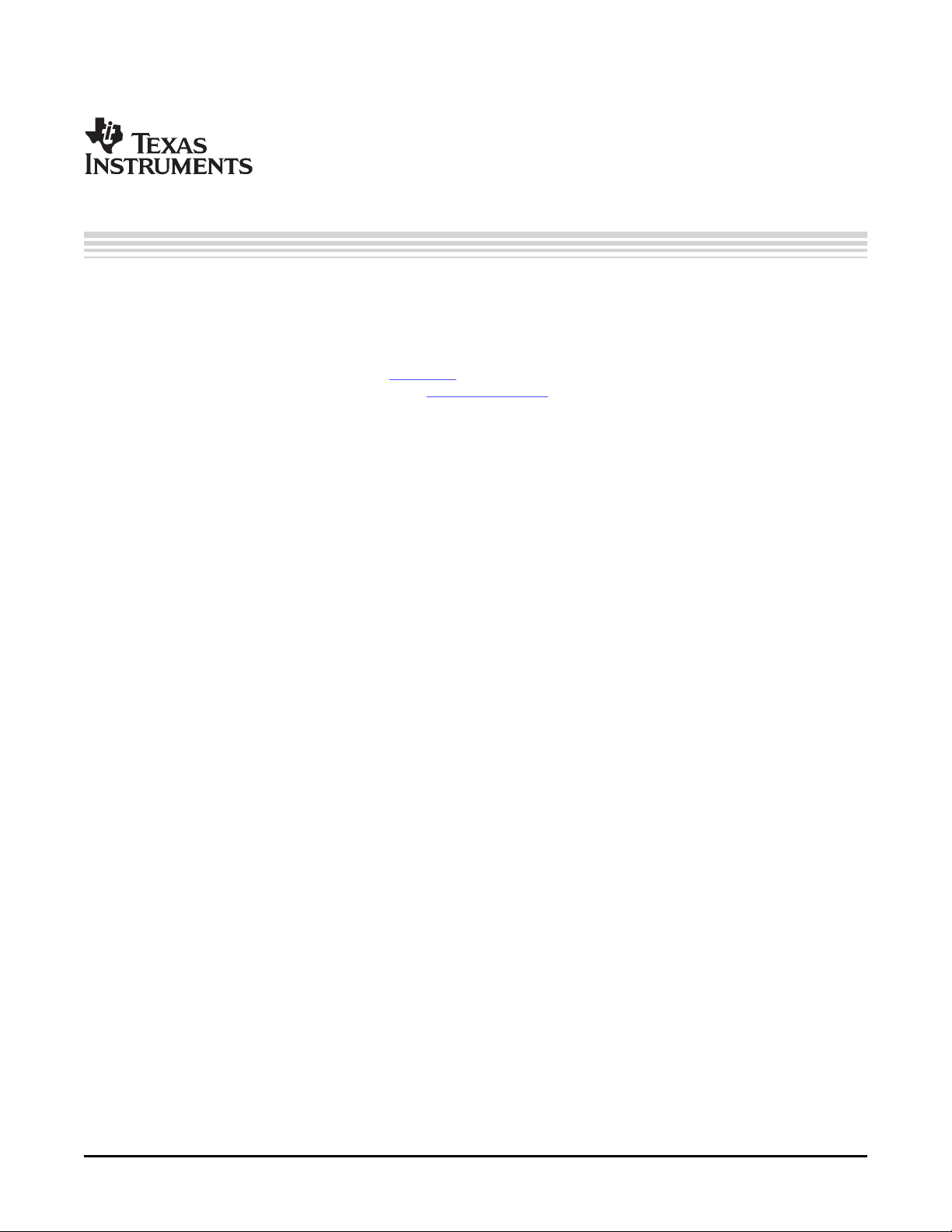
User's Guide
SLAU204 – December 2006
DAC8555EVM User's Guide
This user’s guide describes the characteristics, operation and use of the DAC8555
Evaluation Module (EVM). It covers all matters related to proper use and configuration
of this EVM along with the devices that it supports. The physical printed circuit board
(PCB) layout, schematic diagram and circuit descriptions are also included. For a more
detailed description of the DAC8555 , see the product data sheet available from the
Texas Instruments web site at http://www.ti.com. Additional support documents are
listed in the section of this guide entitled Related Documentation from Texas
Instruments. Throughout this document, the acronym EVM and the phrases evaluation
module and demonstration board are synonymous with the DAC8555EVM.
TMS320C5000, TMS320C6000 are trademarks of Texas Instruments.
LabVIEW is a trademark of National Instruments.
SLAU204 – December 2006 DAC8555EVM User's Guide 1
Submit Documentation Feedback
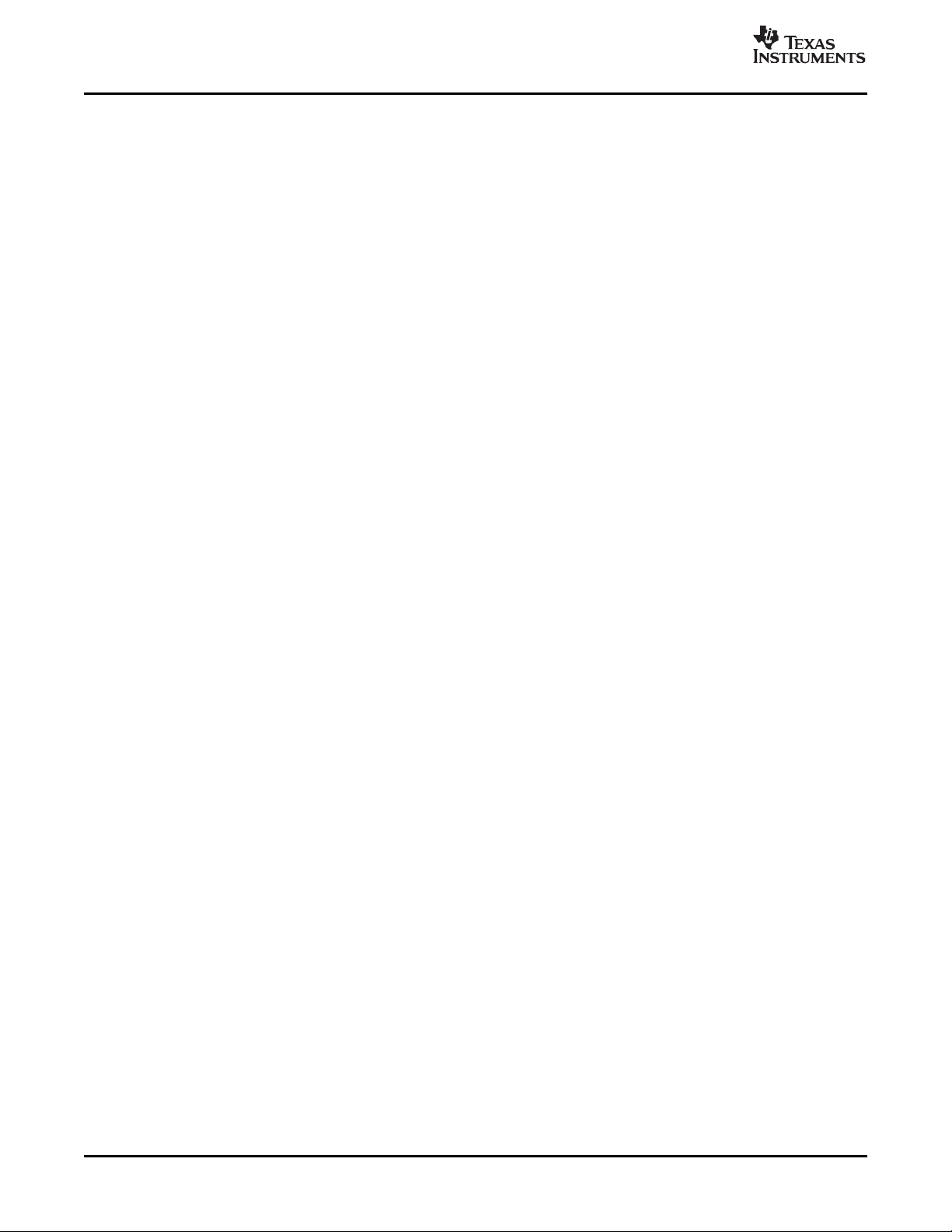
Contents
1 Overview ............................................................................................. 3
2 PCB Design and Performance .................................................................... 6
3 EVM Operation .................................................................................... 16
4 Schematic .......................................................................................... 22
List of Figures
1 DAC8555EVM Functional Block Diagram ....................................................... 5
2 DAC8555EVM PCB—Top Silkscreen Image ................................................... 7
3 DAC8555EVM PCB—Layer 1 (Top Signal Layer) ............................................. 7
4 DAC8555EVM PCB—Layer 2 (Ground Plane) ................................................. 8
5 DAC8555EVM PCB—Layer 3 (Power Plane) .................................................. 8
6 DAC8555EVM PCB—Layer 4 (Bottom Signal Layer) ......................................... 9
7 DAC8555EVM PCB—Bottom Silkscreen Image ............................................... 9
8 DAC8555EVM—Drill Drawing ................................................................... 10
9 INL and DNL Characterization Graph of DAC A .............................................. 11
10 INL and DNL Characterization Graph of DAC B .............................................. 12
11 INL and DNL Characterization Graph of DAC C .............................................. 13
12 INL and DNL Characterization Graph of DAC D .............................................. 14
List of Tables
1 DAC8555EVM Parts List ......................................................................... 15
2 Factory Default Jumper Settings ................................................................ 16
3 DAC Output Channel Mapping .................................................................. 17
4 Unity Gain Output Jumper Settings ............................................................. 18
5 Output Gain of 2 Jumper Settings .............................................................. 18
6 Capacitive Load Drive Output Jumper Settings ............................................... 19
7 Jumper Settings and Functions ................................................................. 19
2 DAC8555EVM User's Guide SLAU204 – December 2006
Submit Documentation Feedback
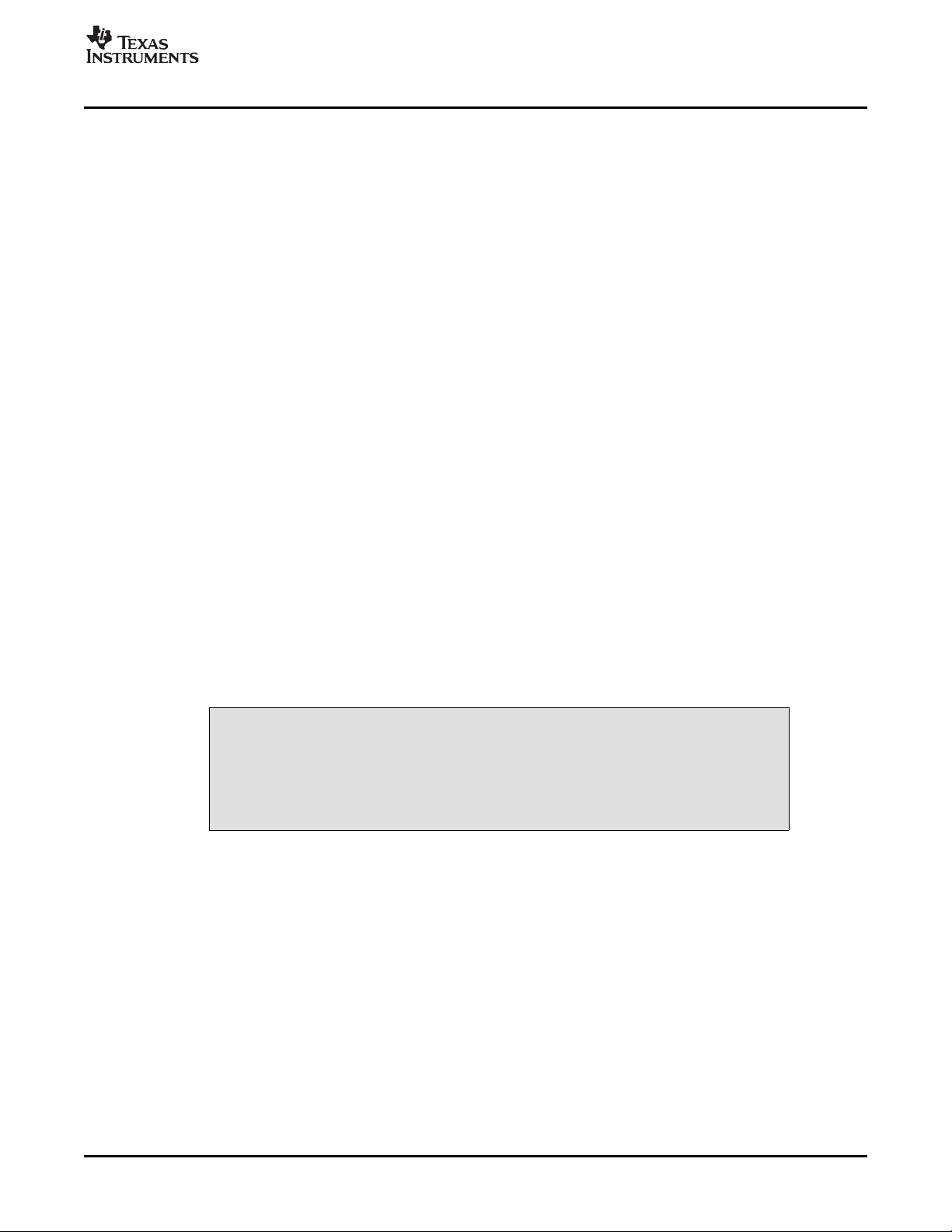
1 Overview
This section gives a general overview of the DAC8555EVM and describes some of the factors that must
be considered when using this demonstration board.
1.1 Features
The DAC8555EVM is a simple evaluation module designed for a quick and easy way to evaluate the
functionality and performance of the high-resolution, quad-channel, serial input DAC8555 digital-to-analog
converter (DAC). This EVM features a serial interface to communicate with any host microprocessor or TI
DSP-based system.
1.2 Power Requirements
This subsection describes the power requirements for this device.
1.2.1 Supply Voltage
The DC power supply requirement for the digital section (V
the J5-1 terminal or via the J3-10 terminal (when plugged in with another EVM board or interface card)
and is referenced to ground through the J5-2 and J3-5 terminals. The DC power supply requirements for
the analog section of this EVM are: V
through J1-3 and J1-1 respectively, or through terminals J3-1 and J3-2. The +5V
terminals J5-3 or J3-3, and the +3.3V
are referenced to analog ground through terminals J1-2 and J3-6.
The analog power supply for the device under test, U1, can be powered by either +5V
selecting the proper position of jumper JMP7. This configuration allows the DAC8555 analog section to
operate from either supply power while the I/O and digital section are powered by +5V, V
The V
reference chip, U3 and the reference buffer, U4. The negative rail of the output op amp, U2, can be
selected between V
provide output signal conditioning or to boost capacitive load drive, or for other desired output mode
requirements.
) of this EVM is typically +5V connected to
DD
and V
CC
connects through terminal J3-8. All of the analog power supplies
A
supply source is primarily used to provide the positive rail of the external output op amp, U2, the
CC
and AGND via jumper JMP10. The external op amp is installed as an option to
SS
range from +15.75V to –15.75V (maximum), connecting
SS
connects through
A
or +3.3V
A
DD
Overview
by
A
.
CAUTION
To avoid potential damage to the EVM board, be sure that the correct cables
are connected to their respective terminals as labeled on the EVM board.
Stresses above the maximum listed voltage ratings may cause permanent
damage to the device.
1.2.2 Reference Voltage
The +5V precision voltage reference is provided to supply the external voltage reference for the DAC
through the REF02 (U3) via jumper JMP8, by shorting pins 1 and 2. The reference voltage goes through
an adjustable 100k Ω potentiometer, R15, in series with 20k Ω , R16, to allow the user to adjust the
reference voltage to its desired settings. The voltage reference is then buffered through U4A as seen by
the device under test. The test points TP2, TP3 and TP4 are also provided, as well as J4-18 and J4-20, in
order to allow the user to connect another external reference source if the onboard reference circuit is not
desired. The external voltage reference should not exceed +5V DC.
The REF02 precision reference is powered by V
SLAU204 – December 2006 DAC8555EVM User's Guide 3
Submit Documentation Feedback
(+15V) through either terminal J1-3 or J3-1.
CC
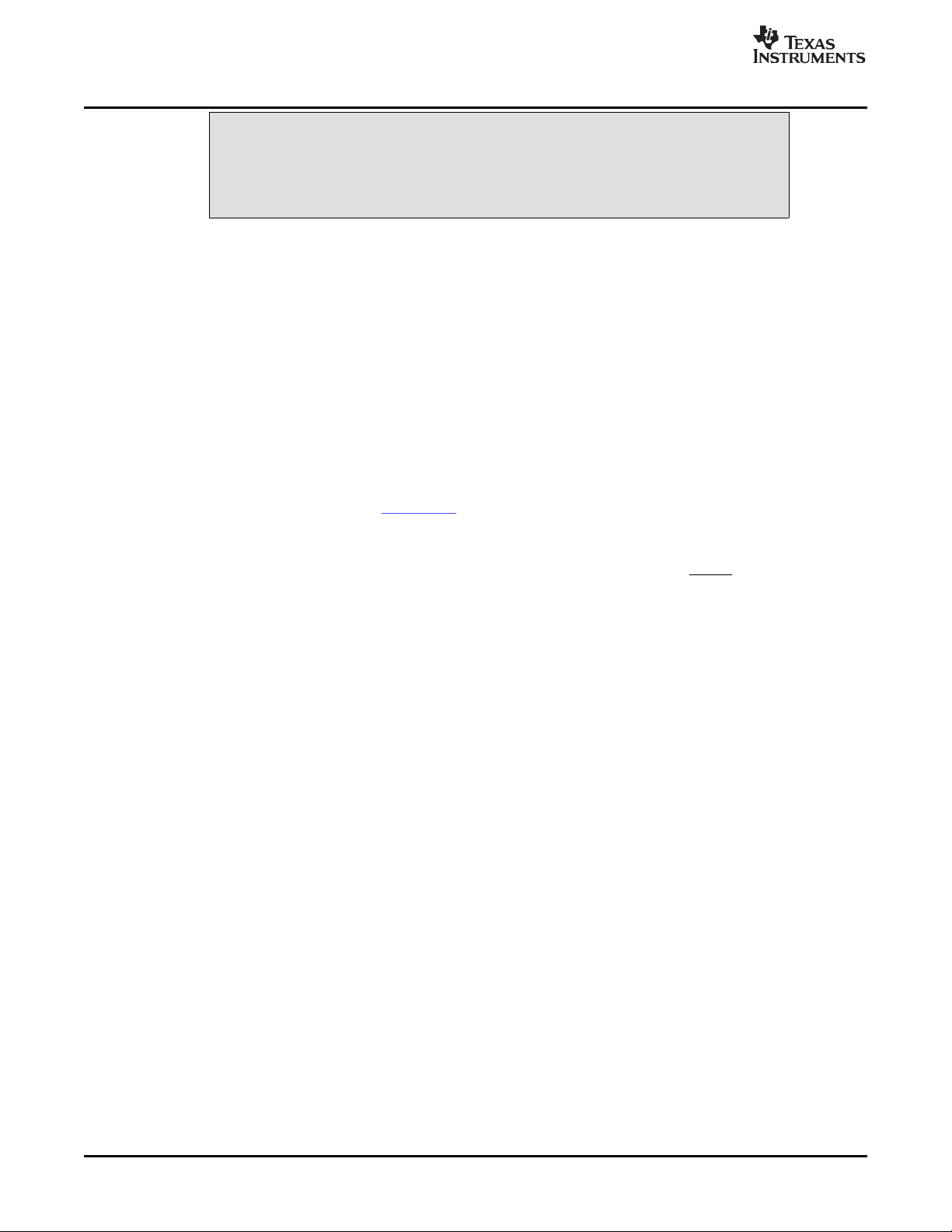
Overview
1.3 EVM Basic Functions
CAUTION
When applying an external voltage reference through TP2 or J4-20, make sure
that it does not exceed +5V maximum. External voltage references in excess of
+5V can permanently damage the DAC8555 being tested (U1).
The DAC8555EVM is designed to provide a demonstration platform for testing certain operational
characteristics of the DAC8555 digital-to-analog converter. Functional evaluation of the DAC8555 can be
accomplished with the use of any microprocessor, TI DSP or some sort of waveform generator.
Headers J2A (top side) and J2B (bottom side) are pass-through connectors provided to interface a host
processor or waveform generator with the DAC8555EVM using a custom-built cable. These connectors
enable the control signals and data to pass between the host and the device.
A mating adapter interface card (5-6k adapter interface) is also available to fit with TI’s TMS320C5000™
and TMS320C6000™ DSP Starter Kits (DSKs). This card resolves most of the trouble involved with
building a custom cable. Additionally, there is also an MSP430-based platform (HPA449) that uses the
MSP430F449 microprocessor, to which this EVM can connect and interface as well. For more details or
information regarding the 5-6k adapter interface card or the HPA449 platform, please contact your Texas
Instruments representative, visit the TI web site or email the Data Converter Applications Support Team at
dataconvapps@list.ti.com.
The DAC outputs can be monitored through the selected pins of the J4 header connector. All outputs can
be switched through their respective jumpers—JMP11, JMP12, JMP13 and JMP14—for the purpose of
stacking. Stacking allows a total of eight DAC channels to be used, provided the SYNC signals are unique
for each EVM board stacked.
In addition, the option of selecting one DAC output that can be fed to the noninverting side of the output
op amp, U2, is also possible by using a jumper across the selected pins of J4. The output op amp (U2)
must first be correctly configured for the desired waveform characteristic. For more information, refer to
Section 3 of this user’s guide.
A block diagram of the EVM is shown in Figure 1 .
4 DAC8555EVM User's Guide SLAU204 – December 2006
Submit Documentation Feedback
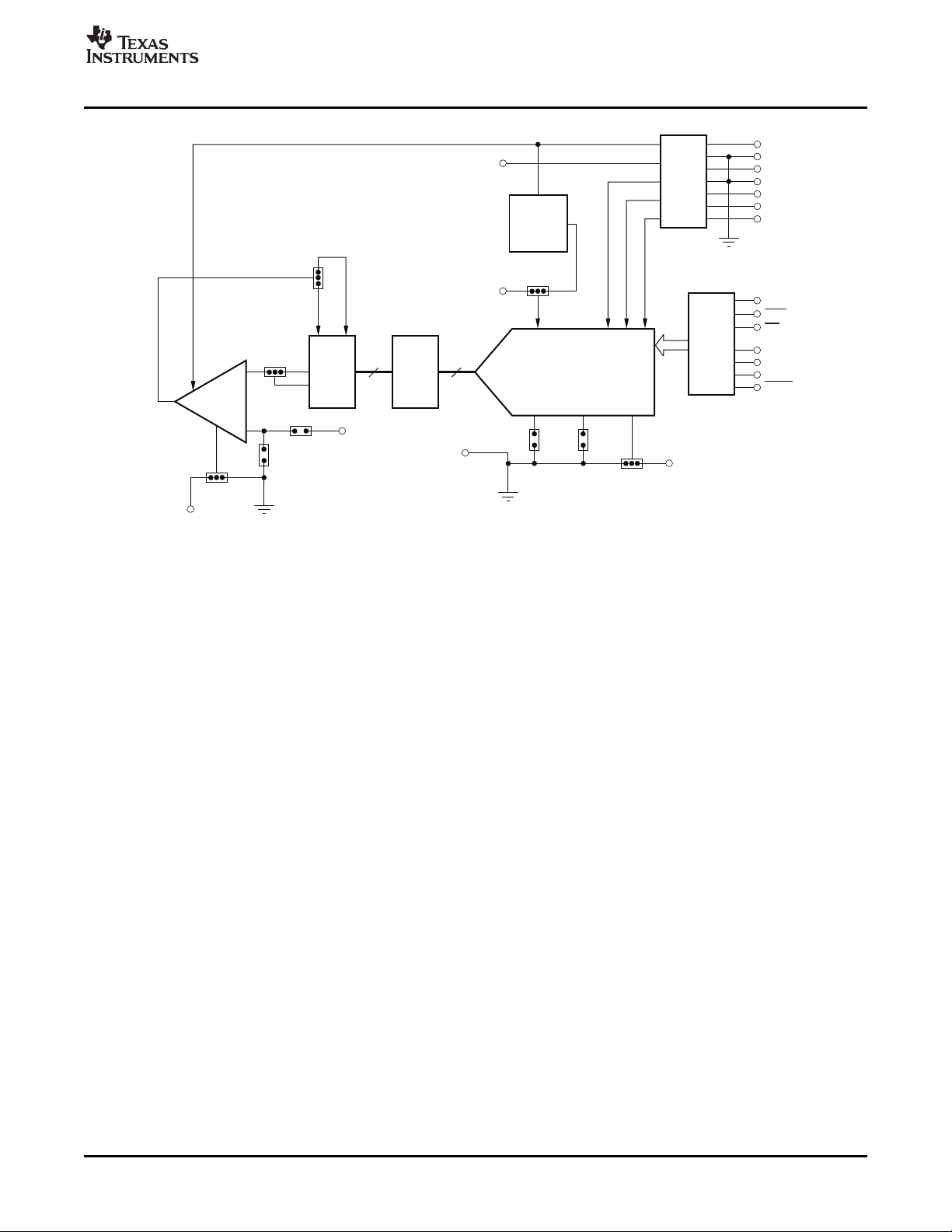
JMP11
JMP12
JMP13
JMP14
External
Reference
Module
+5V
A
V
DD
+3.3V
A
(J2A)
(J2B)
DACModule
(J4A)
(J4B)
8CH
(J1)
(J5)
(J3A)
(J3B)
4CH
JMP15
JMP16
JMP9
JMP10
DACOut
V
SS
V H
REF
TP4
TP3
V
CC
GND
V
SS
GND
V
DD
+5V
A
+3.3V
A
DIN
LDAC
SCLK
SYNC
JMP5
JMP6
JMP4 JMP3
JMP8
V H
REF
TP2
V
SS
V
CC
V L
REF
Output
Buffer
Module
RST RSTSEL
RSTSEL
EN
RST
Overview
Figure 1. DAC8555EVM Functional Block Diagram
SLAU204 – December 2006 DAC8555EVM User's Guide 5
Submit Documentation Feedback
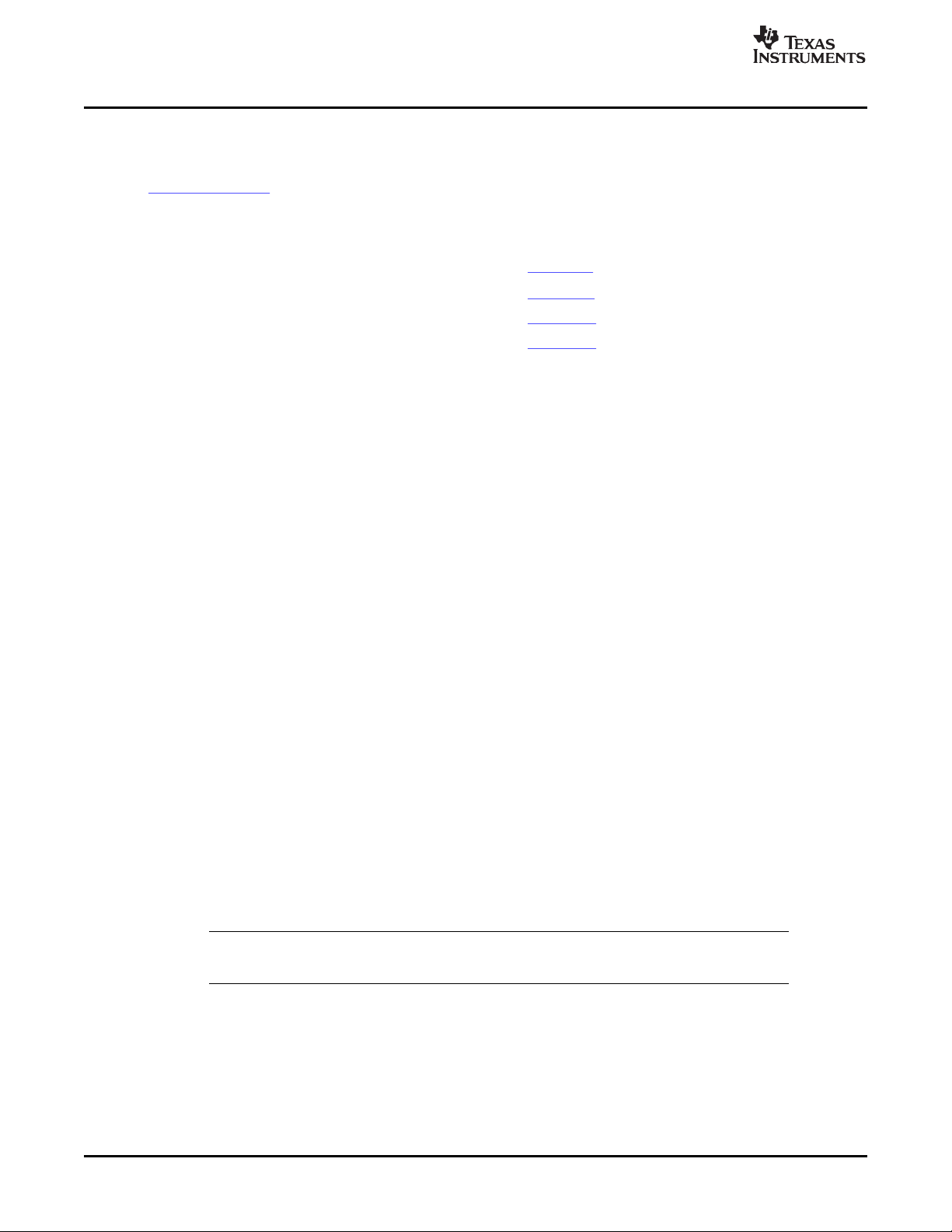
PCB Design and Performance
1.3.1 Related Documentation from Texas Instruments
The following documents provide information regarding Texas Instrument integrated circuits used in the
assembly of the DAC8555EVM. The latest revisions of these documents are available from the TI web site
at http://www.ti.com.
Data Sheet Literature Number
DAC8555 SLAS475
REF02 SBVS003
OPA627 SBOS165
OPA2132 SBOS054
2 PCB Design and Performance
This section discusses the layout design of the DAC8555EVM PCB, describing the physical and
mechanical characteristics of the EVM as well as a brief description of the demonstration board test
performance procedures performed. The list of components used in this evaluation module is also
included.
2.1 PCB Layout
The DAC8555EVM is designed to preserve the performance quality of the DAC8555, the device under
test (DUT), as specified in the data sheet. In order to take full advantage of the EVM capabilities, use care
during the schematic design phase to properly select the right components and to build the circuit
correctly. The circuit design should include adequate bypassing, identifying and managing the analog and
digital signals, and understanding the components' electrical and mechanical attributes.
The primary design concerns during the layout process are optimal component placement and proper
signal routing. Place the bypass capacitors as close as possible to the device pins, and properly separate
the analog and digital signals from each other. In the layout process, carefully consider the placement of
the power and ground planes. A solid plane is ideal, but because of its greater cost, a split plane can
sometimes be used satisfactorily. When considering a split plane design, analyze the component
placement and carefully split the board into its analog and digital sections starting from the DUT. The
ground plane plays an important role in controlling the noise and other effects that otherwise contribute to
the error of the DAC output. To ensure that the return currents are handled properly, route the appropriate
signals only in their respective sections, meaning that the analog traces should only lay directly above or
below the analog section and the digital traces in the digital section. Minimize trace length, but use the
largest possible trace width allowable within the design. These design practices are illustrated in Figure 2
through Figure 8 .
The DAC8555EVM board is constructed on a four-layer PCB using a copper-clad FR-4 laminate material.
The PCB has a dimension of 43,1800mm (1.7000in) by 82,5500mm (3.2500in), and the board thickness is
1,5748mm (0.062in). Figure 3 through Figure 7 show the individual artwork layers.
Note: Board layouts are not to scale. These are intended to show how the board is laid out; they
are not intended to be used for manufacturing DAC8555EVM PCBs.
6 DAC8555EVM User's Guide SLAU204 – December 2006
Submit Documentation Feedback
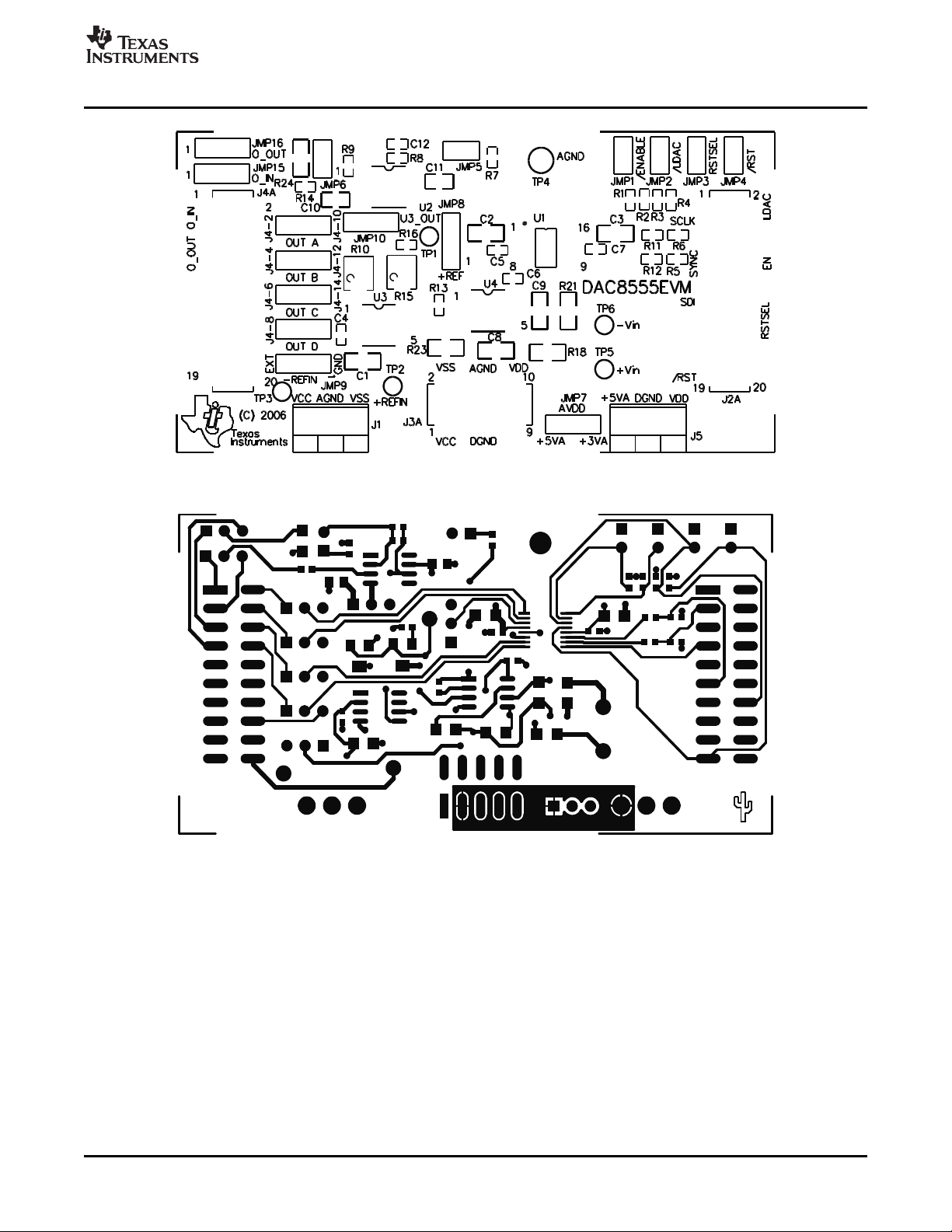
Figure 2. DAC8555EVM PCB—Top Silkscreen Image
PCB Design and Performance
Figure 3. DAC8555EVM PCB—Layer 1 (Top Signal Layer)
SLAU204 – December 2006 DAC8555EVM User's Guide 7
Submit Documentation Feedback
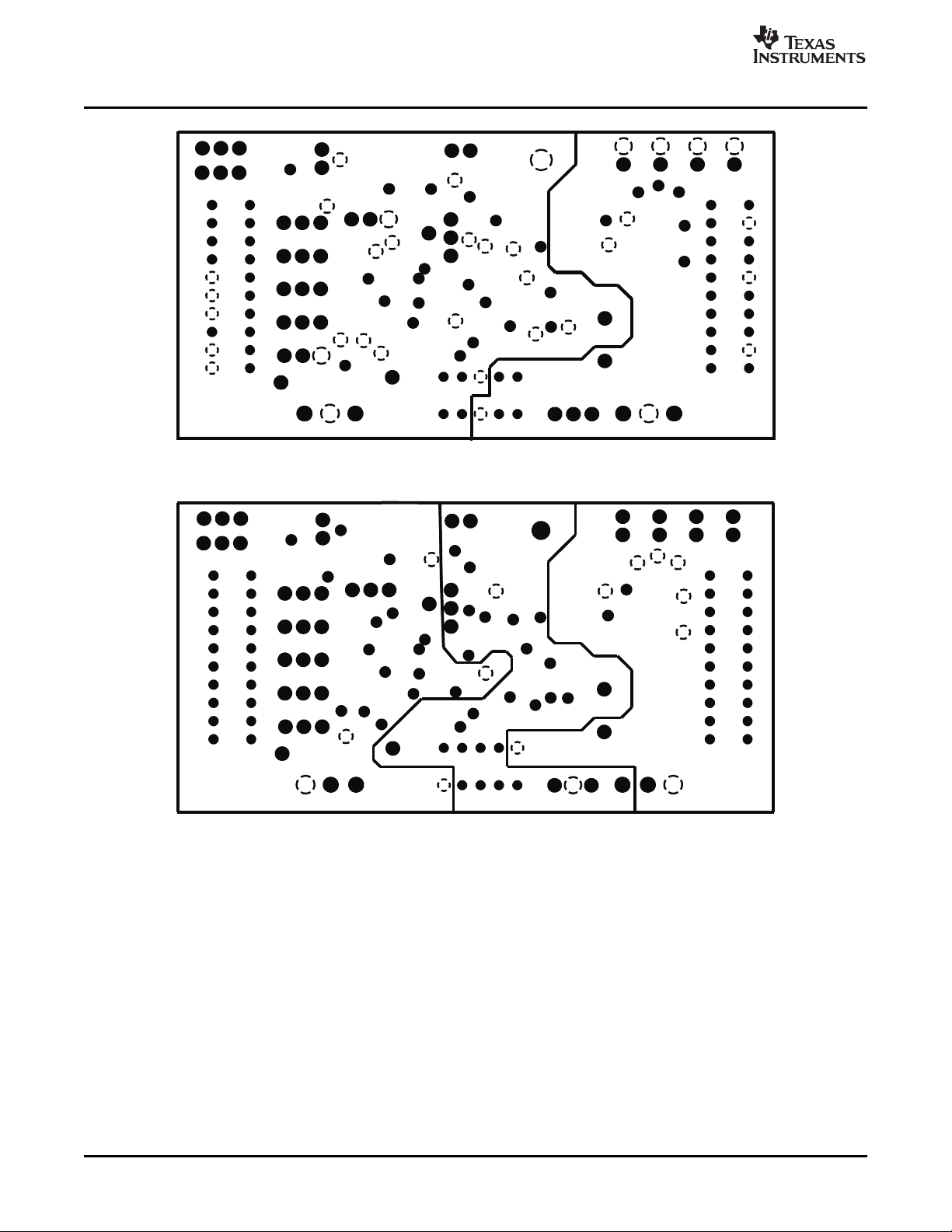
PCB Design and Performance
Figure 4. DAC8555EVM PCB—Layer 2 (Ground Plane)
Figure 5. DAC8555EVM PCB—Layer 3 (Power Plane)
8 DAC8555EVM User's Guide SLAU204 – December 2006
Submit Documentation Feedback

Figure 6. DAC8555EVM PCB—Layer 4 (Bottom Signal Layer)
PCB Design and Performance
Figure 7. DAC8555EVM PCB—Bottom Silkscreen Image
SLAU204 – December 2006 DAC8555EVM User's Guide 9
Submit Documentation Feedback

PCB Design and Performance
2.2 EVM Performance
Figure 8. DAC8555EVM—Drill Drawing
The EVM performance test is executed using a high-density DAC bench test board, an Agilent 3458A
digital multimeter and a PC running LabVIEW™ software. The EVM board is tested for linearity for all
codes between 485 and 64741. The DUT is then allowed to settle for 1ms before the meter is read. This
process is repeated for all codes to generate the measurements for INL and DNL.
Results of the DAC8555EVM tests are shown in Figure 9 through Figure 12 .
10 DAC8555EVM User's Guide SLAU204 – December 2006
Submit Documentation Feedback
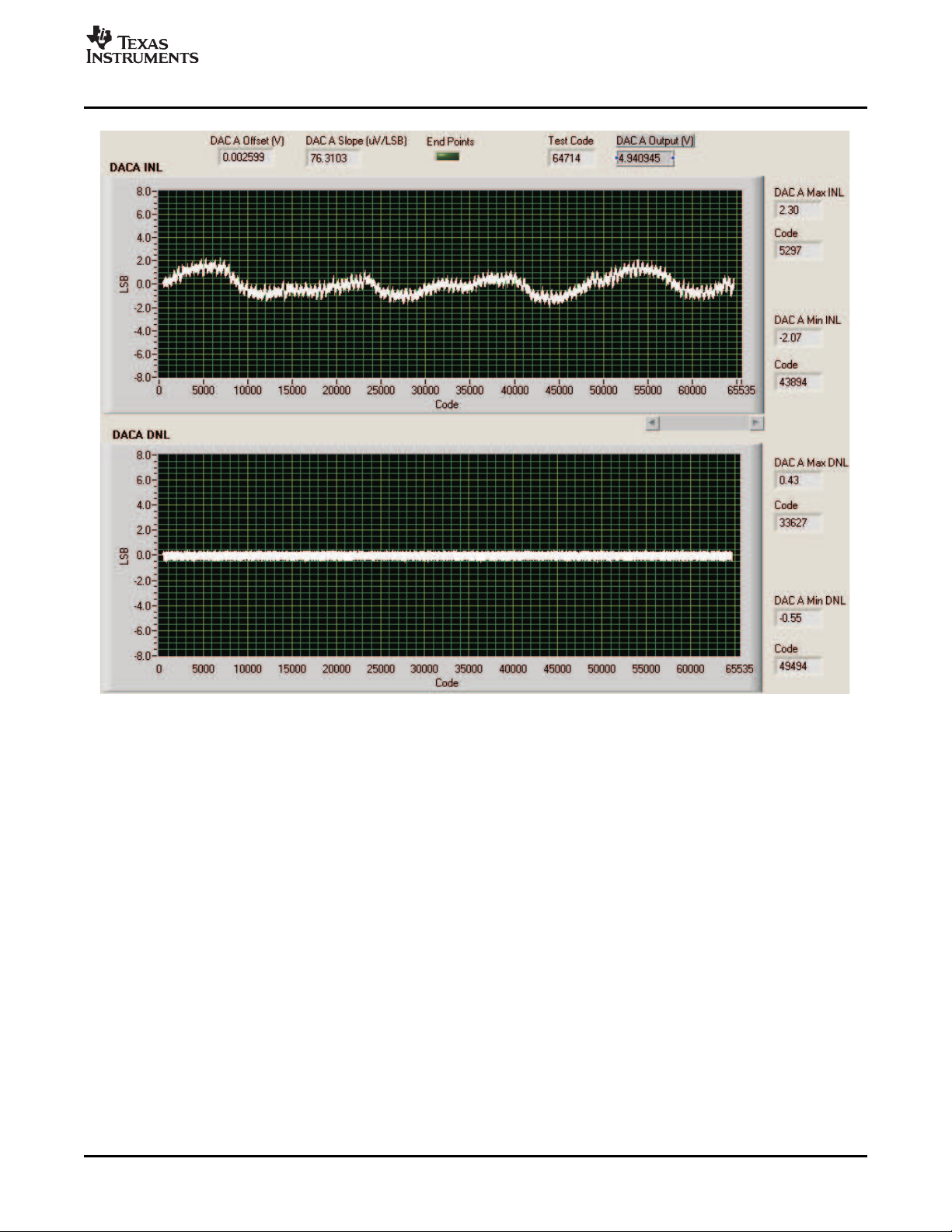
PCB Design and Performance
Figure 9. INL and DNL Characterization Graph of DAC A
SLAU204 – December 2006 DAC8555EVM User's Guide 11
Submit Documentation Feedback

PCB Design and Performance
Figure 10. INL and DNL Characterization Graph of DAC B
12 DAC8555EVM User's Guide SLAU204 – December 2006
Submit Documentation Feedback

PCB Design and Performance
Figure 11. INL and DNL Characterization Graph of DAC C
SLAU204 – December 2006 DAC8555EVM User's Guide 13
Submit Documentation Feedback

PCB Design and Performance
Figure 12. INL and DNL Characterization Graph of DAC D
DAC8555EVM User's Guide14 SLAU204 – December 2006
Submit Documentation Feedback

2.3 Bill of Materials
PCB Design and Performance
The parts list, showing the components used in the assembly of the DAC8555EVM, is given in Table 1 .
Table 1. DAC8555EVM Parts List
QTY
ITEM BOARD Ref Des MFR PART NUMBER DESCRIPTION
1 4 R11–R14 Panasonic ERJ-3GEY0R00V Chip Resistor, 0 Ω , 1/10W, 0603
2 1 R24 Panasonic ERJ-8GEYJ101V Chip Resistor, 100 Ω , 1/4W, 1206
Not
Installed
3 7 Panasonic ERJ-3EKF1002V Chip Resistor, 10k Ω , 1/16W, 0603
4 1 R16 Panasonic ERJ-3EKF2002V Chip Resistor, 20k Ω , 1/16W, 0603
5 1 R10 Bourns 3214W-1-203E Series 5T Pot., 20k Ω , BOURNS_32X4W
6 1 R15 Bourns 3214W-1-104E Series 5T Pot., 100k Ω , BOURNS_32X4W
Not
Installed
7 1 C12 TDK C1608C0G1H102J Multilayer Ceramic Capacitor, 1nF, 0603 C0G
8 4 C4–C7 TDK C1608X7R1E104K Multilayer Ceramic Capacitor, 0.1 µ F, 0603 X7R
9 2 C10, C11 TDK C2012X7R1E105K Multilayer Ceramic Capacitor, 1 µ F, 0805 X7R
10 3 C1, C2, C3 TDK C3216X7R1C106M Multilayer Ceramic Capacitor, 10 µ F, 1206 X7R
Not
Installed
11 1 U1 Texas Instruments DAC8555IPW
12 1 U2 Texas Instruments OPA627AU 8-SOP(D) Precision Op Amp
13 1 U3 Texas Instruments REF02AU +5V, 8-SOP(D) Precision Voltage Reference
14 1 U4 Texas Instruments OPA2132UA 8-SOP(D) Dual Precision Op Amp
Not
Installed
15 2 J2A, J4A Samtec TSM-110-01-L-DV-P
16 1 J3A Samtec TSM-105-01-L-DV-P
17 2 J2B, J4B Samtec SSW-110-22-F-D-VS-K
18 1 J3B Samtec SSW-105-22-F-D-VS-K
19 6 JMP1–JMP6 Samtec TSW-102-07-G-S 2-position Jumper_ .1in spacing
20 10 JMP7–JMP16 Samtec TSW-103-07-G-S 3-position Jumper_ .1in spacing
21 1 TP4 Keystone Electronics 5011 Testpoint, Large-Loop
Not TP1, TP2, TP3,
Installed TP5, TP6
22 16 N/A Samtec SNT-100-BK-G-H Shorting Block
PER MFR
2 R5, R6 Panasonic ERJ-3GEYJ302V Chip Resistor, 3k Ω , 1/10W, 0603
R1–R4, R7, R8,
R9
7 R17–R23 Panasonic Chip Resistor, 1/4W 1206
2 C8, C9 TDK Multilayer Ceramic Capacitor, 1206
16-bit, Quad Voltage Output, Serial Input DAC,
TSSOP-16
2 J1, J5 On-Shore Technology ED555/3DS 3-Pin Terminal Connector
SMT Header, 10x2x0.1, 20-pin, .025in
SMT Header, 5x2x0.1, 10-pin, .025in
SMT Socket, 10x2x0.1, 20-pin, .025in
SMT Socket, 5x2x0.1, 10-pin, .025in
5 Keystone Electronics 5000 Testpoint, Mini-Loop
2
2
2
2
SLAU204 – December 2006 DAC8555EVM User's Guide 15
Submit Documentation Feedback

EVM Operation
3 EVM Operation
3.1 Default Settings
This section covers the operation of the EVM in detail, in order to provide guidance to the user in
evaluating the onboard DAC as well as how to interface the EVM to a specific host processor. Refer to the
DAC8555 datasheet for information about its serial interface and other related topics. The EVM board is
factory-tested and configured.
The EVM is set to its factory default configuration as described in Table 2 to operate in 5V mode.
Table 2. Factory Default Jumper Settings
Reference Jumper Position Function
JMP1 CLOSE ENABLE pin is tied to DGND
JMP2 CLOSE LDAC pin is tied to DGND. Software LDAC is used.
JMP3 CLOSE RSTSEL pin is tied to DGND.
JMP4 OPEN RST pin is tied to VDD.
V
H is not routed to the inverting input of the op amp for voltage offset with gain of 2
JMP5 OPEN
JMP6 OPEN Output op amp U2 is not configured for a gain of 2.
JMP7 1-2 Analog supply for the DAC8555 is +5V
JPM8 1-2 Onboard external buffered reference U3 is routed to V
JMP9 1-2 V
JMP10 1-2 Negative supply rail of U2 op amp is supplied with VSS.
JMP11 1-2 DAC output A (V
JMP12 1-2 DAC output B (V
JMP13 1-2 DAC output C (V
JMP14 1-2 DAC output D (V
JMP15 1-2 J4-1 is connected to the noninverting input of the output op amp U2.
JMP16 1-2 J4-5 is connected to the output of the op amp U2.
REF
output.
.
A
H.
REF
L is tied to AGND.
REF
A) is routed to J4-2.
OUT
B) is routed to J4-4.
OUT
C) is routed to J4-6.
OUT
D) is routed to J4-8.
OUT
3.2 Host Processor Interface
The host processor drives the DAC. Thus, proper DAC operation depends on a successful configuration
between the host processor and the EVM board. In addition, properly written code is also required to
operate the DAC.
As discussed earlier, a custom cable can be made specific to the host interface platform. The EVM allows
interface to the host processor through header connector J2 for the serial control signals and the serial
data input. The output can be monitored through header connector J4.
An interface adapter card is also available for specific TI DSP DSKs as well as an MSP430-based
microprocessor (see Section 1.3 of this manual). Using the interface card alleviates the tedious task of
building customized cables and allows easy configuration of a simple evaluation system.
The DAC8555 interfaces with any host processor capable of handling SPI protocols or the popular TI
DSPs. For more information regarding the DAC8555 data interface, please refer to the DAC8555
datasheet .
3.3 EVM Stacking
Stacking multiple EVMS is possible if there is a need to evaluate two DAC8555s, yielding a total of eight
output channels. A maximum of two EVMs can be stacked since the output terminal, J4, dictates the
number of DAC channels that can be connected without colliding. Table 3 shows how the DAC output
channels are mapped into the output terminal, J4, with respect to the jumper positions of JMP11, JMP12,
JMP13, and JMP14.
DAC8555EVM User's Guide16 SLAU204 – December 2006
Submit Documentation Feedback

EVM Operation
Table 3. DAC Output Channel Mapping
Reference Jumper Position Function
JMP11
JMP12
JMP13
JMP14
1-2 DAC output A (V
2-3 DAC output A (V
1-2 DAC output B (V
2-3 DAC output B (V
1-2 DAC output C (V
2-3 DAC output C (V
1-2 DAC output D (V
2-3 DAC output D (V
A) is routed to J4-2.
OUT
A) is routed to J4-10.
OUT
B) is routed to J4-4.
OUT
B) is routed to J4-12.
OUT
C) is routed to J4-6.
OUT
C) is routed to J4-14.
OUT
D) is routed to J4-8.
OUT
D) is routed to J4-16.
OUT
In order to allow exclusive control of each EVM, different SYNC signals must be selected for each
DAC8555. This difference is not easily accomplished as it involves hardware alterations. The EVM board
that sits on the bottom of the stack can use the SYNC signal coming from J2B-7. The pin of J2A-7 can be
cut so that the SYNC signal coming from the bottom EVM board in the stack does not pass through. The
EVM board that sits on top can use the CNTL signal coming from J2-1. The signal of J2-1 must be
jumpered across to J2-7 of the EVM board that sits on the top of the stack. The LDAC, SYNC and
ENABLE control signals are shared. The DAC8555 only responds when the correct SYNC signal is
generated.
The raw outputs of the DAC can be probed through the even numbered pins of J4, the output terminal,
which also provides mechanical stability when stacking or plugging into any interface card. In addition, it
provides easy access for monitoring up to eight DAC channels when stacking two EVMs together.
3.4 Output Op Amp
The DAC8555EVM includes an optional signal conditioning circuit for the DAC output through an external
operational amplifier, U2. The output op amp is set to unity gain configuration by default. Only one DAC
output channel can be monitored at any given time. JMP15 selects which pin of J4 is the input. Either J4-1
or J4-3 can be used as the op amp signal input. The default setting for JMP15 selects J4-1. A shorting
jumper can be placed between one of the DAC outputs and the op amp input. For example, a jumper
across J4-1 and J4-2 places the DAC A output as the input for the op amp if board jumpers are in the
default position. If JMP15 is in the alternate position, then a shorting block between J4-3 and J4-2 makes
the DAC B output the input to the op amp.
The output of U2 passes through JMP16. In the default position, the output connects to J4-5. When
JMP16 is in the alternate position, the output from U2 connects to J4-7. The output can be monitored
from, or passed to, another device from the J4 connector.
The jumper arrangement of JMP15 and JMP16 connecting to J4 allows U2 to be used in the stacked
board arrangement discussed above in Section 3.3 .
The following subsections describe the different configurations of the output amplifier, U2.
SLAU204 – December 2006 DAC8555EVM User's Guide 17
Submit Documentation Feedback

EVM Operation
3.4.1 Unity Gain Output
The buffered output configuration can be used to prevent loading of the DAC8555, though it may add
some slight distortion because of the feedback resistor and capacitor. The feedback circuit can be altered
by simply desoldering R8 and C12 and replacing them with components of desired value. If desired, R8
and C12 can be removed altogether by replacing R8 with a 0 Ω resistor.
Table 4 shows the jumper setting for the unity gain configuration of the DAC external output buffer in
unipolar or bipolar mode.
Reference Unipolar Bipolar Function
JMP5 Open Open Disconnect V
JMP10 2-3 1-2 Supplies V
JMP6 Open Open Disconnect negative input of op amp from the gain resistor, R9.
3.4.2 Output Gain of 2
There are two types of configurations that will yield an output gain of 2, depending on the setup of jumpers
JMP5 and JMP6. These configurations allow the user to choose whether the DAC output will use V
as an offset. Table 5 shows the proper jumper settings of the EVM for the DAC8555 output gain of 2.
Table 4. Unity Gain Output Jumper Settings
Jumper Setting
H from the inverting input of the op amp.
REF
to the negative rail of the op amp or ties it to AGND.
SS
H
REF
Jumper Setting
Reference Unipolar Bipolar Function
Close Close
JMP5
Open Open
JMP10 2-3 1-2
Close Close
JMP6
Open Open
Table 5. Output Gain of 2 Jumper Settings
Inverting input of the output op amp U2 is connected to V
voltage with a gain of 2. JMP6 must be open.
V
H is disconnected from the inverting input of the output op amp U2. JMP6 must be
REF
closed.
Supplies power, VSS, to the negative rail of op amp U2 for bipolar mode, or ties it to
AGND for unipolar mode.
Configures op amp U2 for a gain of 2 output without a voltage offset. JMP5 must be
open.
Inverting input of op amp U2 is disconnected from the gain resistor, R9. JMP5 must be
closed.
H for use as its offset
REF
DAC8555EVM User's Guide18 SLAU204 – December 2006
Submit Documentation Feedback

3.4.3 Capacitive Load Drive
It may be required to drive a wide range of capacitive loads. However, under certain conditions, all op
amps may become unstable, depending on the op amp configuration, gain, and load value. These factors
are just few of the issues that can affect op amp stability and should be considered during implementation.
In unity gain configuration, the OPA627 op amp (U2) performs very well with very large capacitive loads.
Increasing the gain enhances amplifier ability to drive even more capacitance, and adding a load resistor
even improves the capacitive load drive capability.
Table 6 shows the jumper setting configuration for a capacitive load drive.
Table 6. Capacitive Load Drive Output Jumper Settings
Jumper Setting
Reference Unipolar Bipolar Function
JMP5 Open Open V
JMP10 2-3 1-2
JMP6 Open Open
H is disconnected from the inverting input of the output op amp U2.
REF
Supplies power, VSS, to the negative rail of op amp U2 for bipolar mode, or ties it to AGND
for unipolar mode.
Capacitive load drive output of DAC is routed to pin 2 of JMP6 and may be used as the
output terminal.
3.5 Optional Signal Conditioning Op-Amp (U4B)
One half of the OPA2132 dual package op amp (U4) is used for reference buffering (U4A), while the other
half is unused. This unused op amp (U4B) is left for whatever op amp circuit application the user desires
to implement. The 1206 footprint for the resistors and capacitors surrounding the U4B op amp are not
populated and are made available for easy configuration. Test points TP5 and TP6 are not installed, so it
is up to the user on how to connect the ( ± ) input signals to this op amp. No test point has been made
available for the output because of space restrictions, but a wire can be soldered to the output of the op
amp via an unused component pad that connects to it. The op amp circuit can be configured by populating
the corresponding components to those that match the circuit design while leaving all other unused
component footprints unpopulated.
EVM Operation
3.6 Jumper Settings
Table 7 shows the function of each specific jumper setting of the EVM.
Table 7. Jumper Settings and Functions
Reference Jumper Setting
JMP1
JMP2
JMP3
(1)
Indicates the corresponding pins that are shorted or closed.
(1)
Function
ENABLE pin is set high through pull-up resistor R1. ENABLE can be driven by GPIO2,
J2-8.
ENABLE pin is set low and DAC is enabled.
LDAC pin is set high through pull-up resistor R2. LDAC can be driven by GPIO0, J2-2.
LDAC pin is set low and DAC update is accomplished via software.
RSTSEL pin is set high through pull-up resistor R3. RSTSEL can be driven by GPIO4,
J2-14.
RSTSEL pin is set low.
SLAU204 – December 2006 DAC8555EVM User's Guide 19
Submit Documentation Feedback

EVM Operation
Table 7. Jumper Settings and Functions (continued)
Reference Jumper Setting
JMP4
(1)
Function
RST pin is set high through pull-up resistor R4. RST can be driven by GPIO5, J2-19.
RST pin is set low.
Disconnects V
H to the inverting input of the op amp U2.
REF
JMP5
Connects V
H to the inverting input of the op amp U2.
REF
Disconnects the inverting input of the op amp U2 from the gain resistor, R9.
JMP6
Connects the inverting input of the op amp U2 from the gain resistor, R9 for output gain of
2.
+5V analog supply is selected for AV
.
DD
JMP7
+3.3V analog supply is selected for AV
Routes the adjustable, buffered, onboard +5V reference to the V
DAC8555.
.
DD
H input of the
REF
JMP8
Routes the user-supplied reference from TP2 or J4-20 to the V
DAC8555.
V
L is tied to AGND.
REF
REF
H input of the
JMP9
Routes the user-supplied negative reference from TP3 or J4-18 to the V
DAC8555. This voltage should be within the range of 0V to V
H.
REF
REF
L input of the
Negative supply rail of the op amp U2 is powered by V
for bipolar operation.
SS
JMP10
Negative supply rail of the op amp U2 is tied to AGND for unipolar operation.
Routes V
A to J4-2.
OUT
JMP11
Routes V
A to J4-10.
OUT
20 DAC8555EVM User's Guide SLAU204 – December 2006
Submit Documentation Feedback

Reference Jumper Setting
Table 7. Jumper Settings and Functions (continued)
(1)
Function
EVM Operation
Routes V
B to J4-4.
OUT
JMP12
Routes V
Routes V
B to J4-12.
OUT
C to J4-6.
OUT
JMP13
Routes V
Routes V
C to J4-14.
OUT
D to J4-8.
OUT
JMP14
Routes V
D to J4-16.
OUT
Routes J4-1 to U2 noninverting input.
JMP15
Routes J4-3 to U2 noninverting input.
Routes U2 output to J4-5.
JMP16
Routes U2 output to J4-7.
SLAU204 – December 2006 DAC8555EVM User's Guide 21
Submit Documentation Feedback

Schematic
4 Schematic
22 DAC8555EVM User's Guide SLAU204 – December 2006
Submit Documentation Feedback

REV ENGINEERING CHANGE NUMBER APPROVED
REVISION HISTORY
JMP7
VDD
D
R1
10KR210KR310KR410KR5NIR6NI
+5VA
C5
0.1uFC210uF
LDAC
ENABLE
RSTSEL
RST
SDI
JMP2
JMP1
1 2
C
B
A
1 2
VCC
C1
10uFC40.1uF
U3
2
3
VCC VSS+5VA -5VA VDD+3.3VD +1.8VD +3.3VA
1 2
VIN
TEMP
JMP3
1
3
5
7
9
1 2
JMP4
GND
REF02AU
4
J3A
+VA
+5VA
DGND
+1.8VD
+3.3VD
1
VOUT
TRIM
2
R10 20K
-VA
-5VA
AGND
VD1
+5VD
SCLK
SYNC
6
5
3
2
4
6
8
10
DAUGHTER-POWER
J3A (TOP) = SAM_TSM-105-01-L-DV-P
J3B (BOTTOM) = SAM_SSW-105-22-F-D-VS-
123
TP1
REF OUT
3
R15
100K
1
R16
20k
+3.3VA
AVDD
R11 0
R12 0
2
U1
4
AVDD
16
LDAC
15
ENABLE
14
RSTSEL
13
RST
11
Din
10
SCLK
9
SYNC
6
GND
DAC8555IPW
VCC
C6
0.1uF
84
3
2
U4A
OPA2132UA
R13
0
VCC = +15V Analog
VDD = +2.7V to +5.0V Digital
VSS = 0V to -15V Analog
VCC
VDD
R14
IO_V/DVDD
VrefH
VrefL
VoutA
VoutB
VoutC
VoutD
C7
0.1uFC310uF
12
3
VrefH
JMP11
5
VrefL
OUT_A
1
2
3
OUT A
JMP12
1
2
7
8
OUT_B
OUT_C
OUT_D
1
2
3
1
2
3
OUT B
JMP13
-REFin
+REFin
J4A
2
A0(+)
A1(+)
A2(+)
A3(+)
A4
A5
A6
A7
REFREF+
A0(-)
A1(-)
A2(-)
A3(-)
AGND
AGND
AGND
VCOM
AGND
AGND
4
6
8
10
12
14
16
18
20
OUTPUT HEADER
J4A (TOP) = SAM_TSM-110-01-L-DV-P
J4B (BOTTOM) = SAM_SSW-110-22-F-D-VS-
123
JMP15
OPA IN
1
3
5
7
9
11
13
15
17
19
U2_+IN
JMP5
1 2
R7
10K
VrefH
0
U2_-IN
3
2
C10
1uF
JMP6
OUT C
JMP14
1
2
3
OUT D
1
JMP8
JMP9
1
2
3
3
2
1
+REFin
-REFin
VrefH
TP2
EXTERNAL
REFERENCE
TP3
NOTE: Voltage range of -REFin input should not exceed
0 - VrefH.
VrefL
TP4
AGND
C8
NI
R17
R18
NI
TP5
+Vin
J1
J5
TP6
-Vin
R19 NI
R20 NI
R21
1
2
3
1
2
3
NI
NI
5
6
U4B
R23
7
NI
OPA2227UA
R22
NI
123
JMP16
OPA OUT
J2A
1
SCLK
SYNC
SDI
RST
CNTL
3
CLKX
5
CLKR
7
FSX
9
FSR
11
DX
13
DR
15
INT
17
TOUT
19
GPIO5
DAUGHTER-SERIAL
J2A (TOP) = SAM_TSM-110-01-L-DV-P
J2B (BOTTOM) = SAM_SSW-110-22-F-D-VS-
C9
VSS
VCC VDD
+5VA
NI
ENGINEER
DRAWN BY
DOCUMENT CONTROL NO.
SHEET OF FILE
J. PARGUIAN
R. BENJAMIN
6486604
1 1 C:\USERDATA\Projects\DAC8555\DAC8555EVM .ddb
C11
1uF
71
U2
U2_OUT
6
OPA627AU
5
4
VSS
123
R24
100
JMP10
R8
10K
C12
1nF
R9
12
10K
LDAC
2
GPIO0
4
DGND
6
GPIO1
GPIO2
DGND
GPIO3
GPIO4
SCL
DGND
SDA
ENABLE
8
10
12
RSTSEL
14
16
18
20
ti
DATA ACQUISITION PRODUCTS
HIGH-PERFORMANCE ANALOG DIVISION
SEMICONDUCTOR GROUP
6730 SOUTH TUCSON BLVD., TUCSON, AZ 85706 USA
TITLE
SIZE
DAC8555EVM
B
DATE REV
A11-Oct-2006
D
C
B
A

FCC Warning
This evaluation board/kit is intended for use for ENGINEERING DEVELOPMENT, DEMONSTRATION, OR EVALUATION
PURPOSES ONLY and is not considered by TI to be a finished end-product fit for general customer use. It generates, uses, and
can radiate radio frequency energy and has not been tested for compliance with the limits of computing devices pursuant to part 15
of FCC rules, which are designed to provide reasonable protection against radio frequency interference. Operation of this
equipment in other environments may cause interference with radio communications, in which case the user at his own expense
will be required to take whatever measures may be required to correct this interference.
EVALUATION BOARD/KIT IMPORTANT NOTICE
Texas Instruments (TI) provides the enclosed product(s) under the following conditions:
This evaluation board/kit is intended for use for ENGINEERING DEVELOPMENT, DEMONSTRATION, OR EVALUATION
PURPOSES ONLY and is not considered by TI to be a finished end-product fit for general consumer use. Persons handling the
product(s) must have electronics training and observe good engineering practice standards. As such, the goods being provided are
not intended to be complete in terms of required design-, marketing-, and/or manufacturing-related protective considerations,
including product safety and environmental measures typically found in end products that incorporate such semiconductor
components or circuit boards. This evaluation board/kit does not fall within the scope of the European Union directives regarding
electromagnetic compatibility, restricted substances (RoHS), recycling (WEEE), FCC, CE or UL, and therefore may not meet the
technical requirements of these directives or other related directives.
Should this evaluation board/kit not meet the specifications indicated in the User’s Guide, the board/kit may be returned within 30
days from the date of delivery for a full refund. THE FOREGOING WARRANTY IS THE EXCLUSIVE WARRANTY MADE BY
SELLER TO BUYER AND IS IN LIEU OF ALL OTHER WARRANTIES, EXPRESSED, IMPLIED, OR STATUTORY, INCLUDING
ANY WARRANTY OF MERCHANTABILITY OR FITNESS FOR ANY PARTICULAR PURPOSE.
The user assumes all responsibility and liability for proper and safe handling of the goods. Further, the user indemnifies TI from all
claims arising from the handling or use of the goods. Due to the open construction of the product, it is the user’s responsibility to
take any and all appropriate precautions with regard to electrostatic discharge.
EXCEPT TO THE EXTENT OF THE INDEMNITY SET FORTH ABOVE, NEITHER PARTY SHALL BE LIABLE TO THE OTHER
FOR ANY INDIRECT, SPECIAL, INCIDENTAL, OR CONSEQUENTIAL DAMAGES.
TI currently deals with a variety of customers for products, and therefore our arrangement with the user is not exclusive.
TI assumes no liability for applications assistance, customer product design, software performance, or infringement of
patents or services described herein.
Please read the User’s Guide and, specifically, the Warnings and Restrictions notice in the User’s Guide prior to handling the
product. This notice contains important safety information about temperatures and voltages. For additional information on TI’s
environmental and/or safety programs, please contact the TI application engineer or visit www.ti.com/esh .
No license is granted under any patent right or other intellectual property right of TI covering or relating to any machine, process, or
combination in which such TI products or services might be or are used.
EVM WARNINGS AND RESTRICTIONS
It is important to operate this EVM within the input voltage range of–15.75V to +15.75V and the output voltage range of –15V to
+15V.
Exceeding the specified input range may cause unexpected operation and/or irreversible damage to the EVM. If there are
questions concerning the input range, please contact a TI field representative prior to connecting the input power.
Applying loads outside of the specified output range may result in unintended operation and/or possible permanent damage to the
EVM. Please consult the EVM User's Guide prior to connecting any load to the EVM output. If there is uncertainty as to the load
specification, please contact a TI field representative.
During normal operation, some circuit components may have case temperatures greater than 60 ° C. The EVM is designed to
operate properly with certain components above 60 ° C as long as the input and output ranges are maintained. These components
include but are not limited to linear regulators, switching transistors, pass transistors, and current sense resistors. These types of
devices can be identified using the EVM schematic located in the EVM User's Guide. When placing measurement probes near
these devices during operation, please be aware that these devices may be very warm to the touch.
Mailing Address: Texas Instruments, Post Office Box 655303, Dallas, Texas 75265
Copyright© 2006, Texas Instruments Incorporated

IMPORTANT NOTICE
Texas Instruments Incorporated and its subsidiaries (TI) reserve the right to make corrections, modifications, enhancements,
improvements, and other changes to its products and services at any time and to discontinue any product or service without notice.
Customers should obtain the latest relevant information before placing orders and should verify that such information is current and
complete. All products are sold subject to TI’s terms and conditions of sale supplied at the time of order acknowledgment.
TI warrants performance of its hardware products to the specifications applicable at the time of sale in accordance with TI’s
standard warranty. Testing and other quality control techniques are used to the extent TI deems necessary to support this
warranty. Except where mandated by government requirements, testing of all parameters of each product is not necessarily
performed.
TI assumes no liability for applications assistance or customer product design. Customers are responsible for their products and
applications using TI components. To minimize the risks associated with customer products and applications, customers should
provide adequate design and operating safeguards.
TI does not warrant or represent that any license, either express or implied, is granted under any TI patent right, copyright, mask
work right, or other TI intellectual property right relating to any combination, machine, or process in which TI products or services
are used. Information published by TI regarding third-party products or services does not constitute a license from TI to use such
products or services or a warranty or endorsement thereof. Use of such information may require a license from a third party under
the patents or other intellectual property of the third party, or a license from TI under the patents or other intellectual property of TI.
Reproduction of information in TI data books or data sheets is permissible only if reproduction is without alteration and is
accompanied by all associated warranties, conditions, limitations, and notices. Reproduction of this information with alteration is an
unfair and deceptive business practice. TI is not responsible or liable for such altered documentation.
Resale of TI products or services with statements different from or beyond the parameters stated by TI for that product or service
voids all express and any implied warranties for the associated TI product or service and is an unfair and deceptive business
practice. TI is not responsible or liable for any such statements.
TI products are not authorized for use in safety-critical applications (such as life support) where a failure of the TI product would
reasonably be expected to cause severe personal injury or death, unless officers of the parties have executed an agreement
specifically governing such use. Buyers represent that they have all necessary expertise in the safety and regulatory ramifications
of their applications, and acknowledge and agree that they are solely responsible for all legal, regulatory and safety-related
requirements concerning their products and any use of TI products in such safety-critical applications, notwithstanding any
applications-related information or support that may be provided by TI. Further, Buyers must fully indemnify TI and its
representatives against any damages arising out of the use of TI products in such safety-critical applications.
TI products are neither designed nor intended for use in military/aerospace applications or environments unless the TI products are
specifically designated by TI as military-grade or "enhanced plastic." Only products designated by TI as military-grade meet military
specifications. Buyers acknowledge and agree that any such use of TI products which TI has not designated as military-grade is
solely at the Buyer's risk, and that they are solely responsible for compliance with all legal and regulatory requirements in
connection with such use.
TI products are neither designed nor intended for use in automotive applications or environments unless the specific TI products
are designated by TI as compliant with ISO/TS 16949 requirements. Buyers acknowledge and agree that, if they use any
non-designated products in automotive applications, TI will not be responsible for any failure to meet such requirements.
Following are URLs where you can obtain information on other Texas Instruments products and application solutions:
Products Applications
Amplifiers amplifier.ti.com Audio www.ti.com/audio
Data Converters dataconverter.ti.com Automotive www.ti.com/automotive
DSP dsp.ti.com Broadband www.ti.com/broadband
Interface interface.ti.com Digital Control www.ti.com/digitalcontrol
Logic logic.ti.com Military www.ti.com/military
Power Mgmt power.ti.com Optical Networking www.ti.com/opticalnetwork
Microcontrollers microcontroller.ti.com Security www.ti.com/security
RFID www.ti-rfid.com Telephony www.ti.com/telephony
Low Power www.ti.com/lpw Video & Imaging www.ti.com/video
Wireless
Wireless www.ti.com/wireless
Mailing Address: Texas Instruments, Post Office Box 655303, Dallas, Texas 75265
Copyright © 2007, Texas Instruments Incorporated