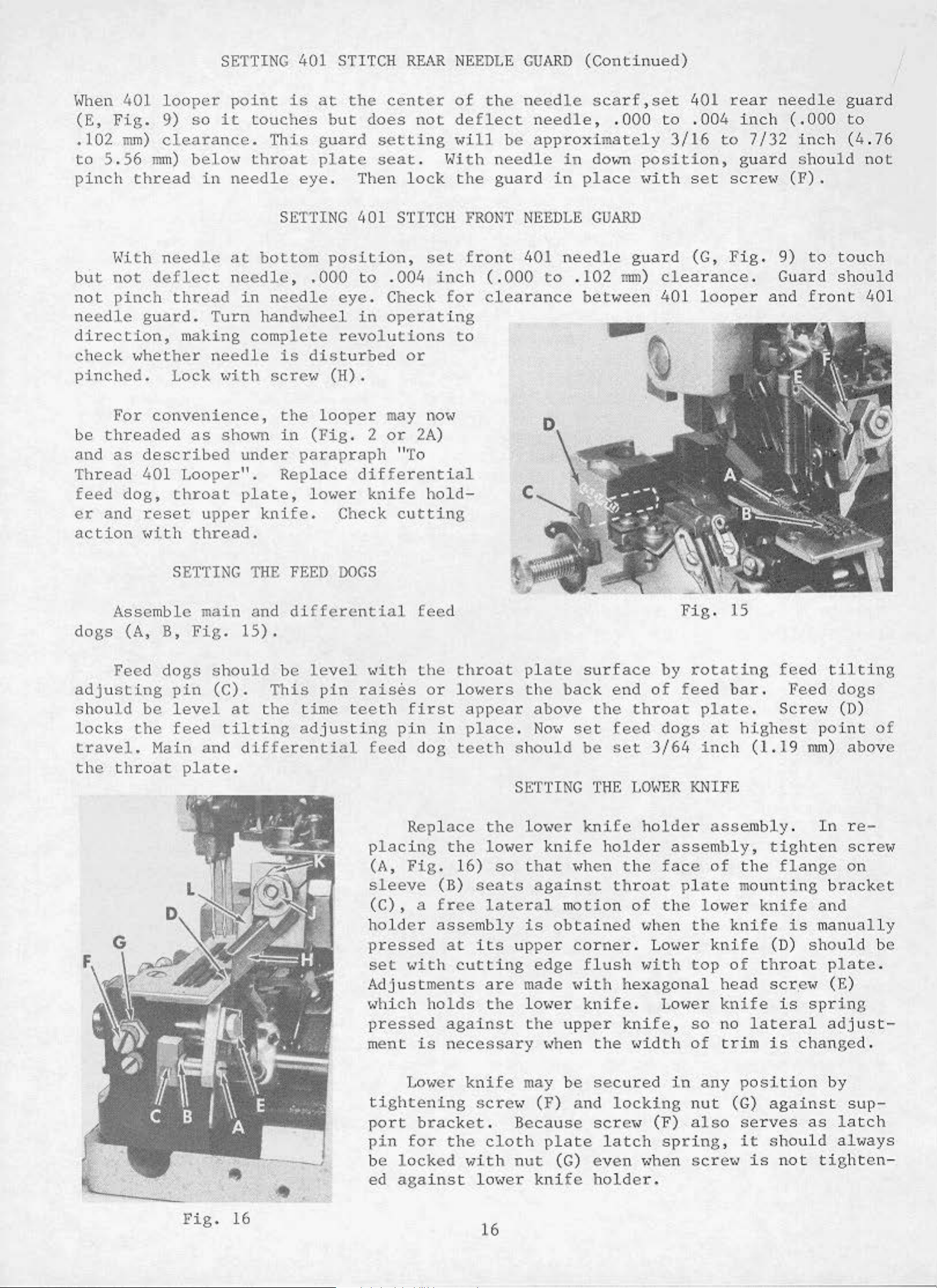
SETTING
401 STITCH
REAR NEEDLE GUARD
(Continued)
lfuen
(E,
.102
to
pinch
but
not
needle
direction,
check
pinched.
be
and
Thread
feed
er
action
401
Fig.
mm)
5 . 56
thread
With
not
pinch
guard.
"hether
For
threaded
as
described
401
dog,
and
reset
toith
looper
9)
so
clearance.
mm)
deflect
convenience,
belo"
needle
thread
making
Lock
as
Looper".
throat
thread.
point
it
in
needle
at
needle,
in
Turn
needle
'''ith
sho\m
under
plate,
upper
is
at
the
touches
This
throat
SETTING
bottom
needle
handv7heel
complete
is
sere"
the
in (Fig.
Replace differential
knife.
but
guard
plate
eye.
position,
. 000
eye.
revolutions
disturbed
(H).
looper
parapraph
lower
Check
center
does
setting
seat.
Then
401 STITCH
to
. 004
Check
in
operating
may
2 or
"To
knife
cutting
not
lock
set
or
noto
2A
hold-
of
the
deflect
••i
ll
Hith
the
FRONT NEEDLE GUARD
front
inch
for
)
(.
clearance
to
needle
needle,
be
approximately
needle
guard
40
000
in
in
1
needle
to
place
. 102
bet"een
scarf,
.000
down
guard
mm)
set
position,
toith
40
to
.0
3/16
set
(G,
clearance.
401
looper
1
rear
04
to
screto
Fig.
needle guar
inch
7/32
guard
9)
Guard
and
(.000
inch
should
(F).
to
front
d
to
(4
. 76
not
touch
should
40
1
Asse
dogs
adjusting
should
locks
travel.
the
(A,
Feed
the
throat
SETTING
mble main
B,
Fig.
dogs
be
Main
pin
level
feed
should
(C).
and
plate.
THE
and
15).
be
This
at
the
tilting
differential
FEED
differential
time tee
ad
DOGS
level
pin
just
t<ith
raises
i ng
feed
p
(A,
sleeve
(C),
holder
feed
the
th
first
pin
dog
Replace
lacillg
Fig.
a
throat
or
lov1ers
appear
in
place.
teeth
the
16)
(B)
free
assembly
seats
plate
the
should
SETTING
the
lotoer
lateral
so
lo"er
that
is
surface
back
above the
Noto
against
set
klli
fe
"h
m
otion
obtained
end
feed
be
set
TilE
knife
holder
en
throat
of
throat
3/64
LO\mR
holder
the
of
vlhen
Fig.
by
rotating
feed
plate.
dogs
assembly,
face
the
at
in
ch
KNIFE
assembly
of
plate
loV~er
the
15
feed
bar.
highest
(
the
mounting
kllife
Feed
Sere•<
1.19
tightell
flallge
knife
is
tilting
point
mm)
.
In
brack
and
manually
dogs
(D)
above
re
-
screto
on
of
et
pressed
set
Adjustments
"hich
pressed
m
tightening
port
pin
be
ed
·
Fig.
16
~·--·
with
ent
Low
for
locked
against
is
brac
at
its
cutting
holds
against
necessary
e~:
knife
scr.e«
ket.
the
Vlith
lo,.er
are
the
cloth
16
upper
edge
made
lo"er
t
he
may
(F)
Because
nut
knife
corner
'•ith
upper
t<hen
be
and
plate
(G)
flush
hexagollal
knife.
knife,
the
secured
locking
scre"'
latch
even
holder.
. Lo<•er
Vlith
Lotoer
"'idth
in
(F)
spring
when
knife
top
so
of
any
nut
also
scre
of
head
knife
no
lateral
trim
position
(G)
serves
,
it
w
is
(D)
throat
scr.e
is
is
changed
against
should
not
should
p
late
t<
(E)
spr
ing
adjust-
.
by
sup-
as latch
altoays
tighten
be
.
-
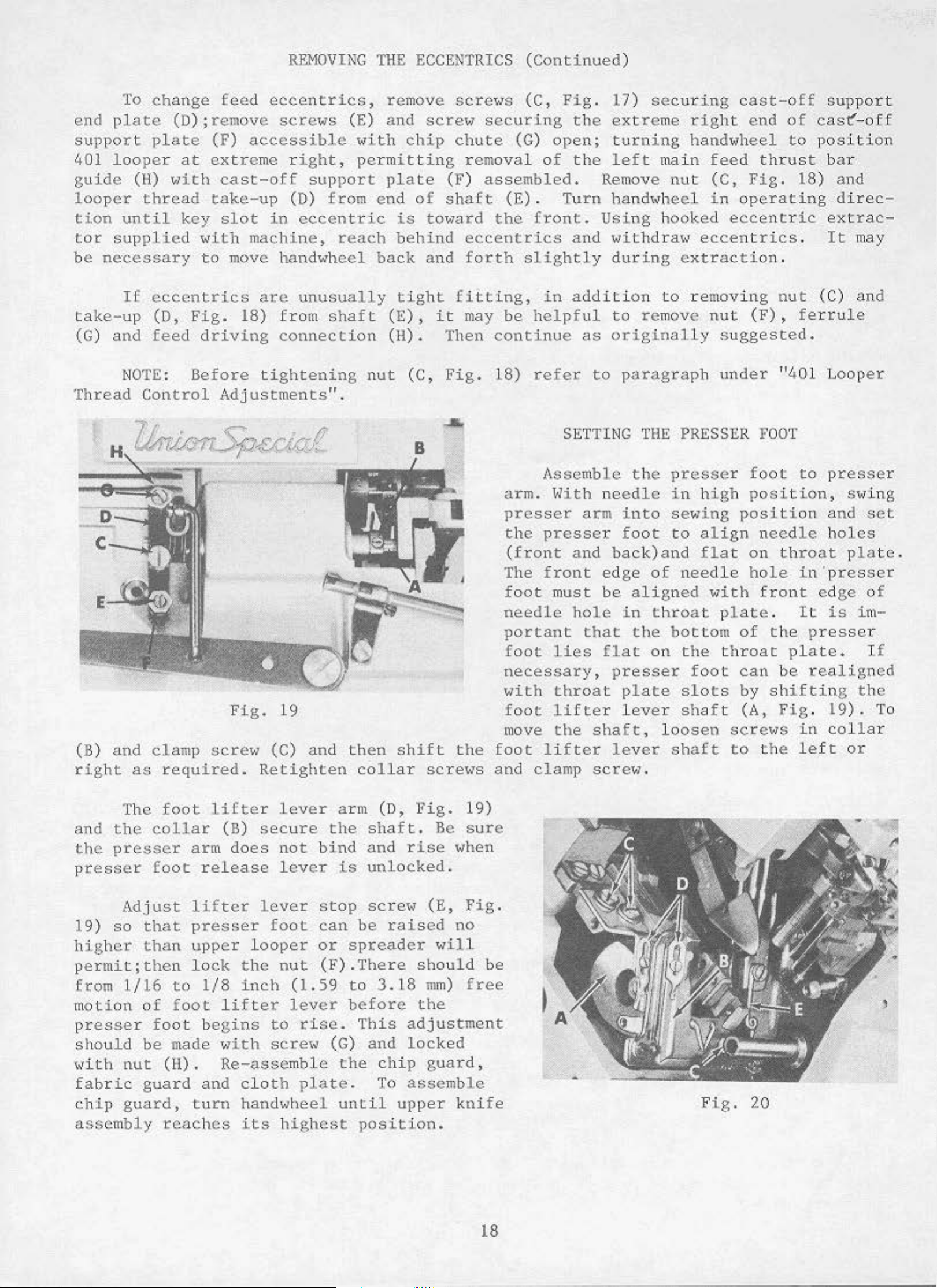
To
end
plate
support
401
looper
guide
looper
tion
tor
be
until
supplied
necessary
I€
take-up
(G)
and
change
(D);
plate
at
(H)
~olith
thread
key
eccentrics
(D,
Fig.
feed
feed
remove
(F)
accessible
extreme
cast-off
take
-up
slot
<dth
to
machine,
move
18)
driving
REMOVING
eccentrics,
screws
right,
support
(D)
in
ecc<mtric
hand wheel
are
unusually
from
connection
THE ECCENTRICS
(E)
with
permitting
fr
om
end
reach
bac.k
shaft
remove scre<,•s
and
scre1o1
chip
securing
chute
removal of
plate
is
behind
(F)
of
shaft
to.,ard
assembled.
the
eccentrics
and forth
tight
(E),
(H). T
it
fitting
may
hen
be
continue
(Continued)
(C,
Fig.
the
(G)
open;
the
Remove
(E).
Turn
front.
Using
and
slil~htly
,
in
addition
helpful
as
17)
extre
securing
me
turning
left
main
nut
hand"heel
hooked
withdra"
during
e
to
to
remove
originally
cast
right
end
handwheel
feed
(C,
in
thrust
Fig
operating
eccentric
eccentrics
xtrac
ti
on.
removing
nut
(F),
suggested.
-o
ff
of
to
.
18)
.
nut
ferrule
support
cas(
-o
ff
position
bar
and
direcextracIt
may
(C)
and
NOTE:
Thread
(B)
and
right
Control
clamp
as
required.
Before
Adjustments"
Fig.
screw
tightening
19
(C)
and
Retighten
nut (C,
.
then
collar
B
shift
scre«s
Fig.
the
18)
refer
SETTING
Assemble
arm.
presser
the
(front
The
foot
needle
portant
foot
necessary,
with throat
foot
move
foot
and
~l
ith
presser
and
front
must
hole
lies
lifter
the
lifter
clamp
to
paragraph
THE
the
needle
arm
that the
in
foot
bac
edge
be
aligned
in
fl
at
presser
pl
lever
shaft,
le
ver
scre1o1.
to
k)
of
on
ate
under
PRESSER
presser
in
high
se~oling
to
align
and
throat
loo
flat
needle
"ith
pl
bottom
the
foot
slots
shaft
sen
shaft
throat
F
OOT
foot
position,
pos
iti
needl
on
hole
front
at
e .
of
the
can
by
(A,
be
shifting
Fig
screws
to
the
"401
to
on
e
Looper
presser
and
holes
throat
in·presser
ed
It
is
presser
pl
ate.
realigned
.
19).
in
collar
left
s
wing
set
plate.
ge
of
im-
If
the
or
To
The
and
the
presser
the
collar
presser
foot
Adjust
19)
higher
so
that
than
permit;then
from
motion
presser
should
«i
fabric
chip
th
1/16
of
foot
be
nut
guard
guard,
assembly
foot
lifter
arm
release
lifter
presser
upper
lock
to
1/8
foot
begins
made
(H)
.
and
turn
reaches
lever
(B)
secure
does
not bind and
lever
lever
foot
looper
the
inch
lifter
Hith
nut
(1.59
lever
to
r.ise.
sere"
Re-assemble
cloth
plate
hand"1heel
i.
ts
highest
arm
the
is
stop
can
or
(D,
shaft.
unlocked.
scre\J
be
spreader
(F).Tbere
to
3.18
before
This
(G)
the
and
chip
. To
until
position.
Fig.
Be
rise
(E,
raised
will
should
m
m)
the
adjustment
locked
guard,
assemble
upper
19)
sure
lohen
Pig.
no
be
free
knife
Fig.
20
18
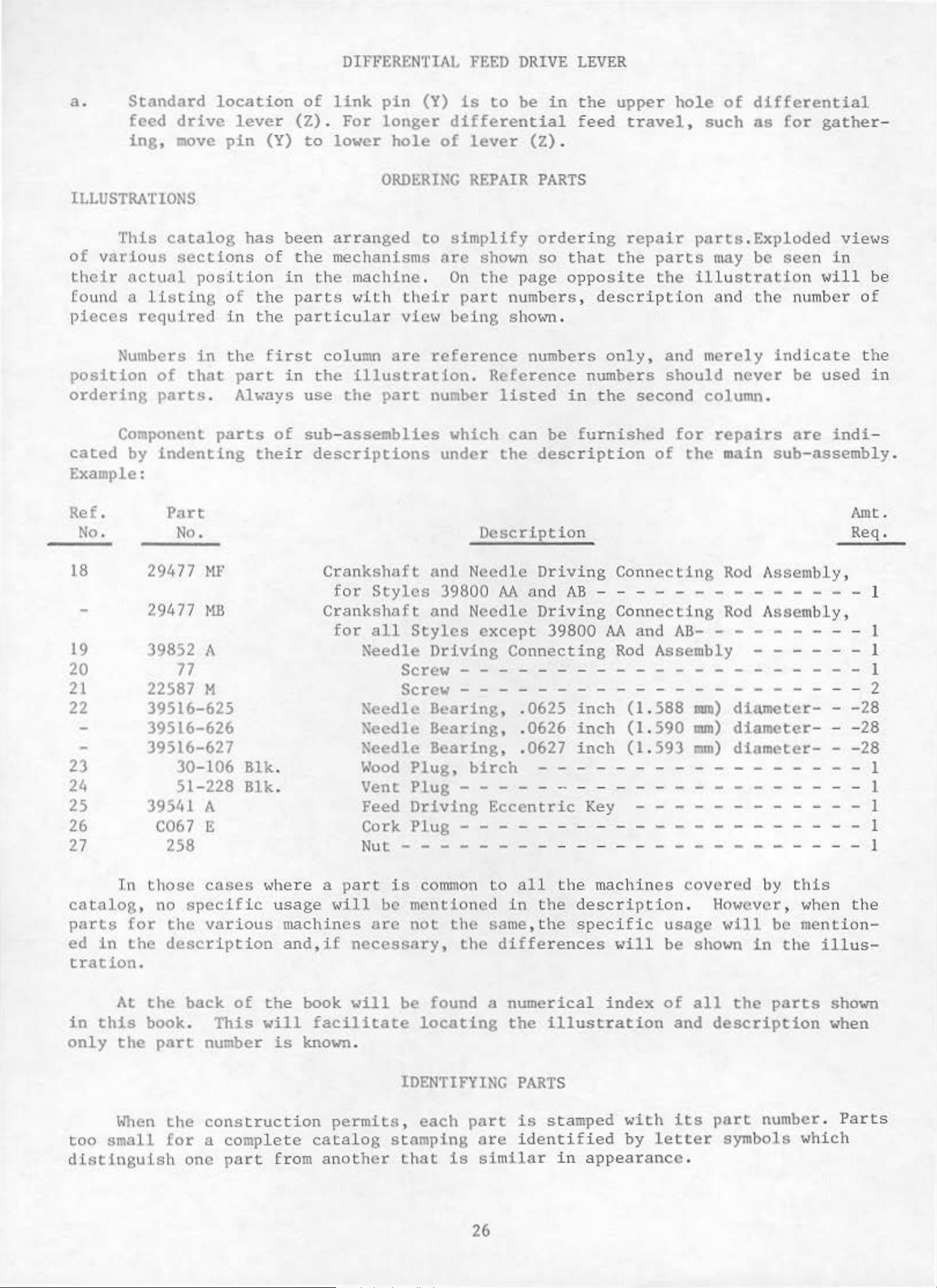
D
IFFERENTIAL
FEED DRIV
E L
EVER
a.
Standard
feed
ing,
drive
move
ILLUSTRATIONS
This
of v
th
eir
ario
actual
found a
ieces
p
Numbers
position
ordering
catalog has
us
secti
position
listi
ng of
require
in
of
t h
parts
Component
cated
by
indenting
location
leve
pin
r (Z) .
(Y)
been a
ons
of
in
the
d
in
t he
the fi
at
part
rs
in
. Always
parts
the
of
ir
of
to
link
For
lower
pin
longer
hole
ORDERING
the
mechani
the mach
part
part
t
colu
s with
ic
rran
ged to
sms are
ine .
th
ular vie
mn
are
the illustration
use
the
part
sub-assemblies
descriptions
(Y)
is
to
differen
of
leve
r (Z) .
REPAIR
simpl
sho
i fy
wn
On the page
ei r
pa
r t numb
1< being sho
reference
.
Reference
number
which
under
lis
can
the
be
in
ti
al
PARTS
orderin
so
ers
••n.
numbe
ted i n
be
des
t he upper
fee
d
tr
avel
g repai r
that
opp
, d
rs
the part
osite
escription and
onl
y,
number s shou
th
e second column.
furnished
criptio
n
hole
,
of
such
parts
s m
ay
differe
as
for
. Exp
be
loded
see
n
gather
n
the illustration wil
th
e number
and m
for
of
erely
ld
never
repairs
the main
indica
be
used
are
sub
-assembl y .
tial
-
view
s
in
l be
of
te the
in
indi
Example:
Ref.
No
.
18
19
20
21
22
23
24
25
26
27
Part
No
.
294
77
m·
29
4 77
~
Ill
39852 A
77
22587
M
39516-625
39516-626
39516-
30-
51
627
106
-228
39541 A
C067
258
E
Blk
Blk
.
.
Cranksha
for
Sty
ft
les
Crankshaft
for
al l St
Needle Dri
Screw - - - - - - - - - - - Screw - - -
Needle
Needle
Needle
Wood
Vent
Feed
Cork P
Nut - - - - - - - - - - - - -
D
escription
and Needle
39800
a1
1d Needle
yles
AA
except
vi ng Connecti ng
Bearing
Bearing
Bearing
, .0625
, .0626
, .0627 i
Plug, birch
Plug
Driving
lug
- - - - - - - - - - - - - - - - Ecce
- - - - - - - - - - - - - - - - - - -
Driving Co
an
d AB - - - - - - - - - - - - - - 1
Driving
39800
nnecti ng Rod Assembl
Connectin
AA
and
Rod Asse
g Rod Assem
AB-
mb
- ly
- - -
y,
bly
- - - 1
- - - 1
- - 2
r-
-
-
-
-
inch
in
nch
(1. 588
ch (1.590
(1 .593
mm)
mm)
mm)
diameterdiameter
diamete
- - - - - - - - - - - - -
ntric
Key
- - - - - - - -
- - -
Am
Req
,
-2
-28
-2
t.
.
1
8
8
1
1
1
1
1
I
11
t h
cat
alog
arts
p
ed
in
ration.
t
in
this
only
, no spe
!or
lhe
Al
the
book.
the
\./hen
too small
distinguis
ose
the va
desc
back
part
the con
for
h one
cas
es
cific
rious
ription
of the
This
number
s t
ructi
a compl
part
•<here a
usa
ge
par
1~ill
machines
and,if necessa
will
is
ete
from
book
facilitate
known
on pe
ca
will
.
rmits,
talog
anoth
t
is
common
to
be menti on ed
a rc not the
sa
r y, t he
be
found a
locating
IDENTIFYING PART
each
stampi.ng a
er
th
at
is
pa
rt i s
re
simil
al
l
the
in the
me, t
he
descr
speci
differences
nume
the
rical
illust
S
sta
mp
ident i fi
ar
in
appea
machin
iption.
fic
will
index
rati
ed
ed
on and
with
by
ranc
es covcr
usa
ge
e.d
How
•~
ill
eve
by
r,
be me
be s hown i n t he
of
all
the
parts
description
it
s
part number . Parts
l etter
sym
bol s
e .
this
when
nti
illu
sho
wh
which
th
on-
s-
'm
en
e
26
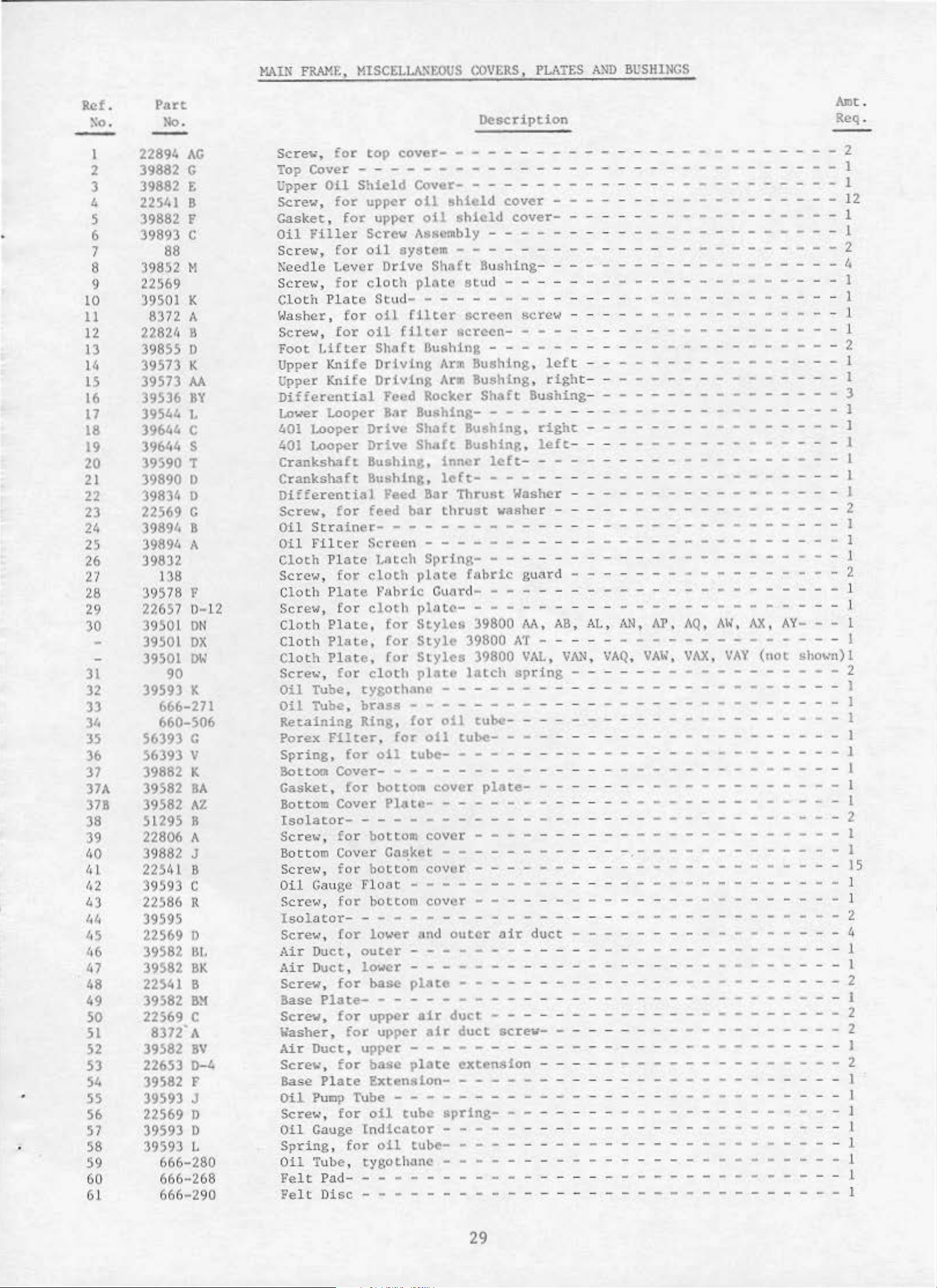
MAIN
FUM",
MISCELLA~t;OUS
COVERS,
PLATES
A~D
llUSHlNGS
Ref.
xo.
Part
llo.
Description
Amt.
Req .
-
I
2
3
~
5
6
7
8
9
10
11
12
13
14
15
16
17
18
19
20
21
22
23
24
25
26
27
28
29
30
31
32
33
34
35
36
37
37A
37B
38
39
40
ld
1
12
~3
41•
ll5
46
47
48
49
50
51
52
53
54
•
55
56
57
58
59
60
61
22894
AG
39882 c
39882 t
22541 B
39882 F
39893 c
88
39852 M
22569
39501 K
8372 A
22824 B
39855 D
39573 K
39573
39536
39544
AA
BY
I.
39644 c
39644 s
39590 T
39890 0
39834 0
22569 c
39894 B
39894 A
39832
138
39578 F
22657 L
39501
39501
39501
>-12
ON
ox
OW
90
39593 K
666-271
660-506
56393 G
56393 \'
39882 K
39582
39582
BA
AZ
51295 B
22806 A
39882 J
22541 B
39593 c
22586 R
39595
22569 0
39582
39582
JlL
BK
22541 B
39582
Ill!
22569 c
8372' A
39582
BV
22653 D-4
39582 F
39593
J
22569 D
39593 0
39593 L
666-280
666-268
666-290
Sere~,
Top
Upper
Scret..•,
Gasket,
Oil
Scr
~eedle
Screw, for:
Cloth Plate
Washer,
Screw,
FootLiflcrShaftl)ushing------
Upper
Upper
Differential
Lower Looper Bar
401
401
Crankshaft
Crankshaft
Differential
Screw·,
011
Oil
C
loth
Serer..;~,
Cloth Plate
Screw,
Cloth
Cloth
Cloth
Scre1.o.•,
Oil
Oil
Recaining
Porex
Spring,
Bottom
Casket,
Bottom Cover
Isolator-
Screw, for
Bottom
Screw,
Oil
Screw,
x~ol
Screw,
Air
A.ir Duct,
Screw,
Base
Screw,
Washer,
Air
Screw,
Sase
Oil
Sere
Oil
Spring, for
O
il
Felt
Fe
lt
for
top
cover-
- - - - - - - - - - - - - - - - - - - - - - 2
Cover - - - - - - - - - - - - - - - - - - - - - - - - - - - - l
Oil
Shield
for
for
Filler
ew,
for
Le
ver
for
for
Knife
Knife
Looper
Loo~r
for
StrainetFilter
Plate
for
upper
upper
Screw Assembly - - - - - - - - - - - - - - 1
oil
cloth
Stud-
oi.l r11car
oil
DrjvinQ
Driv1nj:;
Drive
Drive
Bushing,
Bushing,
feed
Sctccn
J.•tch
cloth
system
Drive
Cover-
oil
oil
Shaft Bu"loing-
p.Latc
- - - - - - - - - - - - - - -
shield
shield
- - - - - - - - - - - - - - - - - - - - 2
stu
cover
cover-
- - - - - - - - - - - - - 1
- - - - - - - - - - - - - - 4
- - - - - - - - - - 12
d - - - - - - - - - - - - - 1
...
- - - - - - - - - - - - - - - - - - - - - - - - 1
fjl~er
Arm
Arm
Feed
Rocker
BushingShnft
Shaft
inner
left-
Feed Bnr
bor
thrust
screen
screen-
Bushing,
Bushing,
Shaft
Bushing,
Bushing,
Thrust
!:>crev.•
- - - - - - - - - - - 1
- - - - - - - - - - - - - - - - - - 1
left
right
Bushing
-
- - - - - - - - - - - - - - 1
- - - - - - - - - - - - 3
-- --
- - - - - - - - - - - - 1
---
--2
- - - - - - - - - - - - - - - - - - 1
right
left
left
- - - - - - - - - - - - - - - - - - - - 1
- - - - - - - - - - - - I
- - - - - - - - - - - - 1
- - - - - - - - - - - 1
Washer - - - - - - - - - - - - - 1
washer - - - - - - - - - - - - - - - - 2
- - - - - - - - - - - - - - - - - - - - - - - - 1
- - - - - - - - - - - - - - - - 1
Spring-
pl.:'lte
- - - - - - - - - - - - - - I
fabric
guard
- - - - - - - - - - - - - - - 2
- 1
F'nhric CuCird- - - - - - - - - - - - - - - - - - - 1
for
Plate,
Plate
Plate,
for
Tube,
Tube,
Filter.
for
Cover-
for
cloth
, Cor
cloth
tygothane
brass
Ring,
oil
bottom
plllt~-
for
Styles
Style
for
Styles
plate
- - - - - - - - - - - - - - - - - - - - - 1
39800
39800
39800
latch
M,
118,
AL,
,\N,
liP,
AQ,
Al<,
AX,
AY-
AT
- - - - - - - - - - - - - - - - - I
VAL,
spring
Vlll<,
VAQ,
- - - - - - - - - - - - - - - - - 2
VAl~,
V/IY.,
VAY
(not
sho•·n)l
- - - - - - - - - - - - - - - - - - - - - I
- - - - - - - - - - - - - - - - - - - - - - - J
for
oil
for
oil
tube-
cube-
tube-
- - - - - - - - - - - - - - 1
- - - - - - - - - - 1
- -
--
- -
--
- - - - - - - 1
- - - - - - - - - - - - - - - - - - - - - - - - 1
Plate-
cover
- - - - - - - - - - - - - - - - - - - l
plate-
- - - - - - - l
- - - - - - - - - - - - - - - - - - - - - - - - 2
bottom
Cov~r
fot
bottom
Gauge
ator-
Duc
Plate-
Floot
for
bottom
- - - - - - - - - - - - - - - - - - - - - - - - - - 2
for
lower
t,
outer
lower
for
base
for
upper
for
Duct,
Plate
Pump
....
•,
Gauge
Tube,
Pad-
D
upper
for
base
Extennlon-
Tube
for
oil
Cndlcacor
tygothanc
isc
- - - - - - - - - - - - - - - - - - - - - - - - 1
Ca~keL
- - - - - - - - - - - - - - - - - - - - - - - - - - - 1
upper
oil
cover
cover
- - - - - - - - - - - - - - - - - - - - - 1
- - - - - - - - - - - - - 1
- - - - - - - - - - - - - - - lS
- - - - - - - - - - - - - - - - - - - - - - - - .. 1
cover
and
- - - - - - - - - - - - - - - - - - - - - - - 1
- - - - - - - - - - - - - - - - - - - 1
ploto
air
atr
- - - - - - - - - - - - - - - - - - - - - 1
outer
air
duct
- - - - - - - - - - - - - 4
- - - - - - - - - - - - - - - - - - - - - - - - 2
duct
- - - - - - - - - - - - - - - - - - 2
duct
screw-
- - - - - - - - - - - - 2
- - - - - - - - - - - - - - - - - 1
place
extension
- - - - - - - - - - - - - 2
- - - - - - - - - - - - - - - - - - - - 1
- - - - - - - - - - - - - - - - - - - - - - - - - - I
tube
spring-
- - - - - - - - - - - - - - - 1
- - - - - - - - - - - - - - - - - - - - - 1
tube-
- - - - - - - - - - - - - - - - - - - - - - 1
- - - - - - - - - - - - - - - - 1
- - - - - - - - - - - - - - - - - - - - - - - J
1
29