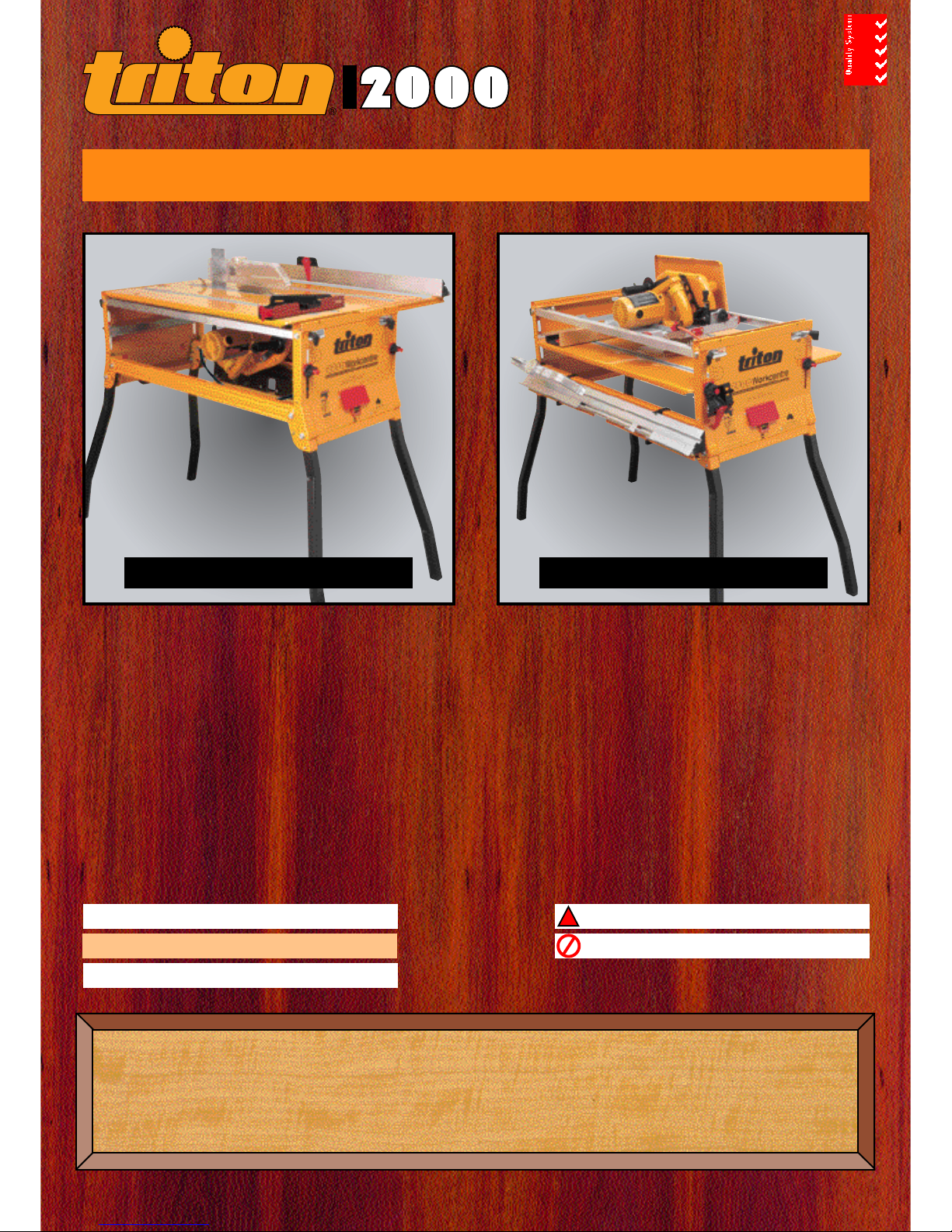
TERMS AND SYMBOLS USED IN THIS MANUAL
“Front of the Workcentre” refers to the end which has the switchbox. The “left-hand &
right-hand side” are when viewed from the front of the Workcentre.
Safety warning or safety instruction.
Handy hint & tip.
Possible fitting or operating difficulty.
Assembly & Operating Manual
A WORD FROM THE MANUFACTURERS
Thank you for your purchase of the Triton Series 2000 Workcentre. If properly set up,
and fitted with a good quality saw and blade, it will give you great accuracy and many
years of trouble-free service.
To set up properly, make sure you follow this manual. Otherwise you could spend
many unnecessary hours, and still not get it right.
Workcentre
Quality
Endorsed
Company
TABLESAW MODE
CROSSCUT MODE
Parts list 2 Test Cuts - Table saw mode 12-13
Basic assembly diagram 3 Test Cuts - Crosscut mode 13-14
Fitting the Triton Precision Saw
4-5 Operating - Table saw 15-23
Fitting other brands of saw 6-7 Operating - Crosscut saw 24-27
Final assembly 8-11 Warranty & Mailing List 28
Take special note of this instruction.
WARNING! Do not attempt this.
!
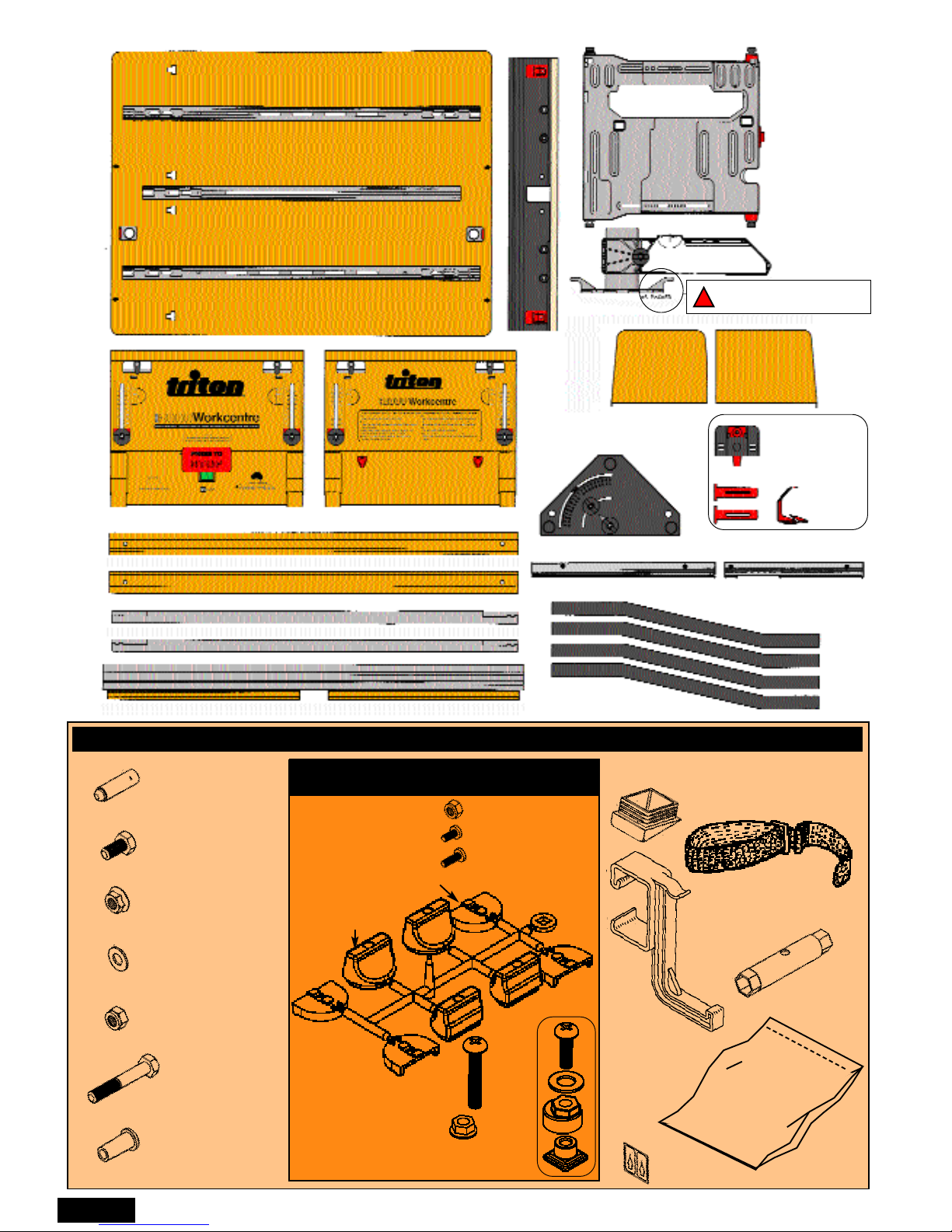
Page 2
PARTS LIST
k. Saw Locators (4)
d. 8mm Washer (20)
m. M6 x 40mm Philips-
head Screws (4)
n. M6 Flange Nuts (4)
a. Leg Locking Pin (4)
b. M8 x 16 Bolt (4)
c. M8 Flange Nut (4)
e. M8 Nyloc Nut (8)
f.
M8 x 50 Bolt (8)
s. Tube Spanner
q. Trigger Strap
u. Scale
Pointer Labels (1)
r. Fence Hanger (2)
g. Push-stick
hanger (2)
p. Angled foot (4)
h. M5 Nyloc Nut (3)
j. M5 x 25 Screw (1)
o. Alignment Cams for Triton Saw
(2 sets packed in separate bag)
A Table (1)
C Rear End Panel (1)
D Legs (4)
E Bearing Channels (2)
F Base Channels (2)
G Protractor (Mitre gauge) (1)
H Crosscut
Fence (1)
I Rip Fence (1)
J Overhead Guard &
Guard Support (1)
K Side Guard (2 parts)
L Slide Chassis (1)
M Guided
Push-stick &
Side Pressure
Finger Kit (1)
N Rip Fence Bevel Guides (3 parts)
MAIN FASTENER BAG
Router Table
Series 2000
Fitting Kit
B Front End Panel (1)
t. Router Table
Fitting Kit
l. Clamping
Knobs (4)
Reverse from packed
position before using
!
SAW CLAMPING HARDWARE
(SEPARATE BAG)
i. M5 x 8 Screw (2)
N Rip Fence Bevel Guides (2 parts)
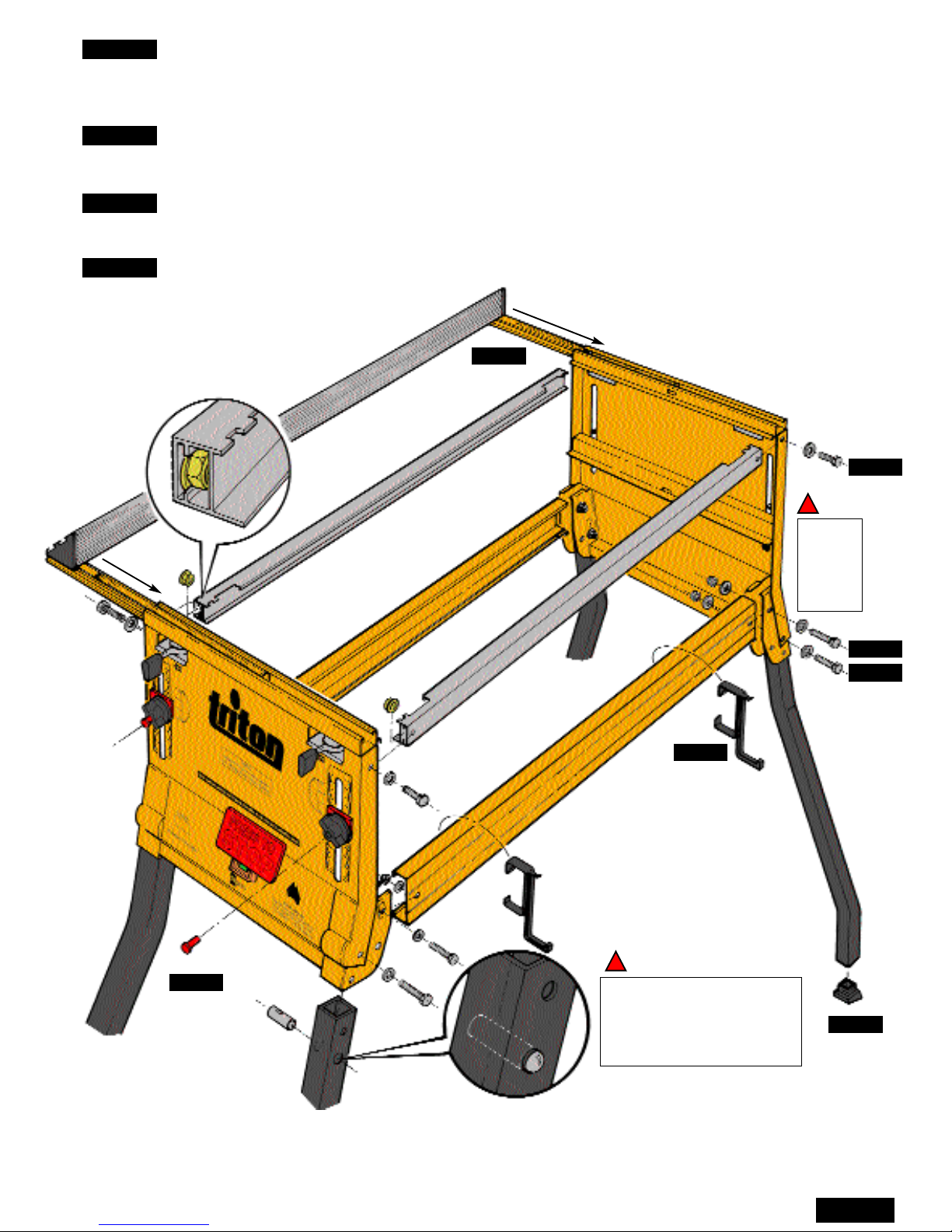
Page 3
Insert Flange Nuts into
the ends of the
bearing channels.
Check that each leg and leg
locking pin is facing the right
way before fitting. Depress
and hold the spring-loaded
ball when fitting the leg.
!
!
Note the
correct
positions
for the
washers.
STEP 1: Fit the Legs (D) to each End Panel (B & C). Before fitting, check that each leg splays
outwards as shown, and that you have fitted the Leg Locking Pin (a) with the springloaded ball facing outwards. Tighten the bolts so that the legs are firm, but still free to
pivot. Use four M8 x 50 bolts (f), eight washers (d) and four M8 Nyloc nuts (e).
STEP 2: Fit the Base Channels (F) as shown. Tighten the bolts until the leg brackets close firmly
on the base channels. Do not overtighten. The Nyloc nuts used are vibration proof and
won’t come undone. Use four M8 x 50 bolts, eight washers and four Nyloc nuts.
STEP 3: Fit the Flange Nuts (c) inside the Bearing Channels (E) and fit the bearing channels to the
end panels. They should click into position when pushed up from below. Fully tighten the
bolts. Use four M8 x 16 bolts (b), four 8mm washers (d) and four flange nuts.
STEP 4: Fit the plastic components (r, g & p) as shown, and then fit the Rip Fence (I).
(r)
(g)
STEP 1
STEP 3
STEP 2
STEP 4
(p)
STEP 4
STEP 4
STEP 4
FENCE LOCKING: You only need use 2 locking levers - one at the front and one at the back. The
locking position of the levers is factory preset. To adjust, simply loosen or tighten the nut at the
bottom of each clamp assembly. The levers should reach at least the half way point in their arc of
travel before tightening up. Lubricate the cam faces occasionally with light machine oil.
(I)
(E)
(F)
(D)
(c)
(b & d)
(a)
(B)
(C)
(d & f)
(e)
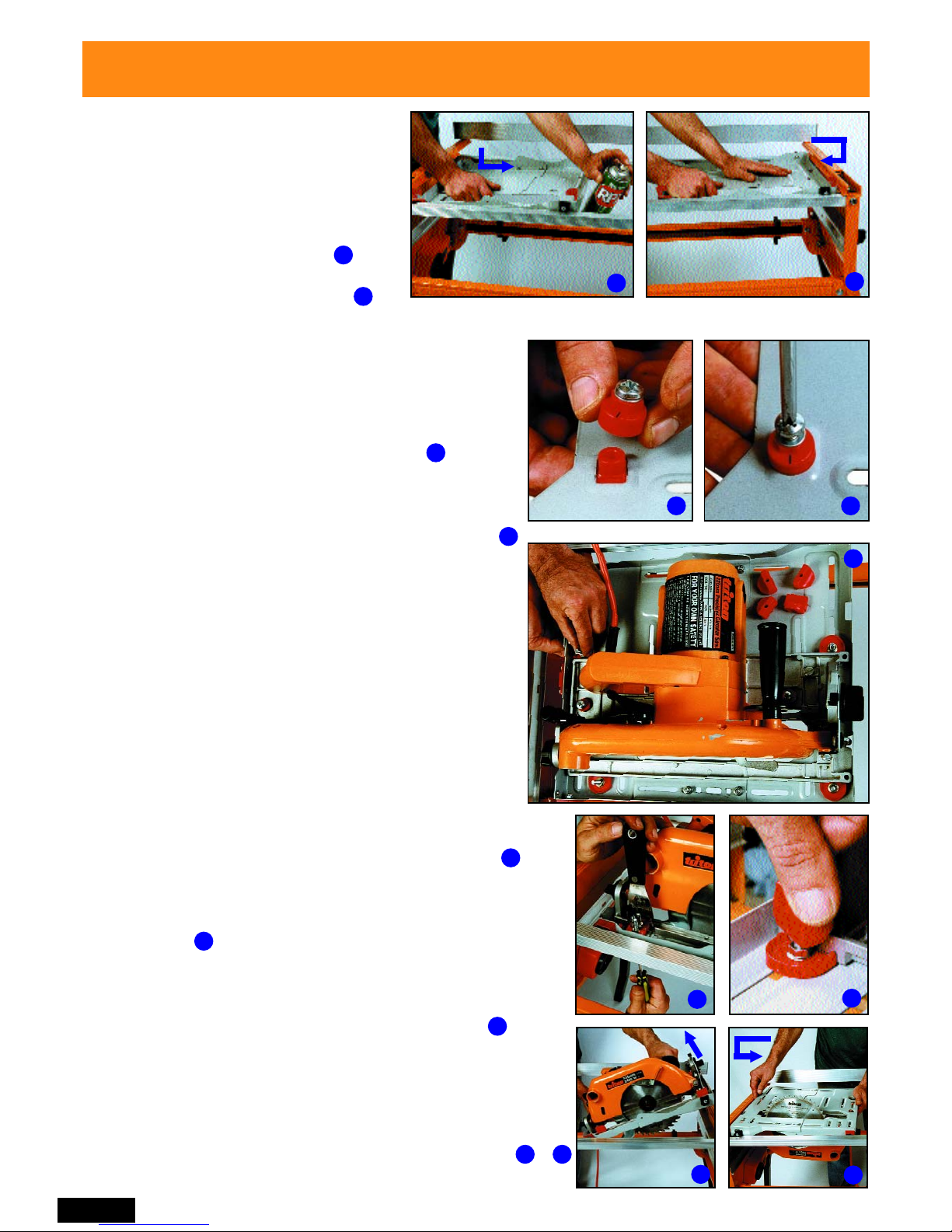
1
Unplug your saw. Check that the blade is set at 0˚ and
at full depth of cut.
2
Page 4
Screw the knobs on (they cut their own thread) until they just
scrape against the top edge of the saw base-plate. This
tension is sufficient to hold the saw upside-down for final
adjustment, and still allow the saw to be shifted sideways
slightly using the alignment cams.
Fitting the Triton 235mm Precision Power Saw
For other brands of saw go to Page 6.
FITTING THE SLIDE CHASSIS
FITTING THE TRITON SAW
Spray the channels with RP7 or WD40 for a smooth slide.
Fit the saw into the chassis with the alignment cams
locating in the holes in the saw base-plate.
If the saw is set at full depth, the saw’s spring-loaded
guard will be held in the retracted position by the back
edge of the chassis cutout.
Break or cut the Saw Locators (k) and Knobs (l) from their
moulding “tree” and carefully trim off any remnants with a
sharp knife. Fit the saw locators in the slots shown in using
4 Philips-head screws (m) and Flange nuts (n). The straight
edges should be against the baseplate, but spaced away
from it slightly to allow for final saw adjustment. (Use a
spatula blade or a piece of cardboard or metal about 1
mm thick as a spacer.) Firmly tighten the screws.
FITTING THE SAW LOCATORS AND KNOBS
2
3 4
5
6
8
7
9
Place the Slide Chassis (L) in the
bearing channels with the red plastic
catch and red bearing spacers closest
to the front panel (the switch box end)
and the flanges upwards. Enter two
bearings in the channel cutouts.
Slide the chassis towards the rear panel
and the other bearings will drop in.
Fit the Saw Alignment Cams (o) from below , holding
the bases in the rectangular slots while you screw into
them. (They cut their own thread.) Make sure the lines
moulded on top of the cams are both pointing towards
the rear panel. Tighten the screws until nipped gently.
Check that the saw is securely mounted. Turn the slide
chassis over, re-engaging the bearings in the channels. &
3
4
6
8 9
7
5
1
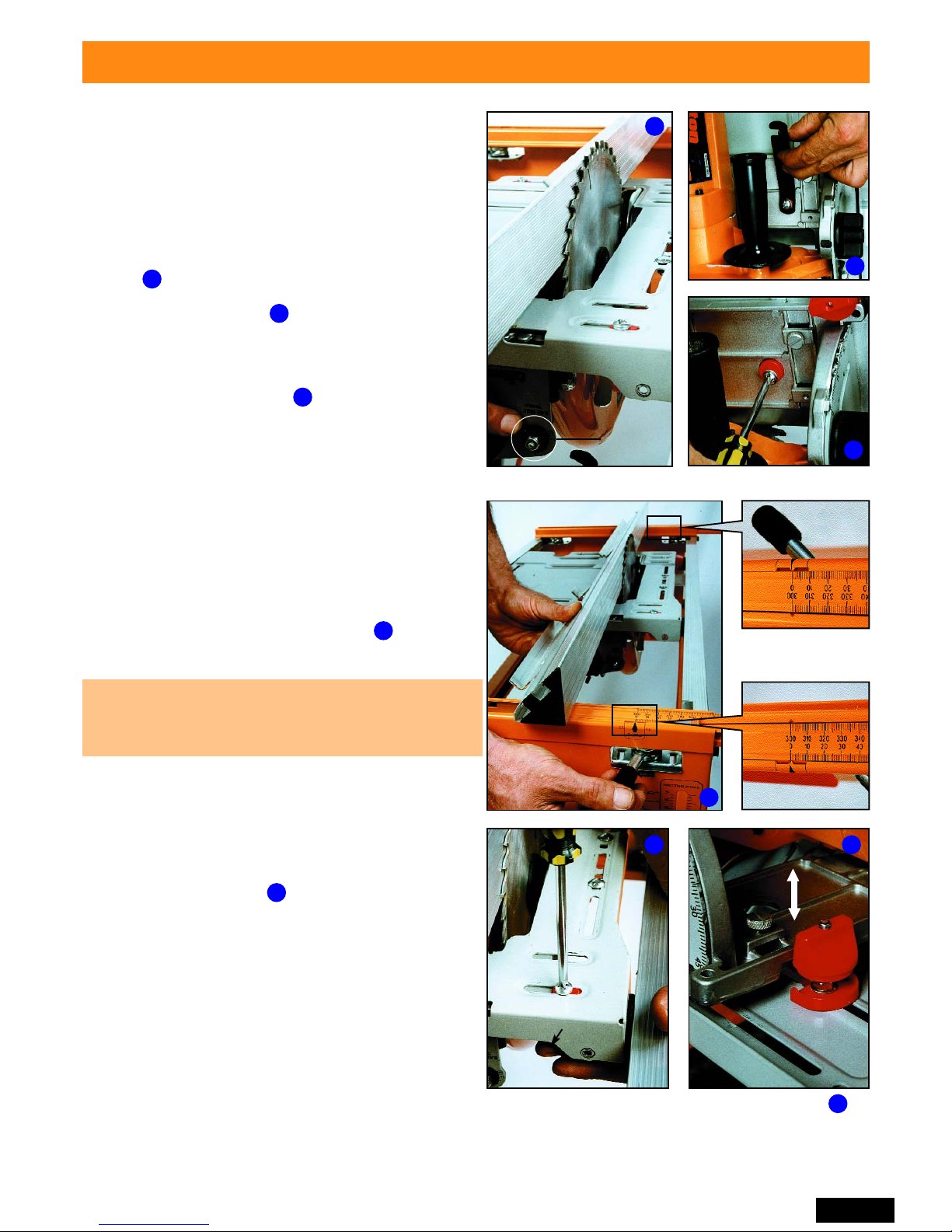
6
5
When satisfied with the position of the saw,
reposition the saw locators hard up against the
edge of the baseplate, as follows. Hold each knob
against turning and loosen the screw about half to
one turn. Push the saw locator into position, and
firmly tighten the screw.
Turn the saw right-way up again and loosen the
four knobs a couple of turns. Check that the saw
cannot move sideways at all, and that all screws
are fully tightened. Do up the knobs again,
perhaps one turn beyond when they first scrape
on the baseplate.
The saw is now set up, and is available at any
time for hand-held use by simply loosening each knob half a turn and lifting the saw straight up.
If the locators are correctly fitted, the saw will go back into exactly the right spot each time.
Triton saw owners, please skip to Page 8.
4
Double-check the saw position by now locking the
fence at 0 mm, and trying to turn the blade
backwards by hand. The teeth should lightly
scrape against the face of the fence. If not,
repeat the above alignment.
3
2
1
This is a very important step, because it will
ensure that your saw cuts are true, and that your
fence scales are accurate, so take your time.
Page 5
Position the chassis halfway between the end
panels. Adjust the fence in close to the blade and
lock it. Make sure the blade is vertical by
comparing it to the face of the fence.If necessary,
loosen the nut holding the Blade Angle Trimmer
(circled), and adjust the blade angle. Re-tighten
the nut.
Use the saw’s spanner or the Tube Spanner
(s) to rotate the cams until the front and rear of
the blade are just touching the fence, when it is
at 0 mm. When satisfied with the position tighten
the alignment cam screws.
ALIGNING THE SAW
FINAL CLAMPING OF SAW
Fitting the Triton 235mm Precision Power Saw (cont.)
1
2
3
4
5 6
Hold knobs while
adjusting locators
Adjust
blade angle
Unscrew the front handle of the saw for better
access to the front cam. Lower the blade for
access to the rear one.
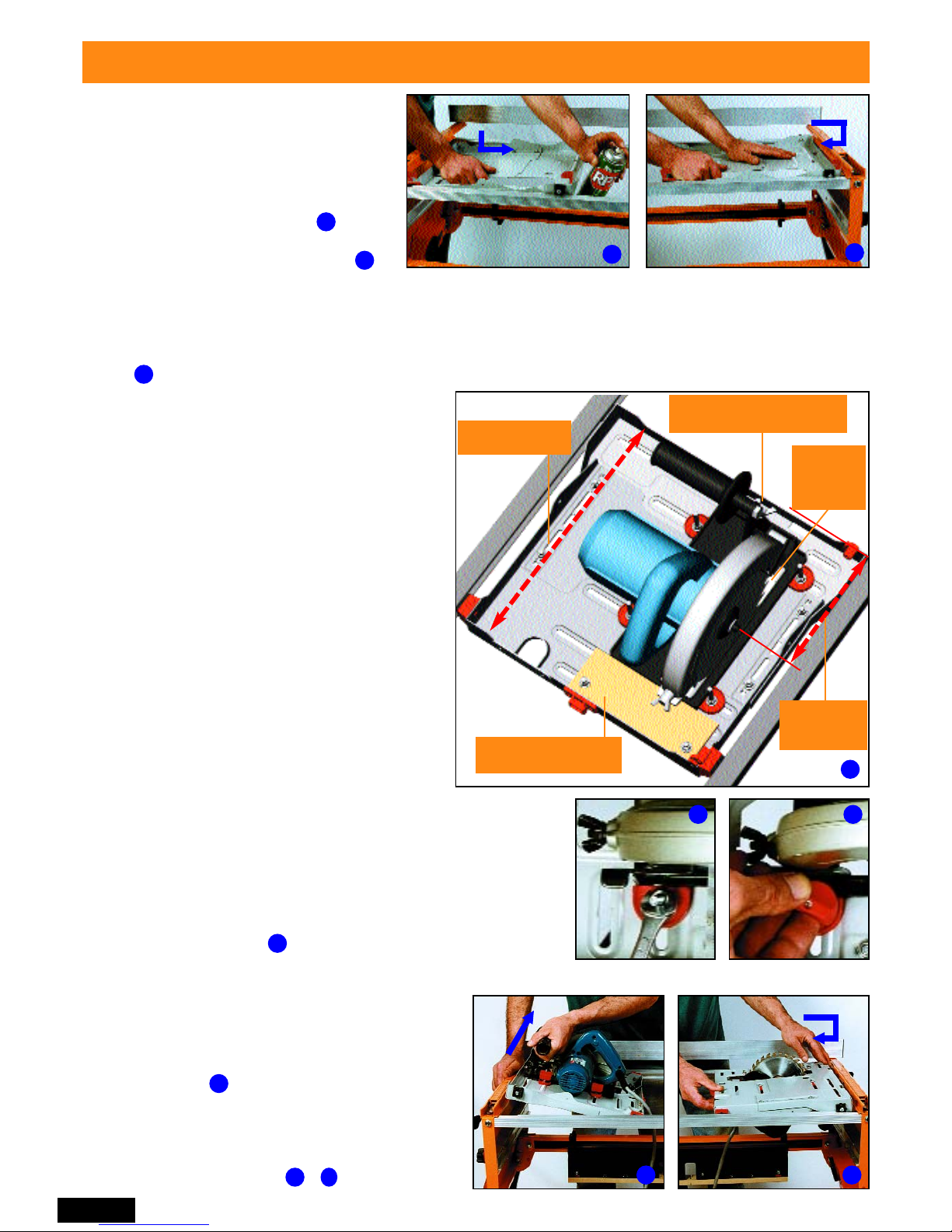
2
4
Break or cut the Saw Locators (k) and Knobs (l) off their
moulding “tree”, and trim any remnants with a utility knife.
Fit the saw locators in the selected slots, with their straight
edges against the base-plate using four M6 screws (m) and
Flange nuts (n). Firmly tighten up the screws using a
screwdriver from below.
The spanner shown is optional, as the Flange nuts are self-gripping.
76
5
Check that your saw is unplugged, make sure the blade is set at full depth of cut, and is set at 0˚.
Study below [especially if you have a small (184mm) saw] and follow steps 1 to 5 as required.
Page 6
Fitting other brands of power saw
FITTING THE SAW LOCATORS
Check that the saw is securely clamped, and
turn the slide chassis over, re-engaging the
bearings in the channels. &
FITTING THE CLAMPING KNOBS
Screw the knobs on (they cut their own thread)
until they scrape against the top edge of the
saw base-plate. Leave the knobs with the
cutaway sections facing away from the saw.
5
6 7
ADJUSTING THE SLIDE CHASSIS
1. Adjust the slide chassis to the shortest
length which will suit your saw, and provide
widely spaced slot positions on the
baseplate edges for fitting the clamps. (In
shortening the chassis, do not overlap any of
the mounting slots. If relocating the four
coach bolts, use the square holes.)
2. Position the saw as far forward as possible
on the chassis, but allow for finger access to
the front wing-nut or knob on the saw.
3. Don’t obstruct the sawdust opening in front
of the saw blade.
4. Try to have the blade nut no more than
170mm from the front of the chassis.
5. For small saws, bolt a thin wooden spacer
(eg. 6mm ply) behind the saw, to prevent
possible saw movement.
3
1. Adjust chassis
to length
2. Saw forward in chassis.
Allow access to adjuster.
4. Maximum
distance
170mm
5. Attach 6mm spacer
for small saws
3
3. Don’t
obstruct
sawdust
opening
1
FITTING THE SLIDE CHASSIS
Spray the channels with RP7 or WD40 for a smooth slide.
2
Place the Slide Chassis (L) in the
bearing channels with the red plastic
catch and red bearing spacers closest to
the front panel (the switch box end) and
the flanges upwards. Enter two bearings
in the cutouts in the channels. Slide
the chassis towards the rear panel and
the other two bearings will drop in.
1
4
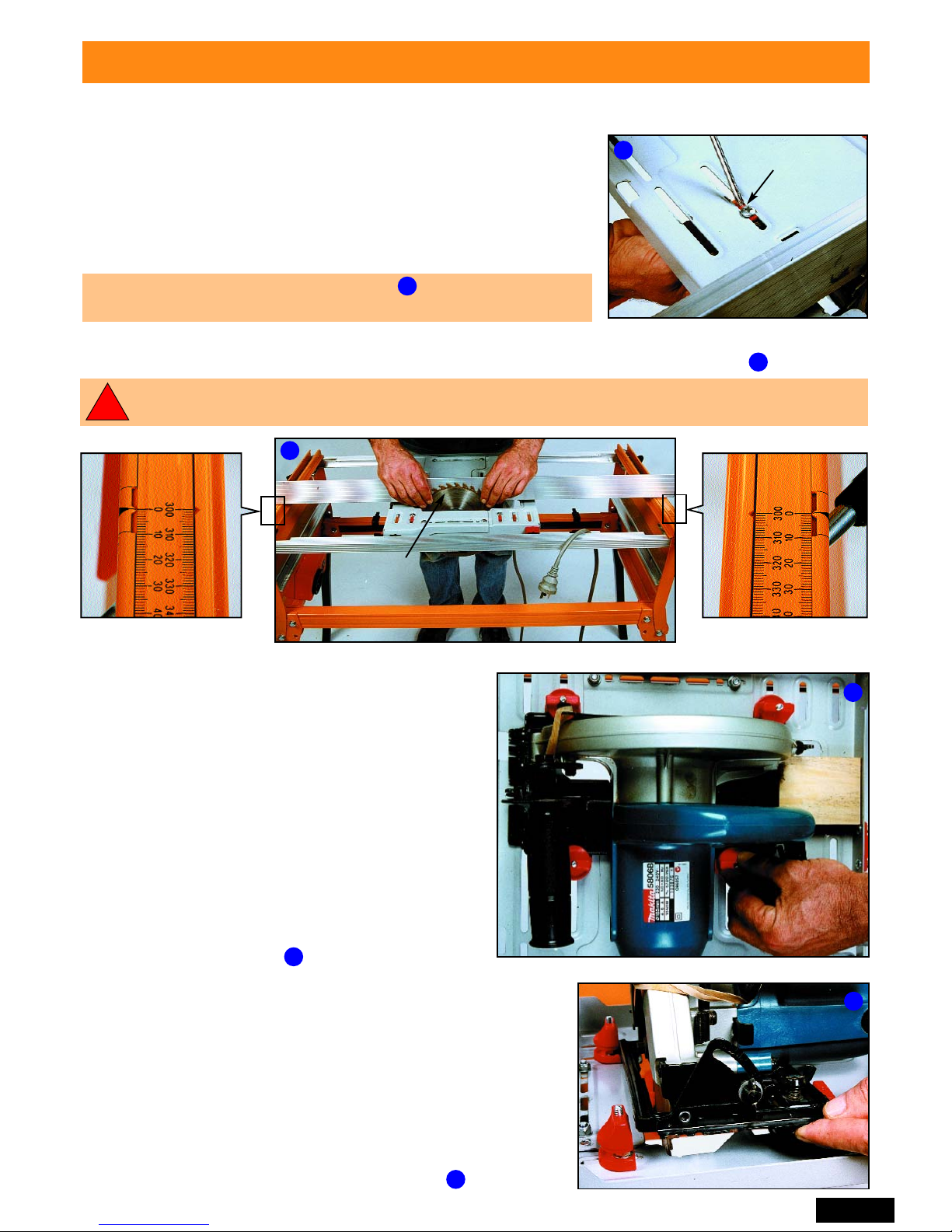
Do up the knobs, and this time you can tighten them a little
more firmly, perhaps one turn beyond when they first scrape on
scrape on the base-plate.
If you tighten any one knob too much, and can’t loosen it, undo
the other three knobs by half a turn, remove the saw and undo
the knob.
Page 7
Fitting other brands of power saw (cont.)
Have the chassis midway between the end panels and lock the rip
fence close to the blade. Compare the blade angle to the vertical
face of the fence, and if necessary adjust the blade angle (using
the saw’s adjuster) until they are parallel vertically.
Hold the clamping knobs to stop them turning and use a
screwdriver to loosen the clamp assemblies - half to one turn only.
Push the saw locators to move the saw. Do not push the saw
itself as this may dislodge the clamps.
Lock the fence at “0” front and rear and align the saw so that the blade is just touching the fence.
Spin the blade backwards by hand. The teeth should lightly scrape against the fence.
ALIGNING THE SAW
This is a very important step, it will ensure that your saw cuts are true, and that your fence
scales are accurate, so take your time.
!
The saw is now set up, and is available at any time for handheld use by loosening the knobs half a turn and lifting the saw
straight up. If the locators are correctly fitted, the saw will go
back into exactly the same position each time.
1
2
1
2
Turn the saw upside down again, re-fit the fence and double
check that the blade is still at “0”.
Push saw locator
not the saw
FINAL CLAMPING OF SAW
3
4
4
3
Check that each saw locator is pressed up against
the baseplate, hold the knobs against turning, and
firmly tighten the four screws.
Remove the fence and turn the saw rightway up.
Undo the clamping knobs a couple of turns and
check that you cannot move the saw sideways at
all between the locators.
Blade just
scrapes
fence at “0”
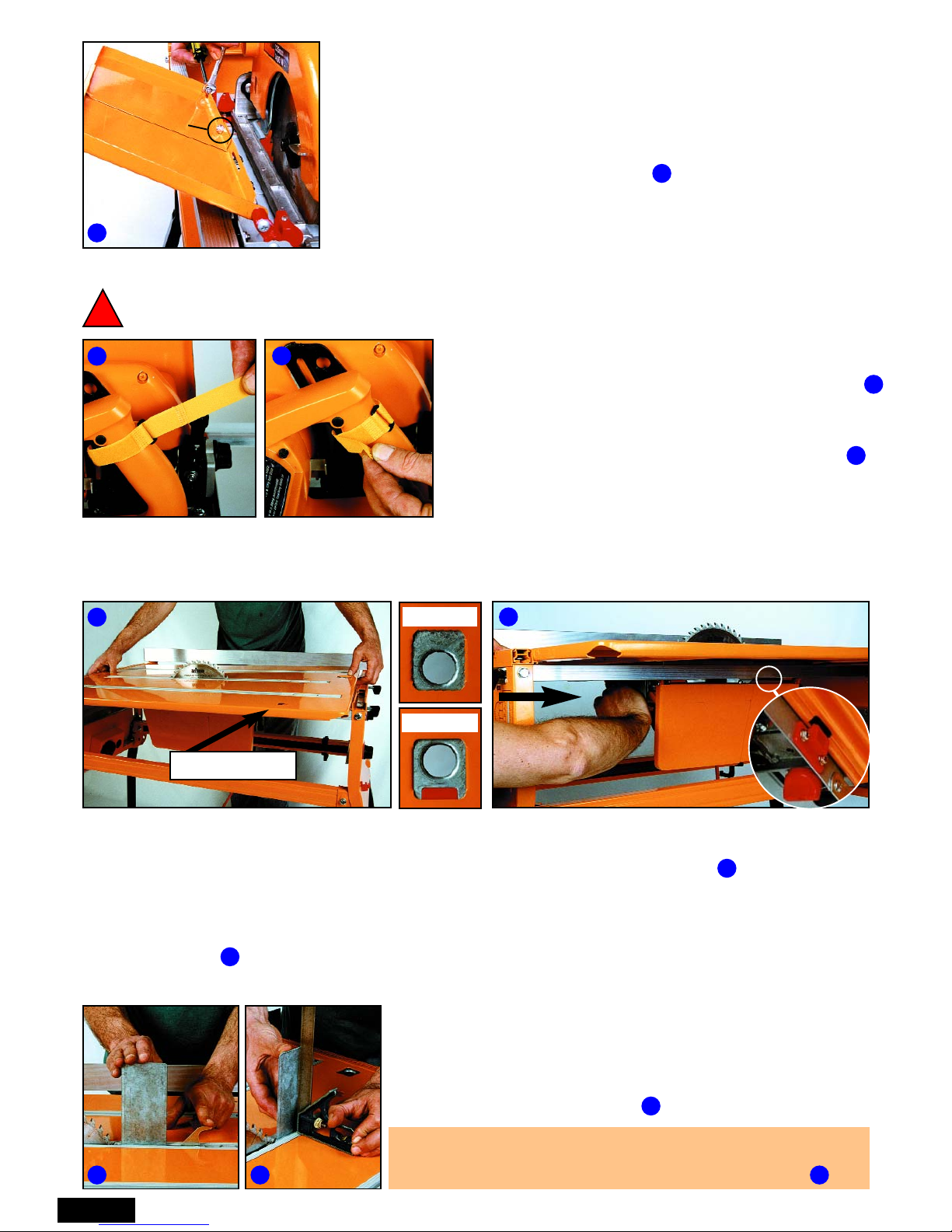
FITTING THE OVERHEAD GUARD & SUPPORT
Loosen the knob on the Overhead Guard (J) to remove the
Guard Support from its shipping position. Fit the support to
the centre table slot, using the cut-outs at the end.Ensure the
saw blade is adjusted to its maximum depth, then position
the support about 12mm behind the blade and lock it in by
pressing the locking lever down.
Lubricate the entry if it’s a tight fit. Check the guard support
is reasonably square to the table, and adjust it if necessary
by pushing evenly with your hand or a block of wood.
Page 8
Wrap the Trigger Strap (q) around the handgrip with
the furry side facing outwards. Pass the strap through
the buckle, until the security loop has passed through.
If your saw has a safety lock-out button press it and
then tighten the strap until the trigger clicks “ON”.
Wrap the free end of the strap around the handgrip.
With most saws, the strap can be slid on and off the
saw trigger, without undoing it each time.
Turn the slide chassis upside down. Position it roughly half-way between the end panels. The front
of the saw must be facing the front panel (switchbox end).
Lower the Table (A) over the blade, with the four T-slots closest to the rear panel. Line up the
arrows on the edges of the table with the scale pointers on top of the end panels. Push the table
latches to the “LOCK” position. The red indicators disappear from view when the latches fully locate.
Reach underneath and push the slide chassis towards the rear panel until the red catch (shown in
the inset view on ) “clicks” home and locks the chassis underneath the table.
LOCKED
UNLOCKED
FITTING THE TABLE
!
Before fitting the trigger strap (q) always ensure that the saw is disconnected from the power
and that the switch on the Workcentre front panel is in the “OFF” position.
FITTING THE TRIGGER STRAP
T-slots to rear
FITTING THE SIDE GUARD
Slide the two sections of the Side Guard (K) together until they fit
between the pivot brackets on the slide chassis. Loosely fit the short
Philips-head screw (i) and a Nyloc nut (h) to hold them together.
Fit the two longer Philips-head screws (j) and Nyloc nuts through the
pivot brackets and into the guard flanges. Tighten until the guard
is firm, but still free to pivot. Finally, tighten the screw holding the
two halves together.
Nyloc nut
on inside
1
2
3
4
5
6 7
1
2
3
4
5
6
7
Do not leave the trigger strap permanently locked on. When you have finished work for the day,
release the strap and allow the spring in the trigger to relax.
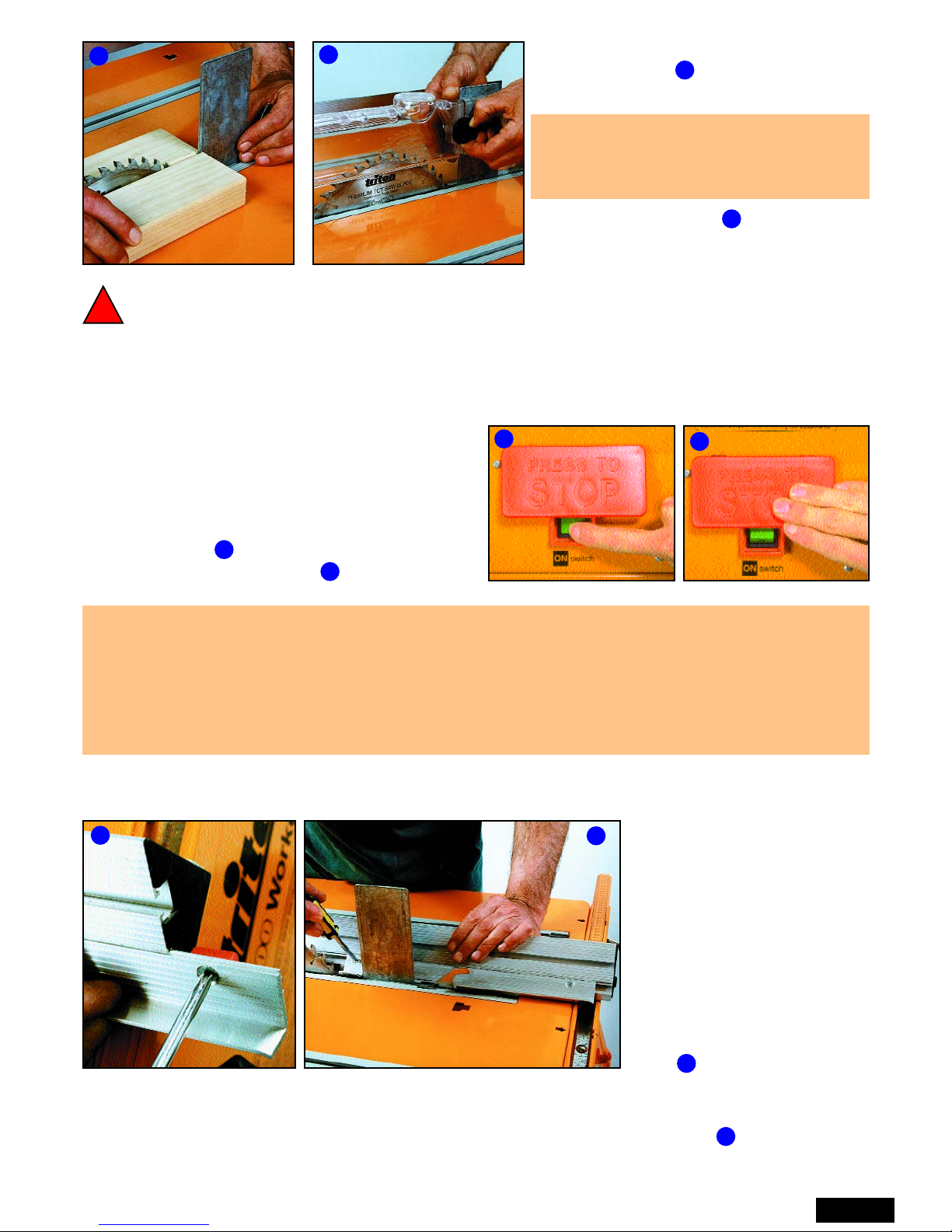
The plain bevel guide fits in front of the blade. The notched bevel guide fits at the rear, with the
small tab locating between the blade and the overhead guard support. (If your power saw is fitted
with a riving knife remove the small tab (circled) from the guide using a hacksaw.)
Tighten the Phillips head screws. The function of the guides is described on 20.
Hold 2 straight pieces of wood lightly
against the blade. The overhead guard
support should fit between the pieces.
Fit and lower the guard. Spin the blade
by hand before connecting the power to
ensure it is not touching anything.
If not you may have to adjust the saw
position slightly. This is only likely if you
have a very thin kerf blade (2.0 - 2.2mm
cut width)
Page 9
CONNECTING THE POWER
Make sure the switch is “OFF”, plug the saw into
the switch box, and bring power to the switch box
via a 10 Amp extension cord.
Press the green switch with your finger to switch
the power “ON”. Tap the stop plate with your
hand or knee to switch “OFF”.
Switch the power on and off and watch the blade. If it quivers sideways on start-up it’s a sign of a
worn arbor in your saw, or excessive slack in the mountings between the motor and baseplate.
If the blade vibrates significantly at full speed or on slow-down, it’s either buckled or not seated
properly on the arbor. Check the flatness of the blade with a straightedge, check the fit of any
arbor-reducing washers, and check for resin/sawdust build-up on the arbor or flange washers.
A slight quiver is generally noticeable on slow-down in most blades, and shouldn’t affect your cuts.
Always make sure the blade is at full height, the guard is fitted, and the table is locked to the
end panels before switching on the power.
Check that the teeth on your blade are pointing in the same direction as the etched symbols
on the guard. If not, you have incorrectly fitted the blade to your saw.
!
Reverse the fence so that
when fitted to the Workcentre
from the left hand side, the 45
o
face is closest to the blade.
To fit the Bevel Guides (N),
loosen the Phillips-head
screws slightly, engage the lip
at the top of each guide in the
mating section of the rip
fence, and guide the red
plastic clamping feet into the
T-slot.
1
2
3
4
5
6
1
2
5
6
3
4
FITTING THE BEVEL GUIDES