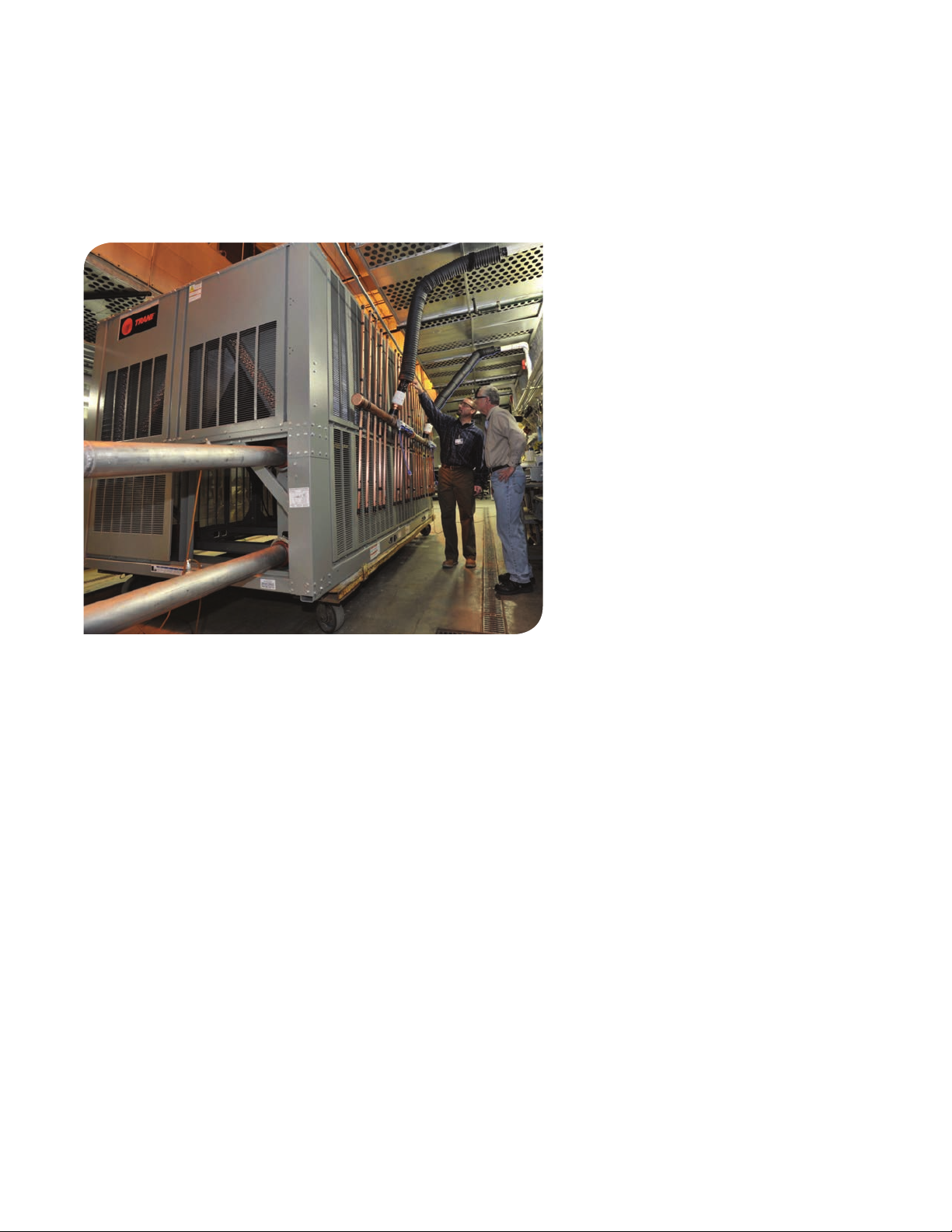
World-class testing sets Trane chillers
apart from the competition.
Our rigorous design verification helps ensure
reliable operation over a wide range of
operating conditions. Testing involves:
• Extreme testing, including cold ambient starts,
hot water starts and high ambient operation
• Compressor-accelerated lifecycle testing,
including high-pressure ratio, high load test,
flooded starts/stops, start/stop testing and
phase reversal
• FEA analysis to confirm the unit structure can
withstand shipping, rigging and operational
activity
• Electrical testing with destructive testing for
short-circuit withstand rating
• Performance modeling and verification, both
during design and for the life of the chiller
Trane offers units
and compressors
that have been
extensively tested to
verify that their
operation is robust
and that a smooth
start-up is ensured.
Reliability
You need performance that is dependable and
reliability you can count on. We are committed
to the highest level of design and
manufacturing accuracy to make sure your
chiller performs as expected.
Over 50,000 Pueblo-built RTAC chillers are
installed around the world and attest to our
unequaled reliability. There are more than
250,000 helical rotary compressors (including
both air and water cooled chillers) operating
with our proven direct-drive, low speed,
semi-hermetic compressor design. These facts,
along with over 25 years of helical-rotary chiller
manufacturing know-how and a continued drive
to improve our processes, are the ingredients for
our sustained reliability.
World-class testing facilities
Trane’s world-class testing facilities set us apart
from the competition. We look at environmental
performance, operating longevity, and overall
operating efficiency in order to provide you with
the most reliable product for the long term.
On-site factory performance testing confirms
that the actual chiller performance matches
predicted performance, and test results serve as
a benchmark during the commissioning process.
On-going testing is conducted to continually
confirm that performance expectations are
being met and quality product is being
produced. After the chiller goes into production,
we keep looking for ways to make it better,
quieter, more reliable, and more efficient.