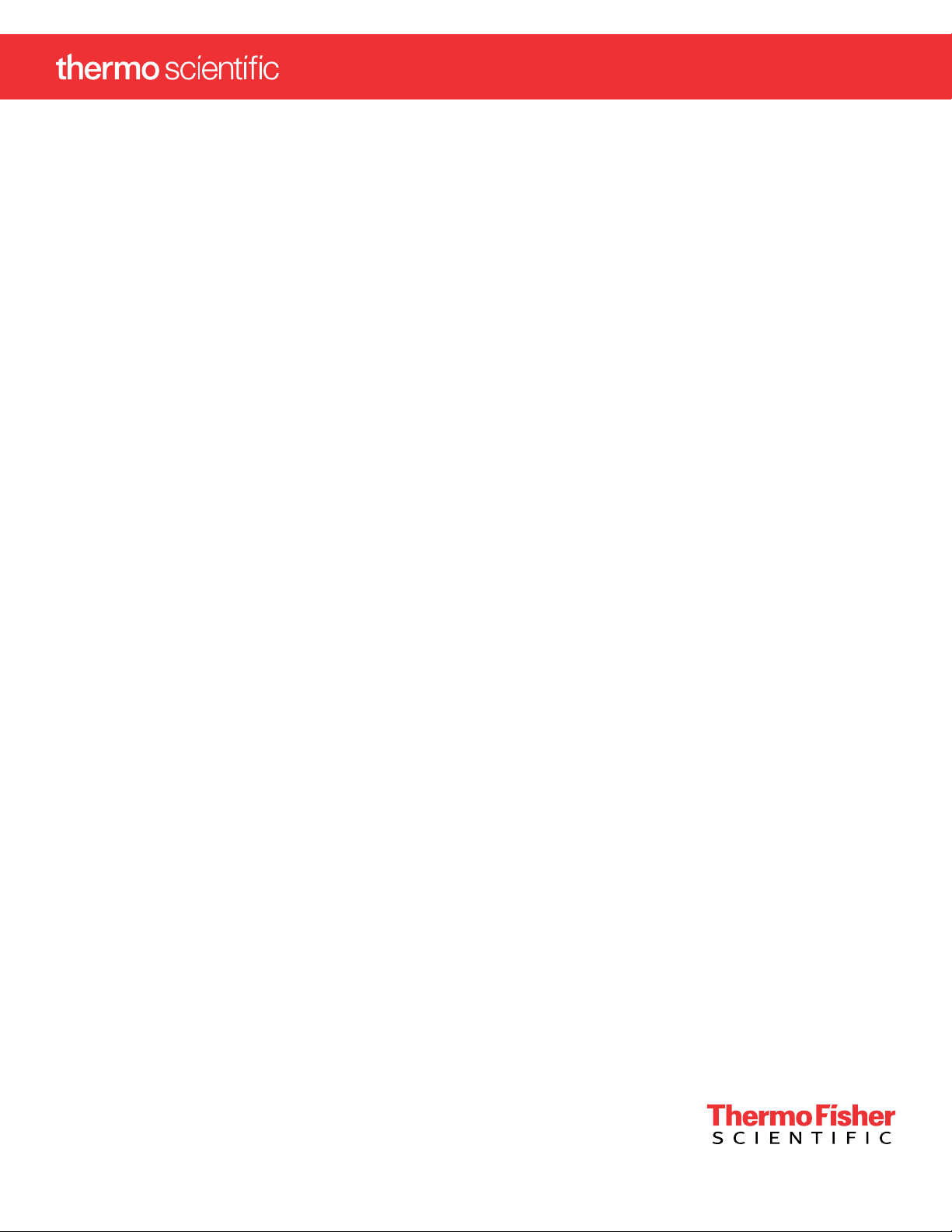
APPLICATION NOTE HyPerforma Single-Use Fermentors
End-user evaluation of 30 L and 300 L HyPerforma
Single-Use Fermentors and scale-down model
Summar y
In moving processes from bench to pilot and ultimately
production fermentors, it is critical to have a reliable
scaledown model. The purpose of a scale-down model is
to demonstrate at the benchtop level what can be achieved
in production-scale fermentors. Scale-down models
can vary depending on the media, strain, and process
conditions. In this case, a customer wanted a scale-down
model of the Thermo Scientific™ HyPerforma™ Single-Use
Fermentor (S.U.F.) in order to establish what fermentation
processes could be scaled into the S.U.F., in particular
for the production of plasmid DNA. The 300 L S.U.F.
exceeded the customer’s expectations. The customer
anticipated that the test process using E. coli with high
oxygen consumption would reach a final OD of ~80 and
the HyPerforma S.U.F. exceeded expectations by reaching
an OD of 147.
This application also was a successful demonstration of
media preparation through culture harvest, using a jacketed
50 L Thermo Scientific™ HyPerforma™ Single-Use Mixer
(S.U.M.) (60 L working volume and heated to 67°C), 200 L
Thermo Scientific™ HyPerforma™ DS 300 Single-Use Mixer
(S.U.M.), Thermo Scientific™ Powdertainer™ BioProcess
Container (BPC) system, 2 L—50 L Thermo Scientific™
2D Labtainer™ BPC systems, pre-irradiated filters, sterile
funnel BPC, seed BPC, 30 L and 300 L HyPerforma
S.U.F.s, and Thermo Scientific™ CentriPAK™ harvest BPCs.
Purpose
To evaluate the 300 L HyPerforma S.U.F. for GMP plasmid
production process using a customer’s standard evaluation
procedure and test strain.
Procedure
The E. coli culture was maintained at 37°C ± 0.1,
pH 7 ± 0.05, maximum pressure of 0.55 psi, and a
minimum dissolved oxygen (DO) of 30%. DO control
cascaded at 200–375 rpm, 200–500 slpm air, and
0–400 slpm of oxygen as needed to maintain the minimum
set point of 30% DO.
After scaling up the model procedure to the 300 L S.U.F.,
the power-to-volume input, kLa, and gassing rates were
scaled down into the 1 L glass fermentors. The same
original procedure was then followed but using the scaleddown power-to-volume input, kLa, and gassing rates for
S.U.F. comparison. The scale-down model could then be
used for estimating performance with all production strains
for this customer.
The procedure was then repeated with the 30 L S.U.F. and
showed scalability within the HyPerforma product line.
After evaluating additional leading single-use fermentors
from two other suppliers, the customer purchased the
Thermo Scientific 300 L HyPerforma S.U.F..
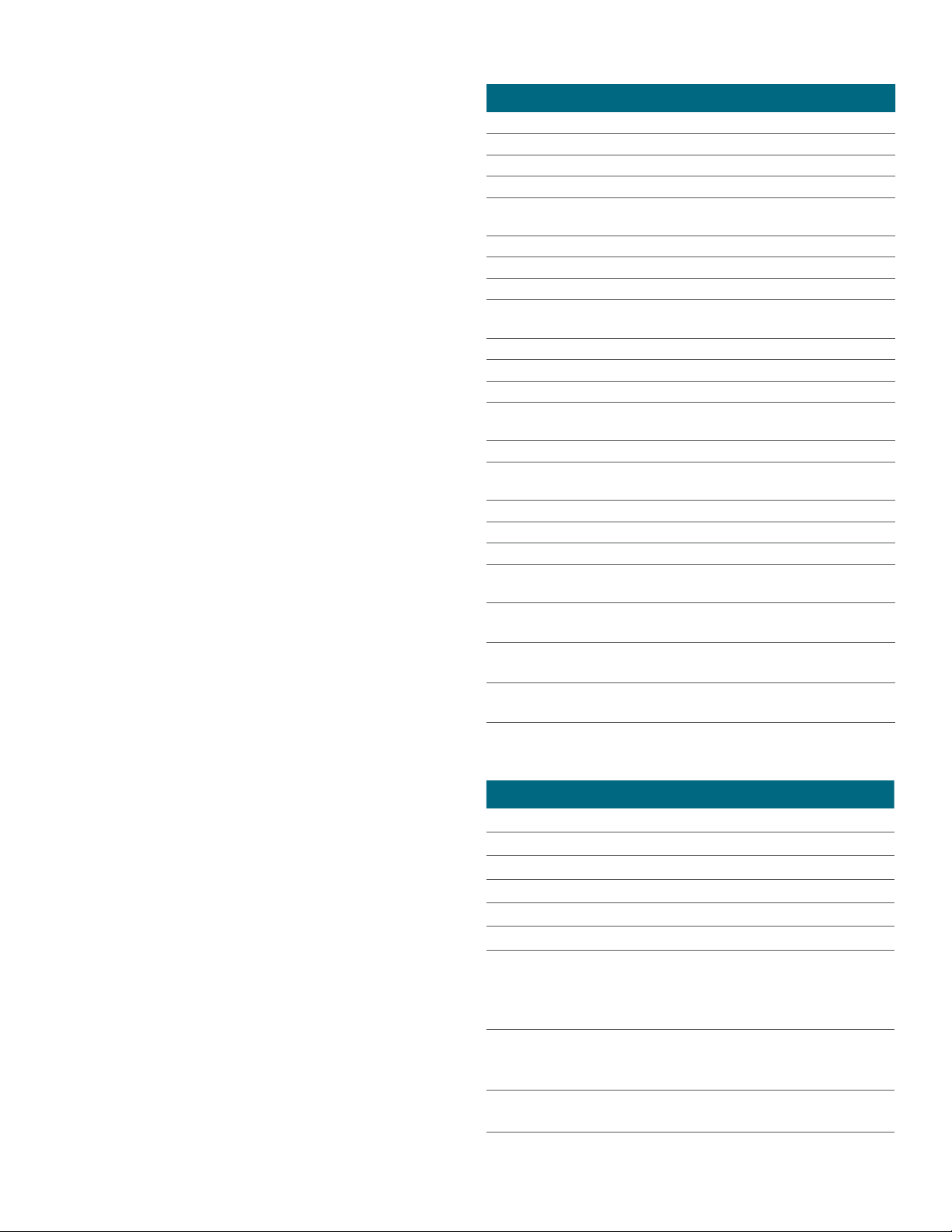
E. coli cells were collected with the Sorvall BIOS 16
centrifuge using CentriPAK BPC singles with quick connect
at 5,373 x g for 15 minutes in 15 L batches. The 30 L S.U.F.
was harvested as closed system in two batches using
CentriPAK manifolds. The 300 L S.U.F. was harvested
within 3 hours using two BIOS 16 centrifuges and
CentriPAK singles filled to about 1.87 L each.
During this feasibility study, the off-gas analyses of the
cultures were compared. It was noticed that the off-gas
trend was comparable. The off-gas analyzer sample line
to each S.U.F. can be placed inside the exhaust filter exit
cavity or connected to a small sterile filter connected to the
S.U.F.’s filter chamber.
Equipment and supplies
Strain:
• HMS174(DE3)
Chemicals:
• Base
• Acid
• Antifoam C8840 (New London Chemicals)
• 60 L nitrogen source, 30% w/v feed solution
• 50 L carbon source, 50% w/v feed solution
• Batch medium
Bioreactor setup
The S.U.F. systems were set up according to the user guide
and controlled by Thermo Scientific™ TruBio™ Software,
powered by powered by the DeltaV™ Distributed Control
Platform from Emerson, utilizing the Thermo Scientific™
TruFluor DO single-use sensors and Hamilton or Mettler
Toledo single-use pH sensors. Operating parameters are
listed in Table 2.
Bioreactor inoculum, cultivation, and scale-up
The inoculum was cultured in an incubator at 37°C,
250 rpm, 1 inch arc, and for 16 hr.
Table 1. Equipment and materials.
Description Cat. No.
30 L S.U.F. Hardware S.U.F.0030.AAA.BAAABB0C00
30 L S.U.F. BPC SH3B11722.01
300 L S.U.F. Hardware S.U.F.0300.AAA.DAAABB0C00
300 L S.U.F. BPC SH3B11861.01
100 L S.U.M., jacketed
with touchscreen console
200 L plastic drum SH30959.03
Drum dolly SH30958.01
™
Nalgene
Nalgene cylindrical
5 gal tank
1.5 L funnel SH3B14865.01
PowderFill or funnel stand 129752
HQ incubator shaker 11-676-235
Seed BPC
(3 L working volume)
Seed BPC clip 122554
0.5, 1, 2, 5, 10, and 50 L Labtainer
BioProcess Container (BPCs)
Powdertainer BPCs SH30737.01 and SH30737.02
HyPerforma
Prima
Bios 16 Sorvall
Bioprocessing Centrifuge
CentriPAK BPC Adapter
2 L bucket liner
CentriPAK BPC 6 x
1.7 L harvest manifold
CentriPAK BPC Single with
Quick connect
polyethylene 5 gal tank liner 11100-0005
™
G3 Controllers NA
™
BT o-gas analyzer NC1256292
SUM0100.9002
43050-0005
SH3B9830.01
SH30712.01-.02 and
SH30963.01-.03
2 x L85007685
4 x 75003873
2 x 75003880
14 x 75003891
Table 2. 30 L and 300 L S.U.F. operating conditions.
Parameter 30 L 300 L
Initial volume 24 L 240 L
Final volume ~30 L ~300 L
Temperature 37°C 37°C
pH 7.0 ± 0.05 7.0 ± 0.05
Agitation
300–600 RPM 200–375 RPM
DO setpoint 30% 30%
DO cascade Cascade
RPM, air, then
supplement
Cascade RPM, air,
then supplement
oxygen
oxygen
Gas flow 3–60 standard
30–500 slpm
liter per min
(slpm)
Antifoam 3 mL, more as
foam detected
30 mL initially, more
as foam detected

Results
The standard procedure for expression in E. coli model
was used for technical transfer to the S.U.F. The culture
conditions in the 300 L S.U.F. are seen in Figure 1, showing
feasibility of plasmid production in the 300 L S.U.F. as per
the customer’s standard procedure. The customer stopped
the feed in 300 L S.U.F. to be able to harvest right away,
where in the 30 L the feed ran out hence the 30 L reached
a higher density.
100
80
60
in sparge, DO%
2
40
% O
20
0
0 105 15
Time (hr)
DO% O2% RPM OD
Figure 1. Data from 300 L S.U.F. (n = 1) after one trial scale-up
following customer’s procedure. The process in the HyPerforma S.U.F.
reached an OD of 147 by 19 hr. Samples showed a wet cell weight (WCW )
of 167 g/L was achieved.
400
350
300
250
200
150
100
50
0
600
The power-to-volume inputs was calculated for reproducing
the conditions from a 300 L S.U.F. to the customer’s 1 L
benchtop glass fermentors. The same original procedure
was then followed, but using the scaled-down power-tovolume input, kLa, and gassing rates. Culture conditions
of one of the two scale-down 1 L fermentors are shown in
Figure 2. The procedure was then scaled to the 30 L S.U.F.
(Figure 3).
100
80
600
60
40
in sparge, DO%
RPM and OD
2
% O
20
0
0 5 10 15
DO% O2% RPM OD
Figure 3. Data from 30 L S.U.F. (n = 1)—second scale-up following
customer’s procedure. In the 30 L S.U.F., an OD of 170 was reached in
our oine measurements. The WCW was 221 g/L.
30 L S.U.F.
Time (hr)
600
500
400
300
200
100
0
600
100
90
80
70
60
50
40
2
30
20
10
0
0 5 10 15 20
1 L glass bioreactor
DO% O2% RPM OD
Time (hr)
Figure 2. Data from 1 L glass vessel (n = 1) used as a working-volume
model for the scale-up procedure. The WCW was 170 g/L for
the final samples, same as that achieved in the 300 L S.U.F.
Find out more at thermofisher.com/suf
1,000
800
600
400
200
0
600
Conclusion
The HyPerforma 300 L S.U.F. exceeded the customer’s
expectations and reached a WCW of 167 g/L before
feed was stopped. It was determined that the 300 L and
30 L S.U.F.s are adequate for production following the
procedures for most of the customer’s strains.
Authors
1. Jason Brown, Process Development Engineer, Research and Development,
Thermo Fisher Scientific
2. Nephi Jones, Senior Manager, Research and Development, Thermo Fisher Scientific
For Research Use or Further Manufacturing. Not for diagnostic use or direct administration into humans or animals.
© 2020-2021 Thermo Fisher Scientific Inc. All right s reserved. All trademark s are the propert y of Thermo Fisher S cientific and its
subsidiaries unless otherwise speci fied. DeltaV is a trademark of Emerson. COL011281 0121