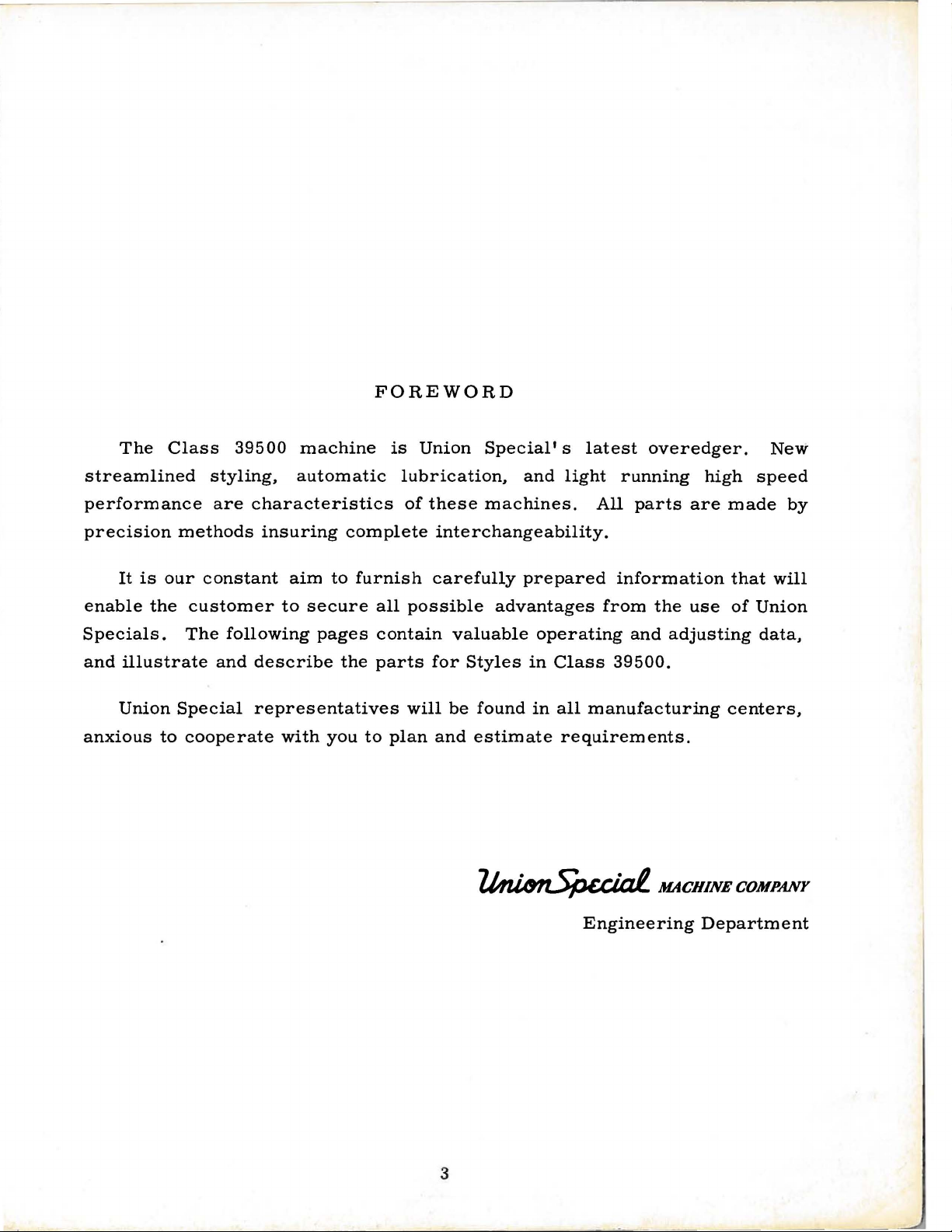
FOREWORD
The
streamlined
performance
precision
It
enable
Specials.
and
Union
anxious
Class
is
our
the
illustrate
to
39500
styling,
are
methods
constant
customer
The
following
and
Special
cooperate
machine
automatic
characteristics
insuring
aim
to
describe
representatives
with
complete
to
secure
pages
the
you
furnish
is
lubrication,
of
all
possible
contain
parts
will
to
plan
Union
these
interchangeability.
carefully
for
and
Special's
machines.
advantages
valuable
Styles
be
found
estimate
and
prepared
operating
in
in
~
latest
light
All
Class
all
manufacturing
requirements.
overedger.
running
parts
information
from
and
39500.
New
high
are
the
use
adjusting
MACHINECOMPANY
speed
made
that
will
of
Union
data,
centers,
by
3
Engineering
Department
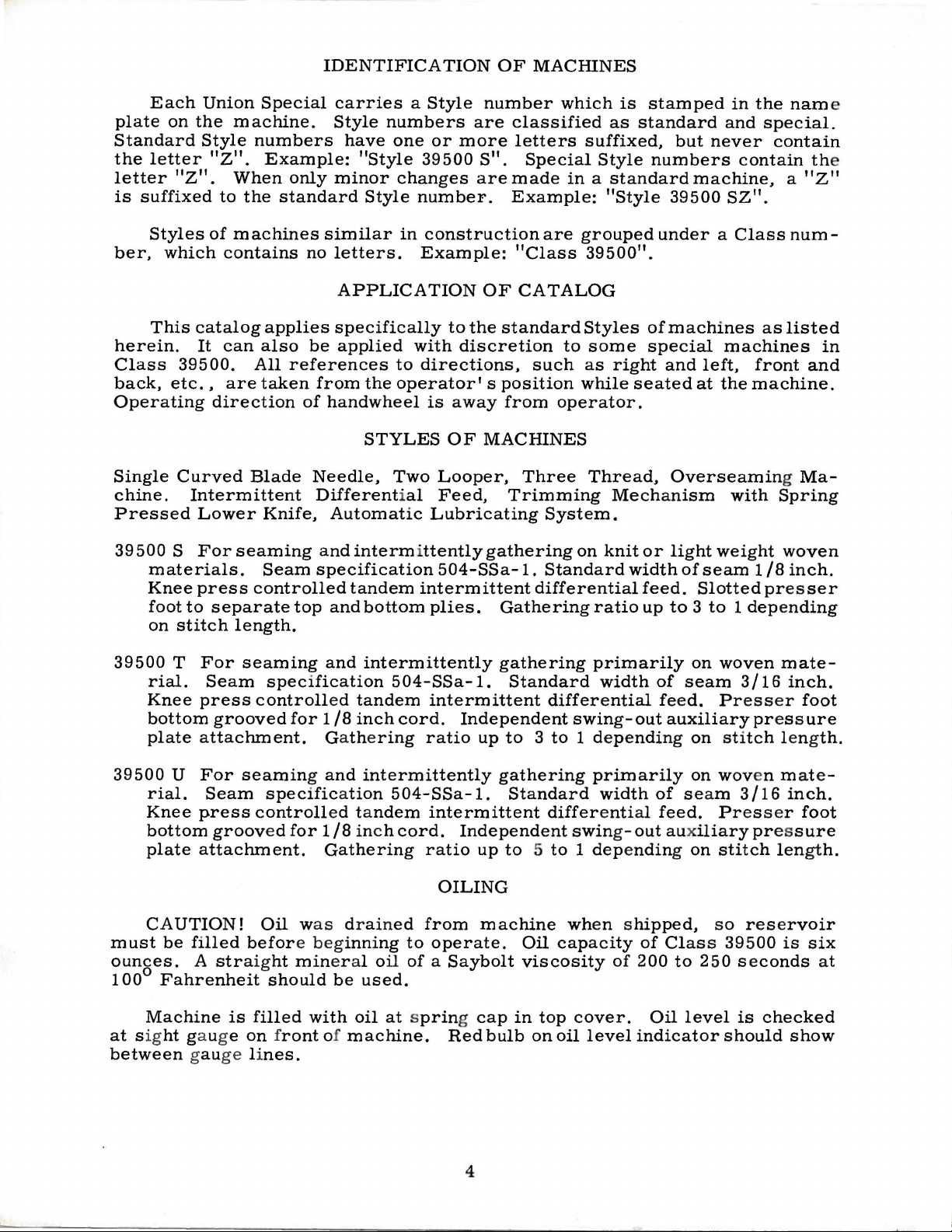
IDENTIFICATION
OF
MACHINES
Each
plate
Standard
the
letter
letter
is
suffixed
Styles
ber,
This
herein.
Class
back,
Operating
Single
chine.
Pressed
Union
on
the
Style
"Z".
"Z".
of
which
catalog
It
39500.
etc. , are
direction
Curved
Intermittent
Lower
39500 S For
materials.
Knee
foot
on
press
to
separate
stitch
Special
machine.
numbers
Example:
When
to
the
machines
contains
applies
can
also
All
taken
Blade
Knife,
seaming
Seam
controlled
length.
carries
Style
only
minor
standard
similar
no
letters.
APPLICATION
specifically
be
applied
references
from
of
handwheel
Needle,
Differential
Automatic
and
specification
top
and
a
Style
numbers
have
one
"Style
or
39500
changes
Style
numbe:r.
in
construction
Example:
to
with
to
directions,
the
operator' s position
is
STYLES
Two
OF
Looper,
Feed
Lubricating
intermittently
504-SSa-1.
tandem
bottom
intermittent
plies.
number
are
classified
more
letters
S".
aremade
Example: "Style
"Class
OF
the
standard
discretion
away
from
MACHINES
,
Trimming
gathering
Gathering
which
suffixed,
Special
Style
in a standardmachine,
are
grouped
39500
CATALOG
Styles
to
some
such
as
while
operator.
Three
Thread,
System.
on
knit
Standard
differential
ratio
is
stamped
as
standard
but
numbers
39500
under a Class
11
•
of
machines
special
right
and
seated
Overseamin
Mechanism
or
light
width
of
feed.
up
to 3 to 1 depending
in
the
and
special.
never
contain
contain the
SZ".
as
listed
machines
left, front
at
the
machine
g
with
weight
seam
Spring
woven
1/8
Slotted pres
nam
a
"Z"
num-
and
Ma-
inch
ser
e
in
.
.
39500
T
For
rial.
Knee
press
bottom
plate
39500
attachment.
U
For
rial.
Knee
press
bottom
plate
attachment.
CAUTION!
must
ounces.
1
00°
Fahrenheit
be
filled
A
Machine
at sig
ht
ga uge
between gau
seaming
Seam
specification
controll
grooved
seaming and
Seam
specification
controll
groov
ed
Oil was
before beg
straight
should
is
filled
on front
ge lines.
and
ed
tandem
for
1/8
inch
Gathe
ed ta
for
1 I 8 inch
Gathering
dr ained
inning
m i ner al o
be
with
oil
of
machine.
intermittently
504-SSa-1.
intermittent
cord. Independent
ring
ratio
intermittently
504-SSa-1.
ndem
intermittent
cord.
Independent
ratio
OILING
from
to
operate.
il
of a Saybolt
used.
at spring cap
Red
gathering
Standard
primarily
width
differential fee
swing-out
up
to 3 to
gathering
Standard
1 depe
primarily
width
differenti
ndi
al
swing-out aux
up
to 5 to 1 depending on
machine
in
bulb
wh
Oil
capacity
viscosity
top
cover.
on
oil
level
en s
of
hipped,
of
200
indicator
on
of
seam
d.
auxiliary
ng
on
on
of seam
feed.
iliary pres
Clas
s 395
to
250 s e
Oil
level
woven
Pr
sti
wov
mate-
3/16
inch.
esser foot
pr
es s
ure
tch
leng
th.
en m at e -
3/16
inch.
Presser foot
sure
stitch
s o r e s e
should
00
conds
is
checked
length.
rvoir
is
six
at
show
4
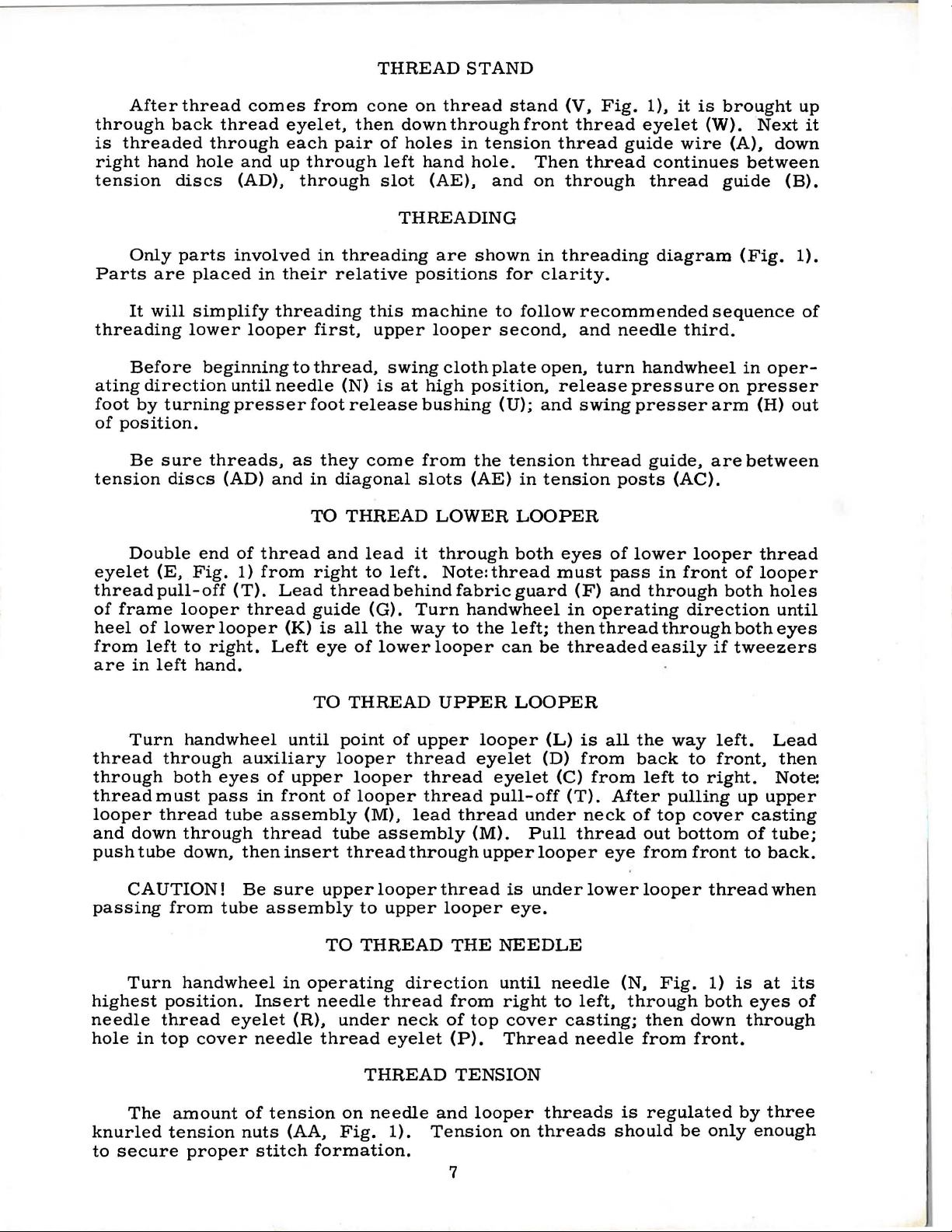
THREAD
STAND
Afterthread
through
is
threaded
right
hand
tension
Only
Parts
It
are
will
threading
Before
ating
foot
of
direction
by
position.
Be
sure
tension
Double
eyelet
thread
of
heel
from
are
(E,
pull-off
frame
of
left
in
left
back
through
hole
discs
parts
placed
simplify
lower
beginning
turning
threads.
discs
end
Fig.
looper
lower
to
right.
hand.
comes
thread
and
(AD).
involved
in
looper
until
presser
(AD)
of
thread
1)
from
(T).
thread
looper
from
eyelet.
each
up
pair
through
through
in
their
relative
threading
first.
to
thread.
needle
foot
as
they
and
in
diagonal
TO
and
right
Lead
thread
guide
(K)
is
Left
eye
cone
then
down
of
holes
left
slot
THREADING
threading
this
machine
upper
swing
(N)
is
at
release
come
THREAD
lead
to
left.
behind
(G).
all
the
way
of
lower
on
thread
through
in
hand
hole.
(AE).
are
shown
positions
looper
cloth
high
position.
bushing
from
slots
the
(AE)
LOWER
it
through
Note:thread
fabric
Turn
handwheel
to
the
looper
stand
front
tension
Then
and
on
for
to
follow
second.
plate
( U);
tension
in
LOOPER
both
guard
left;
can
(V.
thread
thread
thread
through
in
threading
clarity.
recommended
and
open.
turn
release
and
swing
thread
tension
eyes
must
(F)
in
operating
then
thread
be
threaded
Fig.
guide
needle
pressure
posts
of
pass
and
presser
lower
1).
it
is
brought
eyelet
(W).
wire
continues
thread
guide
diagram
sequence
third.
handwheel
on
arm
guide,
are
(AC).
looper
in
front
through
direction
through
easily
if
Next
(A).
down
between
(Fig.
in
oper-
presser
(H)
between
thread
of
looper
both
holes
until
both
eyes
tweezers
up
it
(B).
1).
of
out
Turn
thread
through
through
both
threadmust
looper
and
push
thread
down
tube
CAUTION!
passing
from
Turn
highest
needle
hole
knurled
to
secure
in
The
position.
thread
top
amount
tension
handwheel
auxiliary
eyes
pass
in
tube
through
down,
then
Be
tube
handwheel
Insert
eyelet
cover
needle
of
nuts
proper
stitch
TO
until
of
upper
front
assembly
thread
insert
sure
upper
assembly
TO
in
operating
needle
(R),
thread
tension
(AA.
formation.
THREAD
point
looper
looper
of
looper
(M).
tube
assembly
thread
looper
to
upper
THREAD
thread
under
eyelet
THREAD
on
needle
Fig.
1).
UPPER
of
upper
thread
thread
thread
lead
through
thread
looper
direction
neck
of
and
Tension
LOOPER
looper
eyelet
eyelet
pull-off
thread
(M).
upper
is
eye.
THE
NEEDLE
until
from
(P).
top
right
cover
Thread
TENSION
looper
on
7
(L)
(D)
(C)
under
Pull
looper
under
needle
to
casting;
threads
threads
is
from
from
(T).
neck
thread
eye
lower
left.
needle
all
the
back
left
After
of
out
from
looper
(N.
through
then
from
is
should
way
left.
to
front,
to
right.
pulling
top
cover
bottom
front
thread
Fig.
1)
both
down
front.
regulated
be
only
Lead
then
Note:
up
upper
casting
of
tube;
to
back.
when
is
at
eyes
through
by
three
enough
its
of
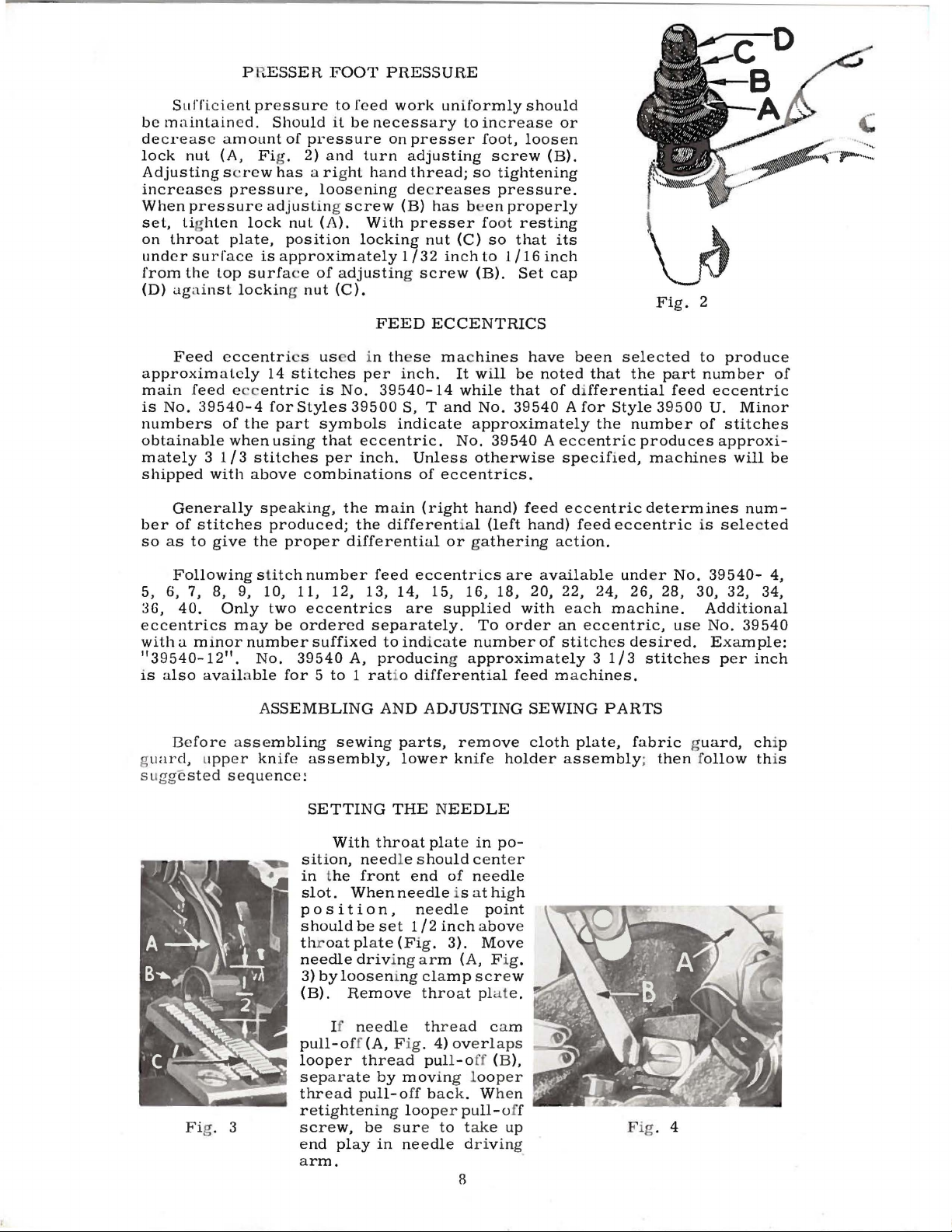
Suffi
be
maintained.
de
crea
s e
lock
nul
Adjusting
increases
When
pressure
set, lig
on
throat
under
from
(D) ug·
surface
the
1insl
P
,ESSER
ci e
nt
pressure
Should
amount
(A, Fig . 2)
s c
rew
has a right
pressure,
adjusting screw
hten
lock
plate,
is
approximately
lop
surfa
locking nut
FOOT
to
il
be
of
pressure
and
loosening dec
nul
(i\).
position
ce
of
adjusting screw
(C).
PRESSURE
feed
necessary
on
turn
hand
Wilh
locking
FEED
work
uniformly
presser
adjusting
thread;
reases
(B)
has been
presser
nut
1 I
32
inch
ECCENTRICS
lo
so
(C)
(B).
should
increase
foot,
loosen
screw
tightening
pressure.
properly
fo
ot
resting
so
that
to
1 I
16
Set
or
(B).
its
inch
cap
Fig.
2
Feed
approximately
main
is
No.
numbers
obtainable
mately
shipped
Generally
ber
of
so
as
Following
5,
6,
36,
eccentrics
with a minor number
"39540-12".
is
also
Defore
uard, upper
g
sugge
feed
39540-4
3 1 I 3
stitches
to
7,
40.
available
sted
eccentri
e c
of
the
when
with
give
8,
9,
Only
may
asse
sequence:
14
stitches
entric
for
part
using
stitches
above
speaking,
produced;
the
proper
stitch
10,
two
be
No.
for 5 to 1 ratio
ASSEMBLING
mbling
knife
s
us
d i n
per
is
No.
Styles
combinations
11, 12, 13,
ordered
39540
39500
symbols
that
eccentric.
per
inch.
the
the
differential
number
eccentrics
suffixed
A,
sewing
assembly,
main
feed
separately.
producing approximately
these
39540-14
different'al
to
AND
machines
inch.
S, T and
indicate
Unless
of
eccentrics
(right
or gathering
eccentrics
14,
15,
are
supplied
indicate
differential
ADJUSTING
parts,
lower
It
knife
have
will
be
noted
while
No.
remove
that
No.
39540 A for
approximately
39540 A eccentric
otherwise
.
hand)
16,
number
(left
18,
To
feed
hand)
are
available
20,
with
order
of
feed mac
SEWING
cloth
holder
been
of differential
specified,
eccentric
action.
22,
each
an
stitch
assembly; then follow this
selected
that
the
Style
the
number
feed
eccentric
under
24, 26, 28,
machine.
eccentric,
es
desired.
3 1 I 3
hines.
PARTS
plate,
fabric guard, chip
to
part
feed
39500
of
produces
machines
determines
is
No.
30, 32, 34,
use
stitches
produce
number
eccentric
U.
Minor
stitches
approxi-
will
num-
selected
39540-
Additional
No.
39540
Example:
per
of
be
4,
inch
Fi
g . 3
SETTING
With
sition,
in the
slot.
position,
should
throat
needle
3)
by
loosening
(B).
If
pull-off(A,
looper
separate
thread
retighten
screw,
end play
arm.
THE
throat
need
front
When
be
set
plate
driving
Remove
needle
F i
thread
by
pull-off
ing
be
sure
in
NEEDLE
plate
in
po-
le
should
end
needle
needle
112
(Fig.
arm
clamp
throat plat
thread
g.
pull-o
mov
loop
needle driving
of
is
inch
3).
(A, F i
4)
overlaps
ing loo
bac
k. W
er
pull-o
to
8
center
needle
at
high
point
above
Move
screw
cam
ff (B),
take
per
hen
g.
e.
ff
up
Fig. 4
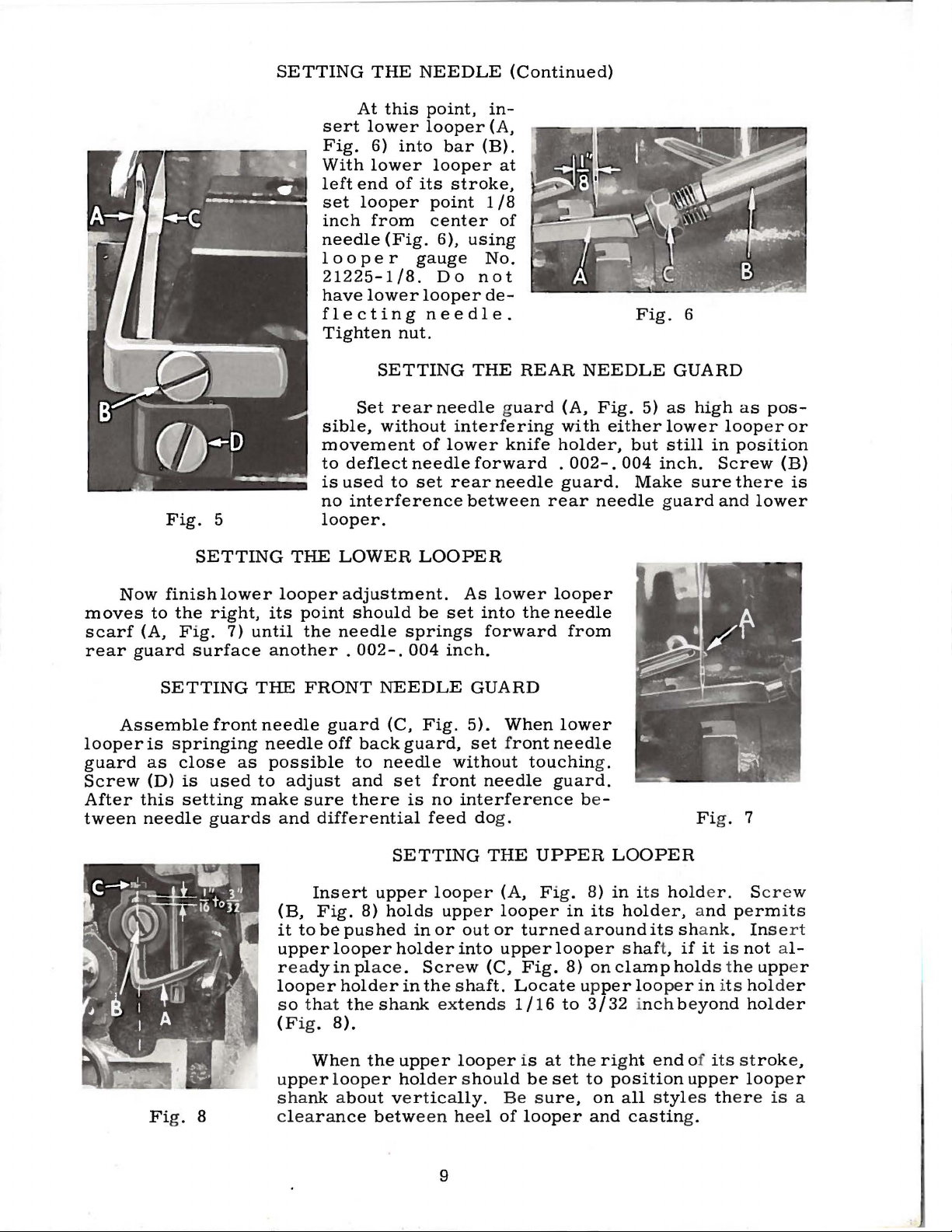
SETTING
sert
Fig.
With
left
set
inch
needle
looper
21225-118.
have
flecting
Tighten
THE
At
this
NEEDLE
point,
lowerlooper(A,
6)
into
bar
lower
end
looper
from
(Fig.
of
looper
its
stroke,
point
center
6),
gauge
Do
lower
looper
needle.
nut.
(Continued)
in-
(B).
at
1
18
of
using
No.
not
de-
Fig.
6
Now
moves
scarf
rear
Assemble
looper
guard
Screw
After
tween
Fig.
finish
to
the
(A,
Fig.
guard
SETTING
is
springing
as
close
(D)
this
needle
5
SETTING
lower
right,
7)
surface
front
as
is
used
setting
guards
THE
looper
its
until
another
THE
needle
needle
possible
to
adjust
make
and
Set
sible,
movement
to
deflect
is
used
no
interference
looper.
LOWER
adjustment.
point
the
should
needle
.
002-.
FRONT
guard
off
back
to
and
sure
there
differential
SETTING
rearneedle
without
of
lower
needle
to
set
LOOPER
be
set
springs
004
inch.
NEEDLE
(C,
Fig.
guard,
needle
set
front
is
no
feed dog.
THE
REAR
g
uard
interfering
knife
forward
rear
needle
between
As
lower
into
the
forward
GUARD
5).
When
set front
without
touchin
needle
interference
NEEDLE
(A,
with
holder,
.
002-.
guard.
rear
looper
needle
from
lower
needle
guard.
be -
Fig.
either
but
004
Make
needle
g.
5)
inch.
as
lower
still
guard
GUARD
high
looper
in
Screw
sure
and
Fi
g. 7
as
pos-
or
position
(B)
there
is
lower
Fi
g. 8
SETTING
Insert
(B,
it
to
upper
Fig.
be
upper
8)
pushed
looper
holds
in
holder
readyin place .
loop
er
hold
er
in the s ha
at the sha
s o th
(Fig.
u
sha
8).
Wh
en
pp
er l
oop
nk about vertically.
clearance
the
er
betw
nk exte
upper
hold
loop
or
Scr
er s
een heel of
9
upp
into
ew
loop
THE
er
er
out
(C,
ft.
nd
hould
UPPER
(A,
Fi
g. 8)
looper
or
turned around
upp
er
looper shaft,
Fig.
Locate upper
s 1 I 16
er is
to
at the rig
be
set
Be sure,
looper
in
8)
LOOPER
in its holde
its
holder, and perm
its shank. Inse
if
on
clamp
hold
looper in it s holde
3 I 32 i
to
on
and
nc
h beyond holde r
ht
end
position
all styl
castin
of
upp
es ther e
g.
r. Scre
it
is
not al-
s the
its strok
er
loop
upp
is
w
it s
r t
er
r
e,
er
a
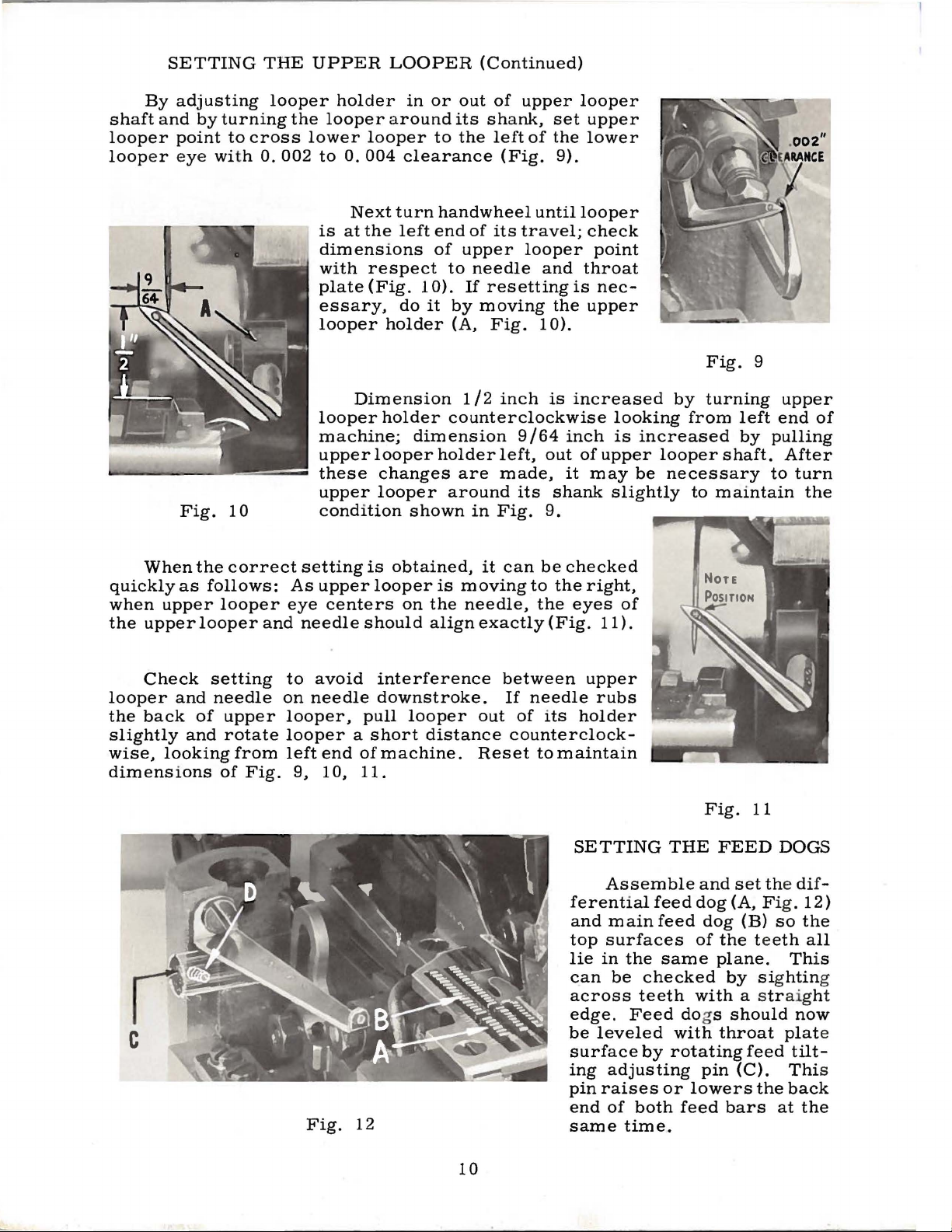
By
shaft
and
looper
loop
er eye with
SETTING
adjusting
by
turning
point
to
THE
looper
cross
0.
002
UPPER
holder
the
looper
lower
to
0.
is
at
dimensions
with
plate
essary,
looper
LOOPER
in
around
looper
004
clearance
Next
turn
the
left
respect
(Fig. 1 0).
do
holder
(Continued)
or
out
its
shank,
to
the
handwheel
end
of
of
upper
to
needle
If
resetting
it
by
moving
(A,
Fig.
of
left
(Fig.
its
upper
set
of
the
9).
until
travel;
looper
and
the
10).
looper
upper
lower
looper
check
point
throat
is
nec-
upper
Fig.
When
quickly
when
the
as
upper
upperlooperand
Check
looper
the
slightly
wise,
and
back
and
looking
dimensions
10
the
correct
follows:
looper
setting
needle
of
upper
rotate
from
of
looper
machine;
upper
these
upper
condition
setting
As
upper
eye
needleshould
to
avoid
on
needle
looper,
looper a short
left
end
Fig.
9,
Dimension
is
centers
pull
ofmachine.
10,
11.
holder
looper
counterclockwise
dim
ens
holder
changes
looper
around
shown
obtained,
looper
on
is
the
alignexactly(Fig.
interference
downstroke.
looper
distance
1/2
inch
ion
left,
are
made,
in
Fig.
it
can
moving
needle,
between
If
out
Reset
is
increased
9 I
64
inch
out
of
upper
it
may
its
shank
9.
be
checked
to
the
right,
the
eyes
11).
upper
needle
of
its
rubs
holder
counterclock-
to
maintain
looking
is
increased
looper
be
slightly
of
Fig.
by
turning
from
shaft.
necessary
to
maintain
Fig.
9
left
by
11
upper
end
of
pulling
After
to
turn
the
Fig.
12
10
SETTING
Assemble
ferential
and
main
top
surfaces
lie
in
the
can
be
across
edge.
be
Feed dogs
leveled
surface
ing
adjusting
pin
raises
end
of
both
same
time.
THE
feed
feed
same
checked
teeth
with
by
rotating
or
feed
FEED
and
set the dif-
dog
(A,
dog
of
the teeth
plane.
by sig
with
should
throat
pin
lowers
bars
DOGS
Fig.
12)
(B)
so
the
all
Th
is
htin
a straight
now
plat
feed
tilt-
(C).
the
Thi
back
at
the
g
e
s
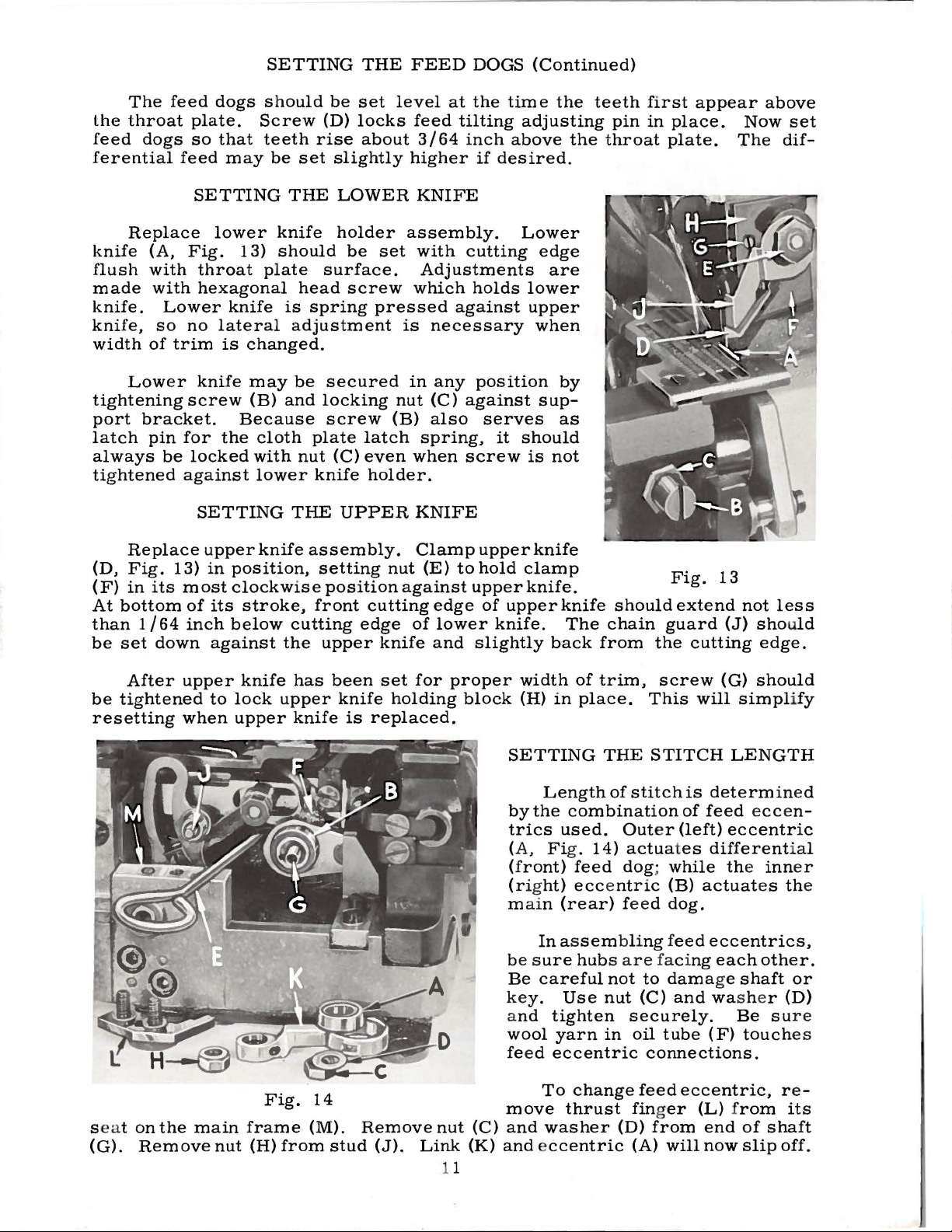
The
the
throat
feed
dogs
ferential
feed
plate.
so
feed
dogs
that
may
SETTING
should
Screw
teeth
be
(D)
rise
set
THE
be
set
locks
about
slightly
FEED
level
feed
3/64
higher
DOGS
at
the
tilting
inch
if
(Continued)
time
adjusting
above
desired.
the
the
teeth
pin
throat
first
in
place.
plate.
appear
The
above
Now
set
dif-
Replace
knife
flush
made
knife.
knife,
width
(A,
with
with
Lower
so
of
Lower
tightening
port
latch
always
bracket.
pin
be
tightened
Replace
(D,
Fig.
(F)
in
its
At
bottom
than
1/64
be
set
down
SETTING
lower
Fig.
throat
hexagonal
no
lateral
trim
is
knife
screw
for
the
locked
against
SETTING
upper
13)
in
most
of
its
inch
against
THE
knife
13)
should
plate
knife
is
adjustment
changed.
may
be
(B)
and
Because
cloth
with
lower
THE
knife
position,
clockwise
stroke,
below
cutting
the
LOWER
holder
be
surface.
head
screw
spring
secured
locking
screw
plate
nut
(C)
knife
UPPER
assembly.
setting
position
front
upper
set
pressed
nut
(B)
latch
even
holder.
nut
cutting
edge
knife
KNIFE
assembly.
with
cutting
Adjustments
which
holds
against
is
necessary
in
any
(C)
against
also
spring,
when
screw
KNIFE
Clamp
(E)
to
against
upper
edge
of
lower
and
slightly
Lower
lower
upper
position
serves
it
should
is
upper
hold
clamp
knife.
of
upper
knife.
edge
are
when
by
sup-
as
not
knife
knife
The
back
should
chain
from
Fig.
extend
guard
the
13
(J)
cutting
not
less
should
edge.
After
be
tightened
resetting
seat
on
(G).
Remove
the
upper
to
when
main
nut
knife
lock
upper
Fig.
frame
(H)
has
upper
knife
14
(M).
from
been
knife
is
stud
set
for
holding
replaced.
Remove
(J).
nut
Link
11
proper
block
(C)
(K)
width
(H)
SETTING
in
of
trim,
place.
THE
Length
by
the
combination
trics
(A, Fig .
(front)
(right)
main
be
Be
key.
and
wool
feed
move
and
used.
feed
eccentric
(rear)
In
assembling
sure
hubs
careful
Use
tighten
yarn
eccentric
To
change
thrust
washer
14)
and eccentric
screw
This
STITCH
of
stitch
Outer
actuates
dog; while
(B)
feed
dog.
feed
are
faci
not
to
dama
nut
(C)
securely.
in
oil
tube
connections.
feed
finger
(D)
from
(A)
will
(G)
should
will
simplify
LENGTH
is
determined
of
feed
eccen-
(left)
eccentric
differential
the
inner
actuates
the
eccentrics,
ng
each
other.
ge
shaft
or
and washe r (D)
Be
sure
(F)
touches
eccentric,
(L) from
end
now
of
slip
re-
its
shaft
off.