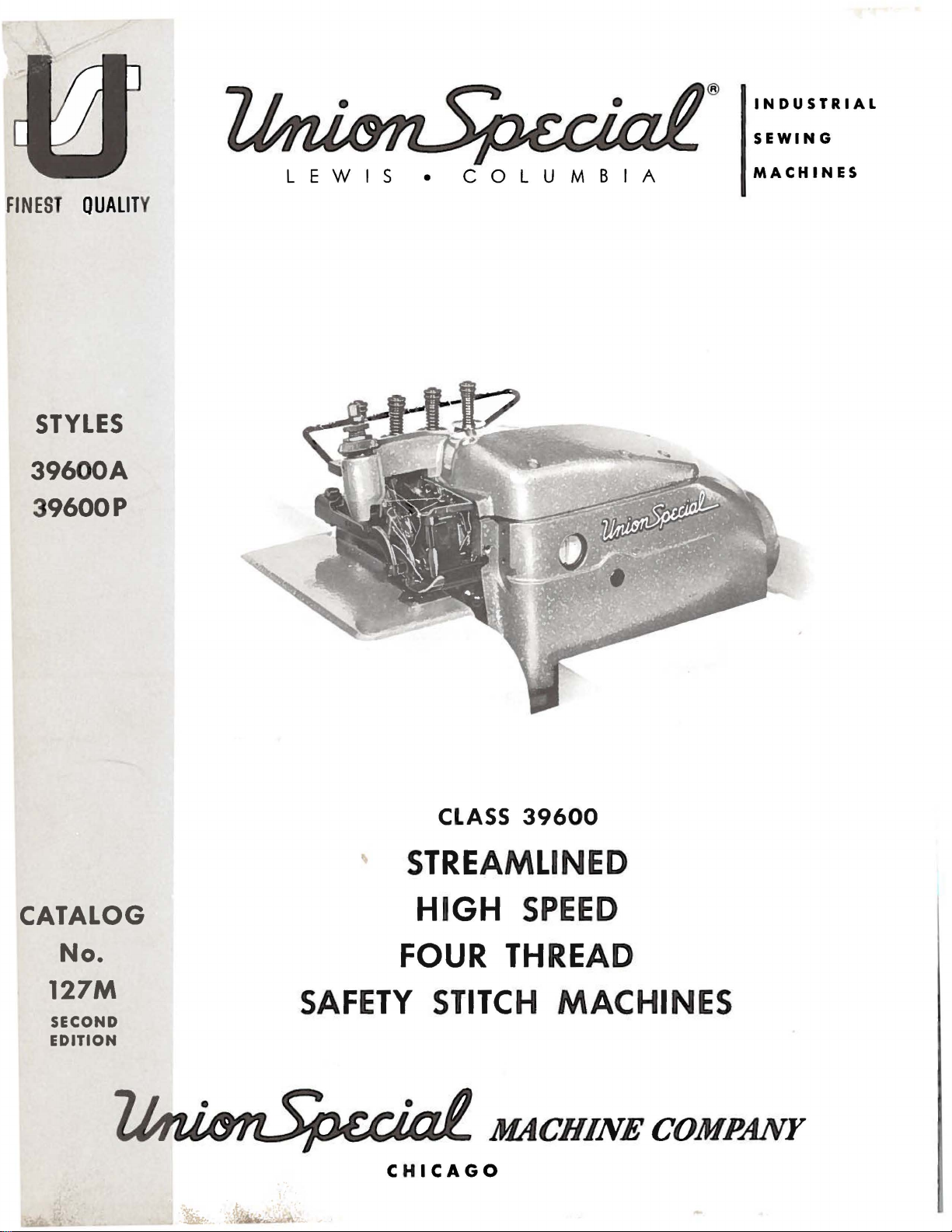
®
INDUSTRIAL
SEWING
FINEST QUALIT
Y
STYLES
39600A
39600P
LEWIS
•
COLUMBIA
MACHINES
CLASS
39600
STREAMLINED
CATALOG
No.
HIGH
FOUR
127M
SECOND
SAFETY
EDITION
STITCH
CHICAGO
SPEED
THREAD
MACHINES
MACHINE
COMPANY
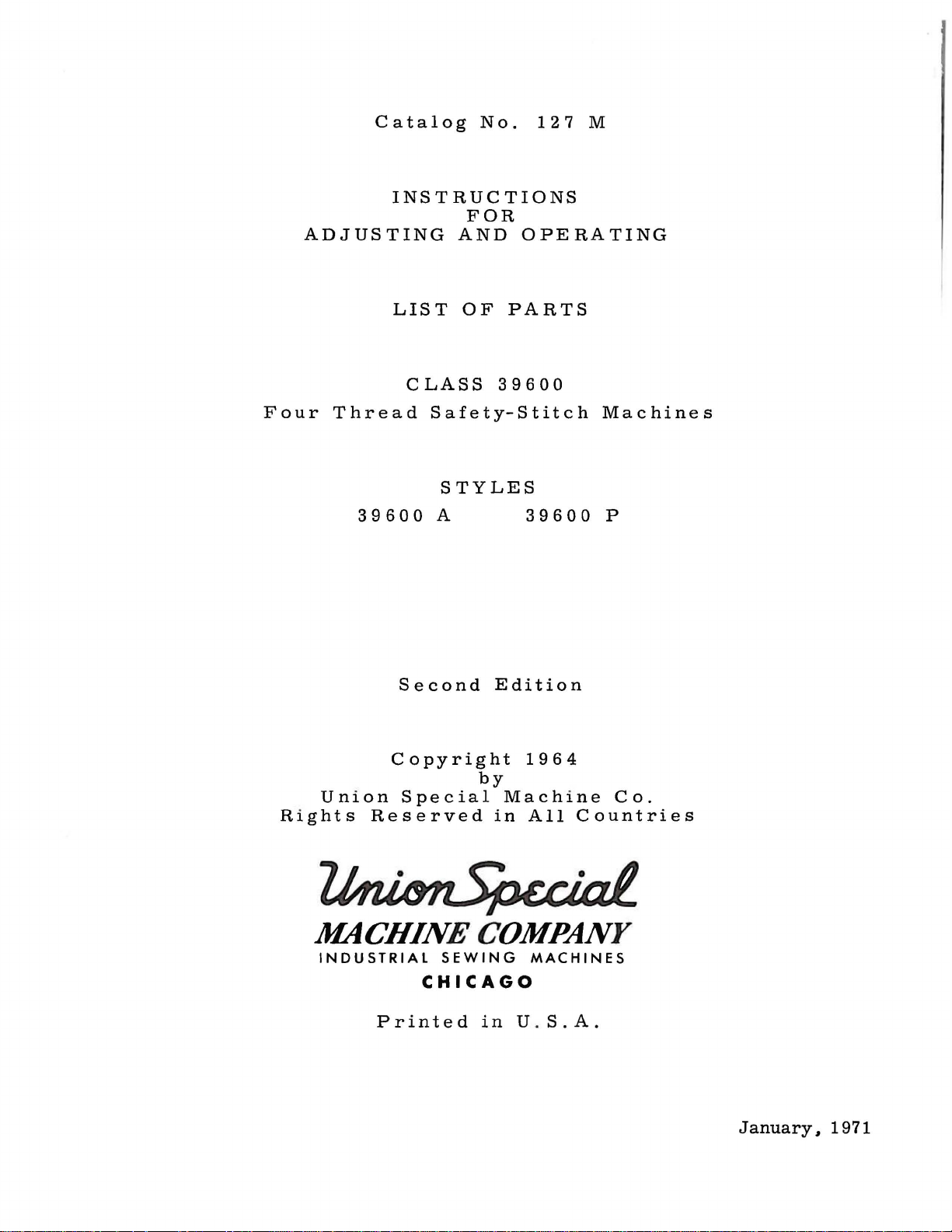
Catalog
INSTRUCTIONS
ADJUSTING
No.
FOR
AND
127
OPERATING
M
Four
Rights
Thread
39600
Union
LIST
CLASS
Safety-Stitch
A
Second
Copyright
Special
Reserved
OF
39600
STYLES
Edition
by
Machine
in
PARTS
39600
1964
All
Machines
p
Co.
Countries
MACHINE
INDUSTRIAL
CHICAGO
Printed
COMPANY
SEWING
in
MACHINES
U .
S.A.
January,
1971
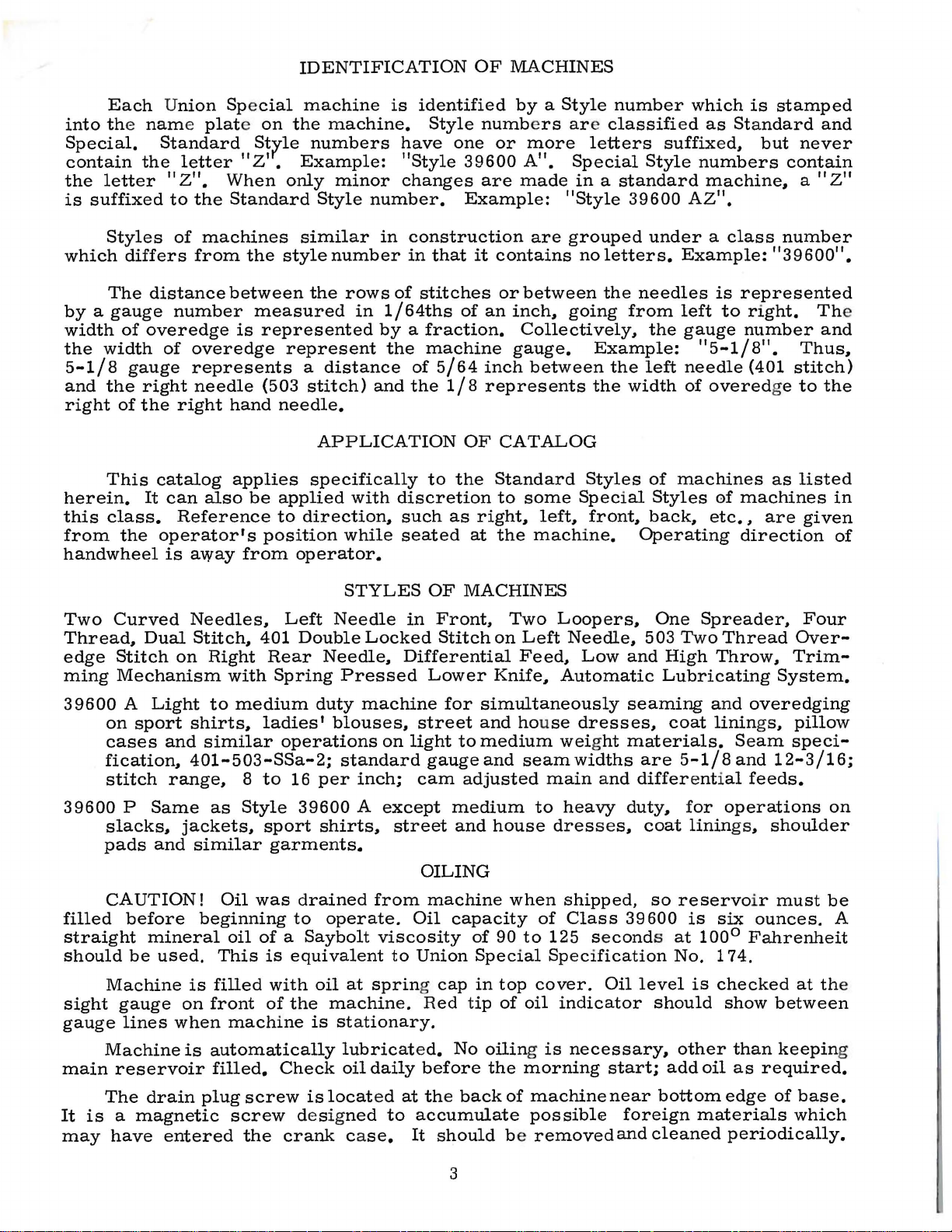
IDENTIFICATION
OF
MACHINES
Each Union
into the
Special.
contain
the
is
suffixed
which
by a gauge
width
the
5-1/8
and
right
herein.
this
from
handwheel
name plate on
the
letter
Styles
differs
The
distance
of
overedge
width
gauge
the
right
of
the
This
It
class.
the
Standard
letter
"Z".
to
the
of
machines
from
number
of
overedge
represents
needle
right
catalog
can
also
Reference
operator's
is
away
Spe
cial
StjYle
"Z'.
When
Standard
between
is
hand
applies
only
the
style
measured
represented
represent
(503
needle.
be
applied
to
position
from
machine
the
machine.
numbers
Example:
minor
Style
similar
the
a
distance
stitch)
APPLICATION
specifically
direction,
operator.
number.
in
number
rows
in
1/
by a fraction.
and
with
while
the
is
identified
Style
have
"Style
changes
of
64ths
discretion
such
seated
one
39600
Example:
construction
in
that
stitches
of
machine
of
5/64
the
1/8
OF
to
the
as
by a Style
numbers are
or
more
A".
are
made
"Style
are
it
contains
or
between
an
inch,
Collectively,
gauge.
inch
between
represents
CATALOG
Standard
to
some
right,
at
the
left,
machine.
number
classifi
letters
Special
in a standard
grouped
no
letters.
the
going
Example:
the
the
Styles
Special
front,
suffixed,
Style
39600
under a class
needles
from
the
left
width
of
Styles
back,
Operating
which
ed
as Sta
numbers
machine,
AZ".
Example:
is
represented
left
to
gauge
needle
of
machines
"5-1/
overed
of
etc.,
number
machines
direction
is
stamped
ndard
but
contain
number
"39600".
right.
8".
(401
ge
as
are
and
never
a
"Z"
Th
and
Thus,
stitch)
to
the
listed
in
given
of
e
Two
Thread,
edge
ming
39600
39600
filled
straight
should
sight
gauge
Curved
Stitch
Mechanism
on
cases
fication,
stitch
slacks,
pads
CAUTION!
Machine
Dual
A
Light
sport
P
Same
and
before
mineral
be
used.
gauge
lines
Needles,
Stitch,
on
Right
with
to
medium
shirts,
and
similar
401-503-SSa-2;
range,
jackets,
similar
is
on
when
8
as
Style
Oil
was
beginning
oil
of a Saybolt
This
filled
front
machine
STYLES
Left
401
Rear
Spring
ladies'
operations
to
sport
garments.
is
with
of
Needle
Double
Needle,
Pressed
duty
blouses,
standard
16
per
39600 A except
shirts,
drained
to
operate.
equivalent
oil
at
the
machine.
is
stationary.
OF
in
Locked
Differential
Lower
machine
street
on
light
gauge
inch;
cam
street
OILING
from
viscosity
spring cap
Oil
to
machine
Union
Red
MACHINES
Front,
Stitch
for
to
medium
and
capacity
Two
on
Knife,
simultaneously
and hou
medium
and
adjusted
house
when shipped,
of
90
Special
in
top
tip
of
Loopers,
Left
Feed,
Needle,
Low
Automatic
se
dresses,
weight
seam
to
oil
widths
main
to
heavy
dresses,
of
Class
125
seconds at
Specification
cover.
indicator
One
503
and
seaming
materials.
are
and
differential
duty, for
coat
so
39600
Oil
level
should
Spreader,
Two
Thread
High
Lubricating
coat
Throw,
and
linings,
5-1/8
linings,
reservo
is
six
100°
No.
174.
is
checked
Se
and
feeds.
operations
Fahrenheit
show
Four
Over-
Trim-
System.
overedging
pillow
am
speci-
12-3/16;
on
shoulder
ir
must
ounces.
between
be
A
at the
Machine
main
It
may
reservoir
The
is a magnetic
have
drain
entered
is
automatically
filled.
plug
screw
screw
the
Check
is
locat
designed
crank
lubric
oil
daily
ed
ca
se.
at e
d.
before
at
the
to
accumulate
It
should
No
back
3
oiling is
the
morning
of
machine
possible
be
removed
necessary,
start;
near
foreign
and
other
add
oil
bottom
materials
cleaned
than
keepin
as
required.
edge
periodically.
of
which
base.
g
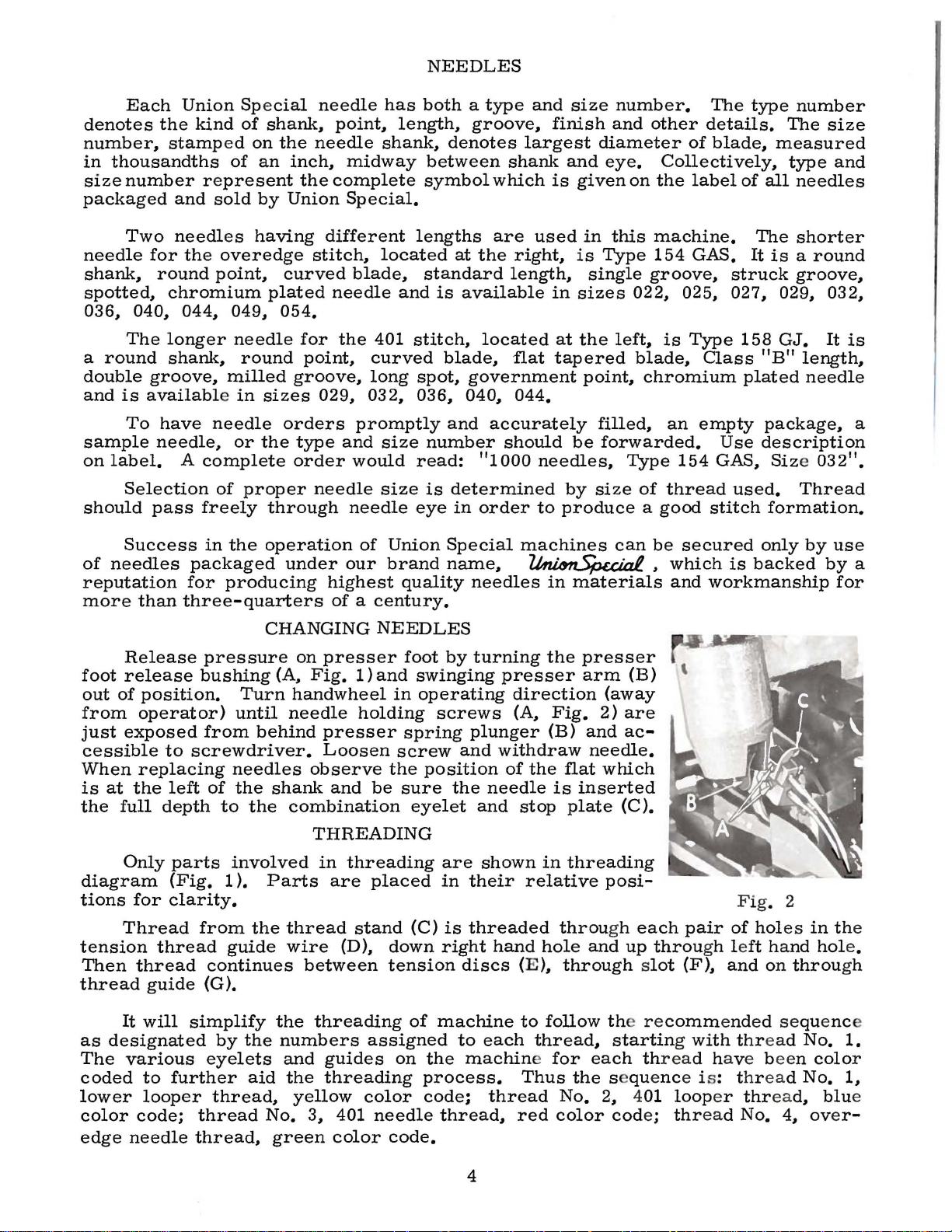
NEEDLES
Each
denotes
number,
in
thousandths
size
number
packaged
Two
needle
shank,
for the
round
spotted,
036,
040,
The
a
round
double
and
groove,
is
available in
To
sample
on
needle,
label.
Selection
should
pass
Success
of
needles
reputation
more
than
Union
the
stamp
kind
ed
Spe
of
of
r e
present
and
sold
needl
es
overedge
point,
chromium
044,
longer
shank,
049,
needle
round
milled
have
needle
or
A
complete
of
proper
freely
in
the
packaged
for
producing
three-quarters
cial
shank,
on
the
an
inch,
the
by
Union
having
curved
plated
054.
for
point,
groove,
sizes
orders
the
type
order
through
operation
under
needle
has
point,
needle
shank,
midway
complete
Special.
different
stitch,
located
blade,
needle
the
401
curved
long
029,
032, 036, 040, 044.
promptly
and
size
would
needle
size
needle
of
Union
our
brand
highest
of a century.
both a type
length,
denotes
between
symbol
lengths
at
standard
and
is
available
stitch,
blade,
spot,
and
number
read:
is
determined
eye
in
Special
name,
quality
and
groove,
finish
largest
shank
which
are
the
is
used
right,
length,
in
located
flat
at
tapered
government
accurately
should
"1000
order
needles,
to
machines
~
needles
in
size
number.
and
other
and
given
in
is
single
sizes
the
diameter
eye.
on
this
Type
022,
left,
of
Collectively,
the
label
machine.
154
GAS.
groove,
025,
is
Type
blade,
point,
be
by
size
chromium
filled,
an
forwarded.
Type
of
thread
154
produce a good
can
be
secured
..
which
materials
and
The
type
details.
blade,
The
measured
type
of
all
The
It
is a round
struck
027,
Class
158
"B"
029,
GJ.
plated
empty
GAS,
Use
description
package,
Siz
used.
stitch
formation.
only
is
backed
workmanship
number
size
and
needles
shorter
groove,
032,
It
is
length,
needle
e 032
11
Thread
by
use
by
for
a
•
a
Release
foot
release
out
of
from
just
operator)
exposed
cessible
When
is
the
replacing
at
the
full
Only
diagram
tions
for
Thread
tension
Then
thread
thread
It
as
designated
The
various
coded
lower
color
edge
code;
needle
pressure
bushing
position.
from
to
screwdriver.
left
depth
parts
(Fig.
clarity.
from
thread
guide
will
to
(G).
simplify
further
looper
thread
thread,
CHANGING
(A,
Turn
until
behind
needles
of
the
shank
to
the
involved
1 ).
Parts
the
guide
continues
the
by
the
eyelets
aid
thread,
No.
green
on
presser
Fig.
1)and
handwheel
needle
holding
presser
Loosen
observe
and
combination
THREADING
in
threading
are
thread
wire
stand
(D),
between
threading
numbers
and
guides
the
threading
yellow
color
3, 401
color
NEEDLES
foot
swinging
in
operating
screws
spring
screw
the
position
be
sure
eyelet
placed
(C)
down
tension
of
machine
assigned
on
the
process.
code;
needle
code.
by
turning
presser
direction
(A,
plunger
and
withdraw
of
the
needle
and
stop
are
shown
in
their
is
threaded
right
hand
discs (E),
to
to
each
machine for
Thus
thread
thread,
red
the
presser
arm
(away
Fig.
(B)
2)
and
needle.
the
flat
which
is
inserted
plate
in
threading
relative
hole
throu
and
posi-
gh
through slot
follow the r e
thread,
starting with
each threa
the sequenc
No.
2, 401
color
cod
(B)
are
ac-
(C).
each
up
e;
throu
Fig
pair
of
gh le
ft
(F),
and
commend
ed sequenc
thr
d have been
e is: thread
loop
er
thr
thread
No.
. 2
hol
es
hand
on
throu
ead No.
No.
ead,
4, ove
in the
hol
e.
gh
e
1.
colo
r
1,
blu
e
r-
4
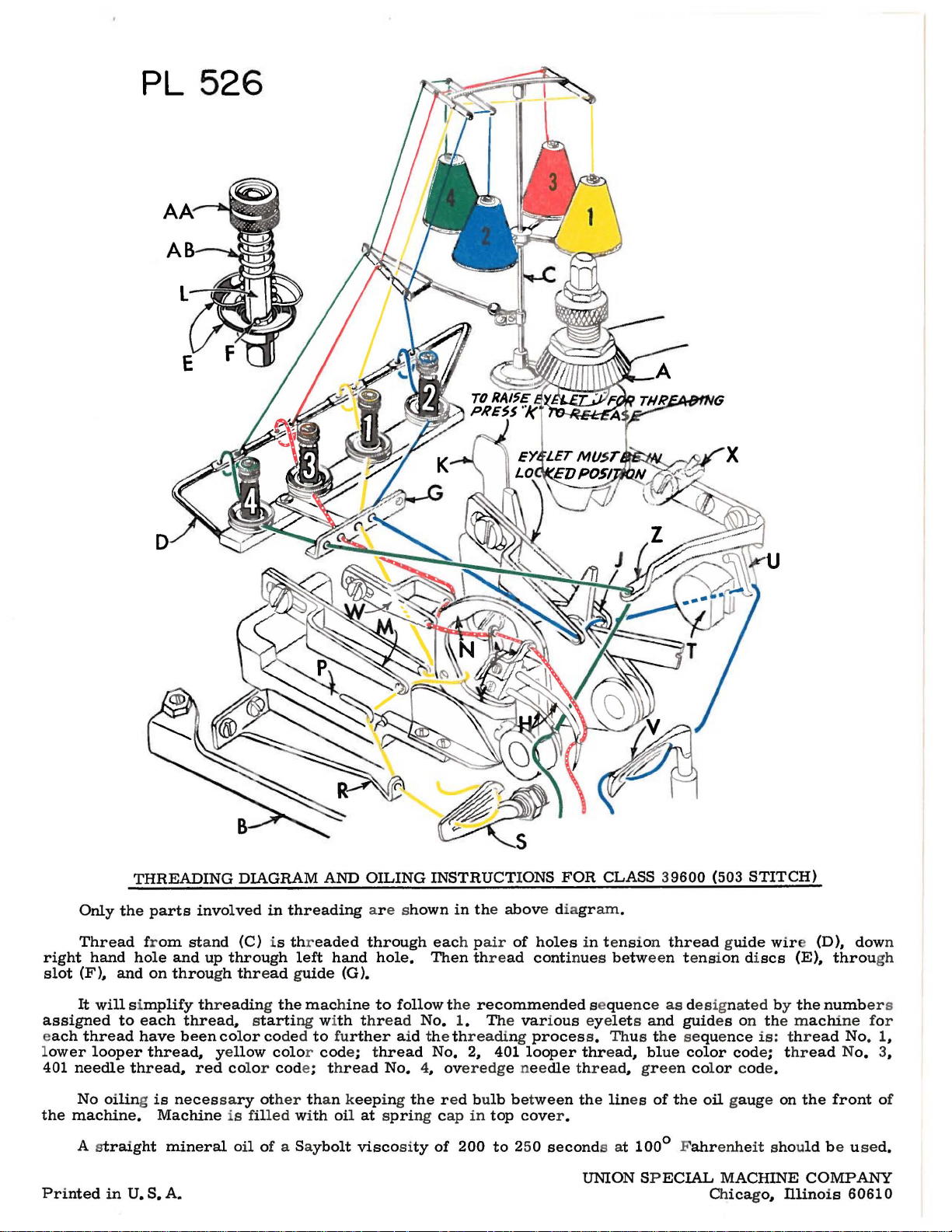
PL
526
THREADING
Only
the
parts
Thread from stand (C) is thr
right
slot
assigned
e
l
401
the
Printed
(F),
It
ach
ower
needle
No oi
machine.
A s
hand
hole
on
each
have
thread,
thread,
Machine
U.S.
A.
and
throu
been col
necessary other than k
mineral
and
will simplify thr
to
thread
looper
ling is
traight
in
thread, starti
DIAGRAM AND
involved
up
through
gh
thread
eading the
or coded
ye
llow
red color
is f
ill
oil
of a Sa
in
threading
eaded
left
guide
machine
ng with
to further
color cod
cod
e; thread
ed with
ybolt
OILING
through
hand
(G).
thr ead
e; t
eeping
oil
at spri
viscosity
INSTRUCT
ar e s
hown
eac
hole.
to
hread
Then thre
follow the
No.
aid th e threadi
No. 2, 401
No.
4, overedg
the
ng cap
of
IONS
in the
1.
r ed bu
200
abov
e diagram.
h p
air
of
holes
ad
continues between t ensi
recommended seque
The various
ng
proces
looper
e nee
lb bet
ween
in
top
cove
to
250
FOR
dle
r .
second
CLASS 3
in te
nsion thread guide
ey e
lets and
s. Thus the seque
thread, blue
thr ead, green col
the
lin
s at
UNION SP
9600
nce
as designat
guid
color
es
of
the
100° Fahr
ECIAL
(503
STITCH)
wir
on discs
ed
by
es on the m
nce
is:
thr
cod
e; thread No.
or cod
oil gauge on
enheit should
Ch
e.
MACHINE
icago,
illinois
e (D), down
(E),
throu
gh
the
numbers
achi
ne
for
ead No. 1,
the
front
be used.
COMPANY
60610
3,
of
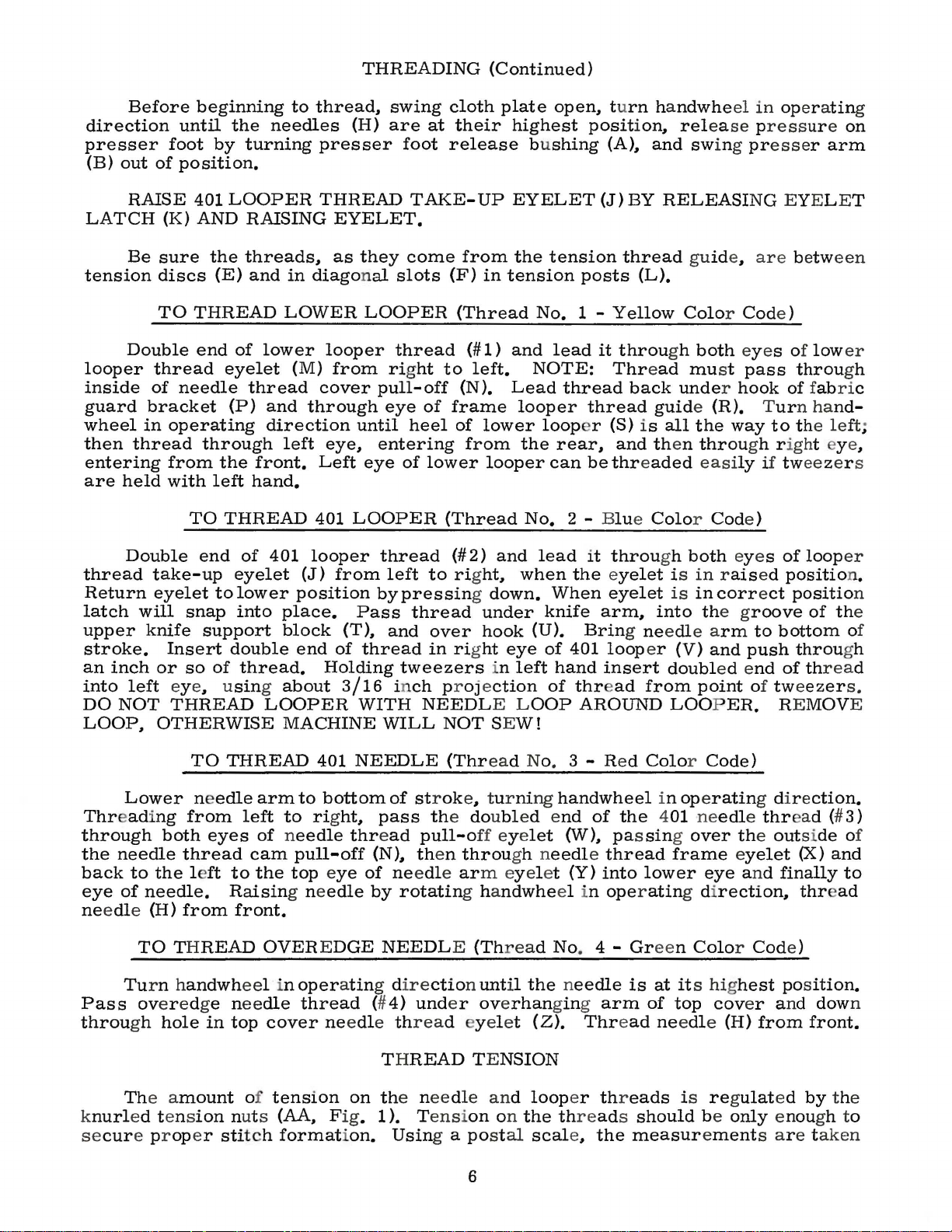
THREADING
(Continued)
Before
direction
presser
(B)
out
RAISE
LATCH
Be
tension
Double
looper
inside
guard
wheel
then
in
thread
entering
are
held
Double
thread
Return
latch
will
upper
stroke.
an
inch
into
left
DO
NOT
LOOP,
beginning
until
foot
of
position.
by
401
the
LOOPER
(K) AND
sure
discs
TO
thread
of
bracket
the
(E)
THREAD
end
of
eyelet
needle
(P)
operating
through
from
with
take-up
eyelet
knife
Insert
or
ey e, u
the
left
TO
end
to
snap
support
so
of
THREAD
of
eyelet
lower
into
double
thread.
sing about
THREAD
OTHERWISE
to
thread,
needles
turning
RAISING
threads,
and
in
diagonal
LOWER
lower
(M)
thread
and
through
direction
left
front.
hand.
401
401
looper
(J)
position
place.
block
end
LOOPER
MACHINE
swing
(H)
are
presser
THREAD
at
foot
TAKE-
cloth
their
release
UP
EYELET.
as
they
looper
from rig
cover
until
eye,
Left
LOOPER
from
Pass
(T),
of
Holding
come
slots
(F)
LOOPER
thread
ht
to
pull-off
eye
of
frame
heel
entering
eye
of
lower
(Thread
thread
left
by
pressing down.
(#2)
to rig
thread
and
over
thread
in rig
tweezers
from
(Thread
(#
left.
(N).
of
from
3/16 inch projection
WITH
NEEDL
WILL
NOT SEW!
plate
highest
EYELET
the
in
tension
1)
and
Lead
looper
lower
the
looper
and
ht,
when
under
hook
ht
eye
·n
left
E L
open, turn handwhe
position,
bu
shing
tension
No.
lead
NOTE:
loop
rear,
can
No.
lead
(A),
and swing presser arm
(J)
BY
thread
posts
1 -
Yellow
it
throu
(L
Thread
thread
back
thread
guid
r (S) i s
and then
be
threaded
2-Blue Color Cod
it
throu
the eyelet
When
knife
(U).
of
hand
of
OOP
eyelet
arm,
Bring needl
401
loop
er (V)
insert
thread
from
AROUND
into the g
el
in
oper a
release pressure
RELEASI
guide,
NG EYEL ET
are betw
).
Color Cod
gh
both
mu
st
e )
eyes of
pass
under hook
e (R). Turn hand-
all
the
way
to the lef
throu
eas
gh r ight ye,
ily
if twee
e )
gh
both
is
is
ey es
in rais
in
correct
ed
of
positio
roove
e a
rm
to
bottom
and
push
doubl
ed e
point
LOOPER.
nd
of threa
of twe
REMOVE
tin
g
on
een
low
er
throu
gh
of fabric
t;
zer s
loop
er
n.
positio
n
of the
of
throu
gh
d
ezer
s.
Lower
Thr adi
through
the
needle
back
eye
needl
to
of
e (H)
Tu
Pass
throu
gh
Th
nurl
k
se
ed t ens
cur
e pr ope r
TO
THREAD
ne
edle
ng
from
both
left
eyes
thread
the left
needle.
from
to
Raisin
front.
TO THREAD
r n h
andwheel in
ov
er edge nee
hole
in
top
e a
mount
ion
of
nuts
stit
401
NEEDLE
arm
to
bottom
to rig
ht,
of needle
cam
pull-off
the
top eye
g ne
edle
OVEREDGE
operatin
dle
thread
of stroke, turning
pass the doubled e
thread
(N), then
of needle arm eyelet (Y)
by
NEEDLE (Th
g d
(#
4)
cover needle threa
TH
tension
(AA,
ch
formation.
on the need
Fig. 1 ). T
Usin
(Thread No.
pull-o
rotatin
ire
ction until
und
d eyelet
READ
ension
g a post
ff
eye
throu
g ha
ndwhe
read No. 4-
er ove
TENSION
le and
on
6
3-
Red
handwheel
nd
of
let
(W),
gh n
eedle thread
passing over the
into
el i n
operatin
the needle
rhanging arm
(Z).
loop
Thread needle (H)
er thr
the threads
al
scal
e,
the
Color Code)
in ope
ratin
g dir e
ction.
the 401 needle thread (#
outside
frame eyelet
lower
Green
is
at its
of
eads
should
eye
g di
rection,
Color Cod
hig
top
cov
is reg
be
measurement
and
hest pos
er a nd down
ulat
only
(X)
finally
thread
e)
ition.
from
ed
front.
by
enough to
s a r e t
and
the
aken
3)
of
to
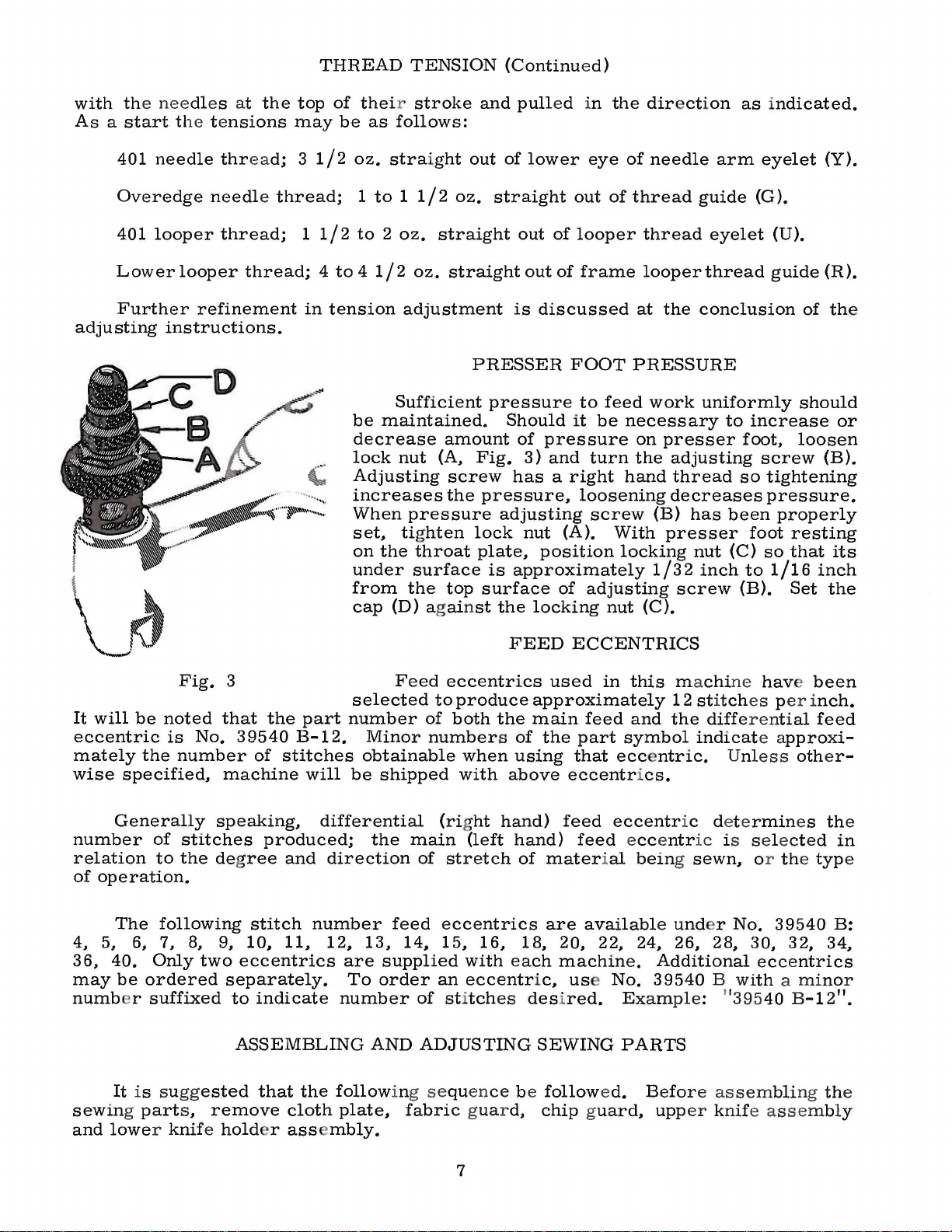
THREAD
TENSION
(Continued)
with
the
As a start
401
Overedge
401
Lower
Further
adjusting
needles
the
needle
at
tensions
thread;
needle
looper
thread;
looper
refinement
instructions.
the
top
of
may
be
3
112
thread;
1
112
thread; 4 to
in
tension
their stroke
as
follows:
oz.
straight
1
to
1 1 I 2
to 2 oz.
4 1 I 2
oz.
adjustment
Sufficient
be
maintained.
decrease
lock
nut
Adjusting
increases
When
set,
on
under
from
cap
pressure
tighten
the
the
(D) ag
throat
surface
and
out
oz.
straight
straight
PRESSER
pressure
amount
(A,
Fig.
screw
the
pressure,
lock
plate,
is
top
surface
ainst
pulled
of
lower
straight
out
out
is
out
of
looper
of
frame
discussed
FOOT
to
Should
of
3)
it
pressure
and
has a right
loosening
adjusting
nut
(A).
position
approximately
of
the
locking
in
the
direction
eye
of
of
thread
thread
looper
at
PRESSURE
feed
work
be
necessary
on
turn
the
hand
screw
With
locking
adjusting
nut
(C).
needle
guide
the
conclusion
presser
adjusting
thread
decreases
(B)
has
presser
nut
1132
screw
as indicated.
arm
eyelet
(G).
eyelet
thread
(U).
guide
uniformly
to
increase
foot,
screw
so
tightening
pressure.
been
foot
(C)
so
inch
to
1116
(B).
(Y).
(R).
of
the
should
loosen
(B).
properly
resting
that
its
inch
Set
the
or
Fig.
It
will
be
noted
eccentric
mately
wise
is
the
number
specified,
No.
Generally
number
relation
of
operation.
4. 5, 6,
36,
may
The
40.
be
of
stitches
to
the deg
following
1.
a. 9,
Only
two
ordered
numb r suffixed
It
is
suggested
sewing
and
parts.
lower
knife
3
that
the
part
39540
of
stitches
B-12.
machine
speaking,
produced;
ree
and
stitch
10.
11.
eccentrics
separately.
to
indicate
ASSEMBLING
that
the
remove
hold
cloth
er
assembly.
selected
number
Minor
obtainable
will
be
differential
the
direction
number
12. 13,
are
To
number
AND
follow
plate,
Feed
to
of
numbers
shipped
main
of
feed
14,
supplied
order
an
of sti
ADJUSTING
ing sequ
fabric
FEED
eccentrics
produce
both
the
when
with
(right
above
hand)
(left
stretch
eccentrics
15, 16.
with
each
eccentric,
tches
ence
guar
d,
ECCENTRICS
used
in
approximately
main
of
using
the
feed
part
that
eccentrics.
feed
hand)
of
1a.
feed eccentr
material
are
available
20.
22. 24.
machine.
use No.
desired.
SEWING
be
follow
ed.
chip guard,
this
m a
chi
ne
12
stitches
and
the
differential
symbol
eccentric.
eccentric
bein
indicate
ic
g
sewn,
Unless
determin
is
selected
or the
und r No.
26,
28,
30,
Additional
eccentrics
39540 B with a minor
Example: 1139540
PARTS
Before
upper
assem
knife assem
have been
per inch.
feed
approxi-
other-
es
the
in
type
39540
B:
32, 34.
B-12".
bling the
bly
7
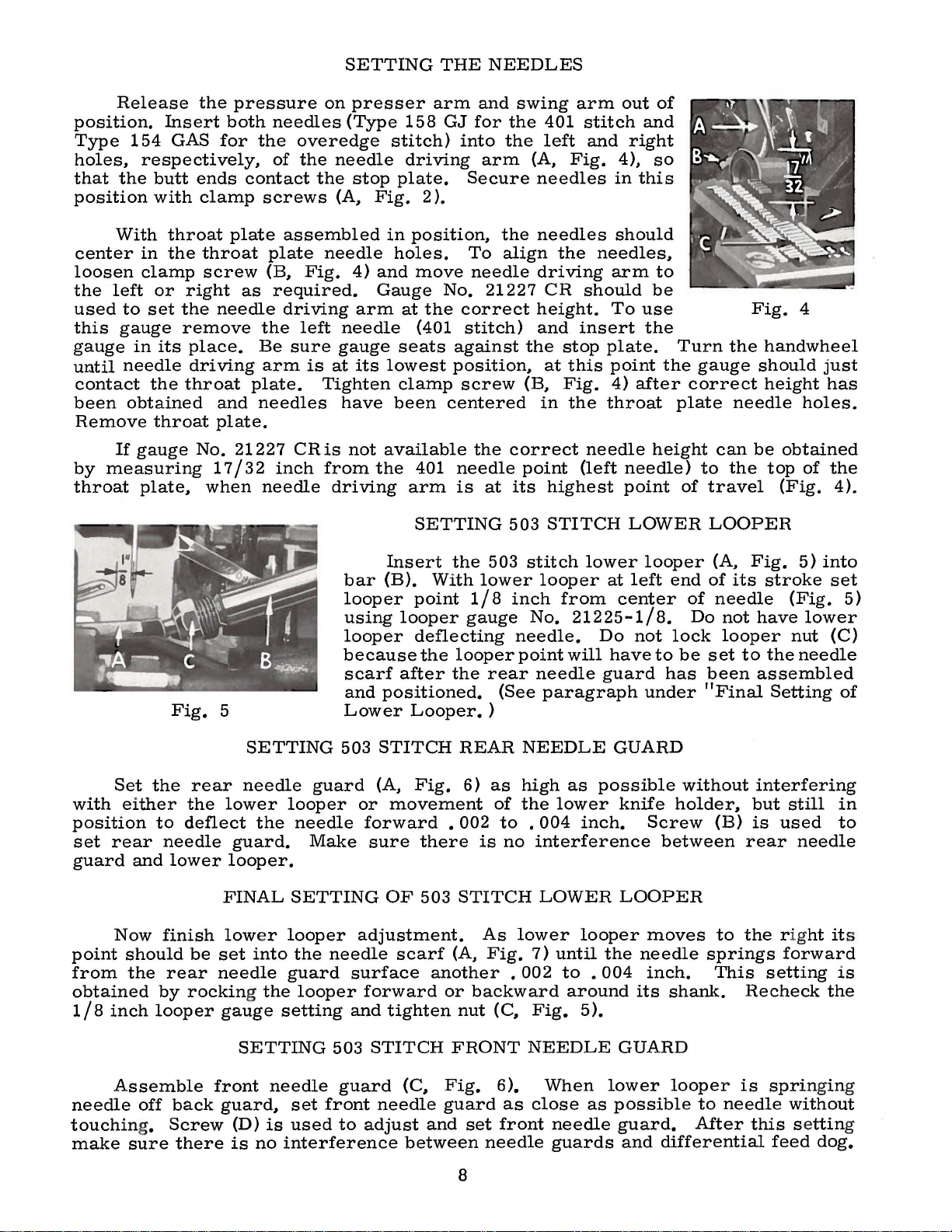
SETTING
THE
NEEDLES
Release
position.
Type
154
holes,
that
the
position
With
center
loosen
the
left
used
this
gauge
until
to
gauge
in
needle
contact
been
obtained
Remove
If
gauge
by
measuring
throat
the
pressure
Insert
GAS
both
for
respectively,
butt
ends
with
clamp
throat
in
the
clamp
or
set
the
plate
throat
screw
right
needle
remove
its
place.
driving
the
throat
and
throat
plate.
No.
21227
17/32
plate,
when
needles
the
of
contact
screws
assembled
plate
(B,
as
required.
driving
the
Be
arm
plate.
needles
inch
needle
on
presser
(Type
overedge
the
needle
the
(A,
needle
Fig.
left
needle
sure
is
gauge
at
Tighten
have
CR
is
not
from
driving
stop
Fig.
in
4)
and
Gauge
arm
its
lowest
available
the
arm
158
GJ
stitch)
driving
plate.
2 ).
position,
holes.
move
No.
at
the
(401
seats
clamp
been
401
arm
SETTING
and
for
the
into
the
arm
Secure
the
To
align
needle
21227
correct
stitch)
against
position,
screw
centered
the
needle
is
at
503
swing
401
left
(A,
needles
needles
the
driving
CR
height.
and
the
at
(B,
in
correct
point
its
highest
STITCH
arm
stitch
and
Fig.
should
insert
stop
this
Fig.
the
needle
(left
out
and
right
4),
so
in
this
should
needles,
arm
to
be
To
use
the
plate.
point
4)
after
throat
height
needle)
point
LOWER
of
the
plate
Turn
gauge
correct
to
of
travel
LOOPER
the
needle
can
the
Fig.
4
handwheel
should
height
holes.
be
obtained
top
of
(Fig.
just
has
the
4).
Set
with
either
position
set
rear
guard
and
Now
point
from
should
the
obtained
1/8
inch
Fig.
the
rear
the
to
deflect
needle
lower
finish
be
rear
by
rocking the
looper
5
SETTING
needle
lower
the
guard.
looper.
FINAL
low
er
set
into
needle
gauge
bar
looper
using
looper
because
scarf
and
Lower
503
guard
looper
needle
Make
SETTING
looper
the
needle
guard
looper
setting
Insert
(B).
point
looper
deflecting
the
after
positioned.
Looper.
STITCH
(A,
Fig.
or
movement
forward
sure
OF
there
503
adjustment.
scarf
surface
forward
and
tighten
the
503
stitch
With
lower
1/8
gauge
looper
inch
No.
needle.
looper
the
rear
(See
point
needle
paragraph
)
REAR
6)
• 002
STITCH
(A,
NEEDLE
as
high
of
the
to . 004
is
no
As
lower
Fig.
interference
LOWER
7)
another • 002
or
backward
nut
(C,
Fig.
lower
at
from
center
21225-1/8.
Do
will
have
guard
GUARD
as
possible
lower
knife
inch.
LOOPER
looper
until
the
to • 004
around
5).
looper
left
not
to
has
under
Screw
between
moves
needle
inch.
its
(A,
end
of
of
Do
lock
be
set
been
"Final
without
holder,
springs
shank.
Fig.
its
needle
not
have
looper
to
assembled
interfering
but
(B)
is
rear
to
the
This
Recheck
5)
stroke
(Fig.
lower
nut
the
needle
Setting
still
used
needle
rig
ht its
forward
setting
into
set
5)
(C)
of
in
to
is
the
Assemble
needle
touchin
make
off
g.
sure
back
Screw
there
SETTING
front
guard,
(D)
is
no
needle
is
interference
set
used
503
guard
front
to
STITCH
(C,
needle
adjust
between
FRONT
Fig.
guard
and
8
set
needle
NEEDLE
6).
as
close
front
When
needle
guards
GUARD
lower
as
possible
guard.
and
looper
to
is
needle
After
differential
springin
without
this settin
feed
dog.
g
g
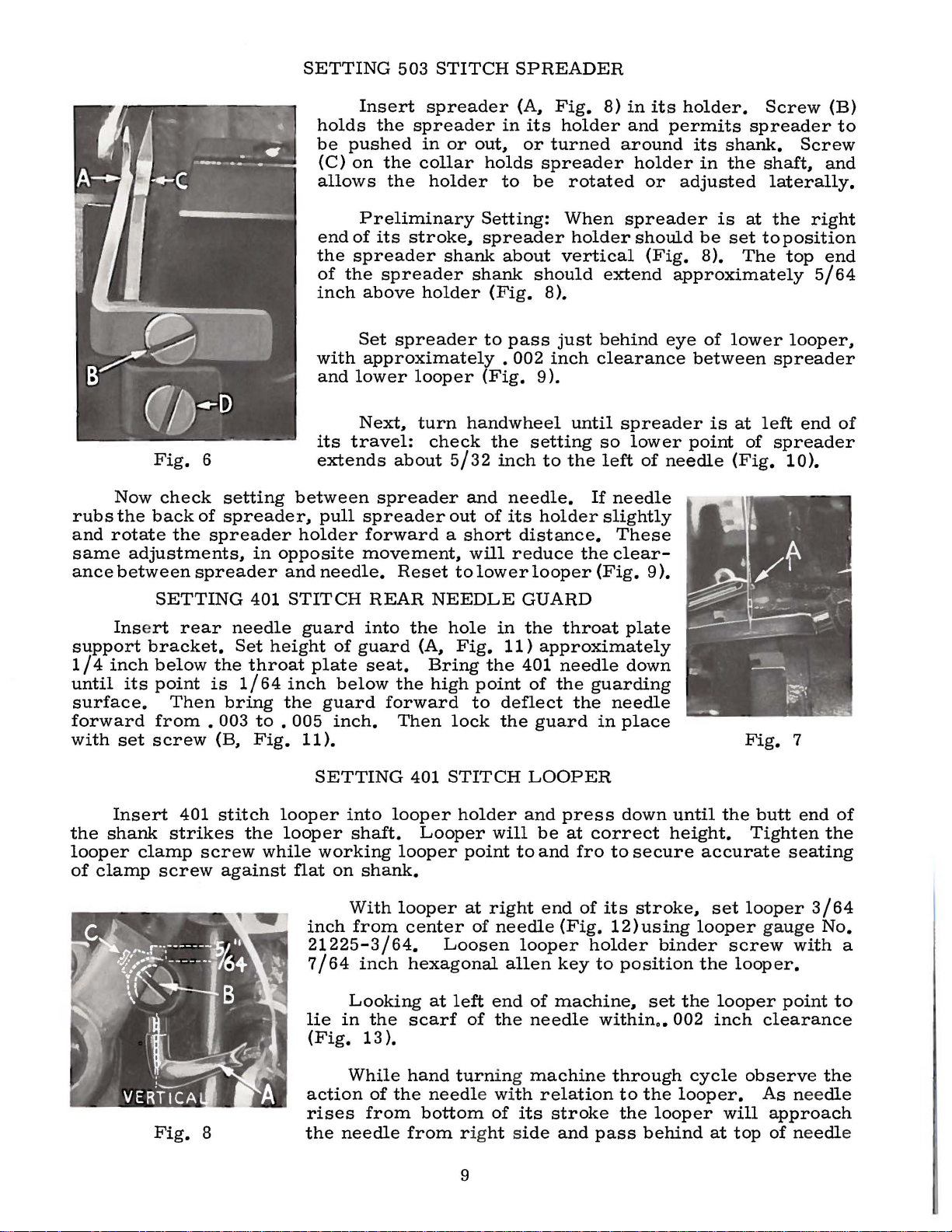
SETTING
503
STITCH
SPREADER
rubs
and
same
ance
Fig.
Now
check
the
back
rotate
the
adjustments,
between
6
setting
of
spreader,
spreader
in
spreader
holds
be
(C)
allows
end
the
of
inch
with
and
its
extends
between
pull
holder
opposite
and
needle.
Insert
the
pushed
on
Preliminary
of
its
spreader
the
above
Set
spreader
spreader
in
the
collar
the
holder
stroke,
shank
spreader
holder
spreader
or
out,
shank
holds
Setting:
spreader
(Fig.
to
approximately • 002
lower
Next,
travel:
spreader
looper
turn
check
about
spreader
(Fig.
handwheel
the
5/32
inch
and
out
of
forward a short
movement,
Reset
will
to
lower
(A,
in
its
or
spreader
to
be
about
should
8).
pass
9 ).
setting
to
needle.
its
holder
distance.
reduce
looper
Fig.
holder
turned
rotated
When
holder
vertical
just
inch
until
the
If
the
8)
in
its
and
around
holder
or
spreader
should
(Fig.
extend
behind
eye
clearance
spreader
so
lower
left
of
needle
needle
slightly
These
clear-
(Fig.
9 ).
holder.
permits
its
in
adjusted
is
be
8).
Screw
spreader
shank.
the
shaft,
laterally.
at
set
to
The
the
approximately
of
lower
between
is
point
at
of
spreader
left
spreader
(Fig.
(B)
to
Screw
and
right
position
top
end
5/64
looper,
end
of
10).
Insert
support
1/4
inch
until
its
surface.
forward
with
set
Insert
the
shank
looper
of
clamp
SETTING
rear
bracket.
below
point
Then
from
screw
401
strikes
clamp
screw
needle
Set
the
is
1/64
bring
• 003
(B.
stitch
screw
against
401
STITCH
height
throat
inch
the
to • 005
Fig.
looper
the
looper
while
flat
REAR
guard
plate
of
into
guard
seat.
below
guard
forward
inch.
11).
SETTING
into
shaft.
working
on
shank.
With
inch
from
21225-3/64.
7/64
inch
Looking
lie
in
the
(Fig.
13
).
NEEDLE
the
hole
(A,
Bring
the
high
Then
401
STITCH
looper
Looper
looper
looper
center
Loosen
hexagonal
at
scarf
Fig.
the
point
to
lock
holder
point
at
of
left
of
GUARD
in
the
11 )
401
of
deflect
the
LOOPER
and
will
to
right
needle
looper
allen
end
the
throat
plate
approximately
needle
the
the
guard
press
be
at
and
end
(Fig.
fro
of
down
guarding
needle
in
place
down
correct
to
its
12)using
holder
key
to
position
of
machine,
needle
within
until
height.
secure
stroke,
binder
set
••
002
the
accurate
set
looper
the
the
looper
inch
Fig.
butt
Tighten
looper
gauge
screw
looper.
clearance
7
end
the
seating
3/64
No.
with
point
of
a
to
Fig.
8
action
rises
the
needle
While
of
the
from
hand
turn
needl
bottom
from rig
9
ing
e wi
th
of
ht side
machine
relation
its
stroke
and
through
to
the
pass
cycle
the
looper.
looper
behind
will
at
observe
As nee
approach
top
of needl
the
dle
e
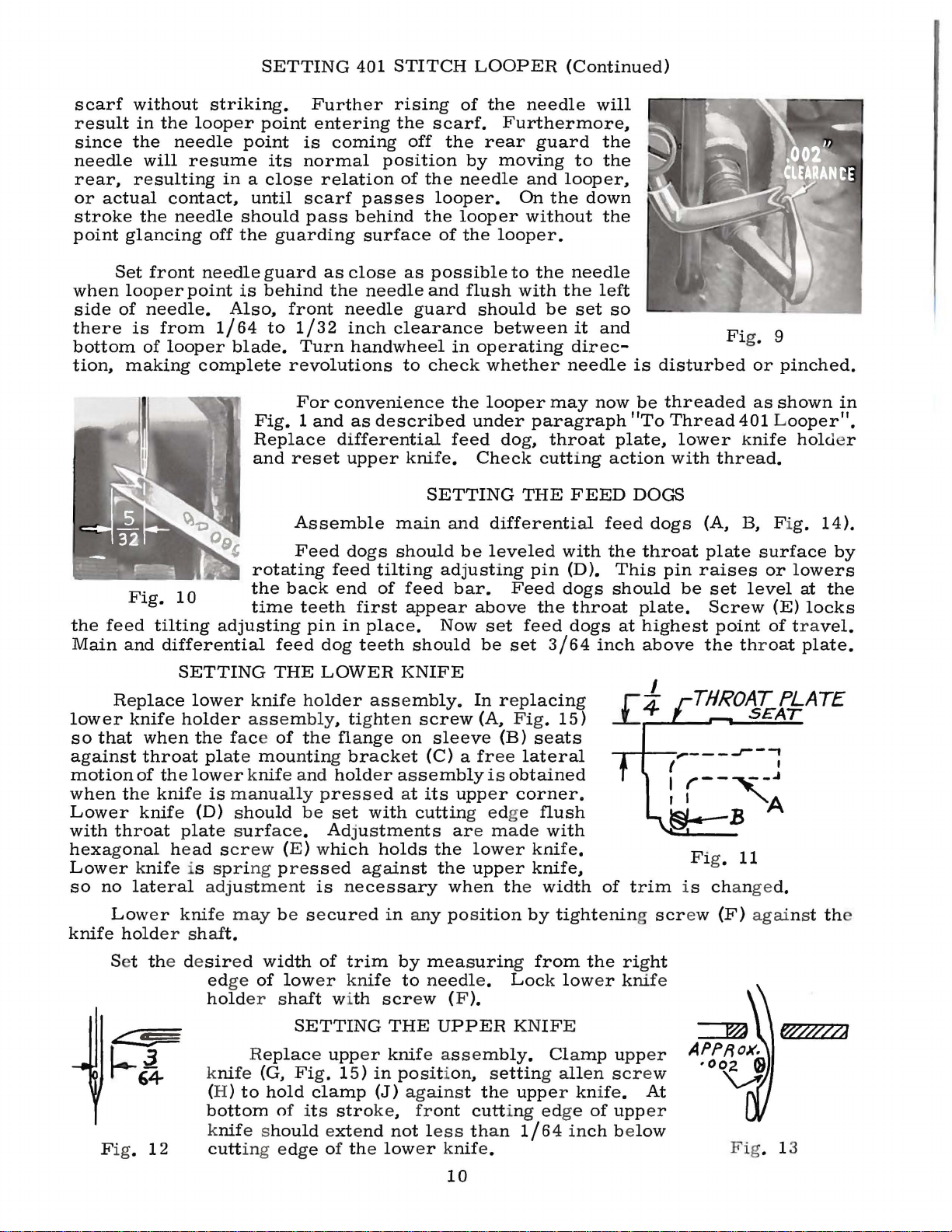
SETTING
401
STITCH
LOOPER
(Continued)
scarf
result
since
needle
rear,
or
actual
stroke
point
Set
when
side
of
there
bottom
tion,
the
feed
Main
without
in
the
the
needle
will
resulting
contact,
the
needle
glancing
front
looper
needle.
is
from
of
looper
making
Fig.
10
tilting
and
differential
striking.
looper
point
resume
in a close
should
off
the
needle
point
is
Also,
1/64
blade.
complete
adjusting
Further
point
entering
is
its
normal
relation
until
scarf
pass
guarding
guard
as
behind
front
to
1/32
Turn
revolutions
For
Fig. 1 and
Replace
and
reset
Assemble
Feed
rotating
the
back
time
teeth
pin
feed
dog
rising
the
coming
off
position
of
passes
behind
surface
close
the
needle
inch
as
needle
guard
clearance
handwheel
to
convenience
as
described
differential
upper
knife.
main
dogs
feed
end
in
tilting
of
first
place.
teeth
should
feed
appear
should
of
the
needle
scarf.
the
the
looper.
the
of
possible
and
Furthermore,
rear
by
moving
needle
looper
the
looper.
to
flush
and
On
without
with
should
between
in
operating
check
the
whether
looper
under
feed
dog,
Check
SETTING
THE
and differential
be
leveled
adjusting
bar.
Feed
above
Now
set
feed
be
set
will
guard
to
looper,
the
down
the
needle
the
left
be
set
it
and
direc-
needle
may
now
paragraph
throat
cutting
FEED
with
pin
(D).
dogs
the
throat
dogs
3/64
inch
the
the
the
so
is
be
"To
plate,
action
DOGS
feed
the
This
should
plate.
at
disturbed
threaded
Thread
lower
with
dogs
throat
pin
be
highest
above
Fi
thread.
(A,
plate
raises
set
Screw
point
the thr
g. 9
or
as
401 L
knife
B,
surface
or
level
(E)
of tra
oat
pinched.
shown
ooper".
hold
Fi
g.
14).
lowers
at
the
locks
vel.
plate.
in
er
by
SETTING
Re
place
lower
so
knife
that
against
motion
of
when the
Lower
with
knif
throat
when
throat plat e
low
holder asse m
the
the
low
knife is man
e (D) s
plate surf
hexagonal head
Low
er k
nif
e i s spr i
so
no
lateral
Low
er
knife may
knife hold
er shaf
Set the de
Fig.
12
er
knife hol
THE
LOWER
der assembly.
bly, tight
face
of
the fla
mounting brack
er k
nif
scr
e and
ually pre
hould
ace.
ew
(E ) w
be
hold
set
Ad
hich
sse
jus
ng pressed against
adj
ust
ment is necessary
be s e
cur
ed
t.
sir
ed
width
ed
ge
of
hold
er shaft with
low
of
er
trim
kni
SETTING
R
ni
fe
k
to
(H)
bottom
nif
e s
k
eplace upp
(G,
Fi
hold
clamp
of its
hould extend
er
g. 15) in posi
stroke, front
cutting edge of the
KNIFE
In rep
en
nge
screw
on
sleeve
(A, Fig.
(B)
et (C) a free
er as
d at
with
tments
holds
sembly
its
cuttin
the
the
is
upp
er
g edge
ar
e made
low
upp
when the
in any pos
by
measuring from
fe
to needle.
scr
ew (F ).
THE
knif
e assembly.
(J)
against the upper kn
ition
UPPER
tion, s
ettin
cutt
not less than
low
er k
nif
e.
lacing
15)
seats
lateral
obtained
corner.
flush
with
er
knife.
er
knife,
width
by
tightening scr
Lock low
KNIFE
Clamp
g allen
ing edge
1/64 in
-r--t-
___
of
trim
the rig
er
kni
ht
fe
upper
scre
w
ife .
of
upp
At
er
ch below
,_--
( I
1
I I
~-.,
r--,--.J
.""A
~B
Fi
g. 11
i s changed.
ew
(F)
agai
Fig
. 13
nst the
10
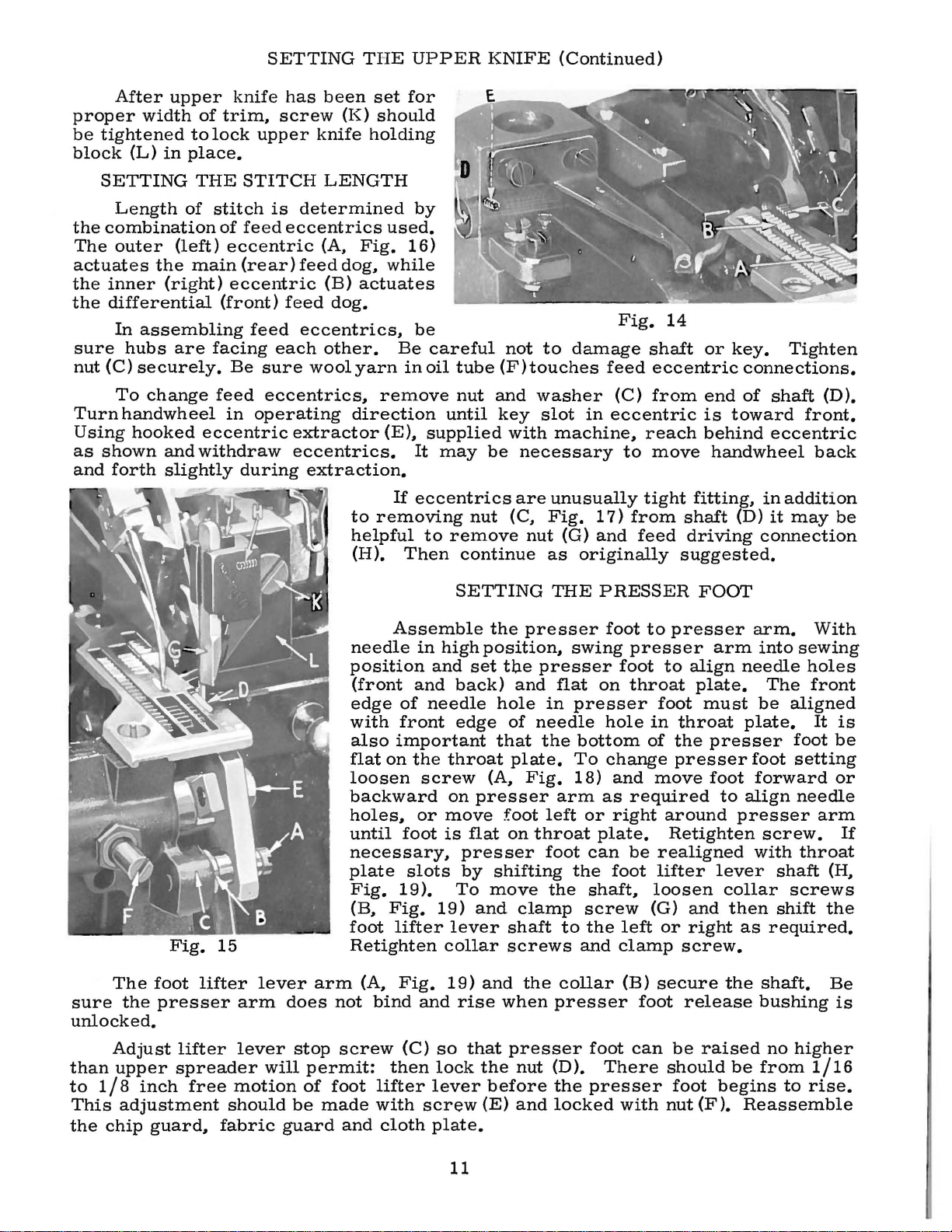
SETTING
THE
UPPER
KNIFE
(Continued)
After
proper
be
tightened
block
the
The
actuates
the
the
sure
nut
Turn
Using
as
and
(L)
SETTING
Length
combination
outer
inner
differential
In
hubs
(C)
To
handwheel
hooked
shown
forth
upper
width
assembling
securely.
change
of
to
in
place.
THE
of
(left)
the
main
(right)
are
and
withdraw
slightly
lock
stitch
facing
feed
eccentric
knife
trim,
upper
STITCH
is
of
feed
eccentric
(rear)
eccentric
(front)
feed
each
Be
sure
eccentrics,
in
operating
during
has
been
screw
eccentrics
feed
extractor
eccentrics.
(K)
knife
LENGTH
determined
(A,
feed
dog,
(B)
dog.
eccentrics,
other.
wool
extraction.
set
for
should
holding
by
used.
Fig.
actuates
yarn
direction
to
helpful
(H).
16)
while
be
Be
in
remove
(E),
It
If
eccentrics
removing
Then
careful
oil
tube
nut
until
supplied
may
nut
to
remove
continue
not
to
(F)touches
and
washer
key
slot
with
machine,
be
necessary
are
unusually
(C,
Fig.
nut
as
Fig.
damage
feed
(C)
in
eccentric
17)
(G)
and
originally
shaft
eccentric
from
reach
to
move
tight
from
feed
14
or
key.
end
is
toward
behind
handwheel
fitting,
shaft
driving
suggested.
Tighten
connections.
of
shaft
eccentric
in
(D)
it
connection
(D).
front.
back
addition
may
be
The
sure
unlocked.
the
Fig.
foot
lifter
presser
15
lever
arm
arm
does
Assemble
needle
position
(front
edge
with
also
important
flat
on
loosen
backward
holes,
until
necessary,
plate
Fig.
(B,
Fig.
foot
lifter
Retighten
(A,
not
bind
in
and
of
needle
front
the
screw
or
foot
slots
19).
Fig.
and
SETTING
high
position,
and
set
back)
edge
throat
on
presser
move
is
flat
presser
by
To
19)
and
lever
collar
19)
and
rise
the
presser
tbe
and
hole
of
needle
that
plate.
(A,
Fig.
foot
on
throat
shifting
move
clamp
shaft
screws
the
when
THE
swing
presser
flat
in
presser
the
bottom
To
18)
arm
left
or
foot
can
the
the
shaft,
screw
to
the
and
collar
presser
PRESSER
foot
to
presser
presser
foot
to
on
throat
foot
hole
in
of
change
and
move
as
required
right
plate.
foot
be
realigned
lifter
loosen
(G)
left
clamp
(B)
secure
foot
around
Retighten
or
FOOT
arm
align
plate.
must
throat
the
presser
presser
foot
to
lever
collar
and
right
screw.
the
release
arm.
into
needle
The
be
plate.
foot
forward
align
presser
screw.
with
then
as
required.
shaft.
bushing
With
sewing
holes
front
aligned
It
foot
setting
needle
throat
shaft
screws
shift
is
be
or
arm
If
(H,
the
Be
is
than
to
This
the
Adjust
upper
1/8
adjustment
chip
inch
guard,
lifter
spreader
free
lever
motion
should
fabric
will
guard
stop
permit:
of
be
made
screw
foot
and
(C)
then
lifter
with
cloth
so
lock
lever
screw
plate.
11
that
the
before
(E)
presser
nut
(D).
the
and
locked
foot
can
There
presser
with
be
raised
should
foot
nut
(F).
no
be
from
begins
Reassemble
higher
1/16
to
rise.
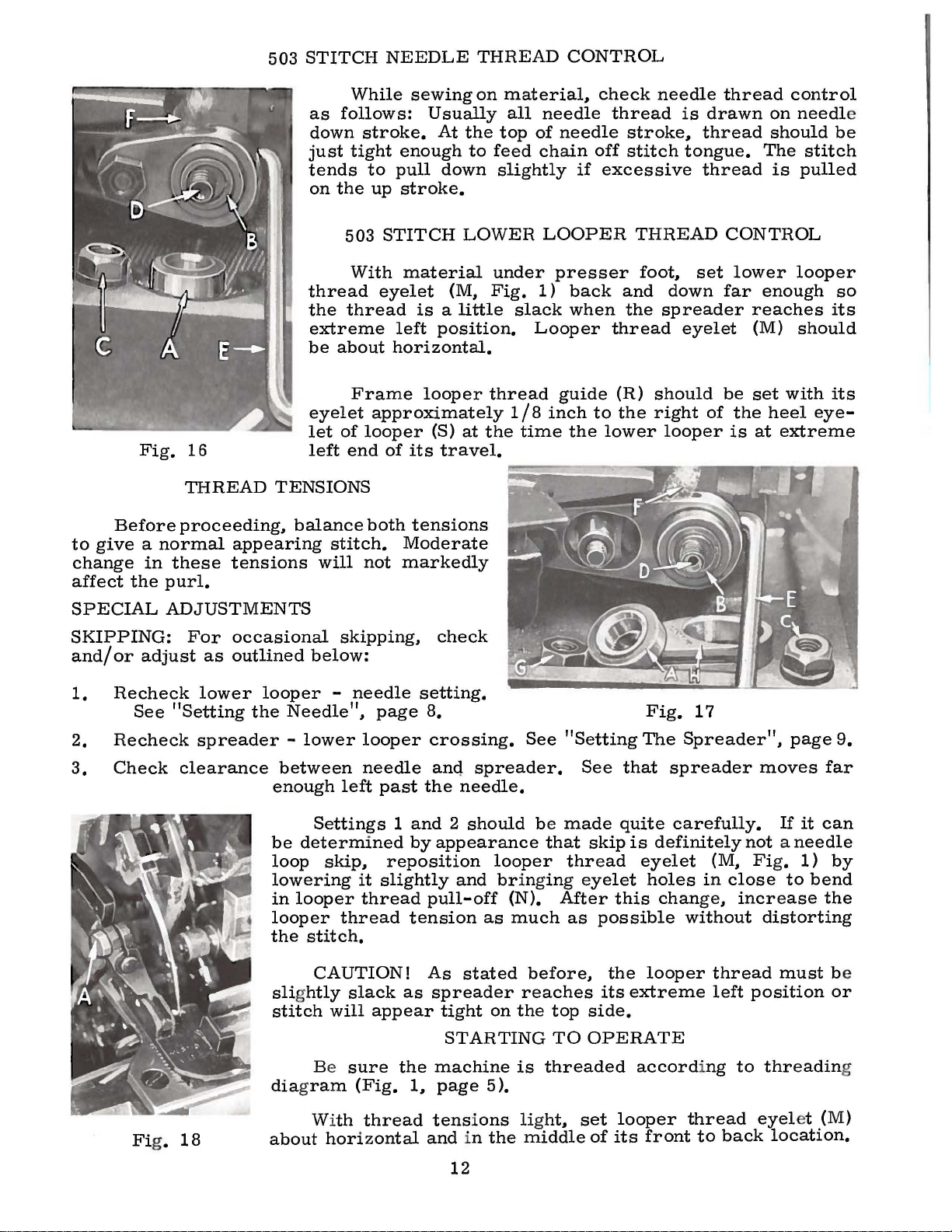
503
STITCH
NEEDLE
THREAD
CONTROL
Fig.
Before
to
give a normal
change
affect
in
the
16
THREAD
proceeding,
appearing
these
tensions
purl.
While
as
follows:
down
just
stroke.
tight
tends
on
the
503
With
thread
the
thread
extreme
be
about
Frame
eyelet
let
of
left
end
TENSIONS
balance
stitch.
will
sewing
Usually
At
the
enough
to
pull
down
up
stroke.
STITCH
LOWER
material
eyelet
(M,
is a little
left
position.
horizontal.
looper
approximately
looper
both
of
its
tensions
(S)
at
travel.
Moderate
not
markedly
on
to
thread
the
feed
under
Fig.
slightly
material,
all
needle
top
of
chain
LOOPER
presser
1)
slack
Looper
guide
1/8
inch
time
check
needle
off
if
excessive
back
when
to
the
lower
needle
thread
stroke,
stitch
THREAD
foot,
and
the
thread
(R)
should
the
right
thread
is
drawn
thread
tongue.
thread
set
down
far
spreader
eyelet
be
of
looper
control
on
needl
should
The
stitch
is
pulled
CONTROL
lower
looper
enough
reaches
(M)
should
set
with
the
heel
is
at
extreme
e
be
so
its
its
eye-
SPECIAL
SKIPPING:
and/
or
adjust
1.
Recheck
See
2.
Recheck
3.
Check
ADJUSTMENTS
For
occasional
as
outlined
lower
"Setting
spreader
clearance
looper
the
between
Needle",
-
enough
be
loop
lowering
in
looper
looper
the
slightly
stitch
skipping,
check
below:
-
lower
left
needle
looper
needle
page
past
setting.
8.
crossing.
anq
the
needle.
spreader.
Settings 1 and 2 should
determined
skip,
it
thread
thread
by
appearance
reposition
slightly
pull-off
tension
and
as
stitch.
CAUTION!
slack
will
appear
As
as
spreader
stated
tight
STARTING
See
be
that
looper
bringing
(N).
much
before,
reaches
on
the
"Setting
See
made
skip
thread
eyelet
After
as
possible
top
side.
TO
OPERATE
that
quite
is
this
the
its
extreme
Fig.
The
17
Spreader",
spreader
carefully.
definitely
eyelet
holes
change,
without
looper
not a needle
(M,
in
close
increase
thread
left
position
page
moves
If
it
Fig.
to
1)
bend
distorting
must
9.
far
can
by
the
be
or
Be
Fi
g.
18
diagram
Wi
about
horizontal
sure
th
(Fig.
thread
the
machine
1,
page 5 ).
tensions lig
and
in
12
the
is
threaded
ht,
middle
set
of
according
looper
its
front
thread
to
back
to
threadin
eyel
g
et (M)
location.

STARTING
TO
OPERATE
(Continued)
inch.
and
Set
then
needle
bring
is a starting
described
corner
of
the
SETTING
If
looper
refer
to
the
Cast-off".
20)
7/32
several
while
direction
thread
thread
Fig.
inch
feet
checking
until
straight
eyelet,
1)
to 1 1/2
Fig.
position
under
19
thread
it
forward
"Sewing
bed
casting.
401
thread
eyelet
1/8
for
this
Off 401
LOOPER
casting-off
paragraph 11Timing
Set
the
of
looper
below
thread
the
tension.
the
needle
toward
adjust
thread
crotch
through
is
the
tension
to 2 ounces.
(X.
inch,
eyelet.
Thread
THREAD
point
401
of
cast-off
the
Turn
totally
operator,
with
Operate
in
place.
the
tongue
SETTING
Bring
eyelets
paragraph
the
needle.
Position
so
that
needle
ward
to
needle
thread
Fig.
tilt
1)
slightly
Later
Stitch".
needle
EYELETS
has
Stitch
cast-off
blade
looper
to
handwheel
raised.
over
the
knurled
Make
freely.
needle
as
shown
"To
Lower
needle
the
thread
bow
arm
is
will
clear
to
the
it
The
from
not
been
Looper
eyelet
(B).
provide
in
Pulling
the
machine
sure
401
NEEDLE
thread
in
Thread
needle
thread
thread
pull-off
the
needle
at
the
the
rear,
upward
may
tail
front
have
of
to
timed
Thread
(A,
Fig.
Pull
slack
operating
the
looper
nut
(AA,
slowly,
chain
Fig.
401
pull-off
is
at
cam
thread
top
pull-off
against
and
to
the
back.
forms
THREAD
through
1
and
Needle".
to
bottom
the
middle
(N)and
of
its
cam
the
tighten
be
adjusted
eyelet
with
presser
and
EYELETS
its
as
described
Do
of
eyelet
mark
far
slightly.
stroke,
by
mounting
the
screw.
may
Fig.
moves
respective
not
thread
its
stroke.
(W,
Fig.
of
enough
When
the
needle
about
1/32
screw,
This
slightly
rest
on
20
foot
off
in
1)
the
for-
the
as
the
Final
observing
foot
and
the
needle
formation
overedge
Fig.
adjustments
the
stitch
observe
thread
is
as
shown
needle,
less.
arm
and,
A
desired
at
the
needle
More
The
enters
21
tight
to
formation.
formation
take-up
in
yet
be
round
To
to
top
using
slight
result.
Needle
two
separate
cam
as
thread
needle
needle
the
when
SEWING
the
401
stitch
Insert
of
the
eyelet
Fig.
(W,
21.
and
lower
the
position
needle
movement,
Then
thread
times.
shown
is
drawn
thread
thread
material.
the
needle
OFF
are
two
needle
Fig.
The
loop
full.
eyelet
and
insert
arm
as
of
1/64
retighten
is
drawn
between
as
will
becomes
The
reaches
13
401
made
narrow
loop
upon
1)
by
should
At
full
tap
left
support,
inch
from
Thread
the
the
be
drawn
slack
needle
STITCH
while
plies
the
raising
not
speed
side;
wide
blade
or
the
eyelet
the
is
first
marks
needle
the
just
thread
the
bottom
hand
of
rising
or
touch
the
to
raise
screwdriver
twist
less,
holding
cone
drawn
(A,
Fig.
reaches
first
before
should
of
turning
the
material
of
the
lowering
the
front
loop
will
eyelet
screwdriver
will
usually
screw.
on
the
upstroke
at
the
22).
The
the
top
time,
the
or
eye
become
its
stroke,
machine
under
needle.
it
until
guard
tend
to
bring
under
to
produce
high
second
of
its
at
point 11A".
of
the
snug
and
and
presser
Adjust
the
loop
of
become
needle
eyelet
the
left.
only
and
point
time,
stroke.
needle
but
should
the
the
of
not

SEWING
OFF
401
STITCH
(Continued)
become
is
again
condition
thread
back.
Observe
take-up
The
looper
lobes,
As
the
needle
thread
until
again
nature
amount
slightly
at
occur
The
slack
drawn
it
frame
at
the
slack
will
the
tension
of
the
of
looper
down.
as
from
may
eyelet
the
bottom
thread
from
arm
begin
end
and
material
Use
the
needle
be
necessary
action
is
the
rises
to
of
the
the
of
the
thread
reverse
the
cone.
(X,
of
of
lying
previous
to
tighten
rise,
looper
looper
being
pull-off
raises
to
Fig.
1)
the
the
needle
across
the
top,
across
casting-off
thread
sewn
procedure
until
To
obtain
move
forward
looper
stroke.
the
casting-off.
the
the
will
thread
and
move
is a notch
movement
required,
when
this
developed
tight
up
thread
this
needle
or
thread
cain
looper
cam
will
lie
at
this
the
the
looper
to
obtain
If
the
time
looper
needle
in
the
crotch
position
operation
thread
less
in
the
with a screwdriver.
a
relaxed
the
needle
the
at
pull-off,
thread
loop.
will
performed.
looper
cast-off
looper
looper
is
at
tension
Fig.
of
be
cast-off
thread
blade
thread
thread
the
top
in
the
is
setting
will
interfere
22
the
cast-off
determined
To
increase
blade
(B, Fig.
pull-off.
to
facilitate
in
the
should
of
its
need
the
with
travel.
1 e
blade.
by
There
stitch
be
slack
thread,
stitch.
pulling
the
the
23)
this
is
At
A
When
shaft
vertically
needle
This
checked
the
needle
maintained.
ing-off
the
be
the
(Fig.
needle
the
the
(B,
holding
the
arm
adjustment
and
cam
arm
may
needle
cast-off
looper
24).
will
top
of
time
of
Fig.
screw.
Fig.
TIMING
the
401
cast-off
below
is
in
moved,
functions
shaft
If
this
be
timed.
(A,
Fig.
when
thread
At
this
be
approximately 1 /6 4 inch
front
casting-off,
23)
up
needle
or
23
looper
corner
top
surface
its
highest
is
made
it
as a thrust
and
correct
setting
24),
the
eye
against
position
move
down,
401
STITCH
thread
will
at
must
is
On
the
looper
of
the
the
guard
rotating
-
cam
be
of
the
bed
position
the
factory,
be
observed
collar
thrust
correct
down
thread
looper
left
side of
the
point
(C).
the
cast-off
Only
the
looper
and
eyelet
off
only
from
LOOPER
is
25/32
when
(Fig.
but
for
must
the
cast-
stroke
should
(B)
brings
needle
of
below
To
chan
blade
it
about
enough
thread
system.
during the
left
to
THREAD
correctly
inch
the
20).
if
that
the
be
of
the
ge
its
tension
to
return
right
and
CAST-OFF
positioned
should
resist
Thread
travel
cease
Fig.
friction
should
on
the
24
be
carried
of
be
of
the
at
casting-off.
needle
in
looper
pulled
looper
arm
14

List
this
of
additional
catalog
parts
to a 504
required
stitch
39600
to
convert
machine.
the
503
stitch
39600
machine
covered
in
Part
No.
52 A
107
108
109
376
21101
22565
22768
22849
29477
35792
39508
39568
39568
39663
43139
51292
A
H-6
c
HU
H
A
E
L
H
A
F-5
Description
Frame
Tension
Tension
Eyelet~
Post
Post
for
Ferrule------------------------------------
Nut----------------------------------------
504
needle
thread
----------------------
TensionDisc--------------------------------------------
Screw~
Thread
Screw~
Screw~
Screw~
Upper
Looper
for
upper
Stand~
for
tension
for
504
for
504
Knife
Driving
Thread
looper
thread
eyelet
(39568
complete----------------------------------
post
needle
frame
thread
eyelet
Arm
(35792
pull-off
(52
Thrust
H)
------------------------eyelet
A)------------------------
Block
and
Tube-----------------------------------TensionPost-------------------------------------------Upper
Auxiliary
Upper
Neejle
Nut~
Tension
Looper-------------------------------------------
Eyelet~
Looper
Thread
for
upper
Spring~
for
Thread
Pull-off
looper
for
504
upper
looper---------------------
Eyelet------------------------------
Eyelet~
thread
504
needle
for
eyelet
thread
504
needle
screw
---------------------
L)
------------
(39663
504
Upper
thread--------
(376
A)-----------
H)-------
Amt.
Req.
1
1
1
2
1
1
1
1
1
1
1
1
1
1
1
1
1
ASSEMBLING
The
setting
guards
as
adjustments
used
needle
503
5/32
stitch
in
the
stitch
inch
spreader
to
spreader
and
described
for
the
504
stitch
formation.
dimension
(Fig.
the
point
or
the
adjustment
earlier
504
formation
from
10).
of
the
upper
AND
stitch.
The
the
upper
looper
ADJUSTING
of
the
needles~
for
the
503
Also~
is
similar
exception
center
The
504
looper
to
be
or
line
stitch
(Fig.
taken
Fig.
SEWING
stitch
the
adjusting and
to
the
difference
of
the
measurement
1 OA).
when
lOA
PARTS
lower
are
applicable
setting
needle
The
they
FOR
looper~
setting of
of
the
being
to
is
the
the
taken
measurement
are
at
504
STITCH
front
when
and
making similar
the
spreader
measurement
lower
point
from
the
left
end
rear
upper
used
the
for
needle
looper
in
of
of
the
center
either
of
travel.
the
the
503
of
the
15

PL529
THREADI
Only the parts involv
Thread fro
r
ig
ht
hand hole an
sl
ot (F
),
and
on throu
It
wi
ll simplify threa
assigned
ea
ch thre
504
N
o.
N
o.
the machin
Pr inted
to each
ad have been
low
er
3, 504 upper
5, ove
No o
A s
loop
red
ili
ng
e.
traight
in
U.S.
ge nee
is
NG
m st a
d up throu
thr
ead, start
er thr e
loop
dle
necessary
Ma
chi
ne
mine
ral
A.
DIAGRAM AND OILING INSTRUCTIONS
ed in thr e
nd
(C)
is
gh thread
colo
ad, yellow
er thr e
gh l
ding the
r c
ad,
threa
other than
is filled with oil
oil
of a Saybolt vis
ading are s
threaded
eft
hand
guid
e
machine
ing
oded
d, green
with
to
color
black
throu
hol
lG
further
keeping
e.
).
to
thread
aid
code; thread
color
code; thread
color
code.
at
spring cap
cosity
hown
gh e
ach
Then thr
follow
No.
the
the
red
of
in the a
pair
ead
recommended
1.
The
thr
eading
No. 2, 401
No.
bulb
in
top
200
to
FOR
bove diagram.
of
holes
continues
various eyelets an
proce
loop
4, 401 nee
between
cover.
250 s
econds
CLASS 3
in
tension
between tension dis
sequence
ss.
Thus the sequence
er
the
lines
at
UNION SPE
9600
thread
as des
d g
thread, blue
dle
thre
ad, red color code;
of the
100° Fahrenheit
CIAL
Chicago,
(504
STITCH)
guide
wir e (D
cs (E
),
igna
ted
by
the
uides
on
the
machine for
is:
thread
color
oil gauge
MACHINE COMPANY
illinois
code;
on
the
should
60610
),
down
throu
number
No. 1,
thread
thread
front
be
used.
gh
s
of

TO
REMOVE
CRANKSHAFT
Crankshaft
1.
Drain
of
base.
2.
Remove
3.
Remove
eccentric
4.
Remove
5.
Remove
be
6.
Remove
through
7.
Remove
assembling
marks
on
the
same
can
be
oil
by
removing
top
and
the
feed
extractor,
key
(H).
two
counterweights
reassembled
screw
bottom
caps
bearing
are
stamped
same
holes
side
from
withdrawn
plug
bottom
eccentric
slip
in
the
(K)
which
of
bed
casting.
of
bearings
caps
on
of
the
which
more
screw
covers
nut
off
the
(J).
proper
holds
on
make
both
halves
bearings.
they
were
Fig.
easily
if
located
of
machine.
and
washer
eccentrics
Identify
place.
crankshaft
crankshaft
sure
they
of
the
Also,
removed.
17
25
these
on
these
split
at
are
screws
back
(F#
(G).
points
in
caps
steps
Fig.
are
of
machine
25} and#
followed:
counterweights
bearing.
their
and
should
A,
B, D and
original
both
This
trademarks
be
near
with
screw
so
bottom
the
that
is
E.
aid
When
position.
should
reassembled
edge
of
they
will
reached
re-
Trade-
in
the
be
the

B
TO
REMOVE
CRANKSHAFT
(Continued)
G
8.
9.
10.
11.
12.
13.
14.
Crankshaft
15.
If
press.
against
16.
Carefully
sembly
parts
Loosen
up.
Loosen
upper
driving
drop,
on
in
Remove
screw
Loosen
Remove
Loosen
Remove
collars
allowing
crankshaft.
paragraph
necessary
and
clamp
knife
arm
screw
is
reached
two
screw
two
three
(V)
and
may
In
replacing
ground
observing
of
crankshaft.
constant
screw
screw
driving
to
the
removal
Observe
7.
(L,
screws
(N);
screws
screws
(W)
now
to
replace
thrust
(A,
(B);
arm
left
until
Fig.
through
(M)
in
take
(R);
(T);
may
be
removed.
ball
the
washer
reverse
Checking
testing
Fig.
swing
(D).
of
same
25)
off
remove
be
bearing it
26)
eyelet
Access
upper
bearing
precautions
which
bottom
fan
collar;
pulley
take
removed
bearing
(X).
of
for
binds
the
exploded
Fig.
which
up.
to
knife
cap
holds
of
bed
cap
pulley
off
bearing
at
(Y),
must
foregoing
during
26
holds
Loosen
clamp
driving
(G).
This
when
inner
casting.
remove
(P).
(S).
this
time.
it
can
be
pressed
view
reassembly
eyelet
nut
lever
right
both
retaining
be
operations
drawings
bracket
clamp
is
(E)
is
at
reassembling
crankshaft
halves
pressed
on
nut
through
and
bearing
of
plate
off
carefully
should
for
will
and
swing
(C)
which
top
cover.
connecting
point
cap
cooling
(U);
shaft
location
also
(C,
as
bearing.
also,
on
until
simplify
prove
bracket
holds
Draw
rod
Fig.
described
This
fan.
spacer
an
arbor
it
seats
reas-
of
various
helpful.
the
(F)
25)
17.
Before
gaskets.
wick
that
cover.
prevent
reassembling,
Before
which
it
lubricates
contacts
Coat
oil
the
leakage.
thoroughly
reassembling
left
shaft.
oil
The
drain
No. 1 Crane
bottom
crankshaft
wick
plug
stands
with a sealing
clean
bearing
Lead
and
dry
cover
vertically
Seal
the
make
is
inserted
compound
is
recommended.
18
top
sure
on
that
its
before
and
in
hole
spring
bottom
spring
reassembling
covers
pressed
in
casting
against
and
oil
and
bottom
to

ILLUSTRATIONS
This
catalog
of
various
actual
listing
quired
sections
position
of
the
in
the
parts
particular
in
has
the
been
of
the
machine.
with
ORDERING
arranged
mechanism
their
view
part
being
to
simplify
are
On
the
numbers,
shown.
REPAIR
ordering
shown
page
opposite
description
PARTS
so
that
repair
the
parts
the
illustration
and
parts.
the
may
be
number
Exploded
seen
will
be
of
pieces re-
views
in
their
found
a
Numbers
position
ordering
Component
cated
Example:
25
26 22559 A
The
complete
be
all
this
part
too
tinguish
by
29126 CG
It
will
reason
Where
shown
machines
At
the
book.
number
Where
small
in
of
that
parts.
indenting
be
noted
is
sub-assembly
parts
in
the
covered
back
This
is
the
for a complete
one
part
the
first
part
in
the
Always
parts
that
illustrations
of
known.
construction
of
their
Spreader
in
the
replacement
should
for
Styles
by
the
book
will
facilitate
from
another
sub-assemblies
descriptions
colunm
illustration.
use
Screw,
above
39600 A and
this
permits.
catalog
are
the
part
example
of
be
or
mentioned
catalog
will
be
locating
IDENTIFYING
that
reference
Reference
number
under
Drive
these
ordered.
stamping
Lever
for
connecting
parts
39600
no
machine
found a numerical
each
is
similar
listed
which
the
that
in
the
the
illustration
part
are
numbers
numbers
in
the
can
be
furnished
description
and
Connecting
rod
assembly
the
ball
stud
individually
Pare
PARTS
is
identified
in
not
descriptions.
style
stamped
appearance.
will
only,
second
and
is
the
be
index
and
with
by
and
merely
should
colunm.
for
of
the
main
Rod
Assembly------
---------------
bearing
not
recommended,
same,
When a part
mentioned.
of
all
description
its
part
letter
symbols
never
repairs
sub-assembly.
are
the
difference
the
parts
when
number.
indicate
be
used
are
not
listed.
so
is
used
shown
only
Parts
which
the
in
indi
- - 4
the
will
in
in
the
dis-
-
1
Part
IMPORTANT!
OF
MACinNE
Success
Special
its
scientific
durability
parts
of
the
are
wise
Needles
subsidiaries
Genuine
are
highest
Prices
forwarded
directed.
numbers
FOR
in
the
principles.
are
assured.
needles
stamped
quality
are
strictly
f.
A
represent
ON
WHICH
USE
operation
and
Repair
and
authorized
are
with
in
o.
b.
shipping
charge
the
ALL
and
the
net
ORDERS.
PART
GENUINE
of
Parts
are
packaged
Union
materials
cash
is
made
same
these
distributors.
made
Special
and
point.
part.
IS
ORDERED.
NEEDLES
machines
as
furnished
with
with
and
workmanship.
subject
Parcel
to
cover
regardless
PLEASE
AND
They
utmost
labels
trademark.
TERMS
marked
to
Post
postage
19
INCLUDE
REPAIR
can
be
by
the
Union
are
precision.
Each
change
shipments
and
of
catalog
PART
PARTS
secured
Special
designed
~
trademark
without
are
insurance.
in
which
NAME
only
with
Machine
according
Maximum
•
is
notice.
insured
they
AND
genuine
Company.
to the most
efficiency
Genuine
your
guarantee
All
shipments
unless
appear.
STYLE
Union
and
r e
pair
other-

20

MAIN
FRAME.
MISCELLANEOUS
COVERS
AND
PLATES
Ref.
No.
1
2
3
4
5
6
7
8
9
10
11
12
13
14
15
16
17
18
19
20
21
22
23
24
25
26
27
28
28A
29
30
31
32
33
34
35
36
37
38
39
40
41
42
43
Part
No.
39594
660-234
22569
39534
R
90
667
H-16
667
D-8
22565
22565
22571 E
22894
22894
AD
AD
660-243
39593
22569
39678
E
D
T
660-210
39678
39678
39158
43443
39678
39673
39594
39594
w
u
u
Q
v
c
G
H
22569 A
39582
41071
D
G
86 X
39501
39501
39578
AB
H
F
138
39532
A
90
22569
39582
c
XA
39595
22586
22653
39582
39593
39593
39582
R
D-4
F
D
c
y
39501 K
22657
D-12
Description
Feed
Oil
Screw~
Feed
Screw~
Dowel
Dowel
Screw,
Screw,
Magnetic
Screw~
Screw,
Oil
Oil
Screw~
Chip
Bar
Connecting
Tube
Coupling---------------------------------
for
Bar
Oil
for
Pin,
Pin~
for
for
Oil
for
for
Gauge
Sight
Seal
Gauge-----------------------------------
for
Guard
Retaining
Hinge
Chip
Guard
Rod
Oil
Tube------------------
cloth
plate
stud-------------------------
Shield-------------------------------
feed
bar
oil
shield----------------------
for
for
top
upper
upper
Drain
lower
lower
eyelet
bracket----------------------
cover
knife
looper
--------------------------
holder
rocker
Plug---------------------------
looper
looper
drive
bar
driving
Ring-------------------------------
chip
guard-----------------------------
Assembly
-----------------------------
Ring--------------------------------
Pin------------------------------------
Base-----------------------------Spring--------------------------------------Nut,
Chip
Upper
Oil
Filter
Oil
Strainer--------------------------------------
Screw~
Feed
Nut~
Screw,
Cloth
Cloth
Cloth
Screw,
Cloth
Screw,
Screw~
Bottom
Mounting
Screw,
Screw,
Bottom
Oil
Gauge
Oil
Gauge
Bottom
Cloth
Screw,
for
hinge
Guard
Knife
Driving
Screen
for
oil
Mechanism
for
feed
for
feed
Plate,
Plate,
for
for
Plate
for
Plate
for
for
bottom
mechanism
pin-----------------------------
Cover-----------------------------
Arm
Thrust
---------------------------------
filter
screen------------------------
Cover----------------------------
cover---------------------
mechanism
cover-----------------semi-submerged
non-submerged
Fabric
cloth
Latch
latch
Guard----------------------
plate
fabric
Spring
spring------------------------
cover---------------------------
Cover------------------------------------
for
for
Cover
Cover
Plate
for
Isolator,
bottom
bottom
Indicator
Float
Stud
cloth
rubber-------------------------
cover---------------------------
and
cover
Base
and
Plate
base
-------------------------------
----------------------------------
Gasket------------------------------
---------------------------------plate-----------------------------
block-----------------
shaft
lever
---------------
shaft
lever
----------shaft------
Block--------------
installation--------
installation
guard
---------
-------------
----------------------
plate
extension
Extension-------------
----
Amt.
Req.
1
1
1
1
1
1
2
1
2
1
2
2
1
1
2
1
1
1
1
1
2
1
1
1
1
3
1
1
1
1
1
1
2
1
2
14
1
4
1
2
1
1
1
1
1
1
21

A
-
NEEDLE
B -
UPPER
c -
UPPER
D E
LOWER
-AUX.
34
22
DRIVE
LOOPER
KNIFE
LOOPER
LOOPER
BEARING
DRIVE
DRIVE
DRIVE
DRIVE
BEARING
BEARING
BEARING
BEARING

CRANKSHAFT
MECHANISM
AND
BUSHINGS
Ref.
No
1
2
3
4
5
6
7
8
9
10
11
12
13
14
15
16
17
18
19
20
21
22
23
24
25
26
27
28
29
30
31
32
33
34
35
36
37
Part
No.
39555
39573
39142
39573
39644
39644
39590
39544
39552
39590
666-94
22894
39591
39591
39590
39590
660-268
39590
39590
39590
39521
22769
39521
95
22569
39690
39690
39622
39622
39690
97
39590
39691
22747
39591
20
18
39541
E
K
G
L
c
s
c
L
B
D
H
G
J
G
R
s
H
A
A
A
A
B
A
N
B
Description
Foot
Upper
Foot
Upper
401
401
Crankshaft
Lower
Needle
Crankshaft
Oil
Screw,
Crank
Crank
Thrust
Crankshaft
Crankshaft
Ball
Spacer
Cranks
Pulley
Screw,
Pulley-------------------------------------------
Screw,
Crankshaft
Stud,
Crankshaft,
Crankshaft,
Crankshaft
Stud,
Crankshaft
Screw,
Crankshaft
Washer,
Nut,
Feed
Lifter
Knife
Lifter
Knife
Looper
Looper
Looper
Driving
Wick
for
Chamber
Chamber
Washer
Bearing
Collar
haft
Cap
for
Screw,
for
for
Screw,
for
for
for
Driving
Shaft
Shaft
Drive
Drive
Bushing,
Bushing,
and
fan
Ball
Ball
Ball
--------------------------------------pulley
for
ball
Bearing,
crankshaft
for
Split
for
split
Counterweight,
counterweights-------------------------
Counterweight,
for
crankshaft
Bushing,
Driving
Driving
Bar
Arm
Spring-----------------------------
collar------------------------------
-----------------------------------
Stop
------------------------------------
bearing
for
split
bearing-----------------------------
crankshaft----------------------------
Eccentric
Arm
Bushing,
Arm
Shaft
Shaft
inner
Bushing
Crank
left---------------------------
Cooling
Cooling
Bearing
Bearing---------------------------
Collar---------------------------
Bearing
cap-----------------------------
pulley-----------------------------
inner
bearing
Style
Style
Bearing---------------------------
39600
39600 P ----------------------
bearing-----------------------
-------------------------------
le
ft
---------------------
Bushing,
right----
Bushing,
Bushin
Bushing,
Fan
Fan
Housing
Retaining
housing
Key------------------------
g,
right
le
left
--------
------------------------
Bushing-----------------
Collar---
-----------------------
-------------------
--------------------
right--------------------
-----------------------
A----------------------
right--------------------
left---------------------
le
ft--------------
-
------------
right
ft----------------
Plate-------------
------------
---------
--
-----------
-
-------------
-
----
-
--
- - 1
Amt.
Re
q.
1
1
1
1
1
1
1
1
1
1
2
1
1
1
1
1
1
1
1
1
1
1
2
3
1
1
1
1
1
2
1
1
4
1
1
1
1
23

24

NEEDLE
DIUVE,
FEED
MECIIANISi\
1 AND
FEED
DOGS
Her.
No.
22565
3!)5:3
2
3
4 5:36a4 c
5
6
7
IJ
!)
10
11
12
1:3
14
15
16
,,
-
,;_,
-
16
,.~t
-
);
-
17
18
·'
·
::
t -
18A
),.
t -
*-
10
20
21
22 :39536 z
23
24
25
26
27
28
20
30
:31
32
33
34
35
36
37
38
39
40
41 77
42
43
44
44A
45
46
47
48
49
5 c
:w5:3
5
22569
:39
534
:395:{5
:39534
:39535
5
:36:34
22569
39536
395:38
39534
22569
39626
3
9626
39626
39626
:39626 G
'39626
93
:J960 5 A-:i
3!1605
39605
30605 A-12-3/16
3
9605
3
0605 C-12-3/16
93 A
:3!)540
:3!)540
20
13
395:36 E
305:l6
39536
22569
8372
3957
8 p
39652-5
3
0652-12
28
22519
3
9578
87
39663
:39552 c
39552
39552
22587
39594
605
39652
39652
154
158
22768
39668
531
Part
No.
F
B
GA
D
c
B
B
[]
G
D
c
E
F
11
-1/!l
C-5-1
/ 8
D-5-1/8
B-12-3/16
-12
B-12
C
A
B
A
B
H
1\1
D
A
E
J
N
B
c
GAS
GJ
B
A
Screw,
F'
i\
Washer,
Screw,
M
Feed
Differential
Differential
Washer,
Screw,
Feed
Feed
Differential
Screw,
Differential
Differential
Diffe.rential
Differential
Differential
Differential
Screw,
?llain
M
M
.:\1ain Feed
M
i\la
Sc
Di
i\lain
Main
Washer,
Nut,
Nut,
Feed
Differential
Screw,
\\'asher,
Fabric
Needle
Ne
Fabric
Screw,
Needle
Needle
Needle
Needle
Screw,
Oil
Screw,
Needle
Needle
Needle,
Needle
Screw,'
Looper
for
eed
Adjusting
1ain
Feed
for
ain
Feed
Bar
for
Bar
Lift
for
auge
Styles 39600 A and P -------------------------------------------------
g
auge
Styles
g
g
auge
Styles
g
auge
Style
g
auge
Style
g
auge
Styles
for
Feed
g
auge
Styles 39600 A and P -------------------------------------------------
ain
F e
g
auge
Styles
ain
Feed
g
auge
Styles
g
auge
Style 39600
ain
Feed
g
auge
Style
in Feed
g
auge
Styles
rew,
for
fferential
Feed
Feed
for
for
Bar
for
Guard
Driving
edle
Driving
Screw,
Screw,
Guard
for
Thread
Driving Arm
Driving
Driving
Screw,
for
Splasher
for
Driving
Driving
for
for
Thread
Screw,
Description
feed
adjusting
Pin
Bar
Guide,
for
feed
bar
main
feed
Bar-------------------------------------------------------------
Guide
Block-------------------------------------------------------
Feed
Bar-------------------------------------------------------
Feed
for feed
Driving
Block
ed
for
feed
feed
Driving
for
for
Bar
bar
feed
bar
Stud------------------------------------------------------
.:.
___ -
F e
ed
Bar
thrust
washer----------------------------------------------------
F e
ed
Dog,
F e
ed
Dog,
39600
Feed
Dog,
30600 A and P -------------------------------------------------
F e
ed
Dog,
3!)600
Feed
Dog,
39600
F e
ed
Dog,
:l!J600 A
differential
Dog,
16
Dog,
22
30600 A and P -------------------------------------------------
Dog,
14 tee
3!1600 A
Dog,
16
Dog,
14 tee
39600
Dog,
22
39600 A and P -------------------------------------------------
main
feed
Feed
Driving
Driving
Bar
Driving
feed
driving
driving
bar
driving
Connection
F e
ed
Bar
fabric
guard
fabric
i\1ounting
Arm,
Arm,
for
needl
for
needle driving
-------------------------------------------
fabric
guard-----------------------------------------------------
Cam
Arm
Arm
for
connecting
oil
splasher
--------------------------------------------------
needle
needle
driving
Arm
Arm
503
stitch--------------------------------------
401
stitch-----------------------------------------
thread
Take-up
for
looper
pin
--------------------------------------------------------guide
bar
Guide,
guide
guide---------------------------------------------------
-------------------------------------------------------
Thrust
1\
and P -------------------------------------------------
P-----------------
1\--------------------------------------------------------
and P ------------------------------------------------teeth
teeth
th
and P -------------------------------------------------
teeth
A--------------------------------------------------------
th
P-----
teeth
dog----------------------------------------------------
Eccentric------------------------------------------------
eccentric-----------------------------------------------
Driving
guard
marked
marked
es
Pull-off-------------------------------------------------
Crank
Crank-------------------------------------------------Crank
Thread
Thread
thread
------------------------------------------------
left---------------------------------------------------
screw--------------------------------------------
guide----------------------------------------------
right-------------------------------------------
screw--------------------------------------------
\\'asher-----------------------------------------
16
teeth
per
inch,
marked
14
teeth
per
inch,
marked
22
teeth
per
inch,
marked
14
teeth
per
inch,
marked
16
teeth
per
22
teeth
per
feed
dog----------------------------------------------
per
inch,
per
inch,
per
inch,
per
inch,
per
inch,
---------------------------------------------------
per
inch,
Eccentric------------------------------------------
Connection-------------------------------------------
eccentric------------------------------------------stud------------------------------------------------
Bushing--------------------
Connection-------------------------------------
mounting
mounting
Bracket----------------------------------------------
"E-5";
"E-12";
----------------------------------------------------arm------------------------
Thrust
Connecting
rod-----------------------------------------------
----------------------------------------------------arm
thread
Eyelet,
Eyelet,
cam
pull-off----------------------------------------
Cam
-----------------------------------------------take-up
---------------------------------------
inch,
marked
inch,
marked
marked
marked
marked
marked
marked
marked
bracket-------
bracket----
\rasher
for
for
"B\V";
"CA";
"BF";
"BH";
"BX";
for
No. 5-1/8
for No.
------------------------------------
Rod------------------------------------
eyelet---------------------------------
No.
No.
cam
------------------------------------
"BH";
"BP";
"BS";
"BT";
"BU";
"BV";
"BC";
for
for
for
for
for
for
-
-----------------------------
-----------------------------
12- :3;
5-1/8
gauge, all
12-3/16 gauge, all
for
No.
for
No.
for
No.
for
No.
for
No.
for
No.
No.
5-1/8
No.
5-1/8
No.
5-1/H
No.
12-3/16
No.
12-3/16
No.
12-3/16
-
--------------------
~auge,
16
all
gauge,
- - -
-
Styles
5-1/
8
5-1/
B
5-1/8
12-:l/16
12-3/16
12-3/16
Styles
-----------
all
Styles
---------
----------------
------------------
-
------------
-------------
Styles
------
-
----------------
----
----------
- - -
Amt.
Hcq.
1
1
1
2
2
1
2
1
1
2
2
2
1
1
:J
1
1
1
1
1
1
1
1
1
1
1
1
1
1
1
1
1
1
2
2
1
2
-
--
2
1
1
-
1
2
1
1
2
1
1
1
1
2
1
1
- -
1
1
1
--
1
1
2
1
1
*
Available
as
extra
send
and
charge
item.
25

26

SPREADER
AND
LOWER
LOOPER
(503
stitch)
DRIVING
PARTS
Ref.
No.
1
2
3
4
5
6
7
8
9
10
11
12
13
14
15
16
17
18
19
20
21
22
23
24
25
26
27
28
29
30
31
31A
31B
31C
32
33
34
35
36
37
38
39
40
41
42
43
44
45
46
47
Part
No.
39560
39543
22564
39543
22
22503
39543
22565
39543
39543
39543
22747
41255
482 c
22894
22565
7446
1280
39543
43143
39543
39543
22562
39543
29126
22559
77
39594
22539
482 c
22894
22894
39694
12982
39508
39151
39544
39544
39644
22729
22729
39644
39644
39644
538
77
39544
39544
22894
51235
1025
A
G
A
KH
F
E
H
T
s
K
B
c
A
R
N
H
M
A
p
CG
A
N
K
c
J
B
u
F
E
D
R-2
R-5
J
B
D
AD
B
L
Description
Spreader------------------------------------------
Spreader
Screw,
Spreader
Screw,
Screw,
Cam
Screw,
Cam
Spreader
Spreader
Screw,
Guide
Spreader
Screw,
Screw,
Spreader
Nut,
Washer,
Locking
Spreader
Clamp
Screw,
Thrust
Spreader
Screw,
Screw,
Holder,
for
Holder
for
for
cam
Follower
for
bushing
Follower
Drive
Drive
for
guide
marked
"J"
-----------------------
spreader----------------------------
Collar-----------------------------
spreader
follower
Locking
and
holder
locking
Clamp
cam
collar
clamp---------------
-----------------------
guide--------------------
------------------------------------Shaft
Shaft
Bushing
and
Cam
-------------------------------
fork-------------------------------
Fork----------------------------------------
for
Drive
for
Drive
locking
for
Stud,
Drive
Lever
for
collar
spreader
Lever
stud
locking
for
Lever
Shaft
Collar-------------------
------------------------------
drive
Shaft
lever
shaft----------------
-------------------------
-------------------------------
stud----------------------------
spreader
drive
lever
------------------------------
Collar--------------------------------------
for
Washer,
Drive
for
for
oil
clamp
for
Lever
connecting
splasher
collar
spreader
and
-----------------------drive
shaft
Connecting
rod
assembly--------------
-----------------------------
OilSplasher--------------------------------------Plug
Lower
Screw,
Knife
Nut,
Lower
Nut,
Lower
Lower
Lower
Shim,
Shim,
Ball
Screw,
Screw,
Lower
Lower
Screw,
Lower
Set
Screw,
Looper
Screw,
for
Drive
for
Looper
for
Looper
Looper
Looper
Screw,
Screw,
for
for
Joint
for
for
Looper
Looper
for
Looper
Screw,
for
Shaft
for
knife
Connecting
knife
drive
-------------------------------------
lower
Bar
Bar
Drive
for
for
ball
joint
ball
joint
Guide
ball joi
connecting
Bar
Bar
lower
Bar
for
lower
looper
shaft-------------------
Collar--------------------------
collar
drive
looper
-----------------------------oil
drip
plate------------------
Rod
Oil
oil
drip
Drip
plate
Plate------------
screw--------------
bar---------------------------
(503
stitch)-----------------------
Driving Lever--------------------
Lever
Connecting
connecting rod-----------------------
connecting rod-----------------------
guide fork,
guide
fork,
• 002
• 005
inch
inch
Fork-------------------------------
nt
guide
Connecting
Connecting
looper
Driving
No.
22565 H -------------------------
fork----------------------
link
pin-----------------------
bar
driving lev
Lever
Link
Link
-----------------Pin---------------
Shaft---------------
---------------
Guide----------
shaft----------
-------------
Rod
Assembly---
Rod
-----------
thick---as
thick---as
er
shaft
-------
Amt.
Req.
1
1
1
1
1
1
1
1
1
1
1
1
1
1
2
2
1
1
1
1
1
1
1
2
1
4
1
1
2
1
2
1
1
1
1
1
1
1
1
2
2
required
required
1
2
2
1
2
2
1
1
27

28

THROAT
PLATES,
UPPER
NEEDLE
AND
LOWER
GUARDS, 401
KNIFE
STITCH
MECHANISM
LOOPER
PARTS,
Ref.
No.
1
2
3
4
5
6
6A
7
8
9
10
11
12
13
14
15
16
17
18
19
20
21
22
23
24
25
26
27
28
29
30
31
32
33
34
35
36
37
38
39
39A
40
41
42
43
44
45
46
47
48
49
50
51
52
53
54
55
56
56A
57
58
59
60
61
62
63
64
65
66
67
68
69
70
71
Part
No.
39673
A
39571 A
39572
B
22829
22650
CB-4
39270
D
39270
E
39571 E
39573 A
39573 E
55235
D
6042 A
55235 E
39673
22587 E
39644
M
c
22565
22565 L
39644
K
39644
p
98
39644
H
22729 E
22729 D
M
39543
22562 A
p
39543
660-206
39644
N
39644
A
39644
39644
R-2
39644
R-5
39644
J
538
22588 A
39550
L
39550
M
482
c
22894
c
39549
p
39649
39650
A
39650
22729 B
395 50 c
14077
22892
22503 F
39543
E
22653
B-12
39580 AC
39525
A
39625
B
22585 A
90
39625
A
39625
396
24
C-5-1/8
39624
C-12-3/16
22524
39550
E
39644
E
22653 J
22564
D
3960
8 c
22503 F
39543 E
39644
B
39644 L
22775
c
41336
22781
39678
p
187
A
-4
Description
Upper
Knife
Upper
Upper
Screw,
Set
Screw,
Upper
Upper
Upper
Upper
Upper
Locking Stud,
Washer,
Nut,
Upper
Screw,
Looper
Set
Screw,
Spot
Screw,
Bushing
Thrust
Screw,
Looper
Screw,
Screw,
Clamp
Screw,
Thrust
"O"
Ring, for l
Lower
Lower
Lower
Shim,
Shim,
Ball
Joint
Screw,
Screw,
Lower
Lower Kni
Lower
Screw,
Lower
Lower
ower
L
Lo
wer
S
crew, fo
Lower Knife
t, for l
Nu
L
ock
ing
Screw,
Needl
e G
Sc
rew, for throat plate support
T
hro
at Plat
eedle Guar
N
eedl
e G
N
Sc
rew
, for 503 stitch
Sc
rew
, for 401 stit
eedl
e G
N
eedle Guard,
N
Throat
Throat
Sc
rew, for throat
ni
fe
Holder Spring
K
L
ooper Holder, for
Screw, for l
Screw for
Loope~,
Screw, for cam follower locking clamp
Cam Follower Locki
L
ower Loo
Cam F ollo
S
crew, for looper avo
ooper
L
S
crew, for looper
Chip Defl
Screw---------------------------------------------------------------------
Driving
Kni
fe
Clamp
Knife
Holder
for
upper
for
Knife,
Knife,
Knife
for
for
for
wide,
Knife
Clamp
Knife
Driving
Knife
Driving Lever--------------------------------------------------
for
for
driving lever---------------------------------------------------
Driving Lever
for
Avoid
for
for
and
Cam
Collar--------------------------------------------------------------
for
Drive
for
for
Collar
for clamp
Washer,
Looper Drive
Loop
er
Looper
ball joi
ball joi
Guide Fork-------------------------------------------------------
for
ball joi
for
lower knife
Knife
Clamp-----------------
fe
Clamp
Looper
for coll
Knife,
Knife, wide, for
Knife Holde
Knife
Plate, marked "BL- 5
P l
for
Clamp
r l
ower
Hold
ocking screw------------------------------------------------------
Scr
ew,
for
needle guard-----------------------------------------------------
uard Locking Cla
e a
d, r ear, f
uard, front,
uard,
ate, mark
401 stitch
mar
ked "CR",
per
wer
--------------------------------------------------------------
Avo
id Li
ector
Arm----------------------------------------------------
Nut------------------------------------------------------
Block
knife
upper
Style
for
driving
connecting
Link----------------------------------------------------------
bushing
bushing and
Guide
thrust
Lever
connecting rod----------------------------------------------connecting rod-----------------------------------------------
-------------------------------------------------------------for
ower looper
Driv
Bar
nt
nt guide
nt gui
Drive Lever
Sty
r---------------------------------------------------------
knife holder l
er
for
nd
Lower Kni
ch front nee
fro
nt, f
rear,
pl ate------------------------------------------------------
ooper
Bar Slee
nk
Pin
avo
-------------------------------------------------------------
-----------------------
holder
knife------------------------------------
39600
for
--------------------------------------------------------Arm
driving
and
collar-------------------------------------------------
Auxiliary
collar-------------------------------------------------
lower
Lever
e L eve
(401
gui
de
clamp------------------------------------------------
Spring---------------------------------------------------
ar-------------------------------------------------------
le
39600
Scr
ew
Locat
lower knife
or
for
needl
or
for 401 sti
ed
"BL
--------------------------------------------------------401 sti
holder
looper-------------------------------------------------
ng Clamp
ve
id
-------------------------
id link
block
------------------------------------------
A-----------------------------------------------
Style
39600 P -----------------------------------------
Washer
lever---------------------------------
rod-----------------------------------------------
-----------------------------------------------------
looper bar-----------------------------------------
r--------------------------------------------------
stitch)-----------------------------------------------
fork,
fork,
de
fork----------------------------------------------
Sty
le 39600 P
Nut
ing
mp
503 s
503
e g
401 stitch
-12-3/1
tch looper
for
------------
link
--------------------------------------------
lever
------------------------------------------
Connecting Rod---------------------
cam
guide-----------------------------------------
cam
guide----------------------------------------
Connecting Rod---------------------------------
driv
e lev
er
Shaft---------------------------------------------
• 002 i
• 005 i
Shaft
A----------------------------------------------
----------------------------------------------ocating st
Stud--------------------------------------------
hold r ----------------------------------------
-----------------------------------------------brac
fe Support Bracket---------------------------------
titch-------------------------------------------
stitch-------------------------------------------
uar
dle guard--------------------------------------
tch-------------------------------------------
-1/
8"; for No .
------------------------------------------------
401 st it ch
------------------------------------------------
------------------------------------------------pin
----------------------------------------------
shaft
nch
thick
nch
thick
-
---------------------------------------
Collar---------------------------------------
-----------------------------------------
ud------------------------------------
ket
---------------------------------------
ds
------------------------------------------
-------------------------------------------
11
6
; for No.
-----------------------------------------
5-1/8
-----------------------------------------
---------------------------------------
-
--------------------------------------
-
---------------------------
----------------------------------
--------------------------as
--------------------------as
gauge,
12-3f16gauge,
-
----------------------------
Styles
39600 A and P----
Styles
-
--------------
-
-------------
-
--------------
39600
A and
requ
requ
P-
Amt.
Rcq.
1
1
1
1
1
1
1
1
1
1
1
1
1
1
2
1
1
1
1
1
2
1
2
2
1
1
2
2
1
1
1
ir ed
ir ed
1
2
1
1
1
1
2
1
1
1
1
1
1
1
1
1
1
2
1
1
1
2
1
1
1
1
1
1
1
1
1
1
1
1
1
1
1
1
1
1
1
1
29

30

TOP
COVER,
EYELETS
AND
PRESSER
SPRING
PARTS
Ref.
No.
1
2
3
4
5
6
7
9
10
11
12
13
14
15
16
17
18
19
20
21
22
23
24
25
26
27
28
29
30
31
32
33
34
35
36
37
38
39
39557
39557
39557
39557
39557
39556
39582
51-103
22562
39582
39582
39582
39582
39582
22541
39668
22825
39663
22757
51758
53678
90
39557
39668
22829
39668
22570
39668
660-219
39668
39668
22570
39668
605
87
39663
39663
22569
Part
No.
B
E
c
F
A
z
A
v
L
AG
w
AA
D
J
E
N
A
E
BA
B
c
H
F
A
G
u
H
K
c
Blk.
N
Presser
Presser
Presser
Lock
Presser
Presser
Top
Cover--------------------------------------
Hinge
Screw,
Spring,
Oil
Hinge
Oil
Top
Cover
Screw,
Looper
Screw,
Top
Cover
Screw,
Needle
Washer,
Screw,
Presser
Take-up
Screw,
Cast-off
Screw,
Eyelet
Roll
Spring
Arm
Screw,
Latch
Screw,
Screw,
Needle
Top
Cover
Screw,
Description
Nut,
Spring
Spring
Spring
for
Plunger
Plunger
Plunger
plunger
Cap
Nut
Lock
Adjusting
adjusting
------------------
Nut
----------------Screw-----------
screw-------------
Spring----------------------------------
Foot
Release
Bushing--------------------
Pin-----------------------------------
for
Filler
hinge
for
oil
Cover-----------------------------
bracket---------------------
filler
cover-------------------
Bracket-------------------------------
Guard-----------------------------------
Gasket
for
top
Thread
for
looper
Needle
for
top
Thread
for
for
needle
Spring
needle
-------------------------------
cover-----------------------------
Eyelet----------------------------
thread
Thread
cover
eyelet-------------------
Eyelet------------------
needle
thread
Eyelet----------------------------
thread
thread
eyelet
screw------------
eyelet-------------------
Plunger--------------------------
Eyelet----------------------------------
for
Blade
for
take-up
cast-off
eyelet
------------------------
---------------------------------blade-------------------------
Bracket----------------------------------
Pin,
for
arm
---------------------------
Washer,
--------------------------------------for
for
clamping
arm----------------------
bracket------------------
Spring--------------------------------
for
for
needle
Thread
Eyelet
for
top
latch
Pull-off
cover
spring
thread
----------------------
pull-off
Eyelet
eyelet------------
--------------------
Bracket------------------------
eyelet
bracket
eyelet----------
---------------
Amt.
Req.
1
1
1
1
1
1
1
1
1
1
1
1
1
1
8
1
1
1
2
1
1
1
1
1
1
1
1
1
1
1
1
1
1
2
1
1
1
2
31

16
20
t9
:a
2:1
22
3
·
'---[1
~
32

PRESSER
FEET,
FOOT
AND
LIFTER
MISCELLANEOUS
PARTS,
THREADED
EYELETS
TENSION
PARTS
Ref.
No.
1
2
3
4
5
6
7
8
9
10
11
12
13
14
15
16
17
18
19
20
21
22
23
24
25
26
27
28
29
30
31
32
33
34
35
36
37
38
39
40
41
42
43
44
45
46
47
48
49
50
51
52
53
54
Part
No.
39555
39555
39555
660-142
39555
39555
12538
22597
627
22566
12865
88
39655
258
22791 H
39656
39656
605
108
51292
51292
107
109
35792
90
39663
BP108
22565
39692
22569
39568
43139
39568
39568
376
39568
73 X
39620
39630
22781
39630
39630
22799
39630
39630
39630
39620
39630
22781
39630
39630
22799
39630
39630
39630
B
D
F
c
E
B
A
B
A
F-2
F-5
H
A
c
B
D
A
B
L
A
w
C-5-1/8
G
N
L
u
F-5-1/8
M
H
C-12-3/16
J
N
L
u
F-12-3/16
M
K
Description
Fo~
Lifter Leve
Foot
Lifter
Foot Lifter
Cotter
Foot
Foot Lifter Lever Arm------------------------------------------
Screw,
Thrust
Foot
Nut,
Screw,
PresserArm---------------------------------------------------
Chain
Screw,
Te
Tension
Te
Tension
Te
Tension
Screw,
Frame
Screw, for
Screw,
Tension
Screw,
Looper
Nut,
Lower
gaug
L
12-3/16
Screw,
Frame
Screw,
Presser
39600 A and
Presser
Styles
Pin,
Lifte
r L ever
Lock
Screw,
Screw,
for
Collar,
Screw,
Lifter Lever
for
presser arm
for
Cutting
for chain
nsion
nsion
nsion
ower Looper
Post
Spring,
Spring,
Post
Disc---------------------------------------------------
Post---------------------------------------------------
for
Thread
for tension
Post
for eyelet
Thread
for lower
Looper
e----------------------------------------------------------
gauge-------------------------------------------------for
Thread
for
Foot,
Presser
Clamp
Spring----------------------------------------------------
Lock
Hin
ge
Presser Foot
Hinge
Needle Hole Se
Foot,
39600 A an
Presser Foot
Clamp
Spring---------------------------------------------------Lock
inge
H
Presser
Hinge
Needle Hole
r-----------------------------------------------
Lever
Intermediat
for connecting link-----------------------------------
Nut,
foot
presser
frame
tension
lower
frame th
Nut
Scr
Scr
Nut
Screw, for
Screw, for
Spring----------------------------------------
e L e
ver-----------------------------------
Connecting
for lever
for
lev
er
arm--------------------------------------
for lev
for thrust
Knife
Nut
Ferrule
Mounting
P--------------------------------------------------
er
arm--------------------------------------
lifter lever--------------------------------------
for
foot
lifter lever
Shaft------------------------------------------
screw
arm-----------------------------------------
---------------------------------------------
cutting
-----------------------------------------------
for
401 sti
for
needles
-------------------------------------------
t hr
ead guide
Guide--------------------------------------------
post
post------------------------------------------
Bracket-----------------------------------
mounting bracket-------------------------------
Eyelet
looper
Thread
Thre
Guid
marked
Foot
------------------------------------------------ew,
ew,
marked "AK-12-3/16",
----------------------------
Foot
Mounting Bracket---------------------------
thread
Eyelet, for
ad Eyele
looper thread
e, f
or lower looper
rea
d g
"AK-5-1/8
Shank, mar ked
Screw------------------------------------------
for
press
Bottom,
for
need
ction,
d P
--------------------------------------------
Shank, marked
Screw------------------------------------------
presser foot
Bottom, mark
needle
Section,
Link--------------------------------
arm-----------------------------------
shaft
collar------------------------------------
-------------------------------------
knife------------------------------------
tch looper
and
503
-----------------------------------
mounting bracket--------------------------
eyelet
Styles
t, for
uide -----------------------------------
le
marked "AP'.!.--------------------------
mark
Styles
eyelet-----------------------------
",
er f
oot
mark
ed
hol
e s e
ed
hol
e s
ed
--------------------------
-----------------------------
stitch
screw-------------------------
"D'!..---------------------------
bottom
"E"
bottom-----------------------ect
"AR'.!.--------------------------
looper------------------
39600
39600
thread
for
No,
"AK-5 1/8"
ction
for
---------------------------
"AK-12-3/16"-----------------
ion
A,
A,
---------------------
5-1/8 gaug e,
-----------------------
-------------------
--------------
No.
12-3/16 gauge,
-
--------------------
------------------------
P, No.
P,
No.
5-1/8
Styl
-
---------
es
Am
Re
t.
q.
1
1
1
2
1
1
2
2
1
1
1
2
1
1
1
1
1
1
4
1
3
4
8
4
1
1
1
4
1
1
1
1
1
1
1
1
2
1
1
1
1
1
1
1
1
1
1
1
1
1
1
1
1
1
1
33

9
34
43
'11
42
<Y

THREAD
STAND
AND
ACCESSORIES
Ref.
No. No.
1
2
3
4
5
6
7
8
9
10
11
12
13
14
15
16
17
18
19
20
21
22
23
24
25 421
26
27
28
*29
*30
>,'<-
*31
32
33
34
35
36
*37
38
39
40
41
42
43
44
Part
21101
21114
21114
21114
258
652-16
21114
21114
21104
21114
21114
21114
22651
21104
21114
22651
21104
652-16
21114
21114
22651
22810
21114
22651
21388
21388
21227
21209
21225-3/64
21225-1/8
21227
660-272
21207
660-264
WR64
WR70
29481 J
22569
604
39503
39603
12957
22758
39603
H-4
S-4
L
M
A
w
v
H-4
L
M
CD-4
B-24
D-4
CD-5
H
u
A
CD-4
T
CD-4
D-34
AU
w
BF
K
CR
A
c
A
A
E
E
Description
Thread
Stand~
Lead
Eyelet-----------------------------------
Eyelet
Nut-----------------------------------------Washer--------------------------------------
Spool
Spool
Pad,
Eyelet
Eyelet-----------------------------------
Eyelet
Screw
Thread
Spool
Screw
complete
Eyelet----------------------------------
Locking
Seat
Disc-------------------------------
Pin
------------------------------------
for
thread
Support--------------------------------
Locking
-----------------------------------
Stand
Seat
Rod-----------------------------
Support
---------------------------
Ring-----------------------
cone--------------------------
Ring-----------------------
----------------------------
-----------------------------------
Nut------------------------------------------ 1
Washer-------------------------------------Lead
Thread
Clamp
Lead
Foot
Socket
Wrench.,
Feed
Hexagon
Looper
Looper
Needle
ThreadTweezers---------------------------------
Screwdriver~
Lifter
feed
with
inches
"S"
Hook1 for
Wrench~
Wrench1 7/64
Edge
Screw~
Screw~
Edge
Edge
SpringWasher--------------------------------
Screw~
Edge
Eyelet
Stand
Screw
Screw---------------------------------
Eyelet
Screw
Treadle
Wrench1 for
eccentric-----------------------------------
curved.,
Eccentric
Socket
handle
Gauge.,
Gauge.,
Height
Ball
Split
Base----------------------------
----------------------------------Socket
-----------------------------------
Chain~
3/8
double
Extractor
Bit.,
7/64
No.
21209
3/64
1/8
Setting
1/8
inch.,
inch.,
Gauge~
inch
Socket-------------------
Ball
-----------------------
34
inches
inch
hexagonal
end.,
G)
diameter
9/32
Hook---------------------
inch
hexagonal
------------------------for
401
stitch-------------
for
503
stitch--------------
for
401
blade~
inch
long--------------------------------------
treadle
3/32
Guide
inch
inch
Assembly
for
edge
for
edge
Guide----------------------------------Guide
Guide
for
Swinging
edge
Mounting
chain-----------------------hexagonal----------------------hexagonal-----------------------
----------------------------guide
guide-------------------------
guide
mounting
Arm----------------------
swinging
Bracket
bracket---------
arm
------------------
long-----------
nut
holding
opening------
(for
use
stitch----------
4
3/32
------------
Amt.
Req.
1
1
4
4
8
4
4
4
4
1
8
8
2
1
1
2
1
2
1
1
1
1
2
1
1
1
1
1
1
1
1
1
1
1
1
1
1
2
2
1
1
1
1
1
*
Available
as
extra
send
and
charge
item.
35

NUMERICAL
INDEX
OF PARTS
Part
No.
18
.......•.•.
20
•.....•.•••
22
KI
-I
28 B ..••.•...•
51-103
WR64
.•.........•
wrno
............
73 X
77
••.......••
86
X
••...•..•••
87
87 u
88
.•..•.•....
90
.••••••••••
93
..•.••••••.
93
A
95
••••..•....
97
A
98
•••••.••...
107
.•••••...•.
108
BP108
*
12538 •••..•••••.
12865 .•••••••.•.
12957 E .•••.•.••
129
*
•.•.•••••••
•••.••••••.
109
.••.•••••.•
138
..•••••••••
154
GAS
158
GJ
187 A •••••.•••
258 A .••.•••••
376 A .••••••••
421
D-34
482
c
531
•••••••••••
538
...........
604
••••••.•...
605
.•••••••.•.
627
•.•.••••.•.
652-16
660-142
660-206
660-210
660-219 N •..•.
660-234 •....••
660-243
660-264 .••••••
660-268
660-272
666-94
667
D-8
667
H-16
1280
..•.••••...
6042 A .••••••••
7446 A .•..•••••
8372 A ••.••••
82
.•.•••••...
102
5 L
•••••••.
Blk
....
.•....•.•
•••••••••
.........
...••••..
.....••..
••••.••
•..••••••
..••••
.........
••••..••
••..•..
•....••
...••.•
•......
•••....
.••••.•
..••••••
...•••.
.•••••
•••••••••
Pa
23,
23,
27
25
31
35
35
33
25,
21
25
31
33
21, 29,
33
25
25
23
23
29
33
33
33
33
21
25
25
29
33,
33
35
27,29
25
27,29
35
25,
33
35
33
29
21
31
21
21
35
23
35
23
21
21
27
29
27
. . 25
33
33
35
27
27
ge
No.
25
25
27
35
31,
31,
33
Part
No.
14077
••...••...••
21101
21104
21104
21104
21114
21114 A ..•...•...
21114
21114
21114
21114 M .........
21114
21114 T .....•....
21114
21114
21207 A •••.•....
21209
21225-3/64
21225-1/8
21227
21227
21388
21388
22503 F .•.....•••
22519 H .•••••••••
22524
22539
22541
22559 A •••.••••••
22562 A •••.•••••.
2256
2256
22565 .•••••••••••
22
2256
2256
22565 L .
22566 B
22
22569 A
22569 B
22569
22
2
22570 A .••••••••
22
22
22585 A
22586 R
22587 E
22587 J
22
22597 E
226
226
226
226
226
226
II-4
.•.•...
B-24
H
.•..•....•
v
..........
............
D-4
•......
H-4
••.....
L
.........
S-4
...•.•..
u
..........
w
.........
K
•••......
...•...
•••••...
BF
.••••••.
CR
....••••
w
.........
AU
.•.•....
.•••..••.•••
K.
.........
.•••••••••••
4 D
••..••••••
4 G
••••••••••
565 c
..........
5 F
•••••••••.
5 H
•••••••••
.•••••••
569
569 D
256
570 B
571 E
588 A •••.•.••••
•••••••••
••••.••••••
•••.•••••
•••••.••.
c
.........
•••••••••
9 G
•••••••••
••.•••••.
•••••••••
•••••••
•••••....
•••.•..••
•••.....••
••••••....
50 CB- 4
51 CD- 4
51 CD- 5
53 B
-12
53 D- 4
53 J - 4
••••••..
••••••.
•.•..•
.•.•••
.•••••
.•••••
••••.•
Pa
29
35
35
35
35
35
35
35
35
35
35
35
35
35
35
35
35
35
35
35
35
35
35
27,29
25
29
27
31
27
27,
29
27
21,
29,
25
27
29
33
21,
21
25, 33
21,
21
25
31
31
21
• • 29
21
29
25
29
33
29
35
35
29
21
29
ge
No.
29,
27
33
23,
31,
31
25
35
P a
rt
No.
22729 B ••.••••.•.••
22729 D ....••..•...
22729
22747
22747 B .••.....•...
22757 E ............
22758 E ..•.•••••..•
22768
22769 A .••..•.•••.•
22775
22781.
22791
22799
22810
22825
22829
22892
22894
22894 D ..•......•••
22894 J ••.........•
22894
29126
29481 J .••..•••.•••
35792 H ..•.•.......
39142 G .••..••.••••
39151
39158
39270 D •••••..•..••
39270 E •••.••••••.•
39501 H ............
39501
39503 A •••.•••••••.
39508 B ••••••...•..
39521
39521 A .•..•••••.••
3952
39532 A ••••••..•..•
39534
39534 H ••••..•••..•
39534 R ••••.•••••..
39534 GA
39535
3953
3953
39535 D ••••.•••...•
39536 A .••.•..•...•
39536 B ......•.••••
39536
39536 E ••...•.•.•••
39536
39538
395
39541.
39
39
39
39
39
39543
E
•.•..••••••.
.••...........
B
.•..•...••..
.••.•.•.•.••••
.••.••...•••.
H
••••...•••••
u
............
.••••••.••••••
.••..••.•••••.
•..••...••....
..•.......••••
c
............
AD
.•••.....•
CG
.......•••
..••..•..•.•••
u
............
AB
.••••••...
.•.•••.•••••••
5 A
.•••••.•....
.••••....•..••
.••.•••..•
••••.•.•••...•
5 B
.......••.••
5 c
............
c
............
z
............
••••...••.....
40 B
-12
•....•..•
•.•..•..•••••
543
....•••••••••.
543 A .••.••••••.•
543 E ............
543 H •••••••••••.
543
K.
...........
i\1
.•••••••.••
Page
No
29
27,
27,
27
23
31
35
25
23
29
29,
33
33
35
31
29,
29
27'
23
27
21,
27
35
33
23
27
21
29
29
21
21
35
27
23
23
29
21
25
25
21
25
25
25
25
25
25
2
25
25
25
25
25
23
27
27
2
7,
27
27
27,
.
2!)
2D
33
31
29
27
29
29
36

NUMEHICAL
INDEX
OF
P
AHTS
Part
No.
39543 P •••••••
39543
39543 8 .......
39543
39544
39544
39544
39544
39544
39549
39550
39550
39550
:39550
39552
39552
39552
:39552
:39555
39555
:39555
:~9555
:
39555
:39555 F
3
39557
39557
:39557 B
:39557 c
3
:3!J557 F
:39560 A
39563
:39563
39568
:
39561:l
39571
30571
39572
39573
39573
3957:3 K
3D573
39578 F .••••••
39578
39578
39580
:39582
:39582 F
3D582 L
39582
39582
39582
39582
39582
39;,82
:HJ5o2 X
:3!J580
3
R
.......
T
.......
.•••....•
B
.......
D
.......
L
.......
u
.......
P
.......
c
.......
E
.......
L
.......
lVI
.•••••
A
.......
B
.......
c
.......
E
.....•.
..•..•.•.
B
••.••••
c
.......
D
..•...•
E
.......
9556 A ...•...
.......
...•.....
A
••.••••
.......
.......
9557
E
••.••••
.••.•••
••.••••
B,,,,,,,
D
.•.•...
L
.......
\V
.••••.
A
.......
E
.•.....
B
.......
A
.......
E
.......
•••••••
L
.......
l\1[
••••••
p
.•....
AC
•••••
D
••.•••.
.•.....
.......
V
.......
w
......
Y
•••.•••
z
.......
AA
.•...
AG
.....
•.
••.....
9590
c . .
.....
•.•
Page
27,
27
27
27
27
27
27
23
27
29
29
29
29
29
25
23
25
25
3:3
33
33
:33
23
3:3
31
31
:n
:n
31
:31
:31
27
33
3:3
33
33
29
29
2D
29
29
23
23
21
25
25
29
21
21
:H
31
31
21
31
31
31
,
21
. . 23
2:3
No.
29
Part
No.
39590 G ....•.••••••••••
39590
39590 J ................
39590
39590.H.
39590
39591
39591 G ••••••••••••.•••
39591
39593
39593
39593
39594
:-!9594 G
39594
:39594 N
39595
39603
3960:3 A
39605
39605
39605 B-12-3/16
39608
39620
39620
39622
:
39622
3
3
3
3
3
:3
3
3
3
39626 G ..•••.••.•....••
39626
39630 F-5-1/8
39630 F-12-3/16
396:30 G
39630
39630 J ................
39630
396:W L
396::l0 l\1[
:
39630
39644
3
:
39644
:
39644
'~
39644
:3
39644
39644 H .•...........••.
39644
39644
39644
39644
H
....••••.•....•.
N
•••••..•..•....•
•..••.••.••.•••
s
................
•••..•...•..••..••
H
.......•••..••.•
c
................
D
...••••.•..••..•
E
.•...•••••••••••
•.••••••.•••.••.•.
••••.•.•...••..•
H
.......•..•...•.
•...•.•...•.••..
•••••..•••.•••••••
•••••••.••.•••••••
•....••.••••••••
A-5-1/8
-12-3/16
c
................
C-5-1/S
C-12-3/16
...••.•..
A
••....•
9624
C-5-1/8
9624
C-12-3/16
9625
..•...•......•..•.
9625
A
..••...
9625
B
.•..••••...•..•.
9626
c
................
9626
D
9626
9626 F .•.•.••.••.•....
9644
9644
...••.•.•.•
E
••.........
H
.•••............
.•.••..
H
.•.••••••.••..
K
•••••.•••••.•••
....•...•.......
N
••••.....
•••••..•........•.
A
.•.•••.•...••...
B
.•..••.•.•.•...•
c
................
s
..............
E
.•...•••...•.•.•
F
................
.J
•••••••..••••••.
K
.••.••.........•
L
.•..........•...
lVI
..••••..••
••••.••••.
.•.....•
•....•••••
•••••••••••••••
.•••••••..••...
....•...
.•••..•.
..•••••.
.
..•...•.
.
..•..•••
•....•.•
.
.......•
•.•...•.
..
.•.•.•.
..
..
.
....
.....
. •
•.•
. •
.. 23
Page
No.
2:3
23
2:3
2:3
23
23
23
23
23
21
21
21
21
21
21
25,
21
35
3.5
2
25
25
29
:33
: 3
2:~
23
29
29
29
29
29
25
25
25
25
25
25
:33
33
33
3:3
33
. 33
33
33
33
29
29
29
23
29
27
29
27,
29
29
29
27
29
Part
No.
39644
39644
:39644
...
39644
-~
:39649
:39650
39650
39652-5
39652-12
39652
39652
39655
39656 A ..•...•.....•
39656
39663 A .••..•...•..•
39663
39663
39663
39663
39668 A ..••••....•..
39668
39668
39668
39668 F •••.••...••••
39668 G .•.••••••••.•
39668
39668
39673
39673 A ........•.•••
39673
39678
39678
39678
39678
3
3
3
3
3
.'39692
:3
4
4
4
4
43
43
5
5
5
5
5:3634 c
53678
55235
55235
N
..•........•.
P
.............
R-2
.•..•.•...•
R-5
••..•..•..•
.••.••....•..••
••...•......•.•
A
.•••.••••••••
............•
•••••••.••••
B
.••.•..•..•..
c
.............
.•••.•......•.•
B
.•••..•...•..
D
..•.....•...•
H.
........•...
.J
••••.••.•••••
K
.•••......•••
c
.............
D
.•.•..•••••.•
E
.••..•••.••••
H
......•......
BA
••.••.••..•
.••....••.....•
c
.............
P
....•.•.....•
T
.............
u
.............
v
.............
9678
\V
.••.••••••••
9690
•.•••.•.•.....•
9690 A .••.••....
9690
9691
9694
1071 G ....••....
1255
1336
3139 A .•••••..••.
1235
1292 F-2
1292 F-5
1758
............•
•.....
.••............
............•••
B
.....••.
c
.............
143
N
.•........•.•
443
Q .••.
B
..•...
....••....•....
.
..•...••.
......
••.•......•
.............
N
.............
D
.•.•••.•.•.••
E
.•.•.•.•.•..•
.
.......•
.
.
....
.
.•••.•
.... •
••
.•
. •
Page
No.
29
29
27,
27,
29
29
29
25
25
25
25
33
33
33
33
25
31
31
31
25
31
31
31
31
31
31
31
29
29
21
29
21
21
21
21
23
23
23
23
33
27
21
27
29
33
27
21
27
33
33
31
25
31
29
29
29
29
37

LEWIS
and
COLUMBIA
®
..
'
Q
W
ORLD'S
......
,..o
..
FINEST QUALITY
FINEST
t
Hand
fo Union Speclal and Columbia only.
t Handlo low
All
othe
uu
taln oxceptlons.
n
ls
and Cotum
hand
QUALITY
bla only.
le Unlon Spec ia l,
UNITED
ALABAMA
ALABAMA
ARKANSAS
*CALIFORNIA 90021,
CALIFORNIA
!CALIFORNIA
COLORADO
CONNECTICUT
FLORIDA
FLORIDA
*GEORGIA
GEORGIA 30529,
GEORGIA 30030,
GEORGIA 31021,
GEORGIA 30501,
GEORGIA 3068
*ILLINOIS 6061
KANSAS
KENTUCKY
LOUISIANA
35206,
Lloyd
D.
(Zip Code 36110),
Taylor, Tel. (501) 376-3121.
Paul
M.
Robert J.
Machine Co., 1155 Minion
5719
leo,
Gaines, Tel. 7.46-3652.
Jng
Equ
Morgan. Tel. 752-1829.
N.E
..
Morrill
Hanley, Tol.
Parker,
Tel.
272-~663.
T~t
l.
Cumm
Tel.
867-320
Koehler, Mgr., Tel. 644-6920.
Rosewood, Cr
Hinton, Tol. 587-0042.
Springs Dtivo, Duane Bunger, Tel. 5
BIRMINGHAM,
Baldwin, Tel.
36107,
MONTGOMERY,
Tommy
72203,
LITTLE
Mason,
Mar., Tel.
94110,
SAN
Vail, Tel.
~15/826-5969.
9~103,
SAN
80002,
ARVADA,
Rood
St., Tel.
06811,
DANBURY,
33 127,
MIAMI,
ipment, tnc., Tel.
33566,
PLANT
3032~.
ATLANTA,
M.
Amb
COMMERCE,
335-~061.
DECATUR,
Tel
. 377-5559.
DUBLIN.
GAINESVILLE,
ing,
Ga.
887
0,
WINDER,
8.
0,
CHICAGO, 400 N.
66208,
KANSAS CITY
oo
C.
Smith, Tel.
~0207
,
LOUISVILLE,
70~5B,
NEW
833-990~.
Hendrix, Tel. 272-6667.
ROCK,
LOS
ANGELES,
Madlaon
FRANCISCO, 3420-25 th Stroot
FRANCISCO, Apparel City Sowing
St.,
ea
~2~·6630.
2525 N.W. 2nd Avo., Trlmco Sow·
633·1138.
CITY,
rose, Mgr., Tel. 871
1713 Coventry Road, Joe V.
16"
·.C732.
508
ORLEANS
SALES
lew
is
and Columbia with
STATES
732-84th Stroot, South,
3223 Willow Lone Dr
P.O. Bo• 17B3, James T.
1100
E.
Plea Blvd.,
5-5828.
Tel.
MArko!
1-6660.
..
,.,
Sowing
Machine
22 Barnum Road, Robert
506
N. Gordon 51. James C.
2120 Plasters Bridge Road,
P.O. Bo• 7261,
·9237.
Lakeview Drive. J.
Kno• St., John W. Jones.
RFD
",
John Bradberry.
Fifth Avo.,
(PRAIR
HE
franklin 51
IE V
2-17
05.
(SLIDELL)
0.C/6.C
B.
ILL
AGE)
3-2.CB.C
D.
Smith,
.,
fred
7351
Raymond E.
275
Pol•
.
INDUSTRIAL
OFFICES
MARYLAND
tMARYLAND
*MASSACHUSETTS
MASSACHUSETTS
MASSACHUSETTS
MICH
.,
MINNESOTA
MISS
IMISS
MISSOURI
·
W.
Tom
OH
L.
O~m~~~~~~·
OKLAHOMA
OREGON, 97220,
!NEW
!NEW
!NEW
NEW
NEW
NEW
*NEW
INEW
NEW
NORTH
St.,
=~:;r'rs~~~~~
Sorv
PE~~~~~~~~~:.~~
21215,
foolor, Tel.
Baltimore St., Tot.
llam E. Patm, Mgr., Tel.
Pedenen, Tel. 828-t.c12.
Woll
313
lou
Boy
U27
91
Mclaughlin, Tel.
63117),
E.
Terrace, Joseph
W. Whitson, Tel. Geneva 8-
Noll, Tel.
Whoolo
bohm, Tel.
m•nal Bldv
l
ng
Cu
Candell, Tel. Ivanhoe 3-
illiam
W
(Z
ip Codo 27407), also Harold E. Mlllor, Tol.
IO
Equipment Co., Tel. 661·5901.
727·B~99.
21204,
02767,
er
P.
Godek, Tel. VanDyke 2·
IGAN
~8223,
-SU-
~21
0.
55~26,
ll
Park, Minn., leonard W. Koehler, Tel. 6.C4-623
ISSIPPI 39209, JACKSON, 327
• tte, Tel. flootwood
(Tu
pelo)
3BBO
OURI
6~105,
5 Broadway, Tel. VIctor
63114, ST
also Je
rry
HAMPSHIRE
Haberman Jr., Tel. Tuxedo
JERSEY
07032,
JERSEY
07010,
JERSEY 08091, WEST
767-~350.
YORK
02110,
r, Tot. 5
1B-
YORK
1~502,
986-~693.
YORK
10001,
.),
Clarence
4-8800.
YORK
U60
lver Rd., Tel. BUller B-725
YORK 11553, UNIONDALE,
CAROLINA
D. Harr
~~109,
CLEVELAND,
~g~~BUS,
1
73119,
G.
B.
Wiley, Tel. 685-2B36.
~
l:
Phon•• 503/771 · 2159 (Portland) 206/ 624·
B:~::2~WNTOWN,
SEWING
MACHINES
AND REPRESENTATIVES
BALTIMORE,
BALTIMORE,
LEx
02111, BOSTON, 179 Lincoln 51., Wll·
02021, CANTON,
DETROIT,
MINNEAPOLIS,
I, Tel.
KANSAS
Che
Jinut 1-2368 . 8
H~cks,
03060,
Logl
lscl, Tel. 991 ·8
RUTHERFORD,
LATHAM,
7B5-6371.
MACEDON,
NEW
9,
ROCH
27~03,
od, Tel. 299-9367.
OKLAHOMA
PORTLAND,
P.O. Bo• 2505, Ralph
J. Doahow, Inc.,
ington 9 ·
1B3
8.
Uberty 2·01
TAUNTON,
5-1976.
LOUIS,
NASHUA,
NORTH
BERLIN,
YORK,
L.
ESTE
7.C77.
GREENS
4914 Pearl Road, Cui &
P.O.
47,
York
St.,
P.O.
Box
61
~9.
1
~56
t
Auburn, John Joyce, Tel.
2BOO
To•a• Avo.,
Eao
lvl
ow
larry l ancaster, P.O.
601/
B42-76 5
0.
CITY,
Toxll
2-9558.
57 Sylvan Avo., Clarence A.
Rosenquist, Mgr,, Tel. ChJcker·
lo Machinery Co.,
9022 Pall
ordy Lane, Carl
725
Warner (Zip Code
P.O.
Box
2-969
8.
ARLINGTON, 32M Gard
211.
2~6
Sylvan 51., Richard
2178.
P.O.
Box
3 Jupiter Way, James Hal·
370
7th
Avo
R,
A.
J. Adams Co., 1051
0.
B73
Henry 51., Anthony
BORO,
P.O.
~216
Ponnydolo Dr.,
Box
8
7~,
Larry
CITY
, 2226 Southwoll 53rd
1950 N.E. 1181h Avo.
P.O.
Box
B.
~17
W.
RFD,
Roy
T.
l-
2 Raynham,
51.
6.
51., Jamie
A.
Box
E.
257, Horman
011
26, Frank
A.
., (Penn Tor·
lox
226,
292-073~.
Sow
Kelson, Tel.
542, Luther
PEriNSYLVANIA
Doooan. Tel.
PENNSYLVANIA
Mcfadden,
Tel. 752-2442.
PENNSYLVANIA
Ave.,
John J,
*PENNSYLVANIA 19124,
Ave.,
Ben
W. Mer
!PENNSYLVANIA 15670,
R.D. No. 1, Bo• 26A, W. Dolo Spoor, Tel. (Pitllburgh)
5B
9,
also
563 -3
PENNSYLVANIA
M.
Bonder, Tol. 267-61
PENNSYlVANIA
Powell, 854-S
SOUT
II
CAROLINA
R. Crisl
er,
Tol. Sunset 7-0B63. P.O.
Corter. Tol.
SOUTH
Orville
fENNESSEE,
John W. Carter 615·6
TE
NNES
rioroce
TENNESSEE 3BI1
Li
TENNESS
follx
*TEXAS
~7~24,
TEXAS
Tel.
TEXAS
wall, Tel. 626·3183.
TEXAS
13126, Tel.
UTAH
Lorry
VIRG
Te
BRITISH
Madison Avo., Tel.
MANITOBA.
Bldg.,
*ONTARIO, TORONTO
Ki
*QUEBEC,
Charlo• do Lolour St. Tel.
25~-~255.
CAROLINA
W.
Gregory, Tel. Cedar 9-553
37~21,
SEE
37919,
E. Clinard, Tel. 5
ndhorst, Tel. Mutual 5-675
EE 3721
M.
Blunkall, Tel.
752~7,
J.
H. Muir Mgr
79926,
EL
59B
-292B.
76106,
FT.
7B213,
Dl
8~105,
SA
F.
Roavall, Tol.
INIA
24006,
l.
703·3~2-3233,
UNION
SPECIAL
COLUMBIA,
WINNIPEG
70
Arthur St., Tel.
ng
51.
Wool, Tel.
MONTREAL
18015,
BETHLEHEM,
868·8204
.
18003,
BERWICK,
lUll, CLARKS
Lafl
er, Tet. JUn,per 7-
PHILADELPHIA,
z,
Mgr., Tel. Gladstone
NEW
R.
N. Bator.
17567,
REAMSTOWN,
09, also
17~0~,
YORK,
O.CO,
also F.
2920~,
COLUMBIA, P.O.
29607,
CHATTANOOGA, 1711
92·UB9.
KNOXVILL
7,
MEMPHIS,
~.
NASHVILLE,
615-25~·753B.
DALLAS,
6718 Oakbrook atvd., P.O. Bo•
.,
PASO, P.O.
WORTH,
1201 Alta mont Dr., Arnold Slier-
SAN
ANTONIO, Jerry Gregory, P.O.
2-5924.
LT
LAKE
CITY,
IN
7-6931.
Roa
noke, P.O. Box 11.5
a
lso
P.
1212
1013
SUMMIT,
2820.
ALEXANDRIA,
P.O. Bo• 176, David
F.
J.
Barloa!c.
P.O.
Box
J,
Bartoslc,
Box
GREENVILL
E, 25 Sir Abbot St
E, 3905 Groonloaf Avo.,
B8-
1B65.
~695
Dunn
0.
2517 Woodber
Tot. 214/ 637-5990.
Box
9573, Edward
1215
C. Ebl
e.
CANADA
MACHINE
Co.
of
N.
BURNABY
2,
MU 3-3917.
2,
Fronk Thlormon,
2B,
Emp
ire
11,
John Coochotlo,
Jam01 Murr
204-
9~3-~933.
Peter fowler, Mgr.-Rop., 355
6·2939.
51
~/387-7191.
*
ea-c
E.
16th 51., Donald
428
Wool
~23~
Macaloalor
5-9800,
(Pittsburgh),
8U,
Harding
Bo•
~2~6.
4112, also
9.
Roy
Jo Circle,
Rd., Richard J.
ry
E.
E.
13th South 51.,
1,
Tom
Canada,
Ltd.
Rm.
201, Whltlo
Mgr
.-Rop., 9595
St
Drive,
S011th,
Traylor,
ay,
..
Grove
Vlrlyn
J.
W.
Box
1522
Ed
T.
..
FINEST
QUALITY
WORK
•
•
HIGHEST
PRODUCTION
RATES
•
•
LOWEST
MAINTENA
COSTS
N C E

Also Agent
AFRICA
ITEXIIlE &
IBAG
ALGERIA
ETHIOPIA,
GHANA.
IVORY
KENYA, NAIROBI -
MALAGA
MAURITIUS,
MOROCCO,
NIGERIA, APAPA,
SUDAN, KHARTOUM-franco Pinto (Sudan) Ltd., P.O.
BAG
MAKING
REPUBliC OF
Pr
llchard St.
72 Commercial Road.
RHODESIA,
Barton House, Corner
ltd
32
CAPETOWN- Wolos
St.
Notai-
ot
Potgleter St.
Rhodos Stroot. SAllSBURY- 95 Victoria
LUSAKA
Road
Mohamed
Asfaho Woosen
3547
(L &
Kolnango St. (P.O. &or 5933)
ganyl
De
IL
Machines) Hall, Geneve, langlolt, ltd., 42
N.wton
tdrlnl
Ltd. 9
305.
BUlAWAY0-133 Fifo
ClOSING
. REPUBliC
&
MACHINESI South African Scalo Co. Ply.,
Von
Brandis St. BlOMFONTEIN- 53 Zoslran St.
EAST
lONDON
355
Murchison.
PIETE~MARITZ8URG,
RHODESIA,
- W. &
& Codring
, AlGIER
V.
(l
ASMARA-5.A
ACCRA-Crown
IL
&
C)
.
COAST·ABIDJAN
C)
ko
and Zanzibar)
SY REPUBliC- TANANARIVE-Sac. Ind.
l'Emyme,
Cl
PORT
St.
CASABLANCA
Eo
Sakall
Warohouso Road.
(l & Cl
MACHINES)
SOUTH
AFRICA-JOHANNESBURG
CAPfTOWN-78
PORT
SWJnley
Of
SOUTH
and
BrH
- 33·35 North Stroot,
PORT
PRETORIA,
BULAWAY0-2
T.
Avory (Zambia) Ltd., Comor Stanley
ton
Street.
s-E
tablluomenl
& C)
. Caldoronl Africa, Avonuo P.
ll & C)
Industrial
- Eh. Joan Abllo·Ga t,
Tronscandla,
Bolte
Postale 1078,
LOUI5-(8ag
- R. Golumann & Fils,
(l)
LAGOS-5unftag Knitting Mil
(L
Berzack Bros.,
Darling S
EliZABETH-277
St.
Ave. and MoRal St.
AFRICA-JOIIAHNESBURG-
Sts.
DURBAN-22
EliZABETH-Box
VEREENGING-2
StrHt, ZAMBIA
All
Amor, 62
Enter
prises
ltd.,
College
(l & C)
(Also Uganda, Tan·
17
Rue
Closing &
& C)
t.
DURBAN-
Main Stroot.
SAliSBURY-2
LADYSMITH,
611. Alt o
Leander
Bou
ltd
., P.O.
Bax
House,
Et
Cletnenceau
Bag
Making
Sir
William
luo
ls
(Nigoroat
ASIA
CAMBODIA,
HONG
INDIA, CALCUTTA-Parrot Sowing Machl
Sovaram Bysack St. G.P.O . Post
JAPAN,
Klla·ku.
Alao
and Okayama.
LAOS,
PAKISTAN, (WEST)
Trading Corp., 29 Zeenat Mantlon, Mcleod Road. (EAST
AND
Thomas
REPUBLIC
(Taiwan)
SINGAPORE
Yong
THAILAND,
Box
VIETNAM,
Trlnh·Minh·Tho.
PHOM·PENH- Donls Froros, 219 P.B. SJsa.
woth, P .
0.
Box
AB.
(C
&
KONG-G.
309,
Marina Hovte,
OSAKA-Kondo
(L)
at1
AJhlkaga,
VIETIANE-Donh
WESTJ
C.
ICeay,
OF CHINA, TAIWAN,
Ltd
3-G
Slak
St.
BANGKOK-Yip
23.
(L & C)
SAIGON-Thai-Binh
Branch-
(Bag cloarna a,.d
., 16 Nan Yang St.
Abo
Ll
R.
Coleman Co. (Hong Kong) Ltd., Rm.
•s
QuMn'•
Sewing
Machlne,
TOKYO. 3·6
Fuka
l, Hokkaido,
Froros, P.
KARACHI·2
Ltd.,
. R. Coleman (Slngoporo lt
(C & L)
all
15
of
(ToxtJio
Bai
Uc Street, Oun
TAIPEI-G.
(l
Malaysia.
In Tool & Co
.Duong Cong.
Road, Centlol.
no
(P.)
Box
2A
.
(l & C)
Ltd
., Umegae· Cho
Glnza Chuo·Ku 163.
Nagoya,
O.
Box
133.
Mach
lnos
)-Unlvonal
bag
making machine•)
dn,
R.
Coleman Ca.
& C)
d.,
(l & C)
., Ltd., P.O.
TY,
Ltd. 9/1
Nllgota,
(C & L)
Scotland.
No. I ·M
147
AUSTRALIA
SOLE
DISTRIBUTORS
Street,
wlck
St.,
St . AGENTS , SOUTH AUSTRALIA·
Charllck
LIA
PERTH-Thomsons Ply.
LAUNCESTON·Sow
, Capron, Carlor
SYDNEY
2000.
Valley,
ltd.,
Branche• at ,
N.t. MELBOURNE
London Road, Milo End. WES
Kn
it Ply.
BRISBANt--45A
ltd
., 789
ltd.,
72·7A Goorgo St.
Ply
.,
ltd.,
A90
300()-15A
A Beckett
ADELAIDE-WIIIIom
TERN
AUSTRA
Hay
St.
TASMANIA
(l
Ltd
135/7
(l)
Allwal
House,
-
levard
Box
1798.
Com.
Boa
Ruo.
Kont
Bruna-
& C)
Sales
Agents For UNION
for
(L)
LEWIS
and
AUSTRIA,
VIENNA
.
O.H.G.,
100
NTN)
BELGIUM,
of
America,
!Cl
DENMARK,
Sy
· lndustrlon
BORG,
AND
SILKEBORG.
FINLAND,
88
Vatlunlemonkatu 13. Branche• at
ltalo.
TURKU,
FRANCE, PARIS-C
france,
Olrectour,
Pare Salnt·Maur.
Alexandre
des Pensoet.
GERMANY,
brl
k,
G.m.
Director.
AT, BERLIN,
BURG,
GREAT
BRITAIN-(Toxtllo Mochlnory)-ENGLAND
OADBY
Lid., Mondervell Road, lnduahlol Estate.
Manager.
Old
St. (A. W. J. Brownloo, Monag
BRISTOL,
MILNGAVIE
bar Avenue.
& Son (S
MANCHESTER
El
Grove Works, lovanshulmo.
FAST
15,
GLASGOW S.E.
(Bag Closing and Bag Making
DUNDEE-Thomas
for entrre British
GREECE,
trak! St.
ICELAND,
Ia
(l
&
IRELAND,
Parnell Street
Mach
ine•) Thomal
Scotland.
ITALY,
I 20121
Varoso
18.
MALTA,
VALLETTA-Frank Borda &
S
hoot (l & C)
THE
NETHERLANDS.
C. &
H.
ARNHEM,
TARD,
TILBURG.
NOR
WAY,
I
!
7.
BERGEN-Bjornsonast 2A.
PORTUGAl,
de
Forrester
SPAIN, 8ARCELONA-Rapldo, S. A., Via
&
C)
SWEDEN.
91.
Branch
and S
TOCKHOLM.
SWITZERLAND,
au1tr. (L-Butto n-Sawer)
YUGOSLAVIA,
33.
(l
& C)
A-,06,-Naeachustar
Marlahllfentr.
BRUSSELS--Union Special
90
Rue
COPENHAGEN-Rothonborg Spoclalmasklnor for
A/S,
HERNING,
KOLN,
KOLD
(l & C)
HELSINKI·LAUTTASAARI
Humallllonkatu 7·B.
e.
91
Avo.
de
Branches af1
LYON,
Bou
tin.
TOULOUSE
(L & CJ
STUTTGART
b.H.,
Schwabstr.
Th.
M.
&aan&tra,
BIELEFELD,
MUNCHEN,
(NR. LEICESTER)-Un lon Special Machine Company,
LEEDS-60
l. J. Heard,
(GlASGOW)-Doorl
SUB·AGENTS
ewing
Mochlno
19-S
Aktox
ltd
-Aito
C. Keay,
hla
ATHENs-Georges
(l
&
C)
REYKJAVIK-Magnus Thorgo lr11on, Skolavordustlg
C).
DUBLIN-(Toatllo Machlnos) W.
(L
I.
C.
MILANO-Giovanni
(l & C)
Verbeek, Klovenlersburgwal n . Offices otr
ENSCHfDE,
(l & C)
MANGLERUD-Joc. Jacobson
OPORTO-Rott
91
A.
(l)
GOTEBORG
at.
BORAS. lunnegoton A.
Ill
URDORF
KIRCHE
LATIN
ARGENTINA,
Son Jose
BOLIVIA-Lowe
·
In
.
8RAZIL,
erct
ALEGRE-Ruo Voluntario •
Prince•a Isabel l 05,
MacKenzie 117.
CHILE,
Santa
COLOMBIA,
30 112·99.
,
BUCARAMANGA-Callo
33/35
MEDELLIN-Carr01a
COSTA
19A9.
DOMINICAN
quez,
BUENOS
350.
(Union Speci
go
3A·5~.
nstoin & Stewart, S.A.C., Calle Santo Oom·
It
AO,
Santiago,
SAO PAULO--Pancostura S.A.
o,
Alameda, Cleveland,
(C & L)
SANTIAGO-Lowonstoln & Stewart, S.A.C., Collo
Domingo I
lAO.
BOGOTA-Macalzado,
&ranchos a t
. MANIZALE5-E.
RICA, SAN
(l & C)
G.,
51,
JOSE-Enrlquo
REPUBLIC,
Calle Dr. Pedro Urena
SPECIAL
(C)
COLUMBIA where marked.
Machines;
EUROPE
Heinri
ch
51,
Polffach
77,
de
Ia Caserne,
Nikolai Plod s 23. Ofllcos
ING, ODENSE, RI
dea Machlnes Union Speci
Ia
(59)
VILLEURBANNE
(7000)-Unlon
Merr
19
Tho
ry),
. A. Sml
. 186 Cavohlll Road. SCOTLAND,
,dl
ce & Co
t.
C)
(Bag Clotlng and Bag
Koay,
Mach
Gutlave
- Suomon Konolllke
TAMPERE-Plenloollhuo
(L
& C)
Republlque-Tho
llllE
5
(HAUTE
Special Maschlnonfa.
33-Dr.
K. Schulz, Managing
Director of Sa loa,
EBINGEN,
OCHTRUP.
lon Stroot.
r LONDON, W.
ltd.,
Yannekouros·Dimoullt,
FRANKFURT,
(l & C)
LONDON-IBA-1
er).
Ride. Kingswood, SCOTLAND,
ck
R.
Robinson,
58 Gr
eat
th,
(MonchesterJ
NORTHERN
., 9 Stevenson Stroot.
Mach
ltd.,
15 Battle Street- Agent
ltd.,
15 Baltic
Schutter
ILJ
(C--ercepl
ine Corporation
Thlerle, Mgr.
ah
SSKOV
.MRHUS
al
s.
de
Semlyen,
Re
tldonce
Cltoau•,
(RHONE)
GARONNE) 9 Rue
ines) SCOTLAND,
58
BRANCHE
LE2
5LN-
Mr
.
J.
C. Spencer,
SALES
OFFICES,
~8
1-G.
Johnson
Tltchneld Street.
Ltd
.,
IRELAND-BEL-
30
llyt~man,
Mak
St.,
Dundee,
Conti & Nlpotl, Via
~
ons
,
AMSTERDAM-H.
GRONINGEN,
(C & Ll
& Jonu1, Succs.
5-Jac
. Jacobson
(ZH)
8902-urqul
ltd. 51/AI
V.
A/S,
A/8,
Machlnohandol
ROTTERDAM,
Enobakkvolon
lda.,
Rua
layot
ona 37.
Mol
ndoh
Aho
in
MALMO
o & Clo., Vog
Zacha•y
vagen
IM (7312)- Josof Scharzor Bou
AMERICA
AIRE5-Pamaco
Chilo.
RIO
(l
&
3A
Bro
36-t
SANTA
Costura S.A.C.I.y.F.
al
Machine
Com
pany),
(l
(l
&
C)
-Induatrla e Com
AAA
. Branche• at
do
Patrio .533; RECIFE-Rua
DE
JANEl
RO-Rua
C)
Mercantll , S.A.,
BARRANQUILLA
I 17·A5.
CALI-Carro
1louor, Carrera 22 I I&.AA.
8.
(l & C)
Rodrigues S. , P.O.
DOMINGO-Roberto
19,
(L & C)
PORTO
Alexandre
Carr
- Carrora A5·B
ra 7 11
Domin·
ECUADOR,
El
GUATEMALA,
HONDURAS, S
Ml·
MEXICO,
0/Y,
-
de
NICARAGUA,
ruo
PANAMA, PANAMA- International
PERU,
S
PUERTO
HAM·
SUR
URUGUAY,
16
VENEZUELA,
Clach·
CYPRUS,
Pork
IRAN, TEHERAN-SoYa Tradlne Corp., Ave.
(C)
IRAQ, BAGHDAD-sons of 0 .
ISRAEL,
Pe-
JOROAN-Bandar & Afactlngl, B.P.
LEBANON,
22A
SYRIA,
ing
TURKEY,
U.A.R., Colro--Misr Impart & Export
SOLE DISTRIBUTOR
SIT·
Barao
(l
GUAYAQUIL-Distrlbul
S.A
., Mal
econ
Avonlda
SALVADOR,
de
El Salvador, Colonia
CIA.,
Box
(l & C)
de
C. V
JARA,
dora Union Especial, S.A.
(Apartada 28
Royos
1
303.
de
Colombia Building, P
Alfonso Ua
Box
INAM, PAIAMARIBO-Kirpalanl's, Ltd.,
St.
Morcodos
Chorro
cauppls St.
881
2021,
(l
& C)
archo Hoyok.
Han Nr.
Toch. Sub.Agont-A.
'hubra.
St.
AUCKLAND.
Nelson St.
Islands, Gilbert Islands,
Tahiti,
CHURCH-90
P.O.
Box
P.O.
Simon
Patrla
768.
SAN
SALVADOR-Distrlbuldora Union Special
GUATEMALA-Union Toxtll
LTDA.,
&a
Avonlda IO·
AN
559.
LIMA,
2352.
(l & C)
P.O.
DAMA5-8andar
Box
602.
Box
PEDRO
TEGUCIGALPA-Carlos Handa!,
MONTERREY,
.,
Cuouhtomoc Norte
JAL.-H
idalgo
070),
e
o.
Ill
MANAGUA-Casa
(l)
Brei\o-Un
arto
1AA5
RICO,
SAN
JUAN-Abarca
(L & C)
MONTEVIDEO-Siorer & Cia . , S.
1312.
(l)
CARACAs-H
29.
(L)
NEAR
NICOSIA-Chrlltodoulldos
Ill
Bax
1720.
Alwlyah.
(l & C)
TEL
AVIV-L.
BEIRUT-Ibrah
(l
& C)
1ST
ANIUl-.
A6·A7.
(l
& C)
IL
&
Cl
NEW
, H.
BRANCH
(l)
Also--New
and Tonga. SUB-AGENTSt Glenderm ld.
Orboll St.
AO.
(C)
FIJI
Ill
SAMOA
2DA.
(L)
PACIFIC
HAWAII
ol.
lontr
& C)
-
era
3·
Box
, HONOLULU-Atlsow, Inc. , 1892-D Kal
(Ted
Ue l & C). (Bog Closing and Bag Maki
H. S. Cray Co.,
PHILIPPINE ISLANDS,
Inc
., 7232 Malugay Street, (Buendia Extens i
CEBU. (L & C)
WEST
JAMA
ICA, KINGSTON- Morris
(l)
TRINIDAD, PORT
(l & C)
759
INDIES
OF SPAIN-
Also--8ARIADOS. GRENADA,
dora
lollvor
(l & C)
Va
SULA-Jocobo
N.L.-Tallerea
A5 y A7t
de
SAN
LUIS
Richard 0 . Custor,
#2308,
&ranch
at
OUITO-
lro.
Ill
Gunter
A3,
Zono I
335.
Branches at• GUADALA·
MEXICO,
C.V., Ave. , Plno Suarez 99·a
POTOSI,
Honnlng &
(l
& C)
E. Handol, P. O.
P.O. Box
Perez Zozayo, S.A.
D.F.-Distrlbul
S.L
.P.- J.
Hontgon, 3A Callo N.
de
Comercl
o,
.0.
lted Agenci
·1 AA7.
Box
(l & C)
127.5.
Warohouso
es,
S.A.
S.A., Banco
(Peru) Av.
Corp.,
17·27
A.,
Uruguaya,
. Blohm, S.A., Dr. Paul A.
EAST
lras
. &
Co.,
Soray Saadlyoh.
0.
Agoplan (IRAQ),
Taubo, ltd., 15
lm R. Audl & Clo.,
& Aractlngl, 8.P.
llenmayor, Mahmutpasa Abut Etondt
Kavaldllan. S.A.R.l.. 200
ZEALAND
A.
Tuck & Co., Ltd.,
AT•
WELLINGTON, Leos
Caledonia, Cook lalands, ElUte
New
Hebrlde1, Samoa (Ame flcon),
DUNEDIN-192·1V
SUVA-Karl
(WESTERN),
lozarto•ehr
(l & Cl
11A"-Damas
llli
tiA~.
Co
.. o Ruo
enblom
11
(l & C)
P.O.
Ruo
17t
ltd
.,
6 Castlo
R. Fleischman, P.O.
APIA-
S. C. Porclval,
ISLANDS
akaua
Puuloa Rd.
MAKATI.
IIZAL-Atk
FEDERATION,
E.
Parkin, 67 Church Stroot.
Ack<lll & Co., 17 Honry St.
ng Machine
lns, Kroll & Co.,
on).
Branch at
JAMAICA
TOBAGO
.
517.
do
los
O.
P.O .
Maagdon
9~
Trl
lo•
St.
Ill
, Syria
Patrl·
Adt>-
Shari•
Atbort
Bld
g.,
CHRIST
St.,
Ave.
·
·
l
-
l)
Additional
Sales
Agents
for
(L)
LEWIS
and
(C)
COLUMBIA Machines
4·U
AUSTRIA
IV, VIENNA-
Wiedner Hauptstraue
BELGIUM
, BRUSSELs-H . V. Machln
Kru
idturnl
FRANCE,
GERMANY,
GREAT
oan
PARI5-Sodete
Ill
KREFELD-Harbert Jannaen, Alte
(C. ti
e ma ch.)
BRITAIN-ENGLAND, LONDON, E.
Mach
lne Company,
DON, 89 Beddlnoton Lane. LEED5--60 Merr
MANCHESTER,
GLASGOW 5
IRELAND,
BELFAST
RE
PUBLIC
OF
223/A Parnell Stroot .
Pranz:
Koerpert & Sa
36.
(C)
57a,
Buy
ltd
105·107A Cerpo ra llan Street. SCOTLAND,
2-11
Drumrooch Placo, Toryg
1"-W.
IRELAND,
(L)
oha
l Bldg.
IL)
G.
Amon & Cle. ,
., 128-1 32 Curtaln Road.
f. Maxwell, 20 Todbu rn Park.
DUBLIN
- Wm. Blythma o.
hne,
ndol C & H Vorbook,
14
Rue
Comm
Unneutr
C.2-Eastman
lon Stre•t.
lon. NORTHERN
K.G ..
ln
.
CROY
ltd.,
..
•oA
.
ISRAEL,
MEXICO,
MOROCCO
TEL
AVIV-Iuaol
Ho
lovy St. (C)
MEXICO, D.F.
Casor, Av. Ropubtlc
, CASABLANCA-Durkopp Coudrex, 25
nona.
(C)
Sowing Machine Co., 22 Yohudo
-Cosa
Dol
Salvador 19 ·93
Dlo• do Maqulnas do
(C)
Ruo
lkucu.
REPUBLIC
OF
SOUTH
Sewf
ng
Machine
Stroot. Branches a h
(C)
RHODESIA,
SWEDEN,
SWITZERLAND,
URUGUAY,
FEDERATION
BULAWAYO-Afrlcan Sowing
(Pvt.)
Lid
., 2
BORAS-Husqvama,
Katr
tnedaltgatan 1
I
MALMO-hak
-STOCKHOLM-IIrunnsgaton 6·8.
"austr
27.
SlhlllraHo
37.
MONTEVIDEO-C.
llncon
658·60. (CI
AFRICA, JOHANNESBURG-African
Com
pany (Ply.)
CAPE TOWN-110
OF
Loanidas
Houso, 138 Rhodos Avo. (C)
3.
Branches1 GOTEBORG-Strgbergsllden
Slaktarogatan
ZURICH-Fritz Zollwogor & Sohno, Sot.
(L.
except
luHon
(C)
ltd
., 11B Prelldent
Plein St.,
DURBAN.
RHODESIA & NYASALAND
Machlno Compaoy (Rhodosla)
lndustrbymotk&ner
9-0IEBRO-Storta
(C)
Sewer) GuttJ
lrandos & Oa
npr A.G.,
.,
SA
A/1-
oot 19
. Cello
,

,...o
..
~
..
0
WORLD'S
,..,lE
FINE
ST
,,
QU
ALITY
*
~'
INDUSTRIAL
SEWING
MACHINES
UNION
SPECIAL
maintains sales
facilities throughout the world. These offices
aid
you
in
the selection of
equipment for your
Special representatives
tory trained
promptly
tion, there
serve you.
ATLANTA,
BOSTON,
CHICAGO,
DALLAS, TEXAS
LOS ANGELES, CAL.
NEW
PHILADELPHIA, PA.
GA.
MASS.
ILL.
YORK, N. Y.
and
and
is
a Union Special Representative to
Check with
particular operation. Union
and
are
able
efficiently. Whatever your loca-
him
the
service men
to serve your needs
today.
MONTREAL, CANADA
TORONTO, CANADA
BRUSSELS,
LEICESTER,
LONDON,
PARIS, FRANCE
sTunGART,
and
service
will
right sewing
are
fac-
BELGIUM
ENGLAND
ENGLAND
GERMANY
400
Representatives
MACHINE
N.
FRANKLIN
industrial
and
cities
distributors
throughout
COMPANY
ST
. ,
CHICAGO,
in
the
all
Important
world.
ILL.
60610