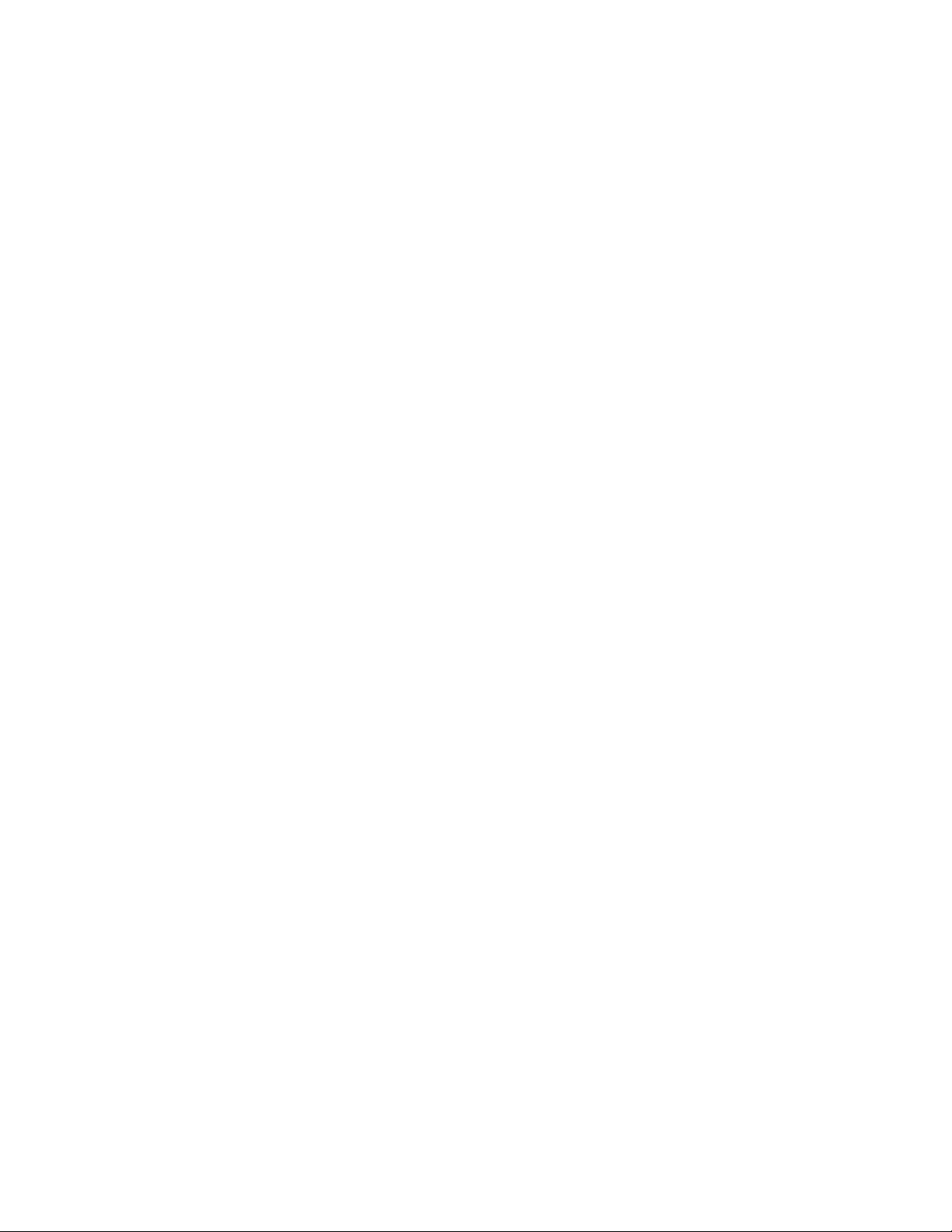
INDUSTRIAL
SEWING
®
QUA
LITY
STYLES
39500QJ
39500QL
39500QN
39580QV
39500QX
39500RP
39500RU
39500SJ
·
C O L U M B I A®
MACHINES
39500SR
39500SX
39500TG ·
39500TY ·
CATALOG
No.
103QJ
MARK
TWO
SERGING
AND
CLASS
IV
SINGLE
AND
THREE
PLAIN
39500
HIGH
SPEED
NEEDLE
THREAD
FEED
OVERSEAMING
MACHINES
UNION SPECIAL
CHICAGO
CORPORATION
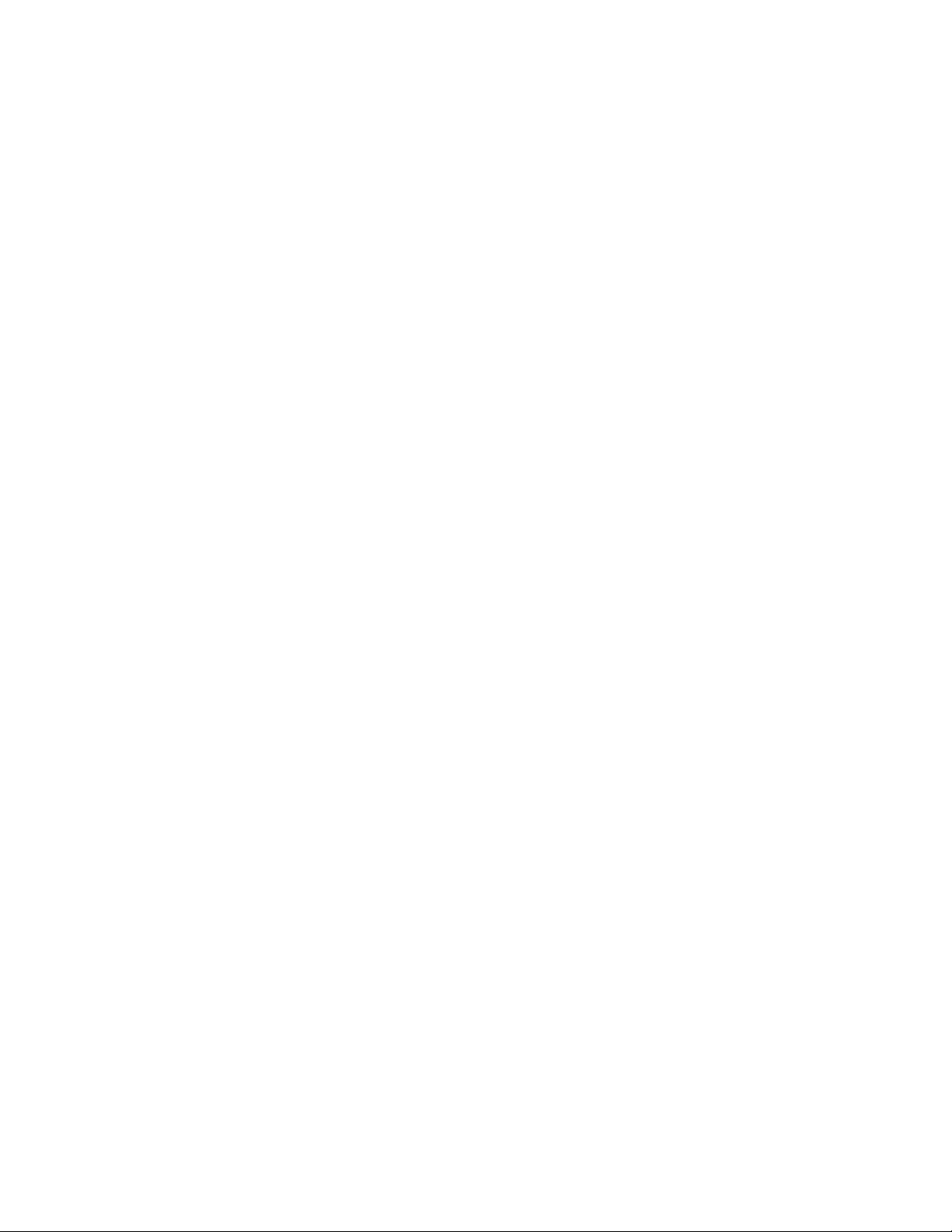
Catal
A
DJUSTING
I
NST
o g N
R
FOR
AND
UC
o.
103
TIO
NS
OPERATING
QJ
39500
39500
39500
Righ
QJ
39500
39500
39500
Union
ts
LIST
CLASS
QL
QN
QV
QX
First
Copyright
Special
Reserved
RP
OF
Styles
Edition
by
PARTS
39500
39500
39500
39
500
39500
39500
©
1973
Corporation
in
All
39500
SR
sx
TG
TY
Countries
RU
SJ
UNION SPECIAL CORPORATION
INDUSTRIAL
Prin
SEWING
CHICAGO
te
d
in
2
MACHINES
U.S.A.
March,
1978
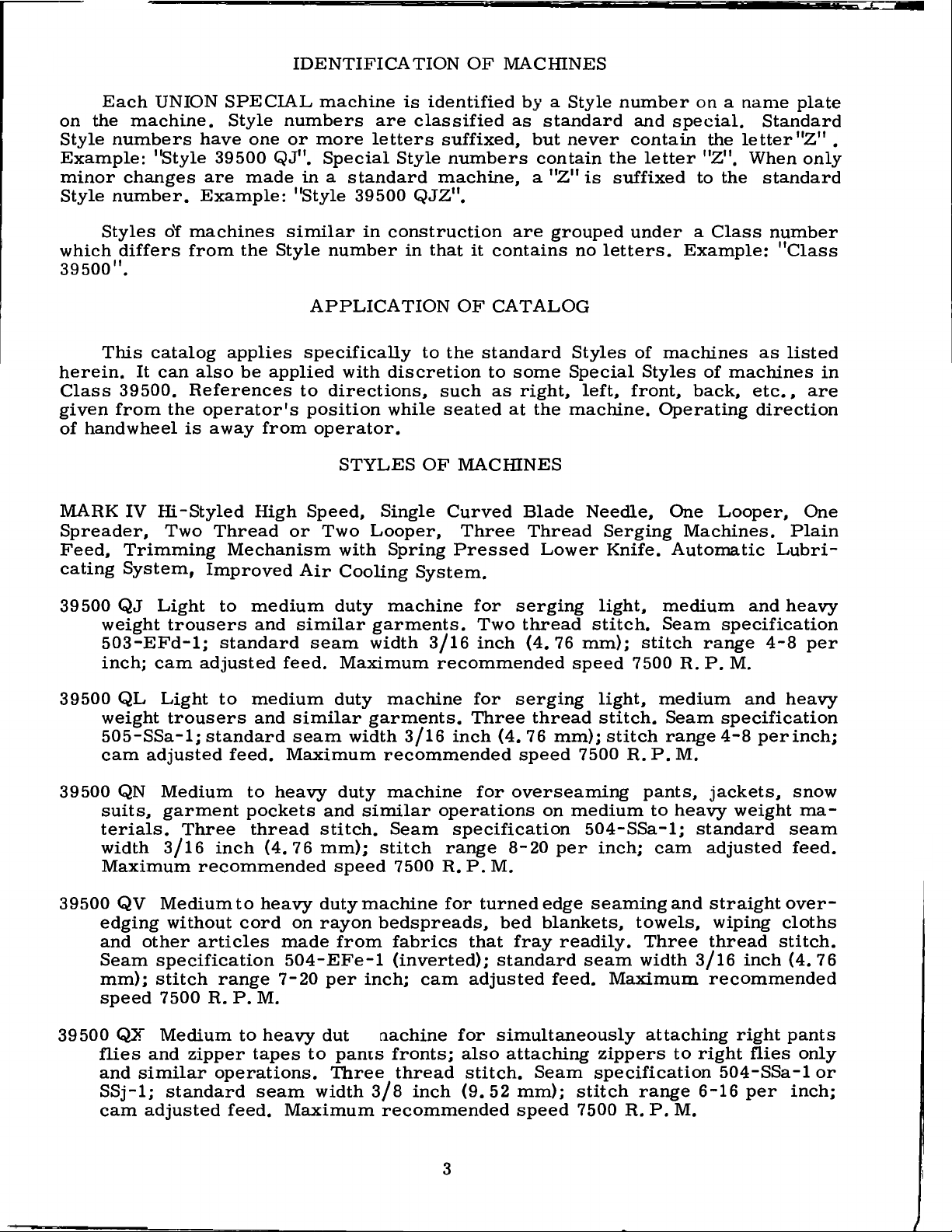
IDENTIFICATION
OF
MACHINES
Each
on
the
Style
numbers
Example:
minor
Style
changes
number.
Styles
which
39500
differs
11
•
This
herein.
Class
given
of
MARK
39500.
from
handwheel
IV
Spreader,
Feed,
cating
Trimming
System,
UNION
machine.
"Style
o'f
machines
from
catalog
It
can
also
References
the
is
Hi-Styled
Two
SPECIAL
Style
have
one
39500
are
made
Example:
the
applies
be
applied
operator's
away
from
High
Thread
Mechanism
Improved
machine
numbers
or
more
QJ".
Special
in a standard
"Style
39500
similar
Style
number
APPLICATION
specifically
with
to
directions,
position
operator.
STYLES
Speed,
or
Two
with
Air
Cooling
is
identified
are
classified
letters
Style
QJZ".
in
construction
in
that
to
discretion
while
OF
Single
Looper,
Spring
System.
as
suffixed,
numbers
machine,
are
it
contains
OF
CATALOG
the
standard
to
some
such
seated
as
at
MACHINES
Curved
Three
Pressed
by a
standard
but
contain
a
"Z"
grouped
right,
the
Blade
Thread
Lower
Style
never
number
contain
the
is
suffixed
under a Class
no
letters.
Styles
Special
left,
front,
machine.
Needle,
Serging
Knife.
and
special.
letter
Example:
of
machines
Styles
Operating
One
Machines.
Automatic
on a name
Standard
the
letter
"Z".
When
to
the
standard
number
as
of
machines
back,
etc.,
direction
Looper,
plat
"Z"
only
"Class
listed
are
One
Plain
Lubri-
e
•
in
39500
39500
39500
terials.
width
Maximum
39500
edging
and
Seam
mm);
spee
39500
flies
and
SSj-1;
cam
QJ
Light
weight
trousers
503-EFd-1;
inch;
weight
QL
cam
Light
trousers
505-SSa-1;
cam
adjusted
QN
Medium
suits,
garment
Three
3/16
QV
Medium
without
other
specification
stitch
.d
7500
QX
Medium
and
similar
standard
adjusted
to
medium
and
standard
adjusted
to
medium
and
standard
feed.
to
heavy
pockets
thread
inch
(4.
recommended
to
heavy
cord
articles
range
made
7-20
R.P.M.
to
heavy
zipper
tapes
operations.
seam
feed.
duty
similar
seam
feed.
Maximum
duty
similar
seam
width
Maximum
duty
and
similar
stitch.
76
mm);
speed
duty
machine
on
rayon
from
504-EFe-1
per
duty
to
pants
Three
width
Maximum
machine
garments.
width
3/16
recommended
machine
garments.
3/16
inch
recommended
machine
operations
Seam
stitch
7500
specification
range
R.P.M.
for
bedspreads,
fabrics
(inverted);
inch;
cam
machine
fronts;
thread
3/8
inch
recommended
for
serging
Two
thread
inch
for
Three
(4.
serging
thread
(4.
76
speed
for
overseaming
8-20
turned
bed
that
fray
standard
adjusted
for
simultaneously
also
attaching
stitch.
(9.
52
mm);
speed
stitch.
76
mm);
speed
mm);
7500
on
medium
504-SSa-1;
per
edge
seaming
blankets,
readily.
seam
feed.
Seam
specification
stitch
7500
light,
medium
Seam
stitch
7500
light,
medium
stitch.
stitch
R.P.M.
pants,
to
inch;
cam
towels,
Three
width
Maximum
attaching
zippers
range
R.
P.
specification
range
R.P.M.
Seam
range
specification
4-8
jackets,
heavy
standard
adjusted
and
straight
wiping
thread
3/16
recommended
to
right
504-SSa-1
6-16
M.
and
4-8
and
per
weight
cloths
stitch.
inch
right
flies
per
heavy
per
heavy
inch;
snow
ma-
seam
feed.
over-
(4.
76
pants
only
or
inch;
3
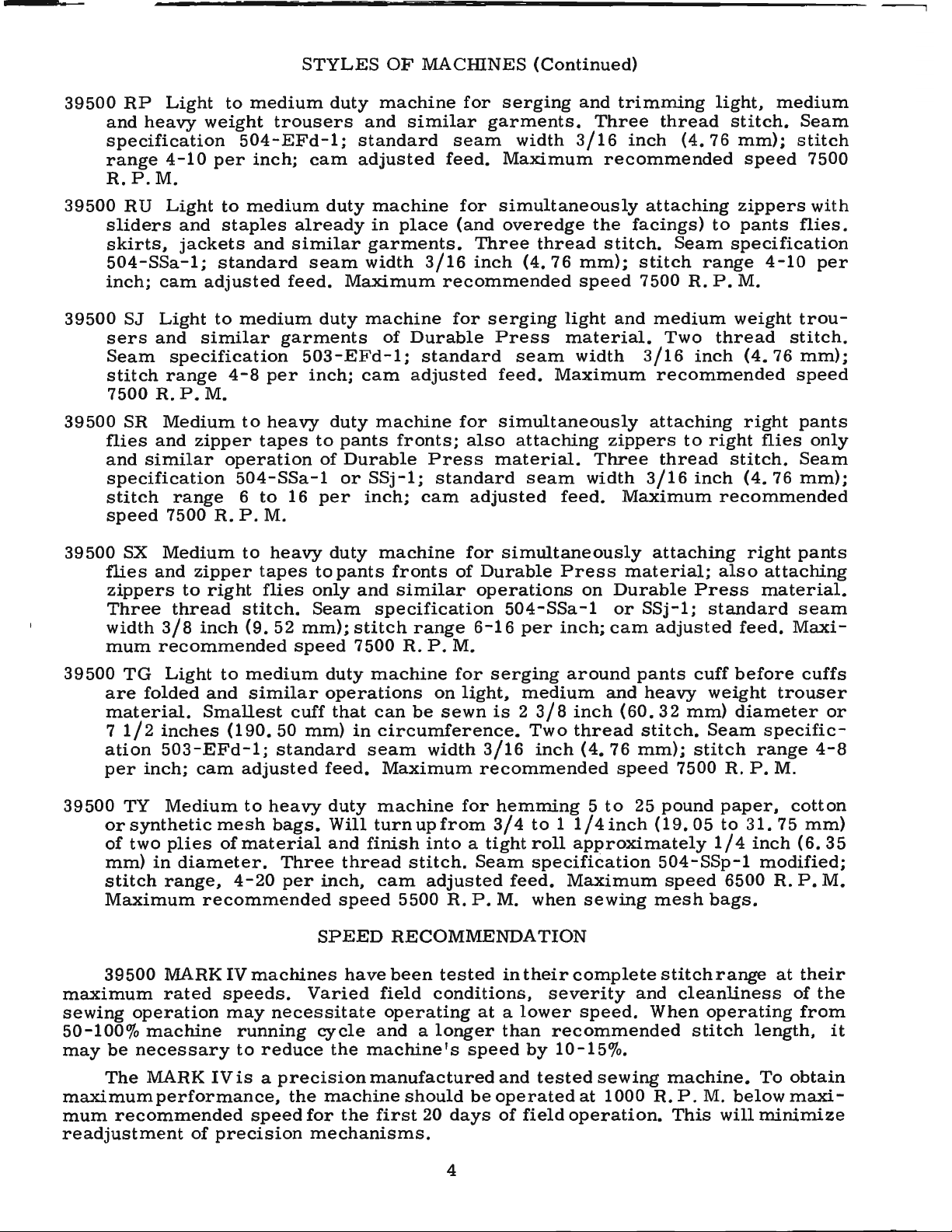
STYLES
OF
MACIDNES
(Continued)
39500
and
specification
range
R.P.M.
39500
sliders
skirts.
504-SSa-1;
inch;
39500
sers
Seam
stitch
7500
39500
flies
and
specification
stitch
speed
39500
flies
zippers
Three
width
mum
RP
Light
heavy
4-10
RU
Light
and
jackets
cam
SJ
Light
and
specification
range
R.P.M.
SR
Medium
and
similar
range
7500
SX
Medium
and
to
thread
3/8
recommended
to
weight
504-EFd-1;
per
to
medium
staples
standard
adjusted
to
medium
similar
4-8
to
zipper
operation
504-SSa-1
6
R.
P.
to
zipper
right
stitch.
inch
(9.
medium
trousers
inch;
already
and
similar
feed.
garments
503-EFd-1;
per
heavy
tapes
to
16
M.
heavy
tapes
flies
52
mm);
speed
duty
and
standard
cam
seam
inch;
adjusted
duty
width
Maximum
duty
machine
cam
duty
to
pants
of
Durable
or
per
inch;
duty
to
pants
only
and
Seam
stitch
7500 R.P.M.
machine
similar
seam
feed.
machine
in
place
garments.
of
machine
fronts;
SSj-
1;
machine
fronts
similar
specification
(and
3/16
recommended
for
Durable
standard
adjusted
Press
standard
cam
of
range
for
serging
garments.
width
Maximum
for
simultaneously
overedge
Three
inch
for
also
adjusted
for
6-16
(4.
serging
Press
seam
feed.
simultaneously
attaching
material.
seam
simultaneously
Durable
operations
504-SSa-1
per
and
Three
3/16
the
thread
76
mm);
speed
light
material.
width
Maximum
Three
width
feed.
Press
on
inch;
trimming
thread
inch
recommended
facings)
stitch.
and
zippers
Maximum
material;
Durable
or
cam
(4.
76
attaching
Seam
stitch
7500
medium
3/16
attaching
3/16
attaching
SSj-1;
adjusted
range
R.P.M.
Two
inch
recommended
to
right
thread
inch
Press
standard
light,
to
thread
recommended
also
medium
stitch.
mm);
speed
zippers
pants
specification
weight
(4.
right
stitch.
(4.
right
feed.
Seam
stitch
7500
with
flies.
4-10
trou-
stitch.
76
mm);
speed
pants
flies
material.
only
Seam
76
mm);
pants
attaching
se
Maxi-
per
am
39500
39500
maximum
sewing
50-100%
may
maximum
mum
readjustment
TG
Light
are
folded
material.
7
1/2
inches
ation
per
or
of
mm)
stitch
Maximum
39500
be
The
recommended speed
503-EFd-1;
inch;
TY
Medium
synthetic
two
plies
in
range,
MARK
rated
operation
machine
necessary
MARK
performance,
to
medium
and
similar
Smallest
(190.
cam
adjusted
to
heavy
mesh
of
material
diameter.
4-20
recommended
IV
machines
speeds. Varied
m ay
necessitate
running
to
reduce
IV
is a
of
precision
duty
machine
operations
cuff
that
can
50
mm)
standard
bags.
Three
per
precision manu
the
for the
in
circumference.
seam
feed.
duty
Will
and
inch,
SPEED
cycl
the
machine should
mechanism s .
Maximum
machine
turn
finish
thread
cam
speed
RECOMMENDATION
ha
ve
been tes
field
operating at a lower
e a
nd a longer
ma
chin
fir
for
serging
on
light,
be
sewn
width
up
from
into a tight
stitch. Seam specification
adjusted
5500
condition
e 's s
fac
tured and tested s
st 20
is 2 3/8
3/16
recommended
for
hemming 5 to
3/4
feed.
R.P.M.
ted
in
s ,
than
peed
be ope
days of
around
medium
Two
inch
to 1 1/4inch
roll
when
their
severity
recommend
by
10-15%.
rated
field ope
and
inch
thread
(4.
approximately
Maximum
sewing
complete stitch range
speed.
at
1000
ration. This will minimi
76
ewi
pants
heavy
(60.
32
stitch.
mm);
speed
25
pound
(19.05
504-SSp-1
mesh bag
and clea
Wh
ed s
ng
R.P
cuff
before
weight
mm)
7500
speed
en
ma
diameter
Seam
stitch
R.
P.
paper, cotton
to
31.
1/4 inch (6.
6500 R.P.M.
s.
nlin
operating from
tit
ch length,
chin
e. To
. M. below
cuffs
trouser
spe
cific-
ran
ge
4-8
M.
75
mm)
modified;
at
their
ess
of
the
obtain
maxi-
or
35
it
ze
4
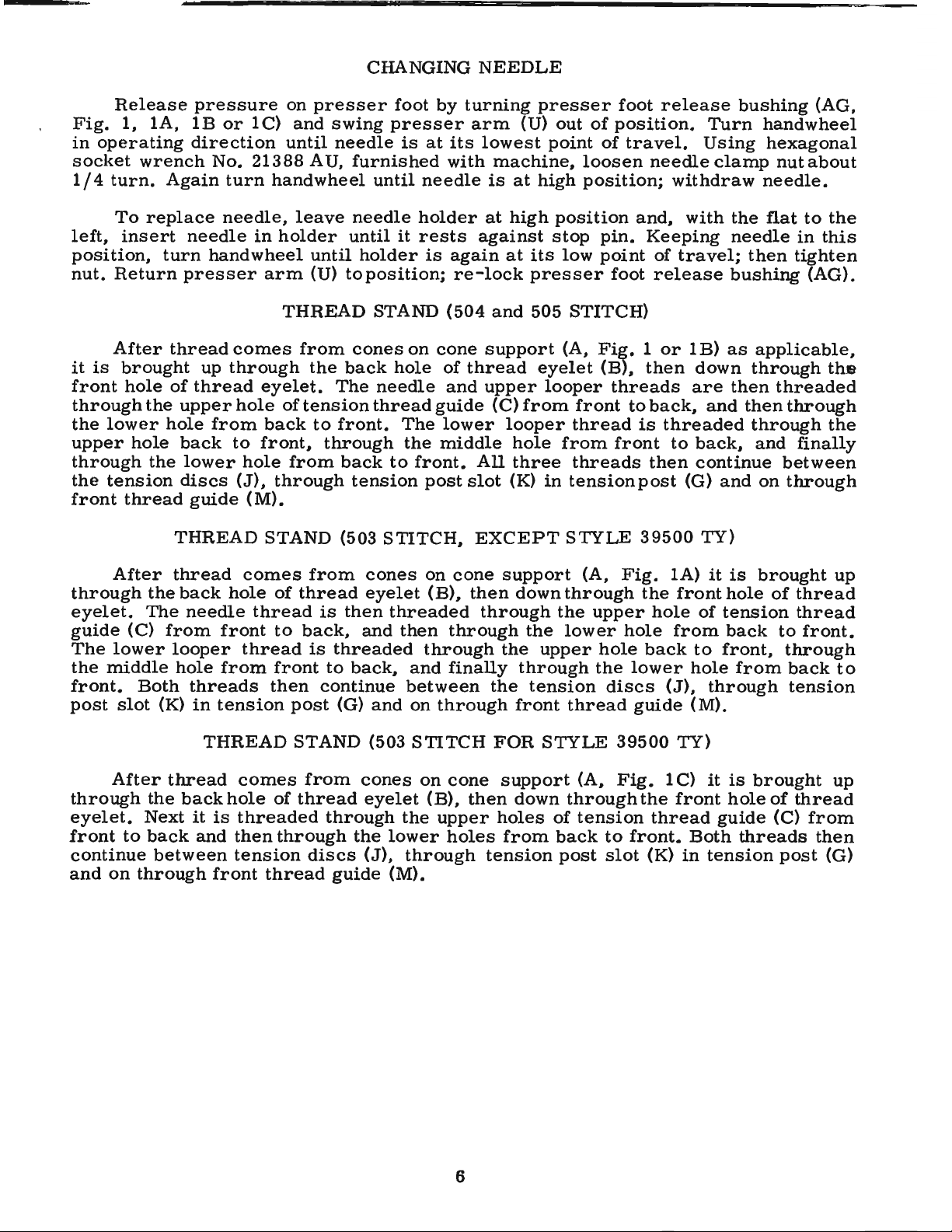
Re
lease pressure
Fig.
in
1,
operating
socket
1/ 4 turn.
To
left,
insert
position,
nut.
Return
lA,
direction
wrench
Again
replace
needle
turn
presser
lB
or
lC)
No.
21388
turn
needle,
in
handwheel
on
presser
and
swing
until
needle
AU,
handwheel
leave
holder
until
arm
(U)
CHANGING
foot
presser
is
furnished
until
needle
until
holder
it
rests
needle
holder
to
position;
by
at
with
is
NEEDLE
turning
arm
its
lowest
machine,
is
at
against
again
re-lock
(U)
at
high
at
its
presser
presser
out
point
loosen
high
position;
position
stop
low
foot
of
position.
of
travel.
pin.
point
foot
release
needle
withdraw
and,
Keeping
of
travel;
release
Turn
Using
clamp
with
bushing
handwheel
hexagonal
nut
needle.
the
flat
needle
then
bushing
(AG,
about
to
the
in
this
tighten
(AG).
After
it
is
brought
front
hole
through
the
lower
upper
through
the
tension
front
thread
After
through
eyelet.
guide
The
lower
the
middle
front.
post
slot
the
hole
the
the
The
(C)
Both
thread
up
of
thread
upper
hole
from
back
lower
discs
guide
THREAD
thread
back
needle
from
looper
hole
threads
(K)
in
THREAD
comes
through
eyelet.
hole
back
to
front,
hole
(J),
(M).
STAND
comes
hole
thread
front
thread
from
tension
THREAD
from
the
of
tension
to
through
from
through
from
of
thread
is
to
back,
is
front
then
to
continue
post
STAND
STAND
cones
back
The
hole
needle
thread
front.
back
to
tension
(503
STITCH,
cones
eyelet
then
threaded
and
threaded
back,
(G)
and
(503
(504
on
cone
of
and
guide ( C)
The
lower
the
middle
front.
post
on
cone
(B),
then
through
through
and
finally
between
on
through
STITCH
and
support
thread
upper
from
looper
hole
All
three
slot
(K)
EXCEPT
support
then
down
through
the
the
through
the
front
FOR
505
STITCH)
(A,
eyelet
looper
front
thread
from
threads
in
tensionpost
STYLE
through
the
lower
upper
tension
thread
STYLE
Fig. 1 or
(B).
threads
to
is
front
(A,
Fig.
upper
hole
hole
the
lower
discs
guide
39500
then
back,
threaded
to
then
(G)
39500
lA)
the
front
hole
from
back
(J),
TY)
lB)
as
down
are
then
and
then
back,
continue
and
TY)
it
is
hole
of
tension
back
to
front,
hole
from
through
(M).
applicable,
through
the
threaded
through
through
and
the
finally
between
on
through
brought
of
thread
thread
to
front.
through
back
tension
up
to
After
through
eyelet.
front
continue
and
on
the
Next
to
back
between
through
thread
back
it
is
and
front
comes
hole
of
threaded
then
through
tension
thread
from
thread
through
discs
guide
cones
eyelet
the
lower
(J),
on
(B),
the
through
(M).
cone
then
upper
holes
6
support
down
holes
from
tension
of
back
post
(A,
Fig.
through
tension
to
slot
1 C)
the
thread
front.
(K)
it
front
Both
in
tension
is
brought
hole
guide
threads
of
(C)
post
up
thread
from
then
(G)
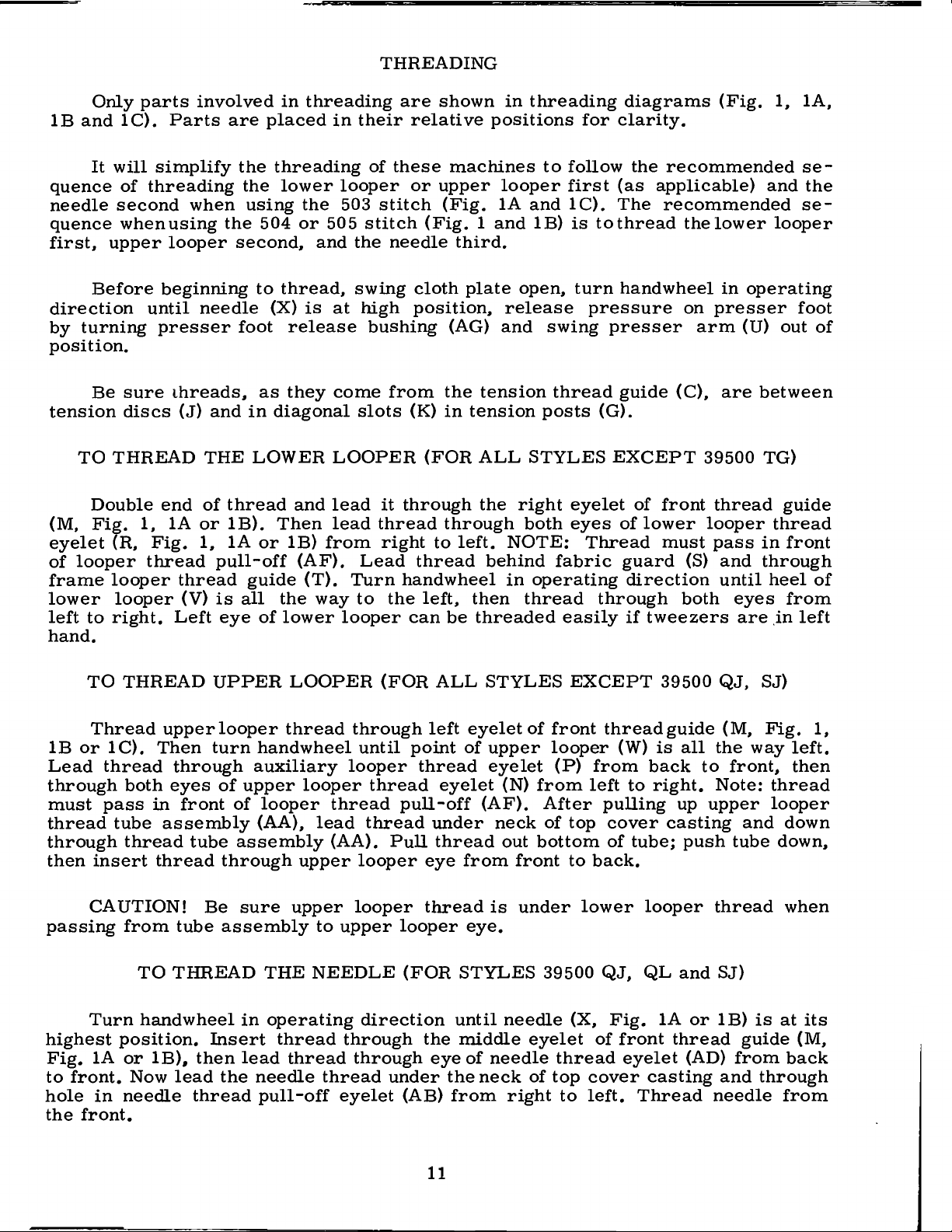
THREADING
Only
1 B
and 1 C).
It
quence
needle
quence
first.
direction
by
position.
tension
(M.
eyelet
of
frame
lower
left
hand.
upper
Before
turning
Be
TO
Double
Fig.
looper
to
parts
Parts
will
simplify
of
threading
second
whenusing
looper
beginning
until
presser
sure
discs
THREAD
(R.
looper
looper
right.
end
1.
lA
Fig.
thread
Left
hreads,
(J)
thread
involved
when
the
needle
and
THE
of
thread
or
1,
pull-off
(V)
is
eye
are
placed
the
threading
the
using
504
second,
to
(X)
foot
as
in
diagonal
LOWER
lB).
lA
or
guide
all
of
in
threading
lower
the
or
and
thread,
is
release
they
and
Then
lB)
(AF).
(T).
the
way
lower
in
their
of
looper
503
stitch
505
stitch
the
swing
at
high
bushing
come
slots
LOOPER
lead
lead
from
it
thread
right
Lead
Turn
to
looper
are
shown
relative
these
needle
from
through
handwheel
the
machines
or
upper
(Fig.
(Fig. 1 and
cloth
position,
(AG)
the
(K)
in
(FOR
through
to
thread
left.
can
be
positions
third.
plate
tension
tension
ALL
the
left.
behind
then
threaded
in
threading
looper
lA
and
lB)
open,
release
and
STYLES
right
both
NOTE:
in
operating
thread
to
follow
first
lC).
is
turn
swing
thread
posts
eyelet
eyes
fabric
easily
diagrams
for
clarity.
the
(as
The
tothread
handwheel
pressure
presser
guide
(G).
EXCEPT
of
Thread
guard
direction
through
if
recommended
applicable)
recommended
the
on
arm
(C).
39500
of
front
lower
tweezers
looper
must
(S)
both
(Fig.
lower
in
operating
presser
(U)
are
between
thread
pass
and
until
eyes
are .in
1.
lA,
se-
and
the
se-
looper
foot
out
of
TG)
guide
thread
in
front
through
heel
of
from
left
TO
Thread
lB
or
Lead
through
must
thread
through
then
insert
CAUTION!
passing
Turn
highest
Fig.
lA
to
front.
hole
the
in
front.
THREAD
lC).
thread
both
pass
in
tube
thread
from
TO
handwheel
position.
or
lB).
Now
needle
UPPER
upper
Then
assembly
thread
turn
through
eyes
front
tube
Be
tube
THREAD
Insert
then
lead
thread
looper
handwheel
auxiliary
of
upper
of
looper
(AA).
assembly
through
sure
assembly
THE
in
operating
thread
lead
the
needle
pull-off
LOOPER
thread
looper
looper
thread
lead
(AA).
upper
upper
to
upper
NEEDLE
through
thread
thread
eyelet
(FOR
through
until
thread
pull
thread
Pull
looper
looper
looper
(FOR
direction
through
under
(AB)
ALL
left
point
thread
eyelet
-off
under
thread
eye
thread
the
eye
STYLES
eyelet
of
upper
eyelet
(AF).
neck
from
is
eye.
STYLES
until
middle
of
needle
the
neck
from
of
(N)
from
After
of
out
bottom
front
under
39500
needle
eyelet
of
right
EXCEPT
front
looper
(P)
from
left
top
to
back.
lower
(X.
of
thread
top
cover
to
left.
thread
(W)
back
to
pulling
cover
of
tube;
looper
QJ,
QL
Fig.
front
eyelet
casting
Thread
39500
guide
is
all
right.
up
casting
push
and
lA
or
thread
(AD)
QJ,
( M,
the
to
front,
Note:
upper
tube
thread
SJ)
lB)
from
and
needle
SJ)
Fig.
way
thread
looper
and
down.
is
guide
through
left.
then
down
when
at
its
(M.
back
from
1,
11

TO
THREAD
THE
NEEDLE
(FOR
ALL
STYLES
EXCEPT
39500
QJ,
QL
and
SJ)
Turn
highest
Fig. 1 or
thread
cover
tension
to
eyelet
needle
The
secure
Fig.
handwheel
position.
1 C,
then
(AD),
thread
amount
nuts
(D,
proper
2
Insert
insert
of
tension
Fig.
stitch
in
operating
thread
needle
under
eyelet
1,
lA,
formation.
should
decrease
nut
screw
pressure,
adjusting
(A).
ing
to
justing
through
thread
neck
1 / 16
of
(AC).
THREAD
on
the
lB
Sufficient
be
(A,
has
With
nut
( C)
inch
screw
FEED
direction
the
from
top
cover
Thread
needle
or
lC).
PRESSER
presser
maintained.
amount
Fig.
2)
and
a
right
loosening
screw
presser
so
(B)
that
(.
79
(B).
ECCENTRICS
until
middle
right
casting;
needle
TENSION
and
Tension
of
foot
its
to
Set
from
looper
foot
Should
pressure
turn
hand
decreases
has
been
resting
under
1. 59
cap
needle
eyelet
to
left,
then
the
threads
on
threads
FOOT
pressure
it
adjusting
thread,
properly
on
surface
mm)
(D)
against
(X,
Fig. 1 or
of
front
through
down
front.
is
should
PRESSURE
to
be
necessary
on
presser
screw
so
tightening
pressure.
throat
is
from
the
locking
lC)
thread
both
eyes
through
regulated
feed
foot,
set,
plate,
approximately
top
hole
by
be
only
work
to
increase
loosen
(B).
When
tighten
position
surface
nut
is
at
its
guide
of
uniformly
Adjusting
increases
pressure
(C).
(M,
needle
in
top
knurled
enough
lock
lock
nut
lock-
1/32
of
ad-
or
Feed
approximately
eccentric
mately
specified,
exploded
The
-5. -6,
-28,
Additional
39540 B with a minor
stitches
Before
cloth
lower
NOTE:
chines
eccentrics
is
the
views
following
-7,
-30,
desired.
plate,
knife
Adjusting
covered
5
stitches
No.
39540
number
machine
in
catalog
-8, -9,
-32,
eccentrics
-34, -36,
Example:
ASSEMBLING
assembling
fabric
holder
assembly;
instructions
in
this
of
Style
stitch
guard,
SETTING
used
in
Style
per
inch.
B-5.
stitches
number
-10, -11, -12,
may
number
catalog,
39500
for
-40.
be
"39540
and
chip
then
Minor
obtainable
QJ
eccentrics
feed
Only
ordered
suffixed
AND
adjusting
guard,
follow
will
unless
THE
39500
It
B-5".
NEEDLE
QJ
will
be
numbers
when
will
be
furnished
eccentrics
-13, -14,
one
eccentric
separately.
to
ADJUSTING
sewing
upper
this
pertain
otherwise
machines
noted
using
shipped
indicate
knife
suggested
to
that
of
the
on
are
-15,
is
SEWING
parts,
assembly
all styles
specified.
have
been
the
part
that
with
available
-16, -18,
To
symbol
eccentric.
above
other
supplied
order
approxima
PARTS
remove
sequence.
of
part
Styles
under
-20.
with
an
and
ma
-
selected
number
indicate
Unless
eccentric.
of
machines.
No.
-22, -24,
each
eccentric,
ely
the
to
produce
of
the
approxi-
otherwise
Refer
39540
number
B-4,
machine.
use
feed
to
-26,
No.
of
With
should
high
position,
above
1/2
inch(12.
throat
center
throat
in
ne
plate
70
mm)
plate
the
edle
(Fi
(A, Fig. 3) assembl
front
for
point
g.
3)
Styl
end
of needle
should
for
Styl
es 39500
be set
es
QN
ed
in
slot.
33/64 inch
39500
and
12
QJ,
SR;
position, needle
When needle
(13.
QL,
and
10
RP a
nd
15/ 32 in
is
at
mm)
SJ ;
ch
Fig. 3
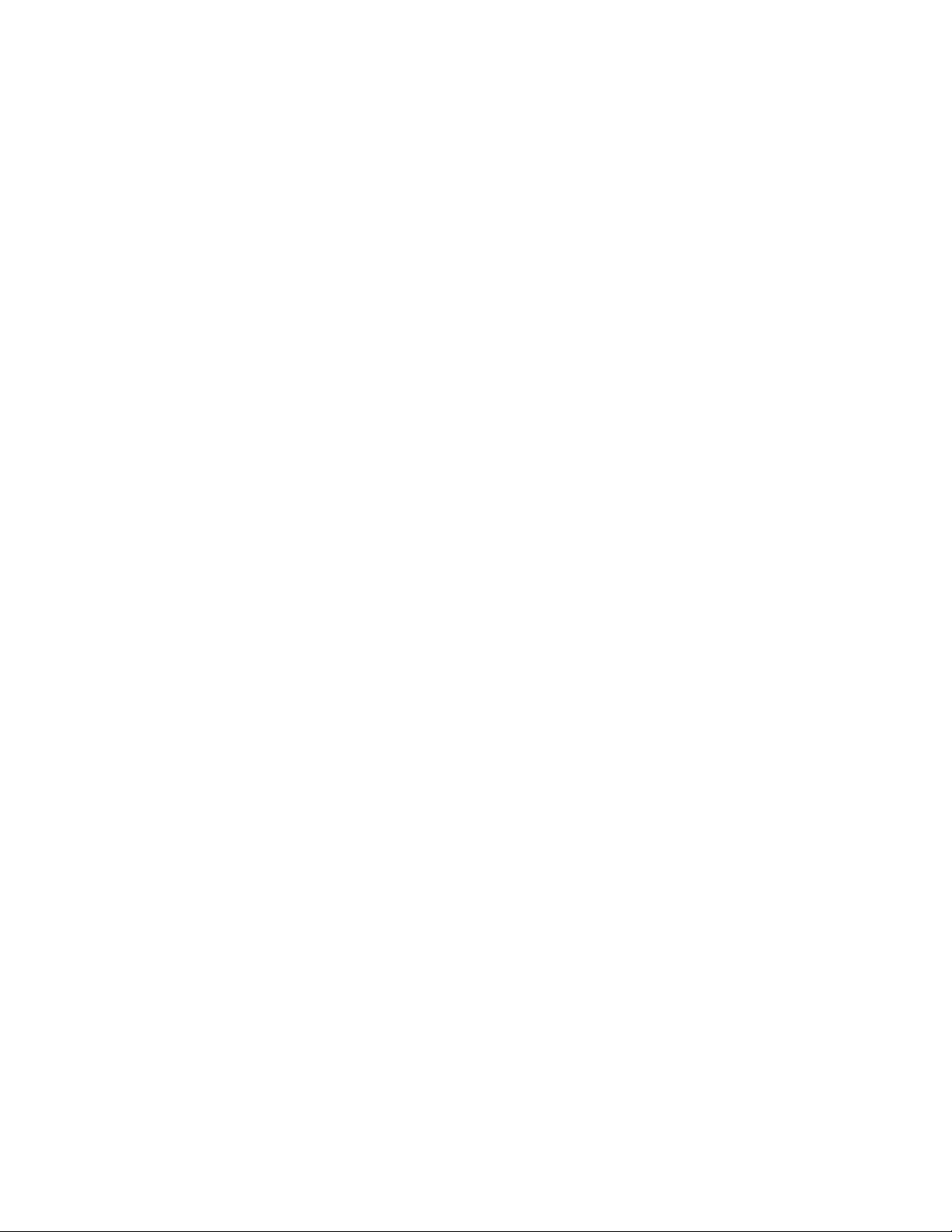
SETTING
THE
UPPER
LOOPER
(ALL
STYLES
EXCEPT
39500
QJ,
SJ)
Insert
its
holder
Fig.
of
looper
of
upper
set
upper
lower
looper
clearance
upper
and
7
and
looper
looper
(Fig.
looper
permits
the
casting.
shaft
point
eye
9).
(A,
it
to
upper
in
holder
the
looper
place.
in
shank
holder
SX
and
39500
RP
When
upper
shank
(Fig.
SR
be
and
set
looper
about
8).
to
slightly
Styles,
By
and
by
turning
to
cross
with . 002
Fig.
be
pushed
holder
Screw
the
extends
(Fig.
TY;
and
the
vertical
On
TG
the
position
back
there
adjusting
lower
to . 004
8)
in
its
holder.
in
or
out
into
upper
(C,
Fig.
shaft.
8),
1/32
1/16
for
Locate
Styles
to
1/16
to
TG.
upper
holder
Styles
upper
of
vertical.
the
looper
should
on
Styles
39500
looper
upper
is a clearance
looper
the
looper
around
looper
inch
(.
051
or
8)
on
upper
3/32
39500
inch
is
be
QL,
holder
looper
Be
sure,
between
holder
to
the
to • 102
Screw
turned
looper
clamp
looper
inch
(.
at
set
39500
RP,
in
its
left
(B)
around
shaft,
(1.
QL,
79
to
the
right
to
QN,
RU,
should
shank
on
all
heel
or
out
shank,
of
the
mm)
holds
if
holds
in
its
59
to
2.
QN,
QV,
1.
59
end
position
QV,
upper
its
it
the
38
mm)
QX,
shank.
is
not
upper
holder
mm)
QX,
for
of
its
upper
SX
looper
Insert
already
loop
so
beyond
RU,
Styles
stroke,
looper
and
in
er
that
SR,
TY
As
heel
head
of
with
Next,
travel;
needle
looper
39500
as
follows:
centers
(Fig.
the
bottom
the
the
check
and
holder
QL
Fig.
on
12).
upper
upper
1/32
turn
looper
looper
to
1/16
handwheel
dimensions
throat
and
(A,
RP.
plate
Fig.
8
As the
the needle,
For
Styles
of
the
needle
moves
should
inch(.
of
(Fig.
10).
NOTE:
the
other
example,
ion
is
holder
left
end
dimension
looper
looper
made
looper
tain
the
When
for
Styles
SR,
SX
upper
looper
the
39500
eye
toward
pass
79
to
until
looper
upper
10).
If
Figure
For
Styles
1/2
increased
the
behind
1.
59
is
looper
resetting
10
represents
the
dimensional
refer
inch
by
counterclockwise,
of
machine;
is
increased
holder
to
the
shaft. After
it
may
be
necessary
around its
condition
the
39500
and
TY
shank
shown
correct
QL,
it
can
is moving
eyes
of
RU
and
should
the
TG
be
upper
about
top
of
its
the
lower
mm)
at
the
point
is
clearance.
left
with
necessary,
the
settings
to
Fig.
(12.
70
mm)
turning
upper
looking
5 / 3 2
by
left,
these
inch ( 3.
pulling
out
changes
to
turn
slightly
in
(Fig.
setting
is
QN, QV,
be
checked
to the right and
looper
when
the
level
looper
with
stroke,
the
looper
end
of
its
respect
dimensional
do
to
it
bymoving
setting
of
11.
For
dimens-
looper
from
9 7
mm)
upper
of
upper
are
upper
to
main-
9).
obtained
QX,
RP,
quickly
the
upper
and needle should
eye
centers
the
top
surface
Fig.
7A
theupper
for
Styles
Fig.
loop
9
er
align exactly
on
the
needle,
of
the
looper.
eye
14
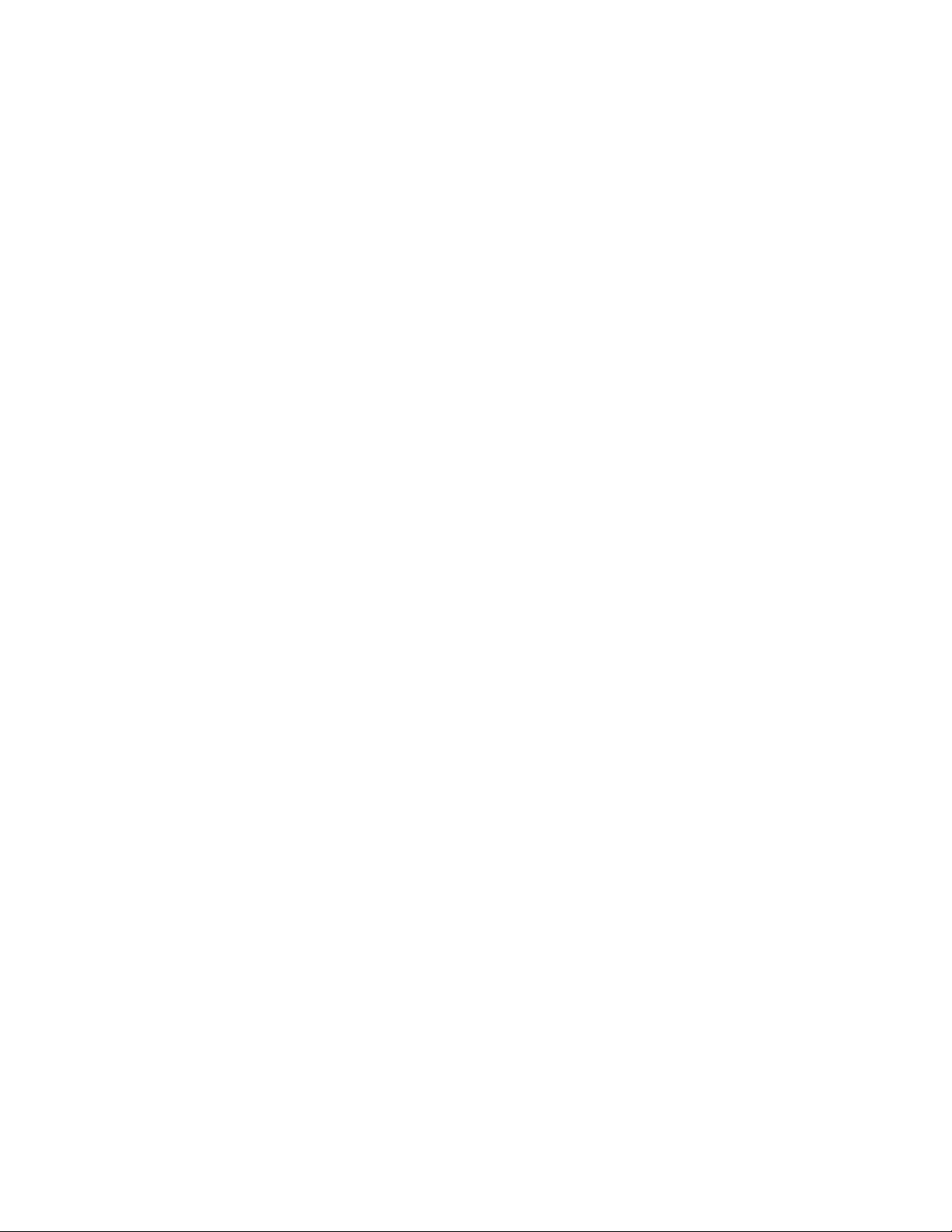
SETTING
THE
UPPER
LOOPER
{ALL
STYLES
EXCEPT
39500
QJ,
SJ)
{Cont.)
Check
downstroke.
slightly
of
machine.
Machine
39500
39500
and
Styles
QL,
QN,
3 9 500 QV,
39500
39500
39500
RU
SR
TG
setting
If
needle rubs
rotate
Reset
RP
TY
QX,
SX
to
avoid
interference
the
looper a short
to
maintain
dimensions
Looper
Needle
5/32
9/64
9/64
5/32
9/64
5/32
back
distance
Point
Center
inch
inch
inch
inch
inch
inch
of
Fig.
(3.
(3.
(3.
(3.
(3.
(3.
between
upper
upper
looper,
counterclockwise,
of
Figs.
10
to
Left
Of
line
97
mm)
57
mm)
57
mm)
97
mm)
57
mm)
97
mm)
9,
looper
pull
10,
and
looper
looking
11,
12.
Looper
Throat
1/2
1/2
1 5 / 3 2
29/64
31/64
15/32
needle
out
inch
inch
inch
inch
inch
inch
of
from
Point
Plate
(12.
(12.
(11.
(11.
(12.
(11.
on
needle
its
hold
left end
Above
70
mm)
70
mm)
91
51
30
91
er
mm)
mm)
mm)
mm)
to
left,
behind
(.
051
looper
Fig.
the
the
12
Vee
eye
to . 102
(Fig.
of
mm)
9A).
notch
the
lower
clearance
SETTING
Insert
(B)
holds
pushed
holder
{C,
shaft,
in
into
Fig.
and
Preliminary
of
its
stroke,
er
shank
Top
end
of
extend
1.
59
er
of
mm)
(Fig.
As
the
1/32
8A).
spreader
spreader
looper,
between
THE
upper
upper
or
out
spreader
8A)
allows
Setting:
spreader
about
spreader
to
above
with.
Fig.
UPPER
11
SPREADER
spreader
spreader
or
turned
shaft,
on
clamp
collar
holder
When
holder
vertical
(Fig.
shank
1/16
the
moves
should
inch
spreader
002
to . 004
from rig
pass
spreader and
(A,
in
its
around
if
to
be
upper
should
(.
79
hold-
lower
Fig.
holder,
it
is
not
holds
rotated
spreader
should
8A).
to
ht
just
inch
(STYLES
8A)
in
and
its
shank.
already
spreader
or
be
set
39500
its
holder.
permits
Insert
in
place.
holder
adjusted
is
at
the
to
position
QJ
and
Screw
it
to
spreader
Screw
in
laterally.
right
spread-
SJ)
be
the
end
left
Turn
end
of
the
handwheel
its
travel.
At
until
this
upper
position,
spreader
the
is
lower
at
point
15
the
Fig.
8A
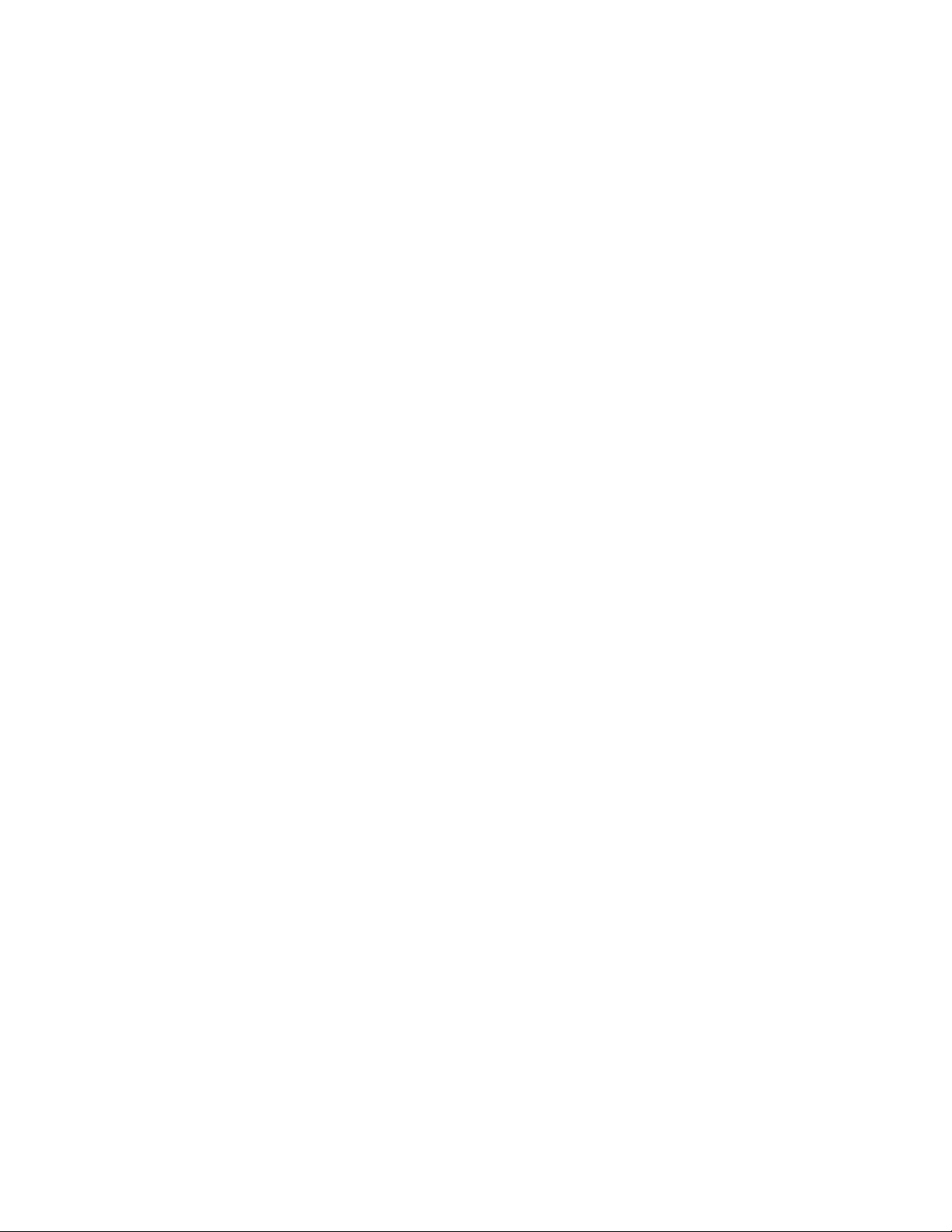
SETTING
of
the
line
of
THE
spreader
the
needle
UPPER
should
and
SPREADER
extend
should
plate
ing
about
be
the
31 /
64
(Fig.
spreader
(STYLES
5/32
inch
l0A).
inch
(12.
If
holder
39500
(3.
97
30
mm)
resetting
(A,
QJ
mm)
is
Fig.
and
SJ)
to
the
above
necessary,
10A).
(Cont.)
left
the
top
of
do
of
the
the
it
center-
throat
by
mov-
feed
bar.
The
appear
justing
of
travel,
3/64
inch
39500
throat
of
throat
SR
and
be
set
Fig.
feed
above
pin
(1.
TY
which
plate.
plate,
SX.
to
the
in
the
19
On
same
9A
dogs
the
place.
top
mm)
should
Now
for
Style
should
throat
With
of
the
above
set
Styles
39
height
needle.
out
ward
opposite
spreader
feed
spect
pin
be
plate.
the
teeth
the
rise
the
chaining
39500
500
QV,
as
the
Now
of
its
a
check
If
needle
holder
short
movement,
and
Assemble
dog
(B).
to
the
(C).
set
This
level
Screw
feed
throat
on
dogs
the
plate,
depth
feed
the
dog
QJ,
QL,
chaining
main
distance.
needle.
SETTING
chaining
Main
throat
pin
at
(D)
locks
at
main
of a full
teeth
QN,
feed
dog
setting
rubs
the
slightly
will
Reset
feed
plate
raises
the
time
feed
their
feed
on
all
tooth
flush
QX,
feed
dog
teeth.
between
back
and
These
reduce
THE
feed
dog
by
rotating
or
teeth
tilting
highest
dog
should
Styles,
above
with
RP,
teeth
of
rotate
to
lower
FEED
dog
should
lowers
first
point
except
the
RU,
should
upper
spreader,
spreader
same
the
adjustments,
clearance
looper
DOGS
(A,
Fig.
be
levelled
feed
the
ad-
be
the
top
SJ,
spreader
pull
holder
(Fig.
13)
tilting
back
Fig.
spreader
for-
between
9A).
to
main
with
adjusting
end
of
l0A
and
in
re-
the
NOTE:
C
screw
be
locked
Styles
(B)
also
with
39500
serves
nut
(C)
TG
Fig.
as
even
or
TY
DO
SETTING
13
latch
pin
when
scr
NOT
THE
for
ew
have a chaining
LOWER
KNIFE
assembly.
14)
flush
Adjustments
gonal
lower
pressed
no
ary
i n
screw
against
the
is
cloth
not tig
plate
htened
feed
Replace
dog.
lower
Lower
should
with
be
set
throat
are
head
knife.
screw
Lower
against
lateral
when
Lower
any
adjustment
width
knife
position
(B)
and
support
latch spring,
agai
nst
lower
knife
with
plate
made
knife
upper
of
trim
may
locking
bracket.
it
should
knife
knife
(A,
cutting
surface.
with
which
is
knife,
is
necess-
is
changed.
be
secured
by
tightening
nut
Because
holder.
holder
Fig.
edge
hexa-
holds
spring
so
(C)
always
16