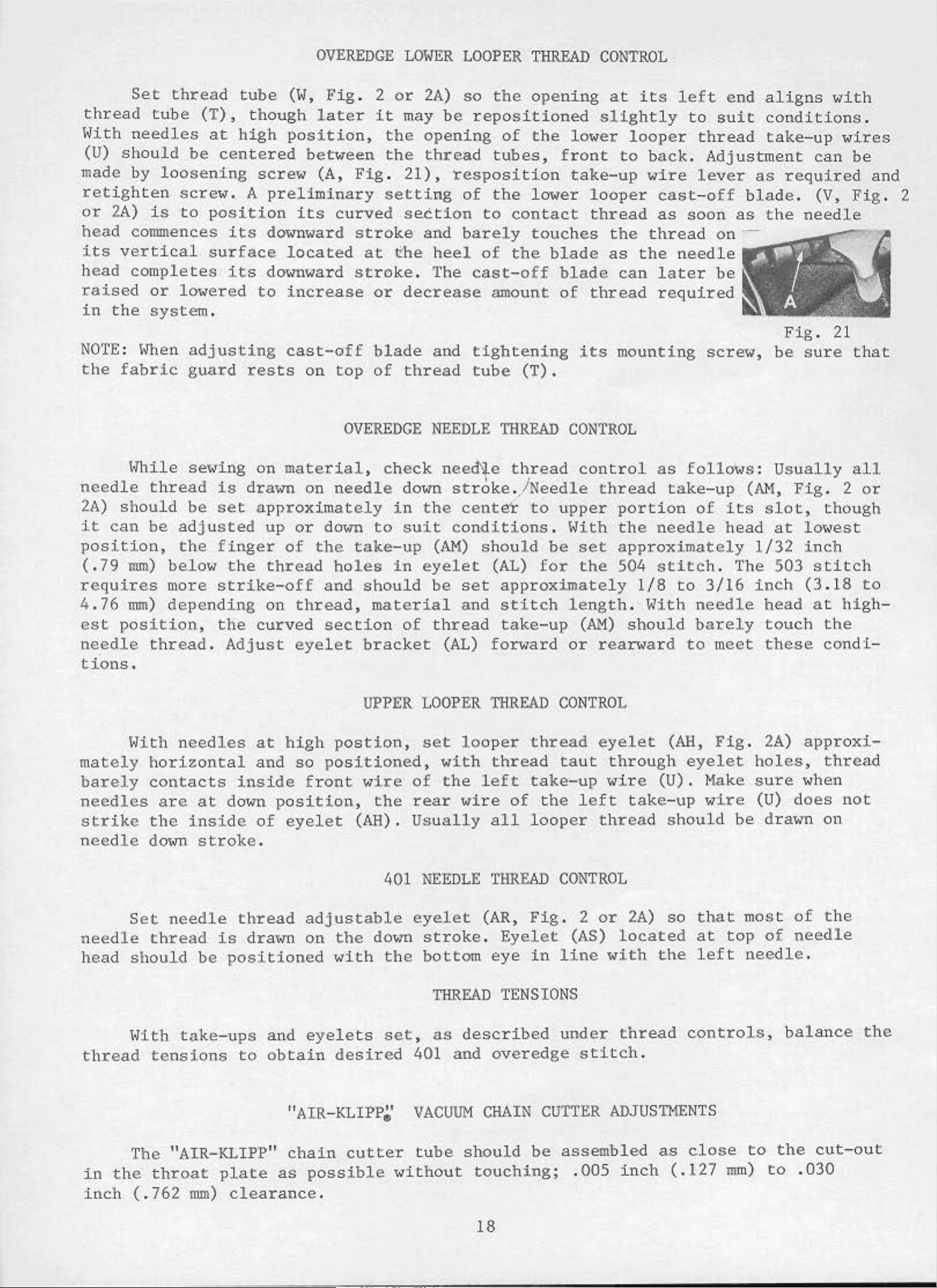
OVEREDGE
LOlmR
LOOPER
THREAD
CONTROL
·
thread
lhth
(U)
should
made
ret
ighten
or
2A)
Set
needles
by
thread
tube
(T
at
be
loosening
screw.
is
to
position
head commences
its verti
head
completes its
raised
in
the syst
NOTE
the
: l,lhen
fabric
or
cal
lm
<ered
surface
em.
adjusting
guard
tube
),
though
high
centered
screw
A
preliminary
its
downward
downward
to
rests
(14,
Fig.
late
position,
between
(A,
its
Fig.
curved section
stroke
located
stroke.
increase
cast-off
on
top
OVEREDGE NEEDLE
2
or
r
it
the
the
setting
at trhe
or
blade
of
2A)
may
so
be
openiQg
thread
21),
resposition
of
and
barely
heel
T
he
decrease
and
thread
the
opening
repositioned
of
the
tubes,
lower
front
take-up
the
to
lm~er
contact
touches
of
the
cast-off
amount
blade
blade
of
tightening
tube
(T).
THREAD
CONTROL
at
slightly
l
ooper
thread
the
as
thread
its
mounting
its
looper
to
back.
wire
cast-off
as
thread
the
can
later
required
left
to
end
suit
thread
Adjustment
lever
soon
on
as
·-
needle
be
screw,
aligns
conditions.
take-up
as
required
blade.
the
needle
Fig.
be
sure
with
can
(V,
21
wires
be
and
Fig.
that
2
l<hile
needle
2A)
it
should
can
position,
(.79
mm)
requires
4.76
est
mm)
position,
needle
tions.
Hith
mately
barely
needles
strike
needle
se~~ing
thread
be adj
the
below
more
is
be
set
usted
finger
the
strike-off
depending
the
thread.
Adjust
needles
horizontal
contacts
ar
e
at
down
the
dmm
inside
stroke.
on
material
drawn on
approxi
up
or
of
thread
on t
curved
eyelet
at
high
and
so
inside
position,
of
eyelet
,
needle
mately
down
the
take
holes
and
hread,
should
material
section
bracket
UPPER
postion,
positioned,
front
wire
(AH). Us
check need'i).e
to
down
in
suit
-up
in
stroke.
the
centet
conditions.
(AH)
eyelet
be
set
and
of
thread
(AL)
LOOPER
set
loo
with
of
th
e
the
rear
wire
ually
thread
' '
/Needle
to
upper
l'ith
should
(AL)
be
for
set
approximately
stitch
length.
take-up
fon1ard
THREAD
per
thread
thread
left
take-up
of
all
looper
or
CONTROL
taut
the
control
thread
portion
the
approximately
the
(AH)
504
should
rearward
eyelet
through
wire
left
tak
thread
as
follol<s:
take-up
of
needle
stitch
1/8
to
With
needle
barely
to
(AH,
eyelet
(U). Hake
e- up
should
(Al'l,
its
slot,
head
1/32
. The 503
3/16
inch
head
touch
meet
these
Fig. 2A)
holes,
sure
wire
(U)
be
drawn on
Usually
Fig.
all
2
though
at lowest
inch
stitch
(3.18
a t
high-
the
condi
approxi-
thread
'<hen
does
not
or
to
-
Set needle
needle
head
should
t•ith
thread
The "
in
the
inch
thread
tensions
AIR
throat
(.762
be
take
-KLIPP"
mm)
thread
is
drawn
positioned
-up
s and
to
obtain
"A IR-
chain
plate
as
clearance
401
adjustable
on
the
with
eyelets
do•10
the
set,
desired
KLIPP~'
cutter
possible
.
NE
EDLE tHREAD
eyelet
stroke.
bottom
THREAD
as
401 and
VACUUM
tube
"ithout
(AR,
Fig
Eyelet
eye
in
TENSIONS
described
overedge stitch
CHAIN CU
should
touch
be
ing;
CONTROL
. 2
line
under
TTER
or
(AS)
2A)
located
with
thread
ADJUSTIIENTS
assembled
. 005
inch
so
the
.
as
( .127 m
that
at
left
most
top
needle.
controls,
close
to
m)
of
of
needle
balance
the
to
. 030
the
the
cut-out
18
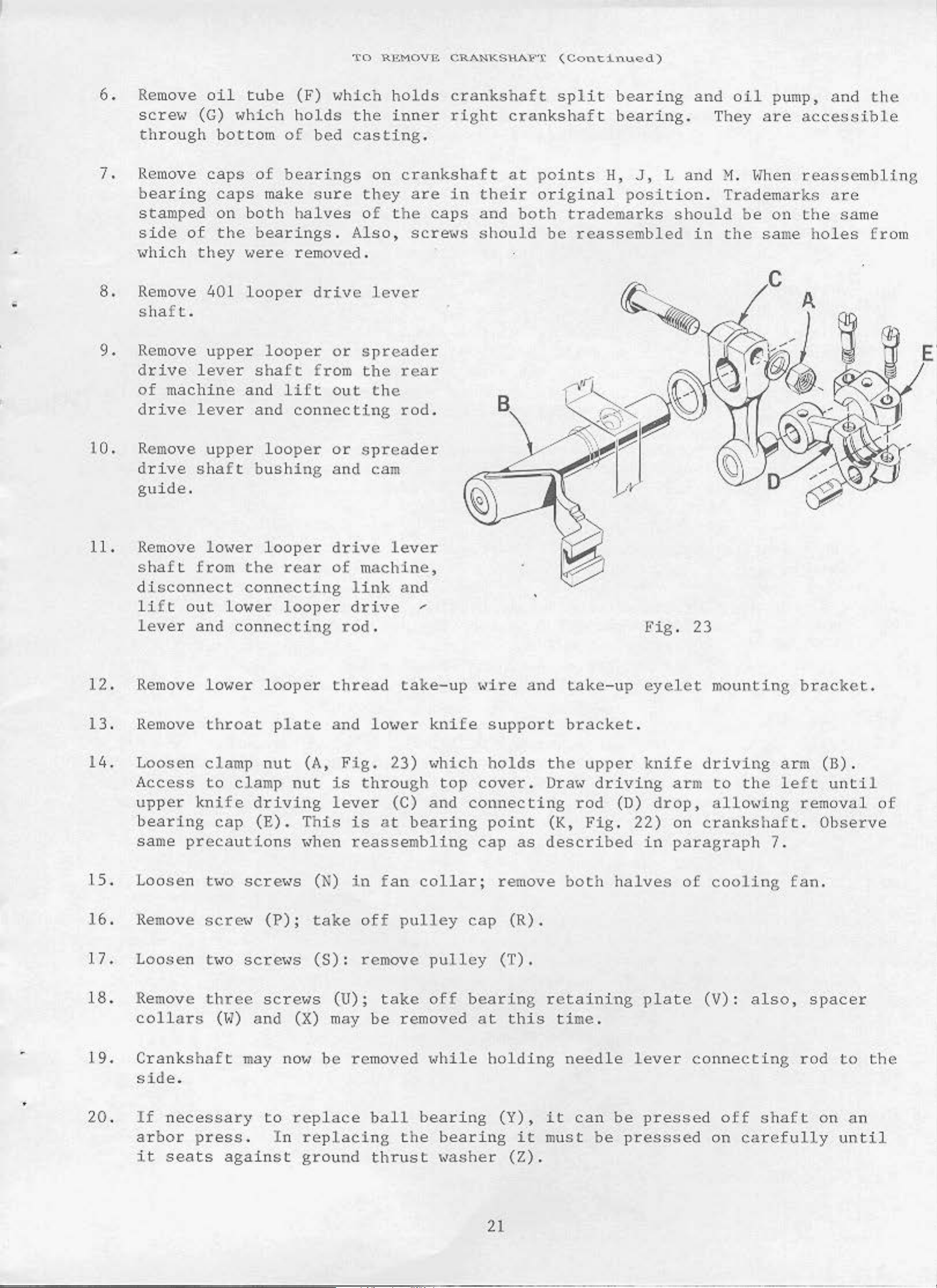
T.O
REMOV'Jl. CRANl<.Sl\Al?'.t ( Con
l:.
i.nued)
6.
7.
8.
9.
Remove
scre\·1
thro
ugh
Remove
bearing
stamped
side
of
"hich
Remove
shaft.
Remove
drive
of
machine
drive
oil
(G)
caps
they
401
tube
which
bottom
of
caps
on
the
make s
both
bearings
'1ere
looper
of
bearings
upper looper
lever
lever
sha£ t fr
and
lift
and
(F)
holds
~1hich
the
bed
casting.
on
ure they
halves
.
of
Also
removed .
drive
or
om
out
lever
spreade
the
the
connecting
holds
inner
cra
are
the
crankshaft
right
nksh
in
caps
, screx<s
·r
rear
rod
.
aft
their
and
should
split
crankshaft
at
points
original
both
trademarks
bt'
reassembled
bearing
bearing.
H,
J,
p
osition.
and
Land
should
in
oil
They a·
~1.
pump,
re
~lhen
Trademarks
be
on
the
same holes
and
the
accessible
reasse
mbling
are
the
same
fro
m
E
1
0.
11.
12.
13.
1
4.
Remove
drive
upper
shaft
guide.
Remove
shaft
l01~er
from
disconnect
li
ft
out
lever
Remove
Remove
Loosen
Access
upper
and
lower
throat
clamp
to
knife
bearing
sa
me
precautions
looper
bushing
looper
the
connecting
lower
connecting
looper
plate
nut
clamp
drivi
cap
(E).
or
and
drive
rear
of
looper
thread
and
(A,
nut
ng
is
lever
This
"hen
sp
reader
cam
lever
machine,
link
drive
and
~
rod.
take-up
l01•er
Fig.
23)
"h
through
is
(C)
at
and
bearing
reassembling
knife
ich
top
~~ire
and
support
holds
cover.
the
Dra"
connecting
point
cap
(K,
as
described
take
-up eyelet
bracket.
upper
driving
rod
(D)
Fig.
Fig
knife
drop,
2
2)
in
.
23
mounting
driving
arm
to
the
allo,,•ing
on
crankshaft
paragraph
bracket.
arm
left
removal
7 .
(B).
until
.
Observe
of
.1.5.
16.
17.
Loose
n
Remove
Loosen
18. Remove
19.
20.
coll
Cr
side.
If
arbor
it
ars
ankshaft
necessary
seats
t"o
sere«
tHo
three
(~
I)
press.
against
screHs
(
P);
scre1•s
scre'ls
and
(X) may
may no"'
to
replace
In
replaci
ground
(N)
take
(S):
(U);
be
in
fan
off
collar;
pulley
remove pulley
be
re
moved
ball
ng
thrust
take
off bearing
removed
1~hile
bearing
the
bearing
~~asher
remove
cap
(T).
at
holding
(Y),
(R).
this
it
(Z).
both
retaining
tim
e .
needle
it
can
must
be
halves
plate
lever
be
pressed
press
of
cooling
(V):
connecting
off
sed on
fan
also,
r od
shaft
carefully
.
spacer
to
on
an
until
the
21
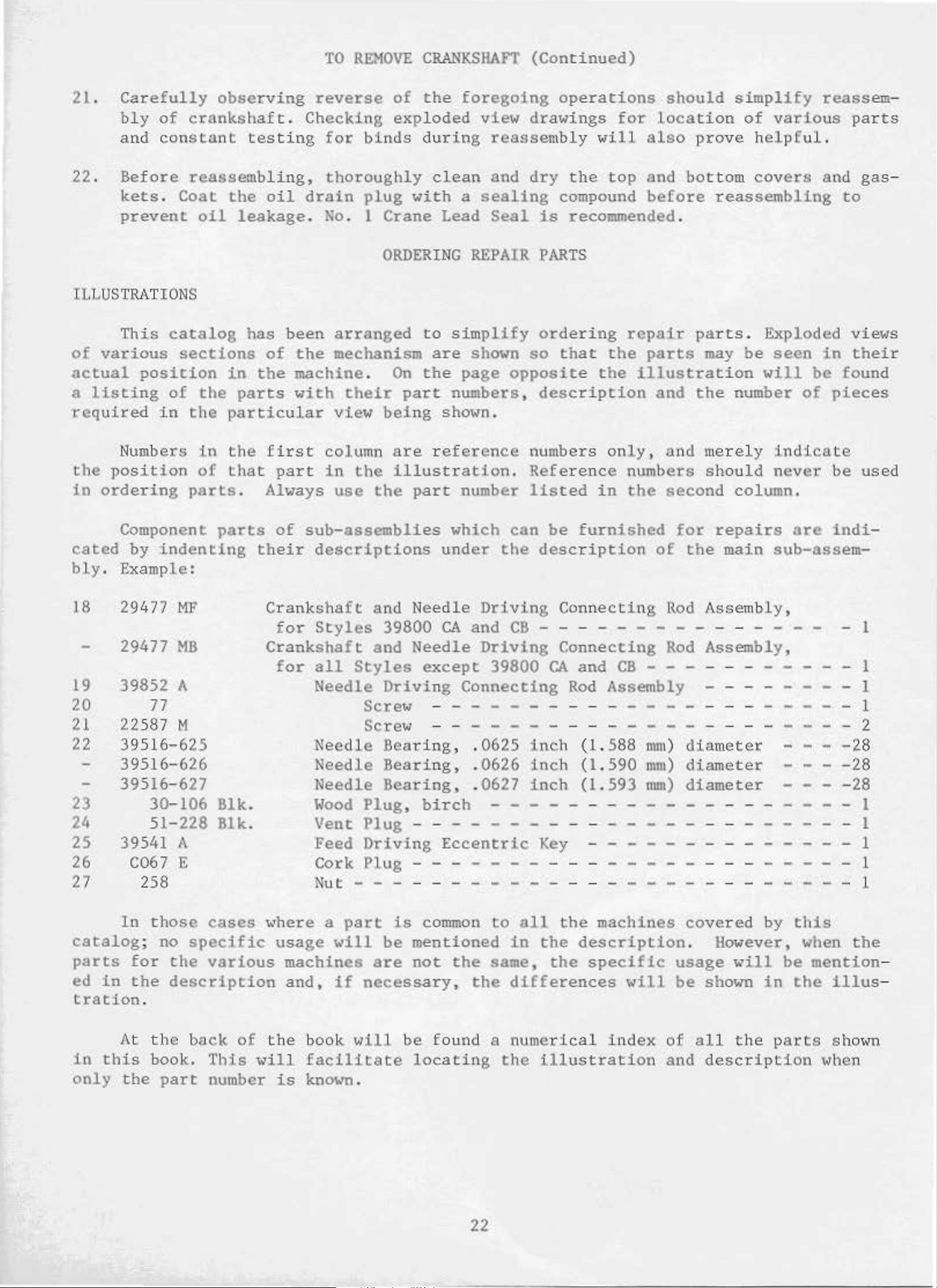
21
22
.
Carefully
bly
and
.
Before
kets.
prevent
observing
of
cranksha
con
stant
reassembling,
Coat
oil
the
leakage
ft.
testing
oil
TO
REMOVE
reverse
Ch
ecking
for bin
thoroughly
drain
.
No
plug
. 1 Crane Lead
CRANKSHAFT
of
the
exploded
ds
durin
with
foregoing
g
clean
a
(Con
operations
view draw
reassembly
and
sealing
Seal
dry
is
tinu
ings
the
compound
recommended.
wi
ed)
for
ll
top
loca
also
and
before
should
tion
prove
bo
ttom
reassembling
simplify
of
various
help
covers
ful
reassem-
parts
.
and
gas
to
-
tL
LUSTRATIONS
This catalog
of
various
actual
listing
a
req
uired
the
in
ordering
cated
bly
. E
position
in
Numbe
position
Component
by
indenting
xample:
sections
of
the
the
rs
in
of
parts
parts
has
in
parts
par
the
tha
. Always
been
of
the
ticu
first
t p
art
of
their
the
machine
with
lar
ORDER
arranged
mechanism
.
their
view
column
in
use
sub-assemblies
description
being
the
the
to
On
the
part
are reference
illustration.
pa
s
ING
are
rt
REPAIR
sim
plify
shown
page
numbers ,
shown.
number
which
under
PAR
or
dering
so
that
opposite
descr
numbers onl
Ref
erenc
lis
ted in
can
the
be
description
TS
repair
the
the
ipti
furnished
on
e numbers
the
parts.
parts
illustration
and
y,
and
second
of
the
for
the
may
merely
should
repairs
Exploded views
be
seen
will
number
indica
never
column.
main
sub-assem-
be
of
are
in
found
piec
te
be
indi-
thei
es
used
r
18
19
20
21
22
23
24
25
26
27
catalog
parts
ed
tration
29477
29477
39852 A
22587 M
39516-62 5
39516-626
39516-627
39541
In
in
77
30-106
51
C067
258
th
; no
for
the
.
MF
MB
Blk
.
- 228
Blk
.
A
E
ose
the
description
cases "'he
specific
various
Cranksha
for
Crankshaft
for all
re a
usage
machines
and,
ft
Styles
Needle
Needle Bea
Needle
Needle
Yood
Vent
Feed
Cork
Nut - - - - - - - - - - - - - - - - - - - - 1
part
will
if
and
and
Styles
Scre
Scre
Plug, birch
Plug
Drivi
Plug
are
necessa
Needle
39800
Driving
w - - - - - - - - - - - - - - - - - - - - 1
w - - - - - - - - - - - - - - - - - - - - 2
Bear
Beari
is
be
CA
Needle
ex
cept
ring,
ing,
ng,
- - - - - - - - - - - - - - - - - - - - - - - 1
ng E
common
mentioned
not
ry,
Driving
and
CB
Driving
39800
Connecting
. 0625 i
.06
26 i
. 0627
- - - - - - - - - - - - - 1
ccentric
- - - - - - - - - - - - - - - - - - - 1
to
all
in
the
same,
the
differences
Connecting Rod
- - - - - - - - - - - - - - - - 1
Connecting
CA
and
Rod
nch
nch
inch
Key
the
(1.588
(1.590
(1.593
- - - - - - - - 1
the
description
the
specific
CB
Assembly - - - - - - 1
machines
will
Rod
- - - - - - - - - 1
mm)
mm)
mm)
Assembly,
Assembly,
dia
meter
diameter
dia
met
er
covere
. However, when
usage
be
shown
d by
will
---
in
-
--
- - -
this
be
the
-28
-28
-28
mention
illus
the
-
-
At
the back
in
this
only
the
book.
part
of
the
This will
number
is
book
facilitate
known.
will
be
locating
found a
22
num
the
eri
ill
cal
ustrati
ind
ex
on
of
and
all
the
descript
part
ion
s
sho
when
'm
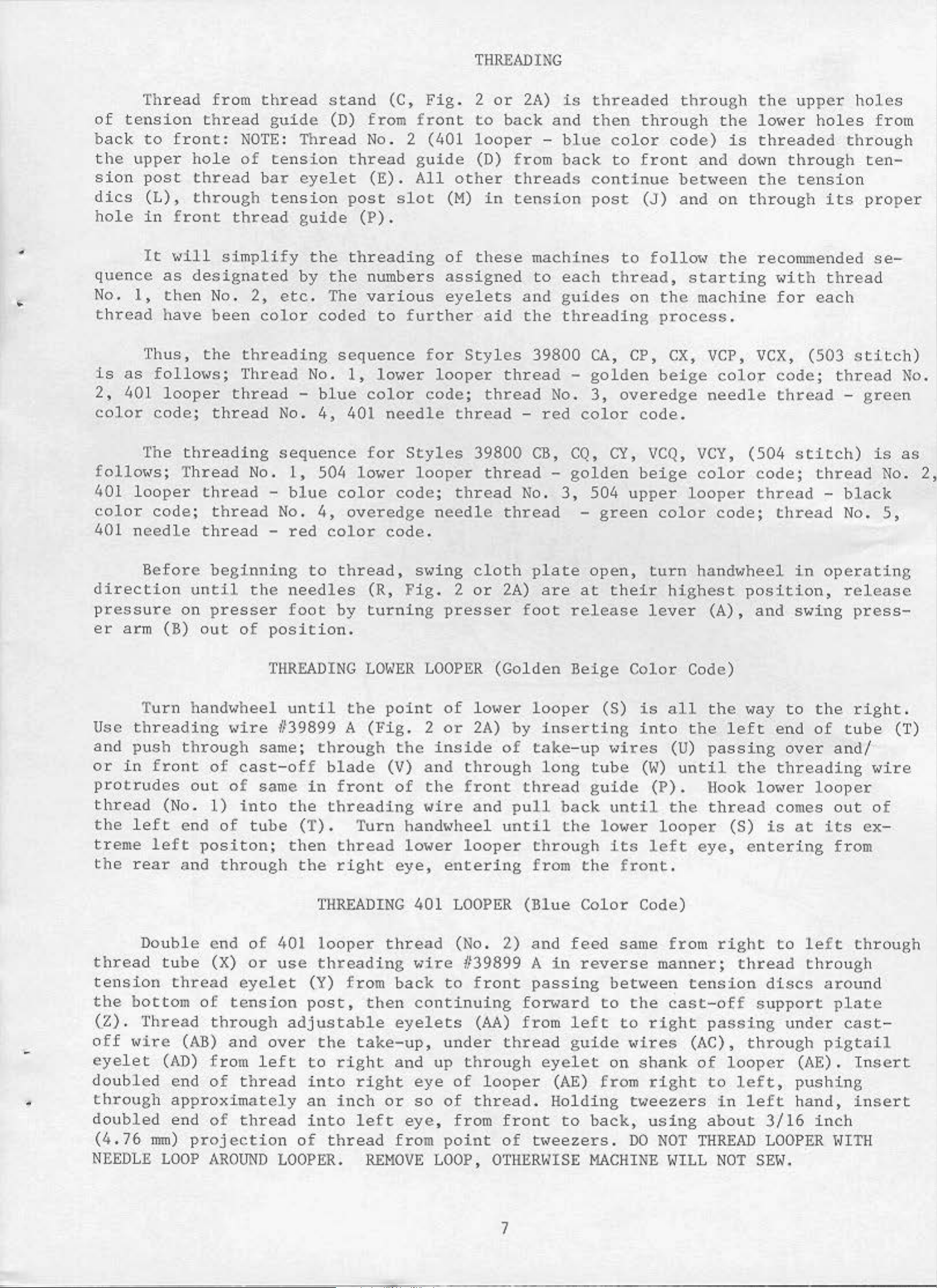
THREADING
Thread
of
tension
back to
the
sion
dies
hole
upper
post
(L),
in
It
quence
No.
1,
thread
Thus,
is
as
follm<s;
2,
401
color
code;
from
thread
front:
hole
thread
through
front
\dll
as
designated
then
have
No.
been
the
looper
thread
thread
guide
NOTE: Thread
of
tension
bar
eyelet
tension
thread
simplify
guide
the
by
2,
etc.
color
threading
Thr ead
thread
No.
-
No.
stand
(D)
from
No. 2 (401
thread
(E).
post
(P
threading
the
The
numbers
various
coded
sequence
1,
blue
4,
color
401
(C,
Fig.
front
guide
All
slot
(M)
).
of
assigned
eyelets
to
further
for
lo\<er
looper
code;
needle thr
2
to
lo
(D)
other
in
these
aid
Styles
thread
ead
or
2A)
back
oper
fro
and
-
m
threads
tension
machines
to
and
the threadi
39800
thread
No.
-
red
is
threaded
then
blue
color
back
continue
post
each
guides
CA,
-
golden
3,
color
through
code)
to
front
(J)
to
follo"
thread,
on
the
ng
process.
CP,
CX,
beige
overedge
code.
through
the
is
and
dmm
bet"een
and
on
the
starting
machine
VCP,
colo:r
needle
the
lo"er
upper
holes
threaded
through
the
throug
tension
h
its
recommended
"ith
for
VCX,
code;
thread
each
(503
thread
thread
holes
from
through
ten-
proper
se-
stitch
No.
-
green
)
The
follo"s
401
color
401
; T
looper
code;
needle
Before
direction
pressure
er
arm (B)
Tu
rn
Use
and
or
threading
push
in
front
protrudes
thread
the
(No.
left
treme left
the
rear
threading
hread
No.
thread
thread
thread
beginning
until
on
out
pre
the
sser
of
handwheel
wire
through
of
cast-off bla
out
end
1)
of
of
in
tube
positon;
and
through
sequence
1,
504 lo\<er
-
blue
No. 4,
-
red
color
to
color
ov
thread,
needles
foot
by
position.
THREADING
until
/139899
same;
same
to
the
in
A
through
front
threading
(T) . Turn
then
the
thread
right
for
eredge
code.
(R,
turning
LOWER
the
point
(Fig.
de
(V)
Styles
looper
code;
thread
needle
S\<ing
Fig
. 2
presser foot
LOOPER
of
2
or
the
of
inside
and
the
through
front
1<ire
hand,.heel
lower
eye,
looper
entering
39800
thread-
thread
cloth
or
2A)
(Golden
lower
2A)
by
of
and
pull
until
CB,
CQ,
golden
No. 3,
plate
are
release
Beige
loop
er
inserting
take
- up
long
thread
back
the
through
from
CY,
504 up
-
green
open,
at
their
(S)
wires
tube
guide
until
lower
its
the
VCQ,
beige
per
turn
lever
Color
is
into
(W)
(P).
left
front
VCY,
color
looper
color
hand>~heel
highest
Cod
all
the
(U)
until
the
looper
eye, entering
.
(504
code;
thread
code;
position,
(A),
and
e)
the
way
left
passing
the
Hook
lo,.er
thread
(S)
stitch)
thread
-
thread
in
operating
swing
to
the
end
of
over
threading
looper
comes
is
at
its
is
black
No.
release
press-
right
tube
and/
wire
out
of
ex
from
as
No.
5,
(T)
-
2,
.
THREADING
Double end
threa
tension
the
(Z)
d
tube
bottom
.
Thread
(X)
thread
of
through
off 1<ire (AB)
eye
let
doubled
•
through
doubled
(
4.
76
NEEDLE
(AD)
end
f rom
of
approximately
end
mm)
LOOP
of
projection
AROUND
of
401
or
use
eyelet
tension
and
over
left
thread
thread
LOOPER.
looper
threading
(Y)
post,
from
then
adjustable
the
to
into
an
into
of
take
right
right
inch
left
thread
REHOVE
401
thread
"ire
back
continuing
eyelets
-up,
and
up
eye
or
so
ey
e, from
fro
m
LOOP,
LOOPER
(No.
1139899
to
front
(AA)
under
through
of
looper
of
thread.
point
OTHERWISE
(Blue
2)
and
A
passing
fon>ard
from
thread
eyelet
front
of
tt<eezers.
7
Color
feed
in
reverse
between
to
left
guide
on
(AE)
fro
Holding
to
back,
~lACHI
Code)
same
fro
m
manner;
tension
the
to
cast-off
right
passin
1<ires (AC),
shank
m
right
of
to
tweezers
using
DO
NE
NOT
WILL
about
THREAD
right
thread
through
looper
left,
in
left
NOT
to
left
through
discs
around
support
g
under
pigtail
(AE).
pushing
hand,
3/16
inch
LOOPER
SEI~.
through
plate
cast
Insert
insert
IHTH
-
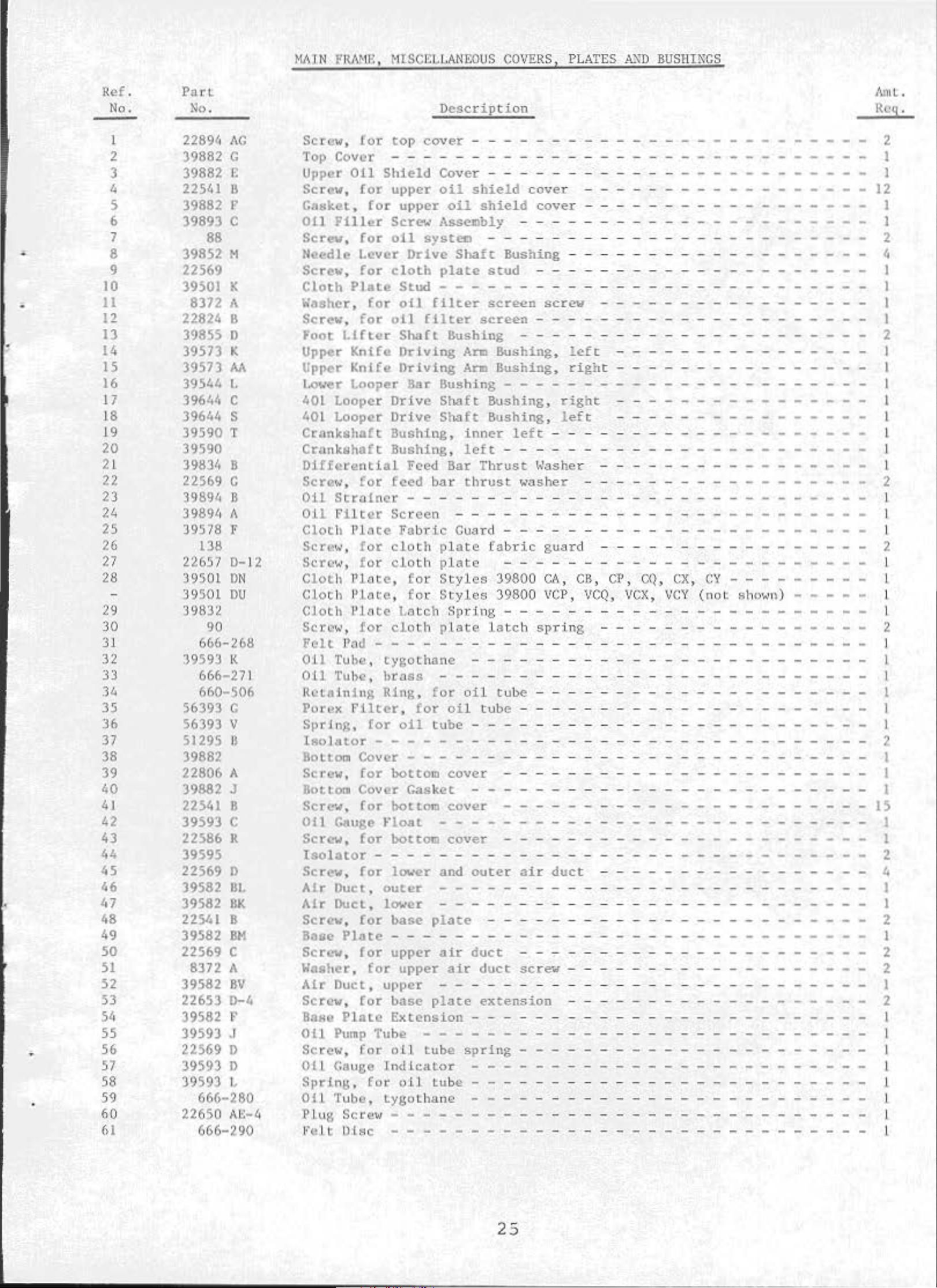
f1A1
N FIWIIJ,
~1lSCELt.ANEO
U S
COVER
S,
PLATES
A~D
BUSlllNCS
Ref .
No.
l
2
3
4
s
6
7
8
9
10
II
12
13
14
IS
16
17
18
19
20
21
22
23
24
25
26
27
28
29
30
31
32
33
34
35
36
37
38
39
40
41
~2
43
44
45
46
47
48
49
50
51
52
53
54
55
56
57
58
59
110
61
Part
No
.
22894
AG
39882 c
39882 c
22541
Jl
39882 r
39893 c
88
39852 H
22569
39501
K
8372 A
22824 8
39855 0
39573 K
39573 A.\
395'4
1,
39644 c
39644 s
39590 T
39590
3983'•
B
22569 c
39891,
39891, A
B
39578 F
138
22657
D-
12
39501 ON
39501
ou
39832
90
666-268
39593 K
666-271
660-506
56393 G
56393 v
51295 ll
39882
22806 A
39882
22541
39593
J
8
c
22586 R
39595
22569
39582
39582
225lo
39582
0
BL
BK
I B
811
22569 c
8372 A
39582
BV
22653 D-4
39582
F
39593 J
22569 D
39593 D
39593
I,
666-280
22650
""-4
666-290
Description
Screw,
Top
Upper
Screw,
Casket,
011
Screw,
Needle Lever
Scre:w,
Cloth
Washer,
Screw,
Foot
Upper
Upper
Lower
401
401
Crankshaft
Crankshaft
Differential
Scre~~o•,
011
Oil
Cloth
Sere
Scrc:::w, for
Cloth
Cloth
Cloth
Sere
Felt
OJ.l
011
Rctalnillg
Porex
SprJn~,
lBolutor
BoLtom
Screw,
BoLtoo Cover Gasket - -
Screw,
0!1
Screw,
Isolator
Screw,
Air
Alr
Screw,
Bose
Scr~~,
Washer,
Air
Screw,
BaHc
011
Scr:cw,
OLI
Sprlng,
OU
Plug
Jo'
c I t 0
for
top
cover
- - - - - - - - - - - - - - - - - - - - - - - 2
Cover - - - - - - - - - - - - - - - - I
Oil
Shield
!or
upper
for
upper
Filler
Plate
Llfter
Kntfe
KnHe
l.ooper
Looper
for
for
for
for
Sere.•
oil
cloth
Stud
oll
oil
Shaft
Driving
Driving
Drive
Looper Drive
Bushing,
Bushing,
for:
feed
Strainer
filter
l'lote
....
•,
Plate,
l
'lote,
Plate
....
•,
Pod - - - - - - - - - - - - - - - - - - - - - - - - - - - - -
Tube,
Tube:,
filter,
Screen
Fabric
for
cloth plate
clot
La
for
cloth plate
cygothanc
brass
Ring,
for
oil
- - - - - - - - - - - - - - - - - - - - - - - - - - - - -
Cover - - - - - -
for
bottom
for
botLom
Cover - - - - - - - - - - - - - - - - I
oil
shield
oil
shield
Assembly
system
Drive
plate
- - - - - - - - - - - - - - - - - - - - - I
filter
filter
- - - - - - - - - - - - - - - - - - - - 2
Shaft
stud
screen
scr~cn
cover
cover
- - - - - - - - - - - - - - - - - - - - - - I
- - - - - - - - - - - -
- - - - - - - - - - J
---
Bushing - - - - - - - - - - - - - - - 4
- - - - - - - - - - - - - - - - - - - I
screw
- - - - - - - - - - - - - - - - -
- - - - - - - - - - - - -
Bushing - - - - - - - - - - - - - - - - - - - -
Arm
Bar
Feed
b.ar
Am
Bushing
Shaft
Shaft
B.ar
Bushing,
Bushing,
inner
left
Thrust
thrust
Bushing,
Bushing,
- - - - - - - - - - - - - - - - - - - - - - -
left
- - - - - - - - - - - - - - - - -
-...•asher
left
right
right
left
- - - - - - - - - - - - - -
t,'asher - - - - - - - - - - - - - - - - -
- - - - - - - - - - - -
- - - - - - - - - - - -
- - - - - - - - - - - - - - - -
- - - - - - - - - - - -
- - - - - - - - -
- - - - - - - -
Guard
h
plate
fo
r
Styles
fo
r
Styles
tch
Spr
- - - - - - - - - - - - - - - - - - - - - - - - - - -
for
oil
for
oi
l tube - - - - - - - - - - - - - - - - - -
tube
cover
cover
- - - - -
fabric
- - - - - - - - - - - - - - -
39800 CA,
39800 VCP,
ing
- - - - - - - - - - - - - - - - - - - - -
latch
- - - - - - - - - - - - - - - - - - - - -
tube
- - - - - - - - - - - - - - - - - - - - - - -
- - - - - -
gu.ard - - - - - - - - - -
CJ\
, Cl' ,
VCQ,
spring
- - - - - - - - - - - - - - - - - - - - -
CQ, CX,
\fCX, V
- - - - - - - - - - - - - - -
CY
CY
(not
-------
shown} - - - - -
- - - -
Gauge FloaL - - - - - - - - - - - - - -
for
bottom
- - - - - - - - - - - - - - - - - - -
for
lower and
l)uct,
DueL, lower - -
Plote
Duct,
Plate
Pump
C8uge
Tube,
Screw-
outer
for
base
- - - - - - - - - - - - - - - - - - - - - - - - - - - - - -
for
upper
for
upper
upper
(or
base
Extension
Tube - - - - - - - - - - - - - - - - - - - - - - - - - - - -
for
oll
Indicator
Cor oil. tube - - - - - - - - - - -
Lygolhili
- - - - - - - - - - - - - - - - - - - -
1sc
- - - - - - - - - - - - - - - - - - - - - - - - - -
cover
---
plate
air
air
-----
plate
tube
)C
- - - - - - - - - -
outer
--
duct
duct
extension
air
duct
----------------
-
--
- - - - - - - - - - - - - - - - - -
- - - - - - - - - - - - - - - - - -
- - - - - - - - - - - - - - - - - - - - - -
screw
- - - - - - - - - - - - - - - - - - -
------------
- - - - - - - - - - - - - - - - -
- - - - - - - - - - - - - - -
------
-
- - - - - - - - - - - - - - - - - - - - - - -
spring
- - - - - - - - - - - - - - - - - - - - - - -
- - - - - - - - - - - - - - - - - - - - - - -
- - - - - - - - - - - - - - - - - - - -
--
- - - - - - - - - -
--
- - - - - - -
--
---
Amt.
Roq.
- 12
I
I
2
I
I
I
I
1
l
I
l
2
I
l
I
2
I
L
l
I
2
I
I
I
I
I
I
2
I
I
I
1$
I
I
2
4
I
I
2
I
2
2
I
2
I
I
l
I
I
l
l
I
25