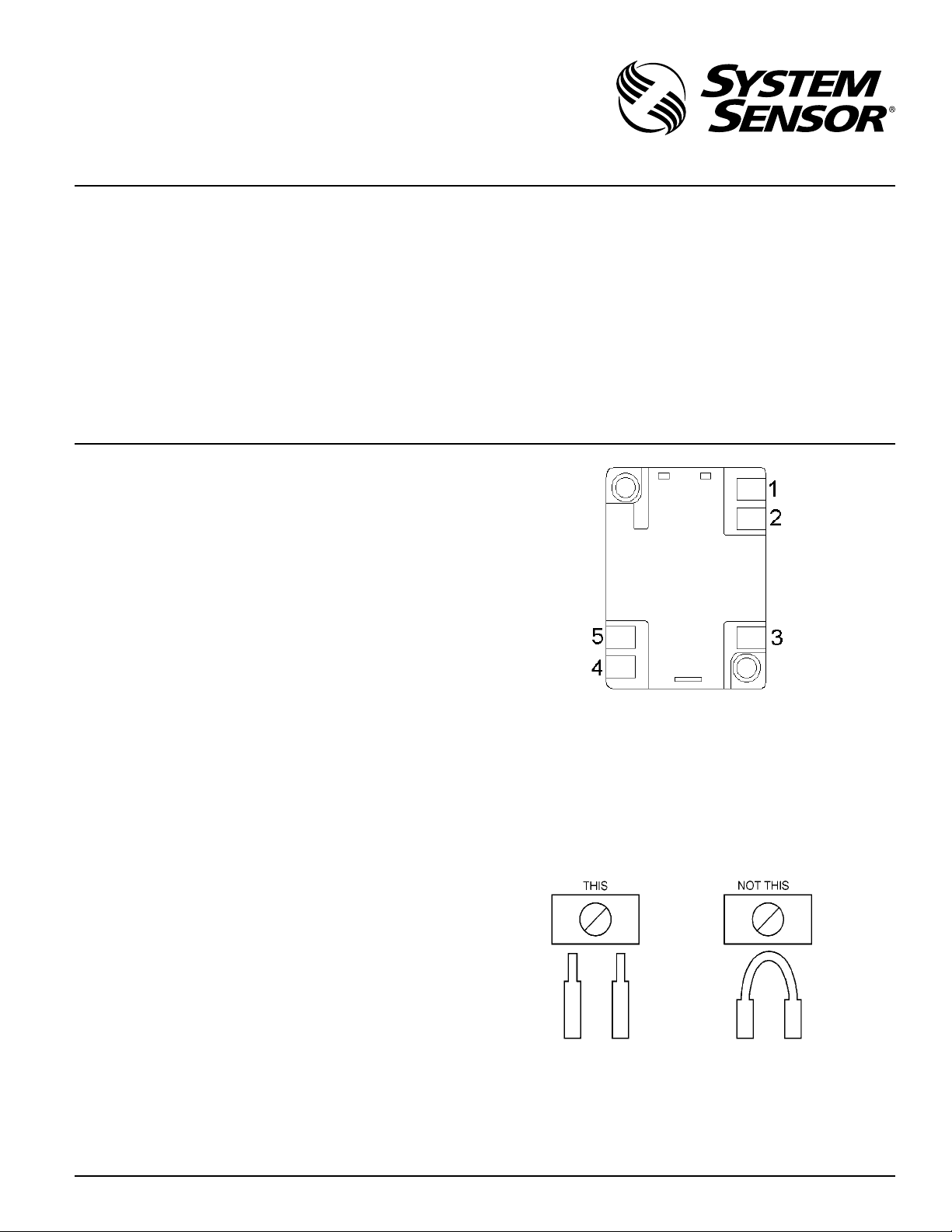
INSTALLATION AND MAINTENANCE INSTRUCTIONS
I56-0612-006R
B401BH and B401BHA
Sounder Bases
SpECIfICATIONS
Base Diameter: 6 inches (152 mm)
Base Height (less base and sensor): 0.75 inches (19mm)
Weight: 0.3 lb. (140 g)
Operating Temperature Range: 14° to 140°F (–10° to +60°C)
Operating Humidity Range: 10% to 95%, noncondensing
Electrical Ratings
Voltage: 17 to 32 VDC
Standby Current: 1.0 mA maximum
Alarm Current: 15 mA maximum
Maximum Ripple Voltage: 10% of supply voltage
Start-up Capacitance: 200 µF
Horn Input Current Requirement: 600 µA maximum
Sound Output: Greater than 90 dBa measured in anechoic room at 10 feet (3 meters),
24 volts. 85 dBa minimum measured in UL reverberant room.
BEfORE INSTALLINg
Please read the
detailed information on detector spacing, placement, zoning, wiring, and
special applications. Copies of this manual are available from System Sensor. NFPA 72 and NEMA
in Canada, refer to CAN/ULC-S524, Standard for the Installation of Fire
Alarm Systems and CEC Part 1, Sec. 32.)
NOTICE: This manual should be left with the owner/user of this equipment.
IMPORTANT: The detector used with these bases must be tested and maintained regularly following NFPA 72 requirements. The detector should be
cleaned at least once a year.
System Smoke Detector Application Guide
guidelines
should be observed. (For installation
, which provides
fIgURE 1. TERMINAL LAyOUT :
3825 Ohio Avenue, St. Charles, Illinois 60174
1-800-SENSOR2, FAX: 630-377-6495
www.systemsensor.com
gENERAL DESCRIpTION
Models B401BH and B401BHA sounder bases are intended for use with System Sensor 400 Series plug-in sensor heads in conventional 2-wire plug-in
systems. Refer to systems manuals for the maximum allowable number of
units per loop. The B401BH requires an external 24VDC (nominal) supply
with reverse polarity capability. The connections of the external supply (terminals 1 and 2) and the initiating loop (terminals 3, 4, and 5) are isolated in the
B401BH to prevent electrical interaction between them.
When the detector head’s visible LEDs are latched on for approximately 10
seconds, the associated horn sounds. A loop of horns can be made to sound
by reversing the polarity of the external supply.
NOTE: When the associated system is NOT used as a supplementary evacuation system, the external 24VDC supply must be treated as a component of the
main power supply system with the result that it falls under the requirements
of NFPA 72.
B401BH AND B401BHA TERMINALS
No. Function
1 External Supply Positive (+)
2 External Supply Negative (–)
3 Negative (–) V
4 Positive (+) V In
5 Positive (+) V Out
Terminals 3, 4, and 5 are used for the communication/initiating circuit.
INSTALLATION WIRINg gUIDELINES
All wiring must be installed in compliance with the National Electrical Code
and all applicable local codes and any special requirements of the authority
having jurisdiction, using the proper wire size. The conductors used to connect smoke detectors to control panels and accessory devices should be colorcoded to reduce the likelihood of wiring errors. Improper connections can
prevent a system from responding properly in the event of a fire.
C0471-00
For signal wiring (the wiring between interconnected detectors), it is recommended that the wire be no smaller than AWG 18. However, the screws and
clamping plate in the base can accommodate wire sizes up to AWG 12. The
use of twisted pair wiring or shielded cable for the power (+ and –) loop is
recommended to minimize the effects of electrical interference on the initiating loop.
Begin electrical connections by stripping about 3/8” insulation from the end
of the wire. Then, slide the bare end of the wire under the clamping plate and
tighten the clamping plate screw. Break the wire at each terminal to ensure
that the connections are supervised, as shown in Figure 2.
fIgURE 2.
C0473-00
DO NOT loop the wire under the clamping plate.
Check the zone wiring of the detector base before the detector heads are installed. Perform continuity, base polarity, and dielectric tests on the wiring.
Smoke detectors and alarm system control panels have specifications for allowable supervision current. Consult the control panel manufacturer’s specifications for the total loop current supervision allowed for the control panel
being used before wiring the detector loops.
D400-50-00 1 I56-0612-006R
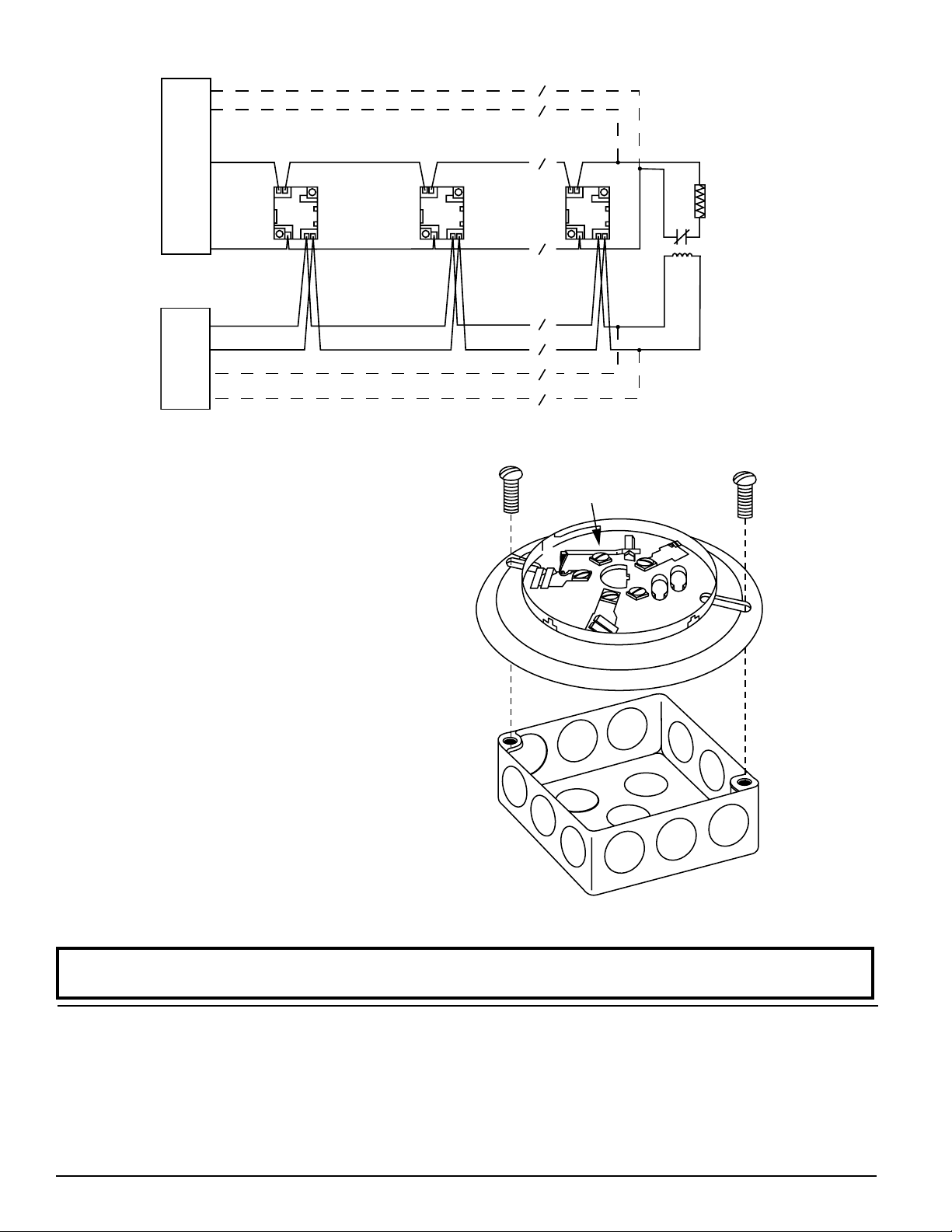
fIgURE 3. TypICAL WIRINg LAyOUT :
CLASS A OPTIONAL WIRING
(+) INIT.
4
5
3
2
UL LISTED COMPATIBLE
CONVENTIONAL CONTROL PANEL
SUPPLY
EXTERNAL 24V
(−) INIT.
(−)POWER
(+)POWER
4
5
3
1
2
CLASS A OPTIONAL WIRING
WIRINg INSTRUCTIONS
The shorting spring in the base will disengage automatically when the detector head is removed from the base.
DO NOT remove the shorting spring since it reengages as the detector head is
turned into the base, completing the circuit.
A typical wiring for a two-wire conventional system is shown in Figure 3. Refer to this diagram as needed while wiring the base into the system.
NOTE: Figure 3 shows external 24V supply polarity when the loop system is
in standby (NOT alarming).
MOUNTINg
NOTE: It is recommended that the base be completely wired before mounting.
See Figure 4. Attach the base directly to an electrical box using the screws
supplied with the box. Then, use the plastic screw covers, supplied with the
base, to cover the screws.
The sounder base is 1.1 inches (28 mm) deep. Electrical boxes must be 4
inches (102 mm) square by at least 1-1/2 inches (38 mm) deep; 2-1/8 inches
(54 mm) is recommended.
TESTINg
Before testing, notify the proper authorities that the smoke detector system
is undergoing maintenance and that the system will be temporarily out of
service. Disable the zone or system undergoing maintenance to prevent unwanted alarms.
Detectors and bases must be tested after installation and following periodic
maintenance.
Test the B401BH/B401BHA as follows:
1. Test the conventional detector head following the procedure in its manual.
The B401BH/B401BHA should sound approximately 10 seconds after the
detector alarms.
2. Reverse the polarity of the external 24 VDC supply. This should cause every
base in the loop to sound after approximately 10 seconds.
4
5
1
3
1
2
UL
LISTED
EOL
RELAY
24V
fIgURE 4. MOUNT BASE TO ELECTRICAL BOx:
SHORTING
SPRING
UL
LISTED EOL
RESISTOR
C0956-01
SCREWS
(NOT SUPPLIED)
DETECTOR
BASE
BOX
(NOT SUPPLIED)
C0503-01
Please refer to insert for the Limitations of Fire Alarm Systems
THREE-yEAR LIMITED WARRANTy
System Sensor warrants its enclosed base to be free from defects in materials and
workmanship under normal use and service for a period of three years from date of
manufacture. System Sensor makes no other express warranty for this base. No agent,
representative, dealer, or employee of the Company has the authority to increase or alter
the obligations or limitations of this Warranty. The Company’s obligation of this Warranty
shall be limited to the repair or replacement of any part of the base which is found to
be defective in materials or workmanship under normal use and service during the three
year period commencing with the date of manufacture. After phoning System Sensor’s
toll free number 800-SENSOR2 (736-7672) for a Return Authorization number, send
defective units postage prepaid to: System Sensor, Repair Department, RA #__________,
D400-50-00 2 I56-0612-006R
©2010 System Sensor
3825 Ohio Avenue, St. Charles, IL 60174. Please include a note describing the malfunction and suspected cause of failure. The Company shall not be obligated to repair or
replace units which are found to be defective because of damage, unreasonable use,
modifications, or alterations occurring after the date of manufacture. In no case shall the
Company be liable for any consequential or incidental damages for breach of this or any
other Warranty, expressed or implied whatsoever, even if the loss or damage is caused by
the Company’s negligence or fault. Some states do not allow the exclusion or limitation of
incidental or consequential damages, so the above limitation or exclusion may not apply
to you. This Warranty gives you specific legal rights, and you may also have other rights
which vary from state to state.