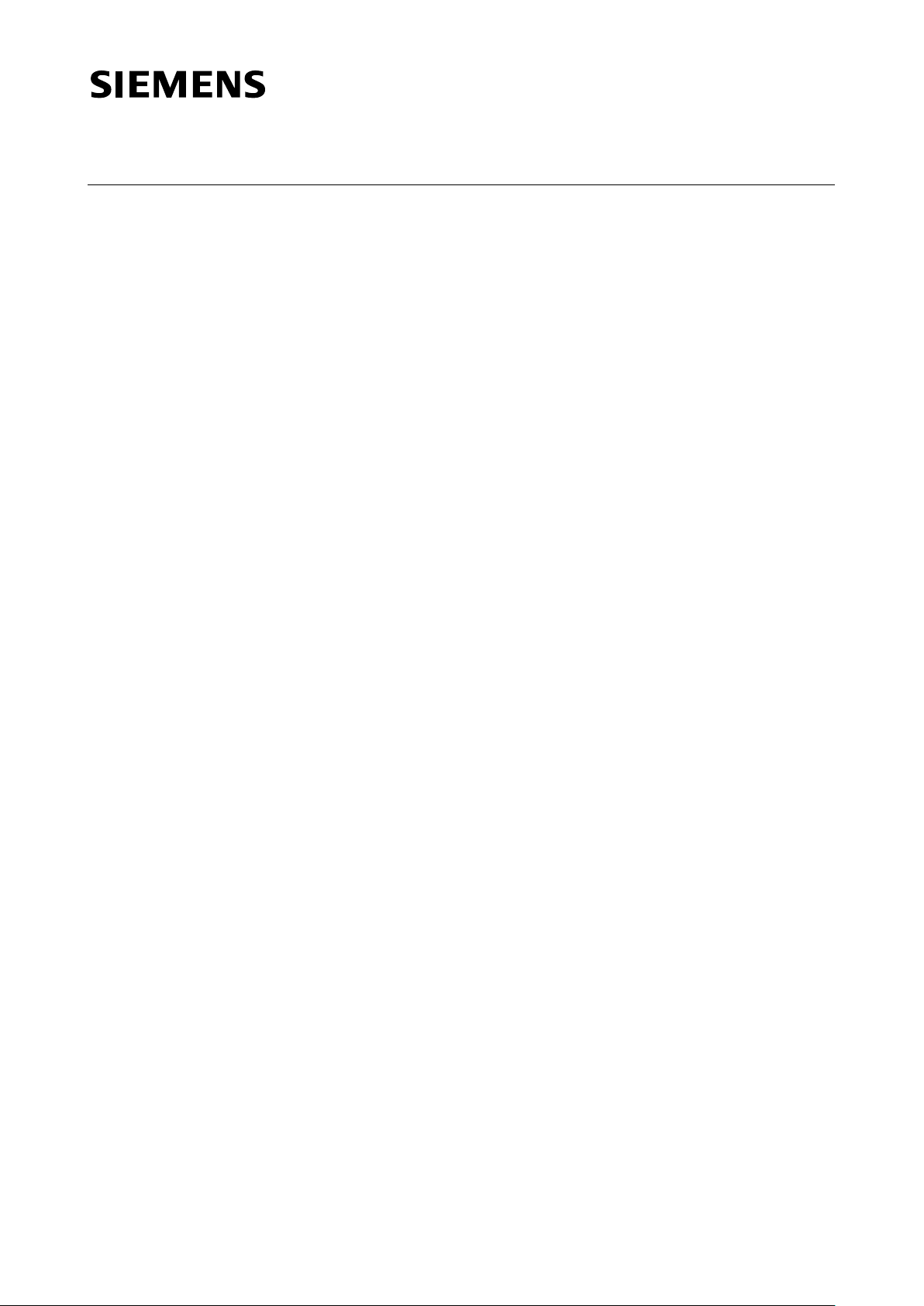
Nuremberg, Germany February 1,
2021
MediaService Digital Industries
Siemens AG
Communications
Head: Clarissa Haller
Wittelsbacherplatz 2
80333 Munich
Germany
Old and new – perfectly combined
• Modernizing of key facility for production of inner races with Siemens RFID
technology
Offenbach am Main, Germany. GKN Driveline Offenbach, supplier of power
transmission systems and solutions for the automotive industry, relies on
RFID technology from Siemens to modernise its key facility for production of
inner races. The new RFID solution for workpiece recognition could be
implemented during ongoing operations, so that the 30-year-old plant
contributes to productivity at the site.
The flexible, automated production – FAP facility for short – takes up almost an
entire hall at GKN Driveline in Offenbach. Every second, the long broaches at the
five broaching machines raise and lower, and parts are conveyed from the
machining to the washer, the hardening equipment and the tempering furnace.
Here, the company produces a majority of its inner races, which are the core
component in constant-velocity joint assemblies in countless vehicles. All machines
are linked together: Up to 12 workpieces are automatically transported on pallets
from one station to the next and machined in accordance with the specification. In
order for the workpieces to pass through every work step exactly as specified, each
of the pallets is equipped with an RFID tag. On the tag, the information on the
workpieces and the process are stored, which is updated as steps are gone through
– so that it is always possible to comprehend which steps have already been
completed and which ones are still pending. By means of readers, each pallet is
identified, fed to the corresponding machining station, and transferred back to the
conveyor systems after completion of the work step – completely without manual
Frei verwendbar Page 1/3
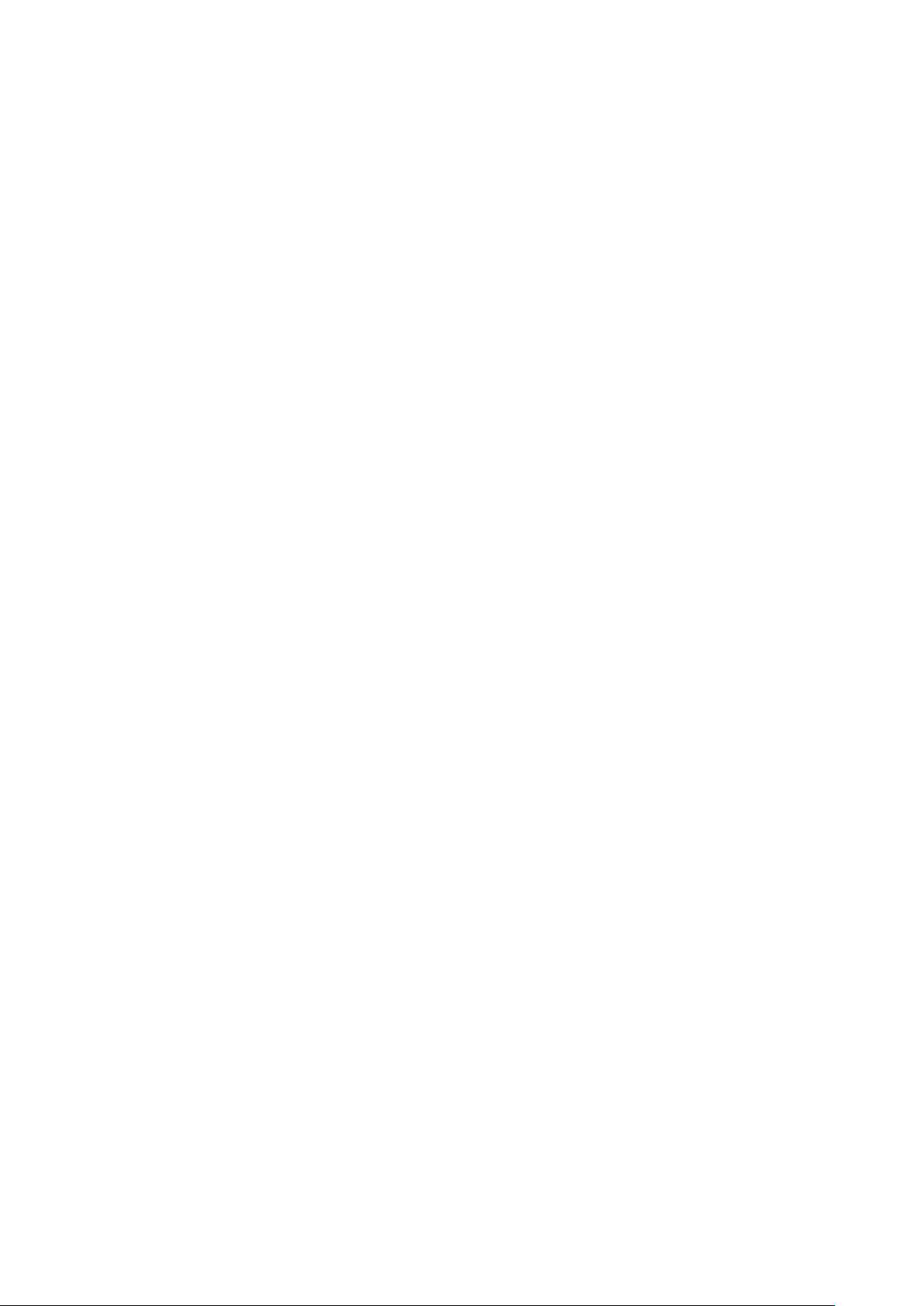
intervention. The complex processes have been controlled for more than 30 years
by a Simatic S5, which is still reliable doing its duty today around the clock and is
absolutely critical for the productivity here at this site.
Time-sensitive modernization of a key facility
Nevertheless
and again – and since the entire production at the Offenbach location is affected by the
downtime of this facility, availability is always paramount, explains Andreas Bartsch, GKN
Driveline Site Service Maintenance. “For scheduled repairs to the facility, we always have
only small time windows available. It is therefore important that a new component can be
integrated as smoothly as possible.” This also applies to the modernisation of a total of 40
Moby I readers for reading out and writing tags on the pallets. Important was for the new
RFID system to be compatible with the existing automation technology in particular with the
existing S5 controller.
, central components of the facility have to be replaced or modernized again
With the new solution the current Simatic RF350 readers can
easily be connected to the existing interface of the Simatic S5 via an adapter cable.
The reader automatically detects the serial protocol and sets the Moby I protocol if it
is connected to a Moby I-capable communication module. The Moby I emulation
processes the telegrams of the Moby I protocol at its serial interface and
communicates the information seamlessly using the matching RF300 transponders.
As a result, GKN Driveline could continue to use the existing configuration, which
considerably simplified the conversion. In addition, to avoid possible production
downtimes, the new system was put into operation in only three days during the
Christmas shutdown. Since their successful commissioning, the new Simatic RF
systems have been working reliably.
GKN Driveline
With approximately 26,000 employees at 46 production sites in 26 countries, GKN
Driveline is the world's leading system developer for drive train technologies with its
constant-velocity joint assemblies and solutions for all-wheel/4-wheel drive and
electromobility. GKN is the only Tier One supplier with a complete portfolio of
system technologies for constant-velocity joints. The company supplies key drive
train components, eDrive and all-wheel/4-wheel drive systems, and is a leading
provider of both torque vectoring and eDrive systems.
Frei verwendbar Page 2/3

This MediaService information and further material are available at
https://press.siemens.com/global/en/article/mediaservice-digital-industries-
newsroom
For further information on Identification and Locating, please see
<www.siemens.com/ident> .
Contact for journalists:
Ursula Lang
Phone: +49 (152) 22915052; E-mail: Ursula.Lang@siemens.com
Follow us on Social Media:
Twitter: www.twitter.com/MediaServiceInd and www.twitter.com/siemens_press
MediaService: https://press.siemens.com/global/en/article/mediaservice-digital-
industries-newsroom
Siemens AG (Berlin and Munich) is a global technology powerhouse that has stood for engineering excellence,
innovation, quality, reliability and internationality for more than 170 years. Active around the world, the company
focuses on intelligent infrastructure for buildings and distributed energy systems and on automation and
digitalization in the process and manufacturing industries. Siemens brings together the digital and physical worlds to
benefit customers and society. Through Mobility, a leading supplier of intelligent mobility solutions for rail and road
transport, Siemens is helping to shape the world market for passenger and freight services. Via its majority stake in
the publicly listed company Siemens Healthineers, Siemens is also a world-leading supplier of medical technology
and digital health services. In addition, Siemens holds a minority stake in Siemens Energy, a global leader in the
transmission and generation of electrical power that has been listed on the stock exchange since
September 28, 2020.
In fiscal 2019, which ended on September 30, 2019, the Siemens Group generated revenue of €58.5 billion and net
income of €5.6 billion. As of September 30, 2019, the company had around 295,000 employees worldwide on the
basis of continuing operations. Further information is available on the Internet at www.siemens.com.
Frei verwendbar Page 3/3